HYDRAULIC PRESSURE SIGNAL DENOISING USING THRESHOLD SELF-LEARNING WAVELET ALGORITHM
泵厂Parker Hannifin公司产品说明书:R4V和R6V比例压力放电压值值
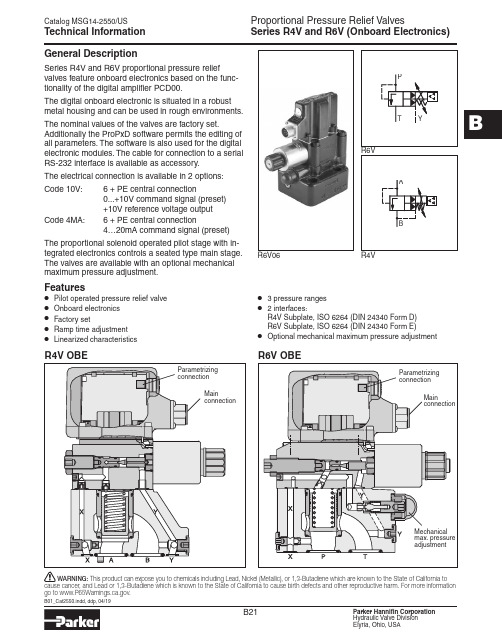
General DescriptionSeries R4V and R6V proportional pressure relief valves feature onboard electronics based on the func-tionality of the digital amplifier PCD00.The digital onboard electronic is situated in a robust metal housing and can be used in rough environments. The nominal values of the valves are factory set.Additionally the ProPxD software permits the editing of all parameters. The software is also used for the digital electronic modules. The cable for connection to a serial RS-232 interface is available as accessory. The electrical connection is available in 2 options:Code 10V: 6 + PE central connection0...+10V command signal (preset) +10V reference voltage output Code 4MA: 6 + PE central connection4…20mA command signal (preset)The proportional solenoid operated pilot stage with in-tegrated electronics controls a seated type main stage. The valves are available with an optional mechanical maximum pressure adjustment.Features• Pilot operated pressure relief valve • Onboard electronics • Factory set• Ramp time adjustment • Linearized characteristics• 3 pressure ranges • 2 interfaces: R4V Subplate, ISO 6264 (DIN 24340 Form D) R6V Subplate, ISO 6264 (DIN 24340 Form E)•Optional mechanical maximum pressure adjustmentR6V06This product can expose you to chemicals including Lead, Nickel (Metallic), or 1,3-Butadiene which are known to the State of California to go to .Ordering Information P r e s s u r e p (% o f m a x i m a l p r e s s u r e )Signal/Pressure Curve – R4V100100204060808060402000Command Signal (%)Performance CurvesP r e s s u r e p (% o f m a x i m a l p r e s s u r e )10010020406080080604020Signal/Pressure Curve – R6V0Command Signal (%)Pressure Maximum Interface 5RSizeDrain Pressure Proportional PInputSignalSealC ode Description 1 Nitrile5 FluorocarbonDesign SeriesC ode DescriptionPN without Mechanical maximum adjustmentPM with Mechanical maximum adjustmentPilot OptionsC odeDescription 10V 0...+10V with ` ref. output +10V 4MA 4...20mARelief VOptions Check with FactoryC ode DescriptionA R4V BR6VWeight:R4V03 4.5 kg (9.9 lbs.) R4V06 6.3 kg (13.9 lbs.) R4V10 7.8 kg (17.2 lbs.) R6V03 5.4 kg (11.9 lbs.) R6V06 6.6 kg (14.6 lbs.) R6V108.6 kg (19.0 lbs.)R4V03 BK505 R4V06 BK485 R4V10 BK506 R6V03 BK494 R6V06 BK366 R6V10 BK507Series R4V (Onboard Electronics)51020152530P r e s s u r e pMinimum Pressure Curve – R4V06210140703502803719567493Flow (Q)LPMGPMPerformance Curves90506030150120168243240Flow (Q)P r e s s u r e pp/Q Performance Curve – R4V03LPMGPM21050140703502803719567493Flow (Q)P r e s s u r e pp/Q Performance Curve – R4V06LPMGPM390502601306505206934103138172Flow (Q)P r e s s u r e pp/Q Performance Curve – R4V10LPMGPM 51020152530906030150120168243240Flow (Q)P r e s s u r e pMinimum Pressure Curve – R4V03LPMGPM102040305060P r e s s u r e pMinimum Pressure Curve – R4V103902601306505206934103138172Flow (Q)LPMGPMSeries R4V and R6V (Onboard Electronics) Block Diagrams – WiringCode 10V6 + PE acc. EN 175201-804Code 4MA6 + PE acc. EN 175201-804Series R4V and R6V (Onboard Electronics)Technical Information The parametrizing cable may be ordered under item no. 40982923.Features• Simple editing of all parameters• Storage and loading of optimized parameter adjustments • Executable with all Windows ®operating systems fromWindows ®95 upwards• Communication between PC and electronics via serialinterface RS-232The valve electronics cannot be connected to a PC with a standard USB cable – this can result in damages of PC and/or valve electronics.Simple to use interface program. Download free of charge /propxdProPxD Interface ProgramThe ProPxD software allows quick and easy setting of the digital valve electronics. Individual parameters as well as complete settings can be viewed, changed and saved via the comfortable user interface. Parameter sets saved in the non-volatile memory can be loaded to other valves of the same type or printed out for documentation purposes.Inch equivalents for millimeter dimensions are shown in (**)NGISO-Codex1x2x3x4x5x6x7y1y2y3y4y5y6106264-06-07-*-9742.9 (1.69)35.8 (1.41)21.5 (0.85)–7.2 (0.28)21.5(0.85)066.7 (2.63)58.8 (2.31)33.4 (1.31)7.9 (0.31)14.3 (0.56)–256264-08-11-*-9760.3 (2.37)49.2 (1.94)39.7 (1.56)–11.1 (0.44)20.6(0.81)079.4 (3.13)73 (2.87)39.7 (1.56) 6.4 (0.25)15.9 (0.63)–326264-10-15-*-9784.2 (3.31)67.5 (2.66)59.5 (2.34)42.1 (1.66)16.7 (0.66)24.6(0.97)96.8 (3.81)92.8 (3.65)48.4 (1.91)3.8 (0.15)21.4 (0.84)–Tolerance at X and Y pin holes and screw holes ±0.1, at port holes ±0.2.NG ISO-Code B1B2H1H2H3H4H5H6L1L2L3L4L5L6106264-06-07-*-9787.3 (3.44)33.4 (1.31)200.3 (7.89)21.0 (0.83)60.0 (2.36)102.0 (4.02)151.0 (5.94)30.0 (1.18)25.0 (0.98)90.8 (3.57)164.2 (6.46) 4.5 (0.18)––256264-08-11-*-97105.0 (4.13)39.7 (1.56)226.8 (8.93)29.0 (1.14)86.5 (3.41)128.5 (5.06)184.0 (7.24)30.0 (1.18)30.9 (1.22)123.0 (4.84)164.2 (6.46) 4.5 (0.18)––326264-10-15-*-97120.0 (4.72)48.4 (1.91)237.3 (9.34)29.0 (1.14)97.0 (3.82)139.0 (5.47)194.5 (7.66)30.0 (1.18)29.8 (1.17)143.5 (5.65)164.2 (6.46) 4.5 (0.18)––NG ISO-Code d1max d2max d3t3d4t4d5d6Subplate 106264-06-07-*-9715.0 (0.59)7.0 (0.28)7.1 (0.28)8.0 (0.31)M1016.0 (0.63)10.8 (0.43)17.0 (0.67)SPP3M6B910256264-08-11-*-9723.4 (0.92)7.1 (0.28)7.1 (0.28)8.0 (0.31)M1018.0 (0.71)10.8 (0.43)17.0 (0.67)SPP6M8B910326264-10-15-*-9732.0 (1.26)7.1 (0.28)7.1 (0.28)8.0 (0.31)M1020.0 (0.79)10.8 (0.43)17.0 (0.67)SPP10M12B910*Please combine seal kit of one size with seal kit of Prop. Section P2 for complete seal kit.。
CG2V-6 8, 10 Series; CG5V-6 8, 20 Series 双阶段压力限制或控

GB-2323ACG2V-6/8, 10 Series; CG5V-6/8, 20 Series Maximum pressure350 bar . . . . . . . . . .(5000 psi)Maximum ow 400 L/min. . . . . . . . . . . . . (106 USgpm)Mounting face to ISO 6264:CG*V-6 valves AR-06-2-A . . . . . . . . . . . . CG*V-8 valves AS-08-2-A. . . . . . . . . . . General DescriptionThese two-stage valves are used to limit or control pressure by directing up to the total system uid ow to reservoir when system pressure reaches the setting of the valve. System actuators are thus protected against overload.Each relief valve incorporates a vent port that can be connected to a separate pilot control valve to remotely control or unload system pressure.Two types of valve are presented in this catalog:CG2V-***, 10 series: relief/sequencevalve with integral manual adjustment of pressure setting.CG5V-***, 20 series: relief valve with solenoid operated pilot valve for loading/unloading.A third type, KCG-*, 10 series, with proportional pilot control valve, is described in catalog 2324.Features and Bene tsClose matching to application requirements from choice of four adjustment control ranges covering 3 to 350 bar (44 to 5000 psi).Electrical on/o load from solenoid controlled models.Remote parallel control by other pilot valves connected to “vent” port.High machine productivity resulting from full system ow being available for work output until system pressure is very close to valve setting.Pressure override optimized without detriment to other performance parameters.Excellent repeatability and stable performance from cartridge-type design of mainstage parts.Low o -load power wastage.International mounting interfaces.Low installed cost and spacerequirement from high power/size ratios (more than double that of many conventional designs).Pressure Relief and Sequence ValvesVickers by Danfoss®Pressure ReliefAF439975160003en-000101Side drain portIf a valve with an integral, reverse free- ow check is required, use a type RCG valve, as in catalog 429.BFor Valves with Manual Adjustment Only(F3-)CG2V-***-1*123411(-1)5For Valves with Manual Adjustment Plus Electrical Load/Unload(F3-)CG5V- ***12349-D(-*)-(V)M-***(-L)-*5-2*67810112Functional SymbolsRelief valve, manually adjusted,CG2V-***-1* modelSequence valve, manually adjusted,CG2V-***-1-1* modelSolenoid controlled relief valve, pilots internally drained, CG5V-***-D-2* modelModel Codes3Operating DataData is typical with oil at 22 cSt (106 SUS) and at 50 C (122F)4VentingSystem pressure can be dropped to near-zero by connecting vent port X to reservoir through a suitable pilot valve, e.g:5Control Data for CG2V ValvesManual adjustment of pressure setting described in “Installation Dimensions ”.Hydraulic Remote ControlRemote adjustment of pressure setting can be made by a pilot relief valve,substituted for the vent valve in the diagram. Suitable pilot relief valves are described in catalogs 411 (type C-175valves) and 409 (type CGR-02 valves).Control Data for CG5V Valves Vent FunctionThe solenoid operated pilot valve isVickers by Danfoss model type DG4V-3S, with spool type “0B ” (ref. catalog 2015). When the solenoid is de-energized, the CG5V relief valve is unloaded by venting the pilot drain to port T. Note that any back pressure at port T is additive to the minimum possible unloaded pressure,and is also additive to the on-load pressure setting.When the solenoid is energized the pilot ow is blocked to bring the relief valve on load. For this function port X would normally be blocked (e.g. no connection from the mounting face). Further remote control pressure settings are possible by connecting port X to suitable pilot relief valves via other DG4V-3S type directional control valves.1106Hydraulic FluidsAll valves can be used with:Antiwear hydraulic oils (class L-HM)Invert emulsions (class L-HFB)Water glycol (class L-HFC)Phosphate ester (class L-HFD), adding “F3-” pre x at model code .The extreme viscosity range is from 500 to 13 cSt (2270 to 70 SUS) but the recommended range is 54 to 13 cSt (245 to 70 SUS).For further information about uids see “Technical Information ” lea et 920.Temperature LimitsMinimum ambient: –20C (–4F)Maximum ambient:For CG2V valves: 70C (158F)For CG5V valves with coils listed inmodel code and at 110% of rated voltage:Coil type and frequencyMax. ambient temperature Dual frequency coils at 50 Hz at 60 Hz65 C (149F)65 C (149F)Single frequency (50 Hz) coils at 50 Hz 65C (149F)DC coils70 C (158F)Fluid temperatures (all models)PetroleumoilWater-containing Min.–20C (–4F)+10C (+50F)Max.*+70C (+158F)+54C (+129F)*To obtain optimum service life from bothuid and hydraulic system, 65 C (150F)normally is the maximum temperature except for water-containing uids.For synthetic uids consult uid manufacturer or Danfossrepresentative where limits are outside those of petroleum oil.Whatever the actual temperature range, ensure that viscosities stay within the limits speci ed in the “Hydraulic Fluids ” section.Contamination Control RequirementsRecommendations on contamination control methods and the selection of products to control uid condition areincluded in Vickers by Danfoss publication 9132 or 561,“Vickers by Danfoss Guide to Systemic Contamination Control ”. The book alsoincludes information on the Vickers by Danfoss concept of “ProActive Maintenance ”.The following recommendations are based on ISO cleanliness levels at2m, 5 m and 15 m. For products in this catalog the recommended levels are:Up to 210 bar (3050 psi)19/17/14. . . . . Above 210 bar (3050 psi)19/17/14. . . .Installation Dimensions in mm (inches)Micrometer Adjustment Options:“K” or “M” in Model Code“K” FeatureTo adjust pressure setting, insert key and turn clockwise. Turn micrometer knob clockwise to increase pressure setting; counter-clockwise to decrease setting. When the key is removed the knob can spin freely without a ecting the pressure setting.47Model A B C D E rad.