新型错齿内排屑深孔钻的结构特点和钻削性能
第十五届“振兴杯”全国青年职业技能竞赛车工赛项理论试题参考题库

第十五届“振兴杯”全国青年职业技能竞赛车工赛项理论试题参考题库一、单项选择题(以下各小题有A、B、C、D四个选项,其中只有一个选项最符合题目要求,本题共600个小题)1.刀具的急剧磨损阶段较正常磨损阶段的磨损速度( )。
A.一样B.慢C.快D.以上均可能2.深孔加工刀具与短孔加工刀具不同的是,( )带有导向垫,有利于保证孔的直线度。
A.前、后B.前C.后D.中间3.使用内径百分表可以测量深孔件的( )精度。
A.同轴度B.直线度C.圆柱度D.以上均可4.刃磨后的刀具从开始切削一直到达到( )为止的总切削时间,称为刀具寿命。
A.刀具崩刃B.磨钝标准C.急剧磨损阶段D.刀具报废5.精车尾座套筒外圆时,可采用( )装夹的方法。
A.四爪单动卡盘B.一夹一搭C.两顶尖D.三爪自定心卡盘6.车削尾座套筒的莫氏圆锥孔时,要求着色( )以上且要求( )端着色。
A.70%,大B.60%,大C.50%,大D.70%,小7.交错齿内排屑深孔钻的特点是刀片在刀具中心两侧( ),这样不仅有较好的分屑作用,还能使刀具两侧受力较平衡。
A.交错排列B.依次排列C.整齐排列D.对称排列8.深孔加工时刀杆受孔径的限制,一般是又细又长,刚性差,车削时容易引起( )现象。
A.振动和扎刀B.振动和让刀C.退刀和扎刀D.退刀和让刀9.车削轴类零件时,如果( )不均匀,工件会产生圆度误差。
A.切削速度B.进给量C.顶尖力量D.毛坯余量10.千分尺读数时( )。
A.不能取下B.必须取下C.最好不取下D.先取下,再锁紧,然后读数11.车削外圆时,( )是垂直于进给方向,待加工表面与已加工表面间的距离。
A.切削速度B.进给量C.切削距离D.背吃刀量12.粗车尾座套筒外圆后,应进行( )热处理。
A.正火B.退火C.淬火D.回火13.精车尾座套筒内孔时,可采用搭中心架装夹的方法。
精车后,靠近卡盘的内孔( ),这是因为中心架偏向操作者方向造成的。
A.粗糙度差B.直径大C.圆度超差D.直径小14.不属于刀具几何参数的是( )。
内排屑深孔钻削机床运动系统设计

西京学院本科毕业设计(论文) 题目:内排屑深孔钻削机床运动系统设计教学单位:机电工程系专业:机械设计制造及其自动化学号: ***********名:***指导教师:***2012年 3月摘要针对传统浇注式内排屑深孔钻削系统(BTA系统或DF系统)存在着切削液消耗量大、生产成本高、污染环境及危害操作者身体健康等问题。
本文是在传统的BTA内排屑深孔钻削系统基础上,增加喷雾装置,建立了亚于式内排屑深孔钻削系统。
亚干式深孔钻削系统是将亚干式切削技术与深孔加工技术相结合,在BTA 内排屑深孔加工系统的基础上,采用风冷雾化排屑系统代替BTA系统中的切削液排屑系统而形成的。
从而实现风冷雾化切削液对刀具进行冷却润滑和排屑的功能,以减少切削液的使用及环境污染。
本次设计以亚干式内排屑深孔钻削系统为研究对象,主要设计内容有低温冷风雾化装置的设计、授油器设计以及负压抽屑装置的设计。
亚干式深孔钻削系统有以下优点:系统加工过程稳定,冷却、润滑、排屑效果良好,可获得较好的刀具耐用度和内孔表面质量,同时极大地减少了切削液的用量并降低环境污染,是一种较为理想的绿色钻削工艺系。
该设计可以节约能源、降低生产成本、减少环境污染,具有良好的经济效益和社会效益。
关键词:内排屑深孔钻削亚干式切削雾化装置授油器负压抽屑ABSTRACTThe traditional cast-type method of inner-chip removal deep hole drilling system (such as BTA system or DF system) has the problems of the high cutting fluid consumption,high production costs,pollution of the environment and endangering the health of the operator and so on. In this paper,in traditional BTA escape of chips deep drilling process system foundation,increases the atomizing device,has established near-dry type deep hole drilling system. The near-dry deep hole drilling system is that the use of compressed air atomized cutting fluid cooling and lubrication cutters in the deep hole processing with combined near-dry cutting technology and deep hole processing technology,based on the BTA inner-chips deep hole processing system,by using the air-cooled liquid escape of chips system instead of the BTA escape of chips system. Finally the air-cooled liquid with cooling and lubricating function for the cutting tool is achieved,and reduce the use of cutting fluid and environmental pollution.The near-dry deep hole drilling system was taken as object in this study,the design of the main contents of the low temperature cold wind atomization device design,coolant supply device design and suction chip removal device design. The result show that the near-dry system drill stability and have better effort in cooling