刹车片检测标准
刹车片检测标准
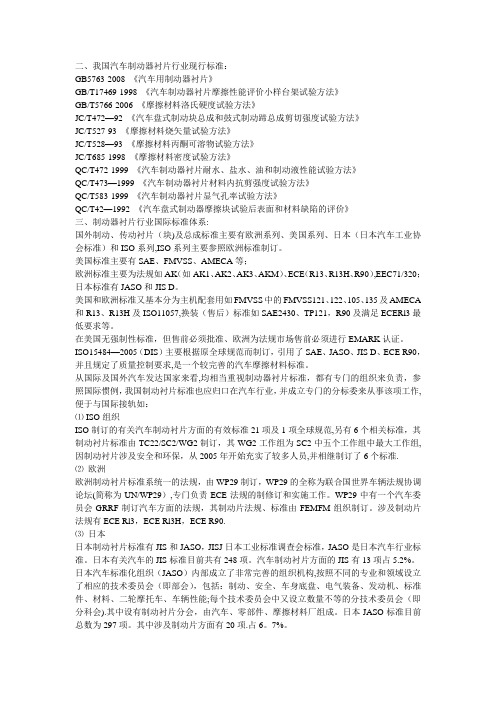
二、我国汽车制动器衬片行业现行标准:GB5763-2008 《汽车用制动器衬片》GB/T17469-1998 《汽车制动器衬片摩擦性能评价小样台架试验方法》GB/T5766-2006 《摩擦材料洛氏硬度试验方法》JC/T472—92 《汽车盘式制动块总成和鼓式制动蹄总成剪切强度试验方法》JC/T527-93 《摩擦材料烧矢量试验方法》JC/T528—93 《摩擦材料丙酮可溶物试验方法》JC/T685-1998 《摩擦材料密度试验方法》QC/T472-1999 《汽车制动器衬片耐水、盐水、油和制动液性能试验方法》QC/T473—1999 《汽车制动器衬片材料内抗剪强度试验方法》QC/T583-1999 《汽车制动器衬片显气孔率试验方法》QC/T42—1992 《汽车盘式制动器摩擦块试验后表面和材料缺陷的评价》三、制动器衬片行业国际标准体系:国外制动、传动衬片(块)及总成标准主要有欧洲系列、美国系列、日本(日本汽车工业协会标准)和ISO系列,ISO系列主要参照欧洲标准制订。
美国标准主要有SAE、FMVSS、AMECA等;欧洲标准主要为法规如AK(如AK1、AK2、AK3、AKM)、ECE(R13、R13H、R90),EEC71/320;日本标准有JASO和JIS D。
美国和欧洲标准又基本分为主机配套用如FMVSS中的FMVSS121、122、105、135及AMECA 和R13、R13H及ISO11057,换装(售后)标准如SAE2430、TP121,R90及满足ECERl3最低要求等。
在美国无强制性标准,但售前必须批准、欧洲为法规市场售前必须进行EMARK认证。
ISO15484—2005(DIS)主要根据原全球规范而制订,引用了SAE、JASO、JIS D、ECE R90,并且规定了质量控制要求,是一个较完善的汽车摩擦材料标准。
从国际及国外汽车发达国家来看,均相当重视制动器衬片标准,都有专门的组织来负责,参照国际惯例,我国制动衬片标准也应归口在汽车行业,并成立专门的分标委来从事该项工作,便于与国际接轨如:⑴ ISO组织ISO制订的有关汽车制动衬片方面的有效标准21项及1项全球规范,另有6个相关标准,其制动衬片标准由TC22/SC2/WG2制订,其WG2工作组为SC2中五个工作组中最大工作组,因制动衬片涉及安全和环保,从2005年开始充实了较多人员,并相继制订了6个标准.⑵欧洲欧洲制动衬片标准系统一的法规,由WP29制订,WP29的全称为联合国世界车辆法规协调论坛(简称为UN/WP29),专门负责ECE法规的制修订和实施工作。
刹车片更换标准

刹车片更换标准
汽车刹车片更换标准:
1.在深度检测刹车片后,如果比原始要求有所增厚就表明刹车片磨损,应立即更换;
2.当刹车片磨损到磨损深度达到1mm时,应立即更换刹车片;
3.如果发现刹车片上有凹点、高低不平、割裂、折断等缺陷,应立即
更换刹车片;
4.发现刹车片表面有轻微腐蚀、锈斑、流油等,应立即更换刹车片;
5.根据设备使用情况,当刹车片磨损深度达到1.5mm时,应立即更换
或更换有关的刹车件;
6.如果发现刹车片表面氧化,流油现象明显,应立即更换刹车片及有
关的刹车件;
7.如果发现刹车片表面有焊接痕迹,应立即更换刹车片及其有关的刹
车件;
8.发现刹车片表面有折断、划伤等缺陷,应立即更换刹车片及其有关
的刹车件。
汽车刹车片磨损检测与更换考核试卷

考生姓名:__________答题日期:__________得分:__________判卷人:__________
一、单项选择题(本题共20小题,每小题1分,共20分,在每小题给出的四个选项中,只有一项是符合题目要求的)
1.汽车刹车片的主要作用是什么?()
A.加速车辆的行驶速度
A.刹车盘磨损
B.刹车卡钳故障
C.轮胎气压不平衡
D.驾驶员操作习惯
14.更换刹车片时,以下哪个操作是错误的?()
A.使用专业工具
B.检查刹车油液位
C.不需要涂抹刹车脂
D.检查刹车片与刹车盘的接触面积
15.以下哪个原因会导致刹车片异响?()
A.刹车片磨损至极限
B.刹车片与刹车盘之间存在异物
C.刹车片过厚
B.防止刹车片粘附
C.降低刹车片磨损
D.提高刹车性能
17.以下哪些措施可以减少刹车片的磨损?()
A.使用ABS系统
B.定期进行车辆保养
C.避免拖拽车辆
D.避免在高速行驶中急刹车
18.以下哪些是刹车系统检查中需要注意的问题?()
A.刹车液的泄漏
B.刹车盘的厚度
C.刹车片的磨损均匀性
D.刹车系统的响应时间
14. ABD
15. ABC
16. ABC
17. ABCD
18. ABCD
19. ABC
20. ABCD
三、填空题
1.刹车片;刹车盘
2. 1-2
3.刹车脂
4.金属陶瓷
5.制动扭矩
6.液位;状态
7.目测检查;使用尺子测量;专业设备检测
8. 100-200
9.速度;刹车系统的性能
摩托车怎样辨别前碟刹车片磨损情况

摩托车怎样辨别前碟刹车片磨损情况摩托车前碟刹车片的磨损情况对于驾驶安全至关重要,及时更换磨损的刹车片可以保持刹车性能,提高刹车的效果。
以下是一些常见的方法来辨别摩托车前碟刹车片磨损情况:1.目视检查首先,停车后,可以目视检查前碟刹车片磨损情况。
通常情况下,新车上的前碟刹车片厚度大约在6-7mm左右。
通过对比刹车片颜色,观察刹车片是否有明显的磨损痕迹。
