-第八章冲模结构及设计
冲压模具结构及设计PPT课件( 32页)

设计时采用经验公式: C (1 .5~2 .0 )t (C 3 m)m
第八章 冲压模具结构及设计
(五)凸模长度计算 当采用固定卸料板和导料板时,其凸模长度按下式计算: Lh1h2h3h 当采用弹压卸料板时,其凸模长度按下式计算:
Lh1h2th
角选取与加工方法有关:放电加工 4'~20',
(落料模 10' ,复合模 5' );机械加工经
钳工精修 15'~30'
机加工β =2。~3。;电火花加工β <1。;线切割加 工 β =1。~1.5。。
第八章 冲压模具结构及设计
5、锥形凹模 用于冲裁薄料和凹模厚度较薄的情况。
•
9、照自己的意思去理解自己,不要小看自己,被别人的意见引入歧途。
•
10、没人能让我输,除非我不想赢!
•
11、花开不是为了花落,而是为了开的更加灿烂。
•
12、随随便便浪费的时间,再也不能赢回来。
•
13、不管从什么时候开始,重要的是开始以后不要停止;不管在什么时候结束,重要的是结束以后不要后悔。
•
14、当你决定坚持一件事情,全世界都会为你让路。
第一节 冲压模具及零件的分类
模具设计主要是确定模具的类型、结构和模具零件的 选用、设计与计算。
一、冲压模具的分类
(1)按工序性质划分 冲裁模、弯曲模、拉深模等。
(2) 按工序组合程度划分 单工序模、级进模、复合模。
第八章 冲压模具结构及设计
(3)按导向方式划分 无导向的开式模、有导向的导板模、导柱模等。
第八章 冲压模具结构及设计
本章目录
第一节 冲压模具及零件的分类 第二节 冲压模具主要零件设计 第三节 级进模结构设计要点 第四节 冲压模具设计要点 第五节 冲压设备的选择 第六节 复合模结构分析 第七节 级进模结构分析 第八节 冲压模具设计实例分析
注塑模具实用教程第8章注塑模结构件设计ppt课件
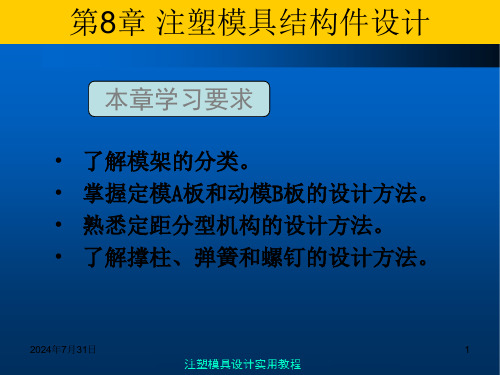
定模A板和动模B板的尺寸取决于内模镶件的外形尺寸,而内模 镶件的外形尺寸又取决于塑件的尺寸、结构特点和数量,内模镶 件设计详见第7章《注塑模具成型零件设计》。
从经济学的角度来看,在满足刚度和强度要求的前提下,模具 的结构尺寸越小越好。
确定定模A板和动模B板的尺寸常用计算法和经验法二种,在实 际工作过程中常用经验法。
2024年7月31日
20
第8章 注塑模具结构件设计
1.计算方法(相关公式见书) 2.经验确定法
模架长宽尺寸E和取决于内模镶件的长宽尺寸A和B,即A、B 板的开框尺寸。
2024年7月31日
21
第8章 注塑模具结构件设计
(1)A、B板的宽度尺寸确定。 一般来说在没有侧向抽芯
的模具中,模板开框尺寸A应大致等于模架推件固定板宽度尺寸C, 在标准模架中,尺寸C和E是一一对应的,所以知道尺寸A就可以 在标准模架手册中找到模架宽度尺寸E。
2024年7月31日
2
第8章 注塑模具结构件设计
8.1 概述