lubrication,chip removal effective. The tool life and surface quality within the hole are better,at the same time,it can greatly reducing the amount of cutting fluid,the costs and the pollution of the environment. So we can get a conclusion that it is an ideal system in green drilling process.The results of research can save energy,lower production costs,reduce environmental pollution,and have good economic and social benefits.Key word:The inner-chip removal deep hole drilling,The near-dry cutting,Atomization device,Coolant supply,Suction chip removal目录摘要 (I)ABSTRACT .......................................................................................................................................... I I 1绪论 (1)1.1深孔加工的特点 (2)1.2内排屑深孔钻削加工系统的发展状况 (2)1.2.1国内相关研究发展状况 (2)1.2.2国外相关研究发展状况 (3)1.3本毕业设计的主要内容 (4)2系统总体方案的布局与设计 (5)2.1总体方案的设计 (5)2.2可行性分析 (6)3低温冷风雾化装置的设计 (9)3.1低温冷风雾化装置的组成及工作原理 (9)3.2雾化装置的组成及零件设计 (11)3.2.1空气供给装置及冷却装置 (11)3.2.2雾化器的设计 (11)3.3冷却液的选择 (13)4授油器的设计 (15)4.1不旋转式授油器结构及其原理 (15)4.2伸缩轴的设计 (16)4.2.1加工材料的选择 (16)4.2.2伸缩轴的结构设计 (17)5负压抽屑装置的设计 (19)5.1DF系统负压抽屑机理 (19)5.2旋转式负压式钻杆联结器 (20)5.3DF深孔钻削中影响抽屑的因素 (21)5.4负压系统的参数计算 (22)5.5负压衬套和前后锥套的设计 (25)6运动控制系统的设计 (28)6.1深孔钻床运动系统的控制要求 (28)6.2运动控制系统的硬件设计 (28)6.3运动控制系统的软件设计 (31)7亚干式深孔钻削系统参数的分析计算 (32)7.1亚干式深孔加工切削参数计算 (32)7.1.1切削力的计算 (32)7.1.2深孔钻头各处速度的计算 (34)7.2剪切面平均温度的计算 (35)8结论 (38)致谢 (39)参考文献 (40)1绪论近年来,随着机械制造行业的不断发展,机械制造业对全球经济的发展做出重大的贡献,但是也在一定程度上对环境造成了污染。
教材习题参考答案(部分)

教材习题参考答案(部分)思考与练习题参考答案(部分)1-1 什么是⽣产过程、⼯艺过程、机械制造⼯艺过程?答:⽣产过程是根据设计信息将原材料和半成品转变为产品的过程。
⼯艺过程是在⽣产过程中,⽑坯的制造成形(如铸造、锻压、焊接等),零件的机械加⼯、热处理、表⾯处理,部件和产品的装配等是直接改变⽑坯的形状、尺⼨、相对位置和性能的过程,称为机械制造⼯艺过程,简称⼯艺过程。
采⽤合理有序安排的各种加⼯⽅法,逐步地改变⽑坯的形状、尺⼨和表⾯质量,使其成为合格零件的过程,称为机械加⼯⼯艺过程。
1-2 什么是⼯序、安装、⼯位、⼯步和⾛⼑?答:⼯序是指由⼀个⼈(或⼀组)⼯⼈在⼀个⼯作地点对⼀个(或同时对⼏个)⼯件连续完成的那⼀部分⼯艺过程;安装——⼯件(或装配单元)经⼀次装夹后所完成的那⼀部分⼯序。
⼯位——在⼀次⼯件的安装中,通过⼯作台的分度、移位可以使⼯件相对于机床变换加⼯位置,⼯件在每⼀个加⼯位置上所能完成的加⼯内容。
⼯步——在同⼀⼯位上,要完成不同的表⾯加⼯时,其中加⼯表⾯、⼑具、切削速度和进给量不变的情况下所完成的⼯位内容。
⾛⼑——⼑具在加⼯表⾯上切削⼀次所完成的⼯步内容。
1-3 什么是⽣产纲领、⽣产类型?答:企业根据市场需求和⾃⾝和⽣产能⼒决定的、在⼀年内应当⽣产的产品的产量和进度计划称为⽣产纲领。
企业(或车间、⼯段、班组,⼯作地)⽣产专业化程度的分类。
⼀般分为⼤量⽣产,成批⽣产和单件⽣产三种类型。
1-4 简述各种⽣产组织类型的特点。
答:单件⼩批⽣产时,其⽣产组织的特点是要能适应产品品种的灵活多变;中批⽣产时,采⽤通⽤设备与专⽤设备相结合,以保证其⽣产组织满⾜⼀定的灵活性和⽣产率的要求;⼤批⼤量⽣产时,⼴泛采⽤⾃动化专⽤设备,按⼯艺顺序流⽔线⽅式组织⽣产,⽣产组织形式的灵活性(即柔性)差。
1-5 简述机械制造过程的基本组成。
答:⾸先,组成机器的每⼀个零件要经过相应的⼯艺过程由⽑坯转变成为合格零件;其次,要根据机器的结构与技术要求,把某些零件装配成部件;最后,在⼀个基准零部件上,把各个零件、部件装配成完整的机器。
一种改进的内排屑深孔钻头

(4)除 外 齿 与 外 缘 一 侧 为 尖 角 外 , 其 余 刀
5
中间尖齿
15°
146°
中心齿
减震块
5°
5°
6°
外刀齿
图 3 改进的深孔钻头 凿 岩 机 械 气 动 工 具 ,2009(1)
齿都进行了倒角, 同时带有 6°~12°的侧后角, 消除了尖角,增大了刀齿的散热体积,同时也 增强了刀齿强度,不易崩刃,有利于提高钻头 的耐用度。
21
明,f =140°~146°之间时, 切屑流出方向近似与 钻头轴线平行,有利排屑。
钻头上也有两个硬质合金导向、 支承块。 几何参数是:
2准=145±5°,Kr1≈73°,Kr2=112°,e= 0.1d, α0 =8° ~12° ,λt2 =5° ~8° ,bα1 =1 ~1.5mm,br1 = 1.2 ~2mm,h =0.4 ~0.5mm,R =1 ±0.1mm,τ =2° ~ 6°,外刃中间齿突前量为(1~2)f。
刃上方与之成 90°的位置(见图 3)。在正常切削
时,切削合力指向两导向块之间,使导向块紧
贴己加工孔壁,起导向作用,而减 振块位于后
端, 刃齿有倒锥使与己加工孔壁有一定的间
