第七章_钻削与钻头
中职金属切削加工基础教案:钻床及常见孔加工(全3课时)

中等专业学校2023-2024-1教案教学内容1、台式钻床台式钻床简称台钻(图2-4-2),是一种小型机床,安放在钳工台上使用,多为手动进钻,其钻孔直径一般在12~15 mm。
台式钻床主要用于加工小型工件上的各种孔钳工中用得最多。
2、立式钻床立式钻床简称立钻(图2-4- 3),是万能性通用机床,一般用来钻中小型工件上的孔,其规格用最大钻孔直径表示。
常用的立式钻床有25 mm、35 mm、40 mm、50 mm等几种。
立式钻床工作台和主轴箱可以在立柱上垂直移动,可用于钻孔、扩孔、铰孔、划端面、钻沉座孔(锪)、攻螺纹等作业,借助于夹具也可以进行镗孔。
教学内容3、摇臂钻床摇臂钻床有一个能绕立柱旋转的摇臂(图2-4- 4)。
主轴箱可在摇臂上做橫向移动,并可随摇臂沿立柱上下做调整运动,因此,操作时能很方便地调整到需钻削的孔的中心,而工件无须移动。
在各类具备钻孔功能的机床中,摇臂钻床由于操作方便、灵活,适用范围广,具有典型性。
特别适用于单件或批量生产带有多孔大型零件的孔加工。
(二)钻床的型号表达(1) Z5135型立式钻床,其型号含义如图2-4-5所示。
教学内容(2) Z3050型摇臂式钻床,其型号含义如图2-4- 6所示。
板书设计钻床及常见孔加工一、钻床二、钻床的型号表达三、总结1.台式钻床四、巩固2.立式钻床五、作业3.摇臂钻床教后札记中等专业学校2023-2024-1教案教学内容麻花钻通常直径范围为0.25~80mm。
麻花钻的工作部分有两条螺旋形的沟槽。
1.麻花钻的结构麻花钻由工作部分、柄部和颈部组成。
如图2-4- 7所示。
(1)工作部分麻花钻的工作部分分为:切削部分、导向部分。
①切削部分麻花钻的切削部分有两条主切削刃、两条副切削刃和一条横刃。
麻花钻的钻心直径为(0.125~0. 15)D(D为钻头直径)。
两条主切削刃在与它们平行的平面上投影的夹角称为顶角(2p),如图2-4- 8所示。
标准麻花钻的顶角2φ= 118°。
钻削与钻头

二、麻花钻的几何角度 1.钻头角度的参考系 基面pr :主切削刃上任 意点的基面,即通过该 点,垂直于该点的切削 速度方向的平面。 切削平面ps : 主切削刃上 任意点的切削平面,是 包含该点的切削速度方 向,而又切于该点加工 表面的平面。 正交平面po、假定工作平 面pf和背平面pp
端平面pt:与钻头轴 线垂直的投影面。 中剖面pc:过钻头轴 线与两主切削刃平行 的平面。 柱剖面pz:过切削刃选定点作与钻头轴线平行的 直线,该直线绕钻头轴线旋转形成的圆柱面。
(7-10)
式中Mc——切削扭矩; vc——切削速度; d ——钻头直径。
影响钻削力的主要因素有: • 螺旋角ω: 螺旋角ω↑,则前角γo↑,并改善了排屑情况, 轴向力F与扭矩M都显著↓。但当螺旋角β>30。 时,其影响减小。
• 顶角2φ: 顶 角 2φ↑ , 会 使 切 削 厚 度 hD↑ , 切 削 宽 度↓,从而切 向 力 Fz↓ 及 切 削扭矩M,轴向 力F↑
2.进给量 普通钻头进给量可按以下经验公式估算: f = (0.01~0.02)d (7-11) 合理修磨的钻头可选用 f = 0.03d 3.钻削速度
第三节 钻头的修磨 一、标准高速钢麻花钻存在问题 (1)沿主切削刃各点前角值差别悬殊(由+30°~-30°),横 刃上的前角竟达-54°~-60°,造成较大的轴向力和扭矩, 使切削条件恶化。 (2)棱边近似为圆柱面(有稍许倒锥)的一部分,副后角为零 度,摩擦严重。 (3)在主、副切削刃相交处,切削速度最大,散热条件最差, 因此磨损很快。 (4)两条主切削刃很长,切屑宽,各点切屑流出速度相差很 大,切屑呈宽螺卷状,排屑不畅,切削液难于注入切削区; (5)横刃较长,其前、后角与主切削刃后角不能分别控制
第六章___钻削与钻头

有沉割刀和导向中心的钻头:
n ↑,不平度↓ 、不圆度↓ (被加工表面弹性变形小, 因木材各向异性和材质不均引起的弹性回复量小,所以 不圆度小)
n↓、u ↑, Fx ↑ → 不圆度↑ 锥形钻: n ↑,不平度↓ 、不圆度↑; u ↑,不平度 ↑ 、不圆度↑
(二)钻头结构 1、锋角 纵钻:最佳锋角为80º ~120º 左右,当2Φ> 80º ~120º 时, Φ↑ 不平度↑; 径切面上锋角对加工质量影响 小,并且径切面加工质量最好, 横断面最差; 钻削加工的孔呈长圆形
3、横棱修磨:
(二)其它螺旋钻
螺旋起塞钻:螺旋角大(40º ~50º ),容屑量大,排屑 性能好,适合旋钻的刚度比扭曲钻好,容屑量大。螺旋起 塞钻一个切削刃单向受载,容易走偏,用于在软材上钻不 太深的孔
七、影响钻削质量的因素
孔的形位精度、尺寸精度和表面质量 (一)主轴转速和进给速度
2、螺旋角w(螺旋展开线与钻头轴线的夹角) 最外点螺旋角:
2 R tgw H
2 R1 任意点螺旋角: tgw1 H
H——螺距; R——最外点半径; R1——任意点半径
螺旋角的影响:螺旋角增大,可使切削角减小,排屑容量 增大,从而可以减小扭矩,增加进给速度;若螺旋角过大, 则楔角过小,刚度不足,一般β>30~35º 。 w=12º ~30º——金属切削用麻花钻
第六章 钻削与钻头
本章重点
各种钻头的应用特点 影响钻削质量的因素
第一节 钻削原理
一、钻头的组成 1、尾部(钻柄):装夹、传递扭矩。圆柱形、圆锥形等 2、颈部:工作部分与柄部的连接部分 3、工作部分:切削部分 导向部分:导向、减少与工件孔壁的摩擦
二、钻削类型
1、横纹钻削:钻孔方向与木材纤维方向垂直。用横向钻头 2、顺纹钻削:钻孔方向与纤维方向一致。用纵向钻头
钻削与钻头

