马氏体相变
《马氏体相变》课件
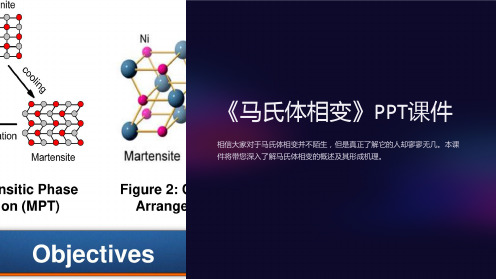
核化和形核
马氏体晶体生长
形核是马氏体相变的起始过程, 晶体结构中形成马氏体的小区域。
形核后的马氏体晶体开始在晶界 上生长,同时产生剩余奥氏体。
相变的影响因素
温度
相变温度是马氏体相变的一 个重要参数,不同温度下会 产生不同的相变行为。
合金化元素
添加合金元素可以调控马氏 体相变的速率和转变温度。
《马氏体相变》PPT课件
相信大家对于马氏体相变并不陌生,但是真正了解它的人却寥寥无几。本课 件将带您深入了解马氏体相变的概述及其形成机理。
马氏体相变的概述
马氏体相变是材料在冷却或应力作用下从奥氏体晶体结构转变为马氏体晶体 结构的过程。这种相变具有显著的物理和机械性能改善效果。
马氏体的形成机理
弹性变形发生
形状记忆合金
马氏体相变可以用于制造形状记 忆合金,可以实现金属材料的形 状记忆和恢复功能。
金属焊接
马氏体相变可以应用于金属焊接, 提高焊接接头的强度和韧性。
相变过程的图解
1
奥氏体
材核化
马氏体晶体开始在晶界上形成小的马氏体区域。
3
马氏体生长
马氏体晶体在晶界上迅速生长,同时奥氏体产生剩余。
总结与展望
马氏体相变具有广泛的应用前景,为材料科学领域带来了新的突破和挑战。未来的研究将致力于探究更高效的 相变控制方法和应用领域的拓展。
晶体结构
晶体结构对于马氏体相变的 发生和转变过程起着重要作 用。
马氏体相变的分类
稳定马氏体相变 非稳定马氏体相变 自适应马氏体相变
通过淬火等方法形成的马氏体相变
通过应力作用下的马氏体相变
通过金属合金中微观结构变化而形成的马氏体相 变
第四章 马氏体相变

第四章 马氏体相变随着科学技术的发展和人们对材料性能的要求越来越高,材料相变的研究也成为了一个热门的领域。
其中,固态相变是最为基础和广泛的相变形式之一。
在这其中,马氏体相变是一个相对特殊和有意义的相变过程。
一、马氏体相变的定义和分类马氏体相变,是指在含碳钢中,当钢经过一定的热处理过程后,在室温下形成一种具有变形性能的组织结构。
其核心原理是在高温下形成一种奥氏体,然后通过快速冷却过程,在室温下形成一种具有弹性、变形及塑性的马氏体组织结构。
根据马氏体相变的不同起始组织结构,其可以分为两种类型:一类是由完全奥氏体组成的马氏体相变,另一类是由贝氏体(以及在贝氏体上产生马氏体)组成的马氏体相变。
1.完全奥氏体马氏体相变当钢经过高温处理后,在其细小的晶粒中,完全转化为奥氏体组织。
通过钢的快速冷却 (通常在水、油、盐水等介质中进行),奥氏体中的部分碳原子被固溶,在马氏体的组织中重新排列,最终形成一种具有高强度和塑性的马氏体组织结构。
这种马氏体相变过程,称为完全奥氏体马氏体相变。
2.贝氏体马氏体相变贝氏体正常情况下是由冷却慢、回火温度低的钢中形成的。
它是由一种由铁与铁素体间化合物构成的细小晶粒组成的组织,这种组织强度比较低,韧性高,且具有较高的弹性变形和形变能力。
当这种钢经过高温处理后,由于组织发生了相变,大量贝氏体消失,而代替它的则是奥氏体组织。
这样在快速冷却的过程中,就会在奥氏体中形成一定数量的针状马氏体组织结构。
二、马氏体相变的影响因素马氏体相变的过程涉及到多个变量和影响因素,其中最重要的一些因素包括:1.冷却速度作为一种固态相变过程,马氏体相变的核心就是快速冷却过程。
通常来说,冷却速度越快,产生的马氏体组织也就越细小,强度也就越高。
2.合金元素含量合金元素在钢制造中有着重要的作用。
它们可以调节钢的合金成分和钢的性能,使钢的性能得到提升。
其中,加入Cr、Ni、Mn等元素可以有效地提高马氏体相变的开始和结束温度,这有利于得到良好的马氏体组织结构。
《马氏体相变 》课件
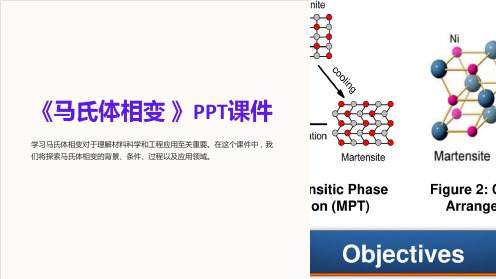
2 条件的作用原理是什么?
马氏体相变的条件是实现马氏体相变的必要 前提,它们直接影响马氏体晶体结构和材料 性能的形成和转化。
马氏体相变的过程
1
马氏体相变的步骤和原理
马氏体相变包括两个基本过程——形变和回复过程,当材料由奥氏体转变为马氏 体时,晶体结构发生相应的改变。
2
过程中有哪些需要注意的地方?
马氏体相变的过程会受到多种因素的干扰,如温度、压力、组织性能等,需要注 意这些影响因素对相变的影响。
应用领域
哪些领域得到应用?
马氏体相变广泛应用于机械、电子、材料等领域, 如机械弹簧、手机天线、记忆合金等。
应用的优势和局限是什么?
马氏体相变具有自修复性、快速响应、压电性、形 状记忆等特性,但仍然存在加工困难和应用的局限 性等问题。
结论和展望
总结发现和成果
本课件详细介绍了马氏体相变的背景、条件、过程和应用,使人们更好地了解该领域的发展 现状。
展望未来的发展前景
马氏体相变技术在自动化、能源、环境等领域有广阔的应用前景,我们期待它能在未来发挥 更大的作用。
参考文献
• 李新. 材料科学[M]. 化学工业出版社, 2013. • 关辰. 马氏体相变的研究进展[C]// 2019第五届全国现代材料学术会议论文集. 2019: 254-259. • 郭宝昌, 焦彦龙. 马氏体晶体几何结构及马氏体相变过程的研究进展[J]. 您刊, 2018, 39(05): 57-63.
