除蜡水配方分析超声波除蜡水的配制(2020新版4.0)
除蜡水配制

除蜡水配制原理及指标时间:2011-01-26 03:39:14 科威达环保器材信息网点击:165 次导读:除蜡水作为目前常用的清洗产品而广泛应用于电镀,钟表,饰品及工艺品等五金行业工件抛光后的除蜡工艺。
其配方技术的研究与开发,主要是通过表面活性剂,助剂,缓蚀剂,助溶剂等的选择,复合,调配,使产品在常温,中温,超声波,浸洗等处理工艺中都能够迅速彻底的去除各种蜡垢,油污。
对不锈钢,碳钢,锌,镁,铝,铜等各种除蜡水配制原理及指标主题关键词:缓蚀剂除蜡水作为目前常用的清洗产品而广泛应用于电镀,钟表,饰品及工艺品等五金行业工件抛光后的除蜡工艺。
其配方技术的研究与开发,主要是通过表面活性剂,助剂,缓蚀剂,助溶剂等的选择,复合,调配,使产品在常温,中温,超声波,浸洗等处理工艺中都能够迅速彻底的去除各种蜡垢,油污。
对不锈钢,碳钢,锌,镁,铝,铜等各种基材不发生腐蚀,氧化等负作用。
有很好的环保性能以及较长的使用寿命。
另外,产品的粘度,颜色,气味,透明度等外观性能也要进行合理的调配,满足客户的心理需求,提升产品的出啦原理除蜡原理金属工件经过抛光蜡的抛光后,其表面的污垢成分主要为石蜡,脂肪酸,松香皂,金属氧化物,磨料,矿物油,动植物油,天然蜡以及一些打磨布碎片,打磨出来的金属基体的粉末及其氧化物。
抛光后的工件上,蜡垢就会以机械吸附,分子间吸附和静电吸附等方式粘附在工件上。
而这些蜡垢的颗粒直径小于0.1μm时就很难除去。
除蜡水制备的关键就在于对各种表面活性剂,助剂,缓蚀剂,助溶剂等成分进行合理的复配。
通过降低表面张力,改善润湿渗透性能和乳化,溶解,分散增溶性能,从而增强产品的渗透力和溶解力,以达到快速去除蜡垢的目的。
除蜡水制备的关键在于表面活性剂的选择和复配。
金属清洗产品的制备中,阴离子表面活性剂和非离子表面活性剂的复配早就广泛的使用。
加入离子型表面活性剂的非离子表面活性剂在使用中有了较宽的温度使用范围,同时也提高了其渗透性能和乳化性能,形成混合胶团。
除蜡效果太差了?如何选择除蜡水添加剂

除蜡效果太差怎么办?工业清洗时,速度非常慢?清洗后金属发生腐蚀?清洗后的工件边角盲孔总有残余的蜡垢?除蜡水是一种广泛应用于电镀、钟表、工艺品、饰品等五金行业工件的抛光之后的除蜡工艺。
除蜡水主要是由一些表面活性剂、助剂、缓蚀剂、助溶剂等的调配,从而使产品在常温、加温、超声波、浸泡等工艺中迅速、彻底去除蜡垢,对不锈钢、碳钢、锌合金、铝合金、镁合金、铜合金等各种基材不产生腐蚀、氧化等副作用,有较长的使用寿命和环保性能。
众所周知,除蜡的快慢、除蜡效果对生产非常重要,否则会影响后续的工艺进行。
然而市面上现有的除蜡水虽然也能够除蜡,但对于较复杂的工件,或有盲孔的产品总会出现清洗不彻底的问题。
那么如何选择合适的除蜡水添加剂呢?有机胺皂类化合物具有脱脂能力强、水溶性佳、配伍性好、耐用性好、无磷环保等特点。
适用于除油/蜡水、玻璃清洗剂、金属切削液及金属加工清洗液等体系,可明显提高体系的润湿性和除油、除蜡能力。
特种有机胺油酸酯为特种有机胺与油酸经化合而成的有机化合物,易溶于水,适用于除蜡水、金属加工液及清洗剂。
