1809-0;1809-2;中文规格书,Datasheet资料
19218;中文规格书,Datasheet资料

Jewel ® Workstation Continuous Mini Monitor DescriptionWorkstation Continuous Mini Monitor Figure 1. Desco 19218 Jewel ® Workstation Continuous Made in AmericaA broken wrist strap may expose products to ESD over an entire shift if it is checked only at shift changeESD MATPush and Clinch Snaps1-5/16"Figure 2. Installation of push and clinch snaps to worksurfaceNOTE: Install the monitor to the worksurface by aligning one snap at a time and applying a downward force directly above that snap.WorksurfaceMonitors worksurface connectionFigure 3. Installation of the monitor to the worksurface one snap at a timeThe following procedure will outline how to correctly wire Workstation Continuous Mini Monitor so as to properly monitor an ESD protected workstation.1. Confirm that the worksurface surface resistance is 5 x 10E8 Ohms or less and has a conductive layer.2. A convenient 120 VAC outlet should be located and tested for proper wiring and grounding. Werecommend the Desco 98130 AC Outlet Analyzer to verify proper wiring and ground.AC AdapterESD MATPark SnapFigure 4. Operating the Jewel® Workstation ContinuousHand Lotion. When leaving the area, a person can take the coil cord along or leave it attached to themonitor in park position.NOTE: Removing the banana plug from the monitor’s operator jack will disable the audio alarm.It is recommended that you use the Park Snap rather than continuously removing the Banana Plug from its jack. Doing so will increase the life span of the operator jack. If your process requires the constant insertion and removal of the banana plug, please contact your Desco Representative for alternate solutions.Specifications:Test range of monitored circuit:500K - 10M ohms†Worksurface Limit*:Set to 500 Megohms ± 20%Operating Voltage:24VAC, 50-60 HzWrist strap open circuit voltage:1.2 Volts peak to peak @ 1-2 MicroAmpsMat test open circuit voltage:5 - 7.5 VoltsResponse time to alarm:<50 mSOperating Temperature:32ºF - 100ºFHumidity Range:0-95% RH, non- c ondensingDimensions:2.77" L x 2.07" W x .71" H† This cannot be verified with standard DC test equipment. The continuous monitor is an impedance sensing device and the limits are determined by the magnitude and angle of the impedance.*Contact factory for special limits.NOTE: Worksurface must have a conductive layer such as Dual Layer Rubber or Dissipative 3-Layer Vinyl or Micastat® Dissipative Laminate with conductive buried layers. Desco continuous monitors are not recommended for use with homogeneous matting.Maintenance and CalibrationThe Jewel® Workstation Continuous Mini Monitor is solid state and designed to be maintenance free. It is calibrated to NIST traceable standards. There are no user adjustments necessary. Because of the wave distortion impedance sensing nature of the test circuit, special equipment is required for calibration. We recommend that calibration be performed annually using the Desco 98220 Continuous Monitor Calibration Unit. The Calibration Unit is a most important product which allows the customer to perform NIST traceable calibration on continuous monitors. The 98220 is designed to be used on the shop floor at the workstation, virtually eliminating downtime, verifying that the continuous monitor is operating within tolerances. The 98220 provides a simple and quick means to assure compliance verificaton Per ANSI/ESD S20.20 Table 3 per ESD TR53.Limited WarrantyDesco expressly warrants that for a period of one (1) year from the dateof purchase Desco Continuous Monitors will be free of defects in material(parts) and workmanship (labor). Within the warranty period, a creditfor purchase of replacement Desco Continuous Monitors, or, at Desco’soption, the Continuous Monitor will be repaired or replaced free of charge.If product credit is issued, the amount will be calculated by multiplying the unused portion of the expected one year life times the original unit purchase price. Call Customer Service at 909-627-8178 (Chino, CA) or 781-821-8370 (Canton, MA) for Return Material Authorization (RMA) and proper shipping instructions and address. Include a copy of your original packing slip,invoice, or other proof of date of purchase. Any unit under warranty should be shipped prepaid to the Desco factory. Warranty replacements will takeapproximately two weeks.If your unit is out of warranty, Desco will quote repair charges necessaryto bring your unit up to factory standards. Call Customer Service at 909-627-8178 (Chino, CA) or 781-821-8370 (Canton, MA) for a Return Material Authorization (RMA) and proper shipping instructions and address.Warranty ExclusionsTHE FOREGOING EXPRESS WARRANTY IS MADE IN LIEU OFALL OTHER PRODUCT WARRANTIES, EXPRESSED AND IMPLIED,INCLUDING MERCHANTABILITY AND FITNESS FOR A PARTICULARPURPOSE WHICH ARE SPECIFICALLY DISCLAIMED. The expresswarranty will not apply to defects or damage due to accidents, neglect,misuse, alterations, operator error, or failure to properly maintain, clean or repair products.Limit of LiabilityIn no event will Desco or any seller be responsible or liable for anyinjury, loss or damage, direct or consequent, arising out of the use of orthe inability to use the product. Before using, users shall determine thesuitability of the product for their intended use, and users assume all riskand liability whatsoever in connection therewith.分销商库存信息: DESCO19218。
S108T02;S108T02F;S208T02;中文规格书,Datasheet资料
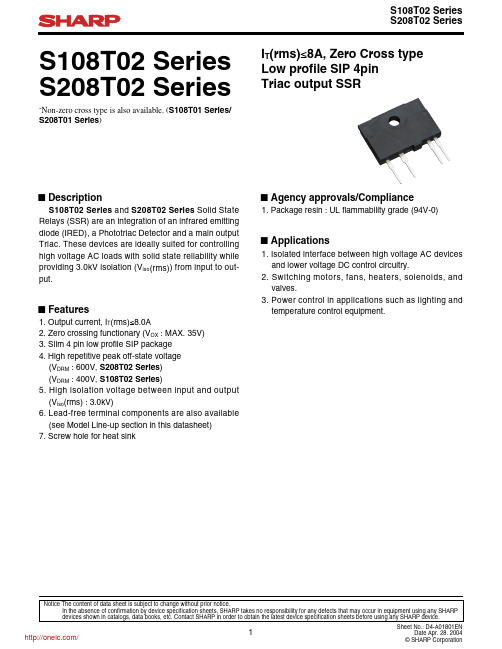
S108T02 Series S208T02 Series■ FeaturesI T (rms)≤8A, Zero Cross type Low profile SIP 4pin Triac output SSR1. Output current, I T (rms)≤8.0A2. Zero crossing functionary (V OX : MAX. 35V)3. Slim 4 pin low profile SIP package4. High repetitive peak off-state voltage (V DRM : 600V, S208T02 Series ) (V DRM : 400V, S108T02 Series )5. High isolation voltage between input and output (V iso (rms) : 3.0kV)6. Lead-free terminal components are also available (see Model Line-up section in this datasheet)7. Screw hole for heat sink■ DescriptionS108T02 Series and S208T02 Series Solid State Relays (SSR) are an integration of an infrared emitting diode (IRED), a Phototriac Detector and a main output Triac. These devices are ideally suited for controlling high voltage AC loads with solid state reliability while providing 3.0kV isolation (V iso (rms)) from input to out-put.Notice The content of data sheet is subject to change without prior notice.In the absence of confirmation by device specification sheets, SHARP takes no responsibility for any defects that may occur in equipment using any SHARP ■ Agency approvals/Compliance1. Isolated interface between high voltage AC devices and lower voltage DC control circuitry.2. Switching motors, fans, heaters, solenoids, and valves.3. Power control in applications such as lighting and temperature control equipment.■ Applications1. Package resin : UL flammability grade (94V-0)∗Non-zero cross type is also available. (S108T01 Series/S208T01 Series)∗ : Do not allow external connection.( ) : Typical dimensions■ Internal Connection Diagram+)−)■ Outline Dimensions(Unit : mm)Date code (2 digit)Rank markThere is no rank mark indicator and currently there are no rank offered for this device.A.D.199019911992199319941995199619971998199920002001MarkABCDEFHJKLMN Mark P R S T U V W X A B C Mark 123456789O N DMonth January February March April May June July August September October November December A.D 20022003200420052006200720082009201020112012······2nd digitMonth of production 1st digitYear of productionCountry of originJapanrepeats in a 20 year cycle■ Electro-optical CharacteristicsParameter Symbol Unit InputOutput (T a =25˚C)Forward voltageReverse currentRepetitive peak OFF-state currentON-state voltageHolding currentCritical rate of rise of OFF-state voltageCritical rate of rise of OFF-state voltage at commutaion Minimum trigger currentZero cross voltageIsolation resistanceTurn-on time Turn-off timeThermal resistanceV F I R I DRM V T (rms)I H dV/dt (dV/dt)c I FT V OX R ISO t ont off R th (j-c)R th (j-a)I F =20mA V R =3V V D =V DRM I T (rms)=2A, Resistance load, I F =20mA −V D =2/3•V DRM T j =125˚C , V D =2/3•V DRM , dI T /dt =−4.0A/msV D =6V, R L =30ΩI F =8mA DC500V, 40 to 60%RH V D (rms)=100V, AC50Hz, I F =20mAI T (rms)=2A, Resistance load V D (rms)=200V, AC50Hz, I F =20mA I T (rms)=2A, Resistance load V D (rms)=100V, AC50Hz, I F =20mAI T (rms)=2A, Resistance loadV D (rms)=200V, AC50Hz, I F =20mAI T (rms)=2A, Resistance loadBetween junction and case Between junction and ambience Conditions MIN.TYP.MAX.Transfer charac-teristics S108T02S208T02S108T02S208T02−−−−−305−−1010−−−−−−1.2−−−−−−−−−−−−−4.5401.41001001.550−−835−10101010−−V µA µA V mA V/µs V/µs mA V Ωmsms˚C /W ■ Absolute Maximum RatingsParameter Symbol Rating UnitInputOutput(T a =25˚C)Forward current Reverse voltage RMS ON-state current Peak one cycle surge current Repetitive peak OFF-state voltage Non-Repetitive peak OFF-state voltage Critical rate of rise of ON-state current Operating frequency Isolation voltage Operating temperature Storage temperature Soldering temperature *2*1I FV R I T (rms)I surge V DRMV DSMdI T /dt fV iso (rms)T opr T stg T solmA V A A VVA/µs Hz kV ˚C ˚C ˚C*3*3*45068804006004006005045 to 653.0−25 to +100−30 to +125260*1 40 to 60%RH, AC for 1minute, f =60Hz *2 For 10s*3 Refer to Fig.1, Fig.2*4 f =60Hz sine wave, T j =25˚C startS108T02S208T02S108T02S208T02Soldering areaShipping PackageModel No.Sleeve 25pcs/sleeve S108T02F S208T02FI FT [mA](V D =6V, R L =30Ω)MAX.8400MAX.8600V DRM [V]Please contact a local SHARP sales representative to see the actual status of the production.■ Model Line-up (1) (Lead-free terminal components)■ Model Line-up (2) (Lead solder plating components)Shipping PackageModel No.Sleeve 25pcs/sleeve S108T02S208T02I FT [mA](V D =6V, R L =30Ω)MAX.8400MAX.8600V DRM [V]F o r w a r d c u r r e n t I F (m A )Ambient temperature T a (˚C)060−2502550751001255040302010Fig.1 Forward Current vs. AmbientTemperatureFig.2 RMS ON-state Current vs.Ambient TemperatureF o r w a r d c u r r e n t I F (m A )Forward voltage V F (mA)1010.1100Fig.4 Forward Current vs. Forward VoltageFig.3 RMS ON-state Current vs.Case TemperatureR M S O N -s t a t e c u r r e n t I T (r m s )(A )Case temperature T C (°C)010−25255075100125987654321R M S O N -s t a t e c u r r e n t I T (r m s )(A )Ambient temperature T a (˚C)0987654321−25100755025125(1)(2)(3)(4)(5)(1)With infinite heat sink(2)With heat sink (200×200×2mm Al plate)(3)With heat sink (100×100×2mm Al plate)(4)With heat sink (50×50×2mm Al plate)(5)Without heat sink(N ote)In natural cooling condition, please locate Al platevertically, spread the thermal conductive silicone grease on the touch surface of the device and tighten up the device in the center of Al plate at the torque of 0.4N•m.Fig.8-b Repetitive Peak OFF-state Current vs.Ambient Temperature (S208T02)Fig.8-a Repetitive Peak OFF-state Current vs.Ambient Temperature (S108T02)R e p e t i t i v e p e a k O F F -s t a t e c u r r e n t I D R M (A )Ambient temperature T a (˚C)10−910−310−410−510−610−710−8R e p e t i t i v e p e a k O F F -s t a t e c u r r e n t I D R M (A )Ambient temperature T a (˚C)10−910−310−410−510−610−710−8Remarks : Please be aware that all data in the graph are just for reference.Fig.5 Surge Current vs. Power-on CycleFig.6 Minimum Trigger Current vs.Ambient TemperatureFig.7 Maximum ON-state Power Dissipationvs. RMS ON-state CurrentM i n i m u m t r i g g e r c u r r e n t I F T (m A )Ambient temperature T a (°C)0108642S u r g e c u r r e n t I s u r g e (A )Power-on cycle (Times)10080604020120M a x i m u m O N -s t a t e p o w e r d i s s i p a t i o n (W )RMS ON-state current I T (rms)(A)010864297531■ Design ConsiderationsIn order for the SSR to turn off, the triggering current (l F ) must be 0.1mA or less.When the input current (I F ) is below 0.1mA, the output Triac will be in the open circuit mode. However, if the voltage across the Triac, V D , increases faster than rated dV/dt, the Triac may turn on. To avoid this situation, please incorporate a snubber circuit. Due to the many different types of load that can be driven, we can merely recommend some circuit vales to start with : Cs=0.022µF and Rs=47Ω. The operation of the SSR and snubber circuit should be tested and if unintentional switching occurs, please adjust the snubber circuit component values accordingly.When making the transition from On to Off state, a snubber circuit should be used ensure that sudden drops in current are not accompanied by large instantaneous changes in voltage across the Triac.This fast change in voltage is brought about by the phase difference between current and voltage. Primarily, this is experienced in driving loads which are inductive such as motors and solenoids. Following the procedure outlined above should provide sufficient results. For over voltage protection, a Varistor may be used.Any snubber or Varistor used for the above mentioned scenarios should be located as close to the main out-put triac as possible.Particular attention needs to be paid when utilizing SSRs that incorporate zero crossing circuitry.If the phase difference between the voltage and the current at the output pins is large enough, zero crossing type SSRs cannot be used. The result, if zero crossing SSRs are used under this condition, is that the SSR may not turn on and off irregardless of the input current. In this case, only a non zero cross type SSR should be used in combination with the above mentioned snubber circuit selection process.The load current should be within the bounds of derating curve. (Refer to Fig.2) Also, please use the optional heat sink when necessary.In case the optional heat sink is used and the isolation voltage between the device and the optional heat sink is needed, please locate the insulation sheet between the device and the heat sink.When the optional heat sink is equipped, please set up the M3 screw-fastening torque at 0.3 to 0.5N•m.In order to dissipate the heat generated from the inside of device effectively, please follow the below sugges-tions.