相对加工性
机械制造工艺题库+参考答案

机械制造工艺题库+参考答案一、单选题(共50题,每题1分,共50分)1、切削脆性金属产生( )切屑。
A、带状B、挤裂C、崩碎正确答案:C2、车刀上过切削刃选定点垂直于假定的主运动方向的辅助平面是( )。
A、正交平面B、主切削平面C、基面正确答案:C3、切削脆性金属材料时,形成( )切屑。
A、节状B、粒状C、带状D、崩碎正确答案:D4、衡量材料最常用的切削加工性指标是相对加工性( )。
A、切削力的大小B、已加工表面质量C、一定刀具耐用度下的切削速度D、切屑控制或断屑的难易正确答案:C5、零件加工过程一般分为粗加工、( )、( )三个阶段。
①半精加工②精加工③光整加工。
正确答案是( )。
A、①②B、②③C、①③正确答案:A6、45钢锻件粗车时,应选用的刀具材料的牌号是( )。
A、T10B、YT5C、YG8正确答案:B7、加工高精度表面时所用的定位基准称为精基准。
( )A、不一定B、正确C、错误正确答案:C8、切削用量包括( )。
①主轴每分钟转数②切削层公称宽度③背吃刀量④进给量⑤切削速度,正确答案是( )。
A、①③④B、①②③C、①④⑤D、③④⑤正确答案:D9、在安排零件的切削加工工序时,常遵循的原则是:( )。
A、先加工基准面,后加工其它表面B、先加工加工其它表面,后加工基准面C、先精加工,后粗加工D、先安排次要表面的加工,穿插加工主要表面正确答案:A10、若用已加工平面定位,一般可采用多个( )或支承板。
A、尖头钉B、球头钉C、平头钉D、网纹钉正确答案:C11、在高温下能够保持刀具材料切削性能的特性称为( )。
A、耐热性B、强度C、硬度D、耐磨性正确答案:A12、属于钻床的是( )。
A、C6140B、X8126D、M7130正确答案:C13、当工件的强度、硬度、塑性越好时,刀具寿命( )。
A、越高B、越低C、不变正确答案:B14、铸铁主要按( )分类。
A、碳的存在形式B、石墨形态C、碳的质量分数D、基体组织正确答案:A15、灰铸铁的( )与钢相似。
机床夹具设计填空题

1、数控机床综合应用了电子计算机、自动控制、伺服驱动、精密检测与新型机械结构等方面的技术成果,具有高柔性、高精度与高自动化的特点。
2、数控机床的发展经历了电子管、晶体管、小规模集成电路、大规模集成电路及小型计算机和微处理机或微型计算机等五代数控系统。
3、FMS表示柔性制造系统。
4、CIMS表示计算机集成制造系统。
5、DNC表示直接数控系统。
6、NC表示普通数控系统。
1、按切削运动在切削加工中的功用不同分为主运动和进给运动。
2、主运动只有一个。
3、工件在切削过程中形成了三个不断变化的表面已加工表面、待加工表面、过渡表面。
4、切削要素包括切削用量和切削层的几何参数。
5、刀具切削部分组成要素前刀面、主后刀面、副后刀面、主切削刃、副切削刃、刀尖。
6、正交平面参考系由基面(Pr)、切削平面(PS)、正交平面(Po)组成。
7、在正交平面中测量的角度有前角(γo) 、后角(αo)、楔角(βo)。
8、在基面中测量的角度有主偏角(κr)、副偏角(κrˊ) 、刀尖角(εr) 。
9、在切削平面中测量的角度有刃倾角(λS)。
10、当刀尖相对于车刀刀柄安装面处于最高点时,刃倾角为正值;当刀尖处于最低点时,刃倾角为负值;当切削刃平行于刀柄安装面时,刃倾角为0°。
11、刀具材料有高速钢、硬质合金、其他刀具材料。
12、常用的硬质合金有三大类钨钴类硬质合金(YG)、钨钛钴类硬质合金(YT)、钨钛钽(铌)类硬质合金(YW)。
13、钨钴类硬质合金(YG):适用于加工脆性材料(铸铁等)。
14、钨钛钴类硬质合金(YT):适用于切屑呈带状的钢料等塑性材料。
15、钨钛钽(铌)类硬质合金(YW) :既能加工钢、铸铁、有色金属,也能加工高温合金、耐热合金及合金铸铁等难加工材料。
16、其他刀具材料包括涂层刀具材料、陶瓷材料、金刚石、立方氮化硼(CNB)。
17、涂层刀具材料:刀具既具有基体材料的强度和韧性,又具有很高的耐磨性18、陶瓷材料:主要用于钢、铸铁、高硬度材料及高精度零件的精加工。
教材习题参考答案(部分)

教材习题参考答案(部分)思考与练习题参考答案(部分)1-1 什么是⽣产过程、⼯艺过程、机械制造⼯艺过程?答:⽣产过程是根据设计信息将原材料和半成品转变为产品的过程。
⼯艺过程是在⽣产过程中,⽑坯的制造成形(如铸造、锻压、焊接等),零件的机械加⼯、热处理、表⾯处理,部件和产品的装配等是直接改变⽑坯的形状、尺⼨、相对位置和性能的过程,称为机械制造⼯艺过程,简称⼯艺过程。
采⽤合理有序安排的各种加⼯⽅法,逐步地改变⽑坯的形状、尺⼨和表⾯质量,使其成为合格零件的过程,称为机械加⼯⼯艺过程。
1-2 什么是⼯序、安装、⼯位、⼯步和⾛⼑?答:⼯序是指由⼀个⼈(或⼀组)⼯⼈在⼀个⼯作地点对⼀个(或同时对⼏个)⼯件连续完成的那⼀部分⼯艺过程;安装——⼯件(或装配单元)经⼀次装夹后所完成的那⼀部分⼯序。
⼯位——在⼀次⼯件的安装中,通过⼯作台的分度、移位可以使⼯件相对于机床变换加⼯位置,⼯件在每⼀个加⼯位置上所能完成的加⼯内容。
⼯步——在同⼀⼯位上,要完成不同的表⾯加⼯时,其中加⼯表⾯、⼑具、切削速度和进给量不变的情况下所完成的⼯位内容。
⾛⼑——⼑具在加⼯表⾯上切削⼀次所完成的⼯步内容。
1-3 什么是⽣产纲领、⽣产类型?答:企业根据市场需求和⾃⾝和⽣产能⼒决定的、在⼀年内应当⽣产的产品的产量和进度计划称为⽣产纲领。
企业(或车间、⼯段、班组,⼯作地)⽣产专业化程度的分类。
⼀般分为⼤量⽣产,成批⽣产和单件⽣产三种类型。
1-4 简述各种⽣产组织类型的特点。
答:单件⼩批⽣产时,其⽣产组织的特点是要能适应产品品种的灵活多变;中批⽣产时,采⽤通⽤设备与专⽤设备相结合,以保证其⽣产组织满⾜⼀定的灵活性和⽣产率的要求;⼤批⼤量⽣产时,⼴泛采⽤⾃动化专⽤设备,按⼯艺顺序流⽔线⽅式组织⽣产,⽣产组织形式的灵活性(即柔性)差。
1-5 简述机械制造过程的基本组成。
答:⾸先,组成机器的每⼀个零件要经过相应的⼯艺过程由⽑坯转变成为合格零件;其次,要根据机器的结构与技术要求,把某些零件装配成部件;最后,在⼀个基准零部件上,把各个零件、部件装配成完整的机器。
第2-7节工件材料的切削加工性

参考资料1:不锈钢的切削加工性
