数控机床中伺服系统现状分析(doc 5)
数控机床进给伺服系统类故障诊断与处理(3篇)

数控机床进给伺服系统类故障诊断与处理数控机床进给伺服系统是数控机床中非常关键的一个组成部分,它直接影响机床加工的精度和效率。
然而,在使用过程中,由于各种原因,进给伺服系统可能会出现故障。
本文将介绍数控机床进给伺服系统的常见故障及其诊断与处理方法。
一、数控机床进给伺服系统常见故障1. 运动不平稳:机床在加工工件时,出现运动不平稳的情况,可能是由于进给伺服系统的故障引起的。
这种情况表现为运动过程中有明显的抖动或者不稳定的现象。
2. 运动失效:机床无法正常运动,不响应操作指令。
这种情况可能是由于进给伺服系统的电源故障、控制器故障或者连接线路故障引起的。
3. 位置误差过大:机床在加工过程中,位置误差超过了允许范围,导致加工工件的尺寸不准确。
这种情况可能是由于进给伺服系统的位置反馈元件(如编码器)故障引起的。
4. 加工速度过慢:机床在加工时,进给速度远低于预设值,导致加工效率低下。
这种情况可能是由于进给伺服系统的电机故障或者速度控制回路故障引起的。
二、故障诊断与处理方法1. 运动不平稳的诊断与处理:首先,检查机床的润滑系统,确保润滑油是否充足,并且清洁。
其次,检查机床的传动系统,确保螺杆和导轨的润滑良好。
如果问题还未解决,可以通过检查进给伺服系统的控制器参数是否正确、电机驱动器是否正常工作等方式进一步诊断。
2. 运动失效的诊断与处理:首先,检查进给伺服系统的电源供应情况,确保电源正常。
其次,检查进给伺服系统的连接线路,包括电源线、编码器连接线等,确保线路没有松动或者断裂。
如果问题还未解决,可以通过检查进给伺服系统的控制器和电机驱动器是否正常工作等方式进一步诊断。
3. 位置误差过大的诊断与处理:首先,检查进给伺服系统的位置反馈元件,如编码器是否损坏或者松动。
如果问题还未解决,可以通过检查进给伺服系统的控制器参数是否正确、电机驱动器是否正常工作等方式进一步诊断。
4. 加工速度过慢的诊断与处理:首先,检查进给伺服系统的电机是否正常工作,包括电机是否有异常声音或者发热等。
数控机床伺服系统的性能分析及其调整

电流环 参数, 设计 中 已保证 电流环 有足够 的增益 响应 : 然后调 整速度环 参数 : 最 后 调整 位置 环参 数 。 只有 电流 环和速 度环 的伺服 参数 设置 合适, 能得到 较 高 才
较好 的伺 服性 能, 图 3 如 : () 噪音 能力 5抗
;
鎏;
撇 脚。哥 ; 伺服系统 的抗噪音 能力描 述 了系统对噪 音源的放 大程度, 噪音干扰会 导致
系统 发热 、振 荡、扭矩 波动 和杂音 等 不 良现 象 。 服增益 越 高, 伺 系统 的抗噪 音
能力 将越 低, 图 4 如 。 2伺服 系统的 调 整过 程研 究
表 1N — C 定 CP 设
圜
() a 快速 响应
图6 :第一组参数
圈 2 ()畸应迟疆 b
… 。 ‘
‘ 翻4
第二组参数
I 玮L_ 环 越 二董 鱼_
当为 蔓座硷 麓鬟式 辩 准鲁) .. 傅疆 簟元
表 2 速度 环调试 参数
要快, 方面要 求过 渡过程 时 间短, ~ 一般 在 20 s 内, 0m 以 甚至 小于几 十毫 秒, 且 速 度变化 时不会有 超调 : 另一方面 是 当负载突 变时, 要求过 渡过程 的前沿 陡, 即 上升率 要大, 复的 时间要 短且 无震 荡 。对 大部分 的伺服 系 统来说 , 恢 追求较 快
科 学论 坛
●I
数控机床 伺服 系统 的性 能分 析及其 调整
白晓灿
( 厦门大 学机 电工程 系 福建 厦门 3 10 ) 60 5 [ 摘 要] 控机床 伺 服系 统调 整的好 会 极大 地影 响 了机床 的加 工性 能 。本 文分 析 了伺服 系 统的性 能 , 数 通过试 验 分析 , 讨论 了针 对一 个伺 服系 统如 何调整 使系 统达 到最 佳 : 介绍 了伺服 系统 增 益调 整 的基 本准 则和 设 定方 法 。 [ 关键 词] 伺服 系统 性 能分 析 增 益 调整 中图分 类号 :G 1 T 6 文献标 识码 : A 文章编 号 :0 9 9 4 (0 0 3 — 0 9 0 10 — 1X2 1 ) 103 2
国内数控机床现状解析与建议(doc 14页)

国内数控机床现状解析与建议(doc 14页)国内数控机床现状简析及建议一、国内数控机床行业近年取得的成绩我国的数控机床无论从产品种类、技术水平、质量和产量上都取得了很大的发展,在一些关键技术方面也取得了重大突破。
据统计,目前我国可供市场的数控机床有1500种,几乎覆盖了整个金属切削机床的品种类别和主要的锻压机械。
领域之广,可与日本、德国、美国并驾齐驱。
这标志着国内数控机床已进入快速发展的时期。
近年来我国机床行业不断承担为国家重点工程和国防军工建设提供高水平数控设备的任务。
如国产XNZD2415型数控龙门混联机床充分吸取并联机床的配置灵活与多样性和传统机床加工范围大的优点,通过两自由度平行四边形并联机构形成基础龙门,在并联平台上附加两自由度串联结构的A、C轴摆角铣头,配以工作台的纵向移动,可完成五自由度的运动。
该构型为国际首创。
基于RT一Linux开发的数控系统具有的实时性和可靠性,能在同一网络中与多台PLC相连接,可控制机床的五轴联动,实现人机对话。
该机床的作业空间4.5mx1.6mx1.2m,A轴转角±1050,C轴连续转角0一4000,主轴转速(无级)最高10000r/min,重复定位精钢类零件)进行中低转速下的强力切削,也适宜冶金、机车、造纸机械等行业对大型工件特别是长轴类零件进行高效、强力车削时采用。
TK68125A型落地式数控镗铣床可广泛适用于大中型柴油机、工程机械、汽车、船舶、航天航空工业的大中型复杂结构件加工,特别适用于对具有空间曲面的复杂零件高速、高效加工。
