第四章 组合机床
组合机床
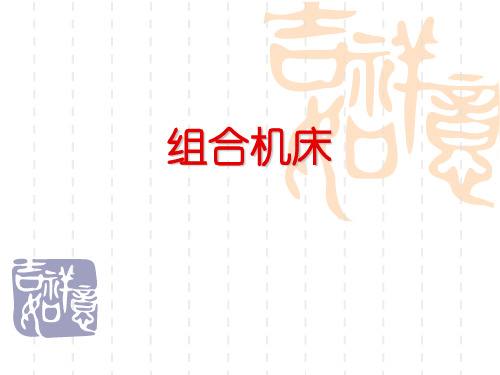
2)具有移动夹具的多工位组合机床
多工位组合机床的夹具和工件可按预定的工作循环,作间歇的 移动或转动,以便依次在不同工位上对工件进行不同的工位加 工。这类机床生产率高,但加工精度不如单工位组合机床,多 用于大批量生产中对中小型零件的加工。 按照夹具和工件的输送方式不同,可分为移动工作台式、回转 工作台式、中央立柱式和鼓轮式四种类型。 a 移动工作台组合机床可以先后在两个工位上从两面对工件进 行加工,夹具和工件可随工作台直线移动来实现工件的变换。
2 组合机床组成 由侧底座1、立柱底座2、立柱3、动力箱5、滑台6及中间底 座7等通用部件、主轴箱4、夹具8等主要专用部件组成。
3 组合机床与专用机床、通用机床相比所具有的 特点: (1)工作稳定且可靠。组合机床中有70%-90%的 通用零部件,而这些零部件是经过精心设计和长 期生产实践考验的。 (2)设计周期短。设计时,对于通用的零部件可以 预先制造出来并可成批生产。 (3)生产周期短,并可降低成本。因为这些通用零 部件可以预先制造出来并可成批生产。 (4)有利于产品的更新。当被加工对象改变时,它 的通用零部件可重新利用,组合成新的组合机床。
4 组合机床的工艺范围
组合机床能够对工件进行多刀、多轴、多面、多 工位同时加工;可完成钻孔、扩孔、镗孔、攻丝、 铣削、车孔端面等工序;随着组合机床技术的的
发展,其工艺范围日益扩大,如:焊接、热处理、
自动测量和自动装配、清洗等非切削工序。
5 组合机床的分类
根据所选用的通用部件的规格大小以及结构和配置形式等 方面的差异,将组合机床分为大型组合机床和小型组合机 床两大类。 滑台台面宽度B≥250mm的为大型组合机床; 滑台台面宽度B<250mm的为小型组合机床。
1) 液压滑台 主要由滑座1,滑台体2和液压缸3三个部分组成。液压缸固定在滑座 上,活塞杆4通过支架固定在滑台2的下面,推动滑台移动。
第四章组合机床设计资料

向力造成的振动。
② 当缸孔孔间距及平行度要求高(±0.02~0.03mm),缸孔
对定位基准位置精度要求高于±0.05mm时,通常采用由单个精
镗头组成的多轴机床结构方案,使各精镗头可单独调整位置。还 需配置高精度动力滑台,来提高机床工作的平稳性。
二、工艺方案的拟订
③ 同样精度的孔,因材料、硬度的不同,其工艺方案也不 同,如加工钢件一般比加工铸铁件的工步数多。 ④ 加工薄壁易振动的工件或刚性不足的工件,安排工序不
机械制造装备设计
第四章 组合机床设计
2019年1月1日
第四章 组合机床设计 第二节 组合机床总体设计
一、 组合机床设计步骤 二、 工艺方案的拟订 三、 确定切削用量及切削力 四、 组合机床三图一卡设计
一、组合机床设计步骤
组合机床设计是根据被加工零件的加工内容、加工精度、生
产率要求、成本价格等原始数据,进行总体设计、传动系设计、 夹具设计。 设计步骤: ♦ 调查研究, ♦ 总体方案设计, ♦ 技术设计, ♦ 工作设计。
二、工艺方案的拟订
3.合理实施工序集中
工序集中 运用多种刀具,采用多面、多工位和复合刀具加 工方法,在一台机床上对一个或几个零件完成多个工序过程,以 提高生产率。
(1)注意工序集中带来的问题
♦ 导致机床结构复杂,刀具数量增加, 调整不方便,可靠性降低,影响生产率 的提高。 ♦ 导致切削负荷加大,造成工件刚 性不足、工件变形而影响加工精度。
4.工作设计
绘制多轴箱、夹具等专用零部件的施工图纸、编制零部件明 细表;编写机床说明书,制订机床检验、试机等验收标准。
二、工艺方案的拟订
(一)工艺方案的制定内容
分析被加工零件图纸 ①根据组合机床各工艺方法能达到的
组合机床
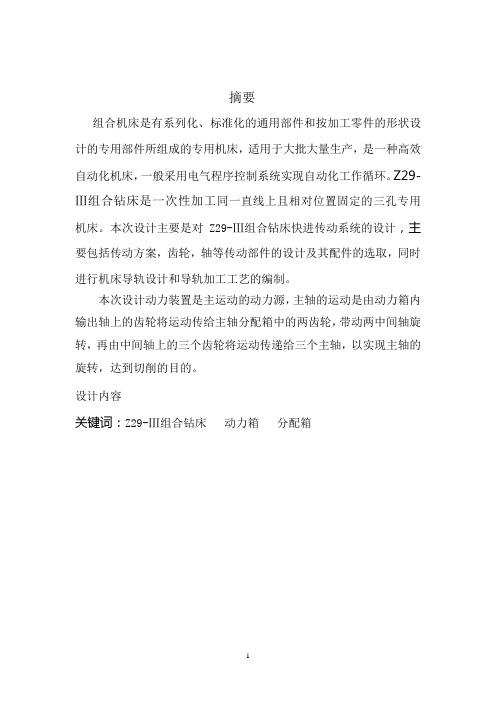
摘要组合机床是有系列化、标准化的通用部件和按加工零件的形状设计的专用部件所组成的专用机床,适用于大批大量生产,是一种高效自动化机床,一般采用电气程序控制系统实现自动化工作循环。
Z29-Ⅲ组合钻床是一次性加工同一直线上且相对位置固定的三孔专用机床。
本次设计主要是对Z29-Ⅲ组合钻床快进传动系统的设计,主要包括传动方案,齿轮,轴等传动部件的设计及其配件的选取,同时进行机床导轨设计和导轨加工工艺的编制。
本次设计动力装置是主运动的动力源,主轴的运动是由动力箱内输出轴上的齿轮将运动传给主轴分配箱中的两齿轮,带动两中间轴旋转,再由中间轴上的三个齿轮将运动传递给三个主轴,以实现主轴的旋转,达到切削的目的。