与45钢相比,1Cr18Ni9Ti不锈钢的相对可切削性约为0.3-.05之间,是一 种难切削材料。 其难加工性主要表现在: 高温强度和高温硬度高,一般钢材切削时,随着切削温度的升高其强度 会明显降低,切屑易被切离,而1Cr18Ni9Ti在700度时仍不能降低其机 械性能,故切屑不易被切离,切削过程中切削力大,刀具易磨损。 塑性和韧性高,虽然1Cr18Ni9Ti的抗拉强度和硬度都不高,但综合性能 很好,塑性和韧性高,它的延伸率、断面收缩率和冲击值都较高, 1Cr18Ni9Ti的延伸率是40%,是40#的210-237%,是45#的250-280%, 是20Cr、40Cr钢的400-500%,所以切屑不易切离、卷曲和折断,切屑 变形所消耗的功能增多,如切除一定体积的1Cr18Ni9Ti所消耗的能量比 切除相同体积的低碳钢约高50%,并且大部分能量转化为热能,使切削 温度升高。 由 于1Cr18Ni9Ti不易加工,切屑不易切离和折断,故刀具和工件之间所 产生的摩擦热也多,而不锈钢1Cr18Ni9Ti的导热率低(约为普通钢的1/21/3),散热差,由切屑带走的热量少。大部分的热量被刀具吸收,致使 刀具的温度升高,加剧刀具磨损。
2、工件材料化学成分的影响 (1)钢材的化学成分对切削加工性的影响
碳素钢的强度与硬度随含碳量的增加而提高,而塑性与韧性 随含碳量的增加而减小。低碳钢的塑性和韧性较高,又不易断 屑,因此切削加工性较差;高碳钢的强度和硬度较高,易使刀 具磨损,因此切削加工性较差;中碳钢的切削加工性较好。 在钢中加入铬、镍、钒、钼、钨、锰、硅、铝等合金元素可 以改变钢的切削加工性。
铁的加工性比冷硬铸铁好。
(3)以切屑控制或断屑的难易为衡量指标
在自动线上或自动机床上,常以切屑控制或断屑的难易程度 作为衡量材料切削加工性的指标。
刀具原理

一,1.在车外圆时,工件的回转运动属于_________,刀具沿工件轴线的纵向移动属于_________。
A 切削运动B 进给运动C 主运动D 加工运动2.车外圆时,车刀随四方刀架逆时针转动θ角后,工作主偏角κr将________,工作副偏角κr’将________。
A 增大减小B 减小增大C 增大不变D 不变不变3.积屑瘤发生在第________变形区,加工硬化发生在第________变形区。
A ⅠⅡB ⅠⅢC ⅡⅢD ⅢⅡ4.在加工条件相同时,用________刀具产生的切削力最小。
A 陶瓷刀具B 硬质合金刀具C 高速钢D 产生的切削力都一样5.下列哪种切屑屑形不属于可接受的屑形________。
A 带状切削B 短环形螺旋切削C 单元切削D 平盘旋状切屑6. 生产中常用的切削液,水溶性的切削液以________为主,油溶性切削液以________为主。
A 润滑冷却B 润滑润滑C 冷却润滑D 以上答案都不正确7.加工塑性材料、软材料时前角________;加工脆性材料、硬材料时前角________。
A 大些小些B 小些大些C 大些大些D 小些小些8 .高速钢刀具切削温度超过550~600时工具材料发生金相变化,使刀具迅速磨损,这种现象称为________磨损。
A 相变磨损B 磨粒磨损C 粘结磨损D 氧化磨损9.不能用于加工碳钢的是__________。
A 高速钢刀具B 陶瓷刀具C PCD刀具D CBN刀具10.主偏角、副偏角、刀尖角,三个角之和等于__________。
A 90°B 180°C 360°D 270°二、填空题(请将正确答案填写在横线上。
每空1分,共20分)1.切削用量三要素________________、_________________、_______________。
2.刀具材料种类繁多,当前使用的刀具材料分4类:________________,________________,________________,________________。
螺钉加工工艺

螺钉加工工艺轴类零件加工材料分析:材料为45号钢。
相对加工性为Kr=1刀材选用:初加工:YT5含Co高,抵抗冲击,增加刀具强度,方便初加工去除大的余量。
精加工:YT14含TiC高,耐磨,且能够达到较好的精度。
刀具参数:初加工:前角15°——18°,Kr=75°λs=0°———-5°增大刀头强度,提高刀具耐用度。
精加工:前角18°——20°,Kr=90°,λs=0——+5°保证工件表面质量,可用于车端面,外圆也可倒角热处理:调质组成表面:轴,端面,台阶,螺帽,外圆。
螺帽。
重要表面:M12.台阶直径16零件构型特点:细长轴,台阶面。
后方螺帽。
采用一夹一顶,螺帽用分度头铣。
当精加工时,采用3爪卡盘,夹住螺帽部分。
阶段划分:粗——半精——精拟定工艺加工路线:下料:棒料热处理:调质初加工:1,端夹,车左端面,外圆,台阶面,打中心孔,倒角。
2,掉头端夹,车有端面外圆保证达到外圆直径25.4,半精加工:1,车两台阶面。
2,用分度头铣床铣螺帽。
去毛刺。
中检精加工:1,一夹一顶磨台阶面和外圆。
2,一端装夹,采用3爪卡盘,小端面倒角,车螺纹终检零件图工部内容:设备:1下料:棒料2粗车:左端面,台阶打中心孔车床3粗车:掉头装夹,右端面,直径为25.4和16 车床的外圆和倒角4中检:热处理,调质5半精车:一夹一顶,直径为25.4和16的外圆车床6铣削:(分度头)螺帽去毛刺铣床7磨削:直径为16的外圆,台阶面磨床8车削:(掉头)一端夹,直径为12的外圆,倒角(左)去毛刺,车螺纹车床9终检转眼间,这次的毕业设计已经接近尾声了。
在老师的指导下,我收获很多。
通过此次设计,使我基本掌握了零件的加工过程分析、工艺文件的编制、机床的选择等。
学会了查相关手册、选择使用工艺装备等等,加深了我对理论知识的理解。
在这次设计过程中,我也看到自己的不足之处,以前上课没有学到的知识,在这次设计当中也涉及到了,使我真正感受到了知识的重要性。
机械制造技术基础真题加解析完整版

2014机械制造技术基础真题完整版一. 判断题(1'×35)。
1.切削铸铁时,切削速度对切削力影响较大。
2.机夹转位刀具的寿命可以制定的短些。
3.粗加工时选择切削用量首先应考虑加大背吃刀量。
4.切削塑性材料时垂直于切削面方向切削温度变化很大。
5.机床型号第一个字母为Y,表示它是螺纹加工机床。
6.以VB作为磨钝标准时,适当加大后角有助于刀具寿命的提高。
7.切削层参数是在切削平面内度量的。
8.切削塑性材料时,变形系数是大于1的。
9.在车床切断工件时,切断刀的工作后角会小于标注后角。
10.工件材料相同时,刀具几何参数不同,单位切削力也不同。
11.刀具刃口的负倒棱是在其后刀面磨出的。
12.切削塑性材料时,切削角大,说明变形程度亦大。
13.直角自由切削时,刀具的刃倾角并不等于零。
14.硬质合金刀具切削塑性材料时,后刀面的磨损形态呈月牙洼形。
15.刀具寿命曲线的m值越大,说明切削速度对刀具寿命的影响大。
16.磨削滚动轴承比磨削45钢更易产生磨削烧伤现象。
