Cu-Fe基金刚石复合材料金刚石石墨化的热力学及动力学分析
《金刚石与磨料磨具工程》2021年总目次

2021年12月 第6期第41卷 总第246期金刚石与磨料磨具工程D i a m o n d &A b r a s i v e s E n g i n e e r i n g D e c .2021N o .6 V o l .41 S e r i a l 246‘金刚石与磨料磨具工程“2021年总目次2021年第1期(总第241期)M P C V D 金刚石的制备与应用研究进展马志斌(1) 基于孕镶金刚石颗粒的硬质合金基底的预固晶预处理新方法简小刚,马千里,唐金垚,等(5) 沉积气压对金刚石膜微米纳米结构转变的影响范冰庆,王传新,徐远钊,等(12) 钨表面激光处理对金刚石膜附着力的影响黄逸豪,马志斌(17) 用于六面顶压机的2种叶蜡石成分及传压性能对比江明全,王义鹏,杨功章,等(21) 新型组装方式烧结纯P c B N 材料邓福铭,王 浩,宋美娇,等(27) N i –C r 合金钎焊镀W 金刚石的微观结构分析苏仕超,肖 冰,王树义,等(32) S L S 和F D M S 制造超薄金刚石锯片对比研究张绍和,苏 舟,刘磊磊,等(38) C V D 金刚石刀具微铣削A A 356铝合金的磨损分析张亚博,白清顺,何 欣,等(44)单颗磨粒划擦S i C f /S i C 陶瓷基复合材料的试验研究周雯雯,王建青,赵 晶,等(51)超声振动螺线磨削砂轮表面的功率谱密度分析王秋燕,梁志强,白硕玮,等(58)18C r N i M o 7–6钢高速外圆磨削残余应力和硬度的试验分析张银霞,原少帅,王子乐,等(65) 基于动态惯性权重粒子群算法的磨削低能耗加工方法张 昆,田业冰,丛建臣,等(71) 基于机器视觉的滚抛磨块缺陷检测方法贾 坡,田建艳,杨英波,等(76) 1,2,4三氮唑和苯并三氮唑对316L 不锈钢化学机械抛光的影响王 浩,陈国美,倪自丰,等(83) 磨粒半径对金刚石研磨加工影响机制的仿真研究张桐齐,岳晓斌,雷大江,等(89) 基于热性能分析的P D C 切削齿选型试验研究王传留(95) 中国超硬材料行业2019年运行情况孙兆达,李志宏,赵兴昊,等(101)2021年第2期(总第242期)超硬磨具发展情况栗正新(1) 微波诱发热爆法制备钛铝碳结合剂金刚石复合材料代 振,张旺玺,梁宝岩,等(4) 热力耦合下轴向旋转热管砂轮的强度分析姜华飞,陈佳佳,傅玉灿,等(9) 单层C B N 砂轮感应钎焊温度的优选方法研究李奇林,丁 凯,雷卫宁,等(17) 金刚石工具用适配型C u S n Z n N i 预合金粉末的研制于 奇,马 佳,龙伟民,等(23) 静态高压国内外最新进展王义鹏,寇自力,江明全(28) 金刚石合成过程中放炮现象的分析及预警刘乾坤,何文江,杜欢龙,等(35) 低功率M P C V D 制备金刚石薄膜朱海丰,王艳坤,丁文明,等(39) 高导热金刚石/铝复合材料的真空热压制备徐 洋,沈维霞,范静哲,等(46) 金刚石–W C –C o 复合材料的高温高压合成杨亚楠,王海阔,侯志强,等(53) 金属/金刚石复合磨料在树脂磨具中的应用刘恒源,徐三魁,韩志静,等(59) 电镀金刚石线锯表面磨粒分布密度的多相机视觉检测赵玉康,毕文波,葛培琪(64)P C B N 刀具高速切削淬硬钢材料的研究叶智彪,江文清,罗 涛(69)金刚石与磨料磨具工程总第246期胎体组分对热压孕镶金刚石钻头胎体腐蚀磨损性能的影响刘志江,姚远基,王文正,等(75) 钇铝石榴石晶体化学机械抛光液成分优化研究张自力,金洙吉,慕 卿,等(82) 基于响应曲面法的304不锈钢化学机械抛光工艺参数优化刘海旭,武庆东,曹潇俊,等(89) 铸件浇冒口砂轮自适应切割王维信,孟广耀,王 哲,等(96)2021年第3期(总第243期)砂轮修整技术的发展崔仲鸣(1) 基于磨削法的金刚石磨料工具精密修磨技术崔仲鸣,冯常财,庄召鹏,等(5) 金刚石砂轮的E C D 修锐和整形研磨及其对硬脆材料的加工康喜军,田牧纯一,久保明彦,等(12) 六方氮化硼直接转化合成多晶立方氮化硼的研究王永凯,位 星,王大鹏,等(19) 聚晶金刚石的研究进展与展望邹 芹,向刚强,王 瑶,等(23) 绕丝结构砂轮磨削沟槽结构化表面唐成志,吕玉山,李兴山,等(33) 3D 打印金刚石工具的研究进展张云鹤,黄景銮,宋运运,等(40) 陶瓷结合剂研磨盘制备及研磨蓝宝石性能研究路家斌,聂小威,阎秋生,等(48) 单晶硅裂纹萌生的刻划深度研究陈自彬,葛梦然,毕文波,等(55) 金刚石线锯切割碳化硅陶瓷的机理与工艺研究陈勇彪,张松辉,张晓红,等(60) 增强纤维对超薄超硬树脂砂轮切割偏摆问题的影响杜晓旭,李大水,李彩虹,等(68) 基于金刚石固结磨具的圆柱滚子高效研磨工艺研究雷 阳,杨晓光,冯凯萍,等(74) 5G 覆铜板叠层复合材料高效切磨工艺试验研究高 航,杨 勇,许启灏,等(82) 静电雾化微量润滑粒径分布特性与磨削表面质量评价贾东洲,张乃庆,刘 波,等(89)2021年第4期(总第244期)再制造加工技术的研究进展刘文浩,陈 燕,周 睿,等(1) 航空发动机叶片再制造技术的应用及其发展趋势李文辉,温学杰,李秀红,等(8) 面向再制造的高能束射流清洗技术综述李 博,郑文光,黄 军,等(19) 垂直排列石墨烯纳米金刚石复合材料的制备及其导热性能研究杨晨光,成晓哲,穆云超,等(25) 石墨烯/纳米金刚石复合电极性能研究张金辉,李 敬,郁建元(31) 六面顶压机合成过程中线性卸压机构的设计与应用王本亮,熊莎莎,冯晓鹏,等(36) F e 基胎体中添加Z n 粉后的金刚石磨边轮组织及性能孙为云,孙长红,康 杰,等(45) 结合剂强度和不同镀层对金刚石工具出刃高度的影响朱振东,张作栋,栗晓龙,等(53) 磨粒有序排布曲面砂轮设计及磨削性能实验研究李瑞昊,石广慧,黄 辉(58) 钎焊C B N 砂轮与陶瓷C B N 砂轮磨削粉末冶金高温合金的加工性能对比研究张 曦,李本凯,丁文锋(64) 刚玉砂轮缓进深切磨削K 444镍基高温合金研究刘 爽,李 敏,丁文锋,等(72) 氮化硅陶瓷轴承外圈磨削的双目标工艺优化谢天舒(82) 基于不同纳米划痕顺序的6H –S i C 单晶片材料去除机理研究郜 伟,张银霞,黄鹏举(92) 不锈钢打磨砂带用酚醛树脂关键参数测试与分析邢 波,赵金坠,宋运运,等(98)29第6期‘金刚石与磨料磨具工程“2021年总目次2021年第5期(总第245期)特种加工技术在再制造领域中的应用与发展牛梓源,陈 燕,张泽群,等(1) 钎涂金刚石在盾构刀具再制造中的应用吴奇隆,张 雷,孙华为,等(9) 纳米金刚石粒径对N i –P 化学复合镀层耐磨性和耐腐蚀性的影响向春彦,张凤林,王 健,等(14) F e -B -C 体系金刚石单晶的高温高压制备与表征徐 洋,张壮飞,黄国峰(21) N 掺杂石墨化纳米金刚石超级电容器电极材料性能张金辉,李 敬,郁建元,等(26) 铜化学机械抛光的弱缓蚀剂研究徐 浩,宋恩敏,卞 达,等(32) 铝粉改性低温陶瓷结合剂的性能研究王延铭,侯永改,夏学锋,等(40) G H 4169超声辅助磨削表面完整性研究韩 璐,康仁科,张 园,等(46) C F R P 砂轮与钢基体砂轮高速磨削过程中的动力学特性杨淮文,冯 伟,朱建辉,等(52) 微粉金刚石钎焊砂轮磨削氧化铝陶瓷的磨削力和表面粗糙度特征李全城,沈剑云,黄国钦(59) 砂带磨削接触压强模型分析与实验王亚杰,黄 云(65) 金刚石涂层刀具加工石墨的切削性能陈守峰,王成勇,郑李娟,等(70) 镍–硼/金刚石超薄切割片的制备与性能张 兰,宋文韬,李 纳,等(77) 金刚石薄圆锯片基体的磨削工艺参数优化邱陆一,王秋燕,白硕玮,等(84) 基于剪切增稠液的高速钢铣刀刃口修整王明海,张静波,龙志凯,等(89) 基于机器人平台的固结磨料工具抛光叶片路径规划刘纪东,徐成宇,朱永伟(95)2021年第6期(总第246期)金刚石表面石墨烯的制备及应用研究进展余 威,栗正新(1) 机匣零件气道面及支板面的机器人磨抛加工曾庆双,郭皓邦,李鼎威(7) 基于环境模型优化的机器人磨抛阻抗控制王竞航,彭云峰(12) 钛合金材料页轮磨抛材料去除深度模型胡智杰,曹诗宇,黄文健,等(18) 孔隙密度对化学气相沉积泡沫金刚石导热性能的影响李崧博,于杨磊,焦增凯,等(24)M P C V D 法制备金刚石膜的工艺李思佳,冯曙光,郭胜惠,等(31) 保温时间对P r 6O 11刻蚀金刚石单晶的影响朱振东,马金明,陈冰威,等(38) 采用旋转电极的金刚石表面镀镍方法及工艺张 杨,崔仲鸣,冯常财,等(44) T i H 2对C u 60Z n 40合金结合剂结构和性能的影响韩 平,刘恒源,徐三魁,等(51) 基于灰色关联理论的R B –S i C 陶瓷电火花机械复合磨削工艺参数优化黄书强,魏宗泽,饶小双,等(56) 基于逐步回归分析法的表面粗糙度预测张家有,宋万万,白玉珍,等(63) 径向振动匹配层换能器的设计参数及模态优化郭帅宏,李 军,王欢涛(68) 电镀金刚石线锯使用性能的试验研究张晨政,葛培琪,陈自彬,等(74) 磨料质量分数对磨硅片用金刚石砂轮磨削性能的影响骆苗地,赵金伟,丁玉龙,等(80) 不同斧型钻齿切削刃角下的破岩方式李尚劼,赵 星,黄继庆,等(85)39。
Sn含量对Cu基金刚石锯片胎体组织与硬度的影响

