高速钢轧辊爆槽原因分析及控制
轧辊爆裂原因

轧辊爆裂是轧制生产中常见的一种失效形式,可能会导致严重的生产事故和经济损失。
以下是几种可能导致轧辊爆裂的原因:
1. 轧辊材质不适:轧辊材质应该具有高的强度、韧性和耐磨性。
如果材料不符合轧辊的使用要求,则会引起轧辊疲劳失效和裂纹扩展,导致轧辊爆裂。
2. 轧辊表面缺陷:轧辊表面缺陷、裂纹、凹坑等缺陷也可能导致爆裂。
这些缺陷将在轧制过程中扩展并使轧辊破裂。
3. 轧辊使用过程中温度过高:过高的轧辊表面温度会使轧辊产生变形和热疲劳裂纹,最终导致轧辊爆裂。
4. 轧辊使用寿命过长:轧辊在使用过程中会不可避免地出现疲劳损伤和磨损,长期使用可能导致轧辊的强度减小,出现裂纹和爆裂。
5. 非正常操作:轧辊在使用过程中需要严格遵循规定的操作程序和参数范围。
如果操作不当,例如过多受力或者运转速度过快,就有可能导致轧辊疲劳损伤和爆裂。
综上所述,预防轧辊爆裂需要严格控制轧辊的材质、缺陷、温度、使用寿命和操作规范,定期检测和维修轧辊以及合理调整轧制过程参数等措施。
高速钢轧辊

【原创】高速钢轧辊的性能与应用作者: xucz 发布日期: 2009-04-08 13:46轧辊是钢铁材料生产中的重要构件,而其本身材质开发与应用也十分重要,在此简要概述一下高速钢辊材的发展与应用,抛砖引玉,请大家讨论!1,应用现状轧制过程自动化、连续化、重型化是现代轧制技术的发展方向。
近年来,随着我国汽车、家电、铁路、桥梁、建筑业的快速发展,推动了轧钢工业的迅速发展,对轧材的尺寸精度、表面质量、使用性能也提出了更高的要求,促进了轧制技术的进步,轧辊的工作环境越来越苛刻,轧辊的使用性能要求也越来越高。
如何提高轧辊的使用性能以适应轧钢的需求是轧辊工作者面临的新课题。
上世纪末,高速钢复合轧辊工业应用已经取得成功,高速钢复合轧辊是将工作层和芯部以熔铸方式复合起来的高性能轧辊,工作层具有高硬度、高耐磨性和优异的抗热裂纹性能。
采用锻钢、铸钢或球墨铸铁作为轧辊芯部材料具有较高的强韧性。
高速钢复合轧辊充分发挥了两种材料的性能优势,使用寿命比高铬铸铁轧辊提高3倍以上。
目前,高速钢轧辊主要应用于热轧精轧前段机架,并逐步向后段机架推广,有可能在未来十年内完全取代高铬铸铁轧辊。
高速钢轧辊的使用可以减少换辊次数、降低辊耗和周转量,还可以提高轧制精度、实现无规程轧制,具有广阔的应用前景。
1988年日本首先开始采用高速钢轧辊,美国在90年代初开始引入高速钢轧辊,欧洲起步相对较晚但发展很快,我国大型高速钢复合轧辊还处于研制阶段,关键生产工艺尚未成熟,高速钢复合轧辊的使用也仅限于宝钢等几家大型钢铁企业。
开展高速钢轧辊的制造和使用技术研究,可以为新型高速钢轧辊的推广应用奠定基础,因而具有十分重要的实用价值。
未完,待续......相关回复:作者: xucz 发布日期: 2009-04-08 14:05热轧工作辊的工况条件非常复杂,承受剧烈的机械负荷、热负荷和冷却水的循环作用,因而存在多种损伤形式。
热轧工作辊承受的基本应力可分为三类:1). 机械应力:即在轧制过程中,由轧制载荷而产生的直接剪应力、弯曲应力和为了驱动轧辊克服轧制摩擦力所必需的转矩而产生的扭转剪切应力,尤其是在咬钢和抛钢瞬时产生的机械冲击负荷,加剧了机械应力的作用。
冷轧生产企业轧辊缺陷产生原因及防范措施

冷轧生产企业轧辊缺陷产生原因及防范措施轧辊是轧钢生产中的一种大型工具,其性能与质量将直接影响轧机产量和产品质量,其消耗在轧钢生产中占很大比例。
因此,轧辊的使用与管理在冷轧的生产中至关重要。
本文所列舉的冷连轧机为四机架六辊UCM(Universal Crown Mill)轧机,设计产量为152.8万t,其技术从国外成套引进,是目前国内装备水平较高的冷轧机之一。
自投产以后,多次与国内外的轧辊专家进行了技术交流,以提高轧辊的使用和管理水平。
研究冷轧辊缺陷产生的原因,并采取相应的具体措施,以便降低轧辊消耗,对降低成本和稳定生产有着重要的意义。
1冷轧辊缺陷的主要形式当前我们所使用轧辊来自于日立金属、美国电钢、英国轧辊、中国一重、邢台轧辊和常冶轧辊等几家轧辊生产制造厂,其材质为3Cr,5Cr和4CrMo锻钢。
目前出现的轧辊缺陷按照所产生的形态可以分成软点、剥落(爆辊)和内部裂纹等三大类。
1·1 轧辊软点轧辊表面的某些地方会显示出比轧辊表面其它地方硬度值变化较大情况。
通常这些软点区域的硬度值要比基体材料的硬度低20HS。
一般情况下软点区域用肉眼是分辨不出来的,但是经过硝酸酒精腐蚀以后,就会显示出来,呈现一片暗色区域(见图1所示)。
在某些情况下,软点疵瑕也可以保持有硬化情况和回火色(兰色/棕色)。
1·2 轧辊剥落轧辊剥落就是指轧辊辊身的某个区域从辊身上分离出来的现象。
剥落按照产生的原因不同可分成下述几类。
1.2.1 轧辊表面剥落轧辊表面剥落可通过裂纹表面的“破损”轨迹来鉴别。
这种疲劳“破损”轨迹的显著特征是具有典型疲劳痕(海滩纹见图2所示)或在疲劳裂纹面上的“扇形”裂纹流线。
疲劳“破损”轨迹蔓延的方向与轧制时轧辊旋转的方向相反。
1.2.2 接触应力引发的剥落由于轧机的负荷以及轧辊在接触点上的局部挤压,造成的最大组合剪切应力(通常称作“赫兹应力”)位于轧辊表面之下的某个较小区域中。
多处的裂纹可以引发并在赫兹应力超过轧辊的抗拉强度时,在表面之下位置发生弥散,导致剥落的产生,这会通过两种模式发生。
轧辊失效方式及其原因分析

轧辊失效方式及其原因分析轧机在轧制生产过程中,轧辊处于复杂的应力状态。