钻削用各种钻头进行钻孔、扩孔或锪孔的切削加工。
钻孔是用麻花钻、扁钻或中心孔钻等在实体材料上钻削通孔或盲孔。
扩孔是用扩孔钻扩大工件上预制孔的孔径。
锪孔是用锪孔钻在预制孔的一端加工沉孔、锥孔、局部平面或球面等,以便安装紧固件。
钻削方式主要有两种:①工件不动,钻头作旋转运动和轴向进给,这种方式一般在钻床、镗床、加工中心或组合机床上应用;②工件旋转,钻头仅作轴向进给,这种方式一般在车床或深孔钻床上应用。
麻花钻的钻孔孔径范围为0.05~100mm ,采用扁钻可达125mm 。
对于孔径大于100mm 的孔,一般先加工出孔径较小的预制孔(或预留铸造孔),而后再将孔径镗削到规定尺寸。
钻削时,钻削速度v 是钻头外径的圆周速度(米/分);进给量f 是钻头(或工件)每转钻入孔中的轴向移动距离(mm/r)。
图2是麻花钻的钻削要素,由于麻花钻有两个刀齿,故每齿进给量a f =f /2(mm/齿)。
切削深度a p 有两种:钻孔时按钻头直径d 的一半计算;扩孔时按(d -d 0)/2计算,其中d 0为预制孔直径。
每个刀齿切下的切屑厚度a 0=a fsin K r ,单位为mm 。
式中K r 为钻头顶角的一半。
使用高速钢麻花钻钻削钢铁材料时,钻削速度常取16~40米/分,用硬质合金钻头钻孔时速度可提高1倍。
钻削过程中,麻花钻头有两条主切削刃和一条横刃,俗称“一尖(钻心尖)三刃”,参与切削工作,它是在横刃严重受挤和排屑不利的半封闭状态下工作,所以加工的条件比车削或其他切削方法更为复杂和困难,加工精度较低,表面较粗糙。
钻削钢铁材料的精度一般为I T13~10,表面粗糙度为R a 20~1.25µm,扩孔精度可达IT10~9,表面粗糙度为R a 10~0.63µm。
钻削加工的质量和效率很大程度上决定于钻头切削刃的形状。
在生产中往往用修磨的方法改变麻花钻头切削刃的形状和角度以减少切削阻力,提高钻削性能,中国的群钻就是采用这种方法创制出来的。
第七章 套筒类零件加工工艺及常用工艺装备
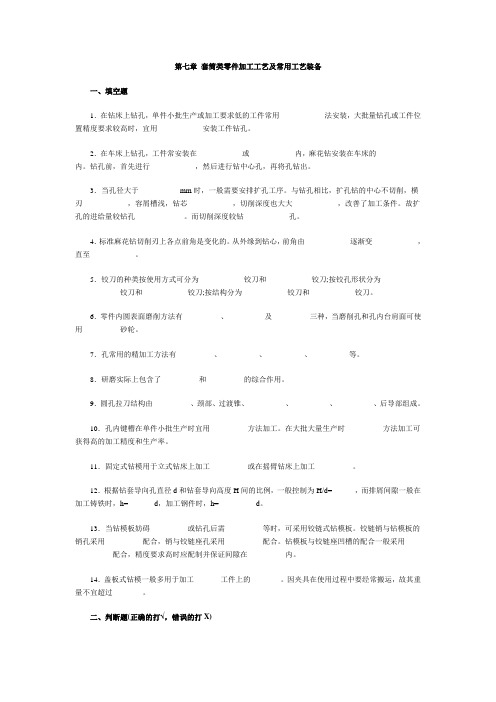
第七章套筒类零件加工工艺及常用工艺装备一、填空题1.在钻床上钻孔,单件小批生产或加工要求低的工件常用____________法安装,大批量钻孔或工件位置精度要求较高时,宜用____________安装工件钻孔。
2.在车床上钻孔,工件常安装在____________或____________内,麻花钻安装在车床的____________内。
钻孔前,首先进行____________,然后进行钻中心孔,再将孔钻出。
3.当孔径大于___________mm时,一般需要安排扩孔工序。
与钻孔相比,扩孔钻的中心不切削,横刃____________,容屑槽浅,钻芯____________,切削深度也大大____________,改善了加工条件。
故扩孔的进给量较钻孔____________ 。
而切削深度较钻____________孔。
4.标准麻花钻切削刃上各点前角是变化的。
从外缘到钻心,前角由____________逐渐变____________,直至____________。
5.铰刀的种类按使用方式可分为____________铰刀和____________铰刀;按铰孔形状分为____________铰刀和____________铰刀;按结构分为____________铰刀和____________铰刀。
6.零件内圆表面磨削方法有__________、__________及__________三种,当磨削孔和孔内台肩面可使用__________砂轮。
7.孔常用的精加工方法有__________、__________、__________、__________等。
8.研磨实际上包含了__________和__________的综合作用。
9.圆孔拉刀结构由__________、颈部、过渡锥、__________、__________、__________、后导部组成。
10.孔内键槽在单件小批生产时宜用__________方法加工。
钻头与钻削加工

