精益生产拉动系统设计
精益生产体系的结构与特征

精益生产体系的结构与特性假如把精益生产体系看作是一幢大厦, 那么大厦的基础就是计算机网络支持下的小组工作方式。
在此基础上的三根支柱就是: (1)准时生产(JIT), 它是缩短生产周期, 加快资金周转和减少成本, 实现零库存的重要方法;(2)成组技术(GT), 它是实现多品种、小批量、低成本、高柔性, 按顾客定单组织生产的技术手段;(3)全面质量管理(TQC), 它是保证产品质量、树立公司形象和达成无缺陷目的的重要措施, 如图1所示。
一、精益生产体系的目的(一)精益生产的基本目的工业公司是以赚钱为目的, 从事商品生产的社会经济组织。
因此, 最大限度地获取利润就成为公司的基本目的。
传统的大量生产方式是以标准化、大批量生产来减少成本, 提高效率的, 完全是依靠规模效益来实现公司利润目的的。
这种生产方式在经济高速增长、市场需求相对稳定的时期能取得良好的效果。
由于在这种情况下, 事实上不需要太严密的生产计划和细致的管理, 即使出现生产日程变动、工序间在制品储备不断增长、间接作业工时过大等问题, 只要能保证产品质量, 公司便可放手大量生产, 保证公司利润就不成问题。
然而, 在市场瞬息万变的今天, 在实行多品种、小批量生产的情况下, 这一生产方式显然是行不通的。
(二)的子目的1. 零库存在传统生产系统中, 在制品库存和成品库存被视为资产, 期末库存与期初库存之差代表这一周期流动资产的增值, 用以表达该部门效益的提高。
当由不拟定的供应者供应原材料和外购件时, 原材料和外购件的库存可视为缓冲器。
所以, 原材料、外购件和成品的库存能作为供应昔不按期供货或顾客订购量增长的缓冲。
工厂的效率是用车间设备运用率来考核的, 车间管理人员的责任是保持各设备及工作中心连续不断地运营, 达成满负荷工作, 即使设备加工的零件并不是现在订单所需的, 继续生产会加大库存也在所不惜。
事实上, 一个充满库存的生产系统, 会掩盖系统中存在的各种问题。
精益生产主要创始人大野耐一说:没有标准化就没有改进

精益生产主要创始人大野耐一说:没有标准化就没有改进。
【目的】:1、了解精益生产产生的背景和必然性;2、企业结合自己的实际需求来采用精益生产;3、理解精益生产的内涵和工具;4、企业能结合实际来应用精益生产。
【核心理论】1、消除八大浪费;2、降低成本。
【两大支柱】1、准时化;2、动化。
【精益生产的十大工具】1、5S现场管理2、目视化管理3、作业标准化(工艺流程);4、防差错5、快速换模(SMED)6、看板管理;7、U型布局8、IE工程9、6个西格玛;10、多能工。
精益生产管理的工具有哪些呢?1、准时化生产(JIT)准时生产方式是起源于日本丰田汽车公司,其基本思想是“只在需要的时候,按需要的量生产所需的产品”。
这种生产方式的核心是追求一种无库存的生产系统,或使库存达到最小的生产系统。
2、单件流JIT是精益生产的终极目标,它是通过不断消除浪费、降低库存、减少不良、缩短制造周期时间等具体要求来实现的。
单件流是帮助我们达到这一目标的关键手法之一。
3、看板管理(Kanban)看板是可以作为交流厂内生产管理信息的手段。
看板卡片包含相当多的信息并且可以反复使用。
常用的看板有两种:生产看板和运送看板。
4、零库存管理工厂的库存管理是供应链的一环,也是最基本的一环。
就制造业而言,加强库存管理,可缩短并逐步消除原材料、半成品、成品的滞留时间,减少无效作业和等待时间,防止缺货,提高客户对“质量、成本、交期”三大要素的满意度。
5、全面生产维护(TPM)以全员参与的方式,创建设计优良的设备系统,提高现有设备的利用率,实现安全性和高质量,防止故障发生,从而使企业达到降低成本和全面生产效率的提高。
6、运用价值流图来识别浪费生产过程中到处充斥着惊人的浪费现象,价值流图(ValueStreamMapping)是实施精益系统、消除过程浪费的基础与关键点。
7、生产线平衡设计由于流水线布局不合理导致生产工人无谓地移动,从而降低生产效率;由于动作安排不合理、工艺路线不合理,导致工人三番五次地拿起或放下工件。
精益思想与生产车间的改善设计案例.doc

精益思想与生产车间的改善设计案例1一、在精益思想指导下的生产车间的改善设计案例精益生产是以消除不增加价值的等待、排队和其他延迟活动为目标,按照确定的生产节拍进行生产并且每次仅生产单件产品的一种先进的生产方式。
与以往的靠计划系统发出指令的推动式生产方式不同,精益生产系统通过采用拉动的生产方式,来实现快速响应顾客实际需求的目的。
改善,是指以实现更好为标准而进行的持续改进或改变的过程,是精益生产实施中的重要基础组成部分。
通过对生产加工车间的布置和生产节拍进行改善设计,可以平衡生产线,使产品在生产线上的流动更加和谐,使之更有利于满足顾客的需要;通过建立“一个流”的生产方式,可以消除或简化生产过程中不产生任何价值的工作,使整个企业的潜在价值得以开发。
我们对某变压器厂箱体车间的物流设施布置进行了深入地分析,通过引入精益思想,提出了对目前大批量“成批与排队”生产线的改善设计步骤及方案。
在充分考虑了原有箱体生产加工的工序、工艺设计基础上,通过对原有设备进行改动,大大减少了产品和在制品的库存量及产品的交货时间,增加了生产线的柔性,提高了生产率。
