本田日本工厂 能源改善 案例
《丰田改善提案》PPT课件

资材科
5.6 3.9 86%
设施管理科
3.1 5.0 100%
人事科
2.4 2.7 64%
财务科
2.5 5.0 92%
电算科 销售管理科 销售企划科 合计
2.0 3.3 2.8 3.8 5.2 5.0 6.0 5.5 80% 100% 83% 82%
提案现况管理
合理化提案登记表
序号
提案编 号
姓名 工号 部门 班组 职位 工龄 提案项目标题
提高员工参与经营的意识 1、加强公司与个人的一体感 2、提高工作热情 3、勇于参加公司经营的实践 4、企业文化的形成
问题表面化 1、使工作现场的问题能够及时暴露在表面 2、使用提案用纸作为现场问题的情报源 3、上下沟通、知晓问题 4、解决问题的起点——把握现状
提高工作现场的活力 1、提高工作场所人员的改善意识 2、高集体配合的水平 3、提高改善活动的水平 4、创造无限生机的现场 5、改善氛围的营造
收到日期 类别
是否 提案 采纳 等级
奖励金额
综合现状管理
提案目标管理
全员参与、人才育成!
——丰田中国工厂提案活动
祝大家改善成功!
感谢下 载
确定有形效果 - 降低成本 - 减少人员 - 减少工时 - 减少面积 - 减少损费、成本节减等
确定无形效果 - 比以前更安全 - 卫生、环境得到改善 - 提高品质 - 树立了企业形象等
广泛性
在本部门改善想法部分可以 利用
改善的想法可以直接利用
在部内可以广泛利用,想法 部分可以
在其他部也可利用,方案可 直独接创利性用
审查结果统计: - 各分会将所有提案的审查结果进行统计后上报公司
事 务局 - 统计上报时间次月末 提案台帐的整理,活动结果的联络: - 事务局将所有评价、得分情况通报各分会担当 - 分会改善担当将得分结果通知提案本人(次月末) - 准备实施奖赏
利用丰田问题解决方法的事例

利用丰田问题解决方法的事例一、丰田问题解决方法简介丰田问题解决方法,又称丰田生产方式(Toyota Production System,简称TPS),起源于20世纪50年代的日本丰田汽车公司。
它是一种以降低成本、提高质量和提高效率为核心的生产管理模式,通过对生产流程、库存管理、质量控制等方面的优化,实现企业的持续改进和可持续发展。
丰田问题解决方法包括以下几个核心理念:1.追求零浪费:通过降低生产过程中的浪费,提高资源利用率,降低成本。
2.Just-In-Time(JIT)生产:根据客户需求进行实时生产,减少库存积压。
3.自动化生产:利用先进技术提高生产效率,降低人为错误。
4.持续改进:不断优化生产流程,实现企业持续发展。
二、丰田问题解决方法的应用事例1.生产线问题在丰田生产方式的应用中,生产线问题是一个典型的案例。
通过引入JIT 生产和自动化技术,丰田公司成功降低了生产过程中的浪费。
例如,当生产线出现故障时,传统企业通常会选择停机维修,从而导致生产延误。
而丰田公司则采用快速换线方式,在维修的同时保持生产进行,从而减少了生产中断时间。
2.供应链管理问题丰田公司通过与供应商建立紧密的合作关系,实现供应链的协同优化。
例如,丰田公司与供应商共享生产计划和库存信息,使供应商能够根据实际需求调整生产,降低库存积压。
同时,丰田公司还会对供应商进行培训,帮助他们提高生产质量和效率。
3.质量管理问题丰田公司注重产品质量的持续提升,采用“三现主义”原则进行质量管理,即“现场、现物、现实”。
当出现质量问题时,丰田公司会立即组织团队到现场调查,针对实际情况制定改进措施。
此外,公司还推行“零缺陷”理念,鼓励员工积极参与质量管理,发现并解决问题。
4.员工培训与激励问题丰田公司注重员工的培训和发展,通过定期举办培训课程,提高员工的技能和素质。
同时,公司采用绩效考核制度,激励员工积极参与改进活动。
此外,丰田公司还鼓励员工提出建议,对优秀建议给予奖励,激发员工的创新潜能。
本田可持续发展报告2021 日文版

本田可持续发展报告2021 日文版本田在全球汽车行业拥有雄厚的基础实力,拥有庞大的用户基础和广泛的品牌影响力。
目前,本田已成为全球汽车行业中不可或缺的一部分。
本田在全球范围内积极推进可持续发展战略,取得了卓越的成果。
在可持续发展的道路上本田一直不断前进,实现了对环境资源保护、能源效率提高和循环经济的重视。
一、积极应对环境问题目前,在节能减排、环境保护方面,中国和美国等国家已经取得了明显的效果。
特别是汽车工业的发展,在促进汽车工业的可持续性发展上发挥了积极作用。
因此本田一直致力于促进汽车行业内节能减排的努力,在产品研发、生产制造、销售以及服务等方面,均不断提高环保技术,以进一步降低二氧化碳污染。
二、提升能源效率,降低碳排放本田通过对燃油发动机、电动机等的改良,提升了发动机的性能和能源效率。
2020年,本田推出了首款纯电动 SUV车型飞度 PHEV。
与前一代产品相比,飞度 PHEV在 NEDC工况下的续航里程提高了35%,百公里油耗下降了%至12 L/100 km,实现了零排放的目标。
另外,还推出了 NEDC工况下行驶里程达400公里的混合动力车型XR-V, NEDC工况下行驶里程达600公里,实现了零排放。
在2020年9月1日举行的“本田能源技术与战略研讨会”上,本田技术研发中心的相关专家表示:“本田希望通过不断优化动力系统及开发新部件、新技术等措施,来不断提高可持续发展水平及减少温室气体排放。
”此外,本田还在不断推进电动化、节能化等方面进行开发及应用革新,积极应对汽车行业节能减排带来“温室效应”。
三、构建循环经济,减少温室气体排放2020年本田进一步推进构建“节约型社会”核心,通过改善汽车的制造过程和资源消耗,通过对废弃零部件的回收再利用获得高额利润和社会财富。
从2020年起,本田将把零配件循环利用作为重要经营目标,制定相关规划管理零配件的回收与循环利用。
本田持续开展节能减排和零配件循环利用工作:2021年本田将在全球范围内展开“2021年节能减排工作”,预计到2024年实现节能减排目标。
范中志共121页文档

机 机机机机 2 3456
滚子台
一般机器工厂
总库
去半成品库
磨床 6
磨床 铣床
5
2
磨床 4
来自料堆
车床 搓丝
1
8
磨床 7
车床 3
车床 1
改进: 去半成品库
车床 3
铣床 2
磨床4 磨床5
车床1 车床1
磨床 6
磨床 7
搓丝 8
来自料堆 节约面积
立体线路图及线路分析的实例见117--125页 (六)线图分析 见126页至130页
原方法350件 改进750件
原方法30秒 改进23秒
双手操作分析的实例见150--156页 实验三:双手操作分析
三。动作分析
动作分析的实质是研究分析人在进行各种
操作的细微动作,删除无效动作,使操作
(三)流程程序分析 流程程序图由操作、检验、搬运、暂存、 贮存五种符号构成。根据研究对象的不同 可分为: 1。材料或产品流程程序图。(物型) 2。人员流程程序图(人型) 现举例说明如下: 例:一张火车票自出售、使用至回收止,
其间经过许多人之手,现用流程程序图表
示如下:
1 在票架上
(物型)
1 1 拿起并查看票价
回工作台
例3:车制长轴的物料型流程程序图 见101页至103页
流程程序图表见图5--15及图5--17。 实验一:流程程序分析(看录象做)
(四)程序分析技巧
1。分析时的六大提问(提问技术)
完成了什么? (what)
要做这,是否必要?有无其他更好的 成就?
