有色金属行业智能冶炼工厂建设指南2020版
有色金属行业智能矿山建设指南2020版

有色金属行业智能矿山建设指南(试行)目录一、建设目标 (3)二、建设原则 (3)三、总体设计 (4)(一)总体架构 (4)1. 技术架构 (5)2. 智能应用 (5)(二)建设路径 (5)1. 现有矿山 (6)2. 新建矿山 (6)(三)关键要素 (7)1. 本质安全 (7)2. 资源集约 (8)3. 绿色高效 (8)四、建设内容 (8)(一)基础设施的数字化改造与建设 (8)1. 智能感知 (8)2. 智能装备 (10)3. 网络建设 (10)4. 信息安全 (11)(二)基于业务驱动的智能生产系统建设 (12)1. 矿山地质资源数字化 (12)2. 采矿生产过程智能控制 (13)3. 选矿生产过程智能控制 (17)4. 本质安全管理 (18)5. 生态环境管理 (19)6. 生产运营管理 (20)7. 矿山虚拟仿真 (21)(三)基于服务型制造的智能服务应用建设 (23)(四)基于工业互联网大数据的协同创新平台建设 (23)1. 规范数据治理 (24)2. 数据应用创新 (24)五、基础支撑 (25)(一)资金投入 (25)(二)组织规划 (25)(三)人才队伍 (26)(四)运营维护 (26)(五)信息资源 (26)(六)标准体系 (26)为贯彻落实国务院《关于深化“互联网+先进制造业” 发展工业互联网的指导意见》《新一代人工智能发展规划》等国家相关政策,按照《国家智能制造标准体系建设指南》的总体要求,切实推进有色金属矿山智能升级,特编制本指南。
本指南是促进行业技术进步和规范发展的引导性文件,不具有行政审批的前置性和强制性。
一、建设目标结合我国有色金属矿山开采环境复杂、安全管理压力大、多元素资源共生等特点,在矿山已有自动化、信息化建设基础上,推进物联网、大数据、人工智能、5G、边缘计算、虚拟现实等前沿技术在有色金属矿山的应用,建成集资源的数字化管理、面向“矿石流”的智能生产管控、全流程的少人无人化生产、集成化的本质安全管理、基于工业大数据的智能决策于一体的本质安全、资源集约、绿色高效的有色金属智能矿山,促进企业转型升级、高质量发展,全面提升企业的综合竞争力和可持续发展能力。
有色金属行业智能冶炼工厂建设指南2020版
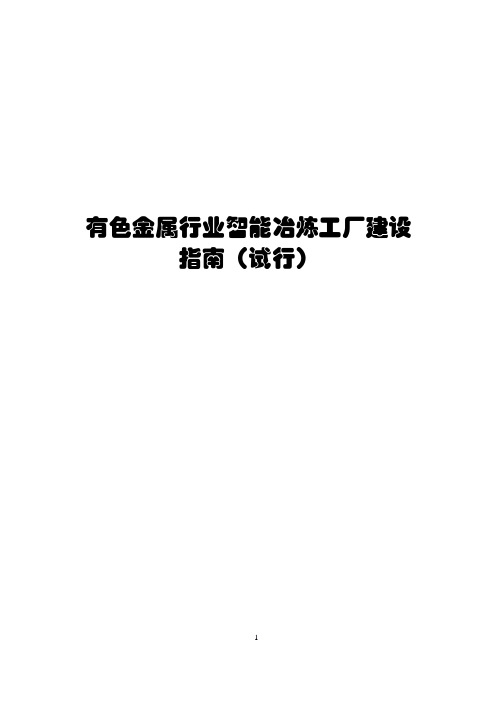
有色金属行业智能冶炼工厂建设指南(试行)目录一、建设目标 (3)二、建设原则 (3)三、总体设计 (5)(一)总体架构 (5)1. 技术架构 (6)2. 智能应用 (6)通过对实时生产数据的全面感知、实时分析、科学决策和 (6)(二)建设路径 (7)1. 现有工厂 (7)2. 新建工厂 (8)(三)关键要素 (9)1. 清洁环保 (9)2. 优质低耗 (9)3. 安全高效 (10)四、建设内容 (10)(一)基础设施的数字化改造与建设 (10)1. 智能感知 (10)2. 智能装备 (11)3. 网络建设 (10)4. 信息安全 (11)(二)数据驱动的智能生产与管理系统建设 (12)1. 生产过程智能控制 (12)2. 生产管理与执行 (14)3. 企业管理与经营决策 (17)4. 冶炼工厂虚拟仿真 (17)专栏6:虚拟仿真场景 (18)(三)基于服务型制造的智能服务应用建设 (19)1. 供应链协同 (19)2. 服务新模式 (19)(四)基于工业互联网大数据的协同创新平台建设 (20)1. 规范数据治理 (20)2. 数据应用创新 (21)五、基础支撑 (22)(一)资金投入 (22)(二)组织规划 (22)(三)人才队伍 (22)(四)运营维护 (22)(五)信息资源 (23)(六)标准体系 (23)为贯彻落实国务院《关于深化“互联网+先进制造业” 发展工业互联网的指导意见》《新一代人工智能发展规划》等国家相关政策,按照《国家智能制造标准体系建设指南》的总体要求,切实推进有色金属冶炼企业智能升级,特编制本指南。
本指南是促进行业技术进步和规范发展的引导性文件,不具有行政审批的前置性和强制性。
一、建设目标结合我国有色金属冶炼多元素资源共生、原料品质波动大、冶炼工艺复杂等特点,在企业已有自动化、信息化建设基础上,推进互联网、大数据、人工智能、5G、边缘计算、虚拟现实等前沿技术在有色冶炼工厂的应用,实现设备、物料、能源等制造资源要素的数字化汇聚、网络化共享和平台化协同,具备在工厂层面全要素数据可视化在线监控、实时自主联动平衡和优化的能力,建成集全流程自动化产线、综合集成信息管控平台、实时协同优化的智能生产体系、精细化能效管控于一体的清洁环保、优质低耗、安全高效的有色金属智能冶炼工厂,促进企业转型升级、高质量发展,提升企业的综合竞争力和可持续发展能力。
智能制造助力有色金属工业高质量发展
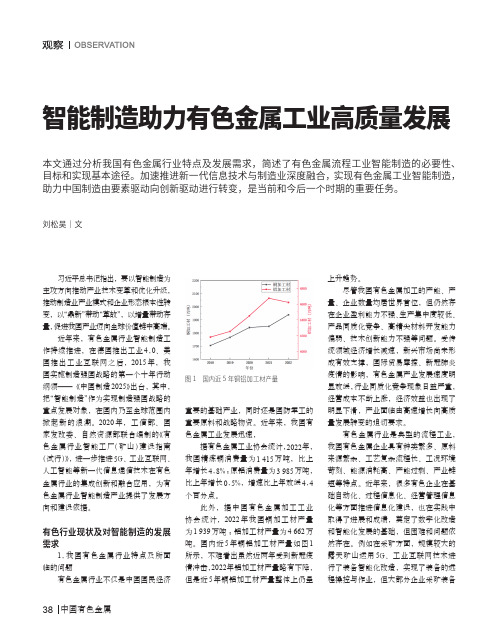
38中国有色金属习近平总书记指出,要以智能制造为主攻方向推动产业技术变革和优化升级,推动制造业产业模式和企业形态根本性转变,以“鼎新”带动“革故”,以增量带动存量,促进我国产业迈向全球价值链中高端。
近年来,有色金属行业智能制造工作持续推进,在德国推出工业4.0、美国推出工业互联网之后,2015年,我国实施制造强国战略的第一个十年行动纲领——《中国制造2025》出台,其中,把“智能制造”作为实现制造强国战略的重点发展对象,在国内乃至全球范围内掀起新的浪潮。
2020年,工信部、国家发改委、自然资源部联合编制的《有色金属行业智能工厂(矿山)建设指南(试行)》,进一步推进5G、工业互联网、人工智能等新一代信息通信技术在有色金属行业的集成创新和融合应用,为有色金属行业智能制造产业提供了发展方向和建设依据。
有色行业现状及对智能制造的发展需求1.我国有色金属行业特点及所面临的问题有色金属行业不仅是中国国民经济智能制造助力有色金属工业高质量发展本文通过分析我国有色金属行业特点及发展需求,简述了有色金属流程工业智能制造的必要性、目标和实现基本途径。
加速推进新一代信息技术与制造业深度融合,实现有色金属工业智能制造,助力中国制造由要素驱动向创新驱动进行转变,是当前和今后一个时期的重要任务。
刘松昊|文上升趋势。
尽管我国有色金属加工的产能、产量、企业数量均居世界首位,但仍然存在企业盈利能力不强、生产集中度较低、产品同质化竞争、高精尖材料开发能力偏弱、技术创新能力不强等问题。
受传统领域经济增长减速,新兴市场尚未形成有效支撑,国际贸易摩擦、新冠肺炎疫情的影响,有色金属产业发展速度明显放缓,行业同质化竞争现象日益严重,经营成本不断上涨,经济效益也出现了明显下滑,产业面临由高速增长向高质量发展转变的迫切要求。
