钻孔灌注桩基础施工方法
桩基础施工方法
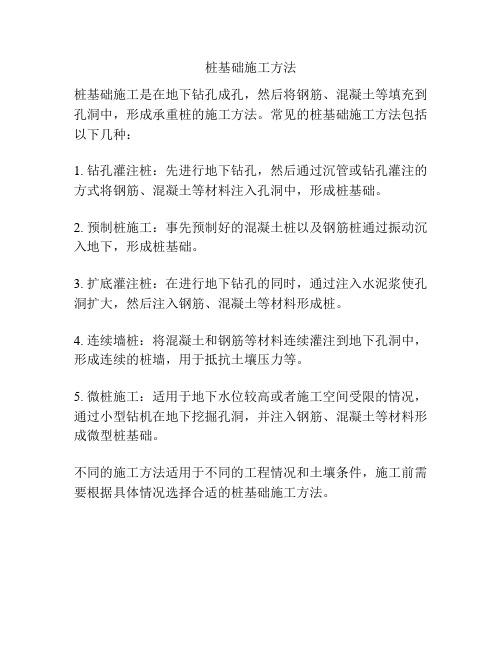
桩基础施工方法
桩基础施工是在地下钻孔成孔,然后将钢筋、混凝土等填充到孔洞中,形成承重桩的施工方法。
常见的桩基础施工方法包括以下几种:
1. 钻孔灌注桩:先进行地下钻孔,然后通过沉管或钻孔灌注的方式将钢筋、混凝土等材料注入孔洞中,形成桩基础。
2. 预制桩施工:事先预制好的混凝土桩以及钢筋桩通过振动沉入地下,形成桩基础。
3. 扩底灌注桩:在进行地下钻孔的同时,通过注入水泥浆使孔洞扩大,然后注入钢筋、混凝土等材料形成桩。
4. 连续墙桩:将混凝土和钢筋等材料连续灌注到地下孔洞中,形成连续的桩墙,用于抵抗土壤压力等。
5. 微桩施工:适用于地下水位较高或者施工空间受限的情况,通过小型钻机在地下挖掘孔洞,并注入钢筋、混凝土等材料形成微型桩基础。
不同的施工方法适用于不同的工程情况和土壤条件,施工前需要根据具体情况选择合适的桩基础施工方法。
钻孔灌注桩(冲击钻)施工方案
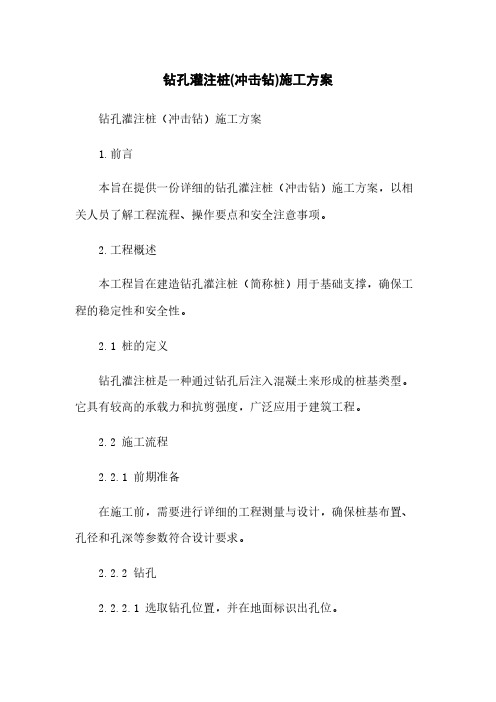
钻孔灌注桩(冲击钻)施工方案钻孔灌注桩(冲击钻)施工方案1.前言本旨在提供一份详细的钻孔灌注桩(冲击钻)施工方案,以相关人员了解工程流程、操作要点和安全注意事项。
2.工程概述本工程旨在建造钻孔灌注桩(简称桩)用于基础支撑,确保工程的稳定性和安全性。
2.1 桩的定义钻孔灌注桩是一种通过钻孔后注入混凝土来形成的桩基类型。
它具有较高的承载力和抗剪强度,广泛应用于建筑工程。
2.2 施工流程2.2.1 前期准备在施工前,需要进行详细的工程测量与设计,确保桩基布置、孔径和孔深等参数符合设计要求。
2.2.2 钻孔2.2.2.1 选取钻孔位置,并在地面标识出孔位。
2.2.2.2 按设计要求选择合适的冲击钻,装配好冲击钻头。
2.2.2.3 开始钻孔,根据地层情况合理调整钻孔进度和进钻方式。
2.2.2.4 钻孔到设计孔深后,停止钻孔,并进行孔内清洗。
2.2.3 灌注桩身2.2.3.1 搅拌混凝土,确保混凝土按照设计配合比制备。
2.2.3.2 使用管线输送混凝土至孔内,同时使用长杆搅拌,保证混凝土均匀分布。
2.2.3.3 在灌注过程中,需避免空隙和孔口冒浆现象的发生。
2.2.3.4 灌注至预定高度后,使用振捣器进行振实处理。
2.2.4 灌注桩顶2.2.4.1 在桩顶部分预埋钢筋,以提高桩顶强度。
2.2.4.2 按照设计要求,在桩顶部分进行振捣处理。
3.安全注意事项3.1 工地安全3.1.1 在施工现场周围设置明显的警示标志,确保施工区域安全。
3.1.2 施工人员应佩戴符合标准的个人防护装备,包括安全帽、防护鞋等。
3.2 设备安全3.2.1 冲击钻使用前,应检查设备完好性,确保各部件安装牢固。
3.2.2 冲击钻操作时,施工人员应站在安全区域,远离冲击区域。
4.附件本所涉及的附件如下:附件1:钻孔灌注桩工程设计图纸附件2:施工现场平面布置图附件3:施工设备清单附件4:施工材料列表5.法律名词及注释本所涉及的法律名词及注释如下:1. 土木工程施工安全管理条例:指对土木工程施工中的安全管理进行规定的法规。
钻孔灌注桩的四种施工方法

钻孔灌注桩的四种施工方法1. 钻孔灌注桩的施工方法1.1 钻孔灌注桩的概述钻孔灌注桩是一种常用的地基处理方法,可用于加固地基、改善土壤的承载力和稳定性。
本文将介绍钻孔灌注桩的四种常用施工方法。
1.2 钻孔灌注桩的基本原理钻孔灌注桩是通过钻孔的方式将混凝土注入到地下,形成一个连续的桩体。
这个桩体可以增加地基的承载力和稳定性,从而达到加固地基的目的。
2. 钻孔施工法2.1 钻孔施工前准备钻孔施工前,需进行必要的勘察和设计。
确定桩的数量、位置和尺寸,并准备好必要的设备和材料。
2.2 钻孔施工过程(1) 在预定的位置用钻机进行钻孔,直至达到设计要求的深度。
(2) 钻孔完成后,将钻孔巡查和清理,确保钻孔的质量和准确性。
(3) 在钻孔进口放置钢筋笼,保证钢筋的位置正确,并且有足够的长度穿出地面。
(4) 开始灌注混凝土,在灌注过程中,要注意控制灌注速度和灌注压力,确保桩体的质量和一致性。
(5) 灌注结束后,进行振捣和抹光,使混凝土达到预期的强度和外观。
3. 爆破施工法3.1 爆破施工前准备爆破施工法需要进行详细的勘察和设计。
确定桩的数量、位置和尺寸,并获得相关的爆破许可证。
3.2 爆破施工过程(1) 进行钻孔,直至达到设计要求的深度。
(2) 在钻孔中放置爆破药物,根据设计要求选择合适的爆破药物。
(3) 进行爆破操作,控制爆破的力度和方向,确保桩体的质量和稳定性。
(4) 爆破后进行挖掘和清理,使桩体达到预期的尺寸和形状。
4. 挤拔施工法4.1 挤拔施工前准备挤拔施工法需要进行详细的勘察和设计。
确定桩的数量、位置和尺寸,并准备好必要的设备和材料。
4.2 挤拔施工过程(1) 在预定的位置进行挖掘坑,确保坑底水平和垂直度。
