精馏塔设计
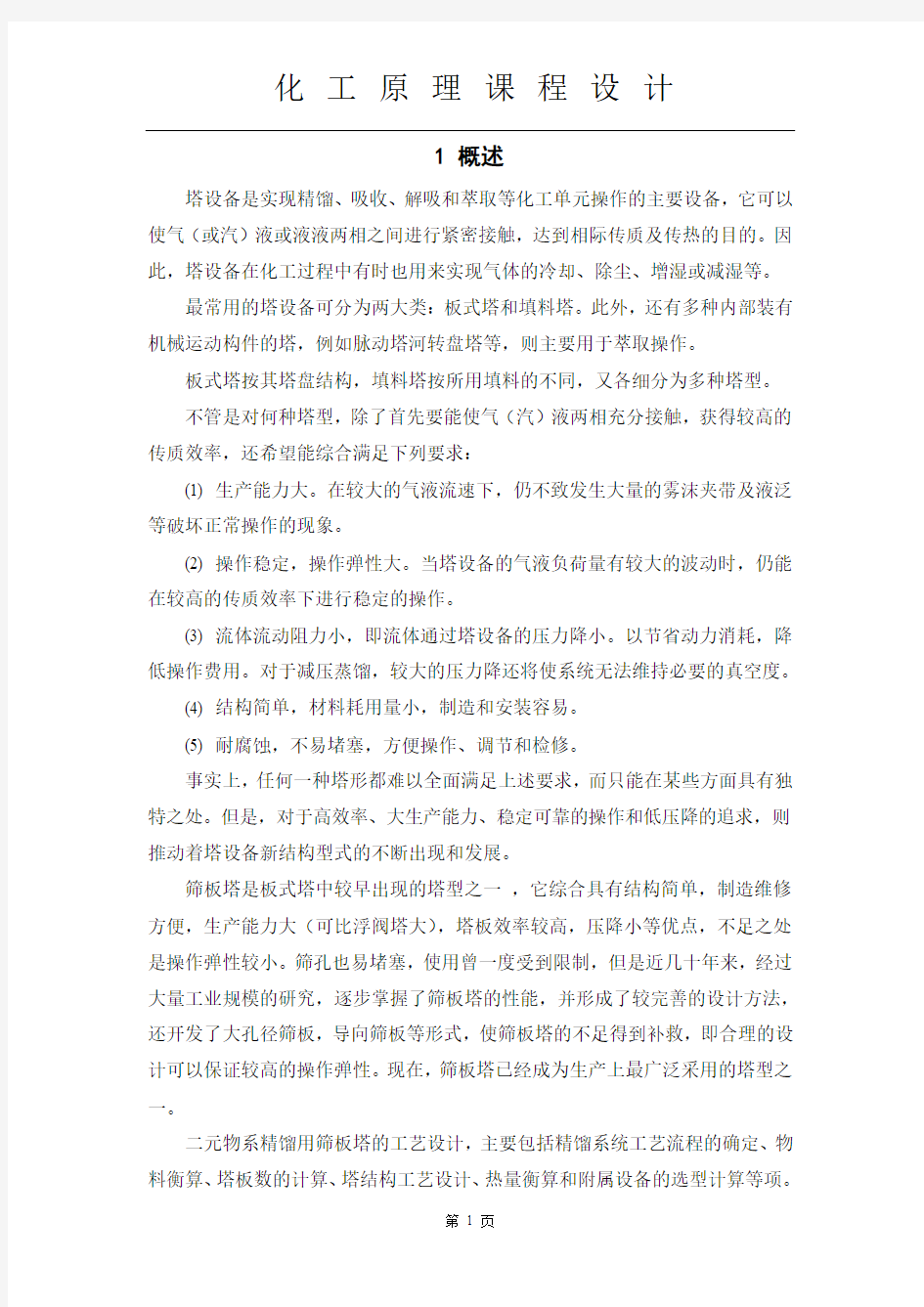

1 概述
塔设备是实现精馏、吸收、解吸和萃取等化工单元操作的主要设备,它可以使气(或汽)液或液液两相之间进行紧密接触,达到相际传质及传热的目的。因此,塔设备在化工过程中有时也用来实现气体的冷却、除尘、增湿或减湿等。
最常用的塔设备可分为两大类:板式塔和填料塔。此外,还有多种内部装有机械运动构件的塔,例如脉动塔河转盘塔等,则主要用于萃取操作。
板式塔按其塔盘结构,填料塔按所用填料的不同,又各细分为多种塔型。
不管是对何种塔型,除了首先要能使气(汽)液两相充分接触,获得较高的传质效率,还希望能综合满足下列要求:
(1) 生产能力大。在较大的气液流速下,仍不致发生大量的雾沫夹带及液泛等破坏正常操作的现象。
(2) 操作稳定,操作弹性大。当塔设备的气液负荷量有较大的波动时,仍能在较高的传质效率下进行稳定的操作。
(3) 流体流动阻力小,即流体通过塔设备的压力降小。以节省动力消耗,降低操作费用。对于减压蒸馏,较大的压力降还将使系统无法维持必要的真空度。
(4) 结构简单,材料耗用量小,制造和安装容易。
(5) 耐腐蚀,不易堵塞,方便操作、调节和检修。
事实上,任何一种塔形都难以全面满足上述要求,而只能在某些方面具有独特之处。但是,对于高效率、大生产能力、稳定可靠的操作和低压降的追求,则推动着塔设备新结构型式的不断出现和发展。
筛板塔是板式塔中较早出现的塔型之一,它综合具有结构简单,制造维修方便,生产能力大(可比浮阀塔大),塔板效率较高,压降小等优点,不足之处是操作弹性较小。筛孔也易堵塞,使用曾一度受到限制,但是近几十年来,经过大量工业规模的研究,逐步掌握了筛板塔的性能,并形成了较完善的设计方法,还开发了大孔径筛板,导向筛板等形式,使筛板塔的不足得到补救,即合理的设计可以保证较高的操作弹性。现在,筛板塔已经成为生产上最广泛采用的塔型之一。
二元物系精馏用筛板塔的工艺设计,主要包括精馏系统工艺流程的确定、物料衡算、塔板数的计算、塔结构工艺设计、热量衡算和附属设备的选型计算等项。
2 精馏工艺流程确定
本设计任务为分离乙醇——水混合物,对于二元混合物的分离采用连续精馏过程,设计中采用泡点进料,将原料液通过预热器加热至泡点,用泵送入精馏塔内,塔顶蒸汽采用全凝气冷凝,冷凝液在泡点下一部分回流至塔内,剩余部分经产品冷却器后送至储罐,塔釜采用分离式间接蒸汽渐热。(附图1,所需工艺流程)
3、精馏塔的物料衡算
3.1、原料液、馏出液、釜液组成
3.1.1、原料液组成
已知 水的摩尔质量:M 水=46.07 kg.mol-1 乙醇摩尔质量:M 乙=18.02 kg.mol-1 质量分率:ωF =25.60 % 摩尔分率:
124
.002
.18)
265.01(07.46265.007
.46265
.01=-+
=
-+
=
水
乙
乙
M
M M x F F
F
F ωωω
3.1.2、馏出液组成
质量分率:ωD =90.70% 摩尔分率:
水
乙
乙
M
M M x D D
D
D ωωω-+
=
1
792.002
.18907.0107.46907.007
.46907
.0=-+
=
)
(
3.1.3、釜液组成
质量分率:ωW =1.04%
摩尔分率:水
乙
乙
M
M M x
W W
W
W
ωωω-+
=
1
00409.002
.180104.0107.460104.007
.460104
.0=-+
=
)
(
3.2、物料衡算
3.2.1、质量流量
全塔物料横算式: m F =m D +m W
m F ωF =m D ωD +m w ωw
并已知m F =8300kg.h-1,代入数据得 8300=m D +mW
8300?0.265=m D ?0.907+m w ?0.0104 联立,解方程得 m D =2356.882 kg·h-1 m w =5943.118 kg·h-1 3.2.2、摩尔流量
原料液的平均摩尔质量
()
()1
498.21124.0102.18124.007.461-?=-?+?=-+=kmol
kg x M x M M
F
F F
水乙
原料液的摩尔流量
1
082.386498
.218300-?===h
kmol M
m F F
F
全塔物料衡算式: F=D+W
Fx F =Dx D +Wx w 代入数据: 386.082=D+W
386.082?0.124=D ?0.792+W
0.00409 解方程得
D=59.250 kmol·h-1 W=326.832 kmol·h-1 3.2.3、体积流量 (1)、进料体积流量
由于采用饱和溶液(泡点)进料,须查ωF =26.50%时,气液混合物的泡点,即当液相组成为0.124时的沸点。
查表
[1]
,用内插法查得当ωF =26.05%时,饱和溶液进料时进料温度
t F =85.635 ℃
查表[2],用内插法查得当t F =85.635 ℃时,水的密度水ρ=968.137 kg ·m-3 查表[3],当t F =85.635 ℃时,乙醇的相对密度为0.735 ,因此乙醇的密度乙ρ= 735 kg ·m -3
进料时混合物的密度
水
乙)(ρωρωρF F F -+
=
11
()
069.893137
.967265.01735
265.01
=-+
=
kg·m-3
进料体积流量
1
33
1
3
1
3
10
58.200258.0m 294.9069
.8938300m ----??=?=?===
s
m s
m h
V F F
F ρ
(2)、馏出液体积流量
由于采用饱和溶液(泡点)进料,须查ωD =0.907%时,气液混合物的泡点,即当液相组成为0.792时的沸点。
查图
[1]
,用内插法查得当ω
D =0.907时,饱和溶液进料时进料温度
t D =78.543 ℃
查图[2],用内插法查得当t D =78.543 ℃时,水的密度水ρ=972.674 kg ·m -3
查图[3]
,当t D =78.8 ℃时,乙醇的相对密度为0.741 ,因此乙醇的密度乙ρ= 741 kg ·m -3
时混合物的密度
()
()
674
.972907
.01741
907.01
11
-+
=
-+
=
水
乙
ρωρωρD D D
= 757.786 kg ·m -3 进料体积流量 V D =
D
D
m ρ
786
.757882.2356=
=3.110m 3·h -1 =0.000864 m 3·s -1=8.64×10-4m 3·s -1
(3)、釜液体积流量
由于采用饱和溶液(泡点)进料,须查ωw =0.0104%时,气液混合物的泡点,即当液相组成为0.00409时的沸点。
查图[1],用内插法查得当ωw =0.0104时,饱和溶液进料时进料温度t W =99.987℃
查图[2]
,用内插法查得当t W =99.987℃时,水的密度水ρ=958.409 kg ·m -3
查图[3],当t W =99.987℃时,乙醇的相对密度为0.722 ,因此乙醇的密度乙ρ= 722 kg ·m -3
进料时混合物的密度
()
()409
.9580104
.017220104.01
11
-+=
-+
=
水
乙
ρωρωρw w w
= 955.156 kg ·m -3
进料体积流量 V W =
W
W
m ρ
156
.955118.5943=
= 6.222 m 3·h -1 =0.00173 m 3·s -1=1.73×10-3 m 3·s -1
3.3、结果汇总表
表1
质量分率/%
摩尔分率/%
进料液 26.5 12.4 溜出液 90.7 79.2 釜液
1.04
0.409
表2
质量流量/㎏?h-1 摩尔流量/mol ?h-1 体积流量/m3?h-1 体积流量m3?s-1 进料液 8300 419.747 9.294 2.58×10-3 馏出液 2356.882 59.250 3.110 8.63×10-4 釜液
5943.118
326.832
6.222
1.73×10-3
4、塔板数的确定
4.1、理论塔板数的确定
4.1.1、最小回流比Rmin
以(x D ,x D )做直线与气液相平衡线相切,此直线即为最小回流比时的精馏段操作线,如附图2:
由图读取操作线截距
=+1
Rmin D χ0.402
由此计算出最小回流比 Rmin =0.970 4.1.2、求最小理论塔板数Nmin
