阴极电弧离子镀膜 cathodic vacuum Arc processing
阴极电弧离子镀原理
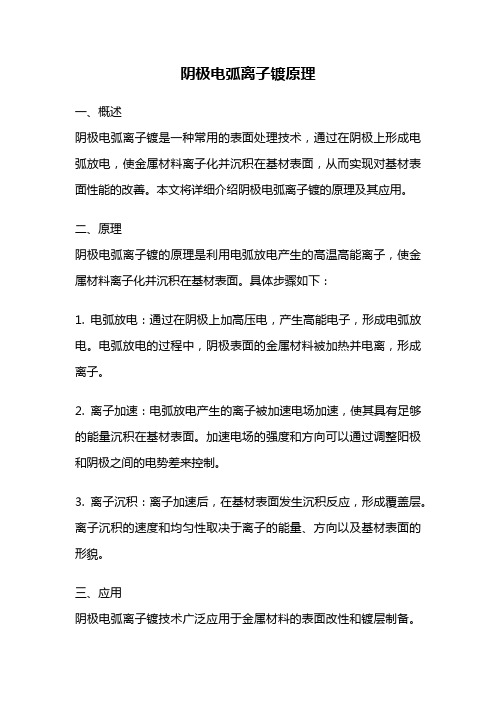
阴极电弧离子镀原理一、概述阴极电弧离子镀是一种常用的表面处理技术,通过在阴极上形成电弧放电,使金属材料离子化并沉积在基材表面,从而实现对基材表面性能的改善。
本文将详细介绍阴极电弧离子镀的原理及其应用。
二、原理阴极电弧离子镀的原理是利用电弧放电产生的高温高能离子,使金属材料离子化并沉积在基材表面。
具体步骤如下:1. 电弧放电:通过在阴极上加高压电,产生高能电子,形成电弧放电。
电弧放电的过程中,阴极表面的金属材料被加热并电离,形成离子。
2. 离子加速:电弧放电产生的离子被加速电场加速,使其具有足够的能量沉积在基材表面。
加速电场的强度和方向可以通过调整阳极和阴极之间的电势差来控制。
3. 离子沉积:离子加速后,在基材表面发生沉积反应,形成覆盖层。
离子沉积的速度和均匀性取决于离子的能量、方向以及基材表面的形貌。
三、应用阴极电弧离子镀技术广泛应用于金属材料的表面改性和镀层制备。
具体应用包括:1. 表面硬化:通过在金属基材表面沉积硬质合金或陶瓷材料,提高基材的硬度和耐磨性,延长使用寿命。
2. 防腐蚀:通过在金属基材表面镀上抗腐蚀性材料,提高基材的耐腐蚀性能,增加使用寿命。
3. 表面修复:对磨损或腐蚀的金属表面进行修复,使其恢复原有的功能和外观。
4. 金属涂层:在金属基材表面沉积金属涂层,如镍、铬、锌等,以改善金属表面的光泽度和装饰性能。
5. 功能涂层:在金属基材表面沉积具有特殊功能的涂层,如导电涂层、隔热涂层、抗反射涂层等,以满足不同的应用需求。
四、优势阴极电弧离子镀具有以下优势:1. 高效节能:离子镀过程中,离子的能量高、速度快,能够实现较高的沉积速率,提高生产效率。
2. 沉积均匀:通过调整加速电场的强度和方向,可以实现对离子沉积的控制,使得镀层均匀、致密。
3. 可控性强:通过控制电弧放电参数、加速电场参数和基材表面的预处理,可以实现对镀层性能的调控。
4. 适应性广:阴极电弧离子镀可用于多种金属材料和非金属材料的镀层制备,对于复杂形状的基材也具有良好的适应性。
阴极电弧离子镀原理

阴极电弧离子镀原理
阴极电弧离子镀是一种先进的表面处理技术,通过在真空环境下利用高能离子束对工件表面进行镀膜,以提高其硬度、耐磨性和耐腐蚀性。
这种技术在航空航天、汽车制造、电子设备等领域得到广泛应用,为产品的性能提升和功能改进提供了重要支持。
阴极电弧离子镀的原理基于电弧放电和离子轰击效应。
首先,在真空室中建立一定的真空度,然后通过阳极和阴极之间的电弧放电产生高温高能离子束。
这些离子束在电场的作用下加速并轰击到工件表面,造成表面原子的脱落和混合,最终形成均匀致密的镀层。
在镀膜过程中,离子束的能量和流量是影响镀层性能的重要因素。
能量越高,离子束对工件表面的轰击力越大,可以提高镀层的结合力和致密性;而流量越大,可以加快镀层的生长速度,提高生产效率。
因此,在实际应用中需要根据工件材料和要求进行合理的参数设置,以获得最佳的镀层效果。
除了镀层性能外,阴极电弧离子镀还具有环保和节能的优势。
相比传统的镀铬等表面处理方法,阴极电弧离子镀不需要使用有害的镀液和大量的水资源,减少了对环境的污染。
同时,由于镀膜过程在真空环境下进行,也减少了能源消耗,符合可持续发展的理念。
总的来说,阴极电弧离子镀作为一种先进的表面处理技术,具有显著的优势和广阔的应用前景。
通过不断的技术创新和工艺改进,相
信这项技术将在未来更多领域发挥重要作用,为产品的质量和性能提升提供有力支持。
真空阴极弧离子镀的发展及应用

真空阴极弧离子镀的发展及应用樊勇【摘要】叙述了真空阴极弧离子镀技术的原理,种类,宏观颗粒的产生以及磁过滤器的应用.重点分析了系统效率,等离子体传输影响因素和真空阴极电孤离子镀技术在薄膜研究和制造中的应用.【期刊名称】《新技术新工艺》【年(卷),期】2008(000)004【总页数】4页(P93-96)【关键词】真空阴极弧离子镀;磁过滤器;系统效率;等离子体传输【作者】樊勇【作者单位】上海汽车集团股份有限公司,乘用车分公司,制造工程部,上海,201804【正文语种】中文【中图分类】工业技术真空阴极弧离子镀的发展及应用樊勇 ( 上海汽车集团股份有限公司乘用车分公司制造工程部,上海 201804)摘要:叙述了真空阴极弧离子镀技术的原理,种类,宏观颗粒的产生以及磁过滤器的应用。