● Design guide● Recommended Operating ConditionsParameterS108T02S208T02Symbol Unit InputOutputInput signal current at ON state Input signal current at OFF state Load supply voltage Load supply currentFrequencyOperating temperatureI F (ON)I F (OFF)V OUT (rms)I OUT (rms)f T oprmA mA V mA Hz ˚C−−−Locate snubber circuit between output terminals(Cs =0.022µF, Rs =47Ω)−−Conditions(∗) See Fig.2 about derating curve (I T (rms) vs. ambient temperature).16080800.147−20240.1120240I T (rms)×80%(∗)6380MIN.MAX.✩ For additional design assistance, please review our corresponding Optoelectronic Application Notes.● Standard CircuitV +V S108T02● DegradationIn general, the emission of the IRED used in SSR will degrade over time.In the case where long term operation and / or constant extreme temperature fluctuations will be applied to the devices, please allow for a worst case scenario of 50% degradation over 5years.Therefore in order to maintain proper operation, a design implementing these SSRs should provide at least twice the minimum required triggering current from initial operation.(a) Make sure there are no warps or bumps on the heat sink, insulation sheet and device surface.(b) Make sure there are no metal dusts or burrs attached onto the heat sink, insulation sheet and device sur-face.(c) Make sure silicone grease is evenly spread out on the heat sink, insulation sheet and device surface.Silicone grease to be used is as follows;1) There is no aged deterioration within the operating temperature ranges.2) Base oil of grease is hardly separated and is hardly permeated in the device.3) Even if base oil is separated and permeated in the device, it should not degrade the function of a device. Recommended grease : G-746 (Shin-Etsu Chemical Co., Ltd.): G-747 (Shin-Etsu Chemical Co., Ltd.): SC102 (Dow Corning Toray Silicone Co., Ltd.) In case the optional heat sink is screwed up, please solder after screwed.In case of the lead frame bending, please keep the following minimum distance and avoid any mechanical stress between the base of terminals and the molding resin.Some of AC electromagnetic counters or solenoids have built-in rectifier such as the diode.In this case, please use the device carefully since the load current waveform becomes similar with rectangu-lar waveform and this results may not make a device turn off.■ Manufacturing Guidelines● Soldering MethodFlow Soldering (No solder bathing)Flow soldering should be completed below 260˚C and within 10s.Preheating is within the bounds of 100 to 150˚C and 30 to 80s.Please solder within one time.Other noticesPlease test the soldering method in actual condition and make sure the soldering works fine, since the impact on the junction between the device and PCB varies depending on the tooling and soldering conditions.分销商库存信息:SHARP-MICROELECTRONICSS108T02S108T02F S208T02。
ISO18092标准(中文)
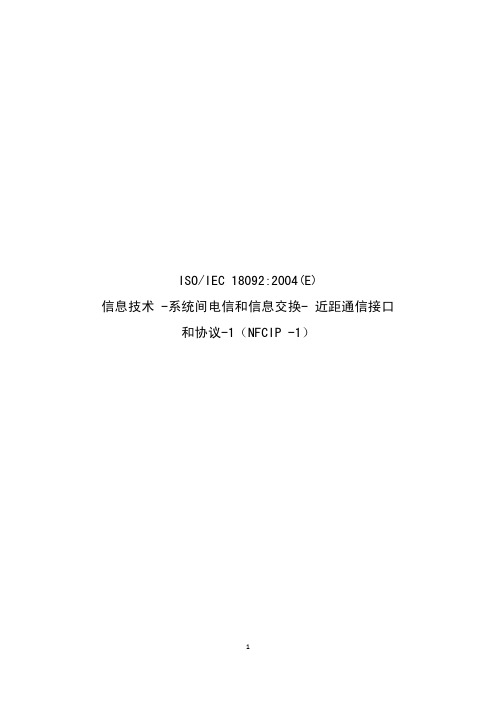
ISO/IEC 18092:2004(E)信息技术 -系统间电信和信息交换- 近距通信接口和协议-1(NFCIP -1)目录前言 (4)1 范围 (4)2 一致性 (4)3 规范性引用文件 (5)4术语和定义 (5)4.1主动通信模式 (5)4.2 ASK调制 (5)4.3 二进制编码十进制(BCD) (5)4.4 碰撞 (5)4.5 帧 (5)4.6 HThreshold (6)4.7发生器 (6)4.8 负载调制 (6)4.9 lsb 优先 (6)4.10 LSB 优先 (6)4.11 曼彻斯特编码 (6)4.12 调制指数 (6)4.13 msb优先 (6)4.14 MSB优先 (7)4.15 NFCIP-1设备 (7)4.16 NFC标识符(NFCIDn) (7)4.17 被动通信模式 (7)4.18 射频冲突避免(RFCA) (7)4.19 SEL_PAR (7)4.20 遥感 (7)4.21 单设备检测阶段(SDD) (7)4.22 副载波 (7)4.23 目标 (8)4.24 时间周期 (8)4.25 时隙 (8)4.26 协定 (8)5公约和符号 (8)5.1数字表示 (8)5.2名称 (8)6 缩略语 (8)7 概要 (10)8 RF场 (11)8.1被动通信模式 (11)8.2主动通信模式 (11)8.3外部RF场的阈值 (11)9射频信号接口 (11)9.1位持续时间 (11)9.2主动通信模式 (12)9.2.1 106 kbps (12)9.2.2 212 kbps和424 kbps (13)9.3被动通信模式 (15)9.3.1 106 kbps的发起到目标 (15)9.3.2 106 kbps目标至发起设备 (15)9.3.3 212 kbps和424 kbps 发起设备到目标 (16)9.3.4 212 kbps和424 kbps 目标至发起设备 (17)10通用协议流程 (17)11初始化 (18)11.1射频冲突避免 (18)11.1.1初始化射频冲突避免 (18)11.1.2反应射频防撞 (20)11.2被动通信模式 (20)11.2.1 106 kbps的初始化与单设备检测 (20)11.2.1.5.1短帧 (21)11.2.2 212 kbps和424 kbps的初始化和SDD (32)11.3主动通信模式 (35)11.3.1 106,212和424 kbps的初始化 (35)11.3.2主动通信模式射频冲突避免 (35)12传输协议 (36)12.1传输数据 (36)12.2被动通信模式的激活流程 (36)12.3主动通信模式激活流程 (37)12.4命令 (38)12.5 协议激活 (39)12.5.1属性请求和响应命令 (39)12.5.2唤醒请求和响应命令 (44)12.5.3参数选择请求和响应命令 (45)12.6数据交换协议 (48)12.6.1数据交换协议请求和响应 (48)12.6.2响应超时延期 (51)12.6.3注意事项–现存目标 (51)12.6.4协议操作 (51)12.6.5多重激活 (51)12.6.6更多信息(链) (52)12.7协议的去激活 (52)12.7.1取消选择请求和响应命令 (53)12.7.2释放请求和响应命令 (54)附件一(规范)CRC计算 (55)A.1 106 kbps的主动和被动通信模式CRC校验 (55)A.2 106 kbps CRC计算示例 (55)A.3 212 kbps和424 kbps下的主动和被动通信模式CRC。
1808382资料

Extract from the online catalog
SMSTB 2,5/ 6-ST BK AU://eshop.phoenixcontact.de/phoenix/treeViewClick.do?UID=1808382
AWG/kcmil UL Nominal voltage UN Nominal current IN AWG/kcmil Certification
30-12
300 V 10 A 30-12 CSA, CUL, UL
PHOENIX CONTACT GmbH & Co. KG http://www.phoenixcontact.de
CSA Nominal voltage UN Nominal current IN AWG/kcmil CUL Nominal voltage UN Nominal current IN 300 V 10 A 300 V 10 A 28-12
PHOENIX CONTACT GmbH & Co. KG http://www.phoenixcontact.de
Product notes Commercial data EAN Pack Customs tariff Weight/Piece 4017918214760 50 Pcs. 85366990 0.0116 KG http:// Please note that the data given here has been taken from the online catalog. For comprehensive information and data, please refer to the user documentation. The General Terms and Conditions of Use apply to Internet downloads. Certificates / Approvals WEEE/RoHS-compliant since: 01/01/2003
中兴1809路由器配置模板
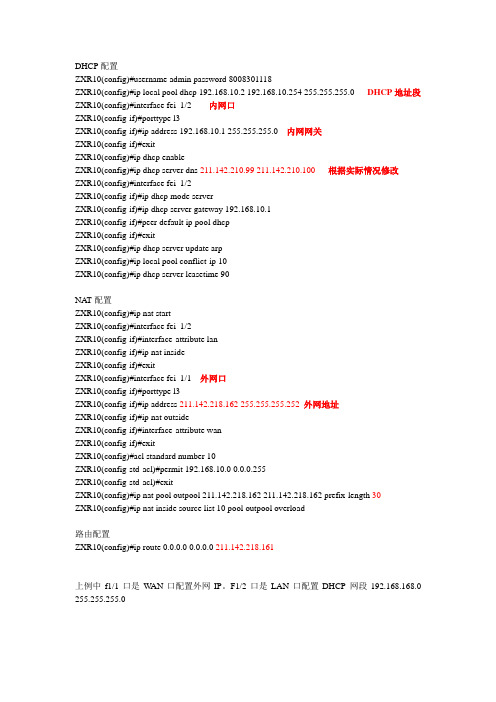
DHCP配置ZXR10(config)#username admin password 8008301118ZXR10(config)#ip local pool dhcp 192.168.10.2 192.168.10.254 255.255.255.0 DHCP地址段ZXR10(config)#interface fei_1/2 内网口ZXR10(config-if)#porttype l3ZXR10(config-if)#ip address 192.168.10.1 255.255.255.0 内网网关ZXR10(config-if)#exitZXR10(config)#ip dhcp enableZXR10(config)#ip dhcp server dns 211.142.210.99 211.142.210.100根据实际情况修改ZXR10(config)#interface fei_1/2ZXR10(config-if)#ip dhcp mode serverZXR10(config-if)#ip dhcp server gateway 192.168.10.1ZXR10(config-if)#peer default ip pool dhcpZXR10(config-if)#exitZXR10(config)#ip dhcp server update arpZXR10(config)#ip local pool conflict-ip 10ZXR10(config)#ip dhcp server leasetime 90NA T配置ZXR10(config)#ip nat startZXR10(config)#interface fei_1/2ZXR10(config-if)#interface-attribute lanZXR10(config-if)#ip nat insideZXR10(config-if)#exitZXR10(config)#interface fei_1/1 外网口ZXR10(config-if)#porttype l3ZXR10(config-if)#ip address 211.142.218.162 255.255.255.252 外网地址ZXR10(config-if)#ip nat outsideZXR10(config-if)#interface-attribute wanZXR10(config-if)#exitZXR10(config)#acl standard number 10ZXR10(config-std-acl)#permit 192.168.10.0 0.0.0.255ZXR10(config-std-acl)#exitZXR10(config)#ip nat pool outpool 211.142.218.162 211.142.218.162 prefix-length 30ZXR10(config)#ip nat inside source list 10 pool outpool overload路由配置ZXR10(config)#ip route 0.0.0.0 0.0.0.0 211.142.218.161上例中f1/1口是W AN口配置外网IP。
10520;中文规格书,Datasheet资料

© 2012 DESCO INDUSTRIES, INC.
Employee Owned
DESCO INDUSTRIES INC. Technical Bulletin TB-7042
Statguard® Static Dissipative Floor Finish Application Instructions & MSDS
General Guidelines
Made in the United States of America
Statguard® eliminates triboelectric generated charges above 100V before costly damage can occur from personnel who approach static sensitive parts and products. Statguard® also drains static charges from personnel who forget to reattach their wrist straps minimizing the damage that could occur from handling. Even when using conductive tiles, a substantial triboelectric charge is generated. When Statguard® is applied over conductive tiles, the enhanced floor tile eliminates charge generation due to walking across the floor. Generally accepted industrial stripping and floor finish application procedures are to be followed as outlined on pages 2 and 3 in this technical bulletin. Figure 1. Statguard® Static Dissipative Floor Finish NOTE: Statguard® Static Dissipative Floor Care products do not have a set life span. The chemicals are not known to degrade over time when stored at the proper temperature conditions as stated in the Material Safety Data Sheet. We also recommend that these products be stored in their original containers and be sealed when not in use. GROUNDING Conventional grounding practices like electrically connecting Statguard® Static Dissipative Floor Finish to earth ground is required for applications of static dissipative floor finish that are less than 50 square feet. For applications that are greater than 50 square feet, the capacitance of Statguard® Floor Finish is MANY, MANY times greater than the capacitance of the human body model. The difference in capacitance is so great that the Statguard® treated floor acts as a theoretical reservoir or natural ground. The capacitance and surface resistance of the Statguard® treated floor will decay a 5000v charge to zero in .05 sec. per FTMS 101B, Method 4046. Statguard® has substantially less than the maximum static decay time of 0.1 seconds. Per ESD Handbook ESD TR20.20 section 5.3.4.2 “Floor finishes and topical antistats, on the other hand. function by two separate mechanisms. First. they reduce the surface’s tendency 10 generate a stalic charge. Second, they provide a path for the dissipation of charge. The charge may dissipate over the surface of the finish or it may dissipate to ground if the floor finish is grounded.” To remove charge form personnel ESD footwear should be used in conjunction with ESD flooring. ESD footwear should be worn on both feet.
MJW18020G;中文规格书,Datasheet资料

10.0
Ic/Ib = 5.0
10.0
Ic/Ib = 10
1.0 TJ = 25°C
TJ = −20°C
1.0 TJ = 25°C
TJ = −20°C
VBE, VOLTAGE (VOLTS)
VBE, VOLTAGE (VOLTS)
TJ = 125°C
0.1
0.001
0.01
0.1
1.0
10
100
IC, COLLECTOR CURRENT (A)
(IC = 3 Adc, VCE = 5 Vdc) (IC = 10 Adc VCE = 2 Vdc) (IC = 20 Adc VCE = 2 Vdc) (IC = 10 mAdc VCE = 5 Vdc)
(TC = 125°C) (TC = 125°C) (TC = 125°C)
Base−Emitter Saturation Voltage (IC = 10 Adc, IB = 2 Adc) (IC = 20 Adc, IB = 4 Adc)
PD
250
W
2.0
W/_C
Operating and Storage Junction Temperature Range
TJ, Tstg −65 to +150 _C
THERMAL CHARACTERISTICS
Characteristic
Symbol
Max
Unit
Thermal Resistance, Junction−to−Case
30 AMPERES 1000 VOLTS BVCES 450 VOLTS BVCEO, 250 WATTS
1 2 3
74435561100;中文规格书,Datasheet资料

74435561100
DATUM / DATE : 2009-11-02 Gurtspezifikation / Tape specification:
G H
SPEICHERDROSSEL WE-HCI POWER-CHOKE WE-HCI
I Rollenspezifikation / tape and reel specification:
74435561100
DATUM / DATE : 2009-11-02
SPEICHERDROSSEL WE-HCI POWER-CHOKE WE-HCI
H Induktivitätskurve / Inductance curve:
Induktivität vs Strom (typ.) Inductance vs Current (typ.)
08-09-29
Geprüft / checked
Kontrolliert / approved
Datum / date
D-74638 Waldenburg · Max-Eyth-Strasse 1 - 3 · Germany · Telefon (+49) (0) 7942 - 945 - 0 · Telefax (+49) (0) 7942 - 945 - 400 http://www.we-online.de
12,00
10,00
8,00
L (µH)
6,00
4,00
2,00
0,00 0 5 10 15 Current (A) 20 25 30 35
Freigabe erteilt / general release:
..................................................................................