如果磨损轻微,刹车片表面可能还有较明显的沟槽纹路;如果磨损严重,刹车片表面会十分光滑,几乎看不到纹路,有时候甚至会出现刹车片的金属基底。
2.触摸检查使用手指可以轻轻触摸前碟刹车片表面,感受刹车片的厚度和平整度。
刹车片厚度如果低于指定的最小值,就需要更换刹车片了。
同时,用手触摸刹车片表面,如果刹车片表面非常光滑,摩擦力会减小,说明刹车片可能已经磨损严重,需要更换。
3.刹车手感当我们刹车时,通过感受手握刹车的感觉,也可以大致判断前碟刹车片的磨损情况。
磨损过多的前碟刹车片刹车力会变弱,可能需要较大的力气才能产生理想的刹车效果。
如果感觉刹车力度不够,同时听到有刺耳的金属摩擦声,那么很可能是前碟刹车片磨损造成的,需要及时更换。
4.检查刹车片标识每个刹车片上通常都会有一些标识和信息,例如制造商、型号、厚度等。
通过查看这些标识和信息,可以了解到刹车片的规格和磨损情况。
通常情况下,标识的厚度数值为新刹车片的厚度,与刹车片实际厚度进行对比,从而判断其磨损情况。
5.刹车距离当在行驶过程中,刹车距离变长了,说明摩托车的刹车片可能已经磨损严重,需要更换。
此时就需要注意及时更换磨损的刹车片,以保障行车安全。
在行车过程中,如果发现刹车片磨损情况不正常,应及时到专业的维修店进行检测和更换。
及时更换磨损的刹车片可以保持刹车的灵敏度和效果,确保摩托车的驾驶安全性。
同时,定期维护和保养摩托车的刹车系统,可以延长刹车片的使用寿命,提高整个刹车系统的性能。
自行车质量检测手册
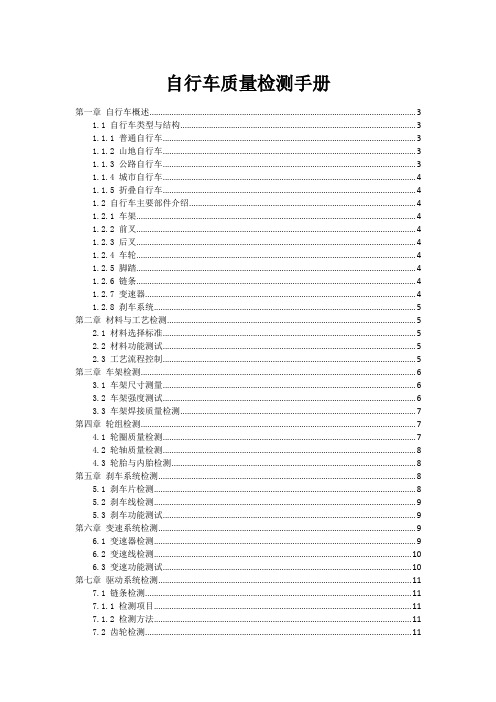
自行车质量检测手册第一章自行车概述 (3)1.1 自行车类型与结构 (3)1.1.1 普通自行车 (3)1.1.2 山地自行车 (3)1.1.3 公路自行车 (3)1.1.4 城市自行车 (4)1.1.5 折叠自行车 (4)1.2 自行车主要部件介绍 (4)1.2.1 车架 (4)1.2.2 前叉 (4)1.2.3 后叉 (4)1.2.4 车轮 (4)1.2.5 脚踏 (4)1.2.6 链条 (4)1.2.7 变速器 (4)1.2.8 刹车系统 (5)第二章材料与工艺检测 (5)2.1 材料选择标准 (5)2.2 材料功能测试 (5)2.3 工艺流程控制 (5)第三章车架检测 (6)3.1 车架尺寸测量 (6)3.2 车架强度测试 (6)3.3 车架焊接质量检测 (7)第四章轮组检测 (7)4.1 轮圈质量检测 (7)4.2 轮轴质量检测 (8)4.3 轮胎与内胎检测 (8)第五章刹车系统检测 (8)5.1 刹车片检测 (8)5.2 刹车线检测 (9)5.3 刹车功能测试 (9)第六章变速系统检测 (9)6.1 变速器检测 (9)6.2 变速线检测 (10)6.3 变速功能测试 (10)第七章驱动系统检测 (11)7.1 链条检测 (11)7.1.1 检测项目 (11)7.1.2 检测方法 (11)7.2 齿轮检测 (11)7.2.2 检测方法 (12)7.3 驱动系统功能测试 (12)7.3.1 测试项目 (12)7.3.2 测试方法 (12)第八章控制系统检测 (12)8.1 把手检测 (12)8.1.1 检测原理 (12)8.1.2 检测设备 (12)8.1.3 检测流程 (12)8.2 脚踏检测 (13)8.2.1 检测原理 (13)8.2.2 检测设备 (13)8.2.3 检测流程 (13)8.3 控制系统功能测试 (13)8.3.1 测试指标 (13)8.3.2 测试方法 (13)8.3.3 测试流程 (14)第九章附件检测 (14)9.1 车灯检测 (14)9.1.1 检测项目 (14)9.1.2 检测方法 (14)9.2 反光镜检测 (14)9.2.1 检测项目 (14)9.2.2 检测方法 (14)9.3 钥匙与锁具检测 (15)9.3.1 检测项目 (15)9.3.2 检测方法 (15)第十章安全功能检测 (15)10.1 整车稳定性测试 (15)10.2 耐久功能测试 (15)10.3 碰撞测试 (16)第十一章包装与运输检测 (16)11.1 包装材料检测 (16)11.1.1 材料成分检测 (17)11.1.2 物理功能检测 (17)11.1.3 化学功能检测 (17)11.1.4 微生物检测 (17)11.2 包装完整性检测 (17)11.2.1 封口检测 (17)11.2.2 结构完整性检测 (17)11.2.3 包装强度检测 (17)11.2.4 包装密封性检测 (17)11.3 运输过程监控 (17)11.3.2 运输湿度监控 (18)11.3.3 运输震动监控 (18)11.3.4 运输时间监控 (18)第十二章质量控制与改进 (18)12.1 质量管理体系 (18)12.1.1 质量管理体系的构成 (18)12.1.2 质量管理体系的实施 (18)12.2 质量改进措施 (19)12.2.1 流程优化 (19)12.2.2 员工培训 (19)12.2.3 质量工具的应用 (19)12.2.4 质量激励制度 (19)12.3 不合格品处理与售后服务 (19)12.3.1 不合格品处理 (19)12.3.2 售后服务 (20)第一章自行车概述1.1 自行车类型与结构自行车作为人类历史上最伟大的发明之一,已经成为了现代生活中不可或缺的交通工具。
简析刹车片中石棉的检测技术要点

学术论坛491简析刹车片中石棉的检测技术要点杨 攀,许 恒,张恒靖(浙江方圆检测集团股份有限公司,浙江 杭州 310018)摘要:刹车系统是汽车整体系统的重要部分,作为刹车系统重要零部件的石棉刹车片起到重要作用。