热轧机轧辊的工作环境更为恶劣:轧辊与轧件接触加热、轧辊水冷引起的周期性热应力,轧制负荷引起的接触应力、剪切应力以及残余应力等。
如轧辊的选材、设计、制作工艺等不合理,或轧制时卡钢等造成局部发热引起热冲击等,都易使轧辊失效。
轧辊失效主要有剥落、断裂、裂纹等形式。
任何一种失效形式都会直接导致轧辊使用寿命缩短。
因此有必要结合轧辊的失效形式,探究其产生的原因,找出延长轧辊使用寿命的有效途径。
1 、轧辊剥落(掉肉)轧辊剥落为首要的损坏形式,现场调查亦表明,剥落是轧辊损坏,甚至早期报废的主要原因。
轧制中局部过载和升温,使带钢焊合在轧辊表面,产生于次表层的裂纹沿径向扩展进入硬化层并多方向分枝扩展,该裂纹在逆向轧制条件下即造成剥落。
1.1 支撑辊辊面剥落支撑辊剥落大多位于轧辊两端,沿圆周方向扩展,在宽度上呈块状或大块片状剥落,剥落坑表面较平整。
支撑辊和工作辊接触可看作两平行圆柱体的接触,在纯滚动情况下,接触处的接触应力为三向压应力。
在离接触表面深度为 0.786b 处 ( b 为接触面宽度之半 ) 剪切应力最大,随着表层摩擦力的增大而移向表层。
疲劳裂纹并不是发生在剪应力最大处,而是更接近于表面,即在 Z 为 0.5b 的交变剪应力层处。
该处剪应力平行于轧辊表面,据剪应力互等定理,与表面垂直的方向同样存在大小相等的剪应力。
此力随轧辊的转动而发生大小和方向的改变,是造成接触疲劳的根源。
周期交变的剪切应力是轧辊损坏最常见的致因。
在交变剪切应力作用下,反复变形使材料局部弱化,达到疲劳极限时,出现裂纹。
另外,轧辊制造工艺造成的材质不均匀和微型缺陷的存在,亦有助于裂纹的产生。
若表面冷硬层厚度不均,芯部强度过低,过渡区组织性能变化太大,在接触应力的作用下,疲劳裂纹就可能在硬化过渡层起源并沿表面向平行方向扩展,而形成表层压碎剥落。
支撑辊剥落只是位于辊身边部两端,而非沿辊身全长,这是由支撑辊的磨损型式决定的。
高线精轧机组成品辊环爆辊原因分析及控制措施

2019年第4期1前言首钢水钢钢轧事业部高线作业区为全连轧高速线材生产线,设计能力为年产50万t/年,全线由6架粗轧机(平立轧机布置),6架中轧机(平立轧机布置),6架预精轧机(平立轧机布置,后四架为285悬臂辊环紧凑型机组)和10架精轧机(顶交45°轧机)组成,共28道次。
轧件依次进入各机组,全轧线为无扭连续轧制。
在预精轧机组前后及预精轧机组各机架间共设有7个活套装置,用于保证轧件的无张力轧制,以提高产品的尺寸精度。
精轧机组为顶交45°无扭轧机,10架轧机集体传动,采用碳化钨辊环。
在精轧机组内轧件为微张力无扭轧制。
2019年6月份以来,高线在轧制8mm、10mm 规格时频繁发生成品机架辊环爆辊,造成辊环的不正常消耗,严重影响正常生产,同时也带来生产成本的上升。
钢轧事业部决定对高线成品机架辊环冷却进行改进,确保辊环冷却均匀避免爆辊事故发生。
2辊环特性高速线材精轧机组采用的轧辊辊环是碳化钨为主的硬质合金辊环,碳化钨硬质合金辊环由于具有良好的热传导性能,在高温下硬度下降作者简介:李勇,(1978~),男,轧钢助理工程师,从事轧钢技术工作。
高线精轧机组成品辊环爆辊原因分析及控制措施李勇蒙世东胡友红王海益吴俊(首钢水钢钢轧事业部贵州六盘水553028)摘要:本文针对水钢高线轧制各规格成品机架辊环出现爆辊进行探讨分析,采取改进辊环冷却效果进行实践生产,解决成品机架辊环爆辊,提高轧机作业率、降低工人劳动强度。
关键词:碳化钨辊环;爆辊;辊环冷却装置;轧机生产率Cause Analysis and Preventive Measure of Finished-Product Roller GrooveOutburst in High-Speed Finishing Rolling Mill GroupLi Yong Meng Shidong Hu Youhong Wang Haiyi Wu Jun(Industrial Department of Steelmaking and Steel Rolling,Shougang Shuicheng Iron &Steel (Group)Co.,Ltd.,Liupanshui 553028,Guizhou,China)Abstract:The causes of finished-product roller groove outburst in high-speed finishing rolling mill group in Shuigang are investigated and analyzed,the measure to improve cooling effect of roller groove is put into practice to prevent roller groove outburst in finished mill stand and improve effi⁃ciency of rolling mill and reduce labor intensity of workers.Keywords:tungsten carbide roller groove;roller groove outburst;cooling device of roller groove;pro⁃ductivity of rolling mill高线精轧机组成品辊环爆辊原因分析及控制措施11··水钢科技SHUIGANG SCIENCE&TECHNOLOGY第150期图1辊环爆辊示意图少,耐热疲劳性能好,耐磨性好,强度高等特点。
