机械制造业--钻削、铰削与镗削加工
机械制造技术基础总结

机械制造技术基础总结机械制造技术基础第一章重点车削加工:工件旋转作主运动,车刀作进给运动的切削加工方法称为车削加工。
铣削加工:铣刀旋转作主运动,工件作进给运动的切削加工方法称为铣削加工。
刨削加工:刀具的往复直线运动为主切削运动,工作台带动工件作间歇的进给运动的切削加工方法称为刨削加工。
钻削加工:钻削是用钻头、铰刀或锪刀等工具在材料上加工孔的工艺过程。
刀具(钻头)是旋转运动为主切削运动,刀具(钻头)的轴向运动是进给运动。
镗削加工:镗削是用镗刀对已经钻出、铸出的孔作进一步加工,通常镗刀旋转做主运动,工件或镗刀直行作进给运动。
磨削加工:用砂轮或涂覆模具以较高的线速度对工件表面进行加工的方法成为磨削加工,主运动是砂轮的旋转。
成形法:成形法是用与被切削齿轮的齿槽线截面形状相符的成型刀具切出齿形的方法,所使用的机床一般为普通机床,刀具为普通铣刀,需要两个简单的成形运动:道具的旋转运动(主切削运动)和直线移动(进给运动)。
展成法:展成法是利用齿轮刀具与被切齿轮保持啮合运动的关系而切出齿形的方法,常用机床有滚齿机、插齿机等,常用加工法有滚齿法、插齿法、磨齿法、剃齿法等。
内传动链:有准确传动比的连接一个执行机构和另一个执行机构之间的传动链。
展成传动链和差动传动链为内联系传动链。
课本P26外传动链:是动力源与执行机构之间或两个执行机构之间没有准确传动比要求的传动链。
速度传动链和轴向进给传动链为外联系传送链。
课本P26表面成型运动:表面成形运动是指在切削加工中刀具与工件的相对运动,可分解为主运动和进给运动。
(来自百度)滚齿原理?滚齿属于展成法加工,用齿轮滚刀在滚齿机上加工齿轮的轮齿,它是按一对螺旋齿轮相啮合的原理进行加工的。
滚齿时的运动主要有:(1)主运动。
主运动是指滚刀的高速旋转。
(2)分齿运动(展成运动)。
分齿运动是指滚刀与被切齿轮之间强制的按速度比保持一对螺旋齿轮啮合关系的运动。
(3)垂直进给运动。
为了在齿轮的全齿宽上切出齿形,齿轮滚刀需要沿工件的轴向作进给运动。
机械制造技术基础4.3钻、铰、镗和拉削加工

6.2 钻削加工
(2)标准高速钢麻花钻的修磨改进方法 1)修磨横刃
6.2 钻削加工
2)修磨前面
3)修磨切削刃
6.2 钻削加工
4)磨出分屑槽
6.2 钻削加工
5)综合修磨
6.2 钻削加工
2.深孔钻 深孔一般指深径比L/d>5~10的孔,必须使用特殊结构的深 孔钻才能进行加工。深孔加工相对普通孔来说,加工难度更 大,技术要求更高,这是深孔加工的特点决定的。其特点如 下:第一、孔的深径比大,钻杆细长,刚性差,工作时易产 生偏斜和振动,因此孔的精度和表面质量难以控制;第二、 排屑通道长,若断屑不好,排屑不畅,可能由于切屑堵塞而 导致钻头破坏;第三、钻头在接近封闭的状态下工作,而且 时间较长,热量大且不易散出,钻头极易磨损。 基于深孔加工的上述特点,设计和使用深孔钻时应注意钻 头的导向、防止偏斜;保证可靠的断屑和排屑;采取有效 的冷却和润滑措施。
6.2 钻削加工
钻削加工是用钻头或扩孔钻在工件上加工孔的方法。其 中用钻头在实体材料上加工孔的方法称为钻孔。钻孔在机械 制造中占有较大的比重,因受钻头结构和切削条件的限制, 加工孔的质量不高,故用于孔的粗加工。
一、钻床
钻床主要是用钻头在实体材料上钻孔,还可以进行扩孔、 铰孔、攻螺纹、锪沉头孔、锪端面等,如图6-1所示。
第六章 钻、铰、镗和拉削加工
本章要点
钻削加工 铰削加工 镗削加工 拉削加工
6.1 概述
钻削、铰削、镗削和拉削加工在机械加工中主要用来进 行孔的加工。它是用相应机床在加工实体材料上钻孔和扩大 已有的孔,并达到一定技术要求的加工方法。
一、孔的类型
按照孔与其他零件的相对连接关系的不同,可分为配合 孔与非配合孔; 按其几何特征的不同,可分为通孔、盲孔、阶梯孔、锥孔 等; 按其几何形状不同,可分为圆孔、非圆孔等。
05第五章 钻削、镗削、铰削与拉削
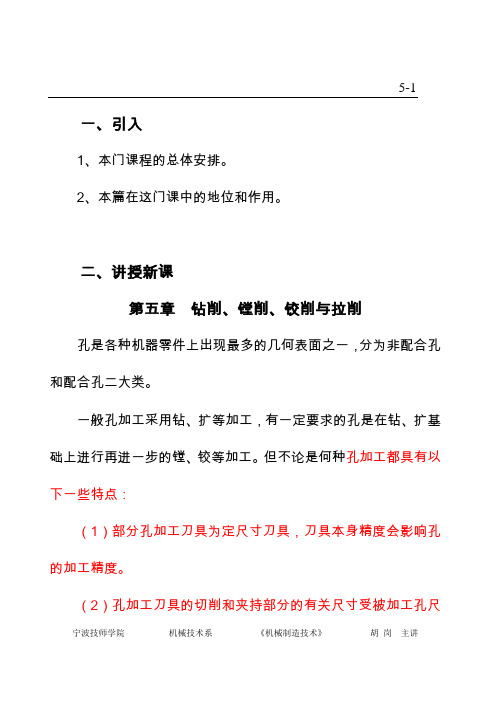
5-1一、引入1、本门课程的总体安排。
2、本篇在这门课中的地位和作用。