TK6913B型落地式数控镗铣床在高刚度方滑枕、数控可移动主轴组件、数控回转工作台、数控平旋盘、大型链式刀库、模块化开发等方面形成了自己的核心技术。
陕西汉江机床有限公司把为数控机床配套的高精度滚珠丝杠副和滚动直线导轨副作为主攻方向,2004年共生产滚珠丝杠副5万套,滚动直线导轨副2万套,其中为数控机床配套的高精度产品占产销量的80%以上。
数控机床进给伺服系统类故障诊断与处理范文(4篇)

数控机床进给伺服系统类故障诊断与处理范文数控机床进给伺服系统是数控机床的重要组成部分,负责驱动工件或刀具在加工过程中进行准确的运动。
然而,由于工作环境恶劣以及长时间使用,进给伺服系统可能会出现各种故障。
本文将介绍数控机床进给伺服系统故障的诊断与处理方法。
一、断电故障:当进给伺服系统无法正常工作或反应迟缓时,首先需要检查是否存在断电故障。
可以检查电源和连接器是否正常。
如果确认没有断电故障,可以进一步诊断。
二、电缆故障:电缆故障是数控机床进给伺服系统常见的故障之一。
可以通过检查电缆连接器的接触情况、电缆是否断裂或接触不良来判断是否存在电缆故障。
如果发现电缆故障,应及时更换或修复受损的电缆。
三、伺服驱动器故障:伺服驱动器是控制进给伺服系统的主要部件,当进给伺服系统出现故障时,可以首先检查伺服驱动器是否正常工作。
可以通过检查伺服驱动器的电源供应情况、电流是否稳定以及反馈信号是否正常来判断是否存在伺服驱动器故障。
如果发现伺服驱动器故障,应及时更换或修复故障的部件。
四、编码器故障:编码器是进给伺服系统的重要传感器,用于检测工件或刀具的位置信息。
当进给伺服系统无法准确移动或位置偏差较大时,可以检查编码器是否损坏或接触不良。
如果发现编码器故障,应及时更换或修复故障的部件。
五、电机故障:电机是驱动进给伺服系统运动的关键部件,当进给伺服系统无法正常工作或运动异常时,可以检查电机是否正常工作。
可以通过检查电机的电源供应情况、电流是否稳定以及转动是否平稳来判断是否存在电机故障。
如果发现电机故障,应及时更换或修复故障的部件。
六、控制器故障:控制器是进给伺服系统的核心部件,当进给伺服系统无法正常工作或运动异常时,可以检查控制器是否正常工作。
可以通过检查控制器的电源供应情况、信号是否稳定以及参数设置是否正确来判断是否存在控制器故障。
如果发现控制器故障,应及时更换或修复故障的部件。
以上是数控机床进给伺服系统常见故障的诊断与处理方法。
数控机床的伺服系统

第6章 数控机床的伺服系统
伺服驱动装置
位置控制模块 速度控制单元
工作台 位置检测
速度环 速度检测 位置环
伺服电机
测量反馈
图6-1 闭环进给伺服系统结构
数控机床闭环进给系统的一般结构如图,这是一个双闭环系统,内 环为速度环,外环为位置环。速度环由速度控制单元、速度检测装置等构成。 速度控制单元是一个独立的单元部件,它是用来控制电机转速的,是速度控 制系统的核心。速度检测装置有测速发电机、脉冲编码器等。位置环是由 CNC装置中的位置控制模块、速度控制单元、位置检测及反馈控制等部分组 成。
第6章 数控机床的伺服系统
A C1 B4 2 B 3C A
逆时针转30º
C 4 B
A 1 2 3 A
B
C 1 B
A 2
B 3 C
C
逆时针转30º
4 A
第6章 数控机床的伺服系统
采用三相双三拍控制方式,即通电顺序按AB→BC→CA→AB(逆时针 方向)或AC→CB→BA→AC(顺时针方向)进行,其步距角仍为30。由于 双三拍控制每次有二相绕组通电,而且切换时总保持一相绕组通电,所以 工作比较稳定。
第6章 数控机床的伺服系统
设 A 相首先通电,转子齿与定子 A 、 A′ 对齐(图 3a )。然后在 A 相继续通电的情 况下接通 B 相。这时定子 B 、 B′ 极对转子 齿 2 、 4 产生磁拉力,使转子顺时针方向转 动,但是 A 、 A′ 极继续拉住齿 1 、 3 ,因 此,转子转到两个磁拉力平衡为止。这时转 子的位置如图 3b 所示,即转子从图 (a) 位 置顺时针转过了 15° 。接着 A 相断电, B 相继续通电。这时转子齿 2 、 4 和定子 B 、 B′ 极对齐(图 c ),转子从图 (b) 的位置又 转过了 15° 。其位置如图 3d 所示。这样, 如果按 A→A 、 B→B→B 、 C→C→C 、 A→A… 的顺序轮流通电,则转子便顺时针 方向一步一步地转动,步距角 15° 。电流 换接六次,磁场旋转一周,转子前进了一个 齿距角。如果按 A→A 、 C→C→C 、 B→B→B 、 A→A… 的顺序通电,则电机 转子逆时针方向转动。这种通电方式称为六 拍方式。
伺服技术在数控加工中的应用

伺服技术在数控加工中的应用随着数控机床的发展,越来越多的加工过程正在向高速化、智能化方向发展。
而伺服系统作为数控机床的核心控制系统,其发展对数控机床的精度、速度和可靠性等方面起着至关重要的作用。
本文将介绍伺服技术在数控加工中的应用,探讨其优势和未来发展方向。
一、伺服技术的概述伺服技术是指利用电机系统的反馈控制技术,通过对电机系统位置、速度和加速度等参数进行反馈控制,实现对机器运动精度、稳定性和速度的控制技术。
伺服技术在工业生产中广泛应用于机床、自动化生产线、机器人等领域,使机器运动更加稳定、精确,提高了工作效率和生产质量。
二、伺服技术作为数控机床的核心控制系统,在数控机床加工过程中,主要应用于以下方面:1、控制轴运动数控机床的加工过程中,需要实时控制工件在X、Y、Z三个方向上的运动,这就需要利用伺服系统进行轴控制,确保机床工作精度和加工质量。
2、控制进给系统伺服系统还可实现对加工进给速度的精确控制,确保加工过程中的进给速度达到要求,同时避免出现过大或过小的进给量,保障工件加工质量。
3、控制加工精度伺服系统具有极高的控制精度和定位精度,可以通过对反馈信号的实时控制,对加工精度实现高精度控制,提高了数控机床加工精度和质量。