Ø F (dia)G CG*V-658,0(2.3)35,0(1.4)68,0(2.7)35,0(1.4)12,0(0.5)20,0(0.78)79,0(3.1)CG*V-842,0(1.7)39,0(1.54)83,0(3.3)30,0(1.2)16,0(0.63)26,0(1.02)103,0(4.1)Model H Ø J (dia)K L M(AC coils)M(DC coils)CG*V-682,0(3.23)13,5(0.53)176,0(7.0)20,0(0.78)160,0(6.3)170,0(6.7)CG*V-8106,0(4.2)17,0(0.7)183,0(7.2)25,0(1.0)169,0(6.65)179,0(7.1)CG5V ModelsWith TypeFor dimensions “B” and “M”, see previous page.Connectors”.With Type “F” Coil Connection(“F(T)J” or “F(T)W” at model code )8Codes“FTJ” and “FTW”: lead wires connected into terminal For dimensions “B” and “M”, see previous page.strip suitable for M3 terminals on customer connection.89(0.24) deep min.remote port is not to be used10Mounting Surfaces, ISO 6264AR-06-2-A AS-08-2-AWhen a subplate is not used a raised pad must be provided for mounting. The pad must be at within0,001 mm/100 mm (0.0001/10) and smooth within 0,8 m (32 in).Dimensional tolerances are0,2 mm (0.008) except where indicated.Port functionsP =Pressure inlet T =Outlet to reservoirX =Vent, or remote pilot control portSize AB C D EF HJ K L AR-0680 (3.2)13,1 (0.5)53,8 (2.12)13,1 (0.5)47,5 (1.87)22,1 (0.87)22,1 (0.87)0 (0)13,1 (0.5)53,8 (2.12)AS-08118 (4.7)35,0 (1.4)66,7 (2.63)16,3 (0.7)55,6 (2.19)33,4 (1.35)11,1 (0.44)23,8 (0.94)16,0 (0.63)70,0 (2.76)Size M N Ø P (dia)Q Ø T (dia)Ø X (dia)Y thread x min. full thread depth Tolerance on bolt and pin locations 0,1 (0.004).These ISO standard dimensions can be used, but improved ow paths to and from valve are obtained by using 48,0 (1.89) instead of 47,5 (1.87), and 22,6 (0.89) instead of 22,1 (0.87).ISO standard does not give UNC bolt sizes. These are recommended equivalents to metric sizes speci ed in the standard.Installation DataMounting Attitude Unrestricted.SubplatesFor CG*V-6 valves see typeCGVM-6-10-R on previous page.For CG*V-8 valves consult your Vickers representative.Mounting Bolts/TorquesFor CG*V-6 valves: bolt kit BKCG2V-6.Bolts should be torqued to 103-127 Nm (76-94 lbf ft), with threads lubricated.For CG*V-8 valves: bolt kit BKCG2V-8.Bolts should be torqued to 257-315 Nm (190-232 lbf ft), with threads lubricated.Mass (approx.)CG2V-63,5 kg (7.7 lb). . . . . . . . . . . . . . . CG2V-84,4 kg (9.7 lb). . . . . . . . . . . . . . . CG5V-6:With AC solenoid 5,0 kg (11 lb). . . . . . . . With DC solenoid 5,2 kg (11.5 lb). . . . . . CG5V-8:AC solenoid 5,9 kg (13 lb). . . . . . . . . . . . DC solenoid 6,1 kg (13.5 lb). . . . . . . . . .Electrical Plugs and Connectors 8For CG5V valves with type F(T)J or F(T)W coils, see model code8For “FTJ ” or “FTW ” at model code 1.For DC coils the +ve lead(s) must be connected to the terminal(s) marked +. When using 3-wire incoming leads to double solenoid valves (i.e. common neutral) the inner pair of terminals must be linked. 2.For correct light indication of energized solenoid ensure that solenoid leads are correctly connected: light terminals are common with each outer pair of solenoid terminals according to the side with + mark.8For “FTJL ” or “FTWL ” at model code +89T11Plugs for ISO 4400 (DIN 43650) Type Coil ConnectionFor CG5V valves with type “U” coils(model code )The cable entry on these plugs can berepositioned at 90 intervals byreassembly of the contact holder relative to the plug housing. The cable entry isPg11 for cable Ø 6-10 mm (0.24-0.4).Terminal Strip and LightsOrdering ProcedureValves, subplates and bolt kits should beordered by full model code designation.Order plugs by part number.Order plugs separately by part number.Voltage Part number Gray (Sol.A)Black (Sol.B)Without indicator light –710776710775With indicator light12- 24V 100-125V 200-240V 977467977469977471977466977468977470Danfoss Power Solutions is a global manufacturer and supplier of high-quality hydraulic and electric components. We specialize in providing state-of-the-art technology and solutions marine sector. Building on our extensive applications expertise, we work closely with you to ensure exceptional performance for a broad range of applications. We help you and other customers around the world speed up system development, reduce costs and bring vehicles and vessels to market faster.Danfoss Power Solutions – your strongest partner in mobile hydraulics and mobile Go to for further product information.outstanding performance. And with an extensive network of Global Service Partners, we also provide you with comprehensive global service for all of our components.Local address:Danfoss Power Solutions GmbH & Co. OHG Krokamp 35D-24539 Neumünster, Germany Phone: +49 4321 871 0Danfoss Power Solutions ApS Nordborgvej 81DK-6430 Nordborg, Denmark Phone: +45 7488 2222Danfoss Power Solutions (US) Company 2800 East 13th Street Ames, IA 50010, USA Phone: +1 515 239 6000Danfoss Power Solutions Trading (Shanghai) Co., Ltd.Building #22, No. 1000 Jin Hai Rd Jin Qiao, Pudong New District Shanghai, China 201206Phone: +86 21 2080 6201Danfoss can accept no responsibility for possible errors in catalogues, brochures and other printed material. Danfoss reserves the right to alter its products without notice. This also applies to products agreed.All trademarks in this material are property of the respective companies. Danfoss and the Danfoss logotype are trademarks of Danfoss A/S. All rights reserved.© Danfoss | September 2022•Cartridge valves •DCV directional control valves •Electric converters •Electric machines •Electric motors •Gear motors •Gear pumps •Hydraulic integrated circuits (HICs)•Hydrostatic motors •Hydrostatic pumps •Orbital motors •PLUS+1® controllers •PLUS+1® displays •PLUS+1® joysticks and pedals •PLUS+1® operator interfaces •PLUS+1® sensors •PLUS+1® software •PLUS+1® software services,support and training •Position controls and sensors •PVG proportional valves •Steering components and systems•Telematics Hydro-Gear Daikin-Sauer-Danfoss 。
FLUENT软件操作界面中英文对照

FLUENT软件操作界面中英文对照编辑整理:尊敬的读者朋友们:这里是精品文档编辑中心,本文档内容是由我和我的同事精心编辑整理后发布的,发布之前我们对文中内容进行仔细校对,但是难免会有疏漏的地方,但是任然希望(FLUENT软件操作界面中英文对照)的内容能够给您的工作和学习带来便利。
同时也真诚的希望收到您的建议和反馈,这将是我们进步的源泉,前进的动力。
本文可编辑可修改,如果觉得对您有帮助请收藏以便随时查阅,最后祝您生活愉快业绩进步,以下为FLUENT软件操作界面中英文对照的全部内容。
FLUENT 软件操作界面中英文对照File 文件Grid 网格Models 模型 : solver 解算器Read 读取文件:scheme 方案 journal 日志profile 外形Write 保存文件Import:进入另一个运算程序Interpolate :窜改,插入Hardcopy : 复制,Batch options 一组选项Save layout 保存设计Pressure based 基于压力Density based 基于密度implicit 隐式, explicit 显示Space 空间:2D,axisymmetric(转动轴),axisymmetric swirl (漩涡转动轴);Time时间:steady 定常,unsteady 非定常Velocity formulation 制定速度:absolute绝对的; relative 相对的Gradient option 梯度选择:以单元作基础;以节点作基础;以单元作梯度的最小正方形。
Porous formulation 多孔的制定:superticial velocity 表面速度;physical velocity 物理速度;solver求解器Multiphase 多相 energy 能量方程Visous 湍流层流,流态选择Radiation 辐射Species 种类,形式(燃烧和化学反应)Discrete phase 离散局面Solidification & melting (凝固/熔化)Acoustics 声音学:broadband noise sources多频率噪音源models模型Materials 定义物质性质Phase 阶段,相Operating conditions 操作压力条件Boundary conditions 边界条件Periodic conditions 周期性条件Grid interfaces 两题边界的表面网格Dynamic mesh 动力学的网孔Mixing planes 混合飞机?混合翼面?Turbo topology 涡轮拓扑Injections 注射DTRM rays DTRM射线Custom field functions 常用函数Profiles 外观,Units 单位User-defined 用户自定义materials 材料Name 定义物质的名称 chemical formula 化学反应式 material type 物质类型(液体,固体)Fluent fluid materials 流动的物质 mixture 混合物order materials by 根据什么物质(名称/化学反应式)Fluent database 流体数据库 user-defined database 用户自定义数据库Propertles 物质性质从上往下分别是密度比热容导热系数粘滞系数Operating conditions操作条件操作压力设置:operating pressure操作压力reference pressure location 参考压力位置gravity 重力,地心引力gravitational Acceleration 重力加速度operating temperature 操作温度variable—density parameters 可变密度的参数specified operating density 确切的操作密度Boundary conditions边界条件设置Fluid定义流体Zone name区域名 material name 物质名 edit 编辑Porous zone 多空区域 laminar zone 薄层或者层状区域 source terms (源项?)Fixed values 固定值motion 运动rotation—axis origin旋转轴原点Rotation—axis direction 旋转轴方向Motion type 运动类型: stationary静止的; moving reference frame 移动参考框架; Moving mesh 移动网格Porous zone 多孔区Reaction 反应Source terms (源项)Fixed values 固定值velocity—inlet速度入口Momentum 动量 thermal 温度 radiation 辐射 species 种类DPM DPM模型(可用于模拟颗粒轨迹) multipahse 多项流UDS(User define scalar 是使用fluent求解额外变量的方法)Velocity specification method 速度规范方法: magnitude,normal to boundary 速度大小,速度垂直于边界;magnitude and direction 大小和方向;components 速度组成?Reference frame 参考系:absolute绝对的;Relative to adjacent cell zone 相对于邻近的单元区Velocity magnitude 速度的大小Turbulence 湍流Specification method 规范方法k and epsilon K—E方程:1 Turbulent kinetic energy湍流动能;2 turbulent dissipation rate 湍流耗散率Intensity and length scale 强度和尺寸: 1湍流强度 2 湍流尺度=0.07L(L为水力半径)intensity and viscosity rate强度和粘度率:1湍流强度2湍流年度率intensity and hydraulic diameter强度与水力直径:1湍流强度;2水力直径pressure-inlet压力入口Gauge total pressure 总压supersonic/initial gauge pressure 超音速/初始表压constant常数direction specification method 方向规范方法:1direction vector方向矢量;2 normal to boundary 垂直于边界mass—flow—inlet质量入口Mass flow specification method 质量流量规范方法:1 mass flow rate 质量流量;2 massFlux 质量通量 3mass flux with average mass flux 质量通量的平均通量supersonic/initial gauge pressure 超音速/初始表压direction specification method 方向规范方法:1direction vector方向矢量;2 normal to boundary 垂直于边界Reference frame 参考系:absolute绝对的;Relative to adjacent cell zone 相对于邻近的单元区pressure-outlet压力出口Gauge pressure表压backflow direction specification method 回流方向规范方法:1direction vector方向矢量;2 normal to boundary 垂直于边界;3 from neighboring cell 邻近单元Radial equilibrium pressure distribution 径向平衡压力分布Target mass flow rate 质量流量指向pressure-far—field压力远程Mach number 马赫数 x-component of flow direction X分量的流动方向outlet自由出流Flow rate weighting 流量比重inlet vent进口通风Loss coeffcient 损耗系数 1 constant 常数;2 piecewise—linear分段线性;3piecewise-polynomial 分段多项式;4 polynomial 多项式EditPolynomial Profile高次多项式型线Define 定义 in terms of 在一下方面 normal-velocity 正常速度 coefficients系数intake Fan进口风扇Pressure jump 压力跃 1 constant 常数;2 piecewise—linear分段线性;3piecewise—polynomial 分段多项式;4 polynomial 多项式exhaust fan排气扇对称边界(symmetry)周期性边界(periodic)Wall固壁边界adjicent cell zone相邻的单元区Wall motion 室壁运动:stationary wall 固定墙Shear condition 剪切条件: no slip 无滑;specified shear 指定的剪切;specularity coefficients 镜面放射系数 marangoni stress 马兰格尼压力?Wall roughness 壁面粗糙度:roughness height 粗糙高度 roughness constant粗糙常数Moving wall移动墙壁Translational 平移rotational 转动components 组成Solve/controls/solution 解决/控制/解决方案Equations 方程 under—relaxation factors 松弛因子: body forces 体积力Momentum动量 turbulent kinetic energy 湍流动能turbulent dissipation rate湍流耗散率Turbulent viscosity 湍流粘度 energy 能量Pressure-velocity coupling 压力速度耦合: simple ,simplec,plot和coupled是4种不同的算法。
英国版电压放大器用于压力阀门系列ED104安装手册说明书

Bulletin HY11-5715-481/UKPower Amplifier for Pressure ValvesInstallation Manual Series ED104Parker Hannifin GmbH & Co. KG Hydraulic Controls Division Gutenbergstr. 3841564 Kaarst, Germany Tel.: +49-181 99 44 43 0Fax: +49-2131-513-230E-mail:******************Copyright © 2004, Parker Hannifin GmbH & Co. KG2IA ED104 UK.INDD RH 02.06Power Amplifier for Pressure Valves Series ED104Installation ManualParker Hannifin GmbH & Co. KG Hydraulic Controls DivisionNoteThis document and other information from Parker Hannifin GmbH, its subsidiaries, sales offices and authorized distributors provide product or system options for further investigation by users having technical expertise. Before you select or use any product or system it is important that you analyse all aspects of your application and review the information concerning the product or system in the current product catalogue. Due to the variety of operating conditions and applications for these products or systems, the user, through his own analysis and testing, is solely responsible for making the final selection of the products and systems and assuring that all performance and safety requirements of the application are met. T he products are subject to change by Parker Hannifin GmbH at any time without notice.Power Amplifier for Pressure Valves Series ED104Installation Manual3IA ED104 UK.INDD RH 02.06Parker Hannifin GmbH & Co. KGHydraulic Controls DivisionElectronic module for the control of proportional pressure relief valves. The pressure values and the changing sequence are determined by externally applied command signals as well as internal limit and ramp potentiometers. There is a linear relationship between input signal and the solenoid current. The pressure value behaves of the valve characteristics and depends partly of the flow.Features• Processing and amplification of the externally supplied positive commands into output signals for the control solenoid.• Can be combined with EZ150 or external pro-grammable control.• DIP switch from internal ramp generation to external ramp setting.• MIN/MAX limiters for matching the working range to the full command signal range.• Pulsed low loss amplifier power stage with sup-porting constant current control for consistant, temperature-independant, solenoid forces.• Dither generator with applied frequency to improve static characteristics.• Diagnosis by means of diagnostic sockets as well as LEDs for indicating working conditions.CharacteristicsOrdering CodeDesign SeriesModuleType Amplifier, adjustable Min/Max-limits Up/Down-rampsElectronic Module Pressure Valves DSA, DWU, DWE, REPower supply range [V]22...38, ripple max. 5%Power required [VA]max. 40Set value voltage [VDC]0...+10Input select voltage [VDC] 5 (30)Reference outputs[V]+10, max. 10mA Solenoid output current max.[A] 1.3Ramp times[s]0 (5)Ambient temperature [°C]0...+60°CConnection31pole male connector, DIN 41617Shielded cable connections Supply connections and valve: AWG16; Commands: AWG20Fuse2A medium lag, DIN 41571ED104004IA ED104 UK.INDD RH 02.06Power Amplifier for Pressure Valves Series ED104Installation ManualParker Hannifin GmbH & Co. KGHydraulic Controls DivisionConnector (Elevation B)14 Input command voltage 0...