重点分析了系统效率,等离子体传输影响因素和真空阴极电弧离子镀技术在薄膜研究和制造中的应用。
关键词:真空阴极弧离子镀;磁过滤器;系统效率;等离子体传输中图分类号:TB43文献标志码:A真空阴极弧离子镀沉积技术是把真空弧光放电用于蒸发源的涂层技术,最早可以追溯到 1877 年,并且在 1892 年出现第一个专利申请¨- ,由美国Multi-Arc 公司和 Vac-Tec 公司研究开发,并且于 1981 年达到实用化,所以也被称为多弧离子镀或者真空弧光蒸镀技术心]。
在这一百多年里,真空阴极弧沉积技术已经得到迅速的发展并且被广泛应用于薄膜的制作上。
不同类型的真空阴极弧源被应用于金属膜,DLC膜,半导体膜,金属氧化膜和金属氮化膜等薄膜的制造上I3-4I真空阴极弧是一种典型的高电流(可高达数百安培)的电弧,电弧以等离子体的形式来传输阴极材料,而且离子电流约占弧电流的 10% 左右。
正因为如此,真空阴极弧具有极高的沉积速率‘ 5]阴极弧产生的离子具有极高的能量,约为 60 ~100eV ,这是其他沉积方法所不能比拟的。
具有高能量的离子对于提高膜基结合力和打乱膜的柱状晶结构是非常有利的,从而也可大幅度地改善膜的组织结构和力学性能。
磁控溅射和电弧离子镀技术和应用介绍
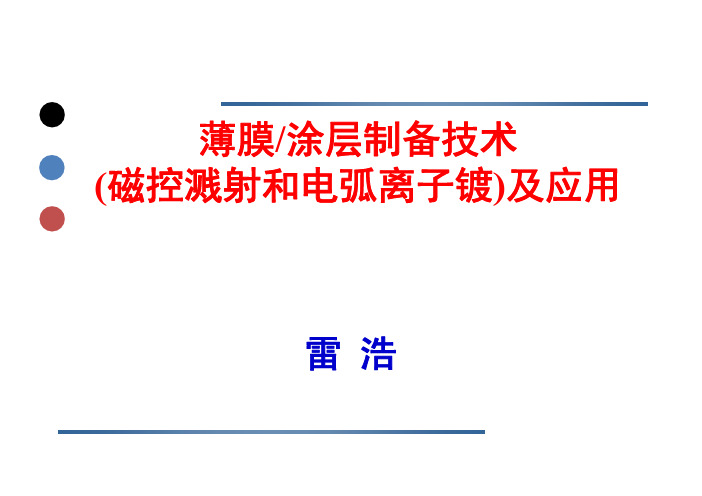
薄膜/涂层的概念与特点与分类
应用: 光学薄膜、微电子薄膜、光电子学薄膜、集成电路薄 膜、防护功能薄膜。 • 种类:
(1)以材料种类划分:金属、合金、陶瓷、半导体、化 合物、高分子薄膜等。 (2)以晶体结构划分:单晶 多晶 纳米晶 非晶 (2)以晶体结构划分:单晶、多晶、纳米晶、非晶 (3)以厚度划分:纳米薄膜,微米薄膜和厚膜。 ( )以薄膜组成结构划分 多层薄膜 梯度薄膜 复合 (4)以薄膜组成结构划分:多层薄膜,梯度薄膜,复合 薄膜。
TMF=0 G
TMF=10 G
TMF=20 G
TMF=30 G
弧 斑 尺 寸 TMF=0 G TMF=15 G TMF=30 G
弧 斑 速 度
轴对称磁场对弧斑运动的影响
电弧离子镀大颗粒问题的解决
电弧离子镀的改进 轴对称磁场
TMF=0 G TMF=15 G TMF=30 G
锥形坑
平整下凹
弧斑运动对靶材刻蚀利用率的影响
磁控溅射的应用 超硬涂层 磁控溅射的应用--超硬涂层
用TiN,TiC等超硬镀层涂覆刀具、模具等表面, 摩擦系数小,化学稳定性好,具有优良的耐热、 耐磨 抗氧化 耐冲击等性能 既可以提高刀具 耐磨、抗氧化、耐冲击等性能,既可以提高刀具、 模具等的工作特性 又可以提高使用寿命 一般 模具等的工作特性,又可以提高使用寿命,一般 可使刀具寿命提高3~10倍。
电弧离子镀大颗粒问题的解决
电弧离子镀的改进 动态拱形磁场
磁场位形
拱形磁场位形随电流比的变化
动态拱形磁场控制的离子镀弧源设计
电弧离子镀大颗粒问题的解决
永磁铁 电磁线圈
传统弧源(轴对称磁场)
俄罗斯弧源(纵向磁场)
静态 准静态磁场 静态/准静态磁场
FCVA镀膜及其应用

在中国缝制机械行业“十二五”时期主要技术攻关方向中,新材料、新工艺是一个重要领域。
在“十一五”期间的行业科技开发实施指南中,新材料、新工艺在产品中的开发与应用就已经是重要内容,主要体现在无油、微油润滑材料和特种材料涂覆工艺的应用与开发,通过在缝制机械的高速运转部件采用耐磨材料涂覆技术,实现无油或微油润滑。
材料及其涂覆工艺的发展与进步,对缝制机械的性能、品质的提升有积极的促进作用。
尤其在高速自动化缝纫机的品种和数量均大幅增加的情况下,如何通过新材料、新工艺的应用满足和提升高速自动化缝纫机的各项性能要求,是缝制机械制造商正在考虑的事情。
目前应用于缝制机械的新材料很多,比如多元填充高分子材料、陶瓷、金属钛、特氟龙、低温液态化油脂等。
而陶瓷、金刚石粉、钛合金、多元填充高分子材料等特种材料的涂覆工艺也在不断改进并且越来越多地应用于缝制机械中。
镀膜,是应用新的材料及新的涂覆工艺较多的一道工序。