何处做? (where)
何时做? (when)
率。
– IE是综合性的应用知识体系(技术和管理) – 注重人的因素是IE区别于其他工程学科特 – 点 之一。 – IE是系统优化技术。 – IE的面向--由微观向宏观管理。
广州本田成功的案例
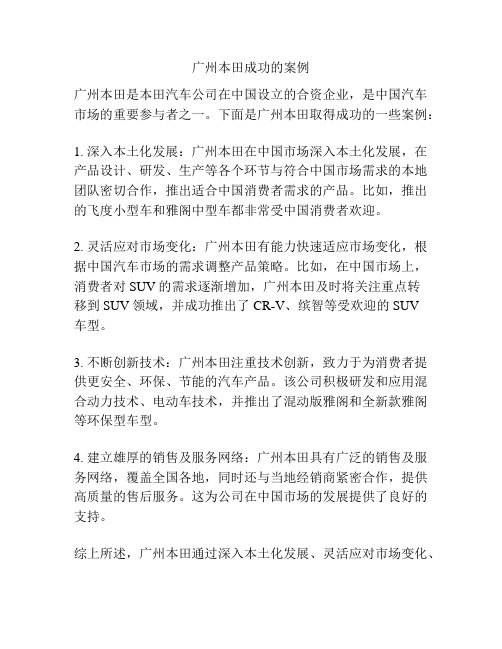
广州本田成功的案例
广州本田是本田汽车公司在中国设立的合资企业,是中国汽车市场的重要参与者之一。
下面是广州本田取得成功的一些案例:
1. 深入本土化发展:广州本田在中国市场深入本土化发展,在产品设计、研发、生产等各个环节与符合中国市场需求的本地团队密切合作,推出适合中国消费者需求的产品。
比如,推出的飞度小型车和雅阁中型车都非常受中国消费者欢迎。
2. 灵活应对市场变化:广州本田有能力快速适应市场变化,根据中国汽车市场的需求调整产品策略。
比如,在中国市场上,消费者对SUV的需求逐渐增加,广州本田及时将关注重点转
移到SUV领域,并成功推出了CR-V、缤智等受欢迎的SUV
车型。
3. 不断创新技术:广州本田注重技术创新,致力于为消费者提供更安全、环保、节能的汽车产品。
该公司积极研发和应用混合动力技术、电动车技术,并推出了混动版雅阁和全新款雅阁等环保型车型。
4. 建立雄厚的销售及服务网络:广州本田具有广泛的销售及服务网络,覆盖全国各地,同时还与当地经销商紧密合作,提供高质量的售后服务。
这为公司在中国市场的发展提供了良好的支持。
综上所述,广州本田通过深入本土化发展、灵活应对市场变化、
不断创新技术和建立雄厚的销售及服务网络等方式取得了在中国市场的成功。
广汽本田节能减排推进体系

广汽本田“节能减排”推进体系李煜零牌顾问机构高级顾问广汽本田汽车有限公司(简称广汽本田)于1998年7月1日成立,它是由广州汽车集团公司与日本本田技研工业株式会社共同出资组建。
广汽本田先后建有黄埔工厂和增城工厂两个厂区,合计占地面积160万平方米,现有员工总数为6800多人(截至2008年12月底),年生产能力达36万辆。
广汽本田目前生产的主要产品有雅阁系列轿车、奥德赛多功能系列轿车、飞度系列轿车和CITY锋范系列轿车共四大系列21种车型。
广汽本田黄埔工厂广汽本田增城工厂众所周知,汽车的制造过程需要用到大量的电,有时候还会直接使用化石燃料(煤炭、石油、天然气、液化石油气LPG等)。
不论是使用化石燃料燃烧发电还是直接投入设备中进行燃烧,都会产生大量的二氧化碳气体(CO2)。
如果这些气体没有得到有效的处理就直接排放到大气中将导致全球气候变暖,即“温室效应”,所以假如工厂能减少对电和化石燃料的用量就能有效减轻温室效应。
因此,在汽车生产过程中,需要在节能、环保方面实施有效的措施,推行循环经济管理模式。
这不仅有利于企业的可持续发展,也是企业社会责任的一种体现。
化石燃料和温室效应的产生作为众多汽车企业中的一员,广汽本田希望通过自己的企业活动,对保护地球环境作出积极的贡献。
在这样的理念引导下,广汽本田在公司内展开了全员的“节能减排”工作,围绕能源的有效利用和减少有害气体的排放开展了一系列的活动,努力打造成高效率、能耗低的“绿色工厂”。
2007年2月,广汽本田启动了全公司范围内的“安全·环保·节能”活动,并成立了总经理领导下的四个事务局,其中包括了环保事务局和节能事务局、生产与交通安全事务局及产品安全事务局等。
其中,环保事务局以及节能事务局推进的工作范围覆盖了从企业内部(包括产品、工厂、企业)到供应商以及特约销售店等行业链条。
节能减排事务局隶属于节能减排管理委员会,委员长一职由公司副总经理担任,负责批准节能减排计划、批准节能减排项目和落实节能减排工作费用,从规划和资金上给予大力支持。
【案例】日本本田汽车公司打进美国市场之谜
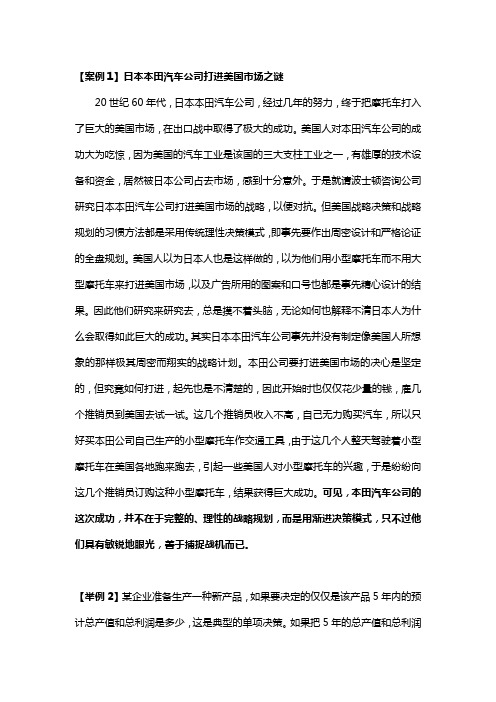
【案例1】日本本田汽车公司打进美国市场之谜20世纪60年代,日本本田汽车公司,经过几年的努力,终于把摩托车打入了巨大的美国市场,在出口战中取得了极大的成功。
美国人对本田汽车公司的成功大为吃惊,因为美国的汽车工业是该国的三大支柱工业之一,有雄厚的技术设备和资金,居然被日本公司占去市场,感到十分意外。
于是就请波士顿咨询公司研究日本本田汽车公司打进美国市场的战略,以便对抗。
但美国战略决策和战略规划的习惯方法都是采用传统理性决策模式,即事先要作出周密设计和严格论证的全盘规划。
美国人以为日本人也是这样做的,以为他们用小型摩托车而不用大型摩托车来打进美国市场,以及广告所用的图案和口号也都是事先精心设计的结果。
因此他们研究来研究去,总是摸不着头脑,无论如何也解释不清日本人为什么会取得如此巨大的成功。
其实日本本田汽车公司事先并没有制定像美国人所想象的那样极其周密而翔实的战略计划。
本田公司要打进美国市场的决心是坚定的,但究竟如何打进,起先也是不清楚的,因此开始时也仅仅花少量的钱,雇几个推销员到美国去试一试。
这几个推销员收入不高,自己无力购买汽车,所以只好买本田公司自己生产的小型摩托车作交通工具,由于这几个人整天驾驶着小型摩托车在美国各地跑来跑去,引起一些美国人对小型摩托车的兴趣,于是纷纷向这几个推销员订购这种小型摩托车,结果获得巨大成功。
