离子镀膜技术概述
离子束镀膜

离子束镀膜一、什么是离子束镀膜?离子束镀膜是一种表面处理技术,它使用离子束将材料沉积在另一个材料表面上。
该技术常用于制造高质量的光学和电子器件,因为它可以产生非常均匀和致密的涂层,同时还可以控制涂层的厚度和化学成分。
二、离子束镀膜的原理离子束镀膜的原理基于物理气相沉积(PVD)技术。
在这种技术中,材料被加热到高温并被蒸发。
然后,这些蒸发物质会在真空室中沉积在另一个材料表面上。
离子束镀膜与传统PVD技术不同之处在于,在此过程中使用了带电粒子(即离子)。
这些带电粒子被加速到非常高速,并且具有足够的能量来改变目标表面的化学和物理性质。
当这些粒子与目标表面相互作用时,它们会改变表面结构并形成致密、均匀且具有良好附着力的涂层。
三、离子束镀膜的优点1.高质量涂层:离子束镀膜可以产生均匀、致密和具有良好附着力的涂层,这些涂层可以提供更好的光学和电学性能。
2.高精度控制:离子束镀膜可以控制涂层的厚度和化学成分,从而实现高精度控制。
3.多种材料可用:离子束镀膜可以使用多种材料进行镀膜,包括金属、陶瓷和聚合物等。
4.环保:离子束镀膜是一种无污染的技术,不会产生有害化学物质或废弃物。
四、离子束镀膜的应用1.光学器件:离子束镀膜常用于制造光学器件,如反射镜、滤波器和透镜等。
该技术可以产生高精度、高反射率和低散射率的涂层。
2.电子器件:离子束镀膜还常用于制造电子器件,如集成电路(IC)和显示器。
该技术可以产生非常均匀且具有良好附着力的金属涂层。
3.医疗器械:离子束镀膜还可以用于制造医疗器械,如人工关节和牙科设备。
该技术可以产生具有良好生物相容性和耐磨性的涂层。
五、离子束镀膜的发展趋势随着科技的不断进步,离子束镀膜技术也在不断发展。
未来,离子束镀膜将更加普及,并应用于更广泛的领域,如太阳能电池、汽车制造和航空航天等。
同时,随着新材料的出现和新技术的引入,离子束镀膜将变得更加高效、环保和经济。
第四章离子镀膜
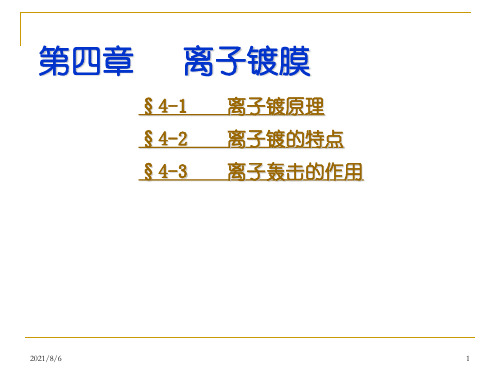
2021/8/6
2222
The End
2021/8/6
23
离化率是指被电离的原子数占全部蒸发原子数的百 分比例。是衡量离子镀特性的一个重要指标,也是衡 量活化程度的主要参量。特别在反应离子镀中更为重 要。被蒸发原子和反应气体的离化程度对薄膜的各种 性质都能产生直接影响。 1.中性粒子的能量
中性粒子所具有的能量Wv主要取决于蒸发温度
2021/8/6
14 14
分析离子镀的成膜条件
若辉光空间只有金属蒸发物质,且只考虑蒸发原子的淀积作
用,则单位时间内入射到单位表面上淀积的金属原子数 n 可用
下式表示
n 104 NA
60M
(4-1)
2021/8/6
66
n 104 N A
60M
式中, --淀积原子在基片表面的淀积速率(m / min ); -薄膜的密度( g / cm3 );
与蒸发镀膜和溅射镀膜相比较,除具有二者的特点 外,还特别具有膜层的附着力强、绕射性好、可镀材 料广泛等一系列优点,因此受到人们的重视。
2021/8/6
22
§4-1 离子镀原理
图4-1为Mattox采用的直流二极型离子镀装置的示意图。
2021/8/6
33
2021/8/6
4
1. 真空室抽至10-4Pa的高真空后,通入惰性气体(如氩气),使真 空度达到 1~10-1 Pa。
15 15
当 nvEv ni Ei 时,可得
ni Ei nv Ev
eUi ( ni ) C Ui
3kTv / 2 nv
Tv
(
ni nv
)(4-7)
式中,ni / nv-离子镀过程中的离化率;C-可调节参数。
离子镀膜技术概述

可镀制的膜层包括几乎全部金属盒部分合金材料。而且,在镀制合金镀层时,该 方法所获得的膜层能保留靶源合金材料的成分比例不变。因此,阳极真空电弧镀 膜方法出现伊始就引起了广泛重视。 1.3.2.3 辅助阳极技术 辅助阳极多弧沉积技术所用弧源与偏压电源和一般的阴极电弧沉积设备相 同, 其目标是提供一种真空电弧沉积装置,不是通过等离子流中离子在进行离子 清洗和基体加热, 而是通过增强此阶段中使用的气体的离化率的一种辉光放电来 达到。 由于辅助阳极的点位相对于等离子体为正,部分等离子体中的电子加速移 向阳极, 获得相应电势差加速带来的能量。此外还可以通过气体的离子轰击基材 表面来达到清理和加热, 防止形成有害的中间层。进一步的发明在于辅助阳极采 用磁性材料制成。为防止大颗粒污染基体表面,对部分阴极靶安装了隔离装置。 它可在两个位置上移动, 一个位置完全挡住靶与基体的直线距离位置,另一位置 完全打开通道。 前一位置主要用在清洗、 加热阶段。 图 1.11 为辅助阳极示意图。