产品具有超强的除蜡性能和一定的除油效果,绿色环保,对环境无害,具有极好的防锈性、渗透性和一定的润滑性。
异构醇羧酸盐是新型烷基羧酸异构支链醇胺皂类有机化合物,具有脱脂能力强、水溶性佳、配伍性好、耐用性好、无磷环保等特点。
适用于除油/蜡水、玻璃清洗剂、金属切削液及金属加工清洗液等体系,可明显提高体系的润湿性和除油、除蜡能力,是异构醇油酸皂和乙二胺油酸酯最佳的代替品。
除蜡效果对生产非常重要,会影响后续的工艺进行。
因此,选择良好的除蜡水添加剂可以提高除蜡性能,从而带来良好的经济效益。
随着工业发展、工业品类的增多、许多工件越来越精细化、多样化,所以会出现工件的夹缝和边角清洗不彻底、工件腐蚀等问题,清洗难度增加。
因此,市场需要清洗力度更大,应用更广泛的清洗剂。
除蜡水配方分析

首饰经过抛光打磨后才能展现金属的表面光泽,而抛光后的抛光膏却难以清除,在此本论文就是要解决抛光膏的清洗问题。
笔者对国内工业抛光膏的成分进行了总结归类,其成分主要是磨料与脂肪酸、油脂(动植物油)、矿物蜡,而对进口首饰用抛光膏的分析结果表明与国内工业抛光膏的成分差异较大,其黏结剂组成中不含国内工业抛光膏含有的油脂与矿物蜡成分,只是硬脂酸与软脂酸的简单混合,不含有国产抛光膏含有的相对难洗去的矿物蜡,清洗也相对容易。
通过对首饰贵金属合金与铜合金的成分的资料总结与对市面的贵金属合金化的材料进行电子探针能谱测试分析,除了传统的贵金属合金,现在市面上的首饰合金多以铜、锌、镍等贱金属作为添加剂来合金化贵金属以降低成本。
由于贵金属中较大量地加入的锌、铝、锡致使首饰合金不耐碱腐蚀。
通过对抛光膏的成分的分析,可知抛光膏的清洗可通过与碱性试剂的皂化作用除去脂肪酸与油脂类成分,通过碱性试剂与表面活性剂的乳化、分散作用溶解掉矿物蜡,而抛光膏中的微细磨料能被分散悬浮在溶液中。
超声波的空化作用使清洗的效果与效率都得到了很大的提高,促进了污垢的清洗。
在前人研究的基础上,通过对各种碱剂的性质与表面活性剂的性质进行分析并选择试剂,大量反复的实验研究,成功研制出一种高效、经济、易于配制的清除抛光膏的配方。
所研制的除蜡水的特点是当硼砂加入到一定量时与工业清洗中的常用碱剂(碳酸钠、磷酸盐、三聚磷酸钠)协同会产生很好的防蚀与去污能力,而偏硅酸钠的加入,让配方的性能更完善,少量非离子表面活性剂的加入则让除蜡水在清除矿物蜡时更有效。
对除蜡后的残留液的清洗进行实验,提出了清洗的流程。
给出了常见宝石中应限用除蜡水的品种,完善了研制的除蜡水的实际生产应用性能。
分析知硼砂的缓蚀作用机理与磷酸三钠、碳酸钠的一致,都是生成沉淀型保护膜的原因。
新版除蜡水配方参考

新版除蜡水配方参考
需要用到的原料:
1、 EDO-86(乙二胺油酸酯) 15.7%
2、 DF-21 (C13 异丙醇酰胺) 12.0%
3、烷基胺酯OTE 2%
4、干净水 70.2%
EDO-86:具有防锈、溶蜡、皂化、润滑、去污、PH值调节与稳定等性能特点。
DF-21:具有乳化性、渗透性、油污分散性以及炭黑碳粒包裹剥离特性。
OTE:阴离子表面活性剂,具有乳化、渗透、脱脂、防锈、洁净能力.