可见,本田汽车公司的这次成功,并不在于完整的、理性的战略规划,而是用渐进决策模式,只不过他们具有敏锐地眼光,善于捕捉战机而已。
【举例2】某企业准备生产一种新产品,如果要决定的仅仅是该产品5年内的预计总产值和总利润是多少,这是典型的单项决策。
如果把5年的总产值和总利润通过平均,得出每年度的平均计划,这时虽然有五个分目标,但实质上仍然是单项决策。
如果既从增加稳妥性,又从尽可能地争取最大利润的角度出发,可以在前两年把更多的资金和时间放在试产试销、研究改进和设计上,通过一段时间的实验后,再定型进行大批量生产,这样第一年和第二年的利润可能会相对少一些,但是后3年经过实验和扩大再生产,利润就会高得多,而且风险也较小。
本田汽车净享地球未来

本田汽车:净享地球未来作者:张霞来源:《环球慈善》2010年第06期在举世瞩目的上海世界博览会上,本田在华合资企业之一的广汽本田以“废水零排放”作为展示案例,在“城市最佳实践区”与观众分享。
城市发展面对的难题和挑战之一,是如何平衡发展经济与保护环境之间的关系,企业作为重要的经济组织,在其中起著关键作用。
广汽本田“废水零排放”项目入驻上海世博会是首个由汽车企业提供的“水环境治理行动”案例。
事实上,除了实现“废水零排放”的绿色工厂之外,本田在环保技术、车型的研发、生产以及社会环保公益活动方面都有积极表现。
在今年的北京车展上,本田以“净享地球未来”为主题,展台以象征生命源泉的水和地球作为主设计元素,演绎本田所倡导的环保理念:移动文化与地球环境和谐共存。
本田株式会社社长伊东孝绅说:去年,我们向全球约2300万客户提供了摩托车、汽车和通用产品。
本田将发挥同时拥有摩托车、汽车和通用产品的优势,一方面努力降低现有产品的能耗,另一方面积极致力于包括太阳能电池在内的各项移动工具电动化技术的研发,全方位努力降低CO2的排放,力争成为“环保、节能技术的领跑者”。
热销车型与绿色工厂齐发力领跑汽车节能环保“除了产品生产之外,绝不生产其他物质”。
这是本田创始人本田宗一郎先生提出的对环境保护的想法,也揭示了本田对社会的责任。
本田在中国市场热销的雅阁、CRV、思铂睿、思域、飞度、锋范、奥德赛等车型都是达到国Ⅳ排放标准,并实现对车内有害污染物及重金属污染物的控制,创造出绿色驾乘环境。
第八代雅阁全新升级的i-VTEC发动机动力更加强劲,燃油经济性更高,功率提高了8%,扭矩提高了4%,油耗却下降了8%。
SUV市场上绝对的王者CRV更是“节油第一”和“环保第一”的双料冠军。
除了在热销产品上竭尽所能实现更环保,本田在企业建设的发展中,一直坚持不以牺牲环境为代价,并将“环境” 的和谐列在企业的基本精神之中。
5月25日,伊东孝绅出席了广汽本田增城工厂扩能启动仪式。
日本向世界推销节能技术

日本向世界推销节能技术2008-07-31 | 作者: | 来源:中国节能技术与产品网日本熊谷,在日本集团太平洋水泥 (Taiheiyo Cement)工厂,火炉高耸,传送带铿锵作响,输送碎石。
该厂看起来更像工业革命的遗迹,而不是一个先进的现代节省能源的典范。
该水泥厂采用先进的节能技术,利用其废热发电,供生产使用,化废为宝,大大减少了能源消耗,降低了买电数量。
来自中国和亚洲其他地方的工程师纷纷前来,学习和研究其节能设计。
这个工厂只是全日本一心一意致力于减少能源消耗的缩影。
该决心要追溯到上世纪70年代发生在这个资源贫乏的国家的石油危机。
之后,日本坚持推行一系列节能政策,使得一次能源消费与GDP比例已经是世界上最低值,过去30年日本能源消费中能效提高了30%。
日本政府的目标是进一步提高能源利用效率,通过技术创新增加能效。
现在,随着石油价格达到令人炫目的水平和世界与全球气候变暖作斗争,日本希望利用良好的节能记录,在应对紧迫的全球性议题——全球变暖中起领导作用。
在正在举行的八国集团峰会上,日本试图为出口节省电能技术作出努力,他们希望号召美国总统布什和其他领导人扩大海上钻探,遏制对冲基金和其他投资者在世界能源市场上的投机行为。
应对全球变暖“先进的技术和避免浪费的精神,让日本成为世界上最节省能源的典范。
”日本首相福田康夫(Yasuo Fukuda)在一次会议中声称,日本要“走向世界,贡献世界”。
日方将在八大工业国高峰会谈上把全球变暖的对策作为主要议题。
福田康夫已促请八国集团的领导人采取量化目标,探讨遏止二氧化碳排放量的新途径。
这是条约谈判的重点,目的在于2009年底达成一个新的全球协议。
因为有能源和气候专家称,现存协定,即始于1992年的气候条约和将于2012年届满的《京都议定书》(the Kyoto Protocol),都未见多少成功。
日本是世界上最节约能源的发达国家。
经历了20世纪70年代的能源危机之后,该国迫使自己通过政府制定能源利用率的目标及征收对石油的高额税,来节约能源。
广州本田:“废水零排放”的汽车工厂

款 审批 的主要考虑因素 ;三是提供多种模式的贷款 ,
“ 我们并不是慈善家 ,只是找 到了一种既符合市