+10VDC16 Output +10V reference 18 Input 24VDC supply22 Input external ramp option26 Output control solenoid 11 Reference potential 0V supply13 Input ramp disable25 Output control solenoid27 Input external ramp option31 Reference potential 0V set value EMCEN 50081-2EN 55011EN 50082-2ENV 50140EN 61000-4-4ENV 50204EN 61000-4-5EN 61000-4-2EN 61000-4-6Power Amplifier for Pressure Valves Series ED104Installation Manual5IA ED104 UK.INDD RH 02.06Parker Hannifin GmbH & Co. KG Hydraulic Controls DivisionOperating and Diagnostic Elements (Elevation A)Dimensions (Eurocard)NotesT urn off the electrical power to this board whenever the hydraulic supply to the valve is not on.Always turn off the power to this board before removing it from the card holder.Only potential-free measur-ing equipment to be used1 MIN-limiting for matching the lowestpressure2 MAX-limiting for matching the highestpressure 3 Not used4 Red socket for current diagnostic5 Black socket for current diagnostic6 Red LED (A) for• function indicator control solenoid • (B unused here) 7 Y ellow LED for:• correct voltage supply8 Red grip strip with reference informationfor measured values on the diagnostic sockets9 UP ramp potentiometer 10 Down ramp potentiometer6IA ED104 UK.INDD RH 02.06Power Amplifier for Pressure Valves Series ED104Installation ManualParker Hannifin GmbH & Co. KG Hydraulic Controls DivisionInstallation guide to electronic modules to provi-sion of electromagnetic compatibilityPower Supply The utilized power supply has to comply with the EMC-standards (CE-sign, certificate of confor-mity). Relais and solenoids operating from the samesupply circuit than the valve electronics has to be fitted by surge protection elements. Wiring Cable The wires between the installation site of the module and the peripheral units, as power supply, valve sole-noids, position transducer, command signal source has to be shielded. The following wire sizes must be reached: power supply AWG 16, other connections AWG 20. The capacity should not exceed a value of approx. 130 pF/m (wire/wire). The maximum cable length is 50m. No power current lines may be placed within the wired shielded cables to the electronic module. The cable shield has to be connected to ground at both ends (see also chapter “Grounding“). Please be aware of ground loops.ConnectorsThe connection of the position transducer needs a sensor connector 4pin+E featuring metal caseand integrated cable shield coupling. Parker can provide suitable connectors:5004108 (Connector 4pin+E)The connectors has to be installed according the connection diagram, the cable shield has tobe tied on the whole periphery to the providedcoupling clamp.InstallationThe module has to be mounted within a conductive, shielded enclosure. Usable is i.e. an EMC-approved control cabinet. A perfect grounding of the enclosure is mandatory (see also chapter “Grounding“)GroundingThe mounting plate of the valve has to be connected to the grounded metal machine frame. The cable shields must be tied to ground at the control cabinet. A low-ohmic potential compen-sation wire has to be provided between the control cabinet and the machine frame (cable wire >AWG 7 cross section) to prevent ground loops.。
机械毕业设计1299石油管接头螺纹保护帽旋压加工专用装备设计

毕业设计说明书石油管接头螺纹保护帽旋压加工专用装备设计指导教师:题目来源:专业名称:设计时间:班级:答辩时间:摘要本次设计题目是石油管螺纹保护帽旋压专用设备设计,在设计过程中,老师要求我们运用机电液的知识完成,设计的内容主要包括,旋压机床总体设计、尾顶的设计、旋压机构设计、液压控制系统设计、主传动系统的设计、电气系统及PLC的设计。
在机械结构中主要是主轴箱的传动设计,根据以给定的条件主轴转速来设计主传动系统能够。
同时要考虑到制动和变速机构。
主传动系统的主要参数包括公比的选择、传动副、级比指数、齿数的确定等等。
旋压进给机构的设计,旋压进给机构主要通过查冷冲压工艺手册确定旋压力,设计相应机构,选择液压缸,同时也要考虑到与机床相关部位的空间位置关系及自身的强度。
尾顶机构是通过计算旋压加工时零件的厚度、加工的形式、以及加工的条件来确定尾顶所需要的力量,同时选择相应的液压缸、弹簧等。
床身及底座主要考虑各个部位之间的联系,机床加工方向选用45度角向上加工主要是为了加强道轨的支撑刚度。
液压控制系统设计设计内容主要为明确设计要求,制定基本方案,绘制液压系统图,并且确定液压系统的主要参数,液压系统的主要参数包括载荷的组成和计算,液压缸的主要结构及安装尺寸,对其它液压控制元件辅助元件的选择电气系统的设计即利用传感器接收信号,PLC对采集的信号进行分析计算并输出控制信号。
PLC控制系统用西门子S7-200编写。
关键词:主轴箱、旋压、尾顶、传感器、PLC。
AbstractDesign topic whether petroleum pipeline whorl protect cap-like cover fasten and press special-purpose device design this time, in the course of designing, the teacher requires us to use the knowledge of the electromechanical liquid to finish, the content designed mainly includes, is it keep lathe overall design , design that tail carry , is it keep design , main design , electric system and design of PLC of transmission , design of organization and control system of hydraulic pressure to fasten to fasten. Design transmission , main shaft of case mainly among mechanical structure, according to with give condition main shaft rotational speed definitely is it design mainly transmission can to come. . Tail carry organization through is it is it press thickness of part when processing to fasten to calculate , form that process , and terms that process is it confirm strength that tail's carrying need to come, choose corresponding hydraulic pressure jar , spring ,etc. at the same time . Lathe bed and base consider connection of each position mainly, machine tooling direction select for use 45 horn it processes to be for strengthen dishes of support rigidity of rail mainly upwards. Hydraulic pressure control system design content mainly for designing requirement of defining, draw the systematic picture of the hydraulic pressure , and confirm the main parameter of the hydraulic pressure system, main parameter including loaded composition and calculate , hydraulic pressure of system, main structure and size of installing , hydraulic pressure of jar, control to other hydraulic pressure component auxiliary choice electric design of system of component utilize the sensor to receive the signal promptly, PLC analyses that calculates and exports the control signal to the signal that is gathered . PLC control system is written with Siemens S7-200.Keyword:Main shaft case、fastenning pressing 、end carrying 、sensor、PLC.前言此次毕业设计根据学校和老师的要求要运用机械、电子、及液压等多方面知识来完成,机电液一体化。
压缩机无油流开关误报警的一种解决方法

第29卷 第07期2022年07月仪器仪表用户INSTRUMENTATIONVol.292022 No.07压缩机无油流开关误报警的一种解决方法杨灵飞,冯金强,武 岳,郑建军(海洋石油工程股份有限公司,天津 300451)摘 要:南海某海洋石油平台的天然气压缩机在运行过程中产生多次关停,给作业公司带来了大量的经济损失。
经过分析所有的停机原因,其中无油流开关误报警导致的停机占比最大,而且一直没有得到有效的解决。
为了减少因无油流开关误报警触发停机给油田带来的经济损失,作业公司决定对天然气压缩机的注油管路进行改造,采用在注油管路使用两组无油流开关和压力变送器,软件的控制逻辑增加表决机制。
通过改造,因无油流开关误报警导致的停机很少发生,同时也通过新增的变送器采集到了注油管路的脉动压力,为天然气压缩机注油管路的进一步诊断、分析、维护提供了直接的数据依据。
在不降低原来的安全性的基础上,提高系统的可用性,得到了更多的数据支持,也挽回了经济损失。
关键词:压缩机;无油流开关;误报警;表决;脉动压力中图分类号:TH45 文献标志码:AA Solution of False Alarm of Compressor Digital No-Flow TimerYang Lingfei ,Feng Jinqiang ,Wu Yue ,Zheng Jianjun (Offshore Oil Engineering Co., Ltd., Tianjin,300451, China )Abstract:The natural gas compressor on an offshore platform in South Sea shut down for a couple of times, bringing great eco-nomic loss for the operation company. After analyzing all reasons of the shutdown, they found the biggest reason of shutdown wasfalse alarm from the no-flow timer which had not been resolved. In order to reduce the economic loss for the oilfield caused by false alarm from the no-flow timer, the operation company made transformation for the oil filling pipeline of natural gas compressor. They applied 2 sets of no-flow timer and pressure transmitter on the oil filling pipeline and added voting mechanism on the con-trol logic software. Benefited by the transformation, the operation company substantially decreased the shutdown probability and collected the pulsating pressure of oil filling pipeline from the added transmitter at the same time, which provided visual data for further diagnose, analysis and maintenance of gas compressor oil filling pipeline. This method can improve the system usability, obtain more data support and save losses without decreasing security.Key words:compressor;digital no-flow timer;false alarm;voting;pulsating pressure收稿日期:2022-04-26作者简介:杨灵飞(1981-),男,山西朔州应县人,本科,工程师,研究方向:海洋油气田设备控制系统。
液压英文总汇

fluid power 流体传动h yd r a u l ic s液压技术h y d r o d y n a m i c s液力技术h y d r o p n e u m a t i c s气液技术h y d r o s t a t i c s静液压技术p n e u m a t i c s气动技术o p e r a t i n g c o n d i t i o n s运行工况r a t e d c o n d i t i o n s额定工况s t a n d a r d c o n d i t i o n s标准工况continuous working conditions 连续工况l i m i t i n g c o n d i t i o n s极限工况s t e a d y-s t a t e c o n d i t io n s稳态工况instantaneous conditions 瞬态工况a c t u a l c o n d i t i o n s实际工况specified conditions 规定工况acceptable conditions 许用工况efficiency 效率d ir e c t io n o f r o t a t io n旋转方向clockwise/right hand 顺时针/右旋anticlockwise/left hand 逆时针/左旋equipment temperature装置温度fluid temperature 介质温度ambient temperature 环境温度nominal pressure 公称压力working pressure 工作压力in le t p r e s s u r e进口压力outlet pressure出口压力p r e s s u r e d r o p压差d i f f e r e n t i a l p r e s s u r e压降b a c k p r e s s u r e背压breakaway pressure 起动压力breakout pressure 起动压力boost pressure/charge pressure 补/充油压力peak pressure 峰值压力cracking pressure 开启压力operating pressure 运行压力proof pressure 耐压实验压力surge pressure 冲击压力system pressure 系统压力sta t ic pressure 静压力pilot pressure 控制压力pre-charge pressure 充气压力suction pressure 吸入压力override pressure 调压偏差ra t ed pressure 额定压力air consumption 耗气量l e a k a g e泄漏internal leakage 内泄漏external leakage 外泄漏flow 流动laminar flow 层流turbulent flow 紊流c a v i t a t i o n s气穴f l o w r a t e流量rated flow 额定流量supply flow 供给流量flow ratio 流量系数hysteresis滞环s ta r t-u p time启动时间r i s e t i m e上升时间fall time 下降时间actuated time 操作时间released time 非操作时间response time 响应时间graphical symbol 图形符号graphical representation 图形表示cir cuit d iag ra m 回路图pressure time diagram 压力时间图function diagram 功能图cycle 循环au t omatic cycle 自动循环working cycle 工作循环cycling speed 循环速度p h a s e工步dwell phase 停止工步working phase 工作工步rapid advance phase 快进工步ra p id return phase 快退工步repeatability 重复性frequency response 频率响应reproducibility 复现性d r i f t漂移ripple 波动l i n e a r r e g i o n线性区linearity 线性度h yd r a u l i c l o c k液压锁紧s t i c k i n g液压卡紧c a p a c i t y;d i s p l a ce m e n t排量ef f e c t i v e c a p a c i t y有效排量g e o m e t r i c几何排量v o l u m e t r i c l o s s e s容积损失h y d r o d y n a mi c l o s s e s流动损失m e c h a n i c a l l o s s e s机械损失d e r i v e d t o r q u e导出转矩e f f e c t i v e t o r q u e有效转矩h y d r a u l i c p u m p s液压泵r o t o d y n a m i c p u m p动力式泵d i s p l a c e m e n t p u m p容积泵f i x e d d i s p l a c e m e n t p u m p定量泵variable displacement pump 变量泵c o n t r o l p u m p泵的控制g e a r p u m p齿轮泵s c r e w p u m p螺杆泵v a n e p u m p叶片泵p i s t o n p u m p柱塞泵r a d i a l p i s t o n p u m p径向柱塞泵a x i a l p i s t o n p u m p轴向柱塞泵angled piston pump 斜轴式柱塞泵h a n d-p u m p手动泵s t a g e d p u m p多级泵m u l t i p l e p u m p多联泵d e r i v e d c a p a c i t y空载排量e f f e c t i v e c a p a c i t y有效排量d e r i v e d o u tp u t f lo w空载输出流量effective output flow 有效输出流量effective hydraulic power 有效液压功率h y d r a u l i c p o w e r液压功率i n p u t p o w e r输入功率i n s t a l l e d p o w e r装机功率vo lu me tr ic eff ic ien c y容积效率hydro-mechanical efficiency 液压机械效率o v e r a l l e f f i c i e n c y总效率m o u n t i n g安装f l a n g e m o u n t i n g法兰安装spigot pilot location 止口导向定位f o o t mo u n tin g底座安装s h a f t e x t e n s i o n轴伸d o u b l e-a c t i o n m o t o r双向马达a i r m o t o r气马达h y d r a u l i c m o t o r液压马达fixed displacement motor定量马达variable displacement motor 变量马达gear moto r 齿轮马达v a n e mo to r叶片马达radial piston motor 径向柱塞马达axial piston motor 轴向柱赛马达m u l t i p l e m o t o r多联马达h ydraulic stepping液压步进马达s e mi-r o t a r y a c t u a t o r摆动马达derived capacity(motor) 空载排量s l i p滑差hydraulic power(motor) 液压功率s t a r ti n g t o r q u e启动转矩hydraulic pump-motor 液压泵-马达variable speed drive units; 变速传动装置integral transmissions 整体传动装置stiffness 刚度n e u t r a l p o s i t i o n中位zero position 零位free position 自由位c y l i n d e r缸rod end 有杆端rear end 无杆端extend stroke 外伸行程retract stroke 内缩行程cushioning (机械/流体)缓冲cushioning 缓冲长度effective piston area 活塞有效面积working stroke 工作行程induced pressure 负载压力damping pressure 缓冲压力force 输出力theoretical force 理论输出力actual force 实际输出力double-acting cylinder 双作用缸single-acting cylinder 单作用缸differential cylinder 压差缸tandem cylinder 串联缸telescopic cylinder 多级伸缩缸pressure intensifier 增压器ratio of intensification增压比d a s h p o t阻尼缸va lve阀s u b-p l a t e;s u b-b a s e底板manifold block 油(气)路块mono-block valve 整体阀s u b-p l a t e v a l v e板式阀ganged valve; sandwich valve 叠加阀c a r t r i d g e v a l v e插装阀directional control valve 方向控制阀s l i d e v a l v e滑阀p o p p e t v a l v e座阀v a l v e e l e m e n t阀心valve element positio ns 阀心位置check va lve 单向阀pilot-controlled check valve 液控单向阀p r e f ill va l ve充液阀s h u t t l e v a l v e梭阀q u ick e xh au s t va lve快速排气阀automatic shut-off valve 自动截止阀maximum flow control valve 自动截止阀pressure control valve 压力控制阀pressure relief valve溢流阀s e q u e n c e v a l v e顺序阀p r e s s u r e r e g u l a t o r;减压阀p r e s s u r e r e d u c i n g v a l v e减压阀c o u n t e r b a l a n c e v a l v e平衡阀u n l o a d i n g v a l v e卸荷阀p o p p e t t y p e座阀式dire ctly ope ra ted typ e直动式mechanically controlled type 机械控制式pilot-operated type 先导式manually operated type 手动式pilot-controlled type 液(气)控制式f l o w c o n t r o l v a l v e s流量控制阀fixed restrictive valve 固定节流阀adjustable restrictive valve 可调节流阀d e c e l e r a t i o n v a l v e减速阀one-way restrictive valve 单向节流阀series flow control valve调速阀bypass flow control valve 旁通调速阀f l o w d i v i d e r v a l v e分流阀f l o w-c o m b i n i n g v a l v e集流阀s h u t-o f f v a l v e截止阀plug valve 转阀globe valve 球阀n eed le va lve针阀diaphragm valve 膜片阀g a t e v a l v e闸阀b u t t e r f l y v a l v e蝶阀s p u r io u s s ig na l寄生信号n o i s e噪声amplifier 放大器analogue amplifier 模拟放大器digital amplifier 数字放大器sensor 传感器logic threshold 逻辑阀值acoustic noise 声频噪声signal-to-noise ratio 信噪比servo-valve 伺服阀hydraulic servo-valve 液压伺服阀electro-hydraulic servo-valve 电液伺服阀mechanical hydraulic servo-valve机液伺服阀f