8.1.1 本章主要内容
• ① 模架的规格型号; • ② 动模板和定模板的设计; • ④ 方铁什么情况下要加高; • ⑤ 定距分型结构的设计; • ⑥ 撑柱的设计; • ⑦ 复位弹簧设计; • ⑧ 定位圈的设计; • ⑨ 紧固螺钉的设计。
2024年7月31日
29
第8章 注塑模具结构件设计
注意:① 表中的“A×B”和“框深a”均指动模板开框的长、 宽和深; ② 动模B板高度B等于开框深度a加钢厚Ha,向上取标准值 (公制一般为10的倍数); ③ 如果动模有侧抽芯,有滑块槽,或因推杆太多而无法加撑 柱时,须在表中数据的基础上再加5~10mm; ④动模板高度尽量取大些,以增加模具的强度和刚度。 动、定模板的长、宽和高度尺寸都已标准化,设计时尽量取 标准值,避免采用非标模架。
冲压模具设计与制造-冲模结构及设计

压力完成金属片的塑性变形。
模,确保冲压过程的准确性和
冲压过程中保持金属片的稳定
稳定性。
性。
冲模设计的基本步骤
1
产品需求分析
根据产品要求和设计需求,分析冲压模具设计的具体要求。
2
模具结构设计
根据产品形状和冲压工艺,设计模具的结构和布局。
3
零部件设计
设计模具的各个零部件,如上模、下模、导柱和导套。
4
模具制造加工
现代冲模设计的趋势和发展方向
自动化和智能化
设计软件的应用
新材料的应用
趋向于自动化生产和智能化控
借助设计软件进行模具设计和仿
研究和应用新材料,提高模具的
制,提高冲压生产效率。
真分析,提高设计质量和效率。
耐磨性和寿命。
冲压模具的分类
按工艺分类 ️
按使用行业分类
包括单工位模具、连续模具和复合模具等。
例如汽车模具、家电模具和电子模具等。
按制造工艺分类
包括压力模具、拉伸模具和弯曲模具等。
冲模结构的基本原理
上模和下模
导柱和导套 ⚙️
顶杆和顶板
上模和下模相互作用,通过冲
导柱和导套用于定位上模和下
顶杆和顶板用于施加压力,在
冲压模具设计与制造-冲
模结构及设计
冲压模具设计与制造的背景:随着工业的发展,冲压模具在制造过程中起着
至关重要的作用。
冲压模的定义
1
关键组成部分 ️
冲压模具由上模、下模和导柱组成,用于完成冲压加工过程。
2
功能和作用 ⚙️
冲压模具用于塑造金属片,例如冲压出汽车零部件等。
3
高精度要求
冲压模具需要具备高精度和稳定性,以确保产品质量。
第八章冲模结构与设计一-四
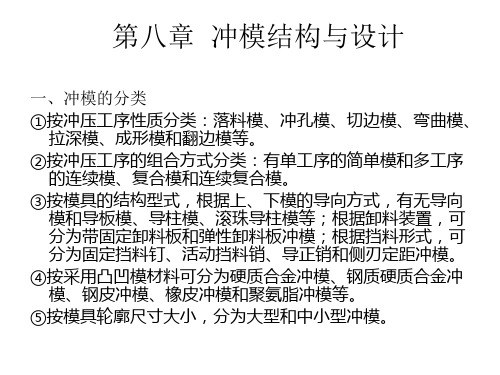
7.冲模零件的材料选用 • 冲模材料,尤其是凸、凹模材料,与模具寿命的 关系很大。在模具设计选用材料时,要求满足一 定的硬度、强度和韧性要求,在可能的情况下还 要考虑减低成本。 • 凸、凹模常用材料及其热处理要求可见P238表8- 13,模具其它零件的材料和热处理要求见P238表8 -14。 • 附带说明:表8-14中列出的材料A3为普通碳素结 构钢(甲类),现采用新牌号为Q235(其屈服强 度约为235MPa).