129-0701-202;129-0701-302;129-0701-201;129-0701-301;140-0000-958;中文规格书,Datasheet资料

To our valued customers:For over 80 years, Johnson Components and Cambridge Products have been providing our electronics distributor and OEM customers with cost-effective, high-quality solutions forconnectivity.This catalog combines the product lines of Johnson Components and Cambridge Products under the Johnson product line of Emerson Network Power Connectivity Solutions .In addition to combining these product lines, we have also combined several of our intercon-nect businesses under the name Emerson Network Power Connectivity Solutions .We believe this name not only reflects our traditional industry focus, but also better communicates the additional resources that we can supply as part of Emerson Network Power.Although our name is changing, our commitment to product quality and to excellent service to our customers will not.Our combined connectivity product line will continue to focus on the wireless, test/measurement, instrumentation, OEM and installer markets for data networks,telecommunications, satellite, security, telemetry and CATV .This catalog offers our customers new products such as the SMK (2.92mm) range of 40 GHz connectors and non-magnetic connectors for the medical industry as well as extensiveenhancements to our existing product portfolio.It continues to provide comprehensive data on our range of coaxial connectors, cable assemblies, hardware, tools and test products to support your design and application needs and those of your customers.Emerson Network Power Connectivity Solutions is a global player with manufacturing, sales and engineering presence in China, the United Kingdom and the United States to meet our customers’requirements around the world.Our goal is to continue to expand our product offerings and capabilities to continue meeting your changing needs.Thank you for allowing us the opportunity to serve you.Best Regards,Brian G.MasonPresidentEmerson Network PowerConnectivity Solutions Connectivity Solutions/MMCX Connectors - 50 OhmPC Mount (7)Specifications (4)Semi-Rigid and Flexible Cable (5)Termination (8)Other InformationAssembly Instructions (205)Assembly T ools (189)Cable Assembly (199)Cable Information (200)Capabilities (198)Mounting Hole Layouts (201)Numerical Index (289)Ordering Information (2)Competitor Cross Reference (281)Connectivity Solutions T el: 800-247-8256 • Fax: 507-833-6287 • /connectivity4Connectivity Solutions Tel: 800-247-8256 • Fax: 507-833-6287 • /connectivityELECTRICAL RATINGSImpedance: 50 ohmsFrequency Range:Connectors..........................................0-6 GHzDummy loads ......................................0-1 GHzVSWR: (f = GHz) Straight Right Angle.047 dia flexible RG-178, RG-316, RG-316 DS 1.20 1.25.086 Semi-Rigid 1.15 1.15Uncabled receptacles, dummy loads ........................................N/AWorking Voltage:Connectors.................................................170 VRMS at sea level †Dummy loads ............................................................................N/ADielectric Withstanding Voltage:Connectors.................................................500 VRMS at sea level †Dummy loads ............................................................................N/AInsulation Resistance: 1000 megohms minContact Resistance: (milliohms maximum)AfterInitial EnvironmentalCenter contact (straight cabled connectorsand uncabled receptacles)......................5.08.0Center contact (right angle cabledconnectors)..............................................5.015.0Outer contact (all connectors).....................1.0 1.5Braid to body...............................................1.5N/ACorona Level: Connectors.................190 volts min at 70,000 feet †Dummy loads ....................................................N/AInsertion Loss: (dB max tested at 1 GHz)Straight cabled connectors.......................................................0.1Right angle cabled connectors .................................................0.2Uncabled receptacles, dummy loads.......................................N/ARF Leakage: (dB minimum, tested at 2.5 GHz)Flexible cable connectors ...................................................-60 dB.086 Semi-Rigid..................................................................-70 dBDummy loads ..........................................................................N/ARF High Potential Withstanding Voltage:(400 VRMS at 4 and 7 MHz)†Power Rating (Dummy Load): 0.5 watt @ +25°C, derated to 0.25 watt@ +125° C†Avoid user injury due to misapplication.See safety advisory definitions inside front cover.Mating Engagement for MMCX Series 1.ID of contact to meet VSWR matingcharacteristics and connector durabil-ity when mated with a dia .016 +/- .001male contact.2.Must meet the force to engage and dis-engage when mated with mating part.JACK JACK PLUGPLUGREFERENCE PLANE MECHANICAL RATINGS Engagement Design: Series MMCX Engagement/Disengagement Force:8 lbs. max axial engagement 1.4 lbs. min axial disengagement Contact Retention: 2.0 lbs. minimum axial force Cable Retention:Connectors for .047 flexible Connectors for RG-178...............................7.0N/A Connectors for RG-316..............................20.0N/A Connectors for RG-316 DS........................25.0N/A Connectors for .086 Semi-Rigid.................30.016*Or cable breaking strength whichever is less.Durability:.......................................................500 cycles minimum ENVIRONMENTAL RATINGS (Meets or exceeds the applicable paragraph of MIL-C-39012)Operating Temperature: Connectors .................- 65°C to + 165°C Dummy loads .............- 65°C to + 125°C Thermal Shock: Connectors: MIL-STD-202, Method 107,Condition C, except -55°C to + 155°C (N/A dummy loads)Corrosion: MIL-STD-202, Method 101, Condition B (N/A dummy loads)Shock: MIL-STD-202, Method 213, Condition B (N/A dummy loads)Vibration: MIL-STD-202, Method 204, Condition D (N/A dummy loads)Moisture Resistance: MIL-STD-202, Method 106 (N/A dummy loads)MATERIAL SPECIFICATIONS Bodies: Brass per QQ-B-626, gold plated* per MIL-G-45204 .00001" min.Contacts: Beryllium copper per QQ-C-530, gold plated* per MIL-G-45204 .00003" min.Interface Spring: Beryllium copper per QQ-C-530, gold plated* per MIL-G-45204 .00003" min.Insulators: PTFE fluorocarbon per ASTM D 1710 and ASTM D 1457Crimp Sleeves: Copper per WW-T -799 or brass per QQ-B-626, gold plated per MIL-G-45204 .00001" min.Mounting Hardware: Brass per QQ-B-626 or QQ-B-613, gold plated per MIL-G-45204 .00001" min.*All gold plated parts include a .00005” min nickel barrier layer.Connectivity Solutions T el: 800-247-8256 • Fax: 507-833-6287 • /connectivity Right Angle Solder Type Plug - Captivated Contact Right Angle Crimp Type Plug - Captivated Contact Assembly instructions page 207.Assembly instructions pages 208 and 209. CABLE TYPEPART NO..086 Semi-Rigid 135-3693-101CABLE TYPEPART NO. “A” “B” TERMINATION .047" Diameter FlexibleHuber K01152-07135-3436-101.354 (8.99).276 (6.98)Crimp Insert Axon P512479AAstrolab 32018 DSRG-178/U, 196135-3402-101.354 (8.99).276 (6.98)Crimp Insert RG-178/U, 196135-3402-111.412 (10.46).334 (8.48)Crimp Sleeve RG-316/U, 188, 187135-3403-101.412 (10.46).334 (8.48)Crimp Sleeve 179, 161, 174RG-316 DS, RG-188 DS 135-3404-101.412 (10.46).334 (8.48)Crimp Sleeve6Connectivity Solutions Tel: 800-247-8256 • Fax: 507-833-6287 •/connectivity Straight Crimp Type Jack -Solder or Crimp Captivated ContactStraight Crimp Type Plug -Solder or Crimp Captivated ContactStraight Crimp Type Bulkhead Jack -Solder or Crimp Captivated ContactAssembly instructions pages 210 and 211.Assembly instructions pages 212 and 213.Assembly instructions page 213.Mounting Hole layout fig. 5 page 201.CABLE TYPEPART NO. “A” “D”TERMINATION .047" Diameter FlexibleHuber K01152-07135-3436-001.462 (11.73).137 (3.48)Crimp Insert Axon P512479AAstrolab 32018 DSRG-178/U, 196135-3402-001.462 (11.73).137 (3.48)Crimp Insert RG-316/U, 188, 161, 174135-3403-001.509 (12.93).173 (4.39)Crimp Sleeve RG-316 DS, 188 DS, 187 DS135-3404-001.509 (12.93).173 (4.39)Crimp Sleeve RG-179/U, 187135-3433-001.509 (12.93).173 (4.39)Crimp Sleeve CABLE TYPEPART NO. “A” “D”TERMINATION .047" Diameter Flexible135-3336-001.462 (11.73).137 (3.48)Crimp Insert Huber K01152-07Axon P512479AAstrolab 32018 DSRG-178/U, 196135-3302-001.462 (11.73).137 (3.48)Crimp Insert RG-316/U, 188,161, 174135-3303-001.545 (13.84).173 (4.39)Crimp Sleeve RG-316 DS, 188 DS, 187 DS135-3304-001.545 (13.84).173 (4.39)Crimp Sleeve RG-179/U, 187135-3333-001.545 (13.84).173 (4.39)Crimp Sleeve CABLE TYPEPART NO.TERMINATION .047" Diameter FlexibleHuber K01152-07135-3336-401Crimp Insert Axon P512479AAstrolab 32018 DSRG-178/U, 196135-3302-401Crimp InsertConnectivity Solutions T el: 800-247-8256 • Fax: 507-833-6287 • /connectivityRight Angle Jack Receptacle Straight Mount Jack ReceptacleMounting Hole layout figure 14 page 202.Recommended Land Pattern figure 17 page 202.Straight Jack Receptacle - Surface MountMounting Hole layout figure 14 page 202.PART NO.PACKAGING 135-3711-201Stock 135-3711-202Tape and Reel1500 pcs/reel “L ”PART NO..115 (2.92)135-3701-201.068 (1.73)135-3701-211“L ”PART NO..115 (2.92)135-3701-301.068 (1.73)135-3701-3118Connectivity Solutions Tel: 800-247-8256 • Fax: 507-833-6287 •/connectivityEnd Launch Jack Receptacle - Surface Mount Straight Plug ReceptacleMounting Hole layout figure 14 page 202.Recommended Land Pattern and Board Notch figure 16 page 202.Plug Dummy LoadPART NO.135-3801-201PART NO.PACKAGING 135-3711-801Stock 135-3711-802Tape and Reel1000pcs/reelFREQ. RANGEPART NO.PLATING RESISTANCE 0-1 GHZ 135-3801-811Gold 50 OhmsMCX Connectors - 50 OhmBulkhead and Panel Mount (18)Flexible Cable (12)In-Series Adapters and T erminations (19)PC Mount (14)Semi-Rigid Cable (11)Specifications (10)MCX Non-Magnetic Connectors - 50 OhmPC Mount (31)Specifications (30)MCX Reverse Polarity - 50 OhmFlexible Cable (21)PC Mount (22)Specifications (20)MCX Connectors - 75 OhmBetween-Series Adapters (28)Flexible Cable (24)In-Series Matched Adapters and Terminations (27)PC Mount (25)Specifications (23)Other InformationAssembly Instructions (205)Assembly Tools (189)Cable Assembly (199)Cable Information (200)Capabilities (198)Mounting Hole Layouts (201)Numerical Index (289)Ordering Information (2)Competitor Cross Reference (281)Connectivity Solutions T el: 800-247-8256 • Fax: 507-833-6287 • /connectivity10Connectivity Solutions Tel: 800-247-8256 • Fax: 507-833-6287 • /connectivity †Avoid user injury due to misapplication. See safety advisory definitions on page 2.** All gold plated parts include a .00005" min. nickel underplate barrier layer.NOTES 1.ID of contact to meet VSWR mating characteristics and connector durability when mated with a dia. .019-.021 (0.48-0.53) male contact.2.Must meet the force to engage and disengage when mated withmating part.PLUGJACK PLUG Mating Engagement for MCX Series Compatible with CECC 22220ELECTRICAL RATINGSImpedance: 50 OhmsFrequency Range:Connectors..............................................0-6 GHzDummy loads ..........................................0-1 GHzVSWR: (f = GHz)Straight Cabled Right AngleConnectors Cabled ConnectorsRG-316 and .086 Semi-Rigid cable .1.13 + .04f 1.07 + .04f Adapters..............................................................................1.13 + .04f Uncabled receptacles, Dummy loads.............................................N/A Working Voltage: (VRMS maximum)†Connectors for Cable Type Sea Level 70K Feet RG-178...................................................25065RG-316, .086 Semi-Rigid uncableduncabled receptacles, adapters (33585)Dummy loads..............................................................................N/A Dielectric Withstanding Voltage: (VRMS minimum at sea level)†Connectors for RG-178..............................................................750Connectors for RG-316, .086 Semi-Rigid,uncabled receptacles, adapters............................................1000Dummy loads..............................................................................N/A Corona Level: (Volts minimum at 70,000 feet)†Connectors for RG-178..............................................................190Connectors for RG-316, .086 Semi-Rigiduncabled receptacles, adapters...............................................250Dummy loads..............................................................................N/A Insertion Loss: (dB maximum, tested at 1 GHz)Straight cable connectors and adapters.................................0.1 dB Right angle cable connectors .................................................0.2 dB Uncabled receptacles, dummy loads..........................................N/A Insulation Resistance: 10,000 megohms minimumContact Resistance: (milliohms maximum)AfterCenter contact (straight cabled connectors,uncabled receptacles and adapters).................5.08.0Center contact (right angle cabled connectors)....5.015.0Outer contact ........................................................1.0 1.5Braid to body (gold plated connectors).................1.0N/A Braid to body (nickel plated connectors)...............2.5N/A RF Leakage: (dB typical tested at 2.5 GHz)Cable connectors...................................................................