FMEA失效模式与效应分析(简体)
FMEA失效模式与效应分析
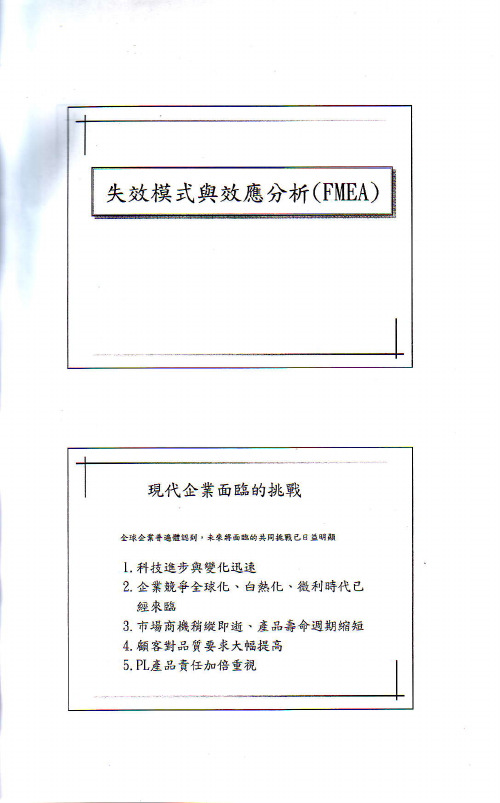
.H:rf+[ fl +:r"&]g6tFi|EA
. fls:lrf lErif ' taEFJ&^R.*.8R.FrdH.!&6th1" .t
.
+} 1+4.1'14d*.r3+El6gf nf'a.&i*1?Wt
n ,
F
a
j
"
t
rE
'
d
n
,
v
'
n
r
'
u
&
E
z
.4 ?fg+k rf tE6 ifrAtFllE(A6 Siena)
.
iF4, .tttt.*rlut
E.
+L'&-+44hhEts+ ' EE4+t-+ztttF,,-.f-rkl4
Wh.JiL*.
. 4*_1Bt-t!.sp.kY.1$( P. DM)
ffE,'"4tf 6t€+1*
4 L++hE-F"fAl*d,'i €.;* Sz.J*1. 6
1 .1 , i , t & e ^ i { ( 5 1 { 2 H ) & D e sr ei svni e u , ( 6- ]j f!l l* ) 23..&E4€i.t4+-6ir1gi f.AA1rE.+'+E#nfjfA| (i.Ci. ustorVr oice) 4. d4 &?E6 ftE&tB nE+;'trt,E 5.€6i a &i{;+ ?rtS.&isrA 6 .F . S 0 f D , : " q { q e R f r l ,rtEE, r € , , t J t r t , % . c } 6 & r a q " , i , t r
FMEA失效模式和效应分析

1 of 19項 目:過程責任:生產準備者:部 門:制一部零件號:關鍵日期:FMEA 日期:中心隊員:FMEA 編號: 0606242 of 19項 目:過程責任:生產準備者:部 門:制一部零件號:關鍵日期:FMEA 日期:中心隊員:FMEA 編號: 0606243 of 19項 目:過程責任:生產準備者:部 門:制一部零件號:關鍵日期:FMEA 日期:中心隊員:FMEA 編號: 0606244 of 19項 目:過程責任:生產準備者:部 門:制一部零件號:關鍵日期:FMEA 日期:中心隊員:FMEA 編號: 0606245 of 19項 目:過程責任:生產準備者:部 門:制一部零件號:關鍵日期:FMEA 日期:中心隊員:FMEA 編號: 0606246 of 19項 目:過程責任:生產準備者:部 門:制一部零件號:關鍵日期:FMEA 日期:中心隊員:FMEA 編號: 0606247 of 19項 目:過程責任:生產準備者:部 門:制一部零件號:關鍵日期:FMEA 日期:中心隊員:FMEA 編號: 0606248 of 19項 目:過程責任:生產準備者:部 門:制一部零件號:關鍵日期:FMEA 日期:中心隊員:FMEA 編號: 0606249 of 19項 目:過程責任:生產準備者:部 門:制一部零件號:關鍵日期:FMEA 日期:中心隊員:FMEA 編號: 06062410 of 19項 目:過程責任:生產準備者:部 門:制一部零件號:關鍵日期:FMEA 日期:中心隊員:FMEA 編號: 06062411 of 19項 目:過程責任:生產準備者:部 門:制一部零件號:關鍵日期:FMEA 日期:中心隊員:FMEA 