镀膜技术
一、多弧离子镀
多弧离子镀技术是采用阴极蒸发源的一种离子镀技术。 阴极电弧蒸发源可以 是 Ti、Al、Zr、Cr 等单相靶材也可以是由它们组成的多相靶材。多弧离子镀应 用面广,实用性强,除了具有其他各种离子镀方法的广泛用途之外,特别是在高 速钢刀具镀覆 TiN 涂层的应用方面发展的最为迅速,并进入了工业化阶段。
图 1.3 阴极靶表面离化区域示意图
离化区域的空间电荷, 是导致加速区强电场的主要原因,该电场一方面使电 子加速离开阴极表面, 另一方面也使得离子回归阴极表面,该回归的离子流可能 导致阴极表面温度在一定程度上的增加。此外,回归的离子流对熔池表面的冲击 作用可能是液滴喷溅的原因, 这可以与一杯水在表面受到冲击时产生的喷溅现象 相类比。按照这种解释,在阴极表面附近只有离子和液滴向外空间发射,即在基 片上只能接收到离子和液滴,而无中性原子。
离子镀原理

离子镀原理一、引言离子镀是一种先进的表面处理技术,其基本原理是将气体引入真空镀膜室内,通过气体放电和离子化过程,将气体或固体颗粒离子化,然后将这些离子沉积在基材表面形成薄膜。
与传统的镀膜技术相比,离子镀具有许多独特的优点,如沉积速率高、附着力强、薄膜质量好等。
因此,离子镀在许多领域得到了广泛的应用,如光学、电子、机械、化学等领域。
二、离子镀原理概述离子镀的基本原理主要包括气体放电和离子化过程、基材偏压和离子能量、薄膜沉积过程等几个方面。
1.气体放电和离子化过程气体放电和离子化过程是离子镀的关键环节之一。
在真空镀膜室内,通过辉光放电或弧光放电等方式,使引入的气体或固体颗粒发生电离,形成大量的正离子和负离子。
这些离子在电场的作用下加速向基材表面运动,从而实现沉积。
气体的放电和离子化过程可以通过各种不同的电源和控制方式来实现。
2.基材偏压和离子能量基材偏压和离子能量是影响离子镀的重要因素。
基材偏压是指基材表面相对于镀膜室电极的电位差,它可以影响离子的运动轨迹和能量。
通过调整基材偏压,可以控制离子的沉积速度、薄膜的质量和附着力等。
离子的能量则决定了其与基材表面原子的相互作用程度,从而影响薄膜的结构和性能。
离子的能量可以通过控制放电电压和电流来调节。
3.薄膜沉积过程薄膜沉积过程是离子镀的主要环节之一。
在气体放电和离子化的过程中,正离子和负离子在电场的作用下加速向基材表面运动,并与基材表面碰撞,将能量传递给基材表面的原子或分子,使其脱离基材表面并被蒸发或溅射。
这些被蒸发或溅射的原子或分子在基材表面重新凝结形成薄膜。
在沉积过程中,可以通过控制沉积速率、温度、气体流量等参数来优化薄膜的结构和性能。
三、离子镀的特点离子镀作为一种先进的表面处理技术,具有许多独特的优点。
其主要特点包括:1.沉积速率高:由于气体放电和离子化的过程中可以形成大量的离子,因此离子镀的沉积速率较高,可以大大缩短加工时间和降低生产成本。
2.附着力强:由于离子镀过程中基材表面被高能离子反复轰击和刻蚀,使其表面粗糙度增加,形成“锚定”效应,使得薄膜与基材的附着力更强。
真空镀膜技术_第10章: 离子镀
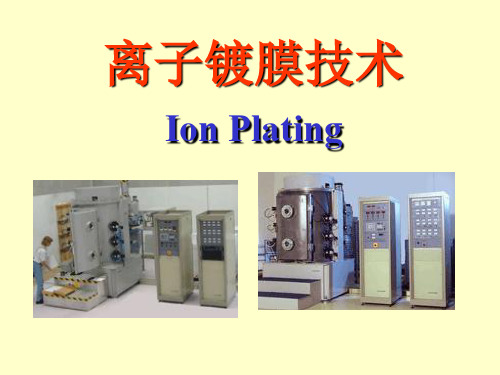
离子镀膜技术——离子镀膜的类型
综上所述,射频放电离子镀具有下述特点:
a. 蒸发、离化、加速三种过程可分别独立控制,离化 率靠射频激励,而不是靠加速直流电场,基板周围不产生 阴极暗区。
b. 在10-1-l0-3 Pa的较低工作压力下也能稳定放电,而且 离化率较高,薄膜质量好。
c. 容易进行反应离子镀。 d. 和其它离子镀方法相比,基板温升低而且较容易控 制。
离子镀膜技术
Ion Plating
§4.4 离子镀膜技术
★ 离子镀膜的原理 ★ 离子镀膜的特点 ★ 离子轰击的作用 ★ 离子镀膜的类型
离子镀是在真空条件下,利用气体放电使气体 或被蒸发物质部分离化,在气体离子或被蒸发物质 离子轰击作用的同时把蒸发物或其反应物沉积在基 片上。
离子镀把气体的辉光放电、等离子体技术与真 空蒸发镀膜技术结合在一起,不仅明显地提高了镀 层的各种性能,而且大大地扩充了镀膜技术的应用 范围。
离子镀膜技术——离子轰击的作用
当 n E 远小于 ni Ei 时,
ni Ei n E
eUi 3kT
2
ni n
C
Ui T
ni n
离子镀膜中的活化系 数与离化率、基片加速电 压、蒸发温度等因素有关。
离子镀膜技术——离子轰击的作用
离子镀膜技术——离子轰击的作用
离子镀膜技术——离子镀膜的类型
