结构件焊接通用技术要求
焊接件通用技术要求

焊接件通用技术要求(JB/ZQ4000.3-86)1.焊接结构件的长度尺寸公差见1-245c尺寸和形位公差数值.Plb,适用于焊接件和焊接足见的长度尺寸,焊接件的直线度、平面度和平行度公差见1-245c尺寸和形位公差数值.Plb,焊接件结构件的尺寸公差于形位公差等级选用见1-245c尺寸和形位公差数值.Plb2.标注和未标注角度的偏差见1-246a角度偏差.Plb,角度偏差的公差尺寸以短边为基准边,其长度从图样标明的基准点算起3.喷丸处理的焊接件,为了防止钢丸钻入焊缝,必须焊接内焊缝,并尽量避免内市和内腔,如果结构上必须有内市和内腔,则必须进行酸洗,以便达到表面除锈质量登记Be(见JB/ZQ4000.10-86附录A),对此图样需作标注4.由平炉钢制造的低碳钢结构件,可在任何温度下进行焊接,但为了避免焊接过程产生裂纹及脆性断裂,厚度较大的焊接件,焊削必须根据工艺要求,进行预热和缓冷,板厚超过30mm的重要焊接结构,焊后应立即消除内应力,消除内应力采用550-600℃回火,或200℃局部低温回火。
5.普通低合金结构制造的焊接件,必须按照焊接零件的碳当量和合金元素含量、零件的厚度、钢结构件的用途和要求进行焊前预热和焊后处理,见表1在气温较低、焊接件厚度较大的情况下焊接的普通低合金结构,应按表2的规定预热。
6.有密封内腔的焊接件,在热处理之前,应在中间隔板上适当的位置加工Φ10mm孔,使其空腔与外界相通,需在外壁上钻孔的,在热处理后要重新堵上。
7.焊缝射线探伤应符合GB3323-82的规定,要进行力学性能试验的焊接,应在图样或订伙技术要求中注明,焊缝的力学性能试验种类、试样尺寸按GB2649-81-GB2656-81的规定,试样板焊后与工件经过相同的热处理,并事先经过外观无损探伤检查。
8.焊件要进行密封性检验和耐压试验时,应按本标准要求进行,对耐压试验有要求时,应在图样或订货要求注明试验压力和试压时间。
焊接件通用技术规范

焊接件通用技术规范 TYYGROUP system office room 【TYYUA16H-TYY-TYYYUA8Q8-焊接件通用技术规范1.目的为统一普通钢结构焊接件在工厂全过程的基本要求,特制订本规范。
2.范围如顾客未对焊接件产品的加工及检验要求做出明确规定(含规范和图纸)、或已给出的规定不全时,在技术文件编制、加工制作、性能试验、检验规则以及标识、包装、运输、贮存和检验等环节须执行本规范的要求。
3.一般要求焊接件的制造应符合经规定程序批准的产品图样、技术文件和本标准的规定。
焊接件材料和焊接材料3.2.1用于焊接件材料的钢号、规格、尺寸应符合产品图样的要求。
3.2.2用于焊接件的材料(钢板型钢等)和焊接材料(焊条、焊丝、焊剂等),进厂时应按照材料标准规定,验收合格后方准使用。
3.2.3对于无牌号和无合格证书的焊接件材料和焊接材料须进行检验和鉴定,确认合格后方准使用。
3.2.4原材料下料前的形状偏差应符合有关标准规定,否则应予以矫正或另作他用(矫正可下料前校正,也可下料后校正),使之达到要求。
矫正后,钢材表面不应留有明显的损伤。
焊接零件未注公差尺寸的形位公差3.3.1零件尺寸的极限偏差手工气割的板材、型钢(角钢、工字钢、槽钢)零件尺寸的极限偏差应符合表1规定。
3.2.2.1板材零件表面的直线度和平面度公差应符合表2规定,直线度应在被测面的全长上测量。
表2 mm3.2.2.2型材零件的直线度、平面度、垂直度公差应符合表3的规定,歪扭误差应符合表4的规定。
表3mm表4图1 L—边棱长度;t—直线度3.2.2.4板材零件边棱之间的垂直度与平行度,不得大于相应尺寸的公差之半(见图2)。
图23.2.2.5型材零件切割断面对其表面的垂直度以及型材零件切割断面的平行度,不得大于型材零件切割断面之间的尺寸公差之半(见图3)。
图33.2.2.6弯曲成型的筒体零件尺寸的极限偏差、圆角和弯角,(≥5mm钢板)应符合表6规定。
焊接件通用技术要求[1]
![焊接件通用技术要求[1]](https://img.taocdn.com/s3/m/bbc97732aaea998fcc220e20.png)
6.钩头键与楔键装配后,工作面上的接触率应在70%以上,其不接触部分不得集中于一段.装配后外露尺寸应为斜面长度的
10-15%(不包括钩头).
7.花键或齿形离合器的装配,单齿分度加工的矩形花键或齿形离合器的工作面研合后,同时接触的齿数不得少于2/3;接触
≥150
600-650回火
4MnMoVB
≥150
在气温较低、焊接件厚度较大的情况下焊接的普通低合金结构,应按表2的规定预热.
表2 :
钢板厚度mm
焊接气温℃
预热温度℃
≤16
-10以下
100-150
16-24
-5以下
100-150
24-40
0以下
任何温度
>40
0以下
任何温度
6.有密闭内腔的焊接件,在热处理之前,应在中间隔板上适当的位置加工Φ10mm孔,使其空腔与外界相通.需在外壁上钻孔的,
和试压时间.
4、涂装通用技术条件(JB/ZQ4000.10-88)
1.涂装前对物体的表面要求应符合本标准的规定.
2.除锈后的金属表面与涂底漆的间隔时间不得大于6h,酸洗处理表面与第一次涂底漆时间不少
于48h,但无论间隔时间多少,涂漆前表面不得有锈蚀或污染.
3.铆接件相互接触的表面,在联接前必须涂厚度30-40μm防锈漆.由于加工或焊接损坏的底漆,
±6
±8
圆角半径、倒角高度未注公差mm
公称尺寸
加工方法
切削加工
冷作成形
0.5-3(≤)
±0.2
±0.2
3-6
±0.5
±1
焊接件通用技术要求精选全文完整版

可编辑修改精选全文完整版焊接件通用技术要求一、主题内容与适用范围本标准规定了本公司产品焊接件的技术要求,试验方法和检验规则;本标准适用于本公司生产的各机型农机及其它焊接件的制造和检验;若本标准规定与图纸要求相矛盾时,应以图纸要求为准;本标准适用于手工电弧焊、CO2气体保护焊等焊接方法制造的焊接件;二、技术要求1、材料用于制造组焊件的原材料钢板、型钢和钢管等、焊接材料焊条、焊丝、焊剂、保护气体等进厂时,须经检验部门根据制造厂的合格证明书验收后,才准入库;对无牌号、无质证书的原材料和焊材,必须进行检验和鉴定;其成份和性能符合要求时方准使用;焊接材料:1焊条、焊丝应存放于干燥、通风良好的库房内,各类焊条必须分类、分牌号堆放,避免混乱;搬运过程轻拿轻放,不要损伤药皮;焊条码放不可过高2仓库内,保持室温在0°C以上,相对湿度小于60%;3各类存储时,必须离地面高300mm,离墙壁300mm以上存放,以免受潮;4一般焊条一次出库量不能超过两天的用量,已经出库的焊条,必须要保管好;焊条使用前应按其说明书要求进行烘焙,重复烘焙不得超过两次;原材料各种钢材在划线前,不能有较大的变形,其形状公差不得超出下列规定:1钢板的平面度不应超过表1规定表1 钢板平面度公差值f2型材的直线度和垂直度公差不超过表2的规定表23歪扭不超过表2的规定,当超过规定,本公司无法矫正时,经检验部门同意,可用于次要结构;下料:尺寸偏差:钢材可采用机械剪切、气割、等离子切割、火焰切割、激光切割等下料方法,零件切割后的尺寸偏差应符合下列规定:剪板机下料零件尺寸的极限偏差按表3规定:气割、等离子切割、火焰切割的零件尺寸的极限偏差按表4规定表3 