編號: 06062412 of 19項 目:過程責任:生產準備者:部 門:制一部零件號:關鍵日期:FMEA 日期:中心隊員:FMEA 編號: 06062413 of 19項 目:過程責任:生產準備者:部 門:制一部零件號:關鍵日期:FMEA 日期:中心隊員:FMEA 編號: 06062414 of 19項 目:過程責任:生產準備者:部 門:制一部零件號:關鍵日期:FMEA 日期:中心隊員:FMEA 編號: 06062415 of 19項 目:過程責任:生產準備者:部 門:制一部零件號:關鍵日期:FMEA 日期:中心隊員:FMEA 編號: 06062416 of 19項 目:過程責任:生產準備者:部 門:制一部零件號:關鍵日期:FMEA 日期:中心隊員:FMEA 編號: 06062417 of 19項 目:過程責任:生產準備者:部 門:制一部零件號:關鍵日期:FMEA 日期:中心隊員:FMEA 編號: 06062418 of 19項 目:過程責任:生產準備者:部 門:制一部零件號:關鍵日期:FMEA 日期:中心隊員:FMEA 編號: 06062419 of 19項 目:過程責任:生產準備者:部 門:制一部零件號:關鍵日期:FMEA 日期:中心隊員:FMEA 編號: 060624。
FMEA失效模式与效应分析
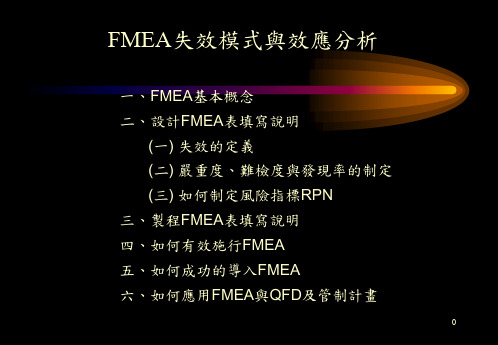
一、FMEA 的基本概念
1. 及時性是成功實施FMEA的最重要因素之一。
2. 它是“事前的預防”而不是“事後的追悔”。
3. 事先花時間進行FMEA分析,能夠容易且低成本 地對產品設計或製程進行修改,從而減輕事後修 改的危機。
4. FMEA能夠減少或消除因修改而帶來更大損失的 機會,它是一個相互作用的過程,永無止境的改 善活動。
2.失效效應分析(failure effect analysis) EA
對每一個失效模式,確定其失效對其上一層模組及最終系統的失 效影響,了解其組件介面失效關聯性,做為改進行動的依據。
3.關鍵性分析(critical analysis)
CA
對每一個失效模式,依其嚴重等級和發生機率綜合評估並予以分
難檢度 15
一、FMEA 的基本概念
腦力激盪法
6 – 3 – 5 原則 6人、3構想、看5次
➢ 禁止批評 ➢ 自由奔放 ➢ 求量 ➢ 搭別人創意便車
成品合格出廠 卻被顧客抱怨 的原因可能有
三菱式 腦力激盪法
➢ 理性過濾,擇取組合,表達具體明確 ➢ 刪除意見要獲得成員大多數同意 ➢ 表達以《名詞+形容詞》方式 ➢ 創意評價
3
一、FMEA 的基本概念
1.對產品設計與製程進行失效分析, 找出元 / 組件的失效模 式,鑑定出它的失效原因,並評估該項失效模式對系統會 產生什麼影響。
2.找出元 / 組件或系統的潛在弱點,提供設計、製造、品保 等單位採取可行之對策,及早進行設計與製程研改,強化 產品品質。
3.書面描述上述分析過程,確保產品品質符合顧客需求。
FMEA” ,而 MIL- STD -1629A因分析項目缺少現行管制方法 故適合設計時使用。 5.FMEA為歸納法之應用,根據零組件的失效資料,由下而上推斷 系統的失效模式及其效應,是一種向前推演的方法。
FMEA失效模式及效应分析说明(ppt 58页)
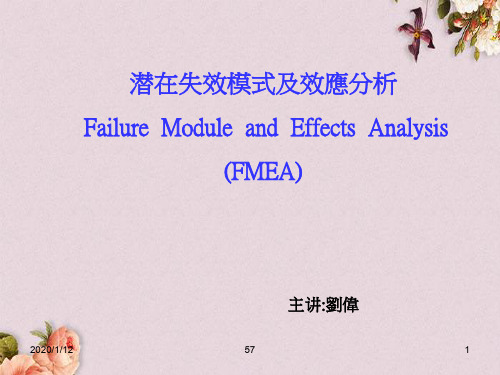