隙,不起作用;当钻削力失去平衡发生振动,产
生偏离导向块方向的位移时, 减振块才起作
用,可以减振、消振,保护刀刃和提高加工孔的
形状精度。
(2)改中间齿为尖齿。 为了提高钻削稳定
凿 岩 机 械 气 动 工 具 ,2009(1)
性,我们将中间齿设计为尖齿(见图 1)。 切削
时,中间齿在孔底形成环形凸筋,与内折线刃
在孔底形成的反锥(见图 2)同时起到定心、稳
定钻削的作用。
(3)增加减振块。 普通深孔钻大都采用两
潜孔钻机产品特点
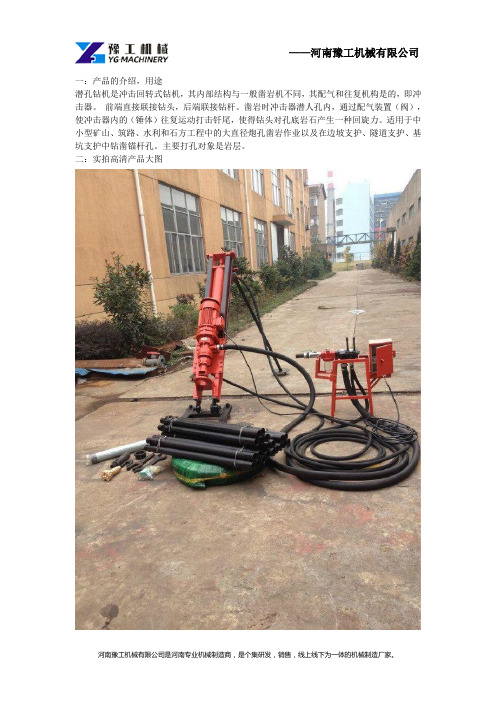
一:产品的介绍,用途潜孔钻机是冲击回转式钻机,其内部结构与一般凿岩机不同,其配气和往复机构是的,即冲击器。
前端直接联接钻头,后端联接钻杆。
凿岩时冲击器潜人孔内,通过配气装置(阀),使冲击器内的(锤体)往复运动打击钎尾,使得钻头对孔底岩石产生一种回旋力。
适用于中小型矿山、筑路、水利和石方工程中的大直径炮孔凿岩作业以及在边坡支护、隧道支护、基坑支护中钻凿锚杆孔。
主要打孔对象是岩层。
二:实拍高清产品大图三:产品结构组成,工作原理潜孔钻机由支承机构、减速器、电动机、推进机构、钻凿系统、油雾器及气动控制阀、电控开关等部分组成。
工作原理是:该钻机是一种复合动力的机型,动力有电机与压缩空气。
钻机钻具旋转的动力来自电动机,冲击器的冲击力来自压缩空气。
电动机工作时将电能转换成旋转扭矩传给减速器,使连接在减速器输出轴上的钻杆旋转,冲击器前端的合金齿不断冲击破碎岩石,破碎的岩石被从钻头排气孔中排出的气压吹至地面。
推进气缸产生的轴向力送进钻具进行钻孔。
四:实拍高清产品大图五:产品特点(对比优势)体积小,重量轻,适合于大、中型钻机无法进行作业的场所,方便灵活。
潜孔钻机采用电能作动力,噪音小、动力强劲。
钻孔速度是一般凿岩机的3-8倍,岩石硬度达到9个,每小时的钻孔深度是8-16米。
六:实拍高清产品大图或施工图七:实拍高清产品施工案例图八:技术参数1、型号 YGD702、钻孔直径φ50-90mm3、适用岩石(普氏硬度)≥204、钻孔深度≥15m5、钻具回转速度 110r/min6、使用气压 0.5-0.7Mpa7、耗气量≥6m3/min8、推进气缸气缸直径 90mm 推进有效行程 1070mm 最大推进力 3600N 9、电动机型号 Y2-4E 功率 3kW 电压 380V额定转速 1410r/min10、钻杆钻杆外径φ42mm钻杆长度 1025mm11、主机外型尺寸重量: 280kg 1740×260×420mm九:使用方法,操作规程1、钻机安装及钻前准备①、钻机运到施工现场后,检查各零、部件有无缺损,确认无损坏再进行组装和加油。
3.3孔加工刀具-钻削与钻头

3.3.1 麻花钻
二、麻花钻的几何角度 4.主切削刃角度分析
钻头的两条主切削刃是前、后面汇交形成 的区域。 前面是螺旋形的刃沟面,后面是刃磨形成 的圆锥或螺旋面,均为曲面。 正交平面参考系标注的前角、后角、主偏 角都是派生角。 钻头切削刃各点的螺旋角、刃倾角、前角、 主偏角都是不同的。
一、群钻 3.左右对称的圆弧刃的作用
防止钻孔偏斜,减少孔径扩大,加强定心导向作 用。 圆弧刃与外直刃转折点处形成自然分屑点,切屑 容易自行折断。 圆弧刃前角平均增大15度左右。 圆弧刃使外刃与内刃参数得以分别控制。可磨出 大内刃顶角,横刃虽然变窄变尖,钻尖强度仍不 被削弱。
3.3.4 先进钻型与结构特点简介
三尖七刃锐当先 月牙弧槽分两边 一侧外刃开屑槽 横刃磨低窄又尖
3.3.4 先进钻型与结构特点简介
一、群钻 2.群钻的优点
横刃缩短,前角增 大,进给量提高, 效率提高。 钻头寿命提高。 钻头定心作用好, 钻孔精度提高,形 位误差与加工表面 粗糙度均较小。
3.3.4 先进钻型与结构特点简介
第三节 孔加工刀具
本小节主要内容
麻花钻 钻削原理 钻头的修磨 先进钻型与结构特点简介 深孔钻
孔加工的特点:
1.孔加工刀具多为定尺寸刀具,如钻头、绞刀等。 2.受被加工孔尺寸的限制,切削速度很难提高,影响生 产率和加工表面质量。 3.刀具的结构受孔的直径和长度的限制,刚性较差。 4.孔加工时,刀具一般是在半封闭的空间内工作,所以 切屑排除困难,冷却液难以进入加工区域,散热条件不 好。
3.3.3 钻头的修磨
定义:
钻头的修磨是指将普通钻头按不同加工要求 对横刃、主刃、前后面进行附加的刃磨。
意义:
车工(普通车工)高级理论知识试卷答案AB

.A卷一、单项选择题(第1题~第160题。
选择一个正确的答案,将相应的字母填入题内的括号中。
每题0.5分,满分80分。
)1.职业道德体现了( A )。
A、从业者对所从事职业的态度B、从业者的工资收入C、从业者享有的权利D、从业者的工作计划2.职业道德不鼓励从业者( D )。
A、通过诚实的劳动改善个人生活B、通过诚实的劳动增加社会的财富C、通过诚实的劳动促进国家建设D、通过诚实的劳动为个人服务3.职业道德基本规范不包括( C )。
A、爱岗敬业忠于职守B、诚实守信办事公道C、发展个人爱好D、遵纪守法廉洁奉公4.不爱护工、卡、刀、量具的做法是( C )。
A、正确使用工、卡、刀、量具B、工、卡、刀、量具要放在规定地点C、随意拆装工、卡、刀、量具D、按规定维护工、卡、刀、量具5.不符合着装整洁文明生产要求的是( D )。
A、按规定穿戴好防护用品B、遵守安全技术操作规程C、优化工作环境D、在工作中吸烟6.保持工作环境清洁有序不正确的是( B )。
A、优化工作环境B、工作结束后再清除油污C、随时清除油污和积水D、整洁的工作环境可以振奋职工精神7.下列说法正确的是( C )。
A、画局部放大图时应在视图上用粗实线圈出被放大部分B、局部放大图不能画成剖视图或剖面图C、回转体零件上的平面可用两相交的细实线表示D、将机件的肋板剖开时,必须画出剖面线8.关于“斜视图”,下列说法错误的是( C )。
A、画斜视图时,必须在视图的上方标出视图的名称“A”,在相应的视图附近用箭头指明投影方向,并注上同样的字母B、斜视图一般按投影关系配置,必要时也可配置在其他适当位置。
在不致引起误解时,允许将图形旋转摆正C、斜视图主要是用来表达机件上倾斜部分的实形,所以其余部分也必需全部画出。
D、将机件向不平行于任何基本投影面的平面投影所得的视图称为斜视图9.基本尺寸是( D )。
A、测量时得到的B、加工时得到的C、装配后得到的D、设计时给定的10.标准公差数值与两个因素有关,它们是( D )。
错齿内排屑深孔钻削技术探讨

机床与液压
MACHI NE OOL & HYDRAULI T CS
Ap . 01 r2 2 Vo . 0 No 8 14 .