(2) 在坑底放置钢筋笼,然后用特殊的挤拔设备将混凝土挤入坑中。
(3) 挤拔过程中,控制挤拔速度和挤压力,确保桩体的质量和一致性。
(4) 挤拔结束后,进行振捣和抹光,使混凝土达到预期的强度和外观。
附件:本文档无附件。
钻孔灌注桩施工方法
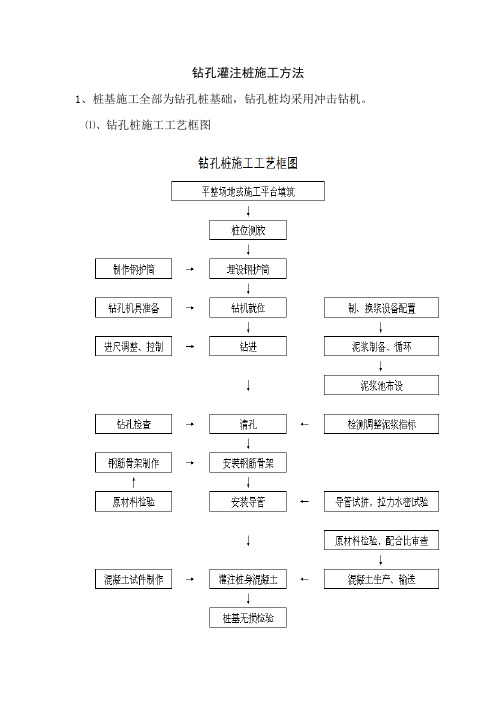
钻孔灌注桩施工方法1、桩基施工全部为钻孔桩基础,钻孔桩均采用冲击钻机。
⑴、钻孔桩施工工艺框图(2)桩基准备:在桩基施工前先定位放线和原地貌测量,清除桩基施工范围内淤泥并回填砂砾石,分层碾压密实方便桩基施工机械就位施工,桩基主要采用占河道较小的反循环冲击钻施工,现场挖3×3×2m泥浆池,先将泥浆沉淀,沉淀后渣装入全封闭的货箱,用汽车运出弃于就近弃土场,待桩基施工完毕后再清除河道内回填的砂砾石并碾压密实,浇筑垫层(现浇桥面脚手架基础)。
(3)、埋设护筒①、钻孔前设置坚固、不漏水的孔口护筒,即孔口护筒采用5mm 钢板制作,内径比桩径大10~20cm,长度为1-1.5m(地质条件差的桩位应加长),护筒底部与土层相接处用粘土夯实,护筒外面与原土之间也要用粘土填满、夯实,严防地表水顺该处渗入。
②、护筒埋设准确竖直,由项目部测量队复合坐标及护筒顶标高。
护筒中心竖直线与桩中心线重合,平均允许误差为5cm,竖直线倾斜不大于1%,可实测定位。
护筒顶部高出施工地面10~20cm。
③、护筒埋置深度应根据设计要求或桩位的水文地址情况确定,特殊情况应加深以保证钻孔和灌注混凝土的顺利进行。
(4)、泥浆准备:①、泥浆的制备采用原土造浆,泥浆池在桩位附近就近开挖,废弃泥浆用泥浆车拉走。
②、泥浆性能指标应符合下列规定:泥浆比重:正循环钻机入孔泥浆比重为1.05~1.2⑹、钻机安装及钻孔:①、安装冲击钻机前,底架应垫平,保持稳定,不得产生位移和沉陷。
钻头或钻杆中心与桩位中心偏差不得大于5cm。
②、开孔孔位必须准确,应使初成孔壁、竖直、圆顺、坚实。
③、钻孔时,孔内水位宜高于护筒底脚0.5m以上或地下水位以上1.5~2.0m。
④、钻孔时,起落钻头速度宜均匀,不得过猛或骤然变速。
⑤、钻孔作业应连续进行,因故停钻时,钻头提离孔底5m以上,钻孔过程中应经常检查并记录土层变化情况,并与地质剖面图核对。
钻孔达到设计深度后,对孔位、孔径、孔深和孔形进行检验,并填写钻孔记录表。
钻孔灌注桩基础施工

钻孔灌注桩基础施工钻孔灌注桩基础施工是一种常用的基础施工方法,它适用于各种土质和地质条件下的建筑物和结构。
本文将介绍钻孔灌注桩基础施工的步骤、施工工艺以及注意事项等内容。
一、钻孔灌注桩基础施工的步骤1. 地质勘察:在进行钻孔灌注桩基础施工之前,必须进行全面的地质勘察,了解土层的性质和地下水位等信息,以便合理设计和施工。
2. 确定桩基位置:根据设计要求和结构布局,在地面上确定钻孔灌注桩的位置。
3. 机械钻孔:使用大型钻机进行机械钻孔,钻孔的直径和深度根据设计要求确定。
在钻孔过程中,要注意控制孔径的垂直度和直径的一致性。
4. 清孔:在钻孔完成后,必须进行清孔作业,以清除孔内的岩屑和松散土壤等杂质。
清孔时可以使用水冲洗、气压吹扫等方法。
5. 钢筋安装:在清孔后,根据设计要求在孔内安装钢筋笼。
钢筋的类型和布置要符合设计要求,并且与桩混凝土的浇注相协调。
6. 混凝土浇注:在钢筋安装完成后,开始进行混凝土的浇注工作。
浇注时要注意控制浇筑速度和浇筑高度,以防止混凝土塌落和气泡的产生。
7. 灌注桩头:在混凝土浇注完成后,可以在桩头部分进行灌注。
灌注时要尽量控制流动性,以确保灌注充分。
8. 桩顶整平:在灌注完成后,应对桩顶部分进行整平,使其与地面齐平。
可以使用刮平机、压路机等工具进行整平。
二、钻孔灌注桩基础施工的工艺要点1. 施工现场安全:进行钻孔灌注桩基础施工时,必须设置施工现场的安全防护措施,包括警示标识、安全通道、消防设备等。
2. 施工监控:在施工过程中,应进行实时监控,以确保施工质量和安全。
可以使用传感器等设备对钻孔、浇筑和灌注等环节进行监测。
3. 设备操作:钻孔灌注桩基础施工需要使用大型机械设备,必须由经过培训和持有效证书的操作人员进行操作,严禁无证人员操作设备。
4. 施工材料:施工过程中所使用的材料必须符合相关标准和规定,并且经过质量检验合格。
5. 现场管理:在施工过程中,要加强现场管理,保持施工现场的整洁和秩序,确保施工工作的顺利进行。
钻孔灌注桩施工方案
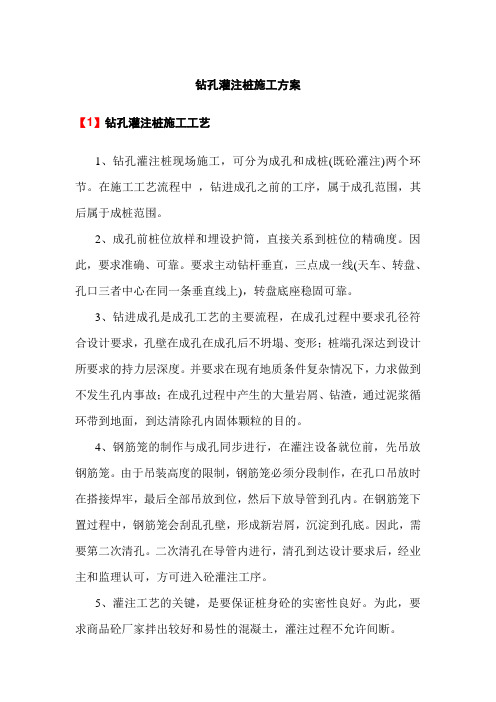
钻孔灌注桩施工方案【1】钻孔灌注桩施工工艺1、钻孔灌注桩现场施工,可分为成孔和成桩(既砼灌注)两个环节。
在施工工艺流程中,钻进成孔之前的工序,属于成孔范围,其后属于成桩范围。
2、成孔前桩位放样和埋设护筒,直接关系到桩位的精确度。
因此,要求准确、可靠。
要求主动钻杆垂直,三点成一线(天车、转盘、孔口三者中心在同一条垂直线上),转盘底座稳固可靠。
