金刚石锯片介绍
金刚石工具分类及属性
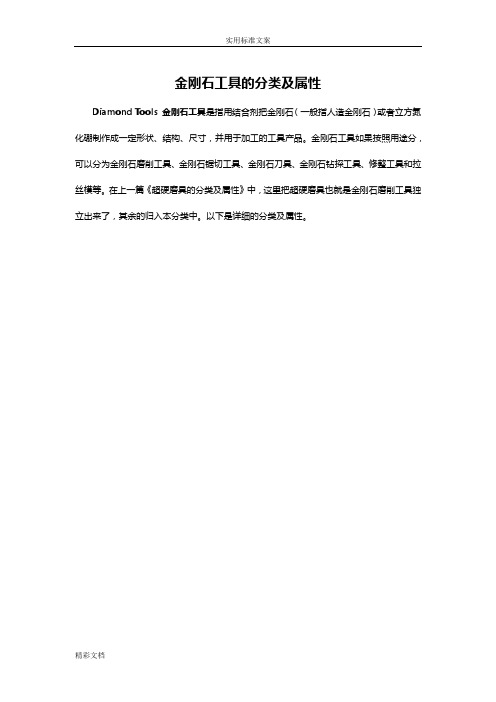
金刚石工具的分类及属性Diamond Tools 金刚石工具是指用结合剂把金刚石(一般指人造金刚石)或者立方氮化硼制作成一定形状、结构、尺寸,并用于加工的工具产品。
金刚石工具如果按照用途分,可以分为金刚石磨削工具、金刚石锯切工具、金刚石刀具、金刚石钻探工具、修整工具和拉丝模等。
在上一篇《超硬磨具的分类及属性》中,这里把超硬磨具也就是金刚石磨削工具独立出来了,其余的归入本分类中。
以下是详细的分类及属性。
如图1所示,金刚石工具目前在这里被分为9个二级分类和24个三级分类。
针对产品数量众多的产品,比如金刚石锯片和,金刚石绳锯、线锯和金刚石刀具等添加了属性,对于数量少的目前只给出了商标和型号两个属性,具体如下:一、Diamond Saw Blades 金刚石锯片金刚石锯片一般是指金刚石圆锯片(Circular Saw Blades ),但金刚石带锯(Band SawBlades )和金刚石排锯(Gang Saw Blades )也应归属于金刚石锯片。
金刚石锯片是一种切割工具,广泛应用于石材,陶瓷等硬脆材料的加工。
金刚石锯片主要由两部分组成;基体与刀头。
基体是粘结刀头的主要支撑部分,而刀头则是在使用过程中起切割的部分。
金刚石锯片可以按照工艺分,也可按照外观或者应用分类。
在本文,这些被作为属性来定义一款金刚石锯片。
Style 外观:Continuous Rim 连续式、Contour Blade 轮廓切割、Ring Saw 环锯片、Segmented 节块式、Turbo 涡轮形、Tuck Point 开槽片、Other;Weld Type 工艺:Sintered 烧结、Brazed 焊接、Laser Brazed 激光焊接、Electroplated 电镀、Other;Diameter 直径:收集了100mm-900mm的常见金刚石锯片直径供用户选择;Sawing Condition 应用环境:Dry 干切、Wet 湿切、Wet / Dry 干湿两用;Concentration 浓度:200%、150%、125%、100%、75%、50%、25%Materials Sawed 应用材料:Asphalt 沥青、Brick 砖块、Concrete 混凝土、Granite 花岗岩、Glass 玻璃、Marble 大理石、Porcelain 瓷器、Refractory 耐火材料、Stone 石头、Slate 石板、Tile 瓷砖、Universal 通用、Other应用材料属性可以让供应商选择多个,但我们不建议每次都全选,可以根据实际情况选择,如果适用于多种材料,建议直接选择Universal 通用。
金刚石锯片标准
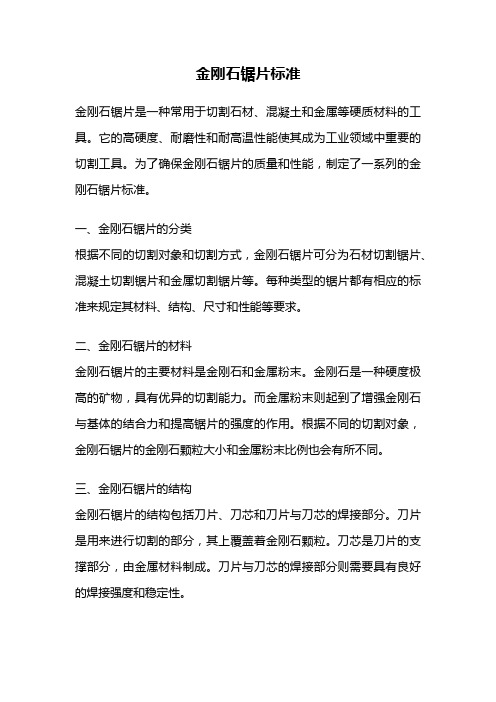
金刚石锯片标准金刚石锯片是一种常用于切割石材、混凝土和金属等硬质材料的工具。
它的高硬度、耐磨性和耐高温性能使其成为工业领域中重要的切割工具。
为了确保金刚石锯片的质量和性能,制定了一系列的金刚石锯片标准。
一、金刚石锯片的分类根据不同的切割对象和切割方式,金刚石锯片可分为石材切割锯片、混凝土切割锯片和金属切割锯片等。
每种类型的锯片都有相应的标准来规定其材料、结构、尺寸和性能等要求。
二、金刚石锯片的材料金刚石锯片的主要材料是金刚石和金属粉末。
金刚石是一种硬度极高的矿物,具有优异的切割能力。
而金属粉末则起到了增强金刚石与基体的结合力和提高锯片的强度的作用。
根据不同的切割对象,金刚石锯片的金刚石颗粒大小和金属粉末比例也会有所不同。
三、金刚石锯片的结构金刚石锯片的结构包括刀片、刀芯和刀片与刀芯的焊接部分。
刀片是用来进行切割的部分,其上覆盖着金刚石颗粒。
刀芯是刀片的支撑部分,由金属材料制成。
刀片与刀芯的焊接部分则需要具有良好的焊接强度和稳定性。
四、金刚石锯片的尺寸金刚石锯片的尺寸包括外径、内径、厚度和切割层厚度等。
外径决定了锯片的切割直径,内径则与切割机座的匹配有关。
厚度和切割层厚度则会影响到切割速度和切割质量。
五、金刚石锯片的性能要求金刚石锯片的性能要求包括切割能力、切割效率、寿命、安全性和环保性等。
切割能力是指锯片在切割硬质材料时的切削力和切割效果。
切割效率是指锯片在单位时间内切割的材料量。
寿命是指锯片在正常使用条件下的使用寿命。
安全性是指锯片在使用过程中是否会产生飞溅、断裂等安全隐患。
环保性则是指锯片在制作和使用过程中是否符合环保要求。
六、金刚石锯片的质量检验金刚石锯片的质量检验包括外观检查、尺寸检查、性能检测和寿命测试等。
外观检查主要是检查锯片的表面是否存在损伤、裂纹等缺陷。
尺寸检查则是通过测量锯片的外径、内径、厚度等尺寸来验证其是否符合标准要求。
性能检测包括切割能力、切割效率和安全性等方面的测试。
寿命测试则是通过模拟实际使用条件来评估锯片的使用寿命。
金刚石锯片用途及分类
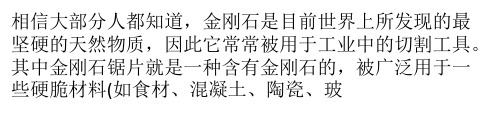
石锯片的应用领域其实与它的制作工艺、锯齿形态等息 息相关。根据生产方式的不同,金刚石锯片主要可以分 为烧结型、焊接型与电镀型三种,其中烧结型还可继续 细分为热压烧结和冷压烧结两种。而根据外观
的不同,金刚石锯片又可以分为连续边缘锯片、刀头型 锯片与涡轮型锯片。在对玻璃与陶瓷材料的加工中,我 们通常用采用烧结法制成的连续边缘锯片来对两者切边 或切断。在石材等建材的加工中,一般适用的
相信大部分人都知道,金刚石是目前世界上所发现的最 坚硬的天然物质,因此它常常被用于工业中的切割工具。 其中金刚石锯片就是一种含有金刚石的,被广泛用于一 些硬脆材料(如食材、混凝土、陶瓷、玻
璃、宝石等)的切割加工的切割工具。而现在,随着技术 的不断改进,它的应用领域还在不断地扩大蔓延,俨然 已经成为文明社会不可或缺的工具之一。首先小编将向 大家介绍的是金刚石锯片的分类,因为金刚
越来越多的限制。而用于宝石的加工流程的,由于要尽 量避免对这些珍贵材料的破坏,需要锯片有较薄的厚度 与较高的机械精度。其中烧结型的锯片由于厚度偏厚, 只能用于较为便宜的宝石的切割。对于贵重宝
石来说,则应选择电镀型锯片或者不属于金刚石锯片范 围内的线锯。而在锯片的外型方面,则要大多选择连续 边缘锯片。从需求市场来看,我国对金刚石锯片的需求 占了世界市场的最大部分,并且随着该项技术
的不断精进,金刚石锯片的应用范围将变得越来越广阔, 市场也将继续扩大。不过我国的生产技术与西方国家还 有一定的差距,这一行业的改革还有待加速。金刚石锯 片价格是多版权所有 禁止转载 谢谢!