lo w c o n tr o l h yd r a u li c s e r vo-va l ve液压流量伺服阀pressure control hydraulic servo-valve液压压力伺服阀t h r e e-w a y v a l v e三通阀hydraulic amplifier 液压放大器t w o-w a y v a l v e两通阀n o z z l e f l a p p e r喷嘴挡板d i t h e r颤振va lve po la r ity 阀极性flow gain(servo-valve) 流量增益symmetry 对称度internal leakage(servo valve) 内泄漏flow limit 流量极限null[quiescent]leakage 零位泄漏lap 遮盖zero lap零遮盖o v e r l a p正遮盖u n d e r l a p负遮盖n u l l b i a s零偏o p e n i n g开口n u l l s h i f t零漂valve pressure drop 阀压降r e s o lu t i o n分辨率threshold 阀值four-way valve 四通阀amplitude ratio 幅值比phase lag 相位移transfer function 传递函数p o we r s u p p l y 动力源flo wline管路r i g i d t u b e;s e m i-r i g i d t u b e硬管flexible hose 软管working line;feed line 工作管路return line 回油管路make-up line; replenishing line 补液管路pilot control line 控制管路drain line 泄油管路bleed line 放气管路connection;fitting 接头flared fitting 扩口式接头flange connection 法兰连接quick release coupling 快换接头e l b o w f i t t in g弯头r e d u c e r f i t t i n g异径接头f l o w p a t h,g a l l e r y流道port 油口/气口r e c e i v e r气罐atmospheric reservoir 开式油箱pressure-sealed reservoir 压力油箱sealed reservoir 闭式油箱reservoir fluid capacity 油箱容量hydraulic accumulator 液压蓄能器spring-loaded accumulator 弹簧式蓄能器weight-loaded accumulator 重力式蓄能器gas-loaded accumulator 充气式蓄能器air contamination 空气污染solid contamination 固体颗粒污染l i q u i d c o n ta mi n a t io n液体污染a i r c o n t a m i n a t i o n蒸汽污染separator drain-valve 分离排污阀a i r d r y e r空气干燥器a i r f i l t e r空气过滤器lubrica tor 油雾器cooler 冷却器h e a t e x c h a n g e r热交换器h e a t e r加热器temperature controller 温度控制器hydraulic silencer 液压消声器pneumatic silencer 气动消声器h yd r a u lic f ilte r液压过滤器d u p l e x f i l t e r双联过滤器two-stage filter 两级过滤器strainer 滤网粗过滤器f ilte r e le me n t 滤芯effective filtration area 有效过滤面积nominal filtration rating 公称过滤精度filter efficiency 过滤效率efficiency curve 效率曲线filter pressure drop 过滤器压降collapse pressure 压溃压力de-aerator 除气器packing seal 填料密封mechanical seal 机械密封d y n a m i c s e a l动密封件static seal 静密封件a x i a l s e a l轴向密封radial seal 径向密封rotary seal 旋转密封sliding seal 滑动密封piston seal 活塞密封件rod seal 活塞杆密封件wiper seal; scraper 防尘圈r o t a r y s h a f t s e a l油封composite seal; 复合密封件bonded seal; bonded washer 组合垫圈elastomer seal 弹性密封件nitrile rubber seal 丁腈橡胶密封件p o l yt e t r a f lu o r o e th yl e n e(P T FE)s e a l聚四氟乙烯密封件polyamide(NYLON) seal 尼龙密封件automatic control 自动控制manual control 人工控制mechanical control 机械控制pressure control 压力控制pneumatic control 气动控制hydraulic control 液压控制electrical control 电器控制servo control 伺服控制feedback 反馈hydraulic feedback 液压反馈electrical feedback 电器反馈pneumatic feedback 气动反馈auxiliary control 辅助控制cverride control 优先控制pressure gauge 压力表e l e c t r i c a l p r e s s u r e t r a n s d u c e r电气压力传感器absolute pressure instrument 绝对压力表liquid level measuring instrument 液位计flowmeter 流量计electrical flow transducer 电气流量传感器flow recorder 流量记录仪pressure switch 压力开关gauge pulsation damper 压力表阻尼器pulse generator 脉冲发生器fluid power system 流体传动系统power unit; power pack 液压泵站compressor installation 压缩机站start-stop pressure control 起停压力控制p n e u m a t i c v a r i a b l e s p e e d c o n t r o l气动变速控制hydraulic motor assembly 液压马达组件pneumatic motor assembly气动马达组件linear motor直线马达air conditioner unit 空气处理装置fluid power circuit 流体传动回路p i l o t c i r c u i t控制回路pressure control circuit 压力控制回路s a f e t y c i r c u i t安全回路flow control circuit 流量控制回路r e g e n e r a t i v e c i r c u i t差动回路meter-in circuit 进口节流回路meter-out circuit 出口节流回路synchronizing circuit 同步回路sequence circuit 顺序回路open circuit 开式回路closed circuit 闭式回路unloading circuit 卸荷回路p r i m e m o v e r原动机pipe installation; pipe-work 管路布置p ip e c la mp管夹a n t i-v i b r a t i o n m o u n t i n g减震器operating station 操作站c o n t r o l c o n s o l e控制台control panel控制屏pneumatic control system 气动控制系统hydraulic fluid 液压油液Newtonian fluid 牛顿流体petroleum fluid 石油基液压油mineral oil 矿物油fire resistant(FR)fluid难燃液压油oil-in-water emulsion 水包油乳化液a q u e o u s f l u i d水基液压液water-in-oil emulsion 油包水乳化液s yn thetic f luid合成液压液v i s c o s i t y粘度a b s o l u t e v i s c o s i t y绝对粘度k i n e m a t i c v i s c o s i t y运动粘度v i s c o s i t y i n d e x粘度指数water content 含水量d e n s i t y密度a i r r e l e a s e空气释放能力seal compatibility 密封相容性f l a s h p o i n t闪点auto ignition temperature(AIT) 自燃点rust protection 防锈性anti-corrosive quality抗腐蚀性anti-wear properties; lubricity 抗磨性s ta b ility 安定性v i s u a l c o u n t i n g o f c o n t a m i n a t i o n目测污染计数法automatic counting of contamination自动污染计数法raw count 原始计数total statistical count 统计计数particle size distribution 颗粒尺寸分布r a te o f c o n ta min a tio n污染度mass index of contamination 质量污染度contamination classes 污染等级。
英文文献翻译-汽车转向系统
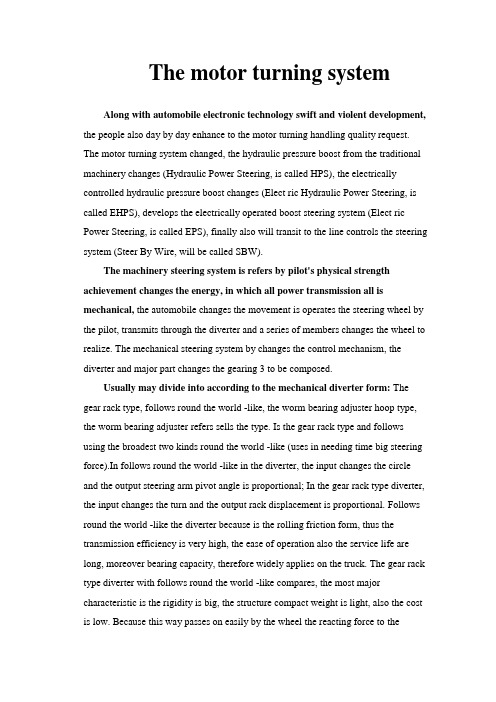
The motor turning systemAlong with automobile electronic technology swift and violent development, the people also day by day enhance to the motor turning handling quality request. The motor turning system changed, the hydraulic pressure boost from the traditional machinery changes (Hydraulic Power Steering, is called HPS), the electrically controlled hydraulic pressure boost changes (Elect ric Hydraulic Power Steering, is called EHPS), develops the electrically operated boost steering system (Elect ric Power Steering, is called EPS), finally also will transit to the line controls the steering system (Steer By Wire, will be called SBW).The machinery steering system is refers by pilot's physical strength achievement changes the energy, in which all power transmission all is mechanical, the automobile changes the movement is operates the steering wheel by the pilot, transmits through the diverter and a series of members changes the wheel to realize. The mechanical steering system by changes the control mechanism, the diverter and major part changes the gearing 3 to be composed.Usually may divide into according to the mechanical diverter form: The gear rack type, follows round the world -like, the worm bearing adjuster hoop type, the worm bearing adjuster refers sells the type. Is the gear rack type and follows using the broadest two kinds round the world -like (uses in needing time big steering force).In follows round the world -like in the diverter, the input changes the circle and the output steering arm pivot angle is proportional; In the gear rack type diverter, the input changes the turn and the output rack displacement is proportional. Follows round the world -like the diverter because is the rolling friction form, thus the transmission efficiency is very high, the ease of operation also the service life are long, moreover bearing capacity, therefore widely applies on the truck. The gear rack type diverter with follows round the world -like compares, the most major characteristic is the rigidity is big, the structure compact weight is light, also the cost is low. Because this way passes on easily by the wheel the reacting force to thesteering wheel, therefore has to the pavement behavior response keen merit, but simultaneously also easy to have phenomena and so on goon and oscillation, also its load bearing efficiency relative weak, therefore mainly applies on the compact car and the pickup truck, at present the majority of low end passenger vehicle uses is the gear rack type machinery steering system.Along with the vehicles carrying capacity increase as well as the people to the vehicles handling quality request enhancement, the simple mechanical type steering system were already unable to meet the needs, the power steering system arise at the historic moment, it could rotate the steering wheel while the pilot to provide the boost, the power steering system divides into the hydraulic pressure steering system and the electrically operated steering system 2kinds.Hydraulic pressure steering system is at present uses the most widespread steering system.The hydraulic pressure steering system increased the hydraulic system in the mechanical system foundation, including hydraulic pump, V shape band pulley, drill tubing, feed installment, boost installment and control valve. It with the aid of in the motor car engine power actuation hydraulic pump, the air compressor and the generator and so on, by the fluid strength, the physical strength or the electric power increases the pilot to operate the strength which the front wheel changes, enables the pilot to be possible nimbly to operate motor turning facilely, reduced the labor intensity, enhanced the travel security.The hydraulic pressure boost steering system from invented already had about half century history to the present, might say was one kind of more perfect system, because its work reliable, the technology mature still widely is applied until now. It takes the power supply by the hydraulic pump, after oil pipe-line control valves to power hydraulic cylinder feed, through the connecting rod impetus rotation gear movement, may changes the boost through the change cylinder bore and the flowing tubing head pressure size the size, from this achieved changes the boost the function. The traditional hydraulic pressure type power steering system may divide into generally according to the liquid flow form: Ordinary flow type and atmosphericpressure type 2 kind of types, also may divide into according to the control valve form transfers the valve type and the slide-valve type.Along with hydraulic pressure power steering system on automobile daily popularization, the people to operates when the portability and the road feeling request also day by day enhance, however the hydraulic pressure power steering system has many shortcomings actually: ①Because its itself structure had decided it is unable to guarantee vehicles rotates the steering wheel when any operating mode, all has the ideal operation stability, namely is unable simultaneously to guarantee time the low speed changes the portability and the high speed time operation stability;②The automobile changes the characteristic to drive the pilot technical the influence to be serious; ③The steering ratio is fixed, causes the motor turning response characteristic along with changes and so on vehicle speed, transverse acceleration to change, the pilot must aim at the motor turning characteristic peak-to-peak value and the phase change ahead of time carries on certain operation compensation, thus controls the automobile according to its wish travel. Like this increased pilot's operation burden, also causes in the motor turning travel not to have the security hidden danger; But hereafter appeared the electrically controlled hydraulic booster system, it increases the velocity generator in the traditional hydraulic pressure power steering system foundation, enables the automobile along with the vehicle speed change automatic control force size, has to a certain extent relaxed the traditional hydraulic pressure steering system existence question.At present our country produces on the commercial vehicle and the passenger vehicle uses mostly is the electrically controlled hydraulic pressure boost steering system, it is quite mature and the application widespread steering system. Although the electrically controlled hydraulic servo alleviated the traditional hydraulic pressure from certain degree to change between the portability and the road feeling contradiction, however it did not have fundamentally to solve the HPS system existence insufficiency, along with automobile microelectronic technology development, automobile fuel oil energy conservation request as well as global initiative environmental protection, it in aspect and so on arrangement, installment,leak-proof quality, control sensitivity, energy consumption, attrition and noise insufficiencies already more and more obvious, the steering system turned towards the electrically operated boost steering system development.The electrically operated boost steering system is the present motor turning system development direction, its principle of work is: EPS system ECU after comes from the steering wheel torque sensor and the vehicle speed sensor signal carries on analysis processing, controls the electrical machinery to have the suitable boost torque, assists the pilot to complete changes the operation. In the last few years, along with the electronic technology development, reduces EPS the cost to become large scale possibly, Japan sends the car company, Mitsubishi Car company, this field car company, US's Delphi automobile system company, TRW Corporation and Germany's ZF Corporation greatly all one after another developsEPS.Mercedes2Benz 和Siemens Automotive Two big companies invested65,000,000 pounds to use in developing EPS, the goal are together load a car to 2002, yearly produce 300 ten thousand sets, became the global EPS manufacturer. So far, the EPS system in the slight passenger vehicle, on the theater box type vehicle obtains the widespread application, and every year by 300 ten thousand speed development.Steering is the term applied to the collection of components, linkages, etc. which