钻头与钻削加工最近在德国金属加工行业所做的一项调查表明,钻削加工是机械加工车间耗时最多的工序。
事实上,在所有的加工工时中,有36%消耗在孔加工操作上。
与此对应的是,车削加工耗时为25%,铣削加工耗时为26%。
因此,采用高性能整体硬质合金钻头取代高速钢和普通硬质合金钻头,能够大幅度减少钻削加工所需的工时,从而降低孔加工成本。
过去几年来,切削加工参数(尤其是切削速度)在不断提高,特别是高性能整体硬质合金钻头的切削速度提高明显。
20年前,整体硬质合金钻头的典型切削速度为60~80m/min。
如今,在机床能够提供足够的功率、稳定性和冷却液输送能力的条件下,采用200m/min的切削速度钻削钢件已不足为奇。
尽管如此,与车削或铣削加工的一般切削速度相比,钻削加工在加工效率上还有很大的提高潜力。
整体硬质合金钻头对于基体的韧性要求很高,而钻头的磨损在可控和均匀稳定的情况下是可以接受的。
因此,典型的钻削刀具牌号比车削或铣削刀具含有更多的钴元素。
钻头材质通常采用微细晶粒硬质合金,以提高切削刃强度,确保均匀磨损而不发生崩刃。
用硬质合金钻头加工时通常要使用水基切削液,因此切削刃处的温度并不太高,但要求钻头具有抗热冲击性。
性能最佳的钻头牌号是典型的纯碳化钨材料,而无需大量添加碳化钽或碳化钛。
对于整体硬质合金钻头而言,涂层必须发挥比仅仅提高表面硬度和耐磨性更大的作用。
涂层必须在刀具与工件材料之间提供隔热层并保持化学惰性;必须将工件材料与涂层之间的粘结作用降至最低以减小摩擦;涂层表面必须尽可能光滑;此外,麻花钻的涂层还必须具有抗裂纹扩散能力。
钻削加工的动力学特性可能会引起微裂纹,为了保持刀具寿命,就必须阻止裂纹扩散。
通过选择正确的涂层工艺和生成适当的涂层显微结构,可使涂层材料处于压应力状态下,从而大幅度延长刀具寿命。
采用多层涂层可以获得良好的使用效果。
多层涂层能阻止微裂纹在各层涂层之间扩散,即使有个别涂层出现损坏和剥落,其它的涂层仍可对硬质合金基体起到保护作用。
《钻削与钻头》课件

1. 切削力大
由于钻头需要施加较大的轴向压力才能使钻尖切 入工件材料中,因此切削力较大,易造成刀具磨 损。
3. 制造成本低Байду номын сангаас
钻削所需的设备和工具相对简单,制造成本较低 。
2. 排屑困难
钻头切削过程中产生的切屑需要通过排屑槽排出 ,但排屑槽的尺寸和形状对排屑效果有很大影响 ,排屑不当易导致切屑堵塞或划伤已加工表面。
选择依据
进给量的选择应考虑工件材料的 硬度、钻头的直径和切削深度等
因素。
注意事项
进给量过大可能导致切削力增大 ,进给量过小则可能导致切削效 率低下,应根据实际情况进行选
择。
切削深度的选择
切削深度
切削深度是指钻头在工件上切削的深度,单位为mm。
选择依据
切削深度的选择应考虑工件材料的硬度、钻头的直径和刚性等因素 。
切削速度是指钻头在每分钟内所 完成的进给量,单位为mm/min
。
选择依据
切削速度的选择应综合考虑钻头的 直径、切削深度、工件材料、钻头 材料和冷却方式等因素。
注意事项
切削速度过高可能导致钻头磨损加 剧,切削速度过低则可能导致切削 力增大,影响加工质量和效率。
进给量的选择
进给量
进给量是指钻头每转一圈,钻头 沿轴线移动的距离,单位为 mm/r。
钻削的特点
01
02
03
总结词
钻削具有加工精度高、适 应性强、制造成本低等优 点,但也存在切削力大、 排屑困难等缺点。
详细描述
钻削作为一种常见的金属 切削加工方法,具有以下 优点
1. 加工精度高
第一节 钻削
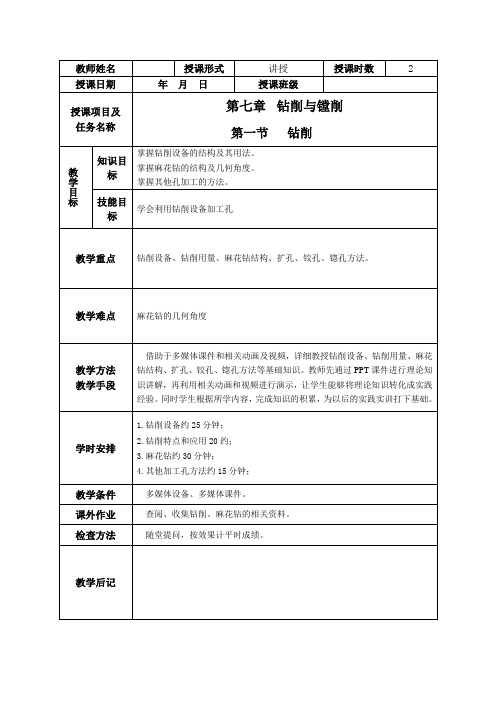
教师姓名授课形式讲授授课时数2授课日期年月日授课班级授课项目及任务名称第七章钻削与镗削第一节钻削教学目标知识目标掌握钻削设备的结构及其用法。
掌握麻花钻的结构及几何角度。
掌握其他孔加工的方法。
技能目标学会利用钻削设备加工孔教学重点钻削设备、钻削用量、麻花钻结构、扩孔、铰孔、锪孔方法。
教学难点麻花钻的几何角度教学方法教学手段借助于多媒体课件和相关动画及视频,详细教授钻削设备、钻削用量、麻花钻结构、扩孔、铰孔、锪孔方法等基础知识。
教师先通过PPT课件进行理论知识讲解,再利用相关动画和视频进行演示,让学生能够将理论知识转化成实践经验。
同时学生根据所学内容,完成知识的积累,为以后的实践实训打下基础。
学时安排1.钻削设备约25分钟;2.钻削特点和应用20约;3.麻花钻约30分钟;4.其他加工孔方法约15分钟;教学条件多媒体设备、多媒体课件。
课外作业查阅、收集钻削、麻花钻的相关资料。
检查方法随堂提问,按效果计平时成绩。
教学后记授课主要内容第一节钻削孔是组成零件的基本表面之一,钻孔经在钻床和车床上进行。
用钻头在实体材料上钻削出盲孔或通孔,并能对已有的孔的进行扩孔的加工称钻孔。
钻孔的公差等级为≤IT10,表面粗糙度Ra为12.5μm一、钻削设备钻孔经常在钻床和车床上进行。
常用的钻床有台式钻床、立式钻床和摇臂钻床。
在车床上钻孔时,工件装夹在卡盘上,钻头安装在尾架套筒锥孔内。
台式钻床放在工作台上的小型立式钻床用于小型零件的小孔加工,一般直径小于12mm手动操作,手动进给,结构简单,使用方便,小巧灵活立式钻床主轴垂直布置,可沿轴线上下移动加工时需移动工件使之与刀具中心线对中,操作不够方便适于中小型工件上的单件、小批生产中,机床整体刚度较好摇臂钻床摇臂可绕立柱回转和升降,主轴箱可在摇臂上作水平移动主轴箱可方便地上下移动和转动,主轴中心(刀具)与加工孔中心很易对中适用单件小批生产中大而重的零件二、钻削的特点、应用与加工步骤由于钻削的精度较低,表面质量不好,所以钻孔主要用于粗加工。
第七章 钻头、铰刀、螺丝攻、铰丝镆

