浅谈铝合金轮毂生产技术的发展现状
轮毂技术发展情况汇报
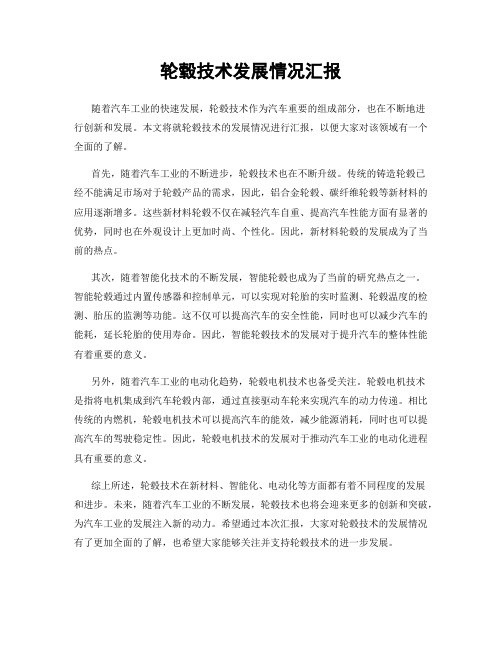
轮毂技术发展情况汇报随着汽车工业的快速发展,轮毂技术作为汽车重要的组成部分,也在不断地进行创新和发展。
本文将就轮毂技术的发展情况进行汇报,以便大家对该领域有一个全面的了解。
首先,随着汽车工业的不断进步,轮毂技术也在不断升级。
传统的铸造轮毂已经不能满足市场对于轮毂产品的需求,因此,铝合金轮毂、碳纤维轮毂等新材料的应用逐渐增多。
这些新材料轮毂不仅在减轻汽车自重、提高汽车性能方面有显著的优势,同时也在外观设计上更加时尚、个性化。
因此,新材料轮毂的发展成为了当前的热点。
其次,随着智能化技术的不断发展,智能轮毂也成为了当前的研究热点之一。
智能轮毂通过内置传感器和控制单元,可以实现对轮胎的实时监测、轮毂温度的检测、胎压的监测等功能。
这不仅可以提高汽车的安全性能,同时也可以减少汽车的能耗,延长轮胎的使用寿命。
因此,智能轮毂技术的发展对于提升汽车的整体性能有着重要的意义。
另外,随着汽车工业的电动化趋势,轮毂电机技术也备受关注。
轮毂电机技术是指将电机集成到汽车轮毂内部,通过直接驱动车轮来实现汽车的动力传递。
相比传统的内燃机,轮毂电机技术可以提高汽车的能效,减少能源消耗,同时也可以提高汽车的驾驶稳定性。
因此,轮毂电机技术的发展对于推动汽车工业的电动化进程具有重要的意义。
综上所述,轮毂技术在新材料、智能化、电动化等方面都有着不同程度的发展和进步。
未来,随着汽车工业的不断发展,轮毂技术也将会迎来更多的创新和突破,为汽车工业的发展注入新的动力。
希望通过本次汇报,大家对轮毂技术的发展情况有了更加全面的了解,也希望大家能够关注并支持轮毂技术的进一步发展。
2023年铝合金轮毂行业市场调研报告

2023年铝合金轮毂行业市场调研报告一、行业概况随着汽车产业的快速发展,轮毂作为汽车零部件中的重要一环,也日益受到市场的关注和重视。
目前,铝合金轮毂已成为汽车轮毂的主流,其也分成多个子行业,如高性能轮毂、赛车轮毂、休闲车轮毂、SUV专用轮毂、VR6轮毂和涂层轮毂等。
二、市场现状1.市场规模和发展趋势根据2019年的市场调查显示,全球轮毂市场规模约为2200亿美元,铝合金轮毂占据主导地位,市场份额约为68%。
随着全球汽车产业的快速发展,铝合金轮毂市场仍有较大发展潜力。
2.市场竞争格局铝合金轮毂市场反映出来的竞争格局优势和劣势非常明显。
目前市场上为数不多的龙头企业仍然占据着绝对的市场份额。
全球轮毂市场的龙头企业主要有美国的Alcoa,日本的BORBET、Enkei和RAYS等,此外还有中国的中信铝业、福耀玻璃、桐城市华东钢铁等品牌。
3.技术发展状况轮毂技术在整个汽车产业链中起到了重要作用。
随着技术的不断发展,越来越多的企业开始将更多的精力和资金投入到轮毂技术的研究和开发当中。
其中,铝合金轮毂的制造技术越来越成熟,产品的外观和结构及安全性能得到了很大改进。
四、行业发展趋势1.技术创新轮毂市场将持续受到技术的推动和改善。
随着新技术的出现,铝合金轮毂的重量和材料成本会继续降低,同时也将迎来更广泛的应用市场。
2.品牌建设品牌建设在整个市场竞争中起着重要的作用,硬件设施以及产品品质是一个品牌能否在市场上站稳脚跟的前提条件。
相信在未来品牌地位将会更加明显。
3.市场多元化市场细分和多元化将成为未来铝合金轮毂发展的新趋势。
不同的汽车类型、需求和用途,对轮毂的要求也不同,这将促进市场仅民化,为产业链上下游带来更多发展机会。
4.环保意识的提升铝合金轮毂在应用中具有重要的环保功能,在未来的发展中必将得到越来越多人的重视。
因此,导入更多环保的铝合金材料制作轮毂将成为未来的重点方向。
2024年汽车铝轮毂市场分析现状

汽车铝轮毂市场分析现状1. 市场概述汽车铝轮毂作为汽车重要的结构材料之一,具有重量轻、抗腐蚀性强、美观等优点,已经成为汽车制造业的主要发展方向之一。
随着汽车行业的不断发展,汽车铝轮毂市场也呈现出快速增长的趋势。
2. 市场规模据行业数据显示,汽车铝轮毂市场在过去几年里保持了稳定增长,预计未来几年内还将保持较高的增长率。
目前,全球汽车铝轮毂市场规模已接近100亿美元,预计到2025年有望达到150亿美元。
3. 市场动态3.1 市场驱动因素汽车铝轮毂市场的快速增长得益于以下几个市场驱动因素: - 车辆轻量化趋势:随着环保意识的增强,汽车制造商越来越注重轻量化设计,而使用铝合金材料的轮毂可以有效减轻汽车整体重量,提高燃油效率和行驶性能。
- 增长的汽车销量:全球汽车销量持续增长,尤其是中国市场的快速发展,推动了汽车铝轮毂市场的增长。
3.2 市场挑战然而,汽车铝轮毂市场也面临一些挑战: - 高成本问题:相比传统的钢制轮毂,铝合金材料的成本较高,这限制了其在低端市场的应用。
- 市场竞争激烈:目前市场上,铝轮毂产品供应商众多,市场竞争异常激烈,成为了企业发展的一个阻碍因素。