17.切削加工中,通常材料的韧性越大,工件加工表面的粗糙度值越小。
18.磨削加工中,大部分的磨削热量通过切屑和冷却液带走。
19.车外圆时,三爪卡盘的中心与车床主轴回转轴线存在的偏心主要影响工件的同轴度。
20.在外圆磨床上磨削工件轴时常采用死顶尖,其目的是使工件的圆柱度不受机床主轴回转误差的影响。
21.平面磨床机床导轨在水平和垂直面内的直线度要求应该同样高。
22.在卧式机床上用顶尖定位进行轴类零件的外圆面车削时,若前后顶尖的连线与刀尖运动轨迹在水平面内存在平行度误差,则工件上将产生中凹形误差。
23.采用拉刀拉孔可以纠正工件上前道工序留下的孔轴线相对于端面的垂直度误差。
24.零件加工时,有时候按照“基准统一原则”选择精基准,采用该原则可以避免基准多次转化,提高工件的形状精度。
25.选择粗基准时,为保证工件上加工面与不加工面之间的位置精度要求,应选择该加工表面作为粗基准。
工件材料切削加工相对性指标初探

母 等 。2 r3 C l 不锈钢加工时塑性变形 大 , 加 硬化 重 , 因此 切 削 力 较 大 。 切 削 不 锈 钢 时 的相 对切 削 力 为 06 , 削 力 比 切 削 4 钢 时 大很 多 。 行 , 的 .0 切 5 它 削 温度 高 , 刀具 磨 损 严 重 ; 屑 不易 卷 r 和 折断 , 损 切 l / : l 会 伤 I加 丁表 面 , 响 表 面 质量 ; ill = _ ! . 影 切  ̄Dl ' : t 较兹, 比较 难加 T 。 铝合 金是现代工业用途最广 的轻金属材料 , 广泛 用 于 飞机 、 表 、 仪 发动 机 、 机械 制造 、 T等部 门 。 m于 化 铝 合 金强 度 和硬 度较 低 , 因此 切 削加 . }切 }力较 小 1I l 、 i f I j . 从 试 验结 果 看 出 , 削锅 合 金 时切 削 力 比 切削 4 铡 , 切 5 J 、 很 多 , 次 切 削 实 验 中 切 削 铝 合 金 时 的 牛 对 切 削 力 本 H 为~ . , 削 力最 小 。再 者 , 合 金 的 导热 率 较 高 , 06 切 9 钒 因此切 削温度 较 低 , 于 易切 削材 料 。 属 灰 铸铁 的组织 是 金属 基体 加 游 离的 行 。7 的 了
切 削力的 大小 。通过试验测 量 出一组切 削力数据 , 计算 出加 工几种 常用材料 时的相对切 削力 , 对其切 削加工性进 并
行 了 分 析 讨 论
【 关键词 】 相对切 削力; 削加.性 ; 切 Y 车削 -
【 中图分类号】 T 56 G 0
0 引 言
【 文献标识码】 A
标 有 很 多 , 中切 削力 是 衡 量 工件 材 料 切 削 加工 性 的 其
重要 指 标 之一 。切 削 力越 大 , 削加 工 性 越 差 。切 削 切
金属切削选择题
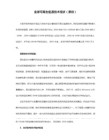
17. (C) 上离切削刃有一定距离处的温度最高,该处扩散作用最强烈,于是在该处形成月牙洼。
A.后刀面 B.副后刀面 C.前刀面 D.基面
18.氧化磨损最容易在 ( D ) 的工作边界处形成。
A.前、后刀面 B.主切削刃、前刀面 C.前、副后刀面 D.主、副切削刃
A.低碳钢 B.中碳钢 C.铸铁件 D.马氏体不锈钢
57.加工 ( B ) ,应选用硬度高、有一定韧性、导热系数大,高温性能好的刀具材料。
A.高强度钢 B.高锰钢 C.冷硬铸铁 D.纯金属
A.高、小 B.低、小 C.高、大 D.低、大
43.对于( C ) 切削的刀具,磨料磨损是磨损的主要原因。
A.高速 B.中速 C.低速 D.中低速
44.在 (B) 刀具正常工作的切削速度和硬质合金刀具偏低的切削速度下,就能满足产生冷焊的条件。
A.切削速度,切削深度,进给量 B.进给量,切削速度,切削深度
C.切削速度,进给量,切削深度 D.切削深度,进给量,切削速度
26.最大生产率使用寿命是指根据 ( B) 的原则来确定刀具使用寿命。
A.单件工序成本最低 B.单件工序工时最短
选择题
1.刀具几何参数对切削温度的影响因素有:前角、( B ) 、负倒棱、刀尖圆弧半径。
A.后角 B.主偏角 C.楔角 D.刃倾角
2.在切削用量中,影响刀具使用寿命最主要的因素是 ( C) 。
A.切削深度 B.进给量 C.切削速度 D.进给速度
A.前部 B.中部 C.后部 D.前中部
51.切削用量三要素对刀具使用寿命的影响由小到大依次为(C )
A.切削速度,切削深度,进给量 B.进给量,切削速度,切削深度
工件材料的切削加工性

第一节工件材料的切削加工性材料的切削加工性是指对某种材料进行切削加工的难易程度。
1.衡量切削加工性的指标切削加工性的指标可以用刀具使用寿命、一定寿命的切削速度、切削力、切削温度、已加工表面质量以及断屑的难易程度等衡量。
某种材料切削加工性的好坏,是相对另一种材料而言的。
因此,切削加工性是具有相对性的。
一般以切削正火状态45钢的v60作为基准,其它材料与其比较,用相对加工性指标Kr表示:(3-1)式中,v60——某种材料其刀具使用寿命为60min时的切削速度;(v60) j——切削45钢,刀具使用寿命为60min时的切削速度。
二。
影响材料切削加工性的主要因素影响材料切削加工性的主要因素有材料的物理力学性能、化学成分和金相组织等。
三。
难加工材料的切削加工性(一)、高锰钢的切削加工性高锰钢加工硬化严重,塑性变形会使奥氏体组织变为细晶粒的马氏体组织,硬度急剧增加,造成切削困难。
高锰钢热导率低,仅为45钢的1/4,切削温度高,刀具易磨损,高锰钢韧度大,约为45钢的8倍,其伸长率也大,变性严重,导致切削力增加,并且不易断屑。
(二)不锈钢的切削加工性奥氏体不锈钢中的铬、镍含量较大,铬能提高不锈钢的强度及韧性,但使加工硬化严重,易粘刀。
不锈钢切屑与前刀面结出长度较短,刀尖附近应力较大,经计算刀尖所收的应力为切削碳钢的1.3倍,造成刀尖易产生塑性变形或崩刀。
奥氏体不锈钢导热性差,切削温度高。
另外,锯齿形切屑并不因速度增高而有所改变,所以切削波动大,易产生振动,使刀具破损。
断屑问题也是不锈钢车削中的突出问题。
车削不锈钢时,多采用韧性好的YG类硬质合金刀片,选择较大的前角和小的主偏角;较低的切削速度,较大的进给量和背吃刀量。
四、改善材料切削加工性的基本方法1.在材料中适当添加化学元素??? 在钢材中添加适量的硫、铅等元素,能够破坏铁素体的连续性,降低材料的塑性,使切削轻快,切屑容易折断,大大地改善材料的切削加工性。
在铸铁中加入合金元素铝、铜等能分解出石墨元素,利于切削。