当全回流时,y n+1=x n ,全塔无精馏段,提留段之分,操作线与相平衡线最远,达到分离要求所需要的塔板数最小,即Nmin.。要求 N min ,先确定全回流状态下的平均相对挥发度由图解法得(附图3)
Nmin =758.6)
00105.00136.0()00409.00136.0(6)
00105.00.0136()x 0136.0(6=--+
=--+
w 块
故去掉塔釜后min N =6.758-1=5.758 块 (不包含再沸器) 4.1.3、选取适宜回流比
由《化工原理 下册》吉利兰夫关联式 Y=0.75×(1-X 0.567) X=
1
min +-R R R
1
min
+-=
Y N N N
通常情况下,适宜的回流比取为最小回流比的1.1-7倍,
在R=(1.1~7)Rmin 范围内取12个回流比,分别利用吉利兰夫关联式求出与其对应的N 值并在直角坐标图上画出N-R 曲线,确定合适的回流比R
例如:取R=1.1Rmin =1.11?0.97=1.654 X 1=0.04692;Y 1=0.6176;N 1=16.6744
数据整理: 表 1
K R X Y N 1.1 1.067 0.0469 0.6176 16.6744 1.5 1.455 0.1976 0.4510 11.3089 2 1.94 0.3299 0.3500 9.3977 2.5 2.425 0.4248 0.2884 8.4971 3 2.91 0.4962 0.2459 7.9622 3.5 3.395 0.5518 0.2147 7.6051 4 3.88 0.5963 0.1906 7.3490 4.5 4.365 0.6328 0.1714 7.1559 5 4.85 0.6632 0.1558 7.0050 5.5 5.335 0.6890 0.1428 6.8837 6 5.82 0.7111 0.1318 6.7840 6.5 6.305 0.7303 0.1224 6.7007 7
6.79
0.7471
0.1143
6.6299
由附图4可以看出在(2.0~3.0)Rmin 时,曲线开始变平缓,取为最佳回流比的范围,即附图4的阴影部分,取R=2.525 ; N=8.375
4.2 操作线方程
由回流比R=
D
L 且D=59.250 kmol ·h -1
,1882.2356-?=h kg m D ,13110.3-?=h m V D
1
606.149
250.59525.2-?=?==h kmol RD L 1
127.5951882.2356
525.2-?=?==h kg Rm m D L 1331310181.2853.7110.3525.2---??=?=?==s m h m RV V D L
由于是泡点进料,则q=1 因此 L + F = L ′ V ′= V = L + D
代入数据,得L ′=149.606+386.082=535.6881-?h kmol V= V ′=149.606+59.250=208.856 1-?h kmol 又 '=+L F L m m m D L x x m m m m +=='
代入数据得 1127.142518300127.5951'-?=+=h kg m L
1
009.8303882.2356127.5951'-?=+==h kg m m v v
V L ’=V L + V F
=7.853+9.294=17.147 13-?h m =4.76313310--??s m 数据整理: 表格 2
质量流量
/kg.h-1
摩尔流量/kmol.h-1 体积流量/m3.h-1 体积流量
V L (m3.s-1) 精馏段下降液体量 5951.127 149.606 7.853
2.181×10-3
精馏段上升蒸汽量 8303.009 208.856
提溜段下降液体量 14251.127 535.688 17.147
4.763×10-3
提溜段上升蒸汽量
8303.009
208.856
4.2.1 精馏段操作线方程
1
1
1++
+=
+R x x R R y D n n
R=2.525 XD =0.792 因此精馏段操作线方程为 225.0716.01+=+n n x y 4.2.2 提溜段操作线方程
m
m m x w
L w x w
L L y -'-
-''=
+1
L '1
688.535-?=h
kmol 1
832.326
-?=h k m o l W 00409.0=w x
因此提溜段操作线方程为
00640
.0565.21
-=+m
x
m y
4.2.3 q 线方程
由于采用泡点进料,则q=1 q 线方程 1
1
--
-=
q x x q q y F
可得 124.0==F x x 4.2.4 用逐板计算出理论塔板数
由y 1=x D =0.792
查表[4]
查,用内插法查得与y1=0.792时,成相平衡的液相组分x 1=0.759 代x 1=0.792入精馏段操作线方程,y n+1=0.716x n +0.225 y 2=0.716?0.759+0.225=0.768 由x 1,y 1可求得相对挥发度α 1
209
.1)759
.0759.01)(
792
.01792.0(
)
1)(1(
11
1
11=--=--=x x y y α
由y 2=0.768,查得x 2=0.722
742
.0225.0722.0716.03=+?=y
α2=1.278
由y 3=0.742,查得x 3=0.682
713.0225.0682.0716.04=+?=y
α3=1.341
由y 4=0.713,查得x 4=0.634
679
.0225.0634.0716.05=+?=y
α4=1.436
由y 5=0.679,查得x 5=0.564
628
.0225.0564.0716.06=+?=y
α5=1.638
由y 6=628,查得x 6=0.438
539
.0225.0438.0716.07=+?=y
α6=2.170
由y 7=0.539,查得216.07=x
380
.0225.0216.0716.08=+?=y
α6=2.170
由y 8=0.380,查得0684.08=x
216.0124.00684
.078=<=<=x x x F α8=8.348 因此,精馏段理论板数=623
.70684
.0216.0124.0216.07=--+
块
将0684.08=x 代入提馏段操作线方程 :0064
.0565.21
-=+m
x
m y
182
.00064.00684.0565.29=+?=y
由y 9=0.182,查得x 9=0.0193 y 10=2.565?0.0193+0.0064=0.0559 α9=11.306
由y 10=0.0559,查得x 10=0.00512 y 11=2.565?0.00512+0.0064=0.0195 α10=11.495
由y 11=0.0195,查得x 11=0.00512 .1000157 .000512.000409.000512.010=--+块(包括塔底再沸器) α10.29851.4)00409 .000409.01)( 0195 .010195.0( =--= 提溜段理论板数为(10.290-1)-7.623 =1.667块 理论塔板数总汇: 表格 3 板数 x y α 1 0.759 0.792 1.209 2 0.722 0.768 1.278 3 0.682 0.742 1.341 4 0.634 0.713 1.436 5 0.564 0.679 1.638 6 0.438 0.628 2.170 7 0.216 0.539 4.225 7.623 0.124 0.380 4.330 8 0.0684 0.380 8.348 9 0.0193 0.182 11.306 10 10.29 0.00512 0.00409 0.0559 0.0195 11.495 4.851 4.3、总板效率η的估计 4.3.1、平均挥发度 由于乙醇-水物系为非理想物系,α随x 的变化不可忽略,将前面所算出的α值,以相近为原则。将前所算出的α数据分为N 组并求平均值 由 n n x 1-n x 2x 1x x x x 1x --= --中中 得 29 .10102110.29 1x x x x x x x x --= --中中 代入数据: 00409 .000512.0722.0759.000409 .0x 759.0--= --中中x 求得:中 x =0.0246 由0246.0x =中内插法 查得216.0y =中 )1)(1( 中 中中中中 x x y y --=∴α 926.10)0246 .00246.01)( 216 .01216.0( =--= 因此平均相对挥发度 00141 .4851.4924.10209.13 29 .1013 13 =??