设计内容关键词:Z29-Ⅲ组合钻床动力箱分配箱目录1 绪论1.1机床在国民经济的地位及其发展简史现代社会中,人们为了高效、经济地生产各种高质量产品,日益广泛的使用各种机器、仪器和工具等技术设备与装备。
为制造这些技术设备与装备,又必须具备各种加工金属零件的设备,诸如铸造、锻造、焊接、冲压和切削加工设备等。
由于机械零件的形状精度、尺寸精度和表面粗糙度,目前主要靠切削加工的方法来达到,特别是形状复杂、精度要求高和表面粗糙度要求小的零件,往往需要在机床上经过几道甚至几十道切削加工工艺才能完成。
因此,机床是现代机械制造业中最重要的加工设备。
在一般机械制造厂中,机床所担负的加工工作量,约占机械制造总工作量的40%~60%,机床的技术性能直接影响机械产品的质量及其制造的经济性,进而决定着国民经济的发展水平。
可以这样说,如果没有机床的发展,如果不具备今天这样品种繁多、结构完善和性能精良的各种机床,现代社会目前所达到的高度物质文明将是不可想象的。
一个国家要繁荣富强,必须实现工业、农业、国防和科学技术的现代化,这就需要一个强大的机械制造业为国民经济各部门提供现代化的先进技术设备与装备,即各种机器、仪器和工具等。
然而,一个现代化的机械制造业必须要有一个现代化的机床制造业做后盾。
组合机床.

组合机床科技名词定义中文名称:组合机床英文名称:modular machine tool定义:以通用部件为基础,配以少量专用部件,对一种或若干种工件按预先确定的工序进行加工的机床。
所属学科:机械工程(一级学科) ;切削加工工艺与设备(二级学科) ;金属切削机床-各种金属切削机床(三级学科)组合机床的定义组合机床(transfer and unit machine)组合机床是以通用部件为基础,配以按工件特定形状和加工工艺设计的专用部件和夹具,组成的半自动或自动专用机床。
组合机床加工方式组合机床一般采用多轴、多刀、多工序、多面或多工位同时加工的方式,生产效率比通用机床高几倍至几十倍。
由于通用部件已经标准化和系列化,可根据需要灵活配置,能缩短设计和制造周期。
因此,组合机床兼有低成本和高效率的优点,在大批、大量生产中得到广泛应用,并可用以组成自动生产线。
组合机床一般用于加工箱体类或特殊形状的零件。
加工时,工件一般不旋转,由刀具的旋转运动和刀具与工件的相对进给运动,来实现钻孔、扩孔、锪孔、铰孔、镗孔、铣削平面、切削内外螺纹以及加工外圆和端面等。
有的组合机床采用车削头夹持工件使之旋转,由刀具作进给运动,也可实现某些回转体类零件(如飞轮、汽车后桥半轴等)的外圆和端面加工。
组合机床的发展史二十世纪70年代以来,随着可转位刀具、密齿铣刀、镗孔尺寸自动检测和刀具自动补偿技术的发展,组合机床的加工精度也有所提高。
铣削平面的平面度可达0.05毫米/1000毫米,表面粗糙度可低达2.5~0.63微米;镗孔精度可达IT7~6级,孔距精度可达O.03~O.02微米。
专用机床是随着汽车工业的兴起而发展起来的。
在专用机床中某些部件因重复使用,逐步发展成为通用部件,因而产生了组合机床。
最早的组合机床是1911年在美国制成的,用于加工汽车零件。
初期,各机床制造厂都有各自的通用部件标准。
为了提高不同制造厂的通用部件的互换性,便于用户使用和维修,1953年美国福特汽车公司和通用汽车公司与美国机床制造厂协商,确定了组合机床通用部件标准化的原则,即严格规定各部件间的联系尺寸,但对部件结构未作规定。
机械制造装备设计第四章组合机床主轴箱设计
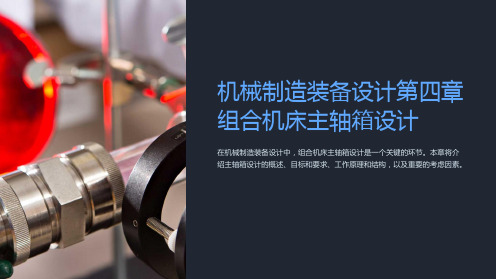
影响因素
主轴箱的设计受到机床类型、 加工要求、切削力、转速范 围等因素的影响。
主轴箱设计的目标和要求
1 高刚性
主轴箱应具有高刚性,以确保机床在高速运 行时的稳定性和加工精度。
2 合理布局
主轴箱的内部结构应合理布局,方便维修和 保养。
3 低振动
主轴箱应减小振动和噪音,提高机床的工作 环境。
4 可靠性
需求分析
明确主轴箱的功能和性能要求。
选型和计算
选择适合的材料和标准件,进行强度、 刚度等计算。
加工和装配
按照设计要求进行主轴箱的加工和装配。
主轴箱设计的优化方法
1 减少质量
通过优化结构设计和材料选择,减少主轴箱的质量。
2 提高刚性
通过改进支撑结构和加工工艺,提高主轴箱的刚性。
3 优化传动
选择合适的齿轮传动方案,提高主轴箱的传动效率。
主轴箱设计实例和案例研究
实例一
某机床工厂成功设计了一款高速主轴箱,提高了机 床的加工效率和产品质量。
实例二
一家机械研究院研发了一种新型主轴箱结构,减小 了机床的振动和噪音。