Sn含量对Cu基金刚石锯片胎体组织与硬度的影响李文生;姜威;冯力;王磊;路阳【摘要】Cu-based diamond composite ultra thin sawing matrixes were prepared through uniaxial die pressing and hot pressing technology using Cu based powders mixed with Co, Fe, Cr and Sn. The microhardness of Cu-based matrixes, microstructure and composition of hot pressed materials were investigated by microhardness tester, OM, SEM and XRD. The effectof Sn content on microstructure and microhardness of hot pressed Cu-based materials was also studied. The results show that the average hardness (HV0.1) of Cu-based materials is the lowest with 2% Sn, which is 885.82 MPa, and the highest with 12% Sn, which is 1914.72 MPa under the sintering condition of 700℃ and 8.2 MPa. With increasing Sn content from 2% to 6%, the contents of Cu and Sn solid solution increase, which leads to the increase of the average hardness. With the increase of Sn content from 8% to 12%, the content of Cu and Sn solid solution decreases but the content of mesophase of Cu and Sn increases, resulting in a maximum average hardness. The melt Sn will outflow, when the content of Sn is over 8%.%以Cu为基体,加入Co,Fe,Cr,Sn粉末,改变Sn含量,经过模压成形与热压,制备Cu基金刚石超薄切锯胎体材料,用显微硬度仪、金相显微镜(OM)、扫描电镜(SEM)和X线衍射(XRD)表征该胎体材料的显微硬度、组织和成分,研究Sn含量对胎体组织和硬度的影响。
金刚石生长过程中Fe基合金催化机制的研究
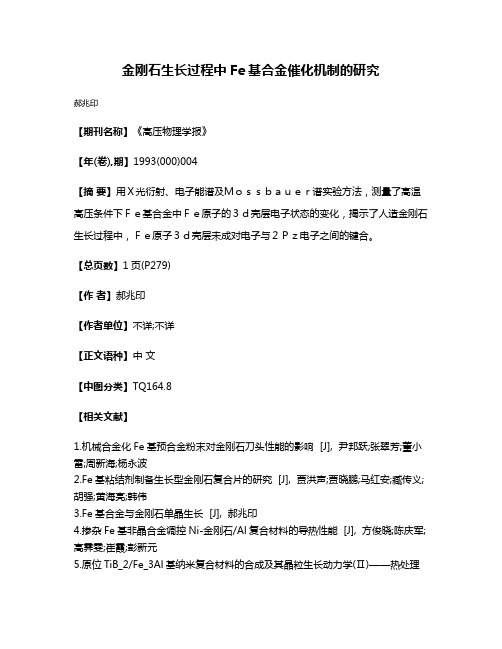
金刚石生长过程中Fe基合金催化机制的研究
郝兆印
【期刊名称】《高压物理学报》
【年(卷),期】1993(000)004
【摘要】用X光衍射、电子能谱及Mossbauer谱实验方法,测量了高温高压条件下Fe基合金中Fe原子的3d壳层电子状态的变化,揭示了人造金刚石生长过程中,Fe原子3d壳层未成对电子与2Pz电子之间的键合。
【总页数】1页(P279)
【作者】郝兆印
【作者单位】不详;不详
【正文语种】中文
【中图分类】TQ164.8
【相关文献】
1.机械合金化Fe基预合金粉末对金刚石刀头性能的影响 [J], 尹邦跃;张翠芳;董小雷;周新海;杨永波
2.Fe基粘结剂制备生长型金刚石复合片的研究 [J], 贾洪声;贾晓鹏;马红安;臧传义;胡强;黄海亮;韩伟
3.Fe基合金与金刚石单晶生长 [J], 郝兆印
4.掺杂Fe基非晶合金调控Ni-金刚石/Al复合材料的导热性能 [J], 方俊晓;陈庆军;高霁雯;崔霞;彭新元
5.原位TiB_2/Fe_3Al基纳米复合材料的合成及其晶粒生长动力学(Ⅱ)——热处理
过程中机械合金化Fe-Al-Ti-B四元粉体的结构演变与晶粒生长动力学 [J], 汤文明;郑治祥;唐红军;吴玉程;任榕;汤志鸣
因版权原因,仅展示原文概要,查看原文内容请购买。
金刚石_铜复合材料的制备及其性能研究

太原理工大学硕士研究生学位论文金刚石/铜复合材料的制备及其性能研究摘要随着电子元器件电路集成规模日益提高,电路工作产生的热量也相应升高,对与集成电路芯片膨胀系数相匹配的封装材料的热导率提出了更高的要求。
本论文以制备高热导率封装材料为目的,以金刚石颗粒、Cu粉、CuTi合金粉末和W靶材作为原材料,分别利用放电等离子体烧结工艺、无压渗透工艺以及金刚石表面镀W后放电等离子体烧结制备Cu/金刚石复合材料,利用X射线衍射分析仪(XRD)研究材料成分、采用扫描电子显微镜(SEM)观察复合材料的组织特征,并且采用激光闪射热导率测试仪测试了复合材料的热导率,着重研究了材料成分对Cu/金刚石复合材料热导率的影响。
本文首先采用无压渗透法制备Cu-Ti/金刚石复合材料。
首先将酚醛树脂和金刚石颗粒混合压制并置于真空烧结炉内800℃碳化处理得到孔隙度为50%的金刚石压坯。
然后将Cu粉和一定质量分数的Ti粉进行均匀混合后对碳化后的金刚石预制体进行包埋熔渗,冷却后得到Cu-Ti/金刚石复合材料。
实验结果表明,当Ti含量低于10wt%时,Cu合金液不能自发渗入多孔金刚石预制体中。
当Ti含量大于10wt%时,Cu-Ti/金刚石复合材料中存在界面层。
随着Ti含量的增加,Cu-Ti/金刚石复合材料致密度从83.2%逐渐增大至89.4%,金刚石颗粒与Cu基体之间的界面层厚度从0.8µm逐渐增大至4µm。
随着基体中Ti含量的增加,复合材料的热导率先增大后减小。
当Ti的质量太原理工大学硕士研究生学位论文分数为15%时,Cu/金刚石复合材料的热导率达到最大值为298W/ (m·K)。
采用扩散不匹配模型对复合材料的理论卡皮查热阻进行理论估算,将所得结果带入Hasselman-Johnson模型对不同Ti含量下制备的Cu-Ti/金刚石复合材料的理论热导率进行计算可知,当Ti含量为15wt%时,复合材料的实际热导率可以达到理论热导率的82%。
【国家自然科学基金】_石墨化程度_基金支持热词逐年推荐_【万方软件创新助手】_20140801

科研热词 碳纳米管 铱 酚醛树脂 表面官能团 腐植酸 纳米铜粒子 粉末冶金 碳纳米空心球 碳弧法 碳化行为 碳 石墨化程度 电催化活性 烧结温度 炭微球 炭/炭复合材料 活性炭纤维 氨气氧化 氧化 气孔率 显微组织 改性处理 抗氧化性能 快速制备 微晶尺寸 形成机理 工程材料 层层自组装 孔结构 各向同性石墨 各向同性度 单质汞吸附 化学液相气化渗入法 化学气相沉积法 化学气相沉积 包覆 前驱体 制备 内包钴的碳纳米颗粒 传感器 介孔碳 二甲硫醚 中空炭微球 y型碳纳米管 cu-fe基复合材料
53 54 55 56 57 58 59 60 61 62
2011年 科研热词 碳纳米管 直接甲酸燃料电池 氮掺杂 化学气相沉积 raman光谱 铜/金刚石 钌 表征 苎麻纤维 纳观结构 纳米划痕 纤维束 碳载pt催化剂 碳载ir催化剂 碳纤维 碳素纤维 碳烟 碳/碳复合材料 石墨化 相结构 界面 电催化活性 电催化性能 甲酸氧化 生物模板 煤焦 热裂解 热膨胀系数 热处理 炭载pd催化剂 炭/炭复合材料 溶胶-凝胶工艺 氧还原 氧化 氢蚀机制 氢气 柴油机 材料物理与化学 有机官能团 有序介孔碳 无金属催化剂 抗弯强度 带状炭纤维 孔隙结构 孔形态 大孔碳 大孔炭 大分子结构 合成氨 合成 各向同性沥青 发射率 推荐指数 3 2 2 2 2 1 1 1 1 1 1 1 1 1 1 1 1 1 1 1 1 1 1 1 1 1 1 1 1 1 1 1 1 1 1 1 1 1 1 1 1 1 1 1 1 1 1 1 1 1 1 1
2012年 序号 1 2 3 4 5 6 7 8 9 10 11 12 13 14 15 16 17 18 19 20 21 22 23 24 25 26 27 28 29 30 31 32 33 34 35 36 37 38 39 钎焊气氛 2 钎焊性能 2 金刚石 2 机械合金化 2 制备 2 过渡金属 1 表征方法 1 表征 1 蜂窝状堇青石 1 自组装 1 聚甲基丙烯酸甲酯 1 聚丙烯腈 1 缺陷 1 络合还原法 1 纳米碳纤维 1 纳米炭纤维 1 纳米晶尖晶石-碳复合粉体 1 空心石墨化炭 1 碳纳米管 1 碳 1 石墨烯载铱催化剂 1 石墨化碳空心球 1 电流型电化学传感器 1 电催化氧化 1 电催化性能 1 甲酸 1 炭纤维 1 氨氧化 1 杂化结构 1 有序中孔炭 1 扫描电镜 1 微结构 1 尖晶石 1 多孔碳纤维 1 共混纺丝 1 催化剂 1 低温催化法 1 产物粉体 1 乙醇 1 x射线衍射 1 x射线光电子能谱 1 pd/cmk-3 1 a1n/c复合泡沫材料 1
金刚石_铜复合材料热导率研究

金刚石/铜复合材料热导率研究*刘永正(北京航空材料研究院先进复合材料国防科技重点实验室,北京100095)摘 要: 采用放电等离子烧结法制备了金刚石/铜复合材料,并研究了增强体粒径及体积分数对复合材料热导率的影响。
结果表明复合材料的热导率随粒径的增大而略有增加,当体积分数10%时热导率最高。
X 射线衍射谱图显示制备过程中金刚石未发生石墨化。
关键词: 金刚石/铜;复合材料;热导率中图分类号: TB331文献标识码:A 文章编号:1001 9731(2009)增刊 0323 031 引 言随着电子技术的不断发展,电子元器件集成化程度越来越高,发热量也越来越大,微处理器及功率半导体器件在应用过程中常常因为温度过高而无法正常工作。
散热问题是电子信息产业发展面临的主要技术瓶颈之一[1,2]。
金刚石的室温热导率为600~2200W/(m K),热膨胀系数0.810-6/K[3]。
目前人工合成金刚石技术已十分成熟,生产成本大幅下降,使人造金刚石在复合材料中的大规模应用成为可能。
如何发挥金刚石的高导热性质来制备各种复合材料,是各国科学家广泛关注的问题[4~7]。
在金属材料中,铜具有良好的热导率,但其热膨胀系数过大,因此可以考虑以铜为基体,金刚石颗粒为增强体制备金刚石/铜复合材料。
本文采用放电等离子烧结法制备了金刚石/铜复合材料,主要研究了金刚石的粒径及体积分数对复合材料热导率的影响。
2 实 验实验用原料为电解铜粉(纯度99.7%),人造金刚石为颗粒形状不规则的普通研磨级单晶金刚石(粒径分别为20~30、40~60、60~80 m)。
将金刚石颗粒与铜粉按金刚石所占体积分数分别为5%、10%、20%、40%、60%进行配料,然后在混料机中进行混料。
将混合后的粉末装入直径 20m m的石墨模具中,在SPS 1050T放电等离子烧结炉中真空加压烧结,压力20M Pa,烧结温度900!,到温后保温5min,随炉冷却至200!后取出。
Cu40Ni30Fe20Sn5Ti5多主元合金
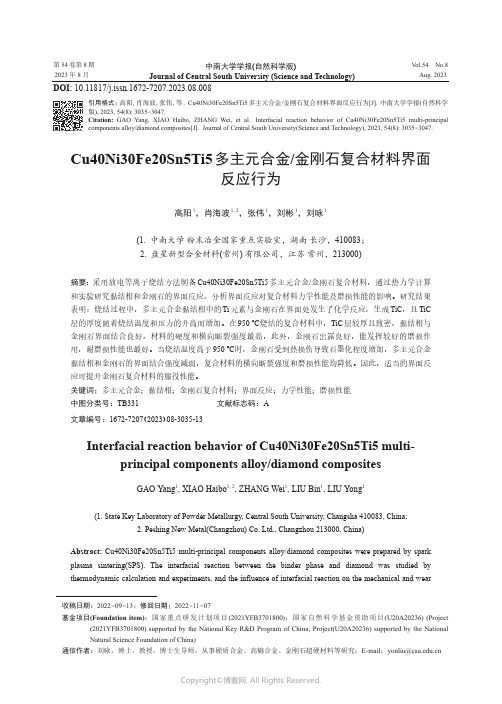