相对加工性

本章主要介绍切削加工性、表面粗糙度和切削液的基本概念;改善切削加工性、降低已加工表面粗糙度和选用切削液的基本规律。
【目的要求】1、明确基本概念;2、会根据加工具体情况正确选择改善切削加工性、降低已加工表面粗糙度和选用切削液;【本章内容】第一次课§5-1工件材料和切削的加工性本章从工工件材料方面本分析影响生产率及表面质量的因素,以及提高它们的途径:从生产实际中了解到,有些材料容易切削(生产率高,表面质量好),而另一些材料却很切削;分析工件材料的机械物理性能以及化学成分如何影响切削加性,如何提高工件材料的切削加工性。
材料的切削加工性是指导某种材料进行切削加工性的难易程度,其易程度,一般与材料的化学成份,热处理状态﹑金相组织﹑物理力学性能以及切削条件有关。
一﹑衡量切削加工的指标工件材料的切削加工性,通常用下面的一个或数个指标衡量:1 ﹑刀具耐用度;2﹑一定刀具耐用度允许的切削速度;3﹑切削力;4﹑切削温度;5﹑加工表面粗糙度或表面质量。
目前,常用一定刀具耐用度下充许的切削速度v T作为衡量指标。
v T__-指刀具耐用度为T时,切削某种材料的允许的切削速度。
v T越高,说明该材料的切削加工性能好。
任何事情都是相对而言,那么对于材料的切削加工性,也要用相对加工性Kr 表示。
它的基准是以切削抗拉强度&b = 0.735Gpa的45#钢,耐用度T=60min时的切削速度Vb60为基准。
相对加工性就是以该基准与切削其它材料时V60的比值。
即①当Kr>1时,说明该材料比45﹟钢难切削;切削加工性好;②当Kr<1时,该材料比45﹟钢难切削,切削加工性能差。
常用材料切削加工性,根据相对加工性Kr的大小切分为八级,见表5—1。
二﹑改善材料可切削性的途经1﹑改善材料的化学成份。
1*在黄铜中加入1%~3%的铅,在钢中加入0.1%~0.25%的铅。
铅可以球状粒子存在于材料的金相组织中,切削时能起很好润滑作用,减少摩擦,使刀具耐用度和表面质量得提高。
机械制造基础英文词汇附表-总2
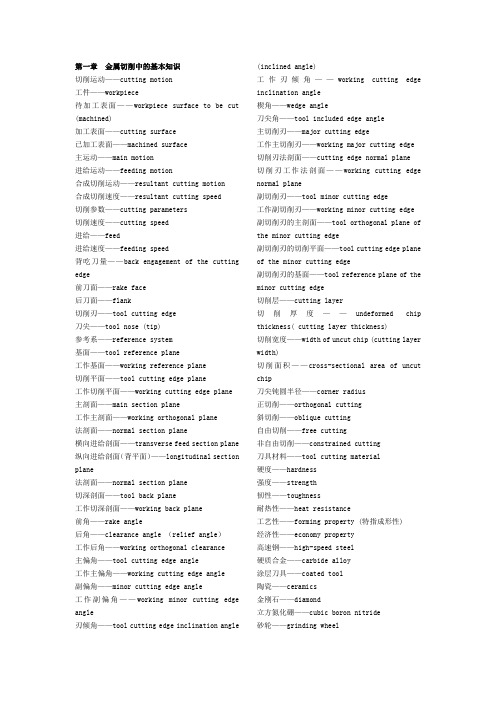
第一章金属切削中的基本知识切削运动——cutting motion工件——workpiece待加工表面——workpiece surface to be cut (machined)加工表面——cutting surface已加工表面——machined surface主运动——main motion进给运动——feeding motion合成切削运动——resultant cutting motion合成切削速度——resultant cutting speed切削参数——cutting parameters切削速度——cutting speed进给——feed进给速度——feeding speed背吃刀量——back engagement of the cutting edge前刀面——rake face后刀面——flank切削刃——tool cutting edge刀尖——tool nose (tip)参考系——reference system基面——tool reference plane工作基面——working reference plane切削平面——tool cutting edge plane工作切削平面——working cutting edge plane 主剖面——main section plane工作主剖面——working orthogonal plane法剖面——normal section plane横向进给剖面——transverse feed section plane 纵向进给剖面(背平面)——longitudinal section plane法剖面——normal section plane切深剖面——tool back plane工作切深剖面——working back plane前角——rake angle后角——clearance angle (relief angle)工作后角——working orthogonal clearance主偏角——tool cutting edge angle工作主偏角——working cutting edge angle副偏角——minor cutting edge angle工作副偏角——working minor cutting edge angle刃倾角——tool cutting edge inclination angle (inclined angle)工作刃倾角——working cutting edge inclination angle楔角——wedge angle刀尖角——tool included edge angle主切削刃——major cutting edge工作主切削刃——working major cutting edge 切削刃法剖面——cutting edge normal plane切削刃工作法剖面——working cutting edge normal plane副切削刃——tool minor cutting edge工作副切削刃——working minor cutting edge 副切削刃的主剖面——tool orthogonal plane of the minor cutting edge副切削刃的切削平面——tool cutting edge plane of the minor cutting edge副切削刃的基面——tool reference plane of the minor cutting edge切削层——cutting layer切削厚度——undeformed chip thickness( cutting layer thickness)切削宽度——width of uncut chip (cutting layer width)切削面积——cross-sectional area of uncut chip刀尖钝圆半径——corner radius正切削——orthogonal cutting斜切削——oblique cutting自由切削——free cutting非自由切削——constrained cutting刀具材料——tool cutting material硬度——hardness强度——strength韧性——toughness耐热性——heat resistance工艺性——forming property (特指成形性)经济性——economy