主轴箱应具有较高的可靠性,以保证机床的 长时间运行。
主轴箱设计的工作原理和结构
工作原理
主轴箱通过传动装置将电机的动力传导到主轴上, 实现转速调节和加工功能。
结构
常见的主轴箱结构包括箱体、主轴、轴承、齿轮传 动、变速箱等组成部分。
主轴箱设计的重要考虑因素
1 切削力
主轴箱要能承受切削力, 保持稳定运行。
2 加工精度
3 主轴高速旋转时会产生大 量热量,需要考虑散热和 冷却措施。
主轴箱设计步骤和流程
1
结构设计
2
确定主轴箱的内部结构和布局。
四工位组合机床的plc控制系统设计 正文2
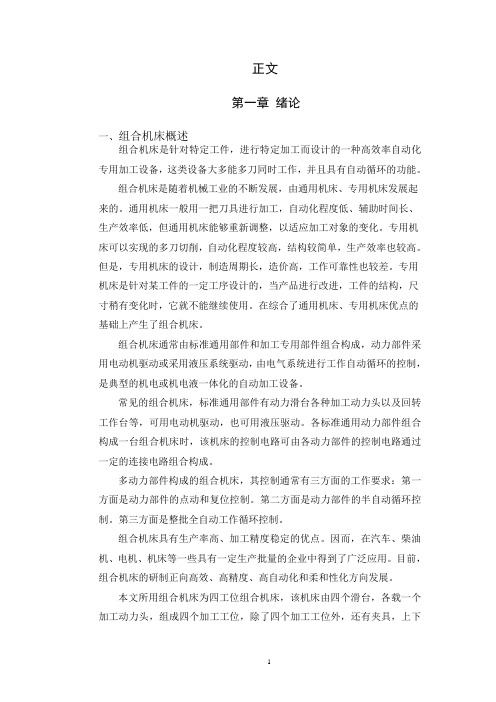
正文第一章绪论一、组合机床概述组合机床是针对特定工件,进行特定加工而设计的一种高效率自动化专用加工设备,这类设备大多能多刀同时工作,并且具有自动循环的功能。
组合机床是随着机械工业的不断发展,由通用机床、专用机床发展起来的。
通用机床一般用一把刀具进行加工,自动化程度低、辅助时间长、生产效率低,但通用机床能够重新调整,以适应加工对象的变化。
专用机床可以实现的多刀切削,自动化程度较高,结构较简单,生产效率也较高。
但是,专用机床的设计,制造周期长,造价高,工作可靠性也较差。
专用机床是针对某工件的一定工序设计的,当产品进行改进,工件的结构,尺寸稍有变化时,它就不能继续使用。
在综合了通用机床、专用机床优点的基础上产生了组合机床。
组合机床通常由标准通用部件和加工专用部件组合构成,动力部件采用电动机驱动或采用液压系统驱动,由电气系统进行工作自动循环的控制,是典型的机电或机电液一体化的自动加工设备。
常见的组合机床,标准通用部件有动力滑台各种加工动力头以及回转工作台等,可用电动机驱动,也可用液压驱动。
各标准通用动力部件组合构成一台组合机床时,该机床的控制电路可由各动力部件的控制电路通过一定的连接电路组合构成。
多动力部件构成的组合机床,其控制通常有三方面的工作要求:第一方面是动力部件的点动和复位控制。
第二方面是动力部件的半自动循环控制。
第三方面是整批全自动工作循环控制。
组合机床具有生产率高、加工精度稳定的优点。
因而,在汽车、柴油机、电机、机床等一些具有一定生产批量的企业中得到了广泛应用。
目前,组合机床的研制正向高效、高精度、高自动化和柔和性化方向发展。
本文所用组合机床为四工位组合机床,该机床由四个滑台,各载一个加工动力头,组成四个加工工位,除了四个加工工位外,还有夹具,上下料机械手和进料器,四个辅助装置以及冷却和液压系统共14个部分。
机床的四个加工动力头同时对一个零件的四个端面以及中心孔进行加工,一次加工完成一个零件,由上料机械手自动上料,下料机械手自动取走加工完成的零件,零件每小时可加工80件。
(完整版)组合机床总体设计
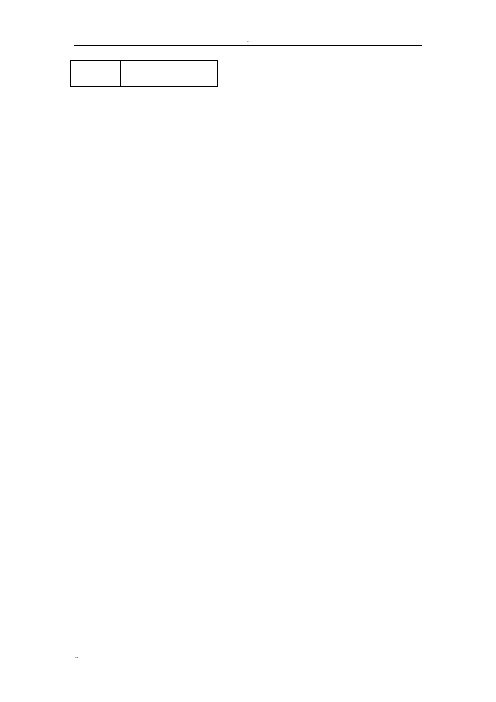
2009年5月23 日目录第一部分组合机床总体设计 (3)一、工艺方案的制定 (3)1.1零件工艺基面的选择 (3)1.2 加工工艺分析 (3)1.3 孔切削用量的选择 (3)二、机床配置型式和结构方案的确定 (4)三、组合机床方案图纸设计 (4)3.1被加工零件工序图 (4)3.2加工示意图 (5)3.2.1加工示意图的编制步骤 (6)3.3组合机床生产率的计算 (11)3.3.1生产率的计算和生产率计算卡的绘制 (11)3.4机床联系尺寸图的绘制 (13)3.4.1机床主要联系尺寸的确定 (14)第一部分组合机床总体设计一、工艺方案的制定1.1零件工艺基面的选择由于被加工零件(缝纫机体)是箱体类零件,所以我选择了“一面二孔”的定位方法。
该方法有以下特点:a、很简便的消除工件的六个自由读,使工件获得稳定的固定位置;b、有同时加工五个面的可能。
既能高度集中加工工序,又有利于提高各面上孔的位置精度;c、该方法可以作为从粗加工到精加工的全部工序加工的基准,使整个工艺过程实现基准统一;d、该方法使夹紧方便,夹紧机构简单。
容易使夹紧力对准支承,消除夹紧力引起工件变形对加工精度的影响。
为了保证零件的加工精度及技术要求,工艺基面必须规定相应的公差。
根据缝纫机体零件的大小,定位销孔径选择∅16,太小时,定位销很细,加工中易受力产生较大的变形。
销孔的精度为2级,两销孔中心距定为321毫米,其公差为±毫米。
0.061.2 加工工艺分析由于被加工零件只需要钻孔,所以该机床只有一个钻孔加工工艺。
而且钻孔深度不大,属于一般钻孔。
1.3 孔切削用量的选择由于该缝纫机体是铸铁件,而且硬度大概在200~241左右,根据下表选取切削用量。