3、钻进成孔是成孔工艺的主要流程,在成孔过程中要求孔径符合设计要求,孔壁在成孔在成孔后不坍塌、变形;桩端孔深达到设计所要求的持力层深度。
并要求在现有地质条件复杂情况下,力求做到不发生孔内事故;在成孔过程中产生的大量岩屑、钻渣,通过泥浆循环带到地面,到达清除孔内固体颗粒的目的。
4、钢筋笼的制作与成孔同步进行,在灌注设备就位前,先吊放钢筋笼。
由于吊装高度的限制,钢筋笼必须分段制作,在孔口吊放时在搭接焊牢,最后全部吊放到位,然后下放导管到孔内。
在钢筋笼下置过程中,钢筋笼会刮乱孔壁,形成新岩屑,沉淀到孔底。
因此,需要第二次清孔。
二次清孔在导管内进行,清孔到达设计要求后,经业主和监理认可,方可进入砼灌注工序。
5、灌注工艺的关键,是要保证桩身砼的实密性良好。
为此,要求商品砼厂家拌出较好和易性的混凝土,灌注过程不允许间断。
6、钻孔灌注桩的施工是一项技术要求非常高的工程,为了确保桩基的施工质量,我们将从施工的每个环节入手,把质量和安全贯穿到每道程序中,做到环环紧扣有条不紊。
【2】泥浆工艺1、泥浆循环系统(1)泥浆池→泥浆→水龙头→沉淀→泥浆池。
(2)为了能及时根据施工需要调整泥浆性能,要求各机单独开挖泥浆池,各自建立一套循环方案。
2、泥浆性能的调整和处理(1)严格把好泥浆护壁,根据钻进地层特征,及时相应调整泥浆各项性能指标,是确保成孔和成桩全过程质量的主要环节。
(2)针对施工场地松散地层的情况,本工程刚开始施工时,先进行一些外工地性能较好的泥浆,钻进过程中利用地层特性造浆。
必要时,采用加入白泥粉和外加剂,强化泥浆性能指标,故有“泥浆是钻孔的血液”之称。
钻孔灌注桩施工方案(3篇)

第1篇一、工程概况钻孔灌注桩施工是建筑基础工程中常用的一种基础形式,适用于各种地质条件。
本方案针对某建筑基础工程,设计钻孔灌注桩基础,以下为施工方案。
1. 工程名称:某建筑基础工程2. 工程地点:某市某区某街道3. 工程规模:总建筑面积约10000平方米4. 基础形式:钻孔灌注桩基础5. 地质条件:根据地质勘察报告,地基土层主要为粉土、粉砂层,局部夹有砾石层。
二、施工准备1. 施工组织(1)项目经理负责整个施工过程的组织协调,确保工程质量和进度。
(2)施工员负责现场施工管理和施工质量控制。
(3)技术员负责技术指导和施工方案的实施。
(4)安全员负责现场安全管理和安全教育培训。
2. 材料准备(1)钢筋:选用符合国家标准的HPB300钢筋,直径为25mm。
(2)水泥:选用符合国家标准的硅酸盐水泥,强度等级为32.5MPa。
(3)砂石:选用符合国家标准的河砂和碎石,级配符合要求。
(4)其他材料:模板、桩帽、护筒、焊条等。
3. 机械设备(1)钻孔设备:选用XY-2型钻机,钻孔直径为600mm。
(2)混凝土搅拌设备:选用JS1000型混凝土搅拌机。
(3)混凝土输送设备:选用HBT60A型混凝土泵车。
(4)钢筋加工设备:选用钢筋弯曲机、钢筋切断机等。
(5)其他设备:汽车吊、搅拌运输车、挖掘机等。
三、施工工艺1. 施工流程(1)场地平整:将施工场地平整,清除障碍物。
(2)护筒埋设:根据设计图纸,埋设护筒,护筒埋设深度应符合设计要求。
(3)钻孔:使用钻机进行钻孔,钻孔深度应符合设计要求。
(4)钢筋笼制作与安装:根据设计图纸,制作钢筋笼,安装钢筋笼。
(5)混凝土浇筑:使用混凝土泵车进行混凝土浇筑,浇筑过程中应严格控制混凝土质量。
(6)成桩:待混凝土达到设计强度后,进行成桩。
2. 施工要点(1)护筒埋设1)根据设计图纸,确定护筒埋设位置。
2)使用挖掘机挖坑,坑底平整,坑底尺寸略大于护筒直径。
3)将护筒放入坑内,确保护筒垂直,使用水平尺校正。
钻孔灌注桩工程施工方案(3篇)
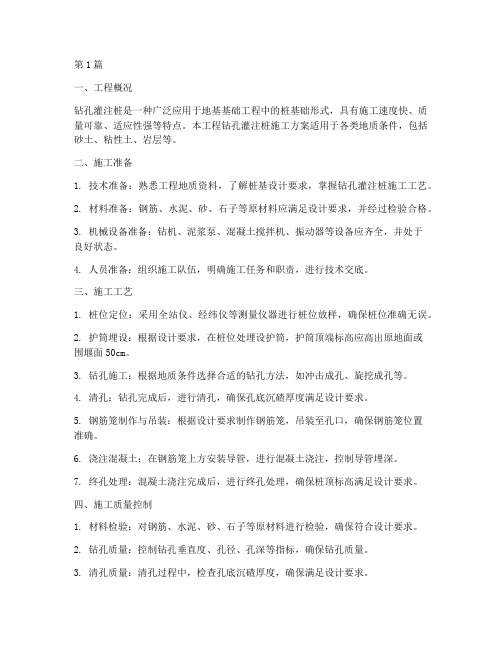
第1篇一、工程概况钻孔灌注桩是一种广泛应用于地基基础工程中的桩基础形式,具有施工速度快、质量可靠、适应性强等特点。
本工程钻孔灌注桩施工方案适用于各类地质条件,包括砂土、粘性土、岩层等。
二、施工准备1. 技术准备:熟悉工程地质资料,了解桩基设计要求,掌握钻孔灌注桩施工工艺。
2. 材料准备:钢筋、水泥、砂、石子等原材料应满足设计要求,并经过检验合格。
3. 机械设备准备:钻机、泥浆泵、混凝土搅拌机、振动器等设备应齐全,并处于良好状态。
4. 人员准备:组织施工队伍,明确施工任务和职责,进行技术交底。
三、施工工艺1. 桩位定位:采用全站仪、经纬仪等测量仪器进行桩位放样,确保桩位准确无误。
2. 护筒埋设:根据设计要求,在桩位处埋设护筒,护筒顶端标高应高出原地面或围堰面50cm。
3. 钻孔施工:根据地质条件选择合适的钻孔方法,如冲击成孔、旋挖成孔等。
4. 清孔:钻孔完成后,进行清孔,确保孔底沉碴厚度满足设计要求。
5. 钢筋笼制作与吊装:根据设计要求制作钢筋笼,吊装至孔口,确保钢筋笼位置准确。
6. 浇注混凝土:在钢筋笼上方安装导管,进行混凝土浇注,控制导管埋深。