1、生产车间的现状及存在的问题箱体车间主要生产S9/10KV A-2000KV A的19个种类变压器的箱体,箱体车间的布置现状图见图1。
由于每个箱体的大体结构相同,其加工工艺也十分相似,由此,该车间将箱体的生产分为大件生产区和小件生产区,其中小件工件通常是由人工搬运,而大件工件通常是由车间内部的天吊来完成。
通过对箱体车间的深入分析,得出该车间存在如下几点问题:(1) 物流的路线太长(见图1),造成运输时间的浪费,并且各工序之间的衔接过程存在许多Muda(浪费),造成各工序的生产效率很低;(2) 生产现场存在大量闲置不用的生产设备,占用了大量的空间,同时生产现场显得十分混乱;(3) 生产设备之间的距离较大,操作人员移动距离较大,使得操作人员每人每次只能操作一台机床,不利于操作人员工作效率的提高。
精益生产方案的设计原则

精益生产方案的设计原则一、整体优化原则“精益”一词起源于日本的“精益生产”(Lean Production),它强调尽可能减少资源的浪费,使生产系统尽可能高效地运转。
精益生产方案的设计原则之一就是整体优化,即以整体最优为目标,通过对全部环节的优化,达到全面提升生产效率和质量的目的。
在精益生产方案的设计中,我们要从整体上审视生产系统的各个环节,包括原材料采购、生产工艺、设备利用、生产计划、库存管理、人员培训等,通过消除浪费,提升生产效率,降低成本等手段,实现整体优化。
因此在制定精益生产方案时,应该以整体最优为目标,通过综合考虑各个环节,找出并解决系统中的瓶颈和短板,使整个生产系统都能够得到最大程度的提升。
二、持续改进原则精益生产方案的另一个设计原则是持续改进,即通过不断地寻找问题、解决问题、改进工艺和设备等手段,不断地提高生产效率和质量。
持续改进是精益生产的核心理念之一,它要求企业不断地反思和改进自己的生产方式和管理模式,使之逐步趋于最优状态。
在制定精益生产方案时,应该注重持续改进的过程,包括对生产过程的不断分析、对潜在问题的及时发现、对解决方案的不断尝试和改进等。
通过不断地寻找问题和解决问题,不断地改进工艺和设备,使企业的生产方式和管理模式在持续改进的过程中逐步趋于最佳状态,从而使生产效率和质量不断地得到提升。
三、注重员工参与原则精益生产方案的设计原则之一是注重员工参与,即充分调动员工的积极性和主动性,使其成为持续改进的中坚力量。
在制定精益生产方案时,应该鼓励员工积极参与各项生产活动,并且在决策过程中给予他们充分的权利和参与。
通过员工的参与,可以充分挖掘员工的潜力和智慧,使他们在实际生产中发挥主动性和创造性,为企业的持续改进贡献力量。
同时,员工参与还能够增强员工的责任感和团队意识,提高生产效率和质量,从而使企业得以持续发展。
四、精益生产的原则和方法精益生产的原则和方法包括价值流图、5S、SMED、Kaizen和其他原则和方法,它们作为精益生产的基本工具和手段,对生产过程进行不断地分析和改进,提高生产效率和质量。
精益思维和精益生产系统

精益思维和精益生产系统简介精益思维和精益生产系统是一种管理方法和生产方式,旨在通过最小化浪费和优化价值流程来提高效率和质量。
本文将介绍精益思维和精益生产系统的定义、原则、工具和实施步骤。
精益思维的定义和原则精益思维是一种注重持续改进和创造价值的思维方式。
其核心原则是消除浪费,包括过度生产、库存、运输、等待、过度加工、不合格品和运动。
精益思维强调不断优化价值流程,使价值流可以顺畅流动而不受阻碍。
以下是精益思维的几个关键原则:1.客户价值:关注客户需求,提供对客户有价值的产品或服务。
2.价值流:分析和优化从原材料到最终产品或服务交付的所有过程。
3.流程改进:通过消除浪费和不必要的环节,优化流程效率。
4.拉动生产:基于客户需求进行生产,避免过度生产和库存。
5.持续改进:通过持续追求更高效率和更好质量,实现持续改进。
精益生产系统的定义和原则精益生产系统是将精益思维应用到生产过程中的综合管理方法。
它旨在通过优化价值流程、减少浪费和提高质量来提高生产效率。
精益生产系统的核心原则包括:1.价值流映射:绘制和分析产品或服务的整个价值流程,找出潜在的浪费和瓶颈。
2.流程改进:通过消除浪费和优化流程,降低生产成本和提高质量。
3.一体化生产:在生产过程中实现不同环节的协调和同步,避免过度生产或不足生产。
4.快速反应:及时响应市场需求的变化,尽可能缩短产品开发和交付周期。
5.持续改进:通过标准化工作和持续的培训,不断改进生产效率和质量。
精益工具和方法精益生产系统使用了多种工具和方法来实现流程改进和持续改进的目标。
以下是一些常用的精益工具和方法:1.5S:用于组织和管理工作区域,包括整理、整顿、清扫、标准化和维护。
2.价值流映射:绘制和分析产品或服务的整个价值流程,发现浪费和瓶颈。
3.一次性流程设计:通过重新设计流程,减少浪费和不必要的环节。
4.精益生产看板:用于可视化生产信息和进度,实时监控生产状况。
5.Kaizen:持续改进的方法,通过小步改进和团队合作来提高效率和质量。
3P精益设计

成本 降低的 = 价值观
1 成本
功能 3P价值观 =
成本
3P和JIT
战略精益 系统精益
3P系统致力于建立精益生产体系. 是一个对制造过程中各 种浪费零容忍的系统.