有色金属行业是典型的流程工业,我国有色金属企业具有种类繁多、原料来源繁杂、工艺复杂流程长、工况环境苛刻、能源消耗高、产能过剩、产业链短等特点。
《有色金属行业智能工厂建设指南》解读

《有色金属行业智能工厂建设指南》解读有色金属行业智能工厂建设指南是有色金属行业智能工厂建设领域的
一部独具特色的参考性指南。
指南从实践出发,总结了有色金属行业智能
工厂建设的思路,给出了搭建有色金属行业智能工厂的导向和有效的路径,从而促进有色金属行业智能工厂的完善建设。
本指南解读的主要内容有:
一、有色金属行业智能工厂的需求和特点:有色金属行业面临技术环
境的变化和市场变化的挑战,精细化程度和规模经济的需求,需要搭建智
能工厂来解决高效、低成本的生产问题,实现微利经营。
二、有色金属行业智能工厂建设的体系支撑:有色金属行业智能工厂
建设要建立智能管理、智能车间、智能物流、智能采购、智能供应链等体系,实现工厂智能化。
三、有色金属行业智能工厂建设的技术支持:搭建有色金属行业智能
工厂的过程中,除了要采用智能装备、自动化设备、智能技术外,还需要
运用物联网、大数据、云计算、人工智能技术等技术支撑,实现智能化的
管理、设备运行和维修等方面的技术支持。
智慧冶炼厂建设方案范文

智慧冶炼厂建设方案范文智慧冶炼厂建设方案一、项目背景我国是矿产大国,但煤、铁等采掘业和冶金业产业分布不均,资源集中度较高,环保压力增大,智能化发展水平相对落后,竞争压力不断加大。
当前,改善工业生产方式,提高智能化水平已成为煤、铁等采掘业和冶金业发展的必然趋势。
为了解决上述问题,提升行业竞争力,本项目提出创建智慧冶炼厂,以智能化手段提高煤、铁等采掘业和冶金业生产效率,降低环保压力,提高经济效益。
二、项目概述1. 项目名称:智慧冶炼厂建设方案2. 项目内容:新建智慧冶炼厂,采用智能化手段提高采掘业和冶金业生产效率,降低环保压力,提高经济效益。
3. 项目目标:(1)提高煤、铁等采掘业和冶金业生产效率,降低物料损失和运行成本;(2)降低环保压力,减少污染排放,提升可持续发展能力;(3)提高产品质量和市场竞争力,打造智能制造领域的优秀品牌。
三、项目实施计划1. 项目规划:(1)建设规模:占地面积200亩,建筑面积30000平方米。
(2)核心设备:智能烧结机、智能炉冷系统、智能燃气发电设备、智能物流系统等。
(3)建设周期:24个月。
2. 技术方案:(1)基于物联网、云计算、大数据等技术的智能生产流程控制系统。
(2)基于视觉识别技术的自动化物料搬运系统。
(3)基于机器学习等技术的产品质量检测系统。
(4)基于智能感知技术的生产协同管理系统。
3. 资金投入:(1)项目总投资:5000万元。
(2)资金来源:自筹资金3000万元,银行贷款2000万元。
4. 经济效益:(1)年产值:5000万元。
(2)年利润:1000万元。
(3)投资回收期:5年。
四、项目实施风险1. 技术风险:由于本项目采用智能化技术,部分技术属于新领域,存在技术风险。
2. 市场风险:冶金行业市场竞争激烈,产品价格存在波动,存在市场风险。
3. 环保风险:本项目需要坚持节能降耗、减少环境污染排放,如影响环保问题未有效控制,存在环保风险。
五、项目保障措施1. 技术保障:与国内外的智能化厂家合作,借鉴经验,加强研发和技术攻关。
有色金属行业智能矿山建设指南
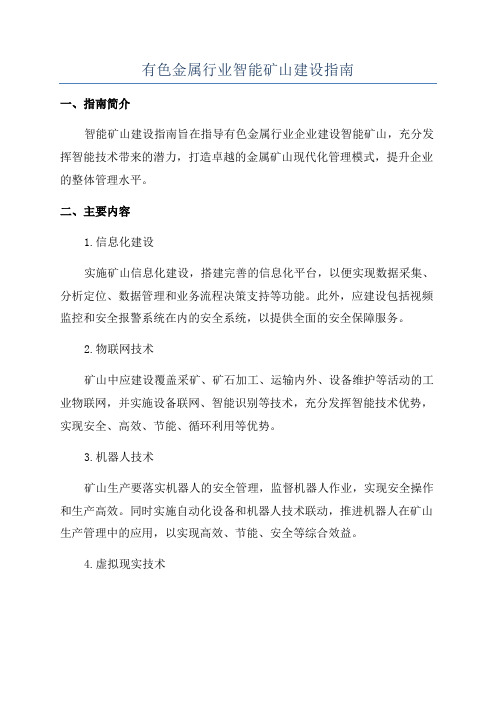
有色金属行业智能矿山建设指南
一、指南简介
智能矿山建设指南旨在指导有色金属行业企业建设智能矿山,充分发挥智能技术带来的潜力,打造卓越的金属矿山现代化管理模式,提升企业的整体管理水平。
二、主要内容
1.信息化建设
实施矿山信息化建设,搭建完善的信息化平台,以便实现数据采集、分析定位、数据管理和业务流程决策支持等功能。
此外,应建设包括视频监控和安全报警系统在内的安全系统,以提供全面的安全保障服务。
2.物联网技术
矿山中应建设覆盖采矿、矿石加工、运输内外、设备维护等活动的工业物联网,并实施设备联网、智能识别等技术,充分发挥智能技术优势,实现安全、高效、节能、循环利用等优势。
3.机器人技术
矿山生产要落实机器人的安全管理,监督机器人作业,实现安全操作和生产高效。
同时实施自动化设备和机器人技术联动,推进机器人在矿山生产管理中的应用,以实现高效、节能、安全等综合效益。
4.虚拟现实技术
虚拟现实技术的应用,可以实现矿山立体空间模型的建立,以及有关
建筑设计、设备安装、矿井运行等活动的模拟和仿真,从而提高工作效率、降低运行成本。
《有色金属行业智能工厂建设指南》解读
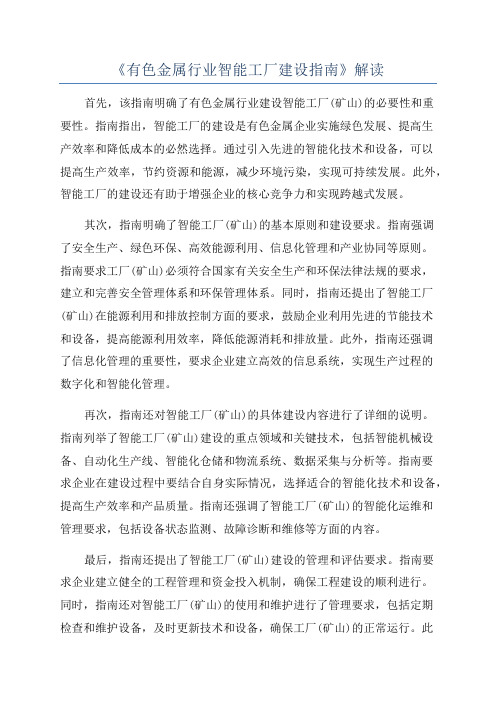
《有色金属行业智能工厂建设指南》解读首先,该指南明确了有色金属行业建设智能工厂(矿山)的必要性和重要性。
指南指出,智能工厂的建设是有色金属企业实施绿色发展、提高生产效率和降低成本的必然选择。
通过引入先进的智能化技术和设备,可以提高生产效率,节约资源和能源,减少环境污染,实现可持续发展。
此外,智能工厂的建设还有助于增强企业的核心竞争力和实现跨越式发展。
其次,指南明确了智能工厂(矿山)的基本原则和建设要求。
指南强调了安全生产、绿色环保、高效能源利用、信息化管理和产业协同等原则。
指南要求工厂(矿山)必须符合国家有关安全生产和环保法律法规的要求,建立和完善安全管理体系和环保管理体系。
同时,指南还提出了智能工厂(矿山)在能源利用和排放控制方面的要求,鼓励企业利用先进的节能技术和设备,提高能源利用效率,降低能源消耗和排放量。
此外,指南还强调了信息化管理的重要性,要求企业建立高效的信息系统,实现生产过程的数字化和智能化管理。
再次,指南还对智能工厂(矿山)的具体建设内容进行了详细的说明。
指南列举了智能工厂(矿山)建设的重点领域和关键技术,包括智能机械设备、自动化生产线、智能化仓储和物流系统、数据采集与分析等。
指南要求企业在建设过程中要结合自身实际情况,选择适合的智能化技术和设备,提高生产效率和产品质量。
指南还强调了智能工厂(矿山)的智能化运维和管理要求,包括设备状态监测、故障诊断和维修等方面的内容。
最后,指南还提出了智能工厂(矿山)建设的管理和评估要求。
指南要求企业建立健全的工程管理和资金投入机制,确保工程建设的顺利进行。
同时,指南还对智能工厂(矿山)的使用和维护进行了管理要求,包括定期检查和维护设备,及时更新技术和设备,确保工厂(矿山)的正常运行。