马氏体晶体结构
晶结构是什么?
马氏体的晶体结构是单斜晶体结构,其单斜晶体形 状由一维位错和孪晶形成。
性质和特点是什么?
马氏体晶体中存在位形、变形、弹性、能量等多种 耦合,与其他晶体类似,但具有独特的特点和性质。
马氏体相变
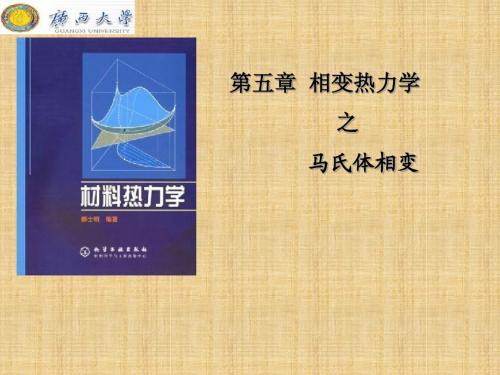
极快,特点:马氏体降温瞬间形核,瞬间长大,可以认为 马氏体转变速度取决于形核率而与长大速度无关。 马氏体转变量取决于冷却所达到的温度,而与时间无关。
2、等温形成马氏体的动力学
特点:马氏体等温形核,瞬间长大,形核需要孕育期,形核率 随过冷度增大而先增后减,转变量随等温时间延长而增加。等 温转变动力学图呈C字形。
各种马氏体的晶体结构、惯习面、亚结构、位向关系汇总表
2、影响马氏体形态及亚结构的因素
化学成分 马氏体形成温度 奥氏体的层错能 奥氏体与马氏体的强度 主要是化学成分和马氏体形成温度
化学成分:片状马氏体的组织形态随合金成分的变化而改变。
对于碳钢: 1)C%<0.3%时, 板条马氏体; 2)0.3%~1.0%时,板条和透镜片状混合的马氏体; 3)C% >1.0%时, 全部为透镜片状马氏体。并且 随着C%增加,残余奥氏体的含量逐渐增加。 合金元素: 1)缩小γ相区,促进板条马氏体。 2)扩大γ相区,促进透镜片状马氏体。
特征5:转变的非恒温性和不完全性
1. 奥氏体以大于某一临界冷却速度的速度冷却到某一温度(马氏 体转变开始温度Ms),不需孕育,转变立即发生,并且以极大 速度进行,但很快停止,不能进行终了。为使转变继续进行, 必须继续降低温度,所以马氏体转变是在不断降温的条件下才 能进行。当温度降到某一温度之下时,马氏体转变已不能进行, 该温度称为马氏体转变终了点即Mf 。 2. 马氏体转变量是温度的函数,与等温时间无关。马氏体的降温 转变称为马氏体转变的非恒温性。由于多数钢的 Mf 在室温以下, 因此钢快冷到室温时仍有部分未转变奥氏体存在,称为残余奥氏 体,记为Ar。有残余奥氏体存在的现象,称为马氏体转变不完全 性。要使残余奥氏体继续转变为马氏体,可采用冷处理。
马氏体相变的基本特征

马氏体相变的基本特征一、马氏体相变的概念及基本过程马氏体相变是指在一定条件下,由奥氏体向马氏体的转变。
奥氏体是指碳钢中的一种组织结构,具有良好的塑性和韧性,但强度和硬度较低;而马氏体则是碳钢中另一种组织结构,具有较高的强度和硬度,但韧性较差。
因此,在特定情况下将奥氏体转变为马氏体可以提高材料的强度和硬度。
马氏体相变的基本过程包括两个阶段:淬火和回火。
淬火是指将钢件加热至适宜温度后迅速冷却至室温,使其形成完全马氏体组织;回火是指将淬火后的钢件加热至适宜温度后进行恒温保持一段时间,然后缓慢冷却至室温,使其形成具有良好韧性和适当硬度的马氏体-贝氏体组织。
二、影响马氏体相变的因素1. 淬火介质淬火介质的选择对马氏体相变的影响非常大。
常用的淬火介质包括水、油和空气等。
水冷却速度最快,可以使钢件形成完全马氏体组织,但易产生变形和裂纹;油冷却速度较慢,可以降低变形和裂纹的风险,但易产生不完全马氏体组织;空气冷却速度最慢,可以避免变形和裂纹,但难以形成马氏体组织。
2. 淬火温度淬火温度是指将钢件加热至何种温度后进行淬火。
淬火温度越高,钢件中残留奥氏体的含量越高,从而影响马氏体相变的程度。
一般来说,淬火温度越低,马氏体相变越充分。
3. 回火温度回火温度是指将淬火后的钢件加热至何种温度进行回火处理。
回火温度对马氏体-贝氏体组织的形成有重要影响。
过高或过低的回火温度都会导致组织不均匀或性能下降。
4. 淬火时间淬火时间是指将钢件放入淬火介质中的时间。
淬火时间越长,相变程度越充分,但也容易产生变形和裂纹。
三、马氏体相变的应用马氏体相变广泛应用于制造高强度、高硬度的零部件。
例如汽车发动机凸轮轴、齿轮、摇臂等零部件,以及航空航天领域中的发动机叶片、转子等部件均采用了马氏体相变技术。
此外,马氏体相变还可以用于制造刀具、弹簧等产品。
总之,马氏体相变是一种重要的金属加工技术,在提高材料强度和硬度方面具有重要作用。
