钣金折弯工艺
钣金折弯方法,图文讲解四种折弯工艺!

折弯是一种对平面板件进行折叠、弯曲的工艺,它在整个加工链中紧随切割工序之后。
工件放在带有V型开口的凹模上。
楔形刀具(上刀)将工件压入V型开口中,并以这种方式将板材折弯到需要的角度。
大多数折弯件采用悬空折弯、模中折弯以及折边与压合等工艺与方法制成。
作业方式均遵循同一原理:冲芯将工件压入凹模的下模中。
因此,执行上述工艺与方法的折弯机被称为模压折弯机。
1、悬空折弯冲芯将工件压入凹模,却不将其压向模具壁。
冲芯下移期间,工件边向上弯折并形成夹角。
冲芯将工件压入凹模的深度越大,角度就越小。
此时,冲芯和凹模之间留有空隙。
悬空折弯也被称为路径依赖型工艺。
每种夹角都需要特定路径。
机床控制系统同时计算路径与相应的冲压力。
路径与冲压力取决于模具、材料与产品特性(夹角、长度)。
2、模中折弯冲芯将工件完全压入凹模,因此凹模、工件与冲芯之间不留空隙。
这种工序被称为合模。
冲芯与凹模必须精确相互贴合。
因此,每种夹角与形状都需要相应的模具组件。
工件一旦完全压入,冲芯则无法继续向下移动。
机床控制系统继续提升冲压力,直至达到规定值。
施加至工件的压力由此上升,从而呈现出冲芯与凹模的轮廓。
夹角在高压作用下逐渐稳固,几乎彻底消除回弹问题。
3、翻板折弯机床内置的折弯摆臂由C形型材构成,其上安装有下部与上部折弯模具。
折弯时C形型材向上或向下移动,或是进行小范围椭圆形运动,即翻转。
摆臂折弯机半自动化运行,以快速性与灵活性着称,即使是小批量生产也完成得毫不逊色。
此外,通过翻板折弯技术还可使用同一模具在单个部件上实现多种半径尺寸的高效折弯。
4、折边与压合板材边缘通常被完全弯折(例如盒边缘),随后折边相互平行。
成品件整体因此更加稳定或是形成边缘防护。
随后折边内通常需要挂入其他零件。
折边与压合分为两个步骤完成:首先操作员预先折好30°夹角,然后将工件重新放入并压合夹角。
如果边缘之间存在空隙,则称为折边。
压合中弯边则完全相互挤压。
折边是路径依赖型,压合却是力度依赖型。
钣金折弯工艺参数的优化方法

钣金折弯工艺参数的优化方法引言钣金折弯是一种常见的金属加工工艺,广泛应用于汽车制造、航空航天、家电等领域。
在钣金折弯过程中,合理设置工艺参数能够提高产品的质量和生产效率。
本文将介绍一些钣金折弯工艺参数的优化方法,帮助读者掌握如何提升钣金折弯工艺的效果。
工艺参数的影响因素钣金折弯工艺参数的设置对于成品精度、外观质量、加工效率等方面都有着重要的影响。
常用的钣金折弯工艺参数包括弯曲角度、压力、模具材料等。
下面将详细介绍这些参数的优化方法。
弯曲角度弯曲角度是指钣金在折弯过程中产生的角度。
弯曲角度的大小会直接影响产品的形状和精度。
在优化弯曲角度时,可以通过以下方法进行调整: - 调整模具凸模和模具座之间的间距,改变间距大小可以控制弯曲角度。
- 调整折弯机上的弯曲速度,较快的速度可以产生更小的弯曲角度,较慢的速度则会产生更大的弯曲角度。
- 选择合适的模具形状,不同的模具形状会对弯曲角度产生不同的影响。
压力压力是在钣金折弯过程中施加在材料上的力。
合理的压力设置可以保证产品的外观质量和尺寸精度。
下面是一些调整压力的方法: - 调整折弯机上的压力控制装置,增大压力可以减小弯曲后的回弹变形。
- 选择合适的模具材料,不同材料的模具表面硬度不同,硬度较高的模具可以施加更大的压力。
模具材料模具材料直接影响着折弯产品的表面质量和尺寸精度。
常用的模具材料有钢、铝、塑料等。
选择合适的模具材料可以提高工艺效果。
以下是一些建议: - 选择耐磨性好的模具材料,减少模具使用过程中的磨损。
- 钣金材料与模具材料的适配性should ensure that the two materials have good compatibility to avoid surface damage during the bending process.工艺参数优化的方法钣金折弯工艺参数的优化是一个复杂而细致的过程,需要根据具体的产品要求和加工设备的特点来进行调整。