包括节能设备供应商模式贷款、节能服务公司模式贷 场需要 ,又能够为银行带来收益的模 式。 ”兴业银行 款 、公共事业服务单位模式贷款等 ;四是根据项 目实 董事会秘书唐斌对 于能效贷款 的优 势有着清醒认识。 施 的现金流和企业 自身的经营情况来选择还款 期限 , 相对 于其他贷款而言 ,能效贷款最大的特征就 是经济
维普资讯
下降 ,自 2 0 04年 以来共节约 用 电量 10 4 万度 ,节省 的严 格 标 准 。 运行费用约 10 0 万元。在污水处理方面,黄埔工厂对
生 产生 活所产 生 的污 水进 行 分别 处 理 ,处 理 合 格率 达
与 此 同 时 ,广 州 本 田还对 上 下 游 合 作伙 伴 进 行环保方 面 的严 格要求 。广州本 田要求供应商 削减
●
度上改变了人们的印象。
水 系统 、L G供应 系统、中央空调系统 、污水处理 P
广州本 田有两大工厂 ,增城工厂和黄埔工厂 。黄 监视系统等六项能源监视系统的建设 。严谨 的管理和 埔工厂是在原有广州标致的基础上不断改造建设起来 不断的改善使得广州本田节能效果非常明显 。仅空压
的 。在 工 厂 改造 的 同时 ,广 州本 田也对 厂 区 的能 源供 机 自动控制系统一项 ,就使单位压缩空气耗 电量明显
维普资讯
S e il s n 企 业公 民 p ca r e t・ Pe
经推出便得到了各地政府 、企业 、社会的充分关注和 普遍认可 。截至 2 0 年 8月底 ,共受理 能效 项 目贷 07 款 申请超过 5 笔 ,贷,总金额达 2 7 亿元 ,每 8 .7 年可节约标准煤 2 . 04万吨,减少二 氧化碳等温 室气
日本精工推出有助提高汽车燃效新一代轴承

加剂 耐性 及 耐高温 性等 出色 的线性 聚苯 硫 醚 ( — P L P
S)。
福 特 推 出
C Ma 混 合动 力  ̄E eg概念 车 - x j n ri
美国福特公 司在 日前开幕 的2 1年 北美国际车展 01 上发布 了两款新 的混合 动力车型 ,一款是传统 的混合
动力车 ,另外一款是 一款 更为先进的插 电式混合 动力 车 ,两车都将 于2 1年上市 。这 两款 亮相车展的新车 02
热 电转化 效率达1 %的新材料 4
美国西北 大学 的化学家 、物理学 家和材料 学家携
手 于 近 日研 发 出一 种 新 材 料 ,这 种 新 材 料 展 示 出 了高
的多个干 扰。同时这个 系统 易于安装和 操作 ,还 可以 通过耳机监测到高质量的声波特征。
韩 国 开 发 出
性能 的热 电特性 ,能更有 效地将机 动车的排气 系统 、 工业生产 过程 和设 备 、太 阳光 等发 热系统产 生的废热 转 化为电力,其转化效率高达1%。该突破可广泛应用 4 于汽车 、玻璃制造等领域 。 研究 团队将岩 盐纳米 晶体溶解 在碲化 铅 内制 造出
意外损坏 和恶意破 坏往往 由于距 离远 、规模 大而面 临 很多 困难 。英国工程 技术人 员近 日开发 出了一种地 下
电缆 光 纤 感应 系统 ,有 效 地解 决 了这 一难 题 。
日本精 工近 日开发 出 了新一 代 “ 带树 脂保持器 ” 的圆锥滚子轴承 ,其摩擦损失约比原产品/, %,且 能 J0 ' 2 适应严 酷的使 用环境 。该产 品应 用于汽车变 速箱 ,有 助于提高 车辆的燃效。 由于机 械式油 泵的混合 动 力车 在依靠 马达行驶 的 情况 下 ,油泵并 不工作 ,因此短 时间 内不会 向轴承供 应润滑 油 ;加之采 用搅拌 阻力较小 的低粘度 润滑油 的 车型 日益 受到 关 注 ,因此 对 轴承 的要 求 也越 来越 严
举例说明本田公司避免浪费,合理利用资源的案例

举例说明本田公司避免浪费,合理利用资源的案例本质上的环保、节能的工厂广汽本田的增城工厂在建设时将节约能源、降低排放作为重要的目标。
广汽本田增城工厂不仅实现了中国汽车行业中第一个“废水零排放”的工厂,将生产对环境的影响降到最低,还是“本质上节能的工厂”。
广汽本田增城工厂在规划时就充分考虑了能源集约化建设。
增城工厂的能源动力站房集中在厂区的中东部,靠近各车间的负荷中心。
在工厂布局中,综合动力站房与公司最大的能耗车间——涂装相邻。
能源动力统一集中供应,在能源节约方面起到了重要作用。
在规划厂房建设时,增城工厂也充分考虑到节能的因素。
增城工厂的厂房建筑采用了节能设计,在屋顶和墙板设置了隔热层,提高了厂房的隔热性能;厂房也充分考虑了自然采光,在白天时采用自然光照明,减少了室内照明用电;综合办公楼采用双层玻璃中空隔热设计,减少了热传导,降低了空调的冷量损失,节约用电。
在能源动力站房的建设中,增城工厂也全面考虑了节能降耗,充分借鉴黄埔工厂的经验,建立了完善的能源供应及自控管理系统。
增城工厂的中央制冷站房采取高低压制冷机组混编,大小制冷机组混编,二次泵循环的系统,最大限度的降低能耗;空压站根据不同用户的需求区别供应压缩空气,采用 0.8Mpa(兆帕)和1.0Mpa两个供应系统,避免了向所有车间提供高压压缩空气所带来的能源浪费;空压站的大容量空压机采用10KV高压电来供电,最大限度的降低了电能变压过程中的能耗。
广汽本田增城工厂项目筹备之初,“建设节能环保的新工厂”就是增城工厂建设项目的目标之一。