此外,指南还要求企业进行智能工厂(矿山)的评估,并根据评估结果进行持续改进。
总之,该指南为有色金属行业智能工厂(矿山)的建设提供了全面的指导。
通过遵循指南的原则和要求,有色金属企业可以实现生产效率的提高,资源和能源的节约,环境污染的减少,从而实现可持续发展。
有色金属行业智能矿山建设指南2020年

附件1有色金属行业智能矿山建设指南(试行)为贯彻落实国务院《关于深化“互联网+先进制造业”发展工业互联网的指导意见》《新一代人工智能发展规划》等国家相关政策,按照《国家智能制造标准体系建设指南》的总体要求,切实推进有色金属矿山智能升级,特编制本指南。
本指南是促进行业技术进步和规范发展的引导性文件,不具有行政审批的前置性和强制性。
一、建设目标结合我国有色金属矿山开采环境复杂、安全管理压力大、多元素资源共生等特点,在矿山已有自动化、信息化建设基础上,推进物联网、大数据、人工智能、5G、边缘计算、虚拟现实等前沿技术在有色金属矿山的应用,建成集资源的数字化管理、面向“矿石流”的智能生产管控、全流程的少人无人化生产、集成化的本质安全管理、基于工业大数据的智能决策于一体的本质安全、资源集约、绿色高效的有色金属智能矿山,促进企业转型升级、高质量发展,全面提升企业的综合竞争力和可持续发展能力。
二、建设原则坚持因企制宜,注重实效。
根据企业发展战略和实际生产经营情况,充分考虑矿山资源禀赋条件、矿山所处生命周期阶段、工艺装备水平以及信息化建设基础,明确企业智能化建设重点,新建矿山直接进行智能化规划与设计,在产矿山有序推进智能化改造。
坚持整体规划,分步实施。
把握智能制造发展方向和重点,从全局、整体层面进行顶层设计,围绕有色金属智能矿山建设主要环节和重点领域,结合矿山自身能力和业务需求等特点,分步实施,有序推进智能矿山建设。
坚持创新引领,数据驱动。
积极探索5G等新型基础设施在企业生产中的应用,推动新技术与有色矿山的融合创新;基于数据和机理融合驱动的理念,应用大数据、人工智能、边缘计算等技术提升信息系统学习与认知的能力,利用AR/VR(增强现实/虚拟现实)等技术形成人机混合增强智能,充分发挥工艺技术人员的智慧与机器智能的各自优势,推动工艺与管理知识的沉淀与复用,支撑企业持续进行技术创新。
三、总体设计(一)总体架构鼓励有色金属智能矿山采用基于工业互联网平台的云、边、端架构,建立面向“矿石流”的全流程智能生产管控系统,将矿山大量基于传统IT架构的信息系统作为工业互联网平台的数据源,继续发挥系统剩余价值,同时逐步推进传统信息化业务云化部署,实现矿山全流程的少人无人化生产。
有色行业智能铜冶炼(湿法)设计标准

有色行业智能铜冶炼(湿法)设计标准摘要:一、有色行业智能铜冶炼概述1.智能铜冶炼的定义2.湿法冶炼的特点二、有色行业智能铜冶炼设计标准1.设计原则2.设备选型与布局3.自动化与信息化系统4.安全环保要求5.经济性分析三、有色行业智能铜冶炼的发展趋势1.提高生产效率2.降低生产成本3.环保与可持续发展4.智能化技术的应用正文:有色行业智能铜冶炼(湿法) 设计标准随着科技的发展,有色行业正逐步向智能化、绿色化方向发展。
智能铜冶炼作为其中的一种新型冶炼方式,以其独特的优势逐渐成为行业发展的热点。
本文将详细介绍有色行业智能铜冶炼的设计标准。
一、有色行业智能铜冶炼概述1.智能铜冶炼的定义智能铜冶炼是指利用现代信息技术、自动化技术、互联网技术等先进科技手段,实现铜冶炼过程的智能化、绿色化、高效化的一种新型冶炼方式。
智能铜冶炼主要包括:矿山选矿、冶炼、电解、铸造等环节。
2.湿法冶炼的特点湿法冶炼是一种以水为溶剂的冶炼方法,具有生产过程环保、资源利用率高、产品纯度高等特点。
湿法冶炼主要包括:浸出、萃取、电积等过程。
二、有色行业智能铜冶炼设计标准1.设计原则智能铜冶炼设计应遵循以下原则:(1) 先进性:采用国际先进的冶炼技术和设备,保证生产过程的稳定性和可靠性。
(2) 可靠性:设计方案应经过充分论证,确保设备选型、布局合理,满足生产需求。
(3) 经济性:在保证生产效果的前提下,降低投资成本和生产成本,提高项目经济效益。
(4) 环保性:严格执行国家和地方环保法规,确保生产过程对环境的影响降到最低。
2.设备选型与布局(1) 设备选型:根据生产工艺要求,选择高效、节能、环保的设备。
(2) 设备布局:合理规划生产车间、设备摆放、工艺流程,提高生产效率。
3.自动化与信息化系统(1) 自动化系统:采用先进的自动化控制技术,实现生产过程的实时监控、故障诊断、优化调整等功能。
(2) 信息化系统:建立生产管理、设备管理、质量管理等模块,实现数据的采集、处理、分析和展示,为决策提供支持。
智慧冶炼厂建设方案设计

智慧冶炼厂建设方案设计随着科技的不断发展和进步,智能化、数字化、自动化的工厂建设也越来越受到人们的关注。
智慧冶炼厂是一种集科技、信息化、节能、环保于一体的高端智能化厂房,是未来工厂发展的重要方向。
本文将从设计方案、技术路线、减排措施、能源管理等方面,对智慧冶炼厂建设方案进行探讨。
一、设计方案智慧冶炼厂的设计方案应该充分考虑到节能、环保、安全和效率的四个重点,具体包括以下几个方面的设计:1.建筑结构厂房建筑结构应考虑成本、安全和效率等综合因素,采用高质量钢材材料,结构设计简洁美观,抗裂性好,有效保证了厂房的整体稳定性。
2.热力设计针对热力设计,应该采用高效节能的办法,例如太阳能电板和热泵等节能设备供给厂房需要的暖气、通风和空调需求,实现余热回收等综合措施,让厂房保持最佳的室内环境,减少能耗。
3. 照明设计厂房的照明设计应该实现自动化控制,采用LED灯具,实现节能降耗。
另外,为了减少对工人的眼睛造成的不适,并避免危险,室内采用光线柔和的灯光设计。
4. 厂区道路和停车位设计除生产车间外,良好的厂区道路设计可以提高生产效率,厂区停车位数量的充足设计不仅可以确保员工的车辆安全,却也可以减少停车的拥堵问题。
二、技术路线智慧冶炼厂的技术路线应该采用高端科技,实现自动化和数字化生产的最佳效果。
具体包括以下几个方面:1. 自动化控制实现自动化控制,对生产环节的监测、数据采集和分析,以及控制系统都应该通过计算机系统进行自动化操作,以达到快速高效和数字化自动化的生产需求。
2. 机器人操作在生产环节中,使用机器人进行操作可以有效提高生产效率,减少由于人工操作错误所造成的质量问题和安全隐患。
3. 互联网+技术利用互联网+技术,实现多网直接交流,以及实时监控、数据传输等一系列科技手段实现生产线上全方位的管理。
三、减排措施实现减排措施是智慧冶炼厂建设方案的重要需求,采取以下措施可以达到减少污染的效果。