allow for a vessel (ship, boat) or vehicle (car) to follow the desired course. An exception is the case of rail transport by which rail tracks combined together with railroad switches provide the steering function.The most conventional steering arrangement is to turn the front wheels using a hand–operated steering wheel which is positioned in front of the driver, via the steering column, which may contain universal joints to allow it to deviate somewhat from a straight line. Other arrangements are sometimes found on different types of vehicles, for example, a tiller or rear–wheel steering. Tracked vehicles such as tanks usually employ differential steering — that is, the tracks are made to move at different speeds or even in opposite directions to bring about a change of course.Many modern cars use rack and pinion steering mechanisms, where the steering wheel turns the pinion gear; the pinion moves the rack, which is a sort of linear gear which meshes with the pinion, from side to side. This motion applies steering torque to the kingpins of the steered wheels via tie rods and a short lever arm called the steering arm.Older designs often use the recirculating ball mechanism, which is still found on trucks and utility vehicles. This is a variation on the older worm and sector design; the steering column turns a large screw (the "worm gear") which meshes with a sector of a gear, causing it to rotate about its axis as the worm gear is turned; an arm attached to the axis of the sector moves the pitman arm, which is connected to the steering linkage and thus steers the wheels. The recirculating ball version of this apparatus reduces the considerable friction by placing large ball bearings between the teeth of the worm and those of the screw; at either end of the apparatus the balls exit from between the two pieces into a channel internal to the box which connects them with the other end of the apparatus, thus they are "recirculated".The rack and pinion design has the advantages of a large degree of feedback and direct steering "feel"; it also does not normally have any backlash, or slack. A disadvantage is that it is not adjustable, so that when it does wear and develop lash, the only cure is replacement.The recirculating ball mechanism has the advantage of a much greater mechanical advantage, so that it was found on larger, heavier vehicles while the rack and pinion was originally limited to smaller and lighter ones; due to the almost universal adoption of power steering, however, this is no longer an important advantage, leading to the increasing use of rack and pinion on newer cars. The recirculating ball design also has a perceptible lash, or "dead spot" on center, where a minute turn of the steering wheel in either direction does not move the steering apparatus; this is easily adjustable via a screw on the end of the steering box to account for wear, but it cannot be entirely eliminated or the mechanism begins to wear very rapidly. This design is still in use in trucks and other large vehicles, where rapidity of steering and direct feel are less important than robustness, maintainability,and mechanical advantage. The much smaller degree of feedback with this design can also sometimes be an advantage; drivers of vehicles with rack and pinion steering can have their thumbs broken when a front wheel hits a bump, causing the steering wheel to kick to one side suddenly (leading to driving instructors telling students to keep their thumbs on the front of the steering wheel, rather than wrapping around the inside of the rim). This effect is even stronger with a heavy vehicle like a truck; recirculating ball steering prevents this degree of feedback, just as it prevents desirable feedback under normal circumstances.The steering linkage connecting the steering box and the wheels usually conforms to a variation of Ackermann steering geometry, to account for the fact that in a turn, the inner wheel is actually traveling a path of smaller radius than the outer wheel, so that the degree of toe suitable for driving in a straight path is not suitable for turns.As vehicles have become heavier and switched to front wheel drive, the effort to turn the steering wheel manually has increased - often to the point where major physical exertion is required. To alleviate this, auto makers have developed power steering systems. There are two types of power steering systems—hydraulic and electric/electronic. There is also a hydraulic-electric hybrid system possible.A hydraulic power steering (HPS) uses hydraulic pressure supplied by an engine-driven pump to assist the motion of turning the steering wheel. Electric power steering (EPS) is more efficient than the hydraulic power steering, since the electric power steering motor only needs to provide assist when the steering wheel is turned, whereas the hydraulic pump must run constantly. In EPS the assist level is easily tunable to the vehicle type, road speed, and even driver preference. An added benefit is the elimination of environmental hazard posed by leakage and disposal of hydraulic power steering fluid.An outgrowth of power steering is speed adjustable steering, where the steering is heavily assisted at low speed and lightly assisted at high speed. The auto makers perceive that motorists might need to make large steering inputs while manoeuvering for parking, but not while traveling at high speed. The first vehiclewith this feature was the Citroën SM with its Diravi layout, although rather than altering the amount of assistance as in modern power steering systems, it altered the pressure on a centring cam which made the steering wheel try to "spring" back to the straight-ahead position. Modern speed-adjustable power steering systems reduce the pressure fed to the ram as the speed increases, giving a more direct feel. This feature is gradually becoming commonplace across all new vehicles.Four-wheel steering (or all wheel steering) is a system employed by some vehicles to increase vehicle stability while maneuvering at high speed, or to decrease turning radius at low speed.In most four-wheel steering systems, the rear wheels are steered by a computer and actuators. The rear wheels generally cannot turn as far as the Alternatively, several systems, including Delphi's Quadrasteer and the system in Honda's Prelude line, allow for the rear wheels to be steered in the opposite direction as the front wheels during low speeds. This allows the vehicle to turn in a significantly smaller radius — sometimes critical for large trucks or vehicles with trailers.汽车转向系统随着汽车电子技术的迅猛发展,人们对汽车转向操纵性能的要求也日益提高。
液压词汇中英文对对照
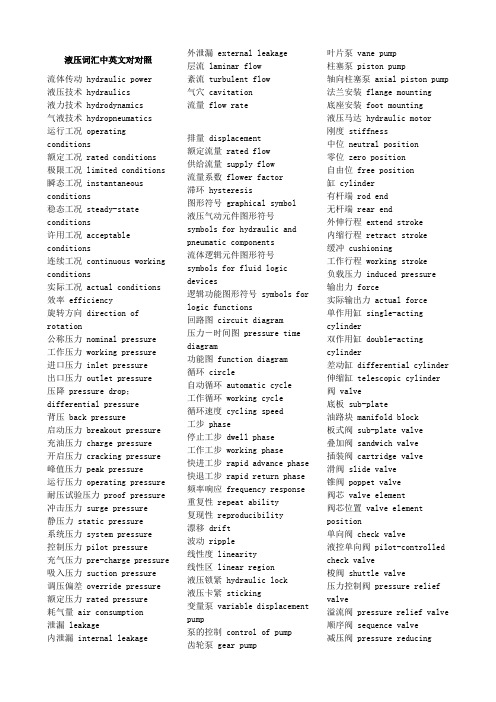
液压词汇中英文对对照流体传动 hydraulic power液压技术 hydraulics液力技术 hydrodynamics气液技术 hydropneumatics运行工况 operating conditions额定工况 rated conditions极限工况 limited conditions 瞬态工况 instantaneous conditions稳态工况 steady-state conditions许用工况 acceptable conditions连续工况 continuous working conditions实际工况 actual conditions 效率 efficiency旋转方向 direction of rotation公称压力 nominal pressure工作压力 working pressure进口压力 inlet pressure出口压力 outlet pressure压降 pressure drop;differential pressure背压 back pressure启动压力 breakout pressure 充油压力 charge pressure开启压力 cracking pressure 峰值压力 peak pressure运行压力 operating pressure 耐压试验压力 proof pressure 冲击压力 surge pressure静压力 static pressure系统压力 system pressure控制压力 pilot pressure充气压力 pre-charge pressure 吸入压力 suction pressure调压偏差 override pressure 额定压力 rated pressure耗气量 air consumption泄漏 leakage内泄漏 internal leakage 外泄漏 external leakage层流 laminar flow紊流 turbulent flow气穴 cavitation流量 flow rate排量 displacement额定流量 rated flow供给流量 supply flow流量系数 flower factor滞环 hysteresis图形符号 graphical symbol液压气动元件图形符号symbols for hydraulic andpneumatic components流体逻辑元件图形符号symbols for fluid logicdevices逻辑功能图形符号 symbols forlogic functions回路图 circuit diagram压力-时间图 pressure timediagram功能图 function diagram循环 circle自动循环 automatic cycle工作循环 working cycle循环速度 cycling speed工步 phase停止工步 dwell phase工作工步 working phase快进工步 rapid advance phase快退工步 rapid return phase频率响应 frequency response重复性 repeat ability复现性 reproducibility漂移 drift波动 ripple线性度 linearity线性区 linear region液压锁紧 hydraulic lock液压卡紧 sticking变量泵 variable displacementpump泵的控制 control of pump齿轮泵 gear pump叶片泵 vane pump柱塞泵 piston pump轴向柱塞泵 axial piston pump法兰安装 flange mounting底座安装 foot mounting液压马达 hydraulic motor刚度 stiffness中位 neutral position零位 zero position自由位 free position缸 cylinder有杆端 rod end无杆端 rear end外伸行程 extend stroke内缩行程 retract stroke缓冲 cushioning工作行程 working stroke负载压力 induced pressure输出力 force实际输出力 actual force单作用缸 single-actingcylinder双作用缸 double-actingcylinder差动缸 differential cylinder伸缩缸 telescopic cylinder阀 valve底板 sub-plate油路块 manifold block板式阀 sub-plate valve叠加阀 sandwich valve插装阀 cartridge valve滑阀 slide valve锥阀 poppet valve阀芯 valve element阀芯位置 valve elementposition单向阀 check valve液控单向阀 pilot-controlledcheck valve梭阀 shuttle valve压力控制阀 pressure reliefvalve溢流阀 pressure relief valve顺序阀 sequence valve减压阀 pressure reducingvalve平衡阀 counterbalance valve 卸荷阀 unloading valve直动式 directly operated type先导式 pilot-operated type 机械控制式 mechanically controlled type手动式 manually operated type液控式 hydraulic controlled type流量控制阀 flow control valve固定节流阀 fixed restrictive valve可调节流阀 adjustable restrictive valve单向节流阀 one-wayrestrictive valve调速阀 speed regulator valve 分流阀 flow divider valve集流阀 flow-combining valve 截止阀 shut-off valve球阀 global(ball) valve针阀 needle valve闸阀 gate valve膜片阀 diaphragm valve蝶阀 butterfly valve噪声等级noise level放大器 amplifier模拟放大器 analogueamplifier数字放大器 digital amplifier 传感器 sensor阈值 threshold伺服阀 servo-valve四通阀 four-way valve喷嘴挡板 nozzle flapper液压放大器 hydraulic amplifier颤振 dither阀极性 valve polarity流量增益 flow gain对称度 symmetry流量极限 flow limit 零位内泄漏 null(quiescent)leakage遮盖 lap零遮盖 zero lap正遮盖 over lap负遮盖 under lap开口 opening零偏 null bias零漂 null drift阀压降 valve pressure drop分辨率 resolution频率响应 frequency response幅值比 amplitude ratio相位移 phase lag传递函数 transfer function管路 flow line硬管 rigid tube软管 flexible hose工作管路 working line回油管路 return line补液管路 replenishing line控制管路 pilot line泄油管路 drain line放气管路 bleed line接头 fitting;connection焊接式接头 welded fitting扩口式接头 flared fitting快换接头 quick releasecoupling法兰接头 flange connection弯头 elbow异径接头 reducer fitting流道 flow pass油口 port闭式油箱 sealed reservoir油箱容量 reservoir fluidcapacity气囊式蓄能器bladderaccumulator空气污染 air contamination固体颗粒污染 solidcontamination液体污染 liquidcontamination空气过滤器 air filter油雾气 lubricator热交换器 heat exchanger冷却器 cooler加热器 heater温度控制器 thermostat消声器 silencer双筒过滤器 duplex filter过滤器压降 filter pressuredrop有效过滤面积 effectivefiltration area公称过滤精度 nominalfiltration rating压溃压力 collapse pressure填料密封 packing seal机械密封 mechanical seal径向密封 radial seal旋转密封 rotary seal活塞密封 piston seal活塞杆密封 rod seal防尘圈密封 wiper seal;scraper组合垫圈 bonded washer复合密封件 composite seal弹性密封件 elastomer seal丁腈橡胶 nitrile butadienerubber;NBR聚四氟乙烯polytetrafluoroethene;PTFE优先控制 override control压力表 pressure gauge压力传感器 electricalpressure transducer压差计 differential pressureinstrument液位计 liquid levelmeasuring instrument流量计 flow meter压力开关 pressure switch脉冲发生器 pulse generator液压泵站 power station空气处理单元 air conditionerunit压力控制回路 pressurecontrol circuit安全回路 safety circuit差动回路 differentialcircuit调速回路 flow controlcircuit进口节流回路 meter-incircuit出口节流回路 meter-out circuit同步回路 synchronizing circuit开式回路 open circuit闭式回路 closed circuit管路布置 pipe-work管卡 clamper联轴器 drive shaft coupling 操作台 control console控制屏 control panel避震喉 compensator粘度 viscosity运动粘度 kinematic viscosity 密度 density含水量 water content闪点 flash point防锈性 rust protection抗腐蚀性 anti-corrosive quality便携式颗粒检测仪 portable particle counter电磁阀 Solenoid valve单向阀 Check valve插装阀 Cartridge valve叠加阀 Sandwich plate valve 先导阀 Pilot valve液控单向阀 Pilot operated check valve板式安装 Sub-plate mount集成块 Manifold block压力溢流阀 Pressure relief valve流量阀 Flow valve节流阀 Throttle valve双单向节流阀 Double throttle check valve旋钮 Rotary knob节流板 Rectifier plate伺服阀 Servo valve比例阀 Proportional valve 位置反馈Position feedback渐增流量 Progressive flow电磁铁释放 De-energizing ofsolenoid二、介质类磷酸甘油酯Phosphate ester(HFD-R)水-乙二醇Water-glycol (HFC)乳化液 Emulsion缓蚀剂 Inhibitor合成油 Synthetic lubricatingoil三、液压安装工程污染 Contamination灌浆 Grout失效 Failure点动 Jog爬行 Creep摩擦 Abrasion(活塞杆)伸出Retract(活塞杆)缩回Extension误动作 Malfunction酸洗 Pickling冲洗Flushing槽式酸洗 Dipping process循环 Re-circulation钝化Passivity柠檬酸 Nitric acid氩气Argon对接焊Butt welding套管焊Socket welding惰性气体焊 Inert gas welding四、管接头Bite type fittings 卡套式管接头Tube to tube fittings接管接头union 直通接管接头union elbow 直角管接头union tee 三通管接头union cross 四通管接头Mal stud fittings 端直通管接头Bulkhead fittings 长直通管接头Weld fittings 焊接式管接头Female connector fittings 接头螺母Reducers extenders 变径管接头Banjo fittings 铰接式管接头Adjustable fittings/swivelnut 旋转接头五、伺服阀及伺服系统性能参数Dynamic response 动态频响DDV-direct drive valve 直动式伺服阀NFPA-National Fluid PowerAssociation 美国流体控制学会Phase lag 相位滞后Nozzle flapper valve 喷嘴挡板阀Servo-jet pilot valve 射流管阀Dither 颤振电流Coil impedance 线圈阻抗Flow saturation 流量饱和Linearity 线形度Symmetry 对称性Hysterics 滞环Threshold 灵敏度Lap 滞后Pressure gain 压力增益Null 