连铸坯表面质量缺陷及处理措施
防止连铸坯夹渣杂缺陷的措施及规定

防止连铸坯夹渣杂缺陷的措施及规定在连铸生产过程中,坯料夹杂或夹渣是一个常见的问题。
坯料夹渣或夹杂会造成铸造坯料表面缺陷,严重的情况下会导致铸坯折断。
为了防止连铸坯夹杂或夹渣缺陷,我们制定了以下的措施及规定。
坯料的质量控制坯料的质量是影响连铸坯料夹杂或夹渣的一个重要因素。
为了保障坯料质量的稳定,需要做到以下几点:1.选择原材料时,需要严格按照规定采购车间标准,增加试做,检查原材料质量的合格率。
2.要求原材料供应商提供合格证明和检验报告,保证原材料的质量符合车间标准要求。
3.对原材料的人工检验和自动检验要做好记录,及时发现和解决问题。
4.对重点原材料,比如矿渣等,要做好监测和抽样分析,及时发现问题。
5.对原材料的质量问题,需要做到及时沟通和处理。
连铸机操作规范连铸机操作规范是实现铸造质量控制的重要手段。
以下是进行连铸操作的规定:1.连铸机操作人员需要经过专业的培训和技术能力考核。
2.连铸机操作人员在接班时,需要对前一班的连铸机操作记录进行查看和交接,及时了解连铸机运行情况。
3.对于连铸机在运行过程中出现的异常情况,需要及时进行处理,保证连铸机运行的稳定性。
4.操作人员需要通过联合巡视和自检来发现问题和解决问题。
5.班组和质量检查组应定期开展连铸机检查和检验,及时发现和解决质量问题。
连铸模具的管理连铸模具是保障连铸坯料质量的关键性因素。
以下是连铸模具的管理规定:1.对连铸模具进行清洗和修理,以便发现隐患和进行预防性维护。
2.对连铸模具进行周期性的检测和检验,判断模具的状况和使用寿命。
3.对连铸模具进行标记和记录,以便在使用过程中进行跟踪和管理。
4.严格控制连铸模具的使用寿命和使用次数,保证坯料的质量和稳定性。
坯料质量的检验和测试坯料质量的检验和测试是确保连铸坯料夹渣杂缺陷的措施之一。
以下是坯料质量的检验和测试规定:1.要求在连铸过程中不断地进行袖口检测,确保坯料不夹杂夹渣。
2.对于连铸生产中的中间产品进行定期检验,以便发现和解决质量问题。
连铸坯质量缺陷

连铸坯的质量缺陷及控制摘要连铸坯质量决定着最终产品的质量。
从广义来说所谓连铸坯质量是得到合格产品所允许的连铸坯缺陷的严重程度,连铸坯存在的缺陷在允许范围以内,叫合格产品。
连铸坯质量是从以下几个方面进行评价的:(1)连铸坯的纯净度:指钢中夹杂物的含量,形态和分布。
(2)连铸坯的表面质量:主要是指连铸坯表面是否存在裂纹、夹渣及皮下气泡等缺陷。
连铸坯这些表面缺陷主要是钢液在结晶器内坯壳形成生长过程中产生的,与浇注温度、拉坯速度、保护渣性能、浸入式水口的设计,结晶式的内腔形状、水缝均匀情况,结晶器振动以及结晶器液面的稳定因素有关。
(3)连铸坯的内部质量:是指连铸坯是否具有正确的凝固结构,以及裂纹、偏析、疏松等缺陷程度。
二冷区冷却水的合理分配、支撑系统的严格对中是保证铸坯质量的关键。
(4)连铸坯的外观形状:是指连铸坯的几何尺寸是否符合规定的要求。
与结晶器内腔尺寸和表面状态及冷却的均匀程度有关。
下面从以上四个方面对实际生产中连铸坯的质量控制采取的措施进行说明。
关键词:连铸坯;质量;控制1 纯净度与质量的关系纯净度是指钢中非金属夹杂物的数量、形态和分布。
夹杂物的存在破坏了钢基体的连续性和致密性。
夹杂物的大小、形态和分布对钢质量的影响也不同,如果夹杂物细小,呈球形,弥散分布,对钢质量的影响比集中存在要小些;当夹杂物大,呈偶然性分布,数量虽少对钢质量的危害也较大。
此外,夹杂物的尺寸和数量对钢质量的影响还与铸坯的比表面积有关。
一般板坯和方坯单位长度的表面积(S)与体积(V)之比在0.2~0.8。
随着薄板与薄带技术的发展,S/V可达10~50,若在钢中的夹杂物含量相同情况下,对薄板薄带钢而言,就意味着夹杂物更接近铸坯表面,对生产薄板材质量的危害也越大。
所以降低钢中夹杂物就更为重要了。
提高钢的纯净度就应在钢液进入结晶器之前,从各工序着手尽量减少对钢液的污染,并最大限度促使夹杂物从钢液中排除。
为此应采取以下措施:⑴无渣出钢。
连铸方坯的缺陷及其处理
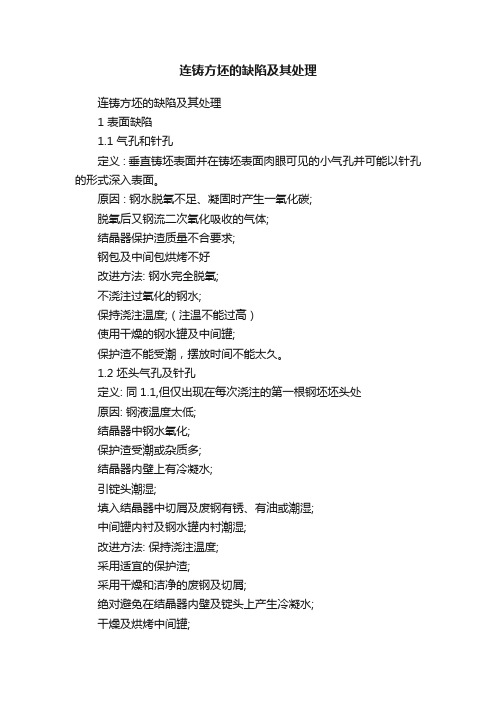
连铸方坯的缺陷及其处理连铸方坯的缺陷及其处理1 表面缺陷1.1 气孔和针孔定义 : 垂直铸坯表面并在铸坯表面肉眼可见的小气孔并可能以针孔的形式深入表面。
原因 : 钢水脱氧不足、凝固时产生一氧化碳;脱氧后又钢流二次氧化吸收的气体;结晶器保护渣质量不合要求;钢包及中间包烘烤不好改进方法: 钢水完全脱氧;不浇注过氧化的钢水;保持浇注温度;(注温不能过高)使用干燥的钢水罐及中间罐;保护渣不能受潮,摆放时间不能太久。
1.2 坯头气孔及针孔定义: 同1.1,但仅出现在每次浇注的第一根钢坯坯头处原因: 钢液温度太低;结晶器中钢水氧化;保护渣受潮或杂质多;结晶器内壁上有冷凝水;引锭头潮湿;填入结晶器中切屑及废钢有锈、有油或潮湿;中间罐内衬及钢水罐内衬潮湿;改进方法: 保持浇注温度;采用适宜的保护渣;采用干燥和洁净的废钢及切屑;绝对避免在结晶器内壁及锭头上产生冷凝水;干燥及烘烤中间罐;1.3 夹渣定义: 表面分布不均匀的夹渣,有时针孔和渣聚集,呈疏松态的外观原因: 由保护渣耐火材料颗粒和钢水氧化产物以及出钢渣等引起,随着钢流带入并被卷至铸坯表面。
改进方法: 用挡渣出钢;采用适宜的保护渣及耐火材料;钢水不能过氧化,注温要合适。
1.4 振动波纹及折叠定义: 在与铸坯轴线垂直方向上,铸坯表面上以均匀间距分布的波纹振痕,在不利的情况下出现折叠。
原因: 浇注速度波动大,使结晶器中钢液面不稳定。