剪板机下料零件尺寸的极限偏差mm表4 气割、等离子切割、火焰切割零件尺寸的极限偏差mm当板厚小于或等于18mm时,气割孔直径尺寸的极限偏差按表5规定:当板厚>18-30时,极限偏差按表5放大;当板厚>30时,极限偏差按表5放大1mm;表5气割孔直径尺寸极限偏差mmδ≤18零件的形位公差应符合下列规定1板材零件表面的直线度与平面度公差应符合表6规定;直线度应在被测面全长上测量; 表62型材角钢、槽钢、工字钢零件的直线度、平面度、垂直度及歪扭公差应符合表7规定; 表73零件机械切割的边棱,不应有高度大于的毛刺和深度大于1mm的划痕;零件气割边棱,不应有裂纹、氧化渣,割痕深度不得大于表8规定表82、焊接参数选择手工电弧焊:焊条直径:焊条直径是根据焊件厚度、焊接位置、接头形式、焊接层数等进行选择的;厚度较大的焊件,搭接和 T 形接头的焊缝应选用直径较大的焊条;对于小坡口焊件,为了保证底层的熔透,宜采用较细直径的焊条,如打底焊时一般选用Φ2.5mm 或Φ3.2mm 焊条;不同的焊接位置,选用的焊条直径也不同,通常平焊时选用较粗的Φ~mm 的焊条,立焊和仰焊时选用Φ~mm 的焊条;横焊时选用Φ~mm 的焊条;对于特殊钢材,需要小工艺参数焊接时可选用小直径焊条;根据工件厚度选择时,可参考表9;对于重要结构应根据规定的焊接电流范围根据热输入确定参照表10焊接电流与焊条直径的关系来决定焊条直径;表9 根据工件厚度选择焊接直径焊接电流:焊接电流是焊条电弧焊的主要工艺参数,焊工在操作过程中需要调节的只有焊接电流,而焊接速度和电弧电压都是由焊工控制的;焊接电流的选择直接影响着焊接质量和劳动生产率; 焊接电流越大,熔深越大,焊条熔化快,焊接效率也高,但是焊接电流太大时,飞溅和烟雾大,焊条尾部易发红,部分涂层要失效或崩落,而且容易产生咬边、焊瘤、烧穿等缺陷,增大焊件变形,还会使接头热影响区晶粒粗大,焊接接头的韧性降低;焊接电流太小,则引弧困难,焊条容易粘连在工件上,电弧不稳定,易产生未焊透、未熔合、气孔和夹渣等缺陷,且生产率低; 因此,选择焊接电流时,应根据焊条类型、焊条直径、焊件厚度、接头形式、焊缝位置及焊接层数来综合考虑;首先应保证焊接质量,其次应尽量采用较大的电流,以提高生产效率;板厚较的,T 形接头和搭接头,在施焊环境温度低时,由于导热较快,所以焊接电流要大一些;但主要考虑焊条直径、焊接位置和焊道层次等因素;1 考虑焊条直径焊条直径越粗,熔化焊条所需的热量越大,必须增大焊接电流,每种焊条都有一个最合适电流范围,表10是常用的各种直径焊条合适的焊接电流参考值;当使用碳钢焊条焊接时,还可以根据选定的焊条直径,用下面的经验公式计算焊接电流:I=dK式中:I 一一焊接电流 A :d——焊条直径 mm :K——经验系数 A/cra ,见表 3-20;表9 焊接电流经验系数与焊条直径的关系2 考虑焊接位置:在平焊位置焊接时,可选择偏大些的焊接电流,非平焊位置焊接时,为了易于控制焊缝成形,焊接电流比平焊位置小 10%~20%;3 考虑焊接层次:通常焊接打底焊道时,为保证背面焊道的质量,使用的焊接电流较小;焊接填充焊道时,为提高效率,保证熔合好,使用较大的电流:焊接盖面焊道时,防止咬边和保证焊道成形美观,使用的电流稍小些;焊接电流—一般可根据焊条直径进行初步选择,焊接电流初步选定后,要经过试焊,检查焊缝成形和缺陷,才可确定;对于有力学性能要求的如锅炉、压力容器等重要结构,要经过焊接工艺评定合格以后,才能最后确定焊接电流等工艺参数;表11 焊接电流与焊条直径的关系电弧电压当焊接电流调好以后,焊机的外特性曲线就决定了;实际上电弧电压主要是由电弧长度来决定的;电弧长,电弧电压高,反之则低;焊接过程中,电弧不宜过长,否则会出现电弧燃烧不稳定、飞溅大、熔深浅及产生咬边、气孔等缺陷:若电弧太短,容易粘焊条;一般情况下,电弧长度等于焊条直径的~1倍为好,相应的电弧电压为16—25V;碱性焊条的电弧长度不超过焊条的直径,为焊条直径的一半较好,尽可能地选择短弧焊;酸性焊条的电弧长度应等于焊条直径;焊接速度焊条电弧焊的焊接速度是指焊接过程中焊条沿焊接方向移动的速度,即单位时间内完成的焊缝长度;焊接速度过快会造成焊缝变窄,严重凸凹不平,容易产生咬边及焊缝波形变尖;焊接速度过慢会使焊缝变宽,余高增加,功效降低;焊接速度还直接决定着热输入量的大小,一般根据钢材的淬硬倾向来选择;焊缝层数厚板的焊接,一般要开坡口并采用多层焊或多层多道焊;多层焊和多层多道焊接头的显微组织较细,热影响区较窄;前一条焊道对后一条焊道起预热作用,而后一条焊道对前一条焊道起热处理作用;因此,接头的延性和韧性都比较好;特别是对于易淬火钢,后焊道对前焊道的回火作用,可改善接头组织和性能;对于低合金高强钢等钢种,焊缝层数对接头性能有明显影响;焊缝层数少,每层焊缝厚度太大时,由于晶粒粗化,将导致焊接接头的延性和韧性下降;表12 手工电弧焊工艺参数示例气体保护焊:CO2气体保护焊在实际生产中用到的比较多,选择焊接工艺参数时,应做到以下几点;1 CO2根据母材先确定焊丝直径和焊接电流;2根据选择的焊接电流,在试板上试焊,细心调整出相匹配的电弧电压;3根据试板上焊缝成型情况,细调整焊接电流,焊接电压,气体流量,达到最佳的焊接工艺参数;4在工件上正式焊接过程中,应注意焊接回路,接触电阻引起的电压降低,及时调整焊接电压;焊丝直径:根据焊件情况,首先应选择合适的焊丝直径;常用焊丝直径为~,各种直径的焊丝都有其通用的电流范围、适合的焊接位置,见表12;从表10中可以看到,小于的焊丝,适合于全位焊;大于的焊丝主要适用于平焊;表12焊接电流:焊接电流主要根据母材厚度,接头形式以及焊丝直径等正确选择;在保证焊头的前提下,尽量选择小电流,因为当电流太大时,易造成熔池翻滚,不仅飞溅大,焊缝成型也非常差;焊接电流与焊丝直径的关系件表10;电弧电压:确定焊接电流的范围后,调整电弧电压;使电弧电压与焊接电流形成良好的匹配;焊接过程中电弧稳定,飞溅小,能听到沙、沙的声音;能看到的焊剂电流表、电压表的指针稳定,搬动小,焊接电流和电弧电压也就达到了最佳匹配;最佳的电弧电压一般在16V~24V之间,粗滴过渡时,电压为25V-45V,所以电弧电压应细心调试;焊接速度:随着焊接速度增大或减小;则焊缝熔宽、熔深和堆积高度都相应减小或增大;当焊接速度过快时,会使气体保护的作用受到破坏,易使焊缝产生气孔;同时焊缝的冷却速度也会相应提高,也降低了焊缝金属的塑形和韧性,并会使焊缝中间出现一条棱,造成成型不良;当焊接速度过慢时,熔池变大,焊缝变宽,易因过热造成焊缝金属组织粗大或烧穿;因此焊接速度应根据焊缝内部与外观的质量选择;一般自动焊速为15m/h~30 m/h;焊丝伸出长度:焊丝伸出长度一般为焊丝直径的10~20倍;焊丝伸出长度与电流有关,电流越大,伸出长度越长;焊丝伸出长度与焊接电流的关系,见表13;焊丝伸出长度越长时,焊丝的电阻热越大,焊丝熔化速度越快,易造成成段焊丝熔断,飞溅严重,焊接过程不稳定;焊丝伸出长度太短时容易使飞溅物堵住喷嘴,有时飞溅物熔化到熔池中,造成焊缝成型差;一般经验公式是,伸出长度为焊丝直径的十倍,即焊丝选择伸出长度为12mm左右;表13气体流量:气体流量会直接影响焊接质量,一般根据焊接电流、焊接速度、焊丝伸出长度及喷嘴直径来选择;当焊接电流越大,焊接速度越快,焊丝伸出长度越长时,气体流量应大些;气体流量越大或越小时,都会造成成型差、飞溅大、产生气孔;一般经验公式是,数量为焊丝直径的十倍,即焊丝选择12L/min;当采用大电流快速焊接,或室外焊接及仰焊时,应适当提高气体流量;CO气体纯度不低于%;2焊枪倾角:当喷嘴与工件垂直时,飞溅都很大,电弧不稳;其主要原因是运条时产生空气阻力,使保护气流后偏吹;为了避免这种情况的出现,一般采用左向焊法焊接,可将喷嘴前倾10°~15°,不仅能够清楚观察和控制熔池,而且能够保证焊缝成型良好,焊接过程稳定; 