1. 采用清洁能源采用清洁能源,如太阳能、风能和水能等,减少对传统能源的依赖,从而降低大气污染和温室气体的排放。
有色金属冶炼的智能工厂建设
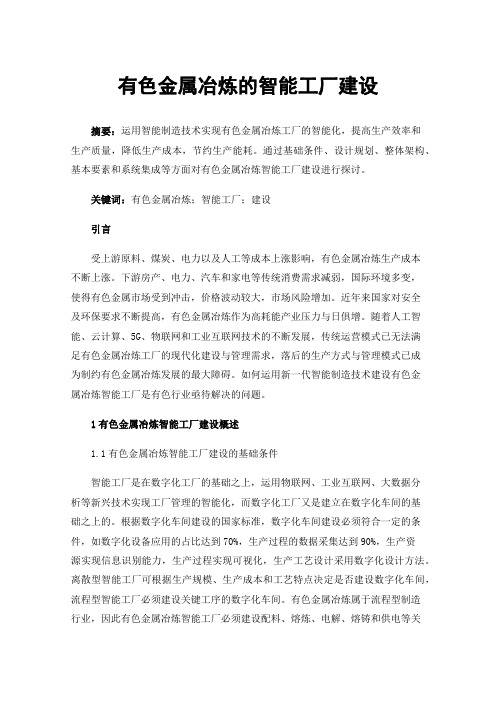
有色金属冶炼的智能工厂建设摘要:运用智能制造技术实现有色金属冶炼工厂的智能化,提高生产效率和生产质量,降低生产成本,节约生产能耗。
通过基础条件、设计规划、整体架构、基本要素和系统集成等方面对有色金属冶炼智能工厂建设进行探讨。
关键词:有色金属冶炼;智能工厂;建设引言受上游原料、煤炭、电力以及人工等成本上涨影响,有色金属冶炼生产成本不断上涨。
下游房产、电力、汽车和家电等传统消费需求减弱,国际环境多变,使得有色金属市场受到冲击,价格波动较大,市场风险增加。
近年来国家对安全及环保要求不断提高,有色金属冶炼作为高耗能产业压力与日俱增。
随着人工智能、云计算、5G、物联网和工业互联网技术的不断发展,传统运营模式已无法满足有色金属冶炼工厂的现代化建设与管理需求,落后的生产方式与管理模式已成为制约有色金属冶炼发展的最大障碍。
如何运用新一代智能制造技术建设有色金属冶炼智能工厂是有色行业亟待解决的问题。
1有色金属冶炼智能工厂建设概述1.1有色金属冶炼智能工厂建设的基础条件智能工厂是在数字化工厂的基础之上,运用物联网、工业互联网、大数据分析等新兴技术实现工厂管理的智能化,而数字化工厂又是建立在数字化车间的基础之上的。
根据数字化车间建设的国家标准,数字化车间建设必须符合一定的条件,如数字化设备应用的占比达到70%,生产过程的数据采集达到90%,生产资源实现信息识别能力,生产过程实现可视化,生产工艺设计采用数字化设计方法。
离散型智能工厂可根据生产规模、生产成本和工艺特点决定是否建设数字化车间,流程型智能工厂必须建设关键工序的数字化车间。
有色金属冶炼属于流程型制造行业,因此有色金属冶炼智能工厂必须建设配料、熔炼、电解、熔铸和供电等关键工序的数字化车间。
同时实现各系统的集成与各车间之间的网络连接或建有全厂网络与数据中心。
1.2有色金属冶炼智能工厂建设的设计规划智能工厂建设不管是新建工厂还是旧厂改造,都是一项复杂而又漫长的工程,尤其是旧厂改造,难度远大于新建工厂,因此智能工厂建设必须有专业详细的设计规划作为指导。
金属冶炼的智慧工厂建设
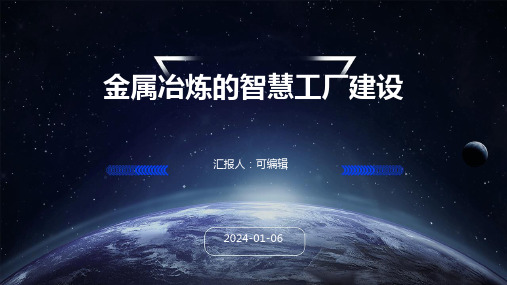
智能监控与预警系统
实时监控
对生产过程进行实时监控,及时发现异常情况并进行预警。
数据分析
对监控数据进行深度分析,挖掘潜在问题,优化生产过程。
远程监控与控制
通过远程监控与控制技术,实现异地管理和调度,提高生产管理 效率。
数据驱动的决策支持系统
数据采集与整合
01
采集生产过程中的各种数据,进行整合和分析。
特点
具备高度的自动化、信息化、网络化 和智能化特征,能够实现生产过程的 可视化管理、实时监控、智能调度和 优化控制。
智慧工厂的重要性
提高生产效率
通过自动化和智能化技 术,减少人工干预,提
高生产效率。
降低能耗和排放
实现能源的智能管理和 优化利用,降低能耗和
排放。
提高产品质量
通过精准控制和实时监 测,提高产品质量和稳
制定智慧工厂能效标准
推动企业提高能源利用效率,降低能耗和排 放。
跨界合作与共赢
与科研机构合作
共同研发新技术和新产品,推动智慧工厂的创新发展。
与上下游企业合作
实现产业链的协同发展,提升整体竞争力。
与政府和行业协会合作
共同制定政策法规,推动智慧工厂的普及和应用。
THANKS
感谢观看
物联网技术
实现设备与设备之间的互联互通,实时监测和调控生产过 程。
人工智能技术
应用机器学习和深度学习算法,优化生产流程,提高产品 质量。
行业标准与规范
制定统一的智慧工厂建设标准
确保不同企业之间的智慧工厂建设具有兼容 性和互操作性。
建立完善的智慧工厂安全规范
保障生产过程的安全可控,防止安全事故的 发生。
通过人工智能技术,实现金属冶 炼产品的智能质量控制,提高产 品质量和合格率。
有色金属行业智能加工工厂建设指南(试行)

有色金属行业智能加工工厂建设指南(试行)
加大人才引进和复合型人才的培养,鼓励企业构建内
外结合的智能加工人才储备机制,实现依托外部专家团队、智能制造系统解决方案供应商完成尖端技术攻关、科研成果转化、项目建设实施,依托内部人才队伍完成系统运营维护的人才格局。
(四)运营维护
依据企业管理模式及生产需要编制智能加工系统运维
及升级准则,规范各类智能加工系统、装备的工作流程与维护保养规程。
(五)信息资源
开展企业内部网络信息资源管理标准化工作,构筑与
智能加工工厂建设规划相匹配的网络信息资源管理标准化体系,规范企业信息资源的管理和使用。
(六)标准体系
在遵循有色行业及智能制造领域已发布的相关标准规
范的基础上,鼓励企业建立包含但不限于如下所列标准和规范体系:数据编码规则、数据治理流程规范、数据使用规范、业务流程标准、数据库设计规范、运维服务规程、运维管理规程。
20。
冶金行业如何推动智能化工厂建设

冶金行业如何推动智能化工厂建设在当今科技飞速发展的时代,智能化已成为众多行业转型升级的重要方向,冶金行业也不例外。
智能化工厂建设不仅能够提高生产效率、降低成本、提升产品质量,还能增强企业的竞争力和可持续发展能力。
那么,冶金行业应如何推动智能化工厂建设呢?首先,要充分认识到智能化工厂建设的重要性和紧迫性。
随着市场竞争的加剧和资源环境约束的日益增强,传统的冶金生产方式已经难以满足企业发展的需求。
智能化工厂能够实现生产过程的自动化、数字化和智能化,有效提高资源利用效率,减少环境污染,降低安全风险,为企业创造更大的价值。
在技术层面,要加强信息化基础设施建设。
这包括构建高速稳定的网络环境,确保生产数据的实时传输和共享。
同时,要建立完善的数据采集系统,对生产过程中的各种参数、指标进行准确、全面的采集。
此外,还需要引入先进的生产设备和控制系统,如自动化生产线、智能机器人、智能传感器等,实现生产过程的自动化控制和智能化调节。
数据管理和分析是智能化工厂建设的核心。
要建立统一的数据管理平台,对采集到的数据进行集中存储、整理和分析。
通过大数据分析、机器学习等技术,挖掘数据中的潜在价值,为生产决策提供科学依据。
例如,可以通过分析生产数据,优化生产工艺参数,提高产品质量和产量;预测设备故障,提前进行维护和保养,减少停机时间。
智能化工厂建设还需要注重人才培养。
培养一支既懂冶金专业知识,又熟悉信息技术和智能化技术的复合型人才队伍至关重要。