7. 终孔处理:混凝土浇注完成后,进行终孔处理,确保桩顶标高满足设计要求。
四、施工质量控制1. 材料检验:对钢筋、水泥、砂、石子等原材料进行检验,确保符合设计要求。
2. 钻孔质量:控制钻孔垂直度、孔径、孔深等指标,确保钻孔质量。
3. 清孔质量:清孔过程中,检查孔底沉碴厚度,确保满足设计要求。
4. 混凝土质量:控制混凝土配合比,确保混凝土强度和耐久性。
5. 桩顶标高:确保桩顶标高满足设计要求。
五、安全措施1. 严格遵守安全操作规程,确保施工安全。
2. 定期对机械设备进行检查、维护,确保设备安全运行。
3. 设置安全警示标志,提醒施工人员注意安全。
4. 加强施工人员安全教育,提高安全意识。
六、环境保护1. 合理安排施工时间,减少对周边环境的影响。
2. 处理好施工废水、废气和固体废弃物,防止污染环境。
钻孔灌注桩基础

钻孔灌注桩基础钻孔灌注桩基础是一种在建筑工程中广泛应用的基础形式,它具有承载能力高、稳定性好、适应性强等诸多优点。
接下来,让我们一起深入了解一下钻孔灌注桩基础。
钻孔灌注桩基础的施工过程相对较为复杂,但大致可以分为以下几个主要步骤。
首先是场地准备。
在施工前,需要对施工现场进行清理和平整,确保场地坚实、平整,以便于施工设备的安装和操作。
同时,还需要根据设计要求确定桩位,并设置好相应的测量控制点。
接下来是钻孔。
这是整个施工过程中的关键环节之一。
通常会使用旋转钻机、冲击钻机等设备进行钻孔。
在钻孔过程中,要控制好钻孔的速度、垂直度和深度,以保证桩孔的质量。
同时,还需要根据地质情况,选择合适的钻进方法和钻头类型。
例如,在遇到坚硬的岩石地层时,可能需要采用冲击钻进的方法;而在软弱地层中,则更适合使用旋转钻进。
钻孔完成后,需要进行清孔。
清孔的目的是清除孔底的沉渣和泥浆,保证桩底的承载力。
清孔的方法有抽浆法、换浆法等。
清孔完成后,需要对孔深、孔径、孔的垂直度等进行检测,确保符合设计要求。
然后是钢筋笼的制作和安装。
钢筋笼是由主筋、箍筋等钢筋按照设计要求焊接而成的。
在制作钢筋笼时,要保证钢筋的规格、数量、间距等符合设计要求,并且焊接牢固。
钢筋笼制作完成后,通过起重机等设备将其吊入桩孔内,并进行固定,确保其位置准确。
再之后是灌注混凝土。
混凝土的灌注是通过导管进行的。
在灌注前,需要对混凝土的配合比进行设计,确保其具有良好的流动性和强度。
灌注过程中,要控制好灌注的速度和导管的埋深,防止出现断桩、夹泥等质量问题。
同时,要保证混凝土的连续灌注,直至灌注到设计标高。
钻孔灌注桩基础的优点是显而易见的。
它能够适应各种地质条件,无论是软土、砂土还是岩石地层,都能够有效地施工。
而且,灌注桩的桩径和桩长可以根据实际需要进行调整,具有很大的灵活性。
此外,灌注桩与周围土体的摩擦力较大,能够提供较高的承载能力,保证建筑物的稳定性。
然而,钻孔灌注桩基础的施工也存在一些难点和需要注意的问题。
钻孔灌注桩施工方案
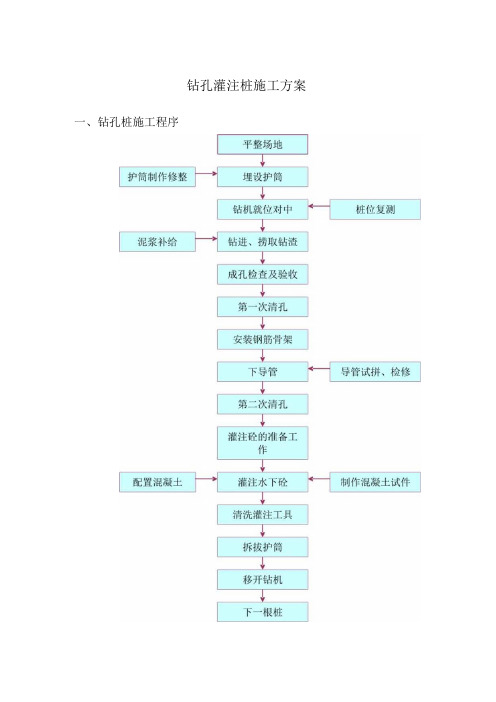
钻孔灌注桩施工方案一、钻孔桩施工程序二、施工方法1、钻孔准备(1)平整桩基范围内的场地,清除杂物,在桩基范围内回填0∙6米回填砂,再铺0.2米石粉或细砂并平整;道路部位采用石硝,填筑高度与工作面齐平。
(2)采用十字法拉线埋设护筒,护筒比桩径大IOCnU护筒沉落后,周边用粘土回填夯实。
护筒下沉时要核对桩轴线,保证与护筒中心一致,护筒高出地面30cm。
2、成孔(1)钻机就位前,对各项准备工作进行检查。
钻机就位后,用枕木作机座,要使底座和顶端平稳,保证在钻进和运行中不产生位移,倾斜和沉陷,否则及时找出原因,及时处理。
(2)钻机就位施钻时,将钻机底盘调成水平状态,当钻头吊入护筒开始钻下第一钻时,应小心使钻尖对准设计中心,然后盖上封口板,卡上推钳,试转数圈。
(3)开钻时,在桩孔内投入一定数量的粘土及相应的水,钻机不进尺空转,利用钻头搅制泥浆,搅拌后抽至循环池泥浆的相对密度为1.05〜1.20,待循环池及桩孔全部储够该桩泥浆后,先启动泥浆泵和转盘,后进行进尺钻进,慢速钻进,(4)在钻进过程中,进尺的快慢根据土质情况来控制,并经常对钻孔泥浆的相对密度和粘度等检查观察,在粘性土及含砂率小的泥岩中,宜用中等转速稀泥浆(相对密度为1.05-1.20)钻进,在砂性土及含砂率高的地层中,宜用低转速、大泵量、稠泥浆(相对密度为1.20〜1.45)钻进。
确保泥浆护壁的相应厚度和质量。
(5)钻进成孔过程中,经常捞取钻渣,观察地层的变化,以及时调整泥浆的稠度,确定是否增加或减少转速,在岩土变化处均捞取渣样,判明分层发表情况,并记入记录表中。
当钻进入基岩后,每10〜30厘米应分段取样一次。
(6)施工作业分班连续进行,职确因故须停止钻进时,将钻头停放在也底不超过12小时,以免被泥浆埋住钻头。
(7)及时详细填写钻孔施工记录,交接班时,交代钻进情况及下一班应注意事项。
