加工余量
加工余量的确定

层厚度。加工余量可分为工序加工余量和总加工 余量。 ? 工序加工余量是指某一表面在一道工序中所切除 的金属层厚度,它取决于同一表面相邻工序前后 工序尺寸之差。加工余量分为单面加工余量和双 面加工余量。如平面的加工,加工余量是单边余 量,它等于实际切除的金属层厚度。
xxxxxxxxx
(二)毛坯设计、质量要求及下料尺寸的计算 ? 模具零件毛坯的设计是否合理,对于模具零件加工的
工艺性以及模具的质员和寿命都有很大的影响,在毛坯的 设计中,首先考虑的是毛坯的形式,在决定毛坯形式时主 要考虑以下几个方面: ? 1、模具材料的类别。 根据在模具设汁中规定的模具材料 类别、可以确定毛坏形式。例如精密冲裁模的上、下模座 多为铸钢材料,大型覆盖件检深模的凸模、凹模和压边圈 零件为合金铸铁时,这类零件的毛坯形式必然为铸钢材料, 又如非标准模架的上、下模座材料多为45钢,毛坯形形 式应该是厚钢板的原型材 。 ? 2、模具材料的类别和作用。对于模具结构中的工作零件, 例如精密冲裁模和重载冲压模的工作零件,多为高碳高合金 工具钢,其毛坯形式应该为锻造件,高寿命冲我模的工作 零件材料多为硬质合金。其毛坯形式为粉末冶金件。对于 模具结构中的一般结构件,多选择原型材毛坯形式。
xxxxxxxxx
二、加工余量及毛坯下料尺寸的确定
(一)确定加工余量的方法 ? 1、经验估计法
根据工艺人员的经验确定加工余量的方法,但 这种方法不够准确。为了防止加工余量不够而产 生废品,所估计的加工余量一般偏大,此法常用 于单件小批生产。 ? 2、查表修正法
查阅有关加工余量的手册来确定,应用比较广 泛。在查表时应注意表中数据是公称值。对称表 面(如轴或孔)的加工余量是双边的,非对称表 面的加工余量是单边的。
加工余量的确定..

1. 加工余量概念
(1)总加工余量
总加工余量是指零件加工过 程中,某加工表面所切去的 金属层总厚度。是毛坯尺寸 与零件图样的设计尺寸之差。
(2)工序余量
工序余量是一道工序内切除的 金属层厚度,为相邻两工序的 工序尺寸之差。
(3)总余量为各工序余量之和
(4)公称余量
公称余量是指相邻两 工序的基本尺寸之差。
(5)余量公差
Tz Z max Z min Ti Ti 1
2. 影响加工余量的因素
1、上工序的表面粗糙度和表面缺陷层(图7-24) 2、上工序的尺寸公差(图7-25) 3、上工序各表面间相互位置的空间偏差(图7-26) 4、本工序安装误差(图7-27)
的尺寸及公差。
解: 1)确定封闭环、建立尺寸链、判别增减环。
假废品的出现
只要测量尺寸的超差量小于或等于其余组成环 尺寸公差之和,就有可能出现假废品,为此应对该 零件各有关尺寸进行复检和验算,以免将实际合格 的零件报废而导致浪费。 假废品的出现,给生产质量管理带来诸多麻烦, 因此,不到非不得已,不要使工艺基准与设计基准 不重合。
3.有关余量的尺寸换算
图9-29 精加工余量校核示例 (1)精加工余量校核 当多次加工某一表面时, 由于所采用的工艺基准可能相同,因此,本工 序的余量的变动量不仅与本工序的公差及前一 工序的公差有关,而且还与其它有关工序的公 差有关。在以工序余量为封闭环的工艺尺寸链 中,如果组成环数目较多,由于误差累积原因, 有可能使工序余量过大或过小,因此须对余量 进行校核, 这在制订工艺规程时是一个不可忽 视的问题。由于粗加工的余量一般取值较大, 故粗加工余量一般不进行校核而仅对精加工余 量进行校核。
加工余量的确定方法

加工余量的确定方法
加工余量是指在加工过程中,为了保证零件尺寸精度和形状精度,特意留下的一定尺寸差,一般为正值。
确定加工余量的方法有以下几种:
1. 根据经验法确定:根据过去的经验和加工零件的特点,确定适当的加工余量。
这种方法简单易行,但需要工人具备丰富的经验。
2. 根据公式法确定:根据零件的设计尺寸、材料特性、加工工艺,利用公式计算得出加工余量。
常见的公式有线性公式、面积公式和体积公式等。
3. 根据定额法确定:根据工艺定额和产品标准,确定加工余量。
这种方法适用于大批量生产,可以确保零件的一致性。
4. 根据测量法确定:先制作出一个初步尺寸较大的零件,然后通过测量零件尺寸并与设计尺寸进行比较,确定需要增加的加工余量。
这种方法需要较为精确的测量工具和技术。