(4) 调节或改变蒸发速率及反应气体压力可以十分方 便地制取不同配比、不同结构、不同性质的同类化合物。
(5)由于采用了大功率、高功率密度的电子束蒸发源, 几乎可以蒸镀所有金属和化合物。
(6)清洁,无公害。
ARE的缺点:电予枪发出的高能电子除了加热蒸发薄膜
离子镀膜法

离子镀膜技术——离子镀膜的类型 ★ 离子镀膜的类型
按薄膜材料气化方式分类:
电阻加热、电子束加热、高频感应加热、阴极弧 光放电加热等。
按原子或分子电离和激活方式分类:
辉光放电型、电子束型、热电子型、电弧放电型、 以及各种离子源。 一般情况下,离于镀膜设备要由真空室、蒸发源 ( 或 气源、溅射源等 ) 、高压电源、离化装置、放置基片的阴 极等部分组成。
离子镀膜技术——离子轰击的作用
溅射清洗
薄膜淀积前对基片的离子轰击。将产生如下 结果:
溅射清洗作用 吸附气体、各种污染物、氧化物
产生缺陷和位错网
入射粒子传递给靶材原子的能量超过靶原子发生离位的 最低能量时,晶格原子将会离位并迁移到晶格的间隙位置上 去,从而形成空位、间隙原子和热激励。轰击粒子将大部分 能量传递给基片使其发热,增加淀积原子在基片表面的扩散 能力,某些缺陷也可以发生迁移、聚集成为位错网。
离子镀膜技术——离子轰击的作用
破坏表面晶格 离子轰击产生的缺陷很稳定的话,表面的晶体结构 就会被破坏而成为非晶态 气体掺入 不溶性气体的掺入能力决定于迁移率、捕获位置、 基片温度及淀积粒子的能量大小 非晶材料捕集气体的能力比晶体材料强。
表面成分改变 溅射率不同 表面形貌变化 表面粗糙度增大,溅射率改变 温度升高
由于高能粒子轰击,基片温度较高,有时不得不 对基片进行冷却。
薄膜中含有气体量较高。
离子镀膜技术——离子轰击的作用 ★ 离子轰击的作用
离子镀膜的整个过程中都存在着离子轰击。 离化率:是指被电离的原子数占全部蒸发原子的百分数。
中性粒子的能量 W n E
3kTv Ev 2
离子镀膜技术——离子镀膜的类型
直流二极型离子镀
离子镀膜工艺

离子镀膜工艺
离子镀膜是利用离子开展的一种表面处理工艺,其步骤如下:
1. 准备基材:首先需要将待镀膜的基材放入真空腔室中进行清洗和抛光,确保表面干净平整。
2. 预处理:在真空腔室中,通过加热或辉光放电的方式,将气体转化为离子,并将其轰击到基材表面,以清除表面的氧化物和其它杂质,同时提高基材表面活性和粗糙度,以便于离子镀膜的开展。
3. 进行离子镀膜:在离子源产生的离子束下,基材表面形成一层薄薄的金属氧化物膜。
通过控制离子束能量和离子束的扫描速度,可获得不同形状、不同厚度、不同复杂度的膜材。
4. 收尾处理:离子镀膜后,需要进行后处理,以确保膜材的质量和稳定性。
常见的后处理方式有氧气退火、氢气退火、压电浸渍和化学强化等。
整个离子镀膜的过程需要严格控制各种工艺参数,如离子能量、离子流量、离子束方向、基材温度等,以获得最理想的膜材特性。
pvd离子镀膜
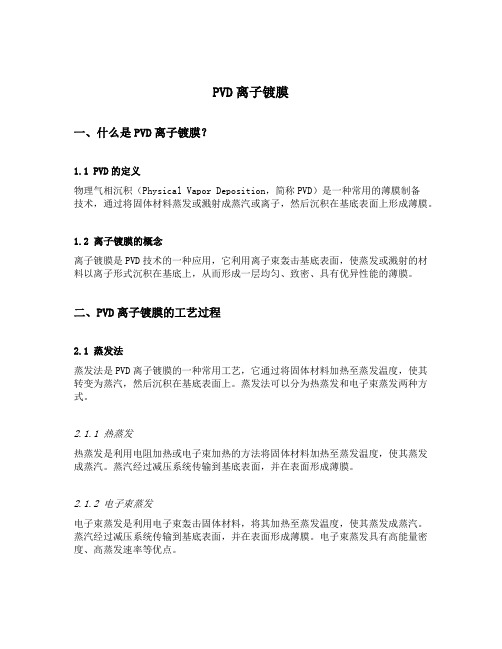
PVD离子镀膜一、什么是PVD离子镀膜?1.1 PVD的定义物理气相沉积(Physical Vapor Deposition,简称PVD)是一种常用的薄膜制备技术,通过将固体材料蒸发或溅射成蒸汽或离子,然后沉积在基底表面上形成薄膜。
1.2 离子镀膜的概念离子镀膜是PVD技术的一种应用,它利用离子束轰击基底表面,使蒸发或溅射的材料以离子形式沉积在基底上,从而形成一层均匀、致密、具有优异性能的薄膜。
二、PVD离子镀膜的工艺过程2.1 蒸发法蒸发法是PVD离子镀膜的一种常用工艺,它通过将固体材料加热至蒸发温度,使其转变为蒸汽,然后沉积在基底表面上。
蒸发法可以分为热蒸发和电子束蒸发两种方式。
2.1.1 热蒸发热蒸发是利用电阻加热或电子束加热的方法将固体材料加热至蒸发温度,使其蒸发成蒸汽。
蒸汽经过减压系统传输到基底表面,并在表面形成薄膜。
2.1.2 电子束蒸发电子束蒸发是利用电子束轰击固体材料,将其加热至蒸发温度,使其蒸发成蒸汽。
蒸汽经过减压系统传输到基底表面,并在表面形成薄膜。
电子束蒸发具有高能量密度、高蒸发速率等优点。
2.2 溅射法溅射法是PVD离子镀膜的另一种常用工艺,它通过将固体材料置于溅射靶材的位置,然后利用离子束轰击靶材,使其溅射成蒸汽或离子,最后沉积在基底表面上。
2.2.1 直流溅射直流溅射是利用直流电源,通过离子轰击靶材,使其溅射成蒸汽或离子。
直流溅射具有操作简单、成本低等优点,但膜层质量较低。
2.2.2 射频溅射射频溅射是利用射频电源,通过离子轰击靶材,使其溅射成蒸汽或离子。
射频溅射具有溅射效率高、膜层质量好等优点,但设备成本较高。