但是由于石棉刹车片在摩擦中生成的粉尘会对人体造成伤害,而且对环境有一定的污染,国际上很多国家已经明令禁止使用石棉刹车片。
于是,针对我国石棉刹车片的发展和使用现状,对刹车片中的石棉检测技术做出一定的分析。
关键词:刹车片;石棉;检测技术刹车在行车安全中起着至关重要的作用,为了行车安全,不仅需要司机熟练的驾驶技术和快速的反应能力,更需要有安全可靠的刹车设施,只有这样,才能保证车辆和人员的安全。
刹车片作为刹车系统中的主要零部件,对行车安全有着十分重要的作用。
我国人口众多,汽车数量也十分可观,所以,行车安全问题是十分值得关注和重视的问题[1]。
1 石棉刹车片 石棉在汽车、化工和建筑等制造部门被广泛使用,由于具备良好的耐火性、绝缘性和绝热性,一直是重要的防火、绝缘和保温材料。
石棉很早就被应用在织布行业,因其可以分裂成富有弹性的纤维丝,又被称为“石棉纤维”。
石棉刹车片是石棉的一种制动产品,是汽车刹车系统中重要的零部件之一。
国产刹车片主要有三种,石棉编制刹车带、橡胶石棉刹车带和石棉纤维橡胶刹车带,第一种多用于矿山机械和拖拉机上,又可分为树脂和油浸两小类。
第三种多被用在轻型机械的制动方面。
和其他化学化工原料一样,石棉也可能会产生一定的危害,比如石棉纤维引起的石棉肺、胸膜间皮瘤等疾病。
其次,石棉也会造成一定的污染。
温石棉是世界上使用最多的石棉,占世界石棉使用量的95%左右。
这种温石棉的污染过程主要是其纤维能分裂成极细的元纤维,经工业消耗释放到环境中造成污染。
元纤维的直径在微米左右,能够在大气和水中悬浮几周、几月,对地球造成持续的污染。
石棉本身并非有毒物质,它对人类造成危害的形式是粉末。
由于工业等操作会让大块的石棉物质产生极其微小的粉末,人们在工作过程中由于防护不到位而将这些粉末吸入肺里,这些粉末附着或沉积在肺部,从而对肺部造成损害,从而成为致癌物。
如何判断汽车刹车片磨损

如何判断汽车刹车片磨损1. 引言汽车刹车片是保证行车安全的重要组成部分,其磨损程度直接影响到刹车性能和行车安全。
因此,及时判断汽车刹车片的磨损情况十分重要。
本文将介绍几种常见的判断汽车刹车片磨损的方法,帮助车主及时发现并解决问题。
2. 视觉检查法视觉检查法是最简单也是最常用的一种方法。
通过观察刹车片的外观来初步判断其磨损情况。
正常情况下,新的刹车片表面应该是光滑平整的,颜色均匀。
而当刹车片磨损严重时,其表面会出现明显的凹槽和磨损痕迹,甚至可能出现裂纹。
此外,如果发现刹车片上有异物或者油污,也可能会影响刹车性能。
3. 声音检测法除了视觉检查法外,声音检测法也是一种常用的方法。
当刹车片磨损到一定程度时,会产生尖锐的刹车声音,这是由于刹车片与刹车盘之间的摩擦引起的。
如果在刹车时听到明显的尖锐声音,那么很可能是刹车片已经磨损严重,需要及时更换。
4. 刹车性能检测法除了外观和声音检测法外,刹车性能检测法也是一种较为准确的方法。
可以通过以下几种方式来测试刹车性能:刹车距离测试:在安全的道路上,以一定速度行驶并进行紧急制动,观察刹车距离是否正常。
如果刹车距离明显延长,那么很可能是刹车片磨损严重。
刹车力测试:在安全的环境下,进行刹车力测试,观察刹车力是否均匀。
如果发现某个轮胎的刹车力明显不足,那么可能是该轮胎的刹车片磨损严重。
制动感觉测试:在行驶过程中,观察刹车踏板的感觉是否正常。
如果发现踏板感觉异常或者有明显的抖动感,那么可能是刹车片磨损不均匀。
5. 专业检测法如果以上方法无法准确判断刹车片的磨损情况,建议寻求专业技师的帮助。
他们可以通过使用专业的检测设备来对刹车片进行全面的检测,包括测量刹车片的厚度、检查刹车片的磨损程度等。
这样可以更加准确地判断刹车片是否需要更换。
6. 结论及时判断汽车刹车片的磨损情况对行车安全至关重要。
本文介绍了几种常见的判断方法,包括视觉检查法、声音检测法、刹车性能检测法和专业检测法。
汽车安全性能检测规定

汽车安全性能检测规定随着汽车行业的快速发展,人们对汽车安全性能的要求也越来越高。
为了确保汽车的安全性能符合相关标准,各国都制定了一系列汽车安全性能检测规定。
本文将就汽车安全性能检测规定的相关信息进行介绍和解析。
一、制动系统检测规定制动系统是汽车最重要的安全系统之一,其可靠性关系到驾驶员和乘客的生命安全。
汽车制动系统检测规定主要包括制动盘磨损、刹车片磨损、制动液压系统漏油以及刹车灯亮度等项目。
制动系统检测规定的目的是确保制动性能达到标准,提高制动的安全性和可靠性。
二、安全气囊系统检测规定安全气囊是汽车被动安全系统的重要组成部分,它能在碰撞事故发生时提供保护。
安全气囊系统检测规定主要包括安全气囊系统工作状态、气囊装配位置和气囊充气速度等。
安全气囊系统检测规定的目的是确保安全气囊在事故发生时能够正常充气,提供有效的保护措施。
三、悬挂系统检测规定悬挂系统是汽车重要的操控部件,它直接关系到汽车的行驶稳定性。
悬挂系统检测规定主要包括悬挂系统的弹簧、减振器等部件的磨损情况,以及车身高度调节装置的正常工作情况。
悬挂系统检测规定的目的是确保悬挂系统的正常运行,提高汽车的操控性和行驶稳定性。
四、车身结构检测规定车身结构是汽车的保护外壳,其牢固性和稳定性直接影响着车辆的抗碰撞能力。
车身结构检测规定主要包括车身强度、车顶抗压能力、车门侧面碰撞能力等。
车身结构检测规定的目的是确保车身结构具备足够的抗碰撞能力,为驾驶员和乘客提供有效的保护。
五、驾驶辅助系统检测规定驾驶辅助系统是现代汽车中广泛应用的技术,它能够提高驾驶的便利性和安全性。