-55 dB Uncabled receptacles and adapters, dummy loads....................N/A RF High Potential Withstanding Voltage: (VRMS minimum, tested at 4and 7 MHz)†Connectors for RG178................................................................500Connectors for RG316 and adapters..........................................700.086 Semi-Rigid..........................................................................670Uncabled receptacles.................................................................600Dummy loads..............................................................................N/A Power Rating (Dummy Load): 0.5 watt @ +25°C, derated to 0.25 watt @ +125°C MECHANICAL RATINGS Engagement Design: Compatible with CECC 22220, Series MCX Engagement Force: 5.6 pounds maximum axial force Disengagement Force: 8 pounds maximum axial force, 1 pound min.Contact Retention: 2.3 pounds min. axial force (captivated contacts)1 inch-ounce min. torque (uncabled receptacles)Cable Retention:Axial Force* (lbs)Torque (in-oz)Connectors for RG17810N/A Connectors for RG316................................20N/A Connectors for RG316DS ...........................25N/A Connectors for .086 Semi-Rigid..................3016* or cable breaking strength whichever is less.Durability:............................................................500 cycles minimum ENVIRONMENTAL RATINGS (Meets or exceeds the applicable paragraph of MIL-C-39012)Operating Temperature: Connectors ......................- 65°C to + 165°C Dummy loads ................. - 65°C to + 125°C Thermal Shock: MIL-STD-202, Method 107, Condition F (N/A dummy loads)Corrosion: MIL-STD-202, Method 101, Condition B (N/A dummy loads)Shock: MIL-STD-202, Method 213, Condition B (N/A dummy loads)Vibration: MIL-STD-202, Method 204, Condition B (N/A dummy loads)Moisture Resistance: MIL-STD-202, Method 106 (N/A dummy loads)MATERIAL SPECIFICATIONS Bodies: Brass per QQ-B-626 or zinc per ASTM B86-71, gold plated**per MIL-G-45204 .00001” min or nickel plated per QQ-N-290 or bright tin plated Contacts: Male - brass per QQ-B-626, gold plated per MIL-G-45204.00003" min.Female - beryllium copper per QQ-C-530, gold plated per MIL-G-45204 .00003" min.Insulators: PTFE fluorocarbon per ASTM D 1710 and ASTM D 1457Expansion Caps: Brass per QQ-B-613, gold plated per MIL-G-45204.00001" min. or nickel plated per QQ-N-290Crimp Sleeves: Copper per WW-T -799, gold plated per MIL-G-45204.00001" min. or nickel plated per QQ-N-290Mounting Hardware: Brass (nuts) per QQ-B-626 or phosphor bronze (lockwashers) QQ-B-750, gold plated per MIL-G-45204 .00001" min.or nickel plated per QQ-N-290JACK分销商库存信息:EMERSON129-0701-202129-0701-302129-0701-201 129-0701-301140-0000-958140-0000-957。
LT1809_1资料

12ELECTRICAL CHARACTERISTICST A = 25°C. V S = 5V, 0V; V S = 3V, 0V; V SHDN = open; V CM = V OUT = half supply, unless otherwise noted.SYMBOL PARAMETER CONDITIONS MIN TYP MAX UNITS I OS Input Offset Current V CM = V+0.05 1.2µAV CM = V– + 0.2V0.24µA ∆I OS Input Offset Current Shift V CM = V– + 0.2V to V+0.25 5.2µA e n Input Noise Voltage Density f = 10kHz16nV/√Hz i n Input Noise Current Density f = 10kHz5pA/√Hz C IN Input Capacitance2pF A VOL Large-Signal Voltage Gain V S = 5V, V O = 0.5V to 4.5V, R L = 1k to V S/22580V/mVV S = 5V, V O = 1V to 4V, R L = 100Ω to V S/2410V/mVV S = 3V, V O = 0.5V to 2.5V, R L = 1k to V S/21542V/mV CMRR Common Mode Rejection Ratio V S = 5V, V CM = V– to V+6682dBV S = 3V, V CM = V– to V+6178dB CMRR Match (Channel-to-Channel) (Note 10)V S = 5V, V CM = V– to V+6082dBV S = 3V, V CM = V– to V+5578dB Input Common Mode Range V–V+V PSRR Power Supply Rejection Ratio V S = 2.5V to 10V, V CM = 0V7187dB PSRR Match (Channel-to-Channel) (Note 10)V S = 2.5V to 10V, V CM = 0V6587dB Minimum Supply Voltage (Note 6) 2.3 2.5V V OL Output Voltage Swing LOW (Note 7)No Load1250mVI SINK = 5mA50120mVI SINK = 25mA180375mV V OH Output Voltage Swing HIGH (Note 7)No Load2080mVI SOURCE = 5mA80180mVI SOURCE = 25mA330650mV I SC Short-Circuit Current V S = 5V±45±85mAV S = 3V±35±70mA I S Supply Current per Amplifier12.517mASupply Current, Shutdown V S = 5V, V SHDN = 0.3V0.55 1.25mAV S = 3V, V SHDN = 0.3V0.310.90mA I SHDN SHDN Pin Current V S = 5V, V SHDN = 0.3V420750µAV S = 3V, V SHDN = 0.3V220500µA Output Leakage Current, Shutdown V SHDN = 0.3V0.175µA V L SHDN Pin Input Voltage Low0.3V V H SHDN Pin Input Voltage High V S – 0.5V t ON Turn-On Time V SHDN = 0.3V to 4.5V, R L = 10080ns t OFF Turn-Off Time V SHDN = 4.5V to 0.3V, R L = 10050ns GBW Gain-Bandwidth Product Frequency = 2MHz160MHz SR Slew Rate V S = 5V, A V = –1, R L = 1k, V O = 4V P-P300V/µs FPBW Full Power Bandwidth V S = 5V, V OUT = 4V P-P23.5MHz THD Total Harmonic Distortion V S = 5V, A V = 1, R L = 1k, V O = 2V P-P, f C = 5MHz–86dB t S Settling Time0.1%, V S = 5V, V STEP = 2V, A V = –1, R L = 500Ω27ns ∆G Differential Gain (NTSC)V S = 5V, A V = 2, R L = 150Ω0.015%∆θDifferential Phase (NTSC)V S = 5V, A V = 2, R L = 150Ω0.05Deg34SYMBOL PARAMETER CONDITIONSMIN TYP MAX UNITS V OSInput Offset VoltageV CM = V + LT1809 SO-8q 1 3.0mV V CM = V – LT1809 SO-8q 1 3.0mV V CM = V +q 1 3.5mV V CM = V –q 1 3.5mV V OS TC Input Offset Voltage Drift (Note 8)V CM = V +q 925µV/°C V CM = V –q 925µV/°C ∆V OSInput Offset Voltage ShiftV CM = V – to V + LT1809 SO-8q 0.5 2.5mV V CM = V – to V +q 0.5 3.0mV Input Offset Voltage Match (Channel-to-Channel)V CM = V –, V CM = V +q 1.2 6.5mV (Note 10)I B Input Bias Current V CM = V + – 0.2V q 210µA V CM = V – + 0.4Vq –30–14µA ∆I BInput Bias Current ShiftV CM = V – + 0.4V to V + – 0.2V q 1640µA Input Bias Current Match (Channel-to-Channel)V CM = V + – 0.2V q 0.15µA (Note 10)V CM = V – + 0.4V q 0.510µA I OS Input Offset Current V CM = V + – 0.2V q 0.05 1.5µA V CM = V – + 0.4Vq 0.40 4.5µA ∆I OS Input Offset Current Shift V CM = V – + 0.4V to V + – 0.2Vq 0.456µA A VOLLarge-Signal Voltage GainV S = 5V, V O = 0.5V to 4.5V, R L = 1k to V S /2q 2075V/mV V S = 5V, V O = 1V to 4V, R L = 100Ω to V S /2q 3.58.5V/mV V S = 3V, V O = 0.5V to 2.5V, R L = 1k to V S /2q 1240V/mV CMRR Common Mode Rejection RatioV S = 5V, V CM = V – to V +q 6480dB V S = 3V, V CM = V – to V +q 6075dB CMRR Match (Channel-to-Channel) (Note 10)V S = 5V, V CM = V –, V CM = V +q 5880dB V S = 3V, V CM = V –, V CM = V +q 5475dBInput Common Mode Rangeq V –V +V PSRR Power Supply Rejection RatioV S = 2.5V to 10V, V CM = 0V q 7083dB PSRR Match (Channel-to-Channel) (Note 10)V S = 2.5V to 10V, V CM = 0V q 6483dB Minimum Supply Voltage (Note 6)q 2.3 2.5V V OLOutput Voltage Swing LOW (Note 7)No Load q 1260mV I SINK = 5mA q 55140mV I SINK = 25mA q 200400mV V OHOutput Voltage Swing HIGH (Note 7)No Loadq 50120mV I SOURCE = 5mA q 110220mV I SOURCE = 25mA q 370700mV I SC Short-Circuit Current V S = 5V q ±40±75mA V S = 3Vq ±30±65mAI SSupply Current per Amplifier q 1520mA Supply Current, ShutdownV S = 5V, V SHDN = 0.3V q 0.58 1.4mA V S = 3V, V SHDN = 0.3V q 0.35 1.1mA I SHDNSHDN Pin CurrentV S = 5V, V SHDN = 0.3V q 420850µA V S = 3V, V SHDN = 0.3V q 220550µA Output Leakage Current, ShutdownV SHDN = 0.3Vq 2µA V L SHDN Pin Input Voltage Low q0.3V V HSHDN Pin Input Voltage Highq V S – 0.5VThe q denotes the specifications which apply over the 0°C ≤ T A ≤ 70°Ctemperature range. V S = 5V, 0V; V S = 3V, 0V; V SHDN = open; V CM = V OUT = half supply, unless otherwise noted.ELECTRICAL CHARACTERISTICS5The q denotes the specifications which apply over the 0°C ≤ T A ≤ 70°Ctemperature range. V S = 5V, 0V; V S = 3V, 0V; V SHDN = open; V CM = V OUT = half supply, unless otherwise noted.ELECTRICAL CHARACTERISTICSSYMBOL PARAMETER CONDITIONSMIN TYP MAX UNITSt ON Turn-On Time V SHDN = 0.3V to 4.5V, R L = 100q 80ns t OFF Turn-Off Time V SHDN = 4.5V to 0.3V, R L = 100q 50ns GBW Gain-Bandwidth Product Frequency = 2MHzq 145MHz SR Slew RateV S = 5V, A V = –1, R L = 1k, V O = 4V P-P q 250V/µs FPBWFull Power BandwidthV S = 5V, V OUT = 4V P-Pq20MHzSYMBOL PARAMETER CONDITIONSMIN TYP MAX UNITS V OSInput Offset VoltageV CM = V + LT1809 SO-8q 1 3.5mV V CM = V – LT1809 SO-8q 1 3.5mV V CM = V +q 1 4.0mV V CM = V –q 1 4.0mV V OS TC Input Offset Voltage Drift (Note 8)V CM = V +q 925µV/°C V CM = V –q 925µV/°C ∆V OSInput Offset Voltage ShiftV CM = V – to V + LT1809 SO-8q 0.5 3.0mV V CM = V –q 0.5 3.5mV Input Offset Voltage Match (Channel-to-Channel)V CM = V +, V CM = V –q 1.27mV (Note 10)I B Input Bias Current V CM = V + – 0.2V q 212µA V CM = V – + 0.4Vq –35–17µA ∆I BInput Bias Current ShiftV CM = V – + 0.4V to V + – 0.2V q 1947µA Input Bias Current Match (Channel-to-Channel)V CM = V + – 0.2V q 0.26µA (Note 10)V CM = V – + 0.4V q 0.612µA I OS Input Offset Current V CM = V + – 0.2V q 0.082µA V CM = V – + 0.4Vq 0.56µA ∆I OS Input Offset Current Shift V CM = V – + 0.4V to V + – 0.2Vq 0.587.5µA A VOLLarge-Signal Voltage GainV S = 5V, V O = 0.5V to 4.5V, R L = 1k to V S /2q 1760V/mV V S = 5V, V O = 1V to 4V, R L = 100Ω to V S /2q 2.57V/mV V S = 3V, V O = 0.5V to 2.5V, R L = 1k to V S /2q 1035V/mV CMRR Common Mode Rejection RatioV S = 5V, V CM = V – to V +q 6380dB V S = 3V, V CM = V – to V +q 5875dB CMRR Match (Channel-to-Channel) (Note 10)V S = 5V, V CM = V – to V +q 5778dB V S = 3V, V CM = V – to V +q 5272dBInput Common Mode Rangeq V –V +V PSRR Power Supply Rejection RatioV S = 2.5V to 10V, V CM = 0V q 6983dB PSRR Match (Channel-to-Channel) (Note 10)V S = 2.5V to 10V, V CM = 0V q 6383dB Minimum Supply Voltage (Note 6)q 2.3 2.5V V OLOutput Voltage Swing LOW (Note 7)No Load q 1870mV I SINK = 5mA q 60150mV I SINK = 25mA q 210450mV V OHOutput Voltage Swing HIGH (Note 7)No Loadq 55130mV I SOURCE = 5mA q 120240mV I SOURCE = 25mA q 375750mV I SC Short-Circuit Current V S = 5V q ±30±70mA V S = 3Vq ±25±60mAI SSupply Current per Amplifier q 1521mA Supply Current, ShutdownV S = 5V, V SHDN = 0.3V q 0.58 1.5mA V S = 3V, V SHDN = 0.3Vq0.351.2mAThe q denotes the specifications which apply over the –40°C ≤ T A ≤ 85°C temperature range. V S = 5V, 0V; V S = 3V, 0V; V SHDN = open;V CM = V OUT = half supply, unless otherwise noted. (Note 5)ELECTRICAL CHARACTERISTICSThe q denotes the specifications which apply over the –40°C ≤ T A≤ 85°C temperature range. V S = 5V, 0V; V S = 3V, 0V; V SHDN = open; V CM = V OUT = half supply, unless otherwise noted. (Note 5)SYMBOL PARAMETER CONDITIONS MIN TYP MAX UNITS I SHDN SHDN Pin Current V S = 5V, V SHDN = 0.3V q420900µAV S = 3V, V SHDN = 0.3V q220600µA Output Leakage Current, Shutdown V SHDN = 0.3V q3µA V L SHDN Pin Input Voltage Low q0.3V V H SHDN Pin Input Voltage High q V S – 0.5V t ON Turn-On Time V SHDN = 0.3V to 4.5V, R L = 100q80ns t OFF Turn-Off Time V SHDN = 4.5V to 0.3V, R L = 100q50ns GBW Gain-Bandwidth Product Frequency = 2MHz q140MHz SR Slew Rate V S = 5V, A V = -1, R L = 1k, V O = 4V P-P q180V/µs FPBW Full Power Bandwidth V S = 5V, V OUT = 4V P-P q14MHzT A = 25°C. V S = ±5V, V SHDN = open, V CM = 0V, V OUT = 0V, unless otherwise noted.SYMBOL PARAMETER CONDITIONS MIN TYP MAX UNITS V OS Input Offset Voltage V CM = V+ LT1809 SO-80.8 3.0mVV CM = V– LT1809 SO-80.8 3.0mVV CM = V+0.8 3.5mVV CM = V–0.8 3.5mV ∆V OS Input Offset Voltage Shift V CM = V– to V+ LT1809 SO-80.35 2.5mVV CM = V– to V+0.35 3.0mV Input Offset Voltage Match (Channel-to-Channel)V CM = V+, V CM = V–16mV (Note 10)I B Input Bias Current V CM = V+210µAV CM = V– + 0.2V–30–12.5µA ∆I B Input Bias Current Shift V CM = V– + 0.2V to V+14.540µA Input Bias Current Match (Channel-to-Channel)V CM = V+0.15µA (Note 10)V CM = V– + 0.2V0.410µA I OS Input Offset Current V CM = V+0.052µAV CM = V– + 0.2V0.405µA ∆I OS Input Offset Current Shift V CM = V– + 0.2V to V+0.457µA e n Input Noise Voltage Density f = 10kHz16nV/√Hz i n Input Noise Current Density f = 10kHz5pA/√Hz C IN Input Capacitance f = 100kHz2pF A VOL Large-Signal Voltage Gain V O = –4V to 4V, R L = 1k30100V/mVV O = –2.5V to 2.5V, R L = 100Ω 4.512V/mV CMRR Common Mode Rejection Ratio V CM = V– to V+7089dB CMRR Match (Channel-to-Channel) (Note 10)V CM = V– to V+6489dB Input Common Mode Range V–V+V PSRR Power Supply Rejection Ratio V+= 2.5V to 10V, V– = 0V7187dB PSRR Match (Channel-to-Channel) (Note 10)V+= 2.5V to 10V, V– = 0V6590dB V OL Output Voltage Swing LOW (Note 7)No Load1260mVI SINK = 5mA50140mVI SINK = 25mA180425mV V OH Output Voltage Swing HIGH (Note 7)No Load35100mVI SOURCE = 5mA90200mVI SOURCE = 25mA310700mV6ELECTRICAL CHARACTERISTICST A = 25°C. V S = ±5V, V SHDN = open, V CM = 0V, V OUT = 0, unless otherwise noted.SYMBOL PARAMETER CONDITIONS MIN TYP MAX UNITS I SC Short-Circuit Current±55±85mA I S Supply Current per Amplifier1520mASupply Current, Shutdown V SHDN = 0.3V0.6 1.3mA I SHDN SHDN Pin Current V SHDN = 0.3V420750µAOutput Leakage Current, Shutdown V SHDN = 0.3V0.175µA V L SHDN Pin Input Voltage Low0.3V V H SHDN Pin Input Voltage High V+ – 0.5V t ON Turn-On Time V SHDN = 0.3V to 4.5V, R L = 10080ns t OFF Turn-Off Time V SHDN = 4.5V to 0.3V, R L = 10050ns GBW Gain-Bandwidth Product Frequency = 2MHz110180MHz SR Slew Rate A V = –1, R L = 1k, V O = ±4V,175350V/µsMeasured at V O = ±3VFPBW Full Power Bandwidth V OUT = 8V P-P14MHz THD Total Harmonic Distortion A V = 1, R L = 1k, V O = 2V P-P, f C = 5MHz–90dB t S Settling Time0.1%, V STEP = 8V, A V = –1, R L = 500Ω34ns ∆G Differential Gain (NTSC)A V = 2, R L = 150Ω0.01%∆θDifferential Phase (NTSC)A V = 2, R L = 150Ω0.01DegThe q denotes the specifications which apply over the 0°C ≤ T A≤ 70°C temperature range. V S = ±5V, V SHDN = open, V CM = 0V,V OUT = 0V, unless otherwise noted.SYMBOL PARAMETER CONDITIONS MIN TYP MAX UNITS V OS Input Offset Voltage V CM = V+ LT1809 SO-8q1 3.25mVV CM = V– LT1809 SO-8q1 3.25mVV CM = V+q1 3.75mVV CM = V–q1 3.75mV V OS TC Input Offset Voltage Drift (Note 8)V CM = V+q1025µV/°CV CM = V–q1025µV/°C ∆V OS Input Offset Voltage Shift V CM = V– to V+ LT1809 SO-8q0.5 2.75mVV CM = V– to V+q0.5 3.25mV Input Offset Voltage Match (Channel-to-Channel)V CM = V– to V+q 1.2 6.5mV (Note 10)I B Input Bias Current V CM = V+ – 0.2V q 2.512.5µAV CM = V– + 0.4V q–37.5–15µA ∆I B Input Bias Current Shift V CM = V– + 0.4V to V+ – 0.2V q17.550µA Input Bias Current Match (Channel-to-Channel)V CM = V+ – 0.2V q0.16µA (Note 10)V CM = V– + 0.4V q0.512µA I OS Input Offset Current V CM = V+ – 0.2V q0.06 2.25µAV CM = V– + 