企业可以通过内部培训、外部引进等方式,提高员工的智能化素养和技能水平。
同时,要营造鼓励创新和学习的企业文化氛围,激发员工的积极性和创造力。
在生产流程优化方面,要对传统的冶金生产流程进行深入分析和评估,找出其中的瓶颈和问题。
运用智能化技术,对生产流程进行重新设计和优化,实现生产过程的高效、协同和精益化。
例如,通过智能调度系统,合理安排生产计划和资源配置,提高生产效率;通过智能物流系统,实现原材料和产品的精准配送,降低库存成本。
有色行业智能制造标准体系建设指南(2022版)
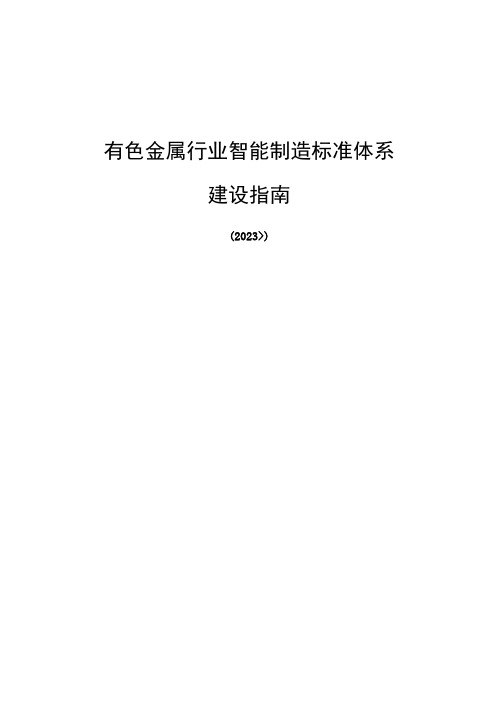
有色金属行业智能制造标准体系建设指南(2023>)2023年6月前言 (I)一、总体要求 (1)(一)指导思想 (1)(二)基本原则 (1)(三)建设目标 (2)二、建设思路 (2)(一)有色金属行业智能制造标准体系结构 (2)(二)有色金属行业智能制造标准体系框架 (4)三、建设内容 (5)(一)基础综合标准(CIA) (5)(二)装备与系统标准(C1B) (6)(三)智能工厂标准(C1e) (8)(四)评价标准(C1D) (17)四、实施路径 (16)附件1有色金属行业智能制造现行及在研标准清单 (18)附件2有色金属行业智能制造拟制定标准清单 (20)刖R有色金属行业是制造业的重要基础产业之一,是实现制造强国的重要支撑。
当前,我国有色金属行业正处于由数量和规模扩张向质量和效益提升转变的关键期,亟待与5G、工业互联网、人工智能等新一代信息技术在更广范围、更深程度、更高水平上实现融合发展。
为切实发挥标准对有色金属行业智能制造发展的支撑和引领作用,规范和引导有色金属行业实现资源要素的数字化汇聚、网络化共享、平台化协同和智能化管控,工业和信息化部依据《国家标准化发展纲要》《“十四五”数字经济发展规划》《“十四五”推动高质量发展的国家标准体系建设规划》《国家智能制造标准体系建设指南(2023版)》《“十四五”智能制造发展规划》《“十四五”原材料工业发展规划》《有色金属行业智能工厂(矿山)建设指南(试行)》,组织编制了《有色金属行业智能制造标准体系建设指南(2023版)》。
一、总体要求(一)指导思想坚持以习近平新时代中国特色社会主义思想为指导,全面贯彻党的十九大和十九届历次全会精神,立足新发展阶段,完整、准确、全面贯彻新发展理念,深入落实《“十四五”数字经济发展规划》《“十四五”智能制造发展规划》《“十四五”原材料工业发展规划》《有色金属行业智能工厂(矿山)建设指南(试行)》的要求,以推动有色金属行业智能化升级为主线,围绕有色金属行业采选的本质安全与资源集约、冶炼的清洁环保与节能降耗、加工的质量稳定与柔性生产等实际需求,加快建立涵盖基础综合、数字化平台、智能工厂、设计建设及评价的智能制造标准体系,不断推进有色金属行业智能化发展。
金属冶炼行业的智能化发展

1
大数据技术是金属冶炼行业智能化发展的重要支 撑,通过大数据分析实现生产过程的优化和改进 。
2
大数据技术包括数据采集、数据处理、数据分析 和数据可视化等技术,能够实现生产过程的数据 监测、分析和预测。
3
大数据技术的应用能够提高生产过程的可预测性 ,优化生产工艺和流程,提高生产效率和产品质 量。
物联网技术
新兴应用领域拓展
金属冶炼产品在新能源、新材料、高端装备 等领域的应用前景广阔,企业需要紧跟市场 需求,拓展新兴应用领域。
感谢您的观看
THANKS
提高产品质量
智能化技术能够实现生产过程 的精准控制和优化,提高产品 质量和稳定性。
提升企业竞争力
智能化技术能够提高企业的生 产效率和成本控制能力,提升 企业的市场占有率和竞争力。
智能化发展的历史与发展
历史
金属冶炼行业的智能化发展经历了从传统的手工操作到机械化和自动化,再到智 能化的过程。
发展
未来金属冶炼行业的智能化发展将更加注重数字化、网络化和人工智能技术的应 用,实现更加高效、安全、环保的生产模式。同时,随着环保要求的提高和资源 的日益紧张,金属冶炼行业将更加注重循环经济和资源综合利用的发展。
特点
智能化发展具有高效、安全、环保、 节能等特点,能够提高金属冶炼的效 率和质量,降低能耗和排放,提升企 业的竞争力和可持续发展能力。
智能化发展的重要性
提高生产效率
智能化技术能够实现自动化控 制和优化调度,减少人工干预 和操作误差,提高生产效率。
降低能耗和排放
智能化技术能够实现能源的精 准控制和优化利用,降低能耗 和排放,符合绿色发展理念。
管理挑战
金属冶炼行业的管理问题主要包括生产安全 、质量控制和供应链管理等方面。
冶金企业的智能工厂如何布局

冶金企业的智能工厂如何布局在当今科技飞速发展的时代,冶金企业面临着日益激烈的市场竞争和不断提高的环保要求。
为了提高生产效率、降低成本、提升产品质量和增强企业竞争力,布局智能工厂已成为冶金企业的重要发展方向。
那么,冶金企业该如何进行智能工厂的布局呢?首先,要明确智能工厂的概念和目标。
智能工厂并非简单地引入先进的设备和技术,而是通过整合信息化、自动化和智能化技术,实现生产过程的高效、灵活、绿色和可持续发展。
其目标是实现生产过程的自动化控制、优化调度、智能决策和精准管理,从而提高企业的综合竞争力。
在基础设施建设方面,冶金企业需要搭建高速稳定的工业网络。
这包括有线网络和无线网络,以确保生产设备、传感器、控制系统和管理系统之间能够实时、准确地传输数据。
同时,要建立强大的数据中心,用于存储和处理海量的生产数据。
数据中心的硬件设施要具备高性能、高可靠性和可扩展性,以满足企业不断增长的业务需求。
生产设备的智能化升级是智能工厂布局的关键环节。
对于冶金企业来说,传统的生产设备往往存在效率低下、能耗高、故障率高等问题。
因此,需要对这些设备进行智能化改造,安装传感器、控制器和执行器,使其具备自动感知、自动控制和自动优化的能力。
例如,在炼铁高炉中,可以安装温度传感器、压力传感器和气体分析仪等设备,实时监测炉内的工作状态,并通过智能控制系统调整风量、料速等参数,以实现高炉的稳定运行和高效生产。
在生产流程优化方面,利用大数据分析和人工智能技术对生产过程进行建模和仿真。
通过对历史生产数据的挖掘和分析,找出生产过程中的瓶颈环节和优化空间,并制定相应的改进措施。
例如,通过优化配料方案、调整工艺流程和改进操作方法,可以降低原材料消耗、提高产品质量和生产效率。
智能质量管理也是智能工厂的重要组成部分。
通过在线检测设备和智能分析系统,对原材料、半成品和成品的质量进行实时监测和分析。