电源极性:气体保护焊电源极性一般采用直流反接焊接,因为直流反接时熔深大,飞溅小,电CO2弧稳定,焊缝成型好;3、点固定位焊零件须检验合格后,方可装配定位焊;焊缝间隙在其全长上的不均匀度,应在间隙量公差范围之内;装配焊接零件时,两个焊件或焊边的相互位置偏差应符合下列规定1钢板对接,如图1图12型钢对接,如图2图23对接接头的错边量,应小于板厚的10%,且最大不超过3mm,当两板厚不同时,应以两者3中薄板计算,如图4装配工字梁或箱形梁或类似结构,应符合表14规定表14焊接结构件点固定位焊焊缝,应符合下列要求1定位焊缝的高度和宽度,不应超过焊接焊缝的尺寸,其长度和间距,根据焊接结构件的大小确定;2定位焊与正式焊接用相同型号的焊条;3若焊件焊接需要预热时,定位焊也应预热相同的温度;4定位焊缝有裂纹时,必须铲掉重焊;4、焊接结构件焊接时应符合下列要求:1应对装配定位焊的焊接结构件进行检验合格后,方可进行焊接;2焊接前应将焊缝处及两侧各20mm范围内工件表面的油、锈及其它污物清理干净;3焊接时,不得在非焊缝区引弧,对多层焊道,应每焊一层焊缝,彻底清渣后,检查无缺陷时,方可再焊;焊接结构件的尺寸公差焊件焊后要求1焊接结构件的非机械加工面未注公差的尺寸的极限偏差应符合表16的规定表162焊接结构件焊后须经机械加工面的尺寸的极限偏差应符合表17的规定,但尺寸偏差不得超过加工余量的2/3,且保证有不小于2mm加工余量;表173焊接结构件的角度偏差,根据产品精度不同,分A、B、C三级,列于表18,角度偏差可直接标注在基本尺寸上,也可在图样或技术要求中标注公差等级,凡无标注角度偏差者,按C 级加工与检验;表18 焊接结构件角度偏差4角度偏差规定以角的短边为基准边,其长度自规定的基准点,基准点必须在图样上绘出,其标准方法如图6中a、b图65焊接结构件平面的平面度,直线度公差应符合表19规定表19 焊接结构件平面的平面度、直线度公差6焊接件的圆柱、圆锥表面的圆度,应在其直径公差之半范围内;7焊接件表面之间的同轴度不得大于相应尺寸最大公差之半,如图78焊接件表面间的垂直度与平行度,不得大于相应尺寸公差之半,如图8图89焊接件表面间的对称度,不得大于相应基准面尺寸公差之半,如图9图910焊接件结构件的机加工余量按表20规定表20 焊接结构件机加工余量5、焊接变形的控制及矫正在焊接中为防止和减小变形,应首先焊接薄的焊缝,再焊接厚的焊缝,对较长的焊缝应采取对称或反方向分段焊法,焊缝长度及间隔应均匀一致,同时应以最快的速度焊接;制作件要求密封连续焊接时,要求焊缝处不得出现气孔沙眼现象;各种焊法的焊缝要求平滑不能出现焊不透、焊穿、裂纹、咬边、气孔、砂眼、夹渣等现象;焊完后应除去药皮进行检查,如发现不合格的应立即返修;减小变形的主要方法:1选择合理的焊接顺序;2尽可能用对称焊缝如工字形截面;3采用反变形法焊接过程中控制变形的主要措施:1采用反变形2采用小锤锤击中间焊道3采用合理的焊接顺序4利用工卡具刚性固定5分析回弹常数;焊接变形的矫正焊接变形矫正可用人工、机械及火焰矫正,其要求同条钢材的矫正;焊缝形状偏差和外部缺陷应符合表21规定表216、焊接缺陷焊缝不应有咬边、焊瘤、烧穿、未焊透、焊缝尺寸不符合要求、气孔等;咬边:在工件上沿焊缝形成的凹陷称为咬边,它减少了接头的工作截面,且在咬边处形成严重的应力集中;产生的原因为:工件被熔化一定深度而填充金属未及时流进去补充所致;因而在电流过大,电弧拉得太长,焊条角度不当时均会造成咬边;焊瘤:熔化金属流淌到熔池边缘未熔化的工件上,堆积而形成焊瘤;它与工件未熔合,焊瘤对静载强度无影响,但会引起应力集中,使动载强度降低;产生的原因:在角焊、立焊、横焊、仰焊时电弧过长,焊速太慢,焊条角度和运转方法不正确;在平时对接电流太大,造成后半根焊条过热,致使熔池铁水猛增而造成焊瘤;预防措施:在角焊、立焊、横焊、仰焊时要压低电弧,适当增加焊接速度,保持正确焊条角度,在对接时注意焊接电流即可;烧穿:部分熔化金属从焊缝反面漏出,甚至烧穿成洞,这种缺陷在底层焊缝和薄板焊接时容易发生,它使接头强度降低,焊接时需将漏出部分铲掉,进行补焊;产生原因为:焊接电流过大、焊接速度过慢,电弧在一处停留过久,装配间隙过大;预防措施:选用适当焊接电流和焊接速度,焊接操作方法熟练,可在焊缝背面加铜垫板,在装配间隙过大处可用跳焊法或灭弧法上一层薄焊缝后在施焊;未焊透:工件与焊缝金属或焊缝层间局部未熔合,它削弱了焊缝的工作面积,造成严重的应力集中,大大降低了焊接接头的强度,成为焊缝开裂的根源;产生原因:焊接电流过小,坡口角度太小,钝边太厚,间隙太小,焊条直径过大没有清理表面的氧化皮、油污,多道焊接时没有清理干净熔渣;预防措施:选择合适的焊接电流,清理干净焊件的氧化皮、油污,作好焊道后清理;焊缝尺寸不符合要求:主要指焊缝宽度角焊指焊角高度和焊缝增高量不符合技术要求,沿焊缝长度方向焊缝尺寸不均匀,这几种缺陷均会降低街头强度;产生原因:焊条焊丝选择不当,操作不熟练;气孔:焊缝金属在高温时吸收了过度气体,熔池内部冶金反应产生的气体在熔池冷却凝固时来不及排除,而在焊缝内部或表面形成气孔;它减少了焊缝的有效工作面积,降低了接头的机械强度,如果有穿透或连续性气孔会严重影响焊件的气密性;产生原因为:焊前工件表面有油污、氧化皮未清理干净,焊条受潮,焊条药皮脱落,焊条烘干温度过高或过低,电弧过长;预防措施:选用抗气孔能力强的酸性焊条,焊前清理干净工件表面,焊接电流和焊接速度适中,焊条受潮需烘干,尽量采用短弧焊接;三、试验方法密封性试验煤油试验,例如1GD-C侧箱体焊合件在试件外部焊缝涂上白粉,内部涂上足够的煤油;经30分钟后,检查白粉的表面是否出现黑色油斑;若无油斑,则认为此焊缝无缺陷;若出现油斑,则此处焊缝有缺陷,应进行返修;对于有工作压力的容器,应进行水压试验;暂时不用水压试验的压力,不得小于工作压力的倍,压力达到试验压力时,保压15分钟,检查焊缝有无渗漏现象;如有渗漏处,作出标记,进行返修;3.2焊缝机械性能试验;焊件由本厂质量检验部门按图样、有关技术文件、本标准及焊接通用质量标准进行检查和验收;焊接件检查项目如下焊缝形状偏差和外部缺陷焊缝内部缺陷焊缝密封性焊缝机械性能几何形状尺寸详细检验方法及规则见焊接通用质量标准。
焊接件通用技术要求

焊接件通用技术要求焊接是一种重要的工艺,在许多行业和领域都得到广泛应用。
为了确保焊接件的质量和稳定性,我们需要遵循一些通用的技术要求。
本文将介绍焊接件通用技术要求,包括焊接材料、焊接过程、焊缝设计和质量控制等方面。
一、焊接材料在焊接过程中选择合适的焊接材料非常重要。
以下是一些关键要求和建议:1. 焊丝:焊丝应选择与被焊接材料相匹配的合金材料,并具有良好的流动性和融合性。