表1用高速钢钻头加工铸铁件的切削用量二、机床配置型式和结构方案的确定由于被加工的缝纫机体是一个箱体件,一次只加工一个,生产率要求不是很高,所以我选择了单工位组合机床,而且该零件孔中心线与定位基准面平行,而且需要同时加工两个面,因此选择单工位组合机床中的卧式双面组合机床。
组合机床说明书正文部分

四川理工学院毕业设计(论文)1 / 40第一章 概述组合机床的组成和特点:组合机床是根据工件加工需要,以大量通用部件为基础,配以少量专用部件组成的一种高效专用机床。
组合机床中各种部件都是具有一定独立功能的部件,并且大都是已经标准化、系列化和通用化的通用部件。
只有多轴箱和夹具是根据工件的尺寸形状和工艺要求设计的专用部件,但其中绝大多数零件如夹压元件、传动件等也是标准件和通用件。
通用部件是组合机床的基础。
用以实现机床切削和进给运动的通用部件,如各种工艺切削头、动力箱、动力滑台等动力部件。
用以安装动力部件的通用部件,如底座等。
组合机床的特点:⒈ 主要用于箱体零件和复杂的孔面加工。
⒉ 生产率高。
因为工序集中,可多面、多工位、多轴、多刀同时自动加工。
⒊ 加工精度稳定。
因为工序固定,可选用成熟的通用部件、精密夹具和自动工作循环来保证加工精度的一致性。
⒋ 研制周期短,便于设计、制造和使用维护,成本低。
因为通用化、系列化、标准化程度高,通用零部件占70-90%,通用部件可组织批量生产,进行预制或外购。
⒌ 自动化程度较高,劳动强度低。
⒍ 配置灵活。
因为结构模块化、组合化。
可按工件或工序要求,用大量通用部件和少量专用部件灵活组成各种类型的组合机床及自动线;机床易于改装,产品及工艺变化时,通用部件一般可以重复利用。
组合机床常用的通用部件有:床身(侧底座)、底座(包括中间底座和立柱底座)、立柱、动力箱、动力滑台、各种工艺切削头等。
对于一些按顺序加工的多工位组合机床,还有移动工作台或回转工作台。
动力箱、各种工艺切削头和动力滑台是组合机床完成切削主运动和进给运动的动力部件,其中还有可能同时完成切削主运动和进给运动动力头。
床身、立柱、中间底座等是组合机床的支承部件,起着机床的基础骨架作用。
组合机床的刚度和部件之间的精度保持性,主要由这些部件保证。
除了上述主要部件之外,组合机床还有各种控制部件,主要指挥机床按顺序动作,以保证机床按规定的程序进行工作。
组合机床简介(5)

(4) 鼓轮式组合机床
用绕水平轴间歇转位的回转鼓轮工作台输送工件,其
工件数一般有3、4、5、6、8个(图中为6工位,其中1个为
装卸工位,其余5个为加工工位)。这种机床一般以卧式配 置为主,可以同时对工件的两个端面进行加工。
动力箱:常与专用部件多轴箱配合使用以实现主运动。 专用切削头:如钻削头、铣削头、镗削头、攻丝头等。
进给运动动力部件:动力滑台。
2、支承部件 功用:用来安装动力部件、输送部件等部件。
立柱:可代替侧底座,组成立式机床; 立柱底座:支撑立柱; 中间底座:安装夹具和输送部件。
侧底座:安装动力滑台及各种切削头,组成卧式机床;
合机床高。但由于有转位或移位的定位误差,所以加 工精度较低,且结构复杂,造价高,多用于大批大量 生产中对较复杂的中小型零件加工。
(1) 移动工作台组合机床 用沿直线间歇移动的 移动工作台完成工位间工
件的输送,工位数一般为
2-3个。常用于加工孔间 距较近的工件。
(2) 回转工作台组合机床 用绕竖直轴间歇转位 的回转工作台输送工件, 其工位数一般有2、3、4、 5、6、8、l0、12个(图 中是4工位,其中1个为装 卸工位,其余3个为加工 工位)。这种机床可配置
(d)
(e)
(f)
单工位组合机床
2、多工位组合机床 工作特点:这类机床有二个或二个以上加工工位,
夹具在工作台上按预定的工作循环使工件顺次从一个
工位输送到另一个工位,即换位,以便在各工位上完
成同一加工部位多工步加工和不同部位加工,从而完
成一个或数个表面的较复杂的加工工序。
应用场合:这类机床工序较集中,生产率较单工位组
三、特点
组合机床与一般的专用机床一样,是针对特定工序ቤተ መጻሕፍቲ ባይዱ
组合机床

1.组合机床是以大量的约(70%--90%)通用部件为基础,配以少量专用部件,对一种或若干种工件按预先确定的工序进行加工的机床。
2.组合机床的特点:①设计制造周期短,经济效益好②自动化程度高,产品质量稳定,劳动强度低③与一般机床相比,结构稳定,工作可靠,使用和维修方便④产品加工质量靠工艺装备保证,对工人技术水平要求不高⑤其通用部件可以重复使用,不必另行设计制造⑥能更好的适应大规模和自动化生产需要。