4. 市场分析4.1 市场细分根据不同需求和用途,汽车铝轮毂市场可以分为以下几个细分市场: - 轻型车市场 - 重型车市场 - 高端车市场4.2 市场地域分布目前,汽车铝轮毂市场主要集中在以下几个地区: - 北美地区 - 欧洲地区 - 亚太地区4.3 未来发展趋势随着汽车工业的快速升级和技术的不断进步,未来汽车铝轮毂市场将呈现以下几个发展趋势: - 轻量化设计将成为主流:随着环保政策的推动,汽车制造商将更加注重车辆轻量化设计,铝合金材料的轮毂将成为主流选择。
- 新材料的应用:随着新材料技术的不断发展,未来可能会涌现出更加轻薄、强度更高的新材料,进一步推动汽车铝轮毂市场的发展。
5. 总结汽车铝轮毂市场目前呈现快速增长的态势,受到车辆轻量化和全球汽车销量增长的驱动。
2023年中国汽车铝轮毂行业全景速览

2023年中国汽车铝轮毂行业全景速览内容概况:目前我国汽车铝轮毂行业的企业数量众多,但总体实力偏弱。
一些大型企业如中信戴卡、万丰奥威等具有较强的技术和品牌优势,能够满足国内市场的需求,并出口到国际市场。
同时,一些中小企业也在市场上占据一定的份额,但整体竞争力较弱。
在需求方面,我国汽车市场的持续增长和消费者对汽车性能和外观的追求不断提高,推动了汽车铝轮毂市场的需求增长。
2022年我国汽车铝轮毂产量约为2.08亿件,需求量约为1.25亿件,出厂价格来到310.8元每件。
关键词:汽车铝轮毂市场规模、汽车铝轮毂发展背景一、行业概况铝轮毂也叫铝圈或铝轮滚,顾名思义就是采用密度较小的铝合金为材料制成的轮毂。
制造铝制轮毂所使用的铝合金材料包括A356、6061等。
其中,A356被铸造铝制轮毂大量选用。
A356铝合金具有比重小,耐侵蚀性好等特点,主要由铝、硅、镁、铁、锰、锌、铜、钛等金属元素组成,铝占92%左右,是一种技术成熟的铝合金材料。
汽车产业是国民经济的重要支柱产业,汽车零部件制造行业作为汽车产业的重要组成部分,是提升我国汽车行业整体发展的关键因素。
为促进汽车零部件制造行业的发展,我国政府出台了若干鼓励政策。
据公安部统计,2022年中国汽车保有量为3.19亿辆,同比增长5.63%,相较于2015年增长了约1.47亿辆,复合增长率为9.2%。
随着机动车保有量的不断增长,汽车服务需求市场也将快速增长。
汽车铝轮毂行业的上游主要是铝材供应商,中游是汽车铝轮毂制造商,下游则是汽车整车制造商和售后服务经销商等。
上游铝材供应商是汽车铝轮毂行业的基础,为汽车铝轮毂制造商提供铝材。
铝材的性能和质量直接影响到汽车铝轮毂的品质和性能。
中游汽车铝轮毂制造商是行业的重要环节,其生产工艺和制造技术直接决定了汽车铝轮毂的质量和性能。
同时,汽车铝轮毂制造商还需要关注市场动态和客户需求,不断进行技术创新和产品升级,以适应市场的变化和客户的需求。
汽车铝轮毂行业发展现状分析,预计未来三年内中国铝合金轮毂市场供需基本持平

汽车铝轮毂行业发展现状分析,预计未来三年内中国铝合金轮毂市场供需基本持平铝轮毂也叫铝圈或铝轮滚,是采用密度较小的铝合金为材料制成的轮毂。
与钢质汽车轮毂相比,铝合金轮毂的优点比较明显。
首先,铝合金轮毂密度小,能够减少10%汽车整车质量;其次,同等条件下,铝合金轮毂的散热性能优于钢质轮毂;最后,铝合金轮毂色泽多样、精致美观。
汽车铝轮毂优点分析数据来源:公共资料整理相关报告:发布的《2020-2026年中国汽车铝轮毂行业市场竞争态势及投资策略分析报告》中国汽车年销售量由2014年的2349万辆增长至2018年的2808万辆,年复合增长率4%。
同时,国内汽车保有量由2014年的8307万辆增长至2018年的13451万辆,年复合增长率10%。
2019年以来,由于国内汽车消费市场出现一定程度的下滑,国内汽车销量增速、保有量增速预计出现一定的下降,预测2019、2020、2021年国内汽车年销售量分别为2864.22、2921.51、2979.94万辆;汽车保有量分别为14124、14830、15571万辆。
中国汽车年销售量、保有量数据来源:公共资料整理将铝合金轮毂市场分为整车市场(OEM市场)和零售市场(AM)市场,按照铝合金轮毂装车率70%、每辆整车配备5只轮毂、AM市场轮毂更新率2%进行计算,2019-2021年国内铝合金轮毂需求量分别为1.11、1.14、1.16亿只。
中国铝合金轮毂需求量数据来源:公共资料整理根据数据,2018年中国铝合金轮毂产量10900万只,占全球的30%。
预测2019-2020年全球铝合金轮毂总产量分别为3.80、3.85、3.99亿只,对应中国地区产量1.14、1.16、1.20亿只。
预计未来三年内国内铝合金轮毂市场供需基本持平。
2018全球铝合金轮毂供给结构数据来源:公共资料整理全球铝合金轮毂产量数据来源:公共资料整理随着国内汽车铝轮毂行业的崛起,中国逐渐成长为全球汽车铝轮毂制造中心,本土企业在满足国内市场需求的同时,也开始加大对国际市场的布局,出口量及出口金额小幅增长。
2024年铝轮毂市场环境分析

2024年铝轮毂市场环境分析1. 市场概述铝轮毂作为汽车重要的零部件之一,承载着车辆的重量,具有重要的安全性和美观性。
随着汽车产业的发展,铝轮毂市场也呈现出快速增长的趋势。
本文将对铝轮毂市场环境进行分析,探讨其发展态势以及市场竞争情况。
2. 市场规模与增长趋势铝轮毂市场在过去几年中保持了稳步增长的趋势。