钣金双边折弯90°的加工方法
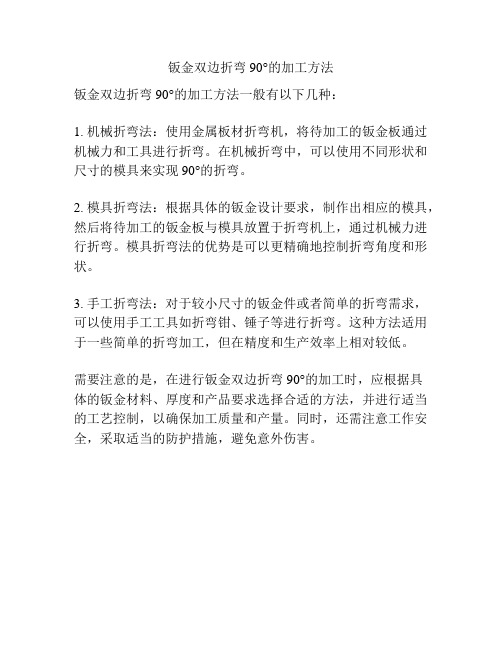
钣金双边折弯90°的加工方法
钣金双边折弯90°的加工方法一般有以下几种:
1. 机械折弯法:使用金属板材折弯机,将待加工的钣金板通过机械力和工具进行折弯。
在机械折弯中,可以使用不同形状和尺寸的模具来实现90°的折弯。
2. 模具折弯法:根据具体的钣金设计要求,制作出相应的模具,然后将待加工的钣金板与模具放置于折弯机上,通过机械力进行折弯。
模具折弯法的优势是可以更精确地控制折弯角度和形状。
3. 手工折弯法:对于较小尺寸的钣金件或者简单的折弯需求,可以使用手工工具如折弯钳、锤子等进行折弯。
这种方法适用于一些简单的折弯加工,但在精度和生产效率上相对较低。
需要注意的是,在进行钣金双边折弯90°的加工时,应根据具
体的钣金材料、厚度和产品要求选择合适的方法,并进行适当的工艺控制,以确保加工质量和产量。
同时,还需注意工作安全,采取适当的防护措施,避免意外伤害。
钣金的折弯工艺汇总(图解)

锁金的折弯工艺汇总(图解)1、什么是镀金折弯?镀金折弯是一种金属加工技术,用于将扁平的镀金件变成V形、U形或槽型。
这是一个重要且方便的制造过程,因为将一块扁平金属板弯曲成新形状比从实心工件加工v、u或通道形状或在铸造厂中铸造要便宜得多。
此外,弯曲产生的零件比例如将两片扁平金属片焊接成V形的零件更坚固。
许多类型的镀金折弯涉及使用称为制动器的机器,有时称为折弯机或镀金折叠机。
可以手动施加力,也可以使用例如液压装置施加力。
2、镀金折弯设备最重要的镀金折弯设备是制动器,它有几种不同的形式: 檐口制动器是一种简单的折弯机——也是制造业中使用最广泛的制动器一一它将一块金属板夹在一个平面上,然后通过可移动的折弯叶片的运动,使用力进行直弯或简单的折痕。
折弯机是一种使用移动冲头和相应模具的折弯机。
在此过程中,金属板被放置在模具上,并且冲头被强制移动到金属中,迫使其进入模具。
根据模具的形状,可以使用折弯机来制作V形弯、U形弯和其他形状。
箱式制动器(也称为手指制动器)是另一种折弯机,它使用一排金属“手指”来实现多个自定义折弯。
顾名思义,箱盘式制动器通常用于制作定制尺寸的盒子。
棒材折叠机是一种小型且简单的折弯机,带有一个手柄,可以夹住金属板并以单一动作弯曲它。
3、镀金折弯的种类有不同种类的镀金折弯用于以不同的方式实现不同的折弯。
其中三种折弯方法(空气折弯、打底和压印)使用折弯机,而其他折弯方法则使用各种机械。
1)空气弯曲空气弯曲是一种折弯折弯方法,在这种方法中,冲头将金属板压入模具,但不会太远以至于它接触到模具的壁。
这种方法不如其他方法准确,但它非常灵活:它可以用来制作V、U和其他形状的弯曲。
这部分是因为模具几何形状不需要完全对应于所需的镀金弯曲,因为两个表面之间没有接触。
2)打底打底是另一种折弯折弯方法。
在打底过程中,冲头将金属板完全压入模具,形成与模具内部几何形状相对应的弯曲。
它用于制作V 形弯曲。
3)冲压冲压是一种更昂贵的折弯折弯类型,其中冲头以更大的力在银金和模具中降低,从而产生永久变形而回弹很小。
钣金折弯工艺间隙经验

钣金折弯工艺间隙经验一、对于折弯缺角计算及折弯包边要求:1、客户图纸有规定哪边包哪边的侧按图纸要求计算展开缺角。
2、如图纸没特别要求侧自行决定包边,但如果清楚装配关系,一般情况下包边面为可见的面,被包边为不可见。
3、图纸没有标明缺角大小的,本厂折弯工艺间隙的计算通常有以下几种:①角位需要满焊焊接的,则两边缩(t+0.1),(折边高度大于100,而且图纸没指定满焊,此工艺则不合适);2)包边而又不需开工艺孔的,其中包边的一端缩短0.35t,(计算取一位小数)被包边则缩(t+0.2t),;3)包边需要开工艺孔的,其中包边一端尺寸不变,被包边侧缩(t+0.2t)。
具体计算方式取决于客户对产品的要求,产品的性能以及材料厚度,材质、折弯高度、以及是否焊接等。