驾驶辅助系统检测规定主要包括电子稳定控制系统、自适应巡航控制系统以及驾驶员疲劳监测系统等。
驾驶辅助系统检测规定的目的是确保这些系统的正常工作,提供有效的驾驶辅助措施。
六、安全带系统检测规定安全带是保证乘员安全的重要设备,其正确使用能够在事故中减少伤亡。
安全带系统检测规定主要包括安全带的拉力测试、固定装置的耐久性测试以及警示装置的正常工作等。
鼓刹检测标准

鼓式刹车片检测标准包括以下方面:
摩擦系数:这是评价鼓式刹车片性能的重要指标之一。
摩擦系数越大,刹车片的制动力就越强。
一般来说,有机材料的摩擦系数在0.35-0.45之间,半金属材料的摩擦系数在0.4-0.5之间,陶瓷材料的摩擦系数在0.45-0.55之间。
在实际使用中,需要根据车辆的制动要求和路况选择合适的刹车片,以确保制动性能和安全性能的平衡。
磨损性能:鼓式刹车片的磨损性能主要取决于刹车片材料、车辆使用条件、行驶里程等。
一般来说,刹车片的磨损速度会随着使用时间的增加而逐渐加快。
因此,需要对刹车片进行定期检查和更换,以确保其正常工作。
制动效果:鼓式刹车片的制动效果受到多种因素的影响,如摩擦系数、磨损性能、制动器结构等。
一般来说,鼓式刹车片能够提供较好的制动效果,但需要注意其磨损性能和更换周期,以免影响制动效果。
安全性:鼓式刹车片的安全性是评价其质量的重要指标之一。
在制动过程中,鼓式刹车片需要保持良好的工作状态,以避免出现制动失灵、制动偏离等情况。
同时,需要注意更换鼓式刹车片时,需要使用合格的零件和专业的维修工具,以确保其安全性和可靠性。
总之,鼓式刹车片检测标准包括摩擦系数、磨损性能、制动效果和安全性等方面。
需要根据车辆的实际情况和使用要求选择合适的刹车片,并定期进行检查和更换,以确保其正常工作。
刹车片技术参数

刹车片技术参数
刹车片的技术参数主要有以下几个:
摩擦系数:这是刹车片最重要的技术指标,它表示刹车片与刹车盘之间的摩擦力大小。
摩擦系数的大小对刹车效果有着直接影响,如果摩擦系数过低,刹车效果不明显,可能导致安全事故;如果摩擦系数过高,则可能对刹车盘产生过大的磨损,缩短其使用寿命。
磨损率:刹车片的磨损率也是重要的技术参数之一。
优质的刹车片应具有较低的磨损率,这样才能保证较长的使用寿命。
热衰减性:刹车片在连续制动过程中,由于摩擦产生热量使得刹车片的温度升高,摩擦系数会随之下降。
优质的刹车片应具有良好的热衰减性,以保证在连续制动时仍能保持稳定的制动效果。
噪音:优质的刹车片在制动时应尽可能减少噪音的产生,以提高驾驶的舒适性。
抗热衰退性能:刹车片在高温下制动性能的稳定性。
好的刹车片应能在连续制动下保持稳定的摩擦系数,即抗热衰退性能好。
尺寸规格:刹车片的尺寸规格应符合车辆要求,以保证与刹车盘的匹配性,避免安装时出现问题。
总之,优质的刹车片需要具备良好的摩擦系数、磨损率、热衰减性、噪音、抗热衰退性能等技术参数,以保证良好的制动效果和安全性。
刹车片检测报告

刹车片检测报告1. 引言本文是对某辆车辆的刹车片进行检测的报告。
刹车片是车辆制动系统中的重要组成部分,对行车安全至关重要。
通过定期检测和维护刹车片的状况,可以确保车辆的制动性能良好,减少事故的发生。
本报告将详细描述刹车片的检测方法,评估刹车片的磨损状况,并提供相应的建议。
2. 检测方法刹车片的检测主要包括以下几个步骤:2.1 视觉检查首先进行刹车片的视觉检查。
观察刹车片的外观,检查是否有明显的磨损或裂纹。
同时注意观察刹车片的厚度和平整度,确保其符合制造商的要求。
2.2 刹车片厚度测量使用刹车片厚度测量仪或卡尺测量刹车片的厚度。
通常,刹车片的最小使用厚度由制造商规定,一旦刹车片磨损到该厚度以下,就需要更换新的刹车片。
2.3 刹车片磨损指示器的检查一些刹车片上安装有磨损指示器,可以通过检查指示器的位置来评估刹车片的磨损程度。
如果磨损指示器露出,表示刹车片已经磨损到需要更换的程度。
2.4 颜色变化检查观察刹车片的颜色是否有明显的变化。
刹车片有时会因为过热而变成蓝色或暗褐色,这可能意味着刹车片的使用温度过高,需要进行更详细的检查和评估。
3. 刹车片磨损评估根据刹车片的检测结果,可以对其磨损程度进行评估。
通常情况下,刹车片的磨损分为以下几个等级:•磨损程度正常:刹车片磨损适中,仍具备良好的制动性能。
•磨损程度较大:刹车片已经磨损到接近最小使用厚度,建议考虑更换新的刹车片。
•磨损严重:刹车片已经磨损超过最小使用厚度,需要立即更换新的刹车片以确保行车安全。
4. 建议根据刹车片的磨损评估结果,我们向车主提供以下建议:•如果刹车片的磨损程度正常,建议继续保持定期检查,并根据制造商的要求进行维护和更换。
•如果刹车片的磨损程度较大,建议尽快更换新的刹车片,以免进一步损坏制动系统。
•如果刹车片的磨损程度严重,需要立即更换新的刹车片,并对制动系统进行全面的检修和维护。
5. 结论刹车片的检测是确保车辆行车安全的重要环节。
通过定期检测和维护刹车片,可以避免因制动失效导致的事故发生。
汽车维修保养质量检查手册