二、讲授新课第五章钻削、镗削、铰削与拉削孔是各种机器零件上出现最多的几何表面之一,分为非配合孔和配合孔二大类。
一般孔加工采用钻、扩等加工,有一定要求的孔是在钻、扩基础上进行再进一步的镗、铰等加工。
但不论是何种孔加工都具有以下一些特点:(1)部分孔加工刀具为定尺寸刀具,刀具本身精度会影响孔的加工精度。
(2)孔加工刀具的切削和夹持部分的有关尺寸受被加工孔尺寸的限制,会使刀具的刚性变差。
(3)孔加工时,刀具一般是封闭或半封闭状态下进行工作,对加工质量和刀具耐用度都会产生不利的影响。
宁波技师学院机械技术系《机械制造技术》胡岗主讲5-2 基于以上原因,在机械设计过程中选用孔和轴配合的公差等级时,经常把孔的公差等级定得比轴低一级。
孔加工的方法很多,常用的有钻孔、扩孔、锪孔、铰孔、镗孔、拉孔、磨孔等,还有金刚镗、珩磨、研磨、挤压及特种加工孔等方法。
其加工孔直径Φ0.01~Φ1000mm,加工精度可达到IT13~IT5,表面粗糙度Ra12.5~0.006μm;可在金属或非金属材料上加工,也可在普通材料或高硬度材料上加工。
在加工中可根据不同要求,合理进行选择最佳的加工方案,达到加工质量能符合要求。
第一节钻削加工(一)一、概述用钻头作回转运动,并使其与工件作相对轴向进给运动,在实体工件上加工孔的方法称为钻孔;在已有孔的情况下,用扩孔钻对孔径进行再扩大的加工称为扩孔;钻孔与扩孔统称为钻削。
钻削可以在各种钻床上进行,也可以在车床、铣床、镗床和组宁波技师学院机械技术系《机械制造技术》胡岗主讲5-3合机床、加工中心上进行,但大多数情况下,尤其是在大批量下生产时,主要还是在钻床上进行。
二、钻床主要用钻头在工件上加工孔的机床称为钻床。
通常以钻头的回转运动为主运动,钻头的轴向移动为进给运动。
钻床的分类:坐标镗钻床、深孔钻床、摇臂钻床、台式钻床、立式钻床、卧式钻床、铣钻床、中心孔钻床等八大类。
(课件) 钻削、铰削和镗削加工
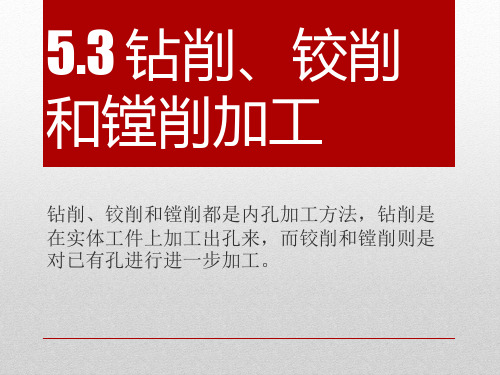
钻套 钻模板
工件
钻头切 削部分
5个刀刃 6个刀面
两条主切削刃 两条副切削刃 一条横刃
两个螺旋形前刀面 两个经刃磨获得的后刀面 两个圆弧段的副后刀面
钻削要素
• 切削速度:钻头外圆处的线速度。vc=πd0n/1000 • 进给量f:钻头或工件每转一转,它们之间的轴向相
5.3 钻削、铰削 和镗削加工
钻削、铰削和镗削都是内孔加工方法,钻削是 在实体工件上加工出孔来,而铰削和镗削则是 对已有孔进行进一步加工。
孔加工的不同方法和特点
• 孔: 连接关系:配合孔、非配合孔 几何特征:通孔、盲孔、阶梯孔、锥孔 几何形状:圆孔、非圆孔 • 孔加工方法: 从实体上加工出孔; 对已有孔进行半精或精加工; • 非配合孔用钻削加工,需要精加工的孔一般在钻削后
多刃镗刀(定尺寸刀具)
固定式:用于粗镗或半精镗 直径大于40mm的孔。 可调浮动式:采用一定结构 可以调整两刀刃之间的距离, 从而是一把刀具可以加工不 同直径的孔。加工质量高、 生产效率高成本高,适用于 批量生产、精加工箱体类零 件上直径加大的孔。
钻床
• 一般用于加工尺寸比较小、精度要求不太高的孔。它 可以进行钻孔、扩孔、铰孔及攻螺纹等加工。
铰刀的主要几何参数
• 前角:加工余量小,前角基本不起作用,一般等于 0°,韧性较大的材料,为了减小变形可取5°~10°
• 后角:为了避免重磨后刀面导致直径尺寸变化,后角 尽量取小。
• 主偏角:过大→切削部分短,定位精度差。过小→铰 韧性材料时产生过大的切屑变形。
• 手用铰刀→较小的主偏角,机用铰刀→大主偏角。 • 铰韧性材料→kr=12~15°,铰脆性材料→kr=3~5° • 粗铰→kr=45°
钻削、铰削与镗削加工
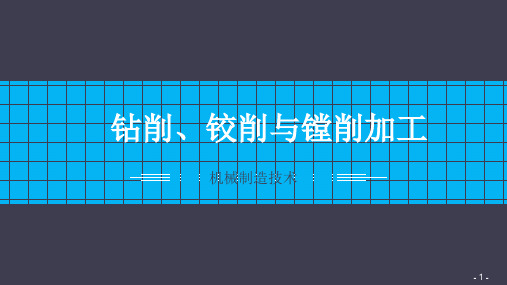
- 17 -
6.2 铰削加工与铰刀
二、铰刀的结构
铰刀由柄部、颈部和工作部组成。工作部包括切削部分和校准部分。切削部分担任主要的切削工作,校准部分起导向、 校准和修光作用。为减少校准部分刀齿与已加工孔壁的摩擦,并防止孔径扩大,校准部分的后端为倒锥形状。
- 26 -