府法規時,有事先警告產生。(車毀人亡/違犯法紀,有預告)
非常高 車輛/項目無法操作,喪失應有功能
8
高
車輛/項目可以操作,但降低功能等級,客戶不滿意。
7
稍有 車輛/項目可以操作,但令人舒適或便利的項目無法運作。客戶通常會感受 6
到不舒適。
低
車輛/項目可以操作,但令人舒適或便利的項目未達到功能要求。客戶有時 5
項目名稱:
ˍ
生效日期:
核心小組: 設計二課成員
設計責任: FMEA(編制)日期:
編制者: (修訂)日期_______
項目 功能
潛在失 效模式
潛在失 效效應
嚴 重 度
等 級
潛在的失 效
發 生
原因 度
負責擔
現行預 防設計 管制
現行偵測 設計
管制
偵 測 度
風險 優先數
RPN
建議 措施
當人 與
完成日 期
採行 的措
资料搜集
提出矫正预防
制订DFMEA计划 建立功能方块图
产品结构树 设计可靠度分析
重新計算矫正預防后风险优先数
N
RPN小于规定值?
Y 分析確認
决定分析之项目/功能 进行DFMEA分析 选择关键失效模式
DFMEA报告 N
设计审查 Y
發佈執行/纪录保存
A
2020/1/12
57
10
設計FMEA表
FMEA編號: 頁 碼: 第 頁 共 頁
2020/1/12
57
12
設計FMEA填寫說明
項目/功能注意:
儘可能簡潔地,填入被分析的項目/功能並使其符合設計意圖。包 括這個系統作業相關環境的資訊(如:溫度、壓力、溼度範圍)。
失效模式与效应分析

*
砫ヴ
* *
2-2 ┦ 2-3砞 璸 琩 靡 2-4砞 璸 糵 琩 2-5 2-6 * 2-7 2-8 2-9瓜 妓 ㎝ 砏 2-10穝 砞 称 2-11疭 2-12秖 砏 〒 2 - 1 3恨 矗瞶 某 ぇや 2-14 材 Output// 材 input 3 1 3 2 玻 杆珇 夹 * & * * 3 3 籹 祘 瑈 * *
失效风险分析
以数据评估失效模式风险-风险关键指数 (RPN:Risk Priority Number) 风险关键指数由下列组成 S= 严重度 P= 发生率 D=侦测度
RPN风险率的构成
效应(影响)
严重度S
失效模式(现象)
原因
发生率P
控制
侦测度D
PFMEA风险的评估与改善评估
制程 管制 难易 度
【准备篇-豫则立,不豫则废】
准备阶段
1.确认产品的可靠度要求及目标。 2.掌握系统、次系统的构造(列出产品所有的机构 组件零件、制程、事务流程所有的步骤) 3.决定失效风险分析(RPN)水平。 4.准备失效模式分析表。
Remark: 时间计划的整合-绝大部份进行此类分析的人员,都 有原本的任务,一方面要能进行日常工作,另一方面 要能完成分析工作,因此时间的妥善安排是非常重要 的
1/2
1/20
1
100
10
低
失败成本
高
预防、改善与灾害控制
预防-FMEA
D&P 商品企划 产品设计、试作 准备 生产
销售、售后服务
改善-8D
QIT&QCC
灾害控制
市场撤退
低
失败成本
高
每 一 良 品 之 成 本
预防与鉴定成本 失敗成本
FMEA失效模式与效应分析2

壞
僅暫時不適,或至保健中心接
受簡 醫院
單 治
之急 療,
救 且
處理, 隨即可
但 回
不 工
需 作
至 崗
僅零
組
件
損
壞
位
危險性工作場所FMEA
二、FMEA方法介紹目的