无论采用何种方法确定加工余量,都需要考虑材料性能、工艺要求、设备精度等因素,以保证零件在加工过程中不仅符合设计要求,还能满足使用要求。
加工余量及工序尺

尺寸链图
2.2、基准不重合的计算
尺寸链图
工艺尺寸链的构成,取决于工艺方案和加工方法, 确定封闭环是关键; 一个尺寸链只能解一个封闭环;
请注意箭头方向:
与封闭环同向者为减环 与封闭环异向者为增环
2.2、基准不重合的计算
尺寸链图
2.2、基准不重合的计算
尺寸链图
2.2、基准不重合的计算
2.2、基准不重合的计算
尺寸链的组成
封闭坏——最终被间接保证精度的那个环 组成环——除封闭环之外的所有其他环
A1
A1
设计基准
A2
A2
A1
A3
定位基准
2.2、基准不重合的计算
尺寸链的组成
增环——当其余各组成环不变,而该环增大时使封闭环也 增大者,及该环减小时使封闭环也减小者 减环——当其余各组成环不变,而该环增大时使封闭环反 而减小者,及该环减小时使封闭环反而增大者
1.3、加工余量的确定
3)计算公式
公称余量(简称余量):
大尺寸基本尺寸-小尺寸基本尺寸
最大余量Zmax:
大尺寸基本尺寸+大尺寸上偏差-小尺寸基本尺寸-小尺寸下偏差
最小余量Zmin:
大尺寸基本尺寸+大尺寸下偏差-小尺寸基本尺寸-小尺寸上偏差
1.3、加工余量的确定
3)计算例子
1.3、加工余量的确定
数控机床加工余量的确定

实现加工余量的自动化控制,提高加工效率。
3
智能化决策
利用人工智能技术,实现加工余量的智能化决策 和控制。
谢谢观看
刀具寿命
刀具寿命较短时,需要较大的加工余量以避免刀具破 损。
刀具类型
不同类型的刀具具有不同的切削性能,因此需要根据 刀具类型确定合适的加工余量。
03
数控机床加工余量的优 化
优化目标与约束条件
优化目标
在满足加工精度和表面质量的前提下,最小化加工余量,提高加工效率。
约束条件
加工过程中的切削力、切削热、刀具磨损等因素需在可承受范围内,同时确保 加工过程的稳定性和可靠性。
优化算法的选择与应用
遗传算法
通过模拟生物进化过程中的遗传 机制,实现全局搜索最优解。适 用于多变量、非线性、离散型优 化问题。
粒子群算法
模拟鸟群、鱼群等生物群体的觅 食行为,通过个体间的信息共享 和协作,寻找全局最优解。适用 于连续型优化问题。
模拟退火算法
借鉴固体退火原理,通过随机搜 索和概率接受劣解,避免陷入局 部最优解。适用于多约束、非线 性优化问题。
04
数控机床加工余量的控 制
加工过程的实时监控
实时采集数据
通过传感器和监测设备,实时采集数控机床的加工数据,如切削 力、切削温度、刀具磨损等。
数据分析与处理
对采集到的实时数据进行处理和分析,以评估加工过程的稳定性 和预测余量变化。
异常检测与报警
通过实时监控系统,及时发现加工过程中的异常情况,如刀具磨 损过度、切削力异常等,并发出报警提示。
数控机床加工余量的确定
目录
• 数控机床加工余量概述 • 数控机床加工余量的计算 • 数控机床加工余量的优化 • 数控机床加工余量的控制 • 数控机床加工余量的未来发展
加工余量的确定.

图3
由图可看出: 公称加工余量 = 前工序尺寸 - 本工序尺寸 最小加工余量=前工序尺寸的最小值 - 本工序尺寸的最大值 最大加工余量=前工序尺寸的最大值 - 本工序尺寸的最小值 工序加工余量的变动范围(最大加工余量与最小加工余量之差)= 前工序工序尺寸公差+ 本工序的工序尺寸公差
(二)总加工余量:总加工余量是指零件从毛坯变为成品的整个加工过 程中从某一表面所切除金属层的总厚度,也即零件毛坯尺寸与零件图 上设计尺寸之差。总加工余量等于各工序加工余量之和,即
z
zi
总
= zi
i =1
n
式中 n–––某一表面的工序(或工步)数目。
--第i道工序加工余量
图4
二、影响加工余量的因素
(一)前工序的工序尺寸公差(Ta)。
(二)前工序形成的表面粗糙度和表面缺陷层深度(Ra+Da)。
(三)前工序形成的形状误差和位置误差(△x、△w)。
(四)本工序的装夹误差(εb)。
三、确定加工余量的方法
(一)查表修正法 (目前应用最广)
(二)经验估计法 (只适用于单件、小批生产)
(三)分析计算法 (目前应用较少)
余量为单边余量
图1
2、旋转表面:
对于轴:Z=da-db 对于孔:Z=db-da
余量为双边余量
图2