3、终孔及清孔钻孔桩施工时密切注意地层的变化,当孔深已达到设计标高,但岩样硬度未能达到设计要求时,则仍继续钻孔并同时通知监理及设计人员,变更该孔的终孔标高。
钻孔灌注桩施工方法

钻孔灌注桩施工方法㈠落放轴线:复核建筑物红线及水准点,按图落放轴线,放出桩点,采用 DS3 水准仪和电子经纬仪。
具体如下:1、按桩位图与控制点连接推算出各桩位的理论坐标数据。
放样时采用极坐标法进行施测,用全站仪进行测量、定点。
2、根据放样位置埋设护筒,然后再校核桩位中心在护筒中的准确位置,并利用十字交叉法,用测量绳十字交叉,交叉点对准桩中心测绳两头引到护筒口上用红漆油做好标记,钻机就位时在护筒标记上拉好十字线,钻机转盘中心也拉好十字线,用测锤对准护筒上十字中心(即桩位中心),校正转盘上的中心,使之符合要求。
3、为确保测量数数据的准确无误,桩位坐标的推算由两名测量专业人员进行推算校核。
桩位放样时由一名测量专业人员放样,另一名校核。
4、在施工中采用二次校核的方法进行护筒埋设,先放样定点,在所测桩位中心先打入一根钢筋或木桩作桩位标志,按放样位置埋设护筒。
护筒埋设好后,在护筒内再校核桩位的准确中心位置,并在护筒口上用红漆油做好十字交叉的标记,钻机就位时在标记上拉好十字线,并且严格按十字线中心对中。
5、埋设护筒要求护筒与桩位垂直并同心,误差小于50mm,护筒厚度8mm,护筒高度0.5m,要用粘土回填夯实,以免护筒移动。
㈡桩位定位:采用十字定位法定位桩点后,挖排放泥浆槽及安放护筒,护筒计划采用加长式护筒使其穿过冲填层,保证桩孔不会产生塌孔,护筒中心与桩点对应,偏移量不超出规范要求。
钻机就位时,主动钻杆中心对准孔位中心,机台转盘用水平尺测量水平度。
经自检和监理验收合格后进行下道工序。
㈢埋设护筒:为防止钻进施工中护筒外圈返浆造成塌孔和护筒脱落,护筒要埋入自然地面以下1.0m(粘性土)或1.5m(砂土),高出自然地面200mm。
护孔内径比设计桩径大100mm,其中心与桩位中心线偏差不得大于20mm,护筒其垂直度偏差小于1/150。
钻孔开始前埋设护筒,以保证钻机沿桩位垂直方向顺利工作,同时保护孔口和提高桩孔内的泥浆水头。
钻孔灌注桩基础施工方案

钻孔灌注桩基础施工方案
一、项目简介
钻孔灌注桩基础是一种常用于建筑工程中的基础施工技术,它
通过在地下使用钻机进行钻孔作业,并在孔底注入混凝土来形成钻
孔灌注桩。
这种基础形式适用于各种土质和地质条件,并且在实际
施工中具有较高的可靠性和稳定性。
本文将从施工前准备、施工步骤、质量控制等方面对钻孔灌注桩基础施工方案进行详细介绍。
二、施工前准备
1.设计方案确认:在进行施工前,需确认设计方案并获取相关
设计图纸和规范要求。
2.排除场地障碍:清理施工场地,排除可能影响施工的障碍物。
3.施工设备及人员准备:配备所需的钻机、混凝土搅拌机、吊
车等施工设备,并组织经验丰富的施工人员。
三、施工步骤
1.钻孔操作:按照设计要求和相关规范,选用合适直径的钻头
进行钻孔。
在钻孔过程中,要保持孔壁的稳定,并根据情况进行钻
进和钻孔土样的采集。
2.钢筋布置:在钻孔完成后,根据设计要求将钢筋布置在孔洞内,并固定牢固。
3.注浆处理:使用适当的注浆设备将混凝土注入钻孔中,注浆
过程要均匀、连续,保证混凝土充满整个孔洞,并与钢筋紧密结合。
4.固化养护:完成注浆后,对刚注入的混凝土进行养护处理,
以确保混凝土的强度和稳定性。
四、质量控制
1.原材料控制:对所使用的钻孔灌注桩基础材料(如钢筋、混
凝土等)进行严格的质量控制,确保其符合相应的标准要求。
2.施工过程控制:在施工过程中,对钻孔、钢筋布置、注浆等
环节进行监控,确保施工过程的质量。
3.验收测试:在基础施工完成后,进行相应的验收和测试,包
括对孔径和混凝土强度等参数的检测。
钻孔灌注桩基础施工方案
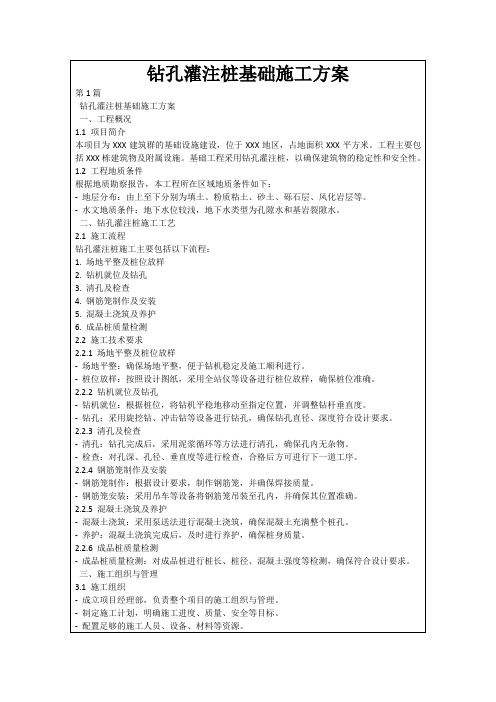
-清孔:钻孔完成后,采用泥浆循环等方法进行清孔,确保孔内无杂物。
-检查:对孔深、孔径、垂直度等进行检查,合格后方可进行下一道工序。
2.2.4钢筋笼制作及安装
-钢筋笼制作:根据设计要求,制作钢筋笼,并确保焊接质量。
-钢筋笼安装:采用吊车等设备将钢筋笼吊装至孔内,并确保其位置准确。
2.2.5混凝土浇筑及养护
-准备足够的施工设备和机具,并进行调试。
2.3现场准备
-对施工场地进行平整,确保施工道路畅通。
-建立临时设施,如搅拌站、仓库等。
-完成施工用水、用电的接通。
三、钻孔灌注桩施工流程
3.1桩位放样
-根据设计图纸,使用专业测量工具进行桩位放样。
-确保桩位准确无误,并设置明显的桩位标志。
3.2钻孔作业
-钻机就位,调整钻杆垂直度,确保孔位偏差在允许范围内。
6.2资源配备
-确保人力资源、材料、设备等资源的充足配备。
-根据施工进度,合理调配资源,提高施工效率。
本钻孔灌注桩基础施工方案旨在为工程提供全面的施工指导,确保工程质量和施工安全。在施工过程中,应根据实际情况灵活调整,以满足工程的实际需求。