已经有不少高速自动化缝纫机的零部件在镀膜时采用了新膜层材料和新镀膜方式。
我们知道,镀膜涉及两项基本内容,一是镀膜的技术与方法,二是所镀膜层的材料。
不同的镀膜方式,所达到的镀膜效果不同,膜层的性能发挥情况也随之有差异,而采用不同的镀层材料也有不同的性能表现。
1 不同的镀膜技术在微观环境下看,镀膜就是将一些物质(反应物)的分子、原子或者离子通过一定的方式被分解出来在其所具有的能量作用下涂覆(沉积)在需要镀膜的工件(基体)上。
镀膜时,要考虑膜层、工件材料的物理或化学性质,选择合适的镀膜方法将膜层紧紧地附着于工件上并且要产生好的性能效果。
真空镀膜技术就是在真空环境下,通过化学、物理方式将反应物或者靶材沉积到基体上的薄膜气相沉积技术。
镀膜通常需要在干净、纯粹的真空环境下进行,既为了避免污染(减少成膜过程中气体分子进入薄膜中成为杂质的量),也在于膜层材料的分子、原子化学性活跃,在常温常态下容易出现问题(比如分子间的碰撞、氧化反应)。
阴极电弧离子镀TiAlSiN涂层的高温抗氧化性能研究
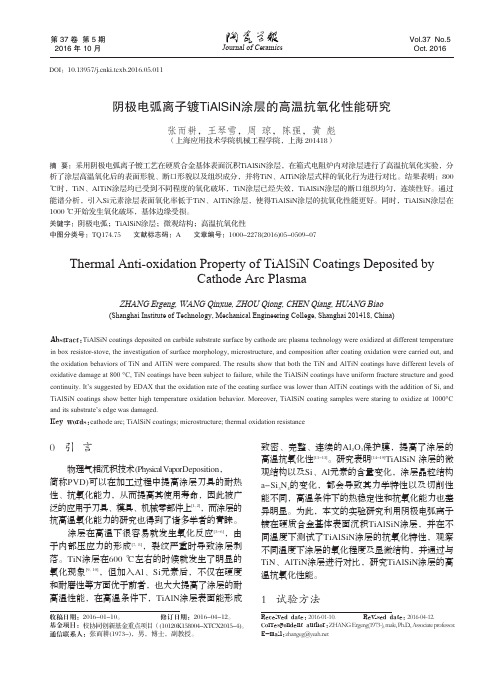
致密、完整、连续的Al 2O 3保护膜,提高了涂层的 高温抗氧化性[11-13]。研究表明[14-19]TiAlSiN 涂层的微 观结构以及Si、Al元素的含量变化,涂层晶粒结构 a-Si 3N 4的变化,都会导致其力学特性以及切削性 能不同,高温条件下的热稳定性和抗氧化能力也差 异明显。为此,本文的实验研究利用阴极电弧离子 镀在硬质合金基体表面沉积TiAlSiN涂层,并在不 同温度下测试了TiAlSiN涂层的抗氧化特性,观察 不同温度下涂层的氧化程度及显微结构,并通过与 TiN、AlTiN涂层进行对比,研究TiAlSiN涂层的高 温抗氧化性能。
(上海应用技术学院机械工程学院,上海 201418)
摘 要:采用阴极电弧离子镀工艺在硬质合金基体表面沉积TiAlSiN涂层,在箱式电阻炉内对涂层进行了高温抗氧化实验,分
Hale Waihona Puke 析了涂层高温氧化后的表面形貌、断口形貌以及组织成分,并将TiN、AlTiN涂层式样的氧化行为进行对比。结果表明:800 ℃时,TiN、AlTiN涂层均已受到不同程度的氧化破坏,TiN涂层已经失效,TiAlSiN涂层的断口组织均匀,连续性好。通过 能谱分析,引入Si元素涂层表面氧化率低于TiN、AlTiN涂层,使得TiAlSiN涂层的抗氧化性能更好。同时,TiAlSiN涂层在 1000 ℃开始发生氧化破坏,基体边缘受损。
in box resistor-stove, the investigation of surface morphology, microstructure, and composition after coating oxidation were carried out, and the oxidation behaviors of TiN and AlTiN were compared. The results show that both the TiN and AlTiN coatings have different levels of oxidative damage at 800 °C, TiN coatings have been subject to failure, while the TiAlSiN coatings have uniform fracture structure and good continuity. It’s suggested by EDAX that the oxidation rate of the coating surface was lower than AlTiN coatings with the addition of Si, and TiAlSiN coatings show better high temperature oxidation behavior. Moreover, TiAlSiN coating samples were staring to oxidize at 1000°C and its substrate’s edge was damaged.