• 工序余量和工序尺寸及其公差的 计算公式: (轴) • Z=Zmin+Ta • Zmax=Z+Tb= Zmin+Ta +Tb • 式中 Zmin——最小工序余量 Zmax——最大工序余量 Ta——上工序尺寸的公差 Tb——本工序尺寸的公差
加工的概念
加工余量:在机械加工过程中,从加工表面切去的金属层厚度。
加工余量的计算公式
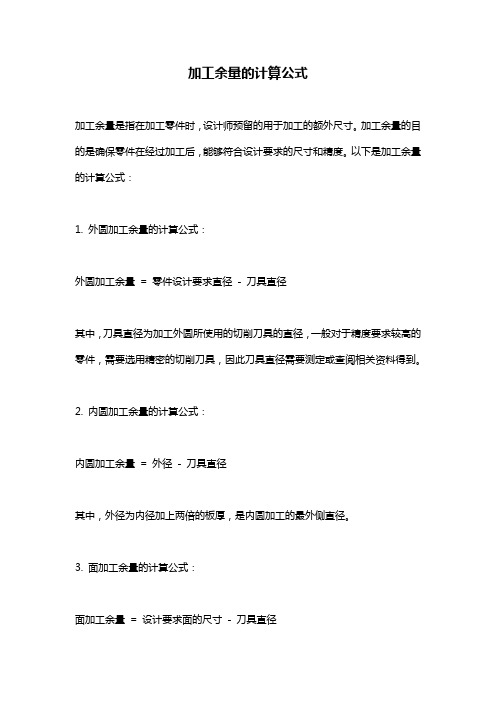
加工余量的计算公式
加工余量是指在加工零件时,设计师预留的用于加工的额外尺寸。
加工余量的目的是确保零件在经过加工后,能够符合设计要求的尺寸和精度。
以下是加工余量的计算公式:
1. 外圆加工余量的计算公式:
外圆加工余量= 零件设计要求直径- 刀具直径
其中,刀具直径为加工外圆所使用的切削刀具的直径,一般对于精度要求较高的零件,需要选用精密的切削刀具,因此刀具直径需要测定或查阅相关资料得到。
2. 内圆加工余量的计算公式:
内圆加工余量= 外径- 刀具直径
其中,外径为内径加上两倍的板厚,是内圆加工的最外侧直径。
3. 面加工余量的计算公式:
面加工余量= 设计要求面的尺寸- 刀具直径
其中,面的尺寸是指设计要求的面的长度或宽度。
需要注意的是,在进行加工余量的计算时,需要考虑到加工材料的特性、切削刀具的类型和精度、零件的尺寸和形状等多种因素,以确保加工余量的计算准确无误。
加工余量工序尺寸与公差
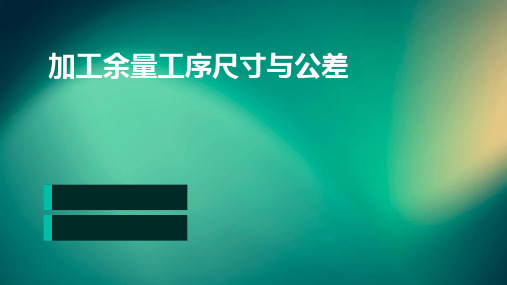
原则
公差配合的选择应满足使用要求, 既要保证机器或部件的精度和性 能,又要使其具有良好的经济效 益。
公差配合类型选择依据
01
间隙配合
过盈配合
02
03
过渡配合
具有间隙(包括最小间隙等于零) 的配合。孔的公差带在轴的公差 带之上。
具有过盈(包括最小过盈等于零) 的配合。孔的公差带在轴的公差 带之下。
可能具有间隙或过盈的配合。孔 的公差带与轴的公差带相互交叠。
提高加工效率
优化切削参数、减少非切削时间等措施,提高加工效率,降低生产 成本。
推动智能化发展
加强数字化基础设施建设、推广智能制造标准等举措,推动企业实 现智能化转型,提升竞争力。
THANKS FOR WATCHING
感谢您的观看
1 2
关键零部件识别
通过对产品结构和功能进行深入分析,识别出对 产品质量和性能有重要影响的关键零部件。
加工余量优化
针对关键零部件的加工特点和使用要求,合理优 化加工余量,减少不必要的材料浪费和加工成本。
3
工序尺寸控制
通过精确控制各道工序的加工尺寸和公差范围, 确保关键零部件的加工精度和一致性。
提升产品精度和稳定性经验总结
加工余量工序尺寸与公差
目录
• 加工余量概述 • 工序尺寸分析 • 公差配合原理及应用 • 加工余量、工序尺寸与公差关系探讨 • 实际应用举例与案例分析 • 未来发展趋势预测与挑战应对
01 加工余量概述
定义与作用
加工余量的定义
加工余量是指在加工过程中,为保证零件的加工精度和表面质量,在工序尺寸上预留的金属层厚度。
合理确定加工余量和工序尺寸方法论述
根据产品图纸和技术要求 确定工序尺寸和公差等级;
《加工余量的确定》课件

加工余量的作用
01
02
03
控制加工精度
通过合理确定加工余量, 可以保证工件的尺寸、形 状和位置精度,提高产品 质量。
提高生产效率
适当增大加工余量可以减 少加工次数和时间,提高 生产效率。
降低制造成本
合理控制加工余量可以减 少刀具磨损、降低能耗和 减少原材料消耗,从而降 低制造成本。
经验估算法 01
基于经验估算
02
这种方法主要依赖于工程师或技 术人员的经验,通过对比类似案 例或历史数据来估算加工余量。
优点:简单易行,快速得到结果 。
03
缺点:依赖于个人经验,可能存 在误差。
04
统计分析法
01
基于数据统计和分析
02
通过收集大量的加工数据,进行统计分析,找出加工余量与加工参数 之间的关系。
《加工余量的确定》 ppt课件
目录
• 加工余量概述 • 加工余量确定的方法 • 加工余量确定的影响因素 • 加工余量确定的实际应用 • 加工余量确定的发展趋势
01
加工余量概述
加工余量的定义
加工余量:在机械加工过程中,为了 去除工件上多余的材料或达到一定的 加工精度要求,而预先设定的材料去 除量。
切削液的选择
01 02 03 04