2. 气体保护剂:对于气体保护焊接,需使用合适的保护剂,如氩气,以确保焊接过程中没有氧气和杂质的污染。
3. 焊剂:焊剂有助于去除焊接过程中产生的氧化物和杂质,并提供更好的焊接效果。
应选择无毒、无害的焊剂,避免对环境和健康造成影响。
二、焊接过程1. 清洁焊接表面:在焊接之前,必须仔细清洁焊接表面,去除油污、氧化物和杂质,以确保良好的焊接连接。
2. 控制焊接温度:焊接时需要控制焊接温度,过高的温度可能导致焊接件损伤或变形,过低的温度则会影响焊接质量。
3. 控制焊接时间:焊接时间应根据焊接材料的厚度和类型来确定,以确保焊接均匀和牢固。
三、焊缝设计焊缝设计是确保焊接件结构强度和稳定性的重要因素。
以下是一些重要的焊缝设计要求:1. 焊缝尺寸:焊缝尺寸应根据焊接材料的厚度和要求的强度来确定,以确保焊接连接的牢固性。
2. 焊缝形状:焊缝形状应考虑焊接件所需的力学要求,并使焊接件具有较好的承载能力和抗拉强度。
3. 焊缝间距:焊缝间距应根据焊接件的尺寸和要求来确定,以确保焊接连接的均匀性和牢固性。
四、质量控制质量控制是确保焊接件质量和稳定性的关键。
以下是一些常见的质量控制方法:1. 非破坏性检测:通过使用超声波、射线或磁粉等非破坏性检测方法,检测焊接件是否存在缺陷或裂纹。
2. 拉力测试:通过对焊接件进行拉力测试,来评估焊接连接的强度和稳定性。
3. 视觉检查:通过目视检查焊接件的外观和表面质量,来评估焊接连接的质量。
综上所述,焊接件的通用技术要求涉及焊接材料的选择、焊接过程的控制、焊缝设计和质量控制等方面。
焊接通用技术条件DB129-2004
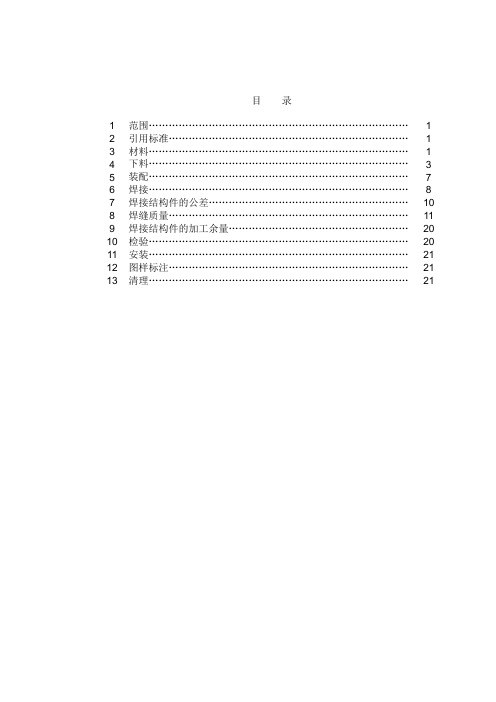
目录1 范围 (1)2 引用标准 (1)3 材料 (1)4 下料 (3)5 装配 (7)6 焊接 (8)7 焊接结构件的公差 (10)8 焊缝质量 (11)9 焊接结构件的加工余量 (20)10 检验 (20)11 安装 (21)12 图样标注 (21)13 清理 (21)东方电机股份有限公司标准DB129—2002焊接通用技术条件代替DB129—931 范围本标准规定了焊接件的下料、成形、装配、焊接、热处理、焊缝质量、焊缝质量检测的一般要求及焊接件尺寸和形位公差。
本标准适用于非压力容器焊接结构件的制造与检查。
也可作为设计焊接结构的参考。
注:压力容器的制造按GB150—1998《钢制压力容器》的规定执行。
2 引用标准GB/T 2649—1989 焊接接头机械性能试验取样方法GB/T 2650—1989 焊接接头冲击试验方法GB/T 2651—1989 焊接接头拉伸试验方法GB/T 2652—1989 焊缝及熔敷金属拉伸试验方法GB/T 2653—1989 焊接接头弯曲及压扁试验方法GB/T 2654—1989 焊接接头及堆焊金属硬度试验方法GB/T 2655—1989 焊接接头应变时效敏感性试验方法GB/T 2656—1981 焊缝金属和焊接接头的疲劳试验法GB/T 3323—1987 钢熔化焊对接接头射线照相和质量分级GB/T 12469—1990 焊接质量保证钢熔化焊接头的要求和缺陷分级JB/T 3223—1996 焊接材料质量管理规程DB130—1996 剪切件与气割件的尺寸偏差DB344—1996 埋弧焊焊缝坡口的基本形式与尺寸DB345—1996 气焊、手工电弧焊及气体保护焊焊缝坡口的基本形式和尺寸DB 443—1996 焊缝符号表示法DB1143—1996 产品零部件和装配场地清洁度规范3 材料3.1 用于制造焊接结构件的原材料(包括钢板、钢管、型材、有色金属和铸、锻件),其型号、规格、尺寸应符合相关的标准和图样要求,若不符合时,应按厂材料代用制度代用。
水工金属结构焊接通用技术条件

水工金属结构焊接通用技术条件水工金属结构焊接是一种常见的金属结构连接方式,广泛应用于建筑、船舶、桥梁等工程领域。
水工金属结构焊接通用技术条件是指在水利工程中对金属结构焊接的要求和规范。
本文将详细介绍水工金属结构焊接通用技术条件的内容和要求。
一、焊接材料的选择水工金属结构焊接通用技术条件要求焊接材料的选择应符合相关标准和规范。
一般情况下,焊接材料应具备良好的焊接性能、机械性能和耐腐蚀性能。
常用的焊接材料有焊条、焊丝和焊剂等。
二、焊接设备的选择水工金属结构焊接通用技术条件要求焊接设备的选择应符合相关标准和规范。
焊接设备应具备稳定的电流输出、可靠的电弧起弧和稳定的电弧维持,并具备自动保护功能,能够及时发现并排除焊接中的缺陷和故障。
三、焊接工艺的选择水工金属结构焊接通用技术条件要求焊接工艺的选择应根据焊接材料的种类、焊接位置和焊接质量要求等因素进行合理选择。
常见的焊接工艺包括手工电弧焊、埋弧焊、气体保护焊等。
四、焊接质量的要求水工金属结构焊接通用技术条件要求焊接质量应符合相关标准和规范。
焊缝应具备良好的密封性和机械强度,焊接接头应具备良好的连接性和稳定性。
焊接质量的评定应根据焊接缺陷的类型和程度进行,常见的焊接缺陷有气孔、夹渣、裂纹等。
五、焊接工艺控制水工金属结构焊接通用技术条件要求对焊接工艺进行有效的控制和监测。
焊接过程中应控制焊接电流、焊接速度、焊接温度等参数,并对焊接过程进行记录和检查。
焊接过程中应采取适当的预热和后热措施,以提高焊接质量。
六、焊接人员的要求水工金属结构焊接通用技术条件要求焊接人员应具备相应的技术能力和工作经验。
焊接人员应熟悉焊接工艺和焊接设备的操作,熟悉焊接材料的性能和使用要求,并具备良好的安全意识和团队合作精神。
水工金属结构焊接通用技术条件是对水利工程中金属结构焊接的要求和规范。
通过合理选择焊接材料和设备,选择适当的焊接工艺,控制焊接质量,提高焊接工艺控制水平,培养合格的焊接人员,可以确保水工金属结构焊接的质量和安全性,提高工程的可靠性和耐久性。
焊接件通用技术条件
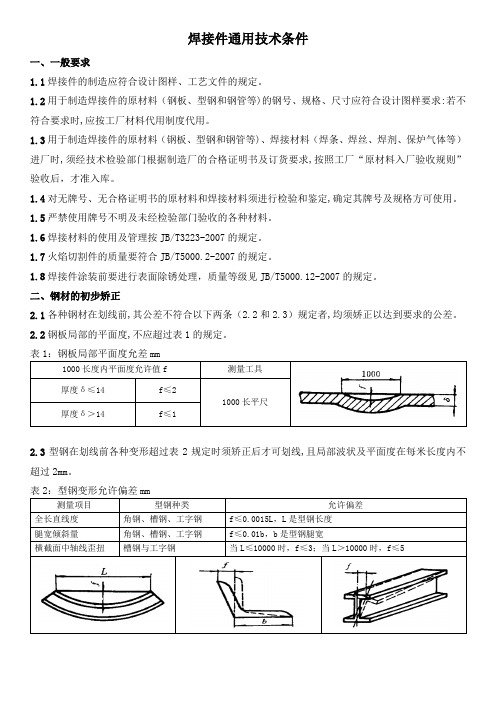
焊接件通用技术条件一、一般要求1.1焊接件的制造应符合设计图样、工艺文件的规定。
1.2用于制造焊接件的原材料(钢板、型钢和钢管等)的钢号、规格、尺寸应符合设计图样要求:若不符合要求时,应按工厂材料代用制度代用。
1.3用于制造焊接件的原材料(钢板、型钢和钢管等)、焊接材料(焊条、焊丝、焊剂、保炉气体等)进厂时,须经技术检验部门根据制造厂的合格证明书及订货要求,按照工厂“原材料入厂验收规则”验收后,才准入库。
1.4对无牌号、无合格证明书的原材料和焊接材料须进行检验和鉴定,确定其牌号及规格方可使用。
1.5严禁使用牌号不明及未经检验部门验收的各种材料。
1.6焊接材料的使用及管理按JB/T3223-2007的规定。
1.7火焰切割件的质量要符合JB/T5000.2-2007的规定。
1.8焊接件涂装前要进行表面除锈处理,质量等级见JB/T5000.12-2007的规定。
二、钢材的初步矫正2.1各种钢材在划线前,其公差不符合以下两条(2.2和2.3)规定者,均须娇正以达到要求的公差。
2.2钢板局部的平面度,不应超过表1的规定。
2.3型钢在划线前各种变形超过表2规定时须矫正后才可划线,且局部波状及平面度在每米长度内不超过2mm。
三、钢材的成型弯曲3.1钢材的卷圆弯曲,当弯曲半径(内半径)大于下列数值时,可冷弯。