4、提高加工效率伺服系统对加工速度和进给速度的实时控制,可以根据不同的加工需要,实现大幅度的加工效率提升。
同时,由于控制精度高,反应迅速,不仅保证了加工效率,而且大大减少了加工过程中的废品率。
三、未来发展方向随着工业技术不断发展和更新,伺服技术也不断更新和完善。
在未来的发展过程中,伺服技术将继续发挥重要的作用,同时也将出现以下发展趋势:1、更加高效随着数控机床的普及和发展,越来越多的制造企业开始注重加工效率和生产效率的提升。
伺服技术的发展趋势将会更加高效,有望实现更高的加工效率和生产效率。
2、更加智能随着人工智能技术的普及和应用,伺服系统有望实现更加智能化的控制,可以自动根据不同的加工需求,自适应调整运动速度和加工精度,提升生产效率和加工质量。
试分析数控机床维修改造中的问题与对策
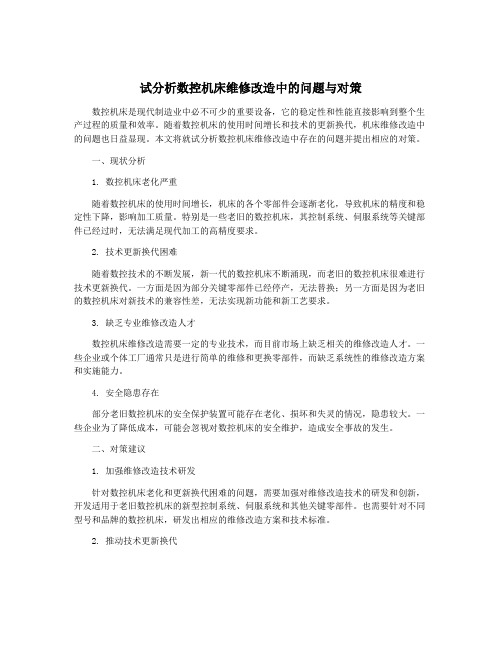
试分析数控机床维修改造中的问题与对策数控机床是现代制造业中必不可少的重要设备,它的稳定性和性能直接影响到整个生产过程的质量和效率。
随着数控机床的使用时间增长和技术的更新换代,机床维修改造中的问题也日益显现。
本文将就试分析数控机床维修改造中存在的问题并提出相应的对策。
一、现状分析1. 数控机床老化严重随着数控机床的使用时间增长,机床的各个零部件会逐渐老化,导致机床的精度和稳定性下降,影响加工质量。
特别是一些老旧的数控机床,其控制系统、伺服系统等关键部件已经过时,无法满足现代加工的高精度要求。
2. 技术更新换代困难随着数控技术的不断发展,新一代的数控机床不断涌现,而老旧的数控机床很难进行技术更新换代。
一方面是因为部分关键零部件已经停产,无法替换;另一方面是因为老旧的数控机床对新技术的兼容性差,无法实现新功能和新工艺要求。
3. 缺乏专业维修改造人才数控机床维修改造需要一定的专业技术,而目前市场上缺乏相关的维修改造人才。
一些企业或个体工厂通常只是进行简单的维修和更换零部件,而缺乏系统性的维修改造方案和实施能力。
4. 安全隐患存在部分老旧数控机床的安全保护装置可能存在老化、损坏和失灵的情况,隐患较大。
一些企业为了降低成本,可能会忽视对数控机床的安全维护,造成安全事故的发生。
二、对策建议1. 加强维修改造技术研发针对数控机床老化和更新换代困难的问题,需要加强对维修改造技术的研发和创新,开发适用于老旧数控机床的新型控制系统、伺服系统和其他关键零部件。
也需要针对不同型号和品牌的数控机床,研发出相应的维修改造方案和技术标准。
2. 推动技术更新换代在政府的支持下,鼓励数控机床制造商和相关企业加大技术更新换代的力度,通过技术创新和工艺改进,提升数控机床的性能和功能,延长机床的使用寿命,降低维修改造的频率和成本。
3. 加强人才培养通过加强对数控机床维修改造技术人才的培养和引进,提高维修改造人员的专业技能和水平,增强企业自身的维修改造能力,提高维修改造的效率和质量。
数控机床伺服驱动装置现状分析

第24期总第178期内蒙古科技与经济No.24.the 178th issue 2008年12月Inner Mongolia Science Technology &Economy Dec.2008数控机床伺服驱动装置现状分析Ξ刘东疆(呼和浩特职业学院,内蒙古呼和浩特 010051) 摘 要:文章认为,伺服驱动装置是CNC 装置和机床的连接环节,是控制机床动态特性和运动精度的重要组成部分。
文章分析了数控机床伺服系统的结构和类型,并对其技术现状及发展趋势作了简要探讨。
关键词:数控机床;伺服驱动装置;进给伺服系统;主轴伺服系统 中图分类号:TN82013 文献标识码:A 文章编号:1007—6921(2008)24—0126—02 伺服驱动装置是CNC 装置和机床的连接环节,CNC 装置发出的位移、速度指令信息,通过伺服驱动装置的变换和放大,由电动机和机械传动机构驱动机床坐标轴、主轴等,带动工作台及刀架,通过轴的联动使刀具相对工件产生各种复杂的机械运动,完成程序所规定的操作,加工出各种复杂形状的工件。
作为数控机床的控制驱动机构,伺服系统随着数字脉宽调制技术、特种电机技术、材料技术、微电子技术、自诊断技术及现代控制技术的进步,历经了从步进到直流,进而到交流的发展过程。
数控机床中的伺服系统种类繁多,本文通过分析其结构和类型,对其技术现状及发展趋势作简要探讨。
1 伺服系统的组成和分类如图为典型的三环反馈伺服系统框图,主要由伺服电机(M )、驱动信号控制转换电路、电力电子驱动放大模块、电流调解单元、速度调解单元、位置调解单元和相应的位置检测装置(如光电编码器G )等组成。
各调解单元以数控系统的给定值和反馈装置检测的实际运行值的差值作为控制信号,进而驱动伺服电动机,以消除差值。
典型的三环反馈伺服系统框图附图中的主要功能模块变化多样,其中任何部分的变化都可构成不同种类的伺服系统。
如根据驱动电动机的类型,可将其分为直流伺服、交流伺服和步进电动机驱动系统;根据有无检测元件和反馈环节可分为开环、闭环和半闭环伺服系统。
浅析伺服系统在数控机床中的应用及发展
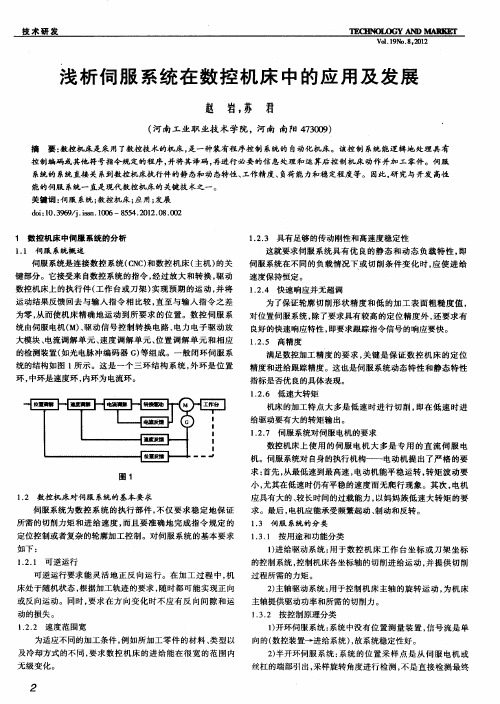
智能化
伺 服 器 控 制 模 式 的 智 能 化 , 在 内 部 预 先 编 程 如
实 现 某 种 运 动 轨 迹 , 制 本 站 点 周 边 的 1 口, 带 主 从 跟 随 控 0 内 模式调整 , 电子 凸轮 等 。
问题 , 如电刷和换 向器 易磨 损 , 护工作 量 大 , 维 成本 高等 。② 交流伺服 系统。其进 给运动系统采用 交流感应 异步伺 服 电机 和永磁 同步伺 服电机 。交流伺服系 统的优点 除 了具 有稳定性 好 、 速性 好 、 度高 的特点 外 , 快 精 与直 流伺 服 电机系 统相 比有
如下 :
13 1 按用途和功能分类 ..