0.4V q0.56µA ∆I OS Input Offset Current Shift V CM = V– + 0.4V to V+ – 0.2V q0.568.25µA A VOL Large-Signal Voltage Gain V O = –4V to 4V, R L = 1k q2780V/mVV O = –2.5V to 2.5V, R L = 100Ωq 3.510V/mV CMRR Common Mode Rejection Ratio V CM = V– to V+q6986dB CMRR Match (Channel-to-Channel) (Note 10)V CM = V– to V+q6386dB Input Common Mode Range q V–V+V78The q denotes the specifications which apply over the 0°C ≤ T A ≤ 70°Ctemperature range. V S = ±5V, V SHDN = open, V CM = 0V, V OUT = 0V, unless otherwise noted.SYMBOL PARAMETER CONDITIONSMIN TYP MAX UNITS PSRR Power Supply Rejection RatioV + = 2.5V to 10V, V – = 0V q 7083dB PSRR Match (Channel-to-Channel) (Note 10)V + = 2.5V to 10V, V – = 0V q 6483dBV OLOutput Voltage Swing LOW (Note 7)No Load q 2080mV I SINK = 5mA q 50160mV I SINK = 25mA q 210475mV V OHOutput Voltage Swing HIGH (Note 7)No Loadq 60140mV I SOURCE = 5mA q 120240mV I SOURCE = 25mAq 370750mV I SC Short-Circuit Current q ±45±75mA I S Supply Current per Amplifier q17.525mA Supply Current, Shutdown V SHDN = 0.3V q 0.6 1.5mA I SHDN SHDN Pin CurrentV SHDN = 0.3V q 420850µA Output Leakage Current, Shutdown V SHDN = 0.3Vq 3µA V L SHDN Pin Input Voltage Low q 0.3V V H SHDN Pin Input Voltage High q V + – 0.5V t ON Turn-On Time V SHDN = 0.3V to 4.5V, R L = 100q 80ns t OFF Turn-Off Time V SHDN = 4.5V to 0.3V, R L = 100q 50ns GBW Gain-Bandwidth Product Frequency = 2MHz q 85170MHz SR Slew RateA V = –1, R L = 1k, V O = ±4V,q 140300V/µs Measured at V O = ±3V FPBWFull Power BandwidthV OUT = 8V P-P q12MHzELECTRICAL CHARACTERISTICSSYMBOL PARAMETER CONDITIONS MIN TYP MAX UNITS V OSInput Offset VoltageV CM = V + LT1809 SO-8q 1 3.75mV V CM = V – LT1809 SO-8q 1 3.75mV V CM = V +q 1 4.25mV V CM = V –q 1 4.25mV V OS TC Input Offset Voltage Drift (Note 8)V CM = V +q 1025µV/°C V CM = V –q 1025µV/°C ∆V OSInput Offset Voltage ShiftV CM = V – to V + LT1809 SO-8q 0.5 3.00mV V CM = V – to V +q 0.5 3.75mV Input Offset Voltage Match (Channel-to-Channel)V CM = V – to V +q 1.27.5mV (Note 10)I B Input Bias Current V CM = V + – 0.2V q 2.814µA V CM = V – + 0.4Vq –45–17µA ∆I BInput Bias Current ShiftV CM = V – + 0.4V to V + – 0.2V q 19.859µA Input Bias Current Match (Channel-to-Channel)V CM = V + – 0.2V q 0.17µA (Note 10)V CM = V – + 0.4V q 0.614µA I OS Input Offset Current V CM = V + – 0.2V q 0.08 2.5µA V CM = V – + 0.4Vq 0.68µA ∆I OS Input Offset Current Shift V CM = V – + 0.4V to V + – 0.2V q 0.6810.5µA A VOLLarge-Signal Voltage GainV O = –4V to 4V, R L = 1kq 2270V/mV V O = –2.5V to 2.5V, R L = 100Ωq310V/mVThe q denotes the specifications which apply over the –40°C ≤ T A ≤ 85°C temperature range. V S = ±5V, V SHDN = open, V CM = 0V,V OUT = 0V, unless otherwise noted. (Note 5)9Note 1: Absolute Maximum Ratings are those values beyond which the life of a device may be impaired.Note 2: The inputs are protected by back-to-back diodes. If the differential input voltage exceeds 1.4V, the input current should be limited to less than 10mA.Note 3: A heat sink may be required to keep the junction temperature below the absolute maximum rating when the output is shorted indefinitely.Note 4: The LT1809C/LT1809I and LT1810C/LT1810I are guaranteed functional over the operating temperature range of –40°C and 85°C.Note 5: The LT1809C/LT1810C are guaranteed to meet specified performance from 0°C to 70°C. The LT1809C/LT1810C are designed,characterized and expected to meet specified performance from –40°C to 85°C but are not tested or QA sampled at these temperatures. The LT1809I/LT1810I are guaranteed to meet specified performance from –40°C to 85°C.The q denotes the specifications which apply over the –40°C ≤ T A ≤ 85°Ctemperature range. V S = ±5V, V SHDN = open, V CM = 0V, V OUT = 0V, unless otherwise noted. (Note 5)Note 6: Minimum supply voltage is guaranteed by power supply rejection ratio test.Note 7: Output voltage swings are measured between the output and power supply rails.Note 8: This parameter is not 100% tested.Note 9: Thermal resistance varies depending upon the amount of PC board metal attached to the V – pin of the device. θJA is specified for a certain amount of 2oz of copper metal trace connecting to the V – pin as described in the thermal resistance tables in the Applications Information section.Note 10: Matching parameters are the difference between the two amplifiers of the LT1810.SYMBOL PARAMETER CONDITIONS MIN TYP MAX UNITS CMRRCommon Mode Rejection RatioV CM = V – to V +q 6886dB CMRR Match (Channel-to-Channel) (Note 10)V CM = V – to V +q 6286dBInput Common Mode Rangeq V –V +V PSRR Power Supply Rejection RatioV + = 2.5V to 10V, V – = 0V q 6983dB PSRR Match (Channel-to-Channel) (Note 10)V + = 2.5V to 10V, V – = 0V q 6383dB V OLOutput Voltage Swing LOW (Note 7)No Load q 23100mV I SINK = 5mA q 60170mV I SINK = 25mA q 220525mV V OHOutput Voltage Swing HIGH (Note 7)No Loadq 75160mV I SOURCE = 5mA q 130260mV I SOURCE = 25mAq 375775mV I SC Short-Circuit Current q ±30±75mA I S Supply Current per Amplifier q1925mA Supply Current, Shutdown V SHDN = 0.3V q 0.65 1.6mA I SHDN SHDN Pin CurrentV SHDN = 0.3V q 420900µA Output Leakage Current, Shutdown V SHDN = 0.3Vq 4µA V L SHDN Pin Input Voltage Low q 0.3V V H SHDN Pin Input Voltage High q V + – 0.5V t ON Turn-On Time V SHDN = 0.3V to 4.5V, R L = 100q 80ns t OFF Turn-Off Time V SHDN = 4.5V to 0.3V, R L = 100q 50ns GBW Gain-Bandwidth Product Frequency = 2MHz q 80160MHz SR Slew RateA V = –1, R L = 1k, V O = ±4V,q 110220V/µs Measured at V O = ±3V FPBWFull Power BandwidthV OUT = 8V P-P q8.5MHzELECTRICAL CHARACTERISTICS10TIME (2 SEC/DIV)1809 G21 Slew Rate vs TemperatureV S = ±5VAPPLICATIO S I FOR ATIOW UUU Table 1. LT1809 6-Lead SOT-23 PackageCOPPER AREA BOARD AREA THERMAL RESISTANCE TOPSIDE (mm 2)(mm 2)(JUNCTION-TO-AMBIENT)2702500135°C/W 1002500145°C/W 202500160°C/W 02500200°C/WDevice is mounted on topside.Table 2. LT1809/LT1810 SO-8 PackageCOPPER AREA TOPSIDE BACKSIDEBOARD AREATHERMAL RESISTANCE (mm 2)(mm 2)(mm 2)(JUNCTION-TO-AMBIENT)11001100250065°C/W 330330250085°C/W 3535250095°C/W 3502500100°C/W 02500105°C/WDevice is mounted on topside.Table 3. LT1810 8-Lead MSOP PackageCOPPER AREA TOPSIDE BACKSIDEBOARD AREA THERMAL RESISTANCE(mm 2)(mm 2)(mm 2)(JUNCTION-TO-AMBIENT)5405402500110°C/W 1001002500120°C/W 10002500130°C/W 3002500135°C/W 02500140°C/WDevice is mounted on topside.Junction temperature T J is calculated from the ambienttemperature T A and power dissipation P D as follows:T J = T A + (P D • θJA )The power dissipation in the IC is the function of the supply voltage, output voltage and the load resistance. For a given supply voltage, the worst-case power dissipation P D(MAX)occurs at the maximum supply current with the output voltage at half of either supply voltage (or the maximum swing is less than 1/2 the supply voltage). P D(MAX) is given by:P D(MAX) = (V S • I S(MAX)) + (V S /2)2/R LExample: An LT1810 in SO-8 mounted on a 2500mm 2area of PC board without any extra heat spreading planeconnected to its V – pin has a thermal resistance of 105°C/W, θJA . Operating on ±5V supplies with both amplifiers simultaneously driving 50Ω loads, the worst-case power dissipation is given by:P D(MAX)= 2 • (10 • 25mA) + 2 • (2.5)2/50= 0.5 + 0.250 = 0.750WThe maximum ambient temperature that the part is al-lowed to operate is:T A = T J – (P D(MAX) • 105°C/W)= 150°C – (0.750W • 105°C/W) = 71°CTo operate the device at higher ambient temperature,connect more metal area to the V – pin to reduce the thermal resistance of the package as indicated in Table 2.Input Offset VoltageThe offset voltage will change depending upon which input stage is active and the maximum offset voltage is guaran-teed to be less than 3mV. The change of V OS over the entire input common mode range (CMRR) is less than 2.5mV on a single 5V and 3V supply.Input Bias CurrentThe input bias current polarity depends upon a given input common voltage at whichever input stage is operating.When the PNP input stage is active, the input bias currents flow out of the input pins and flow into the input pins when the NPN input stage is activated. Because the input offset current is less than the input bias current, matching the source resistances at the input pin will reduce total offset error.OutputThe LT1809/LT1810 can deliver a large output current,so the short-circuit current limit is set around 90mA to prevent damage to the device. Attention must be paid to keep the junction temperature of the IC below the abso-lute maximum rating of 150°C (refer to the Power Dissi-pation section) when the output is continuously short circuited. The output of the amplifier has reverse-biased diodes connected to each supply. If the output is forcedAPPLICATIO S I FOR ATIOW UUU beyond either supply, unlimited current will flow through these diodes. If the current is transient and limited to several hundred milliamps, no damage to the device will occur.Overdrive ProtectionWhen the input voltage exceeds the power supplies, two pairs of crossing diodes, D1 to D4, will prevent the output from reversing polarity. If the input voltage exceeds either power supply by 700mV, diodes D1/D2 or D3/D4 will turn on, keeping the output at the proper polarity. For the phase reversal protection to perform properly, the input current must be limited to less than 5mA. If the amplifier is severely overdriven, an external resistor should be used to limit the overdrive current.The LT1809/LT1810’s input stages are also protected against differential input voltages of 1.4V or higher by back-to-back diodes, D5/D8, that prevent the emitter-base breakdown of the input transistors. The current in these diodes should be limited to less than 10mA when they are active. The worst-case differential input voltage usually occurs when the input is driven while the output is shorted to ground in a unity-gain configuration. In addition, the amplifier is protected against ESD strikes up to 3kV on all pins by a pair of protection diodes on each pin that are connected to the power supplies as shown in Figure 1.Capacitive LoadThe LT1809/LT1810 is optimized for high bandwidth and low distortion applications. It can drive a capacitive load about 20pF in a unity-gain configuration and more with higher gain. When driving a larger capacitive load, a resistor of 10Ω to 50Ω should be connected between theoutput and the capacitive load to avoid ringing or oscilla-tion. The feedback should still be taken from the output so that the resistor will isolate the capacitive load to ensure stability. Graphs on capacitive loads indicate the transient response of the amplifier when driving capacitive load with a specified series resistor.Feedback ComponentsWhen feedback resistors are used to set up gain, care must be taken to ensure that the pole formed by the feedback resistors and the total capacitance at the inverting input does not degrade stability. For instance, the LT1809 in a noninverting gain of 2, set up with two 1K resistors and a capacitance of 3pF (device plus PC board), will probably ring in transient response. The pole that is formed at 106MHz will reduce phase margin by 34 degrees when the crossover frequency of the amplifier is around 70MHz. A capacitor of 3pF or higher connected across the feedback resistor will eliminate any ringing or oscillation.SHDN PinThe LT1809 has a SHDN pin to reduce the supply current to less than 1.25mA. When the SHDN pin is pulled low, it will generate a signal to power down the device. If the pin is left unconnected, an internal pull-up resistor of 10k will keep the part fully operating as shown in Figure 1. The output will be high impedance during shutdown, and the turn-on and turn-off time is less than 100ns. Because the inputs are protected by a pair of back-to-back diodes, the input signal will feed through to the output during shut-down mode if the amplitude of signal between the inputs is larger than 1.4V.Figure 3. 4096 Point FFT ResponseFREQUENCY (MHz)012341809 F035V S = ±5V A V = +2f SAMPLE = 10Msps f IN = 1.394MHz SFDR = 90dBFigure 7. 4096 Point FFT ResponseFigure 5. 4096 Point FFT ResponseFREQUENCY (MHz)012341809 F055V S = ±5V A V = –1f SAMPLE = 10Msps f IN = 1.394MHz SFDR = 90dBFREQUENCY (MHz)012341809 F075V S = 5V A V = +2f SAMPLE = 10Msps f IN = 1.394MHz SFDR = 80dB2122Information furnished by Linear Technology Corporation is believed to be accurate and reliable. However, no responsibility is assumed for its use. Linear Technology Corporation makes no represen-tation that the interconnection of its circuits as described herein will not infringe on existing patent rights.23241630 McCarthy Blvd., Milpitas, CA 95035-7417(408) 432-1900 q FAX: (408) 434-0507 q © LINEAR TECHNOLOGY CORPORA TION 2000sn180910 180910fs LT/TP 1100 4K • PRINTED IN USA。
1809909资料