第七章鑽頭、鉸刀、螺絲攻、鉸絲鏌鑽孔加工可說是相當古老的技藝,它係利用鑽頭的旋轉及擠壓入工件而鑽出孔穴的切削加工。
鑽頭可能是早期人類惟發明槌子之後,創造出來的第一件工具。
最早的鑽頭是利用尖狀的燧石,藉著手的扭轉而鑽孔。
人類發明了弓箭之後,就懂得利用鬆的弓弦纏繞在一端帶有尖形燧石的桿或箭上,並藉著頂在下巴的木塊對著桿子的另一端施加壓力,同時也一方面拉動弓而扭轉桿子,這樣就可以產生火花,亦即所謂的鑽木取火。
稍後又發現到如果加上一些如砂之類的磨料,則可在貝殼或石頭上鑽孔。
孔之加工方法可分為(a)利用鑄造、鍛造、或粉末冶金等不產生切屑的孔成形方式,(b)用衝床衝孔,(c)放電加工、雷射、電子束等非傳統式熔解孔的加工,(d)利用鑽頭、鉸刀、搪孔刀具、拉刀、內孔研磨、游離磨料等產生切屑的孔加工。
其中利用鑽床對孔加工仍是最普通的方式,其基本操作如圖7 - 1 示。
本章除搪孔刀具外,就其中加工孔的刀具及切螺紋刀具加以討論。
若將二支直徑相同的鑽頭分別放置在未鑽孔的工件及該鑽頭已鑽出孔的上綠,並且同時做進給運動。
可看出鑽孔加工是將相當於進給的容積變為切屑排出,進而產生孔空問的一種切削方式。
鑽頭施加扭矩與推力至工件,其尖端刃口切除工件,產生的切屑就由鑽槽送出工件表面。
切屑在孩擠出工件表面之前,必然摩擦到鑽槽與鑽出的孔。
鑽頭在鑽入某付深度後會由於切削阻力的加大而產生彎曲,切屑與孔面間的摩擦影響就漸次增大,所以鑽出的孔徑往往比鑽頭大。
彈性復原性較大的材料在鑽孔加工中呈現出顯著的發熱,由於冷卻時發生收圖7 - l 鑽床的基本操作縮的關係,鑽出的孔徑反而小於鑽頭的直徑。
螺紋的基本加工方法,則可由圖7 - 2 得知。
刀具沿著與工件心軸的垂直方向成 角的方向進給,圖中淡黑色V 形三角溝槽為單牙螺紋圖7 - 2 螺紋加工所切除的螺紋槽,亦即將該三角溝槽的原來金屬變為切屑。
故亦可將螺紋加工看作是孔加工的應用。
(一) 鑽頭1. 鑽頭的製造程序製造鑽頭的程序為圓形材料車製外形→銑溝槽→熱處理→研磨外圓→研磨刀刃。
第七章 钻削与镗削(机械制造工艺第5版答案)

第七章钻削与镗削一、填空1、钻头扩孔钻孔钻孔扩孔2、钻头或扩孔钻钻头或扩孔钻的轴向移动3、台式立式摇臂4、立式35 mm 中小型单件、小批量5、刀柄刀体118°55°6、钻头外缘30°钻头中心7、d/2 (D一d)/28、端面沉孔锪削9、镗刀旋转工件或镗刀10、装夹工件纵向、横向进给11、刀架溜板12、IT9~IT7 3. 2~0.8μm二、判断1. ×2.×3、√4.× 5. ×6.√7.√8. ×9.√三、选择1. C2. B.D3. A. B4. C. D 5 .A.B.D 6. C四、名词解释1.用钻头在实体材料上加工孔的方法称为钻孔。
2.用扩孔工具扩大工件孔径的加工方法称为扩孔。
3.用锪削方法加工平底或锥形沉孔称为锪孔。
4.用铰刀从工件孔壁上切除微量金属层,以提高其尺寸精度和减小其表面粗糙度值的方法称为铰孔。
五、简述1.刃磨麻花钻的基本要求有:(1)根据加工材料的材质刃磨出正确的顶角,通常2Kr=116°~118°。
(2)两主切削刃的长度应相等且成直线,与轴线的夹角也应相等。
(3)后角刃磨适当,横刃斜角一般为ψ=50°~55°。
(4)主切削刃、刀尖和横刃应锋利,不允许有钝口、崩刃。
2.手用铰刀的切削部分较长,2Kr很小,定心作用好,铰削时轴向抗力小,工作时较省力,其校准部分只有一段倒锥,为了获得较高的铰孔质量,手用铰刀各刀齿间的齿距在圆周上不是均匀分布的。
机用铰刀的切削部分较短,2Kr较大,其校准部分有圆柱段和倒锥段两段,为了便于制造,机用铰刀各刀齿间的齿距在圆周上等距分布。
3.两个或两个以上在空间具有一定相对位置的孔称为孔系。
常见的孔系有同轴孔系、平行孔系和垂直孔系。
4.车床上车孔的主运动是工件的回转运动,进给运动是车孔刀纵向移动,主要适用于车削回转体工件上的单一孔或同轴孔系。
钻削与钻头8学习.pptx