据统计数据显示,全球铝轮毂市场规模在不断扩大,预计未来几年内还将保持增长。
此增长趋势主要受到以下因素的驱动:•汽车销量的增加:随着全球汽车销量的增长,铝轮毂的需求量也相应增加。
尤其是在新兴市场,汽车购买力的增强将进一步推动铝轮毂市场的发展。
•汽车轻量化趋势:汽车制造商对汽车整体重量的关注逐渐提高,为了减少燃料消耗和提高汽车性能,他们倾向于使用轻量化材料,如铝合金制造铝轮毂。
•日益增长的豪华车市场:豪华车市场对于高品质铝轮毂的需求也在快速增长。
随着越来越多的消费者对汽车外观的关注度提高,铝轮毂的市场需求将进一步推动。
3. 市场竞争分析铝轮毂市场竞争激烈,主要厂商之间存在激烈的竞争。
市场上的主要竞争者包括国际知名的汽车零部件制造商,以及一些专门从事铝轮毂生产的厂商。
主要竞争力体现在以下几个方面:•产品品质:优质的铝轮毂能够保证安全性和耐久性,在市场上获得更高的认可度,因此德系和日系汽车零部件供应商在产品品质上具有竞争优势。
•制造技术:铝轮毂的制造过程需要高度精确的工艺和设备,高水平的制造技术是铝轮毂制造商之间竞争的重要因素。
•价格竞争:铝轮毂市场价格竞争十分激烈,厂商之间通过优惠价格和市场定位来争夺市场份额。
•品牌影响力:一些知名品牌具有更高的品牌影响力和消费者认可度,这也是市场竞争的重要方面。
4. 市场前景与发展趋势铝轮毂市场发展前景广阔,随着汽车产业的发展和技术的进步,铝轮毂市场将持续增长。
下面是未来市场发展的一些趋势:•高科技铝轮毂的兴起:随着汽车制造技术的不断进步,高科技铝轮毂开始进入市场。
例如,一些厂商研发了具备智能功能的铝轮毂,如无线传感器、可远程监控等。
2023年汽车铝轮毂行业市场发展现状
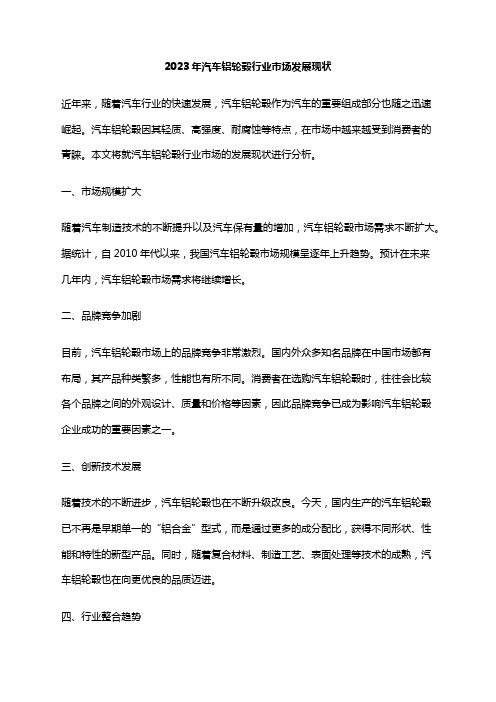
2023年汽车铝轮毂行业市场发展现状
近年来,随着汽车行业的快速发展,汽车铝轮毂作为汽车的重要组成部分也随之迅速崛起。
汽车铝轮毂因其轻质、高强度、耐腐蚀等特点,在市场中越来越受到消费者的青睐。
本文将就汽车铝轮毂行业市场的发展现状进行分析。
一、市场规模扩大
随着汽车制造技术的不断提升以及汽车保有量的增加,汽车铝轮毂市场需求不断扩大。
据统计,自2010年代以来,我国汽车铝轮毂市场规模呈逐年上升趋势。
预计在未来
几年内,汽车铝轮毂市场需求将继续增长。
二、品牌竞争加剧
目前,汽车铝轮毂市场上的品牌竞争非常激烈。
国内外众多知名品牌在中国市场都有布局,其产品种类繁多,性能也有所不同。
消费者在选购汽车铝轮毂时,往往会比较各个品牌之间的外观设计、质量和价格等因素,因此品牌竞争已成为影响汽车铝轮毂企业成功的重要因素之一。
三、创新技术发展
随着技术的不断进步,汽车铝轮毂也在不断升级改良。
今天,国内生产的汽车铝轮毂已不再是早期单一的“铝合金”型式,而是通过更多的成分配比,获得不同形状、性能和特性的新型产品。
同时,随着复合材料、制造工艺、表面处理等技术的成熟,汽车铝轮毂也在向更优良的品质迈进。
四、行业整合趋势
目前,汽车铝轮毂市场上竞争较为激烈,但是同时也存在一些品质不高,生产能力过剩等问题。
为此,不少企业开始采取联合或者兼并等方式,以整合市场资源和建立更有效的生产体系。
总之,汽车铝轮毂作为汽车的一种重要组成部分,在市场上具有广泛的应用前景。
随着时代的不断发展,汽车铝轮毂行业也必将不断创新、不断发展。
中国铝车轮行业发展现状、轻量化设计、制造技术的特点及发展趋势分析
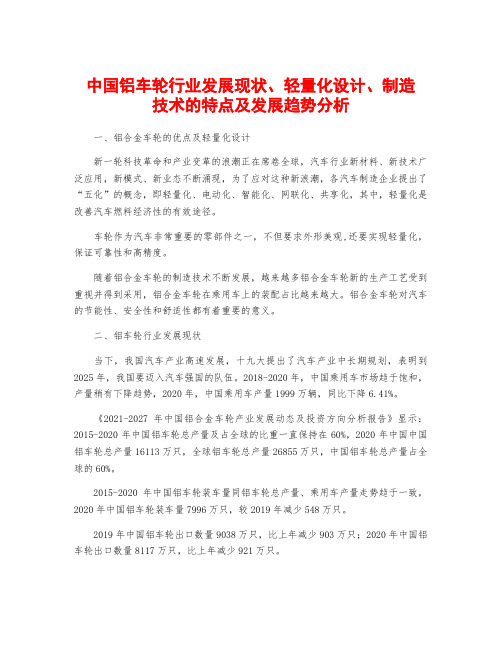
中国铝车轮行业发展现状、轻量化设计、制造技术的特点及发展趋势分析一、铝合金车轮的优点及轻量化设计新一轮科技革命和产业变革的浪潮正在席卷全球,汽车行业新材料、新技术广泛应用,新模式、新业态不断涌现,为了应对这种新浪潮,各汽车制造企业提出了“五化”的概念,即轻量化、电动化、智能化、网联化、共享化,其中,轻量化是改善汽车燃料经济性的有效途径。
车轮作为汽车非常重要的零部件之一,不但要求外形美观,还要实现轻量化,保证可靠性和高精度。
随着铝合金车轮的制造技术不断发展,越来越多铝合金车轮新的生产工艺受到重视并得到采用,铝合金车轮在乘用车上的装配占比越来越大。
铝合金车轮对汽车的节能性、安全性和舒适性都有着重要的意义。
二、铝车轮行业发展现状当下,我国汽车产业高速发展,十九大提出了汽车产业中长期规划,表明到2025年,我国要迈入汽车强国的队伍。
2018-2020年,中国乘用车市场趋于饱和,产量稍有下降趋势,2020年,中国乘用车产量1999万辆,同比下降6.41%。
《2021-2027年中国铝合金车轮产业发展动态及投资方向分析报告》显示:2015-2020年中国铝车轮总产量及占全球的比重一直保持在60%,2020年中国中国铝车轮总产量16113万只,全球铝车轮总产量26855万只,中国铝车轮总产量占全球的60%。
2015-2020年中国铝车轮装车量同铝车轮总产量、乘用车产量走势趋于一致,2020年中国铝车轮装车量7996万只,较2019年减少548万只。