a.钢板:对于低合金钢R≥25δ;对于低碳钢R≥20δ。
其中:R——弯曲半径;δ——钢板厚度。
b.工字钢:R≥25H或R≥25B(随弯曲方向而定)。
其中:H——工字钢高;B——工字钢腿宽。
c.槽钢:R≥45B或R≥25H(随弯曲方向而定)。
其中:H——槽钢高;B——槽钢腿宽。
d.角钢:R≥45B。
其中:B——角钢腿宽(对不等边角钢随弯曲方向而定)。
3.2钢材的卷圆弯曲,当弯曲半径(内半径)小于以上(3.1)规定的数值时,需根据具体工艺进行热弯或弯后热处理。
如热弯,钢材应加热到900~1100℃。
弯曲完成时,温度不得低于700℃。
水工金属结构焊接通用技术条件
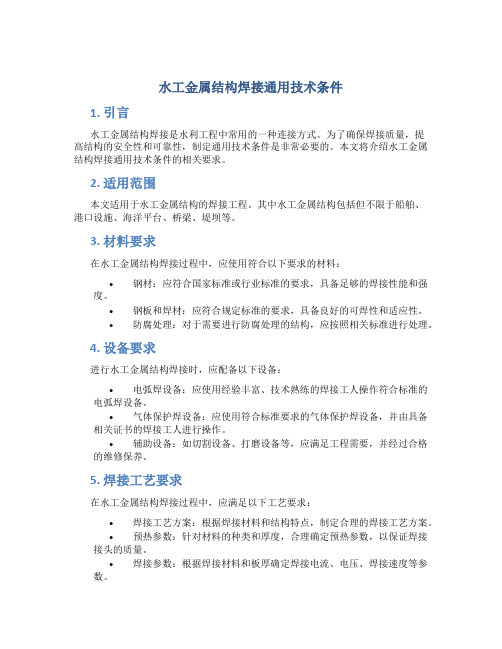
水工金属结构焊接通用技术条件1. 引言水工金属结构焊接是水利工程中常用的一种连接方式。
为了确保焊接质量,提高结构的安全性和可靠性,制定通用技术条件是非常必要的。
本文将介绍水工金属结构焊接通用技术条件的相关要求。
2. 适用范围本文适用于水工金属结构的焊接工程。
其中水工金属结构包括但不限于船舶、港口设施、海洋平台、桥梁、堤坝等。
3. 材料要求在水工金属结构焊接过程中,应使用符合以下要求的材料:•钢材:应符合国家标准或行业标准的要求,具备足够的焊接性能和强度。
•钢板和焊材:应符合规定标准的要求,具备良好的可焊性和适应性。
•防腐处理:对于需要进行防腐处理的结构,应按照相关标准进行处理。
4. 设备要求进行水工金属结构焊接时,应配备以下设备:•电弧焊设备:应使用经验丰富、技术熟练的焊接工人操作符合标准的电弧焊设备。
•气体保护焊设备:应使用符合标准要求的气体保护焊设备,并由具备相关证书的焊接工人进行操作。
•辅助设备:如切割设备、打磨设备等,应满足工程需要,并经过合格的维修保养。
5. 焊接工艺要求在水工金属结构焊接过程中,应满足以下工艺要求:•焊接工艺方案:根据焊接材料和结构特点,制定合理的焊接工艺方案。
•预热参数:针对材料的种类和厚度,合理确定预热参数,以保证焊接接头的质量。
•焊接参数:根据焊接材料和板厚确定焊接电流、电压、焊接速度等参数。
•焊接顺序:合理安排焊接顺序,以减小应力并保证焊缝的质量。
•焊接方法选择:应根据工程的具体要求,选择适用的焊接方法,如电弧焊、气体保护焊等。
6. 质量控制要求为确保水工金属结构焊接质量,以下质量控制要求应得到满足:•焊工资质:焊工应持有相应的焊接技能等级证书,并具备相关经验。
•焊接验收:根据相关标准进行焊接接头的质量验收,并记录验收结果。
•焊接缺陷处理:对于发现的焊接缺陷,应及时进行处理和修复,确保焊接接头的质量。
•焊接记录和报告:应编制焊接记录和报告,并保存至少10年。
7. 安全要求在水工金属结构焊接过程中,应注意以下安全要求:•安全防护措施:焊工应佩戴防护眼镜、手套、口罩等防护设备,确保焊接过程中的人身安全。
焊接件通用技术要求

焊接件通用技术要求(JB/ZQ4000.3-86)1.焊接结构件的长度尺寸公差见1-245c尺寸和形位公差数值.Plb,适用于焊接件和焊接足见的长度尺寸,焊接件的直线度、平面度和平行度公差见1-245c尺寸和形位公差数值.Plb,焊接件结构件的尺寸公差于形位公差等级选用见1-245c尺寸和形位公差数值.Plb2.标注和未标注角度的偏差见1-246a角度偏差.Plb,角度偏差的公差尺寸以短边为基准边,其长度从图样标明的基准点算起3.喷丸处理的焊接件,为了防止钢丸钻入焊缝,必须焊接内焊缝,并尽量避免内市和内腔,如果结构上必须有内市和内腔,则必须进行酸洗,以便达到表面除锈质量登记Be(见JB/ZQ4000.10-86附录A),对此图样需作标注4.由平炉钢制造的低碳钢结构件,可在任何温度下进行焊接,但为了避免焊接过程产生裂纹及脆性断裂,厚度较大的焊接件,焊削必须根据工艺要求,进行预热和缓冷,板厚超过30mm的重要焊接结构,焊后应立即消除内应力,消除内应力采用550-600℃回火,或200℃局部低温回火。
5.普通低合金结构制造的焊接件,必须按照焊接零件的碳当量和合金元素含量、零件的厚度、钢结构件的用途和要求进行焊前预热和焊后处理,见表1在气温较低、焊接件厚度较大的情况下焊接的普通低合金结构,应按表2的规定预热。
6.有密封内腔的焊接件,在热处理之前,应在中间隔板上适当的位置加工Φ10mm孔,使其空腔与外界相通,需在外壁上钻孔的,在热处理后要重新堵上。
7.焊缝射线探伤应符合GB3323-82的规定,要进行力学性能试验的焊接,应在图样或订伙技术要求中注明,焊缝的力学性能试验种类、试样尺寸按GB2649-81-GB2656-81的规定,试样板焊后与工件经过相同的热处理,并事先经过外观无损探伤检查。
8.焊件要进行密封性检验和耐压试验时,应按本标准要求进行,对耐压试验有要求时,应在图样或订货要求注明试验压力和试压时间。
(完整版)结构件焊接通用技术要求

结构件企业生产标准1.定义具有一定形状结构,并能够承受载荷的作用的构件,称为结构件。
如,支架、框架、内部的骨架及支撑定位架等。
2.范围本标准适用于的结构件生产。
本标准适用于本厂图纸技术、加工制造和检验标准的规范。
3. 规范性引用文件下列标准对于本文件的应用是必不可少的。
凡是注日期的引用标准,仅注日期的版本适用于本文件。
凡是不注日期的引用文件,其最新版本(包括所有的修改单)适用于本文件。
XQ/SJ-05-2012《结构件通用焊接工艺》GB/T19804-2005焊接结构的一般尺寸公差和形位公差4. 需要加工的材料下料余量标准4.1表面精度等于或高于的需要留材料长、宽、厚度、圆孔、方孔加工余量长/宽度(mm)单边余量(mm)厚(mm)单边余量(mm)圆孔/方孔(mm)单边余量(mm)焊前加工焊后加工≤10 2 ≤60 3≤100024 10~20 3 61~100 41001~2000 5 21~40 4 >100 52001~3000 3 6 >40 54.2表面精度等于或低于的不需留金加工余量,可直接割出。
5. 焊接工艺5.1 焊工5.1.1焊工必须经过考试并取得合格证后,方可上岗。
5.1.2 焊工必须严格遵守焊接工艺规程,严禁自由施焊及在焊道外的母材上引弧。
5.2 焊前准备5.2.1焊前焊工要熟悉图纸及其组焊要求。
5.2.2 焊接前应检查并确认焊接设备及辅助工具等处于良好状态。
5.2.3 焊接工作尽量在室内进行,当工件表面潮湿或暴露于雨雪条件下,不得进行焊接作业。
5.2.4 焊条、焊剂和药芯焊丝应按产品说明书的规定进行烘干,烘干后存放在保温箱内随用随取。
E4303焊条150℃烘焙1~2小时。
