电子变压器8D报告实你缝合线错位
电子变压器8D报告(尺寸偏小)实例

类似系列产品列入质量管理项目.
D8标准化
(Standardizatio
将此不良现象记录在《品质异常备忘录》中,以便下次生产时能重点管控。
n)
Approved by(核准)
Report by(报 告人)
Report Finish Date
2019.05.27
Delta follow up/追踪
VQA Engineer verify(工程师 确认)
Approved By (认可主管:)
Verify date Approved date
Note: 1.Item2~8 are filled in by supplier ( 2~ 8项由供应商填写) 2.Response Time: Local supplier(国内供应商) 3 Working days 3.Response Time: Oversea supplier(国外供应商)14 Working days
Due day(完成日期)
1.严格要求成型作业员把变形产品挑选干净
2.成型技术员调机时,控制好温度,每隔一小时检查一次产品射出时的温
度
2.要求品管检验时一
定要细心,把变形产品挑干净,FQC抽检时必须用卡尺测量尺寸,
2019.07.13
Before(改善前) :
D6效果确认 (Verification of
D1问题描述 (Problem
Description)
改善对策报告
Corrective Action Report
Vender(厂商)
Failure Q'ty(不良数)
/
P/N(料号)
3143049900
Failure rate(不良率)
电子变压器8D报告(合模线毛边)

库存: 16000 在制品: 无 客户库存: 200
Failure Q'ty(不良数) Failure rate(不良率) How much(产生费用)
Who(客诉类型)
/ 23.00%
/ 进料
不良原因主导者和分析成 员 /Team Leader and member: (Including Name, Department)
D5根本原因及 Long term action(长期对策) 长期对策
(Root cause & long term action)
1.模具定位梢重新定位锁紧固定 2.成型生产时增加一项对模具定位梢检查 3.DF处理由 原来15分钟一次,加长至20分钟一次
Owner(责任人)
Due day(完成日 期)
follow up/客人追 踪
VQA Engineer verify(工程 师确认)
Approved By (认可主管:)
Verify date Approved date
Note: 1.Item2~8 are filled in by supplier ( 2~ 8项由供应商填写) 2.Response Time: Local supplier(国内供应商) 3 Working days 3.Response Time: Oversea supplier(国外供应商)14 Working days
Team Leader(主 导者)
Function(职 务)
主管
Name(姓名)
Function(职务) 工程师
Name(姓名)
D3现状分析
QA经理
/
(Problem Analysis) Team numbers
电子变压器8D报告(合模线错位)
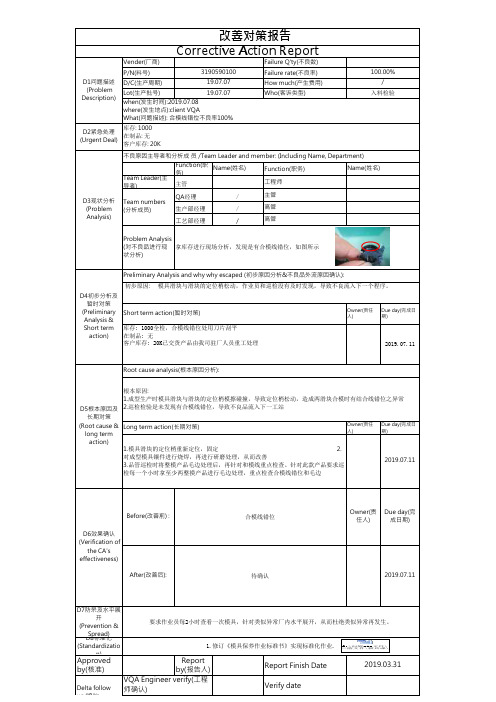
VQA Engineer verify(工程 师确认)
Verify date
Delta follow up/追踪
Approved By (认可主管:)
Approved date
Note: 1.Item2~8 are filled in by supplier ( 2~ 8项由供应商填写) 2.Response Time: Local supplier(国内供应商) 3 Working days 3.Response Time: Oversea supplier(国外供应商)14 Working days
Team Leader(主 导者)
Function(职 Name(姓名) 务) 主管
Function(职务) 工程师
Name(姓名)
Team numbers (分析成员)
QA经理 生产部经理
/
主管
/
高管
工艺部经理
/
高管
Problem Analysis (对不良品进行现 拿库存进行现场分析,发现是有合模线错位,如图所示 状分析)
1.成型生产时模具滑块与滑块的定位梢模擦碰撞,导致定位梢松动,造成两滑块合模时有结合线错位之异常
D5根本原因及 2.巡检检验是未发现有合模线错位,导致不良品流入下一工站
长期对策
(Root cause & Long term action(长期对策) long term
Owner(责任 Due day(完成日
action)
Short term action(暂时对策)
库存: 1000全检,合模线错位处用刀片刮平 在制品: 无 客户库存: 20K已交货产品由我司驻厂人员重工处理
Owner(责任 Due day(完成日
电子变压器8D报告(PIN歪)实例

2019.07.06
Before(改善前) :
D6效果确认 (Verification of
the CA's effectiveness)
After(改善后):
PIN歪 待确认
Owner(责 Due day(完
任人)
成日期)
2019.07.06
初步原因: 此款产品用的是0.6的CP线,CP线比较细,产品挤压容易PIN歪,包装时包装人员未将尾数包装好。 导致PIN歪插品流出
D4初步分析及 暂时对策
(Preliminary Analysis & Short term
action)
Short term action(暂时对策)
库存: 1200 全检,未发现有PIN歪 在制品: 无 客户库存: 1700已交货产品由我司驻厂人员重工处理
D7防呆及水平展 开
(Prevention & Spread)
针对此类似机种在厂内水平展开,从而杜绝类似现象发生。
D8标准化
Байду номын сангаас
(Standardizatio n)
Approved by(核准)
1.修订《包装作业标准书》实现标准化作业.
