氨合成催化剂绝对分层还原法
氨合成塔催化剂升温还原方案

氨合成塔催化剂升温还原方案氨合成铁触媒通常均以氧化态形式存在(FeO、Fe2O3),而其只有在α-Fe状态下才具有活性,起到催化作用,因此在利用前必需将氧化铁还原成α-Fe,且还原质量的好坏将直接阻碍其利用寿命及企业的经济效益,必需严格依照还原方案进行操作,确保催化剂还原质量。
一、还原方程式及理论出水量一、方程式:FeO+H2=Fe+H2O+QFe2O3+H2=2Fe+3H2O-Q二、理论出水量:3、气体流程循环机出口的气体经油分分离油水后,分成三股:第一股10%的环隙气从下部沿内外筒环隙进入塔上部,从塔顶引出,与热交的热气体汇合后约30-35%再进入冷管制。
第二股5%左右零米冷激气从上部进入合成塔上部,用来调剂合成塔上部温度。
第三股,被塔外热互换器加热到170-200℃、约65-70%的主线气体进入合成塔下部的换热器管内,气体加热到360-410℃,经中心管进入触媒层表面。
通过第一绝热层反映后,气体温度达到460-470℃,与段间冷却器出来的气体在混合散布器内混合,温度降到400-430℃,进入径向框与内筒的环隙向下,从圆周方向径向流向径向筐Ⅰ中部的换热器。
气体通过换热器外壳进入管间,气体从换热器管间上部折流向下,温度降至310-340℃出塔。
出塔气经废热回收器进热互换器管内(下进上出)温度90℃,进入水冷却器,水冷出来的气体降温到40℃,进入冷凝蒸发分离器(1)气体进冷凝器管内,再进氨蒸发器管内,进分离器,分离氨后的气体经导气管从分离器底部引来,再进冷凝蒸发分离器(2),气体进冷凝器关键,再进氨蒸发器管内,出氨蒸发器的气体,与补气油分来的新鲜气汇合,经分离器分离氨后,通过氨蒸发器的中心管进入上部冷凝器的管内,从冷凝蒸发器(2)的冷凝器管内出来的气体在进入冷凝蒸发分离器(1)的冷凝器的管间,冷却进入管内的水冷后的热气体,本身温度提高到25℃以上进入循环机,开始新的一轮循环。
二、还原前的预备工作一、各分析仪器齐全,水汽浓度取样管,出水掏出点接管畅通。
合成氨催化剂升温还原方案

合成氨催化剂升温还原方案一、方案背景二、方案目标1.确保催化剂在升温还原过程中活性稳定,提高转化效率。
2.延长催化剂使用寿命,降低生产成本。
3.减少环境污染,实现绿色生产。
三、方案步骤1.准备工作(1)人员培训:组织相关人员进行升温还原方案的培训,确保每个人都熟悉操作流程。
(2)设备检查:检查升温还原设备是否正常运行,包括加热装置、温度控制器、气体输送系统等。
(3)原料准备:确保原料的质量,如催化剂、还原剂等。
2.升温还原过程(1)预还原①将催化剂放入预还原装置,通入还原剂气体。
②设定预还原温度,逐渐升温至规定温度。
③保持预还原温度,观察催化剂颜色变化,直至颜色稳定。
(2)主还原①将预还原后的催化剂转入主还原装置。
②通入还原剂气体,设定主还原温度。
③逐渐升温至主还原温度,保持一段时间。
④观察催化剂颜色和活性变化,如活性达标,则结束升温还原过程。
3.后处理(1)冷却:将升温还原后的催化剂进行冷却,直至温度降至室温。
(2)活性测试:对催化剂进行活性测试,确保达到生产要求。
(3)封装:将合格催化剂进行封装,防止受潮和污染。
四、方案注意事项1.升温还原过程中,要严格控制温度和气体流量,避免温度过高或过低。
2.注意观察催化剂的颜色和活性变化,及时调整操作参数。
3.确保设备运行正常,防止设备故障影响升温还原效果。
4.操作人员要严格遵守安全操作规程,确保人身安全和生产安全。
五、方案实施效果1.通过实施本方案,催化剂活性稳定,转化效率提高。
2.催化剂使用寿命延长,降低生产成本。
3.减少环境污染,实现绿色生产。
4.提高操作人员的安全意识和技能水平。
本方案结合了多年的实践经验和研究成果,旨在为合成氨催化剂升温还原过程提供一套完整、可行的操作方案。
通过实施本方案,可以确保催化剂的活性稳定,提高转化效率,延长使用寿命,降低生产成本,减少环境污染,实现绿色生产。
希望本方案能为相关行业提供参考和借鉴。