这三种原材料都是环保型表面活性剂,先将EDO-86、DF-21、OTE 混合搅拌反应均匀透明(搅拌5分钟)后;加入余量水,搅拌混合均匀即可。
生产中由于搅拌的速度不同可能会有泡沫产生,看起来像是浑浊,放置一段时间就会透明,可清洗任何材质,工件不变色,不发黑,表面光亮度提高,槽液浮油减少,自净化能力提高。
使用条件:
温度:80-100℃
清洗方式:超声波清洗
开槽比例:3—8%,推荐比例:5%
务必满足以上条件才能达到最好除蜡清洗质量!
极个别合金易腐蚀工件案例清洗可加缓蚀剂(W-10A)解决!。
除蜡水配方

除蜡水配方
产品说明
一.特点:环保,无味道,无毒,不含无机盐。
PH值为9(弱碱性)
除蜡水是一种水基的以表面活性剂为主,辅以对金属有缓蚀效果的组分以及溶剂等的多功能清洁剂,具有对蜡质污垢的抓爬乳化能力以及对油污的清洗力。
具有除蜡彻底,除油干净,对工件无腐蚀,清洗后不变色、不氧化生锈,比使用三氯乙烯更经济环保而且无毒。
二.适用对象:通用型,适用于不锈钢等各类金属工件的清洗,包括锌铝铜等。
三.使用方法:3﹪-5﹪使用,一般需要求水温80℃以上浸泡或超声波清洗(最佳水温为100℃),清洁时间为3-10分钟。
锌铝铜等活跃金属要求水温在60℃-80℃之间,清洗时间为1-5分钟。
配制溶液时,将水加入干净槽中,加热。
边搅拌边缓缓加入所需比例的除蜡水,要充分搅拌均匀,升至所需温度即可使用。
为得到最佳清洗效果,根据清洗对象和脏污程度,将原液与水配制成浓度为5%~10%的清洗液。
加温后结合超声波设备清洗后,用纯水漂洗干净后再烘干。
采用热浸泡和手工擦拭的方式清洗时,应不断晃动工件,直到洗干净为止。
配方参考。
除蜡水配方技术

除蜡水配方技术一、背景除蜡水广泛应用于电镀、钟表、工艺品、饰品等五金行业工件的抛光后之除蜡工艺。
禾川化工运用尖端配方剖析技术;专业从事除蜡水成分分析、配方分析,配方还原,配方检测、配方研制,为除蜡水相关企业提供整套技术解决方案一站式服务。
除蜡水的研究主要是选择一些表面活性剂、助剂、缓蚀剂、助溶剂等复合、调配,从而使产品在常温、加温,超声波、浸洗等工艺中都能迅速、彻底去除各种蜡垢,对不锈钢、碳钢、锌合金、铝合金、镁合金、铜合金等各种基材不产生腐蚀、氧化等负作用,有较长的使用寿命和环保性能。
此外,注意对产品的粘度、气味、颜色、透明度等外观性能进行合理的调配,满足客户心理需求,提升产品附加值。
除蜡作为五金电镀件前处理的第一道工序,其速度的快慢、除蜡的彻底性对于电镀线生产具有重要意义。
因此,选择良好的除蜡剂可以提高除蜡性能,从而带来良好的经济效益。
抛光蜡主要分为白蜡、红蜡和绿蜡。
不同蜡种由于其金属磨料不同而应用于不同基材的抛光中。
白蜡膏的主要磨料是氧化钙细微粉末,适用于镍、铝、铜及其合金等软质金属的抛光;红蜡膏的主要磨料是具有中等硬度的氧化铁和长石粉细微粉末,适用于钢制品的抛光;而绿蜡膏的主要磨料为氧化铬绿色细微粉末,适用于铬、不锈钢等硬质金属等的抛光。