Report by(报告人)
Report Finish Date
VQA Engineer verify(工程 follow up/追踪 师确认)
Verify date
Approved By (认可主管:)
Approved date
Note: 1.Item2~8 are filled in by supplier ( 2~ 8项由供应商填写) 2.Response Time: Local supplier(国内供应商) 3 Working days 3.Response Time: Oversea supplier(国外供应商)14 Working days
变压器8D报告(骨架PIN位反)实例样板
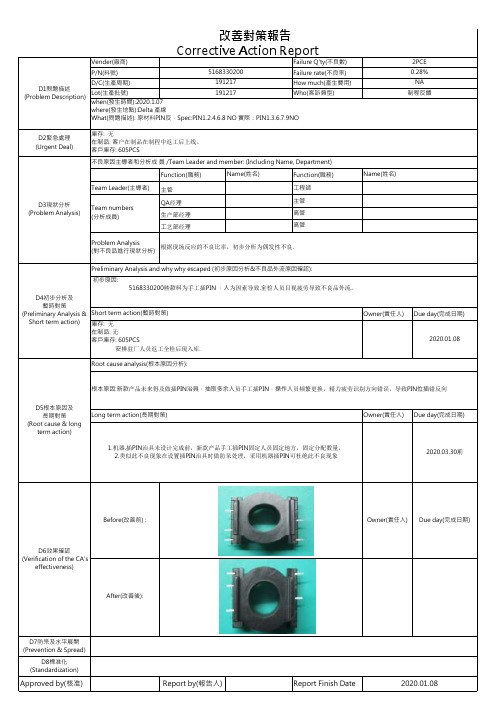
Vender(廠商)Failure Q'ty(不良數)P/N(料號)Failure rate(不良率)D/C(生產周期)How much(產生費用)Lot(生產批號)Who(客訴類型)D2緊急處理(Urgent Deal)Function(職務)Function(職務)Team Leader(主導者)主管工程師QA 经理主管生产部经理高管工艺部经理高管Owner(責任人)Due day(完成日期)Owner(責任人)Due day(完成日期)D7防呆及水平展開(Prevention & Spread)D8標准化(Standardization)Approved by(核准)Report by(報告人)Report Finish Date 根据现场反应的不良比率,初步分析为偶发性不良.Owner(責任人)2020.01.082020.03.30前Due day(完成日期)根本原因:新款产品未来得及做插PIN治具,抽取多余人员手工插PIN,操作人员频繁更换,精力疲劳识别方向错误,导致PIN位插错反向1.机器.插PIN 治具未设计完成前,新款产品手工插PIN 固定人员固定地方,固定分配数量,2.类似此不良现象在设置插PIN 治具时做防呆处理,采用机器插PIN 可杜绝此不良现象D3現狀分析(Problem Analysis)D4初步分析及暫時對策(Preliminary Analysis &Short term action)D5根本原因及長期對策(Root cause & longterm action)D6效果確認(Verification of the CA'seffectiveness)Team numbers (分析成員)Problem Analysis(對不良品進行現狀分析)Before(改善前) :After(改善後):庫存: 无在制品: 无客戶庫存: 605PCS安排驻厂人员返工全栓后现入库.Root cause analysis(根本原因分析):Long term action(長期對策)2020.01.08Preliminary Analysis and why why escaped (初步原因分析&不良品外流原因確認):Short term action(暫時對策) 初步原因:5168330200些款料为手工插PIN ,人为因素导致.全检人员目视疲劳导致不良品外流。
电子变压器8D报告(合模线错位)实例

NG OK
Owner(責 Due day(完
任人)
成日期)
2revention &
要求作业员每2小时查看一次模具,针对类似异常厂内水平展开,从而杜绝类似异常再发生。
DS8p標re准ad化)
(Standardizatio
整理汇总存档,后续量产中连续追踪三批,进行标准化定型。
D3現狀分析 (Problem Analysis)
不良原因主導者和分析成 員 /Team Leader and member: (Including Name, Department)
Team Leader(主 導者)
Function(職 Name(姓名) 務) 主管
Function(職務) 工程師
初步原因: 模具滑块与滑块的定位梢松动,作业员和巡检没有及时发现,导致不良流入下一个程序。
D4初步分析及
暫時對策
(Preliminary Short term action(暫時對策)
Analysis &
Short term 庫存: 5700全检,不良报废
action)
在制品: 无 客戶庫存: 2400挑出的不良我司补货
200311
Who(客訴類型)
when(發生時間):2020.03.12 where(發生地點):VQA What(問題描述): 合模線錯位,呈臺階狀,實測值0.165mm;0.20mm
D2緊急處理 (Urgent Deal)
庫存: 5700 在制品: 无 客戶庫存: 2400
11 11.70%
/ 入料检验
n)
Approved by(核准)
Report by(報告人)
Report Finish Date
电子变压器8D报告(BOBIN排距尺寸不良)
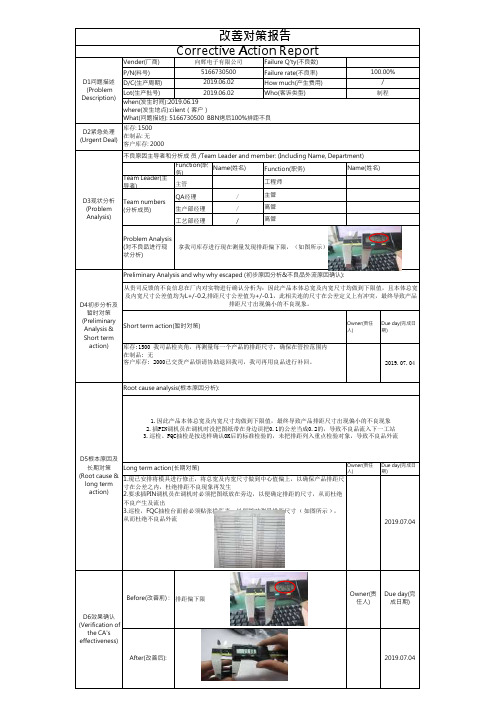