三、PVD离子镀膜的应用领域3.1 光学领域PVD离子镀膜在光学领域有广泛的应用,如镀膜玻璃、反射镜、透镜等。
离子镀膜可以提高光学元件的透过率、反射率和耐磨性,提高光学元件的性能。
3.2 电子领域PVD离子镀膜在电子领域的应用也非常广泛,如集成电路、显示器、光伏电池等。
离子镀膜的原理

离子镀膜的原理离子镀膜是一种通过离子束轰击材料表面,使得材料表面形成一层薄膜的技术。
离子镀膜的原理是利用离子束的能量和动量,使得材料表面的原子或分子发生位移和重排,从而形成一层薄膜。
离子镀膜的过程可以分为三个步骤:准备阶段、镀膜阶段和后处理阶段。
准备阶段:在离子镀膜之前,需要对材料表面进行清洗和处理,以保证表面的纯净度和平整度。
清洗过程可以采用化学方法或物理方法,如酸洗、碱洗、超声波清洗等。
处理过程可以采用机械方法或化学方法,如抛光、电化学抛光等。
镀膜阶段:在准备阶段完成后,将材料放置在离子镀膜设备中,通过加热或加电等方式,使得材料表面发生化学反应或物理变化。
离子束轰击材料表面,将离子束的能量和动量传递给材料表面的原子或分子,使得原子或分子发生位移和重排,从而形成一层薄膜。
离子镀膜的薄膜可以是金属薄膜、氧化物薄膜、氮化物薄膜等。
后处理阶段:在离子镀膜完成后,需要对薄膜进行后处理,以提高薄膜的质量和性能。
后处理过程可以采用退火、氧化、硝化等方法,以改善薄膜的结晶度、致密度、硬度等性能。
离子镀膜的原理可以用以下公式表示:E = 1/2mv²,其中E为离子束的能量,m为离子的质量,v为离子的速度。
离子束的能量和速度决定了离子束轰击材料表面的能力和效果。
离子镀膜的优点是可以制备高质量、高性能的薄膜,具有良好的耐腐蚀性、耐磨性、导电性等性能。
离子镀膜的应用领域广泛,包括电子、光学、机械、航空等领域。
总之,离子镀膜是一种通过离子束轰击材料表面,使得材料表面形成一层薄膜的技术。
离子镀膜的原理是利用离子束的能量和动量,使得材料表面的原子或分子发生位移和重排,从而形成一层薄膜。
离子镀膜的过程可以分为准备阶段、镀膜阶段和后处理阶段。
离子镀膜具有制备高质量、高性能的薄膜的优点,应用领域广泛。
离子镀膜

离子镀膜的原理
离子镀法的基 本原理:将蒸 发了的金属原 子在等离子体 中离子化后在 基体材料中析 出薄膜。另外, 通过输入反应 性气体也能析 出陶瓷等化合 物薄膜
不同的离子镀膜方式
• • • • • • • • • • • 1) 直流二极型(DCIP) 2) 多阴极型 3) 活性反应蒸镀法(ARE) 4)空心阴极离子镀(HCD) 5) 射频离子镀( RFIP ) 6) 增强 ARห้องสมุดไป่ตู้ 型 7) 低压等离子体离子镀( LPPD) 8) 电场蒸发 9) 感应离子加热镀 10) 集团离子束镀 11) 多弧离子镀
多弧离子镀膜设备:
CDA450—2200系列真空多弧离 子镀膜机CDA450—2200系列真 空多弧离子镀膜机是当今世界上 用于表面涂装PVD膜层的先进专 用设备 之一
真空多弧离子镀膜
参考文献:
• • • • • • [1] 王银川 真空镀膜技术的现状及发展,《现代仪器》2000,6 [2] 杨烈宇,关文铎,顾卓明编著,《材料表面薄膜技术》北京:人民交通出版社出 版,1991 [3] 杨邦朝,王文生。《薄膜物理与技术》,电子科技大学出版社,l994,1 [4] 张小诚编《新型材料与表面改性技术》南京:华南理工大学出版社出 版,1990,12 [5] 金原 果( 日本) 著,杨希光译,《薄膜的基本技术》,北京:科学出版社,1952 [6] D.R.Charles,et al:Advances in Electronics and Electron Physics。,33A ,p279(Academic press ,1972) [7] 胡传. 表面处理技术手册[M ]. 北京: 北京工业大学出版社, 1997 [8] 张九渊.表面工程与失效分析。杭州:浙江大学出版社,2005 [9] 吴玉广, 任德亮, 徐前. 离子镀膜技术在制造业中的应用[ J]. 航空制造技术, 2003, ( 9): 64- 66. [10] 吴玉广, 李荣雪. 多弧离子镀技术在航天航空制造维修业中的应用实例 [ J]. 航空工程与维修, 1999, ( 2):47- 48. [11] 许樵府. 离子镀在航空发动机中的应用[ J]. 航空制造技术, 2002, ( 7): 7172. [12] 杨建宏. 多弧离子镀技术在钟表行业中的应用[ J]. 钟表, 1994, ( 2): 26- 29.