切削液的选择对加工余量的确定也有重要影响。
切削液具有冷却、润滑和清洗等作用,能够降低切削温度、减小切削 力和提高加工质量。
选择合适的切削液可以延长刀具的使用寿命,减小刀具的磨损和破损 ,从而合理地确定加工余量。
在选择切削液时,需要考虑工件材料、刀具材料、切削参数和切削条 件等因素。
03
优点:基于数据,较为客观。
加工余量的确定方法
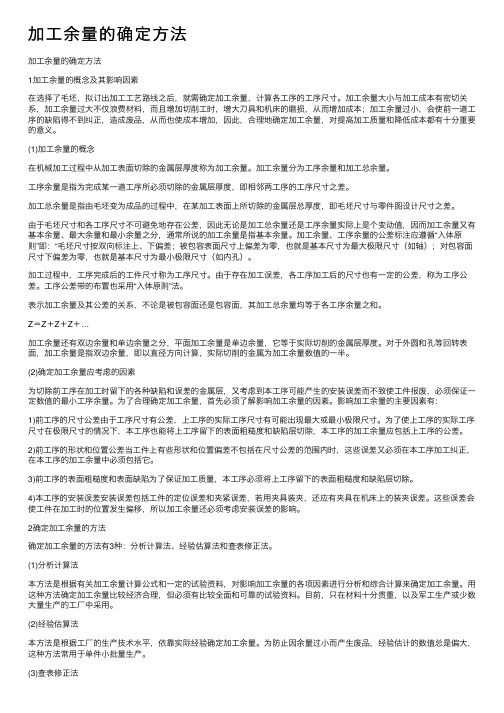
加⼯余量的确定⽅法加⼯余量的确定⽅法1加⼯余量的概念及其影响因素在选择了⽑坯,拟订出加⼯⼯艺路线之后,就需确定加⼯余量,计算各⼯序的⼯序尺⼨。
加⼯余量⼤⼩与加⼯成本有密切关系,加⼯余量过⼤不仅浪费材料,⽽且增加切削⼯时,增⼤⼑具和机床的磨损,从⽽增加成本;加⼯余量过⼩,会使前⼀道⼯序的缺陷得不到纠正,造成废品,从⽽也使成本增加,因此,合理地确定加⼯余量,对提⾼加⼯质量和降低成本都有⼗分重要的意义。
(1)加⼯余量的概念在机械加⼯过程中从加⼯表⾯切除的⾦属层厚度称为加⼯余量。
加⼯余量分为⼯序余量和加⼯总余量。
⼯序余量是指为完成某⼀道⼯序所必须切除的⾦属层厚度,即相邻两⼯序的⼯序尺⼨之差。
加⼯总余量是指由⽑坯变为成品的过程中,在某加⼯表⾯上所切除的⾦属层总厚度,即⽑坯尺⼨与零件图设计尺⼨之差。
由于⽑坯尺⼨和各⼯序尺⼨不可避免地存在公差,因此⽆论是加⼯总余量还是⼯序余量实际上是个变动值,因⽽加⼯余量⼜有基本余量、最⼤余量和最⼩余量之分,通常所说的加⼯余量是指基本余量。
加⼯余量、⼯序余量的公差标注应遵循“⼊体原则”即:“⽑坯尺⼨按双向标注上、下偏差;被包容表⾯尺⼨上偏差为零,也就是基本尺⼨为最⼤极限尺⼨(如轴);对包容⾯尺⼨下偏差为零,也就是基本尺⼨为最⼩极限尺⼨(如内孔)。
加⼯过程中,⼯序完成后的⼯件尺⼨称为⼯序尺⼨。
由于存在加⼯误差,各⼯序加⼯后的尺⼨也有⼀定的公差,称为⼯序公差。
⼯序公差带的布置也采⽤“⼊体原则”法。
表⽰加⼯余量及其公差的关系,不论是被包容⾯还是包容⾯,其加⼯总余量均等于各⼯序余量之和。
Z=Z+Z+Z+…加⼯余量还有双边余量和单边余量之分,平⾯加⼯余量是单边余量,它等于实际切削的⾦属层厚度。
对于外圆和孔等回转表⾯,加⼯余量是指双边余量,即以直径⽅向计算,实际切削的⾦属为加⼯余量数值的⼀半。
(2)确定加⼯余量应考虑的因素为切除前⼯序在加⼯时留下的各种缺陷和误差的⾦属层,⼜考虑到本⼯序可能产⽣的安装误差⽽不致使⼯件报废,必须保证⼀定数值的最⼩⼯序余量。
加工余量与工序尺寸

加工余量与工序尺寸
目录
contents
加工余量概述 工序尺寸确定 加工余量与工序尺寸的关系 加工余量与工序尺寸的实例分析 加工余量与工序尺寸的未来发展
01
加工余量概述
加工余量的定义
加工余量是指工件在加工过程中,为了去除工件表面的材料或修正误差而预留的额外材料。
它通常由工序前后的尺寸差值来表示,是评价加工精度和工艺水平的重要参数。
偏差
工序尺寸的公差与偏差
03
加工余量与工序尺寸的关系
加工余量对工序尺寸的影响
加工余量决定了工件在加工过程中的尺寸变化,是影响工序尺寸的主要因素之一。
加工余量的大小直接影响到加工精度和表面质量,因此需要合理控制加工余量,以保证工件的质量和性能。
VS
工序尺寸是工件在加工过程中需要达到的尺寸要求,是确定加工余量的重要依据。
智能化控制技术
通过传感器和监测设备,实时获取加工过程中的数据,对加工余量和工序尺寸进行动态调整,确保加工过程的稳定性和一致性。
实时监测与反馈
研发和应用环保、低毒、高效的切削液,减少对环境的污染和对人体的危害。
采用新型的加工设备和工艺,降低能耗和减少废弃物排放,实现
总结词:铣削加工余量与工序尺寸的确定对于提高加工效率和加工质量具有重要意义。
实例三:磨削加工余量与工序尺寸
总结词:磨削加工余量与工序尺寸的确定对于提高零件的耐磨性和疲劳强度至关重要。
05
加工余量与工序尺寸的未来发展
加工余量与工序尺寸的智能化控制
利用人工智能、机器学习等技术,实现加工余量和工序尺寸的智能预测和控制,提高加工精度和效率。
经验法
根据加工理论、材料力学和热力学等理论知识,结合加工工艺参数,计算出工序尺寸。理论法具有较高的精度和可重复性,但需要扎实的理论基础和计算能力。
机械制造工艺-加工余量、工序尺寸及公差