property高速钢——high-speed steel硬质合金——carbide alloy涂层刀具——coated tool陶瓷——ceramics金刚石——diamond立方氮化硼——cubic boron nitride砂轮——grinding wheel磨料——abrasive material粒度——grain size油酸——oleic acid松脂——turpentine酚醛树脂——phenolic resin虫胶——shellac树脂——resinoid粘结剂——bond material气孔——porosity第二章金属切削过程中的基本规律及应用切削变形——cutting deformation带状切屑——ribbon chip挤裂切屑——cracked chip单元切屑——unit chip崩碎切屑——splintering chip相对滑移—— relative slide变形系数——deformation coefficient剪切屈服点——shear yielding point剪切角——angle of the shear plane积屑瘤——built-up edge切削合力——resultant tool force轴向进给抗力——axial thrust force径向切深抗力——radial thrust force主切削力——main cutting force水平分力——thrust component of the result tool force切削扭矩——cutting torque单位切削力——specific cutting force切削功率——power required to perform the machining operation单位切削功率——specific cutting power切削热——heat in metal cutting导热系数——thermal conductivity切削温度——machining temperature刀具磨损——tool wear正常磨损——normal wear磨粒磨损——abrasive wear粘结磨损——adhesive wear扩散磨损——diffusion wear相变磨损——phrase change wear氧化磨损——oxidized wear刀具耐用度——tool life月牙洼磨损深度——crate depth 经济耐用度——tool life for the minimum production cost最大生产率耐用度——tool life for the maximum production efficient换刀时间——tool-changing time切削时间——machining time工序工时——operation time单位时间内的金属切除量——metal-removal rate 一定耐用度下的切削速度——cutting speed giving a tool life of T辅助工时——nonproductive time加工性——machinability相对加工性——relative machinability切削液——cutting fluid第三章机械加工工艺基础知识技术条件——specification生产过程——manufacturing process零件加工工艺——process of a part工序——operation走刀——cutting pass安装——set up工位——operation position定位——location定位元件——location element圆柱支承钉——cylindrical support post支承板——support plate圆柱形定位销——cylindrical location pin削角销——rhombic pin定位心轴——location centeringV形块——V-shaped block楔块——wedge定位误差——location error公差——tolerance夹紧力——clamping force夹紧力方向——clamping direction夹紧力作用点——clamping position轨迹法——track machining method成形法——form machining method相切法——tangential machining method展成法——generating process method工艺规程——process route工艺过程卡——process sheet生产纲领——production expectation基准重合原则——principle of coincident locating surfaces夹具——fixture/jig千分尺——micrometer基准面——reference surface自由度——degree of freedom加工余量——allowance (material removal)表面粗糙度——surface roughness调质处理——quality treatment废品率——reject rates尺寸链——dimensional chain封闭环——resultant dimension组成环——component dimension增环——plus dimension减环——minus dimension极值法——extremum method上偏差——upper deviation下偏差——lower deviation概率法——probability method算术平均值——average arithmetic value相对分布系数——relative distribution coefficient 时间定额——time ration临界产量——critical output投资回收期——invest reclaim period第四章回转体零件加工工艺与装备机床——machine tool车床——lathe铣床——milling machine刨床——planer牛头刨床——shaping machine龙门刨床——planing machine镗床——boring machine钻床——drilling machine螺纹机床——screw thread machine拉床——broaching machine锯床——saw machine磨床——grinding machine普通车床——engine lathe落地车床——ground lathe立式车床——vertical