2.组合机床常用的通用部件:动力部件、输送部件、支承部件、控制部件、辅助部件。
(1)动力部件有四种:①机床主运动动力部件:形成机床切削速度或消耗主要动力的工作运动部件。
②机床进给运动动力部件:使工件的多余材料被去除的工作运动部件。
③既能实现主运动又能实现进给运动的动力部件④为单轴头变化主轴转速的跨系列通用部件。
(2)输送部件:它具有定位和夹紧装置,用于安装工件并运送到预定工位的通用部件。
如回转工作台、移动工作台、回转毂轮和自动线的输送装置等。
(3)支承部件:用于安装动力部件和输送部件等的通用部件——侧底座、立柱、立柱底座和中间底座等。
(4)控制部件:用于控制具有运动功能的各个部件,以保证实现组合机床工作循环。
(5)辅助部件:除上述部件以外的其他部件,例:冷却、润滑、排屑以及自动线的清洗装置,气动或液压夹紧装置和机械扳手等。
3.组合机床的配置形式:(1)大型组合机床的配置形式:①固定式夹具的单工位组合机床②移动式夹具的(多工位)组合机床③转塔主轴箱式组合机床。
(2)小型组合机床的特点和配置形式:特点:①加工工件材料品种多②部件综合刚读低,机床不宜加工多层壁的同轴孔工件③避免粗、精加工工位同时切削,防止粗加工的振动影响精加工质量④一般为多刀、多工位加工⑤工作台面积小,夹具和动力部件易发生碰撞⑥生产效率高。
配置型式:①固定式夹具的单工位组合机床②移动式夹具的(多工位)组合机床.4.组合机床自动线的分类:直接输送式、间接输送、悬挂式输送。
6.4 组合机床设计_总体设计3
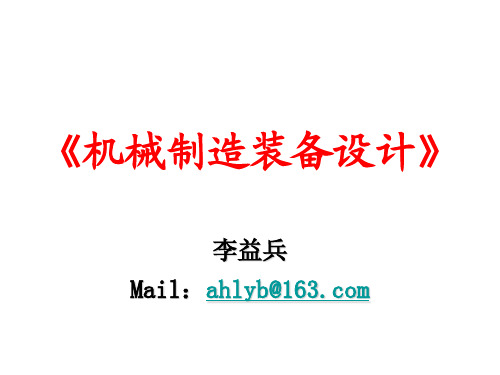
③ 夹具底座与中间底座连接所需要的尺寸。
④ 对于随行夹具需从机床下方返回(从中间底座中间通过)的 自动线,机床装料高度 H=1m左右。
第二节
三图一卡——机床联系尺寸图
4)确定中间底座轮廓尺寸 中间底座轮廓尺寸——以满足夹具在其上安装的需要为原则。 ① 长度方向尺寸 根据滑台和滑座及其侧底座的位置关系、各 部件联系尺寸的合理性来确定。重点如下:
◆ 完整标注机床各主要组成部件的轮廓尺寸及相关联系尺寸。 ◆ 应清楚表示运动部件的原位、终点状态及运动过程情况,以 确定机床最大轮廓尺寸。 ◆ 应注明工件、夹具、动力部件、中间底座对中心线间的位置
关系。
◆ 应注明电动机的型号、功率、转速及通用部件的型号和主要 轮廓尺寸;对机床所有部件分组编号。 以联系尺寸图为基准进行细化,添加电气、液压控制装置,润 滑、冷却、排屑装置,加注技术要求说明,则构成组合机床总图
v快(刀具)< v’ 快(滑台), v工(刀具)> v’滑台额定min
第二节
三图一卡——机床联系尺寸图
选用动力滑台时,必须考虑滑台允许的最
◆ 确定滑台行程
大行程。设计时所确定的动力部件总行程应满足:
L总(动力) < L最大(滑台)
滑台总行程为 = 工作总行程 + 前备量 + 后备量 前备量 考虑刀具磨损或补偿制造、安装误差,动力部件尚可 向前调节的距离,一般取值 >10 ~ 20mm。 后备量 考虑刀具从接杆中或刀 具接杆一起从主轴孔中取出所需要的 轴向距离,一般取值≥40~50mm。 要求:工作总行程 + 前备量 + 后备量 < L最大(滑台)
三图一卡——机床联系尺寸图
图形布置应与实际机床工作位置一致。
组合机床设计总体设计
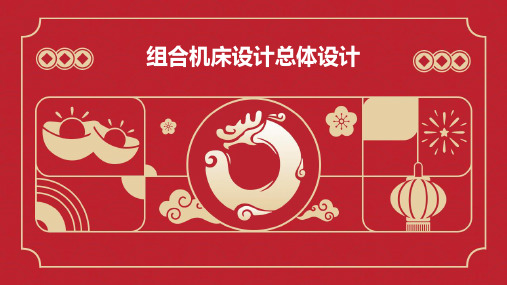
电子和家电制造
组合机床可以用于加工各种电 子元器件和家用电器零部件。
02 组合机床设计流程
CHAPTER
设计准备
明确设计任务
01
确定组合机床的加工要求、生产能力、工艺方案等,为后续设
计提供指导。
收集资料
02
收集相关标准、技术资料、市场需求等信息,为设计提供依据
和支持。
制定设计计划
03
根据设计任务和收集的资料,制定详细的设计计划,包括时间
继电器和接触器
用于实现电气控制回路,保证设备的安全运行。
控制程序设计
输入程序设计
根据加工需求,设计输入界面,方便用户输入加工参数和操作指 令。
输出程序设计
根据加工过程和控制需求,设计输出界面,实时显示加工状态和 结果。
控制算法设计
根据加工特点和要求,设计控制算法,实现高效、稳定的加工过 程。
控制精度与可靠性设计
物流分析
优化物料流动路径,减少物料搬运距 离和时间。
设备选型与配置
根据工艺需求合理选择设备型号,并 优化设备配置。
环境与安全考虑
确保作业环境符合安全和环保要求, 提供必要的防护措施。
04 组合机床传动系统设计
CHAPTER
传动系统类型
机械传动
液压传动
利用机械方式传递动力和运动,包括齿轮 、带、链等传动方式。