锻钢轧辊缺陷产生的原因及对策

锻钢轧辊在轧制中出现问题的原因及对策目录页数1. 引言 42. 轧辊表面迹象A. 夹杂5~6B. 橘皮状轧辊表面7~8C. 辊印9~12D. 软点13~18E. 热裂纹i. 热轧机工作辊19ii. 冷轧机工作辊20~273. 剥落A. 表面迹像28~46B. 表皮下引发i. 与材质有关47~49ii. 接触应力a. 一般机理50~52b. 冷轧机工作辊53~61c. 热轧机工作辊62~64d. 支撑辊65~704. 辊颈断裂A. 表面迹像71~72i. 辊颈应力计算73~77B. 表皮下引发i. 轧辊设计或材料质量78~81C. 辊颈修复82~85D. 瞬时发生i. 深置缺陷86~87ii. 轧机过载88~905. 辊身断裂A. 疲劳--- 深置缺陷91~93B. 瞬时i. 轧机过载94~95ii. 深置缺陷96~976. 轧辊检测98A. 涡流探伤99~100B. 表面波超声波探伤101~105C. 着色渗入探伤106~108D. 刻蚀探伤109~111E. 磁粉探伤112~113F. 硬度检验114~1187. 轧辊处理和储存1198. 轧辊各部位的英文名称120~121引言在轧钢生产中的轧辊性能及质量直接影响轧机产量和产品质量。
因为轧辊采购费用在轧钢厂生产成本中占有较大比重,也是影响轧制成本的重要因素。
本书的目的是针对锻钢轧辊在轧制中可能出现的相关问题,并就问题的类型,特徵,样例(照片,图解),产生机理及预防措施等进行分析。
仅供有关人员参考。
锻造轧辊的无损探伤(NTD)对轧辊生产厂家和轧辊用户都非常重要。
轧辊生产厂家在轧辊热处理以及随后的精加工之前用NDT无损探伤,来确认轧辊的表面和内部是否合格。
轧辊用户(轧辊车间)利用NDT无损探伤确保研磨切削部分满足进一步使用之前的轧辊表面要求。
NDT 无损探伤以及其应用,可以作为最佳化轧辊维护过程的管理方法之一。
轧辊的处理和储存也是轧辊问题发生的因素。
万能轧机轧辊轴向窜动分析与控制

万能轧机轧辊轴向窜动分析与控制随着高速铁路的迅速发展,重轨产品的质量要求越来越高,部分尺寸已达到板带材精度的要求。
本文结合万能轧机生产重轨时出现的轧辊轴向窜动进行了影响分析、窜动值测量、原因分析及控制实施。
标签:万能轧机;轧辊轴向窜动;分析控制1、前言轧辊与两端的轴承座连接在一起,上机后上辊在轴承座内无法移动,而下辊可通过轴向调整装置实现轴向窜动。
本文所述方法对轧辊轴向窜动进行了较好的控制,轧辊轴向窜动由4-5mm减少到1mm左右,大幅度降低了轧机轴向窜动值。
2、轧辊轴向窜动现状分析2.1軋辊轴向固定与磨损轧辊与两端的轴承座连接在一起,上机后上辊在轴承座内无法移动,而下辊可通过轴向调整装置实现轴向窜动。
使用中轴承座、轴承及轧辊连接紧密,轧辊相对于轴承的轴向窜动小,在轴承使用后期在0.3mm以内。
2.2轴向窜动的调整万能轧机采用四辊轧制,与普通轧制相比,控制难度较大,辊缝调整要求沿轧制中心线对中调整。
在空载情况下,辊缝调零的目的就是确定机械的参照点,亦即上、下水平辊和左、右立辊辊缝压靠,此时上、下水平辊轴向位置作为液压动态轴向控制的基准,上、下轴承座均与上、下水平辊相连。
上下水平辊、左右立辊均采用电气传动控制。
轴向位置采用液压伺服阀控制。
动态轧制过程中,势必造成上、下辊轴向产生位移,为此系统采用保持板FC缸、增压缸相互配合来保证上下水平辊的轴向位置。
动态轴向位置控制是以上辊轴向位置为基准,通过对下辊的轴向位置控制来完成动态的调整过程。
控制系统由2台PLC控制,其中一台控制液压平衡、伺服阀电源OK、位置传感器、伺服阀的电流信号采集、液压压力采集、液压缸位置行程编码器、动态轴向偏差值计算、保持板(FC)基准值计算及增压缸控制基准值计算等。
另一台PLC则进行液压位置控制。
2.3轴向窜动值测量2.3.1静态测量静态测量是指换完辊并做完标定后用塞尺测量耐磨板3、耐磨板4的间隙。
此时轧机没有轧件通过,不存在轴向力,立辊标定力(500KN)只起定位作用,也会消除轧机各部位连接间隙,用塞尺测出的间隙值小于均0.1毫米。
减定径机爆辊原因分析Word版

减定径机爆辊原因分析和控制措施摘要:针对碳化钨辊环的特征和裂辊爆辊的现象,分析了高速线材减定径机辊环在生产过程中发生爆辊的主要原因:辊环装配不当、导卫、辊缝、辊环材质以及冷却条件不好等,从而提出了解决措施。
关键词:碳化钨辊环爆辊控制措施减定径机高速线材1 前言武钢高速线材自2006年改造后,为了提高产品表面质量和尺寸精度,双线增加了减定径机组。
投产几年以来,由于各方面的原因,在生产过程中经常出现辊环裂,爆辊等生产事故现象,主要集中在减定径机组上,爆辊,裂辊事故频繁发生。
造成辊环的不正常消耗,严重影响正常生产,同时也带来生产成本的上升。
2 辊环特性高速线材减定径机采用的轧辊辊环是碳化钨为主的硬质合金辊环,碳化钨硬质合金辊环由于具有良好的热传导性能,在高温下硬度下降少,耐热疲劳性能好,耐磨性好,强度高等特点:(1)、硬度高、耐磨性好常温下硬度可HRA78~95,高温下的红硬性好,600℃时超过高速钢,1000℃时超过碳钢的常温硬度值。
(2)、机械强度高抗压强度可高达6000MN/m2,900℃时抗弯强度仍可有1000MN/m2以上。
(3)、弹性模数高常温下刚性较好,无明显的塑性变形。
其杨氏模量为钢的2-3倍。