lathe转塔(六角)车床——turret lathe多刀半自动车床——Semi-automatic lathe 仿形车床及仿形半自动车床——profiling lathe单轴自动车床——single-axis automatic lathe多轴自动车床——multi-axis automatic lathe多轴半自动车床——multi-axis semi automatic lathe 专门化车床——special-purpose lathe数控车床——CNC lathe立式——vertical摇臂——radial深孔——deep hole drills主轴箱——headstock刀架——tool post进给箱——feed-box溜板箱——apron尾座——tailstock床身——bed卡盘——chuck立柱——column工作台——worktable滑鞍——saddle光杆——feed rod丝杆——lead screw刀杆——tool arbor砂带磨削——belt grinding缓进磨削——creep-feed grinding横向进给磨削——plunge feed每齿进给量——feed per tooth扩孔core drilling钻台阶孔——step drilling锪孔——counter boring铰孔——reaming钻中心孔——center drilling深孔钻——gun drilling鞍形支座——saddle support镗杆端部支撑轴承——end support bearing for boring bar坐标镗床——jig boring machine金刚镗床——diamond boring machine麻花钻——twist drill直刃钻——straight-flute drill阶梯钻——step drill扁钻——spade drill枪钻——gun drill铰刀——reamer镗刀——boring tool平面——plane槽——groove螺旋面——spiral surface曲面——curved surfaces主轴——spindle刀轴——arbor横梁——transverse column吊架——cantilever纵向工作台——longitudinal table横向工作台——transverse table升降台——lift table圆柱铣——slab milling周铣——slab milling立铣——face milling端铣——end milling工艺——process烧结——agglomeration注塑——infusing气动夹具——pneumatic fixture液压夹具——hydraulic fixture电动夹具——electric fixture电磁夹具——electromagnetic fixture真空夹具——vacuum fixture自紧夹具——self-clamping fixture螺纹——screw thread齿轮——gear差分传动链——difference chain蜗杆——worm小齿轮——pinion刨齿——gear shaping花键孔——splined hole第5章非回转体加工工艺与装备铣削——milling周铣(周边铣削,圆柱铣削)——peripheral milling 端铣(端面铣削)——face milling立铣——end milling平面铣削——slab milling顺铣——down milling, climb milling逆铣——up milling, conventional milling铣刀——milling cutter, milling tool圆柱铣刀——peripheral cutter, cylindrical cutter端面铣刀——face mill, face cutter立铣刀,指铣刀——end mill 组合铣刀(三面刃铣刀)——face and side cutter 尖齿铣刀——pointed tool, pointed cutter铲齿铣刀——relieving tool, relieving cutter成形铣刀——formed cutter铣床——milling machine, miller万能卧式升降台铣床——horizontalknee-and-column type milling machine立式单轴铣床——vertical single spindle milling machine落地铣床——floor type milling machine龙门铣床——planer-type milling machine工具铣床——tool milling machine仿形铣床——profile milling machine, duplicating milling machine牛头刨上刨削——shaping龙门刨上刨削——planing插削——slotting刨刀——planer tool插刀——slotting tool牛头刨床——shaper龙门刨床——planning machine, planer插床——slotting machine, slotter拉削——broaching拉刀——broach拉床——broaching machine磨削——grinding砂轮——grinding wheel, abrasive wheel, emery wheel油石——abrasive stick周边磨削——peripheral grinding平面磨削——face grinding成形磨削——form grinding磨床——grinder光学曲线磨床——optical contour grinder, optical curve grinding machine夹具——fixture偏心轮—eccentric wheel电磁吸盘——electro magnetic chuck虎钳——vice连杆——link rod, connecting rod机架——chassis, frame台阶轴——stepped shaft曲轴——crank shaft花键轴——spline shaft摩擦轮——friction pulley, friction wheel键槽——key slot, key seat, key way, key groove燕尾槽——dovetail groove链轮——chain wheel, sprocket棘轮——ratchet wheel第六章机械加工精度加工精度——machining