阴极电弧离子镀膜 cathodic vacuum Arc processing
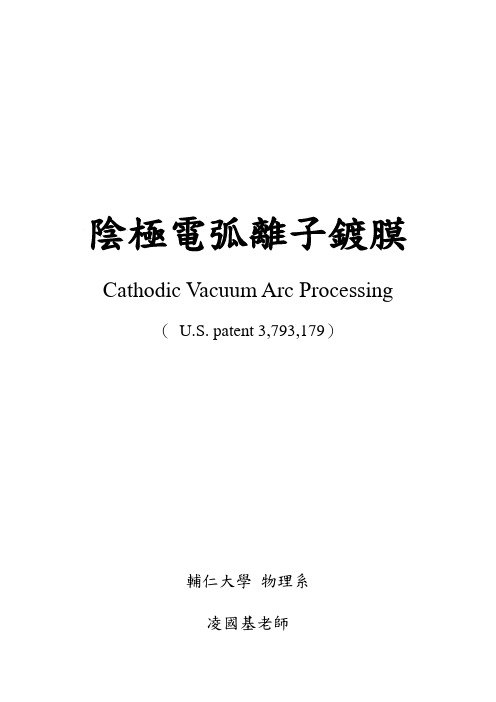
陰極電弧離子鍍膜Cathodic Vacuum Arc Processing (U.S. patent 3,793,179)輔仁大學物理系凌國基老師陰極電弧離子鍍膜一、前言1958年,Wore提出可以用Arc的方法來做鍍膜應用,一直到70年代初,才有4篇專利文章提出工業用的方法。
(1)Arc deposition and apparatus, U.S. patent No 3, 625, 848(1971)(2)Arc deposition and apparatus, U.S. patent No 3, 836, 415(1974)(3)Apparatus for vacuum evaporation of metals Under the action of an electric Arc, U.S.patent No 3, 783, 231(1974)(4)Apparatus for metal evaporation coating, U.S. patent No.3, 793, 179(1974) 到了70年代末期,USSR才有工業用途。
美國到了80年代中期,才有用Arc的方法在工具鋼上鍍TiN,增加硬度,延長工具鋼的壽命。
1.Cathodic vacuum arc processing的主要優點:(1)高度離子化。
(2)鍍膜速度快。
(3)黏著度較佳。
(4)Ti、N比例較佳,且較不會受N2分壓影響。
我們在鍍Ti、N時,最好是同一個比例上去,這個在電子槍中尤其難控制,陰極電弧離子鍍膜則是控制的特別好。
(5)基板溫度可以較低。
2.主要的缺點為:(1)陰極電弧離子鍍膜(cathode arc processing)最大的缺點為是微粒的產生(macro-particles)。
如圖一,大部份的macro-particles出現的角度約為10-20度。
From the cathode plane。
沉积气压对电弧离子镀制备MgO薄膜的结构及性能的影响

沉积气压对电弧离子镀制备MgO薄膜的结构及性能的影响朱道云;郑昌喜;王明东;陈弟虎;何振辉【摘要】采用阴极真空电弧离子沉积技术在玻璃及Si衬底上成功地制备了具有择优结晶取向的透明MgO薄膜。
利用X射线衍射仪(XRD)、扫描电子显微镜(SEM)及紫外-可见吸收光谱仪分别对MgO薄膜微观结构、表面形貌及可见光透过率进行了测试与分析。
XRD结果表明,所制备的MgO薄膜具有NaCl型立方结构的(100)、(110)和(111)3种结晶取向,在沉积气压为0.7~3.0Pa的范围内,薄膜的择优结晶取向随沉积气压的升高先由(100)转变为(110),最后变为(111)。
SEM图表明随着沉积气压的升高,MgO薄膜的晶%MgO thin films with preferred orientation and high optical transparence were prepared on the slide-glasses and Si substrates by the cathodic vacuum arc ion deposition.X-ray diffraction(XRD),scanning electron microscopy(SEM)and UV-visible spectrophotometer were used to investigate the influences of deposition pressure on the crystal structure,the morphology and the properties of MgO thin films,respectively.XRD patterns indicated that MgO thin films had a NaCl-type cubic structure and the film preferred orientation changed from(100) to(110) and then to(111) with the increase of the deposition pressure.SEM images showed that the grain size of MgO decreased with increasing the deposition pressure and the crystal quality also became poorer.The transmittances of MgO thin films decreased with deposition pressure and the film deposited at 0.7Pa had a higher transmittance which was more than 90% in the visible light range of 380-900nm.【期刊名称】《功能材料》【年(卷),期】2011(042)007【总页数】4页(P1316-1319)【关键词】阴极真空电弧离子沉积;沉积气压;MgO薄膜;等离子体显示板【作者】朱道云;郑昌喜;王明东;陈弟虎;何振辉【作者单位】广东工业大学实验教学部,广东广州510006;中山大学物理科学与工程技术学院,广东广州510275;中山大学物理科学与工程技术学院,广东广州510275;中山大学物理科学与工程技术学院,广东广州510275;中山大学物理科学与工程技术学院,广东广州510275【正文语种】中文【中图分类】TB43MgO薄膜由于具有较高的二次电子发射系数、较强的耐等离子体轰击能力及良好的电绝缘性能和高的可见光透过率,近年来已被成功地用作等离子体显示板(plasma display panel,PDP)的电极保护膜[1]。