一旦发现质量问题,能够及时追溯到生产环节,采取相应的措施进行整改。
有色金属行业智能化冶炼与环保方案
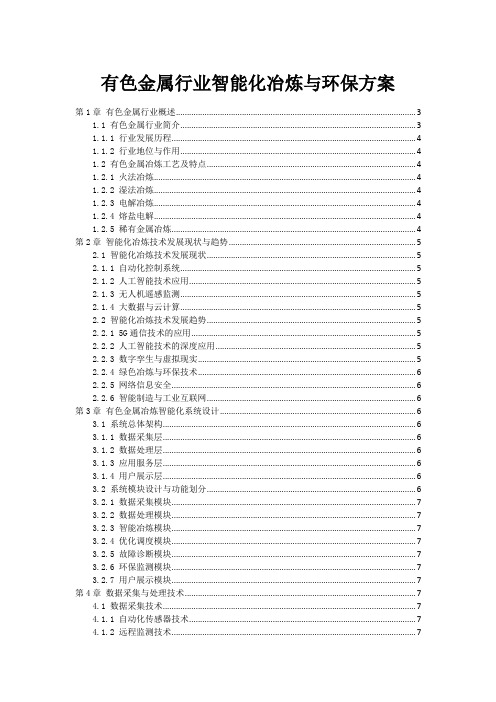
有色金属行业智能化冶炼与环保方案第1章有色金属行业概述 (3)1.1 有色金属行业简介 (3)1.1.1 行业发展历程 (4)1.1.2 行业地位与作用 (4)1.2 有色金属冶炼工艺及特点 (4)1.2.1 火法冶炼 (4)1.2.2 湿法冶炼 (4)1.2.3 电解冶炼 (4)1.2.4 熔盐电解 (4)1.2.5 稀有金属冶炼 (4)第2章智能化冶炼技术发展现状与趋势 (5)2.1 智能化冶炼技术发展现状 (5)2.1.1 自动化控制系统 (5)2.1.2 人工智能技术应用 (5)2.1.3 无人机遥感监测 (5)2.1.4 大数据与云计算 (5)2.2 智能化冶炼技术发展趋势 (5)2.2.1 5G通信技术的应用 (5)2.2.2 人工智能技术的深度应用 (5)2.2.3 数字孪生与虚拟现实 (5)2.2.4 绿色冶炼与环保技术 (6)2.2.5 网络信息安全 (6)2.2.6 智能制造与工业互联网 (6)第3章有色金属冶炼智能化系统设计 (6)3.1 系统总体架构 (6)3.1.1 数据采集层 (6)3.1.2 数据处理层 (6)3.1.3 应用服务层 (6)3.1.4 用户展示层 (6)3.2 系统模块设计与功能划分 (6)3.2.1 数据采集模块 (7)3.2.2 数据处理模块 (7)3.2.3 智能冶炼模块 (7)3.2.4 优化调度模块 (7)3.2.5 故障诊断模块 (7)3.2.6 环保监测模块 (7)3.2.7 用户展示模块 (7)第4章数据采集与处理技术 (7)4.1 数据采集技术 (7)4.1.1 自动化传感器技术 (7)4.1.2 远程监测技术 (7)4.2 数据处理与分析方法 (8)4.2.1 数据预处理 (8)4.2.2 多变量统计分析 (8)4.2.3 机器学习与人工智能算法 (8)4.2.4 大数据分析 (8)4.2.5 云计算与边缘计算 (8)4.2.6 可视化技术 (8)第5章智能优化与控制策略 (9)5.1 智能优化算法 (9)5.1.1 算法概述 (9)5.1.2 遗传算法 (9)5.1.3 粒子群优化算法 (9)5.1.4 模拟退火算法 (9)5.1.5 蚁群算法 (9)5.2 控制策略及其实现 (9)5.2.1 控制策略概述 (9)5.2.2 参数优化 (10)5.2.3 模型预测 (10)5.2.4 控制器设计 (10)5.2.5 系统实现 (10)第6章冶炼过程参数监测与优化 (10)6.1 冶炼过程参数监测 (10)6.1.1 参数监测概述 (10)6.1.2 监测技术及设备 (10)6.1.3 监测系统构建 (10)6.2 参数优化方法及应用 (10)6.2.1 优化方法概述 (10)6.2.2 优化方法应用 (11)6.2.3 实际应用案例 (11)第7章环保方案设计 (11)7.1 有色金属冶炼环保政策与标准 (11)7.1.1 政策背景 (11)7.1.2 主要环保政策与标准 (11)7.2 环保方案总体设计 (12)7.2.1 设计原则 (12)7.2.2 环保方案内容 (12)第8章废气处理与资源化利用 (13)8.1 废气处理技术 (13)8.1.1 吸附法 (13)8.1.2 吸收法 (13)8.1.3 冷凝法 (13)8.1.4 生物法 (13)8.1.5 膜分离法 (13)8.2.1 废气中稀有气体回收 (13)8.2.2 废气中金属颗粒物回收 (14)8.2.3 废气中热量回收 (14)8.2.4 废气中有机物提取 (14)8.2.5 废气处理产物综合利用 (14)第9章废水处理与循环利用 (14)9.1 废水处理技术 (14)9.1.1 物理处理技术 (14)9.1.2 化学处理技术 (14)9.1.3 生物处理技术 (14)9.2 循环利用系统设计 (15)9.2.1 废水收集与预处理 (15)9.2.2 废水处理工艺选择 (15)9.2.3 循环利用系统构建 (15)9.2.4 系统运行与优化 (15)9.2.5 环保与安全措施 (15)第10章智能化环保管理与运维 (16)10.1 环保监测与管理平台 (16)10.1.1 监测系统构建 (16)10.1.2 数据处理与分析 (16)10.1.3 环保管理策略 (16)10.2 智能运维与决策支持系统 (16)10.2.1 智能运维系统设计 (16)10.2.2 决策支持系统 (16)10.2.3 智能调度与优化 (16)10.3 环保效果评估与优化建议 (17)10.3.1 环保效果评估指标体系 (17)10.3.2 评估方法与案例分析 (17)10.3.3 优化建议 (17)第1章有色金属行业概述1.1 有色金属行业简介有色金属是指除了铁、锰、铬以外的所有金属元素,包括铜、铝、铅、锌、镍、锡、钨、钼、镁、钛等。
金属与冶炼行业智能化金属冶炼工艺优化方案

金属与冶炼行业智能化金属冶炼工艺优化方案第一章金属冶炼工艺智能化概述 (3)1.1 智能化金属冶炼工艺的发展背景 (3)1.2 智能化金属冶炼工艺的优势与挑战 (3)第二章矿石准备与预处理 (4)2.1 矿石破碎与筛分智能化 (4)2.1.1 概述 (4)2.1.2 智能化技术应用 (4)2.2 矿石配料与混合智能化 (4)2.2.1 概述 (4)2.2.2 智能化技术应用 (4)2.3 矿石干燥与预热智能化 (5)2.3.1 概述 (5)2.3.2 智能化技术应用 (5)第三章焦炭制备与预处理 (5)3.1 焦炭制备智能化 (5)3.1.1 焦炭制备概述 (5)3.1.2 焦炭制备智能化技术 (5)3.2 焦炭质量检测与评估智能化 (5)3.2.1 焦炭质量检测概述 (6)3.2.2 焦炭质量检测智能化技术 (6)第四章高炉炼铁智能化 (6)4.1 高炉操作参数优化智能化 (6)4.2 高炉过程监控与故障诊断智能化 (6)4.3 高炉生产调度与优化智能化 (7)第五章转炉炼钢智能化 (7)5.1 转炉操作参数优化智能化 (7)5.2 转炉过程监控与故障诊断智能化 (7)5.3 转炉生产调度与优化智能化 (8)第六章电炉炼钢智能化 (8)6.1 电炉操作参数优化智能化 (8)6.1.1 操作参数的实时监测 (8)6.1.2 参数优化算法研究 (8)6.1.3 参数优化智能化系统设计 (8)6.2 电炉过程监控与故障诊断智能化 (9)6.2.1 过程监控技术 (9)6.2.2 故障诊断技术 (9)6.3 电炉生产调度与优化智能化 (9)6.3.1 生产调度策略研究 (9)6.3.2 生产优化算法研究 (9)6.3.3 生产调度与优化智能化系统设计 (9)第七章铸造智能化 (10)7.1 铸造工艺参数优化智能化 (10)7.1.1 引言 (10)7.1.2 铸造工艺参数实时监测 (10)7.1.3 铸造工艺参数智能优化方法 (10)7.1.4 相关技术应用 (10)7.2 铸造过程监控与故障诊断智能化 (10)7.2.1 引言 (10)7.2.2 铸造过程监控 (11)7.2.3 故障诊断智能化 (11)7.2.4 相关技术应用 (11)7.3 铸造生产调度与优化智能化 (11)7.3.1 引言 (11)7.3.2 铸造生产调度智能化 (11)7.3.3 铸造生产优化智能化 (11)7.3.4 相关技术应用 (11)第八章冶炼废渣处理智能化 (12)8.1 冶炼废渣回收与利用智能化 (12)8.1.1 引言 (12)8.1.2 智能化技术概述 (12)8.1.3 废渣成分分析智能化 (12)8.1.4 废渣资源化技术智能化 (12)8.1.5 废渣处理工艺优化智能化 (12)8.2 冶炼废渣处理过程监控与优化智能化 (12)8.2.1 引言 (12)8.2.2 智能化技术概述 (12)8.2.3 过程参数监测智能化 (12)8.2.4 故障诊断与预警智能化 (13)8.2.5 处理效果评估智能化 (13)8.2.6 冶炼废渣处理智能化系统 (13)第九章冶炼环保与安全智能化 (13)9.1 冶炼过程环保监控与优化智能化 (13)9.1.1 引言 (13)9.1.2 环保监控技术 (13)9.1.3 环保优化技术 (13)9.2 冶炼过程安全监控与预警智能化 (14)9.2.1 引言 (14)9.2.2 安全监控技术 (14)9.2.3 安全预警技术 (14)第十章金属冶炼工艺智能化发展趋势与展望 (14)10.1 金属冶炼工艺智能化发展趋势 (14)10.2 金属冶炼工艺智能化应用前景与挑战 (15)第一章金属冶炼工艺智能化概述1.1 智能化金属冶炼工艺的发展背景我国经济的快速发展,金属冶炼行业在国民经济中的地位日益突出。
- 1、下载文档前请自行甄别文档内容的完整性,平台不提供额外的编辑、内容补充、找答案等附加服务。
- 2、"仅部分预览"的文档,不可在线预览部分如存在完整性等问题,可反馈申请退款(可完整预览的文档不适用该条件!)。
- 3、如文档侵犯您的权益,请联系客服反馈,我们会尽快为您处理(人工客服工作时间:9:00-18:30)。
有色金属行业智能冶炼工厂建设指南(试行)目录一、建设目标 (3)二、建设原则 (3)三、总体设计 (5)(一)总体架构 (5)1. 技术架构 (6)2. 智能应用 (6)通过对实时生产数据的全面感知、实时分析、科学决策和 (6)(二)建设路径 (7)1. 现有工厂 (7)2. 新建工厂 (8)(三)关键要素 (9)1. 清洁环保 (9)2. 优质低耗 (9)3. 安全高效 (10)四、建设内容 (10)(一)基础设施的数字化改造与建设 (10)1. 智能感知 (10)2. 智能装备 (11)3. 网络建设 (10)4. 信息安全 (11)(二)数据驱动的智能生产与管理系统建设 (12)1. 生产过程智能控制 (12)2. 生产管理与执行 (14)3. 企业管理与经营决策 (17)4. 冶炼工厂虚拟仿真 (17)专栏6:虚拟仿真场景 (18)(三)基于服务型制造的智能服务应用建设 (19)1. 供应链协同 (19)2. 服务新模式 (19)(四)基于工业互联网大数据的协同创新平台建设 (20)1. 规范数据治理 (20)2. 数据应用创新 (21)五、基础支撑 (22)(一)资金投入 (22)(二)组织规划 (22)(三)人才队伍 (22)(四)运营维护 (22)(五)信息资源 (23)(六)标准体系 (23)为贯彻落实国务院《关于深化“互联网+先进制造业” 发展工业互联网的指导意见》《新一代人工智能发展规划》等国家相关政策,按照《国家智能制造标准体系建设指南》的总体要求,切实推进有色金属冶炼企业智能升级,特编制本指南。
本指南是促进行业技术进步和规范发展的引导性文件,不具有行政审批的前置性和强制性。
一、建设目标结合我国有色金属冶炼多元素资源共生、原料品质波动大、冶炼工艺复杂等特点,在企业已有自动化、信息化建设基础上,推进互联网、大数据、人工智能、5G、边缘计算、虚拟现实等前沿技术在有色冶炼工厂的应用,实现设备、物料、能源等制造资源要素的数字化汇聚、网络化共享和平台化协同,具备在工厂层面全要素数据可视化在线监控、实时自主联动平衡和优化的能力,建成集全流程自动化产线、综合集成信息管控平台、实时协同优化的智能生产体系、精细化能效管控于一体的清洁环保、优质低耗、安全高效的有色金属智能冶炼工厂,促进企业转型升级、高质量发展,提升企业的综合竞争力和可持续发展能力。
二、建设原则坚持企业主体,战略主导。
确立企业智能工厂建设的主体责任,根据企业战略,结合企业区域特征、产品定位、工艺装备、管理模式、两化融合基础,明确企业智能制造建设重点。
坚持整体规划,分步实施。
把握智能制造发展方向和重点,从全局、整体层面进行顶层设计,围绕有色金属智能冶炼工厂建设主要环节和重点领域,结合企业自身能力和业务需求,分步实施,有序推进智能冶炼工厂建设。
坚持问题导向,因企制宜。
以解决企业生产管理和经营管理的实际问题为出发点,实现关键冶炼设备和控制技术的升级、突破;充分考虑企业智能制造建设基础,结合企业对智能制造发展的需求,因企制宜地进行智能工厂建设,有针对性地完善重点领域的智能化建设。
坚持创新引领,数据驱动。
积极探索5G 等新型基础设施在企业生产中的应用,推动新技术与有色冶炼的融合创新;基于数据和机理融合驱动的理念,应用大数据、人工智能、边缘计算等技术提升信息系统学习与认知能力,利用AR/VR(增强现实/虚拟现实)等技术形成人机协同混合增强智能,充分发挥工艺技术人员的智慧与机器智能的各自优势,推动工艺与管理知识的沉淀与复用,支撑企业持续进行技术创新。
三、总体设计(一)总体架构鼓励有色金属智能冶炼工厂采用基于工业互联网平台的云、边、端架构,建立“平台协同运营、工厂智能生产” 两个层面的业务管理控制系统,将企业大量基于传统IT 架构的信息系统作为工业互联网平台的数据源,继续发挥系统剩余价值,同时逐步推进传统信息化业务云化部署,实现企业全流程的智能生产和供应链协同。
参考架构如图1 所示:图1 有色金属智能冶炼工厂参考架构1.技术架构端:通过对生产设备进行智能化改造和成套智能装备的应用,实现全面感知和精准控制。