离子镀膜分类

离子镀膜分类离子镀膜是一种常见的表面处理技术,通过将金属离子沉积到基材表面上,形成一层薄膜,以改善基材的性能和外观。
离子镀膜可以分为金属离子镀膜和非金属离子镀膜两大类。
一、金属离子镀膜金属离子镀膜是指将金属离子沉积到基材表面上,以增加其硬度、耐磨性和耐腐蚀性。
常见的金属离子镀膜技术有镀铬、镀镍、镀银等。
1. 镀铬镀铬是将铬离子沉积到基材表面上的过程。
镀铬可以提高基材的硬度和耐腐蚀性,使其具备更好的耐磨性和耐高温性能。
镀铬常用于汽车零部件、家电产品和装饰品等领域。
2. 镀镍镀镍是将镍离子沉积到基材表面上的过程。
镀镍可以增加基材的硬度和耐腐蚀性,同时还能提升其光泽度和装饰性。
镀镍广泛应用于汽车零部件、厨具、首饰等领域。
3. 镀银镀银是将银离子沉积到基材表面上的过程。
镀银可以使基材具备良好的导电性和抗氧化性能,同时还能提升其外观质感和装饰效果。
镀银常用于电子元器件、餐具、首饰等领域。
二、非金属离子镀膜非金属离子镀膜是指将非金属离子沉积到基材表面上,以改善其特定性能。
常见的非金属离子镀膜技术有氮化、氧化和碳化等。
1. 氮化氮化是将氮离子沉积到基材表面上的过程。
氮化可以增加基材的硬度、耐磨性和耐腐蚀性,改善其表面光洁度和抗氧化性能。
氮化常用于刀具、模具和机械零部件等领域。
2. 氧化氧化是将氧离子沉积到基材表面上的过程。
氧化可以形成一层氧化膜,提高基材的耐磨性、耐腐蚀性和绝缘性能。
氧化常用于铝制品、不锈钢和电子元器件等领域。
3. 碳化碳化是将碳离子沉积到基材表面上的过程。
碳化可以增加基材的硬度和耐磨性,改善其耐腐蚀性和导热性能。
碳化常用于刀具、轴承和机械零部件等领域。
离子镀膜技术在工业生产和科研领域中具有广泛的应用。
通过选择不同的离子镀膜技术,可以根据基材的不同需求,提升其性能和外观质量。
离子镀膜的发展也为许多产业提供了新的发展机遇,推动了相关行业的进步和创新。
随着科技的不断进步,离子镀膜技术也将不断完善和发展,为各行各业带来更多的机遇和挑战。
电镀离子膜

电镀离子膜
电镀离子膜是一种在电镀过程中用于分隔阴阳极的膜状材料。
这种膜通常被设计为能够允许离子流动,同时阻止金属颗粒和其他杂质的通过,从而实现更精确和高效的电镀。
在电镀过程中,金属离子从阳极释放出来,经过电解质溶液传输到阴极,然后在阴极表面还原形成金属沉积。
电镀离子膜的作用是防止阳极处的金属离子直接到达阴极,从而保持阴极区域的纯度。
以下是电镀离子膜的一些特点和应用:
1. 选择透过性:电镀离子膜应该具有一定的选择透过性,使得金属离子能够通过,而其他杂质离子则被阻挡。
2. 化学稳定性:电镀离子膜需要在电镀液中保持稳定,不受化学腐蚀或降解。
3. 耐温性:电镀过程中可能涉及高温,因此电镀离子膜需要具有一定的耐温性。
4. 耐腐蚀性:电镀液中可能存在一些腐蚀性物质,因此电镀离子膜需要具有一定的耐腐蚀性。
5. 阻隔效果:电镀离子膜需要能够有效阻隔金属颗粒和杂质,确保电镀的纯度和均匀性。
电镀离子膜的应用可以在各种电镀过程中找到,包括镀铬、镀镍、镀金等。
这些电镀过程中使用的膜通常被称为阴离子膜或阳离子膜,具体根据其允许哪一类离子通过而定。
1/ 1。
pvd离子镀膜原理

pvd离子镀膜原理PVD离子镀膜原理离子镀膜技术是一种常用的表面处理方法,广泛应用于电子、光学、航空航天等领域。
其中,PVD (Physical Vapor Deposition) 离子镀膜技术是一种通过物理方法将固态材料转化为离子态并沉积到基材表面的技术。
本文将详细介绍PVD离子镀膜的原理及其应用。
一、PVD离子镀膜原理PVD离子镀膜技术是通过将材料加热至高温,使其处于气体、液体或固态的离子态,并利用真空条件下的物理过程将离子沉积到基材表面,形成一层薄膜。
主要包括蒸发、溅射和离子镀三种主要工艺。
1. 蒸发法蒸发法是通过加热材料使其升华,然后蒸发在基材上。
在真空情况下,将固态材料加热至其熔点以上,使其升华为气体。
升华后的气体通过控制温度和压力,使其在基材表面沉积,形成薄膜。
2. 溅射法溅射法是利用高能粒子轰击材料表面,使材料从固态转变为气态,然后沉积在基材表面。
在溅射过程中,通过在真空室中加入一定气体压力,利用离子轰击和反应气体,可以得到所需的薄膜。
3. 离子镀法离子镀法是通过电场将离子加速,然后撞击基材表面,将离子沉积在基材上。
在真空室中加入一定的气体,使其电离成离子,然后通过电场加速离子,并控制其在基材表面的沉积。
二、PVD离子镀膜的应用1. 电子行业PVD离子镀膜技术在电子行业中广泛应用于集成电路、显示屏、光学薄膜等领域。
通过在基材表面沉积金属薄膜或氧化物薄膜,可以提高电子元器件的导电性、抗氧化性和光学性能。
2. 光学行业PVD离子镀膜技术在光学行业中用于制备反射镜、透镜、光学滤波器等光学元件。
通过在基材表面沉积特定的金属薄膜或多层膜,可以改善光学元件的反射率、透过率和抗反射性能。
3. 航空航天行业PVD离子镀膜技术在航空航天行业中常用于制备航空发动机叶片、航天器表面保护层等。
通过在基材表面沉积陶瓷薄膜或合金薄膜,可以提高材料的耐磨性、耐腐蚀性和高温性能。
4. 医疗行业PVD离子镀膜技术在医疗行业中应用广泛,常用于制备人工关节、牙科种植体等。