注意事项:1.温度控制要精准,过高可能会造成催化剂的结构破坏,过低则影响还原效果。
合成氨的工艺流程
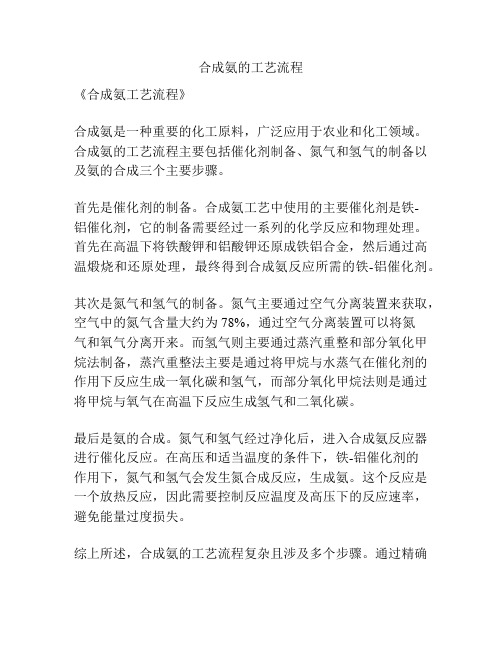
合成氨的工艺流程
《合成氨工艺流程》
合成氨是一种重要的化工原料,广泛应用于农业和化工领域。
合成氨的工艺流程主要包括催化剂制备、氮气和氢气的制备以及氨的合成三个主要步骤。
首先是催化剂的制备。
合成氨工艺中使用的主要催化剂是铁-
铝催化剂,它的制备需要经过一系列的化学反应和物理处理。
首先在高温下将铁酸钾和铝酸钾还原成铁铝合金,然后通过高温煅烧和还原处理,最终得到合成氨反应所需的铁-铝催化剂。
其次是氮气和氢气的制备。
氮气主要通过空气分离装置来获取,空气中的氮气含量大约为78%,通过空气分离装置可以将氮
气和氧气分离开来。
而氢气则主要通过蒸汽重整和部分氧化甲烷法制备,蒸汽重整法主要是通过将甲烷与水蒸气在催化剂的作用下反应生成一氧化碳和氢气,而部分氧化甲烷法则是通过将甲烷与氧气在高温下反应生成氢气和二氧化碳。
最后是氨的合成。
氮气和氢气经过净化后,进入合成氨反应器进行催化反应。
在高压和适当温度的条件下,铁-铝催化剂的
作用下,氮气和氢气会发生氮合成反应,生成氨。
这个反应是一个放热反应,因此需要控制反应温度及高压下的反应速率,避免能量过度损失。
综上所述,合成氨的工艺流程复杂且涉及多个步骤。
通过精确
控制每个步骤的条件和参数,可以确保生产安全高效地进行,从而满足氨的需求并为化工及农业领域提供丰富的原料。
氨合成的催化剂

氨合成的催化剂引言氨是一种重要的化工原料,广泛应用于农业、化肥制造、化工合成等领域。
而氨合成过程中最关键的环节就是催化剂的选取。
本文将会全面介绍氨合成催化剂的种类、工作原理、制备方法以及相关的工业应用,以加深我们对氨合成催化剂的了解。
催化剂种类在氨合成过程中,常用的催化剂主要包括铁系催化剂、钌系催化剂和铑系催化剂。
这些催化剂具有高效能、稳定性好的特点,被广泛应用于工业生产中。
铁系催化剂铁系催化剂是氨合成过程中最常见的催化剂之一。
传统的铁系催化剂主要是以铁为主要成分,常配以适量的铝、钾等元素。
这类催化剂具有成本低、晶体结构稳定等优点,然而其催化活性相对较低,需要高温和高压下进行反应。
近年来,随着纳米技术的发展,铁基纳米催化剂成为了新的研究热点,其催化活性和选择性得到了极大的提高。
钌系催化剂钌系催化剂是氨合成中的另一类重要催化剂。
钌具有较高的催化活性和选择性,常作为铁系催化剂的替代品使用。
研究表明,钌催化剂在较低温下即可实现氨合成反应,大大降低了能耗。
此外,钌系催化剂对反应物质的吸附性能和解离能力较强,可以促进氨合成反应的进行。
铑系催化剂铑系催化剂在氨合成领域中也有着广泛的应用。
铑是一种包括铑金属和铑氧化物等在内的化合物,具有较高的催化活性和稳定性。
铑催化剂不仅可用于氨合成反应的催化剂,还可以在其他化学反应中发挥重要作用。
然而,铑系催化剂的价格较高,限制了其在工业生产中的应用。
催化剂在氨合成反应中起到了至关重要的作用。
一方面,催化剂可以提供活性位点,吸附反应物质并降低其解离能力,从而促进反应的进行。
另一方面,催化剂还可以降低反应的活化能,提高反应的速率。
具体而言,催化剂与反应物之间会发生物理吸附和化学吸附的过程。
在物理吸附中,反应物只是通过分子间的范德瓦尔斯力与催化剂表面相互作用。
而在化学吸附中,反应物会与催化剂发生化学反应,生成中间体。
通过物理吸附和化学吸附的交替作用,反应物逐步转化为产物。
催化剂的选择需要考虑多个因素,如催化活性、化学稳定性、抗中毒性等。
Ru-AC氨合成催化剂还原性能的研究

Ru-AC氨合成催化剂还原性能的研究Ru/AC氨合成催化剂还原性能的研究摘要:本文通过比较不同还原剂还原方法对Ru/AC氨合成催化剂还原性能和氨合成性能的影响,研究发现使用乙二醇和丙烷作为还原剂的还原方法对Ru/AC催化剂还原性能和氨合成性能的影响最小,Ru/AC催化剂在该还原方法下表现出了良好的还原性能和氨合成性能。