(4)、耐腐蚀性和抗氧化性好耐酸、耐碱,600~800℃时不发生明显氧化。
(5)、线胀系数小在20~400℃的范围内为钢的0.35~0.65。
(6)、电导率与铁、铁合金相近(7)、热传导率为钢的1/2,铜的1/3。
(8)、密度高硬质合金辊环的密度远大于钢铁,应用于轧钢领域的硬质合金辊环的粘结剂含量在6%~32%,密度大约在12.6~14.9 g/cm3之间。
3 辊环裂辊爆辊现象(1)辊环的裂辊,在生产过程中有两种现象,一种是环状断裂(见图1),另一种是径向断裂(见图2)。
环状断裂时,裂纹发生在轴环孔槽的槽底,并沿着轧槽成环状;径向断裂时,辊环裂纹沿径向呈放射状。
据经验,在生产实践中,超额定轧制量轧制后若裂纹修磨不干净容易发生环裂,冷却效果差时容易发生径向断裂。
高线辊环槽裂及辊环破碎原因分析及防止措施

3
上述影响因素均可导致辊环出现裂纹或辊 环 � 精轧机成品机架, 1 20 0 � 20 0 0 � 碎, 单一因素或者是几种因素相互作用后产生裂纹 � (5) 制定辊环安装压力� 经多次测试, 对每个机 通过辊环拉环的原因分析, 制定了一些措施: 架的辊环安排压力进行测试, 找出最优的压力值, 在 (1) 制定下线辊环登记制度, 返修要求� 对辊环 安装时执行规定压力, 防止安装过紧或过松 � 辊环安 是正常下线还是堆钢 � 裂纹等非正常下线进行登记 � 并根据不同下线情况, 制定不同的车削量, 将非正常 下线的微裂纹车削干净,同时辊环检验由原来的一 次检验改为初检和复检两次,并制定辊环检验要求 及登记办法,同时在生产班辊环摆放处增加一套样 板� 制定辊环非正常报废的标准, 对破损大, 损坏严 重一定程度的辊环, 直接报废处理 � (2) 设定导卫顶丝装置 (见图 1) , 在导卫上面加 装螺栓和螺母, 导卫安装上去以后, 将螺栓顶在辊环 前的水分配器上, 即使在正常轧制过程中, 导卫底座 螺母有松动现象,导卫也不会在红条的摩擦力带动 下和辊环发生滑动接触� (3 ) 规范辊环冷却水的操作� 通过现场对水压的 测试, 对下线以后辊环温度高低, 轧槽磨损情况, 找 出最合理的水的压力值在 6 k g, 水的 pH 小于 7 .2 , 冷 却水的水量应控制在 250 � 30 0 l/ m i n; 辊环使用效果 较匀,对水分配器周期更换 � 冷却水的压力 0 .4 � 0. 6MPa ; 冷却水喷水方向为径向, 与辊环旋转方向成 1 5�� 30 �角度, 水不能散射或呈雾状, 应直接喷入 50 装时, 锥套与辊环内孔一定要配合适当, 不能过紧或 松动 � 轧制时温度升高, 硬质合金辊环的热膨胀系数 极小, 而钢制锥套的热膨胀系数则较大, 钢体热膨胀 系数约为硬质合金的两倍,辊环内孔将受到钢套热 膨胀产生的张力作用, 因此, 此二者之间的装配需要 严格而适当的配合量� 在高速线材轧制生产中, 辊环 与锥套较好的配合量为 0 . 0 1 �0 .0 3m m � 通常而言,精轧前架钢坯尺寸波动大,表面粗 糙, 轧制剪径面积大, 因此, 要求辊环有高的强度和 冲击韧性 �与此相反,精轧末架上的钢坯尺寸波动 小, 表面状况好转, 剪径面积小, 因此对辊环的强度 要求降低, 但由于接近成品或出成品, 因此要求辊环 有较高的耐磨性和抗热龟裂性, 以此保证棒 � 线材有 良好的尺寸公差和表面光洁度� 精轧中间架次的情 况介于上述之间� 同时, 应该同牌号� 同厂家辊环配 对使用,防止因动平衡问题引起的设备振动而造成 的爆辊环事故 �
高线炸辊原因分析与控制
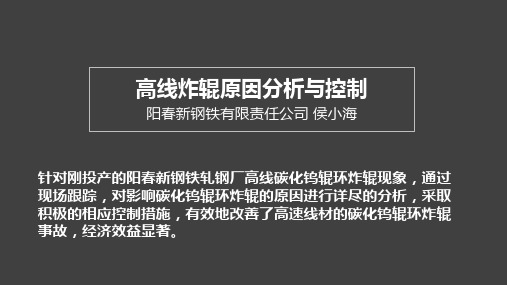
出于优化成本的考虑,辊环采用的是硬质合金碳化钨。通过对辊环炸辊现场进行分析 后,得出原因如下:
1) 由于广东阳春多湿雨,现场环境比较潮湿,辊环和锥套暴露在空气中受湿气影响 锈蚀,造成辊环炸辊; 2) 轧制时轧槽表面任一点温度变化曲线见图1。从图1 看出,轧槽表面温度反复升降, 产生交变热应力和热疲劳裂纹,而且高温对轧槽表面有热腐蚀。为防止辊环破裂,延 缓微裂纹的扩展,延长辊环寿命,提高辊环冷却的效果非常重要。辊环冷却的效果不 良,辊环最高温度、辊环本体平均温度及温度差△T 将进一步提高,引起轧槽热裂纹与 热腐蚀扩展加快、降低轧增轧制量,甚至导致裂纹扩大,这是引起辊环炸辊的主要原 因; 3) 轧槽轧制到一定时间,微裂纹逐步扩大、延长和加深,最后造成辊环炸裂; 4) 辊环的装配没到位,造成辊环锥套与辊轴抱死,锥套损坏,辊环炸辊; 5) 辊环是一种脆性材料,重量又大,非常容易碰坏。
3.3 确定合理的轧制过钢量 一般来说,轧槽微裂纹达到0.2~04mm时就应进行下线修磨,这种裂纹深度被认 为是较安全的,这时的轧制量是较合适的,通常为下列范围:
1、2 架 3、4 架 5、6 架 7、8 架 9、10 架
1800~2500 吨 1800~2500 吨 1500~2000 吨 1500~2000 吨 600~1000 吨
轧制缺陷及质量控制
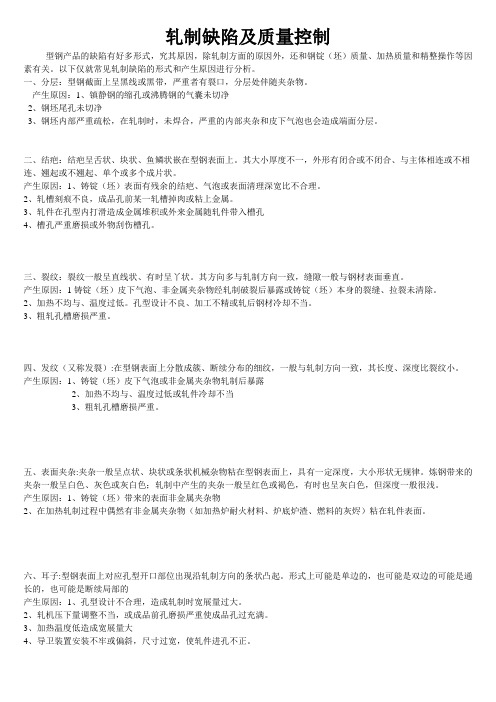
轧制缺陷及质量控制型钢产品的缺陷有好多形式,究其原因,除轧制方面的原因外,还和钢锭(坯)质量、加热质量和精整操作等因素有关。
以下仅就常见轧制缺陷的形式和产生原因进行分析。
一、分层:型钢截面上呈黑线或黑带,严重者有裂口,分层处伴随夹杂物。
产生原因:1、镇静钢的缩孔或沸腾钢的气囊未切净2、钢坯尾孔未切净3、钢坯内部严重疏松,在轧制时,未焊合,严重的内部夹杂和皮下气泡也会造成端面分层。