= = = ααααααα中中n 4.3.2、加料摩尔组成的液体平均摩尔粘度μav 以塔顶温度与塔底温度的平均值作为定性温度 C t t t o w D 265 .892 987 .99543.782 =+= += 查表[5],用内插法得265.89=t ℃时s mPa ?=3187.0水μ 查图[6],用内插法得265.89=t ℃时s mPa ?=393.0乙μ 以加料摩尔组成为准的液体平均摩尔粘度 s mPa x x x F F i i ?=?-+?=-+== ∑328.03187.0124.01393.0124.0)1()(水 乙μμμ μ 4.3.3、估计总板效率η E 可用奥康乃尔关联图的回归方程 ()()()[]% 2.53532.0328.000141.4lg 0815.0328.000141.4lg 276.056 3.0log 0815.0log 276.0563.022 ==?+?-=+-=μ αμαE 此总板效率为: % 5.58585.0532.01.11.1==?==E η 4.3.4 实际板数的确定 精馏段理论板数N 1=7.623块,故实际板数为 块 031.13585 .0623.71 1=== ηN N e 取实际板数为14块, 故为实际加料板为15层 提馏段理论塔板数N 2=1.667块,故实际板数为 块850.2585 .0667.12 2=== η N N e 取实际板数为3块 因此全塔实际板数为18块(不包含塔底再沸器). 5、塔板结构的工艺设计 在本设计中采用精馏段和提溜段塔径相同,故设计时的塔顶第一块板为设计基准 5.1、初选塔板间距H T 板间距对塔的液沫夹带量和液泛汽速有影响,在一定的气液负荷及塔径条件下,适当增加板间距可以减少液沫夹带量,且不易发生液泛,从而提高了操作负荷的上下限,但是,板间距与塔径直接相关,其值不宜过大。 现取H T =450mm 5.2、塔径初算 5.2.1液泛气速u F 第一板气液组分 x 1=0.759 906 .002 .18)792.01(07.46792.007 .46792.0)1(747 .0890 .002 .18)759.01(07.46759.007 .46759.0)1(111111111=?-+??= -+= ==?-+??= -+= 水 乙乙 水 乙乙 M y M y M y y M x M x M x G L ωω 查图[4]查,用内插法查得,第一快板的温度为t=78.6℃ 查表[2] 查,用内插法查得 t=78.6℃时,σ水=62.838mN ·m -1 查图[7] 查,t=78.6℃时,σ乙醇 =17.4 mN ·m -1 混合物的表面张力: 1 35.28838.62759.014.17759.01-?=?-+?=-+=m mN x x D D )()(水 乙σσσ 查图[8],当ωG1=0.906时,气体密度ρG =1.41 kg ·m-3 查表[2] ,t=78.6℃时,ρ乙醇=741 kg ·m -3 查表[3] ,t=78.6℃时,ρ水=972.640 kg ·m -3 () () 3 -m kg 760.934 640 .972890.01741 890.01 11 ?=-+ = -+ = 水 乙 ρωρωρL L L 液体体积流量 1 3 L m 821.7934 .760127.5951V -?== = ' h m L L ρ 133L m 10172.2V --??=s 气体体积流量 0308 .041 .1934.7605892 821.7''FP : m 637.1V m 589241 .1009.8308V 1 3 G 1 3v G =? = = ?=?== =' --G L G L G V V s h m ρρρ汽液流动参数 查图[9],气体负荷参数C 20=0.0849 取液泛分率为0.8,得出塔的有效截面积为 2 n m 969.0113 .28.0637.1u 8.0A =?= = F G V 取A d /A=0.08 , 则塔的总截面积为 2 0533.108 .01969.0A m =-= D= m 758.10533 .14=?π 大于1m 按200mm 递增圆整, 圆整后塔径 D=1200mm 实际操作气速 1 447.13600 2.15892 44 2 2 -?=???= ' = s m D V G ππ μ 5.2.2、塔径的核算 液泛分率: 685.0113 .2447.1==F u u 查图[10],得液沫分率 ψ=0.07<0.10,设计合理,塔径D=1200mm 5.3、塔板上溢流型式的确定 溢流型塔板,流体流动须要克服板上汽液接触元件所引起的阻力,形成液面落差,于是气体较多地从塔板上底液位处通过,影响汽体均匀分布降低板效率,然而筛板塔形成的液面落差小,这一因素影响不大,根据《筛板式精馏塔的设计》表二板上溢流形式与塔径塔体负荷关系中查得塔径与液体流量以及溢流形式 的关系进行综合考虑选择单流型。 5.4、塔板布置 设计降液管形式的弓形降液管,把堰与壁之间的全部截面区域作为降液面积,弓形降液板,塔板面积利用率高。如下图所示: 5.4.1、筛孔孔径 孔径的大小直接影响塔板操作性能。在开孔率、空塔气速和液流量相同的条件下增大孔径,虽可减小板压降,不易阻塞,但漏液量增大,操件弹性降低。一般工业上常用的孔径经常取3~8mm ,通常用d 0=4~6mm 的孔径。孔径太小加工制造困难,而且易堵,结合本设计d 0=5mm 为宜。 5.4.2、筛孔中心距t 0和开孔率φ0 开孔一般采用正三角形排列,筛孔中心距t 0一般为(2.5~5)d 0,t 0、d 0过小,易相互干扰,过大则鼓泡不均匀,都会影响传质效率,实际设计时, 0d t 宜 可能取3~4范围内。本设计取 0d t =3.15为宜 2 00 9069.0??? ? ??=o t d ? =0.9069×( 15 .31)2=0.0914 所以开孔率φ0为9.14%,小于10%,大于5%,符合要求 5.4.3、 筛板厚度tp 在塔板结构强度、刚度许可的条件下,应尽可能选用较薄的板材制作筛板,这不仅可以降低干板压降,而且可以改善气液接触状态。筛孔用冲压加工制造的筛板,其厚度的选取范围为 t p =(0.4~0.8)d 0,本设计采用t p =0.7d 0为宜 t p =0.6 d 0 =0.6×5=3.00mm 5.4.4、溢流堰长l w 溢流堰具有保持塔板上一定的液层高度和促使液流均匀分布的作用,常用的溢流堰长为 L W =(0.68~0.76)D 由于溢流堰过长则堰上溢流强度低,且塔板构件的安装误差,液体越堰时分布不均;堰长不够则堰上液流强度高,堰上液头大,影响塔板操作的稳定性,也不利于液流中的气液分离。本设计L W =0.68D 为宜。 L W =0.68×1200=816mm 堰上溢流强度Li : 1 -2 1 -2 h m 60h m 585.9816 .0821.7?==' =W L l V Li 符合要求 5.4.5、堰板高度h w (1)堰上液头h ow 弗兰西斯经验式 3 /2W L W oW L V 0.0028F h ? ?? ? ? ? '= F W 为弓形堰板校正系数,可由附图 [11] mm m D L W 0793.130130793.00.8167.8211.035250.0028h 025 .1F 72.0438 .9864 .0549.6L 'V 3 /2OW W 5 .25 .2W L ==? ? ? ????===== 查得且 查横坐标 (2)堰板高度一般为h w =h L -h ow , h L 为清液层高度,取h L =50~100mm 本设计取h L =60mm ,h w =60-h ow =80-13.1=46.9mm 所求堰高为46.9mm ,在25~75mm 范围内,符合要求。 5.4.6、降液管下沿与塔板板间距t a 第三章设备选型-精馏塔设计说明书3.1 概述 本章是对各种塔设备的设计说明与选型。 3.2设计依据 气液传质分离用的最多的为塔式设备。它分为板式塔和填料塔两大类。板式塔和填料塔均可用作蒸馏、吸收等气液传质过程,但两者各有优缺点,根据具体情况进行选择。