同时,通过对还原温度、还原时间和还原剂用量进行优化实验,得出了最佳还原条件。
关键词:Ru/AC;氨合成;催化剂还原性能;还原剂;还原条件引言:氨合成是工业化学反应中的重要反应,氨合成催化剂的性能直接影响氨合成的效率和经济效益。
Ru/AC(活性炭载体的钌催化剂)因其良好的催化性能和稳定性成为了氨合成催化剂的研究热点。
而催化剂还原性能对催化剂的性能和稳定性有重要影响。
因此,研究Ru/AC氨合成催化剂还原性能对其性能的进一步提升具有重要意义。
实验:本文采用不同还原剂还原方法对Ru/AC催化剂进行还原,分别为乙二醇还原法、丙烷还原法、氢气还原法,比较了不同还原方法对催化剂还原性能的影响。
同时,优化了还原条件,探究了最佳还原条件。
结果:乙二醇还原法和丙烷还原法对Ru/AC催化剂还原性能和氨合成性能的影响最小,催化剂在这两种还原方法下表现出了良好的还原性能和氨合成性能。
且在经过优化的还原条件下,催化剂表现出了最佳的还原性能和氨合成性能。
其中,最佳还原温度为300℃,最佳还原时间为3小时,最佳还原剂用量为H2O:乙二醇:Ru=50:100:1。
结论:本文通过研究不同还原剂及优化还原条件的方式探究了Ru/AC氨合成催化剂还原性能的影响,得出了最优的还原条件,并提高了催化剂的还原性能和氨合成性能,为催化剂的进一步优化提供了一定的理论基础进一步分析发现,乙二醇还原法和丙烷还原法对Ru/AC催化剂的还原性能影响最小的原因是这两种还原方法都能够有效地还原催化剂表面的金属Ru,并且催化剂经过还原后烧结现象较少,保持了更高的比表面积和较好的催化性能。
氨合成触媒升温还原方案三段带预还原

氨合成触媒升温还原方案还原方案说明合成触媒第一层装填为预还原触媒(HA202WH 20.64吨),第二、三层装填为氧化态触媒(HA202W 41.22吨83.58吨)。
这两种触媒的还原温度不一致。
所以采用分层还原的方法:首先还原第一层的触媒,再依次还原第二、三层的触媒。
即第一床层的触媒基本还原结束后,可提高温度使第二床层进入还原主期。
第三床层触媒不得进入还原主期,等第二层还原结束后,通过提第三层的温度使触媒进入还原主期。
升温还原前的准备工作及注意事项1.)合成操作工认真学习开车方案,熟悉本系统工艺流程,设备阀门位置和用途。
2.)仪电检查电器是否正常,仪表如压力、温度、流量、液位显示是否灵敏可靠,调节阀是否正常工作。
3.)化验室将分析仪器、药品准备妥当。
4.)催化剂装填结束后,要用N2气进行吹除,将其粉尘吹出塔外,以防带入各换热设备,影响今后生产。
若不立即投入升温还原,要用N2进行置换后,合成塔必须处于封闭状态。
5.)对合成塔进行系统试压、试漏,确保合格。
6.)对系统进行置换,置换合格,置换过程中,各放空点均要放空置换,以防死角置换不到。
7.)对已经置换的系统充氨,塔出口的氨含量在2%时合格。
8.)系统升压至7.0MPa时,关闭补气阀。
9.)在还原过程中注意合成塔塔壁温度,主线进口阀绝对不能关死。
10.)按操作规程点开工加热炉。
一、概述合成塔所装触媒使用前必须还原成α-Fe才能起到催化作用,触媒升温还原是催化剂投入使用前的最后一道工序,还原的好坏直接影响到触媒的使用寿命、活性及操作情况。
合理控制还原过程的各种操作参数,对获得性能良好的触媒至关重要。
二、质量要求1.触媒的升温还原,必须在触媒厂家的指导下进行。
2.事先准备好升温还原曲线图,严格按照升温还原曲线进行触媒的升温、恒温与还原。
操作过程中,及时画出实际升温还原曲线。
3.触媒还原采用分层还原法进行,还原操作要力求稳定,升温升压不得同时进行。
4.还原过程中,应保持开工加热炉出口温度与触媒层热点温度之差小于150℃,还原末期小于50℃。
氨合成升温还原方案

TA201-2 / TA201-2-H氨合成催化剂装φ2400mm氨合成塔还原方案催化剂的还原质量关系到催化剂的性能,能否正常发挥。
因此,事先应制定升温还原方案。
本次选用TA201-2型铁钴系氨合成催化剂,采用分层还原方式还原,因此要严格控制好各层还原温度和各层还原温度的交叉配合。