• 群钻的优点: • 横刃缩短,圆弧刃、内刃上前角平均增大了
15度,使进给力下降了35%-50%,转矩 下降了10%-30%,进给两毕普通麻花钻提 高了约3倍,钻孔效率大大提高。 • 钻头的寿命可以提高2-3倍; • 钻头的定心作用提高,钻孔精度提高,形位 误差与加工表面粗糙度减小; • 选用不同的钻型加工不同的材料均可改善钻 孔的质量,取得满意的效果。 • 圆弧刃切出的过渡表面有凸起的圆环筋,可 以防止钻孔偏斜,减少了孔径的扩大,加强 了定心导向作用,
件,提高钻头寿命,这种适合脆性材料。 三、磨处分屑槽,便于排屑
第17页/共36页
三 修磨前面
目的是为了改变前角的分布,增大或减小前角 或改变刃倾角,用来满足不同的加工要求,
第18页/共36页
常见的修磨方式
一将外缘处磨出倒棱面前面,减小前角,增大 进给力,避免钻孔时引起扎刀;
二是沿切削刃磨出倒棱,增加刃口强度,使用 较硬的才,或是钻削韧性较好的材料以增加 变形,有利于断屑。
第34页/共36页
第35页/共36页
感谢您的观看!
第36页/共36页
• 进给量:一般按下列公式进行估算:
f=(0.01-0.02)d ,合理修磨的钻头可以选
用f=0.03d
第14页/共36页
钻的修磨
缺点:前角从+30°到-30°,横刃长前角-55°, 定心差,轴向力大,刚性差,排屑困难 目的:磨短横刃增大前角,修磨主刃顶角分屑槽
一、修磨横刃
十字形修磨
第15页/共36页
• 枪钻切削部分的一个重要特点是只有单刃切削,钻尖与轴线不在一直线上, 而是偏离了一定距离e,外刃余偏角一般大于内刃余偏角,能够使作用在钻 头上的合力的径向分力始终指向切削部分的导向面,这样就能够保证深孔钻 得到很好的导向作用。
钻头与钻削研究的历史、现状与发展趋势

钻头与钻削讨论的历史、现状与进展趋势人类认得和使用钻头的历史可以上溯到史前时代。
燧人氏“钻木取火”所使用的石钻,可以看作最原始的钻头。
现代工业加工中广泛使用的麻花钻(俗称钻头),是一种形状多而杂的实工件孔加工刀具,诞生于一百多年前。
现在,全世界每年消耗的各类钻头数以亿计。
据统计,在美国的汽车制造业,机械加工中钻孔工序的比重约占50%;而在飞机制造业,钻孔工序所占的比重则更高。
尽管钻头的使用如此广泛,但众所周知,钻削加工也是最多而杂的机械加工方法之一。
正由于如此,人们一直致力于钻头的改进和钻削过程的讨论。
本文依据所能得到的英文文献资料,对两沟槽麻花钻的有关技术问题及钻削讨论的历史、现状和进展趋势进行综述。
1.讨论的重要领域和技术问题近几十年来,人们关于钻头和钻削的讨论除了钻头制作材料的改进以外,重要集中在以下五个方面:①钻头数学模型和几何设计讨论:包括螺旋沟槽、后刀面、主刃和横刃数学模型的建立,横向截形与钻尖结构参数的优化,切削角度(分布)的计算与掌控,钻头结构的静态和动态特性分析,钻尖几何形状与切削和排屑性能关系的讨论。
②钻头制造方法讨论:包括钻头几何参数与后刀面刃磨参数之间关系的建立与优化,钻头制造精度和刃磨质量的评价与制造误差的测控,钻头螺旋沟槽加工工具截形的设计计算,钻头加工设备特别是数控磨床与加工软件的开发等。
③钻削过程与钻削质量讨论:包括影响钻削过程的各种因素及显现的各种物理现象的分析、建模与监控(如钻削力、切削刃应力和温度分布的测量、建模和预报);钻头磨损、破损机理与钻头寿命的讨论;钻头的变形、偏斜、入钻时的打滑和钻尖摇摆现象的讨论;钻削工艺(如振动钻削、高速钻削、深孔钻削、钻削过程的稳定性等)与钻削质量(孔的位置精度、直线度、表面粗糙度、圆柱度、直径、孔口毛刺等)的讨论。
④钻削机理与各种高性能钻头(如群钻、枪钻、干切削钻头、微孔、深孔钻头、长钻头、可转位钻头、合成材料加工用钻头、木工钻头、多螺旋槽钻头等)的讨论。
第七章 钻削与钻头

2)可在车、钻、镗床上使用,操作方便,钻孔效 率高。 3)由于钻杆内还有一层内管,排屑空间受到限制, 较难用于小直径。加工精度略低于BTA钻头。
第五节 深 孔 钻
三、喷吸钻
1—工件 2—夹爪 3—中心架 4—引导架 5—向导管 6—支持座 7—连接套 8—内管 9—外管 10—钻头
第五节 深 孔 钻
第一节 麻 花 钻
二、麻花钻的几何角度 5、 几何角度小结
第二节 钻削原理
一、切削用量与切削层参数 1.钻削用量
钻削背吃刀量(mm)
ap d / 2
每刃进给量(mm/z)
钻削速度(m/min)
fz f /2
v( dn )/1000
2.切削层参数
钻削厚度(mm) 钻削宽度(mm)
h fsin( / 2 ) D
第三节 钻头的修磨
一、修磨横刃 1、目的 在保持钻尖强度的前提下,尽可能增大钻尖部分 的前角、缩短横刃的长度,降低进给力,提高钻尖定 心能力。 2、两种较好的修磨形式
a)加大横刃前角
b)磨短横刃并加大前角
第三节 钻头的修磨
二、修磨主切削刃 ——改变刃形或顶角,以增大前角,控制分屑断屑。
a) 磨出内凹圆弧刃
第二节 钻削原理
二、钻削过程特点 2.钻削力 钻头每一切削刃都产生切削力,包 括切向力(主切削力)、背向力(径向 力)和进给力(轴向力)。当左右切削 刃对称时,背向力抵消,最终构成对钻 头影响的是进给力Ff 与切削转矩Mc。 钻削力实验公式:
F C d f f F f
zF yF f f
K F f
思考题:
1.试述孔加工刀具的类型及其用途。 2.作图表示麻花钻结构、标注结构参数与 刃磨角度。 3.分析麻花钻前角、后角、主偏角及端面 刃倾角的变化规律。 4.为什么要对麻花钻进行修磨?有哪些修磨 方法?
第7章 钻削与钻头