2019年中国铝车轮出口数量9038万只,比上年减少903万只;2020年中国铝车轮出口数量8117万只,比上年减少921万只。
我国铝车轮出口量远远大于进口量,2020年12月,中国铝车轮出口数量818.8万只,进口数量16.9万只,出口量较进口量多801.9万只。
2020年中国铝车轮出口金额35.36亿美元,其中12月出口金额3.60亿美元;铝车轮进口金额0.90亿美元,其中12月进口金额0.11亿美元从进出口单价来看,中国铝车轮进口单价高于出口单价,2020年中国铝车轮进口单价64.38美元/只,其中12月份铝车轮进口单价43.56美元/只;铝车轮出口单价65.09美元/只,其中12月份铝车轮出口单价43.97美元/只。
轮毂行业年终总结范文

随着我国汽车工业的飞速发展,铝合金轮毂行业也迎来了前所未有的机遇与挑战。
在过去的一年里,我国铝合金轮毂行业在技术创新、市场拓展、品牌建设等方面取得了显著成果。
现将2021年铝合金轮毂行业年终总结如下:一、行业整体概况1. 市场规模持续扩大:据相关数据显示,2021年我国汽车轮毂行业市场规模达到了1591.1亿元,同比增长2.2%。
其中,铝合金轮毂市场份额占比超过60%,成为市场主流。
2. 产品结构不断优化:在市场需求驱动下,铝合金轮毂产品结构逐渐向高端化、轻量化、环保型方向发展。
高性能、轻量化、低噪音、节能环保的铝合金轮毂产品备受市场青睐。
3. 企业竞争力提升:在激烈的市场竞争中,我国铝合金轮毂企业通过技术创新、品牌建设、市场拓展等手段,不断提升自身竞争力。
部分企业已进入国际市场,成为全球铝轮毂行业的佼佼者。
二、主要工作及成绩1. 技术创新:行业企业加大研发投入,不断突破关键技术,提高产品性能。
例如,高强度铝合金材料的应用、轻量化设计、热处理工艺改进等,使铝合金轮毂产品在强度、耐腐蚀性、使用寿命等方面得到显著提升。
2. 市场拓展:企业积极拓展国内外市场,加强与国内外汽车制造商的合作,提高市场占有率。
同时,通过参加国内外展会、开展线上线下推广活动,提升品牌知名度和美誉度。
3. 品牌建设:行业企业注重品牌建设,打造了一批具有较高知名度和美誉度的品牌。
这些品牌在国内外市场具有较高的竞争力,为我国铝合金轮毂行业赢得了良好的口碑。
4. 产业链协同发展:产业链上下游企业加强合作,共同推动行业进步。
原材料供应商、模具制造商、装备制造商等产业链企业携手,为铝合金轮毂行业提供优质的产品和服务。
三、存在问题及改进措施1. 市场竞争激烈:随着国内外企业纷纷进入铝合金轮毂市场,市场竞争日益激烈。
为应对这一挑战,企业需加大研发投入,提高产品品质,降低成本,提升市场竞争力。
2. 人才短缺:行业人才短缺问题依然存在,企业需加大人才培养力度,提高员工素质,为行业发展提供人才保障。
2023年汽车铝轮毂行业市场发展现状

1、市场竞争激烈。目前,国内轮毂企业众多,市场竞争非常激烈,专业化、差异化趋势日益明显,企业需要加大研发投入,不断提升产品质量和品牌形象。
2、材料成本压力大。铝轮毂的主要原材料——铝合金价格波动较大,市场供需不平衡和金属价格波动都对企业经营构成了一定压力。
3、市场监管不健全。目前,国内汽车铝轮毂市场监管和管理机制尚不完善,一些非法、劣质产品难以从根源上得到治理,从而给消费者带来一定安全隐患。
2023年汽车铝轮毂行业市场发展现状
近年来,பைடு நூலகம்内汽车行业日益发展壮大,且市场需求不断增加,这也带动了汽车零配件市场的快速发展。作为汽车重要零配件的铝轮毂,因其具有良好的轻量化、加工性能、美观等特点而备受青睐。本文将从市场规模、产业链、趋势与挑战等方面分析汽车铝轮毂行业市场发展现状。
一、市场规模
目前,国内汽车铝轮毂市场规模巨大,且呈现逐年上涨的趋势。据中国涂料工业协会汽车油漆分会发布的《2019年中国汽车零配件市场研究报告》数据显示,2018年国内汽车铝轮毂的销售额为53.78亿元,同比增长了29.9%。预计未来几年,随着国内汽车市场需求的不断扩大,汽车铝轮毂市场规模也将会进一步扩大。
二、产业链
汽车铝轮毂的生产需要涉及到多个环节,涉及到材料采购、铝锭、试模、机加工等环节。铝轮毂主要的材料是铝合金,因此铝合金产业也是铝轮毂产业链的重要组成部分。目前,国内铝合金制品的生产技术不断提高,尤其是锻造成型和铸造成型工艺已经成熟,产业链的完整性也得到了不断的提高。
三、趋势
1、消费升级。目前,消费者对汽车外观的要求越来越高,汽车铝轮毂作为重要的装饰零配件,将随着消费升级而逐渐受到消费者重视。
总之,汽车铝轮毂行业市场前景广阔,但也面临着一定的挑战。未来,企业需要紧跟市场趋势,做足市场调研,提高产品质量和创新能力,以此来充分挖掘市场潜力和市场份额,获得更好的发展。
2024年铝合金轮毂市场环境分析

2024年铝合金轮毂市场环境分析1. 引言铝合金轮毂是一种高强度、轻质、具有良好热传导性和耐腐蚀性的汽车零部件,已成为汽车行业中的重要组成部分。
随着全球汽车市场的发展,铝合金轮毂市场也呈现出快速增长的趋势。
本文旨在对铝合金轮毂市场的环境进行分析,了解其发展的重要因素和面临的挑战。
2. 市场规模和增长趋势铝合金轮毂市场在过去几年里呈现出强劲的增长态势。