了解其基本特征和影响因素有助于更好地掌握该技术,并在实践中取得更好的效果。
马氏体转变特点
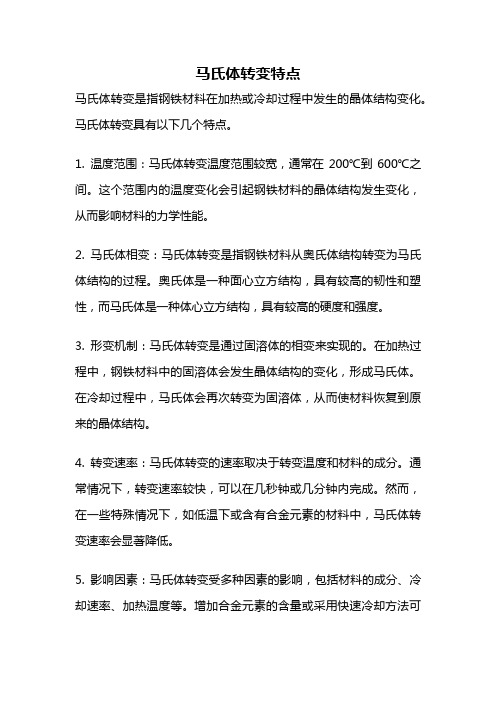
马氏体转变特点马氏体转变是指钢铁材料在加热或冷却过程中发生的晶体结构变化。
马氏体转变具有以下几个特点。
1. 温度范围:马氏体转变温度范围较宽,通常在200℃到600℃之间。
这个范围内的温度变化会引起钢铁材料的晶体结构发生变化,从而影响材料的力学性能。
2. 马氏体相变:马氏体转变是指钢铁材料从奥氏体结构转变为马氏体结构的过程。
奥氏体是一种面心立方结构,具有较高的韧性和塑性,而马氏体是一种体心立方结构,具有较高的硬度和强度。
3. 形变机制:马氏体转变是通过固溶体的相变来实现的。
在加热过程中,钢铁材料中的固溶体会发生晶体结构的变化,形成马氏体。
在冷却过程中,马氏体会再次转变为固溶体,从而使材料恢复到原来的晶体结构。
4. 转变速率:马氏体转变的速率取决于转变温度和材料的成分。
通常情况下,转变速率较快,可以在几秒钟或几分钟内完成。
然而,在一些特殊情况下,如低温下或含有合金元素的材料中,马氏体转变速率会显著降低。
5. 影响因素:马氏体转变受多种因素的影响,包括材料的成分、冷却速率、加热温度等。
增加合金元素的含量或采用快速冷却方法可以加速马氏体转变的速率。
6. 影响性能:马氏体转变对钢铁材料的力学性能具有显著影响。
马氏体具有较高的硬度和强度,但韧性和塑性较低。
因此,在一些特定的应用场合中,需要控制马氏体转变的程度,以获得适当的力学性能。
7. 相变组织:马氏体转变后的钢铁材料会形成不同的相组织。
常见的相组织包括全马氏体组织、马氏体和残余奥氏体组织、马氏体和贝氏体组织等。
不同的相组织具有不同的力学性能。
马氏体转变是钢铁材料在加热或冷却过程中发生的晶体结构变化,具有温度范围广、转变速率快、影响因素多等特点。
了解和掌握马氏体转变的特点对于钢铁材料的制备和应用具有重要意义。
马氏体相变与形状记忆效应
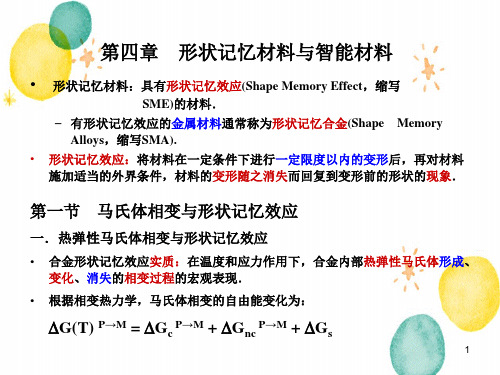
5
二.形状记忆效应的晶体学机制
• 形状记忆合金有三个特征: – 合金能够发生热弹性马氏体相变; – 母相和马氏体的晶体结构通常均为有序的(所谓有序结构, 即溶质原子在 晶格点阵中有固定位置); – 母相的晶体结构具有较高的对称性,而马氏体的晶体结构具有较低的对 称性.
• 当母相是B2型有序结构时,马氏体的晶体结构可看成是以图4-5 a) 第一行所 示(下页)的密排面为底面沿z方向按一定方式的堆垛. – 为保证密排堆垛结构,堆垛时必须按照以下的规则:若第一层的原点在A, 则第二层的原点可放在B或C . 若第二层的原点在B,则第三层的原点可 放在A或C,以此类推. • 当堆垛的顺序是ABABAB…时是2H结构 . • 当堆垛的顺序是ABCABC…时是3R结构. • 当堆垛的顺序是ABCBCACABABCBCACAB…时是9R结构,如图45b)所示 .
12
因此,记忆合金能够回复的最大变形不能超出马氏体完全再取向后所能贡 献出的相变应变.
• 如果马氏体完全再取向后继续施加外力,马氏体将以滑移和孪生的形式继续 变形,这时发生的变形是不可回复的塑性变形.组织中出现位错、形变孪晶 等晶体缺陷,破坏合金的热弹性马氏体相变,损害形状记忆效应.
三.应力诱发马氏体相变与记忆合金的超弹性
17
• 双程记忆训练:通过各种工艺处理方法在合金内部产生特定的内应力场,使 合金具有双程记忆效应.
• 双程记忆训练方法主要有: (1)SIM法:在母相态对记忆合金元件施加变形. (2)SME法:在马氏体态对记忆合金元件施加变形. (3)SIM+SME法:在母相状态下进行变形,约束其应变,冷却到Mf点以 下;或在马氏体状态下进行变形,约束其应变,加热 到Af点以上.也可将这二者结合起来. (4)约束ห้องสมุดไป่ตู้热法:将试样变形,约束其变形并在合金析出第二相的温度进 的行适当的加热.