-制定施工计划,明确施工进度、质量、安全等目标。
-配置足够的施工人员、设备、材料等资源。
3.2施工管理
-建立完善的质量管理体系,对施工过程进行全程监控。
-加强施工现场安全管理,严格执行安全操作规程。
-做好环境保护工作,降低施工对周边环境的影响。
四、质量保证措施
4.1质量保证体系
-建立健全质量保证体系,制定质量管理制度,确保施工质量。
5.2安全防护
-施工现场设置安全警示标志,提醒施工人员注意安全。
(完整版)钻孔灌注桩基础施工方案

(完整版)钻孔灌注桩基础施工方案范本 1:钻孔灌注桩基础施工方案1. 引言1.1 项目概述1.2 目的1.3 范围1.4 术语定义(法律名词及注释)2. 前期准备工作2.1 地质勘察2.2 方案设计2.3 材料采购3. 钻孔设备与工具准备3.1 钻机选型3.2 桩材质准备3.3 钻孔设备与工具清单4. 施工过程4.1 钻孔平台搭建4.2 钻孔操作规范4.3 钻孔过程中的注意事项4.4 钻孔质量控制5. 灌注桩制作5.1 混凝土配合比设计5.2 灌注过程控制5.3 桩混凝土强度监测5.4 灌注桩质量控制6. 工程施工安全措施6.1 钻孔过程的安全注意事项 6.2 灌注过程的安全控制6.3 安全事故应急预案7. 附录7.1 施工工艺图纸7.2 施工材料证明书7.3 施工质量检测报告8. 结论8.1 项目总结8.2 施工效果评价附件:1. 工程图纸2. 材料证明书3. 施工质量检测报告法律名词及注释:1. 钻孔灌注桩:一种构筑物基础形式,通过钻孔施工并灌入混凝土,以达到加固地基的目的。
2. 地质勘察:针对工程所在区域的地质条件进行详细调查和研究的过程。
3. 施工效果评价:对工程施工结果进行评估和总结的过程。
范本 2:钻孔灌注桩基础施工方案1. 引言1.1 项目背景1.2 目的与范围1.3 术语定义(法律名词及注释)2. 基础设计2.1 地质勘察报告分析2.2 施工方案设计2.3 材料选用及规格3. 前期工作准备3.1 施工设备准备3.2 环境保护准备3.3 周边交通组织4. 钻孔施工4.1 钻孔设备及工具配置4.2 钻孔平台搭建4.3 钻孔操作流程4.4 钻孔质量控制5. 灌注桩制作5.1 混凝土配合比控制5.2 灌注过程要点5.3 灌注桩质量检验5.4 灌注桩质量控制6. 施工安全措施6.1 钻孔安全注意事项 6.2 灌注过程安全控制6.3 灾害事故应急预案7. 施工质量控制7.1 施工工艺与技术管控 7.2 施工质量监督检查7.3 现场质量控制要点8. 结尾8.1 工程总结8.2 建议和改进意见附件:1. 地质勘察报告2. 混凝土配合比设计表3. 施工设备配置清单法律名词及注释:1. 钻孔灌注桩:一种基于地下土层特性,通过钻孔施工并灌注混凝土,用于地基加固的建造工程形式。
小直径钻孔灌注桩基础施工方法

小直径钻孔灌注桩基础施工方法一、微型桩施工前应具备的资料(1)微型桩施工前应具备下列资料。
1)场地工程地质资料和必要的水文地质资料。
2)场地和邻近区域内的地下管线、地下构筑物、危房、精密仪器车间等的调查资料。
3)桩基工程的施工组织设计或施工方案。
4)水泥、砂、石、钢筋等原材料及其制品的质检报告。
(2)施工组织设计应结合工程特点,有针对性地制订相应的质量管理措施,主要包括以下内容。
1)施工平面图:标明桩位、编号、施工顺序、水电线路和临时设施的位置。
2)确定成孔机械、配套设备以及合理施工工艺的有关资料,以及相应的泥浆处理措施。
3)施工作业计划和劳动力组织计划。
4)机械设备、备件、工具、材料供应计划。
5)桩基施工时,对安全、劳动保护、防火、防雨、防台风、爆破作业、文物和环境保护等方面应按有关规定执行。
6)保证工程质量、安全生产和季节性(冬雨季)施工的技术措施。
二、微型桩施工的一般规定(1)定位误差:定位平面误差≤10mm。
(2)施工误差:①垂直度≤1%;②桩顶水平位移偏差≤50mm;③标高偏差≤50mm。
(3)成孔桩长:设计桩长+超灌50cm+超钻20cm,基坑开挖后,把超灌部分凿去。
(4)钢筋笼保护层厚度不应小于3cm。
(5)钢筋笼制作应满足相关规程要求。
(6)微型桩与承台连接需满足如下要求:1)桩顶嵌入承台的长度,不宜小于100mm。
2)微型桩桩顶主筋锚入承台的长度不应小于40倍主筋直径,且应满足GB 50010《混凝土结构设计规范》的要求。
3)桩顶主筋应外倾成喇叭形(大约与竖直线夹角为15°),并应设置箍筋或螺旋筋,其直径与桩身箍筋直径相同,间距为100~200mm。
4)当承台高度不满足锚固要求时,竖向锚固长度不应小于20倍纵向主筋直径,并向柱轴线方向呈90°弯折。
三、施工机械及材料详见本书第二章第十三节。
四、投石注浆成桩施工方法(一)成桩步骤及工序1.成孔(1)钻机在工作平台上就位后,直桩应保持钻机底盘水平,斜桩应用罗盘检查钻杆的倾斜度(见图1231)。
钻孔灌注桩主要施工方法