在满足客户要求、满足产品使用性能情况下,角位尽量不要焊接,焊接尽量不要采用满焊方式,(可紧贴内外点焊、修圆角掩盖焊缝,喷涂后消除焊接缝)以达到减少工作量又保证产品质量的目的。
(工艺孔的半径比板厚略小)二、90度'V'形缺角计算:端部至第一个'V'型切口中心尺寸为边长减0.5K,两'V'型切口中心之间距离为边长减K,切口中线各向外偏移0.05至0.2作为工艺间隙(具体根据材料厚度而定,材料厚度越厚间隙越大)三、冲双弯、压死边及折弯系数取值:1)通常直角折边减一个系数;(85度至99度之间可按直角计算)130度至165度角减0.5t;100度至129度角减0.4k至0.7K之间;(角度越小,系数值越大)60度至84度角减1.43t;60度以下需试弯验证后方可批产;(系数值随材质、厚度而变化) 165度到179度可忽咯系数不计算。
2)冲双弯展开计算方法为:零件总长L+0.5t。
3)压死边展开计算方法为:两个边总长度减0.5t,。
钣金折弯工艺

钣金折弯工艺1。
适用范围:本工艺守则适用于生产高、低压开关柜(箱)过程中,低碳钢板的折弯。
允许公差值按标准JB/T6753。
1—5。
1中表1的规定。
适用于产品结构零部件折弯加工工序之用。
2. 工艺过程:3。
准备工作内容:3.1 熟悉图纸和技术要求:备齐板手等手工具和钢卷尺、角度尺、游标卡尺等量具.3.2 检查折弯机的状态,检查内容包括:A。
检查润滑情况是否正常,需要时将各部加足润滑油.B。
检查机械部件是否正常,螺丝有无松动.3.3 检查待折弯的板料尺寸及角度,是否符合图纸要求,图纸无展开尺寸时,应按下表计算核对:4。
检查及调整折弯机:4.1 机器刚开始使用时,对于同步油缸式折弯机,应放掉左右两个同步油缸中的空气,放气步骤如下:A.将放气螺丝松开;B.由按钮控制“充油”“工作”交替进行,并使滑块上下数次,使油缸中的空气放入油箱.C.将放气螺钉旋紧,再由按钮控制充油,充油后折弯机两油缸应保持同步.4.2 调整下刀两端的推拉螺杆,使上下刀口中心线重合。
4.3 调整滑块下限:对于同步油缸式折弯机根据板料厚度和弯曲及开关用按钮通过电动机调整滑块的下限(即滑块下死点)指针旋转一周滑块移动1毫米,注意不得使上刀与下刀槽接触,以免造成顶刀事故,上下刀的间隙不得小于板料厚度.对于机械同步折弯机,先将下止点调整手轮顺时针方向调整到最小值,然后逆时针下调,一边折弯一边转动直到折弯角度合适时停止。
4.4 摇动“直板调节手轮",使制板端面与下刀槽中心等于工件边高减去料厚,调整时使用300毫米深度尺寸在制板两端测量.4.5 正确选用下模V形槽,开口尺寸应符合折弯压力表的规定。
5. 折弯5.1 板料正式折弯前应用一块厚度,长度与工件相同的板料试折,通过试折检查工件尺寸和角度存在的问题,并相应调整滑块下死点、直板等。
折弯机经过调整后应再次试折。
5。
2 为保证获得较好的工件折弯精度,板料必须平整。
5。
3 折弯板料应放在机器中间位置,不许单边载荷使用。
钣金件设计规范

钣金件常用结构的工艺要求
外翻边高度H的规格:
H
R
R
H(MIN-MAX)
T 0.8
2.0 5.0 10.0 2.4-4.0 2.4-6.0 2.4-10.0
1.0 3.0-4.4 3.0-6.8 3.0-10.8
1.2 3.6-4.8 3.6-7.5 3.6-11.5
钣金件常用结构的工艺要求
折弯边到孔的最小距离 L:
四.正反折:
钣金件的折弯工艺
五.切折:
钣金件的折弯工艺
钣金件的段曲成形
山折的成形工艺
钣金件的翻边
钣金件的沙拉孔
两种常用沙拉孔的规格:
钣金件的凸包成形 1.浅凸成形: 冲压工艺可实现一步成形.
钣金件的凸包成形 2.深凸成形: 需多次成形才能实现.
钣金件的卷圆成形 两种卷圆的成形工艺:
钣金件的展开计算
2.折弯角大于90度时: L: 展开长度 δ: 展开系数
L=A+B+(180-a)/90*δt
2
钣金件的展开计算
二.圆角折弯: L: 展开长度 C:中性层长度
R>t时,用求中性层长度的方法来计算展开长.