出国看病 ty93htvv
为焊接型锯片。不过,根据加工工艺的不同,所需锯片 的外形也会有一定的差异。例如锯齿锯片一般用于切板。 在各个发展中国家中金刚石锯片在这两个行业的需求十 分旺盛,并预计将保持良好的发展势头。另
金刚石圆锯片原理

金刚石圆锯片原理及其在材料加工中的应用一、引言金刚石圆锯片,一种以金刚石为切割材料的圆锯片,因其出色的耐磨性、硬度及切割效率,广泛应用于石材、陶瓷、玻璃等硬脆材料的切割加工中。
本文将深入探讨金刚石圆锯片的工作原理及其在材料加工中的应用。
二、金刚石圆锯片的工作原理金刚石圆锯片的工作原理主要基于金刚石的高硬度和耐磨性。
在锯片旋转的过程中,金刚石颗粒与待切割材料表面产生摩擦,从而实现材料的切割。
金刚石颗粒的形状、大小和分布对锯片的切割效果有着决定性影响。
金刚石圆锯片的切割过程通常包括三个阶段:初始切入、稳定切割和退出切割。
在初始切入阶段,金刚石颗粒开始与材料表面接触,形成初始的切割痕迹。
在稳定切割阶段,金刚石颗粒与材料表面形成连续的摩擦,将材料逐渐切割开。
而在退出切割阶段,金刚石颗粒逐渐脱离材料表面,完成切割过程。
三、金刚石圆锯片在材料加工中的应用金刚石圆锯片因其独特的性能,在材料加工领域有着广泛的应用。
在石材加工中,金刚石圆锯片可以实现快速、精确的切割,提高生产效率。
在陶瓷和玻璃加工中,金刚石圆锯片同样展现出优异的切割性能,为这些材料的加工提供了便利。
此外,金刚石圆锯片还在一些特殊领域得到应用,如航空航天、汽车制造等。
在这些领域,材料通常具有较高的硬度和强度,传统的切割工具难以胜任。
而金刚石圆锯片凭借其高硬度和耐磨性,能够有效地解决这些问题。
四、结论金刚石圆锯片作为一种高性能的切割工具,其原理和应用已经得到了广泛的研究和应用。
随着科技的发展,金刚石圆锯片的性能和切割效率还将得到进一步的提升,为材料加工领域带来更多的可能性。
然而,金刚石圆锯片的应用也存在一些挑战,如成本较高、对操作技术要求较高等。
因此,未来的研究应关注如何降低金刚石圆锯片的成本、提高其使用寿命和切割精度,以推动其在更广泛领域的应用。
总的来说,金刚石圆锯片以其独特的工作原理和优异的性能,在材料加工领域发挥着重要作用。
随着科技的不断进步,金刚石圆锯片的应用前景将更加广阔。
金刚石薄型圆锯片相关知识
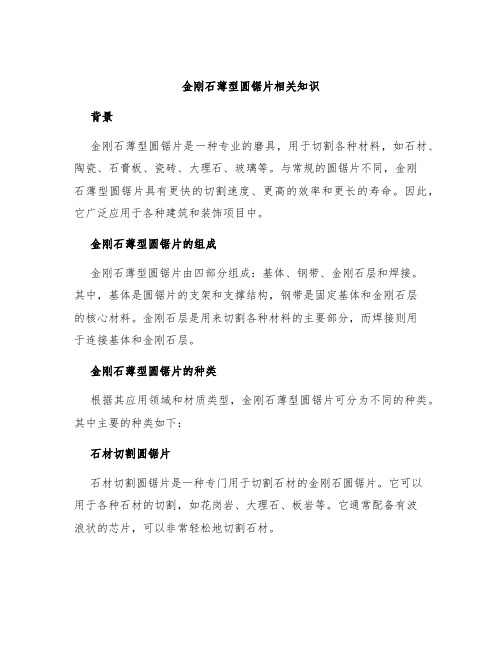
金刚石薄型圆锯片相关知识背景金刚石薄型圆锯片是一种专业的磨具,用于切割各种材料,如石材、陶瓷、石膏板、瓷砖、大理石、玻璃等。
与常规的圆锯片不同,金刚石薄型圆锯片具有更快的切割速度、更高的效率和更长的寿命。
因此,它广泛应用于各种建筑和装饰项目中。
金刚石薄型圆锯片的组成金刚石薄型圆锯片由四部分组成:基体、钢带、金刚石层和焊接。
其中,基体是圆锯片的支架和支撑结构,钢带是固定基体和金刚石层的核心材料。
金刚石层是用来切割各种材料的主要部分,而焊接则用于连接基体和金刚石层。
金刚石薄型圆锯片的种类根据其应用领域和材质类型,金刚石薄型圆锯片可分为不同的种类。
其中主要的种类如下:石材切割圆锯片石材切割圆锯片是一种专门用于切割石材的金刚石圆锯片。
它可以用于各种石材的切割,如花岗岩、大理石、板岩等。
它通常配备有波浪状的芯片,可以非常轻松地切割石材。
瓷砖切割圆锯片瓷砖切割圆锯片是一种专门用于切割瓷砖的金刚石圆锯片。
它具有可调节的进给速度和切割角度,可用于切割各种瓷质材料,如地砖、墙砖、水泥砖等。
龙骨切割圆锯片龙骨切割圆锯片是一种专门用于切割龙骨的金刚石圆锯片。
它可以用于切割轻钢龙骨、木龙骨、铝合金龙骨等。
它通常具有弯曲结构,可以轻松切割各种形状的龙骨。
金刚石薄型圆锯片的保养对于金刚石薄型圆锯片,正确的使用和保养是非常重要的,可以大大延长其使用寿命。
以下是一些有用的保养技巧:清洁圆锯片在使用过程中,圆锯片上会积累大量的灰尘和杂物,这些杂物会削弱其切割效果。
因此,在使用之前和之后,要用氯化铵和水将圆锯片清洗干净。
检查圆锯片在使用过程中,圆锯片上的牙齿会受损。
因此,在使用之前和之后,应检查圆锯片的牙齿是否有损坏。
如果牙齿受损,必须更换圆锯片。
保持圆锯片的湿润切割过程中,圆锯片会产生热量,这会使其磨损更快。
为了减少热量的影响,可以在圆锯片上喷上一些水。
这样可以使圆锯片保持湿润,也可以减少切割爆裂的风险。
总结金刚石薄型圆锯片是一种专业的切割工具,具有高效、高速和长寿命的优点。
TDC金刚石圆锯片使用说明书

DTC金刚石圆锯片使用说明书DTC金刚石圆锯片系采用优质金刚石基体材料,以新工艺精工制造,广泛用来切割大理石、花岗岩、水磨石、混凝土、沥青路面、道路用砖、耐火材料及石棉板等硬质非金属材料。
一、使用金刚石圆锯片切割石材时,切割机必须满足下列要求:1、切割机主轴径向跳动不超过0.03mm。
2、法兰盘外缘端跳动不超过0.03mm。
3、主轴与工作台导轨垂直度不超过0.2/300。
4、主轴箱与升降立柱平移悬臂位置调整完毕必须紧固。
5、主轴功率5.5KW为宜,锯片外缘线速度35-55M/S。
二、安装及使用方法:1、法兰盘直径≥180 mm。
2、锯片下缘超过工作台面10 mm为宜。
3、出厂未开刃的产品,切割石材前,先切割普通耐火砖开刃。
4、切割时应遵循“两缓-正常”的要求,即割切感开始和终了前移速度放缓。
中间应匀速行进,以保证安全和切割质量。
5、锯片切割时,冷却水要充足,流量10-15L/min。
三、用途:A级:用于切割硬度高、研磨性高的花岗岩和地板砖。
具有切割速度快、使用寿命长的特点。
B级:用于切割中硬度及研磨性适中的花岗岩、耐火材料等。