Extract from the onlinecatalogMSTBC 2,5/19-STZF-5,08Order No.: 1809909The illustration shows a 15-position versionhttp://eshop.phoenixcontact.de/phoenix/treeViewClick.do?UID=1809909Plug component, nominal current: 12 A, rated voltage: 320 V, pitch:5.08 mm, no. of positions: 19, type of connection: Crimp connectionhttp://Please note that the data givenhere has been taken from theonline catalog. For comprehensiveinformation and data, please referto the user documentation. TheGeneral Terms and Conditions ofUse apply to Internet downloads. Technical dataDimensions / positionsPitch 5.08 mmNumber of positions19Technical dataInsulating material group IRated surge voltage (III/3) 4 kVRated surge voltage (III/2) 4 kVRated surge voltage (II/2) 4 kVRated voltage (III/2)320 VRated voltage (II/2)630 VConnection in acc. with standard EN-VDENominal current I N12 ANominal voltage U N320 VNominal cross section 2.5 mm2Maximum load current12 AInsulating material PAInflammability class acc. to UL 94V0Connection dataConductor cross section stranded min.0.5 mm2Conductor cross section stranded max. 2.5 mm2Conductor cross section AWG/kcmil min.20Conductor cross section AWG/kcmil max14Certificates / ApprovalsApproval logoCSANominal voltage U N300 VNominal current I N10 AAWG/kcmil20-14CULNominal voltage U N300 VNominal current I N10 AAWG/kcmil20-14ULNominal voltage U N300 VNominal current I N10 AAWG/kcmil20-14Certification CB, CSA, CUL, UL, VDE-PZIAccessoriesItem Designation DescriptionMarking0804293SK 5,08/3,8:FORTL.ZAHLEN Marker card, printed horizontally, self-adhesive, 12 identicaldecades marked 1-10, 11-20 etc. up to 91-(99)100, sufficient for120 terminal blocksPlug/Adapter1734634CP-MSTB Coding profile, is inserted into the slot on the plug or invertedheader, red insulating material3190564MSTBC-MT 0,5-1,0Module female contact, is inserted into the plug housing MSTBCafter crimping the conductor, for conductors from 0.5 to 1.0 mm²3190645MSTBC-MT 0,5-1,0 BA Module female contact, is inserted into the MSTBC connectorshell after the conductor has been crimped, for conductors from0.5 - 1.0 mm², ribbon contact3190551MSTBC-MT 1,5-2,5Module female contact, is inserted into the plug housing MSTBCafter crimping the conductor, for conductors from 1.5 to 2.5 mm²3190658MSTBC-MT 1,5-2,5 BA Module female contact, is inserted into the MSTBC connectorshell after the conductor has been crimped, for conductors from1.5 -2.5 mm², ribbon contact1810529STZ 2-MSTBC-5,08Strain relief for snapping into the latching chambers of the plugcomponents, 2-pos., labeling with ZB 61810532STZ 4-MSTBC-5,08Strain relief for snapping into the latching chambers of the plugcomponents, 4-pos., labeling with ZB 61810516STZ 8-MSTBC-5,08Strain relief for snapping into the latching chambers of the plugcomponents, 8-pos., labeling with ZB 61810503STZ 12-MSTBC-5,08Strain relief for snapping into the latching chambers of the plugcomponents, 12-pos., labeling with ZB 6Tools1204038CRIMPFOX MT 2,5Crimping pliers, for crimping conductors to the module femalecontacts STG-MTN, crimp range: 0.5-2.5 mm², AWG: 20-14 1205037SZS 0,4X2,5Screwdriver, bladed, matches all screw terminal blocks up to 1.5mm² connection cross section, blade: 0.4 x 2.5 mm Additional productsItem Designation DescriptionGeneral1803125MSTBVK 2,5/19-GF-5,08Header, nominal current: 12 A, rated voltage: 320 V, pitch: 5.08mm, no. of positions: 19, mounting: Mounting rail1788512MVSTBU 2,5/19-GFB-5,08Header, nominal current: 12 A, rated voltage: 320 V, pitch: 5.08mm, no. of positions: 19, mounting: Direct mounting3002034UK 3-MSTB-5,08Modular terminal blocks with plug entry, cross section: 0.2 - 2.5mm², AWG: 30 - 12, width: 5.1 mm, color: gray3002076UK 3-MVSTB-5,08Modular terminal blocks with plug entry, cross section: 0.2 - 2.5mm², AWG: 26 - 12, width: 5.1 mm, color: gray3002102UK 3-MVSTB-5,08-LA 24RD Modular terminal block with plug entry, nominal current: 12 A,rated voltage: 320 V, pitch: 5.08 mm, no. of positions: 1, mounting:mounting rail, with red light indicator, voltage light indicator: 24 VAC/DC, current light indicator: 3.3 mA3002063UK 3-MVSTB-5,08/EK Modular terminal blocks with plug entry, cross section: 0.2-2.5mm², AWG: 26-12, width: 5.1 mm, color: blue3002131UK 3D-MSTBV-5,08Modular terminal blocks with vertical plug entry, cross section: 0.2- 2.5 mm, AWG: 30 - 12, width: 5.1 mm, color: gray3002144UK 3D-MSTBV-5,08-LA 24RD Modular terminal block with vertical plug entry, color: Gray, withred light indicator, voltage light indicator: 24 V AC/DC, current lightindicator: 3.3 mA3002173UK 3D-MSTBV-5,08/EK Modular terminal blocks with plug entry, cross section: 0.2 - 2.5mm², AWG: 30 - 12, width: 5.1 mm, color: blue2770888UKK 3-MSTB-5,08Modular terminal blocks with 2 horizontal plug entries, crosssection: 0.2 - 2.5 mm, AWG: 30 - 12, width: 5.1 mm, color: gray 1876615UKK 3-MSTB-5,08-PE Ground terminal block, with 2 horizontal plug entries, nominalcurrent: 12 A, rated voltage: 320 V, pitch: 5.08 mm, no. ofpositions: 1, mounting: mounting rail.1788091UMSTBVK 2,5/19-GF-5,08Header, nominal current: 12 A, rated voltage: 320 V, pitch: 5.08mm, no. of positions: 19, mounting: Mounting rail1873016ZFKK 1,5-MSTBV-5,08Modular terminal blocks with plug entry, cross section: 0.2 - 1.5mm², width: 5.1 mm, color: grayDrawingsDimensioned drawingAddressPHOENIX CONTACT GmbH & Co. KGFlachsmarktstr. 832825 Blomberg,GermanyPhone +49 5235 3 00Fax +49 5235 3 41200http://www.phoenixcontact.de© 2008 Phoenix ContactTechnical modifications reserved;。
10-89-4602;中文规格书,Datasheet资料

ENG. NO: A-70216-0391/0404
DIM. C DIM. E (REF.) FINISH CONNECTOR END PLATING DIM. D (MEASURE PT.) P.C. BOARD END PLATING DIM. F (MEASURE PT.) PACKAGING CKTS EDP NUMBER 04 10-89-4046 06 10-89-4066 08 10-89-4086 10 10-89-4106 12 10-89-4126 14 10-89-4146 16 10-89-4166 18 10-89-4186 20 10-89-4206 22 10-89-4226 24 10-89-4246 26 10-89-4266 28 10-89-4286 30 10-89-4306 (6.10)/.240 (2.79)/.110 30 GOLD GOLD (2.54)/.100 TIN (1.27)/.050 SEE NOTE 4 ON SHT. 1 ENG. NUMBER A-70216-0391 A-70216-0392 A-70216-0393 A-70216-0394 A-70216-0395 A-70216-0396 A-70216-0397 A-70216-0398 A-70216-0399 A-70216-0400 A-70216-0401 A-70216-0402 A-70216-0403 A-70216-0404
SHEET No.
-3APPROVED BY:
DOCUMENT NUMBER:
SD-70216-001
/
ADERR
FSMITH
TEMPLATE FILENAME: PRODUCT_SPEC[SIZE_A](V.1).DOC
光的偏振和相关知识
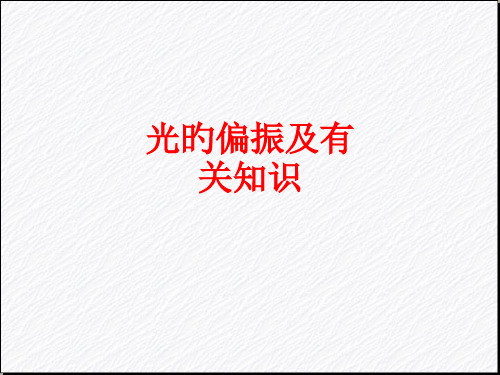
Ip P
I2
由题意,
In 2 I2
I p cos2 I1 / 2
60
即
In 2
In 2
Ip
Ip
4
4
In 2
Ip
/
2
整顿得 In I p 1
偏振度
2023/12/1
Imax In 2 I p
I min
1 2
I
n
3 2
I
n, P
I max I max
Imin Imin
3 2
偏光显微镜 等等
2023/12/1
32
作业:3-5
作业
•3 ~ 5
2023/12/1
33
§3光经过单轴晶体时旳双折射
一. 双折射现象
一束光入射在介质中折射 为两束光(o 光、e 光) 旳现象.
双折射现象
e o
2023/12/1
1. o光(寻常光): 遵照折射定律. 2. e光(非常光): 不遵照折射定律.
e光旳主截面—由e光旳传播方向与光轴构成。
· 主截面
·· o光旳 · 主截面
e光旳 主截面
e光
o光
2023/12/1
光轴
光轴
n2 n1
tgib ? ! = nn12
注意:上表面旳折射角 等于下表面旳入射角
n1 sin ib n2 sin ib ib ib 900
n1 cosi b n2 sin ib
一般玻璃旳反射率只有7.5%左右,要以反 射取得较强旳偏振光,你有什么好主意?
2023/12/1
25
玻璃片堆
要提升反射线偏振光旳强度, 可利用玻璃片堆旳屡次反射。
N9040X18 2;中文规格书,Datasheet资料

Hermetic Environmental Sealing Bootsfor Switches &PotentiometersSWITCH SEALINGSPECIALISTS©APM Hexseal Corp.2009Pushbuttonswitch bootColor MatchingToggle styleswitch Pushbutton switchbootmounted bootsstyle front-of-panel sealing bootsLever style back-of-panelmounted circuit breaker bootsPanel Meter custom cover duty,armored,stainless mushroom head boot Lever style back-of-panel mounted circuit breaker bootWhy hostile switch environment protection is neededUnsealed switches are internally suscep-tible to damage and shorting from water,lubricants,dust,dirt,sand,salt spray,corrosive atmospheres,fungus and other damaging contaminants.Even factory sealed switch function is susceptible to ice and dust build-up.And,all switch panel-mounting cutouts are vulnerable to contaminant seepage including spilled soft drinks,coffee,etc.APM’s UL-recognized HEXSEAL ®and E-SEEL ®sealing boots provide complete and reliable,cost-effective,long-term protection.How HEXSEAL ®&E-SEEL ®Boots protectWorking closely with switch,potentiometer and circuit breaker manufacturers and users for more than 60years,APM has developed an extensive line of tough,pliant silicone rubber (other materials available for specific environments)panel seals that function harmoniously with the switch’s manual and automatic operation and position status viewing.Our panel seals are UL 50tested and Recognized.In this age of recalls and expensive field servicing,installing a HEXSEAL boot is the most effective and least expensive way to protect and guard against switch,circuit breaker and potentiometer failures.Toggle,Pushbutton,Rocker,RotaryActuated Sealing BootsNEMA Mounted Enclosure Example –Switch &Circuit Breaker BootsHEXSEAL ®&E-SEEL ®SEALING BOOTS —LIFE SUPPORT SYSTEMS FOR SWITCHESAll standard EMI/RFI boots feature a knitted Monel shieldTypical Applications•Marine instrument panels•Military equipment and vehicles •Food processing equipment •Air conditioning systems •Heat pumps•Off-road construction equipment •Machine tool controls •Spas/hot tubs•Commercial laundry equipment •Construction elevator controls •Waste treatment system controls •Chemical plant process controls •Paint spraying equipment •Industrial machinery•Medical electronic equipment •Ground support equipment •Electronic/electrical instrument control panels•Emergency power equipment•Outdoor compressor/pump controls •Transport refrigeration systems •Automotive diagnostic equipment •Lighting control centers•Commercial refrigeration systems •Or any application requiring environ-mental protection forswitches.REMOTE HEXSEAL®boots protectswitch,potentiometer &circuit breaker mechanisms from degradation due to harsh environments such as salt air/water,oils,dust and ice.Features &BenefitsRUGGED HEXSEAL®boots are usedfor controls protection in industrial,manu-facturing and processing plants —hostile conditions which are dusty,dirty,greasy and corrosive.EXTREMEHEXSEAL ®boots willprotect switches and keep them functioning to temperatures down to -94°F (-70°C).RELIABLE Surgery rooms and foodprocessing plants require frequent wash downs.Their switches benefit from HEXSEAL ®IP66-68Rated boots by main-taining dry,clean reliableperformance.•Designed and made in USA …to insure high,consistent quality with local full tech service backup.•Exclusive UL-Recognized HEXSEAL ®&E-SEEL ®Boots …facilitate easier “agency approval”of the equipment in which they are used.No other competitive seals in the world have these approvals.•Third party inspection …UL regularly inspects our facili-ties and products.•Military Specifications …most HEXSEAL ®Boots are produced to meet MIL-DTL-5423(see product pages speci-fication charts).•Time Tested …since our original patents and for more than 60years,millions of HEXSEAL ®Boots reliably function in hostile conditions throughout the world.•Transparent RUBRGLAS ®(indicators)rugged silicone rubber material …resists tearing and most hostile environ-mental contaminants.Retains tactile feel,will not discolor,yellow,crack or dry out due to UV/aging.•Choose precise boot color for color matching …to match panel and/or delineate function –identification.•DFARS compliant•RoHS compliant …per document 2002/95/EC•Patented perimeter sealing rib …seals the switch/circuit breaker panel-mounting cutout,preventing contaminant seepage.•Toggle actuated boots feature secondary inner seal …to protect against contaminant entry in the event the upper chamber portion is punctured.And,also protects against differential pressure.(See figure 4.)•All toggle and pushbutton boots feature high-strength rubber-to-metal bond …cross-linking adhesion assures rubber will not separate from the mounting nut.•Pre-lubricated (optional)half-toggle and full-toggle boots …assure easier installation on large diameter actuators.•Custom design requirements welcome …in addition to standard products described in this catalog,APM provides technical design assistance with fast,economical prototyping.Learn how others apply HEXSEAL ®Switch Boots –visit our website “Sealing Solutions”application notes.(Partial list —consult factory for additional listings for these and other manufacturers)Toggle Switchesbe requested where required for proper fit as well.*For metric sizes consult factory.RoHSCompliantToggle Switches(Partial list —consult factory for additional listings for these and other manufacturers)(Continued)SEALED SWITCHESPanel Bushing WasherMeets Military Specifications****APM’s policy is to manufacture our HEXSEAL ®sealing boots as defined by the requirements of MIL-Spec MIL-DTL-5423which we regard as the standard for the switch,circuit breaker and potentiometer industry.These requirements were formulated based on our original patent.DFARS material is standard on all boots.Cage Code:97539Cross ReferenceN.S.N.Series to APM Part NumbersRoHSCompliantAnatomy of a Hermetic Sealing BootFromcomponents.required.Bushing seal for protection of hermetically sealed switchesSealed switches require panel cut-out protection …SNAP-SEALS ®E-SEELS ®HEXSEALS ®GOOD•Commercial Grade ••Neoprene rubber •T wo-piece design•-65°F to +300°F (-53°C to +148°C)temperature range•Suitable for some commercial and consumer applications including low-cost appliances and toolsBETTER•Industrial Grade ••UL-recognized component for US &Canada•High tear-strength silicone rubber (other materials available)•Single-piece construction•-80°F to +400°F (-62°C to +204°C)temperature range•Suitable for industrial and commercial applicationsBEST•Military Grade ••High tear-strength silicone rubber per A-A-59588,Class 3B (other materials available)•Single-piece design•-94°F to +400°F (-70°C to +204°C)temperature range•Suitable for military and industrial applications•UL-recognized component for US &Canada(See page 20)Fig.2Patent No.7,964,812Fig.3BondedCONCENTRO-NUT —fits over switch nutIQ-1030Technical ReferencesSURVIVING HOSTILE CONTROL SYSTEM ENVIRONMENTS There is an IP-rated UL-recognized environmental sealing boot expressly designed for selected control components (e.g.,switches,circuit breakers,potentiometers,panel meters)that mates with and will provide a number of benefits consistent with design considerations that comply with MIL-DTL-5423specifications.Originally designed for itary naval applications—rugged handling(with and without gloves),corrosive atmospheres,lubricant contact,frequent wash-downs—these sealing boots have repeatedly proven their battle-tested worthiness.By supporting all the major manufacturers of switches,potentiometers,and circuit break-ers,the same protection and reliability are available for a wide spectrum of commercial and industrial switches through the APM HEXSEAL®and E-SEEL®sealing boot system.The following reference data and cross reference charts should