L=A+B+C
中性层位移系数 r R/t 0.1 0.2 0.3 0.4 0.5 0.6 0.7 0.8 1.0 1.2 1.3 1.5
L
T
T≦1.0>源自.0L 3.0 >3T
r 0.21 0.22 0.23 0.24 0.25 0.26 0.28 0.30 0.32 0.33 0.34 0.36 3
钣金件的展开计算
三.180度反折: L: 展开长度
L=A+B+1.57t (B>3t)
钣金折弯方法汇总
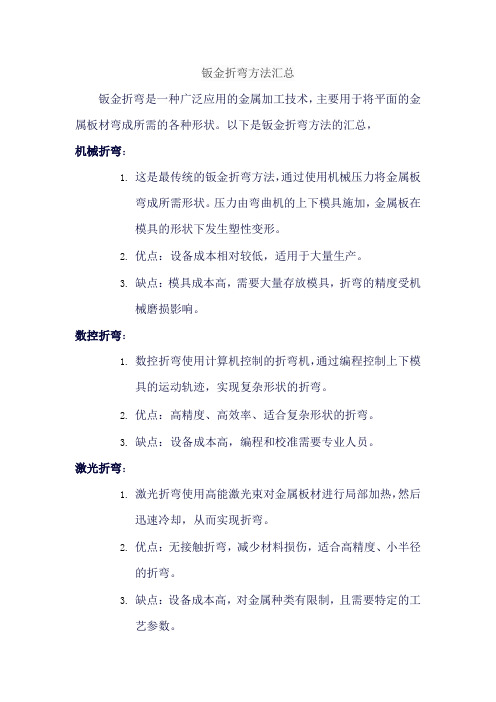
钣金折弯方法汇总钣金折弯是一种广泛应用的金属加工技术,主要用于将平面的金属板材弯成所需的各种形状。
以下是钣金折弯方法的汇总,机械折弯:1.这是最传统的钣金折弯方法,通过使用机械压力将金属板弯成所需形状。
压力由弯曲机的上下模具施加,金属板在模具的形状下发生塑性变形。
2.优点:设备成本相对较低,适用于大量生产。
3.缺点:模具成本高,需要大量存放模具,折弯的精度受机械磨损影响。
数控折弯:1.数控折弯使用计算机控制的折弯机,通过编程控制上下模具的运动轨迹,实现复杂形状的折弯。
2.优点:高精度、高效率、适合复杂形状的折弯。
3.缺点:设备成本高,编程和校准需要专业人员。
激光折弯:1.激光折弯使用高能激光束对金属板材进行局部加热,然后迅速冷却,从而实现折弯。
2.优点:无接触折弯,减少材料损伤,适合高精度、小半径的折弯。
3.缺点:设备成本高,对金属种类有限制,且需要特定的工艺参数。
液压折弯:1.液压折弯使用液体压力对金属板进行弯曲,通常需要一个可移动的弯曲冲头和固定模具。
2.优点:适用于大型和重型材料的折弯。
3.缺点:设备成本高,且对工作环境有特殊要求。
折弯成形一体机:1.这是一种将折弯和成形工艺结合在一起的方法,使用一台机器完成金属板的弯曲和成形。
2.优点:减少生产流程,提高效率。
3.缺点:设备成本和维护成本较高。
柔性折弯:1.柔性折弯使用柔性材料(如柔性金属带或塑料)作为模具,通过加热或弯曲使金属板与之贴合。
2.优点:模具成本低,适合快速原型制作和小批量生产。
3.缺点:精度和效率相对较低。
电化学折弯:1.电化学折弯利用电解的方法对金属板进行局部溶解,通过控制溶解过程实现弯曲。
2.优点:无机械应力,适用于薄片材料。
3.缺点:设备成本高,对工作环境有特殊要求,且加工时间较长。
超声波折弯:1.超声波折弯利用高频振动使金属板发生局部塑性变形,从而实现弯曲。
2.优点:适用于小型零件和高精度折弯。
3.缺点:设备成本高,对材料和工艺参数有特定要求。
钣金件折弯工艺流程

钣金件折弯工艺流程
《钣金件折弯工艺流程》
钣金件折弯工艺是一种广泛应用于金属加工行业的工艺方法,通过将金属板料以一定角度折弯形成所需的形状和结构。
这种工艺流程在汽车、航空、建筑等领域都有着重要的应用。
首先是材料准备,需要准备好待加工的金属板料,一般会根据设计要求选用合适的材质和厚度的金属板料。
接着是进行工艺规划,根据设计图纸要求确定折弯的位置、角度和尺寸等参数,制定出具体的折弯方案。
然后是装夹固定,将待加工的金属板料放置在折弯机的工作台上,并通过夹具进行固定,以确保在折弯过程中板料不会移动或变形。
接下来就是进行折弯操作,将固定好的金属板料放置在折弯机上,通过下模和上模的协同作用,对金属板料进行折弯成型。
最后是检验和修整,将折弯成型的零件进行检验,确保其尺寸和形状符合设计要求,如有需要还可进行修整和矫正。
整个钣金件折弯工艺流程需要在专业人员的指导下进行,严格遵循相关的操作规程和安全规定。
只有这样,才能确保折弯成型的金属零件具有良好的质量和精准的尺寸,满足产品的使用要求。
钣金折弯加工工艺

钣金折弯加工工艺包括:
1.剪板下料法:在剪板上划线并打孔,然后用剪刀沿着划线把材
料剪成所需的形状。
2.模冲切边法:用带齿刀片的模具对毛胚边缘部分进行切断。
3.压延成型法:利用金属塑性变形时体积不变的特点,通过施加
外力使金属产生塑性变形而实现材料的分离与连接的目的。
4.拉深成型法:利用凸模和凹模之间产生的摩擦力来控制零件的
形状尺寸及精度。
5.校平:将上一步得到的平面或弧面工件放在平台上进行校正使
其成为符合要求的工件。
钣金件的折弯工艺

钣金件的折弯工艺钣金的折弯,是指改变板材或板件角度的加工。
如将板材弯成V形,U形等。
一般情况下,钣金折弯有两种方法:一种方法是模具折弯,用于结构比较复杂,体积较小、大批量加工的钣金结构;另一种是折弯机折弯,用于加工结构尺寸比较大的或产量不是太大的钣金结构。
目前公司产品的折弯主要采用折弯机加工。