5.2.5焊接前,母材加工坡口推荐尺寸(见下表1)表1 母材加工坡口形式和尺寸项次厚度T(mm)坡口名称坡口形式坡口尺寸备注间隙(mm)钝边(mm)坡口角度(β) (°)1 1~3I型坡口0~1.5——单面焊3~6 0~2.5 双面焊2 3~9V型坡口0~2 0~20~365~7555~65 9~26 0~33 6~9 带垫板V型坡口3~5 0~20~245~55 9~26 4~64 12~60 X型坡口0~3 0~3 55~655 2~30 T型接头I型坡口0~2 ——6 6~10T型接头单边V型坡口0~2 0~245~55 10~17 0~3 0~317~30 0~4 0~47 20~40 T型接头对称K型坡口0~3 2~3 45~558管径Φ≤76法兰角焊接头2~3 —50~60(30~35)5.3结构件焊接参数5.3.1手工电弧焊:钢板厚度mm 焊条直径mm 6以下8~20 20~30 30以上焊接电流A Φ3.2 100~130 130~185 185~210 210~270 焊接电流A Φ4 185~210 210~270 260~300 5.3.2 CO2气体保护焊:钢板厚度mm 焊接电流A 焊接电压V 焊丝直径mm6以下120~220 20~25Φ1.2Φ1.68~20 120~300 25~35Φ1.2Φ1.620~30 300~400 30~35 Φ1.2 Φ1.630以上400~500 35~40Φ1.2Φ1.65.4 焊接5.4.1受压元件的角焊缝的根部应保证焊透。
焊接的件通用技术的要求规范
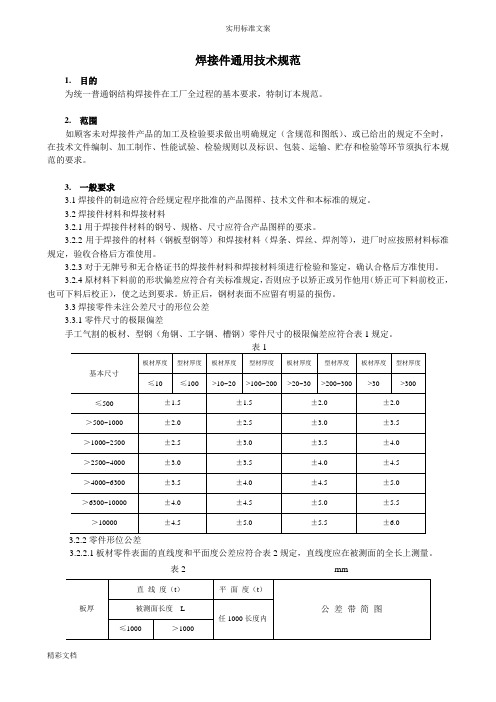
焊接件通用技术规范1.目的为统一普通钢结构焊接件在工厂全过程的基本要求,特制订本规范。
2.范围如顾客未对焊接件产品的加工及检验要求做出明确规定(含规范和图纸)、或已给出的规定不全时,在技术文件编制、加工制作、性能试验、检验规则以及标识、包装、运输、贮存和检验等环节须执行本规范的要求。
3.一般要求3.1焊接件的制造应符合经规定程序批准的产品图样、技术文件和本标准的规定。
3.2焊接件材料和焊接材料3.2.1用于焊接件材料的钢号、规格、尺寸应符合产品图样的要求。
3.2.2用于焊接件的材料(钢板型钢等)和焊接材料(焊条、焊丝、焊剂等),进厂时应按照材料标准规定,验收合格后方准使用。
3.2.3对于无牌号和无合格证书的焊接件材料和焊接材料须进行检验和鉴定,确认合格后方准使用。
3.2.4原材料下料前的形状偏差应符合有关标准规定,否则应予以矫正或另作他用(矫正可下料前校正,也可下料后校正),使之达到要求。
矫正后,钢材表面不应留有明显的损伤。
3.3焊接零件未注公差尺寸的形位公差3.3.1零件尺寸的极限偏差手工气割的板材、型钢(角钢、工字钢、槽钢)零件尺寸的极限偏差应符合表1规定。
3.2.2零件形位公差3.2.2.1板材零件表面的直线度和平面度公差应符合表2规定,直线度应在被测面的全长上测量。
表2 mm3.2.2.2型材零件的直线度、平面度、垂直度公差应符合表3的规定,歪扭误差应符合表4的规定。
表3 mm3.2.2.3板材与型材零件切割边棱对表面垂直度,不得大于表5规定。
图1 L—边棱长度;t—直线度3.2.2.4板材零件边棱之间的垂直度与平行度,不得大于相应尺寸的公差之半(见图2)。
图23.2.2.5型材零件切割断面对其表面的垂直度以及型材零件切割断面的平行度,不得大于型材零件切割断面之间的尺寸公差之半(见图3)。
图33.2.2.6弯曲成型的筒体零件尺寸的极限偏差、圆角和弯角,(≥5mm钢板)应符合表6规定。
3.2.2.7对于焊接H型钢、梁等焊接量较大工件,在腹板冀板下料时,适当放长20~30mm,待焊接、校形完成后再取长短。
结构件焊接通用工艺规范
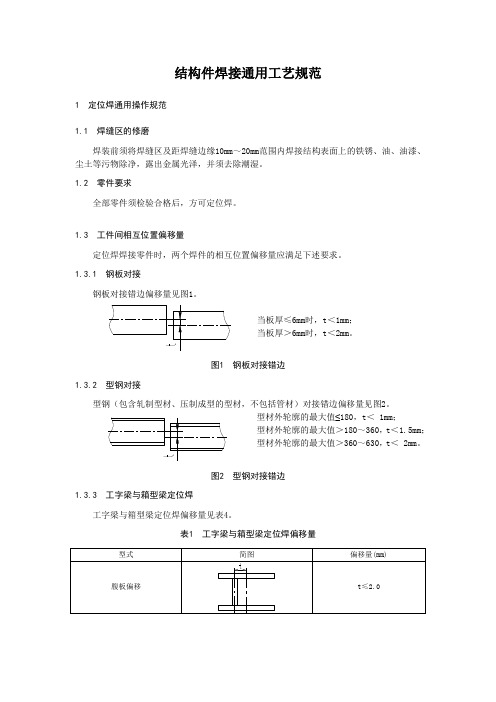
结构件焊接通用工艺规范1 定位焊通用操作规范 1.1 焊缝区的修磨焊装前须将焊缝区及距焊缝边缘10mm ~20mm 范围内焊接结构表面上的铁锈、油、油漆、尘土等污物除净,露出金属光泽,并须去除潮湿。
1.2 零件要求全部零件须检验合格后,方可定位焊。
1.3 工件间相互位置偏移量定位焊焊接零件时,两个焊件的相互位置偏移量应满足下述要求。
1.3.1 钢板对接当板厚≤6mm 时,t <1mm ; 当板厚>6mm 时,t <2mm 。
1.3.2 型钢对接2。
型材外轮廓的最大值≤180,t < 1mm ;型材外轮廓的最大值>180~360,t <1.5mm ; 型材外轮廓的最大值>360~630,t < 2mm 。
型钢对接错边1.3.3 工字梁与箱型梁定位焊工字梁与箱型梁定位焊偏移量见表4。
表1 工字梁与箱型梁定位焊偏移量表2 其他接头的定位焊偏移量要求1.3.6 角焊缝装配不良对于接触承压的焊缝应按照表7中要求执行。
表3 接触承压的角焊缝装配间隙要求1.4 定位焊焊缝要求1.4.1 定位焊时不得在焊缝区以外引弧,定位焊填充材料选用ER50-6焊丝或与构件正式焊接要求一致的填充材料。
1.4.2 定位焊的预热要求:定位焊预热温度与正式焊接时一致。
要求预热的结构件,未预热的定位焊缝应用角磨机等工具彻底清理干净,不得熔入焊缝。
当选用ER50-6焊丝,并且与构件正式焊接要求不一致时,同样应将定位焊缝用角磨机等工具彻底清理干净,不得熔入焊缝。
1.4.3 定位焊缝长度及间距要求:当板厚≤4mm ,定位焊缝的长度为12mm ~20mm ,间距为图1.4.7 桁架臂坡口角度及根部间隙的特殊要求 1.4.7.1 钢管对接焊缝,钢管对接焊缝单侧坡口角度为30度,钝边高0~1毫米,根部间隙为2mm ~3mm 。
1.4.7.2 钢管相贯线焊缝钢管相贯线焊缝,作为臂架腹杆、直杆、斜杆的钢管一端的坡口尺寸为:a)管子壁厚< 6mm,不开坡口;b)管子壁厚≥ 6mm,均开45°坡口,不留钝边。
通用技术要求

一 通用技术要求1 设备制造、验收、包装技术要求1.1 焊接件1.1.1 焊接结构件尺寸公差符合JB/ZQ4000.3-86中表6和表7的B级,形位公差相应按F级检验。
1.1.2 施焊焊工必须进行考核合格,并有相关的资质证书。
1.1.3 焊缝外观质量应符合JB/ZQ400.3-86中Gs级和Bk级,焊接结构件表面。
不允许有明显锤疤,伤痕,其表面飞溅物,焊渣,切割边缘,棱边,毛刺等必须打磨和清理。
1.1.4 焊缝不允许有裂纹、未焊透和任何缺陷,如达不到标准要求,允许通过碳弧气刨等方法,铲除清理干净后重焊或修磨。
1.1.5 焊接结构件(含热处理后),必须经过打磨清理,合格后涂上底漆,方可发送加工或装配,(涂漆前表面预处理质量要求见本要求第5.3.11项油漆要求)。
1.1.6 散件发货的型材数量应考虑留有一定的损耗余量。
1.2 铸件1.2.1 铸件尺寸公差、壁厚公差值应符合GB6414-86的规定,公差等级为CT14。
1.2.2 铸钢件表面粗糙度等级Ra50(GB6060.1-85)。
1.2.3 铸铁件表面粗糙度等级Ra25(GB6060.1-85)。
1.2.4 铸钢件应符合《铸钢件通用技术条件》(JB/ZQ4000.5-86)和《铸件补焊通用技术条件》的规定。
1.2.5 铸铁件应符合《铸铁件通用技术》(JB/ZQ4000.5-86)和《铸铁件补焊通用技术条件》的规定。
1.2.6 毛坯铸件必须经过喷砂,喷丸和打磨清理,合格后涂上底漆(见第5.3.11条油漆要求)。
1.3 锻件1.3.1 锻件应符合《锻件通用技术要求》(Q/ZB71-73)。
1.4 加工件1.4.1、加工件未注尺寸公差为CT12级1.4.2 符合《机械加工通用技术条件》(Q/ZB75-73)的要求。
1.5 气动系统1.5.1 所有关键的气动元器件如电磁换向阀、气缸、气动三联件、压力开关、真空发生器、真空吸盘、真空压力开关、真空减压阀、真空气阀以及气动附件必须采用国际知名供应商的产品。