汽车维修保养质量检查手册第一章检查准备 (3)1.1 检查工具准备 (3)1.1.1 测量工具 (3)1.1.2 检测仪器 (3)1.1.3 维修工具 (3)1.1.4 辅助设备 (3)1.2 检查流程说明 (3)1.2.1 检查前准备 (3)1.2.2 检查发动机 (4)1.2.3 检查制动系统 (4)1.2.4 检查轮胎 (4)1.2.5 检查车身 (4)1.2.6 检查电气系统 (4)1.2.7 检查安全设备 (4)第二章发动机系统检查 (4)2.1 发动机外观检查 (4)2.2 发动机内部结构检查 (5)2.3 发动机功能测试 (5)第三章变速器系统检查 (6)3.1 变速器外观检查 (6)3.2 变速器内部结构检查 (6)3.3 变速器功能测试 (7)第四章制动系统检查 (7)4.1 制动盘与制动鼓检查 (7)4.1.1 检查项目 (7)4.1.2 检查方法与要求 (8)4.2 制动片与刹车片检查 (8)4.2.1 检查项目 (8)4.2.2 检查方法与要求 (8)4.3 制动液检查 (8)4.3.1 检查项目 (8)4.3.2 检查方法与要求 (9)第五章悬挂系统检查 (9)5.1 悬挂系统外观检查 (9)5.2 悬挂系统功能测试 (9)5.3 悬挂系统部件检查 (10)第六章轮胎与轮毂检查 (10)6.1 轮胎外观检查 (10)6.2 轮胎磨损检查 (10)6.3 轮毂检查 (11)第七章电气系统检查 (11)7.1.1 检查项目 (11)7.1.2 检查方法 (12)7.2 灯光系统检查 (12)7.2.1 检查项目 (12)7.2.2 检查方法 (12)7.3 传感器与执行器检查 (12)7.3.1 检查项目 (12)7.3.2 检查方法 (12)第八章冷却系统检查 (13)8.1 冷却液检查 (13)8.1.1 检查冷却液液位 (13)8.1.2 检查冷却液颜色与杂质 (13)8.1.3 检查冷却液冰点 (13)8.2 散热器检查 (13)8.2.1 外观检查 (13)8.2.2 散热器内部检查 (13)8.2.3 散热器功能检查 (13)8.3 冷却系统部件检查 (13)8.3.1 水泵检查 (13)8.3.2 节温器检查 (13)8.3.3 水箱盖检查 (14)8.3.4 风扇及风扇皮带检查 (14)第九章排气系统检查 (14)9.1 排气管检查 (14)9.1.1 检查目的 (14)9.1.2 检查方法 (14)9.1.3 注意事项 (14)9.2 排气尾管检查 (14)9.2.1 检查目的 (14)9.2.2 检查方法 (14)9.2.3 注意事项 (15)9.3 排气系统泄漏检查 (15)9.3.1 检查目的 (15)9.3.2 检查方法 (15)9.3.3 注意事项 (15)第十章整车综合检查 (15)10.1 整车外观检查 (15)10.1.1 检查项目 (15)10.1.2 检查方法 (15)10.2 整车功能测试 (16)10.2.1 检查项目 (16)10.2.2 检查方法 (16)10.3 整车部件检查 (16)10.3.2 检查方法 (17)第一章检查准备1.1 检查工具准备在进行汽车维修保养质量检查之前,保证以下工具准备充分是的:1.1.1 测量工具游标卡尺千分尺直尺水平尺1.1.2 检测仪器气缸压力测试仪发动机故障诊断仪制动试验台轮胎平衡机1.1.3 维修工具常用手工工具(如扳手、螺丝刀等)专用工具(如火花塞专用工具、轮胎拆装工具等)拆装工具(如千斤顶、拖车绳等)1.1.4 辅助设备照明设备拉伸器防护用品(如手套、眼镜等)1.2 检查流程说明1.2.1 检查前准备保证车辆处于熄火状态,并将钥匙拔出。
制动器刹车片磨损标准

制动器刹车片磨损标准摘要:一、制动片磨损极限值概述二、不同品牌制动片磨损极限值差异三、制动片磨损极限值对刹车性能的影响四、如何正确维护和更换制动片五、总结:制动片磨损极限值的重要性正文:制动片磨损极限值是指制动片在正常使用过程中,厚度减少到一定程度时需要更换的标准。
制动片磨损极限值的大小影响着刹车性能和行车安全。
在本文中,我们将探讨制动片磨损极限值的概念、不同品牌制动片磨损极限值的差异、磨损极限值对刹车性能的影响以及如何正确维护和更换制动片。
一、制动片磨损极限值概述制动片磨损极限值通常由制造商规定,一般不能低于1.2mm。
这是因为当制动片厚度低于这个值时,刹车片的制动效果会明显减弱,容易导致刹车失灵,从而影响行车安全。
二、不同品牌制动片磨损极限值差异不同品牌对制动片磨损极限值的要求可能有所不同。
例如,2007款本田思域的制动片厚度标准为9.5-10.5mm(0.37-0.41英寸)。
这意味着在正常使用过程中,当制动片厚度降至9.5mm以下时,就需要考虑更换了。
三、制动片磨损极限值对刹车性能的影响制动片磨损极限值直接关系到刹车性能。
当制动片磨损到达极限值时,刹车片的制动效果会明显减弱,可能导致刹车失灵,增加交通事故的风险。
因此,车主在日常驾驶过程中应密切关注制动片的磨损情况,确保行车安全。
四、如何正确维护和更换制动片1.定期检查制动片厚度。
车主可以定期使用卡尺或专用检测仪器检查制动片的厚度,确保制动片厚度在正常范围内。
2.注意制动片的磨损状况。
观察制动片表面是否有裂纹、硬化等现象,如有异常,应及时更换。
3.选择优质制动片。
在更换制动片时,应选择原厂或知名品牌生产的制动片,确保制动性能和安全性。
4.定期保养。
按照汽车制造商的建议,定期对车辆进行保养,确保制动系统的正常运行。
五、总结:制动片磨损极限值的重要性制动片磨损极限值是衡量制动片磨损程度的一个重要指标,直接关系到行车安全。
车主应重视制动片的磨损情况,定期检查、更换磨损严重的制动片,确保刹车性能良好。
国际汽车零部件检测标准有哪些

国际汽车零部件检测标准有哪些一、安全相关检测标准。
1.1 碰撞安全标准。
在国际上,汽车零部件的碰撞安全那可是重中之重啊。
就像我们常说的“人命关天”,这方面的检测标准可严格了。
比如说汽车的安全带部件,得经过各种不同速度、不同角度的碰撞测试。