第 54 卷第 8 期2023 年 8 月中南大学学报(自然科学版)Journal of Central South University (Science and Technology)V ol.54 No.8Aug. 2023Cu40Ni30Fe20Sn5Ti5多主元合金/金刚石复合材料界面反应行为高阳1,肖海波1, 2,张伟1,刘彬1,刘咏1(1. 中南大学 粉末冶金国家重点实验室,湖南 长沙,410083;2. 盘星新型合金材料(常州) 有限公司,江苏 常州,213000)摘要:采用放电等离子烧结方法制备Cu40Ni30Fe20Sn5Ti5多主元合金/金刚石复合材料,通过热力学计算和实验研究黏结相和金刚石的界面反应,分析界面反应对复合材料力学性能及磨损性能的影响。
研究结果表明:烧结过程中,多主元合金黏结相中的Ti 元素与金刚石在界面处发生了化学反应,生成TiC ,且TiC 层的厚度随着烧结温度和压力的升高而增加。
在950 ℃烧结的复合材料中,TiC 层较厚且致密,黏结相与金刚石界面结合良好,材料的硬度和横向断裂强度最高,此外,金刚石出露良好,能发挥较好的磨损作用,耐磨损性能也最好。
当烧结温度高于950 ℃时,金刚石受到热损伤导致石墨化程度增加,多主元合金黏结相和金刚石的界面结合强度减弱,复合材料的横向断裂强度和磨损性能均降低。
因此,适当的界面反应可提升金刚石复合材料的服役性能。
关键词:多主元合金;黏结相;金刚石复合材料;界面反应;力学性能;磨损性能中图分类号:TB331 文献标志码:A 文章编号:1672-7207(2023)08-3035-13Interfacial reaction behavior of Cu40Ni30Fe20Sn5Ti5 multi-principal components alloy/diamond compositesGAO Yang 1, XIAO Haibo 1, 2, ZHANG Wei 1, LIU Bin 1, LIU Yong 1(1. State Key Laboratory of Powder Metallurgy, Central South University, Changsha 410083, China;2. Peshing New Metal(Changzhou) Co. Ltd., Changzhou 213000, China)Abstract: Cu40Ni30Fe20Sn5Ti5 multi-principal components alloy/diamond composites were prepared by spark plasma sintering(SPS). The interfacial reaction between the binder phase and diamond was studied by thermodynamic calculation and experiments, and the influence of interfacial reaction on the mechanical and wear收稿日期: 2022 −09 −13; 修回日期: 2022 −11 −07基金项目(Foundation item):国家重点研发计划项目(2021YFB3701800);国家自然科学基金资助项目(U20A20236) (Project(2021YFB3701800) supported by the National Key R&D Program of China; Project(U20A20236) supported by the National Natural Science Foundation of China)通信作者:刘咏,博士,教授,博士生导师,从事硬质合金、高熵合金、金刚石超硬材料等研究;E-mail :**************.cnDOI: 10.11817/j.issn.1672-7207.2023.08.008引用格式: 高阳, 肖海波, 张伟, 等. Cu40Ni30Fe20Sn5Ti5多主元合金/金刚石复合材料界面反应行为[J].中南大学学报(自然科学版), 2023, 54(8): 3035−3047.Citation: GAO Yang, XIAO Haibo, ZHANG Wei, et al. Interfacial reaction behavior of Cu40Ni30Fe20Sn5Ti5 multi-principal components alloy/diamond composites[J]. Journal of Central South University(Science and Technology), 2023, 54(8): 3035−3047.第 54 卷中南大学学报(自然科学版)properties of the composites was analyzed. The results show that during the sintering process, the Ti element in the binder phase reacts with diamond at the interface to form TiC, and the thickness of the TiC layer grows with the increase of sintering temperature and pressure. In the composite sintered at 950℃, the TiC layer is thick and dense, and the binder phase is well combined with diamond at the interface, leading to the highest hardness and transverse rupture strength(TRS). In addition, the diamond particles in the composite are well exposed and play a good role in grinding, and so the wear properties of the composite are also optimal. For the composites sintered above 950 ℃, the graphitization of diamond aggravates due to thermal damage, and the bonding strength between the binder phase and diamond weakens, resulting in the decrease of TRS and wear properties of the composites. Therefore, appropriate interfacial reaction improves the service properties of the diamond composites.Key words: multi-principal components alloy; binder phase; diamond composites; interfacial reaction; mechanical properties; wear properties金刚石因其独特的物理化学特性,如极高的硬度、优异的耐磨性、高强度和低热膨胀等被广泛应用于硬质材料的加工中[1−4]。
金属冶炼中的热力学与动力学研究
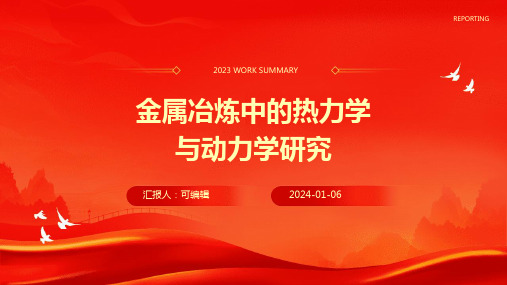
案例三
要点一
总结词
新兴金属冶炼工艺包括钛、锆、铪等稀有金属的冶炼。
要点二
详细描述
在钛冶炼中,热力学与动力学研究对于了解四氯化钛制备 过程中的反应机理和速率至关重要。锆、铪等稀有金属的 冶炼工艺中,研究重点在于探索高效分离和提纯方法,以 降低生产成本和提高资源利用率。新兴金属冶炼工艺中的 热力学与动力学研究还涉及环境友好型工艺的开发,以降 低对环境的负面影响。
PART 05
案例分析
案例一:钢铁冶炼中的热力学与动力学研究
总结词
钢铁冶炼中的热力学与动力学研究主要关注高炉炼铁、平炉炼钢和电弧炉炼钢等工艺过程。
详细描述
在高炉炼铁过程中,热力学与动力学研究有助于了解铁矿石还原反应的机理和速率,优化反应条件,提高铁产量 和降低能耗。平炉炼钢和电弧炉炼钢中,研究重点在于熔池中元素迁移、相变和夹杂物形成等过程,以实现高效 、低耗和环保的冶炼目标。
热力学第二定律
熵增加原理,表示自发反 应总是向着熵增加的方向 进行,即熵是反应自发性 的度量。
热力学第三定律
绝对熵的概念,表示在绝 对零度时,系统的熵为零 。
金属冶炼过程中的热力学原理
1 2 3
熔化与凝固
热力学原理可以解释金属的熔化凝固过程,以 及这些过程中发生的相变和能量变化。
氧化与还原
热力学原理可以预测金属在冶炼过程中是否容易 被氧化或还原,以及如何控制反应条件以获得所 需的产物。
定义
金属冶炼是指通过一系列物理和 化学过程,从矿石或其他含金属 原料中提取和纯化金属的过程。
目的
金属冶炼的目的是为了获得高纯 度、高质量的金属,以满足工业 、科技和日常生活等领域的需要 。
金属冶炼的基本流程
碳含量对高铁基胎体金刚石工具性能的影响

碳含量对高铁基胎体金刚石工具性能的影响韩娟;姚炯彬;葛启录;刘一波【摘要】采用粉末冶金方法制备高铁基胎体的金刚石工具.通过检测材料的硬度、密度、冲击韧性等性能,考察碳含量对高铁基胎体性能的影响.通过SEM,XRD等测试分析手段研究碳含量对胎体微观结构和相组成的影响.结果表明:胎体密度变化随碳含量的增加而具有波动性,碳含量为0.4%时密度达最大值7.65 g/cm3,碳含量为1%时密度获最小值7.47 g/cm3;未加入碳粉的胎体具有最高的抗冲击韧性值,随加入碳粉量的增加,冲击韧性急剧降低,含碳0.8%的胎体和含碳1%的胎体的冲击韧性值仅为1 J/cm2;加入碳粉的高铁基胎体的抗弯试样为脆性断裂.在碳含量高的情况下,胎体中孔隙多,胎体致密性差.【期刊名称】《粉末冶金材料科学与工程》【年(卷),期】2011(016)004【总页数】5页(P625-629)【关键词】铁基胎体;金刚石工具;碳含量;合金粉【作者】韩娟;姚炯彬;葛启录;刘一波【作者单位】中国钢研科技集团公司,北京100081;中国钢研科技集团公司,北京100081;中国钢研科技集团公司,北京100081;中国钢研科技集团公司,北京100081【正文语种】中文【中图分类】TF123;TQ1国内外许多研究者都开展了大量关于金刚石工具胎体的研究,根据胎体中主要成分的不同可归纳为Co基、Cu基、Fe基、WC基等几大类[1−4]。