主切削刃在端面中的投影与通过该点基 端面中的投影与通过该点 端面刃倾角λst:主切削刃在端面中的投影与通过该点基 面之间的夹角。 之间的夹角。
d0 sinλtx = dx
d0钻心直径,dx以钻心为直径,以钻 钻心直径, 以钻心为直径, 心到x点距离为半径圆的直径。 心到 点距离为半径圆的直径。 点距离为半径圆的直径
2、进给量 f=(0.01~0.02)d 、 3、钻削速度 表7-4选择。 、 选择。 选择
第7章 钻削与钻头 章
复习 1、切削部分 、
主切削刃为前、后面汇交的区域。 主切削刃为前、后面汇交的区域。横刃位于两个主后面汇 为前 交的区域。副切削刃是两条刃沟与刃带棱面汇交的两条螺 交的区域。副切削刃是两条刃沟与刃带棱面汇交的两条螺 旋线。 旋线。
第7章 钻削与钻头 章
(3) 钻头刃带无后角,与孔壁摩擦。加 钻头刃带无后角,与孔壁摩擦。 工塑性材料容易产生积屑瘤。 工塑性材料容易产生积屑瘤。
2、钻削力 、
每一个切削刃都产生切削力,包括切向 每一个切削刃都产生切削力,包括切向 主切削力)、 径向力)和进给力 力(主切削力 、背向力 径向力 和进给力 主切削力 背向力(径向力 (轴向力 。 轴向力)。 轴向力 主切削刃 进给力F 进给力 f 40% 扭矩Mc 80% 横刃 57% 8% 刃带 3% 12%
第7章 钻削与钻头 章
7.2 钻削原理
一、钻削用量与切削层参数 πdn 切削速度v 切削速度 v= 1000
v-钻头外径处主运动速度;d-钻头外 钻头外径处主运动速度; 钻头外 钻头外径处主运动速度 钻头或工件的转速。 径;n-钻头或工件的转速。 钻头或工件的转速 进给量f: 进给量 :钻头每转一转沿进给 方间移动的距离。 方间移动的距离。 每齿进给量f 每齿进给量 z:麻花钻每转过 一个刀齿, 一个刀齿,它与工件的相对位 移。 fz=f / 2
Chapter7铣削与钻头ppt32

3、钻削用量选择
(1)钻头直径
由工艺尺寸决定,尽可能一次钻出所要求的 孔。
当机床性能不能胜任时,采用先钻孔再扩孔 的工艺。需扩孔者,钻孔直径取孔径的 50%~70%。
3、钻削用量选择
(2)进给量 钻头进给量受钻头的刚性与强度限制。大直径钻
1、修磨横刃
修磨横刃的目的:在保持钻尖强度的前提下, 尽可能增大钻尖部分的前角、缩短横刃的长 度,以降低进给力,提高钻尖定心能力。
横刃的修磨有十字形修磨和內直刃形修磨两 种形式。
1、修磨横刃
(1)十字形修磨
横刃磨出十字形,长度不变,刃 倾角仍为零,但显著增大了横刃 前角。
这种修磨形式方法简单,使用机 床夹具修磨时,调整参数少。但 钻芯强度有所减弱,并要求砂轮 圆角半径较小。
当左右切削刃对称时,背向力抵消,
最终构成钻头的进给力Ff与切削扭 矩Mc。
进给力
Ff
CFf d zFf
f
K yFf Ff
扭矩
Mc
CMc d zMc
f
K yMc Mc
切削消耗功率
pc
M cvc 30d
图7.4 钻削力
2、钻削过程特点
(3)钻头磨损特点
磨损过程与规律与车刀同。
钻头切削刃各点负荷不均, 外圆周切削速度最高,因此 磨损最为严重。
钻孔时切削层参数包括:
钻削厚度hDfsin/2 钻削宽度bDd/(2sin)
每刃切削层公称横截面积 ADdf/4
图7.3 钻削用量与切削层参数
2、钻削过程特点
(1)钻削变形特点与切屑形状
钻削轴向力大。钻心处切削刃前角为负,特 别是横刃区,切削时产生刮削挤压。钻心区 域直径几乎为零,切削速度也接近为零,但 仍有进给运动,相当于用凿子劈入工件。
6 第六章 钻削与钻头

后角越大 刀具越锋利
(3)横刃斜角
横刃斜角:在端平面度量的中剖面与横刃的钝夹角
横刃斜角与后角
横刃斜角与后角相关
?
控制后角即可通过控制横刃斜角 实现; 横刃斜角便于测量; 控制横刃斜角本质是控制后角。
刃磨钻头后面时,需控制中心部位后角。 越接近中心,后角越大。 原因1 获得较大的前角 原因2 补偿径向各点工作后角变化量, 保证各点基本一致。
运动、十九世纪自然科学的发展
二、BTA深孔钻
可加工D=18-185,L/D≺100的孔
三、喷吸钻
加 工 中 等 直 径 深 孔
作业
7-4 7-8 7-12
END
END
7.3.3 前面的修磨
7.3.4 修磨后面
7.4 先进钻型与结构特点
群钻基本特 征
三尖七刃锐当先, 月牙弧槽分两边, 一侧外刃开屑槽, 横刃磨得低窄尖.
1953年,在北京永定机械厂当钳工的倪志福勇 于创新,发明了后来被称为“倪志福钻头”的 新型麻花钻。这种钻头的加工效率比普通麻花 钻大大提高,倪志福本人因此成为“劳动模范” 并参加了第二次全国青年社会主义建设积极分 子大会和全国工业、财贸系统群英会。1963年 倪志福与北京工业大学于启勋教授及周淑英、 王育民合著的第一本“倪志福钻头”一书出版。
为了与世界接轨,统一名称,倪志福、陈壁 光在1999年出版的“群钻、倪志福钻头”一 书中建议更名为“多刃尖(Multifork drill)钻 头”。 群钻的显著特点: 三尖七刃锐当先、 月牙弧槽分两边, 侧外刃再开槽, 横刃磨低、窄又尖
7.4 先进钻型与结构特点
S 型 横 刃 钻
可转位浅孔钻(L/D=3孔)
钻削加工与钻头