在高速碰撞模拟中,安全带必须能够紧紧地拉住车内人员,不能有丝毫的松动或者断裂。
还有汽车的安全气囊组件,从触发机制到展开速度和力度,都得符合严格的国际标准。
这就好比一场精确的舞蹈,每个动作都得恰到好处,多一点少一点都不行,不然在真正发生事故的时候,就可能危及生命。
1.2 制动部件安全标准。
汽车的刹车系统零部件检测标准也是相当严格的。
刹车盘、刹车片这些部件,得保证在各种路况下都能正常工作。
就像我们平时开车,要是刹车不灵,那可就像“热锅上的蚂蚁”,心里直发慌。
国际标准要求刹车部件有足够的摩擦力,而且要在长时间使用或者极端条件下,比如说高温、潮湿等,依然能够保持良好的制动性能。
二、环保相关检测标准。
2.1 尾气排放零部件标准。
现在环保可是全球的大趋势,汽车尾气排放相关的零部件检测标准是必不可少的。
像汽车的三元催化器,这可是处理尾气的关键部件。
国际标准规定它要能够有效地将有害气体转化为无害气体。
这个部件就像汽车尾气的“清洁工”,要是不达标,那汽车排出的尾气就会像“雾霾制造机”一样,对环境造成极大的污染。
而且不仅仅是三元催化器,整个尾气排放系统的各个零部件都要协同工作,达到规定的排放标准。
2.2 噪音控制零部件标准。
汽车行驶过程中的噪音也受到国际标准的约束。
汽车的消音器等噪音控制部件必须发挥作用。
你想啊,要是汽车开起来像“打雷”一样,那得多扰民啊。
所以这些部件得将汽车产生的噪音降低到一个合理的水平,既能保证车内人员有相对安静的驾驶和乘坐环境,又能减少对车外环境的噪音污染。
三、性能相关检测标准。
3.1 发动机性能零部件标准。
发动机是汽车的心脏,那发动机相关零部件的检测标准自然很严格。
汽车行业产品检验标准

汽车行业产品检验标准汽车行业是现代工业中重要的支柱产业之一,汽车产品的质量和安全对消费者和社会都具有重要意义。
为了确保汽车产品的质量和合规性,制定了一系列的汽车行业产品检验标准,旨在规范汽车生产和销售过程,保障消费者的权益和安全。
本文将从汽车零部件、车辆整车以及环境保护等方面,探讨汽车行业的产品检验标准。
一、汽车零部件的产品检验标准1.发动机部件检验标准发动机是汽车的核心零部件之一,其质量直接影响汽车的性能和可靠性。
发动机部件的产品检验标准主要包括材料的力学性能测试、动力性能测试、耐久性测试以及排放检测等。
例如,发动机的材料应符合相关的标准,如耐热性、抗氧化性等。
动力性能测试则要求发动机在不同工况下的加速性能、扭矩输出和燃油经济性等指标符合相应标准。
2.刹车系统部件检验标准刹车系统是汽车的重要安全装置,其性能直接关系到汽车的制动效果和行驶安全。
刹车系统部件的产品检验标准主要包括刹车片材料的摩擦系数测试、刹车管路的泄漏检测、刹车主缸的制动力检测等。
例如,刹车片的摩擦系数应满足制动性能要求,刹车管路应无泄漏现象,刹车主缸的制动力应符合相应标准。
3.安全气囊系统部件检验标准安全气囊是现代汽车的重要被动安全装置,其质量和可靠性对乘车人员的安全至关重要。
安全气囊系统部件的产品检验标准主要包括气囊的爆炸性能、喷气速度、喷气角度和有效保护区域等方面。
例如,气囊的爆炸性能需要符合对撞测试的要求,喷气速度和角度应满足保护乘车人员的需求,有效保护区域要覆盖车内的关键部位。
二、车辆整车的产品检验标准1.整车安全性能检验标准车辆整车的产品检验标准主要包括碰撞测试、侧翻测试、刹车性能测试、制动距离测试等,以评估车辆在各种紧急情况下的安全性能。
例如,碰撞测试可以通过撞击试验模拟车辆发生碰撞的情况,评估车辆的抗撞性和乘员的保护性能。
侧翻测试可以模拟车辆在转弯时可能发生侧翻的情况,以评估车辆的稳定性和乘员的安全性。
2.车辆环保性能检验标准随着社会对环境保护的要求越来越高,车辆的环保性能也成为汽车行业重点关注的问题之一。
刹车片高温剪切强度试验

刹车片高温剪切强度试验
刹车片高温剪切强度试验是一种用于评估刹车片在高温环境下剪切强度的测试方法。
这种测试方法通常用于检测刹车片在高温工作环境下的性能和耐久性,以确保其能够在极端条件下提供可靠的刹车性能。
测试过程通常包括以下步骤:
1. 样品准备:首先,需要准备用于测试的刹车片样品。
这些样品通常需要从刹车片的生产批次中随机抽取,并确保其具有代表性。
2. 高温环境建立:将样品放置在高温环境中,通常是在一个能够控制温度的实验室环境中。
这个环境的温度通常会设置在刹车片的工作温度范围内。
3. 剪切强度测试:使用专门的测试设备,如剪切试验机,对样品进行高温剪切强度测试。
这个过程通常需要在高温环境下进行,以模拟刹车片在实际工作条件下的剪切强度。
4. 数据分析:对测试数据进行详细的分析,包括剪切强度、变形量、温度变化等,以评估刹车片的高温性能和耐久性。
通过这种测试,可以评估刹车片在高温环境下的性能,包括其剪切强度、耐热性和耐久性。
这对于确保刹车片在极端条件下的性能稳定性和可靠性至关重要。
同时,这种测试
方法也有助于改进刹车片的设计和制造工艺,以提高其性能和耐久性。
- 1、下载文档前请自行甄别文档内容的完整性,平台不提供额外的编辑、内容补充、找答案等附加服务。
- 2、"仅部分预览"的文档,不可在线预览部分如存在完整性等问题,可反馈申请退款(可完整预览的文档不适用该条件!)。
- 3、如文档侵犯您的权益,请联系客服反馈,我们会尽快为您处理(人工客服工作时间:9:00-18:30)。