设计所依据的规范如下: 《F1型浮阀》JBT1118 《钢制压力容器》GB 150-1998 《钢制塔式容器》JB4710-92 《碳素钢、低合金钢人孔与手孔类型与技术条件》HG21514-95 《钢制压力容器用封头标准》JB/T 4746-2002 《中国地震动参数区划图》GB 18306-2001 《建筑结构荷载规范》GB50009-2001 3.3 塔简述 3.3.1填料塔简述 (1)填料塔 填料塔是以塔内的填料作为气液两相间接触构件的传质设备,由外壳、填料、填料支承、液体分布器、中间支承和再分布器、气体和液体进出口接管等部件组成。 填料是填料塔的核心,它提供了塔内气液两相的接触面,填料与塔的结构决定了塔的性能。填料必须具备较大的比表面,有较高的空隙率、良好的润湿性、耐腐蚀、一定的机械强度、密度小、价格低廉等。常用的填料有拉西环、鲍尔环、弧鞍形和矩鞍形填料,20世纪80年代后开发的新型填料如QH—1型扁环填料、八四内弧环、刺猬形填料、金属板状填料、规整板波纹填料、格栅填料等,为先进的填料塔设计提供了基础。 填料塔适用于快速和瞬间反应的吸收过程,多用于气体的净化。该塔结构简单,易于用耐腐蚀材料制作,气液接触面积大,接触时间长,气量变化时塔的适应性强,塔阻力小,压力损失为300~700Pa,与板式塔相比处理风量小,空塔气速通常为0.5-1.2 m/s,气速过大会形成液泛,喷淋密度6-8 m3/(m2.h)以保证填料润湿,液气比控制在2-10L/m3。填料塔不宜处理含尘量较大的烟气,设计时应克服塔内气液分布不均的问题。 (2)规整填料 塔填料分为散装填料、规整填料(含格栅填料) 和散装填料规整排列3种,前2种填料应用广泛。 在规整填料中,单向斜波填料如JKB,SM,SP等国产波纹填料已达到国外MELLAPAK、FLEXIPAC等同类填料水平;双向斜波填料如ZUPAK、DAPAK 等填料与国外的RASCHIG SUPER-PAK、INTALOX STRUCTURED PACKING 同处国际先进水平;双向曲波填料如CHAOPAK等乃最新自主创新技术,与相应型号的单向斜波填料相比,在分离效率相同的情况下,通量可提高25% -35%,比国外的单向曲波填料MELLAPAK PLUS通量至少提高5%。上述规整填料已成功应用于φ6400,φ8200,φ8400,φ8600,φ8800,φ10200mm等多座大塔中。 (3)板波纹填料 板波纹填料由开孔板组成,材料薄,空隙率大,加之排列规整,因而气体通过能力大,压降小。其比表面积大,能从选材上确保液体在板面上形成稳定薄液 在一常压操作的连续精馏塔内分离水—乙醇混合物。已知原料的处理量为2000吨、组成为36%(乙醇的质量分率,下同),要求塔顶馏出液的组成为82%,塔底釜液的组成为6%。设计条件如下: 操作压力 5kPa(塔顶表压); 进料热状况自选; 回流比自选; 单板压降≤0.7kPa; 根据上述工艺条件作出筛板塔的设计计算。 【设计计算】 (一)设计方案的确定 本设计任务为分离水—乙醇混合物。对于二元混合物的分离,应采用连续精馏流程。 设计中采用泡点进料,将原料液通过预料器加热至泡点后送入精馏塔内。塔顶上升蒸气采用全凝器冷凝,冷凝液在泡点下一部分回流至塔内其余部分经产品冷却器冷却后送至储罐。该物系属易分离物系,最小回流比较小,故操作回流比取最小回流比的1.5倍。塔釜采用间接蒸汽加热,塔底产品经冷却后送至储罐。 (二)精馏塔的物料衡算 1.原料液及塔顶、塔底产品的摩尔分率 M=46.07kg/kmol 乙醇的摩尔质量 A M=18.02kg/kmol 水的摩尔质量 B F x =18.002 .1864.007.4636.007.4636.0=+= D x =64.002 .1818.007.4682.007.4682.0=+= W x =024.002.1894.007.4606.007.4606.0=+= 2.原料液及塔顶、塔底产品的平均摩尔质量 F M =0.18×46.07+(1-0.18)×18.02=23.07kg/kmol D M =0.64×46.07+(1-0.64)×18.02=35.97kg/kmol W M =0.024×46.07+(1-0.024)×18.02=18.69kg/kmol 3.物料衡算 以每年工作250天,每天工作12小时计算 原料处理量 F = 90.2812 25007.2310002000=???kmol/h 总物料衡算 28.90=W D + 水物料衡算 28.90×0.18=0.64D+0.024W 联立解得 D =7.32kmol/h W =21.58kmol/h (三)塔板数的确定 1. 理论板层数T N 的求取水—乙醇属理想物系,可采用图解法求理论板层数。 ①由手册查得水—乙醇物系的气液平衡数据,绘出x —y 图,如图。 ②求最小回流比及操作回流比。 采用作图法求最小回流比。在图中对角线上,自点e(0.18 , 0.18)作垂线ef 即为进料线(q 线),该线与平衡线的交点坐标为 q y =0.52 q x =0.18 故最小回流比为 min R =q q q D x y y x --=35.018 .0-52.052.0-64.0=3 取操作回流比为 R =min R =1.5×0.353=0.53 ③求精馏塔的气、液相负荷 L =RD =17.532.753.0=?=kmol/h V =D R )1(+=(0.53+1)20.1132.7=?kmol/h 精馏塔的设计及选型 目录 精馏塔的设计及选型 (1) 目录 (1) 1设计概述 0 1.1工艺条件 0 1.2设计方案的确定 0 2塔体设计计算 (1) 2.1有关物性数据 (1) 2.2物料衡算 (3) 2.3塔板数的确定 (4) 2.4精馏塔的工艺条件及相关物性数据 (8) 2.5塔体工艺尺寸的设计计算 (11) 2.6塔板工艺尺寸的设计计算 (14) 2.7塔板流体力学验算 (18) 2.8负荷性能图 (22) 2.9精馏塔接管尺寸计算 (27) 3精馏塔辅助设备的设计和选型 (31) 3.1原料预热器的设计 (32) 3.2回流冷凝器的设计和选型 (34) 3.3釜塔再沸器的设计和选型 (38) 3.4泵的选择 (40) 3.5筒体与封头 (41) 1设计概述 1.1工艺条件 (1)生产能力:2836.1kg/d(料液) (2)工作日:250天,每天4小时连续运行 (3)原料组成:35.12%丙酮,64.52%水,杂质0.35%,由于杂质含量较小且不会和丙酮一起蒸馏出去,所以可以忽略。所以此母液可以视为仅含丙酮和水两种成分,其质量组成为:35.12%丙酮,水64.88%(下同) (4)产品组成:馏出液99%丙酮溶液,回收率为90%,由此可知塔釜残液中丙酮含量不得高于5.16% 即每天生产99%的丙酮905.54kg。 (5)进料温度:泡点 (6)加热方式:间接蒸汽加热 (7)塔顶压力:常压 (8)进料热状态:泡点 (9)回流比:自选 (10)加热蒸气压力:0.5MPa(表压) (11)单板压降≤0.7kPa 1.2设计方案的确定 (1)、精馏方式及流程: 在本设计中所涉及的浓度范围内,丙酮和水的挥发度相差比较大,容易分离,且丙酮和水在操作条件下均为非热敏性物质,因此选用常压精馏,并采取连续精馏方式。母液经过换热器由塔底采出液预热到泡点,在连续进入精馏塔内,塔顶蒸汽经过塔顶冷凝器冷凝后,大部分连续采出,采出部分经冷却器后进入储罐内备用,少部分进行回流;塔底液一部分经过塔釜再沸器气化后回到塔底,一部分连续采出,采出部分可用于给原料液预热。塔顶装有全凝器,塔釜设有再沸器,进料输送采用离心泵,回流液采用高位槽输送。 (2)、进料状态:泡点进料。 (3)、加热方式:间接蒸汽加热。 (4)、加热及冷却方式:原料用塔釜液预热至泡点,再沸器采用间接蒸汽加热,塔顶全凝器采用自来水作为冷却剂。优点是成本低,腐蚀性小,黏度小,比热容 3.5筛板精馏塔设计示例 3.5.1 化工原理课程设计任务书 设计题目:分离苯-甲苯混合液的筛板精馏塔 在一常压操作的连续精馏塔内分离苯-甲苯混合液。已知原料液的处理量为4000kg/h,组成为0.41(苯的质量分率),要求塔顶馏出液的组成为0.96,塔底釜液的组成为0.01。 设计条件如下:表3-18 操作压力 进料热状态回流比单板压降全塔效率建厂地址 4kPa(塔顶常压)自选自选w0.7kPa ET=52%天津地区 试根据上述工艺条件作岀筛板塔的设计计算。 3.5.2 设计计算1设计方案的确定 本设计任务为分离苯一甲苯混合物。