6.4 钻床与镗床
2. 摇臂钻床 摇臂钻床是摇臂绕立柱回转和升降、主轴箱在摇臂上作水平移动的钻床。
其结构如图6.17 所示,大、中型工件上的孔通常采用摇臂钻床加工。在加工时, 工件在底座(或工作台)上安装固定,通过调整摇臂和主轴箱的位置来对正被 加工孔的中心。摇臂钻床广泛用于大、中型零件的加工。
- 11 -
6.1 钻削加工与钻头
- 12 -
6.1 钻削加工与钻头
2. 可转位浅孔钻 图6.5 所示为硬质合金可转位浅孔钻。它是20 世纪70 年代末出现的新型钻头,适合在车床上加工 d = 17.5 ~ 80 mm、l / d
≤ 3 的中等直径浅孔。
- 13 -
6.1 钻削加工与钻头
3. 错齿内排屑深孔钻 错齿内排屑深孔钻是常用的深孔加工钻头。工作时钻头与钻杆连接,通过刀架带动经液封头钻入工件。通过刀齿的交错排
切削部分的刀齿没有刃带,校准部分刀齿则留有0.05 ~ 0.3 mm 宽的刃带,以起修光和导向作用,也便于铰刀制造和检验。 (2)切削锥角2Φ
主要影响进给抗力的大小、孔的加工精度和表面粗糙度以及刀具耐用度。2Φ 取得小时,进给力小,切入时的导向性好; 但由于切削厚度过小产生较大的切削变形,同时切削宽度增大使卷屑、排屑产生困难,并且切入切出时间增长。
机械制造工艺 第六章 钻削与镗削讲解

立式钻床
第六章 钻削与镗削
摇臂钻床
1—立柱座 2—立柱 3—摇臂 4—主轴 5—工作台 6—底座
第六章 钻削与镗削
2.钻床的主要工作内容
钻孔
扩孔
铰孔 攻螺纹
锪孔 刮平面
第六章 钻削与镗削 二、钻床上常用的夹具和工具
(1)钻夹头与钻钥匙
第六章
(2)过渡锥套
钻削与镗削
(3)平口虎钳
第六章 钻削与镗削
第六章 钻削与镗削
1 第一节 钻削 2 第二节 镗削
第六章 钻削与镗削
第一节 钻削
钻削——用钻头或扩孔钻在工件上加工孔的方法。 包括用钻头在实体材料上加工孔的钻孔和用扩孔钻扩大
已钻出(或制出)孔的 孔径的扩孔。
主运动:钻头或扩孔钻的回转运动。 进给运动:钻头或扩孔钻沿自身轴线方向的运动。
第六章 钻削与镗削
用刃磨不正确的麻花钻钻孔 a)顶角不对称 b)主切削刃长度不等 c)顶角和刃磨长度不对称
第六章 钻削与镗削
2.扩孔工具
麻花钻 扩孔钻 :高速钢扩孔钻、硬质合金扩孔钻。
扩孔钻 a)高速钢扩孔钻 b)硬质合金扩孔钻
第六章 钻削与镗削
3.铰刀
(1)工作部分 由引导锥、切削部分和校准部分组成。 (2)颈部 在铰刀制造和刃磨时起空刀作用。 (3)柄部 铰刀的夹持部分,铰削时用来传递转矩, 有直柄和锥柄(莫氏标准圆锥)两种。
麻花钻不像单刃刀具那样容易弯曲。 金属切除率较高。 钻孔的表面粗糙度值较大。 冷却条件差,切削温度高,影响了生产率。 钻削为粗加工,其加工经济公差等级为IT13~IT11,表
面粗糙度值Ra为50~12.5μm,一般用于要求不高的孔的 加工或高精度孔的预加工。
钻削、铰削、镗削和拉削加工79页PPT

26、机遇对于有准备的头脑有特别的 亲和力 。 27、自信是人格的核心。
28、目标的坚定是性格中最必要的力 量泉源 之一, 也是成 功的利 器之一 。没有 它,天 才也会 在矛盾 无定的 迷径中 ,徒劳 无功。- -查士 德斐尔 爵士。 29、困难就是机遇。--温斯顿.丘吉 尔。 30、我奋斗,所以我快乐。--格林❖ 丰富你的人生
71、既然我已经踏上这条道路,那么,任何东西都不应妨碍我沿着这条路走下去。——康德 72、家庭成为快乐的种子在外也不致成为障碍物但在旅行之际却是夜间的伴侣。——西塞罗 73、坚持意志伟大的事业需要始终不渝的精神。——伏尔泰 74、路漫漫其修道远,吾将上下而求索。——屈原 75、内外相应,言行相称。——韩非
钻削、铰削、镗削和拉削加工
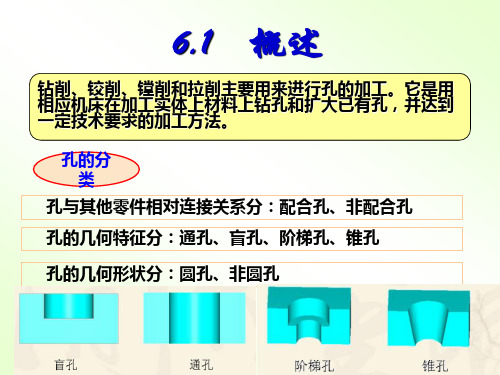
β
γ
f
轴向力和扭矩
切削刃强度和散热条件 一般麻花钻的螺旋角β=25°~ 32°。 黄铜、软青铜: β=10°~ 17° 轻合金、紫铜: β=35°~ 40° 高强度钢、铸铁:β=10°~ 15°
17
麻花钻的主要参数
(2)顶角2φ