The 3P系统通过整合JIT理念来设计生产过程以实现这个 目标:
• 符合节拍( takt time) • 实现流动生产 • 整合拉动系统
为什么3P?
战略精益 系统精益
3P 流程是精益产品开发和资本审核的关键步骤:
• 降低设备开发到投产的周期 • 减少设备投资 • 降低设备运行成本 • 提高盈利能力
什么时候进行3P?
战略精益 系统精益
3P系统应该应用于生产环境发生重大变化的时候,例如:
•新产品导入 (NPI) •产品设计变更 •客户需求量急剧变化 •流程的转移 以及 •获批进行新投资 •由批量生产转为单件流的时候
利润 =售价-成本
在整个系统内降低成本,着眼于:
• 品质 •不流出次品 •足够的工序能力
• 产量 •对产能需求反映迅速 •所有工序都有目标产能
• 时间 •生产时间短,开发周期短 •生产均衡能力 (EPE* Day)
• 成本 •投资成本低 •运营成本低
3P的影响
战略精益 系统精益
细胞 (Cell) 生产线案例 • 制造设备成本节省 $200万, 原料存货量由8周降低为1周
战略精益 系统精益
Day 3
Day 4
七种设计评估
全尺寸模型制 作及操作模拟
模拟, 改进, 记录,选择 并决定设计 方案
完成工序一 览表
Day 5
跟进计划 执行计划 发布会 结束会
每日项目检讨 每日项目检讨 每日项目检讨 管理层现场视察
JIT

需 物 料却 还 没 准备 好 。J I T 系 统 实施 后 ,系统 根据 现场 生产 节拍 、发 动机 实 际工位 、线边 库存 、物 料预 定义 配送频
次 、工 艺路线 、工作 时间表 白动 产生按
J I T系统实施 前 ,当排产 /上 线发
动 机 因市 场变 化进 行调 整后 ,需要 人工
应用范围:
时生产系 统 ,简称 J I T系统 。 基本 思
想 是:只在需要的时候 、按需要的量、生 产 所 需的产 品 ( 适 品・ 适量・ 适 时)。反
包含 所有 生产线 供应 商 一库 房缓 冲 区、库房 一装配 、供应商 一装配 的 J I T 实时物料拉动 。 J I T系统设 计方 案
装机物料需求 ,实现装配 一 库房 ,装配 一
供 应商之 间的物 料 电子 实时拉动 ,提 高 物料配 送 的准 确性 、及 时性 、效率 ,降
什 么是 J I T系统 ?
J u s t I n T i m e ,准时生产 ,又译实
低 线 边 库存 ,改 善装 配 车 间物 流环 境 。
升 级 外 ,大部 分零 件 都 与原 NT8 5 5发
动机 通用 。 ● 整机 匹配继 承 性好
CE L E C T燃 油系统 .对燃 油的 品质要 求
不高。 目前 QSN T已经 为数 家 OE M 完成
OS N T发动机 与原 N T 8 5 5发动机的 外 观 尺 寸 差 别 不 大 .用 户 接 1 3尺 寸 也 保 持 一致 .OEM 在不 进 行较 大 改动 的
供应 商及 时知道 现场 物料 状况 及未 来物 料预计消耗,及时补料 、备料 ,满足现场 装机需求。供应商发货后,系统在 E R P自
汽车公司精益生产案例后拉动式系统看板设计案例

后拉动式系统看板设计案例第一章. 企业介绍企业概述某某公司致力于汽车座椅滑轨、角调、升高器、旋转机构、减震机构等调节机构的研发、制造和销售,同时承接其它行业冲压、焊接件的模、夹具开发和产品制造。
人人是老师人人是学生第一章. 企业介绍客户主要的国内客户有东风雪铁龙、比亚迪、东风轿车、奇瑞汽车、江淮汽车、南京依维柯、宇通客车、一汽解放、济南重汽、福田汽车、三一重工等;国外客户有沃尔沃、卡特彼勒、小松、日立、尼桑等。
人人是老师人人是学生第一章. 企业介绍市场特征该生产部门所生产的产品属于汽车产品的零件,它靠近供应链的上游,根据牛鞭效应的理论,它在需求上的波动将会远大于下游直接供应整机的厂商。
人人是老师人人是学生第一章. 企业介绍目前,下游厂商的订单主要采取以下几种方式给出:1)合约订单:两阶段转拨,未定交期,直到客户提调才算完成交易2)一般订单:是正式订单,只能由交易管理部门录入,临时性较强3)Email订单:由生产管理人员录入成为合约订单,需无条件满足人人是老师人人是学生人人是老师人人是学生企业当前采取按计划生产的方式,由企业生产管理部门按月指定生产计划,下发各部门,再由各工序的生产管理人员制定周生产计划,下发各产线,各产线根据生产计划完成生产。