改进方法: 保持均匀的浇注速度,稳定结晶器钢水液面。
调整振动频率使其与拉速相适应。
1.5 结疤与重皮定义: 铸坯角部和表面上出现的疤痕原因: 由于结晶器内坯壳破裂、钢水渗入到结晶器和铸坯之间的夹缝,以及保护渣结块造成。
改进方法: 保证结晶器具有准确的锥度,当结晶器使用时间过长而磨损会使坯壳过早脱离结晶器内壁而导致坯壳破裂。
1.6 分层: (双浇)定义: 铸坯中间出现分界层原因: 浇注中断又重新开始浇注时,使两次浇注连接出现重接。
改进方法: 浇注过程中不要断流,拉速要相对稳定,不要忽高忽低。
连铸坯缺陷的成因及防止对策

连铸坯缺陷的成因及防止对策你们知道吗?在钢铁生产的时候呀,有一种东西叫连铸坯,它就像是钢铁的“小胚胎”,以后会变成各种各样有用的钢铁制品呢。
可是呀,这个连铸坯有时候也会出现一些小毛病,今天咱们就一起来看看这些小毛病是怎么来的,又有啥办法能防止它们出现哟。
一、连铸坯为啥会有气孔这个小毛病呢。
想象一下呀,连铸坯就像是一个大大的蛋糕,要是在做蛋糕的时候,面粉里混进了好多小气泡,那烤出来的蛋糕里面就会有好多小窟窿,连铸坯有气孔就有点像这个样子哦。
这气孔是咋来的呢?有时候呀,在炼钢的时候,钢水里会混入一些气体,就像我们喝的汽水里面有好多小气泡一样。
这些气体跟着钢水一起进入到连铸坯里面,等连铸坯慢慢冷却凝固的时候,气体跑不出来啦,就留在里面形成了气孔。
比如说,就像我们吹泡泡,泡泡粘在了一个地方,怎么也弄不掉,气孔就是这样留在连铸坯里啦。
那怎么防止气孔出现呢?这就好比我们做蛋糕的时候,要把面粉搅拌均匀,把里面的气泡都赶跑一样。
在炼钢的时候呀,工人们会采取一些办法,让钢水里的气体尽量跑出来。
比如说,他们会让钢水在一个大容器里多待一会儿,就像让汽水的气泡慢慢冒出来一样,这样钢水里的气体少了,连铸坯里出现气孔的可能性也就小啦。
二、连铸坯的裂纹又是咋回事呢。
连铸坯的裂纹呀,就像是我们手上不小心划了一道口子一样,会影响它的质量哦。
那裂纹是怎么出现的呢?有时候呀,连铸坯在冷却的时候,就像我们冬天从温暖的屋里突然跑到寒冷的外面,身体会受不了一样,连铸坯也会因为温度变化太快而受不了。
比如说,连铸坯的外面很快就冷却变硬了,可是里面还是热的,就像一个苹果,外皮已经冻硬了,里面还是软软的,这样一收缩一拉扯,连铸坯就容易出现裂纹啦。
那怎么防止裂纹出现呢?这就需要工人们像照顾小宝宝一样,细心地控制连铸坯的冷却速度。
不能让它冷得太快,要让它慢慢地、均匀地降温,就像我们给发烧的小朋友用温水擦身体,慢慢地让体温降下来一样。
这样连铸坯就不容易因为温度变化太快而出现裂纹啦。
连铸坯的缺陷与控制技术
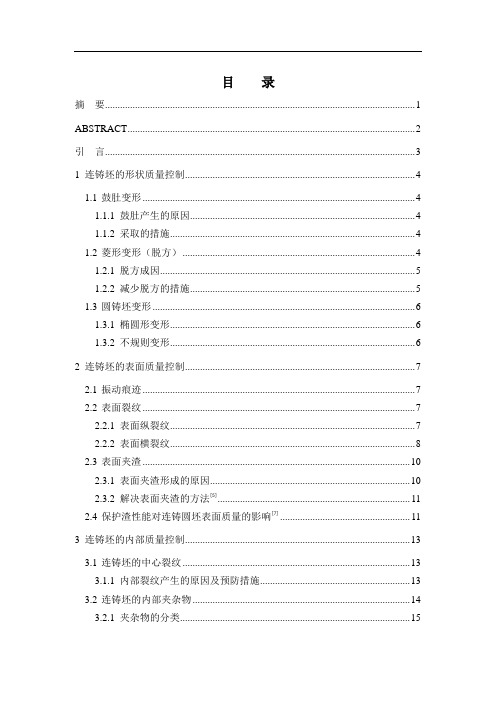
目录摘要 (1)ABSTRACT (2)引言 (3)1 连铸坯的形状质量控制 (4)1.1鼓肚变形 (4)1.1.1 鼓肚产生的原因 (4)1.1.2 采取的措施 (4)1.2菱形变形(脱方) (4)1.2.1 脱方成因 (5)1.2.2 减少脱方的措施 (5)1.3圆铸坯变形 (6)1.3.1 椭圆形变形 (6)1.3.2 不规则变形 (6)2 连铸坯的表面质量控制 (7)2.1振动痕迹 (7)2.2表面裂纹 (7)2.2.1 表面纵裂纹 (7)2.2.2 表面横裂纹 (8)2.3表面夹渣 (10)2.3.1 表面夹渣形成的原因 (10)2.3.2 解决表面夹渣的方法[5] (11)2.4保护渣性能对连铸圆坯表面质量的影响[7] (11)3 连铸坯的内部质量控制 (13)3.1连铸坯的中心裂纹 (13)3.1.1内部裂纹产生的原因及预防措施 (13)3.2连铸坯的内部夹杂物 (14)3.2.1夹杂物的分类 (15)3.2.2 夹杂物的来源[9] (15)3.2.3 连铸坯中夹杂物的控制方法[10] (16)结论 (18)致谢 (19)参考文献 (20)摘要连铸坯质量决定着最终产品的质量。
从广义来说所谓的连铸坯质量是得到严格产品所允许范围以内,叫合格产品。
连铸坯质量是从一下几个方面进行评价的:1. 连铸坯的外观形状:是指连铸坯的几何尺寸是否符合规定的要求。
与结晶器内腔尺寸和表面状态及冷却的均匀程度有关。
2. 连铸坯的表面质量:主要是指连铸坯表面是否存在裂纹,夹渣等缺陷。
连铸坯这些表面缺陷主要是钢液在结晶器内坯壳形成生长过程中产生的,与浇注温度,拉坯速度,保护渣性能,浸入式水口的设计,结晶式的内腔形状,水缝均匀情况,结晶器振动以及结晶器液面的稳定因素有关。
3. 连铸坯的内部质量:是指连铸坯是否具有正确的凝固结构,以及裂纹,偏析,疏松等缺陷程度。
二冷区冷却水的合理分配,支撑系统的严格对中是保证铸坯质量的关键。
连铸坯表面质量缺陷及处理措施

连铸坯表面质量缺陷及处理措施【摘要】对于连铸板坯而言,振痕和裂纹是其主要的质量缺陷问题。
虽然这个缺陷在大多数情况下对连铸坯的质量影响不大,但是如果不及时有效的处理调还会带来很多附加的质量问题。
尤其是在生产不锈钢和高强度钢品种时,这种质量缺陷所带来的弊端更加明显。
【关键词】连铸坯;振痕;质量影响1振痕形成机理在连铸坯生产中,振痕和裂纹是两种最为常见的质量缺陷问题,主要是由于弯月面顶端溢流造成的,该缺陷形成以后会附带其他质量缺陷一并产生。
2振痕对铸坯质量的影响振痕对连铸坯的质量影响会导致后期出现列裂纹,包括横裂纹、角部横裂纹及矫直裂纹。
如果连铸坯内掺杂的杂质较多,会导致大规模网状裂纹的出现,甚至出现穿钢现象。
如果在连铸坯出现振痕的地方晶粒很大,就会产生晶间裂纹现象,在这样的情况下需要对连铸坯修磨,从而提高成材率。