这两种折弯方式有各自的原理,特点以及适用性。
模具折弯:对于年加工量在5000件以上,零件尺寸不是太大的结构件(一般情况为300X300),加工厂家一般考虑开冲压模具加工。
常用折弯模具常用折弯模具,如图1-17所示:为了延长模具的寿命,零件设计时,尽可能采用圆角。
图1-17 专用的成形模具过小的弯边高度,即使用折弯模具也不利于成形,一般弯边高度L≥3t(包括壁厚)。
台阶的加工处理办法一些高度较低的钣金Z形台阶折弯,加工厂家往往采用简易模具在冲床或者油压机上加工,批量不大也可在折弯机上用段差模加工,如图1-18所示。
但是,其高度H不能太高,一般应该在(0~1.0)t ,如果高度为(1.0~4.0)t,要根据实际情况考虑使用加卸料结构的模具形式。
这种模具台阶高度可以通过加垫片进行调整,所以,高度H是任意调节的,但是,也有一个缺点,就是长度L尺寸不易保证,竖边的垂直度不易保证。
如果高度H尺寸很大,就要考虑在折弯机上折弯。
图1-18 Z形台阶折弯折弯机折弯折弯机分普通折弯机和数控折弯机两种。
由于精度要求较高,折弯形状不规则,通信设备的钣金折弯一般用数控折弯机折弯,其基本原理就是利用折弯机的折弯刀(上模)、V形槽(下模),对钣金件进行折弯和成形。
优点:装夹方便,定位准确,加工速度快;缺点:压力小,只能加工简单的成形,效率较低。
成形基本原理成形基本原理如图1-19所示:图1-19 成形基本原理折弯刀(上模)折弯刀的形式如图1-20所示,加工时主要是根据工件的形状需要选用,一般加工厂家的折弯刀形状较多,特别是专业化程度很高的厂家,为了加工各种复杂的折弯,定做很多形状、规格的折弯刀。
钣金折弯工艺技术方案

钣金折弯工艺技术方案钣金折弯工艺技术方案钣金折弯工艺是一种将金属板材通过折弯工序加工成所需形状的加工工艺。
下面是一份钣金折弯工艺技术方案。
1. 设计方案:根据客户提供的图纸或样品,设计产品的折弯计划和加工工序。
确定所需的折弯角度和折弯方向。
2. 材料准备:根据图纸确定所需材料,并进行材料的采购和准备工作。
材料常用的有钢板、铝板等。
3. 材料切割:根据设计方案和所需尺寸,将材料切割成所需的大小。
4. 折弯工序:在折弯机上进行折弯工序。
根据设计方案的要求,将材料放置在折弯机上,通过折弯机的上下模具施加压力,使材料折弯成所需的形状。
5. 折弯角度控制:使用数控折弯机或手动测量工具来控制折弯角度的准确度。
根据设计方案中所需的折弯角度,调整折弯机的参数,确保折弯角度的准确性。
6. 折弯顺序控制:根据设计方案确定折弯的顺序,特别是对于复杂形状的产品。
折弯顺序的确定可以避免材料的变形和折弯过程中的错误。
7. 补偿计算:在进行折弯工序时,需要根据材料的弹性变形进行补偿计算。
通过调整折弯机的参数和折弯顺序,可以减小折弯过程中的材料变形。
8. 完成产品:完成折弯工序后,需要进行打磨、焊接和表面处理等后续工艺。
确保产品的质量和外观完整。
9. 质量检验:进行产品的质量检验,确保产品符合设计要求。
质量检验可以包括外观检查、尺寸检测和功能测试等。
10. 成品包装:按照客户要求进行产品包装,以确保产品在运输和使用过程中不受损坏。
以上是一份钣金折弯工艺技术方案的基本内容。
在实际操作过程中,需要根据具体的产品和工艺要求进行调整和改进。
通过科学的工艺流程和精确的操作控制,可以提高产品的质量和生产效率。
钣金折弯工艺作业指导书

4.6 弯曲力的计算;
弯曲时根据厚,弯曲长度,下模槽宽,参考折弯机的压力表计算压
力,以免超过折弯机的最大承受力。
公 司
名 称
文件编号
生效日期
2011-09-01
工 序
名 称
钣金折弯工艺作业指导书
版 本
A/0
页 次
2/2
操
作
说
明
4.7弯曲编程时,应参考弯曲展开度K值系数,计算定位比子的尺寸,以便达到正确的尺寸,弯曲展开长度K值系数表现如下:单位(mm)
Rt
1
1.5
2
2.5
3
1
1.75
1.95
2.15
2.35
2.55
1.5
2.5
2.65
2.85
3
3.2
2
3.25
3.45
3.55
3.7
3.9
2.5
4
4.1
4.25
4.45
4.6
3
4.75
4.85
5
5.15
5.3
五:检验标准:
5.1 根据图纸参照以上工艺要求,编程加工,进行首件检验,图纸有公差的严格按图纸检验,图纸无要求的按下面的标准检验:
四.工艺要求:
4.1 板料弯曲时,应选择合适的弯曲半径,为减少弯曲力和弯曲变形,应采用较大的弯曲半径,一般最小弯曲半径按以下选择:
在退火或正火状态下,最小弯曲半径取0.4t,在冷作硬化状态下,最小弯曲半径取0.8t.