Vender(厂商)Failure Q'ty(不良数)P/N(料号)Failure rate(不良率)D/C(生产周期)How much(产生费用)Lot(生产批号)Who(客诉类型)D2紧急处理(Urgent Deal)Function(职务)Function(职务)Team Leader(主导者)主管工程师QA 经理主管生产部经理高管工艺部经理高管Owner(责任人)Due day(完成日期)Owner(责任人)Due day(完成日期)拿我司库存进行现在测量发现排距偏下限,(如图所示)2019.07.042019.07.04Due day(完成日期)2019.07.04排距偏下限1.因此产品本体总宽及内宽尺寸均做到下限值,最终导致产品排距尺寸出现偏小的不良现象2.插PIN调机员在调机时没把图纸带在身边误把0.1的公差当成0.2的,导致不良品流入下一工站3.巡检、FQC抽检是按送样确认OK后的标准检验的,未把排距列入重点检验对象,导致不良品外流1.现已安排将模具进行修正,将总宽及内宽尺寸做到中心值偏上,以确保产品排距尺寸在公差之内,杜绝排距不良现象再发生2.要求插PIN 调机员在调机时必须把图纸放在旁边,以便确定排距的尺寸,从而杜绝不良产生及流出3.巡检,FQC 抽检台面前必须贴张排距表,以便随时测量排距尺寸 ﹙如图所示﹚,从而杜绝不良品外流库存:1500 我司品检夹角,再测量每一个产品的排距尺寸,确保在管控范围内在制品: 无客户库存: 2000已交货产品烦请协助退回我司,我司再用良品进行补回。
D3现状分析(Problem Analysis)D4初步分析及暂时对策(PreliminaryAnalysis &Short term action)D5根本原因及长期对策(Root cause &long term action)D6效果确认 (Verification ofthe CA's effectiveness)Team numbers (分析成员)Problem Analysis(对不良品进行现状分析)Before(改善前) :After(改善后):Short term action(暂时对策)Root cause analysis(根本原因分析):Long term action(长期对策)Owner(责任人)//Preliminary Analysis and why why escaped (初步原因分析&不良品外流原因确认):从贵司反馈的不良信息在厂内对实物进行确认分析为:因此产品本体总宽及内宽尺寸均做到下限值,且本体总宽及内宽尺寸公差值均为L+/-0.2,排距尺寸公差值为+/-0.1,此相关连的尺寸在公差定义上有冲突,最终导致产品排距尺寸出现偏小的不良现象。
电子变压器8D报告(合模线错位)实例
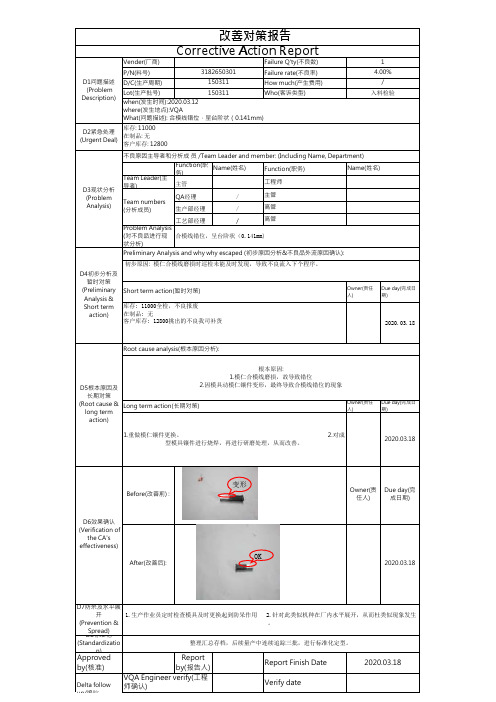
Root cause analysis(根本原因分析):
根本原因:
1.模仁合模线磨损,故导致错位
D5根本原因及
2.因模具动模仁镶件变形,最终导致合模线错位的现象
长期对策
(Root cause & Long term action(长期对策) long term
Owner(责任 人)
actioቤተ መጻሕፍቲ ባይዱ)
Due day(完成日 期)
改善对策报告
Corrective Action Report
Vender(厂商)
Failure Q'ty(不良数)
P/N(料号)
3182650301
Failure rate(不良率)
D1问题描述 (Problem
Description)
D/C(生产周期)
150311
How much(产生费用)
Lot(生产批号)
D4初步分析及 暂时对策
(Preliminary Analysis & Short term
action)
Short term action(暂时对策)
库存: 11000全检,不良报废 在制品: 无 客户库存: 12800挑出的不良我司补货
Owner(责任 Due day(完成日
人)
期)
2020.03.18
1.重做模仁镶件更换。 型模具镶件进行烧焊,再进行研磨处理,从而改善。
2.对成
2020.03.18
Before(改善前) :
D6效果确认 (Verification of
the CA's effectiveness)
After(改善后):
变形 OK
8D 问题分析报告模板及说明

8D 问题分析报告客户:问题发生日期:问题关闭时间:产品名称:产品号:8D编号:8D问题分析报告用法说明标题1) 客户: (如:SGMW)2) 问题发生日期: 问题开口日期3) 问题关闭日期:所有的永久纠正措施已经实施并且确认有效;所有要求的支持文件已经提交4) 产品号: (如:xxxxx)5) 产品名称: (如:xxxx)6) 8D问题编号: 8D问题追踪编号(也可以包括客户或供应商追踪编号)1.小组成员1) 组员姓名/部门/电话号码2.问题描述1) 描述: 从客户的角度描述问题; 他们想知道什么?何时: 零件什么时候制造的? 什么时候组装的? 总成什么时候发运给客户的? 什么时候组装进整车的? 什么时候从主机厂发运的?探测: 公司怎么知道的这个问题? 谁提供的信息?范围: 可疑产品数量,比率,数据的来源 - 在工厂内的, 在运输途中的, 在客户处.失效模式: 问题本身怎么表现的?2) 对客户的影响: 识别潜在的对停机,干扰生产线,召回,索赔等影响.3.