3影响振痕深度的因素振动参数对振痕形状和深度有重要影响。
其中振幅、频率、负滑脱时间及振动方式最为重要;结晶器保护渣的耗量、粘度、保温性能及表面性能等有着重要影响;.钢的凝固特性对振痕有着重要影响,特别是当钢中碳含量和钢中Ni/Cr 比影响最突出。
当钢中碳含量为0.1%左右,Ni/Cr≈0.55左右,铸坯表面振痕最深。
4减少振痕深度的措施采用小振幅(s)、高频率(f)及减少负滑脱时间(tN),可以有效的减少振痕的深度;采用非正弦振动方式可以减少振痕的深度,这是因为非正弦振动其负滑脱时间tN比正弦振动短;采用渣耗量低,粘度高的保护渣,可以使振痕深度变浅。
采用保温性能好和能增加弯月面半径的保护渣可以减少振痕深度;提高不锈钢、钢液的过热度,尤其是含钛和含铝的不锈钢对减少该钢表面振痕深度是有效的。
提高结晶器进出冷却水的温差,对减少振痕深度是有利的。
5铸坯表面裂纹5.1表面纵裂纹铸坯表面纵裂纹是铸坯最主要表面缺陷,对铸坯质量影响极大,特别是板坯和圆坯最为突出,报废量和整修量很大。
5.1.1纵裂纹类型铸坯表面沟槽纵裂纹。
211172579_连铸方坯的常见表面缺陷及控制

管理及其他M anagement and other连铸方坯的常见表面缺陷及控制康旭辉摘要:连铸方坯表面的质量直接影响材料轧制后成品的质量,而近年来,我国部分企业在连铸方坯生产的过程中,存在诸多的表面缺陷问题,不能确保生产的质量和效果。
基于此,本文分析连铸方坯常见表面缺陷问题,提出几点表面缺陷控制的建议和措施,旨在为增强连铸方坯的表面质量提供帮助。
关键词:连铸方坯;常见表面缺陷;控制全面掌握方坯缺陷的类型、形成机理和消除途径是方坯质量控制的关键。
目前,国内外钢铁企业在钢坯质量控制方面取得了可喜的成绩,并获得了大量的生产数据和实际操作经验。
全面提高方坯质量,对提高连铸方坯成品率、改善钢材质量、节能降耗、降低成本具有重要意义。
连铸钢属于直接浇注钢水的工艺。
它的出现从根本上改变了主导了一个世纪的钢锭开坯过程。
液态金属连铸钢的概念早在19世纪中叶就被提出。
1840年,美国的销售商获得了连铸铅管的专利。
1846年,转炉的发明者贝塞默使用水冷旋转双辊连铸机生产锡箔、铅板和玻璃板。
1872年,David提出了移动式结晶器连铸的概念。
1886年~1889年,提出了立式连铸机的设计方案。
1921年,皮尔逊提出了结晶器振动的概念,即结晶器振动使板坯和结晶器之间连续的相对运动。
1933年,连铸的先驱德国准噶斯人建造了第一台1700t/月振动结晶器立式连铸机。
20世纪30年代,第一个成功铸造铜铝合金的有色金属连铸应用于生产。
目前,部分企业在连铸方坯生产的过程中,方坯表面的质量波动幅度很高,存在脱方缺陷、凹陷,缺陷和渣沟缺陷等,不能确保整体结构表面质量符合标准要求,对特钢产品生产质量造成一定的危害,因此,在连铸方坯实际生产的过程中需结合具体表面缺陷问题的发生原因与实际情况,采用有效的措施进行控制,确保连铸方坯表面质量符合标准规范,为特钢产品高质量生产夯实基础。
1 连铸方坯的常见表面缺陷和发生原因1.1 渣沟缺陷与原因从实际情况而言,连铸方坯表面出现渣沟缺陷问题,轧制以后线材表面出现裂纹缺陷问题的发生存在直接联系,从表面观察可以发现坯件有纵向贯通性的沟状缺陷问题,具体是在连铸方坯的内弧部分分布,很小一部分会在侧弧的位置,采用跟踪性轧制12.5mm绞丝钢实验的方式,可以发现线材的表面存在裂纹问题。
《改善连铸板坯缺陷的轧制工艺》范文

《改善连铸板坯缺陷的轧制工艺》篇一一、引言随着现代工业的快速发展,钢铁行业作为国民经济的重要支柱,其产品质量和生产效率的提升显得尤为重要。
连铸板坯作为钢铁生产中的重要环节,其质量直接影响到后续轧制工艺的效率和产品质量。
因此,如何有效改善连铸板坯的缺陷,优化轧制工艺,成为了业界关注的焦点。
本文旨在探讨连铸板坯的常见缺陷及原因,并分析轧制工艺的改进措施,以提高钢铁产品的质量和生产效率。
二、连铸板坯常见缺陷及原因分析1. 中心裂纹:中心裂纹是连铸板坯的主要缺陷之一,其形成原因主要是板坯凝固过程中的温度梯度和热应力过大。
此外,铸坯的化学成分、夹杂物、铸机振动等因素也会对中心裂纹的产生造成影响。
2. 表面裂纹:表面裂纹主要出现在板坯的表面,其形成原因包括钢水质量、结晶器振动、二次冷却制度等因素。
此外,钢中合金元素和夹杂物的含量也会对表面裂纹的产生造成影响。
3. 夹渣和夹杂物:夹渣和夹杂物主要来源于钢水的精炼过程和浇注过程中的夹杂物。
此外,铸模的质量、涂料的性能以及连铸机的维护保养也会影响夹渣和夹杂物的产生。
三、轧制工艺的改进措施针对上述连铸板坯的常见缺陷,轧制工艺的改进措施主要包括以下几个方面:1. 优化轧制参数:通过合理设定轧制温度、轧制速度、压下量等参数,使轧制过程更加稳定,减少轧制过程中的变形和裂纹等缺陷的产生。
2. 调整轧辊质量:选用高质量的轧辊,提高轧辊的硬度和耐磨性,减少轧制过程中的磨损和振动,从而降低板坯的表面裂纹和内部缺陷。
3. 强化轧前准备:在轧制前对连铸板坯进行充分的预热和除鳞处理,以去除表面的夹杂物和氧化皮,提高板坯的表面质量。
4. 优化冷却制度:根据板坯的化学成分、尺寸和轧制要求,制定合理的冷却制度,控制板坯的冷却速度和温度分布,以减少中心裂纹和表面裂纹的产生。
5. 引入无损检测技术:在轧制过程中引入无损检测技术,如超声波检测、X射线检测等,对板坯进行实时监测,及时发现并处理缺陷,提高产品的良品率。
连铸坯缺陷及对策
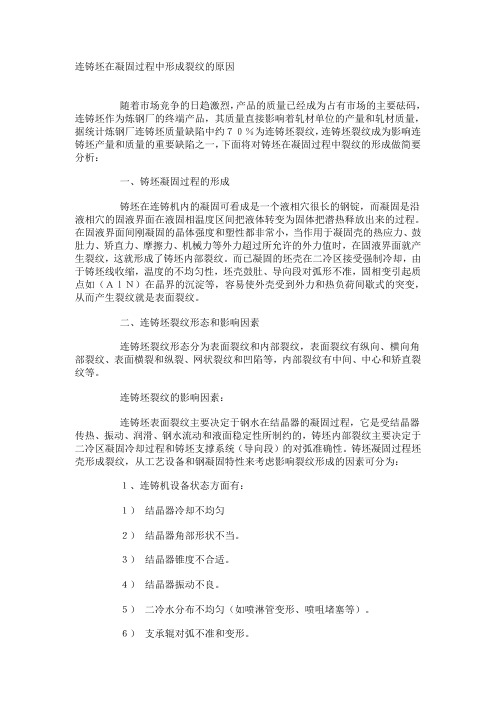