生产特征第一章. 企业介绍第一章. 企业介绍当前企业在生产调控方面面临很大的难题,主要原因在于合约订单。
合约订单由于是按预测进行生产,如果预测与实际的需求有较大的出入,则客户有权延迟提货时间,甚至在市场波动过大时直接取消订单。
这样,就有可能造成完成生产的产品在库房中呆滞数月甚至数年,情况严重时还可能成为找不到买家的废品。
人人是老师人人是学生第一章. 企业介绍由于上述问题的存在,该企业目前致力于推行后拉式生产方式,希望采用拉动的生产方式替代现有的按计划生产的方式,降低在制品库存,缩短生产提前期,以求更好的应对市场需求变化,减少生产中的浪费和不必要的损失。
人人是老师人人是学生生产结构该生产部门包括冲压、电镀、成型和装配下。
精益生产计划PPT课件
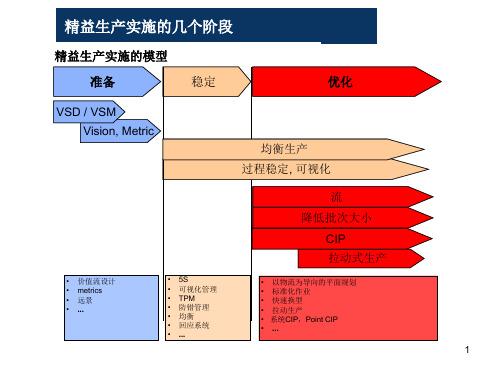
持续改进/CIP • 持续改进价值流并标准化工作流程
4
实施
优化阶段
优化
拉动式生产 • 目标是因工序同步化而形成流动。只有当流动无法进行时才采用拉
动原则 • 焦点是看板的引入:
在制品库存 = 周期需求 * 补充前置期 * (1+alpha) 安全系素 (波动) alpha < 1 补充前置期 < 1 天 根据日常工作经验来核查数据 • 在价值流中(逐步)引入看板
• 以物流为导向的平面规划 • 标准化作业 • 快速换型 • 拉动生产 • 系统CIP,Point CIP
• ...
1
实施 准备
准备阶段
• 利用VSM/VSD创建试点区域的远景 • 由远景得出全局平面规划和物流概念 • 定义 目标追踪的metrics • 根据阶段性模型创建实施计划 • 为主要衡量参数确定点对点的益生产实施的模型
准备
稳定
优化
VSD / VSM Vision, Metric
均衡生产 过程稳定, 可视化
流 降低批次大小
CIP 拉动式生产
• 价值流设计 • metrics • 远景 • ...
• 5S • 可视化管理
• TPM • 防错管理 • 均衡 • 回应系统
• ...
2
实施
稳定阶段
稳定
均衡生产 • 从最初阶段开始的根据客户需求的价值流 • 产量和类型的均衡(A,B,C-产品) • 生产序列标准化,生产稳定化 工艺稳定化 • 增强设备和零件的利用率 (OEE) • 标准、偏差、改善措施可视化
3
实施
优化阶段
优化
流 • 工序同步化,形成流动(平面规划的改变) 批次减小 • 减少工装切换时间,增加工装切换频次,启动pacemaker工艺
智能生产调度系统设计与开发

智能生产调度系统设计与开发随着工业化进程的不断推进和科技的不断进步,生产制造行业也在向智能化、信息化、自动化的方向不断发展。
为了实现生产制造的高效性和智能化,工厂需要采用智能生产调度系统。
智能生产调度系统可以对现场生产的人员、工艺、设备、原材料进行优化调度和控制,实现生产过程的快速响应、自适应和灵活性。
本文将介绍智能生产调度系统的设计与开发。
一、智能生产调度系统的基本结构智能生产调度系统是基于计算机及计算机网络技术,利用先进的调度算法,将多个生产资源进行整合和调度,协调各个环节,提高生产效率和生产质量。
其基本结构原理如下图所示:图一:智能生产调度系统基本结构智能生产调度系统基本结构包括采集、监控、处理、决策和执行五个部分。
其中,采集部分主要负责采集现场生产所需的各种数据,如设备状态、产线负荷、人员出勤情况等;监控部分用于监测生产状态及变化,通过实时监测,将生产数据发送给处理部分;处理部分是核心部分,实行调度与优化算法,并制定优化策略;决策部分从处理部分接收优化方案并进行决策,将调度方案反馈给执行部分进行执行。
二、智能生产调度系统的功能智能生产调度系统可以对生产过程进行跟踪、监测、数据录入和分析,实现以下功能:1. 设备调度功能:自动调度并平衡多台生产设备;2. 生产计划排产功能:通过预测和分析市场需求、生产能力及资源情况等因素,精确合理地安排生产计划和生产进度;3. 生产现场作业调度:优化生产过程,调整生产顺序、生产时间、生产工艺等,提高生产效率和效益;4. 生产质量控制:实现生产质量的监控和检测,提高产品质量可靠性;5. 生产数据分析:可以对生产数据进行分析和处理,为工厂的生产管理决策提供重要参考依据。