钻削、铰削与镗削加工
第一节 钻削加工与钻头
第一节 钻削加工与钻头
一
一
麻花钻的结构 钻削加工的工艺特点
二
本 节 教 学 内 容
三
四 五
钻削用量
钻削力 其它钻头
第一节 钻削加工与钻头
本节教学要求:
(1)熟悉钻削过程特点及钻削用量的选择;
本 节 教 学 要 求
(2)掌握钻削力的计算。 (3)熟悉麻花钻的组成、结构参数、几何角度; (4)了解其它钻头特点。
麻 花 钻 的 结 构
tan x
P
P r
r
tan
增大螺旋角有利于排屑 ,能获得较大前角使切削轻 快,但钻头刚性变差。小直 径钻头,为提高钻头刚性,β 角可设计得小些。钻软材料 、铝合金时,为改善排屑效 果,β角可设计得大些。
3.麻花钻几何角度 车刀刀具角度各参考坐标 系坐标平面均可在钻头上应用。 此外,由于钻头结构的特殊性, 麻 还规定了三个测量平面,即 花 (1)端平面Pt 钻 的 与钻头轴线垂直的端 结 面投影平面。 构 (2)中剖面Pc 过钻头轴线与两主切 削刃平行的平面。
钻削力的计算
通过测力实验,可得经验计算公式如下:
Ff CF d
钻 削 力
xF
f v
f
yMc
yF
zF c
M c CM c d
xM c
zM c vc
由上式计算出转矩后,可计算切削消耗功率Pc。
Pc 2M c n103
式中 Mc——转矩,单位为N· mm; n——转速,单位为r/min。
3.麻花钻几何角度 (2)后角αfx
钻头的后角是过主切削刃 上某选定点x在柱剖面内测量的
- 1、下载文档前请自行甄别文档内容的完整性,平台不提供额外的编辑、内容补充、找答案等附加服务。
- 2、"仅部分预览"的文档,不可在线预览部分如存在完整性等问题,可反馈申请退款(可完整预览的文档不适用该条件!)。
- 3、如文档侵犯您的权益,请联系客服反馈,我们会尽快为您处理(人工客服工作时间:9:00-18:30)。
第四节
先进钻型与结构特点简介
六、可转位浅孔钻
使用硬质合金可转位刀片—— 可高速、大进给切削,效率高。
第五节
深 孔 钻
* 深孔加工概念:长径比L/D>5的孔为深孔。 一般L/D=5~10的深孔可用深孔麻花钻加工, L/D >20则必须使用深孔刀具。
* 深孔加工的难点:
①不能观测到切削情况 ②切削热不易传散 ③孔易钻偏斜 ④刀柄细长、刚度差、易振动
a)
手虎钳
b) 机床用平口虎钳 c) V形块 d) 压板、螺钉
第六节
钻削方法及特点(补充)
(2)钻孔方法及注意事项
1).在斜面上钻孔时,需先用铣刀铣出平台后再钻孔 2).钻半圆孔时,需将两件对合起来钻孔 3).钻不通孔时,要按钻孔深度调整好挡铁来控制孔深 4).对直径大于30mm的孔,一般分两次钻 5).孔即将钻穿时,此时须减小进给量 6).在钻深孔时,需经常退出钻头将切屑排除 7).钻孔时,需用切削液充分冷却
第一节
麻 花 钻
二、麻花钻的几何角度 3、横刃角度分析
sin(180 )
1 tan tan o
结论:横刃斜角、顶角钻心后角相互制约……
第一节
麻 花 钻
二、麻花钻的几何角度 4、 主切削刃角度分析 钻头切削刃各 点的螺旋角、刃倾 角、前角主偏角都 是不同的,其换算 关系详见表7-1。
第二节
钻削原理
二、钻削过程特点 2.钻削力 钻头每一切削刃都产生切削力,包 括切向力(主切削力)、背向力(径向 力)和进给力(轴向力)。当左右切削 刃对称时,背向力抵消,最终构成对钻 头影响的是进给力Ff 与切削转矩Mc。 钻削力实验公式:
Ff C F f d
zF f
f
yF f
K Ff
KMc
详见表7-3
* 深孔加工刀具必须解决的问题:
1)排屑 2)冷却、润滑 3)导向
a)单刃外排屑小深孔钻
b)错齿内排屑深孔钻
c)不重磨内排屑深孔钻 d)喷吸钻 e) 外排屑机夹套料钻 f)不通孔套料刀 g) 机夹单刃内排屑深孔镗 刀 h)小深孔拉铰刀 i)深孔滚压头
常用深孔刀具外形结构图
第五节
一、枪孔钻
深 孔 钻
BTA深孔 钻特点:无横 刃、内外切削 刃余偏角不等、 有钻头偏距切 削刃分段、交 错排列,保证 可靠分屑和断 屑,外缘刀片 耐磨性好,中 心韧性好。
BAT深孔钻
第五节
三、喷吸钻
深 孔 钻
——BAT深孔钻+喷吸排屑装置 喷吸钻的特点: 1)不需要BTA系统的高压输油器及密封装置。不但 提高了排屑效果,又改进了工作条件。
M c CM c d zM c f
yM c
第二节
钻削原理
二、钻削过程特点 3.钻头磨损特点
高速钢钻头磨损的主要原因是相变磨损。外圆周切削速度最高, 因此磨损最为严重。钻头磨损的形式主要是后面磨损。
第二节
钻削原理
三、钻削用量选择 1、钻头直径
2、进给量
经验公式估算
f (0.01 ~ 0.02 )d
b) 磨出双重或多重顶角
c) 磨出分屑槽
第三节
钻头的修磨
三、修磨前面 ——增大或减小前角,改变前角分布,改变刃倾角。
a) 磨出倒棱面前面 b) 磨出倒棱 c) 磨出卷屑槽 d)磨出大前角及正的刃倾角
第三节
钻头的修磨
四、修磨后面 ——增大后角,增大钻槽容屑空间,改善冷却。
——以上修磨形式,实际生产中通常同时选择两到三种组合使用。
第一节
麻 花 钻
一、麻花钻的结构 1、麻花钻组成 由柄部、颈部、工作部分组成。柄部包 括钻柄和颈部,钻柄供装夹用。工作部分又 分为切削部分和导向部分。导向部分在钻孔 时起引导钻头方向和修光孔壁的作用,同时 还是切削部分的备磨部分。
第一节