连铸坯在凝固过程中形成裂纹的原因随着市场竞争的日趋激烈,产品的质量已经成为占有市场的主要砝码,连铸坯作为炼钢厂的终端产品,其质量直接影响着轧材单位的产量和轧材质量,据统计炼钢厂连铸坯质量缺陷中约70%为连铸坯裂纹,连铸坯裂纹成为影响连铸坯产量和质量的重要缺陷之一,下面将对铸坯在凝固过程中裂纹的形成做简要分析:一、铸坯凝固过程的形成铸坯在连铸机内的凝固可看成是一个液相穴很长的钢锭,而凝固是沿液相穴的固液界面在液固相温度区间把液体转变为固体把潜热释放出来的过程。
在固液界面间刚凝固的晶体强度和塑性都非常小,当作用于凝固壳的热应力、鼓肚力、矫直力、摩擦力、机械力等外力超过所允许的外力值时,在固液界面就产生裂纹,这就形成了铸坯内部裂纹。
而已凝固的坯壳在二冷区接受强制冷却,由于铸坯线收缩,温度的不均匀性,坯壳鼓肚、导向段对弧形不准,固相变引起质点如(AlN)在晶界的沉淀等,容易使外壳受到外力和热负荷间歇式的突变,从而产生裂纹就是表面裂纹。
二、连铸坯裂纹形态和影响因素连铸坯裂纹形态分为表面裂纹和内部裂纹,表面裂纹有纵向、横向角部裂纹、表面横裂和纵裂、网状裂纹和凹陷等,内部裂纹有中间、中心和矫直裂纹等。
连铸坯裂纹的影响因素:连铸坯表面裂纹主要决定于钢水在结晶器的凝固过程,它是受结晶器传热、振动、润滑、钢水流动和液面稳定性所制约的,铸坯内部裂纹主要决定于二冷区凝固冷却过程和铸坯支撑系统(导向段)的对弧准确性。
铸坯凝固过程坯壳形成裂纹,从工艺设备和钢凝固特性来考虑影响裂纹形成的因素可分为:1、连铸机设备状态方面有:1)结晶器冷却不均匀2)结晶器角部形状不当。
3)结晶器锥度不合适。
4)结晶器振动不良。
5)二冷水分布不均匀(如喷淋管变形、喷咀堵塞等)。
6)支承辊对弧不准和变形。
2、工艺参数控制方面有:1)化学成份控制不良(如C、Mn/S)。
2)钢水过热度高。
3)结晶器液面波动太大。
4)保护渣性能不良。
5)水口扩径。
6)二次冷却水分配不良,铸坯表面温度回升过大。
连铸坯的缺陷及控制

二冷段和末端区的电磁搅拌可有效抑制枝晶搭桥形成封闭 的液窝。
连铸主要工艺参数
① 拉坯速度及其控制 ② 铸坯的冷却(结晶器冷却、二次冷却)
连铸坯的内部凝固是在出结晶器后进行的,后继的二次水冷、 弯曲矫直等直接影响内部质量。
连铸坯的缺陷及控制
提高连铸坯内部质量的工艺措施:
① 控制二冷段的传热,使铸坯均匀凝固,提高等轴晶率; 偏析、缩孔、缩松
② 降低浇钢的过热度; ③ 使用性能好的保护渣,防止钢水二次氧化和污染; ④ 控制拉速,保证连铸机正常运行; ⑤ 电磁搅拌(二冷段和末端区)。 偏析、缩孔、缩松
连铸坯的缺陷及控制
连铸坯的缺陷及控制
1. 连铸坯的表面缺陷
裂纹 气孔 夹杂 振痕、凹陷 成分偏析
连铸坯的缺陷及控制
1. 连铸坯的表面缺陷
裂纹 气孔 夹杂 振痕、凹陷 成分偏析
连铸坯的缺陷及控制
1. 连铸坯的表面缺陷 裂纹 气孔 夹杂 振痕、凹陷 成分偏析
钢水在结晶器内形成初凝固壳的状态是决定铸坯表面质量的关键
结晶器电磁搅拌:
(2)扩大等轴晶区改善宏观 偏析,减少粗大柱状晶区 。
软接触电磁连铸:
软接触电磁连铸:
(1)减轻结晶器振动对弯月 面的影响,液态渣膜连续均 匀。
软接触电磁连铸:
(2)减小初凝壳对结晶器的 压力和摩擦力 。
连铸坯的缺陷及控制
2. 连铸坯的内部缺陷
裂纹 气孔 夹杂 缩孔、缩松 成分偏析
连铸坯的缺陷及控制
提高连铸坯表面质量的工艺措施:
① 控制结晶器的传热,使初凝固壳均匀; 裂纹、凹陷
② 控制结晶器的振动;
振痕、横裂纹
③ 使用性能好的保护渣;
气孔、夹杂
④ 优化结晶器结构气孔、夹杂
连铸小方坯常见的质量缺陷
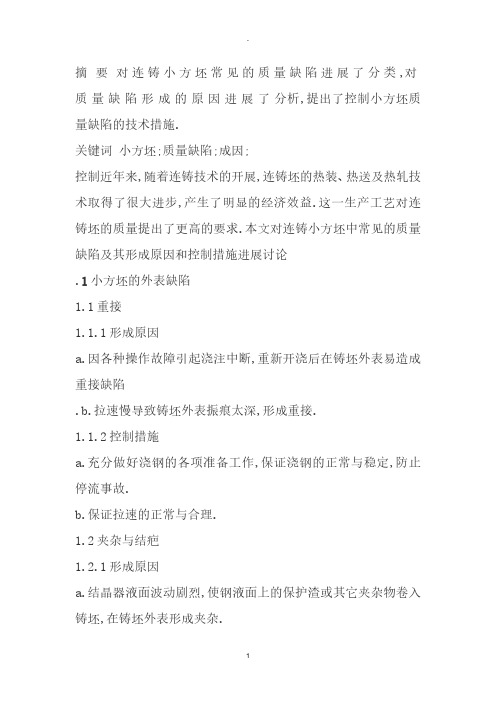
.
b.钢液在拉漏处溢出,被结晶器冷却,在铸坯外表形成缺陷.c.拉 速波动过大且频繁. 1.2.2 控制措施 a.提高操作人员的技术素质和工作责任心,保证结晶器液面的稳 定 .b.改善保护渣的性能,增加熔渣层厚度,使之提高对夹杂物的吸 收能力 .c.严格工艺操作规程,稳定拉速.d.提高中间包水口和塞头的抗 侵蚀性能. 1.3 划痕 1.3.1 形成原因 a.二冷段机架足辊上有废钢,造成铸坯外表划痕. b.拉矫辊不平或二次冷却不均匀,造成铸坯跑偏,铸坯与拉矫机 架接触划伤铸坯外表. 1.3.2 控制措施 a.加强二冷段的维护,发现漏钢要及时处理干净 .b.加强拉矫系统的维护,保证拉矫辊的水平度,并安装侧导向装 置,防止铸坯跑偏. 1.4 振痕 1.4.1 形成原因 a.振痕是结晶器振动的必然结果,难以完全消除,结晶器液面波 常 见 的 质 量 缺 陷 进 展 了 分 类 ,对 质 量 缺 陷 形 成 的 原 因 进 展 了 分析,提出了控制小方坯质 量缺陷的技术措施. 关键词 小方坯;质量缺陷;成因; 控制近年来,随着连铸技术的开展,连铸坯的热装、热送及热轧技 术取得了很大进步,产生了明显的经济效益.这一生产工艺对连 铸坯的质量提出了更高的要求.本文对连铸小方坯中常见的质量 缺陷及其形成原因和控制措施进展讨论 .1 小方坯的外表缺陷 1.1 重接 1.1.1 形成原因 a.因各种操作故障引起浇注中断,重新开浇后在铸坯外表易造成 重接缺陷 .b.拉速慢导致铸坯外表振痕太深,形成重接. 1.1.2 控制措施 a.充分做好浇钢的各项准备工作,保证浇钢的正常与稳定,防止 停流事故. b.保证拉速的正常与合理. 1.2 夹杂与结疤 1.2.1 形成原因 a.结晶器液面波动剧烈,使钢液面上的保护渣或其它夹杂物卷入 铸坯,在铸坯外表形成夹杂.