这些不同种类的磨料与石蜡、地蜡、硬脂酸、脂肪、油酸及粘合剂配制而成抛光膏。
因此,抛光时应根据被抛光材料的性质及抛光面的质量要求选择不同的抛光膏。
工件经过抛光蜡抛光后,蜡垢就以机械吸附、分子间吸附和静电力吸附等粘附方式残留在工件上。
针对抛光蜡的成分配制具有良好润湿、渗透、乳化、分散等性能的高效除蜡剂,配以机械搅拌和超声波除蜡,将加快除蜡速度,达到快速、彻底的除蜡效果。
二、除蜡水2.1概念除蜡水是一种水基的以表面活性剂为主,辅以对金属有缓蚀效果的组分以及溶剂等的多功能清洗剂,具有对蜡质污垢的乳化能力以及对油污的清洗力。
具有除蜡彻底,除油干净,对工件无腐蚀,清洗后不变色、不氧化生锈的功能。
教你如何制作除蜡水的方法除蜡水原料及特性

教你如何制作除蜡水的方法除蜡水原料及特性
一、准备材料:
乙二胺油酸酯EDO-86,C13异丙醇酰胺,胺基糖酯AG1202,干净水,秤,容器,搅拌用的东西。
二、制作方法:
取三种除蜡水原料适量倒入容器,如:
乙二胺油酸酯EDO-86 15%
C13异丙醇酰胺12%
胺基糖酯AG1202 2%
水余量
把EDO-86与C13(碳13)搅拌均匀后,加入AG1202,最后加适量水,搅拌均匀静止20分钟即可。
三、使用方法:
清洗方式:超声波清洗(50-140KNz),浸泡清洗(摆动);
使用量:5% ;
槽液温度:85-100℃;
清洗时间:2-6min ;
抛光工件存放时间:48小时以内;
四、此除蜡水特性:
金亮黄色(金亮剔透),粘稠度高低灵活可控,根据需要改变商品粘稠度,可清洗任何材质工件、各类有色金属、黑色金属、塑胶制品、玻璃制品等打磨抛光工件蜡垢、油垢方面突出,不腐蚀、耐用持久、清洗后的工件表面更具光泽、自净力强槽液更清澈,泡沫低,绿色环保!。
钢铁件超声波除蜡水的研制

钢铁件超声波除蜡水的研制
黄晓蔚
【期刊名称】《广东化工》
【年(卷),期】2009(36)10
【摘要】文章介绍了钢铁件超声波除蜡水的研制,通过合理选用非离子、阴离子表面活性剂和助剂,并经科学调配制得钢铁件超声波除蜡水.结果表明,该除蜡剂具有环保无毒害,表面张力低,润湿、渗透性能强,对钢铁等金属工件有良好的除蜡效果.同时,该除蜡剂具有低成本优势,全面推广可带来良好的社会效益和经济效益.
【总页数】2页(P16-17)
【作者】黄晓蔚
【作者单位】广东省化学工业公共实验室,广东省石油化工研究院,广东,广
州,510665
【正文语种】中文
【中图分类】TB5
【相关文献】
1.响应面优化超声波辅助水酶法提取蜡梅籽蛋白 [J], 逯与运;麻成金;黄群;石莹;夏姣;张颖
2.钢铁件除蜡或除油后表面挂灰去除剂的研究 [J], 蒋国新;陈泽宗;姜贻成
3.不锈钢抛光用低温高效超声波除蜡清洗剂的研制 [J], 黄高山;汪蓉蓉
4.钢铁件环保高效水基除蜡剂的研制 [J], 杨婷姣; 廖磊华; 袁冬
5.不锈钢绿色高效超声波除蜡中性水基清洗剂的研制 [J], 桂绍庸;蔡卫权;古蒙蒙;曹宏
因版权原因,仅展示原文概要,查看原文内容请购买。