指两主切削刃在与它们 平行的平面上投影的夹角
2φ
主切削刃长度
单位切削刃上的负荷及轴向力
21
6.2 钻削加工
6.2.2 钻削工艺特点
由于钻头的强度、刚度有限。容屑、排屑、导向、冷却和润滑 都困难,因此钻削的加工困难,质量不高。
钻孔时钻头易产生“引偏”
引偏概念 由于钻头弯曲而引起孔径扩大, 孔不圆; 孔的轴线歪斜。 “引偏”原因 ① 横刃的存在 ② 钻头的刚性和导向性差
6.2 钻削加工
6.2.1 钻床
钻床上可完成钻孔、扩孔、铰孔、攻丝、钻沉头孔、锪平面
刀具作旋转主运动同时沿轴向移动作进给运动。
6.2 钻削加工
6.2.1 钻床
立式钻床
立式钻床是应用较广的一种机床,其主参数是最大钻孔直径, 常用的有25mm、35பைடு நூலகம்m、40mm和50mm等几种。 特点是主轴轴线是垂直布臵, 而且位臵是固定的。加工时, 为使刀具旋转中心线与被加工 孔的中心线重合,必须移动工 件,因此立式钻床只适用于加 工中小工件上直径d≤50mm的孔。
6.2 钻削加工
用钻头在实体材料上加工孔的方法称为钻孔;用扩孔钻对已 有孔进行扩大再加工方法称为扩孔。它们统称为钻削加工。 钻床主要是用钻头钻削直径不大,精度要求较低的孔,此外 还可以进行扩孔、铰孔、攻螺纹等加工。加工时,工件固定 不动,刀具旋转形成主运动,同时沿轴向移动完成进给运动。 钻床的应用很广,如下图所示。
第8章钻削和镗削加工ppt课件

教学内容
❖ 8.1 钻削加工概述 ❖ 8.2 钻削加工设备 ❖ 8.3 钻孔刀具 ❖ 8.4 扩孔和锪孔 ❖ 8.5 铰孔刀具 ❖ 8.6 复合加工刀具 ❖ 8.7 镗削加工概述 ❖ 8.8 镗削加工刀具
一、钻削加工概述
❖ 1.1 钻削加工特点
径向力相互抵消,切削效率高 排屑困难,加工表面质量差 粗加工,精度为IT13~IT11,Ra为50~12.5μm
进给运动路线表达式
Ⅶ -3 47 8 2 42 1 -Ⅷ -1 38 0//3 2 -Ⅸ 6 4-1 26 /2 /4 31 5-Ⅹ -1 36 //12 45 0-Ⅺ -1 46 0//4 1 -Ⅻ 1 6M 3-M 4(合 )-Ⅹ-Ⅲ 727-M 5(合 )-Ⅹ-Ⅳ z13-齿(条 m3)-轴向进
三、钻削加工刀具
❖ 3.3 麻花钻钻孔方法
按划线位置钻孔 钻较深的孔 在硬材料上钻孔 钻孔径较大的孔 钻高塑性材料上的孔 钻斜面上的孔
三、钻削加工刀具
❖ 3.4 标注麻花钻存在的问题
前角变化且相差较大,使切削变形大 主刃长,宽度大,切屑变形和排屑难 横刃处前角呈负值,轴向力大 外缘转角处和副后刀面摩擦严重 横刃处的前后角是刃磨时自然形成的
灵活性大,适应性强 操作技术要求较高 镗刀结构简单,刃磨方便 可以修正位置误差 尺寸精度和表面质量高
七、镗削加工概述
❖ 7.2 镗床的工艺范围
七、镗削加工设备
❖ 7.1 镗床的加工方法
七、镗削加工设备
❖ 7.2 卧式镗床TP619
镗床的结构组成 镗床的主运动 镗床的进给运动
七、镗削加工设备
三、钻削加工刀具
❖ 3.5 麻花钻的修磨与改进
修磨横刃
第六章-钻削、铰削与镗削加工

应用
下列加工方法中,工件做主运动的是 ( ) (A)铣削加工 (B)车削加工 (C)钻削加工
钻削加工中,刀具作旋转主运动,工件作进给 运动。 ( )
镗削
1、应用:镗床是一种主要用镗刀在工件上加 工孔的机床。通常用于加工尺寸较大,精度 要求较高的孔,特别是分布在不同表面上, 孔距和位置精度要求较高的孔。 2、运动分析:主运动为镗刀的旋转运动,进 给运动为镗刀或工件的移动。 3.镗削加工特点: 刀具结构简单,加工灵活性大、通用性强, 可粗加工也可半精加工和精加工,适用批量较 小的加工,镗孔质量取决于机床精度。
平面磨削
磨削加工的特点
磨削加工是应用较为广泛的切削加工方法之一。 与其他切削加工方式,如车削、铣削、刨削等比 较,具有以下特点: (1)磨削速度高,磨削温度高,将产生大量的 热,需要大量的冷却润滑液。 (2)磨削加工可以获得较高的加工精度和较低 的表面粗糙度。 (3)磨削不但可以加工软材料,而且还可以加 工淬火钢及其他刀具不能加工的硬质材料。 (4)磨削加工的切削深度很小,在一次行程中 所能切除的金属层很薄。 (5)加工范围广。