马氏体相变

体片的惯习面有一定的分散度,会因马氏体片的析出先后
和形貌的不同而有所差异。
4、位向关系
由于马氏体是以切变方式形成的,这就决定了马氏体与
母相间是共格的,它们间存在确定的位向关系。
如果两相中的原子密排面或者密排方向相互平行或者接
近平行,则形成的相界能较低。
已发现的位向关系主要有:
① K-S(Kurdjumov-Sachs)关系:在Fe-1.4%C合金中发现的
故Ms点的物理意义是奥氏体与马氏体的自由能差达
到相变所需要的最小驱动力时的温度。
当T0一定时,Ms点越低,相变阻力越大,相变需要
的驱动力也越大。
因此,在Ms点处的相变驱动力可近似表达为:
GV SV (T0 M s )
2、影响马氏体相变点的因素
T0以及Ms、Mf、As、Af是表征马氏体相变的基本特征温 度,不同合金或者同一合金在不同条件下,这些特征温度 是不同的,相变的某些性质也就不同,研究影响这些特征 温度的因素对合金的应用具有重要意义。
例如,Zener阐述了在fcc结构中原子密排面上的全位错分解为两个不全 位错,不全位错之间的层错区在适当的条件下将转变为bcc结构,从而解 释了fcc→bcc的马氏体转变。
全位错分解为不全位错是能量降低的自发过程,分解后的不全位错由于 位错弹性应力场的相互排斥而分开;因此在一定条件下扩展位错有一个 平衡距离,只有层错能较低的扩展位错才有足够的宽度用于马氏体形核。 这种形核模型在有些合金中已被观察到,故有一定的实验依据。
时,奥氏体转变结束,马氏体全部转变为奥氏体。
Fe-Ni和Au-Cd合金的马氏体转变可逆性比较
冷却时的马氏体转变始于Ms点,终于Mf点;加热时奥氏 体转变始于As点,终于Af点。Fe-Ni和Au-Cd合金在加热 和冷却过程中都出现了相变滞后现象。
马氏体相变的名词解释

马氏体相变的名词解释马氏体相变是固态材料在经历加热后,发生固态相变形成马氏体的一种自发性相变过程。
这个过程是由于固态材料中的结构发生了变化,从而导致其宏观性质发生显著改变。
马氏体相变是一种重要的材料科学研究领域,具有广泛的应用价值,特别是在材料加工、制造以及机械、电子等领域。
马氏体是一种具有特殊晶体结构的金属或合金相。
通过马氏体相变,材料的原子排列发生变化,从立方晶系转变为正交晶系,这种转变导致了材料在微观尺度上的形变。
马氏体相变在材料中的应用包括增加材料的硬度、降低材料的延展性、改变材料的导电性等。
马氏体相变过程可以通过控制材料的组成、冷却速率以及外加应变等手段来实现。
根据不同的材料组成和处理方式,马氏体相变可以分为多种类型,如亚稳的马氏体相变、稳定的马氏体相变等。
亚稳的马氏体相变具有可逆性,即可以通过加热使马氏体再次转变为原有的相,而稳定的马氏体相变则是不可逆的,材料无法通过加热来回复到原有的相。
马氏体相变的研究在金属、合金和陶瓷等材料中广泛进行。
研究者们通过实验和理论模拟等方法,探索材料的晶体结构和其相变机制。
他们研究材料的组成、热处理条件以及外部应力对马氏体相变的影响,并尝试开发新的材料设计和加工方法来改变马氏体相变的性质。
在材料科学领域,马氏体相变被广泛应用于制造高强度材料、形状记忆合金和超弹性材料等。
高强度材料通过马氏体相变提高了材料的硬度和强度,在制造领域具有重要的应用价值。
形状记忆合金则是一种具有记忆效应的特殊合金材料,可以通过马氏体相变来实现形状的记忆和恢复。
超弹性材料具有很高的弹性形变能力,可以通过马氏体相变来实现材料的超大形变。
总结来说,马氏体相变是固态材料在加热过程中发生的一种自发性相变,其通过改变材料的晶体结构和原子排列来实现材料性能的改变。
马氏体相变对于材料科学的发展具有重要的意义,它在材料制造、加工以及电子等领域的应用也呈现出广阔的前景。
研究者们将继续在这一领域进行深入研究,以推动材料科学的发展和创新。
马氏体相变
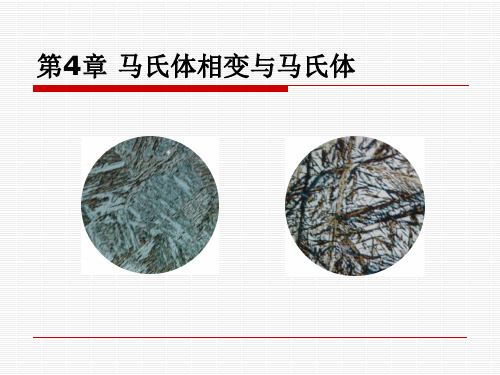
(1)低碳钢立方马氏体(<0.2%C)
板条马氏体(低碳M、位错M): 体心立方结构。具有高密度位错(约 0.3~0.9×1012cm-2 ) 的 亚 结 构 , 属 位错马氏体。其惯习面原为{111} γ , 现修改为{557} γ 。与母相的位向关系 为K-S关系。
低碳板条状马氏体 0.03C-2Mn
é ¯ Î ² ×Ö Ð Ã û ´ µ × ¬ ´ Æ × ¡ ¬ ´ ªÆ × å õ ´ ©Ì × û ´ µ × ¬ ´ Æ × ¬ ´ Æ × ¡ ¬ ´ ªÆ × ¡ ¬ ´ ªÆ ×
/ /
Fe-Ni-C £ Ni24~35% £ ¨ ¬ C~1.0%£ ©
bcc£ ¦ /£ ¨Á © bct£ ¦ /£ ¨Á ©
时,在瞬间形成大量马氏体,T~f曲线的开始阶段呈垂直上升的势态。 称爆发型马氏体相变。
自促发形核、瞬时长大
(4)弹性马氏体相变
弹性马氏体相变是指马氏 体与母相的界面可以发生 双向可逆移动。分为热弹 性和机械弹性两类。
热弹性马氏体的弹性消长
形状记忆效应
一些形状记忆合金
4.3 马氏体相变热力学
将 G 0 的温度定义为T0
Ms、Mf、As、Af、T0与合金成分的关系
As-Ms可因引入塑性变形而减少。 在Ms点以上对奥氏体进行塑性变 形,可诱发马氏体相变而使Ms点上 升到Md点。相应地,塑性变形可使 As点下降至Ad点。 Md点和Ad点分别称为形变诱发马 氏体相变开始点和形变诱发奥氏体相 变开始点。它们的极限温度均为T0。
马氏体相变
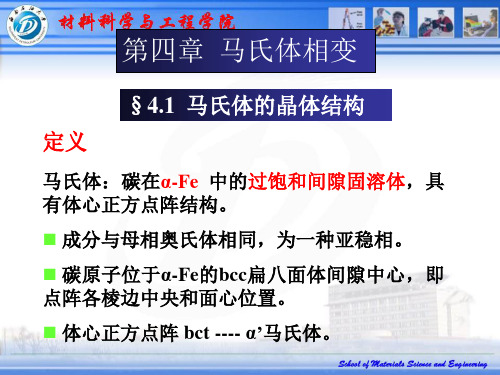
在中、高碳钢, 高镍的 Fe-Ni 合金 中出现,形成温 度较低。
图4-14 片状马氏体示意图