二、我国汽车制动器衬片行业现行标准:GB5763-2008 《汽车用制动器衬片》GB/T17469-1998 《汽车制动器衬片摩擦性能评价小样台架试验方法》GB/T5766-2006 《摩擦材料洛氏硬度试验方法》JC/T472-92 《汽车盘式制动块总成和鼓式制动蹄总成剪切强度试验方法》JC/T527-93 《摩擦材料烧矢量试验方法》JC/T528-93 《摩擦材料丙酮可溶物试验方法》JC/T685-1998 《摩擦材料密度试验方法》QC/T472-1999 《汽车制动器衬片耐水、盐水、油和制动液性能试验方法》QC/T473-1999 《汽车制动器衬片材料内抗剪强度试验方法》QC/T583-1999 《汽车制动器衬片显气孔率试验方法》QC/T42-1992 《汽车盘式制动器摩擦块试验后表面和材料缺陷的评价》三、制动器衬片行业国际标准体系:国外制动、传动衬片(块)及总成标准主要有欧洲系列、美国系列、日本(日本汽车工业协会标准)和ISO系列,ISO系列主要参照欧洲标准制订。
美国标准主要有SAE、FMVSS、AMECA等;欧洲标准主要为法规如AK(如AK1、AK2、AK3、AKM)、ECE(R13、R13H、R90),EEC71/320;日本标准有JASO和JIS D。
美国和欧洲标准又基本分为主机配套用如FMVSS中的FMVSS121、122、105、135及AMECA 和R13、R13H及ISO11057,换装(售后)标准如SAE2430、TP121,R90及满足ECERl3最低要求等。
在美国无强制性标准,但售前必须批准、欧洲为法规市场售前必须进行EMARK认证。
ISO15484-2005(DIS)主要根据原全球规范而制订,引用了SAE、JASO、JIS D、ECE R90,并且规定了质量控制要求,是一个较完善的汽车摩擦材料标准。
从国际及国外汽车发达国家来看,均相当重视制动器衬片标准,都有专门的组织来负责,参照国际惯例,我国制动衬片标准也应归口在汽车行业,并成立专门的分标委来从事该项工作,便于与国际接轨如:⑴ ISO组织ISO制订的有关汽车制动衬片方面的有效标准21项及1项全球规范,另有6个相关标准,其制动衬片标准由TC22/SC2/WG2制订,其WG2工作组为SC2中五个工作组中最大工作组,因制动衬片涉及安全和环保,从2005年开始充实了较多人员,并相继制订了6个标准。
⑵欧洲欧洲制动衬片标准系统一的法规,由WP29制订,WP29的全称为联合国世界车辆法规协调论坛(简称为UN/WP29),专门负责ECE法规的制修订和实施工作。
WP29中有一个汽车委员会GRRF制订汽车方面的法规,其制动片法规、标准由FEMFM组织制订。
涉及制动片法规有ECE Rl3,ECE Rl3H,ECE R90。
⑶日本日本制动衬片标准有JIS和JASO,JISJ日本工业标准调查会标准,JASO是日本汽车行业标准。
日本有关汽车的JIS标准目前共有248项。
汽车制动衬片方面的JIS有13项占5.2%。
日本汽车标准化组织(JASO)内部成立了非常完善的组织机构,按照不同的专业和领域设立了相应的技术委员会(即部会),包括:制动、安全、车身底盘、电气装备、发动机、标准件、材料、二轮摩托车、车辆性能;每个技术委员会中又设立数量不等的分技术委员会(即分科会)。
其中设有制动衬片分会,由汽车、零部件、摩擦材料厂组成。
日本JASO标准目前总数为297项。
其中涉及制动片方面有20项。
占6.7%。
⑷美国美国制动衬片方面标准由美国汽车工程师协会(Society of Automotive Engineers,简称SAE)负责制订,SAE研究对象是轿车、载重车及工程车、飞机、发动机、材料及制造等。
SAE 所制订的标准具有权威性,广泛地为汽车行业及其他行业所采用,并有相当部分被采用为美国国家标准。
目前SAE已拥有97个国家的超过84,000成员,每年新增或修订600余个汽车方面及航天航空工程方面的标准类文件。
其中涉及制动衬片方面标准有17项。
四、国外主要汽车制动器衬片标准简介:A 国际标准(ISO)l、ISO 6310-2001 道路车辆-制动衬片-压缩应变试验方法2、ISO 6311-01 道路车辆-制动衬片-衬片材料内剪切强度试验方法3、ISO 6312-2001 道路车辆-制动衬片-盘式制动块和鼓式制动蹄总成剪切试验方法4、ISO 6313-1980 道路车辆-制动衬片-盘式制动块受热对尺寸和形状影响试验方法5、ISO 6314-1980 道路车辆-制动衬片-耐水,盐水,油及制动液性能试验方法6、ISO 6315-1980 道路车辆-制动衬片-铁偶合面腐蚀粘连试验方法7、ISO 7629-1987 道路车辆-制动衬片-盘式制动块试验后表面和材料缺陷的评价8、ISO 7634-2003 道路车辆-压缩空气制动系统-试验规程9、ISO 7635-2003 道路车辆-气体和气顶液制动系统-试验规程10、ISO/TR 7882-1986 道路车辆-制动衬片-挡热板装置热传导率测定11、ISO 7881-1987 道路车辆-制动衬片-摩擦材料特性评价-小样台架试验方法12、ISO/DIS 15484-2005 道路车辆-制动衬片-摩擦材料-产品鉴定和保证13、ISO11157-1999 道路车辆-制动器总成-惯性测功机试验方法14、ISO CD 22574-2005 道路车辆-制动衬片-摩擦材料-外观检查15、ISO NWI 2560-2005 道路车辆-制动衬片-摩擦材料-汽车制动系统惯性摩擦性能评估16、ISO NWI 12530-2005 道路车辆-制动衬片-摩擦材料-商务车性能测试程序标准17、ISO NWI 2559-2005 