焊接件通用技术要求

焊接件通用技术要求
一、焊接件的通用技术要求:焊接部位应平直、无毛刺、无裂纹、无气孔、无夹杂物;焊丝应选用质量好、规格明确的产品;焊接前应
对钢材进行除毛刺、打磨处理,去除表面油污和灰尘,确保焊接质量;焊接时应保证电弧稳定,控制电流大小,焊接速度均匀;焊接后应按
要求进行除渣、研磨等处理;焊接件应符合相关标准及技术要求,并
保证其使用寿命和安全性。
二、焊接工艺要求:在进行焊接前,应先对工件进行预处理,对其表
面进行去污、除锈等处理,以保证焊接质量;在选择焊接材料时,应
根据工件材料及要求选用合适的焊接材料,严格按照技术规范进行焊
接工艺控制,确保焊接质量和稳定性;焊接时应严格控制焊接温度,
避免过热和过冷引起的质量问题,保证焊接强度和耐腐蚀性;焊接完
成后,应进行磨光、去渣等处理,确保焊缝平整、无裂纹、无毛刺、
无夹杂物,保证焊接质量;焊接工艺应按照规范要求进行记录并进行
质量检测,确保焊接质量和稳定性。
焊接件通用技术条件
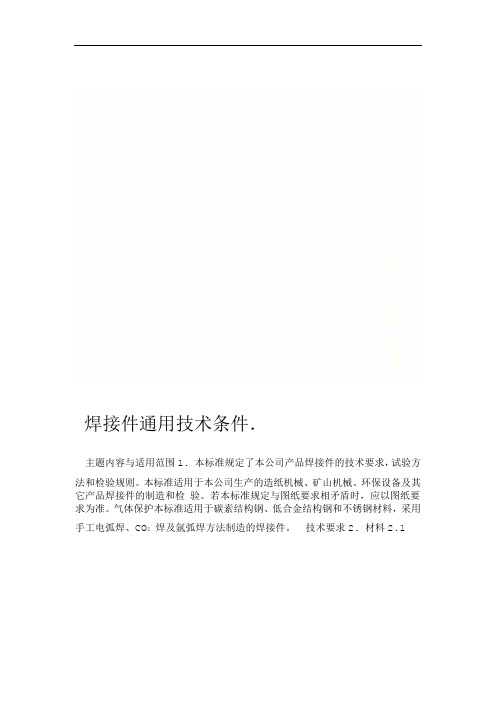
焊接件通用技术条件.主题内容与适用范围1. 本标准规定了本公司产品焊接件的技术要求,试验方法和检验规则。
本标准适用于本公司生产的造纸机械、矿山机械、环保设备及其它产品焊接件的制造和检验。
若本标准规定与图纸要求相矛盾时,应以图纸要求为准。
气体保护本标准适用于碳素结构钢、低合金结构钢和不锈钢材料,采用手工电弧焊、CO2焊及氩弧焊方法制造的焊接件。
技术要求2. 材料2.1用于制造焊接结构件的原材料(板材、型材等)的牌号、规格、尺寸应符合图样或2.1.1 技术文件的要求,若不符时,应按公司内材料代用制度办理材料代用。
用于焊接件的材料(钢板、型钢、铸钢、焊条、焊丝等)购进时,应有质量证明书,2.1.2 并按材料标准规定检验合格后,方准入库使用。
对无牌号、无质证书的原材料和焊材,必须进行检验和鉴定。
其成份和性能符合要 2.1.3 求时方准使用。
钢板的初步矫正2.2各种钢材在划线前,不能有较大的变形,其形状公差不得超出下列规定:2.2.1规定钢板的平面度不应超过表1a1钢板平面度公差f1000:f测量工厚16f=2米平f=1厚16b.型材的直线度和垂直度公差不超过表2的规定2角全长直线度误2/1000,在每米长度内槽超2钢垂直度误1/100,但不大1.(不等角角钢按长边宽度计算工歪扭:100时100时5钢槽钢腿相对腰的垂直度误差f≤1/100b的规定,当超过规定,本公司无法矫正时,经检验部门同意,可用于歪扭不超过表2c.次要结构。
钢材的矫正。
可用机械矫正和火焰矫正,或在平台上锤击。
矫正后的钢材,不得有2.2.21mm。
明显的伤痕,其伤痕深度,钢板一般≤0.5mm,型钢≤不锈钢材料不准用铁锤直接锤击(可垫一铜块锤击或用木锤锤击)2.2.3 号料划线前的准备2.3划线或样板的制作,需考虑结构在焊接时所产生的收缩量,收缩量的大小,按工艺2.3.1一般箱型或工字型结构或类似箱型划工字型结构,要求规定。
如工艺文件没有规定时,L按下式计算纵向焊缝收缩量⊿):筋、隔板数量mm(L:焊件纵向焊缝总长;n⊿L=1/1000L=0.5n按下式计算横向焊缝的收缩量⊿Bmm):焊件横向焊缝总长⊿B=1/1000B (B焊接结构件的装配间隙,在制作样板时应予以考虑。
电力钢结构焊接通用技术条件
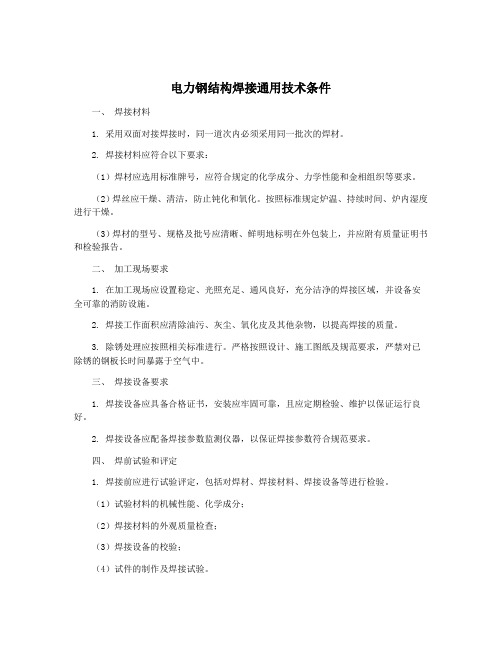
电力钢结构焊接通用技术条件一、焊接材料1. 采用双面对接焊接时,同一道次内必须采用同一批次的焊材。
2. 焊接材料应符合以下要求:(1)焊材应选用标准牌号,应符合规定的化学成分、力学性能和金相组织等要求。
(2)焊丝应干燥、清洁,防止钝化和氧化。
按照标准规定炉温、持续时间、炉内湿度进行干燥。
(3)焊材的型号、规格及批号应清晰、鲜明地标明在外包装上,并应附有质量证明书和检验报告。
二、加工现场要求1. 在加工现场应设置稳定、光照充足、通风良好,充分洁净的焊接区域,并设备安全可靠的消防设施。
2. 焊接工作面积应清除油污、灰尘、氧化皮及其他杂物,以提高焊接的质量。
3. 除锈处理应按照相关标准进行。
严格按照设计、施工图纸及规范要求,严禁对已除锈的钢板长时间暴露于空气中。
三、焊接设备要求1. 焊接设备应具备合格证书,安装应牢固可靠,且应定期检验、维护以保证运行良好。
2. 焊接设备应配备焊接参数监测仪器,以保证焊接参数符合规范要求。
四、焊前试验和评定1. 焊接前应进行试验评定,包括对焊材、焊接材料、焊接设备等进行检验。
(1)试验材料的机械性能、化学成分;(2)焊接材料的外观质量检查;(3)焊接设备的校验;(4)试件的制作及焊接试验。
1. 焊接采用评定文件中明确的工艺规范,确保焊接的质量符合要求。
2. 焊接时必须保持焊接接头必须坚固、平直、符合设计要求。
3. 焊接设备应经常检查、维护和校正,确保焊接质量不受焊接设备的影响。
六、焊后评定1. 焊后应对焊缝及其附近区域进行检查。
2. 检查焊缝及热影响区应采用无损检测,其中必须进行射线检测。
3. 焊接完毕后,应进行外观检验、尺寸检验、化学成分分析、机械性能检验等工作,确保焊接质量符合国家相关规定。
七、操作规范1. 严格按照操作规范进行操作,严格按照工艺流程进行焊接操作。
2. 在焊接过程中要按照规定的参数进行操作,不得随意调整参数。
3. 在焊接过程中要密切关注设备运行情况和焊接品质情况,核实对焊接质量的影响。
焊接件通用技术条件

1. 主题内容与适用范围 本标准规定了本公司产品焊接件的技术要求,试验方法和检验规则。
本标准适用于本公司生产的造纸机械、矿山机械、环保设备及其它产品焊接件的制造和检 验。
若本标准规定与图纸要求相矛盾时,应以图纸要求为准。
本标准适用于碳素结构钢、低合金结构钢和不锈钢材料,采用手工电弧焊、 焊及氩弧焊方法制造的焊接件。
2. 技术要求 2.1材料 2.1.1 CO 2气体保护 2.1.2 2.1.3 用于制造焊接结构件的原材料(板材、型材等)的牌号、规格、尺寸应符合图样或 技术文件的要求,若不符时,应按公司内材料代用制度办理材料代用。
用于焊接件的材料(钢板、型钢、铸钢、焊条、焊丝等)购进时,应有质量证明书, 并按材料标准规定检验合格后,方准入库使用。
对无牌号、无质证书的原材料和焊材,必须进行检验和鉴定。
其成份和性能符合要 求时方准使用。
2.2钢板的初步矫正2.2.1各种钢材在划线前,不能有较大的变形,其形状公差不得超出下列规定: a.钢板的平面度不应超过表1规定 表1钢板平面度公差值f / 7 —1000:f 厚度贾16 f=2 厚度§> 16 f=1 测量工具1米平尺b.型材的直线度和垂直度公差不超过表 2的规定 表2角钢 槽钢 钢管 全长直线度误差fw2/1000L ,在每米长度内不超过2角钢 垂直度误差fw 1/100b,但不大于1.5(不等边角钢按长边宽度计算)工字钢歪扭:当 L< 1000 时,f < 3; L > 1000 时,仕 5槽钢 腿相对腰的垂直度误差fw 1/100bc.歪扭不超过表2的规定,当超过规定,本公司无法矫正时,经检验部门同意,可用于 次要结构。
2.2.2钢材的矫正。
可用机械矫正和火焰矫正,或在平台上锤击。