临时遏止1) 采取了什么措施以立即保护客户并遏止任何可疑库存? 从收到通知开始, 我们在如何遏止这个问题? 目前的遏止状态是什么? 我们做了什么样的挑选, 我们在哪,怎样验证的有效性?如果已经开始实施返工或者返修计划(计划是什么,我们怎样验证有效性),请附上带有草图和趋势图的计划.2) 其他同类产品的风险:可能受此问题影响的其他产品或客户.3) 合格材料的标识:在每一个合格的零件和/或合格材料的容器上贴标签或手写标识,规定标签的颜色,大小,位置和内容.4) 挑选结果:时间,日期,挑选零件总数和拒收数量,包括:客户,内部,供应商 .4.根本原因1) 产生原因& 怎样验证: 识别问题发生的每一个根本原因.已经验证是根本原因了吗?如何验证的?通过统计证据/假设检验来验证.如果没有验证,看作是可疑根本原因.2) 流出原因& 怎样验证: 识别问题没有被发现的每一个根本原因.已经验证是根本原因了吗?如何验证的?通过统计证据/假设检验来验证.如果没有验证,看作是可疑根本原因.5.长期纠正期措施1) 为何制造出问题零件的纠正措施:针对根本原因识别永久纠正措施.纠正措施已经被验证了吗?如何验证的?2) 为何发运出问题零件的纠正措施: 针对根本原因识别长期纠正措施.纠正措施已经被验证了吗?如何验证的?6.纠正措施实施1) 要求对为什么制造出问题零件和为什么发运出问题零件的每个纠正措施实施.2) 纠正措施实施明确责任人3) 目标完成日期:根本原因的所有纠正措施计划完成的日期.4) 纠正措施完成日期:根本原因的所有纠正措施实际完成的日期.7.预防1) 将来如何避免这个问题?识别防止问题再发生的系统性的更改.如果适用,在其他风险区域把所做的改进标准化.2) 其他存在风险的场所或平台? 对于可能存在同样问题的场所或平台,识别零件名称,零件号,负责追踪的纠正措施所有者和完成日期.如果问题是独立的,输入"N/A" .3) 必要的文件已经更新了吗?识别必须更新的文件以包括永久纠正措施,并规定谁负责更新以及完成的日期.如果文件不必更新,输入"N/A".8.关闭1) 对小组成员进行表彰和奖励。
品质异常分析8D报告

XX/XXX
1月10 日
保证日期印错
工程人员在制作印稿时输入错误导致
1. 后续要求工程制稿文件,在发现场前,需业务责任
人进行核对确认,避免制作人员疏忽导致批量性不良
再发
2. 将客户保
证期 3年或 5年要求宣导给生产及制检人员,参照核对。
XXX/XXX
1月11 日
混料问题
经调查为送货人员装卸货时将混入
印刷跑位、保证日 机 期印错、混料问题
料
法
人 机
批号错误
料ห้องสมุดไป่ตู้
传送带未调试好 机器故障 纸张弯翘
尺寸大小不一致 设置方法问题 作业方式错误 单据输入错误 系统故障 物料发错
检查印刷传送带运转走纸正常,不会造成跑位现象 经检维修记录近期生产机台,无故障发生 查证厂商来料纸板有弯翘现象,会在印刷时导致跑位 原纸张为机器红外线感应计数裁切,不存在同批大小问题 经查生产设定参数,均在要求规格内 生产各工站均为老员工,并依照 SOP 进行作业 批号为手工输入,易发生错误 ERP 有专人进行维护,近期无发生故障问题 经与客户确认,实物正确,仅送货批号错误
印刷跑位
保证期印错
混料
4
三 处理对策
紧急应对措施:
A.1:外箱跑位:生产召集会议分析原因,商讨改善方案 . ---- 责任人:XXX 完成时间 2019/01/09
A.2:外箱印刷错误和混料:调查发生原因,梳理管控流程。 ---- 责任人:XXX 完成时间 2019/01/10
B.送货单问题:与客户确认后续格式,并协商好异常品补货时间 ---- 责任人:XXX 完成时间 2019/01/10
品质异常分析改善报告
制作人:JACKEY 审核人:XXXX 时间:2019.01.11
8D报告(变压器bobin塑胶平整度不良)

Failure rate(不良率) How much(产生费 用) Who(客诉类型)
NA 制程反馈
where(发生地点):Delta 产线
What(问题描述): 材料3188891500 产线反馈固定#1平整度不良,针对台达库存41977PCE已要求驻场人员挑选
D2紧急处理 (Urgent Deal)
Approved by(核准)
Report by(报告人)
follow up/追踪
VQA Engineer verify(工程师确认) Approved By (认可主管:)
Note: 1.Item2~8 are filled in by supplier ( 2~ 8项由供应商填写) 2.Response Time: Local supplier(国内供应商) 3 Working days 3.Response Time: Oversea supplier(国外供应商)14 Working days
Preliminary Analysis and why why escaped (初步原因分析&不良品外流原因确认):
初步原因:
因产生平整度有固定模号不良比率非100%,初步判定1#号模平整不良为生产前成型参数调试不当,造成1#号模
D4初步分析及
其中一部份平整度超标.