《改善连铸板坯缺陷的轧制工艺》范文
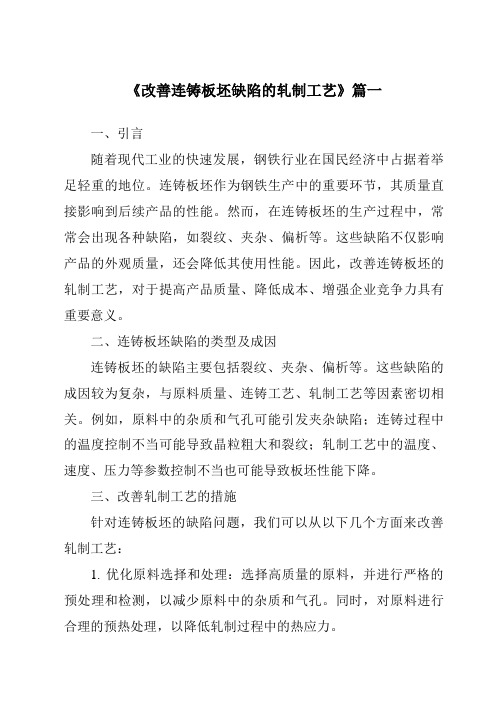
《改善连铸板坯缺陷的轧制工艺》篇一一、引言随着现代工业的快速发展,钢铁行业在国民经济中占据着举足轻重的地位。
连铸板坯作为钢铁生产中的重要环节,其质量直接影响到后续产品的性能。
然而,在连铸板坯的生产过程中,常常会出现各种缺陷,如裂纹、夹杂、偏析等。
这些缺陷不仅影响产品的外观质量,还会降低其使用性能。
因此,改善连铸板坯的轧制工艺,对于提高产品质量、降低成本、增强企业竞争力具有重要意义。
二、连铸板坯缺陷的类型及成因连铸板坯的缺陷主要包括裂纹、夹杂、偏析等。
这些缺陷的成因较为复杂,与原料质量、连铸工艺、轧制工艺等因素密切相关。
例如,原料中的杂质和气孔可能引发夹杂缺陷;连铸过程中的温度控制不当可能导致晶粒粗大和裂纹;轧制工艺中的温度、速度、压力等参数控制不当也可能导致板坯性能下降。
三、改善轧制工艺的措施针对连铸板坯的缺陷问题,我们可以从以下几个方面来改善轧制工艺:1. 优化原料选择和处理:选择高质量的原料,并进行严格的预处理和检测,以减少原料中的杂质和气孔。
同时,对原料进行合理的预热处理,以降低轧制过程中的热应力。
2. 合理控制连铸工艺参数:在连铸过程中,要严格控制温度、速度、冷却等工艺参数,以避免晶粒粗大和裂纹的产生。
同时,采用先进的连铸技术,如电磁搅拌、结晶器振动等,以改善板坯的内部质量。
3. 改进轧制工艺:在轧制过程中,要合理控制温度、速度、压力等参数,以保证板坯的轧制质量。
同时,采用先进的轧制技术,如轧制力控制、轧制速度控制等,以提高轧制过程的稳定性和精度。
4. 强化质量检测与监控:在轧制过程中,要加强质量检测与监控,及时发现并处理板坯的缺陷。
同时,建立完善的质量管理体系,对生产过程进行全面监控和管理。
四、实施效果与展望通过上述措施的实施,我们可以有效改善连铸板坯的轧制工艺,减少缺陷的产生,提高产品的质量。
具体而言,我们可以看到以下实施效果:1. 产品质量明显提高:通过优化原料、控制连铸和轧制工艺参数以及强化质量检测与监控等措施,连铸板坯的缺陷率得到有效降低,产品性能得到显著提高。
连铸坯缺陷及对策
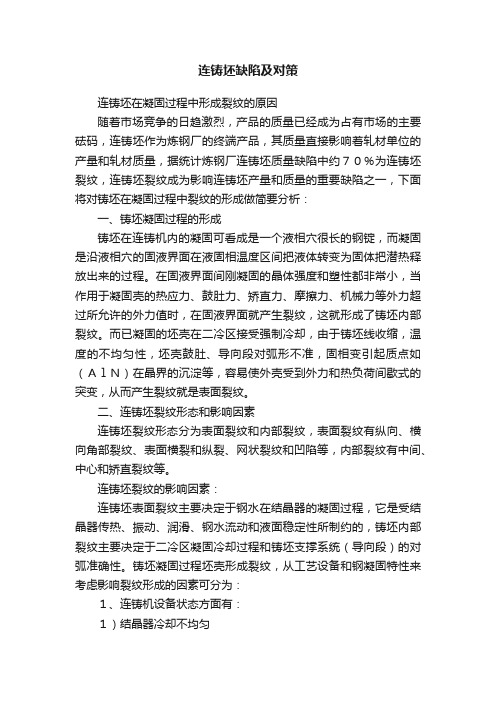
连铸坯缺陷及对策连铸坯在凝固过程中形成裂纹的原因随着市场竞争的日趋激烈,产品的质量已经成为占有市场的主要砝码,连铸坯作为炼钢厂的终端产品,其质量直接影响着轧材单位的产量和轧材质量,据统计炼钢厂连铸坯质量缺陷中约70%为连铸坯裂纹,连铸坯裂纹成为影响连铸坯产量和质量的重要缺陷之一,下面将对铸坯在凝固过程中裂纹的形成做简要分析:一、铸坯凝固过程的形成铸坯在连铸机内的凝固可看成是一个液相穴很长的钢锭,而凝固是沿液相穴的固液界面在液固相温度区间把液体转变为固体把潜热释放出来的过程。
在固液界面间刚凝固的晶体强度和塑性都非常小,当作用于凝固壳的热应力、鼓肚力、矫直力、摩擦力、机械力等外力超过所允许的外力值时,在固液界面就产生裂纹,这就形成了铸坯内部裂纹。
而已凝固的坯壳在二冷区接受强制冷却,由于铸坯线收缩,温度的不均匀性,坯壳鼓肚、导向段对弧形不准,固相变引起质点如(AlN)在晶界的沉淀等,容易使外壳受到外力和热负荷间歇式的突变,从而产生裂纹就是表面裂纹。
二、连铸坯裂纹形态和影响因素连铸坯裂纹形态分为表面裂纹和内部裂纹,表面裂纹有纵向、横向角部裂纹、表面横裂和纵裂、网状裂纹和凹陷等,内部裂纹有中间、中心和矫直裂纹等。
连铸坯裂纹的影响因素:连铸坯表面裂纹主要决定于钢水在结晶器的凝固过程,它是受结晶器传热、振动、润滑、钢水流动和液面稳定性所制约的,铸坯内部裂纹主要决定于二冷区凝固冷却过程和铸坯支撑系统(导向段)的对弧准确性。
铸坯凝固过程坯壳形成裂纹,从工艺设备和钢凝固特性来考虑影响裂纹形成的因素可分为:1、连铸机设备状态方面有:1)结晶器冷却不均匀2)结晶器角部形状不当。
3)结晶器锥度不合适。
4)结晶器振动不良。
5)二冷水分布不均匀(如喷淋管变形、喷咀堵塞等)。
6)支承辊对弧不准和变形。
2、工艺参数控制方面有:1)化学成份控制不良(如C、Mn/S)。
2)钢水过热度高。
3)结晶器液面波动太大。
4)保护渣性能不良。
5)水口扩径。
钢铁冶炼中的连铸坯表面问题分析

钢铁冶炼中的连铸坯表面问题分析钢铁冶炼工艺在现代工业中扮演着非常重要的角色。
然而,在钢铁冶炼过程中,连铸坯表面问题一直是制约钢铁品质的重要因素之一。
本文将详细分析钢铁冶炼中连铸坯表面问题的原因,并探讨相应的解决方案。
1.连铸坯表面问题的原因连铸坯的表面问题主要包括铁水热裂纹、气泡和氧化皮等。
这些问题的产生原因是多方面的。
首先,连铸坯自身的气泡问题是造成连铸坯表面缺陷的原因之一。
钢液在连铸过程中受到高速冷却的影响,表面会形成气泡,严重影响连铸坯外观质量。
其次,由于钢液表面存在氧化皮,当钢液从铸口流出时,氧化皮会不断地被冲刷、碾磨,进入钢液中产生非金属夹杂物。
这些夹杂物不仅会影响钢铁的机械性能,还会对钢铁表面形成气孔,使连铸坯表面平整度降低。
最后,因其连续铸造过程而产生的热应力是导致连铸坯热裂纹的主要原因。
连铸坯的外层由于接触空气而受到约束而形成静态压力,在冷却过程中,内层材料的收缩变形不一定跟上外层变形,就会导致热裂纹的产生。
2.解决方案目前,可以通过改变冶炼工艺来降低连铸坯表面问题的发生率。
以下是一些可行的方案:首先,应采取合适的措施降低钢液中气体的含量,从而减少产生气泡的概率。
可以通过使用脱气剂或杜氧少炉等方法降低气体含量。
其次,采取有效的措施去除钢液表面的氧化皮,并严格控制钢液的流速和流动状态,减少氧化皮的再生,从而减少在连铸过程中非金属夹杂物的产生。