阴极电弧离子镀原理

阴极电弧离子镀原理引言阴极电弧离子镀是一种常用的表面处理技术,可以在金属材料表面形成薄膜,改善材料的性能。
本文将从原理、设备、工艺流程和应用领域等方面对阴极电弧离子镀进行全面探讨。
原理阴极电弧离子镀是通过在真空环境中产生电弧放电,使得阳极材料形成离子,通过电场加速,使离子沉积在阴极材料表面的一种表面处理技术。
其主要原理如下: 1. 真空环境:创建真空环境有助于防止杂质的存在,保证沉积膜的纯度。
2. 电极材料:阳极和阴极材料分别选择不同的材料,以便在电弧放电过程中产生不同的离子。
3. 电弧放电:通过提供足够的电压和电流,在阳极和阴极之间形成电弧放电。
电弧产生瞬间高温、高压的条件,使阳极材料融化,并形成离子。
4. 离子加速:电场的作用下,离子受到加速,并沉积在阴极材料表面形成薄膜。
设备阴极电弧离子镀需要以下几种设备: 1. 真空装置:用于创建和维持真空环境,包括真空室、真空泵和管道等。
2. 电源:提供足够的电压和电流,以产生电弧放电。
3. 阳极和阴极:阳极和阴极材料需要选择合适的金属或合金,以产生需要的离子。
4. 控制系统:用于控制整个镀膜过程的参数,包括电弧放电条件、离子沉积速度和膜厚等。
工艺流程阴极电弧离子镀的工艺流程主要包括以下几个步骤: 1. 准备工作:清洁阴极表面,去除表面的杂质和氧化物,以保证表面的良好粘附性。
2. 真空抽气:将装置抽成一定的真空度,以消除空气对离子镀过程的干扰和污染。
3. 预处理:在真空环境中对阴极进行预处理,如加热、清洗或表面活化处理等,以提高表面的吸附性和离子镀的效果。
4. 电弧放电:通过提供足够的电压和电流,在阳极和阴极之间形成电弧放电,使阳极材料融化并形成离子。
5. 离子沉积:离子受到电场的加速作用,沉积在阴极材料表面,形成均匀的镀层。
6. 后处理:对镀层进行清洗、干燥和检验,以确保镀层质量和性能。
应用领域阴极电弧离子镀广泛应用于各个领域,主要包括以下几个方面: 1. 表面保护:阴极电弧离子镀可形成高质量的镀层,提高材料的防腐蚀性能,延长材料的使用寿命。
阴极电弧离子镀

阴极电弧离子镀阴极电弧离子镀是一种常见的表面处理技术,用于在材料表面形成一层均匀且致密的金属或合金镀层。
该技术利用电弧放电产生的高温高能量离子束,将金属离子沉积在工件表面,从而改变工件的物理和化学性质,提高其耐腐蚀性、硬度和抗磨损性能。
阴极电弧离子镀的过程可以简单描述为:首先,将工件作为阴极放置在电弧离子镀设备的真空室中;然后,在设备中加入金属材料作为阳极,并充入惰性气体,如氩气,以形成真空环境;接下来,通过加热阴极,产生电弧放电,使阳极材料蒸发,形成金属离子束;最后,金属离子在电场的作用下,沉积在工件表面,形成均匀致密的金属镀层。
阴极电弧离子镀技术具有以下几个优点:1. 高镀层质量:由于金属离子束的高能量和高速度,金属离子在沉积时具有较高的动能,可以有效地填充工件表面的凹陷和微孔,形成致密的金属镀层。
这种致密的镀层具有优异的耐腐蚀性和机械性能。
2. 宽镀层范围:阴极电弧离子镀技术适用于多种金属材料的镀层制备,包括铜、铬、镍、银等常见金属,也可以制备一些合金镀层,如钛合金、铝合金等。
同时,该技术还可以在非导电材料表面形成金属镀层,如塑料、陶瓷等。
3. 高镀层硬度:通过阴极电弧离子镀技术,可以获得高硬度的金属镀层,进一步提高工件的抗磨损性能。
这对于一些需要高耐磨性的零部件,如汽车发动机缸套、切削工具等,具有重要意义。
4. 高镀层均匀性:由于阴极电弧离子镀技术中金属离子的高速运动和扩散效应,可以实现较好的镀层均匀性。
这对于一些要求镀层厚度均匀的工件,如光学镜片、光学薄膜等,非常重要。
5. 环保节能:阴极电弧离子镀技术是一种真空镀膜技术,不会产生有害气体和废液,对环境无污染。
同时,由于在真空环境下进行,可以有效避免氧化反应,提高镀层的纯度和结晶度。
此外,该技术还可以实现自动化控制,提高生产效率。
阴极电弧离子镀技术在许多领域都有广泛的应用。
例如,电子器件制造中,常用于制备金属导电膜、光学薄膜和微电子元件等;在航空航天领域,常用于提高航空发动机的耐腐蚀性能和降低飞机表面的雷达反射率;在汽车制造中,常用于制备汽车发动机缸套、气门和座圈等;在医疗器械制造中,常用于提高医疗器械的生物相容性和耐腐蚀性能。
阴极真空电弧原理

1. 减少宏观颗粒的产生 阴极后部使用导向磁场控制阴极斑点的运动速度和运动轨迹, 阴极后部使用导向磁场控制阴极斑点的运动速度和运动轨迹, 当阴极斑点的运动速度加快, 当阴极斑点的运动速度加快,就可以降低熔池的尺寸从而降 低液态颗粒的尺寸。 低液态颗粒的尺寸。另外还有方法是调节阴极靶控制磁场使 得阴极斑点尽量分布在整个阴极表面, 得阴极斑点尽量分布在整个阴极表面,从而减小阴极斑点尺 达到降低液态颗粒尺寸的目的。 寸,达到降低液态颗粒尺寸的目的。 左右, 电弧中的正离子只占弧流的 10%左右,激发的电子电流占 左右 绝大多数。在轴向外磁场作用下,电子做离心圆周运动, 绝大多数。在轴向外磁场作用下,电子做离心圆周运动,因 此不断触碰阴极靶外延,重新引发新的电弧。 此不断触碰阴极靶外延,重新引发新的电弧。