1进 给驱动系 统 : ) 用于数 控机 床工 作 台坐标 或 刀架坐 标 的控制系统 , 控制机床各坐标轴 的切削进给运 动 , 并提供 切削
过 程 所 需 的力 矩 。
12 1 可 逆 运 行 ..
可逆运行要求 能灵 活地 正反 向运行 。在加工 过程 中, 机
控制编码或其他符 号指令规 定的程序 , 并将其译码 , 再进行 必要 的信 息处理和运算后控 制机床 动作 并加 工零件。伺服 系统 的 系统直接 关 系到数控机床执行件 的静 态和动 态特性 、 工作精度、 负荷 能力和稳 定程度等 。因此, 究与开发 高性 研
能 的伺 服 系统 一 直 是现 代 数 控 机 床 的 关键 技 术之 一 。 关键 词 : 服 系统 ; 控 机 床 ; 用 ; 展 伺 数 应 发 di1 .99jin 10 —85 . 1 .8 02 o:0 36/. s.0 6 542 20 .0 s 0
132 按控制原理分类 .. 1开环伺 服系统 : ) 系统 中没有 位置测 量装置 , 号流是 单 信 向的( 数控装置一 进给系统) 故系统稳定性好。 , 2 半开环伺服 系统 : ) 系统 的位 置采样 点是 从伺 服 电机 或 丝杠 的端部 引出 , 采样旋转角度进行检 测 , 不是直接 检测最 终
现在伺服系统实验报告

数字交流伺服系统实验报告姓名:学号:指导老师:学院:数字交流伺服系统实验报告一、实验目的通过实验深入理解伺服系统的系统结构及工作原理,掌握伺服系统的位置控制器设计与系统调试方法。
二、实验内容及结果1. 对系统进行理论分析伺服系统又称随动系统,是用于精确地跟随或复现某个过程的反馈控制系统。
随着工业应用要求的进一步提高,使得位置伺服系统不仅要有很高的定位精度,无超调的定位过程,而且还要保证有尽可能快的动态响应。
目前,应用于数控机床的伺服定位系统中,位置指令通常由上位控制器经固定的算法提供给伺服系统。
由于伺服系统在对指令的响应过程中存在加速和减速的过程,为了避免加速过程中的失步,以及减速过程中的位置超调现象,通常采用一定的速度控制算法。
在实际应用中位置环通常设计成比例控制环节,通过调节比例增益,可以保证系统对位置响应的无超调,但这样会降低系统的动态响应速度。
另外,为了使伺服系统获得高的定位精度,通常要求上位控制器对给定位置和实际位置进行误差的累计,并且要求以一定的控制算法进行补偿,因此,单纯对位置环采用比例调节不仅不能获得理想的响应速度,而且会增加上位控制器的算法复杂度。
另外一种方法是把位置环设计成比例积分环节,通过对位置误差的积分来保证系统的定位精度,这使上位控制器免除了对位置误差的累计,降低了控制复杂度。
但这和采用比例调节的位置控制器一样,在位置响应无超调的同时,降低了系统的动态响应性能。
为了满足高性能伺服定位系统的要求,通常可以采用前馈控制对系统干扰进行抑止,增强控制系统的鲁棒性。
伺服电机控制系统采用了PID和前馈的混合控制,对干扰噪声起到了较好的抑制作用;另外,在输出要求直接跟踪输入信号的应用场合中,系统的闭环调节通常造成跟踪的延迟,这时也可以采用前馈控制来加快系统的跟踪速度。
对于位置信号前馈,可以分为速度前馈和加速度前馈两种,采用速度前馈可以通过开环控制特性来加快伺服系统的速度响应,并且当加大速度前馈增益时,可以减少位置环对位置误差的累积,从而加快位置误差的补偿速度。
数控机床伺服系统性能分析
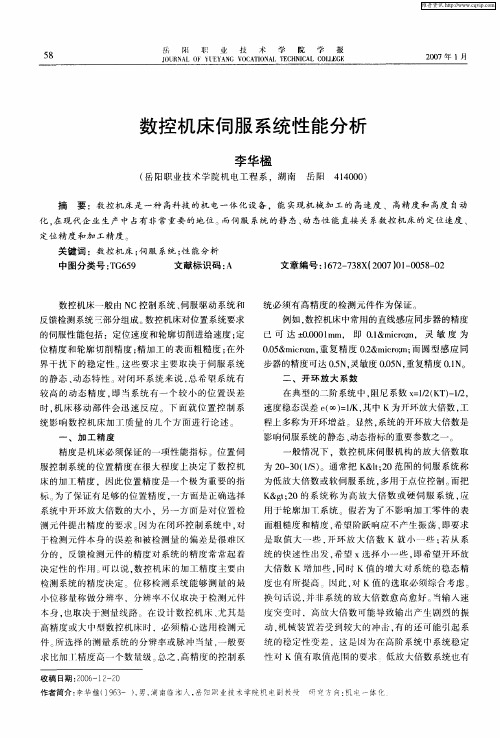
较高 的动态 精度 , 当系统有 一个 较小 的位 置误 差 即
时 . 床移 动部件 会迅 速反应 。下 面就 位置 控制 系 机
在典型的二阶系统 中 , 阻尼 系数 x I ( T 一/, =/ K )1 2 2 速度稳态误差 e 。) I 其中 K为开环放大倍数 , (。=/ K, 工 程上多称为开环增益 。 显然 , 系统 的开环放大倍数是
本身 , 也取决于测量线路 。在设计 数控机床 、 尤其是
高精 度或大 巾型数控 机床时 ,必须 精心选 用检洲元 件 选择的测量 系统 的分辨率或脉 冲当量 , 所 一般要
统 的稳定性变 差 ,这是 为在高阶 系统 I 系统稳 定 1 1 性 对 K值有取值 范围的要求 低放 大倍数 系统也有
般情况下 .数控机床伺服 机构的放大倍 数取
为 2 ~0 1 ) 0 3 (/ 。通 常把 K t2 S &l 0范 围的伺服 系统称 : 为低放大倍 数或软伺服 系统 , 多用 于点位 控制。 而把 K t2 &g:0的 系统称 为 高放 大倍数 或 硬伺 服 系统 , 应 用于轮廓 加 I系统 。假若为 了不 影响加工零件 的表 I 面粗糙度 和精度 , 单阶跃响应不 产生振荡 , 希 即要求 是 取值 大一 些 , 歼环 放 大倍 数 K就 小一 些 : 从系 若 统 的快 速性 出发 , 希望 X选择小 一些 , 即希 望开环放 大倍 数 K增加些 , 同时 K值 的增大对 系统 的稳 态精
维普资讯