增城工厂在环保、节能理念的指导下,在设计和建设过程中,全面地考虑了环保问题,在处理工业及生活废水的处理投入巨资,导入最先进的环境技术“膜处理技术”,废水经过处理后,全部循环使用到厂区的各相应用水点,包括:绿化、马路冲洗、涂装车间工艺用水等,在中国汽车行业中第一个实现“废水零排放”,成为本田公司中第一实现“废水零排放”的样板工厂。
灯塔工厂典型案例

灯塔工厂典型案例:日本丰田汽车公司的生产方式背景灯塔工厂是指在生产过程中以稳定的节奏发出信号,引导整个生产流程。
这种生产方式最早由日本丰田汽车公司引入并应用于其生产线上,成为了世界上最著名的生产方式之一。
丰田汽车公司在20世纪50年代初开始实施灯塔工厂模式,通过优化流程、提高效率、降低成本,并始终保持高质量的产品,使得该公司迅速崛起并成为全球领先的汽车制造商。
过程1. 流程优化在灯塔工厂模式下,丰田汽车公司对整个生产流程进行了彻底的优化。
他们通过分析每个步骤所需时间和资源,并找到了最佳的操作顺序和方法。
他们还使用了精益生产技术,以减少浪费并提高效率。
2. 节奏控制灯塔工厂的关键是保持稳定的节奏。
丰田汽车公司设立了一个称为“Takt Time”的指标来控制整个生产线上各个环节的工作速度。
Takt Time是指每个工作站应该完成一个产品所需的时间,以确保整个生产过程的平衡和协调。
3. 质量控制丰田汽车公司非常注重产品质量。
他们采用了一种称为“Jidoka”的质量控制方法,通过在生产线上引入自动化设备和传感器,及时检测和解决潜在的质量问题。
一旦检测到问题,生产线会立即停止,并通知相关人员进行修复。
4. 持续改进灯塔工厂模式强调持续改进和学习。
丰田汽车公司鼓励员工提出改进建议,并定期组织团队会议来讨论和解决问题。
他们还实施了“Kaizen”原则,即小步骤持续改进的理念,以不断提高生产效率和产品质量。
结果丰田汽车公司通过灯塔工厂模式取得了显著的成果:1.提高了生产效率:通过优化流程、控制节奏和减少浪费,丰田汽车公司显著提高了生产效率。
他们能够更快地交付产品,并根据市场需求进行灵活调整。
2.降低了成本:通过减少浪费和提高效率,丰田汽车公司成功地降低了生产成本。
他们能够以更具竞争力的价格销售产品,并获得更高的利润率。
3.提高了产品质量:丰田汽车公司在灯塔工厂模式下引入了质量控制措施,如Jidoka,确保产品质量达到最高标准。
日本丰田公司应对环境变化的办法案例分析

日本丰田公司应对环境变化的办法案例分析1.1传统技术的改进降低二氧化碳体积的基本原理是改进传统技术,它决定了二氧化碳排放量。
1.1.1动力传动相关汽油发动机、柴油发动机以及传动发展进化:通过采用新技术,如阀门式的机构、共同轨迹的系统和八速自动变速器,为充分提高效率做出了努力。
计划在2010年配备这些新型的发动机和变速器。
1.1.2汽车行驶阻力的降低基于汽车的对策主要集中在降低质量,采用更多轻金属和塑料空气阻力和轮胎的滚动阻力。
进一步地降低汽车行驶阻力需要在设计早期建立空气阻力降低方法和优化汽车结构。
1.1.3剩余能源的回收发展了传统车上浪费的能源的高效回收技术,包括对电池充电进行控制,在减速或制动过程中产生电力。
以排放热循环系统为例。
通过使用发动机排放热来提高燃油点火效率,从而加速了发机冷却温度的降低。
1.2混合动力进一步减少二氧化碳的有效方法是配备混合动力传动。
除了能减少二氧化碳排放外,这些系统还潜在降低石油消费和尾气排放,同时提高加速性能。
自1997年首次引进Prius后,丰田逐渐扩展了混合动力车的阵线。
2007年5月,丰田混合动力车的总销量打破了100万辆的记录。
将来的目标是2010后尽早达到每年销售100万辆。
1.3插入式混合动力车插入式混合动力车(PHV)的目的是通过混合动力技术和高效用电的结合进一步降低二氧化碳。
PHV是带有电池并可在家庭插座充电的混合动力车。
短途时PHV主要靠电动机驱动,而长途时就按普通的混合动力车来操作。
被路途距离的问题所限制是普通电动汽车面临的最大障碍,而PHV就没有这个问题,在不久的将来可能成为使用替换燃料的支柱。
丰田积极从事PHV的开发,目前正在日本、美国和欧洲进行示范试验。
1.4燃料电池汽车氢气被看作将来根本的清洁燃料,丰田正在继续大力发展燃料电池汽车。
诸如低温启动性,动力性能和达到高压油供应的汽油汽车的航程等技术难题被一一攻克,但是仍有汽车领域以外的课题存在,其中包括不产生二氧化碳的氢气制备方法和必需的基础建设。
kaizen案例

kaizen案例在日本经济高速发展的同时,日本企业也迫切需要找到一种持续改进的方式,以保持竞争力。
这时,日本企业家提出了一种名为“kaizen”的改进管理方式。
“Kaizen”一词是由“改变”(kai)和“好的”(zen)两个字组成。
它是一种持续的改进方法,通过不断地进行小规模的改进来达到持续发展和提高产品质量的目标。
一个典型的kaizen案例是丰田汽车公司的生产线改进。
在20世纪50年代,丰田汽车公司的汽车生产线面临着效率低下和质量不稳定的问题。
为了解决这些问题,丰田汽车公司决定采用kaizen的方式进行改进。
首先,丰田汽车公司的领导层意识到了员工参与的重要性。
他们鼓励员工积极参与到改进过程中,并给予他们权力和责任。