其中铁基胎体的特点是价格最低廉,不足钴的1/50,资源上的优势和显著的经济效益使铁基胎体的研究成为金刚石工具行业的1个热点。
许多研究都集中在40%~60%的含铁量上,并通过添加不同的合金组元来实现性能的提升[5−9]。
添加组元的加入主要考虑2个方面[10−12]:一是经济性,添加剂的加入对胎体的成本不会造成大的影响;二是改善胎体性能的有效性。
在铁基配方中加入适量Ni 来提高胎体强度是1个有效的方法,但由于铁、镍会在高温常压下使金刚石发生石墨化,从而降低金刚石工具的锯切性能,所以铁基配方中的铁镍含量应控制在一定的范围内。
材料摩擦磨损分子动力学模拟的研究进展
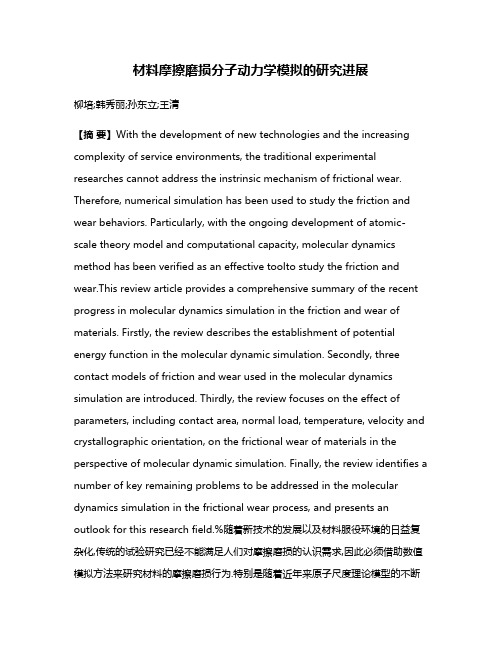
材料摩擦磨损分子动力学模拟的研究进展柳培;韩秀丽;孙东立;王清【摘要】With the development of new technologies and the increasing complexity of service environments, the traditional experimental researches cannot address the instrinsic mechanism of frictional wear. Therefore, numerical simulation has been used to study the friction and wear behaviors. Particularly, with the ongoing development of atomic-scale theory model and computational capacity, molecular dynamics method has been verified as an effective toolto study the friction and wear.This review article provides a comprehensive summary of the recent progress in molecular dynamics simulation in the friction and wear of materials. Firstly, the review describes the establishment of potential energy function in the molecular dynamic simulation. Secondly, three contact models of friction and wear used in the molecular dynamics simulation are introduced. Thirdly, the review focuses on the effect of parameters, including contact area, normal load, temperature, velocity and crystallographic orientation, on the frictional wear of materials in the perspective of molecular dynamic simulation. Finally, the review identifies a number of key remaining problems to be addressed in the molecular dynamics simulation in the frictional wear process, and presents an outlook for this research field.%随着新技术的发展以及材料服役环境的日益复杂化,传统的试验研究已经不能满足人们对摩擦磨损的认识需求,因此必须借助数值模拟方法来研究材料的摩擦磨损行为.特别是随着近年来原子尺度理论模型的不断完善和计算机运算能力的不断提高,分子动力学模拟已经成为研究材料摩擦磨损行为和机制的重要方法.本文详细综述了材料摩擦磨损分子动力学模拟的国内外研究现状.首先阐述了分子动力学模拟中势能函数的建立;其次介绍了材料摩擦磨损分子动力学模拟常用的接触模型;然后概述了采用分子动力学模拟方法研究接触面积、载荷、温度、速度和晶体取向等因素对材料摩擦磨损的影响;最后指出了目前材料摩擦磨损分子动力学模拟中存在的一些问题,并对未来发展方向进行了展望.【期刊名称】《材料科学与工艺》【年(卷),期】2017(025)003【总页数】9页(P26-34)【关键词】摩擦磨损;分子动力学;势能函数;接触模型;晶体取向【作者】柳培;韩秀丽;孙东立;王清【作者单位】哈尔滨工业大学材料科学与工程学院,哈尔滨150001;哈尔滨工业大学材料科学与工程学院,哈尔滨150001;哈尔滨工业大学材料科学与工程学院,哈尔滨150001;哈尔滨工业大学材料科学与工程学院,哈尔滨150001【正文语种】中文【中图分类】TH117.1据统计,每年因摩擦磨损造成的经济损失约占一个工业化国家GDP的1%~2%.正因为摩擦磨损与生产和经济密切联系,关于材料摩擦磨损的研究一直是当今多学科的研究热点[1-2].长期以来,关于摩擦磨损的研究大多是通过试验进行的,主要是通过模拟实际工况条件,获得摩擦磨损的特征和变化,从磨损产物、磨损表面状态、摩擦磨损对组织结构的影响等方面来研究各种摩擦磨损的机制和原理[3-5].但这种试验研究不仅耗费大量的人力、物力和财力,还有以下缺点:1)摩擦磨损是在多因素耦合作用下发生的,任何单一因素对摩擦行为的影响都可能受其他因素的干涉.因此,试验研究很难筛选出影响摩擦磨损的主要因素并定量确定单一因素对摩擦磨损的影响规律.2)摩擦磨损是一个动态过程,但试验研究很难观察到摩擦磨损过程中的动态变化过程,如位错的移动、应力应变的变化、表层和亚表层的变化等.3)摩擦磨损实际上是材料表面原子之间键合的破坏,试验研究很难从原子微观角度来揭示摩擦磨损的特性.随着计算机技术的发展,数值模拟已经成为摩擦学领域研究常用的研究手段[6].作为主要的数值模拟方法之一,分子动力学模拟方法可以通过构造比较理想的模型,定量地再现真实固体中所发生的动态过程,能够很好地弥补实际实验方法的缺陷,还可以根据研究需要轻易地改变周围环境条件和材料的性质.因此,分子动力学模拟已成为摩擦磨损研究的重要手段.目前已经成功应用于超高精密加工、微纳米元器件等研究领域.本文详细综述了材料摩擦磨损分子动力学模拟的最新研究进展,旨在为材料摩擦磨损研究提供有效方法,进而实现材料摩擦磨损性能的改善和减摩抗磨材料的设计.文章结构如下:第1节介绍了分子动力学模拟中势能函数的建立;第2节综述了材料摩擦磨损分子动力学模拟常用的接触模型;第3节重点归纳了接触面积、载荷、温度、速度和晶体取向等因素对材料摩擦磨损分子动力学模拟结果的影响;第4节指出了目前采用分子动力学模拟方法对材料摩擦磨损进行研究的过程中存在的一些问题,并对未来发展方向进行了初步展望.分子动力学模拟方法的原理是通过原子间的相互作用势,按照经典牛顿运动定律求出原子轨迹及其演化过程.因此,建立合适的势能函数是进行材料摩擦磨损分子动力学模拟的第一步,也是最关键一步.势能函数的正确与否,直接关系到模拟结果的精确性和可靠性.1.1 经典对势函数经典对势认为原子之间的相互作用是两两之间的作用,与其他粒子无关.这类函数的特点是虽然不能充分反映材料的一些真实性能(弹性模量或者热力学性质),但是能够反映粒子的一般运动轨迹.这类对势函数的典型代表就是L-J势和Morse 势.L-J势函数的表达式为[7]式中:VLJ为系统势能;ε为能量参数;σ为长度参数;r为2个原子之间的距离.在该表达式中,第1项代表短程泡利排斥力,第2项代表范德瓦尔兹相互吸引力. L-J势能函数可以用于描述稀有气体之间的相互作用,同样可以用于描述一些其他材料.关于材料摩擦学分子动力学模拟的很多显著发现都是采用L-J势.例如,Luan等[8]采用L-J势建立摩擦模型,预测了适用于宏观摩擦的连续介质模型并不适用于纳观尺度摩擦.Cieplak等[9]采用L-J势建立模型,研究了吸附单层对摩擦的效果.此外当摩擦体系中摩擦副(基体)和对磨材料(压头)的性质不同,且无严重磨损的情况下,L-J势可以很好地描述基体和压头之间的相互作用势[10].这可以帮助绝大多数的摩擦磨损模拟体系在保证模拟结果精确的情况下,减小运行时间,提高运行效率.对势除了前面提到的 L-J势之外,还有Morse势.Morse势是在用量子力学解决双原子分子震动谱时给出的分析式.值得指出的是,L-J势和Morse势的参数可直接由原子之间的平衡距离及结合能来拟合获得.因此这2种势函数对于单质和一些简单的合金材料均适用.1.2 多体势函数简单对势函数并不能充分反映多原子体系材料的一些真实性能,因此,学者们一直致力于建立能够更准确描述多原子体系相互作用的多体势函数.常用于摩擦磨损的材料主要包含3种:金属晶体,离子晶体和共价晶体.因为组成这3种晶体的键的性质不同,因此其势能函数的建立方法也不尽相同,下面分开讨论这3种材料势能函数的建立.1.2.1 金属晶体的势能函数对于金属晶体的势函数而言,目前应用最广泛的是BASKES和DAW在1984年提出的嵌入原子法(EAM)理论[7],该理论的基本思想就是将金属晶体总能分为2个部分:一部分就是晶体点阵上原子核之间的相互作用,另一部分是原子核嵌入在电子云背景中的嵌入能.可以表示为式中:Etot为系统的总势能;F表示把原子i嵌入到密度为ρi背景电子云中时的嵌入能;ρi表示原子i处的电子云密度;Φ是原子i和j之间的相互作用对势,rij 是原子i和j之间的距离.