暂时对策
(Preliminary Analysis & Short term action(暂时对策)
成型周期:40" 冷却时间:25" 2.QC人员安客户标准(10000-0162平整度标准≦0.15MM)作平整度实物测量.
Owner(责任 人)
Due day(完成日期)
2019.01.14
质量管理8D改进的详尽报告
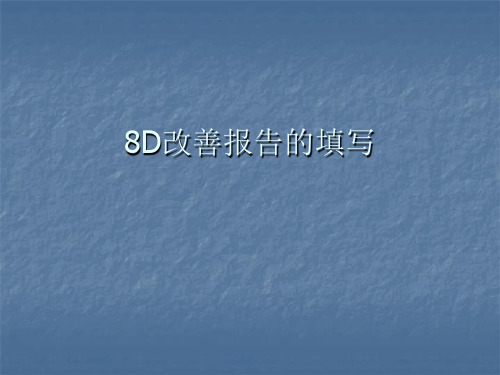
案例:以下通过一件发生在我们身边的平 常小事,来说明8D报告(纠正/预防措施) 的写法。
事由:2010-09-18接收到日本电产投诉8
月30日进货检验的590000130C产品 出现毛刺不良,同时外包装箱破损。
24小时内的快速反应
必须要在24小时内对《8D改善对策报 告》中的1、2、3条进行回复。 同时要求横向展开,对于在途品、再 库品、制程品及类似产品横向展开。明确 批号、数量。
写8D报告的基本原则
8D方法步骤
a)2D问题描述阶段 必须说明所有客户反馈失效的相关信息,失效描述(外观不良,电性能 不良…),退回样品信息(品名,型号,数量,批号),失效发生的信 息(受入检查,整机测试,老化试验,0km,市场…)和具体的失效分 析结果。通过找到失效的真正问题点也是非常关键的,这个对今后的 数据分析和原因分析有很大的帮助。
b)3D遏制行动阶段 3D通常可以包含以下内容,实施有效的遏制行动来停止问题延续,防 止类似不良的产品继续产生并发给客户,可以通过额外/加严的控制 (e.g. 100% 全检),将异常信息传达给相关人员,提升其意识和注意, 对现有的库存和在线产品进行验证,是否有同样的问题,确认受影响 批的生产记录(过程监控的数据(抽样试验的数据,检验数据,测试 数据),合格率数据,过程中不良分类(是否和投诉有关联),前后 批次(通常需要3-5批)的合格率数据,不良分类,设备维修记录(异 常批没有维修记录,需确认之前一次和之后一次),品种更换记录等) --这些记录的整理非常关键,通过挖掘数据,可能会找到问题的规 律。3D中还有一个重要的步骤就是“初始的风险评估”,评估是否需 要召回或隔离,以此避免避免更多的可能存在失效产品被使用。
a)使用简单,正确的语言 简单,但是能够清晰的说明问题 b)符合逻辑性 一步一步的相互印证,没有前后矛盾的说法,也不要从8D里延伸出新的 问题出来。 c)目标读者 外行——在某个项目上没有接受过培训的,人员。 说白了就是让白痴也能看明白。 d)多一些“花花草草”的东西 多放一些图片,比如各种对策实施的证据,过程记录的证据,在线产品 验证的证据。 多采用一些工具,比如鱼骨图,排列图,FTA e)兼顾顾客的要求和公司的利益 了解顾客的心理,在一定程度上去迎合客户的需求,要给客户看出我们 很重视这个8D,并且花了很大的精力和财力才采取各项措施。对公司 明显做不到的改善措施/方法,就没有必要列出,但也可以利用客户来 推动内部的持续改善。
电源适配器8D分析及改善报告

电源适配器8D分析及改善报告深圳市XXX有限公司XXXTechnology Co.,Ltd客户投诉8D 报告编号Report NO:JY20190401D2:问题描述 Problem Description12V/1.5A 国标,市场上退回1PCS 电源损坏.胶壳已裂开.电解电容鼓包,输入部分线路损坏.D3:应急措施Containment Action(s)可插入文本、附件(文件、无图片等)Insert Text and/or attachments (documents, pictures, etc.)测试产品有C5电解电容、F1保险丝、NTC热敏电阻、BD1桥硅元件损坏.产品损坏的有三种原因:一.产品雷击时,浪涌电压造成损坏.产品雷击测试,差模4KV,在不同的相位下(0、90 、180 、270相位)各5次测试,测试结果输出正常。
通过此测试,说明产品可以承受4KV的雷击电压。
二.产品内部有锡渣短路,造成损坏.仔细检查产品锡面及元件面,没有发现有残留锡珠、锡渣、元件脚等异物.通过各个焊点检查,没有发现因异物短路,打火的痕迹.此点可以排除产品内有金属物造成损坏.三.输入端元件知路,造成损坏.将主IC 脚、ZD1、D1、D2、变压器脚分别短路,开机测试,产品不工作或元件FUSE、BD 、NTC损坏,但电解电容C5并没有损坏.与市场退回不一致.四.将C5电容,本体向上搬起,再按平,通电测试,约15分种后,产品损坏。
电容本体C5鼓包,开阀。
损坏元件:C5、F1 、NTC热敏电阻、BD1,与退回的不良品损坏的情景一致.五.通过以上试验,电容失效才会发生同样现状.1.测量电解电容容量,合格品13UF以上,此颗电容仅8.5nF,说明电容容量已失效.2.将电容外表皮去除后,电容负极引脚与阴极铝箔已脱离如左图一所示.进一步铝箔展开,发现阴极导针处铝箔受损.电容导针受外力影响,有拉动后留下的皱纹.皱纹刺破阴极与阳极间的绝缘纸,引脚处阴极铝箔与阳极铝箔间短路,通电瞬间打火,电容防爆开,导针断裂。
(完整版)8D质量整改报告模板