内、外圆磨削
2、平面磨削 平面磨床用于磨削工件上的各种平面。磨削时 , 砂轮的工作表面可以是圆周表面,也可以是端面。 (1)周边磨削 以砂轮的圆周表面进行磨削时, 砂轮与工件的接触面积小,发热少,磨削力引起的 工艺系统变形也小,加工表面的精度和质量较高, 但生产率较低。以这种方式工作的平面磨床,砂轮 主轴为水平(卧式)布置。 (2)端面磨削 用砂轮(或多块扇形的砂瓦)的 端面进行磨削时,砂轮与工件的接触面积较大,切 削力增加,发热量也大,而冷却,排屑条件较差, 加工表面的精度及质量比前一种方式的稍低,但生 产率较高。以此方式加工的平面磨床,砂轮主轴为 垂直(立式)布置。
机械加工的工艺流程
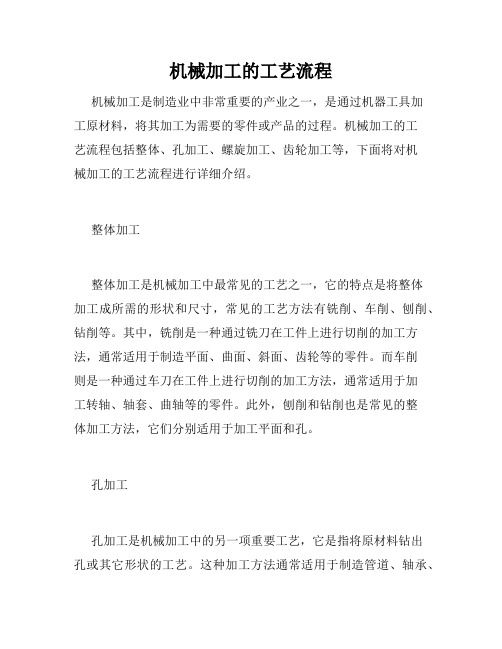
机械加工的工艺流程机械加工是制造业中非常重要的产业之一,是通过机器工具加工原材料,将其加工为需要的零件或产品的过程。
机械加工的工艺流程包括整体、孔加工、螺旋加工、齿轮加工等,下面将对机械加工的工艺流程进行详细介绍。
整体加工整体加工是机械加工中最常见的工艺之一,它的特点是将整体加工成所需的形状和尺寸,常见的工艺方法有铣削、车削、刨削、钻削等。
其中,铣削是一种通过铣刀在工件上进行切削的加工方法,通常适用于制造平面、曲面、斜面、齿轮等的零件。
而车削则是一种通过车刀在工件上进行切削的加工方法,通常适用于加工转轴、轴套、曲轴等的零件。
此外,刨削和钻削也是常见的整体加工方法,它们分别适用于加工平面和孔。
孔加工孔加工是机械加工中的另一项重要工艺,它是指将原材料钻出孔或其它形状的工艺。
这种加工方法通常适用于制造管道、轴承、齿轮、离合器等的零件。
主要的孔加工方法包括钻削、铰削和镗削。
其中,钻削是一种通过钻头在工件上进行切削的加工方法,可以加工直孔、斜孔等不同形状的孔。
铰削是一种通过铰刀在工件上进行切削的加工方法,适用于钻孔后的螺纹加工。
而镗削是一种通过镗头在工件中旋转而切削的加工方法,适用于加工大孔和不规则形状的孔。
螺旋加工螺旋加工是机械加工中的一种特殊的加工方法,它是指通过特殊的机床和刀具,将工件加工成各种形状的螺旋零件。
通常应用在机械传动中,例如蜗杆、升降丝杆、涡轮叶片等。
常见的螺旋加工方法包括螺旋车削、螺旋铣削和螺旋滚压。
齿轮加工齿轮加工也是机械加工中非常重要的一个部分,它的主要目的是将原材料加工成需要的齿轮零件。
加工齿轮有多种方法,包括铣削齿轮、滚齿轮、切齿轮和锲齿轮等,其中滚齿轮是最常用的方法之一。
滚齿轮分为滾削和滚弧两种加工方法,它可以在精度和加工效率方面达到较好的平衡。
总结机械加工的工艺流程包括整体、孔加工、螺旋加工、齿轮加工等多个方面。
不同的加工方法都有其独特的特点和加工适用范围,因此在选择加工方法时需要根据具体的零部件要求来选择。
钻削、车削、磨削、镗孔、拉削的工艺特点

钻削的工艺特点钻削运动构成:钻头的旋转运动为主切削运动,加工精度较低。
钻孔可在钻床上进行,也可在镗床、车床、铣床上进行,常用钻床有台式钻床、立式钻床、摇臂床应用在各类机器零件上经常需要进行钻孔,因此钻削的应用还是很广泛的,但是,由于钻削的精度较低,表面较粗糙,一般加工精度在IT10以下,表面粗糙度Ra值大于12.5μm ,生产效率也比较低。
因此,钻孔主要用于粗加工,例如精度和粗糙度要求不高的螺钉孔、油孔和螺纹底孔等。
但精度和粗糙度要求较高的孔,也要以钻孔作为预加工工序。
单件、小批生产中,中小型工件上的小孔(一般D 13 mrn)常用台式钻床加工,中小型工件上直径较大的孔(一般D<50mm)常用立式钻床加工;大中型工件上的孔应采用摇臂钻床加工;回转体工件上的孔多在车床上加工。
在成批和大量生产中,为了保证加工精度,提高生产效率和降低加工成本,广泛使用钻模、多轴钻的或组合机床进行孔的加工。
一、车削的工艺特点1、易于保证工件各加工面的位置精度a 例如易于保证同轴度要求利用卡盘安装工件,回转轴线是车床主轴回转轴线利用前后顶尖安装工件,回转轴线是两顶尖的中心连线b 易于保证端面与轴线垂直度要求由横溜板导轨,与工件回转轴线的垂直度2、切削过程较平稳避免了惯性力与冲击力,允许采用较大的切削用量,高速切削,利于生产率提高。