式(2)中,右边第1项是原子i在周围原子叠加电子云中的嵌入能,第2项是原子核间的对势能.上式对于纯金属和合金材料均适用,只是纯金属和合金材料的两体势函数的表达式不同.EAM势能函数已经在Pt、Au、Cu、Al和Ag等金属的摩擦磨损分子动力学模拟研究中得到了成功的应用,得到了很多金属的原子尺度摩擦现象,例如:犁沟、切削、冷焊和黏滑[11-13].EAM势函数的建立是基于电子密度球对称分布.但是这种假设在一些情形下与实际情况偏离,例如d电子轨道不满的过渡族(Fe,Co,Ni)元素,金刚石结构的半导体元素及轨道杂化的体系.为了将EAM推广到共价键和过渡金属材料,必须考虑电子云的非球形对称.于是,Baskes等[14]提出了修正型嵌入原子法(MEAM).该方法是在基体电子密度求和中引入原子电子密度分布的角度依赖因素.1.2.2 共价晶体的势能函数用于摩擦磨损的另一大类材料是共价晶体.例如SiO2、石墨、金刚石、类金刚石碳和一些氧化物.共价键有2个主要的特征:首先是结合能非常强,其次是有一个显著的方向性.为了准确反映这2个特征,研究者们建立了一种由键长、键角和扭曲度确定的势能函数.这种势能函数的典型代表是S-W模型,该模型提出最初是为了模拟类金刚石结构的Si[15].该模型能够简化原子间相互作用,但是该模型的缺点是只允许存在一种平衡的结构.为克服这一缺点,人们提出了键序势函数,通过引进一个键序参数来评价不同键的强度,因此一个势能函数可以同时描述含不同键合的平衡结构.但是,因为考虑了更多的参数,所以计算量大大增加.键序势能函数的代表是Tersoff势能函数,REBO势能函数,ReaxFF势能函数.很多共价晶体摩擦的分子动力学模拟都运用了上述势能函数.例如:Li等[16]采用Tersoff函数来描述单晶硅的相互作用势,利用分子动力学模拟方法研究了金刚石压头的切削速度对单晶硅亚表面和表面损伤的影响.Gao等[17]用REBO势能函数描述了氢终端金刚石的势能函数,研究了温度的变化对金刚石-金刚石摩擦磨损的影响.Wen等[18]采用基于ReaxFF势能函数的分子动力学模拟方法研究了水环境中Si/SiO2界面处Si的摩擦磨损机制.1.2.3 离子晶体的势能函数相比于金属晶体和共价晶体而言,对离子晶体的摩擦磨损分子动力学研究较少.离子晶体中包含2个或者更多的反向带电离子.为了对这些离子键进行模型化,需要用长程库仑力来描述原子间相互作用.但是,长程相互作用大大增加了计算时间,这就限制了分子动力学模拟的粒子数目.尽管对离子晶体摩擦磨损的直接模拟很少,但是已经有一些尝试,例如,Wyder等[19]将每一个离子抽象成由一个正离子和周围的负离子网组成,将短程力和长程力相结合来描述KBr的势函数,研究了KBr(100)表面的黏滑摩擦现象.值得说明的是,目前针对一些晶体结构相对简单的一元或者二元化合物的势能函数已经有了很多的报道,而目前针对一些结构相对复杂的三元化合物势能函数鲜有报道.随着新技术的发展,一些具有复杂晶体结构的三元化合物,例如Ti2AlN、Ti3SiC2等,已经成功用于制备抗磨减摩的薄膜材料[20]、陶瓷材料[21]和复合材料[3].因此,为了更好地理解该类化合物的抗磨减摩机制,对该类复杂化合物势能函数的建立也必定是未来的研究方向.摩擦磨损是2种材料之间的接触行为,因此建立合适的摩擦磨损分子动力学接触模型是获得正确和可靠的模拟结果的前提.目前用于摩擦磨损分子动力学的接触模型主要有平面-平面接触、粗糙峰-平面接触、粗糙峰-单峰接触3种.2.1 平面-平面接触模型图1给出了平面-平面接触模型的示意图.在该模型中,2个原子尺度平面在一定的载荷作用下以速度v彼此滑动.在整个模拟过程中,2个接触平面始终保持全部接触.Jeng等[22]建立了面心立方(111)晶面的平面-平面接触模型,采用分子动力学模拟的方法研究了“硬-软”、“软-软”2种接触体系的摩擦行为.Kartikeyan等[23]建立了Fe-Cu的平面-平面接触模型,采用分子动力学模拟方法研究了滑移速度、晶体学取向和晶体缺陷对摩擦副摩擦学特性的影响. 2.2 粗糙峰-平面接触图2给出了粗糙峰-平面接触模型的示意图.在该模型中,一个粗糙峰在一定的载荷作用下以速度v划过平面.粗糙峰可以有不同的尺寸和形状(球形、半球形、棱柱形、圆柱形).在整个模拟过程中,粗糙峰与平面始终保持接触.在很多研究微纳米器件中的超精密切削的报道中,均采用粗糙峰-平面接触模型.例如,Zhang等[24]采用分子动力学方法模拟金刚石压头在铜基体表面的滑动过程来研究纳米尺度的摩擦磨损规律.Cho等[13]建立了Ni压头与Cu表面的接触模型,采用分子动力学方法研究了原子尺度滑移中的黏滑现象.2.3 粗糙峰-粗糙峰接触图3给出了粗糙峰-粗糙峰接触模型的示意图.在该模型中,一个粗糙峰在一定的载荷作用下以速度v划过另一个粗糙峰.粗糙峰可以有不同的尺寸和形状(球形、半球形、棱柱形、圆柱形).在整个模拟过程中,只测试2个粗糙峰接触时的摩擦学特征.Stone等[25]建立了2个球形纳米Ni颗粒的接触模型,采用分子动力学方法研究了球形纳米Ni颗粒相互滑动过程中的摩擦行为.Luan等[26]建立了粗糙峰-粗糙峰接触模型,采用分子动力学方法研究了压头几何结构对黏着接触和非黏着接触过程中的接触力学.从以上分析可以看出,研究的材料体系不同,所采用的接触模型也不尽相同.一般来说,在研究纳米尺度摩擦磨损的时候,3种接触模型均适用;而在研究微纳米器件中的超精密切削时,多采用粗糙峰-平面接触模型.值得指出的是,因为宏观材料摩擦磨损可以看做是许多不同尺度、不同取向的粗糙峰彼此相互作用的结果,所以粗糙峰-粗糙峰接触模型被认为最能真实反映宏观尺度的摩擦磨损.但目前最大的挑战就是粗糙峰的尺寸和数量是多少的时候才能真正反映真实宏观尺寸的表面.这也必定是未来材料摩擦磨损分子动力学研究的重点方向之一.影响材料摩擦磨损的主要因素包括接触面积、载荷、温度、速度和晶体取向等因素.在实际的试验中,这些因素耦合作用,从而使材料摩擦磨损呈现复杂性.而分子动力学模拟法则可以确定单一因素对材料摩擦磨损的影响,因此本小节的每一部分都将对每个单一因素对材料摩擦磨损的影响进行综述.3.1 接触面积根据宏观摩擦定律,摩擦力F与接触面积比Amacro无关.但后来学者们证明,宏观尺度的接触是粗糙的,接触表面含有大量的粗糙峰接触,真实接触面积∑Aasp 远比Amacro要小很多,摩擦力与真实接触面积成线性关系.目前采用分子动力学模拟的方法对接触面积对材料摩擦磨损的影响的报道已经有很多,但是尚没有形成统一的结论.一些材料摩擦磨损分子动力学模拟的研究表明,摩擦力与接触面积成正比.例如Gao等[27]建立了金刚石的单峰摩擦分子动力学模型,模拟结果表明在无黏着和有黏着的情况下,摩擦力F与粗糙峰接触面积Aasp均成正比.Mo等[28]建立了多峰纳米接触摩擦分子动力学模型,研究了氢终端的无定形碳探针与氢终端的金刚石之间的摩擦特性,他们定义真实接触面积Areal=NatAat,Nat是界面处有化学相互作用的原子数,Aat是每个原子的平均表面积.Aasp为接触边界.研究结果表明,摩擦力F与粗糙峰接触面积Aasp不成线性关系,而与真实接触面积Areal成正比.值得说明的是,虽然Gao和Mo的研究结果均表明摩擦力与接触面积成正比,但二者对接触面积的定义不同,此外二者运用的理论也不同.Gao等建立的单峰模型中单峰模型可以用连续介质力学理论描述;而Mo等建立的是多峰纳米接触模型,此时连续介质力学并不适用,需要用原子模型进行解释.另一些材料摩擦磨损分子动力学模拟研究表明摩擦力与接触面积无关.一些学者们在石墨[29]、MoS2[30]等的摩擦磨损分子动力学模拟过程中均发现了同一现象,如图4所示,当原子级光滑的理想晶体表面间非公度接触时(即晶格完全适配)时呈现出一种超滑的现象,此时摩擦力几乎为零,因此摩擦力与接触面积无关.而当其为公度接触时,摩擦力随着接触面积的增大而增加.造成这种“超滑”现象的原因是,在非公度接触界面上,每个原子受到的剪切应力方向是不同的,但整体而言,这些力几乎可以相互抵消,因此呈现超滑现象.从以上的分析可以看出,接触面积对材料摩擦磨损的影响十分复杂,首先是对接触面积的定义还不统一,所以不同的分子动力学模拟的模型就有着不同的模拟结果;其次,摩擦力与接触面积之间的关系还取决于其他影响因素,例如表面公度.3.2 载荷宏观的摩擦定律表明摩擦力为摩擦系数μ与载荷N的乘积,即F=μN.但是当材料摩擦磨损到达原子尺度,黏着变得明显,影响载荷和摩擦力之间关系的因素也增多,因此摩擦力和载荷之间的关系将呈现出明显的复杂性.很多材料摩擦磨损分子动力学模拟研究发现摩擦力与法向载荷之间成近似的线性关系.Fille⁃ter等[31]采用分子动力学模拟的方法研究了SiC基体外延沉积单层和双层石墨烯薄膜的摩擦行为,研究表明摩擦力与载荷成近似的线性关系.Brukman等[17]采用原子力显微镜(AFM)和分子动力学模拟相结合的方法研究金刚石的单峰摩擦行为.研究结果同样表明,摩擦力与载荷之间成近似的线性关系.Xu等[10]采用分子动力学模拟的方法对半圆球的金刚石在γ-TiAl基体中的纳米压痕和摩擦磨损行为进行研究,如图5所示,金刚石压头在滑行过程中的摩擦力和磨损率与载荷之间呈线性关系.但更多的摩擦磨损分子动力学模拟研究发现摩擦力与法向载荷之间是非线性关系.如图6所示,Mo等[28]的分子动力学模拟研究发现当氢终端的无定形碳探针与氢终端的金刚石之间无黏着的时候,摩擦力与法向载荷之间呈线性关系,而有较强的黏着力的时候,摩擦力与法向载荷之间呈非线性关系.Van Wijk等[32]采用分子动力学模拟方法研究了石墨烯与石墨之间的摩擦特征发现当表面之间为公度接触时,摩擦力随载荷线性增大,而非公度接触时,在低载荷下摩擦力变化不大,高载荷下摩擦力与载荷呈指数关系.从以上的分析可以看出,摩擦力与载荷之间的关系主要受材料的本征性质、接触表面间黏附作用、表面接触方式以及塑性变形等的影响,因此,不同的材料以及不同的模拟模型得出的结论也是不一致的.3.3 温度温度能够对原子的热动能产生明显影响,因此温度对材料的摩擦磨损也会产生显著的作用.受实验设备所限,材料在极端温度(低温、高温)下的摩擦磨损特性尚缺乏系统研究.