5 8Leabharlann 岳 阳 职 业 技 术 学 院 学 报 J U N L O IE A G V C TO A T C NC L C L G O R A F Y iY N O A IN l E H IA OLE E
数控机床的伺服系统

4.2 步进电动机驱动控制系统
4.2.3 步进电动机的驱动控制
1.步进电动机的工作方式 从一相通电换接到另一相通电称为一拍,每拍转子转过一个
步距角。按A→B → C → A → …的顺序通电时,电动机的转 子便会按此顺序一步一步地旋转;反之,若按A → C → B → A→…的顺序通电,则电动机就会反向转动,这种三相依次 单相通电的方式,称为三相单三拍式运行,“单”是指每次 只有一相绕组通电,“三拍”是指一个循环内换接了三次, 即A、B、C三拍。单三拍通电方式每次只有一相控制绕组通 电吸引转子,容易使转子在平衡位置附近产生振荡,运行稳 定性较差;另外,在切换时一相控制绕组断电而另一相控制绕 组开始
4.2.2 步进电动机的工作原理与主要特 性
1.步进电动机的工作原理
上一页 下一页 返回
4.2 步进电动机驱动控制系统
步进电动机的工作原理实际上是电磁铁的作用原理。下面以 图4-2所示的一个最简单步进电动机结构为例说明步进电动机 的工作原理。其定子上分布有6个齿极,每两个相对齿极装有 一相励磁绕组,构成三相绕组。
也称为数组的长度。
下一页 返回
6.1 一维数组
对数组的定义应注意以下几点。 (1)数组的类型实际上是指数组元素的取值类型。对于同一
个数组,其所有元素的数据类型都是相同的。 (2)数组名的书写规则应符合标识符的书写规定。 (3)数组名不能与其他变量名相同。 (4)不能在方括号中用变量来表示元素的个数,但是可以用
按伺服控制方式不同,数控机床伺服系统可分为开环、闭环 和半闭环系统。开环型采用步进电动机驱动,控制方式简单, 信号单向传递,无位置反馈,所以精度不高,适用于要求不 高的经济型数控机床中。而闭环控制系统采用直流、交流伺 服电动机驱动,位置检测元件安装于机床运动部件上,
伺服系统的现状及发展趋势分析

伺服系统的现状及发展趋势分析作者:陈甫良来源:《科技资讯》 2014年第33期陈甫良(长沙赛普尔自动化工程设备有限公司湖南长沙 410100)摘要:伴随着技术的进步和工业化的不断发展,加上在高精度化、高速化、小型化、高可靠性、免维护性能以及多品种小批量化等方面不断提高要求的工业自动化设备,促使伺服驱动技术被广泛应用于工业领域。
因在机电设备中发挥着重要作用,方便、快速、灵活及准确的驱动可由高性能的伺服系统提供。
21世纪的今天,交流伺服系统越来越成熟,伺服驱动技术也取得了极大的进步,伺服控制技术已成为工业自动化的支撑性技术之一。
关键词:伺服系统工业自动化发展中图分类号:TP27 文献标识码:A 文章编号:1672-3791(2014)11(c)-0061-02通常我们提到的伺服,与伺服系统、伺服装置、伺服机构、伺服控制系统具有相同的意思,只是提法不同而已。
在很多情况下,伺服系统专指被控制量(系统的输出量)是机械位移或位移速度、加速度的反馈控制系统,其作用是使输出的机械位移(或转角)准确地跟踪输入的位移(或转角)。
伺服系统的结构组成以及其他形式的反馈控制系统没有根本上的区别。
伺服控制系统按驱动元件类型可分为机电伺服系统、液压伺服系统以及气动伺服系统。
1 伺服系统的结构组成机电一体化的伺服控制系统的结构类型繁多,就从自动控制理论的角度来进行分析,伺服控制系统一般包括控制器、被控对象、检测环节、比较环节、执行环节等五部分。
1.1 控制器控制器通常是PID控制电路或计算机, 控制器主要任务是对比较元件输出的偏差信号进行变换处理,用来控制执行元件按要求动作。
1.2 被控对象被控对象多指一些机械参数量,例如:位移、加速度、力、速度和力矩等。
1.3 执行环节执行环节的作用是按控制信号的规则,将输入的各形式能量转化成机械能,驱动被控对象工作。
1.4 检测环节检测环节是指能够对输出进行测量并转换成比较环节所需要量纲的装置,一般包括传感器(编码器)和转换电路。
数控机床中伺服系统现状分析(doc 5)

三、进给伺服系统的现状与展望进给伺服以数控机床的各坐标为控制对象,产生机床的切削进给运动。
为此,要求进给伺服能快速调节坐标轴的运动速度,并能精确地进行位置控制。
具体要求其调速范围宽、位移精度高、稳定性好、动态响应快。
根据系统使用的电动机,进给伺服可细分为步进伺服、直流伺服、交流伺服和直线伺服。
(一)步进伺服系统步进伺服是一种用脉冲信号进行控制,并将脉冲信号转换成相应的角位移的控制系统。
其角位移与脉冲数成正比,转速与脉冲频率成正比,通过改变脉冲频率可调节电动机的转速。
如果停机后某些绕组仍保持通电状态,则系统还具有自锁能力。
步进电动机每转一周都有固定的步数,如500步、1000步、50 000步等等,从理论上讲其步距误差不会累计。
步进伺服结构简单,符合系统数字化发展需要,但精度差、能耗高、速度低,且其功率越大移动速度越低。
特别是步进伺服易于失步,使其主要用于速度与精度要求不高的经济型数控机床及旧设备改造。