对于二元混合物的分离,应采用连续精馏流程。设计中采用泡点进料, 将原料液通过预热器加热至泡点后送人精馏塔内。塔顶上升蒸气采用全凝器冷凝,冷凝液在泡点下一部分回流至塔内,其余部分经产品冷却器冷却后送至储罐。该物系属易分离物系,最小回流比较小,故操作回流比取最小回流比的2倍。塔釜采用间接蒸汽加热,塔底产品经冷却后送至储罐。 2精馏塔的物料衡算 (1)原料液及塔顶、塔底产品的摩尔分率 苯的摩尔质量—~':'■- 甲苯的摩尔质量匚丁 0.41/78. H 0.41/78J1 +0.59/92.13 (2)原料液及塔顶、塔底产品的平均摩尔质量 二0.450X7E.11 + (l-0 450)x9213 =託尾如畑H ^=0.966x78 1U(1-0.9 13 few? ^ = 0.012x73.11 + (1-0.012)x92.13 = 91.9^/^? (3 )物料衡算 F = = 46.6 A 原料处理量二二一 0.450 总物料衡算46.61 = D+ W 苯物料衡算46.6 1X0.45 = 0.966D + 0.012 W 联立解得D = 21.40 kmol / h W=25.21kmol/h 3塔板数的确定 (1)理论板层数NT的求取 苯一甲苯属理想物系,可采用图解法求理论板层数。 ①由手册查得苯一甲苯物系的气液平衡数据,绘出x~y图,见图3-22。 ②求最小回流比及操作回流比。 采用作图法求最小回流比。在图3-19中对角线上,自点e(0.45,0.45 )作垂线ef即为进料线(q线),该线与平衡线的交点坐标为 y q = 0.667 xq = 0.450 故最小回流比为? 2 1■' 取操作回流比为77■■ ■―■:--' ③求精馏塔的气、液相负荷 L = R^D= 2.76x 21.40 = 7+1)D =(2 76 +l)x 21 40 = 80.46^;^ Z r= L + ^ = 59.06+46,^1 = 分离乙醇-水的精馏塔设计设计人员: 所在班级:化学工程与工艺成绩: 指导老师:日期: 化工原理课程设计任务书 一、设计题目:乙醇---水连续精馏塔的设计 二、设计任务及操作条件 (1)进精馏塔的料液含乙醇35%(质量分数,下同),其余为水; (2)产品的乙醇含量不得低于90%; (3)塔顶易挥发组分回收率为99%; (4)生产能力为50000吨/年90%的乙醇产品; (5)每年按330天计,每天24小时连续运行。 (6)操作条件 a)塔顶压强 4kPa (表压) b)进料热状态自选 c)回流比自选 d)加热蒸汽压力低压蒸汽(或自选) e)单板压降 kPa。 三、设备形式:筛板塔或浮阀塔 四、设计内容: 1、设计说明书的内容 1)精馏塔的物料衡算; 2)塔板数的确定; 3)精馏塔的工艺条件及有关物性数据的计算; 4)精馏塔的塔体工艺尺寸计算; 5)塔板主要工艺尺寸的计算; 6)塔板的流体力学验算; 7)塔板负荷性能图; 8)精馏塔接管尺寸计算; 9)对设计过程的评述和有关问题的讨论; 2、设计图纸要求; 1)绘制生产工艺流程图(A2 号图纸); 2)绘制精馏塔设计条件图(A2 号图纸); 五、设计基础数据: 1.常压下乙醇---水体系的t-x-y 数据; 2.乙醇的密度、粘度、表面张力等物性参数。 一、设计题目:乙醇---水连续精馏塔的设计 二、设计任务及操作条件:进精馏塔的料液含乙醇35%(质量分数,下同),其余为 水;产品的乙醇含量不得低于90%;塔顶易挥发组分回收率为99%,生产能力为50000吨/年90%的乙醇产品;每年按330天计,每天24小时连续运行。塔顶压强 4kPa (表压)进料热状态自选回流比自选加热蒸汽压力低压蒸汽(或自选)单板压降≤0.7kPa。 三、设备形式:筛板塔 四、设计内容: 1)精馏塔的物料衡算: 原料乙醇的组成 xF==0.1740 原料乙醇组成 xD0.7788 塔顶易挥发组分回收率90% 平均摩尔质量 MF = 由于生产能力50000吨/年,. 则 qn,F 所以,qn,D 2)塔板数的确定: 板式精馏塔设计方案 第三节精馏方案简介 (1) 精馏塔的物料衡算; (2) 塔板数的确定: (3) 精馏塔的工艺条件及有关物件数据的计算; (4) 精馏塔的塔体工艺尺寸计算; (5) 塔板主要工艺尺寸的计算; (6) 塔板的流体力学验算: (7) 塔板负荷性能图; (8) 精馏塔接管尺寸计算; (9) 绘制生产工艺流程图; (10) 绘制精馏塔设计条件图; (11) 对设计过程的评述和有关问题的讨论。 设计方案的确定及工艺流程的说明 原料液由泵从原料储罐中引岀,在预热器中预热至84 C后送入连续板式精馏塔(筛板塔),塔顶上升蒸汽 流采用强制循环式列管全凝器冷凝后一部分作为回流液,其余作为产品经冷却至25 C后送至产品槽;塔釜采用热虹吸立式再沸器提供气相流,塔釜残液送至废热锅炉。 第四节:精馏工艺流程草图及说明 、流程方案的选择 1. 生产流程方案的确定: 原料主要有三个组分:C2°、C3二、C3°,生产方案有两种:(见下图A , B )如 任务书规定: 图(A ) 为按挥发度递减顺序采出,图(B )为按挥发度递增顺序采出。在基本有机化工 生产过程中,按挥发度递减的顺序依次采出馏分的流程较常见。 因各组分采出之 前只需一次汽化和冷凝,即可得到产品。而图(B )所示方法中,除最难挥发组 分外。其它组分在采出前需经过多次汽化和冷凝才能得到产品, 能量(热量和冷 量)消耗大。并且,由于物料的循环增多,使物料处理量加大,塔径也相应加大, 再沸器、冷凝器的传热面积相应加大,设备投资费用大,公用工程消耗增多,故 应选用图(A )所示的是生产方案。 2. 工艺流程分离法的选择: 在工艺流程方面,主要有深冷分离和常温加压分离法。 脱乙烷塔,丙烯精制 塔采用常温加压分离法。因为 C2, C3在常压下沸点较低呈气态采用加压精馏沸 点可提高,这样就无须冷冻设备,可使用一般水为冷却介质,操作比较方便工艺 简单,而且就精馏过程而言,获得高压比获得低温在设备和能量消耗方面更为经 济一些,但高压会使釜温增加,引起重组分的聚合,使烃的相对挥发度降低,分 离难度加大。可是深冷分离法需采用制冷剂来得到低温, 采用闭式热泵流程,将 精馏塔和制冷循环结合起来,工艺流程复杂。综合考滤故选用常温加压分离法流 程。 1、 脱乙烷塔:根据原料组成及计算:精馏段只设四块浮伐 塔板,塔顶采用分 凝器、全回流操作 2、 丙烯精制塔:混合物借精馏法进行分离时它的难易程度取决 于混合 物的沸点差即取决于他们的相对挥发度丙烷一丙烯的 C2 C3 = C3 ° iC4 W% 5.00 73.20 20.80 0.52 0.48 100 工艺特点: 原料 C 工 C 。 (A ) (B ) 精馏塔设计 目录 § 1 设计任务书 (1) § 1.1 设计条件 (1) § 2 概述 (1) § 2.1 塔型选择 (1) § 2.2 精馏塔操作条件的选择 (3) § 2.3 再沸器选择 (4) § 2.4 工艺流程 (4) § 2.5 处理能力及产品质量 (4) § 3 工艺设计 (5) § 3.1 系统物料衡算热量衡算 (5) § 3.2 单元设备计算 (9) § 4 管路设计及泵的选择 (28) § 4.1 进料管线管径 (28) § 4.2 原料泵P-101的选择 (31) § 5 辅助设备的设计和选型 (32) § 5.1 贮罐………………………………………………………………………………… 32 § 5.2 换热设备…………………………………………………………………………… 34 § 6 控制方案…………………………………………………………………………………… 34 附录1~………………………………………………………………………………………… 35 参考文献………………………………………………………………………………………… 37 后 记 (38) §1 设计任务书 §1.1 设计条件 工艺条件:饱和液体进料,进料量丙烯含量x f =65%(摩尔百分数) 塔顶丙烯含量D x =98%,釜液丙烯含量w x ≤2%,总板效率为0.6。 操作条件:建议塔顶压力1.62MPa (表压) 安装地点:大连 §2 概述 蒸馏是分离液体混合物(含可液化的气体混合物)常用的一种单元操作,在化工、炼油、石油化工等工业中得到广泛的应用。其中,简单蒸馏与平衡蒸馏只能将混合物进行初步的分离。