• 4.凸、凹模和垫板等零件的强度计算以及弹 簧、橡皮等弹性零件的计算和选用 • 5.选择冲压设备 • 6.绘制模具总图,列出模具零件明细表和标 准件清单,绘制模具零件图,提出各种技 术要求。 在《冲压模具课程设计》(2个星期) 中将进行一次较全面的训练。 [完]
F
F0
F1
工作负荷P和工作时的压缩量F 必须控制在弹簧的极限范围之内, 即P<P1(=P0+ Δ P),F < F1 (=F0+ Δ F),这就是设计弹簧 的依据。
卸料弹簧的选用方法
• 右图中,S1——空载时凸模 缩入卸料板内的距离 S2——工作时凸模伸入凹模刃 口内的距离 S3——旧凸模相对于新凸模的 最大磨削量 t——板料厚度 工作时凸模前端的最大工作行程(=总行程 -空行程),即卸料弹簧的相对压缩量为
四.模具设计的步骤和内容
• 1.根据工艺分析选定模具种类,确定模具结 构型式(P239) • 2.确定模具的压力中心 模具压力中心是冲裁时合力的作用点。 模具压力中心应位于模柄轴线上,与压力 机滑块中心一致。否则,冲压时会产生偏 载,导致模具以及压力机滑块与导轨的急 剧摩擦,降低模具和压力机使用寿命。
第八章 冲模结构与设计
一、冲模的分类 ①按冲压工序性质分类:落料模、冲孔模、切边模、弯曲模、 拉深模、成形模和翻边模等。 ②按冲压工序的组合方式分类:有单工序的简单模和多工序 的连续模、复合模和连续复合模。 ③按模具的结构型式,根据上、下模的导向方式,有无导向 模和导板模、导柱模、滚珠导柱模等;根据卸料装置,可 分为带固定卸料板和弹性卸料板冲模;根据挡料形式,可 分为固定挡料钉、活动挡料销、导正销和侧刃定距冲模。 ④按采用凸凹模材料可分为硬质合金冲模、钢质硬质合金冲 模、钢皮冲模、橡皮冲模和聚氨脂冲模等。 ⑤按模具轮廓尺寸大小,分为大型和中小型冲模。
冲压模具设计与制造-冲模结构及设计
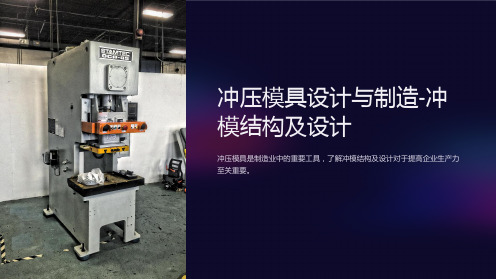
存储液压系统所需的油液,通过油泵加压作用 于液压缸、阀门等部件。
冲模设计-材料选择
冷硬性
材料的硬度越高越难冲压,当然硬度越高的材料强 度和韧性越好。
热延性
材料的热延性越好,形变过程中的抗力就越小,越 容易冲出完整的形状。
塑性变形
材料的塑性变形越大,就越容易在制造过程中出现 毛边、裂纹等不良现象。
冲模设计-模具结构设计
构件要求
• 表面应经过精细加工 • 工件切口处应防止毛刺 • 件与件连接处应精确匹配
技术要求
• 壳体设有去气槽 • 导向、顶出、顶针等机构要结合工件特性设
计合理布置 • 穿孔器、切床等工具要相互匹配
冲模设计-角度设计
1 角度选取
根据材料和凸模角度之间的摩擦系数,选取适合的凸模工作角度。
定位销
通过定位销使得模具装配过程中上下啮合间隙 在同一方向消除,保证上下模在生产运行过程 中不发生左右晃动、卡死。
滑移销
一般用在弯曲模上,使得模具在正常运行过程 中能够保持产品轴线在同一平面内转动。
限位销
适用于弯曲模、月牙形模等多向度运动的模具, 避免发生与底板接触,保证正常冲裁顺利进行。
承重销
用于超大模具,保证模具在运行过程中不会发 生变形、受力不均等情况。
冲头及底板
冲头和底板位于模具上、下两个构件间,承受升降 架、压脚和切角等附属部件,不能承受冲压抗力。