离子镀

4—3 离子轰击的作用
离子镀膜区别于普通真空蒸发的许 多特性均与离子、高速中性粒子参与镀 膜过程有关。而且,在离子镀的整个过 程中都存在着离子轰击。因此,必须了 解离子轰击的作用。
参1、《薄膜物理与技术》杨邦朝等, 第四章 第三节 参2、《薄膜物理》薛增泉等,(0484/X85)
4—3 离子轰击的作用
2.离子的能量
离子的能量Wi,主要由阴极加速电 压决定,其值为: Wi=ni Ei ……(4-2) 式中,ni—单位时间对单位面积轰击的离子数; Ei—离子的平均能量, Ei≈eUi,
其中,Ui是淀积离子的平均加速电压。
3.薄膜表面的能量活性系数
薄膜表面的能量活性系数近似为: =(Wi +W)/ W =( niEi+ nE)/ nE ……(4-3) 当 nE《 niEi时,可得 ≈niEi/ nE=(ni/ n ) • eUi/(3kT /2 ) =C (ni/ n ) Ui/T ……(4-4) 式中, ni/ n —离子镀过程中的离化率; C —可调节参数。
(2)在基片表面产生缺陷和位错网。
若入射粒子传递给靶材原子的能量超过靶 原子发生离位的最低能量(约为25eV)时,晶格 原子将会离位并迁移到晶格的间隙位置上去, 从而形成空位、间隙原子和热激励(短时间微区 的高温化)。轰击粒子将大部分能量传递给基片 使其发热,增加淀积原子在基片表面扩散的能 力,某些缺陷也可以发生迁移、聚集成位错网。 (轰击过的表面尽管有缺陷的聚集,但仍将有大 量的点缺陷在表面层留下来)。
此图是 在典型的蒸 发温度T= 1800K时, 能量活性系 数与离化率 ni/ n和离子 的平均加速 电压Ui的关 系。
从图(4-2)可看出,能量活性系数与 加速电压的关系,在很大程度上受离化 率的限制。为了提高离子镀活性系数, 通常可通过提高离子镀装置的离化率来 实现。 几种离子镀装置的离化率值见表4— 2所示。
第6章 离子镀膜

•
• •
n n
j
• •
成膜条件分析 ①只考虑蒸发原子或离子的沉积作用,则单位时间内入 射到单位面积上淀积的蒸发原子数n可用下式表示
n 10
6
NA
60 M
•
• • •
式中,μ——淀积原子在基片表面的淀积速率 (μm/min);ρ——薄膜的密度(g/cm3);M—淀积物质 的摩尔质量,NA=6.029×1023,阿伏伽德罗常数。例 如,对于Ag, M 1 0 7 .8 8, 1 0 .4 9 g / cm 当其蒸发速率为 1μm/min时, Ag的 16 2 则 。s n 9.76 10 / cm ②溅射剥离效应 设离子电流密度为j,则单位时间内轰击到基片表面的 离子数,溅射率为η ,则单位时间内溅射的原子数nj,
• (3)绕射性能好。 • 离子镀过程中,部分膜材离子被离化成正离子后,它们将 沿着电场的电力线方向运动,凡是电力线分布之处,膜材 离子都能到达。在离子镀中由于工件为阴极,且带负高压, 因此,工件的各个表面(包括孔、槽、面向蒸发源或背向 蒸发源的表面)都处于电场之中。这样,膜材的离子就能 到达工件的所有表面。 • 另外,由于膜材在压强较高的情况下(>1Pa)被电离, 气体分子的平均自由程λ比源基之间的距离h小,所以蒸 气的离子或分子在它到达基片的路程中将与惰性气体分子、 电子及其它蒸气原子之间发生多次碰撞,产生非定向的气 体散射效应,使膜材粒子散射在整个工件周围。 • 由于上述原因,离子镀可以在基片的所有表面上淀积薄膜。 这是真空蒸发所无法比拟的。
5.离子入射到固体表面的三种现象
• 金属离子照射到固体表面上,根据入射的离子能量E值的 大小的不同,一般来说可以产生下述三种现象: E 5 0 eV • (1)沉积现象( ) E 5 0 eV ) • (2)溅射现象( • (3)离子注入现象( E 1 K eV )。 • 沉积现象是指照射的金属离子附着在固体表面上的现 象,这一现象与离子的动能有关,一般来说,动能小,附 着几率越大,获得的沉积速率也高。 • 随着入射离子能量的增加,因离子轰击作用,基片原子即 会被溅射出并进入到真空室中,这就是溅射作用。这时已 经附着在表面上的部分金属原子当受到后续入射的同种离 子的溅射作用后还会重新返回到真空室中。 • 而且,如果入射离子能量再进一步增大时,离子还会注入 到表面的原子层中,即产生离子注入现象。
- 1、下载文档前请自行甄别文档内容的完整性,平台不提供额外的编辑、内容补充、找答案等附加服务。
- 2、"仅部分预览"的文档,不可在线预览部分如存在完整性等问题,可反馈申请退款(可完整预览的文档不适用该条件!)。
- 3、如文档侵犯您的权益,请联系客服反馈,我们会尽快为您处理(人工客服工作时间:9:00-18:30)。
图 1.7 受控电弧蒸发源
6
1—线圈 2—冷却水 3—点弧源 4—钛阴极 5、6—导磁环 7—磁轭