为了获得较高纯度的产品,应 分离乙醇—水混合液的筛 板精馏塔设计 This model paper was revised by the Standardization Office on December 10, 2020 课题名称:化工课程设计任务书 系别:化环学院 专业:化工2班 学号: 姓名: 指导教师: 时间:2011年12月01-16日 附 化工原理—化工设备机械基础课程设计任务书-1专业化工班级 0409402 设计人 一. 设计题目 分离乙醇—水混合液的筛板精馏塔设计 二. 原始数据及条件 生产能力:年处理量8万吨(开工率300天/年),每天工作24小时; 原料:乙醇含量为20%(质量百分比,下同)的常温液体; 分离要求:塔顶,乙醇含量不低于90%, 塔底,乙醇含量不高于 8%; 操作条件: 三. 设计要求: (一)编制一份设计说明书,主要内容包括: 1. 前言 2. 设计方案的确定和流程的说明 3. 塔的工艺计算 4. 塔和塔板主要工艺尺寸的设计 a. 塔高、塔径及塔板结构尺寸的确定 b. 塔板的流体力学验算 c. 塔板的负荷性能图 5. 附属设备的选型和计算 6. 设计结果一览表 7. 注明参考和使用的设计资料 8. 对本设计的评述或有关问题的分析讨论。 (二)绘制一个带控制点的工艺流程图(2#图) (三)绘制精馏塔的工艺条件图(1#图纸) 四. 设计日期:2011年 12月01日至 2011 年12 月16日 五. 指导教师:谭志斗、石新雨 推荐教材及主要参考书: 1.王国胜, 裴世红,孙怀宇. 化工原理课程设计. 大连:大连理工大学出版社,2005 2.贾绍义,柴诚敬.化工原理课程设计. 天津:天津科学技术出版社,2002. 3、马江权,冷一欣. 化工原理课程设计. 北京:中国石化出版社,2009. 4、《化工工艺设计手册》,上、下册; 5、《化学工程设计手册》;上、下册; 6、化工设备设计全书编辑委员会.化工设备设计全书-塔设备;化学工业出版社:北京. 2004,01 简单填料精馏塔设计 设计条件与任务: 已知F 、xF 、xD 、xw 或F 、xF 、xD 和η,塔顶设全凝器,泡点回流,塔底间接(直接)蒸汽加热。 1 全塔物料衡算求产品流量与组成 (1)常规塔 全塔总物料衡算 总物料 F = D + W 易挥发组分 F χF = D χD + W χW 若以塔顶易挥发组分为主要产品,则回收率η为 D F Dx Fx η= 式中 F 、D 、W ——分别为原料液、馏出液和釜残液流量,kmol/h ; χF 、χD 、χW ——分别为原料液、馏出液和釜残液中易挥发组分的摩尔分率。 由(3-1)和(3-2)式得: W D W F x x x x F D --= (2) 直接蒸汽加热 总物料 * 0F S D W +=+ 易挥发组分 ** 00F D W Fx S y Dx W x +=+ 式中 V 0 ——直接加热蒸汽的流量,kmol/h ; У0 ——加热蒸汽中易挥发组分的摩尔分率,一般У0=0; W * ——直接蒸汽加热时釜液流量,kmol/h ; χ*W ——直接蒸汽加热时釜液中易挥发组分的摩尔分率。 2 计算最小回流比 设夹紧点在精馏段,其坐标为(xe,ye)则 min D e e e x y R y x -= - 设夹紧点在提馏段,其坐标为(xe,ye) min min (1)(1)e W e W y x R D qF L V R D q F x x -+==+--- 基础数据:气液相平衡数据 3 确定操作回流比 min (1.1~2.0)R R = 4 计算精馏段、提馏段理论板数 ① 理想溶液 图解法或求出相对挥发度用逐板计算法求取。 ② 非理想溶液 相平衡数据为离散数据,用图解法或数值积分法求取 精馏段 1 1 R D f N x R x n n dx N dN x x += =-? ? 因 111 D n n x R y x R R += +++ 所以 ()/D f x R x n n D n dx N y x x y R = ---? (4) 提馏段 1 1 S f W N x S x n n dx N dN x x += =-? ? 因 11 W n n x R y x R R +'+= -'' 蒸汽回流比(1)(1)(1)(1)V R D q F D F R R q W W W W +--'= ==+-- 所以 ()/(1) f w x S x n n n w dx N y x y x R = '---+? (5) 式(4)、(5)中塔板由下往上计数。 5 冷凝器和再沸器热负荷 冷凝器的热负荷 ()C DV DL Q V I I =- 再沸器的热负荷 B C D W F Q Q DI WI FI =++- 待求量:进料温度t F 、塔顶上升蒸汽温度t DV (与x D 对应的露点温度)、回流温度t DL (与x D 对应的泡点温度)、再沸器温度tw (与x W 对应的泡点温度)。 物性数据: ① 各组分在平均温度下的液相热容、气相热容或汽化热。 ② 各组分的热容方程常数 如 2 3 p c A BT CT DT =+++ ③ 由沃森公式计算汽化热 21 0.38211( )1r V V r T H H T -?=?- ∠1∶10 设计数量 职务姓名日期制图校核审核审定批准 比例 图幅 1∶20 A1 版次 设计项目设计阶段 毕业设计施工图 精馏塔 重量(Kg) 单件总重备注 件号 图号或标准号 名称 材料12345基础环 筋板盖板垫板静电接地板14824241Q235-A Q235-A Q235-A Q235-A Q235-A Q235-A Q235-A Q235-A Q235-A Q235-A Q235-A Q235-A·F 16MnR Q235-A 6 789 10 111213 14151617JB4710-92 GB/T3092-93HG20594-97JB4710-92GB/T3092-93HG20594-97JB4710-92 GB/T3092-93HG20594-97HG5-1373-80引出孔 φ159×4.5引出管 DN40法兰 PN1.0,DN40排气管 φ80接管 DN20,L=250法兰 PN1.0,DN20液封盘 塔釜隔板筒体 φ1600×16进料管 DN32法兰 PN1.0,DN32吊柱 111411111111 6.723.931.55322.7 94.2374.19140.62.97 5.382.364.67 1.170.411.0321.9376181210.69 2.02380Q235-A·F Q235-A 1111111311177511组合件16MnR Q235-A Q235-A Q235-A Q235-A Q235-A Q235-A 45Q235-A·F Q235-A Q235-A Q235-A Q235-A 组合件Q235-A 111111224Q235-A 16MnR Q235-A Q235-A Q235-A Q235-A Q235-A 1819202122232425 2627282930313233343536 3738394041 扁钢 8×16HG20594-97HG20594-97HG20594-97HG20594-97GB/T3092-93GB/T3092-93GB/T3092-93HG8162-87JB/T4737-95HG20594-97HG20594-97GB/T3092-93GB/T3092-93GB/T3092-93JB/T4736-95HG21515-95HJ97403224-3HJ97403224-7JB/T4734-95JB4710-92JB4710-921Q235-A HG20652-1998JB/ZQ4363-86上封头DN1600×16接管 DN20,L=250法兰 PN1.0,DN20出气管 DN600法兰 PN1.0,DN600接管 DN20,L=250法兰 PN1.0,DN20气体出口挡板回流管 DN45法兰 PN1.0,DN45补强圈 DN450×8人孔 DN450塔盘接管 DN20,L=250法兰 PN1.0,DN20下封头DN1600×16裙座筒体 法兰 PN1.0,DN20引出管 DN20引出孔 φ133×4检查孔 排净孔地脚螺栓M42×4.5GB704-88370.70.411.0382.3248.10.411.031.874.150.962.36118.3 310.10.411.03370.738021.032.612.2442.540.6 16.944.3δ=8 1 40 6 23 45 41 39 38 37789 10 1112 3635 34 33 3213 14 31 15 1630 2917 28 2726 25 24 2318 19 202122 a b c d e f i g h j1 k l n m5 m7 Ⅵ Ⅴ Ⅳ Ⅲ Ⅱ Ⅰ 技术要求 1、本设备按GB150-1998《钢制压力容器》和HG20652-95《钢制化工容器制造技术要求》进行 制造、试验和验收,并接受劳动部颁发《压力容器安全技术监察规程》的监督;2、焊条采用电弧焊,焊条牌号E4301; 3、焊接接头型式及尺寸,除图中标明外,按HG20583-1998规定,角焊缝的焊接尺寸按较薄板 厚度,法兰焊接按相应法兰中的规定; 4、容器上A、B类焊缝采用探伤检查,探伤长度20%; 5、设备制造完毕后,卧立以0.2MPa进行水压试验; 6、塔体直线允许度误差是H/1000,每米不得超过3mm,塔体安装垂直度允差是最大30mm; 7、裙座螺栓孔中心圆直径允差以及相邻两孔或任意两弦长允差为2mm; 8、塔盘制造安装按JB1205《塔盘技术条件》进行; 9、管口及支座方位见接管方位图。 