定義-以元件故障為出發點,推論失效類型對系統 產生的影響性,並據此分析結果建立防範措 施或更改設計
目的:增加產品的可靠度與即時處置異常狀況之 發生(減少事故發生、增進製程安全、提高 生產效率)
D.消 減 措 施
(一 )消 防 (二 )除 毒 (三 )卸 爆 口
(一 )緊 急 應 變 SOP (二 )落 實 人 員 訓 練 (三 )稽 核
危險性工作場所FMEA
一、簡介執行之思考方向
(三)針對改善建議
針對改善建議加以執行之思考方向 人為操作教育訓練、
SOP (表單配合) 稽核(考績+獎懲+升遷 配合)
• FMEA以單一元件失效出發,無法考慮數個元件 同時失效的模式,一者因為太複雜,再者不實際 。FMEA是分析產品自身的失效影響,不討論人 員操作的問題。
• FMECA=FMEA+CA(Criticality Analysis)
二、FMEA方法介紹優缺點
優點: 對於硬體設備的檢核相當徹底 複雜系統的利器 易於實施 一件產品的零件在某特定的時間及情況下, 如何失去功能,故障的次數是多少,故障之 後對其它零件或對整個系統會產生怎樣的影 響等。
未發生事故前之完整分析 (1)利用What-if、FMEA、HazOp、FTA
危險性工作場所FMEA
一、簡介改善建議之思考方向
(二)提出改善建議改善建議之思考方向及架構
FMEA失效模式与效应分析课件

該方法 的檢測 能力有 多好?
12
功能方塊圖範例
原子筆範例
墨水 墨水管
筆蕊頭
筆蕊
筆管
尾蓋
筆前蓋
13
原子筆功能方塊圖範例
完整功能範圍
作記號 適合手指運用 顯示資訊
墨水管
儲存墨水 輸送墨水 配合筆蕊頭
墨水
作記號 維持順暢
筆蕊頭
固定墨汁管 固定筆蕊心 輸送墨水 配合筆管
筆管
固定筆蕊頭 固定尾蓋 顯示資訊 適合手指運用
(16)
(16)
(17)
(18)
(19)
(20)
(21) (22) (22) (22) (22)
11
FMEA表各欄位關連性說明.
項目 功能 潛在 失效模式 潛在 失效效應
後果是 什麼?
嚴重 度 分類 (S)
有多 糟糕?
潛在原因/ 設備失效
發生 度(O)
現行管制 預防 檢測
難檢 風險優先數 度 RPN (D)
8
國際間採用FMEA之狀況.
1.ISO 9004 8.5 節FMEA作為設計審查之要項。
2. CE標誌認證,以FMEA作為安全分析方法。 3.ISO 14000,以FMEA作為重大環境影響面分 析與改進方法。 4.QS 9000 以FMEA作為設計與製程失效分析方法。
9
FMEA作業流程
組成FMEA小組 資料蒐集 釐訂FMEA計畫 建立功能方塊圖 產品結構樹 可靠度展開(QFD) 決定分析之項目功能 FMEA報告 N 設計審查 Y 紀錄保存
流出源>>
2.對失效的產品進行分析,找出零組件之 失效模式,鑑定出它的失效原因,研究 該項失效模式對系統會產生什麼影響。
失效模式与效应分析(FMEA)
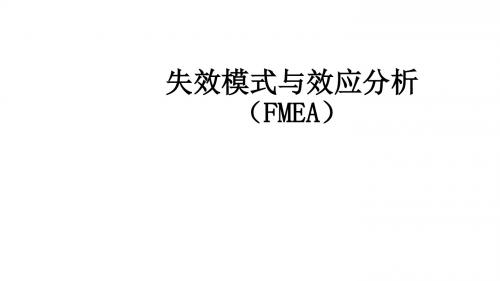
失效模式与效应分析 (FMEA)
起源
FMEA大约于1950年代由美国Grumman公 司提出,当时由于飞机系统复杂并且需要 预防失效情况发生,因此渐渐发展成安全 性与可靠度的设计模式,以期能够增加产 品质量,降低不良问题的发生。
FMEA具体项目