1D:成立小组
1、成立时间:
2、人员分工:
3、实施计划:3.1 项目计划
3.2工作计划
2D:问题说明
1、特性失效模式分析:
2、市场表现:
对产品市场主流情况进行描述3、生产表现:
4
、改进目标:
现状: 目标 3D :临时措施
4D :根本原因
从人、机、料、法、环、测进行分析(鱼刺图):
2、可能因素分析: 要因(关键因子)标识为“●” 、非要因标识为“○”
方
面 序
号
可能因素
分析、试验、确认过程
重要度
备注
人
1
○
机
2
●
料
3
●
法
4
●
测
5
●
5D :制定措施并验证
1、实施计划:
人
机 料
法
测
操作不当
未按工艺要求对新换感应器验证
感应器验证缺
乏有效监督
R
部层深浅和脱碳层深
检测手段健全
金相检测人员未按工艺
切割检测面
表面淬火工艺合理
设备维护问题
未明确感应器验证要求
金相切割机夹紧装置失效
调质后中杆未
进行机械加工去除脱碳层
2、措施早期验证:
综上分析:
3、市场处理方案:6D:永久措施
7D:预防措施
8D:总结激励。
电子变压器8D报告(尺寸超规格)
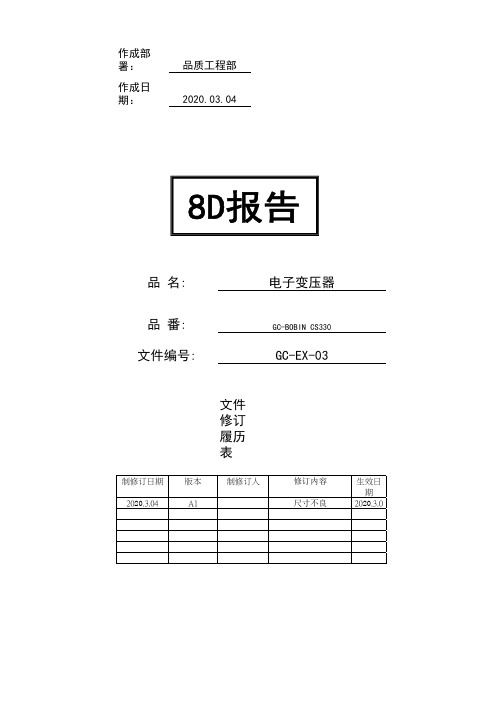
作成部署:作成日期:文件修订履历表文件编号:GC-EX-03品质工程部2020.03.04品 名:电子变压器品 番:GC-BOBIN CS330Vender(厂商)Failure Q'ty(不良数)P/N(料号)Failure rate(不良率)D/C(生产周期)How much(产生费用)Lot(生产批号)Who(客诉类型)D2紧急处理(Urgent Deal)Function(职务)Function(职务)Team Leader(主导者)主管工程师QA 经理主管生产部经理高管工艺部经理高管Owner(责任人)Due day(完成日期)Owner(责任人)Due day(完成日期)改善前: J1:28.00±0.25 28.35 28.42 尺寸偏大NG库存: 无在制品: 无客户库存: 200PCS已交货至客户端产品我司安排驻厂人员挑选处理.客人2020.03.05来料检验发现51688260200 J1尺寸超出公差,(如图)经驻厂人员确认J1宽度尺寸超出公差0.1-0.2量产模加工处理中,待确认。
产品“U"形端模具结构为:主体与滑块两部分组合而成,产生的根本原因一穴滑块制作精度不够(分析图例)产品成型后镶件边高于主模形成错位,致使J1尺寸偏大.1.停止使用样品模具,后续将量产新模滑块尺寸由原来3.7MM降低0.2MM (如图所示)2.样品订单,依据流程正常生产杜绝越流程化作业.(见D8项附档)Owner(责任人)2020.03.132020.03.13Due day(完成日期)2020.03.13D1问题描述 (Problem Description)D3现状分析(Problem Analysis)D4初步分析及暂时对策(PreliminaryAnalysis &Short term action)D5根本原因及长期对策(Root cause &long termaction)D6效果确认 (Verification ofthe CA's effectiveness)Team numbers (分析成员)Long term action(长期对策)Before(改善前) :After(改善后):/Preliminary Analysis and why why escaped (初步原因分析&不良品外流原因确认):初步原因分析:合模线错位引发产品“U”形端毛边,导致有一模号J1尺寸偏大.(如图):外流原因分析:因样品订单数量较小,生产排程未进行正常排单QC人员未检验,样品负责人直接入仓出货,导致J1尺寸不良重复发生.Short term action(暂时对策)Root cause analysis(根本原因分析):Problem Analysis (对不良品进行现状分析)//20.03.04进料库存: 无在制品: 无客户库存: 200PCS不良原因主导者和分析成 员 /Team Leader and member: (Including Name, Department)Name(姓名)Name(姓名)when(发生时间):2020.03.04where(发生地点):客人(区内)What(问题描述): 5168260200 J1尺寸超出规格实测:28.35,28.42,不良率5%/51688260200 5.00%20.03.04/ 改善对策报告Corrective Action Report毛边主体面OK 滑块面NG3.7MM3.7MM制定《样品制作管理程序》实现流程化作业.(如附档)样品制作管理程序.doc。
8D报告-线束分支错误 - 副本

考虑事项
更新
详细
设计FMEA
图纸/CAD
设计/开发/品质保证基准
管理计划书附图
工程FMEA
工程流程图
管理计划书 / 管理图
工程内作业/检查指导书
已检查作业指导书,为最新状态
检具
对二级及以下供应商的跟踪
水平展开(是否对其他产品/类似工程?)