技术特性表 管口表 总质量:27685 Kg e m1-7a f i g h j2n j4 l j3 k j1 b c d j3 序号 项 目指 标11 109 87654 3 21设计压力 MPa 设计温度 ℃工作压力 MPa 工作温度 ℃工作介质主要受压元件许用应力 MPa 焊缝接头系数腐蚀裕量 mm 全容积 m 容器类别 0.11500.027102 筒体、封头、法兰1700.58157.9327符号公称尺寸连接尺寸标准紧密面 型式用途或名称b c d e f g h i j1-4k l m1-7n 2060020453220202020402045040 HG20594-97HG20594-97HG20594-97HG20594-97HG20594-97HG20594-97HG20594-97HG20594-97HG20594-97HG20594-97HG20594-97HG20594-97 HG21515-95凹凹凹凹凹凹凹凹凹凹凹凹凹 温度计口气相出口压力计口回流口进料口液面计口液面计口温度计口排气管口至再沸器口出料口人孔再沸器返回口 313028263335373929 2732 3436 38404142 43 444546 474849 505125 24 2322 21201918 1716 151******** 8 7654 32114m6 m7 m5 m4 m3 m2 m1 1 2 3 4 5 30 31 32 33 3435 5051管口方位示意图 A、B类焊缝 1:2 整体示意图1:2 Ⅵ Ⅴ 1:5 1:5 Ⅳ A B B向 A向 Ⅲ 1:5 Ⅱ 1:5 Ⅰ 1:10 平台一 平台二 357 2901 第三章 精馏塔工艺设计计算 塔设备是化工、石油化工、生物化工、制药等生产过程中广泛采用的气液传质设备。根据塔内气液接触构件的结构形式,可分为板式塔和填料塔两大类。 板式塔内设置一定数量的塔板,气体以鼓泡或喷射形势穿过板上的液层,进行传质与传热,在正常操作下,气象为分散相,液相为连续相,气相组成呈阶梯变化,属逐级接触逆流操作过程。 本次设计的萃取剂回收塔为精馏塔,综合考虑生产能力、分离效率、塔压降、操作弹性、结构造价等因素将该精馏塔设计为筛板塔。 3.1 设计依据[6] 3.1.1 板式塔的塔体工艺尺寸计算公式 (1) 塔的有效高度 T T T H E N Z )1( -= (3-1) 式中 Z –––––板式塔的有效高度,m ; –––––塔内所需要的理论板层数; –––––总板效率; –––––塔板间距,m 。 (2) 塔径的计算 u V D S π4= (3-2) 式中 D –––––塔径,m ; –––––气体体积流量,m 3 u –––––空塔气速, u =(0.6~0.8) (3-3) V V L C u ρρρ-=m a x (3-4) 式中 L ρ–––––液相密度,3 V ρ–––––气相密度,3 C –––––负荷因子, 2 .02020?? ? ??=L C C σ (3-5) 式中 C –––––操作物系的负荷因子, L σ–––––操作物系的液体表面张力, 3.1.2 板式塔的塔板工艺尺寸计算公式 (1) 溢流装置设计 W OW L h h h += (3-6) 式中 L h –––––板上清液层高度,m ; OW h –––––堰上液层高度,m 。 3 2100084.2??? ? ??=W h OW l L E h (3-7) 式中 h L –––––塔内液体流量,m ; E –––––液流收缩系数,取1。 h T f L H A 3600= θ≥3~5 (3-8) 006.00-=W h h (3-9) ' 360000u l L h W h = (3-10) 式中 u 0ˊ–––––液体通过底隙时的流速,。 (2) 踏板设计 开孔区面积a A : ??? ? ? ?+-=-r x r x r x A a 1 222s i n 1802π (3-11) 1 / 2 ∠1∶10 设计数量 职务姓名日期制图校核审核审定批准 比例 图幅 1∶20 A1 版次 设计项目设计阶段 毕业设计施工图 精馏塔 重量(Kg) 单件总重备注 件号 图号或标准号 名称 材料1 2345基础环 筋板盖板垫板静电接地板14824241Q235-A Q235-A Q235-A Q235-A Q235-A Q235-A Q235-A Q235-A Q235-A Q235-A Q235-A Q235-A·F 16MnR Q235-A 6 789 10111213 14151617JB4710-92 GB/T3092-93HG20594-97JB4710-92GB/T3092-93HG20594-97JB4710-92 GB/T3092-93HG20594-97HG5-1373-80引出孔 φ159×4.5引出管 DN40法兰 PN1.0,DN40排气管 φ80接管 DN20,L=250法兰 PN1.0,DN20液封盘 塔釜隔板筒体 φ1600×16进料管 DN32法兰 PN1.0,DN32吊柱 111411111111 6.723.931.55322.7 94.2374.19140.62.97 5.382.364.67 1.170.411.0321.9376181210.69 2.02380Q235-A·F Q235-A 1111111311177511组合件16MnR Q235-A Q235-A Q235-A Q235-A Q235-A Q235-A 45Q235-A·F Q235-A Q235-A Q235-A Q235-A 组合件Q235-A 111111224Q235-A 16MnR Q235-A Q235-A Q235-A Q235-A Q235-A 1819202122232425 2627282930313233343536 3738394041 扁钢 8×16HG20594-97HG20594-97HG20594-97HG20594-97GB/T3092-93GB/T3092-93GB/T3092-93HG8162-87JB/T4737-95HG20594-97HG20594-97GB/T3092-93GB/T3092-93GB/T3092-93JB/T4736-95HG21515-95HJ97403224-3HJ97403224-7JB/T4734-95JB4710-92JB4710-921Q235-A HG20652-1998JB/ZQ4363-86上封头DN1600×16接管 DN20,L=250法兰 PN1.0,DN20出气管 DN600法兰 PN1.0,DN600接管 DN20,L=250法兰 PN1.0,DN20气体出口挡板回流管 DN45法兰 PN1.0,DN45补强圈 DN450×8人孔 DN450塔盘接管 DN20,L=250法兰 PN1.0,DN20下封头DN1600×16裙座筒体 法兰 PN1.0,DN20引出管 DN20引出孔 φ133×4检查孔 排净孔地脚螺栓M42×4.5GB704-88370.70.411.0382.3248.10.411.031.874.150.962.36118.3 310.10.411.03370.738021.032.612.2442.540.6 16.944.3δ=8 1 40 6 23 45 41 39 38 37789 10 1112 3635 34 33 3213 14 31 15 1630 2917 28 2726 25 24 2318 19 202122 a b c d e f i g h j1 k l n m5 m7 Ⅵ Ⅴ Ⅳ Ⅲ Ⅱ Ⅰ 技术要求 1、本设备按GB150-1998《钢制压力容器》和HG20652-95《钢制化工容器制造技术要求》进行 制造、试验和验收,并接受劳动部颁发《压力容器安全技术监察规程》的监督;2、焊条采用电弧焊,焊条牌号E4301; 3、焊接接头型式及尺寸,除图中标明外,按HG20583-1998规定,角焊缝的焊接尺寸按较薄板 厚度,法兰焊接按相应法兰中的规定; 4、容器上A、B类焊缝采用探伤检查,探伤长度20%; 5、设备制造完毕后,卧立以0.2MPa进行水压试验; 6、塔体直线允许度误差是H/1000,每米不得超过3mm,塔体安装垂直度允差是最大30mm; 7、裙座螺栓孔中心圆直径允差以及相邻两孔或任意两弦长允差为2mm; 8、塔盘制造安装按JB1205《塔盘技术条件》进行; 9、管口及支座方位见接管方位图。 