• 累积经验,早期发现失效原因及采取因应之道。 • 促进设计改良。 • 改善操作方法及建立维护计划的参考。 • 帮助操作人员之训练,让员工能在短期内找出 失效原因与解决之法。 • 公司人员异动时,能让员工快速上手。
FMEA表格建立
失效机率
字码体系
严重性分析
多要因评估法
单要因评估法
列表评估法
失效报告
范例
范例
范例
范例
范例
故障树分析符号
故障树分析范例
故障树简化
故障树关键性估计范例
结论
• 透过FMEA模式,可有效找出来自品失效原因,进而解决问题,是一 个可靠性的解析手法。 • 藉由实施FTA ,能让不希望发生的事情明确化,并能判别事件发 生时所带来的一些事象与对成品的影响。
FMEA前期失效模式与效应分析

失效模式 失效效應 重
失效原因 生
項目
度級
率
現行 管制方式
端子/塑膠投入 標示不清或錯誤 無法辨識產品 2
狀態
signal pin端子 缺pin
客戶無法使用 7
插入,折carrier
及打 kink
塑膠刮傷
客戶不滿意
4
(外觀方面)
人為疏忽
1.電鍍制程中測試時 取樣
2.換端子時碰掉 1.自動機流道不順使
19
Failure Mode & Effects Analysis
7. FMEA 制作
7-2: 表格各欄位填寫說明(續)
5 1.開/調機時確認有無刮 傷
2.IPQC&IPQA 每4hrs 抽驗 3.終檢將此不良作為重點
檢驗項目之一 4 1.後制程CCD 100%測試
2.連續發生異常時調打 kink機構
3 1.列入外觀檢驗項目 2.刀具更換
3 1.作業人員自主檢查 2.IPQC/IPQA 抽驗 1.每次拿取不超5 pcs
4.客戶問卷調查
9.顧客抱怨分析
5.產品驗收測試
9
Failure Mode & Effects Analysis
3. FMEA淵源
Grumman Aircraft Company
1950 FMEA 飛機主操縱系統 失效分析
Boeing & Martin Marietta Aerospace Company
客戶需求及其他可取得資訊. 2) 使用統計推論,數學模式,模擬分析,同步工程及可靠度工程
等. 使用FMEA並不意謂這種方法比其他手法更好,或是更準確.如果正 確及時的使用,FMEA方法會更準確,更正確及更有效率.
FMEA失效模式与效应分析

設計責任: 生效日期:85.08
FMEA編號:
0001
頁次: 1 of 1
準備者:
FMEA日期 (製訂) 85.7.15(修訂)
¶µ ¥Ø ¼ç ¦b ¥¢ ¼ç ¦b ¥¢ ¥\ ¯à ®Ä ¼Ò ¦¡ ®Ä ®Ä À³
¨R ¼Ò §@ ·~ ¨R ¼Ò ¤§ ¦¨ «~ ±Y µõ ¹L ¦h P ¥~ Æ[ ÄY 5 « ¤£ ¨}
¡E ®¶ °Ê ±µ ÂI ¯} ·l
6
²{ ¦æ ¹w ¨¾ ³] p ºÞ ¨î
²{ ¦æ ÀË ´ú ³] p ºÞ ¨î
Ãø ÀË «×
· ÀI Àu ¥ý ¼Æ
«Ø ij ±¹ ¬I
t ³d ¤H »P
¤é ´Á
°õ ¦æ µ² ªG ±Ä ¦æ ±¹ ¬I S O D RPN
¤@ ¯ë ¥i ¾a «× ¶µ ¥Ø ¹ê Åç
¥[ ±j ¤H û ¤§
±Ð ¨| °V ½m
5
· ÀI Àu ¥ý ¼Æ
90
«Ø ij
t ³d ¤H
°õ ¦æ µ² ªG
±¹ ¬I
»P ¤é ´Á
±Ä ¦æ ±¹ ¬I
SO