対策实施
水平展开 (Yes / No)
24010-2ZB4A库存品/在线品排查确认
考虑事项
实施内容
在制品
2013-8-8日对我司在制品进行排查,无在制品
在线品 保管场所的产品
排查产线在线品,无在线品 排查库存品,共计29条
售后服务零部件 其他
经确认无售后服务件(此产品为新开发产品) 确认化工厂、日产理料区、日产车间均无库存
临时对策详细内容
1、将日产车间不良品调换。
2、对库存品进行排查,确认与图纸要求相符,并重新进行导通、外观检测。
Yes
责任者
部门
日期
张军
技术
2013/8/9
详细 2013-8-10~2013-8-27 共计389条无不良
5.对产线班组长进行教育宣导,严格按照不良品处理流程作业,在返修作业时接受返修品人员必需认真核对返
修品品番、数量,返修完成后进行检验核对品番数量无误后办理入库避免遗漏 6.新产品验证时,依据图纸进行逐项检查,发现问题及时改正 7.对相似产品明确差异点,在样线上明确标出,外观检查时重点检查(附件五) 8.在外观检查工位对每条线束的搭铁分支进行全检,检查OK后在线数上打点标识(附件六)
NISSAN
A
N
P
Q
P
再 发 防 止 对 策 报 告 书 ― 8
电子变压器8D报告(烧缺不良)案例

人)
期)
2020.03.20
Root cause analysis(根本原因分析):
因产品在射出时,没有及时清理模腔,使模具排气不顺利,出现原料不足的现象。
D5根本原因及 长期对策
(Root cause & Long term action(长期对策) long term action)
1 缺料:要求调机技术人员在生产前用铜刷清理模腔,以确保模腔无异物残留,利 于模腔的排气顺,减少缺料现象。 2 注塑时将溶损选别出来报废
(Prevention & DS8p标re准ad化)
(Standardizatio n)
要求巡检每2小时检查一次,针对次类似机种在厂内水平展开,从而杜类似现象在发生。 整理汇总存档,后续量产中连续追踪三批,进行标准化定型。
Approved by(核准)
Delta follow up/追踪
Report by(报告人) VQA Engineer verify(工程 师确认)
200318 200318
D2紧急处理 (Urgent Deal)
库存: 1000 在制品: 无 客户库存: 3000
Failure Q'ty(不良数) Failure rate(不良率) How much(产生费用) Who(客诉类型)
5 1.00%
/ 入料检验
D3现状分析 (Problem Analysis)
QA经理 生产部经理
/
主管
/
高管
工艺部经理
/
高管
Problem Analysis (对不良品进行现 融损不良 状分析)
Preliminary Analysis and why why escaped (初步原因分析&不良品外流原因确认):
8D 报告标签与实物不符
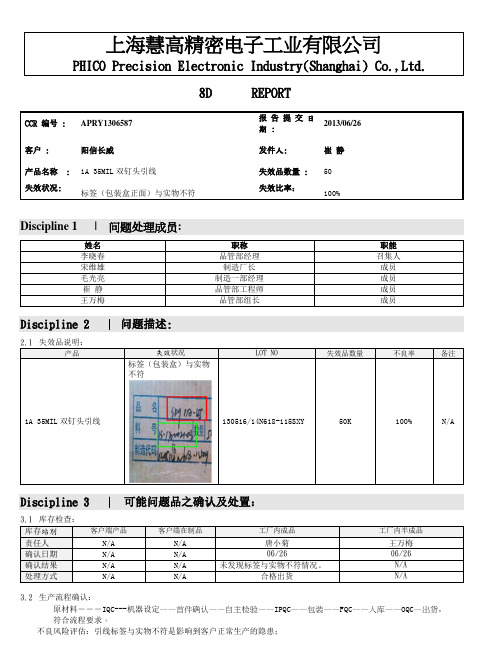
上海慧高精密电子工业有限公司PHICO Precision Electronic Industry(Shanghai) Co.,Ltd.8D REPORTCCR 编号 : APRY1306587报告提交日期 :2013/06/26客户 : 阳信长威发件人: 崔静产品名称 : 1A 35MIL双钉头引线失效品数量 : 50失效状况:标签(包装盒正面)与实物不符失效比率:100%Discipline 1 | 问题处理成员:姓名职称职能李晓春品管部经理召集人宋维雄制造厂长成员毛光亮制造一部经理成员崔静品管部工程师成员王万梅品管部组长成员Discipline 2 |问题描述:2.1 失效品说明:产品失效状况LOT NO 失效品数量不良率备注1A 35MIL双钉头引线标签(包装盒)与实物不符130516/14N618-115SXY 50K 100% N/ADiscipline 3 | 可能问题品之确认及处置:库存站別客户端产品客户端在制品工厂内成品工厂内半成品责任人N/A N/A唐小菊王万梅确认日期N/A N/A06/26 06/26确认结果N/A N/A未发现标签与实物不符情况。
N/A处理方式N/A N/A合格出货N/A3.2 生产流程确认:原材料―――IQC---机器设定——首件确认——自主检验——IPQC——包装——FQC——入库——OQC—出货,符合流程要求。