二、结疤:结疤呈舌状、块状、鱼鳞状嵌在型钢表面上。
其大小厚度不一,外形有闭合或不闭合、与主体相连或不相连、翘起或不翘起、单个或多个成片状。
产生原因:1、铸锭(坯)表面有残余的结疤、气泡或表面清理深宽比不合理。
2、轧槽刻痕不良,成品孔前某一轧槽掉肉或粘上金属。
3、轧件在孔型内打滑造成金属堆积或外来金属随轧件带入槽孔4、槽孔严重磨损或外物刮伤槽孔。
三、裂纹:裂纹一般呈直线状、有时呈丫状。
其方向多与轧制方向一致,缝隙一般与钢材表面垂直。
产生原因:1铸锭(坯)皮下气泡、非金属夹杂物经轧制破裂后暴露或铸锭(坯)本身的裂缝、拉裂未清除。
2、加热不均与、温度过低。
孔型设计不良、加工不精或轧后钢材冷却不当。
3、粗轧孔槽磨损严重。
四、发纹(又称发裂):在型钢表面上分散成簇、断续分布的细纹,一般与轧制方向一致,其长度、深度比裂纹小。
产生原因:1、铸锭(坯)皮下气泡或非金属夹杂物轧制后暴露2、加热不均与、温度过低或轧件冷却不当3、粗轧孔槽磨损严重。
五、表面夹杂:夹杂一般呈点状、块状或条状机械杂物粘在型钢表面上,具有一定深度,大小形状无规律。
炼钢带来的夹杂一般呈白色、灰色或灰白色;轧制中产生的夹杂一般呈红色或褐色,有时也呈灰白色,但深度一般很浅。
产生原因:1、铸锭(坯)带来的表面非金属夹杂物2、在加热轧制过程中偶然有非金属夹杂物(如加热炉耐火材料、炉底炉渣、燃料的灰烬)粘在轧件表面。
六、耳子:型钢表面上对应孔型开口部位出现沿轧制方向的条状凸起。
轧辊铸造缺陷原因分析

辊面夹渣.、针孔
1外层出铁温度、浇注温度不合理;
2炉内、铁水包内的垃圾处理不干净;
3铁水包没烘干,铁水内夹气严重;
4孕育、球化处理后立刻浇注,作用不充分,铁水镇定时间太短;
5浇注外层时,开浇速度过慢,表层铁水凝固过快,垃圾不能及时往里浮出。
1外层用浇注系统修复不及时或没烘干,降低铁水进入型腔温度,并夹带进部分垃圾及气体;
4离心机开机不及时,开始浇注外层时离心速度未达到,浇注在加速中进行,使得表面一层组织致密性差,组织形态不好,合金碳化物分部不均(底)
5浇注时离心机震动大或冷型窜动大
6调整成分后未经一定时间一定温度的熔炼就出铁,使得部分合金还来不及熔化,
成份设定不合理,原材料质量不稳定。
7
合金层厚或薄
(冲偏)
1填芯铁水温度过低或过高;(厚、薄)
1成分控制不严,硬度过高;
2离心机振动剧烈;
3原材料质量差。
14
结合不良
1离心机离心时间或停转到填芯间隔时间过长
2冲芯温度偏底
冲芯浇斗出铁出铁口尺寸偏小
2配箱底箱冒口或者冷型用错
1冷圈选用错误;
2有歪头颈缺陷;
3底箱、冒口张冠李戴。
1选用不合理的工装模具,型样模具残缺或损坏严重;
2冒口底箱修复不及时,或重复使用次数过多,精确度降低。
工艺不合理。
13
辊身裂纹
1外层浇注温度过高,缩率大;
2开浇速度慢,有滴铁现象,辊面常伴有“疤块”。
3离心时间(外层)过长,形成热裂纹。
4铁水在炉内经高温时间太长,铁水氧化严重,吸氢或吸氧量大
5严禁在浇注外层过程中用吹风机向冷型中吹风
6浇辊环冲芯时未换浇注系统,在铁水冲击下把富着在浇注系统里的铁,渣等带入铁水中造成夹渣
轧制缺陷及质量控制
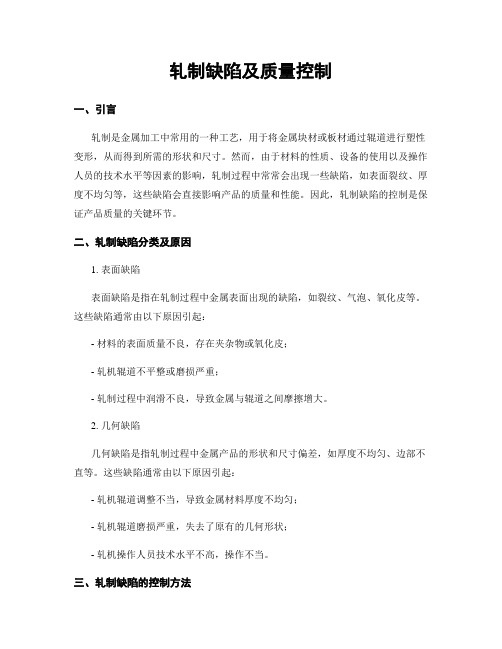
轧制缺陷及质量控制一、引言轧制是金属加工中常用的一种工艺,用于将金属块材或板材通过辊道进行塑性变形,从而得到所需的形状和尺寸。
然而,由于材料的性质、设备的使用以及操作人员的技术水平等因素的影响,轧制过程中常常会出现一些缺陷,如表面裂纹、厚度不均匀等,这些缺陷会直接影响产品的质量和性能。
因此,轧制缺陷的控制是保证产品质量的关键环节。
二、轧制缺陷分类及原因1. 表面缺陷表面缺陷是指在轧制过程中金属表面出现的缺陷,如裂纹、气泡、氧化皮等。
这些缺陷通常由以下原因引起:- 材料的表面质量不良,存在夹杂物或氧化皮;- 轧机辊道不平整或磨损严重;- 轧制过程中润滑不良,导致金属与辊道之间摩擦增大。
2. 几何缺陷几何缺陷是指轧制过程中金属产品的形状和尺寸偏差,如厚度不均匀、边部不直等。
这些缺陷通常由以下原因引起:- 轧机辊道调整不当,导致金属材料厚度不均匀;- 轧机辊道磨损严重,失去了原有的几何形状;- 轧机操作人员技术水平不高,操作不当。
三、轧制缺陷的控制方法为了控制轧制过程中的缺陷,提高产品的质量和性能,可以采取以下措施:1. 材料预处理在轧制之前,对原材料进行预处理是非常重要的。
首先,对材料的表面进行清洁,去除氧化皮和夹杂物。
其次,对材料进行退火处理,以提高其塑性和可加工性。
最后,对材料进行表面润滑处理,减少与辊道的摩擦。
2. 轧机设备维护保持轧机设备的良好状态对于控制缺陷至关重要。
定期检查和维护轧机辊道,确保其平整度和几何形状的精确性。
同时,及时更换磨损严重的辊道,以保证轧制过程的稳定性和一致性。
3. 润滑控制在轧制过程中,适当的润滑是减少摩擦、防止表面缺陷的关键。
选择合适的润滑剂,并确保润滑剂的供应充足、均匀。
同时,及时清洗辊道和润滑系统,避免杂质对产品质量的影响。
4. 操作人员培训轧制过程需要经验丰富的操作人员进行操作和监控。
因此,对轧机操作人员进行培训,提高其技术水平和操作规范性是非常重要的。
操作人员应熟悉轧机设备的使用方法和调整技巧,能够及时发现和解决轧制过程中的问题。
高速钢轧辊的特征及使用技术要求