三、智能生产调度系统的开发应用智能生产调度系统可以采用多种技术集成,如物联网技术、大数据分析技术、云计算技术等,构建可靠、高效、灵活的生产制造流程。
在实际应用中,应制定一套完整的系统开发和应用方案,如下图所示:图二:智能生产调度系统应用开发方案智能生产调度系统的应用开发可分为三个主要步骤:1. 确定系统需求:根据工厂的具体情况和需求,确定系统的功能设计和开发目标。
准时化生产方式与精益生产方式
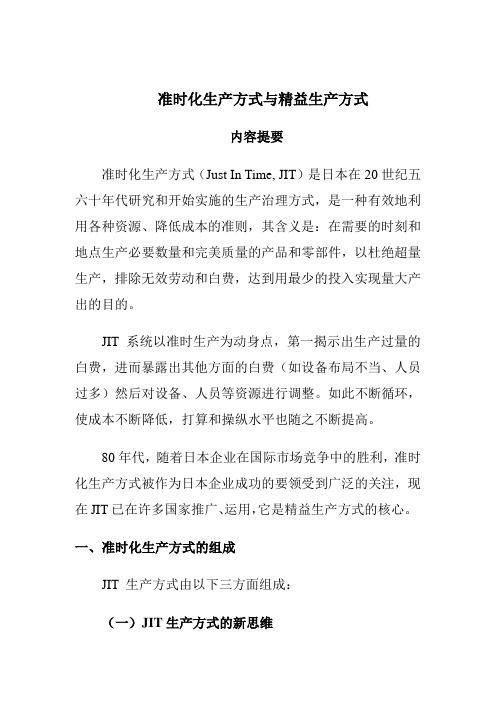
准时化生产方式与精益生产方式内容提要准时化生产方式(Just In Time, JIT)是日本在20世纪五六十年代研究和开始实施的生产治理方式,是一种有效地利用各种资源、降低成本的准则,其含义是:在需要的时刻和地点生产必要数量和完美质量的产品和零部件,以杜绝超量生产,排除无效劳动和白费,达到用最少的投入实现量大产出的目的。
JIT系统以准时生产为动身点,第一揭示出生产过量的白费,进而暴露出其他方面的白费(如设备布局不当、人员过多)然后对设备、人员等资源进行调整。
如此不断循环,使成本不断降低,打算和操纵水平也随之不断提高。
80年代,随着日本企业在国际市场竞争中的胜利,准时化生产方式被作为日本企业成功的要领受到广泛的关注,现在JIT已在许多国家推广、运用,它是精益生产方式的核心。
一、准时化生产方式的组成JIT 生产方式由以下三方面组成:(一)JIT生产方式的新思维JIT之因此成功,第一是由于它大胆地向传统治理观念提出了挑战,使得生产治理的观念发生了庞大的变化。
JIT 生产方式的新思维是JIT最差不多的方面。
(二)JIT生产系统设计与打算技术为达到准时生产、杜绝白费、合理利用资源,在JIT系统中要进行广义的生产系统设计。
JIT生产系统设计与打算技术表达JIT的新思维,同时为JIT的生产现场治理与操纵打下基础。
(三)JIT生产现场治理JIT的零部件权当后续工序提出要求时才生产,是一种“拉动”的生产方式,后工序需要多少,前工序就生产或供应多少。
它将传统生产过程中前道工序向后工序送货,改为后道工序依照“看板”向前道工序取货。
看板系统是JIT生产现场操纵技术的核心。
二、准时生产的目标JIT方式的目标是完全排除无效劳动造成的白费。
用专业化的术语来讲明,JIT寻求达到以下目标:(1)废品量最低(零废品);(2)预备时刻最短(零预备时刻);(3)库存量最低(零库存);(4)搬运量最低;(5)机器损坏率低;(6)生产提早期短;(7)批量小。
精益生产线设计方法

精益生产线设计方法1.引言1.1 概述精益生产线设计方法是一种旨在优化生产效率和降低成本的方法。
它通过精确分析和整合各个生产环节,以消除浪费、减少不必要的工序和资源的使用,从而实现高效、灵活和可持续的生产流程。
在传统的生产线设计中,往往存在着生产节拍不均匀、库存过高、产品质量不稳定等问题。
而精益生产线设计方法则致力于解决这些问题,以实现高质量、低成本和快速交付的目标。
精益生产线设计方法的核心理念是“精益”,即通过深入研究和理解现有生产线的各个环节,找出并消除非价值增加的工序,最大限度地减少浪费,提高生产效率。
这一方法强调对生产过程的持续改进和不断学习,以追求最佳的生产效果。
在实施精益生产线设计方法时,关键步骤包括价值流分析、工序优化、拉动生产等。
通过对价值流进行深入分析,可以找出生产线上的瓶颈和浪费点,从而有针对性地进行优化和改进。
而拉动生产则是指根据实际需求来控制生产节奏和产量,以减少库存和提高交付速度。
总之,精益生产线设计方法是一种以提高生产效率和质量为目标的方法。
它通过深入分析和优化生产线的各个环节,消除浪费和提高效率,从而实现高效、灵活和可持续的生产过程。
随着企业对效率和质量要求的不断提高,精益生产线设计方法将在未来得到更广泛的应用和发展。
1.2文章结构1.2 文章结构本文主要介绍了精益生产线设计方法,旨在帮助读者了解该方法的基本原理和关键步骤,并总结了其在生产线设计中的优势。