升降架
升降架也称为移载板,起支架、供模颗、导向等方 便的作用。
冲模结构-顶出机构
弹簧复位-主要应用于冲裁模
顶出呈圆柱形,与上模座固连,下端通过影响 杆与活塞连接。
高弹性橡胶板顶出-主要应用于细长件 模
冲模设计-回头阀设计
第8章冲模结构与设计
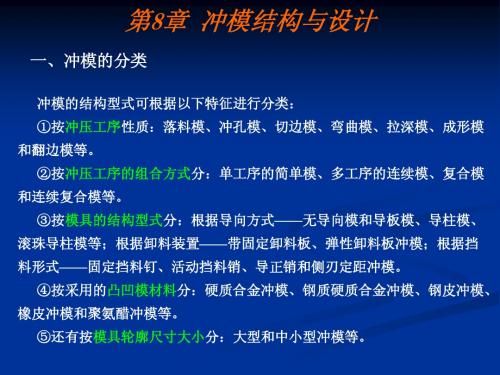
特点:与单工序模相比,主要优点是生产效率和冲压件精度高,
图8-29为冲压电机定子的落料、冲孔复合模。该模具的落料凹模5 在上部,凸凹模8固定在下部,故称为倒装式复合模。
倒装式模具的特点 是每次冲压后,冲 压件由推料板16推 出,不留在凹模内, 所以冲压件比较平 整,适于冲压薄的 材料。
图8-30所示的落料、冲孔模,落料凹模固定在下部,凸模在上 部,称为顺装式复合模。
有时为了便于卸件、半成品定位和防止拉深时的零件偏移, 在反向拉深时也有带压边圈的,如图8-27和图8-28所示。
2、复合模
定义:复合模是在压力机的一次行程内在模具的一个工位上完
成两道以上冲压工序的模具,是一种多工序冲压模。 类型:落料和冲孔复合模、落科和首次拉深复合模等。 其缺点是模具结构复杂,不易制造。 适用于:生产精度要求较高的软材料或薄板料冲压件。
图8-15所示的U形件弯曲模,凹模1是摆动式的。
弯曲时,毛坯由定位板2定位,凸模3下行,凹模绕轴销5摆动。 弯曲后,顶杆4在弹簧作用下,使凹模复位,同时顶出U形件。 该模具可以避免图8-14所示弯曲模的缺点。
3) 圆形件弯曲模
图8-16a所示的圆形件弯曲 模系由两套简单弯曲模组
成的,先预弯成波浪形,
冲压时,零件变形很 小,平整度更高—— 该模具适于冲孔精度
要求高的零件冲压。
缺点:零件和废料同 时卸落在凹模上,每 次冲压后,必须同时
取件和清理废料。
(图中压料块1的作用 是卸下废料)
5) 带小导柱和弹性卸料板的冲孔模
上、下模除用导柱和导套 导向外,还设计了小导柱
和弹性卸料板以及凸模和
弹性卸料板的精确导向, 所以该冲孔模的冲孔精度
2) 图8-35为冲孔、切边和落料连续模,图8-36为零件图和排样图 特点:采用侧刃 (图中1、2)切边 定位,侧刃长度a 恰为条料每次送 料距离,所以该 连续模的送料步 距。 应用:该模具可以 同时冲压两个工件, 工件之间无间隙, 材料利用率高,而 落料凸模形状比较 简单,便于制造和 修理。
冲压模具结构及其设计介绍

3. 磷青铜片PBS(Phosphor Bronze Spring)
磷青铜是青铜(铜锌合金)添加脱氧剂(P)及其 它微量元素如Fe组成的,具有较强的延展性和 耐疲劳性。
主要作用:电气开关,端子,EMI等弹片及导电材 料,材料强度差于不锈钢,一般表面需要电镀。 分类:根据金属元素的含量及加工工艺分,常用 的牌号有C5102, C5191, C5212, C5210等。
6.打沙拉孔设计标准
• • • 沙拉孔的成形步骤:a.先打沙拉后冲孔 b.先冲孔后打沙拉 c.先冲孔,打沙拉, 再冲孔 沙拉孔分为两种:a.淺沙拉孔 b.深沙拉孔 1. 浅沙拉孔分为三个步骤,第一步,先沖底孔,第二步,打沙拉孔,第三步, 再沖沙拉過孔,具体尺寸见下图示意.