矫正后的钢材,不得有 明显的伤痕,其伤痕深度,钢板一般W 0.5m m ,型钢W 1mm 。
2.2.3不锈钢材料不准用铁锤直接锤击(可垫一铜块锤击或用木锤锤击) 2.3号料划线前的准备2.3.1划线或样板的制作,需考虑结构在焊接时所产生的收缩量,收缩量的大小,按工艺 要求规定。
- 1、下载文档前请自行甄别文档内容的完整性,平台不提供额外的编辑、内容补充、找答案等附加服务。
- 2、"仅部分预览"的文档,不可在线预览部分如存在完整性等问题,可反馈申请退款(可完整预览的文档不适用该条件!)。
- 3、如文档侵犯您的权益,请联系客服反馈,我们会尽快为您处理(人工客服工作时间:9:00-18:30)。
结构件焊接技术要求
1.目的
为统一结构件焊接标准,方便零件检验,提高焊接质量,制定本技术要求。
2.适用范围
本文件适用于本厂的结构件,本文件为图纸技术要求、加工制造要求和检验标准要求的完善和补充。
3. 规范性引用文件
下列标准对于本文件的应用是必不可少的。
凡是注日期的引用标准,仅注日期的版本适用于本文件。
凡是不注日期的引用文件,其最新版本(包括所有的修改单)适用于本文件。
YTQ 322-1989 焊接件通用技术要求
GB/T19804-2005 焊接结构的一般尺寸公差和形位公差
4. 焊接工艺
4.1 焊工
4.1.1焊工必须经过考试并取得合格证后,方可上岗。
4.1.2 焊工必须严格遵守焊接工艺规程,严禁自由施焊及在焊道外的母材上引弧。
4.2 焊前准备
4.2.1 焊接前应检查并确认焊接设备及辅助工具等处于良好状态。
4.2.2 焊接工作尽可能在室内进行,当工件表面潮湿或暴露于雨雪条件下,不得进行焊接作业。
4.2.3 焊条、焊剂和药芯焊丝应按产品说明书的规定进行烘干,烘干后存放在保温箱内随用随取。
低氢焊条在施焊前必须进行烘干,烘干温度为350~400℃,时间1~2h。
一般在常温下超过4h后,必须重新烘干。
酸性焊条一般可不烘干,但焊接重要结构时经150~200℃烘干1~2h。
4.2.4 焊接前,母材加工坡口推荐尺寸(见下表1)
表1 母材加工坡口形式和尺寸
项次
厚度T
(mm)
坡口名称坡口形式
坡口尺寸
备注
间隙
(mm)
钝边
(mm)
坡口角度
(β) (°)
1 1~3
I型坡口
0~1.5
——
单面焊3~6 0~2.5 双面焊
2 3~9
V型坡口
0~2 0~2
0~3
65~75
55~65 9~26 0~3
3 6~9
带垫板
V型坡口
3~5 0~2
0~2
45~55 9~26 4~6
4 12~60 X型坡口0~3 0~3 55~65
5 2~30 T型接头I型坡
口
0~2 ——
6 6~10
T型接头单边
V型坡口
0~2 0~2
45~55 10~17 0~30~3
17~30 0~40~4
4.3 焊接
4.3.1根据具体情况选用合理的焊接参数进行焊接,不允许超大电流焊接。
4.3.2 焊接零件应根据材料的厚度和焊接特性采用合适的焊接工艺,保证焊接质量。
4.3.3 多层焊时,前一层焊道表面必须进行清理,检查、修整,如发现有影响焊接质量的缺陷,必须修整清除后再焊。
4.3.4 焊接部位必须进行焊前清理、去除铁锈、油污等杂质,重要部位需要打磨光洁。
4.4 焊后处理
4.4.1 焊接结束,焊工应清理焊道表面的熔渣飞溅物,检查焊缝外形尺寸及外观质量,焊缝不平整时应进行修整。
4.4.2焊缝外形应光顺、均匀,焊道与焊道、焊道与基本金属之间过渡平滑。
4.4.3 焊缝缺陷(焊接缺陷主要特征见下文)超标允许返修,但返修次数不超过两次。
4.4.4 对于一些封闭型结构,多焊缝、长焊缝的构件,焊后应进行锤击、振动等方法消除残余应力,若零件有热处理要求的,应采用热处理消除应力。
5. 焊缝缺陷
5.1焊接裂纹:在焊接应力及其它致脆因素的共同作用下,焊接过程中或焊接后,焊接接头中局部区域(焊缝或焊接热影响区)的金属原子结合力遭到破坏而出现的新界面所产生的缝隙,称为焊接裂纹。
焊接裂纹是最危险的缺陷,除降低焊接接头的力学性能指标外,裂纹末端的缺口易引起应力集中,促使裂纹延伸和扩展,成为结构断裂失效的起源。
5.2气孔:焊接过程中熔池金属高温时吸收和产生的气泡,在冷却凝固时未能逸出而残留在焊缝金属内所形成的孔穴,称为气孔。
5.3夹渣:焊后残留在焊缝中的熔渣,称为夹渣。
夹渣可以是单个颗粒状分布,也可以是长条状或线状连续分布。
5.4未焊透:焊接时,接头根部未完全熔透的现象,称为未焊透。
5.5咬边:因焊接造成沿焊趾(或焊根)处出现的低于母材表面的凹陷或沟槽称为咬边。
它是由于焊接过程中,焊件边缘的母材金属被熔化后,未及时得到熔化金属的填充所致。
5.6焊瘤:焊接过程中,在焊缝根部背面或焊缝表面,出现熔化金属流淌到焊缝之外未熔化的母材上所形成的金属瘤称为焊瘤。
在立焊、横焊、仰焊时多出现。
5.7未熔合:熔化焊时,在焊缝金属与母材之间或焊道(层)金属之间未能完全熔化结合而留下的缝隙,称为未熔合。
5.8凹坑:焊后在焊缝表面或背面形成低于母材表面的局部低洼缺陷。
5.9未焊满:由于填充金属不足,在焊缝表面形成的连续或断续的沟槽。
5.10烧穿:焊接过程中熔化金属自坡口背面而流出,形成穿孔的缺陷。
5.11焊接变形:焊接时局部温度过高,超过材料允许的使用温度,一段时间后即产生了局部变形。
6. 焊接技术要求
6.1采用任何焊接方式,焊缝表面不得有表面气孔、夹渣、裂纹、焊瘤、烧穿、弧坑、弧坑、裂纹、咬边、电焊擦伤、未焊满等缺陷(见表2)。
表2 角焊缝表面质量等级(mm)
序
号
缺陷名称图例优等焊缝合格焊缝
1裂纹不允许不允许
2气孔不允许100mm长度的焊缝,允许
直径不大于1,气孔一个
3夹渣不允许不允许
4飞溅不允许不允许
5咬边不允许咬边不得超过板厚的5%,最大不得超过1.5,总长不超过每条焊缝的10%
6弧坑不允许不允许
7凸度b-a≤1+0.10a
且≤3b-a≤1+0.15a
且≤4
8凹度不允许a-b=0.3+0.05a
不大于1,且只能是局部
9焊脚不等△K=0.5+0.15a△K=1+0.15a
10未焊透不允许不允许
11单面焊错边e≤0.1δ且≤2e≤0.1δ且≤3
12双面错焊边e≤0.1δ且≤2e≤.0.1δ且≤3
13余高h≤1+0.10b且≤3h≤1+0.10b且≤3
14塌陷不允许允许局部塌陷
e′≤0.2+0.02δ且≤0.5 6.2板材焊接时焊缝要求:若图纸有相关要求,按图纸执行。
图纸未要求时可采用以下焊接工艺:当零件板厚≤3mm时,焊缝允许采用断续焊,每段焊缝长度15~40mm,当零件板厚大于3mm小于等于6mm时,焊缝允许采用交错焊,当零件板厚大于6mm时,应采用满焊。
6.3 焊接螺母焊点要求:焊接螺母直径小于等于M6时,焊点为2到3个;焊接螺母直径大于M6时,焊点为3到4个。
焊接标注方式(见下表3):
表3 焊接螺母标注方式
符号符号解释
K---焊缝高度(mm)e---点焊间距(mm)
n---点焊数量N---焊接螺母数量
l---点焊长度(mm)
6.4零件焊后应进行校正,零件校正后的形位公差要求,图纸有规定的按图纸执行,图纸无明确要求的按YTQ 322-89《焊接件通用技术要求》规定执行,未注焊接尺寸公差应符合GB/T19804-2005《焊接结构的一般尺寸公差和形位公差》B级精度有关规定。