道路车辆-制动衬片-摩擦材料-商务车摩损性能测试程序标准18、ISO 6597-1991 液压制动系统-制动性能检测19、ISO/WD 25865 道路车辆-制动衬片-摩擦材料-乘用车性能测试程序20、ISO/WD 26866 道路车辆-制动衬片-摩擦材料-乘用车磨损性能测试程序2l、ISO 7629-1987 道路车辆-制动衬片-摩擦材料-盘式制动块试验后表面和材料缺陷的评价22、盘式制动块背板表面漆面耐腐蚀性标准有:⑴ ISO 2409-1992 色漆和清漆-划格试验⑵ ISO 2812-1-2007 色漆和清漆-耐液性能测定-第1部分:浸入非水液体中⑶ ISO 4628-2-2003 色漆和清漆-涂层裂解评价-缺陷量和大小及外观匀变密度的标示-第2部分:起泡等级评定⑷ ISO 4628-3-2003 色漆和清漆-涂层裂解评价-缺陷量和大小及外观匀变密度的标示-第3部分:生锈等级评定⑸ISO 4628-4-20034 色漆和清漆-涂层裂解评价-缺陷量和大小及外观匀变密度的标示-第4部分:裂纹等级评定⑹ ISO 9227-2006 在人造环境中腐蚀试验-盐雾试验B美国汽车工程师协会标准(SAE)l、SAE J 160-2001 摩擦材料在升温时尺寸稳定性2、SAE J 379-2004 制动衬片高氏硬度3、SAE J 380-2002 摩擦材料比重4、SAE J 661-1997 制动衬片质量试验方法5、SAE J 662-1990(1997)制动块倒角6、SAE J 840-1998 制动蹄和衬片粘接试验方法7、SAE J 866-2002 制动衬片摩擦系数标识体系8、SAE J 1073-1990(1995)弹簧加载离合器高速旋转试验方法9、SAE J 2115-2006 商用车辆惯性试验台气制动效能和磨损试验规范10、SAE J 2430-1999 轿车和轻型货车制动摩擦片台架效能特性试验11、SAE J 2521-2006 盘式和鼓式制动器噪音台架试验12、SAE J 2522-2003 全球制动效能台架试验13、SAE J 2598-2006 汽车盘式制动块振动频率和阻尼试验14、SAE J 2707-2005 制动摩擦材料惯性台架磨损试验方法15、SAE J 2724-2006 盘式制动摩擦材料底层分布测量16、SAE J 2515-2006 盘式制动摩擦材料磨损试验方法17、SAE J 1652-2000 小型车和轻型车盘式制动器用摩擦片测功机效能特性试验C日本工业标准(JIS)1、JIS D4311-1995 汽车用离合器面片2、JIS D4411-1993 汽车用制动器衬片和衬垫3、JIS D4413-2005 汽车零部件-制动衬片与盘式制动块-压缩应变试验方法4、JIS D4414-1-1998 汽车零部件-制动衬片与盘式制动块-第l部分:铁偶合面腐蚀拈连试验方法(吸湿法)5、JIS D 4414-2-1998 汽车零部件-制动衬片与盘式制动块-第2部分:铁偶合面腐蚀拈连试验方法(浸水法)6、JIS D 4415-1998 汽车零部件-制动衬片与盘式制动块-剪切强度试验方法7、JIS D 4416-1998 汽车零部件-盘式制动块-热膨胀试验方法8、JIS D 4417-1986(1992)汽车制动衬片与衬垫比重试验方法9、JIS D 4418-1996 汽车制动衬片与衬垫气孔率试验方法10、JIS D 4419-1986 汽车盘式制动块接触面锈蚀试验方法11、JIS D 4420-1986 汽车制动衬片与衬垫耐水,盐水,油及制动液的试验方法12、JIS D 4421-1996(2006)汽车制动衬片,衬垫与离合器面片硬度试验方法13、JIS D 4422-2007 汽车零部件-鼓式制动蹄总成和盘式制动块-剪切强度试验方法D日本汽车行业标准1、JASO C102-1989 汽车离合器从动盘总成2、JASO C402-1999 乘用车-行车制动器道路试验规程3、JASO C403-1979 行车制动器性能要求4、JASO C404-1999 货车和大客车-行车制动器道路试验规程5、JASO C405-1981 货车和大客车-行车制动器性能要求6、JASO C406-2000 乘用车-行车制动系统试验规程7、JASO C407-2000 货车和大客车-制动装置-测功机试验规程8、JASO C417-1998 乘用车-行车制动系统试验规程9、JASO C418-1991 制动摩擦衬片特性试验规程10、JASO C419-1989 乘用车行车制动系统测功机试验规程11、JASO C421-1974 货车和大客车乘用车行车制动系统测功机试验规程12、JASO C427-1983 制动摩擦材料-惯性测功机疲劳试验规程13、JASO C430-2002 气制动系统试验规程14、JASO C436-1999 驻车制动装置测功机试验规程15、JASO C441-1977 行车制动耐久性台架试验规程16、JASO C442-1977 驻车制动测功机实验规程17、JASO C443-1977 测功机-模拟山区衰退试验规程18、JASO C447-1979 驻车制动系统道路试验规程19、JASO C448-1980 乘用车-钳盘式制动器台架试验规程20、JASO C458-1986 制动摩擦衬片PH值测试法E欧洲法规(标准)l、ECE(欧洲经济委员会)法规:ECE R13,ECE R90,ECE R13-H2、EEC(欧共体)法规:EEC 71/3203、AK(欧洲标准):AK1,AK2,AK3,AK M。