3、适于有色金属零件的精加工有色金属零件表面粗糙度大Ra值要求较小时,不宜采用磨削加工,需要用车削或铣削等。
用金刚石车刀进行精细车时,可达较高质量。
4、刀具简单车刀制造、刃磨和安装均较方便。
二、车削的应用在车床使用不同的车刀或其他刀具,可以加工各种问转表面,如内外圆柱面、内外圆锥面、螺纹、沟槽、端面和成形面等,加工精度可达IT8一IT7 ,表面粗糙度Ra 值为1.6~0.8,车削常用来加工单一轴线的零件,如直轴和一般盘、套类零件等。
若改变工件的安装位置或将车床适当改装,还可以加工多轴线的零件(如曲轴、偏心轮等)或盘形凸轮。
第六章机械制造基础钻削铰削镗削和拉削加工

第五节
第六章 钻削、铰削、镗削和拉削加工
图6-37 拉削过程
2021/9/23
返回目录
37
第五节
第六章 钻削、铰削、镗削和拉削加工
图6-38 同廓式拉削图形
2021/9/23
返回目录
38
第五节
第六章 钻削、铰削、镗削和拉削加工
图6-39 渐成式拉削图形
2021/9/23
返回目录
39
第五节
第六章 钻削、铰削、镗削和拉削加工
第三节 铰削加工
图6-27 铰刀的刃倾角
2021/9/23
返回目录
27
第六章 钻削、铰削、镗削和拉削加工
第三节 铰削加工
图6-28 铰刀的浮动连接
2021/9/23
返回目录
28
第四节
第六章 钻削、铰削、镗削和拉削加工
图6-29
2021/9/23
返回目录
29
第四节
第六章 钻削、铰削、镗削和拉削加工
第六章 钻削、铰削、镗削和拉削加工
第二节 钻 削 加 工
图6-1 钻床上能完成的典型加工
2021/9/23
返回目录
1
第六章 钻削、铰削、镗削和拉削加工
第二节 钻 削 加 工
图6-2
2021/9/23
返回目录
2
第六章 钻削、铰削、镗削和拉削加工
第二节 钻 削 加 工
图6-3
2021/9/23
返回目录
图6-30 固定式双刃镗刀
2021/9/23
返回目录
30
第四节
第六章 钻削、铰削、镗削和拉削加工
图6-31
2021/9/23
返回目录
机加工种类及范围

一、车削加工1、加工范围车外圆及台阶、车端面、镗孔、车锥面、车螺纹、车成形面、切槽和切断等。
2、粗车、精车与镜面车(1)粗车目的:尽快从毛坯上切去大部分余量,合工件接近要求的形状和尺寸。
(生产效率)考虑因素:应给精车和半精车留有合适的余量,一般为1-2mm。
(2)精车目的:保证加工精度和表面粗糙度的要求。
(生产效率其次)精车是指直接用车削方法获得IT6-IT7级公差,Ra为1.6-0.04μm的外圆加工方法。
(3)镜面车镜面车是用车削方法获得工件尺寸公差≤1μm的数量级,Ra≤3.2μm的外圆加工方法。
二、铣削加工1、加工范围可以加工各种零件的平面、台阶面、沟槽、成形表面、型腔表面、螺旋表面等。
铣削加工可以对工件进行粗加工和半精加工,加工精度可达IT7-IT9段,精铣表面粗糙度达Ra3.2-1.6μm.三、钻削、铰削与镗削加工1、钻削加工在钻床上以钻头的旋转作主运动,钻头向工件的轴向移动作进给运动,在实体工件上加工出孔为钻削。
按孔的直径、深度的不同,生产中有各种不同结构的钻头,其中,麻花钻最为常用。
由于麻花钻存在的结构问题,采用麻花钻钻孔时,轴向力很大,定心能力较差,孔易引偏;加工中摩擦严重,加之冷却润滑不便,表面较为粗糙。
故麻花钻钻孔的精度不高,一般为IT13-IT12,表面粗糙度达Ra12.5-6.3μm,生产效率也不高。
所以,钻孔主要用于φ80以也孔径的粗加工。
如加工精度、粗糙度要求不高的螺钉孔,油孔或对精度、粗糙度要求较高的孔作预加。
生产中为提高孔的加工精度、生产效率和降低成本,广泛使用钻模,多轴钻或组合机床进行孔加工。
当孔的深径比达到5及以上时为深孔。
深孔加工难度较大,主要表现在刀具刚性差,导向难;排削难;冷却润滑难几方面,有效地解决以上加工问题,是保证深孔加质量的关键。
一般对深径比在5-20的普通深孔,在车床或钻床上用加长麻花钻加工;对深径比达20以上的深孔,在深孔钻床上用深孔钻加工;当孔径较大,孔加工要求较高时,可在深孔镗床上加工。