4.2 弯曲件的孔到弯曲边的最小距离。
弯曲处属于板材变形,在其周围的孔受其影响易变形,弯曲件的孔到弯曲方向的最小距离应按照以下要求:当孔为圆孔和垂直于弯曲方向的长圆孔时,t<2mm时,L≥2 + r. t≥2mm时L≥3t + r 当孔为方孔和平行于弯曲方向的圆孔时L≥4t + r
钣金折弯工艺的意义与作用
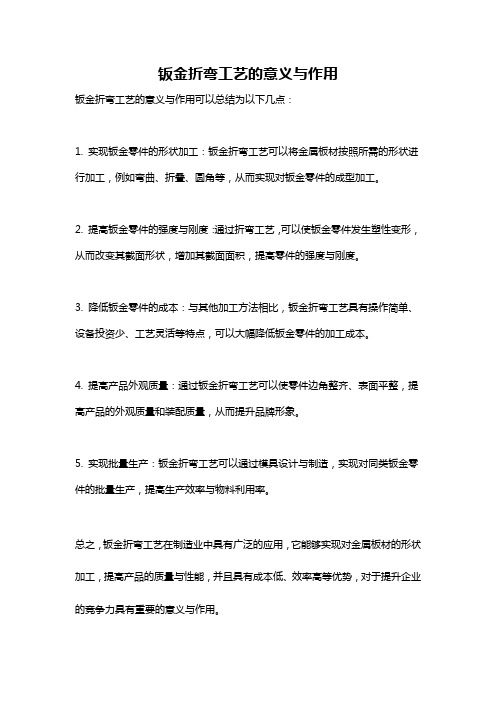
钣金折弯工艺的意义与作用
钣金折弯工艺的意义与作用可以总结为以下几点:
1. 实现钣金零件的形状加工:钣金折弯工艺可以将金属板材按照所需的形状进行加工,例如弯曲、折叠、圆角等,从而实现对钣金零件的成型加工。
2. 提高钣金零件的强度与刚度:通过折弯工艺,可以使钣金零件发生塑性变形,从而改变其截面形状,增加其截面面积,提高零件的强度与刚度。
3. 降低钣金零件的成本:与其他加工方法相比,钣金折弯工艺具有操作简单、设备投资少、工艺灵活等特点,可以大幅降低钣金零件的加工成本。
4. 提高产品外观质量:通过钣金折弯工艺可以使零件边角整齐、表面平整,提高产品的外观质量和装配质量,从而提升品牌形象。
5. 实现批量生产:钣金折弯工艺可以通过模具设计与制造,实现对同类钣金零件的批量生产,提高生产效率与物料利用率。
总之,钣金折弯工艺在制造业中具有广泛的应用,它能够实现对金属板材的形状加工,提高产品的质量与性能,并且具有成本低、效率高等优势,对于提升企业的竞争力具有重要的意义与作用。
钣金加工折弯工艺及解决办法汇总!

钣金加工折弯工艺及解决办法汇总!来源网络转载众多,如有侵权请联系我们!问题一:折弯边不平直,尺寸不稳定原因:1、设计工艺没有安排压线或预折弯2、材料压料力不够3、凸凹模圆角磨损不对称或折弯受力不均匀4、高度尺寸太小解决办法:1、设计压线或预折弯工艺2、增加压料力3、凸凹模间隙均匀、圆角抛光4、高度尺寸不能小于最小极限尺寸问题二:工件折弯后外表面擦伤原因:1、原材料表面不光滑2、凸模弯曲半径太小3、弯曲间隙太小解决办法:1、提高凸凹模的光洁度2、增大凸模弯曲半径3、调整弯曲间隙问题三:弯曲角有裂缝原因:1、弯曲内半径太小2、材料纹向与弯曲线平行3、毛坯的毛刺一面向外4、金属可塑性差解决办法:1、加大凸模弯曲半径2、改变落料排样3、毛刺改在制件内圆角4、退火或采用软性材料问题四:弯曲引起孔变形原因:采用弹压弯曲并以孔定位时弯臂外侧由于凹模表面和制件外表面摩擦而受拉,使定位孔变形。
解决办法:1、采用形弯曲2、加大顶料板压力3、在顶料板上加麻点格纹,以增大摩擦力防止制件在弯曲时滑移问题五:弯曲表面挤压料变薄原因:1、凹模圆角太小2、凸凹模间隙过小解决办法:1、增大凹模圆角半径2、修正凸凹模间隙问题六:制件端面鼓起或不平原因:1、弯曲时材料外表面在圆周方向受拉产生收缩变形,内表面在圆周方向受压产生伸长变形,因而沿弯曲方向出现挠曲端面产生鼓起现象。
解决办法:1、制件在冲压最后阶段凸凹模应有足够压力2、做出与制件外圆角相应的凹模圆角半径3、增加工序完善问题七:凹形件底部不平原因:1、材料本身不平整2、顶板和材料接触面积小或顶料力不够3、凹模内无顶料装置解决办法:1、校平材料2、调整顶料装置,增加顶料力3、增加顶料装置或校正4、加整形工序问题八:弯曲后两边对向的两孔轴心错移原因:材料回弹改变弯曲角度使中心线错移解决办法:1、增加校正工序2、改进弯曲模结构减小材料回弹问题九:弯曲后不能保证孔位置尺寸精度原因:1、制件展开尺寸不对2、材料回弹引起3、定位不稳定解决办法:1、准确计算毛坯尺寸2、增加校正工序或改进弯曲模成型结构3、改变工艺加工方法或增加工艺定位问题十:弯曲线与两孔中心联机不平行原因:弯曲高度小于最小弯曲极限高度时弯曲部位出现外胀现象解决办法:1、增加折弯件高度尺寸2、改进折弯件工艺方法问题十一:弯曲后宽度方向变形,被弯曲部位在宽度方向出现弓形挠度原因:由于制件宽度方向的拉深和收缩量不一致产生扭转和挠度解决办法:1、增加弯曲压力2、增加校正工序3、保证材料纹向与弯曲方向有一定角度问题十二:带切口的制件向下挠曲原因:切口使两直边向左右张开,制件底部出现挠度解决办法:1、改进制件结构2、切口处增加工艺留量,使切口连接起来,弯曲后再将工艺留量切去。
钣金折弯压筋的加工工艺