常温除蜡水成分析,除蜡水配方原理及生产工艺
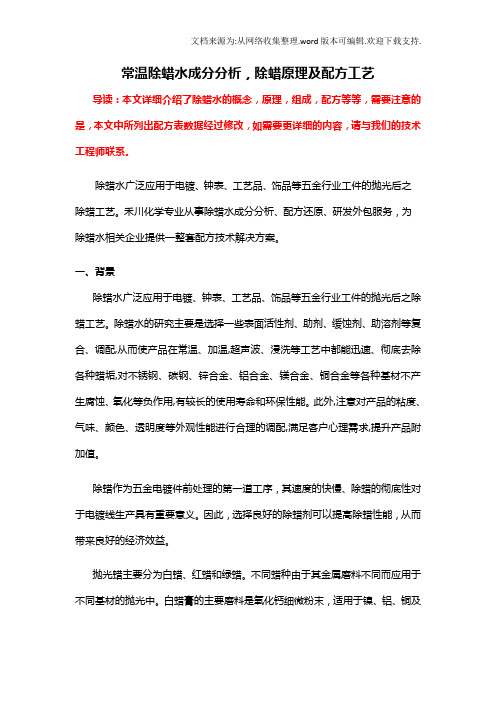
常温除蜡水成分分析,除蜡原理及配方工艺导读:本文详细介绍了除蜡水的概念,原理,组成,配方等等,需要注意的是,本文中所列出配方表数据经过修改,如需要更详细的内容,请与我们的技术工程师联系。
除蜡水广泛应用于电镀、钟表、工艺品、饰品等五金行业工件的抛光后之除蜡工艺。
禾川化学专业从事除蜡水成分分析、配方还原、研发外包服务,为除蜡水相关企业提供一整套配方技术解决方案。
一、背景除蜡水广泛应用于电镀、钟表、工艺品、饰品等五金行业工件的抛光后之除蜡工艺。
除蜡水的研究主要是选择一些表面活性剂、助剂、缓蚀剂、助溶剂等复合、调配,从而使产品在常温、加温,超声波、浸洗等工艺中都能迅速、彻底去除各种蜡垢,对不锈钢、碳钢、锌合金、铝合金、镁合金、铜合金等各种基材不产生腐蚀、氧化等负作用,有较长的使用寿命和环保性能。
此外,注意对产品的粘度、气味、颜色、透明度等外观性能进行合理的调配,满足客户心理需求,提升产品附加值。
除蜡作为五金电镀件前处理的第一道工序,其速度的快慢、除蜡的彻底性对于电镀线生产具有重要意义。
因此,选择良好的除蜡剂可以提高除蜡性能,从而带来良好的经济效益。
抛光蜡主要分为白蜡、红蜡和绿蜡。
不同蜡种由于其金属磨料不同而应用于不同基材的抛光中。
白蜡膏的主要磨料是氧化钙细微粉末,适用于镍、铝、铜及其合金等软质金属的抛光;红蜡膏的主要磨料是具有中等硬度的氧化铁和长石粉细微粉末,适用于钢制品的抛光;而绿蜡膏的主要磨料为氧化铬绿色细微粉末,适用于铬、不锈钢等硬质金属等的抛光。
这些不同种类的磨料与石蜡、地蜡、硬脂酸、脂肪、油酸及粘合剂配制而成抛光膏。
因此,抛光时应根据被抛光材料的性质及抛光面的质量要求选择不同的抛光膏。
工件经过抛光蜡抛光后,蜡垢就以机械吸附、分子间吸附和静电力吸附等粘附方式残留在工件上。
针对抛光蜡的成分配制具有良好润湿、渗透、乳化、分散等性能的高效除蜡剂,配以机械搅拌和超声波除蜡,将加快除蜡速度,达到快速、彻底的除蜡效果。
除蜡水

漂洗性能试验:将盛有400ml试液的烧杯,放入60度左右的恒温水浴里,将准备好的试片挂在S形挂钩上,全浸在试液中5分钟,取出后,立即用滤纸吸去试片下端及孔眼的液体,垂直悬挂于试片架上,放入40度左右烘箱中干燥30分钟,取出试片在400 ml60度左右的蒸馏水中来回摆动10次(往返为1次),摆洗时间不超过10秒。
取出后,用热风吹干,检查试片外观,同时用两片试片作平行试验。
结果评定查看试片表面有无净洗剂残留物PH值测定用PH值计测定3%的式样溶液。
一般用PH纸测定。
按标准要求,对钢铸铁类用洗涤剂PH值要求大于7;而对铜及铜合金,铝及铝合金用洗涤剂则要求PH值在7-11.5之间。
金属清洗剂配方的筛选1;表面活性剂各类表面活性剂的清洗效果与被洗物的种类,污垢的性质以及温度等有关,例如把炭黑和矿物油以质量比1:2组成的污垢涂在钢表面上,在相同条件下,各类表面活性剂的清洗效果顺序如下。