be helpful in making your selection,however please do not hesitate to contact our sales support depart-ment for assistance.Enclosure RatingsTo cost-effectively satisfy this application diversity,manu-facturers of electrical/electronic equipment enclosures offer a range of products which provide varying degrees of envi-ronmental protection.In the interest of“standardizing”an electrical enclosure’s performance,standards-making organ-izations such as NEMA,UL,CSA,and IEC have established various standards(T able1).Use of NEMA ratings does not require independent testing. Compliance is left to the manufacturer.On the other hand,UL conducts an independent evaluation of the submitted product. Tests are performed either at UL’s laboratories or witnessed by UL engineers at the manufacturer’s location.In addition,UL requires follow-up inspections(which may include testing)to assure adherence to prescribed materials and manufacturing procedures.These ratings provide a quantitative measure of an enclo-sure’s ability to operate in the environment in which it will be used.Each rating defines the degree of protection against rain,snow,sleet,wind-blown dust,hosedown,corrosive agents,and occasional submersion.While the detailed wording of ratings from standard to stan-dard varies,each is based on similar application descriptions and performance expectations(Table2).For example,an enclosure meeting UL Standard50,T ype6ratings(and simi-larly NEMA Standard No.250,T ype6)is designed for indoor and outdoor use.It provides the degree of protection against hosedown,icing,dust,and the entry of water during temporary submersion at the limited depth required for this rating.Toggle SwitchBootsHEXSEAL ®and E-SEEL ®toggle switch boots are molded from a high tear-strength silicone rubber (other materials available for specific environments)bonded to a built-in mounting nut.Each encloses the base of the protruding switch bushing and forms a watertight and dust-tight seal against the front panelsurface.FIGURE1FIGURE 2FIGURE 3DIMENSIONS FOR REFERENCE ONL Y .Current dimensional drawings can be viewed on our website and CAD drawings can also be downloaded.RoHSCompliantFull-Toggle Boot with Integral Secondary Inner Seal –IP66/68RatedFigure 1Half-Toggle Boots (toggle actuator protrudes)–IP66/68RatedFigure 3Full-Toggle Boots (with constant I.D.)–IP66/68RatedFigure 2DTL-5423which we regard as the standard for the switch,circuit breaker and potentiometer industry.These requirements were formulated based on our original patent.分销商库存信息: APM-HEXSEALN9040X1/8 2。
10408;10409;中文规格书,Datasheet资料
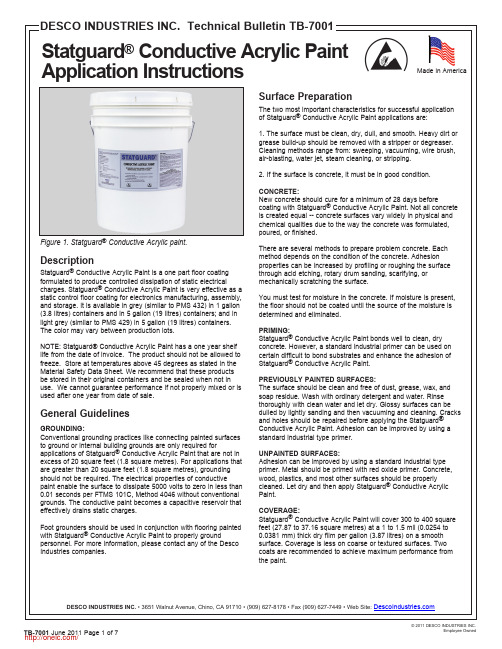
Made in AmericaThe two most important characteristics for successful applicationConductive Acrylic Paint applications are:1. The surface must be clean, dry, dull, and smooth. Heavy dirt or grease build-up should be removed with a stripper or degreaser. Cleaning methods range from: sweeping, vacuuming, wire brush, air-blasting, water jet, steam cleaning, or stripping.2. If the surface is concrete, it must be in good condition.New concrete should cure for a minimum of 28 days beforeConductive Acrylic Paint. Not all concrete is created equal -- concrete surfaces vary widely in physical and chemical qualities due to the way the concrete was formulated,There are several methods to prepare problem concrete. Each method depends on the condition of the concrete. Adhesion properties can be increased by profiling or roughing the surface through acid etching, rotary drum sanding, scarifying, or mechanically scratching the surface.You must test for moisture in the concrete. If moisture is present, the floor should not be coated until the source of the moisture isConductive Acrylic Paint bonds well to clean, dry concrete. However, a standard industrial primer can be used on certain difficult to bond substrates and enhance the adhesion of Conductive Acrylic Paint.PREVIOUSLY PAINTED SURFACES:The surface should be clean and free of dust, grease, wax, and soap residue. Wash with ordinary detergent and water. Rinse thoroughly with clean water and let dry. Glossy surfaces can be dulled by lightly sanding and then vacuuming and cleaning. Cracks and holes should be repaired before applying the Statguard Conductive Acrylic Paint. Adhesion can be improved by using atest area be coated to ensure that the adhesion and electrical of the paint is acceptable. (See Adhesion Testing, Figure 5.) If the 3. Saturate a 1/4” (6.35 mm) fine nap roller or an industrial brush ure must be above 50°F (10°C).Conductive Acrylic Paint is recommended for appropriate static protection.Mix any settled solids to produce a uniform grey color.Saturate a 1/4” fine nap roller with paint, remove excess paint and trapped bine separate cans into a larger A minimum number of strokes from the applicator is recommended.Figure 2. Paint application with roller.Figure 3. Spray paint application Clean UpWash applicators with water immediately after painting. Remove paint spills promptly with a wet cloth. Close container after each use. Keep container from freezing.Drying TimeIt is recommended that Statguard ® Conductive Acrylic Paint be allowed to dry at a temperature in excess of 45°F (7°C) until dry. A minimum of 1 to 2 hours drying time should be allowed before applying the second coat. The finish can be applied after 48-72 hours or until the last coat of paint is cured. Wait a minimum of 12 hours drying time after the last coat before allowing light traffic on the coated area. At high humidity levels, a longer drying time may be necessary. Do not force dry.MaintenanceUse sweeper, vacuum, or broom to remove dirt. Allow two weeks drying time before using a damp mop to clean the coated area. Do not use abrasive cleaners, floor rinse, or scrubbing machine to clean the floor.Finish/SealerDesco Statguard Conductive Acrylic Paint can be overcoated or sealed with Statguard Floor Finish static dissipative coating to increase durability, enhance shine, improve ease of maintenance, and seal out dirt and debris. Desco Statguard ® Conductive Light Grey Acrylic Paint needs the Statguard ® Floor Finish for gloss and ease of maintenance . Statguard ® is a polymer base floor finish/sealer that can be used as a top coat on the Conductive Acrylic Paint. Surface resistivity will then be in the 10E6-10E7 ohms range. Two coats are recommended. Three coats will improve electrical properties, durability and reduce frequency ofLead free, iron oxide, titanium dioxide and extenders 10.27 lbs per gallon (1.0 kilograms per Use a razor to cut into a painted, dried floor.3.Pull the tape off.Apply tape on the precut area.4.Examine the degree of paint separationfrom the concrete.Figure 5. Adhesion test on the painted floor.10E5 ohms/sq. per ASTM D257Static Charge Decay:<0.01 sec. per FTMS 101B, Method 4046Charge Generation:Zero per AATCC Step Test, Method 134-1979RTT:10E5 ohms per ANSI ESD-S7.1RTG:10E5 ohms per ANSI ESD-S7.1TestingTest patch areas should be tested for adhesion and electricalperformance of the paint before applying paint to the entire floor. To best ensure consistent results, the test should be done at various locations.ELECTRICAL PROPERTIES:Test the surface resistivity, point-to-point resistance, and resistance-to-ground properties of coated area per ANSI ESD-S7.1 test method. For quick and easy verification of the paint’s electrical properties, we recommend the use of our a Surface Resistance Test Kit (Figure 4). For more information contact any of the Desco Industries Inc. companies.ADHESION:Allow newly applied paint to dry a minimum of 48 hours before proceeding with the test. At humidity levels over 55% RH, allow 72 hours of drying time before testing. Use a razor to cut a cross or a few perpendicular lines over a 3” by 3” (75 mm by 75 mm) area on several spots of the thoroughly dried area. Use a piece of masking tape to cover the marked area. Make sure the tape is thoroughly adhered to the test area. Pull the tape off the surface and examine the amount of paint which has peeled off during the test. If any significant portion is transferred to the tape, better surface preparation (acid etching, cleaning or sanding) should be done on the substrate to enhance the adhesion.8. EXPOSURE CONTROL/PERSONAL EXPOSUREControl Parameters TLV-value 50 ppm maximum for n-butanol and 25 ppm for Ethylene GlycolMonobutyl EtherOther Regulations NoneMeasures For Technical Control Preferences of technical measure to prevent or control contact with the product.Isolating process and personnel, mechanical ventilation (dilution and localexhaust) and the regulation of process conditions. In case of non-prevention or non-control, a proper protective wearing should be used. Respiratory Protection Not required. Wear MSHA/NIOSH approved respirator where exposure limits areexceeded.Hand Protection Impervious/Neoprene GlovesEye Protection Chemical Splash Goggles (ANSI Z-87.1)Work/Hygienic Practices Wash hands before eating, smoking, or using washroom facilities9. PHYSICAL AND CHEMICAL PROPERTIESForm FluidColor Grey, OpaqueSmell MildpH 8.5Boiling Point at °C >100-101°C (212-214°F)Freezing Point at °C 0.0°C (32.0 °F)Flash Point at °C 65 °CExplosive Limits LEL: 0.8 UEL: 25.0Inflammability Limits N/A(vol.% in air)Solubility in water CompleteVOC per method 24 of EPA 2.3 -2.5 lbs VOC/ galVapor Pressure (mmHg) 92.43 mm @ 20 °CVapor Density (air=1) Heavier than airDensity at 20°C 8.17 lbs./gal or 1.14 g/cm3Specific Gravity (H20=1) 1.21Inflammability Classification according to OSHA and EC-regulations “non-flammable”Ignition Temperature 240.0 °CEvaporation Rate Slower than n-butyl acetate% Volatile by Volume 13.229%10. STABILITY AND REACTIVITYStability/Reactivity Stable product at normal conditionsConditions to avoid Temperatures above 49°C/120°F and below 1°C/34°F, Open flames and sparks. Materials to avoid Strong Oxidizing agents and alkalies.Hazardous Decomposition Oxides of carbon and nitrogen. If involved in fire (from other sources) could conceivably result in release of Carbon Dioxide and Carbon Monoxide fumes.11. TOXICOLOGICAL INFORMATIONIngredient-Material Description PEL TLV (twa) LD50 (mg/kg) LC50 (ppm)mg/m3 ppm (rat) (rbt) (rat)oral dermal inhalEthylene Glycol Monobutyl Ether * 50.0 0.0 25.0 470.0 220.0 0.0Butanol* 50.0 0.0 50.0 0.0 0.0 0.0Mineral Spirits 100.00 0.0 100.0 0.0 0.0 0.02-(2-Butoxyethoxy)ethanol 0.0 0.0 0.0 6560.0 4120.0 0.02-ethyl-1-Hexanol 0.0 0.0 0.0 3730 1970 0.0Ammonium Hydroxide 0.0 35.0 50.0 350.0 0.0 0.0*Listed Chemical Subject To Reporting Requirement of SARA Section 313 of Title III• Acute toxicity• Primary irritant effect:• On the skin: No irritant effect• On the eye: No irritant effect• Sensatization: No sensitizing effects known• Additional toxicological information:The product in not classified according to the calculation method of the General EU Classification guideline for Preparations as issued in the latest version. When used and handled according to specifications, the product does not have any harmful effects to our experience and the information provided to us.12. ECOLOGICAL INFORMATIONGeneral Notes:Water hazard class 1 (German Regulations) (self-assessment): slightly hazardous for water. Do not allow undiluted product or large quantities of it to reach ground water, water course or sewage system.Mobility The product is aqueous and will be separated in aqueous conditions Degradability N/ABioaccumulation Not likelyEcotoxicity None knownReference to BimSchV N/A13. DISPOSAL CONSIDERATIONSProduct Dike and collect material into plastic container. Water rinse and drain, flush smallamounts. Use sanitary landfill d isposal. Follow state and local regulations(RCRA; Subtitle D).Hazardous Waste Number Nonregulated14. TRANSPORT INFORMATIONThis product is not classified for transport under ADR/IMDG regulations.15. REGULATORY INFORMATIONLabeling according To EU guideline: Observe the general safety regulations when handeling chemicals. The product is not subject to identification regulations under EU Directives and the Ordinance on Hazardous Materials (Genman GefStoffV).National Regualtions:Waterhazard class: Water hazard class 1 (Self-assessment): slightly hazard for waterPhysical/Chemical Indication Non-flammableSafety Phrase (S2): keep away from children, (S7): keep containers well closed, (S24/25): avoidcontact with skin and eyes, (S45): in case of accident or if you feel unwell, seekmedical advice immediately, show label where possible, (S53): avoid exposureobtain special instruction before use, (S62): if swallowed, do not induce vomiting;seek medical advice immediately and show this container or label.EU Classification This product does not have to be classified according to the EU Regulations.(67/548/EEC-88/379/EEC)EINECS Status All components are included in the EINECS Inventories except cas #104-76-7 TSCA All ingredients of this product are listed or are excluded from the listing on the U.S. Toxic Substance Control Act (TSCA) Chemical Substance inventory.16. OTHER INFORMATIONFurther Information None KnownDisclaimerThe information given in this publication has been worked up to the best of the knowledge of Desco Industries Inc, as well as taking into consideration the applicable laws and regulations. We cannot anticipate all conditions under which this information and our products or the products of the manufacturers in combination with our products may be used. We accept no responsibility for the results obtained by the application information or the safety and suitability of our product or product combination with other products. Users are advised to make their own tests to determine the safety and suitability of each such product or product combination for their own purposes. Unless otherwise agreed in writing, we sell the products without warranty, and buyers end users assume responsibility and liability for loss or damage arising from the handling and use of our products, whether used alone or in combination with other products.分销商库存信息:DESCO1040810409。