钣金折弯压筋加工工艺一、材料准备在进行钣金折弯加工前,首先需要准备合适的材料。
材料应具备以下特性:.强度高:为了确保钣金件在折弯过程中不发生变形,应选择强度高的材料。
.塑性好:塑性好的材料在折弯过程中不易开裂,能够保证钣金件的平整度。
.厚度适中:厚度过薄会导致折弯后强度降低,厚度过厚则会导致折弯困难。
根据实际需要,可以选择不同规格和材质的钢材、铝合金等材料。
二、模具设计模具设计是钣金折弯加工中的重要环节。
根据钣金件的实际形状和尺寸,设计适合的模具。
以下是模具设计的主要步骤:.分析图纸:了解钣金件的设计要求,包括形状、尺寸、角度等。
.确定折弯线:确定钣金件的折弯线,包括折弯角度、半径等。
.设计模具:根据钣金件的要求和折弯线的确定,设计适合的模具。
.模具制作:根据设计图纸制作模具,确保模具的精度和硬度。
三、折弯工艺在模具准备好后,可以进行钣金件的折弯加工。
以下是折弯工艺的主要步骤:.上料:将准备好的钣金件放入模具中。
.定位:确保钣金件在模具中的位置准确,避免在折弯过程中发生位移。
.折弯:通过压机或折弯机进行折弯加工,按照预先设计的折弯线进行折弯。
.检查:在折弯完成后,检查钣金件的形状、尺寸是否符合设计要求。
四、压筋工艺压筋工艺是钣金加工中的一种常用技术,用于增加钣金件的强度和美观度。
以下是压筋工艺的主要步骤:.模具设计:根据需要压筋的部位和形状,设计适合的模具。
.上料:将准备好的钣金件放入模具中。
.定位:确保钣金件在模具中的位置准确,避免在压筋过程中发生位移。
.压筋:通过压机或专用压筋设备进行压筋加工,使钣金件表面形成所需的筋条。
.检查:在压筋完成后,检查钣金件的形状、尺寸是否符合设计要求。
五、冲孔工艺在钣金加工中,冲孔工艺是常用的加工方法之一。
以下是冲孔工艺的主要步骤:.模具设计:根据需要冲孔的部位和形状,设计适合的模具。
.上料:将准备好的钣金件放入模具中。
.定位:确保钣金件在模具中的位置准确,避免在冲孔过程中发生位移。
钣金折成圆圈的工艺
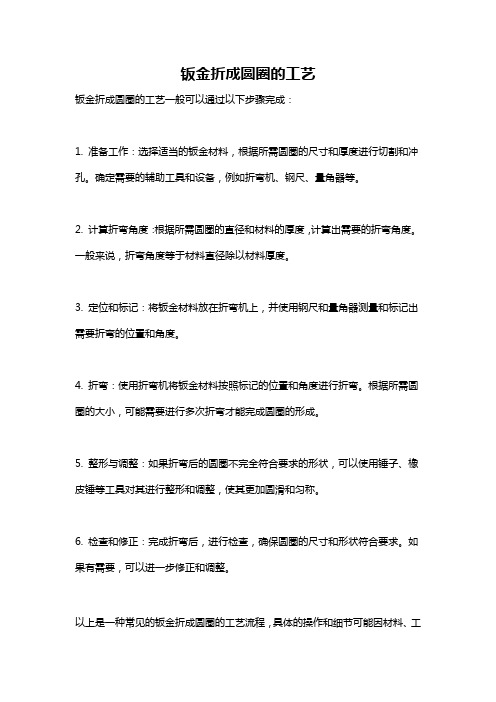
钣金折成圆圈的工艺
钣金折成圆圈的工艺一般可以通过以下步骤完成:
1. 准备工作:选择适当的钣金材料,根据所需圆圈的尺寸和厚度进行切割和冲孔。
确定需要的辅助工具和设备,例如折弯机、钢尺、量角器等。
2. 计算折弯角度:根据所需圆圈的直径和材料的厚度,计算出需要的折弯角度。
一般来说,折弯角度等于材料直径除以材料厚度。
3. 定位和标记:将钣金材料放在折弯机上,并使用钢尺和量角器测量和标记出需要折弯的位置和角度。
4. 折弯:使用折弯机将钣金材料按照标记的位置和角度进行折弯。
根据所需圆圈的大小,可能需要进行多次折弯才能完成圆圈的形成。
5. 整形与调整:如果折弯后的圆圈不完全符合要求的形状,可以使用锤子、橡皮锤等工具对其进行整形和调整,使其更加圆滑和匀称。
6. 检查和修正:完成折弯后,进行检查,确保圆圈的尺寸和形状符合要求。
如果有需要,可以进一步修正和调整。
以上是一种常见的钣金折成圆圈的工艺流程,具体的操作和细节可能因材料、工
具和实际情况而有所不同。
在进行钣金加工时,需要在安全的环境下进行,并根据实际情况选择合适的材料和工具,确保安全和质量。
钣金折弯工艺介绍

钣金折弯工艺介绍钣金折弯工艺是一种常见的金属加工方法,用于将金属板材折弯成所需的形状和角度。
它在许多工业领域中都有广泛的应用,包括汽车制造、航空航天、电子设备等。
本文将介绍钣金折弯工艺的基本原理、工艺流程和常见的折弯方法。
一、基本原理钣金折弯工艺利用机械力将金属板材按照所需的角度弯曲。
在折弯过程中,金属板材的外层受到拉伸力,内层受到压缩力。
通过合理的控制力度和角度,可以使金属板材保持一定的强度和稳定性,同时实现所需的形状和角度。
二、工艺流程钣金折弯工艺的一般流程包括设计、材料准备、模具制作、加工和检验等步骤。
1. 设计:根据产品的要求,设计出需要折弯的金属板材的尺寸、形状和角度。
2. 材料准备:根据设计要求,选择合适的金属板材,并进行切割、去毛刺等处理,以保证板材的质量和表面光滑度。
3. 模具制作:根据设计图纸,制作适用于折弯的模具,包括上模、下模和弯边模等。
4. 加工:将准备好的金属板材放置在折弯机的工作台上,根据设计要求调整机器参数,将模具安装到机床上,进行折弯加工。