非离子表面活性剂>阳离子表面活性剂=烷基硫酸盐>肥皂选择表面活性剂应注意以下问题在金属清洗剂中应用得较多的是非离子表面活性剂和阴离子表面活性剂,若把两者复合使用则能产生较好的协同效应,其乳化增溶分散净洗作用将得到增强。
应注意HLB值,综合考虑金属清洗剂卷离和分散污垢的能力,所用的表面活性剂HLB 值一般在8-16.多数分子离子表面活性剂具有浊点,作为金属清洗剂用的表面活性剂其浊点不宜太低,一般应高于清洗剂的使用温度。
否则在清洗过程中会出现浑浊,会降低其表面活性。
但浊点也不必太高,HLB值升高会使表面活性剂憎水基团过弱,也不利于油污的清洗。
在水基金属清洗剂中,表面活性剂的净洗力和防锈性往往是互相矛盾,互相抑制的。
清洗的主要作用是使油污脱离金属表面,并且防止再沉积于金属表面上;而防锈的机理主要是加强吸附作用,在金属表面形成密集的吸附膜,以隔绝一切腐蚀介质。
尽管如此,仍有脂肪酸烷醇酰胺,聚氧乙烯脂肪胺等同时兼有去污和防锈两种作用,它们可用于防锈型金属清洗剂。
除腊水精物质安全资料表
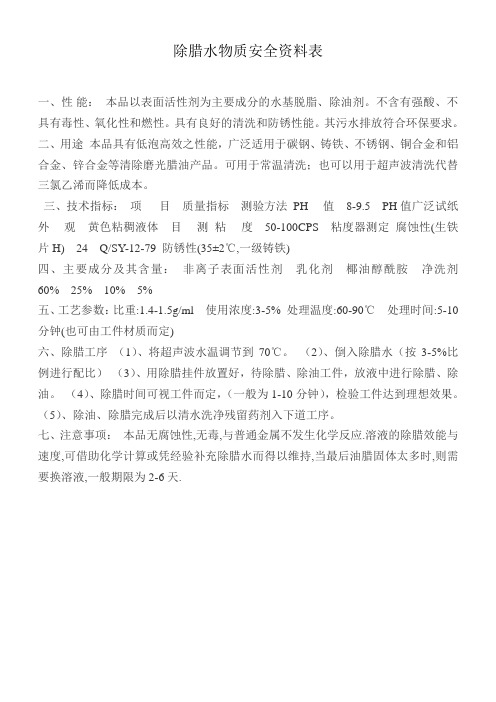
除腊水物质安全资料表
一、性能:本品以表面活性剂为主要成分的水基脱脂、除油剂。
不含有强酸、不具有毒性、氧化性和燃性。
具有良好的清洗和防锈性能。
其污水排放符合环保要求。
二、用途本品具有低泡高效之性能,广泛适用于碳钢、铸铁、不锈钢、铜合金和铝合金、锌合金等清除磨光腊油产品。
可用于常温清洗;也可以用于超声波清洗代替三氯乙浠而降低成本。
三、技术指标:项目质量指标测验方法PH 值 8-9.5 PH值广泛试纸外观黄色粘稠液体目测粘度 50-100CPS 粘度器测定腐蚀性(生铁片H) 24 Q/SY-12-79 防锈性(35±2℃,一级铸铁)
四、主要成分及其含量:非离子表面活性剂乳化剂椰油醇酰胺净洗剂60% 25% 10% 5%
五、工艺参数:比重:1.4-1.5g/ml 使用浓度:3-5% 处理温度:60-90℃处理时间:5-10分钟(也可由工件材质而定)
六、除腊工序(1)、将超声波水温调节到70℃。
(2)、倒入除腊水(按3-5%比例进行配比)(3)、用除腊挂件放置好,待除腊、除油工件,放液中进行除腊、除油。
(4)、除腊时间可视工件而定,(一般为1-10分钟),检验工件达到理想效果。
(5)、除油、除腊完成后以清水洗净残留药剂入下道工序。
七、注意事项:本品无腐蚀性,无毒,与普通金属不发生化学反应.溶液的除腊效能与速度,可借助化学计算或凭经验补充除腊水而得以维持,当最后油腊固体太多时,则需要换溶液,一般期限为2-6天.。
除蜡水配制原理及指标和漂洗性能试验

漂洗性能试验:将盛有400ml试液的烧杯,放入60度左右的恒温水浴里,将准备好的试片挂在S形挂钩上,全浸在试液中5分钟,取出后,立即用滤纸吸去试片下端及孔眼的液体,垂直悬挂于试片架上,放入40度左右烘箱中干燥30分钟,取出试片在400 ml60度左右的蒸馏水中来回摆动10次(往返为1次),摆洗时间不超过10秒。