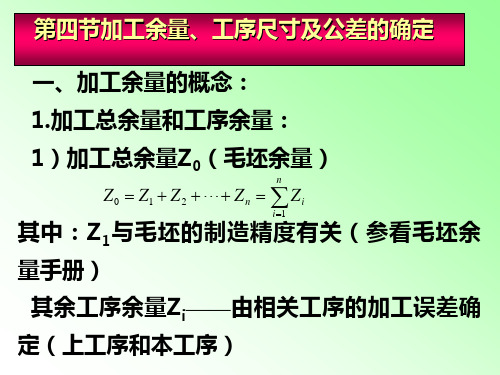
例题: 某轴直径φ50mm,其尺寸精度为IT5,表
面粗糙度为Ra0.04μm,并要求高频淬火,毛 坯为锻件。其工艺路线为:粗车-半精车 -高频淬火-粗磨-精磨-研磨,计算轴 的各工序尺寸及公差 解:
加工余量:由工艺手册确定。 工序尺寸:研磨工序尺寸即零件的设计 尺寸50-0.011 、Ra0.04μm
n1
T0 Ti i1
注: 公差的值大小——应按国标规定各公
差等级标准选取。 当T0一定时,各环公差Ti随n增加而减小。
3、封闭环的上偏差ES0
m
n1
ES0 ESp EIq
p1
qm1
ESP——增环上偏差 EIq——减环下偏差 m——增环环数
4、封闭环的下偏差EI0
m
n1
EI0 EIp ESq
1)基准不重合(待加工表面为工序基准) 2)待加工表面留有余量Z
解:画工艺尺寸链图(图1-45) (方法:从一个尺寸出发,到尺寸的基准后转
入相接的下一个尺寸链,通过所有相关联尺寸, 最终返回出发点。)P53 其中,键槽深为由本工序和终工序而间接获得, 为封闭环。 解得:L2=53.7(本工序工序尺寸及公差)
例:图4-22轴线弯曲造成的余量不均匀误差。 各项位置误差造成的影响参看表4-11
4)本工序的装夹误差εb 包括定位误差、夹紧误差。
5)余量计算公式 由于空间位置误差和装夹误差的
方向性,所以用矢量相加表示。 单边余量
Zmin Ta Ry Ha ea b
双边余量
Zmin Ta / 2 Ry Ha ea b
求:本工序工序尺寸L2(渗碳深度) 分析:渗碳层保留深度L0 —单边值(图面尺寸)
渗碳深度L2—单边值。 按尺寸链图,代入公式求解得:L2=0.7+0.025
一.加工余量的概念.
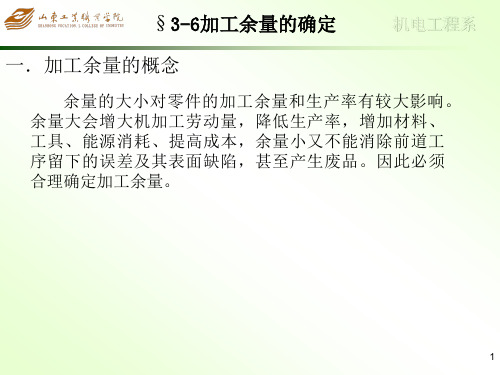
二.工序余量的影响因素
机电工程系
第一道粗加工工序余量与毛坯制造精度有关。毛坯 制造精度高则第一道粗加工序加工工序余量小,毛坯 制造精度低则第一道粗加工工序的加工余量就大。其 它工序的工序余量的影响因素有以下几个方面: 1.上工序的尺寸公差 Ta:本工序应切除上道工序尺寸 公差中包含的各种可能产生的误差。 2.上道工序产生的表面粗糙度 Ry和表面缺陷层深度 Ha 。
机电工程系
4
机电工程系
余量公差:工序尺寸有公差,所以加工余量也必然在 某一公差范围内变化,其公差大小等于本道工序尺寸 公差与上道工序尺寸公差之和 TZ=Zmax-Zmin=Tb+Ta TZ——工序余量公差 Zmax——工序最大余量 Zmin——工序最小余量 Tb——本道工序的工序尺寸公差 Ta——上道工序的工序尺寸公差 Zb——工序基本余量
6
机电工程系
7
机电工程系
3.上工序留下的需单独考虑的空间误差εa ,这些误差 可能是上工序加工方法带来的,也可能是热处理后产生 的,也可能是毛坯带来的。如下图所示的轴线直线度误 差和表表1—18所示的各种位置误差。
8
机电工程系
4.本工序的装夹误差εb:定位误差和夹紧误差。此项 误差直接影响被加工表面和切削刀具的相对位置,所 以加工余量中应该包括此项误差。 5.余量计算公式 如下图所示 单边: Z min Ta R y H a ea b
加工总余量:毛坯尺寸与余零件设计尺寸之差,其大 小取决于加工过程中每个工序切除金属层厚度的总和。 工序余量:每一工序所切除的金属层厚度称为工序余 量。 加工总余量和工序余量之间的关系用下式表示:
Z0=Z1+Z2+Z3+…+Zn=
加工余量、工序尺寸与工序公差的确定

61.5
61.500.018 61.500.018 0.4
细镗
0.3
H
6(
0.018 0
)
0.8
61.5-0.003=61.497 61.49700.018
61.500..001053
0.8
精镗
0.7
H
9(
0.046 0
)
1.6
61.497-0.3=61.2
61.200.046
61.200.05 1.6
5.4.1加工余量的概念
总余量与工步余量 之间的关系:
n
Zs Zi i1
粗刨Z1 精刨Z2 磨Z3
H1 H2
Zs H设 H坯
式中:Zs—某加工表面的总余量; n—该表面的机械加工工序(工步)数; Zi—该表面第i个工序(工步)的加工余量。
5.4.1加工余量的概念