3.四元涂层 四元涂层
TiCห้องสมุดไป่ตู้AlN,TiCrCN等。 , 等
4.纳米多层膜 纳米多层膜
C-C ,WC-CrAlN等。 等
2.阴极电弧的形成过程 2.阴极电弧的形成过程
阴极电弧是在低气压条件下( Pa) 阴极电弧是在低气压条件下(约102 Pa~10-5 Pa)阴阳极之间低电压高电 流的气体放电现象。 流的气体放电现象。 阴极电弧的稳定燃烧电弧中的带电粒子指的是电子、正离子和负离子。 阴极电弧的稳定燃烧电弧中的带电粒子指的是电子、正离子和负离子。 引燃电弧和维持电弧燃烧的带电粒子是电子和正离子。 引燃电弧和维持电弧燃烧的带电粒子是电子和正离子。其中在阴极电 弧等离子体中电子占到了90%以上。 以上。 弧等离子体中电子占到了 以上 正离子主要是依靠电弧中气体介质的电离产生的。 正离子主要是依靠电弧中气体介质的电离产生的。 电子的产生过程主要有: 电子的产生过程主要有: 1.热发射 热发射 2.场发射 场发射 3.热游离 热游离 4.碰撞游离 碰撞游离
阴极弧离子镀磁过滤器

阴极弧离子镀磁过滤器李刘合 夏立芳(哈尔滨工业大学)Magnetic Filter of Cathode Arc Ion C oatingLi Liuhe,Xia Lifang(School of M aterial S cience and Engineering )AbstractT he catho de spo t o f a vacuum ar c depo sitio n g ener ates a spray o f macr opart icles (M P's)be-ca use o f the ver y hig h cur rent densities and the spot temper ature.T he questio n o f M P 's contam i-na tion is frequently r aised.Sev era l labo rat or ies hav e fo cused their resear ch in different techno lo g i-ca l o ptions such as cur vilinear of rectilinear to elimina ted the M P 's .T his pa per discussed the gen-erat ion theo ry o f M P's and the str uct ur e o f filt ered v acuum ar c devices .A nd we place emphasis on the discussion of the character and io n distr ibute in t he ex it o f a quart er -tor us .T he films ma de by the technique of filt ering using the mag netic plasma duct is rev iew ed.摘 要 在真空阴极弧离子镀的过程中,在阴极材料表面阴极斑点处的电流密度很大、斑点温度很高,发射出来的物质中包含有很多宏观粒子团(M P's:macro par ticles),构成对成膜表面的污染,人们采用了磁过滤器对M P 's 进行过滤。
阴极电弧离子镀原理
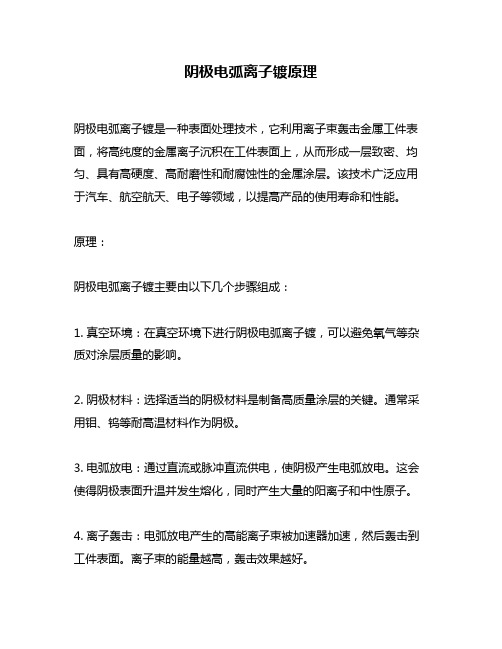
阴极电弧离子镀原理阴极电弧离子镀是一种表面处理技术,它利用离子束轰击金属工件表面,将高纯度的金属离子沉积在工件表面上,从而形成一层致密、均匀、具有高硬度、高耐磨性和耐腐蚀性的金属涂层。
该技术广泛应用于汽车、航空航天、电子等领域,以提高产品的使用寿命和性能。
原理:阴极电弧离子镀主要由以下几个步骤组成:1. 真空环境:在真空环境下进行阴极电弧离子镀,可以避免氧气等杂质对涂层质量的影响。
2. 阴极材料:选择适当的阴极材料是制备高质量涂层的关键。
通常采用钼、钨等耐高温材料作为阴极。
3. 电弧放电:通过直流或脉冲直流供电,使阴极产生电弧放电。
这会使得阴极表面升温并发生熔化,同时产生大量的阳离子和中性原子。
4. 离子轰击:电弧放电产生的高能离子束被加速器加速,然后轰击到工件表面。
离子束的能量越高,轰击效果越好。
5. 沉积:离子束轰击到工件表面后,会在表面形成一层薄膜。
这些离子在表面结构上重新排列,从而形成一层致密、均匀、具有高硬度、高耐磨性和耐腐蚀性的金属涂层。
优点:阴极电弧离子镀具有以下优点:1. 高质量涂层:由于离子束能够精确地控制沉积过程,因此形成的涂层具有致密、均匀、高硬度、高耐磨性和耐腐蚀性等特点。
2. 高效率:相较于其他表面处理技术,阴极电弧离子镀具有较高的生产效率和良好的重复性。
3. 适用范围广:该技术可以用于各种材料的表面处理,包括金属、陶瓷、塑料等。
4. 环保节能:由于该技术是在真空环境下进行的,因此不会产生废气、废水等污染物,具有较好的环保效益。
缺点:阴极电弧离子镀也存在以下缺点:1. 设备成本高:制备阴极电弧离子镀设备需要高端技术和复杂的工艺流程,因此设备成本较高。
2. 镀层厚度受限:由于离子束轰击过程中,离子束只能沉积在表面一定深度范围内,因此涂层厚度受到限制。
3. 涂层质量受到工艺参数影响:涂层质量受到许多工艺参数的影响,如离子束能量、轰击时间、沉积速率等。