文章结构如下:第二部分为正文部分,主要分为两个小节。
首先,我们将介绍精益生产线设计方法的基本原理,包括其核心理念和基本概念。
其次,我们将详细讲解精益生产线设计方法的关键步骤,包括需求分析、价值流分析、布局设计、设备选择和安装、人员培训等。
最后一部分为结论部分,我们将对精益生产线设计方法的优势进行总结,并展望其未来的发展趋势。
在总结中,我们将强调精益生产线设计方法能够有效地提高生产线的效率和质量,并降低成本和浪费。
在展望中,我们将探讨如何进一步推动精益生产线设计方法的发展,以适应不断变化的市场需求和技术创新的挑战。
精益生产系统设计及改进方案
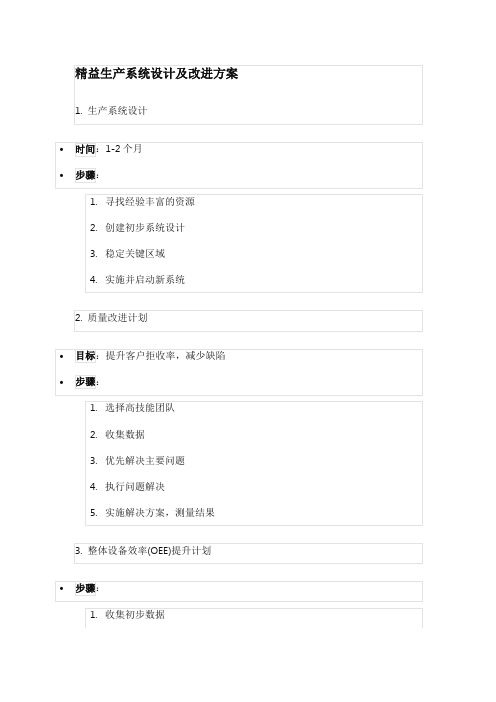
• 步骤: 1. 收集初步数据
2. 选择改进方法和目标 3. 实施改进措施 4. 测量结果
4. 改善计划(Kaizen)
• 目标:改善劳动生产力 • 步骤:
1. 选择目标区域 2. 进行 Kaizen 活动 3. 实施新方法 4. 推广到其他车间
5. 排程计划
• 目标:设计拉动式排程系统 • 步骤:
ห้องสมุดไป่ตู้
精益生产系统设计及改进方案
1. 生产系统设计
• 时间:1-2 个月 • 步骤:
1. 寻找经验丰富的资源 2. 创建初步系统设计 3. 稳定关键区域 4. 实施并启动新系统
2. 质量改进计划
• 目标:提升客户拒收率,减少缺陷 • 步骤:
1. 选择高技能团队 2. 收集数据 3. 优先解决主要问题 4. 执行问题解决 5. 实施解决方案,测量结果
细节解读:
• 实施与持续支持: • 制定持续支持计划 • 周期性"健康检查" • 审核流程
• 管理与反馈: • 强化高层管理参与 • 建立关键绩效指标(KPIs) • 实施绩效管理系统
应用工具:
• 5S
• 可视化管理工具 • 标准化工作 • 问题解决工具(如 5 Whys,鱼骨图) • 拉动系统工具(如看板系统)
1. 开发系统设计 2. 试行平衡排程 3. 开发拉动系统 4. 推广到供应商
6. 视觉性能改进
• 目标:通过视觉管理提升性能
• 步骤: 1. 安装大型显示屏 2. 收集并优先处理问题 3. 建立绩效回顾机制
7. 组织/能力建设
• 目标:建立支持结构,提升基础能力 • 步骤:
1. 培训基础 Lean 概念 2. 资源投入 3. 流程稳定性建设
精益生产七大要素管理-20220228145305

精益生产七大要素管理精益生产是一种以提高效率、降低成本和提升产品质量为核心的生产方式。
它强调通过消除浪费、持续改进和员工参与来实现生产过程的优化。
为了有效地实施精益生产,需要关注七个关键要素,这些要素共同构成了精益生产的基础。
本文将详细介绍这七个要素,并探讨如何通过管理这些要素来提高生产效率和产品质量。
一、价值价值是精益生产的核心概念,它指的是满足客户需求的产品或服务。
在精益生产中,价值是通过客户的需求来定义的,而不是由生产者或供应商来决定。
因此,了解客户需求是精益生产的第一步。
企业需要通过市场调研、客户反馈等方式来收集客户需求信息,以便更好地满足客户的需求。
二、价值流价值流是指产品从原材料到最终成品的生产过程。
在精益生产中,价值流是连续的,没有中断或浪费。
为了实现价值流的连续性,企业需要识别和消除生产过程中的浪费,包括过度生产、等待、运输、库存、动作、过度加工和缺陷等。
通过消除这些浪费,可以提高生产效率,降低成本,并提高产品质量。
三、拉动拉动是指按照客户需求来生产产品,而不是按照生产计划来生产产品。
在精益生产中,拉动是通过看板系统来实现的。
看板系统是一种信息传递工具,它可以帮助企业实时了解客户需求,并按照客户需求来生产产品。
通过拉动,企业可以减少库存,降低成本,并提高生产效率。
四、流动流动是指产品在生产过程中不断地移动,而不是停滞不前。
在精益生产中,流动是通过生产线的平衡来实现的。
生产线平衡是指通过调整生产线上的工作流程,使得每个工人的工作负荷相对均衡,从而实现生产线的连续流动。
通过流动,可以提高生产效率,降低成本,并提高产品质量。
五、拉动系统拉动系统是指通过拉动来实现生产过程的优化。