但近年发展起来的恒斩波驱动、PWM驱动、微步驱动、超微步驱动和混合伺服技术,使得步进电动机的高、低频特性得到了很大的提高,特别是随着智能超微步驱动技术的发展,将把步进伺服的性能提高到一个新的水平。
(二)直流伺服系统直流伺服的工作原理是建立在电磁力定律基础上。
与电磁转矩相关的是互相独立的两个变量主磁通与电枢电流,它们分别控制励磁电流与电枢电流,可方便地进行转矩与转速控制。
另一方面从控制角度看,直流伺服的控制是一个单输入单输出的单变量控制系统,经典控制理论完全适用于这种系统,因此,直流伺服系统控制简单,调速性能优异,在数控机床的进给驱动中曾占据着主导地位。
然而,从实际运行考虑,直流伺服电动机引入了机械换向装置。
其成本高,故障多,维护困难,经常因碳刷产生的火花而影响生产,并对其它设备产生电磁干扰。
同时机械换向器的换向能力,限制了电动机的容量和速度。
电动机的电枢在转子上,使得电动机效率低,散热差。
为了改善换向能力,减小电枢的漏感,转子变得短粗,影响了系统的动态性能。
伺服电动机在数控系统中的应用分析
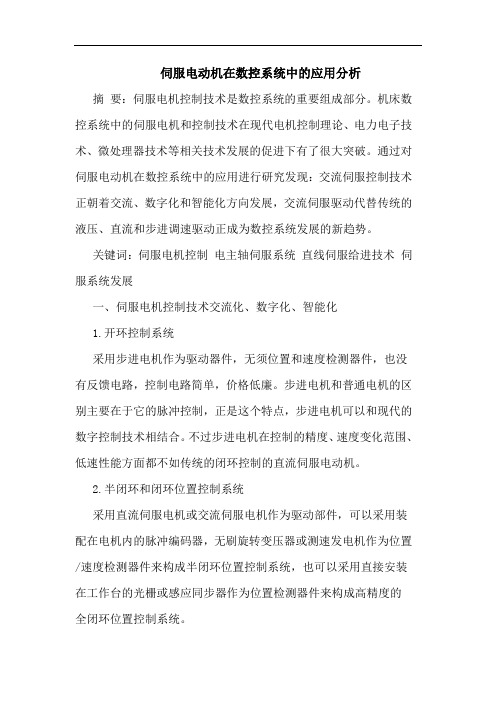
伺服电动机在数控系统中的应用分析摘要:伺服电机控制技术是数控系统的重要组成部分。
机床数控系统中的伺服电机和控制技术在现代电机控制理论、电力电子技术、微处理器技术等相关技术发展的促进下有了很大突破。
通过对伺服电动机在数控系统中的应用进行研究发现:交流伺服控制技术正朝着交流、数字化和智能化方向发展,交流伺服驱动代替传统的液压、直流和步进调速驱动正成为数控系统发展的新趋势。
关键词:伺服电机控制电主轴伺服系统直线伺服给进技术伺服系统发展一、伺服电机控制技术交流化、数字化、智能化1.开环控制系统采用步进电机作为驱动器件,无须位置和速度检测器件,也没有反馈电路,控制电路简单,价格低廉。
步进电机和普通电机的区别主要在于它的脉冲控制,正是这个特点,步进电机可以和现代的数字控制技术相结合。
不过步进电机在控制的精度、速度变化范围、低速性能方面都不如传统的闭环控制的直流伺服电动机。
2.半闭环和闭环位置控制系统采用直流伺服电机或交流伺服电机作为驱动部件,可以采用装配在电机内的脉冲编码器,无刷旋转变压器或测速发电机作为位置/速度检测器件来构成半闭环位置控制系统,也可以采用直接安装在工作台的光栅或感应同步器作为位置检测器件来构成高精度的全闭环位置控制系统。
开环系统逐渐由闭环系统取代。
以直流伺服电机作为驱动器件的直流伺服系统,控制电路比较简单,价格较低。
其主要缺点是直流伺服电机内部有机械换向装置,碳刷易磨损,维修工作量大,运行时易起火花,给电机的转速和功率的提高带来较大的困难。
从70年代末,数控机床逐渐采用异步电机为主轴驱动电机。
目前交流伺服系统已在很大范围内取代了直流伺服系统。
在当代数控系统中,伺服技术取得的突破可以归结为:交流伺服取代直流伺服、数字控制取代模拟控制、或者把它称为软件控制取代硬件控制。
这两种突破的结果产生了交流数字驱动系统,应用在数控机床的伺服进给和主轴装置上。
由于电力电子技术及控制理论、微处理器等微电子技术的快速发展,软件运算及处理能力的提高,采用高速微处理器和专用数字信号处理的计算速度大大提高,采样的时间大大减少。
机械机床毕业设计174数控机床伺服系统故障诊断与分析论文
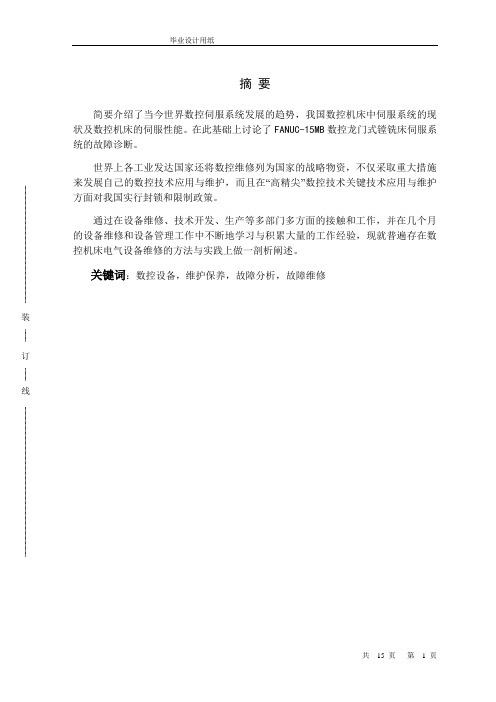
摘要简要介绍了当今世界数控伺服系统发展的趋势,我国数控机床中伺服系统的现状及数控机床的伺服性能。
在此基础上讨论了FANUC-15MB数控龙门式镗铣床伺服系统的故障诊断。
世界上各工业发达国家还将数控维修列为国家的战略物资,不仅采取重大措施来发展自己的数控技术应用与维护,而且在“高精尖”数控技术关键技术应用与维护方面对我国实行封锁和限制政策。
通过在设备维修、技术开发、生产等多部门多方面的接触和工作,并在几个月的设备维修和设备管理工作中不断地学习与积累大量的工作经验,现就普遍存在数控机床电气设备维修的方法与实践上做一剖析阐述。
关键词:数控设备,维护保养,故障分析,故障维修目录第一章数控伺服系统 (3)1.1伺服系统的发展 (3)1.2数控系统的构成与特点 (3)第二章数控机床中伺服系统的现状 (5)2.1概述 (5)2.2伺服系统的结构及分类 (5)2.3进给伺服系统的现状与展望 (6)第三章数控机床的伺服系统性能 (8)3.1加工精度 (8)3.2开环放大倍数 (8)3.3宽范围调速 (9)第四章FANUC-15MB数控伺服系统的故障诊断 (10)4.1F A N U C-15M B数控进给轴的伺服控制原理及故障 (10)4.2F A N U C-15M B数控同步轴组的控制原理及故障 (12)4.3F A N U C-15M B数控的自诊断 (13)第五章结论与建议 (14)参考文献 (15)附录:伺服系统结构图第一章数控伺服系统1.1伺服系统的发展(1)直流伺服系统伺服系统的发展经历了由液压到电气的过程。
电气伺服系统根据所驱动的电机类型分为直流(DC)伺服系统和交流(AC)伺服系统。