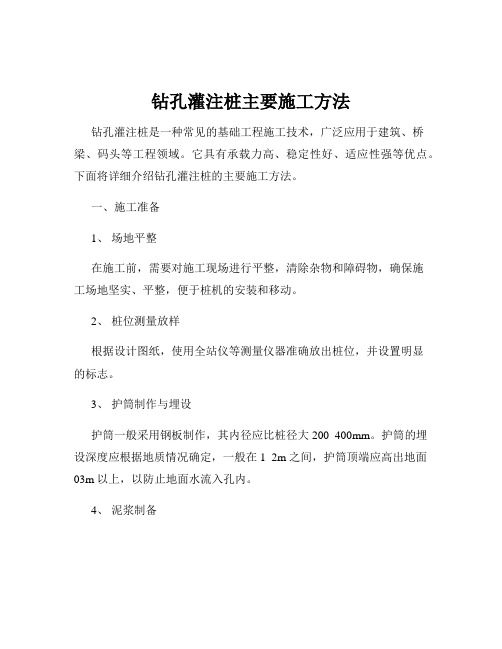
钻孔灌注桩主要施工方法钻孔灌注桩是一种常见的基础工程施工技术,广泛应用于建筑、桥梁、码头等工程领域。
它具有承载力高、稳定性好、适应性强等优点。
下面将详细介绍钻孔灌注桩的主要施工方法。
一、施工准备1、场地平整在施工前,需要对施工现场进行平整,清除杂物和障碍物,确保施工场地坚实、平整,便于桩机的安装和移动。
2、桩位测量放样根据设计图纸,使用全站仪等测量仪器准确放出桩位,并设置明显的标志。
3、护筒制作与埋设护筒一般采用钢板制作,其内径应比桩径大 200 400mm。
护筒的埋设深度应根据地质情况确定,一般在 1 2m 之间,护筒顶端应高出地面03m 以上,以防止地面水流入孔内。
4、泥浆制备泥浆在钻孔灌注桩施工中起着重要的作用,它可以护壁、悬浮钻渣和冷却钻头。
泥浆的性能指标应根据地质情况和施工要求进行调整,一般包括比重、黏度、含砂率等。
二、钻孔1、钻机就位将钻机安装在平整、坚实的地面上,调整钻机的水平和垂直度,使钻头中心与桩位中心重合。
2、钻进根据地质情况选择合适的钻进方式和钻头。
在钻进过程中,要控制好钻进速度和钻进压力,避免钻孔偏斜和坍孔。
同时,要及时清理孔内的钻渣,保持孔内清洁。
3、终孔检查当钻孔达到设计深度后,应对孔深、孔径、孔位和孔形等进行检查,确认符合设计要求后方可进行下一步施工。
三、清孔1、第一次清孔在钻孔完成后,立即进行第一次清孔。
清孔的方法一般采用正循环或反循环清孔,将孔内的钻渣和泥浆清除干净,使孔底沉渣厚度符合设计要求。
2、第二次清孔在安放钢筋笼和导管后,进行第二次清孔。
清孔的方法与第一次清孔相同,清孔结束后,应立即进行混凝土灌注。
四、钢筋笼制作与安放1、钢筋笼制作钢筋笼应在施工现场制作,根据设计图纸的要求,将钢筋焊接或绑扎成钢筋笼。
钢筋笼的尺寸和钢筋间距应符合设计要求,同时要保证钢筋笼的刚度和稳定性。
2、钢筋笼安放钢筋笼安放时,应采用吊车或塔吊等起重设备进行。
在安放过程中,要保持钢筋笼的垂直和居中,避免碰撞孔壁。
钻孔灌注桩基础施工方法要点

钻孔灌注桩基础施工方法要点1、钢护筒打入护筒埋设采用人工挖埋护筒底部、周边与土层相接处用50cm厚粘土夯实,严防水流渗入。
护筒埋设准确竖直,护筒顶面中心和护筒底面中心位置与设计桩中心偏差应小于5,护筒竖向的倾斜度不大于1%。
2、制造泥浆制浆前,先把粘土尽量打碎,使其在搅拌中容易成浆,缩短成浆时间,提高泥浆质量。
制浆时,可将打碎的粘土直接投入筒内,使用冲击锥冲击制浆,待粘土已冲搅成泥浆时,即可进行钻孔。
多余的泥浆用管子导入钻孔外泥浆池贮存,以便随时补充孔内泥浆。
钻孔时,采用自流回灌式泥浆循环系统,由泥浆池、沉淀池、循环槽和泥浆搅拌站组成。
泥浆池容积应为桩孔容积的1.5——2.0北以上。
泥浆池、沉淀池、循环槽和泥浆搅拌站在施工时根据现场实际情况进行合理布置。
泥浆原料粘土的性能要求:泥浆原料尽可能使用膨润土,使用粘土时符合以下要求:(1)自然风干后,用手不易掰开捏碎;(2)干土破碎时,断面有坚硬的尖锐棱角;(3)用刀切开时,切面光滑、颜色较深;(4)水湿后有粘滑感,如水和成泥膏后,容易搓成1mm的细长泥条,用手指揉捻,感觉砂粒不多,侵水后能大量膨胀;(5)胶体率不低于95%;(6)含砂率不大于4%;(7)制浆能力不低于2.5L/kg.选用优质粘土和添加剂造浆,入孔泥浆比重控制在1.1~1.3范围(特殊情况单独设计)。
泥浆性能指标应经试验检验并达标。
钻进中应随时检验泥浆比重、粘度、含砂率、胶体率等,并填写泥浆试验记录表。
废弃泥浆沉淀后送污土场处理。
3、钻孔钻机就位前,对主要机具进行检查、维修和安装,保证配套设施的就位及水电供应的接通。
钻孔前,根据施工图设计所提供地质、水文资料,绘制钻孔处地质剖面图,挂在钻台上,以供对不同土层选择适当的钻头、钻进压力和速度以及适当的泥浆比重参考数据。
钻进过程中,应注意土层变化,在土层变化处均应捞取渣样,判断土层,并记入记录表中。
钻机安装就位后,底座和顶端应平稳,不得产生位移和沉陷。
钻孔灌注桩基础施工工艺流程

钻孔灌注桩基础施工工艺流程一、工艺流程场地布置→桩位放样→埋设护筒→旋挖机就位→旋挖钻进成孔→一次清孔→成孔验收→钢筋笼吊装→安装导管→二次清孔→水下灌注混凝土→成桩→提拔护筒→钻机移位。
二、施工要点2.1、桩位放线1、测量方法首先,根据已提供的坐标,经过复核合格后,用极坐标法放出桩的平面位置,用另一控制点上进行复核检查。
标高用水准仪测出护筒顶标高,以控制孔深和钢筋笼标高、混凝土面标高。
依据设计图纸的桩位进行测量放线,使用全站仪测定桩位。
在桩位点打300mm深的木桩,桩上标定桩位中心,并采用“十字栓桩法”作好标记,并加以保护。
测量结果经自检、复检后,报请监理复核,复核无误并签字认可后,方可施工。
2、测量管理(1)测量队伍我项目部设专职测量人员,负责测量统筹管理和复核,经复核合格,报监理复核合格后,方可开钻。