技术特性表 管口表 总质量:27685 Kg e m1-7a f i g h j2n j4 l j3 k j1 b c d j3 序号 项 目指 标11 109 87654 3 21设计压力 MPa 设计温度 ℃工作压力 MPa 工作温度 ℃工作介质主要受压元件许用应力 MPa 焊缝接头系数腐蚀裕量 mm 全容积 m 容器类别 0.11500.027102 筒体、封头、法兰1700.58157.9327符号公称尺寸连接尺寸标准紧密面 型式用途或名称b c d e f g h i j1-4k l m1-7n 2060020453220202020402045040 HG20594-97HG20594-97HG20594-97HG20594-97HG20594-97HG20594-97HG20594-97HG20594-97HG20594-97HG20594-97HG20594-97HG20594-97 HG21515-95凹凹凹凹凹凹凹凹凹凹凹凹凹 温度计口气相出口压力计口回流口进料口液面计口液面计口温度计口排气管口至再沸器口出料口人孔再沸器返回口 313028263335373929 2732 3436 38404142 43 444546 474849 505125 24 2322 21201918 1716 151******** 8 7654 32114m6 m7 m5 m4 m3 m2 m1 1 2 3 4 5 30 31 32 33 3435 5051管口方位示意图 A、B类焊缝 1:2 整体示意图1:2 Ⅵ Ⅴ 1:5 1:5 Ⅳ A B B向 A向 Ⅲ 1:5 Ⅱ 1:5 Ⅰ 1:10 平台一 平台二 357 2901 精馏塔尺寸设计计算 初馏塔的主要任务是分离乙酸和水、醋酸乙烯,釜液回收的乙酸作为气体分离塔吸收液及物料,塔顶醋酸乙烯和水经冷却后进行相分离。塔顶温度为102℃,塔釜温度为117℃,操作压力4kPa。 由于浮阀塔塔板需按一定的中心距开阀孔,阀孔上覆以可以升降的阀片,其结构比泡罩塔简单,而且生产能力大,效率高,弹性大。所以该初馏塔设计为浮阀塔,浮阀选用F1型重阀。在工艺过程中,对初馏塔的处理量要求较大,塔内液体流量大,所以塔板的液流形式选择双流型,以便减少液面落差,改善气液分布状况。 4.2.1 操作理论板数和操作回流比 初馏塔精馏过程计算采用简捷计算法。 (1)最少理论板数N m 系统最少理论板数,即所涉及蒸馏系统(包括塔顶全凝器和塔釜再沸器)在全回流下所需要的全部理论板数,一般按Fenske方程[20]求取。 式中x D,l,x D,h——轻、重关键组分在塔顶馏出物(液相或气相)中的摩尔分数; x W,l,x W,h——轻、重关键组分在塔釜液相中的摩尔分数; αav——轻、重关键组分在塔内的平均相对挥发度; N m——系统最少平衡级(理论板)数。 塔顶和塔釜的相对挥发度分别为αD=1.78,αW=1.84,则精馏段的平均相对挥发度: 由式(4-9)得最少理论板数: 初馏塔塔顶有全凝器与塔釜有再沸器,塔的最少理论板数N m应较小,则最少理论板数:。 (2)最小回流比 最小回流比,即在给定条件下以无穷多的塔板满足分离要求时,所需回流比R m,可用Underwood法计算。此法需先求出一个Underwood参数θ。 求出θ代入式(4-11)即得最小回流比。 式中——进料(包括气、液两相)中i组分的摩尔分数; c——组分个数; αi——i组分的相对挥发度; θ——Underwood参数; ——塔顶馏出物中i组分的摩尔分数。 进料状态为泡点液体进料,即q=1。取塔顶与塔釜温度的加权平均值为进料板温度(即计算温度),则 在进料板温度109.04℃下,取组分B(H2O)为基准组分,则各组分的相对挥发度分别为αAB=2.1,αBB=1,αCB=0.93,所以 利用试差法解得θ=0.9658,并代入式(4-11)得 (3)操作回流比R和操作理论板数N0 操作回流比与操作理论板数的选用取决于操作费用与基建投资的权衡。一般按R/R m=1.2~1.5的关系求出R,再根据Gilliland关联[20]求出N0。 取R/R m=1.2,得R=26.34,则有: 查Gilliland图得 解得操作理论板数N0=51。 4.2.2 实际塔板数 (1)进料板位置的确定 对于泡点进料,可用Kirkbride提出的经验式进行计算。 化工原理课程设计任务书 专业:班级: 姓名: 学号: 设计时间: 设计题目:乙醇——水筛板精馏塔工艺设计 (取至南京某厂药用酒精生产现场) 设计条件: 1. 常压操作,P=1 atm(绝压)。 2. 原料来至上游的粗馏塔,为95——96℃的饱和蒸汽。因沿 程热损失,进精馏塔时原料液温度降为90℃。 3. 塔顶产品为浓度92.41%(质量分率)的药用乙醇,产量为 40吨/日。 4.塔釜排出的残液中要求乙醇的浓度不大于0.03%(质量分 率)。 5.塔釜采用饱和水蒸汽加热(加热方式自选);塔顶采用全凝器,泡点回流。 。 6.操作回流比R=(1.1——2.0)R min 设计任务: 1. 完成该精馏塔工艺设计,包括辅助设备及进出口接管的计 算和选型。 2.画出带控制点的工艺流程图,t-x-y相平衡图,塔板负 荷性能图,筛孔布置图以及塔的工艺条件图。 3.写出该精流塔的设计说明书,包括设计结果汇总和对自己 设计的评价。 指导教师:时间 1设计任务 1.1 任务 1.1.1 设计题目乙醇—水筛板精馏塔工艺设计(取至南京某厂药用酒 精生产现场) 1.1.2 设计条件 1.常压操作,P=1 atm(绝压)。 2.原料来至上游的粗馏塔,为95-96℃的饱和蒸气。 因沿程热损失,进精馏塔时原料液温度降为90℃。 3.塔顶产品为浓度92.41%(质量分率)的药用乙醇, 产量为40吨/日。 4.塔釜排出的残液中要求乙醇的浓度不大于0.03% (质量分率)。 5.塔釜采用饱和水蒸气加热(加热方式自选);塔顶 采用全凝器,泡点回流。 6.操作回流比R=(1.1—2.0) R。 min 1.1.3 设计任务 1.完成该精馏塔工艺设计,包括辅助设备及进出口接 管的计算和选型。 2.画出带控制点的工艺流程示意图,t-x-y相平衡 图,塔板负荷性能图,筛孔布置图以及塔的工艺条 件图。 3.写出该精馏塔的设计说明书,包括设计结果汇总 和对自己设计的评价。 1.2 设计方案论证及确定 1.2.1 生产时日 设计要求塔日产40吨92.41%乙醇,工厂实行三班制,每班工作8小时,每天24小时连续正常工作。 1.2.2 选择塔型 精馏塔属气—液传质设备。气—液传质设备主要分为板式塔和填料塔两大类。该塔设计生产时日要求较大,由板式塔与填料塔比较[1]知:板式塔直径放大时,塔板效率较稳定,且持液量较大,液气比适应范围大,因此本次精馏塔设备选择板式塔。筛板塔是降液管塔板中结构最简单的,它与泡罩塔相比较具有下列优点:生产能力大10-15%,板效率提高15%左右,而压降可降低30%左右,另外筛板塔结构简单,消耗金属少,塔板的造价可减少40%左右,安装容易,也便于设备选型-精馏塔设计说明书
精馏塔设计流程
精馏塔的设计及选型
筛板精馏塔设计示例
分离乙醇水精馏塔设计含经典工艺流程图和塔设备图
板式精馏塔项目设计方案
精馏塔设计
分离乙醇—水混合液的筛板精馏塔设计
精馏塔设计指导书
精馏塔设计图(参考)
精馏塔工艺工艺设计计算
精馏塔设计图(参考)
精馏塔的设计(毕业设计)
化工原理课程设计--- 乙醇——水筛板精馏塔工艺设计