根据切屑的形状、大小和排出要求,选择合适的排屑方式, 如刮板式、螺旋式等。
排屑装置的结构设计
排屑装置应具备结构简单、排屑效果好、安全可靠的特点。
安全防护装置设计
01
安全防护装置的作用
安全防护装置用于保护操作者和机床设备的安全,防止意外事故的发生。
机械制造装备设计习题与思考题
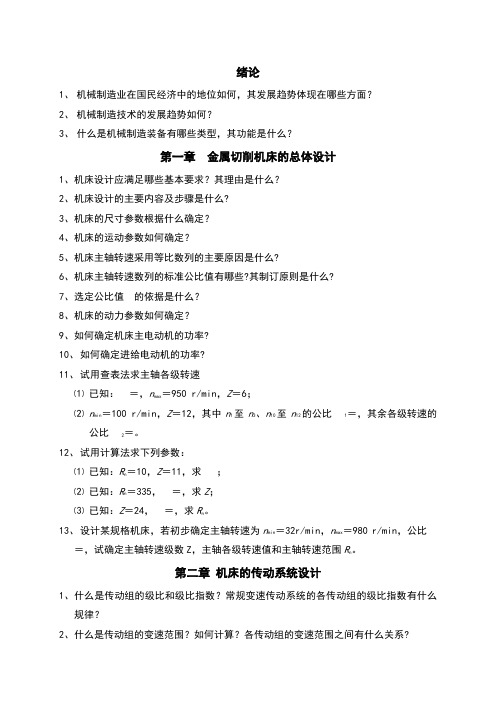
绪论1、机械制造业在国民经济中的地位如何,其发展趋势体现在哪些方面?2、机械制造技术的发展趋势如何?3、什么是机械制造装备有哪些类型,其功能是什么?第一章金属切削机床的总体设计1、机床设计应满足哪些基本要求?其理由是什么?2、机床设计的主要内容及步骤是什么?3、机床的尺寸参数根据什么确定?4、机床的运动参数如何确定?5、机床主轴转速采用等比数列的主要原因是什么?6、机床主轴转速数列的标准公比值有哪些?其制订原则是什么?7、选定公比值的依据是什么?8、机床的动力参数如何确定?9、如何确定机床主电动机的功率?10、如何确定进给电动机的功率?11、试用查表法求主轴各级转速⑴已知:=,n max=950 r/min,Z=6;⑵n min=100 r/min,Z=12,其中n1至n3、n10至n12的公比 1=,其余各级转速的=。
公比212、试用计算法求下列参数:⑴已知:R n=10,Z=11,求;⑵已知:R n=335,=,求Z;⑶已知:Z=24,=,求R n。
13、设计某规格机床,若初步确定主轴转速为n min=32r/min,n max=980 r/min,公比=,试确定主轴转速级数Z,主轴各级转速值和主轴转速范围R n。
第二章机床的传动系统设计1、什么是传动组的级比和级比指数?常规变速传动系统的各传动组的级比指数有什么规律?2、什么是传动组的变速范围?如何计算?各传动组的变速范围之间有什么关系?3、某机床的主轴转速级数Z=18,采用双副和三副变速组,试写出符合级比规律的全部结构式,并指出其中扩大顺序与传动顺序一致的和不一致的方案各有多少个。
4、判断下列结构式是否符合级比规律,符合者需说明其扩大顺序与传动顺序是否一致;不符者则需简要说明会出现什么情况。
⑴ 8=21×22×24;⑵ 8=24×21×22;⑶ 8=22×21×23;⑷ 8=22×23×245、画出结构式12=23×31×26相应的结构网,并分别求出第一变速组和第二扩大组的传动副数、级比、级比指数和变速范围。
第四章组合机床

被 加 工 零 件 工 序 图
在被加工零件工序图上应标注的内容
1)加工零件的形状、主要外廓尺寸和本机床要加工部 位的尺寸、精度、表面粗糙度、形位精度等技术要求, 以及对上道工序的技术要求等。 2)本工序所选定的定位基准、夹紧部位及夹紧方向。 3)加工时如需要中间向导,应表示出工件与中间向导 间有关部位的结构和尺寸,以便检查工件、夹具、刀 具之间是否相互干涉。 4)被加工零件的名称、编号、材料、硬度及被加工部 位的加工余量等。
普通高等教育“十一五”国家级规划教材
第四章 组合机床设计
主 编:李庆余 孟广耀 副主编:张 佳 董 锋
目录
第一节 概述 第二节 组合机床总体设计 第三节 通用多轴箱设计
第一节 概述
组合机床是根据工件加工需要,以大 量系列化、标准化的通用部件为基础, 配以少量专用部件,对一种或数种工件 按预先确定的工序进行加工的高效专用 机床。
在每一工位上可以同时加工一个或几个工件,其上 的夹具和工件安装在绕垂直轴线回转的回转工作台 上,并随其作周期转动以实现工位的变换。由于这 种机床适宜于对中小型工件进行多面、多工序加工, 具有专门的装卸工位,使装卸工件的辅助时间和机 动时间重合,所以能获得较高的生产率。
多工位组合机床
3.中央立柱式组合机床
(3)主轴的结构类型、尺寸及外伸长度;刀具类型、 数量和结构尺寸;接杆(包括镗杆)、浮动卡头、 导向装置、攻丝靠模装置的结构尺寸;刀具与导向 装置的配合,刀具、接杆、主轴之间的连接方式。 刀具应按加工终了位置绘制。
2.绘制加工示意图的有关计算
加工示意图绘制时,应进行刀具、导向装置的 选择及切削用量、转矩、进给力、功率和有关联系 尺寸的计算。
三、组合机床的通用部件
第四章 组合机床设计(3)
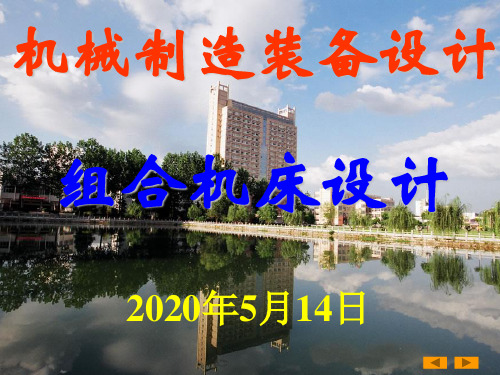
第二节 1.被加工零件工序图 1.被加工零件工序图
(1)工序图的作用 被加工零件工 序图是组合机床设 计的主要依据, 计的主要依据,也 是制造、使用、 是制造、使用、检 验和调整机床的重 要技术文件。 要技术文件。
组合机床总体设计