第4 O卷 第 8期
D :1 . 9 9 jis. 0 1—3 8 . 0 2 0 . 1 OI 0 3 6 /.sn 1 0 8 12 1. 80 5
在机 械加 工 中经 常会 碰 到工 件深 孔 ( / L D>5 ) 的钻削 ,它是一个很复杂的工艺问题 ,深孔钻削是在
一
6 4m 1 m、长径 比达 10的 中等精度小 深孔甚 为有效 。 0
个封 闭的环 境 下进行 的,加 工 时有 着许 多不 利 因
素 ,其 主要特点为 :
( )不易 观 测 刀具 切 削 情 况 ,只 能靠 听声 音 、 1 看切屑 、测油压等手段来判断排屑与刀具磨损情 况。 ( )切屑 排 出 较 困难 ,当切 削 到 一定 深 度 时 , 2 特别是加工不易断屑材料 ,螺旋状切屑很难从孔 中及 时排 出。 ( ) 由于切 屑 阻塞 ,冷却 液很 难 进入 到切 削 区 3 域 ,切削热不易传散 ,集中在切削区 ,使 刀具钝 化加 剧 ,钻削扭矩增加 ,甚至钻头折断。 ( )加工时孔易偏斜 。 4 ( )刀杆细长 ,刚性差异振动 。 5 如何顺利地排 出切屑并及时冷却钻头 ,这是深孔 钻 削加工方法 的基本 出发点 ,它们是 保证加 工精度 、 刀具耐用度及提高生产率 的关键。 1 钻 削方 案 的确 定 与 比较 般深孔 L D= / 5~1 ,可 以用 接长 的麻 花钻加 0 工 ,但是加工 L D>2 / 0的 深孔 时排 屑 困难 ,往 往造 成钻头折断 ,必须用深孔刀具方能 加工 。下 面比较 3 种典型深孔钻 的特点 :
BTA深孔钻的结构优化及切削仿真分析

BTA深孔钻的结构优化及切削仿真分析作者:吴雪峰马路苑忠亮杨树财来源:《哈尔滨理工大学学报》2018年第04期摘要:BTA 深孔钻是一种典型的深孔加工内排屑钻头,刀具结构与刀具角度是影响加工质量与加工效率的重要因素。
深孔加工过程中封闭,通过实验的方法优化刀具结构与角度难度较大。
采用有限元的方法,用ANSYS软件建立了BTA深孔钻静力及模态三维分析模型,得到了BTA深孔钻变形特点及六阶振型图,为BTA深孔钻钻头结构优化提供参考;采用AdvantEdge软件建立了BTA深孔钻各刀齿钻削过程模型,研究了切屑形成过程及刀具角度对切削力、扭矩的影响规律,进而为刀具角度优化提供理论参考。
关键词:BTA深孔钻;有限元仿真;模态分析;钻削仿真;结构优化DOI:10.15938/j.jhust.2018.04.004中图分类号: TG501.1文献标志码: A文章编号: 1007-2683(2018)04-0018-07Abstract:BAT deephole drill is a typical innerchip removal drill. Structures and angles of tools are the main factors that influence the machining quality and machining efficiency. Because the processing of deephole drilling is not visible, it is very difficult to optimize structure and angles of tool through the experiment method. In this paper, finite element method is used as follows: static analysis and modal analysis of BAT deephole drill are built by ANSYS, and then the deformation and sixset vibration mode diagram of BAT deephole drill are carried out as a reference for structural optimization of BAT deephole drilling; Drilling process model of each tool tooth is built by AdvantEdge, and the effect of chip formation process and tool angles on cutting force and torque are studied as reference for tool angle optimization.Keywords:BAT deephole drilling; finite element simulation; modal analysis; drilling simulation ; structural optimization深孔加工在机械行业中有着举足轻重的地位,当钻头孔深与孔径之比大于 10时,称之为深孔加工[1]。
BTA钻头受力分析

BTA钻头受力分析作者:师毓华来源:《科学与财富》2018年第30期摘要:BTA深孔钻削是金属切削中一种较为复杂的加工方式。
本文对首先对钻削过程中钻削力的来源进行了阐述,进而对BTA钻头的在加工过程中的受力进行了简化,从而获得了BTA深孔钻头的受力分析,为后续BTA钻头的设计与优化提供一定的参考。
关键词:BTA钻头;钻削力;深孔加工0.引言:BTA深孔钻削是深孔加工中常用的一种加工方法,由于其加工效率高产品质量好,目前广泛的应用于各种加工领域当中。
由于BTA深孔钻削属于内排屑自导向加工模式,所以钻头的受力对钻头在加工过程中的稳定性与自导性有着十分重要的影响。
1.钻削力的来源钻削过程是由刀具通过旋转加轴向进给,在待加工工件上加工出所需要的深孔,由于材料具有一定的韧性和硬度,材料在被加工过程中发生一系列的弹塑性变形,对钻头产生阻力,在切屑与工件分离的过程中切屑沿着前刀面流出,和前刀面接触并产生摩擦阻力。
随着刀具向前移动,工件已加工表面会有一定弹性恢复,继而与后刀面进行接触,然后产生摩擦力。
由此,钻削力的来源主要由以下三个方面组成[1]:(1)钻削过程中,被加工材料发生弹性变形所产生的阻力。
(2)钻削过程中,被加工材料发生塑性变形所产生的阻力。