但是在分子动力学模拟中,可以很容易地控制材料模拟系统中的温度,所以分子动力学方法能够很好地研究温度对材料摩擦磨损的影响.目前大部分的材料摩擦磨损分子动力学研究表明,随着温度的升高,摩擦力会显著降低.例如,Harrison等[33]通过分子动力学模拟的方法研究了温度对氢终端的金刚石接触表面间摩擦的影响,研究结果表明随着温度的升高,摩擦力降低.Brukman等[17]采用分子动力学模拟的方法研究了温度在24~225 K内变化时对金刚石单峰摩擦行为的影响,研究结果表明,随着温度的升高,摩擦力降低. 但也有一些研究表明系统温度的升高并不会降低摩擦,例如Cook等[34]采用分子动力学模拟方法研究了多壁碳纳米管层间的摩擦行为,研究结果表明,随着温度的升高,层间原子发生非接触碰撞的频率增加,因此增加了层间摩擦力.此外还有一些材料摩擦磨损分子动力学模拟报道表明材料的摩擦与接触表面的黏附作用和公度有关.Spijker等[35]采用分子动力学模拟的方法研究了原子尺度下温度与干摩擦之间的关系.研究结果如图7所示,接触表面为公度的情况下,摩擦力随着温度的升高而降低,但是当接触表面为非公度的情况下,摩擦力随着温度的升高而升高,这主要是因为表面原子的热震荡所致.3.4 相对速度对于大多数的摩擦过程而言,相对滑移可引起表面层或者亚表面层发热、变形、化学变化甚至磨损,因此,不同的相对速度会对摩擦行为产生显著影响.一些摩擦磨损分子动力学模拟研究表明,随着相对速度的增加,摩擦力增大,磨损率增加.例如Li等[11]采用分子动力学方法研究了Au(111)表面的摩擦特性,发现当相对速度低于某一临界值时,摩擦力随着相对速度的增加而增加,当相对速度超过该临界值时,摩擦力不再随温度的增加而变化.Li等[16]采用分子动力学模拟法研究了金刚石压头的切削速度对单晶硅的切削磨损机制.如图8所示,当切削速度低于180 m/s的时候,高的切削速度导致一个更大的磨损,降低了亚表面的损伤.但是当切削速度高于180 m/s时,亚表面损伤厚度增加,因为高的切削速度导致了切削力和温度的提高,加速了位错的形核.另外有一些摩擦磨损分子动力学模拟研究表明,随着相对速度的增加,摩擦力降低,磨损率下降.Sørensen等[36]采用分子动力学方法模拟了Cu探针沿着晶体Cu表面的黏滑现象,研究结果如图9所示,相对速度的增加会使得摩擦力下降.这主要是因为当相对速度很大的时候,变形能没有得到充分的释放,所以为接下来的滑移提供了一些能量,从而降低摩擦.Hu等[37]采用分子动力学模拟的方法研究了滑移表面之间加入Cu纳米颗粒的加入对固体表面摩擦特性的影响,研究结果表明随着相对速度的增加,摩擦力降低.这主要是因为纳米颗粒的加入能够在固体表面形成一个过渡层所致.3.5 晶体取向摩擦现象,归根到底属于2种材料之间的接触力学行为,因此基体的晶体结构、表面原子结构的取向,以及压头与基体之间的取向均会对摩擦产生显著的影响.分子动力学模拟方法在研究晶体取向对摩擦磨损的影响方面有着很大的优势,因此很多学者开展了这方面的研究.不同的晶体结构,摩擦特性会有明显的不同.例如一些自润滑材料,如石墨、MoS2和无定形碳薄膜等,其自润滑的本质就是其层状的晶体结构.Matsushita等[38]采用分子动力学研究了干净石墨表面之间的原子尺度摩擦,模拟结果表明石墨呈现出在原子尺度黏滑移动和低的摩擦系数.石墨低的摩擦系数的原子尺度起源不仅仅是层与层之间的弱的结合作用,而是因为石墨的蜂巢结构.低的摩擦系数来源于薄片之间2种不同的晶格位置之间力的抵消.Miyamoto等[39]用联合量子化学和经典分子动力学的方法研究了MoS2的润滑机制.他们发现2个S层之间的主导相互作用力是库伦排斥力,直接阻止了2个MoS2层不会靠的太近.也就是MoS2层有一个好的阻止载荷的能力.Ma等[40]采用分子动力学方法研究了无。
CSB-2预合金粉质量分数和烧结温度对热压富铁基胎体力学性能的影响

CSB-2预合金粉质量分数和烧结温度对热压富铁基胎体力学性能的影响艾昆;李静仪;段隆臣;贾永江;谭松成;方小红【摘要】热压富铁基金刚石钻头具有成本低、钻速高的优点,已在钻探中广泛应用.对比相同的热压富铁基胎体配方,通过测试试样的致密度、显微硬度、抗弯强度和抗冲击韧性,研究CSB-2预合金粉质量分数和烧结温度对金刚石钻头胎体力学性能的影响.试验结果表明:添加CSB-2预合金粉的胎体性能均比单质混粉胎体性能好.随CSB-2质量分数的增加,胎体的致密度、显微硬度、抗弯强度和抗冲击韧性分别最大提高了7.68%、27.99%、94.43%和312.82%;同时,胎体粉末预合金化有利于降低胎体的热压烧结温度;为获得良好的应用效果,CSB-2质量分数应大于30%,且最佳烧结温度为940~980℃.【期刊名称】《金刚石与磨料磨具工程》【年(卷),期】2018(038)004【总页数】5页(P45-49)【关键词】预合金粉;烧结温度;金刚石钻头;富铁基胎体【作者】艾昆;李静仪;段隆臣;贾永江;谭松成;方小红【作者单位】中石化华北石油工程有限公司井下作业分公司,郑州450000;中国地质大学工程学院,武汉430074;桂林金刚石工业有限公司,广西桂林541199;中国地质大学工程学院,武汉430074;中石化华北石油工程有限公司井下作业分公司,郑州450000;中国地质大学工程学院,武汉430074;中国地质大学工程学院,武汉430074【正文语种】中文【中图分类】TG74由于铁资源丰富且价格便宜,热压富铁基金刚石钻头成为近年来金刚石工具的一个研究热点[1-5]。
要获得性能良好的铁基(富铁)金刚石复合材料,需要解决下列问题[6-9]:一是烧结温度高且控温范围窄;二是热压烧结时铁元素容易侵蚀金刚石从而降低钻头性能;三是铁粉活性大、易氧化,从而对铁基胎体性能产生严重影响。
针对上述问题,选取一种Fe质量分数40%以上,并同时含有Cu、Sn、Zn、P、稀土等元素的预合金粉CSB-2,通过在胎体配方中添加质量分数0%~50%的CSB-2预合金粉,胎体中Fe以单质粉形式、单质粉与预合金粉混合形式以及预合金粉形式加入,并分别在900、940、980、1020 ℃下进行热压烧结制备胎体试样。
超硬磨料套料钻水下钻削P110钢的磨损实验
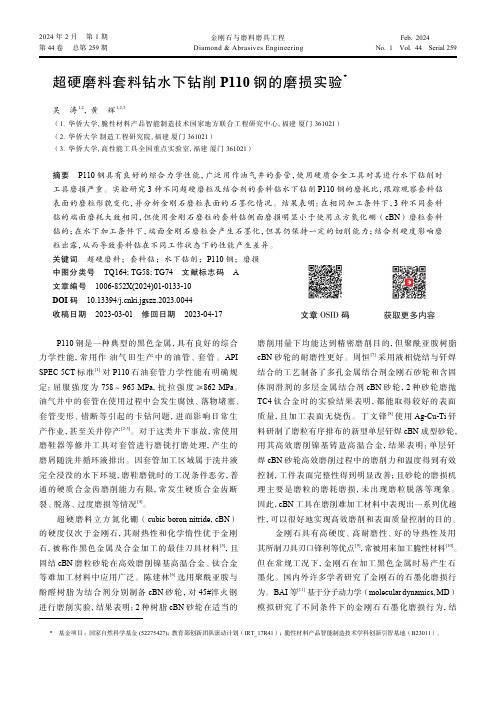
超硬磨料套料钻水下钻削P110钢的磨损实验*吴 涛1,2, 黄 辉1,2,3(1. 华侨大学, 脆性材料产品智能制造技术国家地方联合工程研究中心, 福建 厦门 361021)(2. 华侨大学 制造工程研究院, 福建 厦门 361021)(3. 华侨大学, 高性能工具全国重点实验室, 福建 厦门 361021)摘要 P110钢具有良好的综合力学性能,广泛用作油气井的套管,使用硬质合金工具对其进行水下钻削时工具磨损严重。
实验研究3种不同超硬磨粒及结合剂的套料钻水下钻削P110钢的磨耗比,跟踪观察套料钻表面的磨粒形貌变化,并分析金刚石磨粒表面的石墨化情况。
结果表明:在相同加工条件下,3种不同套料钻的端面磨耗大致相同,但使用金刚石磨粒的套料钻侧面磨损明显小于使用立方氮化硼(cBN )磨粒套料钻的;在水下加工条件下,端面金刚石磨粒会产生石墨化,但其仍保持一定的切削能力;结合剂硬度影响磨粒出露,从而导致套料钻在不同工作状态下的性能产生差异。
关键词 超硬磨料;套料钻;水下钻削;P110钢;磨损中图分类号 TQ164; TG58; TG74 文献标志码 A 文章编号 1006-852X(2024)01-0133-10DOI 码 10.13394/ki.jgszz.2023.0044收稿日期 2023-03-01 修回日期 2023-04-17P110钢是一种典型的黑色金属,具有良好的综合力学性能,常用作 油气田生产中的油管、套管。
API SPEC 5CT 标准[1]对P110石油套管力学性能有明确规定:屈服强度为758~965 MPa ,抗拉强度≥862 MPa 。
油气井中的套管在使用过程中会发生腐蚀、落物堵塞、套管变形、错断等引起的卡钻问题,进而影响日常生产作业,甚至关井停产[2-3]。
对于这类井下事故,常使用磨鞋器等修井工具对套管进行磨铣打磨处理,产生的磨屑随洗井循环液排出。
因套管加工区域属于洗井液完全浸没的水下环境,磨鞋磨铣时的工况条件恶劣,普通的硬质合金齿磨削能力有限,常发生硬质合金齿断裂、脱落、过度磨损等情况[4]。
金刚石与铜复合材料的研究

合材料热导率低。Cu 不是碳化物形成元素,通常不能润湿金刚石表面。为了实现 Cu/金刚
石的结合,通常有两种方法:一是金属化法,利用碳化物形成元素(如 W、Cr、Ti 等)在
金刚石的表面镀一层薄膜;另一种金属基体改性,即是强碳化物形成元素只记得加入到金属
基体中或制成金属粉末。这样在合适的温度下进行烧结,可以获得具有良好结合界面,致密
金、Si、 Mo、玻璃纤维 、有机物、氮化铝 等材料。但这些材 料在导热性及热膨 胀系数方面
均有一定的局限性,因此研究具有较高热导率和低膨胀系数的电子封装材料是一个亟待解决
的课题。由于复合材料可以将不同材料的优良性能结合起来,甚至会产生新的优异性能,所
以成为今年研究高热导性材料的重点。
理论分析:Cu 具有较高的热导率(k=400W/mK),是电子封装中常用的材料,但是它的热 膨胀系数较大(17.5×10-6K-1),在电子电路中会因材料热膨胀系数不匹配引起电子电路和器
件的热疲劳失效。金刚石是自然界中热导率最高的材料,常温下可达到 2200W/mK,热膨胀 系数为 1.2×10-6K-1,以铜为基体,将铜和金刚石结合起来制成复合材料,可以进一步提高材
料的热导率,并能降低其热膨胀系数。但是 Cu 和金刚石复合过程中存在两个主要的问题:
(1)界面不容易结合,难以形成牢固的结合界面;(2)结合界面处存在界面热阻,造成复
度较高的 Cu/金刚石复合材料。
Cu/金刚石复合材料中,电子控制金属的导热,声子控制金刚 石的导热。由于金刚石与金
属的润湿性差,它们的结合界面在导热时还需考虑电子—声子和声子—声子的匹配。界面处
热阻被认为是被认为是 Cu 中由于电子—声子匹配耗损产生的本征热阻和 Cu 与金刚石界面
石墨转化为金刚石的热力学分析

耿磊
( 吉林省长春市东北师范大学附属中学 130021)
摘 要: 从热力学相关数据分析了石墨转化为金刚石的实验条件,进一步能够认识石墨和金刚石这两种
同素异形体的性质差异.