C级:推荐用于切割混凝土也可切割大理石、水磨石、轻质耐火材料等。
四、产品的标识:我公司生产的金刚石圆锯片可分为A、B、C三个品级。
分别在基体上打“A”、“B”、“C”钢印。
A级品印红色、B级品印黑色、C 级品印兰色油墨的我公司规格标志。
包装盒上印刷“A”、“B”、“C”为标识。
钢印下面的阿拉伯数字为焊接操作者工号。
请您在验钞灯下鉴别DTC公司防伪与合格证。
另外长方形防伪中有国际认证标志,谨防假冒。
五、售后服务:欢迎广大客户选用DTC金刚石圆锯片,如果使用后有确有质量问题刀头磨损不超过1 mm,无条件退换。
如遇其它质量问题时请及时与公司联系,我们将竭力为您服务。
北京兴东瀚科技有限公司。
PCD金刚石锯片

PCD金刚石锯片
Pcd金刚石锯片广泛用于木工切削、石材切削、金刚石木工锯片采用碳素工具钢锯片基体,使基体具有持久不变形精度恒久保持;优质的金刚石锯齿材料,使产品具有超强稳定性和耐用度.
金刚石是目前世界上最硬的刀具材料,比硬质合金材料硬50-150倍,金刚石PCD圆锯片具有硬度高,耐磨性能超强,并具有高韧性,高耐热等特性,其使用寿命是硬质合金锯片的50倍,一张金刚石PCD圆锯片胜过50张进口合金锯片,PCD耐酸性强,刀口不易钝化,更锋利,切割质量好,减少每天换刀磨刀时间,减少生产成本,提高加工质量及效率。
木业加工中,尤其刨花板,贴面板,高中密度板,中纤板,防火板,木地板等含杂质及高硬度材料,
PCD锯片锯切实木、刨花板、中密板应选左右齿,能锐利地将木纤维组织切断,切口平滑;为了保持槽底平整的开槽,则用平齿齿形或者用左右平组合齿;锯切贴面板、防火板一般选择梯平齿,计算机开料锯由于锯切切率大,用的合金锯片直径和厚度都比较大,直径在350-450mm左右,厚度在4.0-4.8mm之间,多数采用梯平齿,以减少崩边、锯痕。
平齿锯口较粗糙,切削速度较慢,修磨最为简单。
主要用于普通木材的锯切,成本较低,多用于直径较小的铝用锯片,以保持切削时减少粘连,或用于开槽锯片以保持槽底平整。
株洲三鑫针对的木工板料进行加工生产的金刚石锯片,在材料上使用硬质合金与金刚石相结合的,基体采用硬质合金刀头采用金刚石,大大提高了产品本身的耐磨度和使用的寿命,由于金刚石制造成本高、硬度高、耐磨性强、加工难度大、制造门槛高、价格昂贵,一直以来难以普及木工机械加工切削作业。
我公司针对“刨花板、密度板、硫酸钙板、水泥纤维板等一系列的木工板料进行切削作业,生产制造的金刚石木工锯片进行了多方面的研发和实验,表现出卓越的切削性能。
金刚石刀具标准

金刚石刀具标准引言金刚石是一种无色晶体,硬度排名世界第一。
由于其优异的硬度和耐磨性能,金刚石被广泛用作工业材料,特别是在切削和磨削工具领域。
本文将介绍金刚石刀具的标准,包括金刚石刀具的分类、性能要求、测试方法以及标准化组织。
一、金刚石刀具的分类根据金刚石刀具的用途和结构,金刚石刀具可以分为以下几类:1.金刚石砂轮:用于磨削和抛光材料的表面,例如金属、玻璃、陶瓷等。
2.金刚石锯片:用于切割各种材料,如石材、玻璃、陶瓷、金属等。
3.金刚石钻头:主要用于钻孔,可钻取混凝土、砖石、岩石等硬质材料。
4.金刚石刀片:用于切割各类材料,如金属、玻璃、陶瓷、塑料等。
二、金刚石刀具的性能要求由于金刚石具有高硬度、高耐磨性和高热导率等特点,金刚石刀具在使用过程中需要具备以下性能:1.高硬度:金刚石刀具应具有足够的硬度,以确保在切割和磨削过程中不易磨损。
2.高耐磨性:金刚石刀具应具有出色的耐磨性能,能够承受长时间的使用而不损坏。
3.高热导率:金刚石刀具应具备良好的热导率,以便及时散热,防止刀具过热。
4.良好的切削性能:金刚石刀具应具备良好的切削性能,以确保切削效果稳定。
三、金刚石刀具的测试方法为确保金刚石刀具的质量和性能符合标准要求,需要进行相应的测试。
以下是常用的金刚石刀具测试方法:1.硬度测试:通过Vickers硬度测试仪进行硬度测试,以确定金刚石的硬度。
2.耐磨性测试:使用标准化的磨损测试设备,在一定条件下进行耐磨性测试,评估金刚石刀具的耐磨性能。
3.热导率测试:采用热导率测试仪,测试金刚石刀具的热导率,以评估其散热性能。
4.切削性能测试:使用特定的材料进行切削实验,通过切削力、表面质量等指标评估金刚石刀具的切削性能。
四、金刚石刀具标准化组织金刚石刀具的制定和管理工作需要一个专门的标准化组织来制定和推广相关标准。
以下是一些国际上常用的金刚石刀具标准化组织:1.国际电工委员会(IEC):IEC负责制定和推广有关电气、电子和相关技术的国际标准,其中包括金刚石刀具的相关标准。
金刚石圆锯片使用说明书
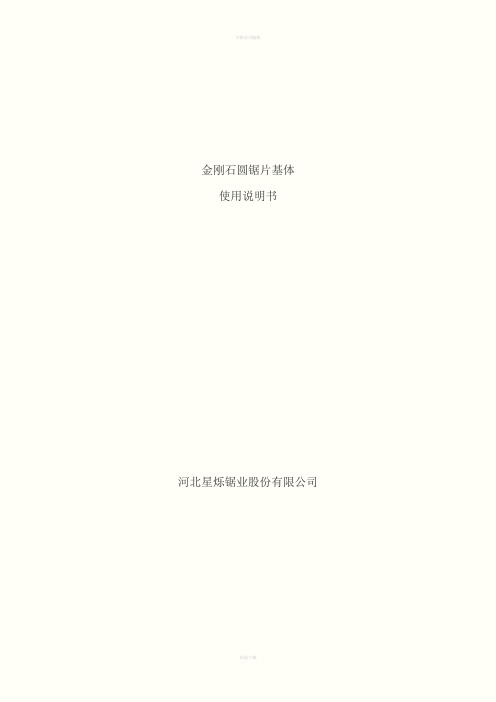
140
0.03
400
150
焊接后锯片经过检查如需修整,请聘请相关专业人员或与本公司售后服务人员联系进行处理,并注明基体的旋向。如未修整达不到锯片锯片使用要求造成任何质量问题,本公司将对其质量事故不负法律责任。
六、使用注意事项
(一)锯片安装
锯片安装精度与切割效率、切割质量及锯片的使用寿命关系密切。为确保锯片在切割过程中运行平稳,种情形,应改用结合式法兰盘。
4)法兰盘的直径达到锯片直径的1/4较为可靠,绝不可太小。<见表4>
5)主轴径跳、法兰盘端跳要符合表1的规定。
法兰盘直径、端跳值、主轴径跳值:表1
锯片直径
法兰盘直径
法兰盘端跳
主轴径跳
200
80
0.02
0.02
250
100
300
120
1)锯片主轴座安装孔及法兰盘表面要用400#金刚石砂布,擦拭干净,不得有毛刺及污物。
2)旋紧法兰盘螺栓,手动检查圆锯片的端跳和径跳。