据市场研究数据显示,截至2020年,全球铝合金轮毂市场规模已达到X亿美元,并预计在未来几年里将保持稳定增长。
这一增长趋势可以归因于以下几个因素:•汽车产量增加:随着全球汽车产量的不断增加,汽车制造商对轻量化材料的需求也在增加。
铝合金轮毂由于其轻质、高强度的特点,能够提高汽车的燃油效率和行驶性能,因此受到汽车制造商的青睐。
•消费者需求变化:消费者对汽车外观的重视程度不断提升,他们越来越倾向于选择具有时尚外观和个性化设计的汽车产品。
铝合金轮毂以其优雅的外观和丰富的样式选择成为消费者的首选,从而推动了市场需求的增长。
3. 市场竞争格局铝合金轮毂市场竞争激烈,主要的竞争者包括国内外的铝合金轮毂制造商和汽车制造商。
目前市场上的主要竞争格局包括以下几个方面:•品牌竞争:一些知名的轮毂制造商拥有强大的品牌影响力和市场渗透能力,能够吸引消费者的关注和购买意愿。
这些品牌通常具有先进的制造技术和高品质的产品,从而在市场上获得较高的份额。
•价格竞争:铝合金轮毂市场的价格竞争较为激烈。
一些厂家通过降低售价来吸引消费者,但往往会导致产品质量的下降和利润的减少。
因此,合理的价格策略对于企业在市场竞争中具有重要意义。
•技术竞争:技术创新是铝合金轮毂制造商在市场上获取竞争优势的重要手段。
采用先进的材料和制造工艺,提高轮毂的强度和耐久性,可以赢得消费者的认可,并在市场上获得更高的份额。
4. 市场影响因素铝合金轮毂市场的发展受到多个因素的影响。
以下是主要的市场影响因素:•政策环境:政府对汽车行业的政策和法规对铝合金轮毂市场的发展产生重要影响。
2023年铝合金轮毂行业市场环境分析

2023年铝合金轮毂行业市场环境分析铝合金轮毂是指用铝合金材料制成的汽车轮毂,具有轻质、耐腐蚀、美观等优点,近年来受到汽车制造业的青睐,市场需求量持续增加。
本文将对铝合金轮毂行业市场环境进行分析。
一、市场规模铝合金轮毂市场正迅速增长。
随着汽车工业的发展,消费者对于汽车轮毂的改装需求不断增加。
铝合金轮毂相比传统的铁质车轮轻量化,美观性更强,大大提高了行驶舒适度和操控性,受到广大汽车用户的欢迎。
据市场研究报告,2019年全球铝合金轮毂市场销售额为114.4亿美元,预计到2027年将达到179.3亿美元,年复合增长率为5.6%。
二、市场竞争目前,铝合金轮毂市场上主要的竞争厂商有美国的Maxion Wheels、加拿大的Ion Alloy Wheels和日本的RAYS等。
中国的铝合金车轮市场竞争也日趋激烈,目前行业头部企业主要为碳离子、赛麟轮毂、澎晖轮毂、飞毛腿轮毂等。
这些公司采用不同的战略来应对市场挑战,其中市场占有率最高的是碳离子,其销售额和市场份额最大。
三、市场趋势1. 轻量化趋势:随着环保意识不断增强,汽车制造企业推出了更多的轻量化汽车产品。
铝合金车轮的轻质化特性可以减轻汽车重量,并提高油耗效率,未来市场上将有更多轻量化铝合金车轮出现。
2. 智能化趋势:铝合金轮毂制造企业开始研发智能化的轮毂,通过可穿戴设备、互联网、自动驾驶等技术进行数据互联,在轮毂上安装传感器、芯片等,实现监测轮毂的健康状况,进一步提高驾驶安全性。
3. 定制化趋势:消费者对于汽车风格的要求千差万别,个性化需求显著增长。
铝合金车轮制造企业开始开展定制化生产,能不断升级生产工艺及技术、灵活应对用户的个性化需求,从而提高产品差异化和竞争力。
四、市场风险铝合金轮毂市场的风险主要包括三大方面:1. 成本风险:合金价格波动及原材料成本的上升对铝合金轮毂制造商的经营管理和利润造成不利影响。
2. 技术风险:铝合金轮毂在制造、加工、模具等方面要求较高的技术和设备投入,在技术积累方面存在一定的风险,同时竞争厂商不断升级技术,可能对企业造成压力。
2024年铝合金轮毂市场前景分析
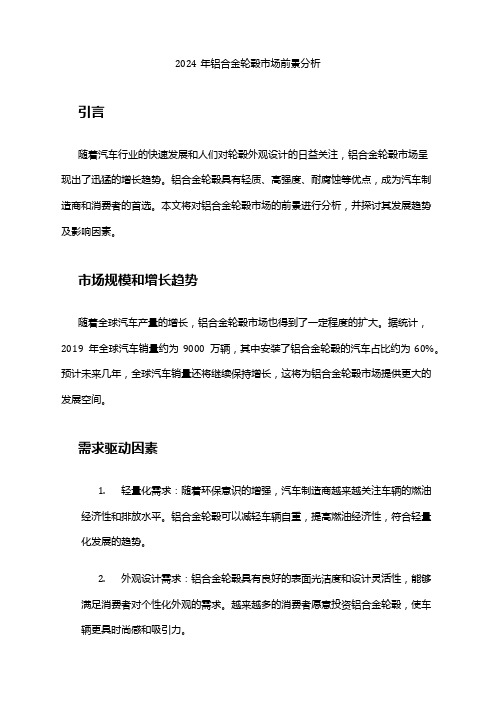
2024年铝合金轮毂市场前景分析引言随着汽车行业的快速发展和人们对轮毂外观设计的日益关注,铝合金轮毂市场呈现出了迅猛的增长趋势。
铝合金轮毂具有轻质、高强度、耐腐蚀等优点,成为汽车制造商和消费者的首选。
本文将对铝合金轮毂市场的前景进行分析,并探讨其发展趋势及影响因素。
市场规模和增长趋势随着全球汽车产量的增长,铝合金轮毂市场也得到了一定程度的扩大。
据统计,2019年全球汽车销量约为9000万辆,其中安装了铝合金轮毂的汽车占比约为60%。
预计未来几年,全球汽车销量还将继续保持增长,这将为铝合金轮毂市场提供更大的发展空间。
需求驱动因素1.轻量化需求:随着环保意识的增强,汽车制造商越来越关注车辆的燃油经济性和排放水平。
铝合金轮毂可以减轻车辆自重,提高燃油经济性,符合轻量化发展的趋势。
2.外观设计需求:铝合金轮毂具有良好的表面光洁度和设计灵活性,能够满足消费者对个性化外观的需求。
越来越多的消费者愿意投资铝合金轮毂,使车辆更具时尚感和吸引力。
3.性能要求:铝合金轮毂具有较高的强度和耐腐蚀性,能够在不同的道路条件下保持稳定和安全的使用,因此受到汽车制造商的青睐。
市场挑战和限制因素1.成本压力:与传统的钢质轮毂相比,铝合金轮毂的制造成本较高。