边:充分利用企业原有及新建控制系统数据,汇聚区域数据资源,实现边缘侧的数据分析和实时决策。
云:集成工业微服务、大数据服务、应用开发与部署等功能,实现海量异构数据汇聚与建模分析、工业经验知识软件化与模块化、各类创新应用开发与运行。
2.智能应用智能生产与管理:聚焦企业生产制造和运营管理层面,通过对实时生产数据的全面感知、实时分析、科学决策和精准执行,实现生产过程优化;通过对产品、设备、质量、能源、物流、成本等数据的分析,实现管理决策优化。
智能服务:聚焦供应链层面,通过对供需信息、制造资源等数据的分析,实现资源优化配置。
协同创新:聚焦数据价值挖掘,通过对生产过程数据和企业运营数据的分析、挖掘,不断形成创新应用。
(二)建设路径坚持“融合发展,并行推进”,循序渐进推进企业智能工厂建设进程。
1.现有工厂(1)依据实际业务特点和支撑配套条件,对企业智能制造基础进行评估,编制总体规划,考虑企业实际需求紧迫程度、基础条件和资金承受能力等因素制定实施方案,明确阶段任务目标、预期效果及详细的实施计划,分步开展建设。
(2)开展信息化标准化的建设工作,制定数据标准、流程标准、操作标准;对设备进行数字化、智能化改造,提高产线的自动化率,加装智能视频监控和智能仪表,开展成套智能装备应用,实现工厂数字化、网络化、少人化。
(3)建设综合集成信息管控平台,实现安环管理、设备管理、计划管理、调度管理、质量管理、能源管理等,实现工厂全面可视化。
(4)建设工业大数据分析平台,充分挖掘数据潜在价值,实现设备故障智能诊断、过程参数优化、生产流程优化、数字仿真优化、经营决策优化等。
以工业互联网为基础,打造具有自感知、自学习、自决策、自执行、自适应的有色金属智能冶炼工厂。
2.新建工厂依据新建企业特点和配套条件,根据可研报告、初步设计编制总体规划,考虑先进工艺、先进装备、先进信息技术以及先进制造技术等因素制定高标准、高起点、高水平的智能制造实施方案,明确阶段任务目标、预期效果及详细的实施计划,分步开展建设。
(1)基建阶段完成对智能设备的要求,完成自动化、工控网络、视频网络、安全系统、物联网等的建设,做到工厂设备智能化、过程自动化、网络化、少人化。
(2)基建后期同步开展智能生产与管理系统建设,包括经营决策、安环管理、设备管理、计划管理、调度管理、质量管理、能源管理等信息系统,实现工厂全面可视化。
(3)投产并实现达产达标后,在积累一定量数据的基础上,开始建设工业大数据分析平台,挖掘数据潜在价值,实现设备故障智能诊断、过程参数优化、生产流程优化、数字仿真优化、经营决策优化等,打造具有自感知、自学习、自决策、自执行、自适应的有色金属智能冶炼工厂。
针对现有工厂、新建工厂的特点,鼓励有条件的企业建设工业互联网平台,鼓励中小企业使用工业互联网平台。
鼓励企业以硬件、软件、数据等基础要素迁入云端为先导,快速获取数字化能力,不断变革原有体系架构和组织方式,有效运用云技术、云资源和云服务,逐步实现核心业务系统云端集成,促进跨企业云端协同。
(三)关键要素1.清洁环保通过对污染源头、排放口和厂界等的实时自动监控和虚拟工厂建设,实现对重点污染物和特征污染物的实时监测,对无组织排放、违法排放和事故排放等行为进行有效预警,自动追溯污染源头,支撑企业实现发现、分析和解决环境问题的闭环管理。
2.优质低耗通过生产过程精细化管控、质量的全流程跟踪与追溯、工艺过程的虚拟仿真,构建全流程质量管理体系,实时采集工艺过程数据和检验设备数据,实现“事后检验”向“事前预防”转变,提高质量的稳定性一致性;通过对原燃辅料、能源的在线监控、实时分析、动态调度,不断优化物料投入和能源平衡,提高资源、能源利用率。
3.安全高效通过产线的自动化改造、工业机器人的应用,减少现场操作人员,建立全区域安健环系统以及覆盖设备、人员、生产多维度的安全管理体系,实现生产安全的“实时监控、提前预警、应急响应”;通过智能生产与管理系统建设,及时发现、解决问题,提升企业运行效率与管理水平。
四、建设内容围绕物联网、云计算、大数据、人工智能、5G 等新一代信息通信技术与先进制造技术深度融合,在企业的感知层面、管控层面、供应链层面、决策层面实现新的业务模式、新的管理模式,推进企业转型升级,实现高质量发展。
(一)基础设施的数字化改造与建设结合企业生产工艺条件、工况特点,应用自动控制、智能感知等技术对沸腾炉、回转窑、闪速炉、熔池熔炼炉、电解槽等工业设备和其他基础设施进行数字化改造,完善工业网络及信息安全建设,通过生产设备的自动化、集成化、智能化改造替代人工操作,以设备改造提升和互联互通推动产线的整体升级,实现节能减排,减员增效,提高资源利用效率和优质产品率。
1.智能感知鼓励企业加快部署传感器、智能摄像机、射频识别、网关等数字化工具和设备,融合高温热管、图像识别、声音识别等关键技术,实现设备数据、产品标识数据、工厂环境数据等生产现场数据的全面采集,实时感知生产过程和关键装备运行数据和状态。
专栏1:智能仪器仪表通用仪器仪表:物料成分在线检测、烟气成分在线检测、产品外观质量检测、光谱分析仪、荧光分析仪等。
火法冶金:炉体熔池高度检测、炉窑热场图像识别、固体物料自动取样分析、料堆形态自动监测、熔体温度在线检测、炉膛温度在线检测、熔体成分在线检测等。
湿法冶金:高压釜内液位检测、溶液/料浆成分在线分析/PH 值在线检测、电势电位在线检测、管道结疤厚度判断、在线粒度分析仪、泥层探测仪、在线浊度仪、管道磨损检测仪器等。
电冶金:阴极温度在线检测、阴阳极电流在线检测、铝液与电解质水平在线检测装置、电解槽在线测温装置、热成像分析仪、电解槽极板短路自动识别等。
2.智能装备在有色冶炼生产中劳动作业强度大、作业环境恶劣(高温、多粉尘、强腐蚀、强磁场等)、人员安全风险大的熔铸、熔体开堵口、堆取料场、赤泥/尾渣堆场、电解铸造、电解槽操作、密闭容器清理等岗位,鼓励企业应用具备自我检测、自我诊断、自我调节等功能的智能装备,使用工业机器人进行熔铸加料、堆取料、扒渣、吹气、搅拌、取样、开堵口和清理等作业,降低人员劳动强度,提高生产安全性、质量稳定性和生产效率。
专栏2:智能装备通用装备:智能多功能天车、自动测温取样机器人、巡检机器人、自动取样制样装备、智能堆取料机、智能包装机、智能拆装机、金属板打磨机、智能轨道吊、AGV(自动导引运输车)、极板/铝锭/锌锭等成品自动转运机器人、产品码垛包装机器人。
火法冶金:智能抓斗天车、转炉自动捅风眼机、自动浇铸机、智能打砖机、熔体自动取样机、清结焦智能机器人、自动开堵口机、自动换枪装置、阳极板拍平机等。