(3)钻削过程中,切屑流出时对刀具前刀面产生的摩擦力和刀具向前移动时工件过渡表面和已加工表面对刀具后刀面挤压所产生摩擦力。
2.错齿BTA钻头钻削力分析BTA深孔钻削的过程中,除了刀具切削刃与工件接触以外,还有导向块与工件接触,致使加工过程中刀具的的受力分为三个部分,分别为切削刃所受的切削力、导向块所受的正压力和导向块与工件之间的摩擦力,这样一来使得刀具的受力相当复杂。
在一般的切削加工中,例如在车削加工中,只存在着工件、刀具、床身之间的正常力系,所以只需将车刀装在三向测力仪上,就可以测量出车刀所受的三向力。
而在深孔钻削的过程中,由于存在着导向块与工件之间的正压力和摩擦力,使工件与刀具切削刃和导向块之间构成封闭力系,所以就不能直接测量出切削刃所受的三向分力,只能测出刀具所受的轴向力与扭矩。
深孔钻头厂家分享深孔钻头的优缺点和性能特点

深孔钻头厂家共享深孔钻头的优缺点和性能特点专门用于加工深孔的钻头,深孔钻头。
在加工中,孔径比大于6的孔通常称为深孔。
由于钻杆刚性差,深孔钻孔时热量和碎屑难以排出,简单弯曲振动。
冷却系统通常用于解决冷却和排屑的问题。
深孔钻头在汽车、模具和航天工业中特别受欢迎。
可分为外部芯片和内部芯片。
深孔钻头,在钻深孔时,由于需要从孔中排出大量的切屑,并且需要向刀具的切削刃中进给足量的冷却液,所以一般的麻花钻钻头很难充足这一要求。
当钻直径较大的深孔时,可以使用内冷麻花钻,其中冷却液在压力下通过钻头体中的孔或通过放置在钻头体上的凹槽中的小管输入。
钻超深孔必需使用特别的内部冷却深孔钻头深孔钻头,有什么优缺点和性能特点?大家一起讨论一下吧。
优势1、加工孔径尺寸精度高;2.加工孔的偏斜度小;3.枪钻可以重磨,一刀总加工深度大;4.这个洞又深又大。
劣势1.由于刀杆上的V形排屑槽,刀杆强度差,加工效率低;2.铁屑会摩擦被加工的内表面,降低加工粗糙度;3.刀头角度多而杂,需要专门的重磨工具和专业人员重磨;4.整体焊接的枪钻更换起来很麻烦。
运行特性1.沟槽的优化几何设计。
这些硬质合金深孔钻头具有先进的凹槽几何形状,旨在优化各种材料孔深度的排屑;2.放大冷却液管的形状。
为了向切削刃供给更好的冷却剂供应,刀具具有更大的冷却剂管道轮廓,这确保了向切削刃和排屑的有效冷却剂供应;3.没有问题芯片。
这种钻头设计有适当的切削参数,即使没有问题也能从深孔中切屑。
有效防止包装和后续干扰工具。
以上就是这个我对深孔钻头的优缺点和性能特点的介绍。
希望这篇文章能让你对深孔钻头有更多的了解。
浅谈深孔加工技术

技术与应用A PPLICATION157OCCUPATION2014 11摘 要:本文探讨了深孔加工的特点、关键技术、加工类型、刀具及结构等问题。
关键词:深孔加工 加工特点 关键技术 加工方法浅谈深孔加工技术文/杨营营所谓深孔,是指孔深与孔径之比大于5的孔。
深孔又分为一般深孔(L /d >5~20)、中等深孔(L /d >20~30)、超深孔(L /d >30~100)三类。
不同类型的深孔,其加工方法也不相同。
一、深孔加工的特点和关键技术1.深孔件加工的特点一是深孔加工时,孔轴线容易歪斜,钻削中钻头容易引偏。
二是刀杆受内孔限制,一般细而长,刚性差,强度低,车削时容易产生振动和“让刀”现象,使零件易产生波纹、锥度等缺陷。
三是钻孔或扩孔时切屑不易排出,冷却润滑液输入困难。
四是加工时难以观察孔的加工情况,加工质量不易控制。
2.深孔加工的关键技术深孔加工的关键技术是深孔刀具几何形状的确定和切削时的冷却、排屑问题。
在加工中可采用以下措施来保证加工质量:一是粗精加工分阶段进行,二是合理选择加工刀具,三是采用导向和辅助支承,四是配置冷却液输入装置。
二、深孔加工类型一是按其所用刀具分类,可分为实心钻孔法、镗孔法、套料钻孔法。
二是按运动形式分类,可分为工件旋转,刀具做进给运动;工件不动,刀具旋转又做进给运动;工件旋转,刀具也做反向旋转又做进给运动;工件做旋转运动与进给运动,刀具不动,这种形式采用不多。
三是按排屑方法分类,可分为外排屑、内排屑。
三、深孔加工刀具及其结构1.扁钻该刀具结构简单,容易制造,在钻削加工时冷却液由钻杆内部注入孔中,切屑从零件孔内排出,适用于精度和表面粗糙度要求不高的较短深孔。
图1 简易扁钻1-钻头 2-钻杆 3、4-紧固螺钉2.单刃外排屑小深孔钻该深孔钻由切削部分和钻杆焊接而成,切削部分用W 18Cr 4V 制造或硬质合金刀头镶制;钻杆为35#~45#钢无缝钢管,上压120°V 形槽用以排屑,中空可通过切削液,从自切削部分腰圆孔处进入切屑区域。
各大类型钻头的特点及用途
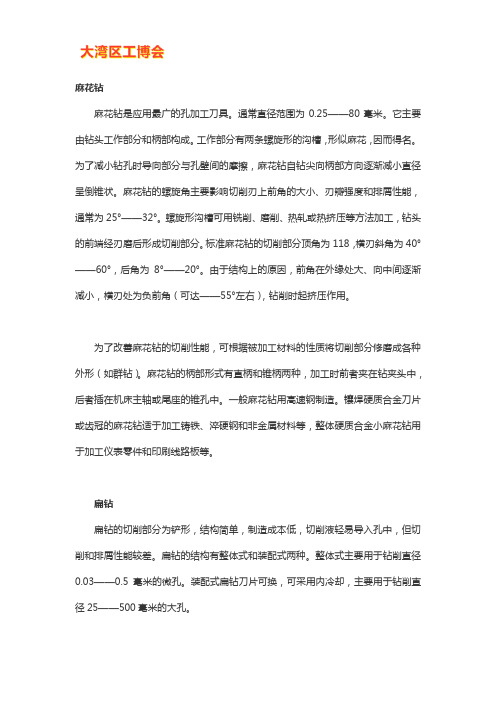
麻花钻麻花钻是应用最广的孔加工刀具。
通常直径范围为0.25——80毫米。
它主要由钻头工作部分和柄部构成。
工作部分有两条螺旋形的沟槽,形似麻花,因而得名。
为了减小钻孔时导向部分与孔壁间的摩擦,麻花钻自钻尖向柄部方向逐渐减小直径呈倒锥状。
麻花钻的螺旋角主要影响切削刃上前角的大小、刃瓣强度和排屑性能,通常为25°——32°。
螺旋形沟槽可用铣削、磨削、热轧或热挤压等方法加工,钻头的前端经刃磨后形成切削部分。
标准麻花钻的切削部分顶角为118,横刃斜角为40°——60°,后角为8°——20°。
由于结构上的原因,前角在外缘处大、向中间逐渐减小,横刃处为负前角(可达——55°左右),钻削时起挤压作用。
为了改善麻花钻的切削性能,可根据被加工材料的性质将切削部分修磨成各种外形(如群钻)。
麻花钻的柄部形式有直柄和锥柄两种,加工时前者夹在钻夹头中,后者插在机床主轴或尾座的锥孔中。
一般麻花钻用高速钢制造。
镶焊硬质合金刀片或齿冠的麻花钻适于加工铸铁、淬硬钢和非金属材料等,整体硬质合金小麻花钻用于加工仪表零件和印刷线路板等。
扁钻扁钻的切削部分为铲形,结构简单,制造成本低,切削液轻易导入孔中,但切削和排屑性能较差。
扁钻的结构有整体式和装配式两种。
整体式主要用于钻削直径0.03——0.5毫米的微孔。
装配式扁钻刀片可换,可采用内冷却,主要用于钻削直径25——500毫米的大孔。
深孔钻深孔钻通常是指加工孔深与孔径之比大于6的孔的刀具。
常用的有枪钻、BTA 深孔钻、喷射钻、DF深孔钻等。
套料钻也常用于深孔加工。
扩孔钻扩孔钻有3——4个刀齿,其刚性比麻花钻好,用于扩大已有的孔并提高加工精度和光洁度。