如果这些参数不能得到精确控制,则可能会影响涂层质量。
- 1、下载文档前请自行甄别文档内容的完整性,平台不提供额外的编辑、内容补充、找答案等附加服务。
- 2、"仅部分预览"的文档,不可在线预览部分如存在完整性等问题,可反馈申请退款(可完整预览的文档不适用该条件!)。
- 3、如文档侵犯您的权益,请联系客服反馈,我们会尽快为您处理(人工客服工作时间:9:00-18:30)。
陰極電弧離子鍍膜Cathodic Vacuum Arc Processing (U.S. patent 3,793,179)輔仁大學物理系凌國基老師陰極電弧離子鍍膜一、前言1958年,Wore提出可以用Arc的方法來做鍍膜應用,一直到70年代初,才有4篇專利文章提出工業用的方法。
(1)Arc deposition and apparatus, U.S. patent No 3, 625, 848(1971)(2)Arc deposition and apparatus, U.S. patent No 3, 836, 415(1974)(3)Apparatus for vacuum evaporation of metals Under the action of an electric Arc, U.S.patent No 3, 783, 231(1974)(4)Apparatus for metal evaporation coating, U.S. patent No.3, 793, 179(1974) 到了70年代末期,USSR才有工業用途。
美國到了80年代中期,才有用Arc的方法在工具鋼上鍍TiN,增加硬度,延長工具鋼的壽命。
1.Cathodic vacuum arc processing的主要優點:(1)高度離子化。
(2)鍍膜速度快。
(3)黏著度較佳。
(4)Ti、N比例較佳,且較不會受N2分壓影響。
我們在鍍Ti、N時,最好是同一個比例上去,這個在電子槍中尤其難控制,陰極電弧離子鍍膜則是控制的特別好。
(5)基板溫度可以較低。
2.主要的缺點為:(1)陰極電弧離子鍍膜(cathode arc processing)最大的缺點為是微粒的產生(macro-particles)。
如圖一,大部份的macro-particles出現的角度約為10-20度。
From the cathode plane。
(2)因為鍍的速度太快,很難控制它的均勻度。
二、 Cathodic Spot (Arc Spot )圖一、不連續的陰極點示意圖1. 見圖一,圖中有陰極靶(Target at cathode potential )、陽極(Anode )、基板(Substrate ),通過的大電流產生磁場(Magnetic field )。
2. 電子因強電場的作用,使電子自陰極表面微突處發射並激發靶上方之氣體離子化(形成電漿),當其中的一個氣體正離子撞擊陰極靶上的某一點,因為大電流這點形成一個Arc spot(這現象有點類似於閃電,就如閃電一樣會打到原Arc spot 附近較高的點)而這點瞬間高溫熔融濺射出電子(electrons )、原子與分子及微粒(macro-particles ),形成離子雲。
3. 電子、原子與分子濺射的速度不同,相同溫度下所帶的能量一樣,從212mv 來看電子的質量是最小的,所以速度是最快的。
因此在陰極和陽極間會形成一個強電場區(positive space charge region ,圖一中虛線所圈之處)。
4. 部分離子通過電漿打向基板、部分折返撞擊陰極靶打出靶材正離子及電子如圖一。
由於磁場的關係,正離子會往左邊移動,形成另一個Arc spot 。
不斷地重覆第1到第4點的循環,也就形成了鍍膜的機制。
5. 如果沒有外加磁場作用,Arc spot 會隨機散亂地在陰極靶表面移動,稱為Random Arc model 。
※ 備註:1. 中性粒子是由macro-particles 與plasma 作用,蒸發而得。
高溫材料之ionization ratio 最高。
2. Arc spot 移動速度與不同的之氣體亦有關係。
活性氣體移動的比較快,而且macro-particles 的產生也較少。
B【範例一】圖二、這是1974年,俄國人在美國申請的專利之ㄧ。
我們將圖二當成一個設計例子,上面紅色虛線框起來的部份(1、2、3、4、5、6、7),整個是一個真空系統。
8為冷卻系統,9是陰極靶(target),10為蒸發表面(evaporation surface),11、12為non-evaporation surface,整個Target為一(平坦的圓盤)flat disk。
13為基板,放置在一虛構的球面14上,如此才能得到好的均勻度。
而陰極的底部12和冷卻系統8要用焊接的方式接起來,因為它所需的電流大約是100A,也就是離子上去的速度是100A,可見其鍍膜速度非常的快。
前面有說過Arc spot的機制會不斷的在附近循環,為了避免在鍍膜的過程中,Arc spot打在我們的系統上,損毀設備,因此陰極靶和系統之間需要一個溝,隔了一個溝,上空的電漿離子雲感應不到可以引發Arc的點也就不會產生閃電的現象,也就是圖二中的gap 22所以這閃電現象就只能發生在我們接有大電流的靶材上。
17為銅製的冷卻系統(colding bed),此系統同時有導電(通大電流)及導熱(保持都只是局部熔融)之作用;電由18進去,水由19進去。
作者觀察到,當Target surface10溫度越低,則Arc spot移動速度越快,越穩定,微粒越少。