¥Ñ ®ð À£ ¦¡ ¨R ¼Ò ¾÷ §ó ´« ¡A ªo À£ ¦¡
À£ ű ½Ò µ{
2 ¤p ®É ÀË ¬d ¤@ ¦¸ ½T «O ¥~ Æ[ ¨} ¦n
2.失效分析在找出零組件或系統的潛在弱 點,提供設計、製造、品保等單位採取 可行之對策。
第三版(2002.8.1)
docin/sundae_meng
2
失效的定義
在失效分析中,首先要明確產品的失效是什麼 ,否則產品的數據分析和可靠度評估結果將不一樣, 一般而言,失效是指: 1.在規定條件下 (環境、操作、時間 )不能完成既
FMEA失效模式与效应分析(PPT 54页)

国际间采用FMEA之状况
1.ISO 9004 8.5节FMEA作为设计审查之要项 ,另FTA亦是。 2.CE标志,以FMEA作为安全分析方法。 3.ISO 14000,以FMEA作为重大环境影响面分 析与改进方法。 4.QS 9000以FMEA作为设计与制程失效分析方法。
8
设计FMEA之目的
1.帮助设计需求与设计方案的评估。 2.帮助初始设计对制造和装配的需求。 3.在设计发展阶段,增加失效模式和系统效应分析的次数。 4.提供另一项分析信息,帮助设计验证之规划。 5.根据对顾客需求的影响性,列出失效模式的排序,并按序
(建议将所有小组成员名字、单位、电话号号、地址等另行列表)。 (9)项目/功能:填入要被分析的名称和编号。利用专用名词和工程
图面上显示的设计等级。于首次正式发行之前,可以使用实验时 使用的编号。
尽可能简洁地,填入被分析项目的功能使之符合设计意图。包括 这个系统作业相关环境的信息(如:设定温度、压力、湿度范围)。 如果项目包含一个以上有不同潜在失效模式功能时,则列出所有个别 功能。
4.1980修改为MIC-STD-1629A,延用至今。 5.1985由国际电工委员会(IEC)出版之
FMECA国际标准(IEC812),即参考MIC-STD-1629A 加以部份修改而成。
6
FMEA之特征
1.是一项以失效为讨论重点的支持性与辅助性的可靠度 技术。
2.用表格方式进行工程分析,使产品在设计与制程规划时 ,早期发现缺陷及影响程度以便及早提出解决之道。
FMEA日期(制订) (7) (修订) (7)
(8)
11
设计FMEA表(范例1)
系统
子系统
零组件: 冷凝器
设计责任:
失效模式与效应分析(FMEA)

無法傳遞扭力
配合作業或零件,填寫如下: 組配鬆動 / 扣件斷裂
填表說明 —潛在失效的影響
項目 功能 潛在失效模式 潛在失效的 影響 嚴 重 等 度 級 S 潛在失效的 原因 發 生 率 O 現行設計控制 預防 偵測 偵 測 度 D R P N 措施執行結果 建議 措施 責任/ 目標 完成日 採取 措施 嚴 發 偵 R 重 生 測 P 度 率 度 N
定義:在下一個組件、系統、次系統 或客戶發生失效之潛在影響程度的嚴 重度。 使用:評估嚴重度時以1~10分表示。 唯一降低嚴重度的方法是設計變更。
嚴重度評分之例
發生之失效極為嚴重,危及安全,並違反政府法令。 9~10 發生失效會影響產品主要功能之表現,並有可能形成不合法 規問題,但不致有安全問題。 7~8 發生失效後,會引起使用者相當的不滿,例如駕駛不靈便、 收音機故障等不影響主要功能之系統失效等。 6 發生失效後,可能引起使用者少許不滿,使用者通常是略感 不便,例如車輛收音機偶有雜音,離合器踏板不便等,使用 者偶而發現此種異常現象。 4~5 發生失效後,至少只對使用者造成輕微的不便,使用者只會 偶而發現此種異常狀況。 2~3 發生失效後通常不致對產品發生顯著影響,使用者甚難發現 此種失效存在,要消除此種失效亦甚困難。 1