先形成的第一片马氏体横贯整个奥氏体晶粒,使 后形成的马氏体片的大小受到限制。后形成的马氏 体片,则在奥氏体晶粒内进一步分割奥氏透镜状,多数马氏 体片的中间有一条中脊面,相邻马氏体片互不平行, 大小不一,片的周围有一定量的残余奥氏体。
§4.3.4 工业用钢淬火马氏体的金相形态
(1)低碳钢中的马氏体 C%<0.3%的低碳钢、低碳低合金 钢,如 20# 、 15MnVB 钢等,组织为 板条马氏体,具有高强度、高韧性、 低的冷脆转化温度。
(2)中碳结构钢中的马氏体 如45#、40Cr 钢等,淬火后为板条马 氏体+片状马氏体的混合组织。 由于通常选用较低的奥氏体化温度, 淬火后获得的组织极细,光学显微镜较 难分辨。
扁八面体: 长轴为 2a ,短轴为c α-Fe点阵中的这个扁八面体间隙在短轴方向上的 半径仅为0.19埃,而碳原子有效半径为0.77埃, 因此,在平衡状态下,碳在α-Fe中的溶解度极小 (0.006%)。 一般钢中马氏体的碳含量远远超过这个数值,所 以会引起点阵发生严重畸变。 短轴方向的铁原子间距伸长36%,而在另外两个 方向则收缩4%,使体心立方变成体心正方点阵。
(1)化学成分和形成温度的影响
Ms点高 ---- 形成板条马氏体。
Ms点低 ---- 形成片状马氏体。
C%↑ → Ms ↓ 板条M → 板条M+片状M →片状M 位错M → 孪晶M
随碳含量增加及温度降低,马氏体形态由板条状向片状转化
合金元素: 缩小γ相区的元素均促使得到板条马氏体 扩大γ相区的元素均促使得到片状马氏体
亚结构为细小孪晶,一般集中在中脊面附近,片 的边缘为位错。随形成温度下降,孪晶区扩大。 马氏体片互成交角,后形成的马氏体片对先形成 的马氏体片有撞击作用,接触处产生显微裂纹。
马氏体相变及记忆.pptx

体迁移,每个原子移动的距离不超过一个原子间距,且原子之间的相对位
置不发生变化。
•
1、一些具有有序结构的合金发生马氏体转变后有序结构不发生变化;
•
2、Fe-C合金奥氏体向马氏体转变后,C原子的间隙位置保持不变;
•
3、马氏体转变可以在相当低的温度范围内进行,且转变速度极快。
例如:Fe-C、Fe-Ni合金,在-20~-196℃之间一片马氏体形成的时间约
3.马氏体相变的动力学分析 马氏体相变由于其具有转变速度快的特点,研究其动
力学转变特点很困难,可以将马氏体转变的动力学分成 三种情况。
1 马氏体降温形成(降温形核、瞬间长大)
2、等温转变(等温形核、瞬间长大)
3、表面转变
第32页/共52页
1、马氏体降温形成(降温形核、瞬间长大)
特点:
(1)由于降温形成的ΔG 很大,共格关系(势垒低,界面 阻力很小),因此形核率很大,转变速度极快,可认为 与长大速度无关; (2)爆发式转变,总转变量与温度有关 (3)细晶粒爆发量较少,晶界是爆发传递的障碍。
形变诱发马氏体相变热力学条件示意图
第25页/共52页
3、影响Ms点的主要因素
1)化学成分
(1)C%影响
C%的影响最为显,C% 升,Ms 和Mf均下降,马氏体转 变温度区间移向低温,残余奥 氏体量增加。
碳含量对MS、Mf的影响
第26页/共52页
2)合金元素
总体上: ① 除了Co、Al 提高Ms外,合金元素均有降低Ms作用。 ② 强碳化物形成元素加热时溶入奥氏体中很少,对Ms点影响不大。 ③ 合金元素对Ms点的影响表现在影响平衡温度T0和对奥氏体的强化作用。
为均匀切变。 • 造成均匀切变且惯习面为不变平面的应变即为不变平面应变。
马氏体相变的基本特征

马氏体相变的基本特征引言马氏体相变是指固体材料经过快速冷却或机械应力作用后,在普通的冷处理条件下发生的晶体结构相变现象。
马氏体相变具有广泛的应用背景,在材料科学和工程领域具有重要的意义。
本文将从马氏体相变的定义、形成机理、基本特征以及应用方面进行探讨。
马氏体相变的定义马氏体相变是指固体材料在冷却过程中经历组织相变,从高温相变为低温相的过程。
这种相变过程是一种固态相变,属于无序到有序的结构转变,通常发生在低温下。
马氏体相变的特点是快速、均匀和可逆的。
马氏体相变的形成机理马氏体相变的形成机理主要涉及晶格畸变、原子扩散和位错运动等过程。
通常情况下,当固体材料经历冷却过程时,晶格会发生畸变,从而形成新的有序结构。
这种畸变能够通过原子的扩散来进行传播,并且位错运动也会促进马氏体相变的形成。
马氏体相变的基本特征马氏体相变具有以下几个基本特征:1.快速性:马氏体相变是一个快速的相变过程,通常在毫秒至微秒的时间尺度内发生。
这种相变速度快的特点使得马氏体相变在某些应用中具有重要意义,比如形状记忆合金。
2.可逆性:马氏体相变是可逆的,即当加热到一定温度时,马氏体又会重新转变为高温相。
这种可逆性使得马氏体材料可以多次进行相变过程,具有重复使用的特点。
3.形状记忆效应:马氏体相变材料具有形状记忆效应,即在经历应力作用后,材料可以保持其原来的形状。
这种形状记忆效应使得马氏体相变材料在机械领域有广泛的应用,比如医疗器械和航空航天。
4.结构转变:马氏体相变是由无序的高温相向有序的低温相转变的过程。
在相变中,晶格结构会发生改变,从而影响材料的力学性能和磁性能等。
马氏体相变的应用马氏体相变具有广泛的应用背景,主要包括以下方面:1.形状记忆合金:马氏体相变材料在形状记忆合金中有广泛的应用。
形状记忆合金可以通过调控温度或应力来改变其形状,并且具有良好的可逆性和稳定性。
这种特性使得形状记忆合金在医疗器械、汽车工业和航空航天等领域有广泛的应用。
第4章 马氏体转变

惯习面:马面示意图
M板条或 片总是平 行于母相A 某个晶面
(5)马氏体相变的非恒温性和不完全性
M转变非恒温性的特点
1)无孕育期,在一定温度下转变不能进行 到底。 2)有转变开始和转变终了温度。M转变在 不断降温下进行,转变量是温度的函数 3)有些Ms在0℃以下的合金,可能爆发形 成 4)有些可能等温形成,但不能转变完全。