一、氨合成催化剂的升温还原氨合成催化剂以氧化铁为主要成份,未还原的催化剂不起催化作用,用氢气还原成α-Fe结晶才有催化活性。
氨合成催化剂的升温还原过程中,催化剂的物理化学性质将发生重要变化,这些变化将对催化剂的催化性能起重要影响,因此还原过程中的操作条件控制十分重要。
催化剂在还原过程中的主要化学反应可用下式表示:Fe3O4+4H2=3Fe+4H2O △H0298=149.9J/mol还原产物铁是以分散很细的α-Fe晶粒(~200A0)的形式存在催化剂中,构成氨合成催化剂的活性中心。
氨合成催化剂升温还原时理论出水量的计算催化剂还原操作的终点是以催化剂还原度来判断的。
还原操作实践中还原度通常又是以累计出水量来间接量度。
一般要求还原终点的累计出水量应达到理论出水量的95%以上。
理论出水量计算公式:G==18/55.86×7%/(1+M)×(M+3/2)W式中:G-----理论出水量,Kg;M---铁比,Fe+2/Fe+3== Fe+2%/Fe+3%W---待还原催化剂总重量Kg;二、催化剂还原前的准备工作1、合成单元的气密试验工作已结束。
2 、各设备、调节阀、仪表元件等均处于良好状态。
3、合成回路进行氮气置换合格,合成塔吹灰后,压缩机采用氮气进行系统循环,并清除过滤器中的催化剂灰。
4、排氨水的临时管道配置结束,稀氨水接收装置具备接收氨水的条件。
5 、化验室具备分析还原水汽浓度和气体成分等条件6 、开工加热电炉具备投入运行的条件。
7 、对所有连接处进行检查,确认无泄漏。
8、检查g1、g2、g3、g4测温电偶各点长度是否正确,插入电偶套管后需留长度500mm,复查各仪表均正常,合成回路各仪表,特别是合成塔床层温度指示均应处于正常运行状态。
合成氨催化剂卸装及升温还原总结

该公司采用卡萨利装填技术 ,利用催化剂高
度 落差 ,用专 用 的催化 剂装 填喷 头装 填 。此方 法 不需 振动 就能 达到所 需 的装 填密 度 ,有效 地提 高 了催 化剂 的装 填速 度 和质 量 ,而且 避 免 了振荡 装 填过 程 中振 动 棒 损 坏 催 化 剂 筐 和 引 起 催 化 剂 粉 碎 。塔顶 固定一 放料 斗 ,料 斗下部 接 有 4根带 钢 丝橡胶 管 ,每根 管 的下端 接 有 1 锥 型喷 头 ( 个 喷
剂筐损 坏 事故 的发生 。 2 催 化剂 的装填
化。在煤气量 7 0 ~7 0 3h时 ,即使将 50 O 80 0m / 合 成氨 系 统 弛放 气量 加 到最 大 ( 0 O 20 0 儿 0 ~1 0
m3h ,合 成 系统 仍 经 常超 压 放空 ,合 成 氨 产 量 /) 偏 低 。鉴 于此 ,决 定更 换催 化剂 。
环系统、供给人体呼 吸的空气 系统 ) ,我公 司只 提供 焊 接 各种 支 架所 需 的材 料 和 60m3h的氮 0 /
气 。将合 成 塔 与 系 统 隔离 ,氮气 从 塔 底 向 上 反 吹 ,用来 补充循 环 氮气 的损 失 。 该公 司采 用干 法卸还 原态 催化 剂技术 。大盖 打开 后 ,拆 除合 成 塔 内件 ,用 棉 白布保 护好 密封 面及 塔 内外壁 环隙 ,用球 胆塞 实冷 激人 口,用 苫 布将 塔顶 盖好 ,确保 塔 内为 氮气正 压 ,氧含量 < 05 ( 4h分 析 1次 ) .% 每 ,防止 还 原态催 化 剂遇 氧气发 生燃 烧 。启动 真空 抽 吸系统 ,将真 空抽 吸 管插入 催 化 剂 床 层 ,保 持 真 空 度 在 0 0 a .4MP , 抽出 的催 化 剂 储 存在 1个 45m3的 储 存 罐 中 , . 储 存罐 架高 41。当储存 罐 中的催 化 剂积 累 到一 I T
氨合成催化剂还原小结

第 5期
杨
瑾 :氨合 成催 化 剂还原 小 结
・ 9・ 2
部 又装 填 了 大 颗 粒 预 还 原 态 催 化 剂 ,装 填 量 0 1 ,装填 高 度 02m。 氧化 态 催 化 剂 是 河 南 .5t .