AS8510 DB;中文规格书,Datasheet资料
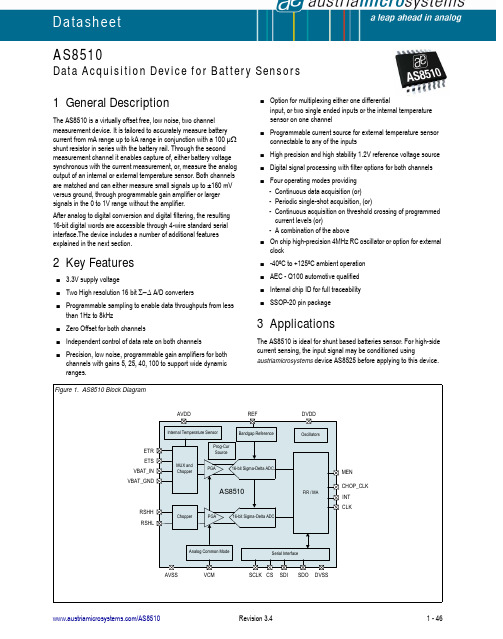
AS8510Data Acquisition Device for Battery SensorsDatasheet1 General DescriptionThe AS8510 is a virtually offset free, low noise, two channel measurement device. It is tailored to accurately measure battery current from mA range up to kA range in conjunction with a 100 µΩ shunt resistor in series with the battery rail. Through the second measurement channel it enables capture of, either battery voltage synchronous with the current measurement, or, measure the analog output of an internal or external temperature sensor. Both channels are matched and can either measure small signals up to ±160 mV versus ground, through programmable gain amplifier or larger signals in the 0 to 1V range without the amplifier.After analog to digital conversion and digital filtering, the resulting 16-bit digital words are accessible through 4-wire standard serial interface.The device includes a number of additional features explained in the next section.2 Key Features3.3V supply voltageTwo High resolution 16 bit Σ−Δ A/D convertersProgrammable sampling to enable data throughputs from lessthan 1Hz to 8kHzZero Offset for both channelsIndependent control of data rate on both channels Precision, low noise, programmable gain amplifiers for bothchannels with gains 5, 25, 40, 100 to support wide dynamic ranges.Option for multiplexing either one differentialinput, or two single ended inputs or the internal temperature sensor on one channelProgrammable current source for external temperature sensorconnectable to any of the inputsHigh precision and high stability 1.2V reference voltage source Digital signal processing with filter options for both channels Four operating modes providing-Continuous data acquisition (or)-Periodic single-shot acquisition, (or)-Continuous acquisition on threshold crossing of programmed current levels (or)-A combination of the aboveOn chip high-precision 4MHz RC oscillator or option for external clock-40ºC to +125ºC ambient operation AEC - Q100 automotive qualified Internal chip ID for full traceability SSOP-20 pin package3 ApplicationsThe AS8510 is ideal for shunt based batteries sensor. For high-side current sensing, the input signal may be conditioned usingaustriamicrosystems device AS8525 before applying to this device.Contents1 General Description (1)2 Key Features (1)3 Applications (1)4 Pin Assignments (4)4.1 Pin Descriptions (4)5 Absolute Maximum Ratings (6)6 Electrical Characteristics (7)6.1 Operating Conditions (7)6.2 DC/AC Characteristics for Digital Inputs and Outputs (7)6.3 Detailed System and Block Specifications (8)6.3.1 Electrical System Specifications (8)6.4 Current Measurement Ranges (across 100µΩ shunt resistor) (9)6.4.1 Differential Input Amplifier for Current Channel (10)6.4.2 Differential Input Amplifier for Voltage Channel (11)6.4.3 Sigma Delta Analog to Digital Converter (12)6.4.4 Bandgap Reference Voltage (12)6.4.5 Internal (Programmable) Current Source for External Temperature Measurement (13)6.4.6 CMREF Circuit (VCM) (14)6.4.7 Internal AVDD Power-on Reset (14)6.4.8 Internal DVDD Power-on Reset (14)6.4.9 Low Speed Oscillator (14)6.4.10 High Speed Oscillator (15)6.4.11 External Clock (15)6.4.12 Internal Temperature Sensor (15)6.5 System Specifications (16)7 Detailed Description (17)7.1 Current Measurement Channel (17)7.2 Voltage/Temperature Measurement Channel (17)7.3 Digital Implementation of Measurement Path (18)7.4 Modes of Operation (18)7.4.1 Normal Mode 1 (NOM1) (19)7.4.2 Normal Mode 2 (NOM2) (20)7.4.3 Standby Mode1 (SBM1) (21)7.4.4 Standby Mode2 (SBM2) (21)7.5 Reference-Voltage (22)7.6 Oscillators (22)7.7 Power-On Reset (22)7.8 4-Wire Serial Port Interface (22)7.8.1 SPI Frame (23)7.8.2 Write Command (23)7.8.3 Read Command (24)7.8.4 Timing (25)7.8.5 SPI Interface Timing (26)7.9 Control Register (27)7.9.1 Standby Mode - Power Consumption (38)7.9.2 Initialization Sequence at Power ON (38)7.9.3 Soft-reset Using Bit D[7] of Reset Register 0x09 (39)7.9.4 Reconfiguring Gain Setting of PGA (40)7.9.5 Configuring the Device During Normal Mode (40)7.10 Low Side Current Measurement Application (41)8 Package Drawings and Markings (42)8.1 Recommended PCB Footprint (43)9 Ordering Information (45)4 Pin AssignmentsFigure 2. Pin Assignments (Top View)4.1 Pin DescriptionsTable 1. Pin DescriptionsPin NumberPin Name Pin Type Description1RSHH Analog inputPositive Differential input for current channel 2RSHL Negative differential input for current channel3REFAnalog outputInternal reference voltage to sigma-delta ADC; connect 100nF to AVSS from this pin.4VCM Common Mode voltage to the internal measurement path; connect 100nF to AVSS from this pin.5AVDD Supply pad +3.3V Analog Power-supply 6AVSS 0V Power-supply analog 7ETR Analog input Voltage channel single ended input 8ETS 9VBAT_IN Battery voltage (high) input 10VBAT_GNDBattery voltage (low) input11CS Digital input with pull-up Chip select with an internal pull-up resistor (SPI Interface)12SCLK Digital input Clock signal (SPI Interface)13SDODigital outputSerial Data Input (SPI Interface)14DVSS Supply pad0V Digital Ground 15DVDD+3.3V Digital Supply16CHOP_CLKDigital outputChop Clock used in High side measurements to synchronize external chopper.(As an example, when AS8525 is used to condition the input signal to the input range of AS8510, the chop clock is used by AS8525.)17MENDigital output issued during the Standby Mode (SBM) to signal the short duration of data sampling. This signal is useful in the case of a High Side Measurement application.(For example: This signal is used by AS8525 device to wake-up and enable the measurement path.)18SDI Digital input Data signal (SPI Interface)19CLK Digital I/OBy default this pin is the internal clock output which can be used by a Microcontroller. The internal clock may also be disabled as an output by programming Register 08. To use an external Clock, Register 08 has to be programmed. 20INTDigital outputActive High Interrupt to indicate data is readyTable 1. Pin DescriptionsPin NumberPin Name Pin Type DescriptionDatasheet - A b s o lu t e M a x im u m R a ti n g s5 Absolute Maximum RatingsStresses beyond those listed in Table 2 may cause permanent damage to the device. These are stress ratings only. Functional operation of the device at these or any other conditions beyond those indicated in Electrical Characteristics on page 7 is not implied. Exposure to absolute maximum rating conditions for extended periods may affect device reliability.Table 2. Absolute Maximum RatingsParameter Min Max Units NotesElectrical ParametersDC supply voltage (AVDD and DVDD)-0.35VInput voltage (V IN)-0.3AVDD + 0.3DVDD + 0.3VInput current (latchup immunity)(I SCR)-100100mA AEC - Q100 - 004 Electrostatic DischargeElectrostatic discharge (ESD) all pins±2kV AEC - Q100 - 002 Continuous Power DissipationTotal power dissipation(all supplies and outputs) (P t)50mW SSOP20 in still air, soldered on JEDEC standard board @ 125º ambient, static operation with no time limitTemperature Ranges and Storage ConditionsStorage temperature (T STRG)-50125ºCJunction temperature (T J)130ºCThermal resistance (R thJC)80K/W JEDEC standard test board, 0 air velocityPackage body temperature (T BODY)260ºCNorm: IPC/JEDEC J-STD-020The reflow peak soldering temperature (body temperature) is specified according IPC/ JEDEC J-STD-020 “Moisture/Reflow Sensitivity Classification for Nonhermetic Solid StateSurface Mount Devices”.The lead finish for Pb-free leaded packages ismatte tin (100% Sn).Humidity non-condensing585%6 Electrical Characteristics6.1 Operating Conditions6.2 DC/AC Characteristics for Digital Inputs and OutputsAll pull-up and pull-down have been implemented with active devices. SDO has been measured with 10pF load.Table 3. Operating Conditions Symbol ParameterConditions Min Max Units AVDD Positive analog supply voltage3.0 3.6V AVSS 0V Ground00V A - D Difference in analog and digital supplies0.1V DVDD Positive digital supply 2.97 3.63V DVSS 0V Digital Ground 00V T AMB Ambient temperature -40125ºC I SUPP Supply current 5.5mA f CLKSystem clock frequency11.Nominal clock frequency from external or internal oscillator.4.096MHzTable 4. INTSymbol Parameter ConditionsMin TypMax Units I LEAK Tri-state leakage current -1+1µA V OH High level output voltage 2.5V V OL Low level output voltage0.4V I OOutput Current4mATable 5. CS InputSymbol Parameter ConditionsMin TypMaxUnits V IH High level input voltage 2.0V V IL Low level input voltage 0.8V I LEAK Input leakage current -1+1µA Ipu Pull up currentCS pulled to DV DD = 3.3V-150-15µATable 6. SDISymbol Parameter ConditionsMin TypMaxUnits V IH High level input voltage 2.0V V IL Low level input voltage 0.8V I LEAKInput leakage current-1+1µATable 7. SDO OutputSymbol Parameter Conditions Min Typ Max Units V OH High level output voltage Isource = 8mA 2.5V V OL Low level output voltage Isink = 8mA 0.4VI o Output Current8mA Table 8. CHOP_CLK OutputSymbol Parameter Conditions Min Typ Max Units V OH High level output voltage 2.5V V OL Low level output voltage0.4VI o Output Current4mA Table 9. CLK I/O with Input Schmitt Trigger and Output BufferSymbol Parameter Conditions Min Typ Max Units V IH High level input voltage DV DD = 3.3V 2.4V V IL Low level input voltage DV DD = 3.3V 1.0VI LEAK Input leakage current-1+1µAI PD Pull down current CLK pulled to DVSS10100µAI o Output Current4mAV OH High level output voltage 2.5V V OL Low level output voltage0.4V Table 10. SCLK with Input Schmitt TriggerSymbol Parameter Conditions Min Typ Max Units V IH High level input voltage DV DD = 3.3V 2.4V V IL Low level input voltage DV DD = 3.3V 1.0VI LEAK Input leakage current-1+1µA Table 11. MEN OutputSymbol Parameter Conditions Min Typ Max Units V OH High level output voltage 2.5V V OL Low level output voltage0.4VI O Output Current2mA6.3 Detailed System and Block Specifications6.3.1 Electrical System Specifications6.4 Current Measurement Ranges (across 100µΩ shunt resistor)Note:The Data Rate at the output can be calculated according to the formula:fsout=2*fchop /R2 (R2 is down sampling ratio taking values 1, 2, 4 up to 32768 as powers of 2)Table 12. Electrical System SpecificationsSymbol ParameterMinTyp Max Units NotesIDD NOM Current consumption normal mode 3 5.5mA IDD SBMCurrent consumption standby mode40µAAverage of NORMAL Mode Power consumption over a period of 10sec when the device is in STANDBY ModeTable 13. Current Measurement RangesSymbol ParameterImax [A]Vsh [mV]PGA Gain Nominal Data Rate (f OUT )V INADC 1[mV]1.V INADC = Vsh * Gain, gain deviations to be considered according to Table 15 and Table 16.PSR 2[dB]2.AVDD, DVDD of 3.3V with ±5% variation.I10 Input current range of 10A in NOM ±10±1100@ 1 kHz ±10060I200Input current range of 200A in NOM ±200±2040@ 1 kHz ±80060I400Input current range of 400A in NOM ±400±4025@ 1 kHz ±100060I1500Input current range of 1500A in NOM ±1500±1505@ 1 kHz ±75060I1Input current range of 1A in SBM33.For low power current monitoring, single shot measurement is performed with internal oscillator.±1±0.1100@ 1 Hz ±1060I10Input current range of 10A in SBM3±10±1100@ 1 Hz ±10060I200Input current range of 200A in SBM3±200±2040@ 1 Hz±80060Table 14. Valid Combinations of the Chopper Clock, Oversampling Clock and Decimation RatiosOver Sampling FrequencyChopper FrequencyDecimation Ratio1MHz 2kHz 642MHz 2kHz 642MHz 2kHz 1282MHz4kHz646.4.1 Differential Input Amplifier for Current ChannelNotes:1. Leakage test accuracy is limited by tester resource accuracy and tester hardware.2. For gain 100 PGA input common mode is 0V and the minimum supply is3.15V.3. The measurement ranges are referred only by the gain of input amplifier, while other parameters such as bandwidth etc. are pro-grammed independently.4. This parameter is not measured directly in production. It is measured indirectly via gain measurements of the whole path. It is guaran-teed by design.5. Pole frequency of input amplifier changes with GAIN. The number is valid for the gain at G1, while the bandwidth will be higher for other ranges. This parameter is not measured in production.6. Based on device evaluation. Not tested.7. These offsets are cancelled if chopping enabled (default).8. Noise density calculated by taking system bandwidth as 150Hz.9. Refer to Measurement Ranges shown in Table 13.10. No impact on the measurement path. If the chopping is enabled, both the offset and offset drift will be eliminated.11. For negative input voltages up to -160mV below ground, Input leakage is typically -20nA @ 65ºC due to forward conductance of protection diode.Table 15. Differential Input Amplifier for Current ChannelSymbol Parameter Conditions Min Typ Max Units V IN _AMP Input voltage range RSHH and RSHL-160+160mV I IN _AMP Input current1, 11RSHH and RSHL@ +160mV input voltage at 125ºC with PGA-50250nA ICM Absolute input voltage range2-160+300mVG = G1Gain1 3, 4, 9I10100G = G2Gain2 3, 4, 9I20040G = G3Gain3 3, 4, 9I40025G = G4Gain43, 4, 9I15005e Gain deviation i = 1, 2, 3, 40.9 * Gi 1.1 * Gif P _AMP Pole frequency4, 515kHzεT1Gain drift with temperature 6-20ºC to +65ºCGain 5, 25, referenced to roomtemperature±0.3%V OSDRIFT Offset drift with temperature 7, 10350µVVos Input referred offset7, 10After trim,for temperature range -20 to +65ºC350µV Vos_ch Chopping enabled0LSB VNdin Noise density4, 825nV/√Hz THD Total harmonic distortion For 150 Hz input signal 70dB分销商库存信息: AMSAS8510 DB。