二、影响M形态和亚结构的因素
一)化学成分 C:为主要因素 C%,由M板条M片、M薄板 C<0.3% 板条状 C>1.0% 透镜片状M 0.3-1.0% 板条和片混合结构
合金元素影响(Me):
(1)缩小相区的 Me(Mo、W、Si、Al、 Nb、V等) 板条M (2)扩大相区的Me(Ni、Mn、Cu、N) 促使板条M转化为片状 能显著降低层错能的Me ’-M
(4)片状马氏体尺寸决定因素:
① 奥氏体晶粒越粗大,则马氏体片越大; ② 奥氏体晶粒越细小,则马氏体片越小。 ③当最大尺寸的马氏体片小到光学显微镜 无法分辨时,便称为隐晶马氏体。 例:高碳钢尤其是高碳合金钢,由于正常 淬火时有大量未溶碳化物,阻碍了奥氏体晶 粒的长大,晶粒细小,淬火得到的马氏体一 般都是隐晶马氏体。
(5)透镜片状马氏体的亚结构:
① 主要是孪晶。 ② 孪晶间距约为5~10nm,因此片状马氏体又称为孪 晶马氏体。 ③ 孪晶仅存在于马氏体片的中部,在片的边缘则为 复杂的位错网络。形成温度愈低,孪晶区所占比例就愈大。 ④ 片状马氏体的惯习面及位向关系与形成温度有关: 形成温度高时,惯习面为{225},位向关系为K-S关系;
形成温度低时,惯习面为{259},位向关系为西山关系。
⑤ 在马氏体针的中间有一直线,称为中脊。在 电子显微镜下可以看清楚,这个中脊面是密度很 高的微细孪晶区。
马氏体

一.马氏体的定义马氏体是经无(需)扩散的,原子集体协同位移的晶格改组过程,得到具有严格晶体学关系和惯习面的,相变常产物中伴生极高密度位错,或层错或精细孪晶等晶体缺陷的整体组合。
马氏体相变:原子经无需扩散的集体协同位移,进行晶格改组,得到的相变产物具有严格晶体学位向关系和惯习面,极高密度位错,或层错或精细孪晶等亚结构的整合组织,这种形核----长大的一级相变,称为马氏体相变。
二.马氏体相变的基本特征1.马氏体相变的无扩散性在较低的温度下,碳原子和合金元素的原子均已扩散困难。
这时,系统自组织功能使其进行无需扩散的马氏体相变。
马氏体相变与扩散性形变不同之处在于晶格改组过程中,所有原子集体协同位移,相对位移量小于一个原子间距。
相变后成分不变,即无扩散,它3仅仅是成分改组。
2.位相关系和惯习面马氏体相变的晶体学特点是新相和母相之间存在一定的位向关系。
马氏体相变时,原子不需要扩散,只作有规则的很小距离的移动,新相和母相界面始终保持着共格和半共格连接,因此相变完成之后,两相之间的位相关系仍保持着。
惯习面:马氏体转变时,新相和母相保持一定位向关系,马氏体在母相的一定晶面上形成,此晶面称为惯习面。
通常以母相的晶面指数表示。
钢中马氏体的惯习面随着碳含量和形成温度不同而异。
有色金属中马氏体的惯习面为高指数面。
3.马氏体的精细亚结构马氏体是单向组织,在组织内部出现的精细结构称为亚结构。
低碳马氏体内出现极高密度的位错(可达1012/cm)。
今年来发现板条状的马氏体中存在层错亚结构。
在高碳钢马氏体中主要以大量精细孪晶(孪晶片间距可达30nm)作为亚结构,也存在高密度位错;有的马氏体中亚结构主要是层错。
有色金属马氏体的亚结构是高密度的层错、位错和精细孪晶。
4.相变的可逆性,即新旧相界面可逆向移动有色金属和合金中的马氏体相变多具有可逆性,包括部分铁基合金。
这些合金在冷却时,母相开始形成马氏体的温度称为马氏体点(Ms),转变终了温度标为Mf;之后加热,在As温度逆转变形成高温相,逆相变完成的温度标以Af。
马氏体转变

马氏体的塑性与韧性 低碳位错型马氏体具有相当高的强度和良 好的韧性,高碳孪晶型马氏体具有高的强度 但韧性极差。 高碳孪晶型马氏体高脆性的原因:
① 亚结构为细小孪晶
② 容易产生显微裂纹
上海应用技术学院 材料工程系
School of Mechanical and Automotive Engineering 19 Anhui Polytechnic University
(4)切变共格
相变以共格切变方式进行所至。
M与A之间界面上的原子为两相共有---共格界面
上海应用技术学院 材料工程系
School of Mechanical and Automotive Engineering 6 Anhui Polytechnic University
(5)马氏体相变的变温性
School of Mechanical and Automotive Engineering 4 Anhui Polytechnic University
上海应用技术学院 材料工程系
(2)表面浮凸现象
切变过程使磨光表面出现倾动,相交表面发生 转动,形成浮凸。 原因: A已转变为M部分 引起宏观切变使点 阵改组,带动靠近 界面的未转变A发 生弹性变形。
奥氏体的热稳定化
定义:使奥氏体转变 为马氏体能力减低的 一切现象,称为奥氏 体的热稳定化。由于 冷却缓慢或中断引起
本质:
奥氏体的热稳定化是由 于在适当温度停留过程中, 奥氏体中的碳、氮原子与位 错发生交互作用形成柯氏气 团,从而强化了奥氏体,使 马氏体相变的阻力增大所致。
表现为M s 点降低、 AR 量增多。
2. 马氏体相变
低温转变<230℃(Ms线) Adolph Martens(德国) 研究最多,转变最复杂 在一个温度范围内连续冷却完 成; 无扩散转变( Fe、C原子均不扩 散 ), M与原A的成分相同,造成晶 格畸变。 转变速度极快,即瞬间形核与长 大; 转变不完全性,
马氏体相变的体积效应

马氏体相变的体积效应
马氏体相变是指,将钢从奥氏体状态快速冷却,使其来不及发生珠光体转变而形成的一种非扩散型相变。
其具有热效应和体积效应,其中体积效应是指马氏体相变过程中,由于晶体结构的变化导致体积发生膨胀。