设某加工表面上道工序的尺寸为a,本道工序的 尺寸为b,则本道工序的基本余量Zb可以表示为:
Zmin Ta 2(Ry H a )
5.4.2确定加工余量的方法
1.分析计算法
2)无心磨床磨外圆时无装夹误差,公式可简化
为:
Zmin Ta 2(Ry H a ) 2 | a |
砂轮 工件
导轮
托板
5.4.2确定加工余量的方法
3)精密加工方法如研磨、珩磨、 超精加工等,加工时仅去掉上 工序留下的加工痕迹,公式可 简化为:
3)除终加工工序外,根据各工序的加工方法及其经 济加工精度,确定其工序公差和粗糙度。
4)按入体原则以单向偏差方式标注工序尺寸,并可 作适当调整。
5.4.3工序尺寸及公差的确定
例5.1
某连杆大头孔的设计尺
加工余量、工序尺寸与工序公差的确定

加工余量、工序尺寸与工序公差的确定加工余量、工序尺寸与工序公差的确定是制造过程中非常重要的环节。
这些参数的正确选择可以确保产品的质量和性能符合设计要求,同时也可以提高生产效率和减少成本。
首先,加工余量是指工件的最终尺寸与设计尺寸之间的差值。
加工余量的大小会直接影响到零件的相对尺寸和形状。
通常情况下,在加工过程中需要保留适当的加工余量,以确保加工后的尺寸与设计要求相符。
加工余量的选择需要考虑材料的收缩率、热胀冷缩等因素,并结合加工方法和机械设备的精度要求进行确定。
其次,工序尺寸是指在制造过程中每个工序中所需达到的尺寸要求。
在多道工序的加工中,每个工序所要求的尺寸有时会与前后工序有关。
因此,确定工序尺寸时需要考虑工序之间的配合要求,以确保各工序之间的相互协调和流畅。
最后,工序公差是指在加工过程中允许的尺寸偏差范围。
工序公差可以直接影响到产品的装配性能、运转精度和可靠性。
确定工序公差时需要综合考虑产品的功能要求、装配及使用条件、工艺能力等因素。
通常情况下,工序公差需要在确保产品质量和性能的前提下尽量缩小,以提高生产效率和降低成本。
总而言之,加工余量、工序尺寸和工序公差的确定是制造过程中十分重要的环节。
正确选择和确定这些参数,可以确保产品符合设计要求,同时提高生产效率和降低成本。
因此,在进行加工过程中,工程师和技术人员需要综合考虑多种因素,并依据实际情况进行合理的确定。
加工余量、工序尺寸与工序公差的确定是制造过程中非常重要的环节。
这些参数的正确选择可以确保产品的质量和性能符合设计要求,同时也可以提高生产效率和减少成本。
加工余量是在加工过程中需要保留的尺寸差值。
加工余量的大小会直接影响到零件的相对尺寸和形状。
加工过程中的各种因素,如材料的物理特性、工件的几何形状、加工方法的选择等都会影响到加工余量的确定。
首先,材料的收缩率是影响加工余量选择的重要因素。
不同材料的收缩率不同,加工后的尺寸会有所变化。
在设计零件时,需要预留一定的加工余量,以弥补加工过程中材料收缩产生的尺寸变化。
机械加工工艺-加工余量、工序尺寸及公差
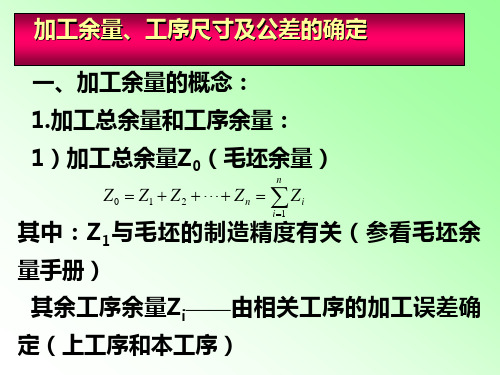
(一)设计 1、合理的结构工艺性、加工精度、表面
粗糙等。 2、零件、部件、产品的三化程度(通用、
标准、系列) (二)先进的工艺及设备
1、毛坯 2、机加工 3、装配
(三)先进的管理:计划、准备、服务、技术、
质量、经济分析等。
提高机加工生产率的工艺途径:
(一)缩短t基 1、(V、F、ap)↑。 2、多刀、多刃、及单刀多件等。
加工余量、工序尺寸及公差的确定
一、加工余量的概念: 1.加工总余量和工序余量: 1)加工总余量Z0(毛坯余量)
n
Z0 Z1 Z2 Zn Zi i 1
其中:Z1与毛坯的制造精度有关(参看毛坯余 量手册)
其余工序余量Zi——由相关工序的加工误差确 定(上工序和本工序)
2)工序余量Zi——相邻两工序基本尺寸之差;
求:本工序工序尺寸L2(渗碳深度) 分析:渗碳层保留深度L0 —单边值(图面尺寸)
渗碳深度L2—单边值。 按尺寸链图,代入公式求解得:L2=0.7+0.025
+0.008
(四)、余量校核 各工序中加工余量由查表及经验确定。 因为各工序尺寸的公差存在,实际余量是变化 的。 例图1-49,
1、工艺路线 1)精车A面,由B处切断。 2)以A面定位,精车B面。 3)以B面定位,磨A面。 4)以A面定位,磨B面。