第六章 钻削、铰削与镗削加工

(1)铰刀的直径及公差
1)加工后孔径扩大时: dmax =Dmax-Pmax dmin =Dmax-Pmax-G
铰 刀 的 结 构
铰刀直径应选小一些
铰刀直径公差分布图
(1)铰刀的直径及公差 2)孔径缩小时:
dmax =Dmax+Pmin
铰 刀 的 结 构 dmin =Dmax+Pmin-G 铰刀直径应选大一些
6)特种钻头
(1)扩孔钻
(2)中心钻
用于孔加工的预制精确定位,引导麻花钻进行孔加工,减少误差 。
(3)枪钻
用于加工 L/D>20~100的深孔加工。
1、钻削加工
钻削运动
回转体零件上的孔——在车床上加工; 箱体类零件上的孔或孔系——在钻床上加工。
主运动:钻头的旋转运动(钻床),或工件的旋转 运动(车床)。 进给运动:钻头沿轴线作直线进给运动(钻床), 或工件沿钻头轴线作直线进给运动(铣床)
上加工出孔的道具,如麻花钻、中心钻及深孔钻等;另一类 是对工件上已有孔进行再加工的道具,如扩孔钻、锪钻、铰 刀及镗刀等。
深孔:孔深与孔径之比大于5~10倍的孔称为深孔。 孔加工刀具的共同特点:刀具工作部分处于加工表面包 围之中,刀具的强度、刚度及导向、容屑及冷却润滑等都比 切削外表面时问题更突出。
二、孔的种类
钻孔
扩孔
铰孔
攻螺纹
锪埋头孔
锪端面
2. 扩孔钻的结构
图 扩孔钻 1) 齿数多(3、4齿); 2)不存在横刃;
3)切削余量小,排屑容易。
锪孔
在已加工的孔上加工圆柱形沉头孔、锥形沉头孔和凸台断面 等。 锪孔的目的是为了保证孔口与孔中心线的垂直度,以便与孔 连接的零件位置正确,连接可靠。在工件的连接孔端锪出柱形或 锥形埋头孔,用埋头螺钉埋入孔内把有关零件连接起来,使外观 整齐,装配位置紧凑。将孔口端面锪平,并与孔中心线垂直,能 使连接螺栓(或螺母)的端面与连接件保持良好接触。
- 1、下载文档前请自行甄别文档内容的完整性,平台不提供额外的编辑、内容补充、找答案等附加服务。
- 2、"仅部分预览"的文档,不可在线预览部分如存在完整性等问题,可反馈申请退款(可完整预览的文档不适用该条件!)。
- 3、如文档侵犯您的权益,请联系客服反馈,我们会尽快为您处理(人工客服工作时间:9:00-18:30)。
铰刀的基本结构如图所示
2、铰削过程特点
铰刀的直径是指铰刀圆柱校准部分的刀齿直径, 它直接影响到被加工孔的尺寸精度、铰刀的制造成本 及使用寿命。
(1)铰削的加工余量一般小于0.1mm,铰刀的主偏 角Kr一般小于45度,因此铰削时切削厚度ac很小,约 0.01~0.03mm。
(2)铰削过程所采用的切削速度一般都较低,因而切 削变形较大。
2)由于受被加工孔尺寸的限制,切削速度很难提 高,影响加工生产率和加工表面质量。
3)刀具的结构受孔尺寸的直径和长度的限,刚 性较差。
4)孔加工时,刀具一般是在半封闭的空间工伯, 切屑排除困难;冷却液难以进入加工区域,散 热条件不好。
钻削:一般精度为IT3~IT10,表面粗糙度值为 Ra=20~10um
第6章 钻削、铰 削与镗削加工
内孔表面也是零件上的主要表面之一,根据零件在 机械产品中的作用不同,不同结构的内孔有不同的精度 和表面质量要求。按照孔与其他零件的相对连接关系的 不同,可分为配合孔与非配合孔;按其几何特征的不同 ,可分为通孔、盲孔、阶梯孔、锥孔等;按其几何形状 不同,可分为圆孔,非圆孔等。 由于孔加工是对零件内表面的加工,对加工过程的观察 、控制困难, 加工难度要比外圆表面等开放型表面的加工大得多。孔 的加工过程主要有以下几个方面的特点: 1)孔加工刀具多为定尺寸刀具,如钻头、铰刀等,刀 具磨损造成的形状和尺寸的变化会直接影响被加工孔的 精度。
三、其他钻头
1、群钻:三尖七刃锐当先,月牙弧槽分两边,一 侧外刃开屑槽,横刃磨得低窄尖
2、可转位浅孔钻 3、错齿内排屑深孔钻 4、单刃外排屑深孔钻(枪钻) 5、喷吸钻
四、扩孔钻
扩孔钻是用于对已钻孔进一步加工,以 提高孔的加工质量的刀具,其加工精度可达 IT10—IT11,表面粗糙度可达Ra6.3—3.2 。 扩孔钻的刀齿比较多,一般有3—4个, 故导向性好,切削平稳,由于扩孔余量较小,容 屑槽较浅,刀体强度和刚性较好;