在精益生产中,拉动系统是通过看板系统和生产线的平衡来实现的。
看板系统可以帮助企业实时了解客户需求,并按照客户需求来生产产品。
生产线的平衡可以帮助企业实现生产线的连续流动,从而提高生产效率,降低成本,并提高产品质量。
- 1、下载文档前请自行甄别文档内容的完整性,平台不提供额外的编辑、内容补充、找答案等附加服务。
- 2、"仅部分预览"的文档,不可在线预览部分如存在完整性等问题,可反馈申请退款(可完整预览的文档不适用该条件!)。
- 3、如文档侵犯您的权益,请联系客服反馈,我们会尽快为您处理(人工客服工作时间:9:00-18:30)。
A B C D E F 新的产品 G H
供应商工厂
上游流程补充取走的产品
拉动 需要的零件
顾客工厂
拉动系统 –“内部”
谢谢
前面的流程
Press
我可以取走 一些零件吗?
冲压超市
后面的流程 成品存储
精益价值流的特征
• 连续流动
工序 1, 2, 3
1
2
3
• 超市拉动系统
INV 非增值库存
生产看板
供应流程 1, 2, 3
供应信息
零件信息
仓库B
原材料代码 T45GG00 原材料箱# 箱 – 19-36
零件# 52107
描述 钛
数量 500lbs/skid
顾客信息
用户工序 普里马单元
存放位置 C-12 看板# / 日期 #4/5 3/12/02
• 零件 • 数量 • 它来自哪里 • 它去哪里 • 是否需要条形码 • 看板卡号
例子:计算生产看板数量
K(p)
混合/质检/填充
1
2
3
连续流
K(w) 发货站台
需求= 21 单位/天
(1 班)
D (P) K(p) =
Q
1 天 = 480分钟 容器(Q) = 3 单位 生产循环时间 (1) = 17 分钟/单位 切换时间(1)=6 分钟, 每2单位切换 生产循环时间(2) = 20 分钟/单位 生产循环时间 (3) = 20 分钟/单位 在(1)和(2)以及(2)和(3)之间允许1个单位的在制品(忽略安全库存) 需要多少生产看板?
76000BDF40 钛
39 “
当生产分批时使用 重新订货或触发
批量 大小
生产轮 我在触发点位置吗?
叠放板
Lot Size
制造
生产看板
在生产轮中,我开始生产了吗?
取货看板
看板的许多类型
零件 1#1066
零件 # 11023 数量.= 50
(卡片) 描述CY: HOUSING RH
颜色:
数量3:0
1
2
3
超市
工序 4
INV 非增值库存
取货看板 顾客流程 4
看板的好处
• 消除过量生产 • 有助于简化取货流程 • 以可视化方式整合供应流程在一起 • 暴露隐藏在系统中的浪费 • 迫使我们准确了解系统何时、为什么需要多少库存
看板
看板类型
运输看板 批准物料移动
生产看板 批准生产
供应商看板
给供应商的订单
装配流程
生产看板
装载均衡箱
Part 8:00 8:15 9:15 9:30 9:45 8:30 8:45 9:00 10:00 10:15 10:30
Part # KJ-467
基于发货计划放入看板
拉动零件 到装配
Gravity fed Store
发送到码头
停止生产 必须补充
汇报结束 谢谢大家!
请各位批评指正
在你的未来价值流图中建立流动
• 方针3:在连续流不能扩展到上游的地方利用拉动 系统控制 – 在价值流中总有不可能连续流动、必须批量的地方 – 不要由独立的计划部门来计划这些过程。 – 通过拉动系统来联系它们 – 在连续流动被中断的地方,以及必须以批量模式运行的上游流程建立拉动系统
传统系统的基本问题
拉动系统 定义 : • 仅仅按使用需要生产,或替代已经使用的东西. • 在材料控制中,由使用工序按需求提取库存。直到用户来了信号才能分发材料.
APICS Dictionary, 7th Edition
拉动系统影响反馈
供应商 (上道工序)
物流“拉动”
生产工序
物流“拉动”
顾客
(下道工序)
“我需要零部件来替换用完的”
过量生产
工序 1
INV 非增值库存
工序 2
INV 非增值库存
工序3
过量生产造成哪些浪费?
处理 存储空间 短缺 关键能力
物流/畅通 库存搬运成本 反馈变慢 交货期加长
推动系统
我们怎样识别推动系统?