不良风险评估:引线标签与实物不符是影响到客户正常生产的隐患;Discipline 4 | 失效问题确认:4.1 失效样品确认:确认依据:根据对客户提供的不良图片分析,确认为引线标签与实物不符的现象。
确认结果:产品不合格。
4.2 问题品失效原因:4.3问题品流出原因:由于FQC出货检验时未抽查到,导致不良品流出。
Discipline 5 | 改善计划执行:Discipline 6 | 改善计划效果确认:6月25日起生产的产品符合规格要求。
Discipline 7 | 防止问题产品之再发生:Discipline 8 | 结语:8.1 持续改善。
实例-8D改善措施报告
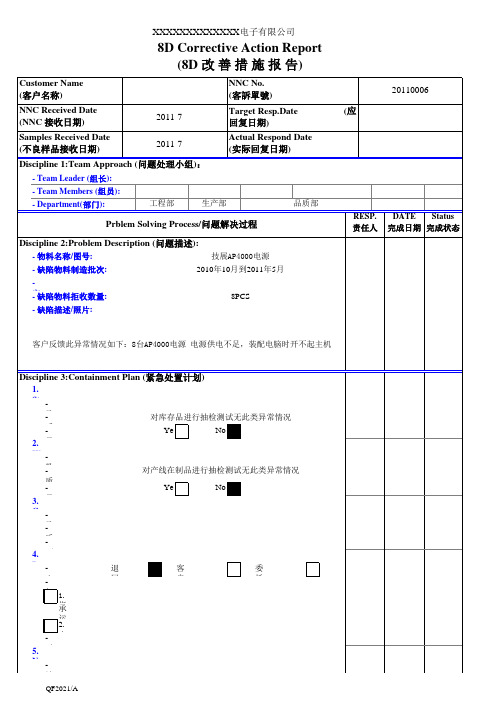
XXXXXXXXXXXXX电子有限公司
8D Corrective Action Report
(8D 改善措施报告)
- 送货数量:
- 原定的交期是否能按时完成?Yes No
Discipline 4:Describe The Root Cause (根本原因描述):
1. Root Cause (根本原因):
客户投诉的8PCS电源封条编码分别为:① 8429566(2011年1月)②7340100(2011年3月的)③6991373(2010年10月)④ 7240224(2011年4月)⑤7371092(2011年3月)⑥7061714(2010年10月)⑦
6876661(2010年7月)⑧509809(2011年5月)
对以上8台电源进行全面测试,结果如下:①-⑥的6台电源均为好机高压、负载测试、线材测试均正常,⑦⑧(封条编码:6876661和
509809)2台电源测试时有敲保护现象
进一步分析结果如下:⑦6876661电源R05与IC的10脚相碰
⑧509809电源R05与R22脚相碰造成电源敲机测试时出现敲保护现象
测试、异常原因截图见附件1,对6台良品电源进行装机老化测试,老化时间为4小时,老化后电源均为良品,老化情况见附件2/sheet1
⑧509809电源R05与
R22脚相碰
⑦6876661电源R05
与IC的10脚相碰。
手把手教你写客户满意的人为操作失误8D报告
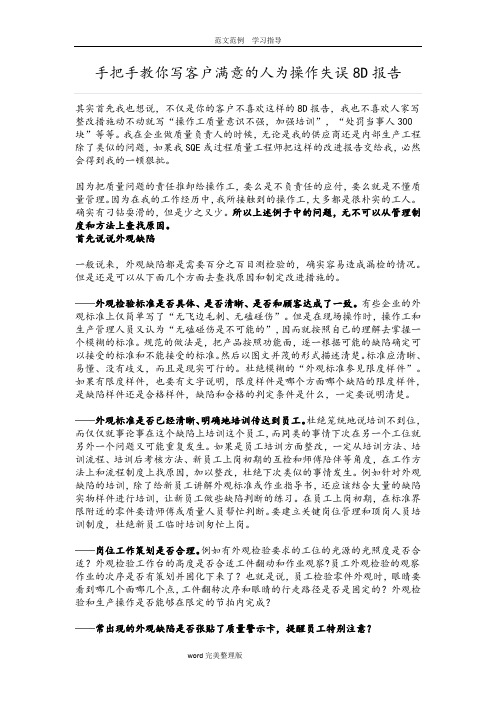
其实首先我也想说,不仅是你的客户不喜欢这样的8D报告,我也不喜欢人家写整改措施动不动就写“操作工质量意识不强,加强培训”,“处罚当事人300块”等等。
我在企业做质量负责人的时候,无论是我的供应商还是内部生产工程除了类似的问题,如果我SQE或过程质量工程师把这样的改进报告交给我,必然会得到我的一顿狠批。
因为把质量问题的责任推卸给操作工,要么是不负责任的应付,要么就是不懂质量管理。
因为在我的工作经历中,我所接触到的操作工,大多都是很朴实的工人。
确实有刁钻耍滑的,但是少之又少。
所以上述例子中的问题,无不可以从管理制度和方法上查找原因。
首先说说外观缺陷一般说来,外观缺陷都是需要百分之百目测检验的,确实容易造成漏检的情况。
但是还是可以从下面几个方面去查找原因和制定改进措施的。
——外观检验标准是否具体、是否清晰、是否和顾客达成了一致。
有些企业的外观标准上仅简单写了“无飞边毛刺、无磕碰伤”。
但是在现场操作时,操作工和生产管理人员又认为“无磕碰伤是不可能的”,因而就按照自己的理解去掌握一个模糊的标准。
规范的做法是,把产品按照功能面,逐一根据可能的缺陷确定可以接受的标准和不能接受的标准。
然后以图文并茂的形式描述清楚。
标准应清晰、易懂、没有歧义,而且是现实可行的。
杜绝模糊的“外观标准参见限度样件”。
如果有限度样件,也要有文字说明,限度样件是哪个方面哪个缺陷的限度样件,是缺陷样件还是合格样件,缺陷和合格的判定条件是什么,一定要说明清楚。
——外观标准是否已经清晰、明确地培训传达到员工。
杜绝笼统地说培训不到位,而仅仅就事论事在这个缺陷上培训这个员工,而同类的事情下次在另一个工位就另外一个问题又可能重复发生。
如果是员工培训方面整改,一定从培训方法、培训流程、培训后考核方法、新员工上岗初期的互检和师傅陪伴等角度,在工作方法上和流程制度上找原因,加以整改,杜绝下次类似的事情发生。
例如针对外观缺陷的培训,除了给新员工讲解外观标准或作业指导书,还应该结合大量的缺陷实物样件进行培训,让新员工做些缺陷判断的练习。