其检查方法:将法兰盘固定在芯轴上,用百分表触头分别置于基体侧面距槽底部10mm处和锯片外径,缓慢旋转锯片分别测出端跳值和径跳值。锯片在锯机芯轴上的端面及径向跳动公差应符合相关标准要求。
为了让您充分了解星烁牌金刚石圆锯片基体系列产品的特点及最佳使用方法,请详细阅读本说明书。
一、用途及特点:
金刚石圆锯片基体外圆齿顶镶焊金刚石节块(刀头)后,即成为金刚石圆锯片,主要用于石材、水泥制品、玻璃、耐火砖等非金属硬脆材料的切割加工。可在单片切机上使用,也可在组合切机上使用。
星烁牌金刚石圆锯片基体是根据我国锯机、石材等具体情况,在参照国外同类产品特点的基础上设计制造的,具有制造精度高、刚度韧性好、不易变形、热稳定性高、使用寿命长、复焊次数多等特点,是金刚石圆锯片加工和石材厂家理想选择。
讲述金刚石圆锯片的锯切参数:金刚石工具

可是尽管我费尽口舌,金刚石工具据理力争,我仍然逃不开
刚石圆锯片的线速度较大时,应选取大的切削深
度。但当在锯机性能和强度许可范围内,应尽量
取较大的切削浓度进行切削,以提高切削效率。 当对加工表面有要求时,则应采用小深度切削。
金刚石圆锯片的锯切参数: (1)锯片线速度:
在实际工作中,金刚石圆锯片的线速度受到设备
条件、锯片质量和被锯切石才性质的限制。从最 佳锯片使用寿命与锯切效率来说,应根据不同石
材的性质选择锯片的线速度。锯切花岗石时,锯
片线速度可在 25m~35m/s 范围内选定。对于石
英含量高而难于锯切的花岗石,锯片线速度取下 限值为宜。在生产花岗石面砖时,使用的金刚石
的花岗石,可适当提高进刀速度,若进刀速度过 低,金刚石刃容易被磨平。但锯切粗粒结构而软
硬不均的花岗石时,应降低进刀速度,否则会引
起锯片振动导致金刚石碎裂而降低锯切率。锯切
花岗石的进刀速度一般在 9m~12m/min 范围内选 定。
2dp0f6c7a 金刚石工具金刚石锯片,金刚石工具,石材加工工具,金刚石滚筒
可是尽管我费尽口舌,金刚石工具据理力争,我仍然逃不开
圆锯片直径较小,线速度可以达到 35m/s.(2)
锯切深度:锯切深度是涉及金刚石磨耗、有效锯
切、锯片受力情况和被锯切石材性质的重要参数。 一般来讲,当金刚石圆锯片的线速度较高时,应
选取小的切消深度,从目前技术来说,锯切金刚
石的深度可在 1mm~1进给
速度。它的大小影响锯切率、锯片受力以及锯切
区的散热情况。它的取值应根据被锯切石材的性 质来选定。一般来讲,锯切较软的石材,如大理
金刚石切割片标准

金刚石切割片标准介绍金刚石切割片是广泛应用于工业领域的一种切削工具。
它采用金刚石粉末与金属粉末经过高温高压处理而成,具有高硬度、耐磨损、耐腐蚀等特点,适用于切割陶瓷、玻璃、石材、金属等硬质材料。
为了确保金刚石切割片的性能和质量,制定相关的标准非常重要。
本文将介绍金刚石切割片的标准要求,包括外观、尺寸、硬度、耐磨性、安全性等方面。
外观要求金刚石切割片应具有光滑、平整的表面,无裂纹、砂眼、气孔和夹杂物等缺陷。
切割片边缘应整齐锋利,没有毛刺或齿状。
尺寸要求金刚石切割片的尺寸应符合预定标准。
常见的切割片直径为100mm、115mm、125mm、150mm等,厚度为1.2mm、1.4mm、1.6mm、1.8mm等。
尺寸的偏差应控制在合理范围内,以确保切割效果和安全性。
硬度要求金刚石切割片的硬度是其重要的性能指标之一。
硬度直接影响切割片的切割效果和寿命。
根据不同的切割对象,需要选择不同硬度的切割片。
硬度的测定可采用洛氏硬度测试方法。
一般来说,硬度在80HRA95HRA之间的金刚石切80HRA之间的切割片适用于切割软质材料,如金割片适用于切割硬质材料,如陶瓷、石材等;而硬度在60HRA属。
耐磨性要求金刚石切割片的耐磨性是指切割片在使用过程中能否保持锋利、高效地切割硬质材料。
耐磨性的好坏直接影响切割片的使用寿命。
耐磨性可以通过切割性能测试来评价。
常用的测试方法包括切割速度、切割深度、切割时间等。
耐磨性要求应根据具体应用场景和材料选择。
安全性要求金刚石切割片在使用过程中需要注意安全。
为了保证使用的安全性,金刚石切割片应符合以下要求:1.安装牢固:切割片安装时应确保固定可靠,避免在高速旋转中脱离。
2.使用平稳:使用时应保持平稳,避免突然打角、切削过深等造成意外伤害。
3.使用防护措施:操作人员应穿戴好防护眼镜、手套等安全装备,防止切割片碎片飞溅伤人。
4.注意降温:长时间高速切割会引发切割片过热,应适时冷却以保证切割质量和切割片寿命。
金刚石锯片知识讲座
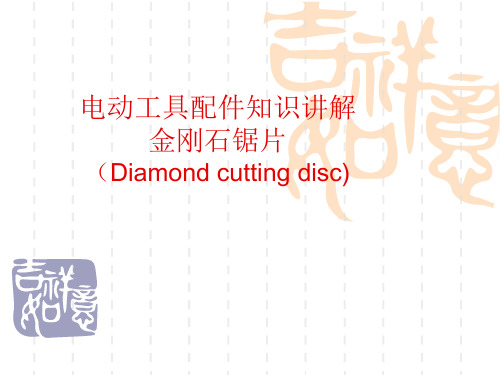
通用片和专业片
概念 所谓通用片就是比较笼统的什么材料的都可以切 的,我们分为3个档次。 专业片主要体现在一个针对性,是专门切割某种 材料的,比如水泥,大理石,瓷砖,花岗岩。 并不是说你的工艺越好金刚石的级别越高就是专 业,激光片也用通用片。当然冷压片由于工艺上 先天的缺陷就无所谓专业片了,所以专业片至少 是热压的,还有激光的。
外观分类
干片 切割时候不用加水 湿片 切割时候需加水散热 涡轮片(波片)锯齿连续呈现涡轮状均匀凸凹,提高了切 割速度,增加使用寿命。切割时候既可以加水也可以不加 加强涡轮片 机体上面多了几条条纹,有加强的作用,防 止基体因温度过高而软掉
干片
湿片
涡轮片
加强涡轮片
按刀头的制造工艺来分
烧结片 冷压 档 次 热压 低 到 高 片 由
电动工具配件知识讲解 金刚石锯片
(Diamond cutting disc)
结构
基体 一般是65Mn 刀头 是粉末冶金 铜基、铁基、镍基、钴基、 钨基和铝基粉末掺金刚石热压烧结成型