图 1.4 为阴极自然冷却,用电启动器进行引弧的电弧发源示意图。弧光蒸发 源由圆锥状阳极、圆板状阴极组成。采用 200A、30V 的直流电源。引弧电极设 在阴极附近,通过绝缘材料,利用与阴极间的火花进行引弧。图 1.5 为阴极强制 冷却的电弧蒸发源。 圆板状阴极从背后用水等强制冷却,绝缘材料将圆锥状阳极 与阴极隔开。 在弧光蒸发源周围防止磁场线圈,引弧电极安装在有回转轴的永久 磁铁上。磁场线圈中无电流时,由于作用于永久磁铁的磁力使轴回转,引弧电极 从阴极离开。通过此电极与阴极接触和分离时的火花实现引弧。图 1.6 是离子枪 型多弧离子镀蒸发源,其特点是蒸发源可移动,阴极面积小,离子束以很窄面积 发射出来。因阴极小,在厚度方向消耗快,所以把阴极制成圆柱状可从后慢慢推 出连续使用。图 1.7 为采用外加横向磁场以提高弧斑在阴极表面上的于东速度的 受控电弧蒸发源。阴极直接水冷,采用电磁线圈以便调节磁场强度。 1.3.1.2 国内早期设备 从 1985 年开始我国几家刀具生产厂先后从美国引进了多台多弧离子镀膜机, 在此基础上, 国内掀起了多弧离子镀膜设备研究开发的热潮,很多科研院所和生 产厂家纷纷研制国产设备, 对国外的设备进行了消化和吸收,并逐步形成了自己 的技术。
图 1.4 阴极自然冷却电弧光蒸发源示意图 1—真空室 2—基板 3—阳极 4—火花间隙 5—阴极 6—绝缘 7—引弧电源 8—DC 电源
5
图 1.5 阴极强制冷却的电弧光蒸发源示意图 1—直流电源 2—磁场线圈 3—绝缘体 4—阳极 5—阴极 6—引弧电源 7—复位弹簧 8—冷却水
图 1.6 离子枪型多弧离子镀蒸发源 1—气体 2—屏蔽 3—阳极 4—阴极 5—气体喷嘴 6—水套
图 1.2 阴极电弧产物示意图
为了解释这种高度离化的过程,已经建立了一种稳态的蒸发离化模型,如图
2
1.3 所示。该模型认为,由于阴极弧斑的能流密度非常大,在阴极的表面形成微 小熔池, 这些微小熔池导致阴极靶材的剧烈蒸发。热发射和场致发射共同导致电 子发射,而且电子被阴极表面的强电场加速,以极高的速度飞离阴极表面,在大 约一个均匀自由程之后,电子与中性原子碰撞,并使之离化,这个区域称为离化 区。在这一区域内将形成高密度的热等离子体。由于电子比重离子轻得多,所以 电子飞离离化区的速度要比重离子高得多, 这样在离化区就出现正的空间电荷云。
7
流在工件负压的作用下加速到达工件表面, 与反应气体离子化合并沉积形成涂层。 该设备金属离化率较高,操作简便,蒸发源没有固定熔池,阴极电弧源可以任意 安放,镀膜均匀区大,对工件转架要求低,得到广泛使用。
1.3.2 国外设备进展
1.3.2.1 阴极电弧斑点的控制 在真空电弧技术中, 弧源的性能无疑是决定真空电弧沉积设备整体性能的关 键。设法稳定放电过程,实现对电弧的稳定控制具有重要作用。阴极斑点以很高 的速度做无规则的运动, 常常因此而跑向阴极发射表面以外的部位。这一现像尤 其易发生在初始放电阶段, 发射表面的氧化物等其他杂质的存在诱发了放电过程 的不稳定, 导致杂质气体的产生,因此限制和控制阴极斑点的运动成为问题的关 键。 小电流真空电弧的运动受磁场的影响较大, 所以可以利用磁场限制电弧并控 制阴极斑点的运动轨迹。 当磁场平行于阴极表面时, 电弧斑点作所谓的反向运动, 即运动方向与安培力方向相反。 当磁场与阴极表面相交时,则在反向运动上还叠 加一个漂移运动, 漂移运动的方向指向磁力线与阴极表面所夹的锐角区域,此即 为锐角定则。上述规律用于真空电弧沉积阴极弧源设计时,有两种表现形式:一 是在阴极表面形成环拱型磁场。 根据反向运动原理和锐角法则,电弧将沿着磁力 线与阴极表面的切线作环绕运动。调整切线的位置,可以将阴极斑点限制在某一 区域内;二是改变阴极的形状,使磁场与阴极的非烧蚀面斜交,通过漂移运动使 电弧转移至烧蚀面,如图 1.9 所示
图 1.3 阴极靶表面离化区域示意图
离化区域的空间电荷, 是导致加速区强电场的主要原因,该电场一方面使电 子加速离开阴极表面, 另一方面也使得离子回归阴极表面,该回归的离子流可能 导致阴极表面温度在一定程度上的增加。此外,回归的离子流对熔池表面的冲击 作用可能是液滴喷溅的原因, 这可以与一杯水在表面受到冲击时产生的喷溅现象 相类比。按照这种解释,在阴极表面附近只有离子和液滴向外空间发射,即在基 片上只能接收到离子和液滴,而无中性原子。
图 1.8 多弧离子镀膜机设备结构示意图 1—阴极弧电源 2—反应进气口 3—工件 4—氩气进气口 5—主弧源 6—偏压源
图 1.8 为多弧离子镀膜机设备结构示意图。在镀膜过程中,工件被烘烤加热 和轰击净化后启动引弧针, 在引弧针离开阴极表面时触发引燃弧光放电,在真空 条件下这种冷场致弧光放电可以自动维持。 阴极电弧源发射出的高密度金属离子
1.2 多弧离子镀的技术特点
多弧离子镀具有以下特点: (1) 金属阴极蒸发器不融化,可以任意安放使涂层均匀,基板转动机构简 化。 (2) 金属离化率高, 有利于涂层的均匀性和提高附着力,是实现离子镀膜
3