取出后,用热风吹干,检查试片外观,同时用两片试片作平行试验。
结果评定查看试片表面有无净洗剂残留物PH值测定用PH值计测定3%的式样溶液。
一般用PH纸测定。
按标准要求,对钢铸铁类用洗涤剂PH值要求大于7;而对铜及铜合金,铝及铝合金用洗涤剂则要求PH值在7-11.5之间。
金属清洗剂配方的筛选1;表面活性剂各类表面活性剂的清洗效果与被洗物的种类,污垢的性质以及温度等有关,例如把炭黑和矿物油以质量比1:2组成的污垢涂在钢表面上,在相同条件下,各类表面活性剂的清洗效果顺序如下。
非离子表面活性剂>阳离子表面活性剂=烷基硫酸盐>肥皂选择表面活性剂应注意以下问题在金属清洗剂中应用得较多的是非离子表面活性剂和阴离子表面活性剂,若把两者复合使用则能产生较好的协同效应,其乳化增溶分散净洗作用将得到增强。
应注意HLB值,综合考虑金属清洗剂卷离和分散污垢的能力,所用的表面活性剂HLB 值一般在8-16.多数分子离子表面活性剂具有浊点,作为金属清洗剂用的表面活性剂其浊点不宜太低,一般应高于清洗剂的使用温度。
否则在清洗过程中会出现浑浊,会降低其表面活性。
但浊点也不必太高,HLB值升高会使表面活性剂憎水基团过弱,也不利于油污的清洗。
在水基金属清洗剂中,表面活性剂的净洗力和防锈性往往是互相矛盾,互相抑制的。
清洗的主要作用是使油污脱离金属表面,并且防止再沉积于金属表面上;而防锈的机理主要是加强吸附作用,在金属表面形成密集的吸附膜,以隔绝一切腐蚀介质。
尽管如此,仍有脂肪酸烷醇酰胺,聚氧乙烯脂肪胺等同时兼有去污和防锈两种作用,它们可用于防锈型金属清洗剂。
除蜡水配制

除蜡水配制原理及指标时间:2011-01-26 03:39:14 科威达环保器材信息网点击:165 次导读:除蜡水作为目前常用的清洗产品而广泛应用于电镀,钟表,饰品及工艺品等五金行业工件抛光后的除蜡工艺。
其配方技术的研究与开发,主要是通过表面活性剂,助剂,缓蚀剂,助溶剂等的选择,复合,调配,使产品在常温,中温,超声波,浸洗等处理工艺中都能够迅速彻底的去除各种蜡垢,油污。
对不锈钢,碳钢,锌,镁,铝,铜等各种除蜡水配制原理及指标主题关键词:缓蚀剂除蜡水作为目前常用的清洗产品而广泛应用于电镀,钟表,饰品及工艺品等五金行业工件抛光后的除蜡工艺。
其配方技术的研究与开发,主要是通过表面活性剂,助剂,缓蚀剂,助溶剂等的选择,复合,调配,使产品在常温,中温,超声波,浸洗等处理工艺中都能够迅速彻底的去除各种蜡垢,油污。
对不锈钢,碳钢,锌,镁,铝,铜等各种基材不发生腐蚀,氧化等负作用。
有很好的环保性能以及较长的使用寿命。
另外,产品的粘度,颜色,气味,透明度等外观性能也要进行合理的调配,满足客户的心理需求,提升产品的出啦原理除蜡原理金属工件经过抛光蜡的抛光后,其表面的污垢成分主要为石蜡,脂肪酸,松香皂,金属氧化物,磨料,矿物油,动植物油,天然蜡以及一些打磨布碎片,打磨出来的金属基体的粉末及其氧化物。