高速钢轧辊的特征及使用技术要求目前人们所称的高速钢轧辊均为高碳高速钢复合轧辊,即轧辊的工作层材料采用高碳高速钢,轧辊的芯部材料采用球墨铸铁、石墨钢或锻钢等,两种不同的材料通过离心铸造或者是采用CPC工艺复合而成,与传统的M2、M4等标准类型钨钼高速钢有着本质上的区别。
在正常的轧制条件下,高速钢轧辊的使用寿命是合金铸铁轧辊3倍以上。
一、高速钢轧辊的特点1、高速钢轧辊含碳量较高,而且含有较高的钒、铬、钨、钼、铌等合金元素,因此,轧辊组织中碳化物的类型以MC型和M2C型为主,碳化物硬度高、耐磨性好。
2、高速钢轧辊具有较好的热稳定性,在轧制温度下,辊面具有较高的硬度和良好的耐磨性。
3、高速钢轧辊具有良好的淬透性,从辊身表面到工作层内部的硬度几乎不降,从而确保轧辊从外到内具有同等良好的耐磨性。
4、轧辊使用过程中,在良好的冷却条件下,辊身表面形成薄而致密的氧化膜,这种均匀、薄而致密的氧化膜长时间存在而不脱落,使得高速钢轧辊耐磨性得到显著提高。
5、高速钢轧辊在轧制时辊面氧化膜的形成,降低了轧材与辊面间的磨擦,因此在轧制过程中易引起打滑现象,使轧机调整难度增加。
6、高速钢材料膨胀系数大,导热性能好,在轧制时易引起辊形变化,影响轧材精度。
因此,高速钢轧辊在板带材轧机上使用时,不仅要改变冷却系统的设计,而且还要重新改变辊形的设计。
7、由于高速钢轧辊芯部采用合金球墨铸铁、石墨钢或者是锻钢等材料制成,因此轧辊辊颈强度高。
8、由于高速钢材料耐磨性好、抗事故能力差,因此高速钢轧辊使用效果的好坏不仅取决于高速钢轧辊本身的质量,而且更重要取决于轧辊的使用条件和轧辊的维护保养。
二、高速钢轧辊的加工轧辊的硬度提高后,轧辊的加工难度相应就增加,对用于线、棒材轧机高速钢轧辊的孔型加工,特别是轧制螺纹钢轧辊在重复使用时的切削加工,由于是断续切削,其加工难度更大,因此选用合理的加工刀具和切削用量是决定高速钢轧辊能否在线棒材轧机上正常使用的先决条件。
高速钢轧辊热处理断裂原因分析
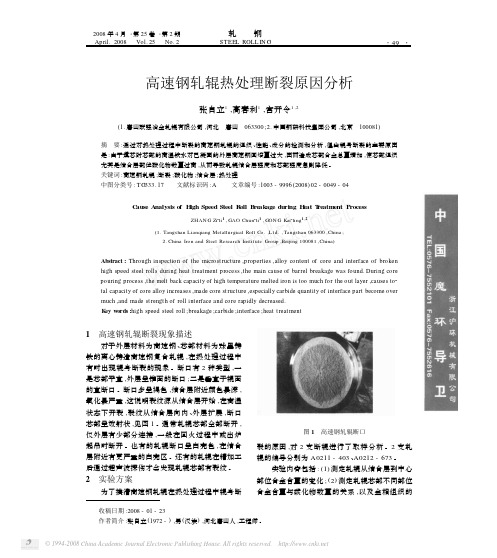
收稿日期 :2008 - 01 - 23 作者简介 :张自立 (1972 - ) ,男 (汉族) ,河北唐山人 ,工程师 。
© 1994-2008 China Academic Journal Electronic Publishing House. All rights reserved.
2008 年 4 月 Ap ril. 2008
·第 25 Vol.
卷 25
·第 2 No
期 .2
S
轧 钢
TEEL ROLL IN
G
· 4 9 ·
高速钢轧辊热处理断裂原因分析
张自立1 ,高春利1 ,宫开令1 ,2
(1. 唐山联强冶金轧辊有限公司 ,河北 唐山 063300 ;2. 中国钢研科技集团公司 ,北京 100081)
1 - Cr ;2 - Mo ;3 - V ;4 - W
图 4 A0211 - 403 轧辊从结合层至中心不同部位碳化物的数量及形态
a) 结合层处 ,碳化物量 33 % ;b) 距结合层 15mm 处 ,碳化物量 12. 64 % ;c) 距结合层 32mm 处 ,碳化
物量 10. 31 % ;d) 距结合层 51mm 处 ,碳化物量 13. 14 % ;e) 距结合层 66mm 处 ,碳化物量 7. 81 % ;
1 高速钢轧辊断裂现象描述
对于外层材料为高速钢 、芯部材料为球墨铸 铁的离心铸造高速钢复合轧辊 ,在热处理过程中 有时出现辊身断裂的现象 。断口有 2 种类型 ,一 是芯部平直 ,外层呈锥面的断口 ;二是垂直于辊面 的直断口 。断口多呈褐色 ,结合层附近颜色最深 , 氧化最严重 ,这说明裂纹源从结合层开始 ,在高温 状态下开裂 ,裂纹从结合层向内 、外层扩展 ,断口 芯部呈放射状 ,见图 1 。通常轧辊芯部全部断开 , 仅外层有少部分连接 ,一般在回火过程中或出炉 起吊时断开 。也有的轧辊断口呈白亮色 ,在结合 层附近有更严重的白亮区 。还有的轧辊在精加工 后通过超声波探伤才会发现轧辊芯部有裂纹 。
热轧轧辊剥落或断裂的原因及预防方法探究

热轧轧辊剥落或断裂的原因及预防方法探究【摘要】热轧轧辊剥落或断裂是热轧生产中常见的问题,严重影响生产效率和产品质量。
本文从热轧轧辊剥落或断裂现象引起注意和研究目的和意义两个方面展开,然后深入探讨了造成这一问题的原因,包括金属材料的质量问题、外部环境因素和工艺参数设置不当等。
针对这些原因,提出了一些有效的预防方法,如加强材料检验、保持良好的生产环境和合理设置工艺参数。
在研究成果总结和未来研究展望两个方面进行总结,指出今后需要深入研究轧辊剥落或断裂的原因及预防方法,以提高热轧生产的效率和质量。
通过本文的研究,有望为解决热轧轧辊剥落或断裂问题提供一定的参考和借鉴。
【关键词】热轧轧辊、剥落、断裂、金属材料、质量问题、外部环境、工艺参数、预防方法、研究成果、展望。
1. 引言1.1 热轧轧辊剥落或断裂现象引起注意热轧轧辊剥落或断裂是热轧生产中常见的问题,一旦发生会给生产带来严重的影响。
轧辊是热轧生产中不可或缺的重要设备之一,承担着对金属带材进行塑性加工的重要任务。
由于受到多种因素的影响,轧辊往往会出现剥落或断裂的现象,如果不及时处理和预防,将导致生产事故的发生,影响生产效率和产品质量。
热轧轧辊剥落或断裂现象需要引起注意,因为其主要危害包括:一是轧辊剥落或断裂会导致生产线停机,给企业带来直接的经济损失;二是剥落或断裂的轧辊会造成产品表面质量不达标,影响产品的销售和企业的声誉;三是轧辊剥落或断裂会增加生产中的安全隐患,可能导致事故发生,影响员工的生命安全。