第二节 组合机床总体设计
(2)工序图表示的内容 1)零件的形状、 零件的形状、 轮廓尺寸及与本机床 设计有关的部位的结 构形状和尺寸。 构形状和尺寸。 如需设置中间导 向套,还应表示内部 向套, 的肋、 的肋、壁布置和有关 的结构形状及尺寸, 的结构形状及尺寸, 以检查工件、夹具、 以检查工件、夹具、 刀具是否干涉。 刀具是否干涉。
◆ 有时受结构限制,使用双导向或多导向时,也可固定导向 有时受结构限制,使用双导向或多导向时, 和旋转导向混合使用。 和旋转导向混合使用。
第二节 组合机床总体设计
③ 确定导向主要参数 导向主要参数 导套的直径及公差配合,导套的长度及离工件 导套的直径及公差配合, 端面的距离等。结合实际加工要求,查阅设计手册选择参数。 端面的距离等。结合实际加工要求,查阅设计手册选择参数。
◆ 零件图上不对称 位置尺寸公差换算成对 称尺寸公差时,确定公 称尺寸公差时, 差值要考虑: 差值要考虑:能够达到 零件要求的精度,用组 零件要求的精度, 合机床能够加工出来。 合机床能够加工出来。 如 零件图中尺寸
10−0.1 应换算为工序图 −0.3 中的尺寸 9.8 0.1,以 9.8±
便后续确定导向孔与主 轴孔的位置坐标尺寸。 轴孔的位置坐标尺寸。
第二节 组合机床总体设计
2)加工所用的定 位基准、 位基准、夹压部位及 夹压方向。 夹压方向。 3)本工序加工部 位尺寸精度、 位尺寸精度、表面粗 糙度、 糙度、形状位置尺寸 精度; 精度;对前道工序提 出的定位基准要求。 出的定位基准要求。 4)被加工零件的 编号、名称、材料、 编号、名称、材料、 硬度、 硬度、重量及加工部 位的余量等。 位的余量等。
组合机床总结
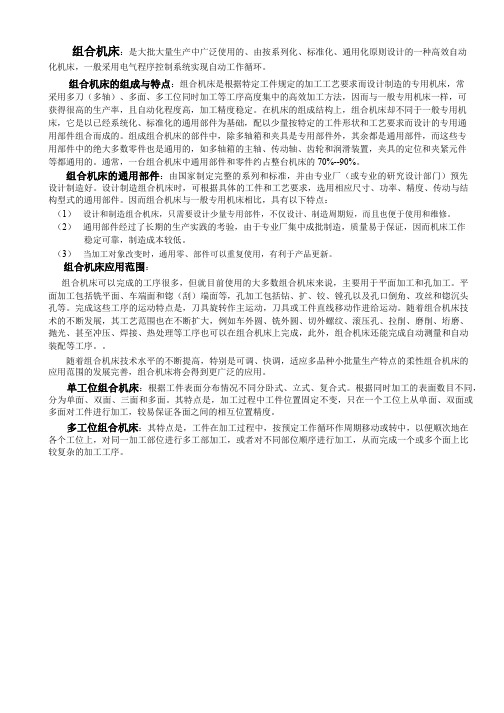
组合机床:是大批大量生产中广泛使用的、由按系列化、标准化、通用化原则设计的一种高效自动化机床,一般采用电气程序控制系统实现自动工作循环。
组合机床的组成与特点:组合机床是根据特定工件规定的加工工艺要求而设计制造的专用机床,常采用多刀(多轴)、多面、多工位同时加工等工序高度集中的高效加工方法,因而与一般专用机床一样,可获得很高的生产率,且自动化程度高,加工精度稳定。
在机床的组成结构上,组合机床却不同于一般专用机床,它是以已经系统化、标准化的通用部件为基础,配以少量按特定的工件形状和工艺要求而设计的专用通用部件组合而成的。
组成组合机床的部件中,除多轴箱和夹具是专用部件外,其余都是通用部件,而这些专用部件中的绝大多数零件也是通用的,如多轴箱的主轴、传动轴、齿轮和润滑装置,夹具的定位和夹紧元件等都通用的。
通常,一台组合机床中通用部件和零件约占整台机床的 70%--90%。
组合机床的通用部件:由国家制定完整的系列和标准,并由专业厂(或专业的研究设计部门)预先设计制造好。
设计制造组合机床时,可根据具体的工件和工艺要求,选用相应尺寸、功率、精度、传动与结构型式的通用部件。
因而组合机床与一般专用机床相比,具有以下特点:(1)设计和制造组合机床,只需要设计少量专用部件,不仅设计、制造周期短,而且也便于使用和维修。
(2)通用部件经过了长期的生产实践的考验,由于专业厂集中成批制造,质量易于保证,因而机床工作稳定可靠,制造成本较低。
(3)当加工对象改变时,通用零、部件可以重复使用,有利于产品更新。
组合机床应用范围:组合机床可以完成的工序很多,但就目前使用的大多数组合机床来说,主要用于平面加工和孔加工。
平面加工包括铣平面、车端面和锪(刮)端面等,孔加工包括钻、扩、铰、镗孔以及孔口倒角、攻丝和锪沉头孔等。
完成这些工序的运动特点是,刀具旋转作主运动,刀具或工件直线移动作进给运动。
随着组合机床技术的不断发展,其工艺范围也在不断扩大,例如车外圆、铣外圆、切外螺纹、滚压孔、拉削、磨削、垳磨、抛光、甚至冲压、焊接、热处理等工序也可以在组合机床上完成,此外,组合机床还能完成自动测量和自动装配等工序。
《组合机床》复习概要.docx

组合机床的特点:1,通用性强,具有通有机床的特点,便于产品更,新。
2,专用性强,具有专用机床的特点,易实现最合理的加工工艺。
3,生产率高,易于组织自动化生产。
4, 零件精度由机床控制,能保证加工质量,5,工作可靠,维护方便。
6,设计,制造周期短,经济效益好。
工艺范围:钻孔,钻深孔,扩孔和扩锥孔,镇孔,攻丝,外螺纹加工,车槽,球面及内孔端面,车外圆,加工阶梯孔,铳平面。
分类:大型U,小型H,微型W,数控K单工位大型组合机床配置形式:卧式,立式,复合式,倾斜式。