三、用图表法确定工序尺寸及余量 适用于当零件同一方向尺寸较多的复杂情况。 如:工序多,工序基准转换多,工序中基准不 重合需用尺寸链计算,公差,余量确定复杂。 步骤: (一)绘制加工过程尺寸联系图
1、画出工件简图,标注相关设计尺寸。 2、按加工工序列表填写工艺过程,画加工符 号(箭头等)。 (二)工艺尺寸链查找
尺寸链中封闭环只有一个,用L0表示。 工艺尺寸链中的封闭环的定义见P.53倒10行。
加工余量

加工余量为了加工出合格的零件,必须从毛坯上切去的那层金属的厚度,称为加工余量。
加工余量又可分为工序余量和总余量。
某工序中需要切除的那层金属厚度,称为该工序的加工余量。
从毛坯到成品总共需要切除的余量,称为总余量,等于相应表面各工序余量之和。
在工件上留加工余量的目的是为了切除上一道工序所留下来的加工误差和表面缺陷,如铸件表面冷硬层、气孔、夹砂层,锻件表面的氧化皮、脱碳层、表面裂纹,切削加工后的内应力层和表面粗糙度等。
从而提高工件的精度和表面粗糙度。
加工余量的大小对加工质量和生产效率均有较大影响。
加工余量过大,不仅增加了机械加工的劳动量,降低了生产率,而且增加了材料、工具和电力消耗,提高了加工成本。
若加工余量过小,则既不能消除上道工序的各种缺陷和误差,又不能补偿本工序加工时的装夹误差,造成废品。
其选取原则是在保证质量的前提下,使余量尽可能小。
一般说来,越是精加工,工序余量越小。
编辑本段基准机械零件是由若干个表面组成的,研究零件表面的相对关系,必须确定一个基准,基准是零件上用来确定其它点、线、面的位置所依据的点、线、面。
根据基准的不同功能,基准可分为设计基准和工艺基准两类。
1.设计基准在零件图上用以确定其它点、线、面位置的基准,称为设计基准。
如图32-2所[cc2]示的轴套零件,各外圆和内孔的设计基准是零件的轴心线,端面A是端面B、C的设计基准,内孔的轴线是外圆径向跳动的基准。
2.工艺基准零件在加工和装配过程中所使用的基准,称为工艺基准。
工艺基准按用途不同又分为装配基准、测量基准及定位基准。
(1)装配基准装配时用以确定零件在部件或产品中的位置的基准,称为装配基准。
(2)测量基准用以检验已加工表面的尺寸及位置的基准,称为测量基准。
如图32-2中的零件,内孔轴线是检验外圆径向跳动的测量基准;表面A是检验长度L尺寸l和的测量基准。
(3)定位基准加工时工件定位所用的基准,称为定位基准。
作为定位基准的表面(或线、点),在第一道工序中只能选择未加工的毛坯表面,这种定位表面称粗基准.在以后的各个工序中就可采用已加工表面作为定位基准,这种定位表面称精基准。
机械加工余量及影响因

尺寸链
1)首先根据工艺过程,找出间接保证的尺寸,定作封闭环, 一个尺寸链只有一个封闭环。 2)从封闭环开始,按照零件表面的联系,依次画出直接获 得的尺寸作为组成环,直至尺寸的终端回到封闭环的起点, 形成一个封闭图形。
2、尺寸链的分类
(1)直线尺寸链,直线尺寸链由彼此平行的直线尺寸所组成。 (2)平面尺寸链,平面尺寸链由位于一个平面内但相互间不都平 行的尺寸组成。 (3)空间尺寸链,空间尺寸链由位于几个不平行平面内的尺寸组 成。
50 0.06 及26 0.2
基本尺寸 H 0 200.02 25
ES -0.02
50 0.06
EI -0.06
-20
5
0.02 0.06
+0.02
0
0
-0.06
50 0.06
25
24.98
0 0.04
4、极值法解尺寸链的计算公式
(1)封闭环基本尺寸
A 式中,m—组成环数;k—增环数;
p 1 q k 1
A0 Ap
k
m
q
(2)封闭环极限尺寸
A0 max Ap max
p 1 k
k
q k 1 m
A
m
q min
A0 min Ap min
p 1
公称余量、最大余量、最小余量
由于工序尺寸有偏差,故各工序实际切除的余量值是变化 的,因此工序余量有公称余量(简称余量)、最大余量Zmax、 最小余量Zmin之分。 对于图示被包容面加工情况,本工序加工的公称余量: Zb =la-lb 公称余量的变动范围: Tz=Zmax-Zmin=Tb+Ta 式中: Tb——本工序工序尺寸公差; Ta——上工序工序尺寸公差;
加工总余量名词解释
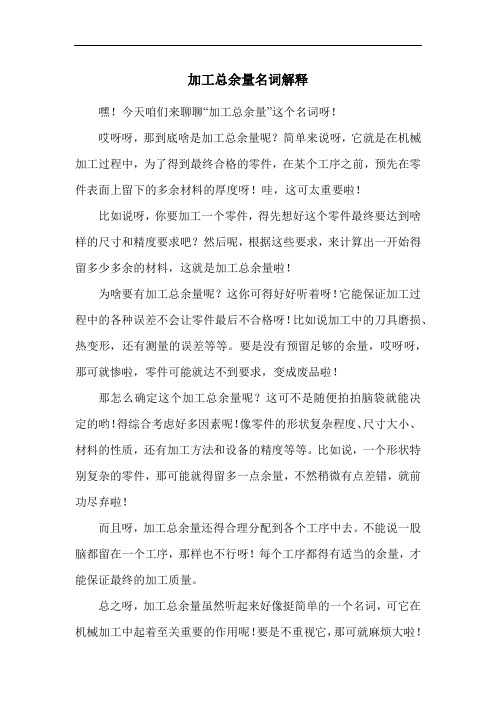
加工总余量名词解释
嘿!今天咱们来聊聊“加工总余量”这个名词呀!