马氏体相变的体积效应主要包括以下几个方面:
1. 奥氏体和马氏体的晶体结构不同:奥氏体的单个晶胞中含有4个原子,而马氏体的单个晶胞中只含有2个原子。
因此,在转变过程中,一个奥氏体晶胞会转变为两个马氏体晶胞,从而导致体积膨胀。
2. 马氏体是碳溶于α-Fe形成的过饱和间隙固溶体:碳在奥氏体中的最大溶解度为2.11%,在α-Fe中的溶解度为0.0218%。
在马氏体相变过程中,超出α-Fe最大溶解度的碳会把其晶格撑大,形成正方结构,从而导致体积膨胀。
3. 马氏体相变过程中的自协调效应:马氏体变态间的自协调效应会导致相变时体积发生变化。
第十二章马氏体相变

12.1.7 形变诱发马氏体转变
马氏体逆转变:把马氏体以足够快的速度加热时,马氏体可以不分
解而直接转化成奥氏体。
形变诱发马氏体转变:在Ms点以上对奥氏体进行塑性变形而促生
的马氏体转变。
形变诱发奥氏体转变:在As点以下对马氏体进行塑性变形而促生
的奥氏体。
As:马氏体逆转变开始温度
Ad
Af:马氏体逆转变终了温度
转变不 完全性
及AR
马氏体转变量与温度的关系
12.1.3 切变共格性和表面浮凸现象
(1)马氏体转变时在预先磨光的表面上产生有规则的表面浮凸。 (2)马氏体形成有惯习面,马氏体转变时马氏体与奥氏体之间保持共
格关系(第二类共格) 。
12.1.4 晶体学位向关系
马氏体转变时马氏体与奥氏体存在着严格的晶体学关系。
➢ 对于碳钢: • C%<0.3%时,板条束和板条块比较清楚; • 0.3%<C%<0.5%时,板条束清楚而板条块不清楚; • 0.6%<C%<0.8 %时,无法辨认板条束和板条块,板条组织逐渐消失
并向片状马氏体组织过渡。
➢ 与奥氏体晶粒的关系: 奥氏体晶粒越大,板条束越大,而一个原奥氏体晶粒内板条束个数基 本不变,奥氏体晶粒大小对板条宽度几乎没影响。
➢ 定义:淬火时因缓慢冷却或在冷却过程中停留,引起过冷
奥氏体稳定性提高,使马氏体转变热稳迟定滞化的程现度象可用称滞为后过温冷度奥间隔θ
氏体的热稳定化。
和残余奥氏体增量δ来表示
在TA温度停留ԏ后再继续冷却, 马氏体转变并不立即恢复,而
要冷至Ms'才重新形成马氏体。
即要滞后θ(θ=TA-Ms')度, 转变才能继续进行。与正常情
特征
条状马氏体
- 1、下载文档前请自行甄别文档内容的完整性,平台不提供额外的编辑、内容补充、找答案等附加服务。
- 2、"仅部分预览"的文档,不可在线预览部分如存在完整性等问题,可反馈申请退款(可完整预览的文档不适用该条件!)。
- 3、如文档侵犯您的权益,请联系客服反馈,我们会尽快为您处理(人工客服工作时间:9:00-18:30)。
上海应用技术学院 材料工程系
26
图4-13 (a)板条马氏体 (b)片状马氏体
上海应用技术学院 材料工程系
27
§4.3.2 片状马氏体
{225}γ或 {259}γ
在中、高碳钢, 高 镍 的 Fe-Ni 合 金 中出现,形成温 度较低。
图4-14 片状马氏体示意图
上海应用技术学院 材料工程系
17
图4-8-1 K-S关系和西山关系的比较
上海应用技术学院 材料工程系
18
5016’
图4-8-2 K-S关系和西山关系的比较
上海应用技术学院 材料工程系
19
图4-9 K-S关系和西山关系的比较
上海应用技术学院 材料工程系
20
(4)马氏体相变的变温性
MS----马氏体相变开始点。 Mf ----马氏体相变终了点。
上海应用技术学院 材料工程系
12
(3)马氏体和奥氏体具有一定的位向关系
相变以共格切变方式进行所至。 ① K-S 关系:
{111}γ∥{110}M ; <110>γ∥<111>M 由于3个奥氏体<110>γ方向上(每个方向上有2
种马氏体取向)可能有6种不同的马氏体取向, 而奥氏体的 {111}γ 晶面族中又有4种晶面, 从而马氏体共有24种取向(变体)。
钢中:<0.5%C,惯习面为{111}γ,0.5~ 1.4%C,为{225}γ,1.5~1.8%C,为{259}γ。
直线划痕在倾动面处改变方向,但仍保持连续, 且不发生扭曲。说明马氏体与母相保持切变共格, 惯习面未经宏观可测的应变和转动,即惯习面为 不变平面。
上海应用技术学院 材料工程系
10
③ 不变平面应变
图4-15 滑移和孪生的临界分切应力与温度的关系
上海应用技术学院 材料工程系
32
当马氏体在较高温度形成时,滑移的临 界分切应力较低,滑移比孪生更易于发生, 从而在亚结构中留下大量位错,形成亚结构 为位错的板条马氏体。
由于温度较高,奥氏体和马氏体的强度 均较低。相变时,相变应力的松驰可以同时 在奥氏体和马氏体中以滑移方式进行,故惯 习面为 (111)γ 。
上海应用技术学院 材料工程系
3
图4-2 点阵常数与碳含量的关系
上海应用技术学院 材料工程系
4
马氏体的正方度
c/a = 1 + 0.046 P
(4-2)
碳原子在马氏体点阵中的分布:
碳原子发生有序分布,80%优先占据c轴方向 的八面体间隙位置,20%占据其它两个方向 的八面体间隙位置,此时出现(4-2)式的正 方度。
上海应用技术学院 材料工程系
30
§4.3.3 影响马氏体形态及其亚结构的因素
(1)Ms点
Ms点高 ---- 形成板条马氏体。 Ms点低 ---- 形成片状马氏体。
C%↑ → Ms ↓ 板条M → 板条M+片状M →片状M 位错M → 孪晶M
上海应用技术学院 材料工程系
31
(2)奥氏体与马氏体的强度
上海应用技术学院 材料工程系
7
(2)表面浮凸现象和不变平面应变
① 表面浮凸现象
倾动面
图4-3 马氏体形成时引起的表面倾动
上海应用技术学院 材料工程系
8
图4-4 直线划痕的变形情况 (a)实验结果 (b)在界面处失去共格 (c)划痕扭曲
上海应用技术学院 材料工程系