最后,为了减小冶炼过程中钢铁的热应力,可以优化连铸工艺及连铸设备的设计,增加连铸温度和减少冷却速度等措施,使冷却过程变的温和,防止热裂纹的产生。
此外,我们还可以采用表面削除技术,该技术会削除连铸坯表面几毫米厚的层,以去除裂纹和氧化皮等缺陷,提高钢铁的机械性能和表面质量。
该技术适用于生产无缝钢管和铸轧板产品。
总之,钢铁冶炼中连铸坯表面问题的出现在一定程度上会影响钢铁的质量和产量。
为了解决连铸坯表面问题,在钢铁生产中,我们需要探索更加智能效益高、环保一体化的生产工艺技术和装备,不断提高钢铁生产效率和品质,为推进钢铁产业高质量发展打下坚实基础。
连铸圆坯缺陷类型

连铸圆坯缺陷类型摘要:一、连铸圆坯缺陷类型概述二、连铸圆坯常见缺陷及原因分析1.表面缺陷1.1 划伤1.2 麻点1.3 裂纹2.内部缺陷2.1 缩孔2.2 疏松2.3 夹渣三、连铸圆坯缺陷的控制与预防措施1.改进连铸工艺1.1 优化浇注制度1.2 控制结晶器振动2.提高钢水质量2.1 严格控制成分2.2 去除夹杂物3.设备维护与管理3.1 定期检查设备3.2 确保设备完好运行4.加强操作人员培训4.1 提高操作技能4.2 增强质量意识正文:连铸圆坯作为钢铁产业链中的重要环节,其质量直接影响到后续加工和产品性能。
然而,在连铸过程中,圆坯易出现各种缺陷,严重影响产品质量。
本文将对连铸圆坯的缺陷类型进行详细分析,并提出相应的控制与预防措施。
一、连铸圆坯缺陷类型概述连铸圆坯缺陷主要包括表面缺陷和内部缺陷。
表面缺陷主要包括划伤、麻点和裂纹等;内部缺陷主要包括缩孔、疏松和夹渣等。
二、连铸圆坯常见缺陷及原因分析1.表面缺陷(1)划伤:由于结晶器振动过大、铸坯与结晶器壁摩擦等原因导致。
(2)麻点:一般是由于钢水中氧化物等夹杂物在结晶器内壁上吸附形成的。
(3)裂纹:主要是由于铸坯收缩不均、内应力过大等因素引发。
2.内部缺陷(1)缩孔:由于铸坯在凝固过程中体积收缩,内部产生真空所致。
(2)疏松:钢水中的气体和夹杂物在凝固过程中未能及时排出,形成孔洞。
(3)夹渣:钢水中杂质含量过高,连铸过程中未能完全去除。
三、连铸圆坯缺陷的控制与预防措施1.改进连铸工艺(1)优化浇注制度,确保钢水在结晶器内充分凝固。
(2)控制结晶器振动,避免铸坯与结晶器壁过度摩擦。
2.提高钢水质量(1)严格控制成分,确保钢水纯洁度。
(2)去除夹杂物,降低钢水中氧化物含量。
3.设备维护与管理(1)定期检查设备,确保设备运行稳定。
(2)加强设备维护,提高设备使用寿命。
4.加强操作人员培训(1)提高操作人员技能水平,降低人为因素导致的缺陷。
(2)增强操作人员质量意识,从源头把控连铸圆坯质量。
连铸车间铸坯质量问题分析解决报告

连铸车间铸坯质量问题分析解决报告
本月19日轧钢厂反应铸坯存在质量问题,随即进行取样、切割、分析、调整(详见附表)。
一、具体采取措施如下:1、根据实际情况调整配水系数(由1.2L/kg调至
1.18L/kg)、配水比例(0段35%、1段50%、2段15%调至0段35%、1段45%、2段20%)。
2、控制钢水过热度。
3、调整结晶器铜管冷却水(由150m3/h调至130m3/h)。
4、整理喷淋架。
5、调整V流1段喷嘴。
6、堵0段4角2个下喷嘴。
二、具体效果:裂纹有所减轻,但不可完全消除。
V流效果明显。
三、存在问题:
1、因铸坯切后切割面发现不了裂纹,使在生产中调整滞后。
2、二冷水喷淋架、支撑架、分水环变形,铸坯跑偏导致配水不均匀,。
虽经整理,但偏差仍然存在。
影响调水结果与分析判断。
四、下步措施:
1、按流标准调整配水,进一步跟踪、分析。
2、尽快完善喷淋冷却系统,解决铸坯跑偏。
3、继续控制中包钢水过热度及生产节奏稳定拉速。
连铸坯剪切面不平缺陷的成因与对策
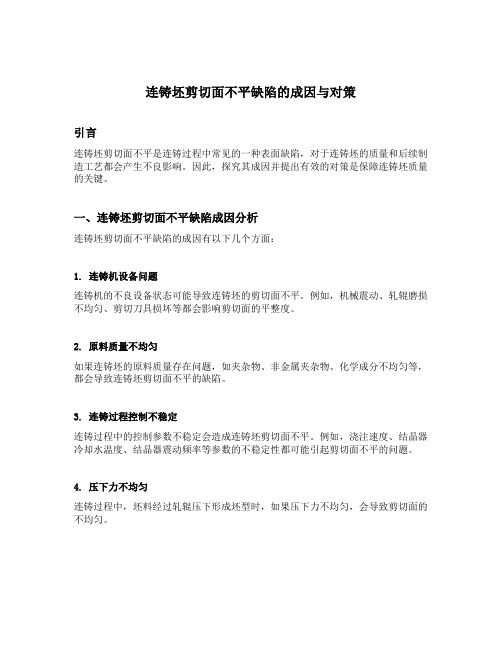
连铸坯剪切面不平缺陷的成因与对策引言连铸坯剪切面不平是连铸过程中常见的一种表面缺陷,对于连铸坯的质量和后续制造工艺都会产生不良影响。
因此,探究其成因并提出有效的对策是保障连铸坯质量的关键。
一、连铸坯剪切面不平缺陷成因分析连铸坯剪切面不平缺陷的成因有以下几个方面:1. 连铸机设备问题连铸机的不良设备状态可能导致连铸坯的剪切面不平。
例如,机械震动、轧辊磨损不均匀、剪切刀具损坏等都会影响剪切面的平整度。
2. 原料质量不均匀如果连铸坯的原料质量存在问题,如夹杂物、非金属夹杂物、化学成分不均匀等,都会导致连铸坯剪切面不平的缺陷。
3. 连铸过程控制不稳定连铸过程中的控制参数不稳定会造成连铸坯剪切面不平。
例如,浇注速度、结晶器冷却水温度、结晶器震动频率等参数的不稳定性都可能引起剪切面不平的问题。
4. 压下力不均匀连铸过程中,坯料经过轧辊压下形成坯型时,如果压下力不均匀,会导致剪切面的不均匀。
5. 剪切操作不当操作人员在剪切过程中的操作不当,如切刀刃口不尖锐、力度不均匀等,都可能造成剪切面不平缺陷的出现。
二、连铸坯剪切面不平缺陷对策针对连铸坯剪切面不平缺陷,可以采取以下对策来提高连铸坯的质量:1. 定期检查和维护连铸设备定期检查和维护连铸设备,确保设备处于良好的状态。
及时修复机械故障,更换磨损严重的轧辊和剪切刀具,提高设备的稳定性和工作效率。
2. 优化原料质量控制加强对原料质量的控制,确保原料的化学成分均匀,夹杂物和非金属夹杂物的含量控制在合理的范围内。
通过合理的混合和预处理工艺,提高原料的均匀性。
3. 稳定连铸过程参数加强对连铸过程参数的控制,保持浇注速度的稳定性,调整结晶器冷却水温度以提高均质化效果,合理控制结晶器震动频率等。
通过稳定的连铸过程,减少剪切面不平的概率。
4. 均匀施加压下力优化压下装置,保证连铸过程中施加的压下力均匀。