锪钻锪钻有较多的刀齿,以成形法将孔端加工成所需的外形,用于加工各种沉头螺钉的沉头孔,或削平孔的外端面。
中心钻中心钻供钻削轴类工件的中心孔用,它实质上是由螺旋角很小的麻花钻和锪钻复合而成,故又称复合中心钻。
BTA深孔钻结构及加工原理要点

BTA深孔钻的结构特点及加工原理要点bta深孔钻是内排屑深孔钻的一种典型结构,它是在单刃内排屑深孔钻的基础上改进而成,其切削刃呈双面错齿状,切屑从双面切下,并经双面排屑孔进入钻杆排出孔外。
bta深孔钻切削力分布均匀,分屑、断屑性能好,钻削平稳可靠,钻削出的深孔直线性好。
1、BTA深孔钻的结构特点BTA深孔钻具有以下结构特点:(1)刀体上分布有外刃刀片、中刃刀片、内刃刀片、导向块和双面排屑孔,并通过刀体上的浅牙多头矩形螺纹与空心钻杆联接。
(2)钻芯部分由内刀刃代替了麻花钻的横刃,从而克服了麻花钻横刃较长、轴向阻力较大的缺点;由于钻芯相对于钻孔轴心线偏移了一段距离,加工时钻芯处刀刃低于中心处刀刃,因此会形成一个导向芯柱,使钻头具有较好的导向性,钻孔时不易偏斜,该导向芯柱增长到一定长度后会自行折断并随切屑一起排出。
(3)主刀刃采用非对称的分段、交错排列形式,可保证分屑可靠,并避免用整体硬质合金刀片磨削卷屑槽、分屑槽时易产生裂纹的情况。
(4)刀片材料可采用几种不同牌号的硬质合金,以适应各部分结构对耐磨性和强度的不同要求,如钻芯部分切削速度低、切削力大,在切屑挤压作用下易发生崩刃,可选用韧性较好的硬质合金刀片;钻头外缘部分则可选用耐磨性较好的硬质合金刀片。
2、BTA深孔钻的加工原理BTA深孔钻在普通车床上的工作情况:被加工工件由车床大拖板上的v形铁定位并用螺栓压板夹紧。
钻孔加工时,钻杆由主轴内的专用夹头夹紧并在主轴带动下旋转,工件则由大拖板带动作进给运动。
机床工作台上安装了进液器,并通过o形密封圈与工件左端面密封连接。
加压切削液由进液器的进液口注入,经过钻杆外径与孔壁间的缝隙流入切削区,对进行冷却,切屑随同切削液一起由钻杆内孔通过专用夹头的出液口从排液箱排出。
切削液可采用浓度5%的乳化液;切削用量可选用:v=60~90m/min,s=0.035~0.23mm/r。
由于钻杆细长,容易变形,因此在机床导轨上安装了活动中心支承,可对钻杆的任意位置进行支承。
钻削与镗削加工钻削运动与加工范围

单刃外排屑深孔钻 ( 枪钻 ) :可加工长径比达 100 的小 深孔。
深孔钻
深孔加工难度大,技术要求高, 这是深孔加工的特点所决定的。因此, 设计和使用深孔钻时时应注意: 钻头要导向,防止偏斜; 保证可靠的断屑和排屑; 采取有效的冷却和润滑措施。
3 、 深孔钻 对于孔的深度与直径之比 l/d=5 ~ 10 的普通深 孔,可以用接长麻花钻加工;对于孔的深度与直径之 比 l/d>5 ~ 10 的深孔,必须采用特殊结构的深孔钻 才能加工。 深孔加工难度大,技术要求高,这是深孔加工 的特点所决定的。因此,设计和使用深孔钻时时应注 意钻头的导向,防止偏斜;保证可靠的断屑和排屑; 采取有效的冷却和润滑措施。
第一节
一、钻削加工概述
钻削加工与钻头
钻削加工:以钻头或工件的旋转为主运动,两者的相 对运动为进给运动,对实体工件进行加工的切削加工 方法。 钻孔是孔的粗加工方法,孔的尺寸精度一般在 IT13~IT11 , Ra 为 50~12.5μm 。 可加工直径 0.1 ~ 80mm 的孔。钻削中最常用的刀具 是麻花钻。
3 、麻花钻结构上的缺点 ( 1 )横刃处负前角; ( 2 )主切削刃的前角、后角是变化的 ; ( 3 )主切削刃长,切削宽度大,不易 卷曲排屑。
引偏原因:
1) 麻花钻是最常用刀具,由于细长而刚性差 2) 麻花钻上有两条较深的螺旋槽,刚性差 3) 钻头仅有两条很窄二棱边与孔壁接触,接触刚度和导 向作用也 很差。 4) 钻头横刃处前角有很大负值,切削条件极差,钻孔时 一半以上的轴向力由横刃产生,稍有偏斜将产生较大附加力 矩,使钻头弯曲;此外,两切削刃不对称,工件材料不均匀 ,也易引偏
( 1 )错齿内排屑深孔钻
错齿内排屑深孔钻适于
加工直径 d>20mm ,孔深与直径比 l/d﹥5-10 的深孔。 其工作原理见图 6.6 。切削时高压切削液(约 2 ~ 6 ΜΡa )由工件孔壁与钻杆的表面之间的间隙进入切 削区,以冷却、润滑钻头切削部分,并利用高压切削 液把切屑从钻头和钻管的内孔中冲出。 刀齿交错排列实现分屑,便于排屑。
深孔加工简介

2.喷吸钻
喷吸钻是一种新型的内排屑深孔钻,主要用于加工直径18~ 180mm、深径比在100以内的深孔。加工精度为IT10~IT7,表面 粗糙度Ra3.2~0.8μm,孔的直线度可达0.1mm/1000mm。
(1)喷吸钻的结构
喷吸钻的组成结构
喷吸钻钻头结构
(2)喷吸钻的工作原理 喷吸钻利用液体的喷吸效应实现冷却排屑。即当高压
➢有利于分屑和排屑,可使径向分力得到较合理的平 衡,减少导向支承块上的支承力。
➢刀齿也可根据受力情况和切削条件不同,选用不同 的刀具材料。
错齿内排屑深孔钻的工作原理
一、深孔加工的特点
➢深孔加工时,刀杆细长,刚性差。 ➢切削液难以引入到切削区,切屑不易排出,钻尖冷却困难。 ➢切削刃上各点的切削速度变化较大,尤其是近中心处的切 削速度为零,切削条件差。 ➢转矩和轴向力大,钻进困难,且易引偏,致使刀具耐用度 及生产率很低。
二、深孔钻
(1)按切削刃的多少分 ➢单刃 ➢多刃
流体经过一个狭小的通道高速喷射时,在这股喷射流的周 围形成了低压区,将喷嘴附近的流体吸走。
3.错齿内排屑深孔钻(高压内排屑钻)
错齿内排屑钻由钻头和钻杆两部分组成。 用途:加工直径60mm以上、深径比在100以内的深孔。 加工精度为IT9 ~IT7,表面粗糙度为Ra6.3~1.6μm。
ห้องสมุดไป่ตู้
结构特点:切削刃成交错排列,刀具上无横刃。 优点:
(2)按深孔钻的排屑方式分 ➢内排屑 ➢外排屑
常用的深孔钻有枪孔钻、喷吸钻和高压内排屑钻。
1.枪孔钻
概念:枪孔钻是单刃外排屑深孔钻,因最早用于加工枪 管而得名。
特点:仅在轴线的一侧有切削刃,没有横刃,并分为外 刃和内刃两段,使切出的切屑短小,便于排屑。
深孔钻的设计与研究
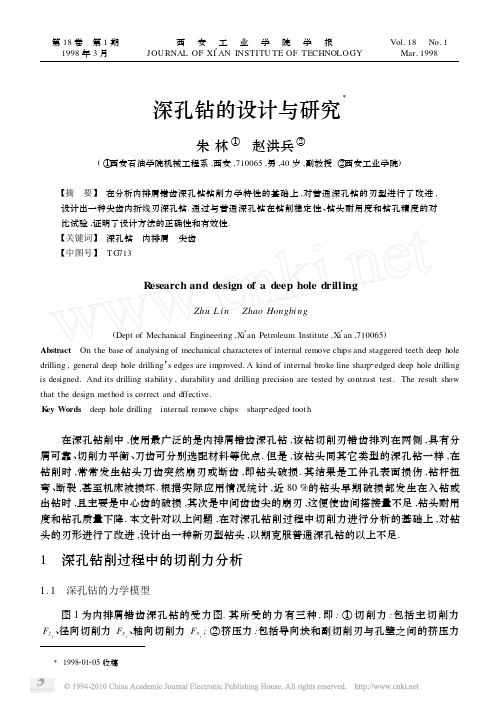
内折线刃还增大了中心齿的散热体积和钻尖强度.