9
② 惯习面和不变平面
马氏体往往在母相的一定晶面上开始形成,这 一定的晶面即称为惯习面。马氏体和母相的相界 面,中脊面都可能成为惯习面。
上海应用技术学院 材料工程系
43
§4.4.3 应变诱发马氏体
在Ms点以上一定温度范围内,因塑 性变形而促生的马氏体称为应变诱发 马氏体。
塑性变形能促生马氏体的最高温度 称为Md 点,高于此温度的塑性变形将 不会产生应变诱发马氏体。
上海应用技术学院 材料工程系
44
在Ms~Md之间对奥氏体进行塑性变形, 为向马氏体转变提供了机械驱动力,从
上海应用技术学院 材料工程系
35
(2)中碳结构钢中的马氏体
如45#、40Cr 钢等,淬火后为板 条马氏体+片状马氏体的混合组织。
由于通常选用较低的奥氏体化温 度,淬火后获得的组织极细,光学 显微镜较难分辨。
上海应用技术学院 材料工程系
36
(3)高碳工具钢中的马氏体
如 T8、T12钢,为片状马氏体。
图4-11 转变量-温度关系
上海应用技术学院 材料工程系
22
(5)马氏体相变的可逆性
A↔M
Ms , Mf ; As , Af ; As > Ms
钢中马氏体加热时,容易发生回火分解, 从马氏体中析出碳化物。
Fe-0.8%C钢以5000℃/S快速加热,抑制回 火转变,则在590~600℃发生逆转变。
上海应用技术学院 材料工程系
28
先形成的第一片马氏体横贯整个奥氏体晶 粒,使后形成的马氏体片的大小受到限制。 后形成的马氏体片,则在奥氏体晶粒内进一 步分割奥氏体晶粒,所以后形成的马氏体片 越来越短小。
片状马氏体的立体外形呈双凸透镜状,多 数马氏体片的中间有一条中脊面,相邻马氏 体片互不平行,大小不一,片的周围有一定 量的残余奥氏体。
温度
图4-19 奥氏体与马氏体的自由能-温度曲线示意图
上海应用技术学院 材料工程系
42
(2)其它因素对Ms 点的影响
① 奥氏体的晶粒大小 奥氏体晶粒细化 → Ms ↓ 晶粒细化 → σs ↑→ 切变阻力↑ → Ms ↓
② 弹性极限以内的应力 多向压应力阻碍马氏体转变,→ Ms ↓ 拉应力促进马氏体转变,→ Ms ↑
上海应用技术学院 材料工程系
13
5016’
图4-6 奥氏体 (111)面上马氏体的六种不同K-S取向
上海应用技术学院 材料工程系
14
② 西山关系:
{111}γ∥{110}M ; <112>γ∥<110>M
按西山关系,在每个{111}γ面上,马氏 体可能有3种取向,故马氏体共有12种 取 向(变体)。
若奥氏体的σS超过206MPa,相变应力在两
相中均以孪生方式松弛,则形成惯习面为 (259)γ的片状马氏体。
上海应用技术学院 材料工程系
34
§4.3.4 工业用钢淬火马氏体的金相形态
(1)低碳钢中的马氏体
C%<0.2%的低碳钢、低碳低合金 钢,如20#、15MnVB钢等,组织为 板条马氏体,具有高强度、高韧性、 低的冷脆转化温度。
通常采用不完全加热淬火(在Ac1稍 上加热,保留一定量未溶渗碳体颗 粒),获得隐晶马氏体+渗碳体颗粒的 混合组织。
隐晶马氏体极细,光学显微镜较难 分辨。
上海应用技术学院 材料工程系
37
§4.4 马氏体相变热力学 §4.4.1 相变驱动力
T0 为 相 同 成 分 的 马 氏体和奥氏体两相热 力学平衡温度,此时
③ 解释:
碳或者合金元素降低A3点,降低奥氏体的自 由能并提高马氏体(过饱和铁素体)的自由能, 也降低了T0 温度,从而降低Ms 点。
碳或者合金元素固溶强化了奥氏体,σs ↑,使 切变所需能量增高,Ms ↓。
上海应用技术学院 材料工程系
41
临界驱动力
G
A ΔGA→M
ΔGA→M
M
Ms
T0 Ms
T0
而使相变可以在较高的温度发生,即相
当于升高了Ms温度。
在Ms~Md温度范围的塑性变形度越大, 由形变诱发的马氏体量越大。但对未转 变的奥氏体,在随后的冷却过程中,马 氏体相变却受到了抑制(发生了机械稳 定化)。
上海应用技术学院 材料工程系
45
图4-20 应变诱发马氏体相变热力学条件
上海应用技术学院 材料工程系
上海应用技术学院 材料工程系
33
随着形成温度的下降,孪生的临界分切应力 较低,变形方式逐渐过渡为以孪生进行,形成 亚结构为孪晶的片状马氏体。
若奥氏体的σS低于206MPa,应力在奥氏体
中以滑移方式松弛。由于形成的马氏体强度较 高,应力在马氏体中只能以孪生方式松弛,则 形成惯习面为 (225)γ的片状马氏体。
每个惯习面上可能有六种不同的取向,板条束 内具有相同取向的小块称为板条块,常常呈现为 黑白相间的块。
上海应用技术学院 材料工程系
25
板条马氏体的亚结构为高密度位错,所以板 条马氏体也称为位错马氏体 。
不呈孪晶关系的板条间存在一层残余奥氏体 簿膜,这种微量的残余奥氏体对板条马氏体的 韧性贡献很大。
上海应用技术学院 材料工程系
15
图4-7 奥氏体 (111)面上马氏体的三种不同西山取向
上海应用技术学院 材料工程系
16
③ G-T关系:
和 K-S关系略有偏差 {111}γ∥{110}M 差10 <110>γ∥<111>M 差20
④ K-S关系和西山关系的比较: 晶面关系相同,只是晶面内的方向相差 5016’。
第四章 马氏体相变
§4.1 马氏体的晶体结构
马氏体----碳在α-Fe 中的过饱和固溶体。 成分与母相奥氏体相同,为一种亚稳相。 碳原子位于α-Fe的bcc扁八面体间隙中心, 即点阵各棱边中央和面心位置。 体心正方点阵 bct ---- α’马氏体。
上海应用技术学院 材料工程系
1
图4-1 奥氏体的正八面体间隙 a) 马氏体的扁八面体间隙 b)
MS 点以下,无需孕育, 转变立即开始,且以极大
速度进行,但很快停止,
不能进行到终了,需进一 步降温。
图4-10 转变量-时间关系