这种员工参与的方式被称为“班组活动”,每个班组都有自己的改进目标,并通过工作组的合作来解决问题。
其次,丰田汽车公司还采用了一种名为“5S”的工作场所整理方法来改善工作环境。
5S分别代表整理(Seiri)、整顿(Seiton)、清扫(Seiso)、清洁度维护(Seiketsu)和纪律(Shitsuke)。
通过5S的实施,工作场所的整洁度和生产效率得到了显著提升。
最后,丰田汽车公司还引入了所谓的“持久改进循环”系统。
这是一种持续追求改进的系统,通过反复进行PDCA(计划、实施、检验、行动)循环来不断优化生产线。
经过一系列的kaizen活动,丰田汽车公司取得了显著的成果。
汽车生产效率显著提高,质量稳定性得到保证,产品质量受到了广泛认可。
丰田汽车公司也因此成为了全球领先的汽车制造商之一。
丰田汽车公司的kaizen案例不仅是一个成功的例子,也是一个启示。
它告诉我们,在面对困难和挑战时,持续的改进是我们取得成功的关键。
无论是个人还是组织,只有不断改进才能不断进步。
精益生产成功案例

精益生产成功案例精益生产是一种管理理念和方法,旨在通过消除浪费,提高生产效率和品质,实现持续的改进和提升。
下面我们将介绍一些精益生产的成功案例。
1.丰田生产系统(TPS):丰田汽车公司是精益生产的开创者。
TPS主要关注生产过程中的浪费和瑕疵,并通过“Just-in-Time”(即时生产)和“Jidoka”(自动停工)的原则,实现了高效的生产和优质的产品。
TPS的成功在于其对员工参与和持续改进的鼓励,以及对质量问题的立即回应。
2.通用电气:通用电气公司采用精益生产理念,优化了其生产流程和供应链管理。
通过分析和优化整个生产过程中的活动和环节,通用电气成功地减少了废品、库存和停工时间。
精益生产的应用帮助通用电气实现了高效生产和投资回报,同时提高了产品质量和客户满意度。
3.美国电子零件制造公司(AMEC):AMEC是一家为全球电子制造企业提供电子零件生产和组装服务的公司。
AMEC采用了精益生产的原则,在生产流程中消除了多余的步骤和浪费。
该公司通过提高生产效率和质量,降低成本和交货时间,有效提升了其竞争力。
AMEC还鼓励员工积极参与,提供培训和奖励机制,以促进持续改进和创新。
4.日本曙光灯泡公司:日本曙光灯泡公司是一家生产灯泡和光源产品的公司。
该公司采用精益生产的原则,通过持续改进和创新,实现了生产效率的提高和成本的降低。
曙光灯泡公司注重员工的培训和参与,鼓励他们提出改进建议,并将其纳入生产流程中,以实现更好的效果。
通过精益生产的应用,曙光灯泡公司成功地提高了生产效率和产品质量,同时降低了生产成本。
5.伊顿公司:伊顿公司是一家全球性的动力管理企业,采用精益生产的原则优化了其生产和供应链管理。
伊顿通过减少库存、提高生产效率和质量,实现了较高的客户满意度和市场份额。
该公司还通过精益思维培养了员工的持续改进意识和能力,并鼓励他们参与决策和问题解决过程。
以上是一些成功应用精益生产的案例,这些企业通过消除浪费、提高效率和质量,实现了更高水平的竞争力和持续的发展。
汽车行业自工序完结案例
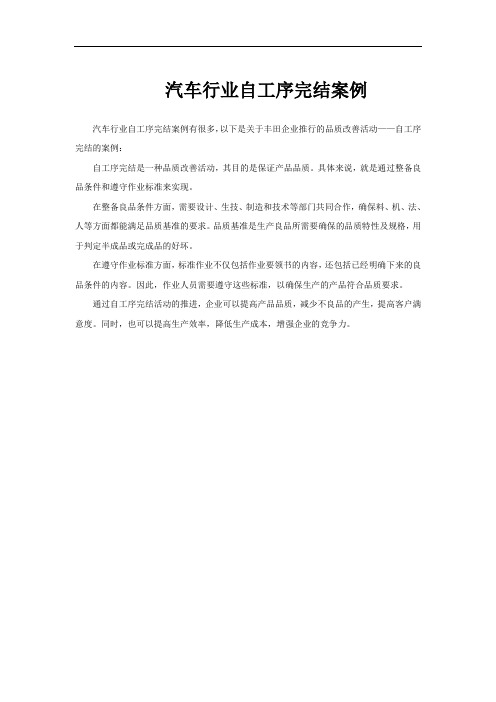
汽车行业自工序完结案例
汽车行业自工序完结案例有很多,以下是关于丰田企业推行的品质改善活动——自工序完结的案例:
自工序完结是一种品质改善活动,其目的是保证产品品质。
具体来说,就是通过整备良品条件和遵守作业标准来实现。
在整备良品条件方面,需要设计、生技、制造和技术等部门共同合作,确保料、机、法、人等方面都能满足品质基准的要求。
品质基准是生产良品所需要确保的品质特性及规格,用于判定半成品或完成品的好坏。
在遵守作业标准方面,标准作业不仅包括作业要领书的内容,还包括已经明确下来的良品条件的内容。
因此,作业人员需要遵守这些标准,以确保生产的产品符合品质要求。
通过自工序完结活动的推进,企业可以提高产品品质,减少不良品的产生,提高客户满意度。
同时,也可以提高生产效率,降低生产成本,增强企业的竞争力。
日本企业变革管理案例
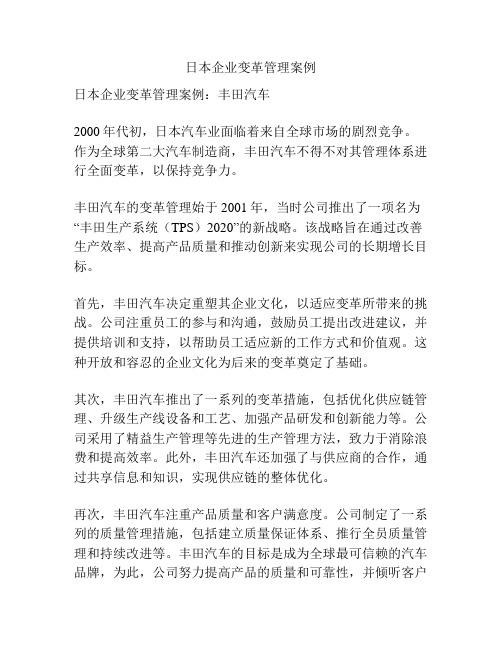
日本企业变革管理案例日本企业变革管理案例:丰田汽车2000年代初,日本汽车业面临着来自全球市场的剧烈竞争。
作为全球第二大汽车制造商,丰田汽车不得不对其管理体系进行全面变革,以保持竞争力。
丰田汽车的变革管理始于2001年,当时公司推出了一项名为“丰田生产系统(TPS)2020”的新战略。
该战略旨在通过改善生产效率、提高产品质量和推动创新来实现公司的长期增长目标。
首先,丰田汽车决定重塑其企业文化,以适应变革所带来的挑战。
公司注重员工的参与和沟通,鼓励员工提出改进建议,并提供培训和支持,以帮助员工适应新的工作方式和价值观。
这种开放和容忍的企业文化为后来的变革奠定了基础。
其次,丰田汽车推出了一系列的变革措施,包括优化供应链管理、升级生产线设备和工艺、加强产品研发和创新能力等。
公司采用了精益生产管理等先进的生产管理方法,致力于消除浪费和提高效率。
此外,丰田汽车还加强了与供应商的合作,通过共享信息和知识,实现供应链的整体优化。
再次,丰田汽车注重产品质量和客户满意度。