关键词: 金刚石; 石墨; 热力学
中图分类号: G632
文献标识码: A
文章编号: 1008 - 0333( 2019) 10 - 0078 - 02
二、石墨的一般介绍
石墨是碳质 元 素 结 晶 矿 物,它 的 结 晶 格 架 为 六 边 形 层状结构. 每一网层间的距离为 340pm,同一网层中碳原 子的间距为 142pm. 属六方晶系,具完整的层状结构. 其具 有耐高温、导电,导热、润滑、抗热震等性质. 石墨中每个 碳原子以 sp2 杂化轨道参与邻近的 3 个碳原子以共价单键 相连,构成片层结构. 每个碳原子均有 1 个未参与杂化的 p 电子,形 成 离 域 大 π 键 ( 60 个 中 心 共 同 拥 有 60 个 电 子) . 由于石墨结构中层与层之间的结合力很弱,所以层 间易于滑动. 石墨质软且具有润滑性,是最软的晶体之一. 同 时在其结构中层与层之间原子的位置是相互错开的. 基于上 述性质,石墨被大量用来制作电极、电刷、铅笔芯等.
反应不能自发进行. 但是由于金刚石和石墨的密度不同, 金刚石密度为 3. 51g / cm3 ,石墨密度为 2. 25g / cm3 ,也就是
说石墨转变为金刚石是一个体积变小的反应. 虽然固相反应
受压强影响极小,但是加压对上述反应也是有利的. 因而可以
预言,加压将可使体积减小,从而可把石墨转化为金刚石. 热
为高温高压 将 会 极 大 地 改 变 转 化 反 应 的 熵 变 、焓 变 和 摩
过渡金属作用下的金刚石石墨化机理研究

过渡金属作用下的金刚石石墨化机理研究郭晓光;刘涛;翟昌恒;苑泽伟;金洙吉;郭东明【期刊名称】《机械工程学报》【年(卷),期】2016(52)20【摘要】从电子和原子角度解释了过渡金属对金刚石石墨化催化作用的机理,即过渡金属具有空d轨道,并且在某一面上与金刚石(111)面原子符合对准原则。
为了验证此结论,基于第一性原理建立铬、铁、钴、钛、铂、铝、铜原子与金刚石原子的作用模型,进行仿真计算,得到不同过渡金属对金刚石石墨化的影响规律。
仿真结果表明:Cr、Fe、Co、Ti、Pt作用下的金刚石结构出现不同程度的石墨化现象,而Al、Cu作用下的金刚石无石墨化现象。
不同金属作用下金刚石原子结构的平面度由小到大依次为铁、铬、钴、钛、铂、铝、铜;碳原子间方差由小到大依次为铁、铬、钴、铂、钛、铝、铜;系统能量变化由大到小的顺序依次为铁、铬、钴、铂、钛。
通过比较,铁、铬、钴原子对金刚石石墨化具有明显的催化作用,铂、钛原子有一定的催化作用,而铝、铜原子则无催化作用。
当金属具有空d轨道且与金刚石在一定面上符合对准原则,未配对电子越多,金属对金刚石石墨化的催化作用越强;反之,当金属价电子层无d轨道或d轨道电子是充满状态时,金属对金刚石石墨化无催化作用。
该研究为利用金刚石石墨化机理刃磨金刚石刀具提供了理论基础。
【总页数】7页(P23-29)【关键词】金刚石石墨化;第一性原理;未配对电子;对准原则【作者】郭晓光;刘涛;翟昌恒;苑泽伟;金洙吉;郭东明【作者单位】大连理工大学精密与特种加工教育部重点实验室;沈阳工业大学机械工程学院【正文语种】中文【中图分类】TG111【相关文献】1.过渡金属表面CVD石墨烯的生长机理研究进展 [J], 吴涛;张晓伟;蒋业华2.金刚石界面金属碳化物过渡层形成机理的研究rn(金刚石焊接机理研究之一) [J], 李岳3.金刚石界面金属碳化物过渡层强度的研究rn(金刚石焊接机理研究之二) [J], 李岳4.过渡金属Fe、Ni和Co对金刚石膜表面腐蚀作用的研究 [J], 吕宪义;金曾孙;郝世强;彭鸿雁;刘建设5.铁基作用下的金刚石石墨化研究 [J], 郭晓光;翟昌恒;金洙吉;郭东明因版权原因,仅展示原文概要,查看原文内容请购买。
六--固体无机化学概要
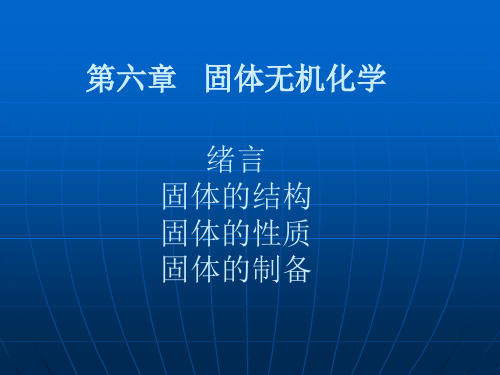
阳离子比阴离子小很多时,就容易产生此类 缺陷。如CaF2, AgCl晶体。
2)肖特基(Schottky)缺陷
产生的原因:受热激发 特点:阳离子和阴离子成对出现。
空位与间隙原子的出现和复合 是动态平衡过程。
晶体的体积增加。 阳离子和阴离子相差不大时, 就容易产生此类缺陷。如KCl晶体。 热缺陷的浓度随着温度上升而 成指数地上升。 室温时,1毫克氯化钠含有近似 1019个原子,有近似104个缺陷。
高乐玻璃窑炉专用粘土砖
新型玻璃电坩埚窑炉
三、无机晶体
金属晶体——密堆积结构 分子晶体——范德华力,氢键,干冰,硼酸 离子晶体——静电力,NaX, MgO 原子晶体——化学键, 石墨, 金刚石,黑磷
石英 无机晶体:含氧酸盐,氧化物,复合氧化物,
卤化物
离子晶体
原子晶体
分子晶体
金属晶体
晶体的特征主要表现在: (1)具有规则的几何外形; (2)均一性:晶体的质地均匀,具有确定的熔点。 (3)各向异性:晶体的导热、导电、光的透射、
研究实际固体物质的化学反应、合成方法、 晶体生长、化学组成和晶体结构;
研究固体中的缺陷及其对物理及化学性质 的影响,探索固体物质作为材料实际应用 的可能性。
固体无机化学的研究热点和前沿
新的合成方法和反应 热压技术,水热、溶剂热合成技术,熔盐中单
晶生长,LB膜,微波加热合成 非整比化合物; 高温超导混价氧化物 晶界、表面和低维化合物; 陶瓷的晶界 新型稀土化合物; 稀土间化合物,复合氧化物 价态异常元素的化合物和功能材料 Fe4+,Cu3+
差不超过15%;
在无限固溶体中两个物质的结构要相同, Al2O3-Cr2O3 (刚玉结构) MgO-CoO (NaCl结构)。
金属基复合材料的热力学与动力学研究进展

金属基复合材料的热力学与动力学研究进展金属092 张亮0914054264前言金属材料是实际应用最广泛和最重要的材料,金属材料通过可设计的复合化而构成金属基复合材料之后,不仅使其具有更高、更好的机械性能,而且具有更加优异的功能性能。
正是由于金属基复合材料具有可设计性,因而可以最大限度地发挥材料的综合性能优势:①能够实现性能优势互补或独特组合;②可以使其性能在一定范围内连续变化;③可以复合出原材料本身所不具备的性能。
由于金属基复合材料具有结构功能一体化和材料的可设计性突出优点:高比模量、比强度、抗蠕变、尺寸稳定性高和耐磨性好等一系列优异性能;且兼具阻尼、耐热性、导热优良和热膨胀系数低、高中子吸收等优异功能性;因此金属基复合材料成为高科技及环境、核能源、电子通讯、交通运输、国防建设及航天航空的重要材料,在国民经济和国防工业中具有不可替代的应用价值【1-2】。
金属基复合材料根据引入颗粒的复合化方式不同可分为两类:一类是直接引入外加颗粒作为强化相增强金属基复合材料ExSitu MM C s,另一类是反应自生强化相增强金属基复合材料( InSitu MMC s),即强化相是在复合材料制备过程中通过两种或多种元素或化合物在基体中反应自生的。
两种复合强化技术各有优缺点: 外加复合强化技术具有高的可设计性,并且增强相形状和尺寸易控等优点,但是存在增强相润湿性差而难加入,以及增强相与基体发生界面反应等缺点。
对于反应自生强化技术,由于增强相是从基体中反应自生成的,所以具有增强相热力学稳定性高、增强相与基体界面洁净以及增强相与基体界面结合好等优点,但是这种复合强化技术存在有效反应体系少、增强相尺寸和形状控制困难等缺点【3-4】。
为了进一步扩大金属基复合材料的应用范围和领域,必须克服金属基复合材料制备科学中存在的这些问题。
为此,人们针对金属基复合材料制备过程的科学问题开展了大量的研究,大多数研究主要是试验型的,以“试错法”Trial and Error M ethod 为主,这是一种预见性不强的方法,不仅曲折迂回,而且费工费时。
- 1、下载文档前请自行甄别文档内容的完整性,平台不提供额外的编辑、内容补充、找答案等附加服务。
- 2、"仅部分预览"的文档,不可在线预览部分如存在完整性等问题,可反馈申请退款(可完整预览的文档不适用该条件!)。
- 3、如文档侵犯您的权益,请联系客服反馈,我们会尽快为您处理(人工客服工作时间:9:00-18:30)。
Cu-Fe基金刚石复合材料金刚石石墨化的热力学及动力学分析张杰李文生董洪峰刘毅李亚明(兰州理工大学甘肃省有色金属新材料国家重点实验室兰州 730050)摘要利用真空热压烧结技术制备切屑大理石和花岗岩的Cu-Fe基金刚石复合材料锯片刀头。
通过热力学和动力学理论计算分析及扫描电镜、X射线衍射仪和激光拉曼光谱仪试验分析判断烧结刀头中金刚石的石墨化程度。
结果表明:1093K、13MPa真空烧结刀头中的金刚石在热力学上不稳定,金刚石-石墨相变可以自发进行;但在动力学上是稳定的,金刚石石墨化概率可忽略不计。
拉曼光谱和X射线衍射分析验证了实验中金刚石没有发生石墨化。
关键词Cu-Fe基复合材料;金刚石;石墨化;热力学;动力学0 引言从上世纪30年代粉末冶金技术进入金刚石工具制造业以来,特别是1954年人造金刚石的诞生,使得金刚石工具制造业获得了迅速的发展。
金刚石工磨具广泛应用于地质勘探、石材、机械、汽车及国防工业等各个领域制造,机械加工用的磨具、地质钻头及石材锯切工具等[1,2]。