50年代,无刷电机和直流电机实现了产品化,并在计算机外围设备和机械设备上获得了广泛的应用。
70年代则是直流伺服电机的应用最为广泛的时代。
(2)交流伺服系统从70年代后期到80年代初期,随着微处理器技术、大功率高性能半导体功率器件技术和电机永磁材料制造工艺的发展及其性能价格比的日益提高,交流伺服技术—交流伺服电机和交流伺服控制系统逐渐成为主导产品。
伺服系统发展现状

伺服系统发展现状
目前,伺服系统在各个领域的发展非常迅速。
伺服系统是一种控制系统,可以精确控制电机等执行器的位置、速度和力矩。
它广泛应用于机械、机床、自动化生产线、机器人、航空航天等各个领域。
在机械工程方面,伺服系统的发展为机器性能提供了有效改进的方式。
通过使用伺服系统,机械运动可以更加精确、平稳,并且可以快速响应外部指令。
这使得机器的生产效率大大提高,同时还能够提高产品的质量和可靠性。
在机床制造方面,伺服系统的应用非常广泛。
伺服系统可以实现高速高精度的机床运动,使得加工效率大大提高。
同时,伺服系统还可以实现复杂的切削轮廓和加工路径,从而实现更加精细的加工。
在自动化生产线方面,伺服系统是实现自动化控制的重要组成部分。
伺服系统可以精确控制各种运动元件的运动轨迹和速度,实现复杂的生产过程控制。
这对提高生产线的效率和生产质量非常重要。
在机器人领域,伺服系统是机器人运动控制的核心技术。
伺服系统可以实现机器人精确的位置和姿态控制,从而使机器人可以完成各种复杂的任务。
伺服系统的应用使得机器人在工业自动化、医疗、服务等领域得到了广泛应用。
在航空航天领域,伺服系统的精确控制能力非常重要。
伺服系
统可以控制飞机、火箭等航空器的各种运动,实现高度稳定和精确控制。
伺服系统的发展对提高航空航天器的性能和可靠性具有重要意义。
总的来说,伺服系统在各个领域的发展非常迅速,为相关行业带来了巨大的改进和进步。
随着科技的不断发展,伺服系统将继续发挥重要的作用,推动相关产业的发展。
- 1、下载文档前请自行甄别文档内容的完整性,平台不提供额外的编辑、内容补充、找答案等附加服务。
- 2、"仅部分预览"的文档,不可在线预览部分如存在完整性等问题,可反馈申请退款(可完整预览的文档不适用该条件!)。
- 3、如文档侵犯您的权益,请联系客服反馈,我们会尽快为您处理(人工客服工作时间:9:00-18:30)。
数控机床中伺服系统现状分析(doc 5)
数控机床中伺服系统的现状分析
一、概述
伺服系统是以机械运动的驱动设备,电动机为控制对象,以控制器为核心,以电力电子功率变换装置为执行机构,在自动控制理论的指导下组成的电气传动自动控制系统。
这类系统控制电动机的转矩、转速和转角,将电能转换为机械能,实现运动机械的运动要求。
具体在数控机床中,伺服系统接收数控系统发出的位移、速度指令,经变换、放调与整大后,由电动机和机械传动机构驱动机床坐标轴、主轴等,带动工作台及刀架,通过轴的联动使刀具相对工件产生各种复杂的机械运动,从而加工出用户所要求的复杂形状的工件。
作为数控机床的执行机构,伺服系统将电力电子器件、控制、驱动及保护等集为一体,并随着数字脉宽调制技术、特种电机材料技术、微电子技术及现代控制技术的进步,经历了从步进到直流,进而到交流的发展历程。
数控机床中的伺服系统种类繁多,本文通过分析其结构及简单归分,对其技术现状及发展趋势作简要探讨。
二、伺服系统的结构及分类
从基本结构来看,伺服系统主要由三部分组成:控制器、功率驱动装置、反馈装置和电动机(图1)。
控制器按照数控系统的给定值和通过反馈装置检测的实际运行值的差,调节控制量;功率驱动装置作为系统的主回路,一方面按控制量的大小将电网中的电能作用到电动机之上,调节电动机转矩的大小,另一方面按电动机的要求把恒压恒频的电网供电转换为电动机所需的交流电或直流电;电动机则按供电大小拖动机械运转。
图1 伺服系统的结构
图1 伺服系统的结构
图1中的主要成分变化多样,其中任何部分的变化都可构成不同种类的伺服系统。
如根据驱动电动机的类型,可将其分为直流伺服和交流伺服;根据控制器实现方法的不同,可将其分为模拟伺服和数字伺服;根据控制器中闭环的多少,可将其分为开环控制系统、单环控制系统、双环控制系统和多环控制系统。
考虑伺服系统在数控机床中的应用,本文首先按机床中传动机械的不同将其分为进给伺服与主轴伺服,然后再根据其它要素来探讨不同伺服系统的技术特性。
与直流伺服系统相媲美。
同时可实现弱磁高速控制,拓宽了系统的调速范围,适应了高性能伺服驱动的要求。
目前,在机床进给伺服中采用的主要是永磁同步交流伺服系统,有三种类型:模拟形式、数字形式和软件形式。
模拟伺服用途单一,只接收模拟信号,位置控制通常由上位机实现。
数字伺服可实现一机多用,如做速度、力矩、位置控制。
可接收模拟指令和脉冲指令,各种参数均以数字方式设定,稳定性好。
具有较丰富的自诊断、报警功能。
软件伺服是基于微处理器的全数字伺服系统。
其将各种控制方式和不同规格、功率的伺服电机的监控程序以软件实现。
使用时可由用户设定代码与相关的数据即自动进入工作状态。