2. 深沙拉孔分为两个步骤,第一步,先沖底孔, 第二步,打沙拉孔
2. SUS304 含碳量低于SUS301,所以强度硬度低于301,但由 于添加了Ni抗腐蚀能力较强。通过热处理能够 得到较高强度和硬度的材料,广泛应用于EMI要 求的cover和Bracket. 3. 特殊功能要求的不锈钢产品 a.外观件:光面,绒面,耐指纹 b.添加特殊的元素达到一些特殊的性能要求, 如添加Ag增加抗菌性能等等。
2. SECC
(1).电镀锌钢板是一般的冷轧钢板在连续电镀锌 产线 经过脱脂、酸洗、电镀及各种后处理 后的产品。 (2).SECC与SPCC一样,根据拉伸等级分为SECC、 SECD、SECE。 (3).SECC的特点是自身带有镀锌层,防腐蚀性能 良好,可以直接作为产品的外观件,所以近几 年来,在电子行业广泛应用并逐步取代SPCC。 缺点是断口容易生锈。
7.滑块结构设计标准
滑块固定形式常用的有如下几种﹕ a. 适用于中小形滑块﹐依靠滑块的垂直边限位(如图1)﹔ b. 适用于以共用方式加工的大型滑块﹐限位块采用入块形式 (如图2)﹔ c. 适用于需快速装卸的大中型滑块﹐依靠滑块底部的限位板限 位(如图3)﹔ d. 适用于需要滑块在接触料片前先复位的场合﹐靠滑块中的顶 料销作用﹐先將滑块复位﹐顶料销长度通常为7mm﹐浮出端 面2.0mm﹐选用紅色扁线弹簧。(如图4) e. 适用于要求中间垂直p上下运动﹐左右滑块水平运动的块 合﹐中间滑块依靠內导柱导向﹐左右滑块用等高套筒限位﹐ 等高套筒长度取夾板厚度加0.5mm。(如图5)
冷冲压模具试题库

《冲压模具与设备》试题库绪论一、填空(每空1分)T-1-1-01-2-3、冷冲压是利用安装在上的对材料施加外力,使其产生从而获得冲件的一种压力加工方法。
T-1-1-02-2-1、因为冷冲压主要是用加工成零件,所以又叫板料冲压。
T-1-1-03-2-1、冷冲压不但可以加工材料,而且还可以加工非金属材料。
T-1-2-04-2-1、冲模是利用压力机对金属或非金属材料(包括板料和型材)加压,使其而得到所需冲件的工艺装备。
T-1-2-05-2-2、冷冲压加工获得的零件一般无需进行加工,因而是一种节省原材料,节省能耗的少、无加工方法。
T-1-5-06-3-2、冷冲压工序按变形性质可分为、两大类。
T-1-5-07-4-1、冲件的产品尺寸稳定,互换性好,是因为其尺寸公差由保证。
二、判断题(正确的打√,错误的打×)(每题2分)P-1-1-01-2-2、冲模的制造一般是单件小批量生产,因此冲压制件也是单件小批量生产。
()P-1-1-02-2-2、落料和弯曲都属于分离工序,而拉深、翻边则属于变形工序。
()P-1-2-03-2-2、复合工序、连续工序、复合-连续工序都属于组合工序。
()P-1-2-04-2-2、分离工序是指对工件的剪裁和冲裁工序。
()P-1-2-05-2-2、所有的冲裁工序都属于分离工序。
()P-1-3-06-2-2、成形工序是指对工件弯曲、拉深、成形等工序。
()P-1-2-07-2-2、成形工序是指坯料在超过弹性极限条件下而获得一定形状。
()P-1-2-08-2-2、冷冲压不但可加工具有塑性的金属材料,而且还可加工非金属材料。
()P-1-3-09-2-2、冷冲压只能加工形状简单的零件。
()P-1-3-10-2-2、模具是冷冲压工艺不可缺少的至关重要的工具。
()P-1-5-11-2-2、冲压生产的自动化就是冲模的自动化。
()三、问答题D-1-1-01-2-5、冷冲压工序可分为哪两大类? 5分D-1-1-02-2-5、分离工序有哪些工序形式? 5分D-1-2-03-3-5、变形工序有哪些工序形式? 5分D-1-2-04-4-5、冲压工艺的特点?5分D-1-2-05-4-5、塑性变形的特点?5分第一章冲压成形原理与成形极限一、填空题(每空1分)T-1-1-01-3-1、塑性变形的物体体积保持。