改中间齿为尖齿 为了提高钻削稳定性 ,我们将中间齿设计为尖齿 , 见图 4. 切削时 , 中间
齿在孔底形成环形凸筋 ,与内折线刃在孔底形成的反锥 (见图 5) 同时起到定心 、稳定钻削的作
用.
图 4 尖齿内折线刃深孔钻 图 5 孔底的形状
230
0. 03
230
0. 08
230
0. 15
85. 9 8ห้องสมุดไป่ตู้. 5 78. 3
84. 3 76. 7 78. 6
图 6 瞬间轴向力变化曲线 图 7 钻杆振幅对比曲线
3. 3 试验结果分析 (1) 由表 1 可以看出 ,随着进给量的增加 ,两种钻头的轴向力和扭矩相应增大 ,但尖齿内折
第 18 卷 第 1 期 西 安 工 业 学 院 学 报 Vol. 18 No. 1 1998 年 3 月 J OU RNAL OF XIπAN INSTITU TE OF TECHNOLO GY Mar. 1998
深孔钻的设计与研究 Ξ
第 1 期 朱 林 赵红兵 :深 孔 钻 的 设 计 与 研 究 55
有外齿和部分中间齿在切除残余部分 ,因而形成“切削 帽”. 此时能量瞬时释放 ,切削扭矩突降并趋于零 ,见图 中 D~ E 段.
由此可知 ,钻头的入钻使切削扭矩骤然产生 , 钻头 的出钻又使切削扭矩骤然消失. 可见 , 扭矩的突变是造 成钻头破损的主要因素. 这种大幅度的扭矩变化必然影 响工件加工质量和钻头耐用度.
1 深孔钻削过程中的切削力分析
1. 1 深孔钻的力学模型 图 1 为内排屑错齿深孔钻的受力图. 其所受的力有三种 , 即 : ① 切削力 :包括主切削力
Fzi 、径向切削力 Fyi 、轴向切削力 Fxi ; ②挤压力 :包括导向块和副切削刃与孔壁之间的挤压力
- 1、下载文档前请自行甄别文档内容的完整性,平台不提供额外的编辑、内容补充、找答案等附加服务。
- 2、"仅部分预览"的文档,不可在线预览部分如存在完整性等问题,可反馈申请退款(可完整预览的文档不适用该条件!)。
- 3、如文档侵犯您的权益,请联系客服反馈,我们会尽快为您处理(人工客服工作时间:9:00-18:30)。
! " #$ % & ’ ( % ’ & #) " * & * ( % + 01 # & 2 3 & 4* + ( #3 2 ; ; 5 6# 7! 8 9 #3 2 $ % * 0 0 # & ! 3 3 % ": + + # & ( " . 9< # 43 = * / # # 9 " 3 / #& . / / 西安石油大学深孔加工技术研究所 > ? @ A A B C D 彭海
图 8 钻杆振幅对比曲线
钻 头 在 切 削 过 程 中 的 振 动 情 况! 当中心齿C J点D )
新型错齿内排屑深孔钻的切削性能试验
为了验证新 型 错 齿 内 排 屑 深 孔 钻 的 切 削 性 能 ! 首先进行了与普通型错齿深孔钻的切削力对比试 以分析 &种钻头的切削力大小及切削平稳性 4 其 验! 次 进 行了批量零 件 的 钻 削 试 验 ! 以测试新型钻头的 耐用度 ) 加工质量以及加工效率 " 2 $&种钻头切削力的对比试验 采用 9 工件材料 3 8 5车 床 改 装 的 深 孔 钻 镗 床 ! 为 # 硬 度 ;< 钻头直径为 5 & 0 78 & ! 9 :合 金 钢 ! 9 采用钻杆上粘贴电阻应变片并连接测量 * 0 $ # = >>" 仪器的方法测量切削过程中的轴向力及扭矩的变 化 " 从 钻 削试验数据 表明 ? 随着进 给 量 @的 增 大 ! & 种钻 头 的轴向力 和 扭 矩 相 应 增 大 ! 但新型深孔钻比 普通型深孔钻轴向力平均降低 & 扭矩 平 均 降低 2 6! 随着进给量增加 ! 新型深孔钻切削力 2 # $ . 6" 而且 ! 增 加较为缓慢 ! 如当 @ 时! 新型深孔钻 A5 $ 5 8 >>B : 比普通型的深孔钻的轴向力仅减 小 2 扭 矩减 小 * 6) 而当 @ 时! 轴向力和扭矩分别减 2 # 64 A5 $ 2 * >>B : 小了 & 新型深孔钻 5 $ . 6和 & 2 $ . 6" 由此可以看出 ! 在大进给量的切削过程中 ! 切削更轻快平稳 " 另 外! 从记录下的轴向力瞬时变化图中也可看
新型错齿内排屑深孔钻的结构及刃形特点
针对 普通错 齿 内 排 屑 深 孔 钻 所 存 在 的 问 题 G 我 们在 普通错 齿内 排 屑 深 孔 钻 的 基 础 上 G 对钻头结构 及刃形进行 相 应 的 改 进G 设计了一种 新型的错齿 内排屑深孔 钻> 又称多尖 齿内排屑深
图 @ 新型错齿内排屑深孔钻 孔 钻D 其头 G 部 结构及 刃形如 图 @所 示 G 其结构及刃形上的主要 特点如下 V
出! 在较大进给量C 下! 新型深孔钻 A5 $ 2 * D @ >>B :
谷值仅相当于普通型 深孔钻 的 2 切削力波动的峰 ) B 说明新型深孔钻钻削平稳 这同新型深孔钻钻削 8 ! " 时能产生定心环形凹槽和定心反锥起到双重定心和 稳定钻削作用是一致的 "
耐用度及加工质量的对比试验 & $钻削振动 ) 对 这 &种 钻 头 进 行 了 批 量 零 件 钻 削 加 工 试 验 !