accuracy加工误差——machining error工艺系统——processing system原始误差——original errors静态加工误差——static processing error动态加工误差——dynamic processing error加工原理误差——Principle error调整误差——Adjustment error主轴回转误差——spindle rotational error导轨误差——guideway error传动链误差——transmission error静态刚度——static stiffness工艺系统的热变形——thermal deformation of the processing system系统误差——system error随机误差——random error分布曲线法——method of error distribution curve正态分布曲线——normal distribution graph误差补偿法——error compensation误差分组法——error grouping误差转移法——Error transforming“就地加工”法——Machining on spot误差平均法——error average method控制误差法——error controlling method第七章机械加工表面质量表面波纹度——surface waviness金相组织变化——metallurgical structure change残余应力——Residual stress疲劳强度——fatigue strength应力集中——stress concentration冷作硬化——work-hardening抗腐蚀——anti-erosion砂轮的修整——dressing of grinding wheel金相组织——metallurgical structure 回火烧伤——tempering burn淬火烧伤——quenching burn退火烧伤——annealing burn热态塑性变形——hot plastic deformation冷态塑性变形——cold plastic deformation金相组织的变化——variation of metallurgical structure磨削裂纹——grinding crack冷作硬化——work cold hardening喷丸——shot peening滚压——press rolling强迫振动——forced vibration自激振动——self-excited vibration。
金属切削机床与刀具模拟试题必考
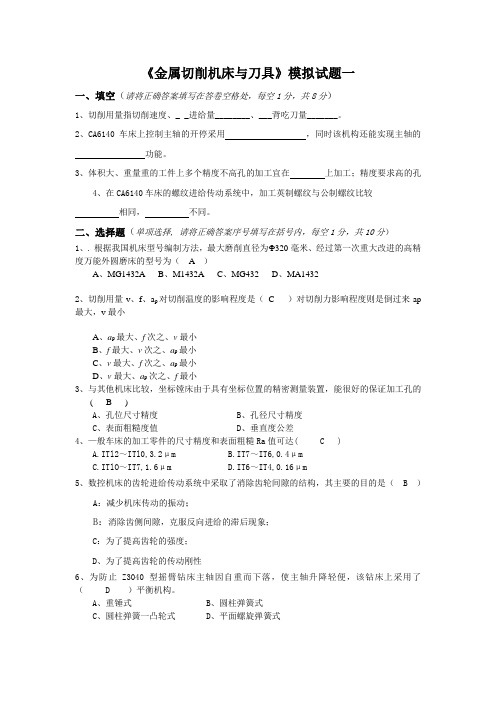
《金属切削机床与刀具》模拟试题一一、填空(请将正确答案填写在答卷空格处,每空1分,共8分)1、切削用量指切削速度、_ _进给量________、___背吃刀量_______。
2、CA6140车床上控制主轴的开停采用,同时该机构还能实现主轴的功能。
3、体积大、重量重的工件上多个精度不高孔的加工宜在上加工;精度要求高的孔4、在CA6140车床的螺纹进给传动系统中,加工英制螺纹与公制螺纹比较相同,不同。
二、选择题(单项选择, 请将正确答案序号填写在括号内,每空1分,共10分)1、. 根据我国机床型号编制方法,最大磨削直径为 320毫米、经过第一次重大改进的高精度万能外圆磨床的型号为( A )A、MG1432AB、M1432AC、MG432D、MA14322、切削用量v、f、a p对切削温度的影响程度是(C )对切削力影响程度则是倒过来ap 最大,v最小A、a p最大、f次之、v最小B、f最大、v次之、a p最小C、v最大、f次之、a p最小D、v最大、a p次之、f最小3、与其他机床比较,坐标镗床由于具有坐标位置的精密测量装置,能很好的保证加工孔的( B )A、孔位尺寸精度B、孔径尺寸精度C、表面粗糙度值D、垂直度公差4、—般车床的加工零件的尺寸精度和表面粗糙Ra值可达( C )A.ITl2~ITl0,3.2μmB.IT7~IT6,0.4μmC.ITlO~IT7,1.6μmD.IT6~IT4,0.16μm5、数控机床的齿轮进给传动系统中采取了消除齿轮间隙的结构,其主要的目的是( B )A:减少机床传动的振动;B:消除齿侧间隙,克服反向进给的滞后现象;C:为了提高齿轮的强度;D、为了提高齿轮的传动刚性6、为防止Z3040型摇臂钻床主轴因自重而下落,使主轴升降轻便,该钻床上采用了( D )平衡机构。
A、重锤式B、圆柱弹簧式C、圆柱弹簧一凸轮式D、平面螺旋弹簧式7、标准齿轮滚刀采用阿基米德滚刀原因是( B )A 、理论要求这种滚刀B 、便于制造和测量其齿形C 、可以减少加工齿面的粗糙度D 、修正齿形误差8、蝶型砂轮磨齿机是利用( C )原理来进行磨齿的。
机械制造基础名词解释简答题分析题
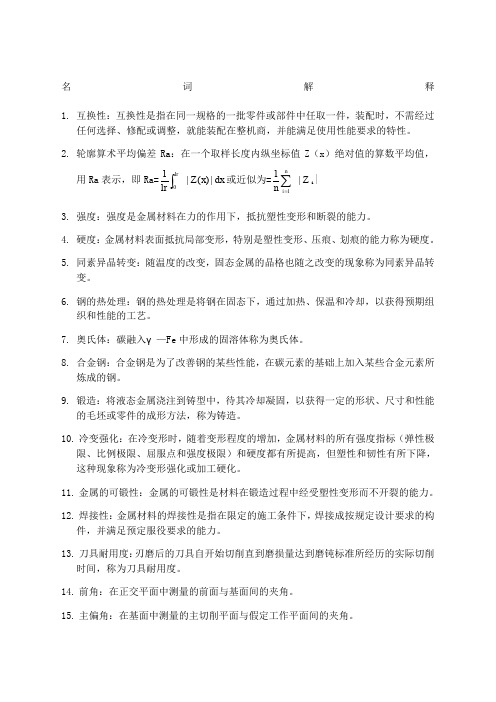
名词解释1. 互换性:互换性是指在同一规格的一批零件或部件中任取一件,装配时,不需经过任何选择、修配或调整,就能装配在整机商,并能满足使用性能要求的特性。
2. 轮廓算术平均偏差Ra :在一个取样长度内纵坐标值Z (x )绝对值的算数平均值,用Ra 表示,即Ra=dx x Z lr lr |)(|10⎰或近似为=Z n n i |11∑=i | 3. 强度:强度是金属材料在力的作用下,抵抗塑性变形和断裂的能力。
4. 硬度:金属材料表面抵抗局部变形,特别是塑性变形、压痕、划痕的能力称为硬度。
5. 同素异晶转变:随温度的改变,固态金属的晶格也随之改变的现象称为同素异晶转变。
6. 钢的热处理:钢的热处理是将钢在固态下,通过加热、保温和冷却,以获得预期组织和性能的工艺。
7. 奥氏体:碳融入γ—Fe 中形成的固溶体称为奥氏体。
8. 合金钢:合金钢是为了改善钢的某些性能,在碳元素的基础上加入某些合金元素所炼成的钢。
9. 锻造:将液态金属浇注到铸型中,待其冷却凝固,以获得一定的形状、尺寸和性能的毛坯或零件的成形方法,称为铸造。
10. 冷变强化:在冷变形时,随着变形程度的增加,金属材料的所有强度指标(弹性极限、比例极限、屈服点和强度极限)和硬度都有所提高,但塑性和韧性有所下降,这种现象称为冷变形强化或加工硬化。
11. 金属的可锻性:金属的可锻性是材料在锻造过程中经受塑性变形而不开裂的能力。
12. 焊接性:金属材料的焊接性是指在限定的施工条件下,焊接成按规定设计要求的构件,并满足预定服役要求的能力。