公司制定了一系列的质量管理措施,包括建立质量保证体系、推行全员质量管理和持续改进等。
丰田汽车的目标是成为全球最可信赖的汽车品牌,为此,公司努力提高产品的质量和可靠性,并倾听客户的反馈和需求,不断改进产品和服务。
此外,丰田汽车还注重环境可持续发展。
公司制定了一系列的环境保护措施,包括减少废物和能源消耗、推广环保技术和绿色产品等。
丰田汽车致力于成为环境友好型企业,为此不断推动技术创新和改进。
通过以上的变革措施,丰田汽车在2000年代实现了快速增长和国际化。
公司的销售额和市场份额持续增加,丰田汽车成功地超越了通用汽车,成为全球最大的汽车制造商之一。
丰田汽车的成功经验可以总结为以下几点:1. 强调企业文化的改变:丰田汽车重视员工的参与和沟通,鼓励创新和改进。
企业文化的变革为后来的变革奠定了基础。
2. 注重供应链的优化:丰田汽车加强了与供应商的合作,通过共享信息和知识,实现供应链的整体优化。
- 1、下载文档前请自行甄别文档内容的完整性,平台不提供额外的编辑、内容补充、找答案等附加服务。
- 2、"仅部分预览"的文档,不可在线预览部分如存在完整性等问题,可反馈申请退款(可完整预览的文档不适用该条件!)。
- 3、如文档侵犯您的权益,请联系客服反馈,我们会尽快为您处理(人工客服工作时间:9:00-18:30)。
第3届 Honda 绿色大会 节省能源课题
解析 Ⅲ
*曲线图中未分析到的 “变数 ”
到燃烧器点火为 止
启动时,因为直接 吸入外气,温度急 剧变化!
到煅烧器升 温至750℃为止
更替期
冬季
启动 点火 脱臭炉 升温中
第3届 Honda 绿色大会 节省能源课题
解析 Ⅲ
* 相互交换数据时发现了新的“着眼点”
正常
43 分11192℃分
65 分残業
91110012000℃℃℃℃
110 ℃ 100 ℃
43 分
90℃ 加班65分钟
【 休日加班时的变化 】
110 分 100 分 90 分 80 分
29 ℃ 92 分 正常
37 ℃
6分
86 分 补产
40 ℃ 30 ℃ 20 ℃ 10 ℃
第3届 Honda 绿色大会 节省能源课题
炉内温度
提前收工 生产结束
加班・补产
冬季
夏季
升温时间变化 时间
启动时刻 升温完毕
【 结论 】
条件变化带来的影响
・ 因启动时刻炉内温度的不同,升温完毕的时刻大幅度变化。
・ 升温速度几乎不受外界条件影响。
第3届 Honda 绿色大会 节省能源课题
解析 Ⅰ
*干燥炉的升温能力
启动时 炉内温度[℃]
130 120 110 100 90 80 70 60 50 40 30 20
第3届 Honda 绿色大会 节省能源课题
目标
升温完毕 → 开始生产之间的无效时间 ±1分钟
向『理想图』挑战,形成原理+技术
5:30 升温启动
6:26 升温完毕
6:47 炉内流动开始
5:30
升温启动
±1分
炉内流动开始 升温完毕
第3届 Honda 绿色大会 节省能源课题
解析 Ⅰ
* 炉内温度数据变化的趋势
*干燥炉升温波动的主要原因
现状把握 Ⅱ
升温时间变动原因
季
设备
节
更
替
过隔空
滤热调
器材平
料衡
调
节
人 节假开 能日始 停工时 止程刻
设 定
生产时间变动
休加提
日班前
加
收
班
工
【 季节引起的升温时间的变化 】
80 分
昇温時間
起動時炉内温度
70 分
86 ℃
98 ℃
60 分 50 分
64 分 冬季(2月)
59 分 中間期(5月)
干燥炉控制盘
第3届 Honda 绿色大会 节省能源课题
*电力消费日报
120Kwh 100Kwh
80Kwh 60Kwh 40Kwh 20Kwh
0Kwh
浪费电力 生产电力
结论
生产前升温阶段中存在着很大的电力浪费
炉内温度上升到160℃所需 要的这段时间
现状把握 Ⅰ
中途干燥炉 :2000年8月28日(星期一)
涂黑干燥炉
WAX
返修
返修干燥炉
送总装 PBS
第3届 Honda 绿色大会 节省能源课题
设备概要 Ⅰ
* 铃鹿制作所No3Line的干燥炉有6台。
溶接から
電着乾燥炉
PVC乾燥炉
前処理・電着
シーラー・PVC
全部干燥炉的能源消费量
上塗乾燥炉 LNG消耗量 = 2中9塗0乾燥炉万 Nm3/年中 塗 电力消上耗量塗 = 230 万 Kwh/年
【能源节省效果】 以2001年2月份~ 实绩进行计算
LNG消耗:33,540Nm3 /年 电力消耗:42,128KwH/年 的削减量
把它换算成原油节省量 = 51KL/年 (2,092千円/年)
第3届 Honda 绿色大会 节省能源课题
总结
干燥炉的启动时刻控制优化所带来的成果
掌握了与实际升温时间仅误差±1分钟的理论计算技术。
1区 2区 3区 4区 5区
入口
出口
热源
第3届 Honda 绿色大会 节省能源课题
*改进试作系统
对策实施
炉内温度的出力 信号变换器
炉内温度[℃] 启动
标准系统
PV
SP-( PV -
)
K1 + (PV - 15 )
K2
T=
K0
T : 升温时间K0 : 升温变化率 SP : 设定温度 K1 : 降温系数
第3届 Honda 绿色大会 节省能源课题
现状把握 Ⅰ
* 关于干燥炉的升温阶段
※ 9月分(工作日)的升温所需 时间不同而预 留的时间段?