冲裁模的结构与设计

定期检查与保养
定期检查冲裁模的外观和结构, 确保没有损坏或变形。
检查冲裁模的刃口是否锋利, 如需磨刃应及时进行。
定期对冲裁模进行润滑,以减 少磨损和保持其良好的工作状 态。
常见故障与排除方法
冲裁出的工件尺寸不稳定
检查冲裁模的刃口是否磨损或松动,调整刃 口间隙或更换磨损件。
冲裁出的工件表面质量差
检查冲裁模的刃口是否锋利,如需磨刃应及 时进行。
冲裁模的应用领域
汽车制造
汽车面板、座椅、车门等部件 的制造。
家用电器
洗衣机、冰箱、空调等产品的 制造。
电子行业
手机、电脑、平板等产品的制 造。
航空航天
飞机、火箭、卫星等高端设备 的制造。
02
冲裁模的结构
上模
01
上模是冲裁模的主要组 成部分,通常安装在冲 压机上。
02
03
04
上模主要由凸模、卸料 板、上模板和垫板等组 成。
标注模具各零件的尺寸、材 料和热处理要求。
绘制详细的装配图,包括各零 件之间的装配关系、配合尺寸
和连接方式等。
审核与修改设计
对设计完成的模具进行审核,确 保其满足工艺要求和结构形式要
求。
根据审核结果,对设计进行必要 的修改和完善。
与制造部门沟通,确保模具制造 的可行性和经济性。
05
冲裁模的维护与保养
04
冲裁模的设计流程
确定工艺要求
1
确定冲裁件的材料、尺寸、精度和表面质量要求。
2
分析冲裁件的工艺性,评估是否适合采用冲裁工 艺。
3
确定冲裁工艺方案,包括冲裁次数、工序组合方 式等。
确定模具结构形式
01
根据冲裁件形状、尺寸和精度要求,选择合适的模具结构形 式。
冲模基本结构.ppt

2020/4/8
15
成形模結構
局部結構( 三)
壓筋 常用形式:
2020/4/8
16
2020/4/8
17
2020/4/8
3
第一階段:彈性變形階段
凸模與材料接觸後,先將材
料壓平,繼而凸模及凹模刃
口壓入材料中,由於彎矩M
的作用,材料不僅產生彈性
壓縮且略有彎曲。隨著凸模
繼續壓入,材料在刃口部分
所受的應力也逐漸增大,直
到H1深度時,材料的內應力
達到了彈性極限,此為材料
2020/4/8
的彈性變形階段。
4
第二階段:塑性變形階段
凸模繼續壓入,壓力增加, 材料內的應力達到屈服極 限,產生塑性變形,隨著 塑性變形程度的增大,材 料內部的拉應力和彎矩隨 之增大。變形區材料硬化 加劇,當壓入深度達到H2 時,刃口附近的應力值達 到最大值,此為塑性變形 階段。
2020/4/8
5
第三階段:斷裂階段
凸模壓入深度達到H3時, 先後在凹凸模刃口側面 產生裂紋。裂紋產生後 沿最大剪應力方向向材 料內層發展,當凹、凸 模刃口處的裂紋相遇重 合時,材料便被剪斷分 離。此為斷裂階段。
沖模基本結構講析
講 師: 郭 鐵
2008/01/28
2020/4/8
1
目錄
沖孔模結構 復合模結構 成形模結構 結束語
2020/4/8
2
沖孔(落料)模
它是利用沖模在壓力機(俗稱沖床)上使 板料分離的一種沖壓工藝。它包括切斷、 落料、沖孔、修邊、切口等多種工序。主 要用於落料和沖孔工序。
冲压模具总体结构设计
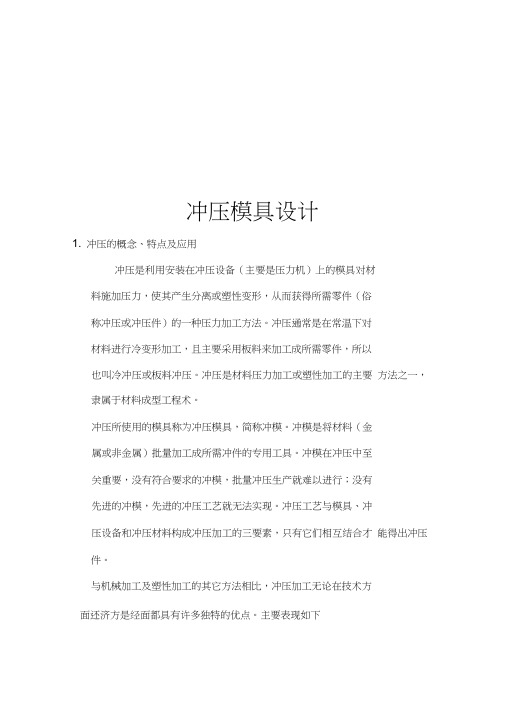
冲压模具设计1. 冲压的概念、特点及应用冲压是利用安装在冲压设备(主要是压力机)上的模具对材料施加压力,使其产生分离或塑性变形,从而获得所需零件(俗称冲压或冲压件)的一种压力加工方法。
冲压通常是在常温下对材料进行冷变形加工,且主要采用板料来加工成所需零件,所以也叫冷冲压或板料冲压。