前角 :钻头的前角是在正交平面内测 量的前刀面与基面间的夹角 。对于标准麻 花钻,前角由30°逐渐变为-30°,故靠近中 心处的切削条件很差。
后角 f:钻头的后角是在假定工作平面 (即以钻头轴线为轴心的圆柱面的切平面)内 测量的切削平面与主后刀面之间的夹角 。 考虑到进给运动对工作后角的影响,同 时为了补偿前角的变化,使刀刃各点的楔角较 为合理,并改善横刃的切削条件,麻花钻的后 角刃磨时应由外缘处向钻心逐渐增大。
铰削:一般精度为IT8~IT6,表面粗糙度值为 Ra=1.6~0.4um
镗削:一般精度为IT8~IT7,表面粗糙度值为 Ra=6.3~0.8um
§6-1 钻头和钻削加工
孔加工刀具按其用途一般分为两大类:一类是从 实体材料上加工出孔的刀具;另一类是对已有孔进行 再加工的刀具。
一、麻花钻的结构
麻花钻是一种形状较复杂的双刃钻孔或扩孔的标 准刀具。一般用于孔的粗加工(IT11以下精度及表面 粗糙度Ra25—6.3um),也可用于加工攻丝、铰孔 、拉孔、镗孔、磨孔的预制孔。
(3)在切削液润滑作用下,切削刃的钝圆部分只在加 工表面上润滑,使工件表面受到熨压作用,熨压后已 加工表面发生弹性恢复。
铰孔时,应根据工件材料、结构和铰削余 量的大小,综合分析决定切削液的使用。 二、铰刀的结构参数 1、直径及公差
扩孔钻的主要类型有两种,即整体式扩 孔钻和套式扩孔钻,其中套式扩孔钻适用于 大直径孔的扩孔加工。
§6-2 铰刀和铰削加工
铰孔之前,被加工孔一般需经过钻孔或经过钻、扩孔加工 。
一、铰削过程特点
1、铰刀的结构 铰刀用于中、小尺寸孔的半精加工和精加工,也
可用于磨孔或研孔前的预加工。铰刀齿数多(6—12 个),导向性好,芯部直径大,刚性好。铰削余量小 ,切削速度低,加上切削过程中的挤压作用,所以能 获得较高的加工精度(IT6—IT8)和较好的表面质量 (Ra1.6—Ra0.4um)。铰刀分为手用铰刀和机用铰 刀两类。手用铰刀又分为整体式和可调式,机用铰刀
)为两主切削刃在与其平行的轴向平面上投影 之间的夹角。标准麻花钻的2 =118°,此时 的主切削刃是直线。
钻头的顶角2 直接决定了主偏角κr的大小 ,且顶角之半 在数值上与主偏角κr很接近。 顶角越小,切削刃长度增加,单位切削刃长度 上负荷降低,刀尖角 r增大,改善了散热条件 ,提高了钻头的耐用度。同时,轴向力减小。 但切屑变薄,切屑平均变形增加,故使扭矩增 大。
二、钻削过程特点及钻削用量
1、钻削过程特点 刀具刚性差,排屑困难,切削热不易排出
2、钻削用量 (1)钻削深度ap 它是钻头的半径 (2)进给量f和每刃进给量af 钻头(或工件) 每转一转,钻头在进给方向相对于工件的位移 量称进给量f(mm/r)。由于麻花钻有两个刀齿 (即Z=2),故每个刀齿的进给量为 af=f/2(mm/z) (3)钻削速度Vc 钻削速度指钻头外径处的主运 动线速度(m/min)
1、麻花钻的构造
标准麻花钻由3个部分组成:工作部份、 柄部、颈部尾部是钻头的夹持部分,用于与机 床联接,并传递扭矩和轴向力。按麻花钻直径 的大小,分为直柄(小直径)和锥柄(大直径) 两种。
颈部是工作部分和尾部间的过渡部分,供磨 削时砂轮退刀和打印标记用。小直径的直柄钻 头没有颈部。
2、麻花钻的主要几何参数
横刃角度——横刃是两个后刀面的交线, 其长度为bψ 。横刃角度包括横刃斜角ψ,横刃 前角γoψ和横刃后角αoψ。横刃斜角ψ为在钻 头端平面内投影的横刃与主切削刃之间 的 夹 角,它是刃磨后刀面时形成的。
由于标准麻花钻在结构上存在着很多问题 ,在使用时常常进行修磨,以改变标准麻花钻 切削部分的几何形状,改善其切削条件,提高 钻头的切削性能。
螺旋角 :钻头螺旋槽最外缘处螺旋线的 切线与钻头轴线间的夹角为钻头的螺旋角 。 较大的螺旋角,使钻头的前角增大,故切削扭 矩和轴向力减小,切削轻快,排屑也较容易。 但是螺旋角过大,会削弱钻头的强度和散热条 件,使钻头的磨损加剧。标准麻花钻的
=18°—30°,小直径钻头 值较小。 顶角2 和主偏角κr:钻头的顶角(即锋角