配有数字接口,改变工作方式、更换电动机规格时,只需重设代码即可,故也称万能伺服。
交流伺服已占据了机床进给伺服的主导地位,并随着新技术的发展而不断完善,具体体现在三个方面。
一是系统功率驱动装置中的电力电子器件不断向高频化方向发展,智能化功率模块得到普及与应用;二是基于微处理器嵌入式平台技术的成熟,将促进先进控制算法的应用;三是网络化制造模式的推广及现场总线技术的成熟,将使基于网络的伺服控制成为可能。
(四)直线伺服系统
直线伺服系统采用的是一种直接驱动方式(Direct Drive),与传统的旋转传动方式相比,最大特点是取消了电动机到工作台间的一切机械中间传动环节,即把机床进给传动链的长度缩短为零。
这种“零传动”方式,带来了旋转驱动方式无法达到的性能指标,如加速度可达3g以上,为传统驱动装置的10~20倍,进给速度是传统的4~5倍。
从电动机的工作原理来讲,直线电动机有直流、交流、步进、永磁、电磁、同步和异步等多种方式;而从结构来讲,又有动圈式、动铁式、平板型和圆筒型等形式。
目前应用到数控机床上的主要有高精度高频响小行程直线电动机与大推力长行程高精度直线电动机两类。
直线伺服是高速高精数控机床的理想驱动模式,受到机床厂家的重视,技术发展迅速。
在2001年欧洲机床展上,有几十家公司展出直线电动机驱动的高速机床,快移速度达100~120m/min,加速度1.5~2g,其中尤以德国DMG公司与日本MAZAK公司最具代表性。
2000年DMG公司已有28种机型采用直线电动机驱动,年产1500多台,约占总产量的1/3。
而MAZAK公司最近也将推出基于直线伺服系统的超音速加工中心,切削速度8马赫,主轴最高转速80000r/min,快移速度500m/min,加速度6g。
所有这些,都标志着以直线电动机驱动为代表的第二代高速机床,将取代以高速滚珠丝杠驱动为代表的第一代高速机床,并在使用中逐步占据主导地位。
四、主轴伺服系统的现状及展望
主轴伺服提供加工各类工件所需的切削功率,因此,只需完成主轴调速及正反转功能。
但当要求机床有螺纹加工、准停和恒线速加工等功能时,对主轴也提出了相应的位置控制要求,因此,要求其输出功率大,具有恒转矩段及恒功率段,有准停控制,主轴与进给联动。
与进给伺服一样,主轴伺服经历了从普通三相异步电动机传动到直流主轴传动。
随着微处理器技术和大功率晶体管技术的进展,现在又进入了交流主轴伺服系统的时代。
(一)交流异步伺服系统
交流异步伺服通过在三相异步电动机的定子绕组中产生幅值、频率可变的正弦电流,该正弦电流产生的旋转磁场与电动机转子所产生的感应电流相互作用,产生电磁转矩,从而实现电动机的旋转。
其中,正弦电流的幅值可分解为给定或可调的励磁电流与等效转子力矩电流的矢量和;正弦电流的频率可分解为转子转速与转差之和,以实现矢量化控制。
交流异步伺服通常有模拟式、数字式两种方式。
与模拟式相比,数字式伺服加速特性近似直线,时间短,且可提高主轴定位控制时系统的刚性和精度,操作方便,是机床主轴驱动采用的主要形式。
然而交流异步伺服存在两个主要问题:一是转子发热,效率较低,转矩密度较小,体积较大;二是功率因数较低,因此,要获得较宽的恒功率调速范围,要求较大的逆变器容量。
(二)交流同步伺服系统
近年来,随着高能低价永磁体的开发和性能的不断提高,使得采用永磁同步调速电动机的交流同步伺服系统的性能日益突出,为解决交流异步伺服存在的问题带来了希望。
与采用矢量控制的异步伺服相比,永磁同步电动机转子温度低,轴向连接位置精度高,要求的冷却条件不高,对机床环境的温度影响小,容易达到极小的低限速度。
即使在低限速度下,也可作恒转矩运行,特别适合强力切削加工。
同时其转矩密度高,转动惯量小,动态响应特性好,特别适合高生产率运行。
较容易达到很高的调速比,允许同一机床主轴具有多种加工能力,既可以加工像铝一样的低硬度材料,也可以加工很硬很脆的合金,为机床进行最优切削创造了条件。
(三)电主轴
电主轴是电动机与主轴融合在一起的产物,它将主轴电动机的定子、转子直接装入主轴组件的内部,电动机的转子即为主轴的旋转部分,由于取消了齿轮变速箱的传动与电动机的连接,实现了主轴系统的一体化、“零传动”。
因此,其具有结构紧凑、重量轻、惯性小、动态特性好等优点,并可改善机床的动平衡,避免振动和噪声,在超高速切削机床上得到了广泛的应用。
从理论上讲,电主轴为一台高速电动机,其既可使用异步交流感应电动机,也可使
用永磁同步电动机。
电主轴的驱动一般使用矢量控制的变频技术,通常内置一脉冲编码器,来实现厢位控制及与进给的准确配合。
由于电主轴的工作转速极高,对其散热、动平衡、润滑等提出了特殊的要求。
在应用中必须妥善解决,才能确保电主轴高速运转和精密加工。
五、结论
作为数控机床的重要功能部件,伺服系统的特性一直是影响系统加工性能的重要指标。
围绕伺服系统动态特性与静态特性的提高,近年来发展了多种伺服驱动技术。
可以预见随着超高速切削、超精密加工、网络制造等先进制造技术的发展,具有网络接口的全数字伺服系统、直线电动机及高速电主轴等将成为数控机床行业的关注的热点,并成为伺服系统的发展方向。