使水 汽浓度 不致 过高 。上 床层 温度 在 20 时水 2
汽浓 度 已达到 29 2×1 一,3 0~4 0℃ 开始 出 4 0 8 0
骏化催化剂厂生产 的 A 1- 302型氨合成催 化剂 , 粒 径在 1 5— . m;预还原 态催 化剂 是南 京南 . 3 0m 化公 司生 产 的 A 1 —H 型 氨 合 成 催 化 剂 ,小 颗 10 1
[ 中图分 类号]T 1.4 7 [ Q 132 文献标识码 ]B [ 文章编号] 10 9 3 (0 2 0 0 2 0 0 4— 92 2 1 )5— 0 8— 2
我产 能 力 为
6 ta 0k/ ,氨 合 成 塔 内件 原 采 用 瑞 士 卡 萨 利 公 司
第 5期 21 0 2年 9月
中 氮
肥
No 5 .
M— i d N t g n u e t ie r g e s S z i o e o sF ri z r P o r s e r l
S p. 2 2 e t 01
氨 合 成 催 化 剂 还 原 小 结
杨 瑾
1 14 ) 6 0 1 ( 黑龙江黑化集 团有 限公 司 ,黑龙江 齐齐 哈尔
被 冷却至 5 8℃ ,然后 去水 冷 器进 一 步冷 却 到 3 5 ℃ 以下 ,经 氨 分 离 器 分 离 掉 液 氨 后 进 5 2循 环 1 机 ,补充 压力 后开 始下一 个循 环 。
情 况作一 介 绍 。
氨合成催化剂升温还原方案

JR型合成塔A202氨合成催化剂升温还原方案
1、氨合成岗位试压和置换结束后,向高压系统充氨50~100Kg(3~5g/Nm3)。
锅炉应在氨合成升温前开始通蒸汽煮废锅,并在升温还原期间,控制好温度,充分利用余热,减轻电炉负荷。
2、温度升到120℃排水一次,200℃时开启水冷器上水阀,250℃时氨冷器开始加液氨,并控制气氨压力,380℃以上每小时排水一次,380℃开始做水汽浓度,430℃以上每半个小时排一次水。
3、进入还原主期时,补气阀保持常开,用塔后放空阀控制系统压力,CH4≥4%时开大塔后放空阀,同时开大补气阀确保系统压力稳定。
4、水汽浓度尽可能控制在2.5~3.0mg/L,并参考出水量控制升温速度,出水量大、水汽浓度较高时应恒温。
是否提温以水汽浓度和出水量为准。
5、当循环机跳闸急停时,立即紧急切断电炉,开大塔后放空阀,关闭补气阀;循环机开车恢复送气后,即可开电炉,缓慢提升电炉电流、电压,恢复升温还原前的工况。
6、当电炉跳闸时,立即开大系统近路和循环机近路阀,关补气阀和塔后放空阀;电炉恢复送电后缓慢提升电流、电压,视温升趋势关小系统近路和循环机近路阀,直至恢复停电前的原工况。
7、催化剂还原结束条件:(1) 水汽浓度连续2小时≤0.2mg/L。
(2) 底部温度提到460℃以上,恒温6~10小时即可降温转低负荷生产。
8、在还原过程中,以高空速、高氢、高电炉功率和低氨冷温度、低压、低水汽浓度的“三高三低”原则执行。
9、由于此次还原循环量不够,在进入还原主后期时,要根据情况及时、逐渐增压。
附:A202型触媒ø1000内冷绝热型氨合成塔升温还原计划表
生产部
2012.11.17。
合成氨催化剂升温还原技术在化工中的应用

合成氨催化剂升温还原技术在化工中的应用我们知道,合成氨是化学工业中的一种重要反应,而这个过程的核心就是催化剂。
今天,我们要聊的就是合成氨催化剂升温还原技术在化工中的应用。
我们要明白,催化剂在合成氨的过程中起到的是什么作用。
合成氨的反应式是N2+3H2→2NH3,这是一个需要能量的反应,而催化剂就是帮助这个反应快速进行,降低反应所需的能量。