6:26 6:35 6:47
升温完毕
⇒中涂喷房 干燥炉开始流动
开始流动
56分钟
21分钟
从干燥炉升温完毕到Body 进入干燥炉之前的这段时 间,能源被白白浪费了。
111 ℃
9分
55 分 夏夏期季((夏8)月)
120 ℃ 100 ℃ 80 ℃ 60 ℃ 40 ℃ 20 ℃ 0℃
第3届 Honda 绿色大会 节省能源课题
理想图
* 理想升温时什么样的
炉内温度
启动时刻随条件变化而变化 升温时段长度的最小化 能源浪费“0”
炉内温度
启动
生产开始
时间
自动计算
如果由人来进行计算的话,必然会出现误差 和失误,很难做到在稳定的前提下节省能源!
跟班保全人员
第3届 Honda 绿色大会 节省能源课题
*干燥炉升温波动的主要原因
升温阶段
升温完毕
现状把握 Ⅱ
炉内车体流动开始
升温时间变动原因
季
设备
节
交
替
过隔空
滤热调
器设器
备的
状
态
人
节假升
能日温
时工开
的程始
停
时
止
刻
的
设
定
生产时间变动
周生提
六 日 加
产 线
前 收
班班工
后
加
班
第3届 Honda 绿色大会 节省能源课题
改造后(2001/2/6)
5:06 5:12 5:18 5:24 5:30 5:36 5:42 5:48 5:54 6:00 6:06 6:12 6:18 6:24 6:30 5:40 5:46 5:52 5:58 6:04 6:10 6:16 6:22 6:28 6:34 6:40 6:46 6:52 6:58
活用了现有设备与机器,实现了低投资。
无需再进行计划启动时间的设定,以设备代替人工,避免了人 工误差与失误。
【 今后开展课题 】 对具有类似升温过程的前处理设备进行改造。
提前收工
加班/补产 夏季
冬季
1.58℃/分
6:40
按交点位置来制定 启动时间吧
第3届 Honda 绿色大会 节省能源课题
解析 Ⅱ
*确定干燥炉的自然冷却速度
炉内温度
下降了几度?
10分钟 4点开始
1.58℃/分
时刻X
6:40
好像这样就可以实 现自动计算了!!
第3届 Honda 绿色大会 节省能源课题
* 系统的构筑・测试
解析 Ⅲ
1区 2区 3区 4区 5区
入口
出口
炉内温度
干燥炉控制盘
时间
启动信号
冷却-升温曲线的交点 时间让电脑计算 !
第3届 Honda 绿色大会 节省能源课题
*系统的构筑・测试
炉内温度
怎么会这 样?
解析 Ⅲ
5:00
6:40
奇怪了?
升温中的 ・ 区域温度变化 ・ 调节阀的开合大小
第3届 Honda 绿色大会 节省能源课题
干燥炉点火时刻控制的优化
【 公司名称 】 本田技研工业㈱ 铃鹿制作所 涂装树脂车间 磷化3组
【 成员 】 保全Gr 菅野 拓也 等8名
第3届 Honda 绿色大会 节省能源课题
题目选定理由
干燥炉的启动是在每天的某同一时刻通 过中央控制室发出启动指令,使机器开始运 转。这种设备消耗着巨大的能源,所以有必 要事前进行“怎样将能源消耗量降到最低限 度”这一课题的研究。
本研究内容就是自动计算最合适的启动时刻, 以最节能的方式控制干燥炉的升温。
目标
升温完毕时间
无效时间 ±1分
生产开始时间
第3届 Honda 绿色大会 节省能源课题
设备概要 Ⅰ
* 铃鹿制作所No3Line的干燥炉有6台。
焊接进车
电泳干燥炉
前处理・电泳
密封胶干燥炉 密封胶
上涂干燥炉 上涂
中途干燥炉
中涂
检查・涂黑
乣 1:00 乣 2:00 乣 3:00 乣 4:00 乣 5:00 乣 6:00 乣 7:00 乣 8:00 乣 9:00 乣10:00 乣11:00 乣12:00 乣13:00 乣14:00 乣15:00 乣16:00 乣17:00 乣18:00 乣19:00 乣20:00 乣21:00 乣22:00 乣23:00 乣24:00
*干燥炉升温波动的主要原因
现状把握 Ⅱ
炉内温度 点火时温度
炉内(自然)冷却时间
提前收工
加班・休日加班
升温时间变动
生产结束
启动 升温完了
时间
【 加班时的变化 】
昇温時間 起動時炉内温度
80 分
119 ℃ 120 ℃
60 分
24680000 分分分分
40 分
20 分
111℃
55 分111 ℃ 通常
55 分
検査・SSB
换算成原油消耗量 = 3,500 KL 每年要消耗如此多的能源!
SSB乾燥炉