基本尺寸
Φ 115 x 7 x 22.23
外径 刀头高度 内径
外径:105、115、125、150、180、200、230、250、 300、350、400等 刀头高度:5、7、8、10等 内径:16、20、22.23、25.4、50 单位都是:mm
瓷砖:高频焊接, 瓷砖:高频焊接,热压烧结
大理石: 大理石:高频焊接
花岗岩:高频焊、激光 花岗岩:高频焊、
切割含有大量钢筋 的高强度混凝土
切割含有适量钢筋的 混凝土
切割较软, 切割较软,研磨性强的 新水泥、 新水泥、混凝土
影响金刚石锯片好坏的因素
主要有:基体的材料尺寸、刀头的配方尺寸还有 工艺 基体 厚度的大小一般是1.4~1.7mm 基体材料 烧结片要求低一点一般是65Mn,焊接 片要求就比较高,传统高频焊接主要用含碳量高 的合金钢做基体如SiMn6、8CrV、T10、T12等, 激光焊接则是用高强度的特种低合金钢,目前主 要采用35CrMo、 3CrMo、28CrMo等 刀片的基体
金刚石锯切工具分类

(一)生产设备
金刚石锯片冷压-烧结工艺流程示意图见图5-6。其所需设 备为:混料机、冷压机、烧结炉和开刃机等。
1.压机
压机的选择主要是根据产品的规格大小确定压机吨位。压 制所需的总压力按下式计算 P总=S0P设 式中 P总—压制工件时所需总压力,kN; S0—工件压制横截面积,cm2; P设—设计(或实际)冷压单位面积压力kN/cm2 所选择压 机的压力P压机应符合下式: P总≤70% P压机 (5—2) 根据计算结果,可以选择25t、40t、63t单臂压力机或者l00t、 200t、315t四柱压机。在满足压制压力要求的前提下,应尽量 选择小吨位压机,以避免“大马拉小车”。锯片的单位压制压 力一般为294~490MPa(3~5tf/cm2)。
(四)绳索锯 绳索锯简称绳锯,如图5-4所示,由很多个 金刚心锯节(也称串珠)串装在一根钢丝绳上而成。 绳锯主要用于石材矿山的开采.也有用于大石 块的破块。其方法是先在采掘面上打孔,将绳 锯穿入孔中,将两头接牢,套在由动力机带动的 轮子上,轮子带动绳锯运转,岩石一面一面地依 次切开
图5-4 金刚石绳锯示意图
图5-1 金刚石圆锯片示意图 a-结块式锯片,b-外圆锯片,c-内圆式锯片
金刚石连续齿切割片又称为金刚石湿切片. 因为金刚 石刀头是连续的, 排削冷却效果不好, 一般在加水或冷却 液的条件下切割.这种切割片一般较适合用于切割容易碎 边的大理石, 瓷砖, 玻璃, 石英等极脆材料. 当然也可用于 切割花岗岩混凝土等
(一)圆锯片 圆锯片(图5-1)是最常用的一种锯切工具,其直径跨
度大,从φ5mm到φ2800mm,厚度范围从0.1mm到15mm。其 用途广泛,制造方法多且难度大。圆锯片主要有三种: (1)节块式锯片(图5-1a)。包括由直接冷压、烧结制造的φ105— 450mm干切片,和经热压、焊接制造的φ350一2200mm的大理 石、花岗岩切割片,用途最为广泛。 (2)连续周边式锯片(图5-1b),一般由冷压、烧结法制造,包括用 于玉石切割的玉雕锯片、其他用途的干切片和湿切片。 (3)内圆切割片(图5-1C)。主要用于单晶硅等贵重材料的切割,为 了节约贵重材料,要求其厚度很薄(δ= 0.1~0.5mm),一般用电 镀法制造。
金刚石锯片的选择和工艺类型:陶瓷锯片

率高,但受 200℃-250℃温度时其硬度和耐磨性
急剧下降,热处理变形大,淬透性差,回火时间 长易开裂。除此之外,高速工具钢不仅具有良好
不知道是不是能够在现实中成为呢?这不是我
淬透性,而且硬度及刚性强,耐热变形少,是比
金刚石锯片的工艺类型主要有如Байду номын сангаас三种,一
是焊接金刚锯片、烧结金刚石锯片以及电镀金刚 石锯片。广泛应用于于陶瓷、石材等行业中,那
下面就给大家介绍下,我们在选择金刚石锯片时,
其锯片应如何选择。选择正确的金刚石锯片可以 根据锯切材料的种类、厚度、锯切的速度、锯切
不知道是不是能够在现实中成为呢?这不是我
的方向、送料速度、锯路宽度需要正确选用锯片。
较力量的锯片材料。合金工具钢与碳素工具钢相 比,耐热性,耐磨性好,处理性能较好,耐热变
形温度在 300℃-400℃适宜制造高档合金圆锯片。
因此,我们在选择锯片时,要根据实际的要求, 选择好的锯片。
2dn0f2c9a 陶瓷锯片陶瓷锯片,大理石锯片,马赛克锯片,金刚石锯片,金刚石工具,石材加工工具
角磨机切割片用途分类

角磨机切割片用途分类角磨机是一种常用的切割工具,用途广泛。
根据不同的切割片形状和材质,角磨机的切割片可以分为多种类型,包括砂轮切割片、金刚石切割片、切金刚石切割片、瓷砖切割片、多功能切割片等。
1. 砂轮切割片砂轮切割片是角磨机常用的切割工具之一。
它通常由砂轮粒子和粘结剂组成。
砂轮切割片适用于金属、石材、钢筋等硬质材料的切割,具有高速度、高效率的特点。
在金属加工、建筑施工、机械制造等行业中得到广泛应用。
2. 金刚石切割片金刚石切割片是由金刚石颗粒和金属粉末经高温高压压制而成的切割工具。
金刚石切割片具有极高的硬度和耐磨性,适用于切割各种硬质材料,如混凝土、砖石、花岗岩等。
金刚石切割片被广泛应用于建筑、装饰、石材加工等领域。
3. 切金刚石切割片切金刚石切割片是一种尖端切割工具,它采用专利技术制造,可用于金刚石、人造石、陶瓷等材料的切割。
切金刚石切割片具有高效、高精度、低噪音等特点,适用于室内装饰、石材加工等领域。
4. 瓷砖切割片瓷砖切割片是一种专门用于切割瓷砖的工具。
它通常由纤维材料和金属粒子组成,具有耐磨、耐高温的特点。