零位Null bias 零偏Null shift 零飘Frequency response 频率响应Slope 曲线斜坡液压系统(hydraulic system)执行元件(actuator)液压缸(cylinder)液压马达(motor)液压回路(circuit)压力控制回路(pressurecontrol)流量(速度)控制回路(speedcontrol)方向控制回路(directionalvalve control)安全回路(security control)定位回路(position control)同步回路(synchronise circuit)顺序动作回路(sequeunt circuit)液压泵(pump)阀(valve)压力控制阀(pressure valve)流量控制阀(flow valve)方向控制阀(directional valve)液压辅件(accessory)普通阀(common valve)插装阀(cartridge valve)叠加阀(superimposed valve)air-compressor valve 空气压缩机阀门automatic cutout valve 自动切断阀门backlash valve 无游隙阀门High temperature valve 高温阀门hose valve 水带阀门pipe manifold valves 管道汇集器阀门pneumatic cylinder cock valve 风动汽缸排水阀阀门pneumatic positioner valve 气动阀门定位器pneumatic sander valve 风动撒砂器阀门quick opening valve 快开阀门quick-opening gate valve 速启阀门standby valve 应急阀门; 备用阀门two selenoid 双螺管阀门valve chest 阀门室valve clearance 阀门间隙;阀余隙valveman 阀门操作者wash-out valve 清洗阀门adjusting valve 调整阀, 调节阀admission valve 进气阀; 进浆阀air admission valve 进气阀air bleed(ing) valve 排气阀; 排气嘴air control valve 空调阀air cylinder valve 气筒阀air escape valve 泄气阀air inlet valve (=air intake valve)进气阀; 进风阀air operated throttle motor 风动节流器, 风动节流阀马达air pilot valve 空气导向阀air pressure governor valve 风压调压阀air relay valve 空气中继阀air release valve (=air relief valve)排气阀; 放空阀air reversing valve 空气换向阀air shut-off valve 空气关闭阀air signal reducing valve 空气信号减压阀air slide valve 空气分配阀air starting (control) valve 空气起动(控制)阀air straining check valve 空气滤尘止回阀air valve 空气阀air vent valve 气动调压阀, 排气阀air-actuated direction valve 气动控制换向阀air-compressor valve 空气压缩机阀门air-operated valve 气动换向阀air-vacuum proportional valve 空真比例阀air-vacuum two way valve 空真二位阀alarm valve 报警阀aligned grid valve 栅极中点校直的电子管阀Allan valve 阿伦滑阀altitude valve 【航空】高度阀(航空发动机汽化器的可调整阀)ammonia valve 【工】氨阀angle back-pressure valve 背压角阀angle globe valve 折角球形阀angle stop valve 弯形止阀, 折角止阀angle valve 角阀angle water valve 折角水阀annular ring valve 环形阀; 环状阀anti-g valve 【航空】防超重活门,抗重力阀application pilot valve 作用导阀application valve 作用阀, 控制阀ashpan blower valve 灰盘吹风阀Askania valve 射流管阀atmos valve (=atmospheric valve)大气阀, 空气阀; 放空阀autocontrol valve 自动控制阀automatic air valve 自动空气阀automatic brake valve 自动制动阀automatic control valve 自动控制阀automatic cutout valve 自动切断阀门automatic delivery control valve自动输送控制阀automatic drain valve 自动排水阀automatic expansion valve (定压式)自动膨胀阀automatic gas sampling valve 自动气体进样阀automatic reducing valve 自动减压阀(高速制动机)automatic regulating valve 自动调节阀automatic spring loaded valve 自动弹簧阀Regulator valve 稳压阀。
Hydraulic Power Supply 液压供应单元
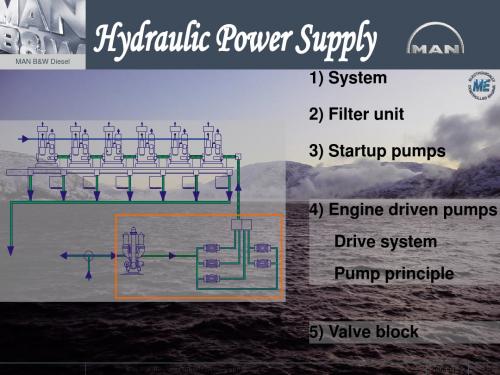
© MAN B&W Diesel Hydraulic power supply - Tom Ballegaard/4140
Back flushing process
2006-01-23 <6>
Backflushing line to Lub. Oil tank
MAN B&W Diesel
The purifier suction pipes have the same diameters but a different lenght.
Manual mode: Controlled by the operator via the Main Operating Panel
© MAN B&W Diesel
Hydraulic power supply - Tom Ballegaard/4140
Hydraulic and pneumatic systems_i
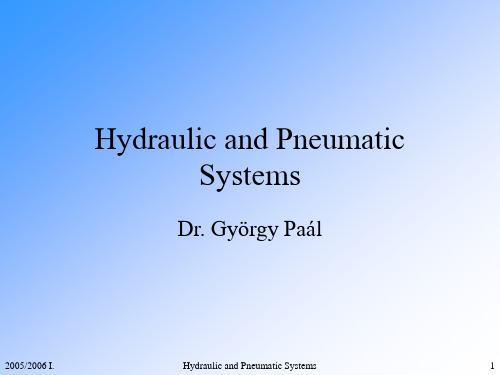
•
•
The relative spatial position of prime mover is fixed
If the motor is electrical (DC motor or AC motor with variable frequency), then the rotational speed can be continuously changed but they are expensive
4
Structure of a hydrostatic drive
Aggregate
Control
Actuator
elements
Pump, motor Fluid reservoir Pressure relief valve Filter Piping
Valves, determining the path, pressure, flow rate of the working fluid
2005/2006 I.
Hydraulic and Pneumatic Systems
3
Hydrostatic vs hydrodynamic systems
Power density Roughly speaking: kg P = Dp· Q kW Large Q, small Dp hydrodynamic transmission Large Dp, small Q hydrostatic transmission. But there is no general rule, depends on the task. Hydrostat.
2005/2006 I.
Hydraulic and Pneumatic Systems
SPEARS 中国版《塑料管手册》说明书
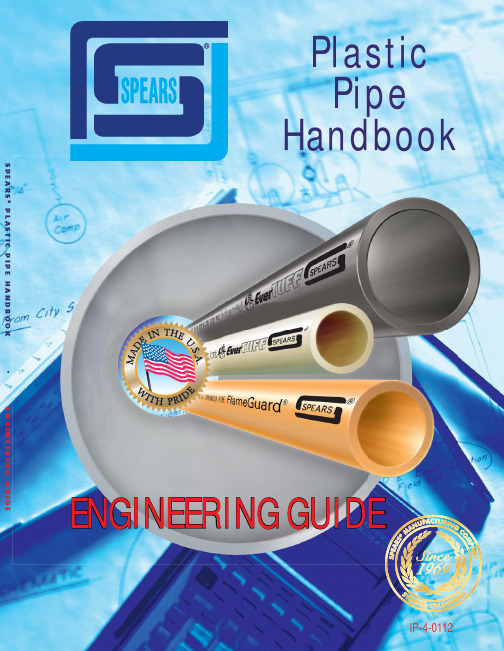
Table of Contents
General Information .........................................................................................................1 Purpose of this Manual..................................................................................................1 Spears® PVC & CPVC Materials ..................................................................................1
Physical Properties of PVC & CPVC Pipe......................................................................2 Dimensions & Pressure Ratings.....................................................................................3
SPEARS® PLASTIC PIPE HANDBOOK
Plastic Pipe
水轮机电液调节系统及装置技术规程(英文版)
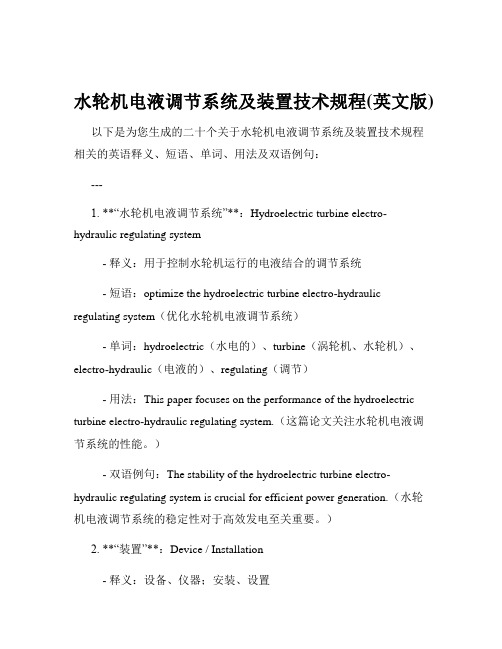
水轮机电液调节系统及装置技术规程(英文版)以下是为您生成的二十个关于水轮机电液调节系统及装置技术规程相关的英语释义、短语、单词、用法及双语例句:---1. **“水轮机电液调节系统”**:Hydroelectric turbine electro-hydraulic regulating system- 释义:用于控制水轮机运行的电液结合的调节系统- 短语:optimize the hydroelectric turbine electro-hydraulic regulating system(优化水轮机电液调节系统)- 单词:hydroelectric(水电的)、turbine(涡轮机、水轮机)、electro-hydraulic(电液的)、regulating(调节)- 用法:This paper focuses on the performance of the hydroelectric turbine electro-hydraulic regulating system.(这篇论文关注水轮机电液调节系统的性能。
)- 双语例句:The stability of the hydroelectric turbine electro-hydraulic regulating system is crucial for efficient power generation.(水轮机电液调节系统的稳定性对于高效发电至关重要。
)2. **“装置”**:Device / Installation- 释义:设备、仪器;安装、设置- 短语:testing device(测试装置)、installation procedure(装置安装程序)- 单词:test(测试)、procedure(程序、步骤)- 用法:The new device has improved the efficiency of the system.(新装置提高了系统的效率。
Parker Hannifin Corporation 集成水力分部 Lincolnshire, I

300 21
200 14
100 7
0 LPM
0 GPM
DPR083C5
DPR083C2
4
8
11
15
19
1
2
3
4
5
Flow (Q)
Regulated Pressure vs. % of Rated Current
PSI Bar 400 28
Hydraulic Oil 150 SSU @ 100°F (32 cSt)
Reg (1)
THIRD-ANGLE PROJECTION
Ordering Information
DPR083C
Size 08 D.A., N.C. Proportional
Reducing/Relieving Valve
Flow Option
Code Flow Option 2 7.5 LPM (2 GPM) 5 18.8 LPM (5 GPM)
(2) (3)
Pressure (2)
Reg. (1)
(3) Tank
Specifications
Rated Flow Maximum Inlet Pressure Maximum Reduced Pressure
Maximum Leakage Hysteresis @ 200 Hz PWM Cracking (Dead band) Frequency Maximum Control Current Cartridge Material
Code Override Options
M Push Type with Flush Rod
Code Seals / Kit. No. Omit Nitrile / (SK08-3N)
液压压力传感器(Hydraulicpressuresensor)

液压压力传感器(Hydraulic pressure sensor)HYDAC (He Deke) hydraulic pressure sensor1. overviewThe hydraulic pressure sensor is one of the most pressure sensors used in the industry practice, which is widely used in various industrial control environment, involving oil pipelines, water conservancy and hydropower, railway transportation, intelligent buildings, production automation, aerospace, military, petrochemical, oil, electric power, shipbuilding, machine tools, air duct, negative pressure boiler etc. industry.2. working principleThe working principle of the hydraulic pressure sensor is pressure directly on the sensor diaphragm, the diaphragm will produce micro displacement is proportional to the medium pressure, the sensor resistance changes, and the electronic circuit used to detect this change, and convert a standard signal output corresponding to the pressure.3. correlation parameterA, pressure range (German druckbereich):-0.1 ~ 0~1 ~ 1000 (MPa)1 BA (bar) =100 (KPa) =10 Newton kPa / cm2 =0.1MPa bar is pressure units, previously used in meteorology mbar, now use international unit equivalent hpa. 1 pa is the abbreviation of "1 Pascal", that is, one square meter is under the pressure ofone newton. The project is still in use in this unit kilogram force, 1 kilograms force equal to 9.80665 Newton, resulting in engineering atmospheric pressure: 1 Engineering atmospheric pressure =1 kg / cm2 =0.967841 atmospheric pressure =98066.5 mm Hg Pascal is also a common unit of pressure, the pressure generated by the definition of the unit of pressure of 1 mmHg for support (Torr) 1 Torr =1 mm Hg =133.32 Pascal 1 atmospheric pressure =760 supportB, comprehensive accuracy: 0.1%FS, 0.25%FS, 0.5%FS (FS is Full Scale, meaning is full range of a few percent)C, output signal: 4 ~ 20mA (two-wire system), 0 ~ 5V, 1 ~ 5V, 0 ~ 10V (three wire system)D, supply voltage (German: Versorgung), 24DCV (9 ~ 36DCV)E, medium temperature: -20 ~ 85~150 DEG CF, ambient temperature: normal temperature (-20 ~ 85 DEG C)G, zero temperature drift: less than 0.05%FS DEG CH, the range of temperature drift: less than 0.05%FS DEG CI and compensation temperature: 0~70 DEG CJ, safety overload: 150%FSk, limit overload: 200%FSL, response time: 5 mS (up to 90%FS)M, load resistor: current output type: maximum 800; voltage output type: greater than 5KN, insulation resistance: greater than 2000M (100VDC)O, seal grade: IP65 long term stability: 0.1%FS/ yearsP, vibration effect: in the mechanical vibration frequency 20Hz ~ 1000Hz, the output change is less than 0.1%FSQ, electrical interface (signal interface): tightening nut + four core shielding wireR, mechanical connection (thread interface),:M20 * 1.5, etc., other threads can be designed according to customer requirements4, features introduced1. sensor: a device or device that senses a prescribed amount of measurement and converts it into usable output signals in accordance with certain rules. There are usually sensitive components and conversion components. A sensitive element is a part of a sensor that can be directly (or responded) to be measured. A conversion element refers to the north side of a sensor that can sense or respond to sensitive components, converting it into electrical signals that are part of the transmission and / or measurement. When the output is the standard signal, it is called the transmitter.2. range of measurements: the range of the measured values within the allowable error limit.3. range: the algebraic differencebetween the upper and lower limits of the measurement range.4. accuracy: the degree of agreement between measured and true values.5. from the complex: in all the following conditions, the degree of correspondence between the same quantity to be measured many times measuring results:6. resolution: sensors in the specified measuring range round minimum change in the quantity being measured may be detected.7. threshold: the minimum amount of variation that can be measured at the end of a sensor to produce measurable variations.8. Zero: the state of minimizing the absolute value of an output, such as a balanced state.9. excitation: the external energy (voltage or current) applied to make the sensor work properly. TenMaximum excitation: the maximum value of an exciting voltage or current that can be applied to a sensor in urban conditions.11. input impedance: the impedance measured at the end of the sensor when the output is shorted. 12. output: the amount of electricity produced by the sensor and measured as a function.13. output impedance: the impedance measured at the output of the sensor when the input is shorted. 14. zero output: under local conditions, the output of the sensor is measured at zero.15. lag: the maximum difference in output within a specified range when the measured value is increased and decreased. 16. delay: the time delay in which the output signal changes with respect to the input signal. 17. drift: the amount of unnecessary change in which the output of the sensor is finally measured at a given time interval. 18. zero drift: changes in the output of zero points at specified time intervals and indoor conditions. 19. sensitivity: the ratio of the increment of the sensor output to the increment of the corresponding input quantity. 20. sensitivity drift: the change of slope of thecalibration curve due to sensitivity changes. 21. thermal sensitivity shift: sensitivity shift due to changes in sensitivity. 22. thermal zero drift: zero drift due to changes in ambient temperature. 23. linearity: the extent to which a calibration curve is consistent with a given regulation. 24. degree of linearity: the degree to which a calibration curve deviates from a specified line. 25. long term stability: the ability of the sensor to keep within a specified time without exceeding the allowable error. 26. inherent rate: in the absence of resistance, the freedom of the sensor (without external force) oscillation rate. 27. response: the characteristics of the output being measured. 28. range of compensation temperature: the temperature range compensated by the sensor to keep the range and zero balance within the specified limit. 29. creep: changes in the amount of output within a specified time when the machine is maintained with constant environmental conditions. 30. insulation resistance: if not specified, refer to the resistance value measured between the insulation section of the sensor when the specified DC voltage is applied at room temperature.。
昆士莱Hydraulic Valve Division发布的D1TX throttle valve产