那么,催化剂的还原是什么意思呢?还原,就是指物质失去氧原子或者获得电子。
在合成氨的过程中,催化剂需要通过还原,才能发挥出最大的效果。
而这个还原的过程,就是升温还原技术。
升温还原技术,简单来说,就是通过升温,让催化剂中的金属离子失去氧原子,恢复其活性。
这个技术在合成氨的工业生产中,起到了至关重要的作用。
升温还原技术可以提高催化剂的活性。
催化剂的活性,是指催化剂在单位时间内催化反应的能力。
催化剂经过升温还原后,其活性会得到显著提高,从而提高了合成氨的反应速度。
升温还原技术可以延长催化剂的使用寿命。
催化剂在反应过程中,会逐渐失去活性,而升温还原技术可以恢复催化剂的活性,使其重新焕发活力。
这样,催化剂的使用寿命就会得到延长。
升温还原技术可以提高合成氨的产率。
催化剂的活性提高了,合成氨的反应速度就会加快,从而提高了产率。
总的来说,合成氨催化剂升温还原技术在化工中的应用,不仅可以提高催化剂的活性,延长使用寿命,还可以提高合成氨的产率,对于化工产业的发展,具有重要的意义。
然而,升温还原技术并不是没有缺点。
比如,升温还原过程需要消耗大量的能源,而且升温过程中,催化剂可能会发生结构变化,影响其活性。
因此,如何在保证催化剂活性的同时,降低能源消耗,就是合成氨工业中需要解决的问题。
总的来说,合成氨催化剂升温还原技术在化工中的应用,是一种重要的技术手段。
虽然存在一些问题,但随着科技的发展,我们相信这些问题都会得到解决。
合成氨催化剂升温还原技术在化工中的应用,将会越来越广泛。
合成氨催化剂升温还原技术在化工中的应用,是一项关键的技术。
氨合成催化剂的分层快速还原
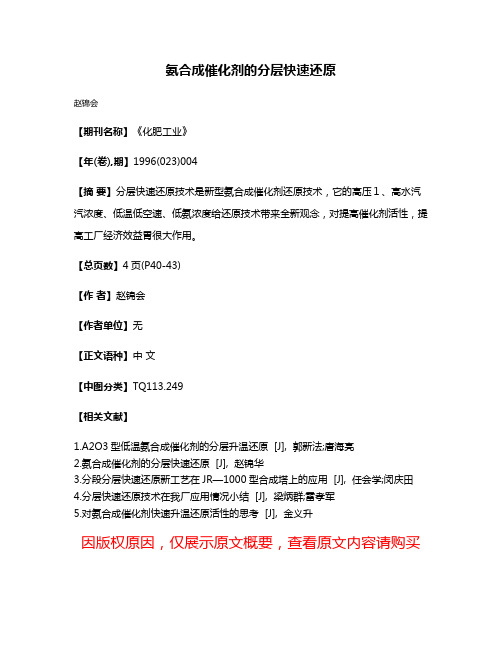
氨合成催化剂的分层快速还原
赵锦会
【期刊名称】《化肥工业》
【年(卷),期】1996(023)004
【摘要】分层快速还原技术是新型氨合成催化剂还原技术,它的高压1、高水汽汽浓度、低温低空速、低氨浓度给还原技术带来全新观念,对提高催化剂活性,提高工厂经济效益胃很大作用。
【总页数】4页(P40-43)
【作者】赵锦会
【作者单位】无
【正文语种】中文
【中图分类】TQ113.249
【相关文献】
1.A2O3型低温氨合成催化剂的分层升温还原 [J], 郭新法;唐海亮
2.氨合成催化剂的分层快速还原 [J], 赵锦华
3.分段分层快速还原新工艺在JR—1000型合成塔上的应用 [J], 任会学;闵庆田
4.分层快速还原技术在我厂应用情况小结 [J], 梁炳群;雷孝军
5.对氨合成催化剂快速升温还原活性的思考 [J], 金义升
因版权原因,仅展示原文概要,查看原文内容请购买。
氨合成催化剂的选择及相关工作

氨合成催化剂的选择及相关工作1 国内氨合成催化剂概况解放前我国没有氨合成催化剂工业,而目前我国研制和生产的氨合成催化剂在国际上已处于领先或先进的水平。
最初用于我国小氮肥厂的是南化公司开发生产的A106型氨合成催化剂,以后由南化研究院和南化公司催化剂厂研制开发了A109型催化剂,于1971年经国家鉴定,其质量水平超过了丹麦的KM-1型催化剂。
以后又开发了A110型催化剂,这是一种低温高活性易还原的催化剂,但其抗毒性和热稳定性较差。
在进一步改进后,南化公司研究院开发了A110-1,浙江工业大学研制开发了A110-2型(即ZA-1型)。
A110-1、A110-2型催化剂抗毒性和耐热性有了较大的提高,因而在氮肥行业普及很快。
到了20世纪80年代中后期和90年代初期,国内催化剂的研制开发又上了一个新的台阶。