摘要 F 在分析普通错齿内排屑深孔钻存在问题的基础上 G 介绍 @种新型错齿内排屑深孔钻的 E 结构特点 G 并用这 H种深孔钻进行切削性能对比试验 G 证明新型深孔钻具有较好的钻削性能 I 关键词 深孔钻削 内排屑深孔钻 对比试验
; G ; ; G( # # 9 " 3 / #, & . / / . + 0 : + + # & ( " . 9& # 43 = * / , # # 9 " 3 / #, & . / / 3 49 * & . + 0% # R % JK L M N O P Q , 在深孔加工 中 G 错齿内排屑深孔钻由于具有分 屑效果好 G 排屑顺畅 S 加工效率高以及加工精度较高 因此得到了广泛的应用 I 但普通的错齿内排 等特点 G 屑深孔钻也存在着一些不足之处 G 针对这些问题 G 我 们 设 计了一种新 型 的 错 齿 内 排 屑 深 孔 钻 G 经过实际 使 用 及切削性能 试 验 G 证明该深孔钻具有良好的切 削性能及应用效果 I 钻头 G 其压向导向块的径向合力较小 G 而当刀片磨损 或 遇上 材料硬 质 点 时 G 径向合力瞬时会指向相反方 这样就会失去钻削平衡而产生振动 G 从而引起钻 向G 孔偏斜及螺旋沟问题 G 影响了钻孔质量 I
易崩刃 ! 有利于提高钻头的耐用度 " 并在中心齿的内刃上 ! # $增 大 了 钻 尖 偏 心 量 % 磨 出 两条折线形 内 刃 ! 即 内 刃 由 &条 斜 度 不 同 的 折 这样就有效地降低了钻头高度 ’ 缩短 线 刃 组 成! ! ( 了入钻 ) 出钻的时间 ! 从而使得入钻时能很快地进入 而且中心齿和中间齿几乎同时切入 稳 定钻削阶段 ! 工件 ! 可以改善刀齿的受力状态 ! 减小切削振动 " 而 出钻时! 由 于 出 钻 时 间 短! 切 削 帽 减 薄! 各刀齿上切 削力几乎同时消失 ! 有利于减振及提高钻削稳定性 " 中 * $根据各刀齿不同的切削负荷及切削状态 ! 心 齿 所受 到 的 轴 向 力 较 大 ! 挤 压) 摩 擦 严 重! 切削条 件恶劣 ! 可选用抗弯强度高 ) 抗冲击性好的 +, 类刀 片! 而外齿和中间齿由于切削速度较中心齿高 ! 故应 选 用 红 硬 性 好) 耐 磨 性 高 的 刀 片 材 料! 如 +-. / 0 ) 等 +12 " 以保护刀齿和提高 3 $在刀体后端增设减振块 ! 加 工 孔的形状精 度 4 当刀齿磨损或有崩刃造成钻削 振动时 ! 它可以起到减振 ) 消振的作用 " 提高导向块 . $减小导向块与刀体之间的高度 ! 的抗弯强度 " 同时 ! 为了增大冷却流液面积 ! 在刀体 上 铣 有矩形或半 圆 形 输 液 槽 ! 从而可使流液面积增 大 & 增 大 冷 却 液 流 量! 以增强钻削过程 5 67 8 5 6! 中的冷却润滑效果 "
参考文献
孔加工技术 $ 石油工业出版社 ! 2 $王世清 $ 2 / / 8 深孔钻削稳定性研究及应用 $ 机械工程学报 ! & $朱林 $ 2 / / 0
责任编辑 & 5 5 8年 第 /期
周守清 S2 . S
万方数据
新技术新工艺 U T S 机械加工与自动化
新型深孔钻的钻出的 &倍多 "对钻孔质量进行测量 ! 孔! 圆度误差比普通型深孔钻约小 8 孔径扩大 O >! 量小 5 孔尺寸精度可达到 P 表面 $ 5 # 7P ! >>! -. -0 粗糙度 Q A2 $ 5 78 $ & O >" R
结
语
新型错齿内排屑深孔钻的结构和刃型由切削性 能试验证明是合理的 ! 能有效提高钻削的平稳性 ! 延 长钻头使用寿命 ! 提高孔加工精度 ! 是一种具有良好 应用效果的新型错齿内排屑深孔钻头 "
图 H 加工孔底的形状
锥> 见图 H 双重定心和稳定钻削 I D G 其余刀齿都进 T W除外齿与外缘一侧为尖角外 G
万方数据
行了倒角 G 同时带有 B 的侧后角 G 消除了尖角 G [ \@ H [ 增大了刀齿的散热体积 G 同时也增强了刀齿强度 G 不 H A A T年 第 ‘期
]@ B ]
新技术新工艺 _ ^ ] 机械加工与自动化
选 择 在 某 石 油 机 械 厂 进 行 实 际 加 工! 机 床 为 -& 2 8 5 深 孔 钻 镗 床! 工件材料为 # 硬度 5 *合 金 钢 ! 9 : EF GH 钻孔直径为 = & * 5 78 5 5 ! * 0 $ # ;I >>" 在 授 油 器 后 端 的 钻 杆 处 安 装 2个 百 分 表 ! 测量 导向块 C 及减振块 C 入钻时钻杆的振幅和 K点 D L点 D 出钻时C M) N 之 间 D钻 杆 的 振 幅 对 比 曲 线 如 图 8所 示" 可以看出 ! 新型深孔钻在入钻及整个钻削过程中 而且在 L点后 ! 新型深 的振动均小于普通型深孔钻 " 孔钻在其 减振 块 进 入 工 件 后 ! 钻头还有一个减振稳 定过程 ! 使钻削扭矩迅速减弱到正常水平 ! 而普通型 深孔 钻 没 有 这 一 过 程 " 出钻时C 普通型 M) N之 间D ! 深孔钻振动开始加剧 ! 振幅增大 ! 而新型深孔钻由于 各刀齿高度差小 ! 几乎同时透钻 ! 且又有减振块的保 护作用 ! 可以平稳出钻 ! 振幅增加很小 " &种 钻 头 进 行 批量零件钻孔试验 后! 在同样大小的后 刀面磨损时 ! 新型错 齿内排屑深孔钻的 平均钻孔长度可达 是普通型错齿 2 3 >! 深孔钻钻孔长度的
普通错齿内排屑深孔钻存在的问题
普通的错齿内排屑深孔钻 G 根据钻头直径大小 G 可分为 T刀齿或 C刀齿结构 G 各刀齿分别为外齿 S 内 齿 和 中间齿 G 由于中间齿与中心齿和外齿不在同一 锥 面 上G 而是要高出它们锥面一个 U 值> 轴向上D G 因此 可 取得比较 好 的 分 屑 效 果 G 同时各刀齿还可根 据各自不同的切削状态选用不同的刀片材料 I 但普 通错齿内排屑深孔钻在刀齿结构及几何参数上也存 在着一些不足 G 主要表现在 V 钻尖较高 G 外齿到导向块之间 @ W锋角 H X较小 G 的滞后量较大 G 入钻和出钻的时间较长 G 容易造成入 钻过程中的断齿和崩刃现象 G 钻头耐用度较低 G 钻孔 质量也较差 I 各刀齿在钻头锥面上沿半径依 H W因锋角较小 G 次 排列时G 刀 齿 间 的 轴 向 高 度 差 相 对 较 大I故 在 入 钻S 出钻阶段 G 中心齿要单独承受较大的轴向力和径 向力 G 使切削振动较大 G 定心效果差 G 易产生崩刃 I 外齿的刀尖角较小 G 尖角突出 G 强度 T W中间齿 S 降 低G 一 旦 尖 角 出 现 磨 损G 齿间的搭接量就遭到破 坏G 容易造成崩齿及扭钻事故 I 钻削时孔底反锥高度较 Y W内 刃 偏 角 Z H 较 小G 低G 定心作用减弱 G 容易引发切削振动 I 钻头上作用的径向合力应始 C W在钻削过程中 G 终 指 向两导向块 之 间 G 以保证钻头处于稳定切削状 态I 但由于钻头直径及刀片尺寸限制 G 有时所设计的