特别是金属基金刚石工磨具作为一种特殊的复合材料,以其特有的性能在非金属及硬脆材料加工方面(70%应用于石材开采加工)获得了愈来愈广泛的应用[3,4]。
由于Co与金刚石相匹配的各种优良性能,传统的金刚石工具大部分是以Co(18-25wt.%)为粘结剂金属,但是在我国,钴资源极其匮乏,而且是重要的战略物质,这就导致钴的价格是居高不下,所以现在研究代钴配方成为一个热点[5,6,7]。
而Cu-Fe基复合材料又是近期发展起来的新型材料,它具有高强度、高导电率及良好的导热性,且硬度高、耐磨性好,受到越来越广泛的应用[8],兰州理工大学采用真空热压烧结方法制备了低钴含量的Cu-Fe基金刚石复合材料刀头,用以切屑大理石和花岗岩[2]。
金刚石的石墨化严重影响金刚石的热导率、强度、硬度以及结构等,使其在界面处容易产生应力集中而导致显微裂纹的出现,在应用过程中发生非正常断裂或金刚石早期脱落, 严重影响金刚石工磨具的使用性能。
总所周知,在低温条件下金刚石是亚稳相,而高温下便自发转化为石墨相。
本文对制备的以Cu-Fe基粉末为结合剂的金刚石刀头中金刚石的石墨化进行实验分析,并进行热力学和动力学理论验证,为金刚石工磨具制造工艺提供实验及理论依据。
1 实验方法1.1 试样制备制备Cu-Fe基粉末烧结金刚石复合材料刀头胎体的化学成分(质量分数)如表1所示。
电解铜粉粒度为200~250目、纯度≥99.7%,铁粉为氧化还原铁粉,粒度180~200目,纯度≥99.7%。
钴粉和镍粉为电解粉末,粒度250~300目、纯度≥99.7%。
金刚石选用MBD12型,粒度40~50目。
表1 基体合金的主要化学成分(wt. %)CuFeNiCo-Cr预合金粉末其它45-55 34-38 5-10 5-8 1-3粉末与金刚石按照一定比重称重后,在三维涡旋混料机(TD-2)混合1h。
然后再按试样重量称取混合粉末装模,装载在高纯高强石墨模具中的混合粉末在真空热压烧结机(RYJ-2000Z)中烧结成成形试样。
烧结压力为13MPa,烧结温度为1093K,保温时间为3min,烧结后出炉,样品随模具冷却。
1.2 试验及分析方法采用冷场发射电子显微镜(SEM-6700F)、X射线衍射仪(D8 ADV ANCE XRD)、激光拉曼光谱仪(Via-Reflex)对复合材料的断口金刚石形貌、组织以及金刚石石墨化情况进行分析。
2 实验结果2.1 断口金刚石形貌图1是在烧结温度1093K和烧结压力13MPa条件下烧结的样品断口金刚石形貌的扫描电镜图片。
由图可以看出,金刚石保持完整的六方和立方晶形,而且金刚石边缘棱角完整,表面层结构致密,没有明显被石墨化所刻蚀的迹象。
图1 断口金刚石SEM新貌A) ×80; B) ×2002.2 断口X射线分析图2为在烧结温度1093K和烧结压力13MPa条件下烧结的金刚石复合材料样品断口的X射线衍射分析结果。
烧结体的组织主要由Cu、Fe、Ni-Cr-Fe、(Fe, Cr)、Cr、 Ni 和金刚石组成,没有发现石墨衍射峰。
图2 金刚石复合材料断口XRD 分析2.3 金刚石的拉曼光谱分析图3为在烧结温度1093K 和烧结压力13MPa 条件下烧结的金刚石复合材料中金刚石的拉曼衍射光谱图。
样品中只存在1332cm -1[9]金刚石的一阶拉曼谱线,没有出现任何1581cm -1石墨的拉曼谱线,尖锐狭窄的衍射峰表明金刚石的完善的结晶有序度没有被破坏,即说明了金刚石的完整晶型没有被破坏。
所以金刚石刀头中金刚石并没有发生石墨化现象。
图3 金刚石的拉曼光谱3 分析及讨论化学反应相变过程是由其反应热力学和动力学条件所决定的,只有到反应热力学和动力学条件全部满足时反应才能发生。
以下将从热力学和动力学理论分别分析验证Cu-Fe 基粉末金刚石刀头中金刚石的石墨化进程,并与实验分析结果进行对比。
3.1 热力学分析根据经典热力学理论,由公式∫Δ+Δ=ΔP T P T VdP G G 00 (1)式中,0T G Δ为常压温度为T 时反应的自由能变化,V Δ表示反应前后体积的变化。
同时,00T T T S T H G Δ−Δ=Δ (2)式中,0T H Δ,0T S Δ分别表示为常压下稳定为T 时的反应的热焓和熵变。
则(1)式可转化为: ∫∫Δ+Δ−Δ=Δ+Δ=ΔPT T P T P T VdP S T H VdP G G 00000 (3) 同时,∫Δ+Δ=ΔT p T dT C H H 29802980 (4) ∫Δ+Δ=ΔT p T T d C S S 29802980ln (5) 因此,(3)式又可转化为()()002982982982980=ln T T P P T p p G H T S C dT T C d T VdP ΔΔ−Δ+Δ−Δ+Δ∫∫∫ (6) 根据(6)式即可计算反应在温度为T 、压力为P 时的自由能变化。
由热力学数据[10]及热膨胀系数[11]和三阶Birch-Murnaghan 状态方程[12]可以计算出在1200K 以下的金刚石石墨化的吉布斯自由能为:()()002982982982980=ln T T P P T p p G H T S C dT T C d T VdP ΔΔ−Δ+Δ−Δ+Δ∫∫∫ 263511409.05259.6880.013 2.89310 2.364109.207ln T T T T T T −−=−−+×−×+528313418200.160 4.33910 1.40310 6.32010P TP T P T P T P −−−++−×+×−×165234351.3851044.5 2.0280.076 1.68410T P P P P P −−−×−+−+×561.54010P −−× J/mol (7)此式中的压力P 的单位为GPa ,温度T 的单位为K 。
将实验条件T =1093K 和P =0.013GPa 代入(7)式计算得: P T G Δ=-5391.663J/mol (8)由以上分析可知:在实验金刚石刀头烧结过程中的烧结温度和烧结压力的热力学条件下,金刚石-石墨相变的吉布斯自由能变化为负值,金刚石-石墨相变在热力学上是可以自发进行。
但自由能之差仅是相变的动力,为金刚石-石墨相变必要条件。
在烧结过程中,金刚石-石墨相变达到平衡时,即0PT G Δ=,可得平衡压力P 和平衡温度T 的关系,这时亦忽略P 的高次项,只留一次项,则有 51641338251536210385.110320.610403.110339.4160.01820ln 207.910364.210893.2013.0688.59052.1409TT T T T T T T T T T P −−−−−−×+×+×−×+−−+×−×+−−=(9)图4为对(9)式P-T 拟合关系图。
如图中所示:在左上方为金刚石相稳定区,在右下方为石墨相稳定区,其分界线为金刚石-石墨相变平衡状态。
在本实验的1093K 烧结温度和13MPa 烧结压力的热力学条件下,落在了在平衡相图的石墨相稳定区,亦可说明此热力学条件下,金刚石的热力学不稳定性而石墨的稳定性。
计算中忽略了压力对热力学参数(如焓、熵和比热)的影响。
图4 1200K 以下的石墨-金刚石相平衡曲线3.2 动力学分析在动力学方面,金刚石和石墨都是碳原子的不同点阵排列,金刚石结构转变成石墨结构需要晶格重组,需要很大的激活能(728kJ/mol)[13]才能越过势垒变成石墨。
金刚石石墨化程度与烧结气氛中的含氧量有关,当金刚石与氧或氧化物反应生成CO 或CO 2,这将导致金刚石颗粒表面小部分被刻蚀,这种小面积的刻蚀将加快整个面的石墨化,所以烧结此种复合材料需要在真空或者惰性气体气氛中进行。
另外,金刚石石墨化的初始温度与金刚石的纯度有关,在合成金刚石的过程中,往往会使用Fe 、Ni 作为触媒来降低石墨-金刚石相变的激活能,而将少量Fe 、Ni 原子保留在合成金刚石中,这种触媒也同样的降低了金刚石石墨化的激活能[14],再者烧结的Cu-Fe 基粉末金刚石刀头中含有的Fe 、Ni 等成分,烧结过程中与金刚石表面接触也可以发挥触媒作用,这种触媒也同样的降低了金刚石石墨化的激活能。
金刚石转变为石墨相的几率( f )的一般表达式为()'exp P g a T f E G RT ⎡⎤=−−Δ⎣⎦ (10)式中,'P T G Δ为金刚石和石墨的自由能之差(即'P P T T G G Δ=−Δ);a E 为相变激活能;R 为气体常数,其值为8.31J/mol·K 。
将T =1093K 、R =8.31J/mol 、'P T G Δ=5391.663J/mol 、a E =728kJ/mol 代入(10)式计算得石墨化概率为10-8,完全可忽略不计[15]。
在本实验的真空烧结过程中,没有足够的氧,烧结温度也只有1093K 左右,而且烧结时间只有数分钟,使用的金刚石纯度也较高,这样就减少了金刚石的表面刻蚀,提高了金刚石石墨化的初始温度,增加了这种晶格重组的困难,抑制了金刚石-石墨转变。
在1093K 烧结温度和13MPa 烧结压力条件下,金刚石石墨化的几率只有10-8,并且由X 射线衍射分析和拉曼光谱分析可知烧结过程中金刚石表面确实没有石墨化发生。
因此,在1093K 烧结温度、13MPa 烧结压力的真空烧结刀头中的金刚石在热力学上是不稳定,但在动力学上是稳定。