福州大学相继研制开发成功A201、A202型含,钴催化剂,南化院研制开发了NCA型含钴催化、剂,华南理工大学研制开发A203型稀土催化剂和浙江工业大学研制开发了亚铁基的A301型氨、合成催化剂。
这些催化剂都具有低温、高活性、易还原的特点,其中A301型氨合成催化剂突破了传统的Fe3O4熔铁催化剂体系,从性能比较看是,国内最先进的氨合成催化剂之一。
2 如何选择氨合成催化剂目前在市场上流通的氨合成催化剂主要有福州大学开发的A201、A202型含钴催化剂,南化研究院开发的NCA型含钴催化剂,华南理工大学研制开发A203型稀土催化剂,郑州大学开发的HA310Q型球形催化剂,浙江工业大学开发的A301型亚铁基催化剂以及上一代的A110系列催化剂等。
A110型系列氨合成催化剂主要是由Fe3O4、Al2O3、K2O、CaO、MgO、SiO2及某些微量元素的化合物组成,它在较低温度下具有较高的催化活性,是一种较理想的氨合成催化剂,在小氮肥厂使用量很大。
A201型氨合成催化剂是铁钴双活性组分的低温高活性氨合成催化剂;它由于氧化钴的加入,导致催化剂的晶体结构、表面结构、孔结构明显变化而提高了催化剂的活性。
合成氨催化剂升温还原方案

合成催化剂升温还原方案一、催化剂还原前的准备工作1、合成单元的气密试验工作已结束。
甲烷化升温还原结束。
2 、各设备、调节阀、仪表元件等均处于良好状态。
3、合成回路进行氮气置换合格,合成塔吹除后,压缩机采用氮气进行系统循环,并清除过滤器中的催化剂灰。
4、排氨水的临时管道配置结束,稀氨水接收装置具备接收氨水的条件。
5 、化验室具备分析还原水汽浓度和气体成分等条件各分析仪器齐备;水汽浓度取样接管、出水取样点接管畅通。
6 、开工加热电炉具备投入运行的条件。
电加热器和调压设备要处于完好状态,使用时要选派专业人员监护。
7 、对所有连接处进行检查,确认无泄漏。
8、公布升温还原方案,宣布升温还原的临时专门组织领导机构。
9、合成圈内检测仪表符合开车要求,内套管插入以前必须用化学溶剂(无水酒精等)擦洗,确保测温准确无误。
10、向已经置换并做了气密试验的系统充氨,使循环气中氨含量>1%。
11、向系统补入合格的新鲜气,压力5.0MPa。
二、催化剂的升温还原1、第一床层为轴向层,从常温升至350℃,用8小时,每小时40~45℃,合成回路的操作压力为5MPa左右。
2、气量由压缩机和合成塔前的主阀、放空阀等控制,在满足升温速率的情况下,尽量提高空速,只要电炉功率允许,循环机最多开4台17m3/min机。
3、热负荷由开工加热电炉提供,应根据设计单位提出的对加热电炉安全气量的要求进行操作,在容许的条件下加大电路功率,提高床层温度。
4、一层催化剂温度达到350℃,开始分析水汽浓度,每小时一次,严格控制出口气体中水汽浓度小于1.5g/m3三、还原初期从350-420℃为催化剂还原初期1、当催化剂床层温度达到300℃左右,催化剂便进入还原初期。
此时催化剂开始出水。
当达到350℃以上,出水已十分明显。
应加大水汽浓度分析频率,建议每半个小时分析一次。
并每两个小时测定一次进口气体中水汽含量。
入塔气体水汽浓度越低越好,最大不得超过0.2g/m3。
合成氨工艺操作规程
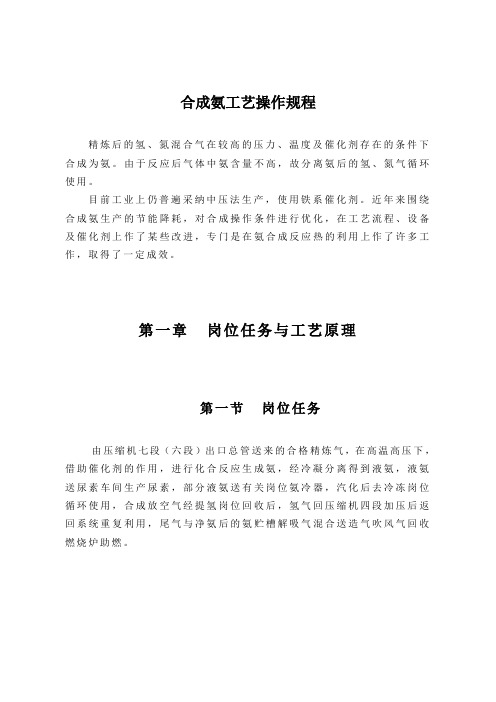
合成氨工艺操作规程精炼后的氢、氮混合气在较高的压力、温度及催化剂存在的条件下合成为氨。
由于反应后气体中氨含量不高,故分离氨后的氢、氮气循环使用。
目前工业上仍普遍采纳中压法生产,使用铁系催化剂。