瓷砖切割片适用于家庭装饰、建筑施工等领域,能够实现精确、平整的瓷砖切割。
5. 多功能切割片多功能切割片是一种具有多种切割功能的工具,常用于装修、家仪维修等领域。
它可以切割金属、塑料、木材等材料,还可用于开槽、磨削等操作。
多功能切割片具有灵活性和通用性,可适应不同的切割需求。
综上所述,角磨机切割片的用途主要包括金属加工、建筑施工、石材加工、装饰装修等方面。
根据不同的切割片类型,角磨机可适用于各类硬质材料的切割,从而满足不同行业的需求。
金刚石锯片应用场景

金刚石锯片的应用场景主要涉及建筑施工、机械工程和家装
领域。
在建筑施工领域,金刚石锯片可以用于切割钢筋混凝土、水泥、砖墙等建筑材料,特别适用于局部修剪、改建、拆除等作业。
在机械工程中,金刚石锯片则可以配合各种工程机械,如电锯、石材机、钻头等,切割各种硬度的材料,如大理石、花岗岩、人造石、陶瓷等。
在家装领域,金刚石锯片主要用于切割石材、瓷砖、地板等装饰材料,使装修更加快捷、美观。
此外,金刚石锯片还可应用于以下场景:
1. 切割难加工有色金属材料:如铜、锌、铝等,以及其合金。
由于这些材料易粘附刀具,加工困难,金刚石锯片因其低摩擦系数、小亲和力和高导热率等特点,可以有效防止金属与刀具发生粘结,提高加工表面质量。
2. 切割木材:尤其适用于对硬质木材的切割,如橡木、松木等。
由于金刚石的极佳的耐磨性和高效的切削效果,使切割工作更为高效。
3. 金属切割:金刚石锯片能轻松切割钢铁、铝、铜等金属材料,切削效果好且精准。
金刚石锯片用途广泛,性能优越,是各种材料切割作业中的理想工具。
金刚石锯片的种类及用途介绍
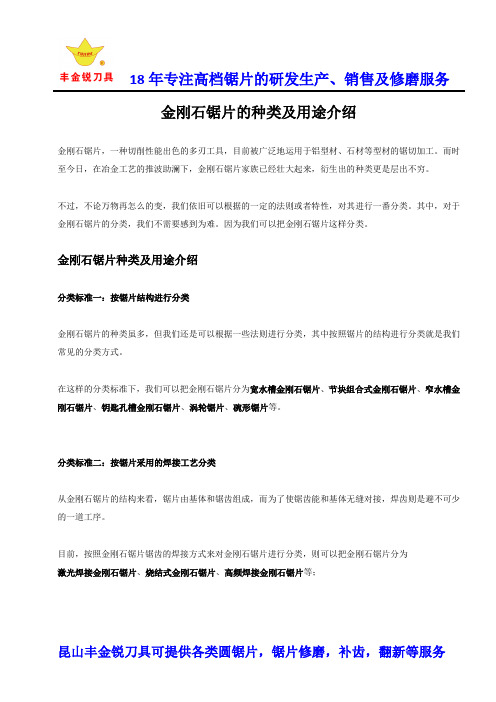
金刚石锯片的种类及用途介绍金刚石锯片,一种切削性能出色的多刃工具,目前被广泛地运用于铝型材、石材等型材的锯切加工。
而时至今日,在冶金工艺的推波助澜下,金刚石锯片家族已经壮大起来,衍生出的种类更是层出不穷。
不过,不论万物再怎么的变,我们依旧可以根据的一定的法则或者特性,对其进行一番分类。
其中,对于金刚石锯片的分类,我们不需要感到为难。
因为我们可以把金刚石锯片这样分类。
金刚石锯片种类及用途介绍分类标准一:按锯片结构进行分类金刚石锯片的种类虽多,但我们还是可以根据一些法则进行分类,其中按照锯片的结构进行分类就是我们常见的分类方式。
在这样的分类标准下,我们可以把金刚石锯片分为宽水槽金刚石锯片、节块组合式金刚石锯片、窄水槽金刚石锯片、钥匙孔槽金刚石锯片、涡轮锯片、碗形锯片等。
分类标准二:按锯片采用的焊接工艺分类从金刚石锯片的结构来看,锯片由基体和锯齿组成,而为了使锯齿能和基体无缝对接,焊齿则是避不可少的一道工序。
目前,按照金刚石锯片锯齿的焊接方式来对金刚石锯片进行分类,则可以把金刚石锯片分为激光焊接金刚石锯片、烧结式金刚石锯片、高频焊接金刚石锯片等;分类标准三:按锯片锯切对象分类金刚石锯片,归根到底是一种切削工具,终究会被运用到型材的锯切。
而根据锯切对象,我们亦可以对锯片进行一番分类。
目前,按照金刚石锯片锯切的对象进行分类,我们可以把金刚石锯片分为:大理石切割锯片、花岗石切割锯片、混凝土切割锯片等。
当然,上述分类方法不能把所有的金刚石锯片都包括进去,还有一些特殊用途的金刚锯片无法覆盖到,但对于常见的金刚石锯片已经覆盖到。
经过上述分类,我们已经对金刚石锯片有了一定的认识,而对于众多的金刚石锯片使用企业而言,要想用好金刚石锯片,充分发挥一片锯片的性能,则需要做到专锯专用。
目前,在金刚石锯片的应用领域,各型的金刚石锯片各行其职,在各个型材锯切的领域发挥着自己的功用。
而谈及其主要的用途。
其主要的用途在于:锯切硬脆材料。
金刚石锯片的制造工艺
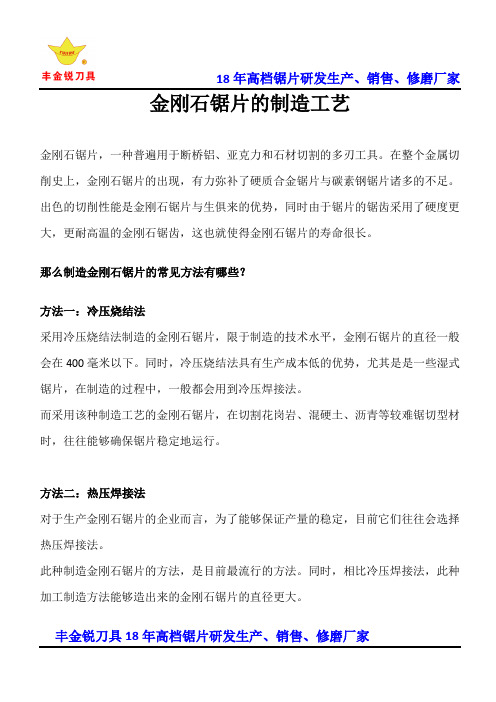
金刚石锯片的制造工艺金刚石锯片,一种普遍用于断桥铝、亚克力和石材切割的多刃工具。
在整个金属切削史上,金刚石锯片的出现,有力弥补了硬质合金锯片与碳素钢锯片诸多的不足。
出色的切削性能是金刚石锯片与生俱来的优势,同时由于锯片的锯齿采用了硬度更大,更耐高温的金刚石锯齿,这也就使得金刚石锯片的寿命很长。
那么制造金刚石锯片的常见方法有哪些?方法一:冷压烧结法采用冷压烧结法制造的金刚石锯片,限于制造的技术水平,金刚石锯片的直径一般会在400毫米以下。
同时,冷压烧结法具有生产成本低的优势,尤其是是一些湿式锯片,在制造的过程中,一般都会用到冷压焊接法。
而采用该种制造工艺的金刚石锯片,在切割花岗岩、混硬土、沥青等较难锯切型材时,往往能够确保锯片稳定地运行。
方法二:热压焊接法对于生产金刚石锯片的企业而言,为了能够保证产量的稳定,目前它们往往会选择热压焊接法。
此种制造金刚石锯片的方法,是目前最流行的方法。
同时,相比冷压焊接法,此种加工制造方法能够造出来的金刚石锯片的直径更大。
其直径的范围一般在350毫米至2200毫米之间,一些巨型的金刚石锯片,诸如锯切石料的金刚石锯片,在制造环节采用的就是此种工艺。
其基本的制造程序是混料、热压烧结、磨弧、焊接和开刃等。
方法三:滚压法采用滚压法制造的金刚石锯片,其制造成本相对较低,同时采用此种制造工艺制造出来的金刚石锯片一般用于锯切钟表、宝石、轴承等材料。
而采用此种方法制造的金刚石锯片,其锯身所采用的的材料一般为马口铁,其直径一般在80~120毫米之间,厚度在0.2~0.4毫米之间。
方法四:镶齿法顾名思义,镶齿法就是把金刚石锯齿镶嵌在锯片基体齿座上,采用此种制造工艺的方法制造出来的金刚石锯片较薄,锯齿在外圆呈不连续状,锯齿在轮缘中镶嵌牢固,切片锋利,切屑易于排出。