计划
MRPII
工序 1
INV 非增值库存
工序2
工序 3 INV 非增值库存
我们生产许多的产品…… 但我们仍然超过或丢失顾客的订单
供应商 超市
混合/磨
FIFO
稀释和调色 FIFO
流动
你把计划放在哪里以控制顺序?
填充
三角看板箱-浇注工艺
模制品存放
为什么要均衡生产?
• 平滑对上游作业的需求 • 拉动系统的基础 • 库存最小化 • 最好地利用资源 • 建立满足需求变化的最大柔性
均衡/稳定的计划
• 装载均衡箱用于均衡看板取货 • 从零部件区域拉动 • 装配到补充存储
• 零件 • 订货数量 • 供应商(它从哪里来) • 接收区域(它去哪里) • 存储位置 • 触发 • 是否需要条形码 • 看板卡数量 • 卡丢失的帮助说明
生产看板
上道工序 卷形物装饰
到 卷形物装饰超市
零件 #
76000BDF40 钛 白 39英寸宽
超市位置
条形码
M-4-B 容器
76000BDF40 钛 看板的#
例子:计算生产看板数量
K(p)
混合/质检/填充
1
2
3
连续流
K(w) 发货站台
需求= 21 单位/天
(1 班)
D (P) K(p) =
Q
1 天 = 480 分钟 容器(Q) = 3 单位 生产循环时间(1) = 17 分钟/单位 切换时间 (1)=6 分钟, 每2单位切换 生产循环时间(2) = 20 分钟/单位 生产循环时间(3) = 20 分钟/单位 在(1)和(2)以及(2)和(3)之间允许1个单位
卷
2/4
容器大小
3000 平方英尺
• 零件号 • 要生产的数量 • 供应工序(从哪里来) • 接收区域(它到哪里去) • 存放区域 • 是否需要条形码 • 看板卡号
分批生产时使用信号看板
生产看板
三角(分批)看板
批量大小 5卷
零件# 76000BDF40
重新订货点 2卷
卷涂层
卷切口
超市位置 M-4-B
“我需要产品”
仅仅当顾客有需求信号时物料才流动
拉动系统象救火队
何时使用拉动系统
• 带切换的工序流程、进行高产量的多品种生产 • 工艺流程的循环时间有很大不同 • 因为距离远,流程之间脱节了 • 工艺流程不可靠 • 流程交货期长
简化的拉动系统 下游流程在需要时取走所需要的产品
空箱 +生产看板
空箱 + 取货看板
取货看板
工序间的物料移动
生产看板
不要求切换的工序
信号看板
要求切换的工序
超市拉动系统
生产看板
看板
取货看板
供应工序
A
产品
产品
超市
1. 顾客工序(B)在需要时走到超市并取走需要的产品 2. 供应工序(A)生产补充取走的产品 3. 目的:不需要计划来控制供应工序的生产。控制流动之间的生产。
顾客工序 B
看板-“卡”或“标牌”
看板数量计算
看板数量(最大)
D (LT)
式中: K=看板数量
K= Q
+ 安全库存
D=需求(消耗率或顾客需求数率)
LT (交货期)=生产交货期(P) + 运输时间 (C)
Q=标准容器的大小
安全库存=应付顾客变化、切换时间、停机时间、取走批量大小的货等的缓冲
例子:计算取货看板数量
流转时间
箱中等待=32 分钟 移动超市=52 分钟 移动到装配=60 分钟 等待装配使用看板并放到箱中=48 分
的在制品(忽略安全库存)
平均循环时间=20分钟 总的生产交货时间 = 第一件60分钟 +第二件20
分钟+第三件20分钟 = 100 分钟
K(p) = (21* (100 / 480))/ 3 = 1.5 -> 2
系统中总的WIP的最大允许数量 瓶颈移动时,预防过量生产的方法
先进现出通道应对在制品
停
M1A3CHINE
Z3ONE TIME NEEDED
1
RPROEEOOSIRRTDD:IOEENRR: POINT
5 2
963170411812
(推车)
1
2
3
(货盘)
与超市有关的图标:
取货(拉动箭头) 生产看板 取货看板 超市
看板分批到达 看板箱位置
信号看板
看板规则
• 下游工序从上游工序取货 • 上游工序仅仅生产下游工序取走的货 • 100%无缺陷品送到下游 • 必须建立均衡生产 • 看板总是伴随物料或产品 • 看板的数量应该随时间逐步减少
3.
ASSOC/DAT
E/SHIFT JE
12/20/95 1st
GOLD Desc
NU1T0S Lroipti
0 pcs.Trti on TRo2tuenggSe iz sTTi4om0t r e eesec.
PA5RN3TU42M0 BER RDQHEU1SF5AC-SNRETIPRITTIEIYOSNPRIV SVS
钟
总流转时间 = 192 分钟
K(w) 发运到顾客
需求= 21 单位/天
(1 班)
计划
D (C) K(w) =
Q
1 天 = 480分钟 容器(Q) = 3 单位 转运 (C)=192 分钟/480 分钟/天= .4 天 (忽略安全库存) 那么, K(w)= (21 * .4)/ 3 = 2.8 取货看板, 圆整: K(w) = 3 看板