Arc burning中有30%的熱量會被冷卻系統17帶走,因此冷卻系統是個很重要的因素,因此陰極的底部12和冷卻系統8最好要焊接在一起。
圖中擋板21(shield,此區的材質一定要是絕緣體若有隔空放電的現象,還是有可能引發閃電。
)的頂部24之高度與evaporation surface10需同高。
若24較高,則蒸鍍時,鍍料會跑到21;若蒸鍍時間較長,則gap22會被導通。
若24較低,則陰極圓柱的表面11(cathode cylindrical surface)也會被鍍上去,如此原本的gap22也會被導通。
之前說的是理想的例子才可以一直不間斷的發生閃電現象,當實際在鍍膜時我們需要一個可以當它有狀況,不發生閃電時可以再次促發閃電機制的系統。
而這系統還要一點,就馬上離開,要不然電極會好像焊接一樣接在一起。
25為陽極(anode),由feedthrough27連接到power suppl y。
左下角虛線框起來的部份(40),是大電流供應的部份(power suppl y)。
45為正電,正電分成兩條,一條是46往上延伸;一條是38往上,經過一個電阻39(目的是限制電流),再往上通過一條電線35,接著藉由29接到靶上(29與靶的接觸點為一針狀物)。
另一條48為負電,往上經過一電磁鐵30,穿過49的地方,到達負電相接處。
當我們電源一打開,正電往上跑,瞬間藉由29在靶上產生一個局部的Arc後,使靶上的氣體離子化,造成電子、原子與分子的濺射鍍膜機制開始運作;此時,磁鐵30被往上吸,將彈簧34壓扁,29也跟著彈離陰極靶。
當因為某些原因,鍍膜機制停掉了,磁鐵30就會彈回原位,此時29又接觸到陰極靶,在靶上產生一個局部的Arc…,此鍍膜機制又可以開始運轉了。
這就是最陽春的陰極電弧離子鍍膜(無外加磁場作用,Arc spot會隨機散亂地在陰極靶表面移動,稱為Random Arc model)。
因在Arc 過程中會有電流突然消失約10-7秒左右,此時會有反向電動勢的產生,所以裝了大電容50來吸收這個反向電動勢,因此負極47的電壓要比42的電壓低,這可由可變電阻43來得到。
這裡說的系統是沒有辨法控制Arc spot打在什麼地方的,那要控制打在那最簡單的方法就是外加磁場,加上如圖一所示的磁場後,原本是隨機亂跳的Arc spot,如果直接用肉眼觀察會變成往左方不斷延伸的一條虛線。
因Arc spot有不斷打在高處的現象,故不論有無加上磁場,最後在陰極靶上都會形成一個平面。
經過長時間的蒸鍍,陰極靶會變成圖三的形狀(在此設計中是沒有加磁場的)。
這是sputter達不到的,因sputter鍍久了因磁場作用始終還是只有一個圓環的地方凹下去,而也凹不了這麼深,作者聲稱就算從他開始做鍍膜一直用到退休也沒有這麼深,就可以知道鍍膜速率比sputter快了幾倍;它的ionization ratio比sputter高太多了。
圖三圖三中,15的長度不能比陰極靶(trget)9的直徑長,否則在蒸發一段時間之後,若15太圓,arc buring會不穩定。
陰極靶9 之厚度也和arc buring蒸發材料的導熱有關,因為evaporation surface必須保持一個固定的溫度,因此厚度大約為。
陰極靶直徑的20~50%。
表二-1.1呈上表二-1.1,如果我們用的陰極靶為「鉬」:1.「Arc voltage」表示為保持Arc繼續所需的電壓「Ion K.E.(ev)」表示Ion Kinetic Energy氣體是Ar「%in Charge State」中的1、2、3...5表示一個或兩個或三個...電子跑掉的百分比,跑掉的電子數目與陰極靶有關。
(通常suptter都只會有一個電子跑掉,由這即可知它的ionization ratio有多高)2.每一個Arc spots的電流大約為固定,若電流增加則分為多個Arc spots。
3.因為一個Arc spots消失,另一個開始進行很快,所以會有high frequency fluctuationsin both voltage and current。
4.我們也可由表看出,No和Ta為高熔點金屬,溫度越高越鍍的漂亮。
Macro-particles為什麼會有Macro-particles的產生呢?當Arc發生接觸的那一點會被局部氣化,當在理想狀態下那真的瞬間全部變成氣體,不過實際上不然。
它一定會有某個地方先被氣化,當它是在最底層的位置先被氣化時就會有氣泡破掉的感覺,那還在熔融態的靶材四濺就形成所謂的Macro-particles。
要減少Macro-particles的最好方法,就是使每一個Arc spot凹的深度淺一點,較淺的話就越接近理想狀態。
想凹的淺就是要讓Arc spot每一點間的距離拉大,儘量不要打在上一個Arc spot點的週圍並加強冷卻系統。
這樣就不會有熱量累積的問題,使靶材的溫度都一直很低。
每個Arc spot出現的間隔時間是一樣的,相同的時間要走較長的距離,相對的它每次熔融的量就降低了,而出現Macro-particles的機會也就跟著降低。
再來因Macro-particles大多都是往左右濺射,可以設計個擋板只留中間濺射。
都可以減少膜層上出現Macro-particles的機率。
※Target溫度愈低spot移動速度愈快,macro-particle愈少。
三、蒸發原設計的考量Source design consideration蒸發原設計的考量可以分為1.電弧的引弧arc initiation。