同时,切割效率高、材料损失小,又可以切割较薄的材料更是采用此种制造工艺锯片的优势所在,因为除了在石材领域,铝型材加工领域也会用到采用此种工艺制造的锯片。
- 1、下载文档前请自行甄别文档内容的完整性,平台不提供额外的编辑、内容补充、找答案等附加服务。
- 2、"仅部分预览"的文档,不可在线预览部分如存在完整性等问题,可反馈申请退款(可完整预览的文档不适用该条件!)。
- 3、如文档侵犯您的权益,请联系客服反馈,我们会尽快为您处理(人工客服工作时间:9:00-18:30)。
金刚石锯片介绍金刚石锯片是一种切割工具,广泛应用于石材,陶瓷等硬脆材料的加工.金刚石锯片主要由两部分组成;基体与刀头.基体是粘结刀头的主要支撑部分,而刀头则是在使用过程中起切割的部分,刀头会在使用中而不断地消耗掉,而基体则不会,刀头之所以能起切割的作用是因为其中含有金刚石,金刚石作为目前最硬的物质,它在刀头中摩擦切割被加工对象.而金刚石颗粒则由金属包裹在刀头内部。
制造工艺分类1、烧结金刚石锯片:分冷压烧结和热压烧结两种,压制烧结而成。
2、焊接金刚石锯片:分高频焊接和激光焊接两种,高频焊接通过高温熔化介质将刀头与基体焊接在一起,激光焊接通过高温激光束将刀头与基体接触边缘熔化形成冶金结合。
3、电镀金刚石锯片:是将刀头粉末通过电镀方法附着在基体上。
外观分类:1、连续边缘锯片:连续锯齿金刚石锯片,一般通过烧结方法制作,常用青铜结合剂作为基础胎体料,切割时须加水以保证切割效果,并有用激光将刀头切割缝隙的种类。
2、刀头型锯片:锯齿断开,切割速度快,适合干、湿两种切割方法。
3、涡轮型锯片:结合了前面1、2两项的优势,锯齿连续呈现涡轮状均匀凸凹,提高了切割速度,增加使用寿命。
锯片线速度:在实际工作中,金刚石圆锯片的线速度受到设备条件、锯片质量和被锯切石才性质的限制。
从最佳锯片使用寿命与锯切效率来说,应根据不同石材的性质选择锯片的线速度。
锯切花岗石时,锯片线速度可在25m~35m/s 范围内选定。
对于石英含量高而难于锯切的花岗石,锯片线速度取下限值为宜。
在生产花岗石面砖时,使用的金刚石圆锯片直径较小,线速度可以达到35m/s。
锯切深度锯切深度是涉及金刚石磨耗、有效锯切、锯片受力情况和被锯切石材性质的重要参数。
一般来讲,当金刚石圆锯片的线速度较高时,应选取小的切消深度,从目前技术来说,锯切金刚石的深度可在1mm~10mm之间选择。
通常用大直径锯片锯切花岗石荒料时,锯切深度可控制在1mm~2mm之间,与此同时应降低进刀速度。
当金刚石圆锯片的线速度较大时,应选取大的切削深度。
但当在锯机性能和刀具强度许可范围内,应尽量取较大的切削浓度进行切削,以提高切削效率。
当对加工表面有要求时,则应采用小深度切削。
进刀速度进刀速度即被锯切石材的进给速度。
它的大小影响锯切率、锯片受力以及锯切区的散热情况。
它的取值应根据被锯切石材的性质来选定。
一般来讲,锯切较软的石材,如大理石,可适当提高进刀速度,若进刀速度过低,更有利于提高锯切率。
锯切细粒结构的、比较均质的花岗石,可适当提高进刀速度,若进刀速度过低,金刚石刃容易被磨平。
但锯切粗粒结构而软硬不均的花岗石时,应降低进刀速度,否则会引起锯片振动导致金刚石碎裂而降低锯切率。
锯切花岗石的进刀速度一般在9m~12m/min范围内选定。
金刚石粒度常用的金刚石粒度在30/35~60/80范围内。
岩石愈坚硬,宜选取用较细的粒度。
因为在同等压力条件下,金刚石愈细愈锋利,有利于切入坚硬的岩石。
另外,一般大直径的锯片要求锯切效率高,宜选取用较粗的粒度,如30/40,40/50;小直径的锯片锯切的效率低,要求岩石锯切截面光滑,宜选用较细的粒度,如50/60,60/80。
刀头浓度所谓金刚石浓度,是指金刚石在工作层胎体中分布的密度(即单位面积内所含金刚石的重量)。
“规范”规定,每立方厘米工作胎体中含4.4克拉的金刚石时,其浓度为100%,含3.3克拉的金刚石时,其浓度为75%。
体积浓度表示结块中金刚石所占体积的多少,并规定,当金刚石的体积占总体积的1/4时的浓度为100%。
增大金刚石浓度可望延长锯片的寿命,因为增加浓度即减小了每粒金刚石所受的平均切削力。
但增加深度必然增加锯片的成本,因而存在一个最经济的浓度,且该浓度随铖切率增大而增大。
刀头结合剂的硬度一般来说,结合剂的硬度越高,其抗磨损能力越强。
因而,当锯切研磨性大的岩石时,结合剂硬度宜高;当锯切材质软的岩石时,结合剂硬度宜低;当锯切研磨性大且硬的岩石时,结合剂硬度宜适中。
力效应、温度效应及磨破损金刚石圆锯片在切割石材的过程中,会受到离心力、锯切力、锯切热等交变载荷的作用。
由于力效应和温度效应而引起金刚石圆锯片的磨破捐损。
力效应:在锯切过程中,锯片要受到轴向力和切向力的作用。
由于在圆周方向和径向存在力的作用,使得锯片在轴向呈波浪状,在径向呈碟状。
这两种变形都会造成岩石切面不平直、石材浪费多、锯切时噪音大、振动加剧,造成金刚石结块早期破损、锯片寿命降低。
温度效应:传统理论认为:温度对锯片过程的影响主要表现在两个方面:一是导致结块中的金刚石石墨化;二是造成金刚石与胎体的热奕力而导致金刚石颗粒过早脱落。
新研究表明:切割过程中产生的热量主要传入结块。
弧区温度不高,一般在40~120℃之间。
而磨粒磨削点温度却较高,一般在250~700℃之间。
而冷却液只降低弧区的平均温度,对磨粒温度却影响较小。
这样的温度不致使石墨炭化,却会使磨粒与工件之间摩擦性能发生变化,并使金刚石与添加剂之间发生热应力,而导致金刚石失效机理发生根本性弯化。
研究表明,温度效应是使锯片破损的最大影响因素。