哎呀呀,那到底啥是加工总余量呢?简单来说呀,它就是在机械加工过程中,为了得到最终合格的零件,在某个工序之前,预先在零件表面上留下的多余材料的厚度呀!哇,这可太重要啦!
比如说呀,你要加工一个零件,得先想好这个零件最终要达到啥样的尺寸和精度要求吧?然后呢,根据这些要求,来计算出一开始得留多少多余的材料,这就是加工总余量啦!
为啥要有加工总余量呢?这你可得好好听着呀!它能保证加工过程中的各种误差不会让零件最后不合格呀!比如说加工中的刀具磨损、热变形,还有测量的误差等等。
要是没有预留足够的余量,哎呀呀,那可就惨啦,零件可能就达不到要求,变成废品啦!
那怎么确定这个加工总余量呢?这可不是随便拍拍脑袋就能决定的哟!得综合考虑好多因素呢!像零件的形状复杂程度、尺寸大小、材料的性质,还有加工方法和设备的精度等等。
比如说,一个形状特别复杂的零件,那可能就得留多一点余量,不然稍微有点差错,就前功尽弃啦!
而且呀,加工总余量还得合理分配到各个工序中去。
不能说一股脑都留在一个工序,那样也不行呀!每个工序都得有适当的余量,才能保证最终的加工质量。
总之呀,加工总余量虽然听起来好像挺简单的一个名词,可它在机械加工中起着至关重要的作用呢!要是不重视它,那可就麻烦大啦!
怎么样,这下你对加工总余量是不是有更清楚的认识啦?。
- 1、下载文档前请自行甄别文档内容的完整性,平台不提供额外的编辑、内容补充、找答案等附加服务。
- 2、"仅部分预览"的文档,不可在线预览部分如存在完整性等问题,可反馈申请退款(可完整预览的文档不适用该条件!)。
- 3、如文档侵犯您的权益,请联系客服反馈,我们会尽快为您处理(人工客服工作时间:9:00-18:30)。
(1)、加工尾座体的底平面,粗糙度要求为Ra=1.6,采用粗铣—精铣—刮研。
粗铣余量2.7mm,精铣余量0.9mm,刮研余量0.15mm。
(2)、加工尾座体的两侧孔端面,粗糙度要求为Ra=3.2,采用粗铣—半精铣。
采用两次铣加工(粗、精铣)可以满足,粗铣余量取2mm,精铣余量取1mm。
(3)、加工尾座体的前侧面阶梯孔端面,粗糙度要求为Ra=6.3,采用粗铣—半精铣。
加工方法同上。
粗铣深度取1.5mm。
(4)、加工右侧小凸台,粗糙度要求为Ra=3.2,采用粗铣—半精铣。
粗铣余量取1mm,精铣余量取0.7mm。
(5)、加工Φ40H6孔,粗糙度要求Ra=0.4,采用粗镗—半精镗—精镗—浮动镗刀块精镗。
采用粗镗和半精镗、精镗和浮动镗刀块精镗的方式,故考虑分四次进行镗加工。
取粗镗双边余量3mm,半精镗双边余量1.5mm,精镗单边余量0.5mm,浮动镗刀块精镗的双边余量0.2。
(6)、加工肩Φ20H7的孔,粗糙度要求Ra=1.6,采用钻—扩—铰。
钻的单边余量为9mm,扩的单边余量为0.9mm,铰的单边余量为0.1mm。
(7)、加工Φ20H9的凸台孔,粗糙度要求Ra=3.2,采用钻—扩—铰。
钻的单边余量为9mm,扩的单边余量为0.9mm,铰的单边余量为0.1mm。
(8)、加工前侧面Φ10H9孔,粗糙度要求Ra=3.2,采用钻—铰。
采用钻—铰的加工方式,钻的单边余量为4.9mm,再铰加工即可满足要求。
(9)、加工两个阶梯孔,孔内壁粗糙度要求均为Ra=12.5,,采用钻Φ14大孔—钻Φ10小孔,锪出阶梯的加工方式。
(10)、加工Φ6H7后侧面孔和Φ6H7下表面底孔,粗糙度要求Ra=1.6,采用钻—铰。
一次钻不能满足要求,故采用钻—铰的加工方式,钻至直径Φ5.8,再铰加工。
(11)、加工M8和M5螺纹孔,由【7】213页
M8螺纹孔:首先选用Φ7的麻花钻头进行钻加工,再用丝锥攻M8螺纹。
M5螺纹孔:首先选用Φ4.2的麻花钻头进行钻加工,再用丝锥攻M5螺纹。
加工余量一览表:
最终毛坯余量:
根据【3】公式2-1
最终毛坯余量=机械加工余量+毛坯铸件公差/2
该毛坯是金属模铸造,材料是灰铸铁,故公差等级为8~10,取公差等级为9,尺寸公差为2.8mm。
可得新的表格如下
最终毛坯余量一览表:
3、设计工艺路线
根据工艺顺序的安排原则①先加工基准面,再加工其他表面②一般情况下,先加工平面,后加工孔③先加工主要表面,后加工次要表面④先安排粗加工工序,后安排精加工工序。