(2)测量仪器测量班配备如下测量仪器和设备:J2级全站仪1套(测角中误差±2″,测距精度3mm±2ppm)包括主机、脚架、棱镜和觇牌;DS3水准仪1套,包括主机、脚架、水准尺和尺垫。
2.2、埋设护筒采用钢护筒,护筒直径大于钻头直径,护筒顶标高应高于施工面200~300mm,并确保筒壁与水平面垂直,隔离地面水,稳定孔口土壤和保护孔壁不塌,以保证其垂直度并防止泥浆流失,以利钻孔工作进行。
护筒周围用粘土分层夯实。
护筒定位时应先对桩位进行复核,然后以桩位为中心,定出相互垂直的十字控制桩线,并作十字栓点控制,挖护筒孔位,吊放入护筒,同时用十字线校正护筒中心及桩位中心,使之重合一致,并保证其护筒中心位置与桩中心偏差小于20mm。
钻孔前应再次测定桩位,并确保护筒底端坐在原状土层。
2.3、桩机就位目前现场基底部分区域处在淤泥层,且地下孔隙水位上涌,受其影响场地西侧、东侧及能源地面泥泞,无法满足桩机的承载力要求。
为确保安全,桩基施工前利用砖渣铺设承载力不足的区域,铺设厚度约1.0m。
桩机就位前要求场地处理平整坚实,以满足施工垂直度要求,桩机按指定位置就位后,须在技术人员指导下,调整角度及对孔。
钻孔灌注桩基础施工方案
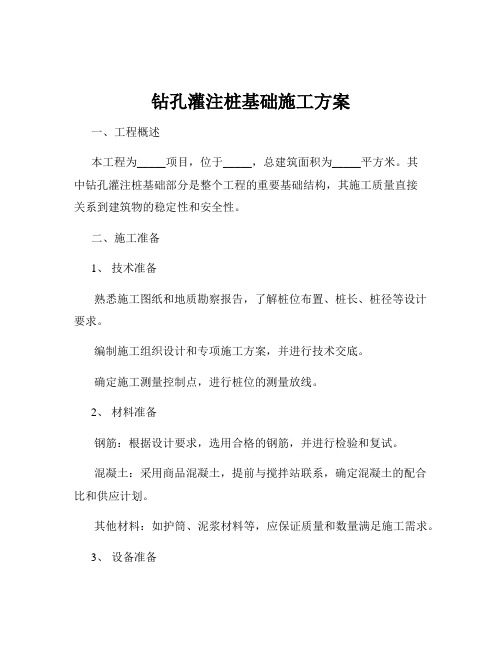
钻孔灌注桩基础施工方案一、工程概述本工程为_____项目,位于_____,总建筑面积为_____平方米。
其中钻孔灌注桩基础部分是整个工程的重要基础结构,其施工质量直接关系到建筑物的稳定性和安全性。
二、施工准备1、技术准备熟悉施工图纸和地质勘察报告,了解桩位布置、桩长、桩径等设计要求。
编制施工组织设计和专项施工方案,并进行技术交底。
确定施工测量控制点,进行桩位的测量放线。
2、材料准备钢筋:根据设计要求,选用合格的钢筋,并进行检验和复试。
混凝土:采用商品混凝土,提前与搅拌站联系,确定混凝土的配合比和供应计划。
其他材料:如护筒、泥浆材料等,应保证质量和数量满足施工需求。
3、设备准备钻孔设备:根据地质条件和桩径、桩长等要求,选用合适的钻孔机械,如旋挖钻机、冲击钻机等。
起重设备:配备吊车或塔吊,用于钢筋笼的吊运和安装。
灌注设备:准备混凝土灌注导管、料斗等。
4、现场准备平整场地,清除杂物,修筑施工便道。
设置泥浆池和沉淀池,保证泥浆的循环和排放。
安装水电设施,确保施工用电和用水的供应。
三、施工工艺流程1、测量放线根据设计图纸和测量控制点,使用全站仪或经纬仪进行桩位的测量放线。
桩位偏差应符合规范要求,经复核无误后,在桩位四周设置护桩。
2、埋设护筒护筒采用钢板制作,内径应比桩径大 200 400mm。
护筒埋置深度应根据地质情况确定,一般为 15 20m,护筒顶面应高出地面 03m 左右。
护筒中心与桩位中心偏差不应大于 50mm,垂直度偏差不应大于1%。
3、泥浆制备泥浆采用膨润土或优质粘土配制,根据地质情况和施工经验确定泥浆的比重、粘度等性能指标。
泥浆在钻孔过程中起到护壁、排渣和冷却钻头的作用。
4、钻孔钻机就位后,应调整钻机的水平和垂直度,保证钻孔的垂直度偏差符合规范要求。
按照钻进工艺要求,控制钻进速度和钻进压力,及时补充泥浆,保持孔内水头高度。
钻进过程中应做好钻孔记录,记录地层变化情况和钻进参数。
5、清孔钻孔达到设计深度后,进行第一次清孔,采用换浆法或抽浆法清除孔底沉渣。
- 1、下载文档前请自行甄别文档内容的完整性,平台不提供额外的编辑、内容补充、找答案等附加服务。
- 2、"仅部分预览"的文档,不可在线预览部分如存在完整性等问题,可反馈申请退款(可完整预览的文档不适用该条件!)。
- 3、如文档侵犯您的权益,请联系客服反馈,我们会尽快为您处理(人工客服工作时间:9:00-18:30)。
矿产资源开发利用方案编写内容要求及审查大纲
矿产资源开发利用方案编写内容要求及《矿产资源开发利用方案》审查大纲一、概述
㈠矿区位置、隶属关系和企业性质。
如为改扩建矿山, 应说明矿山现状、
特点及存在的主要问题。
㈡编制依据
(1简述项目前期工作进展情况及与有关方面对项目的意向性协议情况。
(2 列出开发利用方案编制所依据的主要基础性资料的名称。
如经储量管理部门认定的矿区地质勘探报告、选矿试验报告、加工利用试验报告、工程地质初评资料、矿区水文资料和供水资料等。
对改、扩建矿山应有生产实际资料, 如矿山总平面现状图、矿床开拓系统图、采场现状图和主要采选设备清单等。
二、矿产品需求现状和预测
㈠该矿产在国内需求情况和市场供应情况
1、矿产品现状及加工利用趋向。
2、国内近、远期的需求量及主要销向预测。
㈡产品价格分析
1、国内矿产品价格现状。
2、矿产品价格稳定性及变化趋势。
三、矿产资源概况
㈠矿区总体概况
1、矿区总体规划情况。
2、矿区矿产资源概况。
3、该设计与矿区总体开发的关系。
㈡该设计项目的资源概况
1、矿床地质及构造特征。
2、矿床开采技术条件及水文地质条件。