对热轧轧辊剥落或断裂现象引起足够的重视,研究其发生的原因以及预防方法,对于提高生产效率、保证产品质量和保障人员安全具有重要意义。
本文旨在探究热轧轧辊剥落或断裂的原因及预防方法,为热轧生产提供一定的参考和指导。
1.2 研究目的和意义研究的目的在于深入探究热轧轧辊剥落或断裂的原因,分析其中可能存在的金属材料质量问题、外部环境因素以及工艺参数设置不当等方面的因素。
通过研究分析,可以为预防热轧轧辊剥落或断裂提供理论依据和技术支持,提高轧辊的使用寿命和生产效率。
轧制烧槽事故报告

轧制烧槽事故报告前言柳钢一高线于2003- 05建成投产,是由国内设计,关键设备国外进口的先进连轧线材生产线。
一高线全线共28架轧机,其中粗轧机组6架,中轧机组8架,预精轧机组 4 架,采用平立交替布置;精轧机组10 架,为Morgan V 型无扭机组。
全线采用单线无扭轧制,保证速度105m/s(轧制Φ5.5~7.5 mm),设计生产能力40 万吨/ 年,实际能力超过60万吨 / 年。
高线生产中,造成堆钢的因素很多,结合现场设备情况可划分为机械故障堆钢、电气故障堆钢、工艺故障堆钢3类。
按轧制过程可划分为轧件头部堆钢,中部和尾部堆钢。
按轧制区域分为粗中轧堆钢、飞剪堆钢、活套堆钢、水箱恢复段导槽堆钢、夹送辊吐丝机堆钢等等。
尽管划分方式不同,但堆钢的现象是相似的,原因或简单或复杂,呈多样性[1] 。
本文分析各轧制区域内产生堆钢事故的原因,总结处理措施。
2、堆钢及其处理2.1 、粗中轧2.1.1、轧件头部(1)坯料严重脱方或劈头,无法进入轧机或是把出口导卫顶出造成堆钢。
处理措施:加强炉前上料的检查,发现不合格坯料及时剔废,发现劈头要快速拍急停,减少处理时间。
(2)坯料出炉打滚翻身换面,头部出机架后(多在出 3 架或 5架后)走偏或带出导板不进下一机架而堆钢。
此为坯料加热不均匀,出现阴阳面,轧制应力方向改变造成的,因此,加热炉岗位人员要加强进出钢的工作,要求走钢到位,把钢坯加热均匀,适当提高钢坯头部温度。
(3)换辊换孔后,轧件头部打滑而堆钢。
此为辊缝值设定过小,咬入角过大或是对新孔打磨不够,咬入摩擦力过小造成的。
处理措施:用新孔时适当放大辊缝,用砂轮机仔细打磨轧槽;粗轧前几架次换孔时,可在该架次咬入前快速地在轧件头部撒沙子增加摩擦力,并且关掉该架次冷却水直到完全咬入。
(4)轧件尺寸过大,在进入下一道次机架时挤在进口导卫内而堆钢。
此时要测量轧件头部,根据尺寸重新设定辊缝。
(5)轧件头部出轧机后翘头不进下一机架或是顶导卫而堆钢。
- 1、下载文档前请自行甄别文档内容的完整性,平台不提供额外的编辑、内容补充、找答案等附加服务。
- 2、"仅部分预览"的文档,不可在线预览部分如存在完整性等问题,可反馈申请退款(可完整预览的文档不适用该条件!)。
- 3、如文档侵犯您的权益,请联系客服反馈,我们会尽快为您处理(人工客服工作时间:9:00-18:30)。
2)优化 K3、K4 切分楔。预切分处楔尖圆弧半径 一般设计为 1.4~2.0 mm,切分道次楔尖半径一般设 计为 0.6~0.9 mm,从设计角度出发,要求这两道次
1
135°
40
30
A向展开
1- 下轧辊;2- 进口导卫;3- 上轧辊;4- 进水管;5- 方管;6- 喷嘴; 7- 轧件;8- 出口导卫
作者简介:王建(1970—),男,现为山东钢铁股份有限公 司 莱 芜 公 公 司 棒 材 厂 工 程 师 , 从 事 管 理 工 作 。 Tel: 0634- 6823451,E- mail:xl_3102@
点就会产生爆裂(爆槽),形成事故[1]。 2.2 机械及摩擦应力产生的裂纹
轧制过程中,作用在轧辊上的机械应力主要包 括:由轧制载荷产生的直接剪应力、弯曲应力和为了 驱动轧辊克服轧制摩擦力所必需的转矩而产生的扭 转剪切应力、轧辊与轧件之间的相对滑动产生的摩 擦力[2]。轧件咬入和抛出瞬间产生的机械冲击负荷, 也会加剧机械应力的作用。生产实践过程中异常,如 冷却水使用不当或飞剪切头误差造成的“黑头钢”, 调整不当造成的低温轧边、低温拉丝或其他硬质杂 物,进入轧槽后都会产生剧烈的冲击载荷,极具破坏 性。高速钢轧辊虽然有较高的硬度和耐磨性,但韧性 和抗冲击能力较低,当机械应力裂纹达到一定极限, 极易引发轧槽爆裂事故。现场发现,机械应力裂纹无 明显分布特征,属于斜裂纹,一般逆轧制方向扩展且 扩展速度较快,一旦发生,很难控制。 3 控制措施 3.1 改善轧机浊环水水质
轧机系统冷却水直接与冷却设备接触,用后水 质较差,主要污染因子是悬浮物和 pH、废油等。水质 达不到要求会影响轧辊冷却效果,严重时在管道或 喷嘴内结垢堵塞,为此,棒材厂在原平流池加药自然 沉淀的基础上,增加了高效斜板化学除油器、污泥压 滤机等设备。轧机冷却回水汇入铁皮沟,自流入旋留 沉淀池,经初步沉淀后,提升至污水化学除油器,经 加药沉淀、除油、pH 值调整,自流入泵站热水井,用 冷却泵提升至冷却塔降温后,泵送到冷水井,再由循 环水泵送至浊环水用户。根据轧辊冷却对水质要求, 轧机浊环水水质应满足下页表 1 的要求。 3.2 水量、水压的要求
热轧工作辊实际工作时,往往同时承受热疲劳、 机械、摩擦等应力的综合作用,要想减少高速钢轧辊 爆槽事故的发生,必须综合考虑轧辊使用工况。上述 措施实施后,高速钢轧辊爆槽次数由原来的每月 4~5 次降到目前的不到一次,有效降低了工艺故 障,提高了生产效率及产品质量。