可以采用自适应控制技术,实时监测压下力,根据实际情况自动调整,提高剪切面的均匀度。
连铸坯缺陷及预防措施
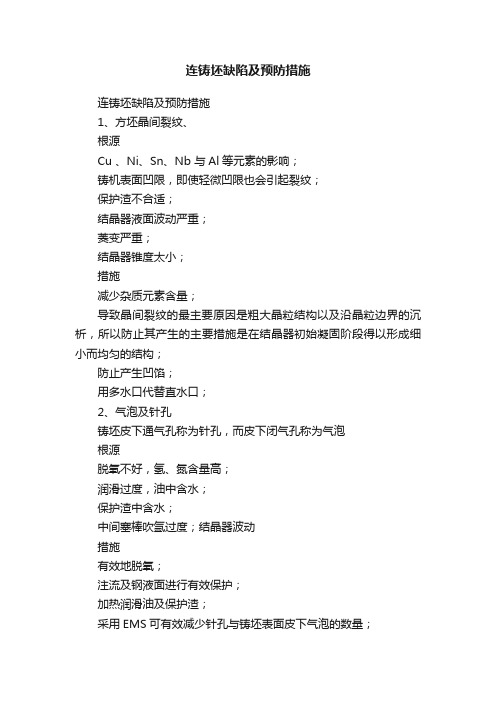
连铸坯缺陷及预防措施连铸坯缺陷及预防措施1、方坯晶间裂纹、根源Cu 、Ni、Sn、Nb 与Al等元素的影响;铸机表面凹限,即使轻微凹限也会引起裂纹;保护渣不合适;结晶器液面波动严重;菱变严重;结晶器锥度太小;措施减少杂质元素含量;导致晶间裂纹的最主要原因是粗大晶粒结构以及沿晶粒边界的沉析,所以防止其产生的主要措施是在结晶器初始凝固阶段得以形成细小而均匀的结构;防止产生凹馅;用多水口代替直水口;2、气泡及针孔铸坯皮下通气孔称为针孔,而皮下闭气孔称为气泡根源脱氧不好,氢、氮含量高;润滑过度,油中含水;保护渣中含水;中间塞棒吹氩过度;结晶器波动措施有效地脱氧;注流及钢液面进行有效保护;加热润滑油及保护渣;采用EMS可有效减少针孔与铸坯表面皮下气泡的数量;减少结晶器液面波动3、铸坯表面夹渣根源钢水脱氧不够;钢水中氧化铝含量高,SiO2、MnO与FeO含量低(铝镇静钢);耐火材料质量差;结晶器喂铝线;中包水口及结晶器中形成的块渣进入钢水。
措施采用无渣出钢;对钢水进行有效脱氧,采用保护浇注;中间包碱性覆盖剂;加深中包,增大中包钢液深度;中包采用挡堰;采用能快速吸收钢水夹杂的保护渣(高碱度);加大保护渣的用量;减少结晶器液面波动,水口侵入深度必须100-150mm4、横向裂纹横向裂纹通常出现在角部,但中部区域也会出现,横向裂纹一般出现在振痕的底部。
1、因热脆而形成的表面裂纹C含量0.17-0.25%;S含量高;随合金元素含量增加,如:Al、Nb、V 及大于1%Mn,裂纹数量增加;Al、Nb、N及C沉析于晶粒表面;二冷区冷却不挡导致晶粒粗大;二冷区支撑辊对中不好;保护渣选择不当;负滑脱时间过长。
2、横向角部裂纹角部冷却过度;结晶器冷却不当;结晶器和支撑辊对中不好;矫直温度过低;高如:Al、Nb、V 及大于1%Mn含量钢水非常敏感,加入钛能有效降低裂纹的程度;?二冷区冷却不均或冷却过度;保护渣不合适;铜管弯月面区域变形过大;钢水温度过低;结晶器锥度过大。
连铸坯剪切面不平缺陷的成因与对策

连铸坯剪切面不平缺陷的成因与对策
连铸坯剪切面不平缺陷的成因与对策
连铸坯是经过连铸机连续铸造而成的一种形态为长条的铸造品。
在连铸过程中,常常会出现剪切面不平的缺陷,给铸造生产造成很大的影响。
造成这种缺陷的原因有很多,但主要是由于结晶器板与坯料接触面积不够大,结晶器板与坯料之间存在导热不良的缺陷,以及坯料冷却不均匀等。
针对这种缺陷,我们可以采取以下对策:
1. 改进结晶器板的设计
为了增大结晶器板与坯料接触面积,可以在结晶器板上刻上一些凹槽或者凸起,这样就可以增大接触面积。
此外,还可以在结晶器板上加装导热管或者喷淋系统,调节结晶器板表面温度,保证结晶器板与坯料之间的导热性能良好。
2. 改变坯料的注入方式
一些连铸流程中存在注入速度过快的问题,造成坯料长条的中心部分
温度高,导致冷却不均。
为了解决这个问题,可以改变注入速度,控制坯料中心部位温度,在坯料结晶中心部位注入氧气或氩气,将过热的中心部位温度迅速冷却。
3. 确保冷却水的充足供应
坯料冷却不均的情况下,是由于冷却水没有充足供应,导致冷却不均匀。
为了确保充足水量,可以适量增加冷却水管的数量,确保冷却水的供应。
同时,可以在水管的位置上创造屏蔽作用,减少坯料受到的水流冲击,防止出现冷却不均的情况。
4. 增加坯料中添加剂的数量
在坯料中添加适当的添加剂,如钛、锆等元素,可以有效提高坯料的晶界能,促进晶界的形成,从而防止坯料在冷却过程中出现裂缝的情况。
总之,连铸坯的生产过程中,剪切面不平的缺陷是常见问题,但是通过上述对策,可以有效解决这个问题,提高工艺质量,提高连铸坯的生产效率和产量。
- 1、下载文档前请自行甄别文档内容的完整性,平台不提供额外的编辑、内容补充、找答案等附加服务。
- 2、"仅部分预览"的文档,不可在线预览部分如存在完整性等问题,可反馈申请退款(可完整预览的文档不适用该条件!)。
- 3、如文档侵犯您的权益,请联系客服反馈,我们会尽快为您处理(人工客服工作时间:9:00-18:30)。
连铸坯表面质量缺陷及处理措施
【摘要】对于连铸板坯而言,振痕和裂纹是其主要的质量缺陷问题。
虽然这个缺陷在大多数情况下对连铸坯的质量影响不大,但是如果不及时有效的处理调还会带来很多附加的质量问题。
尤其是在生产不锈钢和高强度钢品种时,这种质量缺陷所带来的弊端更加明显。
【关键词】连铸坯;振痕;质量影响
1振痕形成机理
在连铸坯生产中,振痕和裂纹是两种最为常见的质量缺陷问题,主要是由于弯月面顶端溢流造成的,该缺陷形成以后会附带其他质量缺陷一并产生。
2振痕对铸坯质量的影响
振痕对连铸坯的质量影响会导致后期出现列裂纹,包括横裂纹、角部横裂纹及矫直裂纹。
如果连铸坯内掺杂的杂质较多,会导致大规模网状裂纹的出现,甚至出现穿钢现象。
如果在连铸坯出现振痕的地方晶粒很大,就会产生晶间裂纹现象,在这样的情况下需要对连铸坯修磨,从而提高成材率。
3影响振痕深度的因素
振动参数对振痕形状和深度有重要影响。
其中振幅、频率、负滑脱时间及振动方式最为重要;结晶器保护渣的耗量、粘度、保温性能及表面性能等有着重要影响;.钢的凝固特性对振痕有着重要影响,特别是当钢中碳含量和钢中Ni/Cr 比影响最突出。
当钢中碳含量为0.1%左右,Ni/Cr≈0.55左右,铸坯表面振痕最深。
4减少振痕深度的措施
采用小振幅(s)、高频率(f)及减少负滑脱时间(tN),可以有效的减少振痕的深度;采用非正弦振动方式可以减少振痕的深度,这是因为非正弦振动其负滑脱时间tN比正弦振动短;采用渣耗量低,粘度高的保护渣,可以使振痕深度变浅。