这增加了轮毂的价格,对消费者的购买意愿构成一定的压力。
2.技术和材料限制:铝合金轮毂需要采用高技术和高成本的制造工艺,对生产企业的技术要求较高。
此外,合适的铝合金材料供应也可能成为制约市场发展的因素。
市场趋势和机会1.新能源汽车市场增长:随着电动汽车和混合动力汽车市场的快速发展,对轮毂的需求也将进一步增长。
铝合金轮毂因其轻量化和耐腐蚀性等特点,将成为新能源汽车的首选。
2.自动驾驶技术发展:随着自动驾驶技术的不断进步,汽车制造商对轮毂的要求也在不断提高。
铝合金轮毂能够满足自动驾驶汽车对高强度和稳定性的需求,具备较大的市场机会。
总结铝合金轮毂市场具有广阔的发展前景。
随着汽车行业的持续增长和消费者需求的增加,铝合金轮毂将成为未来的主流选择。
2024年汽车铝合金车轮市场分析现状

2024年汽车铝合金车轮市场分析现状摘要本文对当前汽车铝合金车轮市场进行了详细的分析。
首先介绍了汽车铝合金车轮的定义以及其在汽车行业中的重要作用。
然后,对全球汽车铝合金车轮市场进行了概述,并对市场规模、发展趋势、竞争格局等进行了分析。
接着,通过对不同地区汽车铝合金车轮市场的比较,探讨了市场的地域分布和消费特点。
最后,对汽车铝合金车轮市场的未来发展进行了展望,并提出了相应的建议。
1. 引言汽车铝合金车轮是指使用铝合金材料制造的汽车车轮。
相比于传统的钢制车轮,铝合金车轮具有更轻、更坚固和良好的制动性能等优势。
随着全球汽车工业的发展,铝合金车轮在汽车制造中的应用越来越广泛。
本节将介绍铝合金车轮的定义,以及其在汽车行业中的重要性。
2. 全球汽车铝合金车轮市场概述2.1 市场规模全球汽车铝合金车轮市场规模不断扩大,预计将继续保持良好的增长势头。
汽车制造商对轻量化技术的需求不断增加,而铝合金车轮可以显著降低车轮重量,提高燃油效率。
因此,汽车铝合金车轮在市场中的份额不断增加。
2.2 发展趋势随着汽车行业的快速发展和技术进步,汽车铝合金车轮市场正面临着一些新的趋势和挑战。
其中包括电动汽车、自动驾驶技术和智能交通系统的兴起。
这些新兴技术对铝合金车轮的需求将不断增加,推动市场的进一步发展。
2.3 竞争格局全球汽车铝合金车轮市场竞争激烈,主要厂商之间展开了激烈的竞争。
主要的参与者包括美国、日本、欧洲等地的汽车制造商和供应商。
他们通过不断提升产品质量、降低成本和增加产品创新力来争夺市场份额。
3. 不同地区汽车铝合金车轮市场比较不同地区的汽车铝合金车轮市场具有一定的地域特点和消费习惯。
本节将比较北美、欧洲和亚洲地区的汽车铝合金车轮市场。
3.1 北美市场北美地区是全球最大的汽车铝合金车轮市场之一。
该地区的汽车制造商对轻量化技术的需求较高,铝合金车轮得到了广泛应用。
同时,北美地区有完善的供应链体系和丰富的铝资源,这也为汽车铝合金车轮市场的发展提供了有利条件。
2023年汽车铝合金车轮行业市场前景分析
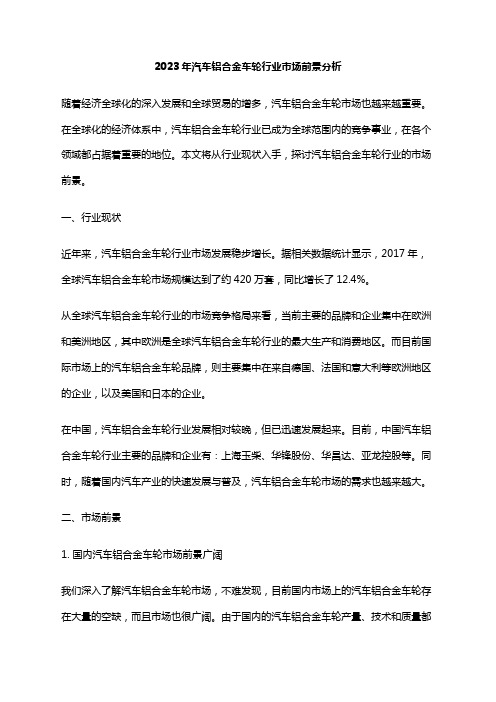
2023年汽车铝合金车轮行业市场前景分析随着经济全球化的深入发展和全球贸易的增多,汽车铝合金车轮市场也越来越重要。
在全球化的经济体系中,汽车铝合金车轮行业已成为全球范围内的竞争事业,在各个领域都占据着重要的地位。
本文将从行业现状入手,探讨汽车铝合金车轮行业的市场前景。
一、行业现状近年来,汽车铝合金车轮行业市场发展稳步增长。
据相关数据统计显示,2017年,全球汽车铝合金车轮市场规模达到了约420万套,同比增长了12.4%。
从全球汽车铝合金车轮行业的市场竞争格局来看,当前主要的品牌和企业集中在欧洲和美洲地区,其中欧洲是全球汽车铝合金车轮行业的最大生产和消费地区。
而目前国际市场上的汽车铝合金车轮品牌,则主要集中在来自德国、法国和意大利等欧洲地区的企业,以及美国和日本的企业。
在中国,汽车铝合金车轮行业发展相对较晚,但已迅速发展起来。
目前,中国汽车铝合金车轮行业主要的品牌和企业有:上海玉柴、华锋股份、华昌达、亚龙控股等。
同时,随着国内汽车产业的快速发展与普及,汽车铝合金车轮市场的需求也越来越大。
二、市场前景1. 国内汽车铝合金车轮市场前景广阔我们深入了解汽车铝合金车轮市场,不难发现,目前国内市场上的汽车铝合金车轮存在大量的空缺,而且市场也很广阔。
由于国内的汽车铝合金车轮产量、技术和质量都相对较低,同时国内行业市场的竞争程度还相对低,因此,国内企业在汽车铝合金车轮市场的竞争中具有无限的机会和前途。
2. 轻量化趋势助推市场增长近些年来,随着环保日益受到重视,汽车工业的发展方向也就逐渐转向了轻量化。
这时,汽车铝合金车轮就应运而生。
汽车铝合金车轮具有高强度、高耐热性、高耐腐蚀性、轻质化等特性,因此能够为汽车减轻重量,从而提高汽车的经济性、性能和安全性。
由此可见,随着轻量化趋势的不断发展,汽车铝合金车轮市场也将会得到进一步的发展和壮大。
3. 二三线城市汽车消费市场的增长众所周知,汽车消费市场一直是国内经济增长的重要驱动力。
2024年铝轮毂市场分析现状
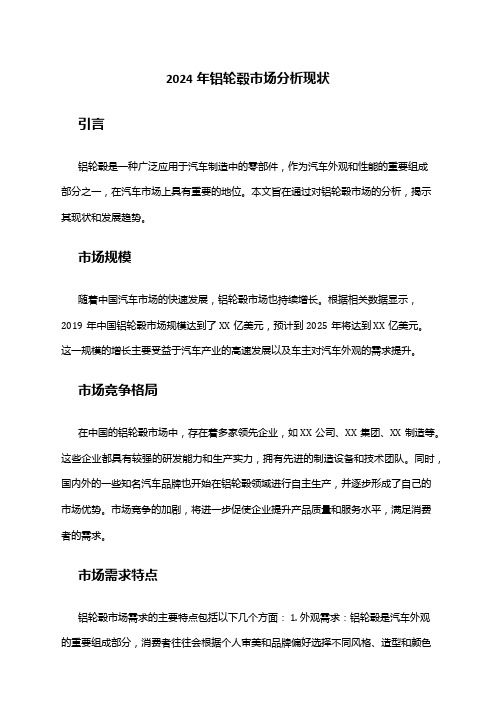