中等:造成客戶不舒適或感到困擾如擋風玻璃漏水、引擎聲音 超大。 評分方法:4-6(根據客戶不舒適程度而定) 低 :客戶感到輕微的困擾 評分方法:2-3(根據客戶不舒適程度而定) 輕微:懷疑這個失效可能會真的影響操作(使用),大部份的 客戶將可能不會注意到此項失效之影響。 評分方法:1
填表說明 — 項目/功能
潛在原因/機構的失效 定義:一種設計上的缺點所導致之失效模式。 使用:列出每一可能潛在失效原因,頇盡可能的依其重要性順序準確的提出。例: 潛在失效因素 規定的材料不正確 設計壽命估計不足 壓力大材質 潤滑能力不足 潛在機構失效 不穩定 化學性氧化 彎曲變形 電位移 1
失效模式与效应分析(FMEA)

失效模式与效应分析(FMEA)一、定义失效模式与效应分析(failure mode and effects analysis,FMEA)是一种前瞻性的管理模式,是在行动之前就认清问题并预防问题发生的分析。
FMEA由失效模式(failure oode,FM)及效应分析(effects analysis,EA)两部分组成。
其中,失效模式是指能被观察到的错误或缺陷(俗称安全隐患),应用于护理质量管理中就是指任何可能发生的护理不良事件;效应分析是指通过分析该失效模式对系统的安全和功能的影响程度,提出可以或可能采取的预防改造措施,以减少缺陷,提高质量。
二、目的、目标FMEA的目的是防患未然;设计屏障,让事情不要发生;降低损害,即使有风险存在,也是可容许的最低风险;是发现、评价流程中潜在的失效及其后果,找到能够避免或减少这些潜在失效的措施,并将上述过程文件化。
FMEA的主要目标是分析现有系统(流程)或将建立之系统(流程):哪里会出错?一旦出错会有多糟糕?哪里需要修正以避免事故发生?三、执行时机1、新设计的流程2、修改现行的流程3、旧的流程用于新的情境中四、实施步骤(一)步骤一:确认问题选择那些高风险或非常薄弱的程序进行研究。
高风险流程的特性有:高复杂性(步骤多)的作业、高差异性的输入来源、未标准化的作业、紧密相依的作业、作业时间间隔太紧或太松、高度依赖人员的判断或决定。
医疗行为中的高风险流程有:用药、病人处于危险的操作流程(放射治疗,CT扫描,磁振造影)、输血与输成分血、抑制作用的药物、对高危人群进行照顾或提供服务、与复苏相关等。
(二)步骤二:组建团队组建一个多学科的综合FMEA团队,团队中至少应该有一个领导者、一个所硏究流程方面的专家、一个FMEA咨询师(即FMEA专家,可以为团队领导者提供建议,保证FMEA的顺利实施)、一个对所研究流程不太熟悉的人(可以从不同的角度和方面提出有价值的建议)。
一般建议团队成员在6〜10人之间,以便于管理,所有成员必须接受过FMEA培训。
FMEA失效模式及效应分析说明

•2.在規定條件下,產品參數值不能維持在規定的上 • 下限之間。
•3.產品在工作範圍內,導致零組件的破裂、斷裂、 • 卡死等損壞現象。(產生影響)
书山有路勤为径, 学海无涯苦作舟
•2020/4/13
•57
•FMEA過程順序
•系統有哪些功能,特徵,需要條件?