参考文献 [1] 符寒光,刑建东.高速钢轧辊制造技术[M].北京:冶金工业出
严格控制过钢量,防止轧辊的过度使用,带肋钢 筋 K1 辊单槽过钢量推荐 400~450 t、预切分辊 K4 辊 2 000~2 500 t,修复轧辊时确保轧槽边部、底部 裂纹全部车削掉,尤其槽口处不得有黑皮、细小裂 纹;严格安装出口导卫装置,不得造成导卫直接接触 轧槽;严格控制轧辊进口冷却水量,以减轻对轧件头 部激冷;加强生产过程中的动态监控,减少缠辊故 障,缠辊时,必须用冷却水将缠辊的废品全部冷却至 室温,才允许停水处理废钢。 4 结语
生产中轧辊冷却水压力应维持在 0.4~0.6 MPa
2012年第 3 期
王建:高速钢轧辊爆槽原因分析及控制
· 73 ·
表 1 轧机浊环水水质控制标准
参数
单位
控制值 参数 单位 控制值
pH
7~9 总铁 mg/L ≤1.0
3
浊度
NTU
<30 油分 mg/L ≤5
2
总硬度 mg/L(以 CaCO3 计) <500 氯离子 mg/L(以 Cl- 计) ≤400
1)增大轧槽中心距。为避免槽间爆裂,满足进口 导卫要求的情况下适度增大轧槽中心距。一般轧制 Φ10~Φ14 mm 带肋钢筋时,轧槽中心距由原来的 10 mm 增加到 15 mm,Φ16~Φ25 mm 轧槽中心距由 原来的 15 mm 增加到 20 mm,Φ25 mm 以上轧槽中心 距增加到 25 mm。同时加大槽口圆角,由原来 0.8 mm 加大到 1.2 mm,以此减轻应力的集中。
引起的,通过实施冷却水应用改进、工艺参数优化等措施,减少了爆槽事故的发生,提高了生产效率。
关键词:高速钢轧辊 爆槽 原因分析 控制措施
中图分类号:TG333.17
文献标识码:B
收稿日期:2012- 03- 19
山东钢铁股份有限公司莱芜公公司棒材厂现有 4 条钢筋生产线,年产建筑用螺纹钢、矿业锚杆钢、预应力 精轧螺纹等 270 万 t,为提高钢筋表面质量及生产效率, 2010 年起开始在精轧机组推广使用高碳高钒系列高速 钢轧辊,替代原来的高铬铸铁及无限冷硬球墨铸铁轧 辊。经使用对比,高速钢轧辊的耐磨性及耐表面粗糙性 明显优于普通轧辊,单槽过钢量可以提高 5~6 倍,轧材 表面质量、外形尺寸精度明显改善,轧辊的性价比较高。 但是,在原轧辊使用工况的环境下,发现成品槽 K1 及切 分、预切分槽 K3、K4 轧槽频繁出现爆槽现象,主要表现 为成品 K1 轧槽底部螺纹横肋掉块和两相邻轧槽中间辊 环崩裂,K3、K4 轧槽切分楔龟裂,造成生产事故及钢材 合格率下降,给生产及产品质量带来较大影响。为此,棒 材厂对高速钢轧辊使用工况、工艺参数等进行了全面优 化,以适应其自身特性,减少事故发生。 2 轧辊爆槽原因分析 2.1 疲劳热应力产生的裂纹
总第 137 期 2012 年第 3 期
文章编号:1672-1152(2012)03-0072-02
山西冶金 SHANXI METALLURGY
高速钢轧辊爆槽原因分析及控制
Total 137 No.3,2012
王建
(山东钢铁股份有限公司莱芜分公司棒材厂, 山东 莱芜 271104)
摘 要:系统分析了高速钢轧辊使用工况,明确了轧辊爆槽主要原因是由热疲劳、机械、摩擦等应力的综合作用
版社,2007. [2] 文铁铮,郭玉珍.冶金轧辊技术特性概论[M].石家庄:河北科
技技术出版社,1995.
(编辑:苗运平)
44
图 1 螺纹钢 K1 辊三切分冷却喷淋装置示意图
轧槽既要有较高的耐磨性,又要具有一定的韧性,否 则极易发生楔尖过度磨损或楔尖崩掉,因此,满足切 分要求的前提下,圆弧半径尽可能取上限值。
3)严格控制 K2 料型宽度与轧槽内径比值不超 过 1.7 倍。防止 K2 宽度过大,造成 K1 压下量过大, 造成金属流动快,在轧件反复作用下,导致轧槽出现 细丝状掉肉或形成周期性掉块。 3.5 严格工艺纪律
传统的轧槽冷却一般在轧件进口、出口两端上 下辊各设置一个冷却喷嘴,喷嘴的大小及喷射角度 较随意,不能做到标准化,致使轧槽冷却不均匀,轧 辊温度过高,经常因冷却问题造成轧槽爆裂。为保障 高速钢轧辊的冷却要求,避免热应力的急剧增加,根 据轧制规格对冷却水量的不同要求,专门设计了呈 环形分布的组合喷淋装置(见图 1)。采用不锈钢材 质,喷射水幕宽度超出轧槽槽口宽度 2~4 cm,喷射 水幕沿轧辊切线方向成 30°夹角,出口端环 1/2 轧 槽水量占总水量 70%,进口导卫冷却水尽量不要直 接喷淋到轧件上,防止造成黑头钢。靠近出口导卫处 为主喷嘴,水量为整个轧槽上总水量的 30%,保证把 冷却水喷到轧槽中刚刚脱离轧件的部位,目的是把 轧槽上的热量迅速置换,减少热应力的生成。由于下 辊的冷却条件比上辊差,因此在设计下辊的冷却喷 嘴时,计算总水量比上辊增加 10%~15%。 3.4 优化轧槽工艺参数
电导率 Us/cm <1500 细菌 个 /mL <1.0×105
50
A
30°
4
5 6 7
8 4
3LLຫໍສະໝຸດ 500Φ403
之间,根据不同的轧制规格及速度采用不同流量的 冷却喷嘴,轧制 Φ10~Φ50 mm 钢筋时,单槽冷却水 量一般控制在 300~500 L/min。根据环境温度变化, 及使调整水量与水压。特别是北方冬季,当环境温度 降到摄氏 - 10 ℃以下时,应加强运行监护,轧辊在冷 状态开轧时过钢频率不宜过快,让轧辊有一个缓慢 温升的过程,经测试,停止过钢后,轧槽表面温度与 环境温度差控制在 15 ℃以内为宜。 3.3 改变传统的轧槽冷却方式