2024年铝轮毂市场分析现状引言铝轮毂是一种广泛应用于汽车制造中的零部件,作为汽车外观和性能的重要组成部分之一,在汽车市场上具有重要的地位。
本文旨在通过对铝轮毂市场的分析,揭示其现状和发展趋势。
市场规模随着中国汽车市场的快速发展,铝轮毂市场也持续增长。
根据相关数据显示,2019年中国铝轮毂市场规模达到了XX亿美元,预计到2025年将达到XX亿美元。
这一规模的增长主要受益于汽车产业的高速发展以及车主对汽车外观的需求提升。
市场竞争格局在中国的铝轮毂市场中,存在着多家领先企业,如XX公司、XX集团、XX制造等。
这些企业都具有较强的研发能力和生产实力,拥有先进的制造设备和技术团队。
同时,国内外的一些知名汽车品牌也开始在铝轮毂领域进行自主生产,并逐步形成了自己的市场优势。
市场竞争的加剧,将进一步促使企业提升产品质量和服务水平,满足消费者的需求。
市场需求特点铝轮毂市场需求的主要特点包括以下几个方面: 1. 外观需求:铝轮毂是汽车外观的重要组成部分,消费者往往会根据个人审美和品牌偏好选择不同风格、造型和颜色的铝轮毂。
2. 材质需求:铝轮毂相较于传统的钢轮毂具有轻量化、高强度等优势,因此消费者更倾向于选择铝轮毂。
3. 市场细分需求:随着汽车市场的细分化发展,特定车型和消费群体对铝轮毂的需求也呈现出多样化和个性化的特点。
技术发展趋势随着科技的进步和市场需求的变化,铝轮毂行业也在不断创新和发展。
以下是铝轮毂技术发展的趋势: 1. 轻量化设计:为了满足汽车消费者对省油性能的需求,铝轮毂制造商正致力于研发更轻、更强度更高的铝合金材料。
2. 表面处理技术:为了提高铝轮毂的外观质量和抗氧化能力,表面处理技术变得越来越重要。
烤漆、喷涂和电镀等技术在市场上得到广泛应用。
3. 智能制造技术:随着工业4.0的推进,铝轮毂制造正在向智能化、自动化方向发展。
机器人装配和数据分析等技术将有效提升生产效率和产品质量。
发展机遇与挑战铝轮毂市场虽然面临着巨大的发展机遇,但也面临着一些挑战。
轮毂技术发展情况汇报
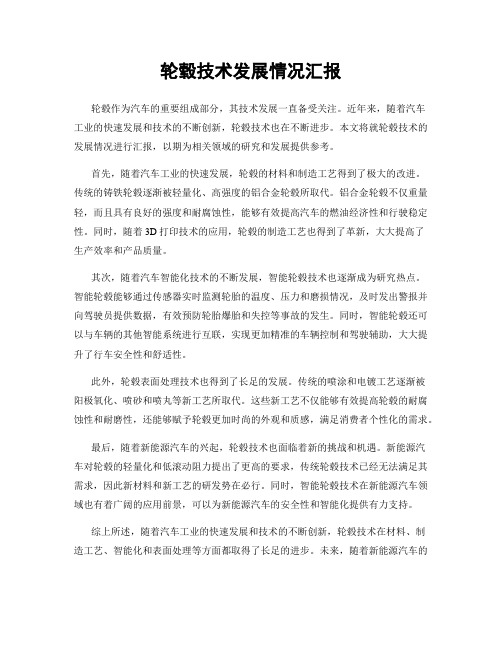
轮毂技术发展情况汇报轮毂作为汽车的重要组成部分,其技术发展一直备受关注。
近年来,随着汽车工业的快速发展和技术的不断创新,轮毂技术也在不断进步。
本文将就轮毂技术的发展情况进行汇报,以期为相关领域的研究和发展提供参考。
首先,随着汽车工业的快速发展,轮毂的材料和制造工艺得到了极大的改进。
传统的铸铁轮毂逐渐被轻量化、高强度的铝合金轮毂所取代。
铝合金轮毂不仅重量轻,而且具有良好的强度和耐腐蚀性,能够有效提高汽车的燃油经济性和行驶稳定性。
同时,随着3D打印技术的应用,轮毂的制造工艺也得到了革新,大大提高了生产效率和产品质量。
其次,随着汽车智能化技术的不断发展,智能轮毂技术也逐渐成为研究热点。
智能轮毂能够通过传感器实时监测轮胎的温度、压力和磨损情况,及时发出警报并向驾驶员提供数据,有效预防轮胎爆胎和失控等事故的发生。
同时,智能轮毂还可以与车辆的其他智能系统进行互联,实现更加精准的车辆控制和驾驶辅助,大大提升了行车安全性和舒适性。
此外,轮毂表面处理技术也得到了长足的发展。
传统的喷涂和电镀工艺逐渐被阳极氧化、喷砂和喷丸等新工艺所取代。
这些新工艺不仅能够有效提高轮毂的耐腐蚀性和耐磨性,还能够赋予轮毂更加时尚的外观和质感,满足消费者个性化的需求。
最后,随着新能源汽车的兴起,轮毂技术也面临着新的挑战和机遇。
新能源汽车对轮毂的轻量化和低滚动阻力提出了更高的要求,传统轮毂技术已经无法满足其需求,因此新材料和新工艺的研发势在必行。
同时,智能轮毂技术在新能源汽车领域也有着广阔的应用前景,可以为新能源汽车的安全性和智能化提供有力支持。
综上所述,随着汽车工业的快速发展和技术的不断创新,轮毂技术在材料、制造工艺、智能化和表面处理等方面都取得了长足的进步。
未来,随着新能源汽车的发展和智能化技术的深入应用,轮毂技术将迎来更加广阔的发展空间,我们期待着更多的创新和突破,为汽车工业的发展贡献更多的力量。
2024年铝合金汽轮市场环境分析

2024年铝合金汽轮市场环境分析一、市场概述铝合金汽轮是指使用铝合金材料制造的汽车轮毂。
随着汽车行业的快速发展,铝合金轮毂在汽车市场中的需求逐渐增加。
本文将对铝合金汽轮市场的环境进行分析。
二、市场规模铝合金汽轮市场规模是衡量市场发展的重要指标之一。
根据市场调研数据,近年来铝合金汽轮市场规模呈现稳步增长的趋势。
随着人们生活水平的提高和对汽车外观美观要求的增加,铝合金汽轮的市场需求有望进一步扩大。
三、市场竞争铝合金汽轮市场竞争激烈,主要厂商包括国内外知名汽车零部件制造商。
目前,市场上已经有多家企业涉足铝合金汽轮生产,并且提供了多种规格和款式的产品。
竞争力强的企业往往拥有先进的生产技术和优质的产品品质。
四、政策环境政策环境对铝合金汽轮市场的发展也起着影响作用。
近年来,随着国家环保政策的推进,对汽车轮毂的要求也在不断提高。
政府对铝合金轮毂的环保性能提出了更高的要求,这对铝合金汽轮行业构成了一定的挑战和促进。
五、技术创新技术创新是铝合金汽轮市场发展的重要推动力量。
随着精密铸造技术和轮毂制造工艺的不断进步,铝合金汽轮在质量、强度和耐腐蚀性能方面得到了显著提升。