Series D1TXTechnical InformationGeneral DescriptionThe D1TX throttle valve is designed to vary theamount of fluid flow in proportion to a variable inputcommand signal. The valve will respond to voltagecommand signals of 0 to +10 VDC, or current com-mand signals of 4-20 mA. The valve features on-board electronics and built-in spool position feedbackfor low hysteresis.OperationA minimum of 20 PSI must be maintained on the “Yor L” ports for proper operation. An external supply of20 PSI or a 20 PSI check valve may be used for thispurpose.To simplify piping of the valve for the maximum flowoutput, order our flow conversion module, FCB03**which has the 20 PSI check valve already installed.This module converts all of the flow paths internally.Connect the “P” for supply pressure, “B” for outletflow, and “Y or L” for drain line flow.Features•Integral Electronics — Eliminates the time consumingand often costly wiring between the valve and drivercard. Provides a fully tested valve/driver package.•LVDT — The spool position feedback provides lowhysteresis.•Manual Override•Diagnostic Indicator — An LED confirms movement ofthe spool.•Rugged Construction — Integral electronics arepackaged in a rugged die cast aluminum enclosure toprotect it from harsh environments.•Electrical Interface — Standard MS style connector forinterface to computers and PLC's.24 volt model:Operating Temp.-20° to 60°C (-4° to 140°F)Range (Ambient)12 volt model:-29° to 60°C (-20° to 140°F)Spool Version BJ, DJ: (-10 VDC)Position Voltage Version DK: (-5 VDC)Reference+10 VDC @ 10 mA (BJ, DJ)Supply+5 VDC @ 10 mA (DK)Low Power20 VDC (BJ, DJ)Fault Protection 11 VDC (DK)Diagnostics Red LED for spool positionViscosity Range75 - 600 SSUFluid Cleanliness ISO Class 16/13, SAE Class 4or betterProtection Class Nema 4 (IP65)InputVersion Command Signal ImpedanceBJ, DJ 0 to + 10 VDC Sgl. Coil 100 k ohmsDK 0 to + 5 VDC Sgl. Coil 100 k ohmsBJ, DJ 4 to 20 mA Command 499 ohmsDK 4 to 20 mA Command 249 ohms SpecificationsInterface NFPA D03, CETOP 3Maximum Pressure 207 Bar (3000 PSI)Drain Line 1.4 Bar (20 PSI) minimumPressure 35 Bar (500 PSI) maximum("T" and "Y" or "L")Flow Up to 61 LPM (16 GPM) (Dual Ported)Frequency> 20 Hz with 10% CMD at 50%Response spool strokeVersions BJ, DJ:Step Full Shift, <60 mSResponse Version DK:Full Shift, <70 mSRepeatability< 0.5% of spool strokeHysteresis< 1.5%Nominal Deadband 10%24 VDC @ 3 amps nom.**(BJ, DJ)Power Range 21 to 30 VDC regulatedRequirements12 VDC @ 3 amps nom. (DK)**Range 11.5 to 15 VDC regulated**4 amp regulated power supplyrecommendedSeries D1TXOrdering InformationDesign Series NOTE: Not required when orderingD1TD03 Control Equal Spool Electronic FlowExternal Supply Valve Accessories010EEStyleSealX9Electronic Code Description NNitrileV FluorocarbonC ode Description 03D03Code Description Y “Y” Drain Port (standard) L“L ” Drain Port (optional)Use Bolt Kit BK243 when including the FCB under the D1TX.FCBFlow ConversionBlockSizeSubplate Drain Port03Seal3.2 kg (7.0 lbs.)(4) 10-24x1.25 SHCSOperating LimitsMax.Pressure Drop/Flow Envelopeat 100% Command SignalP r e s s u r e D r o p (P S I )Flow (Q)LPMParallel Flow Path*P A & BT or P B & A TNominal Supply Voltage7.6215.1422.76830.353.01460.61637.91045.41200PSIBarFlow Conversion Block FCB03* Requires Flow Conversion Block FCB**Performance Curves** Flow rate for different ∆p per control edge: Q x = Q Nom. · √∆p x∆p Nom.Inch equivalents for millimeter dimensions are shown in (**)F l o w (Q )Command Signal (% of Max.Signal)Flow vs.Input CommandParallel Flow Path Connected*P = 125 PSI**D 204080100600LPM GPMDimensionsHydraulic ConnectionsMounting SurfaceRequired PortsCOM B INA TION P A B T Y LD1TX valve alone ✓ ✓ ✓ ✓ ✓D1TX w/FCB03Y ✓ ✓ ✓*D1TX w/FCB03L✓✓✓**Y & L port not required if external drain port (SAE-4) is used.Surface must be flat within 0.10 (.0004) T .I.R. andsmooth within 32 micro-inch. T orque bolts to 5.6 N.m.(50 in.-lbs.)。
maximator 3 3-way-proportional valve 技术手册说明书

3/3-Way-Proportional ValveContentPageGeneralDescription1Design2Function 2TechnicalData3Options4Dimensions5Accessories6FlowCurves 7General DescriptionThis proportional valve in combination with the elec-tronic control system allow for easy, swift and conti-nuous regulation of the variables fl ow and pressure ingases and fl uids with a high level of repeating accura-cy.The valve is manufactured in sizes 10mm and 4mmwhich allows the application in a variety of controltasks in process engineering.The 3/3-Way-proportional valve is pilot operated andcan be supplied with or without integrated pilot controlhydraulic supply.DesignThe MAXIMATOR proportional valve consists of the following main elements: • Valve box• Attached control valve for actuation of the main valve • Main valve unit with seals, piston and reset spring•Pressure-resistant distance sensor to check main valve stroke• Pressure transducer (external) optional • Control electronics (external) optionalFunctionThe valve is a metallic seal 3/3 way - seat valve. Theopening and closing of the valve takes place by means of a hydraulically actuated set piston.An electrical signal is set by the control electronics as a reference. This target value may be the analog output of a process computer, a controller or a manually operated set point sensor.The command signal causes the control electronics of the control valve to displace the piston against the direction of action of the spring.The friction-locked valve cone is lifted through the spindle from the valve seat or rather the valve stem is moved to the opening of the relief connection. Thus the consumer can be supplied with gas or relieved.The actual value of the pressure on the consumer side, which is measured by a pressure transducer, is taken into account of the position control loop of the valve as an analog value.Normal-PositionAfter switching on the hydraulic and electric supply the set piston moves into the normal position of the valve.No pressure increasing takes place. A to T open!Pressure increasingThe set piston moves to the right site and closes the R-Medium return line and opens the P-Medium Inlet.The pressure increasing takes place. T-Medium ReturnPressure decreasingThe set piston moves to the left site and closes the P-Medi-um Inlet and opens the R-Medium Return.The pressure decreasing takes place. T-Medium Return -from A to T!Figure: Assembly 3/3-Way Proportional ValveFigure: Block diagram 3/3-Way Proportional ValveFigure: schematic diagram 3/3-Way Proportional ValveTechnical DataOptionsServo valve with control cardThe electronic control system with PID controller, actual value and setpoint input is supplied as a 19“card, tailored to the respective valve.The 19“ control card belonging to the valve contains the pressure and position controller for the valve and the ampli-fier for the pilot valve.The reference inputs for pressure, valve opening and the actual value are present as differential inputs.The characteristics of the PID controller is roughly set using a DIL switch on the card and fine adjustment on the front panel.Servo valve with On-Board-Elektronic (OBE) The pilot valve with integral position feedback and integra-ted valve electronics is calibrated at the factory.For electrical connection a 6P+PE signal input with diffe-rential amplifier (interface A1 ±10V (Rs 200 Ω)) is available. IAC-R Servo valveThe servo valve with integrated digital axis controller (IAC-R) and field bus interface provides control functionality for:• Volume flow control• Position control• Pressure control• P/Q-Function• Replacing position/pressure control and position/force controlThe set point / actual value feedback can take place by analog (current or voltage) or via field bus.Mounting versionsThe 3/3-Way Proportional valve is available as a tube con-nection or a plate connection version.The following figure shows the plate connection versionof the 3/3-Way proportional valve mounted in a standardcontrol block with pilot control hydraulic supply.Figure: MAXIMATOR-control block with two proportional valvesand pilot control hydraulic supplycableFigure: Dimensions 3/3-Way Proportional ValveAccessoriesConnection plateDepending on the type (NG10 or NG4) and pressure range Maximator offers the right connection plate. The following table lists the order codes of the connecting plates.Hydraulic UnitsAs an auxiliary power, hydraulic actuating power is requi-red. There should be a minimum pressure of 120 bar used. To control the valve large quantities of hydraulic oil may be required for a short time.The flow rate depends on the task of regulation. Flow rates of up to 40 l/min may be required from the servo valve for a short time, but for each control cycle a maximum oil volume of approx. 56 cm 3 (NG 10) or 15 cm 3 (NG 4).By using a hydraulic accumulator and depending on the control frequency the appropriate unit for the hydraulicdrive can be selected.3920.01133920.14293920.2792Figure: Block diagram control block with pilot controlhydraulic supplyliquid: hydraulic oil SAE 48 valve: NG 4Characteristic curve NG10Characteristic curve NG4。
Parker Hannifin 方向控制阀门目录HY14-2500 US A系列说明书

Series D31, D3*PInstallation InformationThe following is important installation informationwhich applies to all directional control valves describedin this catalog.Mounting PositionDetent – HorizontalSpring Offset – UnrestrictedSpring Centered – UnrestrictedFluid RecommendationsPremium quality hydraulic oil with a viscosity rangebetween 32-54 cst. (150-250 SSU) At 38°C (100°F) isrecommended. The absolute operating viscosity rangeis from 16-220 cst. (80-1000 SSU). Oil should havemaximum anti-wear properties and rust and oxidationtreatment.Fluids and SealsValves using synthetic, fire-resistant fluids requirespecial seals. When phosphate esters or its blends areused, FLUOROCARBON seals are required. Water-glycol, water-in-oil emulsions and petroleum oil maybe used with STANDARD seals.FiltrationFor maximum valve and system component life, thesystem should be protected from contamination ata level not to exceed 125 particles greater than 10microns per milliliter of fluid (SAE class 4/ISO 16/13).Series NFPA SizeD31V*, D3P D05H, CETOP 5 3/8"D31D*, D3DP, D31NW D05HE, CETOP 5H 3/8" FOR MAXIMUM VALVE RELIABILITY, ADHERE TOTHE FOLLOWING INSTALLA TION INFORMATION.Mounting PatternsTorque SpecificationsThe recommended torque values for the bolts whichmount the valve to the manifold or subplate are asfollows: 16.3 Nm (12 ft-lb).SiltingSilting can cause any sliding spool valve to stickand not spring return if held under pressure for longperiods of time. The valve should be cycled periodicallyto prevent sticking.Special InstallationsConsult your Parker representative for any applicationrequiring the following:• Pressure above rating.• Fluid other than those specified.• Oil temperature above 71.1°C (160°F).• Flow path other than normal.1/16 Pipe Plug for Variations 4 & 5T orque to:11.67 ± 1.67 Nm (105 ± 15 in-lbs)1/16 Pipe Plug for Variations 1 & 4T orque to:11.67 ± 1.67 Nm (105 ± 15 in-lbs)NFPA D05HE,CETOP 5H Pattern D31DW1/16 Pipe Plug for Variations 1 & 4T orque to:11.67 ± 1.67 Nm (105 ± 15 in-lbs)1/16 Pipe Plug for Variations 4 & 5Torque to:11.67 ± 1.67 Nm (105 ± 15 in-lbs)Installation InformationSeries D31Style Description No Solenoid/Operator Solenoid/Operator A Solenoid/Operator BCode Energized Energized EnergizedB Spring Offset P ➝A and B ➝T — P ➝B and A ➝TC Spring Centered Centered P ➝A and B ➝T P ➝B and A ➝TD Detented Last Position HeldP ➝A and B ➝T P ➝B and A ➝TE Spring CenteredCentered—P ➝B and A ➝T F† Spring Offset, Shift to Center P ➝A and B ➝T — CenteredH Spring Offset P ➝B and A ➝T P ➝A and B ➝T —K Spring CenteredCenteredP ➝A and B ➝T —M†Spring Offset, Shift to CenterP ➝B and A ➝T Centered—† D31*W only.SERIES D31*W, D31*A, D31*LPILOT OPERATED,DIRECTIONAL CONTROL VALVES Tank and Drain Line SurgesIf several valves are piped with a common tank or drain line, flow surges in the line may cause an unexpected spool shift. No spring style valves are most susceptible to this. Separate tank and drain lines should be piped in installations where line surges are expected.Electrical Failure orLoss of Pilot Pressure (D31*A)Should electric power fail or loss of pilot pressure occur, spring offset and spring centered valves will shift to the spring held position. Detented valves will stay in the last position held before power failure. If main flow does not fail or stop at the same time power fails, machine actuators may continue to function in an undesirable manner or sequence.Electrical Characteristics (Detented Spool)Only a momentary energizing of the solenoid isnecessary to shift and hold a detented spool. Minimum duration of the signal is 0.1 seconds for DC voltages. For AC voltages the response time is 0.06 seconds. Spool position will be held provided the spoolcenterline is in a horizontal plane, and no shock or vibration is present to displace the spool.Pilot/Drain CharacteristicsPilot Pressure: 6.9 to 345 Bar (100 to 5000 PSI)External: An oil source sufficient to maintain minimum pilot pressure must be connected to the “X” port of the main body. When using the external pilot variation, an