多工位大型组合机床:夹具固定式,工作台移动式,工作台回转式,鼓轮式,中央立柱式。
组合机床通用部件的分类:动力部件支承部件输送部件控制部件辅助部件。
组合机床总体设计的步骤:调查制造工艺方案机床总体设计部件设计工作图设计零件工艺分析:1,产品及零件图纸的分析。
2,零件技术要求的分析。
零件结构特点与结构工艺分析。
4,生产纲领分析。
拟定工艺路线:1,粗、精加工分开。
2,工序合理集中。
3,先粗后精,先面后孔。
4,采用易于保证技术要求的工艺方法和先进工艺。
组合机床通用部件的选择依据:切削过程屮所需的切削力和争削功率。
选定后再校验切削扭矩是否合格。
而以上三者的确定首先要确定加工过程中的切削用量。
组合机床争削用量的选择有以下特点:1,组合机床大多数情况下是多刀多刃同时工作,应合理选用切削用量使所有刀具每分钟的进给量相同。
2,当机床生产率受到限制性工序上争削用量的限制时,可适当加大争削用量以缩短加工时间提高生产率。
3,对于复合刀具中的各把刀具,其合理的争削用量也是不同的,选择原则是:转速按低切削速度的上限取,进给量按低进给量的上限取。
4,选用的每分钟进给量不能小于动力头允许的最小值。
5,主轴转速不可使刀具在导向套内的线速度超过允许值。
6,当某些刀具的导向、润滑条件不良吋,可适当降低其切削速度。
机械动力滑台:进给稳定,修理技术要求较液压滑台低,但进给确定后不易变换。
- 1、下载文档前请自行甄别文档内容的完整性,平台不提供额外的编辑、内容补充、找答案等附加服务。
- 2、"仅部分预览"的文档,不可在线预览部分如存在完整性等问题,可反馈申请退款(可完整预览的文档不适用该条件!)。
- 3、如文档侵犯您的权益,请联系客服反馈,我们会尽快为您处理(人工客服工作时间:9:00-18:30)。
第四章
组 合 机 床
Transfer and unit machine tool
第一节 组合机床的组成及工艺特点
第四章 组合机床
组合机床的组成
以系列化、标准化的通用部件为基础,配以少量专
用部件组成的多轴、多刀、多工序、多面同时加工 的专用机床。通用件和标准件占70~80%。 加工效率高
液压滑台:HY 机械滑台:HJ
镗孔车端面头:TC 钻削头:TZ
立柱:CL 立柱底座:CD
铣削头:TX
镗削头:TA
第四章 组合机床
动力箱:TD
侧底座:CC
中间底座:CZ
支架:CJ
第四章 组合机床
二、动力滑台 1. 液压滑台 A型:双矩形导轨 B型:山型、矩形导轨
第四章 组合机床
第四章 组合机床
二、机械滑台
第四章 组合机床
第四章 组合机床
2. 多工位组合机床 工序高度集中,装卸 时间与加工时间重合, 效率高。 存在移位和转位定位 误差,精度较低。 适合于大批、大量生 产中小型零件
第四章 组合机床
三、组合机床的工艺范围及特点
适合大、中型箱体类零件加工 主要用于加工箱体等的平面和孔 生产率高 加工精度稳定
减少加工时间和辅助时间,并尽可能使辅助时间和加工时 间重合。 使每个工位安装多个工件同时进行多刀加工,以实现高度 工序集中。
第四章 组合机床
组合机床的组成
第四章 组合机床
第四章 组合机床
第四章 组合机床
第四章 组合机床
第四章 组合机床
组合机床的配置形式
※ 单工位组合机床 可保证有较高的位置精度,适用于大、中型箱体 类零件加工
设计、制造周期短、维修方便
自动化程度高 配置灵活,有利于产品更新 面临以高速切削技术为基础的柔性制造技术的挑
战
第四章 组合机床
汽车轮毂螺栓孔高速加工实例(日产公司)
1 2 3 4
钻孔 表面倒棱 内侧倒棱 铰孔
高速钻孔 表面和内侧倒棱
专用组合机床 5轴×4工序 = 20轴(3万件/月) 刚性(零件、孔数、孔径、孔 型固定不变)
第四章 组合机床
第四章 组合机床
三、交流伺服数控机械滑台
第四章 组合机床
三、动力箱
齿轮传动 联轴器传动
第四章 组合机床
第四章 组合机床
第四章 组合机床
四、单轴头
第四章 组合机床
第四章 组合机床
第四章 组合机床
第四章 组合机床
第四章 组合机床
第四章 组合机床
第四章 组合机床
第四章 组合机床
高速加工中心 1台1轴1工序(3万件/月) 柔性(零件、孔数、孔 径、孔型可变)
第四章 组合机床
机械制造技术装备及设计
第四章
组 合 机 床
Transfer and unit machine tool
第二节 组合机床的通用部件
第四章 组合机床
一、通用部件的型号编制 △ □
□□ □—△
型别(用Ⅰ、Ⅱ区分) 结构特性代号(用字母A、B区分) 主参数(与其配套的滑台台面宽度头两位数表示) 通用部件字头 改进设计顺序号