磨破损:由于力效应和温度较应,锯片经过一段时间的使用往往会产生磨破损。
磨破损的形式主要有以下几种:磨料磨损、局部破碎、大面积破碎、脱落、结合剂沿锯切速度方向的机械擦伤。
磨料磨损:金刚石颗粒与式件不断摩擦,棱边钝化成平面,失去切削性能,增大摩擦。
锯切热会使金刚石颗粒表面出现石墨化薄层,硬度大大降低,加剧磨损:金刚石颗粒表面承受交变的热应力,同时还承受交变的切削应力,就会出现疲劳裂纹而局部破碎,显露出锐利的新棱边,是较为理想的磨损形态;大面积破碎:金刚石颗粒在切入切出时承受冲击载荷,比较突出的颗粒和晶粒过早消耗掉;脱落:交变的切削力使金刚石颗粒在结合剂中不断的被晃动而产生松动。
同时,锯切过程中的结合剂本身的磨损和锯切热使结合剂软化。
这就使结合剂的把持力下降,当颗粒上的切削力大于把持力时,金刚石颗粒就会脱落。
无论哪一种磨损都与金刚石颗粒所承受的载荷和温度密切相关。
而这两者都取决于铖切工艺和冷却润滑条件。
金刚石刀具的制造方法目前金刚石的主要加工方法有以下四种:薄膜涂层刀具、厚膜金刚石焊接刀具、金刚石烧结体刀具和单晶金刚石刀具。
2.1 薄膜涂层刀具薄膜涂层刀具是在刚性及高温特性好的集体材料上通过化学气相沉积法(CVD)沉积金刚石薄膜制成的刀具。
由于Si3N4系陶瓷、WC-Co系硬质合金以及金属W的热膨胀系与金刚石接近,制膜时产生的热应力小,因此可作为刀体的基体材料。
WC-Co系硬质合金中,粘结相Co的存在易使金刚石薄膜与基体之间形成石墨而降低附着强度,在沉积前需进行预处理以消除Co的影响(一般通过酸腐蚀去Co)。
化学气相沉积法是采用一定的方法把含有C源的气体激活,在极低的气体压强下,使碳原子在一定区域沉积下来,碳原子在凝聚、沉积过程中形成金刚石相。
目前用于沉积金刚石的CVD法主要包括:微波、热灯丝、直流电弧喷射法等。
金刚石薄膜的优点是可应用于各种几何形状复杂的刀具,如带有切屑的刀片、端铣刀、铰刀及钻头;可以用来切削许多非金属材料,切削时切削力小、变形小、工作平稳、磨损慢、工件不易变形,适用于工件材质好、公差小的精加工。
主要缺点是金刚石薄膜与基体的粘接力较差,金刚石薄膜刀具不具有重磨性。
2.2 金刚石厚膜焊接刀具金刚石厚膜焊接刀具的制作过程一般包括:大面积的金刚石膜的制备;将金刚石膜切成刀具需要的形状尺寸;金刚石厚膜与刀具基体材料的焊接;金刚石厚膜刀具切削刃的研磨与抛光。
(1)金刚石厚膜的制备与切割常用的制备金刚石厚膜的工艺方法是直流等离子体射流CVD法。
将金刚石沉积到WC-Co合金(表面进行镜面加工)上,在基体的冷却过程中,金刚石膜自动脱落。
此方法沉积速度快(最高可达930μm/h),晶格之间结合比较紧密,但是生长表面比较粗糙。
金刚石膜硬度高、耐磨、不导电决定了它的切割方法是激光切割(切割可在空气、氧气和氩气的环境中进行)。
采用激光切割不仅能将金刚石厚膜切割成所需要的形状和尺寸,还可以切出刀具的后角,具有切缝窄、高效等优点。
(1)金刚石厚膜刀具的焊接金刚石与一般的金属及其合金之间具有很高的界面能,致使金刚石不能被一般的低熔点合金所浸润,可焊性极差。
目前主要通过在铜银合金焊料中添加强碳化物形成元素或通过对金刚石表面进行金属化处理来提高金刚石与金属之间的可焊性。
①活性钎料法焊料一般用含Ti的铜银合金,不加助熔剂在惰性气体或真空中焊接。
常用的钎料成分Ag=68.8wt%,Cu=26.7wt%,Ti=4.5wt%,常用的制备方法是电弧熔炼法和粉末冶金法。
Ti作为活性元素在焊接过程中与C反映生成TiC,可提高金刚石与焊料的润湿性和粘结强度。
加热温度一般为850℃,保温10分钟,缓冷以减小内应力。
②表面金属化后焊接金刚石表面的金属化是通过表面处理技术在金刚石表面镀覆金属,使其表面具有金属或类金属的性能。
一般是在金刚石的表面镀Ti,Ti与C反应生成TiC,TiC与Ag-Cu合金钎料有较好的润湿性和结合强度。
目前常用的镀钛方法有:真空物理气相沉积(PVD,主要包括真空蒸发镀、真空溅射镀、真空离子镀等),化学气相镀和粉末覆盖烧结。
PVD法单次镀覆量低,镀覆过程中金刚石的温度低于500℃,镀层与金刚石之间是物理附着、无化学冶金。
CVD法Ti与金刚石发生化学反应形成强力冶金结合,反应温度高,损害金刚石。
(2)厚膜金刚石刀具的刃磨金刚石厚膜刀具的加工方法有:机械磨削,热金属盘研磨,离子束、激光束和等离子体刻蚀等。
2.3 金刚石烧结体刀具将金刚石厚膜用滚压研磨破坏的方法加工成平均粒度为32~37μm的金刚石晶粒或直接利用高温高压法制得金刚石晶粒,把晶粒粉末堆放到WC-16wt%Co合金上,然后用Ta箔将其隔离,在5.5GPa、1500℃条件下烧结60分钟,制成金刚石烧结体,用此烧结体制成的车刀具有很高的耐磨性。
2.4 单晶金刚石刀具单晶金刚石刀具通常是将金刚石单晶固定在小刀头上,小刀头用螺钉或压板固定在车刀刀杆上。
金刚石在小刀头上的固定方法主要有:机械加固法(将金刚石底面和加压面磨平,用压板加压固定在小刀头上);粉末冶金法(将金刚石放在合金粉末中,经加压在真空中烧结,使金刚石固定在小刀头上);粘结和钎焊法(使用无机粘结剂或其它粘结剂固定金刚石)。
由于金刚石与基体的热膨胀系数相差悬殊,金刚石易松动,脱落。
金刚石锯片总结目前在金刚石的产业化中还存在一些关键问题函待解决,如高速大面积的金刚石厚膜沉积工艺、控制金刚石膜的晶界密度和缺陷密度、金刚石膜的低温生长,金刚石薄膜与基体结合力弱等。
金刚石刀具优异的性能和广泛的发展前途吸引国内外无数的专家进行研究,有些已经取得了突破性进展,相信不久的将来金刚石刀具将广泛应用到现代加工中。