冲压是材料压力加工或塑性加工的主要方法之一,隶属于材料成型工程术。
冲压所使用的模具称为冲压模具,简称冲模。
冲模是将材料(金属或非金属)批量加工成所需冲件的专用工具。
冲模在冲压中至关重要,没有符合要求的冲模,批量冲压生产就难以进行;没有先进的冲模,先进的冲压工艺就无法实现。
冲压工艺与模具、冲压设备和冲压材料构成冲压加工的三要素,只有它们相互结合才能得出冲压件。
与机械加工及塑性加工的其它方法相比,冲压加工无论在技术方面还济方是经面都具有许多独特的优点。
主要表现如下(1)冲压加工的生产效率高,且操作方便,易于实现机械化与自动化。
这是因为冲压是依靠冲模和冲压设备来完成加工,普通压力机的行程次数为每分钟可达几十次,高速压力要每分钟可达数百次甚至千次以上,而且每次冲压行程就可能得到一个冲件。
(2)冲压时由于模具保证了冲压件的尺寸与形状精度,且一般不破坏冲压件的表面质量, 而模具的寿命一般较长, 所以冲压的质量稳定, 互换性好, 具有“一模一样”的特征。
(3)冲压可加工出尺寸范围较大、形状较复杂的零件,如小到钟表的秒表,大到汽车纵梁、覆盖件等,加上冲压时材料的冷变形硬化效应,冲压的强度和刚度均较高。
(4)冲压一般没有切屑碎料生成,材料的消耗较少,且不需其它加热设备,因而是一种省料,节能的加工方法,冲压件的成本较低。
但是,冲压加工所使用的模具一般具有专用性,有时一个复杂零件需要数套模具才能加工成形,且模具制造的精度高,技术要求高,是技术密集形产品。
所以,只有在冲压件生产批量较大的情况下,冲压加工的优点才能充分体现,从而获得较好的经济效益。
冲模结构1[1] 2
![冲模结构1[1] 2](https://img.taocdn.com/s3/m/64135f166c175f0e7cd137a3.png)
第三篇 冲压模具 第8章 冲模结构与设计冲模是冲压生产的主要工艺设备,冲模结构设计对冲压件品质、生产率及经济效益影响很大。
因此,了解冲模结构,研究和提高冲模的各项技术指标,对冲模设计和发展冲压技术是十分必要的。
8.1 冲模分类及其特点按不同的特征对冲模进行分类,其分类方法主要有:(1) 按冲压工序性质可分为冲裁模、拉深模、翻边模、胀形模、弯曲模……。
习惯上把冲裁模当作所有分离工序模的总称,包括落料模、冲孔模、切断模、切边模、半精冲模、精冲模及整修模等。
(2) 按冲压工序的组合方式可分为单工序模、级进模和复合模。
1)单工序模 在压力机一次冲压行程内,完成一道冲压工序的模具。
2)级进模 在压力机一次冲程内,在模具不同工位上完成多道冲压工序的模具。
3)复合模 在压力机一次行程内,在模具一个工位上完成两道以上冲压工序的模具。
三种模具的简单比较如表8-1。
(3) 按模具的结构形式,根据有无导向装置和不同的导向装置形式可分为无导向的开式模、有导向的导板模、导筒模、导柱模等;根据挡料或定位方式可分固定挡料销、活动挡料销、导正销和侧刃定距冲模;根据卸料方式可分为带刚性卸料板和带弹性卸料板的冲模。
(4) 按进料、出件及排除废料方式可分为手动模、半自动模、自动模。
(5) 按模具零件组合通用程度可分为专用模(包括简易模)和组合冲模。
(6) 按凸、凹模材料可分钢模、硬质合金模、钢结硬质合金模、聚氨酯模、低熔点合金模等。
(7) 按模具轮廓尺寸可分为大型模、中型模、小型模等。
8.2 冲模零部件分类及功能各种类型冲模复杂程度不同,所含零件各有差异,但根据其作用都可归纳为如下五种类型:(1) 工作零件工作零件直接使被加工材料变形、分离,而成为工件,如凸模、凹模、凸凹模等。
(2) 定位零件定位零件控制条料的送进方向和送料进距,确保条料在冲模中的正确位置,有挡料销、导正销、导尺、定位销、定位板、导料板、侧压板和侧刃等。