操作人员需要根据需要调整机器的压力和角度,保证折弯的精度和质量。
5. 检验:对折弯后的产品进行检验,包括尺寸、角度、外观等方面。
如果有不合格的地方,需要进行修正或重新加工。
三、常见的折弯方法钣金折弯工艺有多种方法,常见的包括V型折弯、U型折弯和Z型折弯。
1. V型折弯:V型折弯是通过将模具上的上模和下模夹紧金属板材,在板材两侧施加力量,使金属板材弯曲成V形。
这种折弯方法适用于金属板材较薄的情况,可以获得较小的弯曲半径。
2. U型折弯:U型折弯是通过将模具上的上模和下模夹紧金属板材,在板材两侧施加力量,使金属板材弯曲成U形。
这种折弯方法适用于金属板材较厚的情况,可以获得较大的弯曲半径。
3. Z型折弯:Z型折弯是通过将模具上的上模和下模夹紧金属板材,在板材两侧施加力量,使金属板材弯曲成Z形。
这种折弯方法适用于需要多次折弯的情况,可以获得更复杂的形状和角度。
- 1、下载文档前请自行甄别文档内容的完整性,平台不提供额外的编辑、内容补充、找答案等附加服务。
- 2、"仅部分预览"的文档,不可在线预览部分如存在完整性等问题,可反馈申请退款(可完整预览的文档不适用该条件!)。
- 3、如文档侵犯您的权益,请联系客服反馈,我们会尽快为您处理(人工客服工作时间:9:00-18:30)。
钣金折弯工艺
1. 适用范围:
本工艺守则适用于生产高、低压开关柜(箱)过程中,低碳钢板的折弯。
允许公差值按标准JB/T6753.1-5.1中表1的规定。
适用于产品结构零部件折弯加工工序之用。
2. 工艺过程:
3. 准备工作内容:
3.1 熟悉图纸和技术要求:备齐板手等手工具和钢卷尺、角度尺、游标卡尺等量具。
3.2 检查折弯机的状态,检查内容包括:
A. 检查润滑情况是否正常,需要时将各部加足润滑油。
B. 检查机械部件是否正常,螺丝有无松动。
3.3 检查待折弯的板料尺寸及角度,是否符合图纸要求,图纸无展开尺寸时,应按下表计算核对:
4. 检查及调整折弯机:
4.1 机器刚开始使用时,对于同步油缸式折弯机,应放掉左右两个同步油缸中的空气,放气步骤如下:
A.将放气螺丝松开;
B.由按钮控制“充油”“工作”交替进行,并使滑块上下数次,使油缸中的空气放入油箱。
C.将放气螺钉旋紧,再由按钮控制充油,充油后折弯机两油缸应保持同步。
4.2 调整下刀两端的推拉螺杆,使上下刀口中心线重合。
4.3 调整滑块下限:
对于同步油缸式折弯机根据板料厚度和弯曲及开关用按钮通过电动机调整滑块的下限(即滑块下死点)指针旋转一周滑块移动1毫米,注意不得使上刀与下刀槽接触,以免造成顶刀事故,上下刀的间隙不得小于板料厚度。
对于机械同步折弯机,先将下止点调整手轮顺时针方向调整到最小值,然后逆时针下调,一边折弯一边转动直到折弯角度合适时停止。
4.4 摇动“直板调节手轮”,使制板端面与下刀槽中心等于工件边高减去料厚,调整时使用300毫米深度尺寸在制板两端测量。
4.5 正确选用下模V形槽,开口尺寸应符合折弯压力表的规定。
5. 折弯
5.1 板料正式折弯前应用一块厚度,长度与工件相同的板料试折,通过试折检查工件尺寸和角度存在的问题,并相应调整滑块下死点、直
板等。
折弯机经过调整后应再次试折。
5.2 为保证获得较好的工件折弯精度,板料必须平整。
5.3 折弯板料应放在机器中间位置,不许单边载荷使用。
5.4 在满载时,板料宽度应大于1米,严禁在较大工作压力下窄料折弯。
折弯机有“单次”和“点动”连续三种工作方式,一般折弯应选用“点动”方式,对于机械同步折弯机调整好后,一般采用单次或连续行程。
5.6 箱门类产品折弯时,应按工件尺寸配上刀,一般先折小面;然后根据大面尺寸搭配上刀,使上刀总长小于大面尺寸5-6毫米左右,如无法搭配出上述尺寸,可使几条上刀具之间留有间隙,但间隙不应大于10毫米。
5.7 长度或厚度超过折弯机负荷能力的板料不得加工。
6. 检验:
6.1 批量生产的工件其首件折弯后要经小组组长检验合格后方允许继续生产。
6.2 加工过程中操作人要随时检查工件的质量,发现质量问题要马上停机找出和消除问题原因后,方允许继续开机。
6.3 折弯工作的质量应达到以下要求:
A.弯角误差2°/1000mm;
B.弯角棱角直线度0.3‰;
C.折弯尺寸误差±0.3mm。