的最佳工艺。 (3) 一弧多用,既是蒸发源,又是加热源、预轰击净化源和离化源。 (4) 设备结构简单,可以拼装,适于镀各种形状的零件。 (5) 可以外加磁场改善电弧放电,使电弧细碎,细化膜层微粒,对带电粒 子产生加速作用。 (6) 会降低零件表面光洁度。 在化学气相沉积和蒸镀以及溅射镀中,必须在基片保持高温的条件下,才有 可能获得良好的膜层组织, 对于多弧离子镀,离子对基片轰击的效果相当于对基 片加热, 基片温度就取决于离子能量和离子流密度,即阴极弧斑所发射的等离子 体重的离子直接关系到膜层的组织。 而离子到达基片的能量主要由基板负偏压供 给;通过对弧源电流的调整来改变离子流密度。如果需要考虑基片的温度限制, 完全可以通过沉积工艺过程的调整, 在保证膜层质量的同时, 又不超过温度限制。 同样,由于等离子体中离子的较高能量,易于使已沉积的松散粒子被溅射下来, 从而造成膜层的高致密度。 多弧离子镀膜层与集体的结合牢固,是高能离子的又一贡献。高能粒子导致 膜层与基片之间以原子键结合, 并于界面处建立一互扩散层,同时还能减少或消 除膜层与基体界面之间的孔隙缺陷,因此使膜层具有良好的致密性和附着性。当 然,离子的能量主要依赖于基片负偏压,在镀前轰击清洗基片表面时,尤其需要 较高的负偏压。 对于反应物膜层的沉积, 在多弧离子镀中主要影响反应效果的因素是等离子 体的离化程度和离子处于各种价态上的几率, 由于充分电离的金属等离子体具有 很大的活性,因此促使化学反应容易发生。此外,当反应气体进入镀膜室后,阴 极辉点和电弧离子体的作用都能促使它们部分电离,有利于反应的充分进行。多 弧离子镀进行反应沉积所制备的反应膜几乎都是化学计量的, 而且反应过程也易 于控制。 在多弧离子镀中, 由于阴极靶可以安装在镀膜室壁的任一面上,而且靶的形 状可以根据需要进行调整, 气体的碰撞和等离子体中的库伦散射使膜层可以再基 片的侧面和背面沉积, 因此多弧离子镀具有良好的绕镀性。随着工件架设计的不 断改善, 基片在镀膜过程中同时参与自转和公转, 使得基片各面的沉积条件均等,
9
可镀制的膜层包括几乎全部金属盒部分合金材料。而且,在镀制合金镀层时,该 方法所获得的膜层能保留靶源合金材料的成分比例不变。因此,阳极真空电弧镀 膜方法出现伊始就引起了广泛重视。 1.3.2.3 辅助阳极技术 辅助阳极多弧沉积技术所用弧源与偏压电源和一般的阴极电弧沉积设备相 同, 其目标是提供一种真空电弧沉积装置,不是通过等离子流中离子在进行离子 清洗和基体加热, 而是通过增强此阶段中使用的气体的离化率的一种辉光放电来 达到。 由于辅助阳极的点位相对于等离子体为正,部分等离子体中的电子加速移 向阳极, 获得相应电势差加速带来的能量。此外还可以通过气体的离子轰击基材 表面来达到清理和加热, 防止形成有害的中间层。进一步的发明在于辅助阳极采 用磁性材料制成。为防止大颗粒污染基体表面,对部分阴极靶安装了隔离装置。 它可在两个位置上移动, 一个位置完全挡住靶与基体的直线距离位置,另一位置 完全打开通道。 前一位置主要用在清洗、 加热阶段。 图 1.11 为辅助阳极示意图。
图 1.102—辉光放电电极 3—阴极 4—屏蔽罩 5—抽气系统 6—阳极 7—阳极偏压 8—样品 表 9—衬底偏压
阳极真空电弧镀膜装置结构示意图见图 1.10。在真空室内,有一个水冷棒状 阳极, 其前端用难熔金属棒弯成一个支架,然后将所要镀制的材料加工成金属丝 并缠绕在支架上。正对阳极前端是水冷盘状阴极,可由金属或合金制成,同时利 用磁场控制阴极斑点的位置, 使之不逸出阴极端面。 在阴极外围, 有一个屏蔽罩, 用以限制阴极斑点的运动, 并阻止阴极熔化金属液滴向衬底喷射。样品架位于放 电区间的上方,并施加一定的负偏压,以加速离子向衬底运动;如果衬底为非导 电材料,则可在阳极上加一定的正偏压,也可达到使衬底吸引离子的效果。 阳极真空电弧镀膜方法是一种区别于阴极真空电弧镀膜的全新薄膜沉积方 法,它保留了 VAC 技术的长处,克服了大颗粒污染的弊端,同时又具有自身独 特的优点,如设备结构简单,衬底温升低,可在金属、非金属衬底上进行镀膜,
a
b
图 1.9 磁场控制电弧斑点的两种表现形式 a—在阴极表面形成环拱型磁场;b—改变阴极的形状,使磁场与阴极的非烧蚀斜交,通过漂
8
移运动使电弧转移到烧蚀面
1.3.2.2 真空阳极电弧沉积技术 为改善膜层表面出现的大颗粒缺陷, 以及弧斑对阴极表面的腐蚀不均所造成 靶面局部穿孔从而使靶材浪费的缺陷, 提出了阳极弧设想, 即被镀材料作为阳极, 可有效解决上述问题。该技术利用电子轰击阳极靶材,经过电弧等离子体,可使 蒸发出来的靶材与背底气体之间发生化学反应, 因而在各种化合物薄膜及多元合 金膜层的制备方面有很大应用前景。
1.1 多弧离子镀的基本结构与沉积原理
多弧离子镀的基本组成包括真空镀膜室、阴极弧源、基片、负偏压电源、真 空系统等,如图1.1所示。阴极弧源是多弧离子镀的核心,它所产生的金属等离 子体自动维持阴极和镀膜室之间的弧光放电。 多弧离子镀的工件原理主要是基于 冷阴极真空弧光放电理论, 按照这种理论, 电量的迁移主要借助于场电子发射和 正离子电流,这两种机制同时存在, 而且互相制约。在放电过程中, 阴极材料大 量蒸发产生等离子体, 这些等离子体所产生的正离子在阴极表面附近很短的距 离内产生极强的电场, 约为108V/cm2。在这种强电场作用下, 电子能直接从金属 的费米能级逸出到真空, 产生所谓 “场电子发射” , 发射电流可达到5× 107A/cm2, 从而产生新的等离子体。 上述过程的进行维持电弧持续工作。一般阴极靶本身既 是蒸发源又是离化源。 外加磁场可以改变阴极弧斑在阴极靶面的移动速度,并使 弧斑均匀、细化,以达到阴极靶面的均匀烧蚀,延长靶的使用寿命。