未来,技术创新将继续推动铝合金汽轮市场的发展。
六、市场前景铝合金汽轮市场前景广阔。
随着汽车市场的持续增长和对汽车外观美观要求的提高,铝合金汽轮的市场需求将进一步增加。
同时,随着技术创新的不断推进,铝合金汽轮的性能将不断提高,市场竞争将更加激烈。
七、总结综上所述,铝合金汽轮市场具有良好的发展潜力和广阔的市场前景。
企业在面对激烈竞争的同时,应加强技术创新,提高产品质量,适应市场需求的变化。
同时,要密切关注政策环境的变化,并积极拓展市场,提升企业竞争力,实现可持续发展。
*以上为对铝合金汽轮市场环境的分析,总字数约为290字。
铝合金车轮制造技术及发展趋势
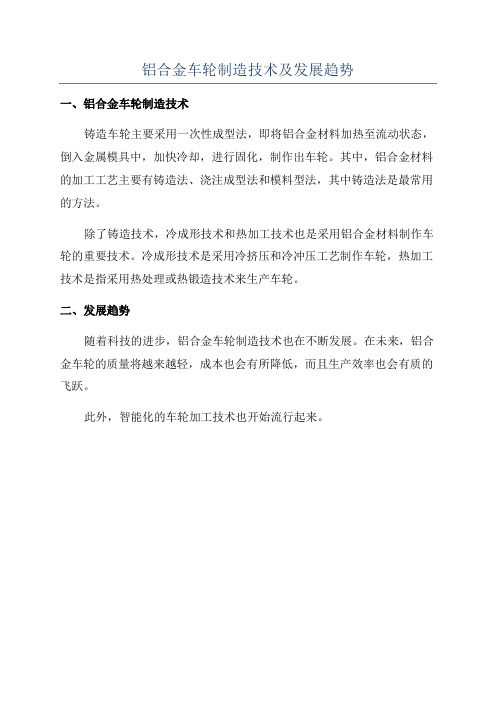
铝合金车轮制造技术及发展趋势
一、铝合金车轮制造技术
铸造车轮主要采用一次性成型法,即将铝合金材料加热至流动状态,倒入金属模具中,加快冷却,进行固化,制作出车轮。
其中,铝合金材料的加工工艺主要有铸造法、浇注成型法和模料型法,其中铸造法是最常用的方法。
除了铸造技术,冷成形技术和热加工技术也是采用铝合金材料制作车轮的重要技术。
冷成形技术是采用冷挤压和冷冲压工艺制作车轮,热加工技术是指采用热处理或热锻造技术来生产车轮。
二、发展趋势
随着科技的进步,铝合金车轮制造技术也在不断发展。
在未来,铝合金车轮的质量将越来越轻,成本也会有所降低,而且生产效率也会有质的飞跃。
此外,智能化的车轮加工技术也开始流行起来。
2023年铝合金轮毂行业市场前景分析

2023年铝合金轮毂行业市场前景分析一、行业概况随着汽车产业的不断发展,作为汽车重要零部件之一的轮毂也在不断变革和升级。
铝合金轮毂因其重量轻、强度高、美观等优点已成为极具发展前景的轮毂。
目前,全球铝合金轮毂市场规模逐年扩大,预计到2025年将达到300亿美元以上。
国内铝合金轮毂行业自20世纪90年代起起步,经过近几年的快速发展,行业规模逐渐扩大。
目前,行业企业众多,包括一些大型制造企业和配套企业。
据华泰证券报告显示,2019年铝合金轮毂行业市场规模已超过300亿元,随着汽车产业的不断发展,行业市场前景广阔。
二、市场分析1. 政策驱动:国家政策对铝合金轮毂行业的发展起到了重要推动作用。
国家政策大力支持节能环保型汽车的发展,其中铝合金轮毂作为环保材料之一,受到政策大力支持,市场前景广阔。
2. 汽车市场需求增长:汽车市场需求的不断增长是铝合金轮毂市场发展的重要推动力。
随着消费者的生活水平提高和汽车消费升级,铝合金轮毂越来越被人们所认知和接受,市场需求逐年增长。
3. 产业革新:随着轮毂制造技术的不断提高和制造工艺的革新,铝合金轮毂的制造成本逐渐降低,产品性能、品质得到了提升,铝合金轮毂的市场发展也迎来了新的机遇。
4. 消费升级:随着国民经济快速发展和消费升级趋势的不断加强,消费者对于汽车外观、性能、品质等方面的要求也越来越高,铝合金轮毂因其重量轻、强度高、美观等优点逐渐成为消费者的首选。
三、市场前景铝合金轮毂行业市场前景广阔,未来将面临以下几方面的发展机遇:1. 节能环保型汽车的推广不断加强,为铝合金轮毂的发展提供了重要机遇。
2. 汽车市场需求不断增长,铝合金轮毂得到广泛应用,市场增长空间巨大。
3. 轮毂行业技术不断提高,制造成本不断降低,产品性能和品质得到进一步提高,铝合金轮毂的市场前景更加广阔。
4. 未来随着消费升级趋势的不断加强,消费者对于汽车外观、性能、品质等多方面的要求也将不断提高,铝合金轮毂作为一种优质轮毂产品,将得到广泛应用和发展。
- 1、下载文档前请自行甄别文档内容的完整性,平台不提供额外的编辑、内容补充、找答案等附加服务。
- 2、"仅部分预览"的文档,不可在线预览部分如存在完整性等问题,可反馈申请退款(可完整预览的文档不适用该条件!)。
- 3、如文档侵犯您的权益,请联系客服反馈,我们会尽快为您处理(人工客服工作时间:9:00-18:30)。
矿产资源开发利用方案编写内容要求及审查大纲
矿产资源开发利用方案编写内容要求及《矿产资源开发利用方案》审查大纲一、概述
㈠矿区位置、隶属关系和企业性质。
如为改扩建矿山, 应说明矿山现状、
特点及存在的主要问题。
㈡编制依据
(1简述项目前期工作进展情况及与有关方面对项目的意向性协议情况。
(2 列出开发利用方案编制所依据的主要基础性资料的名称。
如经储量管理部门认定的矿区地质勘探报告、选矿试验报告、加工利用试验报告、工程地质初评资料、矿区水文资料和供水资料等。
对改、扩建矿山应有生产实际资料, 如矿山总平面现状图、矿床开拓系统图、采场现状图和主要采选设备清单等。
二、矿产品需求现状和预测
㈠该矿产在国内需求情况和市场供应情况
1、矿产品现状及加工利用趋向。
2、国内近、远期的需求量及主要销向预测。
㈡产品价格分析
1、国内矿产品价格现状。
2、矿产品价格稳定性及变化趋势。
三、矿产资源概况
㈠矿区总体概况
1、矿区总体规划情况。
2、矿区矿产资源概况。
3、该设计与矿区总体开发的关系。
㈡该设计项目的资源概况
1、矿床地质及构造特征。
2、矿床开采技术条件及水文地质条件。