抛光后的工件上,蜡垢就会以机械吸附,分子间吸附和静电吸附等方式粘附在工件上。
而这些蜡垢的颗粒直径小于0.1μm时就很难除去。
除蜡水制备的关键就在于对各种表面活性剂,助剂,缓蚀剂,助溶剂等成分进行合理的复配。
通过降低表面张力,改善润湿渗透性能和乳化,溶解,分散增溶性能,从而增强产品的渗透力和溶解力,以达到快速去除蜡垢的目的。
除蜡水制备的关键在于表面活性剂的选择和复配。
金属清洗产品的制备中,阴离子表面活性剂和非离子表面活性剂的复配早就广泛的使用。
加入离子型表面活性剂的非离子表面活性剂在使用中有了较宽的温度使用范围,同时也提高了其渗透性能和乳化性能,形成混合胶团。
- 1、下载文档前请自行甄别文档内容的完整性,平台不提供额外的编辑、内容补充、找答案等附加服务。
- 2、"仅部分预览"的文档,不可在线预览部分如存在完整性等问题,可反馈申请退款(可完整预览的文档不适用该条件!)。
- 3、如文档侵犯您的权益,请联系客服反馈,我们会尽快为您处理(人工客服工作时间:9:00-18:30)。
除蜡水的配方新升级除蜡水分析T-101#(4.0版)除蜡水T-101#(4.0版)介绍:
1、T-101#除蜡水4.0版在快速清除各类有色金属、黑色金属、塑胶制品、玻璃制品等打磨抛光工件蜡垢、油垢方便更佳突出,除蜡时间进一步压缩,适用材料范围更广;
2、防腐蚀、防锈、持久使用、商品透光度提高到新的高度;
3、清洗后的工件制品表面光洁度(光亮度)大幅提升,产品质量认可度(合格率)更高;
4、槽液自净化功能全面强化,浮油、浮蜡在一定时间内基本消溶,更换槽液频率明显降低;
5、环保要求更为严格,使用“碳13异丙醇酰胺”而非含壬基酚类的异丙醇酰胺,增加精油乳化剂(绿色可持续)加持,提高商品自净化能力,减少废水处理排放负担;
6、商品外观华丽变身,从浅淡黄色(浑浊朦胧)转变为金亮黄色(金亮剔透),粘稠度高低灵活可控,根据需要改变商品粘稠度,大大提高产品可视竞争力,增加商品市场价格附加值!
7、中低泡沫,更易消泡,提升车间清洁度;
商品特性:
可快速清洗任何材质工件、不腐蚀、耐用持久、清洗后的工件表面更具光泽、自净力强槽液更清澈,泡沫低,绿色环保!
使用方法:
清洗方式超声波清洗(50-140KNz)浸泡清洗(摆动)
使用量(标准版) 5% 5%
槽液温度 85-100℃ 100℃(沸腾)
清洗时间 2-6min 5-15min
抛光工件存放时间 48小时以内 24小时以内
槽液维护:
1、由于清洗工件的蜡垢、油垢轻重程度的不可控性,可根据槽液的洁净程度或清洗工件的多少决定是否添加料;不过根据我们专家建议当工作槽体积小于500L以内时,添加料次数最多不应超过三次就需换槽;
2、同槽清洗请遵循先清洗“活泼金属”后“惰性金属”(不活泼金属)
包装储存与运输:
规格:25公斤/桶
有效期:12个月
储存:按普通化学品处理,避免阳光直射或高温储存,轻拿轻放避免泄漏!
运输:按普通化学品运输,轻装轻卸防止破损泄漏对环境有害!。