采用保温性能好和能增加弯月面半径的保护渣可以减少振痕深度;提高不锈钢、钢液的过热度,尤其是含钛和含铝的不锈钢对减少该钢表面振痕深度是有效的。
提高结晶器进出冷却水的温差,对减少振痕深度是有利的。
5铸坯表面裂纹
5.1表面纵裂纹
铸坯表面纵裂纹是铸坯最主要表面缺陷,对铸坯质量影响极大,特别是板坯和圆坯最为突出,报废量和整修量很大。
5.1.1纵裂纹类型
铸坯表面沟槽纵裂纹。
这种裂纹在铸坯表面纵向沟槽内,裂纹通常又长、又宽、又深,严重时引起漏钢事故发生;铸坯表面平纵裂。
这种裂纹与表面一样平(或凹下很浅),而且直,长度较短(50~200mm左右),其深度和宽度在1~2mm 范围内;结晶器划痕引起铸坯表面纵裂纹。
5.1.2铸坯表面纵裂纹产生原因
铸坏表面纵裂纹产生的条件,一是由于初生坯壳生长不均匀;二是由于传热速度快(温度梯度大和传热不均匀);纵裂纹产生在结晶器由上部和水口附近。
似隐纹(未裂开)形成存在,随着铸坯下行时隐裂纹裂开成为开放式的纵裂纹。
同样钢种板坯比方坯纵裂要多。
与钢种密切相关,特别是碳的含量在0.09~0.14%纵裂纹最为严重,或者说亚包晶钢最为严重;结晶器内液面波动大,使弯月处传热不均匀,从而使初生坯壳生长不均匀引起纵裂纹产生;铸机对中(或对弧)不良和夹持辊开口度过大,使铸坯发生鼓肚,造成纵裂纹的产生;保护渣性能选择不当,这是板坯表面纵裂纹产生的最重要原因,尤其是保护渣的传热性能;结晶器振动参数选择不当,尤其是S、f、tN、NS和NSR的选择较为重要,因为这些参数对传热均匀性有影响;钢水质量对纵裂纹影响较大,尤其是过热度、可浇性及成分控制(C、S、P、Mn/S)最为重要。
同时不能忽视钢中Cu和As的含量对纵裂纹的影响;伸入水口尺寸选择不当和使用不当都能使铸坯表面纵裂纹增加;结晶器状况不良,如安装精度差、结晶器变形和结晶器锥度选择不当等都会引发表面纵裂纹;中间包塞捧吹Ar过大和冲棒操作增加纵裂纹的产生。
拉坯速度选择不当及变化频繁都会引起纵裂的产生。
5.1.3防治铸坯表面纵裂纹的措施
严格控制钢水的质量,如浇注温度、可浇性和成份,其中C、S、P、Mn/S 及Cu和As含量,通常将S和P控制0.02%左右,优质钢在0.01%以下;Mn/S≥25,最好大于30,S+P+As≤0.075;采用结晶器液面自动控制对减少纵裂纹是很有效的;铸机应保持良好状态,板坯采用密节辊铸机,尤其铸机对中(对弧)和夹持辊开口度的精度非常重要。
板坯要求小于±0.5mm方坯,控制在±1mm如宝钢板坯铸机对中精度大于0.5mm时,纵裂纹增多;选择性能良好的板坯结晶器保护渣是当今控制板坯纵裂纹最经济,最有效的手段,是控制纵裂特效“药”;选择合理的振动参数不仅能保持结晶器内传热均匀,而且保持工艺的顺利,从而减少纵裂纹;采用恒速浇注对减少纵裂纹是有益的。
严防塞棒吹Ar过大和“冲棒”操作,否则将会增加表面纵裂纹;选择合理的一冷和二冷制度,即采用“弱冷”。
5.2铸坯角部纵裂纹
5.2.1角部纵裂纹产生原因
板坯窄面支撑不当,造成窄面鼓肚,如窄面有6~12mm鼓肚,伴随角部纵裂纹产生,甚至导致漏钢;结晶器锥度选择不当——锥度过小;窄面冷却水不足,产生鼓肚;结晶器转角半径选择不当;水口在结晶器偏流(即不对中);
5.2.2防治角部纵裂纹的措施
调整窄面足辊间隙使其向内1~2mm,限制鼓肚;选择合适的锥度(1.0%/m);控制好侧边水量,不使窄面产生鼓肚;选择合适的结晶器转角半径;水口要对中不应偏流。
5.3表面横裂纹
表面横裂纹都出现在铸坯振痕谷处,而且内弧多于外弧,尤其是宽厚板坯更易出现。
C-Mn-Nb(V)钢更易出现,往往在横裂纹处有AlN的沉淀。
5.3.1横裂纹产生的原因
铸坯振痕过深易产生横裂纹;有Al、Nb、V、B含量的钢,易出现横裂纹;矫直温度选择不当,温度过低或在脆性区矫直易产生横裂纹;结晶器保护渣性能选择不当,使结晶内摩擦力过大;结晶器锥度选择过大,使结晶器内铸坯阻力过大;振动参数选择不当,使铸坯振痕较深阻力增加;二冷强度过大,又不均匀,易产生横裂纹;拉坯速度变换过频、过大。
5.3.2防止表面横裂纹的措施
结晶器采用高频率小振幅的振动方式;二冷采用均匀的弱冷制度,避免铸坯表面温度反复回升;矫直温度应高,并避开脆性区;选用性能良好的结晶器保护渣,尤其是润滑性能;结晶器液面波动要采用液面自动控制。
5.4角部横裂纹
由于结晶器锥度过大,铸坯阻力较大;结晶器表面划伤严重,增大结晶器铸坯阻力;结晶出口与零段对弧不准或对弧不对中造成拉坯阻力过大;矫直时铸坯角部温度过低,内弧角部产生横裂纹;拉矫机的压力在横向上不对称造成铸坯偏离中心线,使铸坯一侧边受压,另一侧边受拉,造成角部和侧边产生横裂纹。
通常在宽厚板坯和大方坯出现率较多,尤其是内弧角部横裂纹比外弧多。
防止期产生的措施是选择合适的结晶器锥角;严格对弧对中;调整二冷水,使铸坯角部在矫直时有较高的温度,应不小于800℃;选择良好性能的保护渣,减少角部振痕深度和良好润滑性能。
5.5铸坯表面星状和网状裂纹
通常在铸坯氧化铁皮覆盖的情况下表面星状裂纹和网状裂纹是难以发现的,经过技术处理后才显现出来,它们往往是成群在一起的细小的晶间隙裂纹,或呈星状或呈网状分布,有的也称龟裂,其深度3mm左右。
矫直时可能扩展成横裂纹,而这种裂纹是沿晶界开裂的。
严格意义上来讲星状裂纹与网状裂纹是有区别的。
星状裂纹主要由高温铸坯表面吸收了Cu而引起的;网状裂纹主要由中、高强度钢和钢中含有Nb、AlN、V、BN元素引的。
在轧制时这两种裂纹可以造成成品报废。
参考文献:
[1]田燕翔主编.《现代连铸新工艺、新技术与铸坯质量控制》.当代中国音像出版社.
[2]蔡开科程富士主编.《连续铸钢原理与工艺》.冶金工业出版社.
[3]冯捷贾艳主编.《连续铸钢实训》.冶金工业出版社.。