近年来围绕合成氨生产的节能降耗,对合成操作条件进行优化,在工艺流程、设备及催化剂上作了某些改进,专门是在氨合成反应热的利用上作了许多工作,取得了一定成效。
第一章岗位任务与工艺原理第一节岗位任务由压缩机七段(六段)出口总管送来的合格精炼气,在高温高压下,借助催化剂的作用,进行化合反应生成氨,经冷凝分离得到液氨,液氨送尿素车间生产尿素,部分液氨送有关岗位氨冷器,汽化后去冷冻岗位循环使用,合成放空气经提氢岗位回收后,氢气回压缩机四段加压后返回系统重复利用,尾气与净氨后的氨贮槽解吸气混合送造气吹风气回收燃烧炉助燃。
第二节差不多原理1氨合成的生产原理氨合成反应的化学方程式:N2+3H22NH3+Q氨合成反应的特点:①可逆反应②放热反应:A标准状况下(25℃)101325KPaB每生成1mol NH3放出46.22KJ热量③体积缩小的反应:3摩尔氢与1摩尔氮生成2摩尔氨,压力下降④必需有催化剂存在才能加快反应2 氨合成反应的平稳氨合成反应是一个可逆反应,正反应与逆反应同时进行,反应物质浓度的减少量与生成物质浓度的增加量达到相等,氨含量不再改变,反应就达到一种动态平稳。
从平稳观点来看:提高反应温度,可使平稳向吸热反应方向移动,降低温度向放热方向移动。
3 氨合成反应速度及阻碍合成反应的因素反应速度是以单位时刻内反应物浓度的减少或生成物浓度的增加量来表示的。
阻碍氨反应速度的因素:3.1压力:提高压力能够加快氨合成的速度,提高压力确实是提高了气体浓度,缩短了气体分子间的距离,碰撞机会增多,反应速度加快。
3.2温度:温度提高使分子运动加快,分子间碰撞的次数增加,又使分子克服化合反应时阻力的能力增大,从而增加了分子有效结合的机会,关于合成反应当温度升高,加速了对氮的活性吸附,又增加了吸附氮与氢的接触机会,使氨合成反应速度加快。
浅析新型合成氨催化剂的还原

1 氨 合 成 催 化 剂 的 发 展
11A1系列催 化剂 的 开发 .
15 9 1年 , 南京 化 学 工 业 公 司 开 发 成 功 了 我 国第 1个 合 成 氨 催 化 剂~ A1 2型 催 化 剂 , 以后 又 成 功 开 发 了 Al6型 和 0 0 A19型催化剂 ;2 0 0世纪 7 0年代末 ,浙 江工业大学的 A102 1— 型 、 南 京 化 工 研 究 院 的 A10 1型 、 福 州 大 学 的 A l03型 、 — l 1— 临朐 催 化 剂 厂 的 AI04型 、 郑 州 大 学 的 A105 型 ( 形 ) — l —Q l 球 、 湖 北省 化 学 院 的 Al06型 等 催 化 剂 相 继 开 发 成 功 ,形 成 了 我 1— 国2 O世 纪 8 ,9 0 0年 代 广 为 应 用 的 A10系 列 催 化 剂 。 1
1y eZA一 e —O—ae mmo i s nh ssctlssa dt eslcinpicpe ft e tp w— mp rtr,o pe sr, iha t i t 01c tls s I 5F Ix b sda p na y te i aayt n h ee t r ils hen w el t eaue lw—rsue hg ci t wi A3 aay t o n o y o e vy h a
a x m p e t e o d c i nb e t go e f w p m io n i s n h ssc t l s wa ic s e ea l nea l, h m f e u t y h a i ft e t ea n — a l y t e i aa y t sd s u s d i d t i r o n h l y n .