M5 x 0.8 x 6mm long set screw must be present in themain body pilot passage. (For details see Dimension pages.) This plug will be furnished in valves ordered with pilot code 2 or 5.Internal: Flow is internally ported from the pressure port of the main valve body to the “P” port of the pilot valve. The pressure developed at the “P” port of the pilot valve must be 100 PSI (6.9 Bar) minimum at all times.If the valve center condition allows flow from pressure to tank, 100 PSI (6.9 Bar) back pressure must be developed in the tank line to ensure sufficient pilot force at “P”. The “X” port in subplate must be plugged when using internal pilot variation (1/16 NPT).Pilot Valve Drain:Maximum pressure 102 Bar (1500 PSI), 207 Bar (3000 PSI) optional.External: When using an external drain, an M6 x 1 x 10mm long set screw must be present in the main body drain passage. (For details see Dimension pages.) This plug will be furnished in valves ordered with drain code 1 or 2.Drain flow from the pilot valve is at the “Y” port of the main body and must be piped directly to tank. Maximum drain line pressure is 102 Bar (1500 PSI), 207 Bar (3000 PSI) optional. Any drain line backpressure is additive to the pilot pressure requirement.Internal: Drain flow from the pilot valve is internally connected to the main valve tank port. Tank and drain pressure are then identical so tank line pressure should not exceed 102 Bar (1500 PSI), 207 Bar (3000 PSI) optional. Any tank line back pressure is also additive to the pilot pressure requirement. If flow surges (a cause of pressure surges) areanticipated in the tank line, an external drain variation is recommended. The “Y” port in subplate must be plugged when using internal drain variations.D31*W, D31*A, D31*L Flow PathsPilot Drain CharacteristicsPilot Pressure: 6.9 to 345 Bar (100 to 5000 PSI)Direct pilot operated valves use the “X” and “Y” portsto supply pilot oil directly to the ends of the spool,providing spool shifting force. A block mounted ontop of the valve body is internally cored to make thenecessary connections. Thus when “X” is pressurized,“Y” is used as a drain; and when “Y” is pressurized, “X”becomes the drain.Any back pressure in these lines when they arebeing used as a drain is additive to the pilot pressurerequirement.Internal Drain: On spring offset models, only the “X”port is pressurized, as the spring returns the spoolto its at rest position. On these models, “Y” may beinternally drained through the main tank passage inthe valve.SERIES D3P, D3DP PILOT OPERATEDDIRECTIONAL CONTROL VALVESTank and Drain Line SurgesIf several valves are piped with a common tank or drainline, flow surges in the line may cause an unexpectedspool shift. Separate tank and drain lines should bepiped in installations where line surges are expected.Loss of Pilot PressureShould oil pilot pressure fail, spring offset and springcentered valves will shift to the spring held position.Detented valves will stay in the last position heldbefore power failure. If main flow does not fail or stopat the same time power fails, machine actuators maycontinue to function in an undesirable manner orsequence.Mounting PatternD3P valves may be mounted on a standard D05pattern subplate or manifold only if the “X” and “Y”ports are externally connected to the pilot block ontop of the main body. All other mounting styles requirea D05H or D05HE pattern which incorporates portsfor the “X” and “Y” pilot and drain passages. Locationof these ports can be found on the RecommendedMounting Surface pages in this section.D3P Flow Path/Pilot PressureFor maximum valve reliability,adhere to the following installation information.Mounting Pattern — NFPA D05H, CETOP 5Inch equivalents for millimeter dimensions are shown in (**)Series D31VW, D31VA, D31VL, D3P Subplate Mounting NFPA D05H, CETOP 5Recommended Mounting SurfaceSurface must be flat within .102 mm (0.0004 inch) T .I.R and smooth within 812.8 micro-meters (32 micro-inch). Torque bolts to 16.3 Nm (12 ft-lbs).Mounting PositionValve Type Mounting Position Detent (Solenoid) Horizontal Spring Offset Unrestricted Spring Centered UnrestrictedSeries D31DW, D31DA, D31DL, D3DP, D31NWSubplate MountingNFPA D05HE, CETOP 5HRecommended Mounting SurfaceSurface must be flat within .102 mm (0.0004 inch) T.I.R.and smooth within 812.8 micro-meters (32 micro-inch).Torque bolts to 16.3 Nm (12 ft-lbs).Mounting PositionValve Type Mounting PositionDetent (Solenoid) HorizontalSpring Offset UnrestrictedSpring Centered UnrestrictedFor maximum valve reliability,adhere to the followinginstallation information.Mounting Pattern — NFPA D05HE, CETOP 5HInch equivalents for millimeter dimensions are shown in (**)M6x1(1/4-20)UNC-2Bthreadx9.7(.38)min.thread depth4places11.2(O.44)max.P.A.B.&T ports6.3(O.25)max.X&Y ports.56(.022).56(.022)75.0(2.95)91.9(3.62)min.with X&Y ports72.1(2.84)min.without X&Y ports.28(.011)AAAABBBYTPXBBA46.0(1.81)11.1(.44)11.1(.44)43.6(1.72)6.4(.25)27.0(1.06)32.5(1.28)7.9(.31)37.3(1.47)54.0(2.13)50.8(2.00)61.9(2.44)57.9(2.28)min.21.4(.84)SLL16.7(.66)。
红外传感器说明书

R od RedundantG eneral data SeriesRod Redundant BTL7Shock load 100 g/6 ms as per EN 60068-2-27Vibration12 g, 10...2000 Hz as per EN 60068-2-6Polarity reversal protected to 36 V Overvoltage protection to 36 VDielectric strength500 V AC (GND to housing)Degree of protection as per IEC 60529IP 67Housing material Aluminum anodized/protective tube stainless 1.4571, fl ange stainless 1.4571FastenersModel TB thread M18×1.5, Model TZ thread 3/4" 16 UNF Model TK, 18h6 with 6 cheese head screws, Model TT thread M30x1.5Pressure rating with 10.2 mm protective tube 600 bars if installed in a hydraulic cylinder up to 2000 mm in nominal stroke 300 bar for nominal stroke > 2000 mmPressure rating with 21 mm protective tube 250 bars if installed in hydraulic cylinder up to 2000 mm nominal stroke Connection Connector or cable connectionEMC testingRadio interference emission EN 55016-2-3 (industrial and residential area)Static electricity (ESD)EN 61000-4-2 Severity level 3Electromagnetic fi elds (RFI)EN 61000-4-3 Severity level 3Fast transient interference pulses (BURST)EN 61000-4-4 Severity level 3Surge voltage (SURGE)EN 61000-4-5 Severity level 2Conducted interference induced by high-frequency fi elds EN 61000-4-6 Severity level 3Magnetic fi eldsEN 61000-4-8 Severity level 4Standard nominal strokes [mm]25...7620 mm in 1-mm incrementsy o f C M A /F l o d y n e /H y d r a d y n e ŀ M o t i o n C o n t r o l ŀ H y d r a u l i c ŀ P n e u m a t i c ŀ E l e c t r i c a l ŀ M e c h a n i c a l ŀ (800) 426-5480 ŀ w w w .c m a f h .c o mRod RedundantG eneral data1) Unusable range2) Not included in the scope of delivery 3) Ø 6.1 for hook wrench Ø 744) Included in the scope of deliveryPressure-resistant up to 600 bar, high repeatability,redundant, non-contactBTL7 redundant Micropulse transducers: the robust position measuring system for use in safety-related valves and hydraulic cylinders for measuring ranges between 25 and 7620 mm.Up to three independent position measuring systems in the same housing enable fail-safe linear measurement of, for example, safety valves or the combined monitoring of position and velocity.Stroke Lengths up to 7620 mmMicropulse transducers Profi le PProfi le PF Profi le AT Profi le BIWRodRod Compact and Rod AR Rod EX Filling level sensor in zone 0/1Transducer in zone 1Rod DEX Rod J-DEXC Rod PEX Rod NEX Floats and magnets Rod T Redundant General data Programming Magnet Rod CD General dataFilling Level Sensor SF Accessories BasicInformation and Defi nitionsy o f C M A /F l o d y n e /H y d r a d y n e ŀ M o t i o n C o n t r o l ŀ H y d r a u l i c ŀ P n e u m a t i c ŀ E l e c t r i c a l ŀ M e c h a n i c a l ŀ (800) 426-5480 ŀ w w w .c m a f h .c o mRod RedundantGeneral dataProperties of Micropulse BTL7-A/C/E/G to TB/TZ/TK/TT ■2 or 3 times redundant■Non-contact detection of piston position ■IP 67, insensitive to contamination■Shock and vibration resistant 100 g/12 g ■Absolute output signal■Measurement lengths 25 to 7620 mm in 1-mm increments ■Flexibly confi gurable measuring range via computer programming ■Status LED to indicate the operating state ■Temperature range –40 to +85°CFlexible measuring rangeThe start and end point of the measuring range can be adapted to the application. The output signal for the position indicator or the movement speed can be set just as conveniently.Once confi gured, settings can easily be copied redundantly to the remaining measuring channels of the BTL7.Ordering example:BTL7-_5_ _-M_ _ _ _-_ _ _-_ _ _Rod version, fastener TB2= Standardmounting thread 3/4"-16 UNF ,O-ring, roddiameter 10.2 mm,2 times redundant TB3= Standardmounting thread 3/4"-16 UNF , O-ring, rod diameter 10.2 mm,3 times redundant For additional designs, see page 219Output gradient 04 1 output can be confi gured as rising 051 output can be confi gured as fallingNominal stroke [mm]25...7620 mmin 1-mm incrementsOutput signal A 0...10 V or 10...0 V C 0...20 mA or 20...0 mA E 4...20 V or 20...4 VG–10...10 mA or 10...–10 mAConnection S328-pin, M16 plugaccording to IEC 130-9S1356-pin, M16 plugaccording to IEC 130-9KA055 m cable, PURreliable 3 in 1y o f C M A /F l o d y n e /H y d r a d y n e ŀ M o t i o n C o n t r o l ŀ H y d r a u l i c ŀ P n e u m a t i c ŀ E l e c t r i c a l ŀ M e c h a n i c a l ŀ (800) 426-5480 ŀ w w w .c m a f h .c o mRod RedundantGeneral dataPlease enter code for output signal, nominal stroke,design, and connection in the part number.Scope of delivery ■Transducer■Quick start instructions■Fastening screws, stainless steel, "600 bar" (only design TK)■Adapter fl ange (only design TK)Please order separately:Calibration box, page 178Magnet, page 223Micropulse transducers Profi le P Profi le PF Profi le AT Profi le BIW Rod Rod Compact and Rod AR Rod EX Filling level sensor in zone 0/1Transducer in zone 1Rod DEX Rod J-DEXC Rod PEX Rod NEX Floats and magnets Rod T Redundant General data Programming Magnet Rod CD General data Filling Level Sensor SF Accessories BasicInformation and Defi nitionsy o f C M A /F l o d y n e /H y d r a d y n e ŀ M o t i o n C o n t r o l ŀ H y d r a u l i c ŀ P n e u m a t i c ŀ w w w .c m a f h .c o mRod RedundantP rogramming System requirements ■Standard PC■Operating system: Windows 2000/XP/Vista/7■Screen resolution at least 1024 × 768 pixels ■10 MB available hard disk space■Install Java Runtime Environment (JRE) Version 1.4.2 or higher /getjava ■USB portUSB confi gurationStart, end value setting and confi guration via USB The Micropulse Confi guration Tool software enables Balluff transducers of type BTL7-A/E50... to be quickly and easily confi gured on a computer.The most important features are:■Online display of the current position of the magnet■Graphic support for setting the functions and characteristics ■Display of information about the connected transducer ■Selectable number formats and units for display ■Reset to factory settings possible■Demo mode without having a transducer connectedConnecting the USB communication boxWith the BTL7-A/504/505-S32 transducers, the communication box can be connected between the transducer and controller. The communication box is connected to the PC using a USB cable.USB communication boxBTL7-A-CB01-USB-S32,for BTL7-A/E504/505... with S32 connector BTL7-A-CB01-USB-KA,for BTL7-A/E504/505... with cable connectionScope of delivery■USB communication box ■Cable set■Quick start instructionsConnecting the communication box with S32 or S115 connectorCommunication box connected via cable in the control cabinetThe computer software and corresponding manual are available on the Internet at/downloads-btl7y o f C M A /F l o d y n e /H y d r a d y n e ŀ M o t i o n C o n t r o l ŀ H y d r a u l i c ŀ P n e u m a t i c ŀ E l e c t r i c a l ŀ M e c h a n i c a l ŀ (800) 426-5480 ŀ w w w .c m a f h .c o mRod RedundantM agnet MagnetMagnet MagnetMagnet Rod BTL Rod BTLRod BTL Rod BTL BAM013LBAM013YBAM013JBAM013RBTL-P-1013-4R BTL-P-1028-15R BTL-P-1012-4R BTL-P-1014-2R Aluminium Aluminium Aluminium Aluminium approx. 12 g approx. 68 g approx. 12 g approx. 10 g anyanyanyany–40...+100°C –40...+100°C–40...+100°C –40...+100°CBAM013MBAM013KBTL-P-1013-4R-PA BTL-P-1012-4R-PA PA 60 glass fi ber reinforced PA 60 glass fi ber reinforced approx. 10 g approx. 10 g anyany–40...+100°C–40...+100°CMicropulse Transducers Profi le P Profi le PF Profi le AT Profi le BIW Rod Rod Compact and Rod AR Rod EX Filling level sensor in zone 0/1Transducer in zone 1Rod DEX Rod J-DEXC Rod PEX Rod NEX Floats and magnets Rod T Redundant General data Programming Magnet Rod CD General data Filling Level Sensor SF Accessories BasicInformation and Defi nitionsy o f C M A /F l o d y n e /H y d r a d y n e ŀ M o t i o n C o n t r o l ŀ H y d r a u l i c ŀ P n e u m a t i c ŀ E l e c t r i c a l ŀ M e c h a n i c a l ŀ (800) 426-5480 ŀ w w w .c m a f h .c o m。