麻 花 钻
一、麻花钻的结构 2、麻花钻的结构参数
(1)直径d (2)直径倒锥 (3)钻芯直径d0 (4)螺旋角ω
深 孔 钻
* 配备DF系统的深孔钻
第六节
1.扁钻
钻削方法及特点(补充)
使用最早的钻孔工具,结构简单、刚性好、成本低、刃磨 方便。 2.中心钻 三种结构形式:带护锥中心钻,无护锥中心钻和弧形中心 钻(见后图)。 3.麻花钻 最广泛应用的孔加工工具。适应性较强、成熟的制造工艺 及完善的刃磨方法。 4.深孔钻 孔深与孔径之比大于5~10倍的孔称为深孔。
第一节
麻 花 钻
二、麻花钻的几何角度 5、 几何角度小结
第二节
钻削原理
一、切削用量与切削层参数 1.钻削用量
钻削背吃刀量(mm)
ap d / 2
每刃进给量(mm/z)
钻削速度(m/min)
fz f / 2
v (dn) /mm) 钻削宽度(mm)
hD f sin( / 2)
思考题:
1.试述孔加工刀具的类型及其用途。 2.作图表示麻花钻结构、标注结构参数与 刃磨角度。 3.分析麻花钻前角、后角、主偏角及端面 刃倾角的变化规律。 4.为什么要对麻花钻进行修磨?有哪些修磨 方法?
2rx rx tan x tan ( ) L r
上式表明:钻头越靠近中心处螺旋角越小。增大螺旋 角使前角增大,有利于排屑,使切削轻快,但钻头刚 性变差。
第一节
麻 花 钻
二、麻花钻的几何角度 1、钻头角度的参考系
增加测量平面: (1)端平面pt (2)中剖面pc (3)柱剖面pz
第一节
第六节
钻削方法及特点(补充)
三种结构形式:
带护锥中心钻 图a)
无护锥中心钻 图b) 弧形中心钻 图c)
a) 带护锥中心钻
b) 无护锥中心钻
c) 弧形中心钻
第六节
钻削方法及特点(补充)
一、钻削的方法 1.在钻床上的钻孔
(1)工件装夹 根据工件形状常选用手虎钳、机床用平口虎钳、V形块和压 板、螺钉等辅助工具来装夹。
第四节
一、群钻
刃形特点: 三尖七刃
先进钻型与结构特点简介
第四节
一、群钻 优点:
先进钻型与结构特点简介
1)横刃长度短、圆弧刃和内刃前角增大,使进给力 和扭矩减小,效率提高; 2)寿命长; 3)定心作用好,使钻孔精度和表面质量提高; 4)不同钻型用于不同材料和不同工艺加工,改善了 钻孔质量。
第四节
麻 花 钻
二、麻花钻的几何角度 2、钻头的刃磨角度
普通麻花钻只 需刃磨两个后面, 控制三个角度: (1)顶角2φ (2)外缘后角αf (3)横刃斜角ψ
第一节
麻 花 钻
二、麻花钻的几何角度 2、钻头的刃磨角度
——越靠近钻头中心,后角磨得越大: (1)使横刃获得较大前角,增加其锋利程度; (2)使切削刃各点的工作后角差较小。外缘后角αf
先进钻型与结构特点简介
二、S形横刃钻
——钻尖处顶角 较小,横刃前角 较大,因此定心 精度性能好,进 给力小。
第四节
先进钻型与结构特点简介
三、深孔麻花钻
四、手用通用型钻头
深孔麻花钻
手用通用型钻头
第四节
先进钻型与结构特点简介
五、硬质合金钻 硬质合金钻头应用广泛,结构基本上与高速钢钻 头相同,相应差别主要有: 1)硬质合金刀具要求较小的前角,相应的β角也 要小。 2)硬质合金刀具要求较高的刚度和强度,均修磨, 容屑槽较宽。 3)硬质合金钻头本身备磨量较高速钢钻头少得多, 工作部分长度较短。 4)用加强锥柄,以保证可靠的工作,倒锥较大。
钻削方法及特点(补充)
2.锥柄钻夹头
内外表面都是锥体,称为钻套。
1—内锥孔
2—外圆锥
3—扁尾
第六节
钻削方法及特点(补充)
3.其他钻夹头
(1)自动退卸钻头装置
1—主轴 2—挡圈 3—螺钉销 4—横销 5—外套 6—垫圈 7—硬橡胶垫 8—导向套 9—主轴箱 10—弹簧 11—钻头
第六节
钻削方法及特点(补充)
bD d / 2 sin
fd 2 n Q 250 vc df 4
公称横截面积/ 齿(mm2) AD df / 4
材料切除率(mm3 /min)
第二节
钻削原理
二、钻削过程特点 1.钻削变形特点与切屑形状
钻削在半密闭空间内进行,横刃的切削角度不理想,故切削变 形较为复杂: 1)钻心处切削刃前角为负——刮削挤压,切屑呈粒状并被压碎; 2)钻心横刃区域工作后角为负——楔劈挤压,轴向力增加; 3)主切削刃各点前角、刃倾角不同——使切屑变形、卷曲、流 向也不同,排屑困难; 4)钻头刃带无后角——加工塑性材料容易产生积屑瘤。
(2)快换钻夹头的用途及构造
快换钻夹头 1—钢珠 2—滑环 3—可换套 4—弹簧环 5— 夹头体
拆卸钻头 1—斜铁 2—主轴 3—钻头
第六节
拆卸方法:
钻削方法及特点(补充)
①将斜铁放钻床主轴圆弧孔内,贴紧锥钻扁尾的斜角部分。 ②用锤子锤击斜铁即可。
注意:
①将半圆弧一边放在上面,否则会将钻床半圆弧孔打坏。 ②拆卸前,在工件或工作台上要垫木块,防钻头掉下打坏 工件或工作台。
3、钻削速度
表7-4 高速钢钻头钻削速度 加工材料 低碳钢 中高碳钢 20~25 合金钢 15~20 铸钢 20~25 铝合金 40~70 铜合金 20~40
钻削速度/(m/min) 25~30
第三节
钻头的修磨
概念: 普通钻头按不同的加工要求对横刃、主刃、后刀 面进行附加的刃磨。 麻花钻的修磨原因: 1)改善本身的结构缺陷; 2)切削刃部分变钝; 3)在钻削不同工件材料时,麻花钻切削部分的 角度和形状都略有不同。
第七章 钻削与钻头
麻花钻 钻削原理 钻头的修磨 先进钻型与结构特点简介 深孔钻