•(7) 項目/功能:填入要被分析的名稱和編號。利用專用名詞和工程 • 圖面上顯示的設計等級。於首次正式發行之前,可以使用實驗時 • 使用的編號。
•
书山有路勤为径, 学海无涯苦作舟
•2020/4/13
•57
•設計FMEA填寫說明
• 項目/功能注意:
• 儘可能簡潔地,填入被分析的項目/功能並使其符合設計意圖。包 括這個系統作業相關環境的資訊(如:溫度、壓力、溼度範圍)。 • 如果項目包含一個以上有不同的潛在失效模式功能時,則列出所有 個別功能。
•PFMEA– 開始於基本的操作方法討論,完成時間早於過程設計開
始
• 书山有路勤为径,
学海无涯苦作舟
之前•20,20/用4/1於3 指導過程設計展開。
•57
•FMEA之特徵
•1.是一項以失效為討論重點的支援性與輔助性的可靠度分析 • 技術。 •2.用表格方式進行工程分析,使產品在研發/設計/製程規劃時 • ,早期發現缺陷及影響程度以便及早提出解決之道。 •3.是一種系統化之工程設計輔助工具。 •4.FMEA以分析對象不同分成 “設計FMEA--DFMEA” 及“製程FMEA--PFMEA •5.FMEA為歸納法之應用,根據零組件的失效資料,由下(失效模式) • 而上推斷系統的偵測及預防管制措施,是一種向前推演的方法。
FMEA讲义失效模式效应分析课件
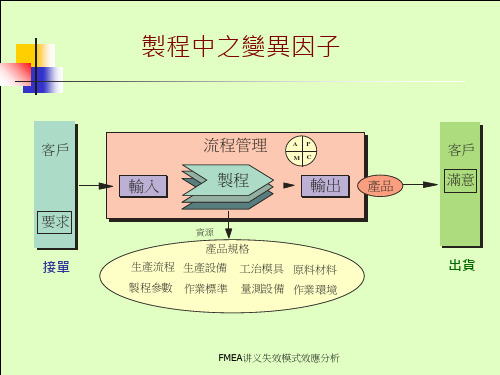
時,採取適當行動以降低
RPN
值
‧對
RPN
之項目應最優先採取必要措施,其目的在
降低嚴重性、發生性及偵測性之分數。若不採
有
效之改正措施則製程
FMEA
之成效將受局限
‧嚴重性×發生性×偵測性
不良模式舉例:變
型、破裂、
影像模
糊
、
訊號不清
失效效應影響範例:
收訊不
穩定,操作不
靈,
當機
原因範例:
機殼
f
軟板
d
電池
座
b
面板
a
1
5
4
5
4
3
2
零件
a
.
面板
b
.
電池
座
c
.
按鍵
d
.
軟板
原型品管制計劃
製造流程圖 作業流程 作業內容 作業功能 驗明及研訂
製程監測及量產管制計劃定稿
量試
檢驗標準書研定
量試管制計劃
初期製程能力分析
量試檢討Process FMEA 對策驗證及修訂
量具、檢具、夾治 具、測試設備及相關生產設備規劃
量產
量、檢、測試設備變異分析及對策
FMEA 對策
原型品驗證 產品規格確認
度,不
良之
預防必須加以考慮
‧
偵
測性係對該零件或裝配件送交生產前,其可
能
存在之設計弱點是否能經設計
驗證而查出之能
力
‧
設計工程師應負責確認各項改正行動均經完成
或均經通知負責人確實執行
‧
將已採取之改正行動之內容及其完成日期填入
記錄,重新預估並記錄改正後之嚴重性、發生性
- 1、下载文档前请自行甄别文档内容的完整性,平台不提供额外的编辑、内容补充、找答案等附加服务。
- 2、"仅部分预览"的文档,不可在线预览部分如存在完整性等问题,可反馈申请退款(可完整预览的文档不适用该条件!)。
- 3、如文档侵犯您的权益,请联系客服反馈,我们会尽快为您处理(人工客服工作时间:9:00-18:30)。
52
完整版ppt
53
完整版ppt
54
完整版ppt
55
完整版ppt
56
完整版ppt
57
完整版ppt
58
完整版ppt
59
此课件下载可自行编辑修改,供参考! 感谢您的支持,我们努力做得更好!
35
完整版ppt
36
完整版ppt
37
完整版ppt
38
完整版ppt
39
完整版ppt
40
完整版ppt
41
完整版ppt
42
完整版ppt
43
完整版ppt
44
完整版ppt
45
完整版ppt
46
完整版ppt
47
完整版ppt
48
完整版ppt
49
完整版ppt
50
完整版ppt
51
完整版ppt
18
完整版ppt
19
完整版ppt
20
完整版ppt
21
完整版ppt
22
完整版ppt
23
完整版ppt
24
完整版ppt
25
完整版ppt
26
完整版ppt
27
完整版ppt
28
完整版ppt
29
完整版ppt
30
完整版ppt
31
完整版ppt
32
完整版ppt
33
完整版ppt
34
完整版ppt
完整版ppt
1
完整版ppt
2
完整版ppt
3
完整版ppt
4
完整版ppt
5
完整版ppt
6
完整版ppt
完整版ppt
8
完整版ppt
9
完整版ppt
10
完整版ppt
11
完整版ppt
12
完整版ppt
13
完整版ppt
14
完整版ppt
15
完整版ppt
16
完整版ppt
17
完整版ppt