13. 刀具耐用度:刃磨后的刀具自开始切削直到磨损量达到磨钝标准所经历的实际切削时间,称为刀具耐用度。
14. 前角:在正交平面中测量的前面与基面间的夹角。
15. 主偏角:在基面中测量的主切削平面与假定工作平面间的夹角。
16.工艺过程:生产过程中,直接改变原材料(或毛坯)的形状、尺寸或性能,使之变为成品的过程,称为工艺过程。
2013机械制造技术基础真题加解析(完整版)

9.错误。 书中原话,其次是切削速度。
10.正确. 书中原话,一般情况下,多采用最低成本耐用度。
11.错误。 书中原话,内控镗削时,装刀高低对工作角度的影响是与外圆车削相反的。
5.A.切削用量三要素对切削力影响程度的大小的排序为a-f-v;对切削热影响程度的排列顺序依次为a-v-f;对切削温度影响程度的大小的排序为v-f-a.
6.B.精加工时切削厚度很小,磨损主要发生在后刀面上,宜取较大后角;粗加工时切削厚度较大,前刀面磨损加大,宜取较小后角,以利于增强刀刃和散热。
7.B.受进给运动影响,实际的切削平面和基面都要偏转一个附加的螺旋升角,使工作的前角增大,后角减小。
12.正确。 书中原话,假如改变挤裂切屑的条件,如进一步减小刀具前角,降低切削速度,加大切削厚度,就可以得到单元切屑,反之,则可以得到带状切屑。
13.错误。 书中原话,顺铣容易窜动并打刀,逆铣容易振动。两者都会加剧刀具的磨损,生产中多选用逆铣。
14.错误。 书中原话,后角是在正交平面内测量的主后刀面与切削平面之间的夹角。
八、合格率计算分析题(16分)
用钻头加工一批零件,共300个,工序尺寸公差18-0.08—18+0.09,加工后尺寸为17.96mm,标准差0.02 (1)计算合格品数,不合格品率以及可修复不合格品数(2)计算工艺能力指数(3)该工艺中存在哪些误差,分析其原因,并怎样改进措施?(4)分析哪些是属于常值系统误差,哪些是变值系统误差,哪些是随机误差,分析其原因?(16分)
答案解析
一.判断题
1.正确。 书中原话,切削主运动一个,进给运动可以多个。例如车削时车刀的纵向或横向运动,磨削外圆时工件的旋转运动和工作台带动工件的纵向移动等。
切削刀具期末复习的题目
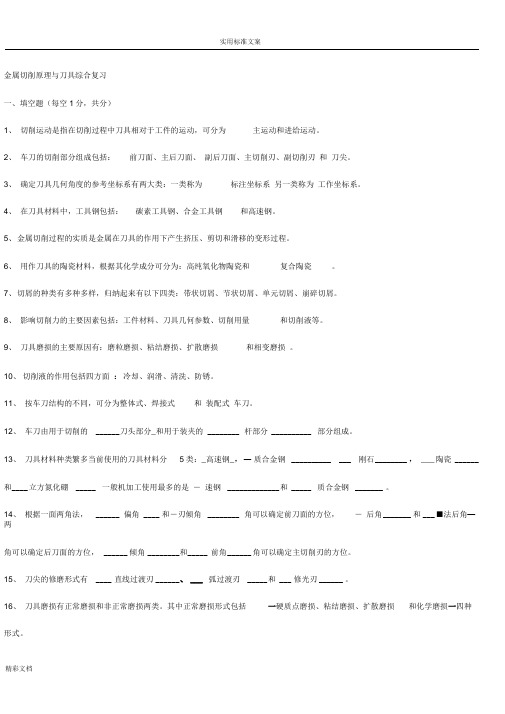
金属切削原理与刀具综合复习一、填空题(每空1分,共分)1、切削运动是指在切削过程中刀具相对于工件的运动,可分为主运动和进给运动。
2、车刀的切削部分组成包括:前刀面、主后刀面、副后刀面、主切削刃、副切削刃和刀尖。
3、确定刀具几何角度的参考坐标系有两大类:一类称为标注坐标系另一类称为工作坐标系。
4、在刀具材料中,工具钢包括:碳素工具钢、合金工具钢和高速钢。
5、金属切削过程的实质是金属在刀具的作用下产生挤压、剪切和滑移的变形过程。
6、用作刀具的陶瓷材料,根据其化学成分可分为:高纯氧化物陶瓷和复合陶瓷。
7、切屑的种类有多种多样,归纳起来有以下四类:带状切屑、节状切屑、单元切屑、崩碎切屑。
8、影响切削力的主要因素包括:工件材料、刀具几何参数、切削用量和切削液等。
9、刀具磨损的主要原因有:磨粒磨损、粘结磨损、扩散磨损和相变磨损。
10、切削液的作用包括四方面:冷却、润滑、清洗、防锈。
11、按车刀结构的不同,可分为整体式、焊接式和装配式车刀。
12、车刀由用于切削的 ______ 刀头部分_和用于装夹的________ 杆部分 __________ 部分组成。
13、刀具材料种类繁多当前使用的刀具材料分5类:_高速钢_,― 质合金钢__________ ___ 刚石________ ,___ 陶瓷 ______ 和____ 立方氮化硼 _____ 一般机加工使用最多的是― 速钢_____________ 和 _____ 质合金钢_______ 。
14、根据一面两角法, ______ 偏角____ 和―刃倾角________ 角可以确定前刀面的方位,― 后角_______ 和___ ■法后角—两角可以确定后刀面的方位,______ 倾角________ 和_____ 前角______ 角可以确定主切削刃的方位。
15、刀尖的修磨形式有 ____ 直线过渡刃______ 、___ 弧过渡刃 _____ 和 ___ 修光刃______ 。
切削基础知识
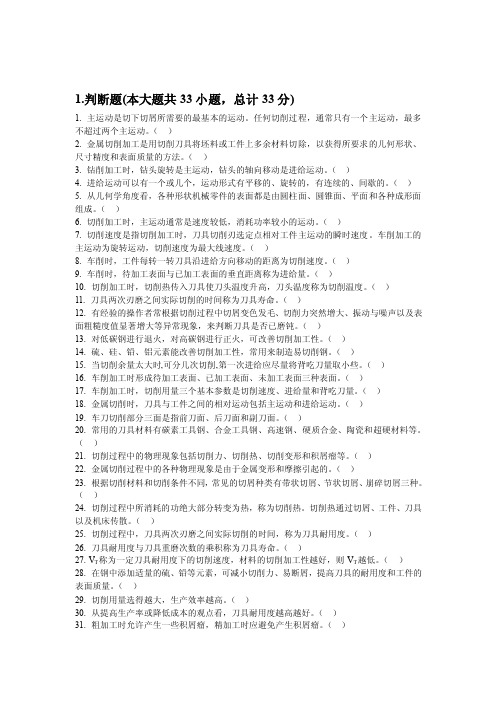
1.判断题(本大题共33小题,总计33分)1. 主运动是切下切屑所需要的最基本的运动。
任何切削过程,通常只有一个主运动,最多不超过两个主运动。
()2. 金属切削加工是用切削刀具将坯料或工件上多余材料切除,以获得所要求的几何形状、尺寸精度和表面质量的方法。
()3. 钻削加工时,钻头旋转是主运动,钻头的轴向移动是进给运动。
()4. 进给运动可以有一个或几个,运动形式有平移的、旋转的,有连续的、间歇的。
()5. 从几何学角度看,各种形状机械零件的表面都是由圆柱面、圆锥面、平面和各种成形面组成。
()6. 切削加工时,主运动通常是速度较低,消耗功率较小的运动。
()7. 切削速度是指切削加工时,刀具切削刃选定点相对工件主运动的瞬时速度。
车削加工的主运动为旋转运动,切削速度为最大线速度。
()8. 车削时,工件每转一转刀具沿进给方向移动的距离为切削速度。
()9. 车削时,待加工表面与已加工表面的垂直距离称为进给量。
()10. 切削加工时,切削热传入刀具使刀头温度升高,刀头温度称为切削温度。
()11. 刀具两次刃磨之间实际切削的时间称为刀具寿命。
()12. 有经验的操作者常根据切削过程中切屑变色发毛、切削力突然增大、振动与噪声以及表面粗糙度值显著增大等异常现象,来判断刀具是否已磨钝。
()13. 对低碳钢进行退火,对高碳钢进行正火,可改善切削加工性。
()14. 硫、硅、铅、铝元素能改善切削加工性,常用来制造易切削钢。
()15. 当切削余量太大时,可分几次切削,第一次进给应尽量将背吃刀量取小些。
()16. 车削加工时形成待加工表面、已加工表面、未加工表面三种表面。
()17. 车削加工时,切削用量三个基本参数是切削速度、进给量和背吃刀量。
()18. 金属切削时,刀具与工件之间的相对运动包括主运动和进给运动。
()19. 车刀切削部分三面是指前刀面、后刀面和副刀面。
()20. 常用的刀具材料有碳素工具钢、合金工具钢、高速钢、硬质合金、陶瓷和超硬材料等。
316l不锈钢标号
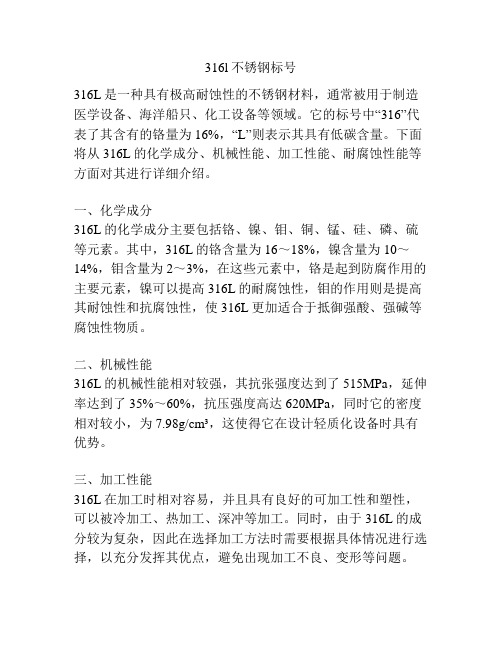
316l不锈钢标号316L是一种具有极高耐蚀性的不锈钢材料,通常被用于制造医学设备、海洋船只、化工设备等领域。
它的标号中“316”代表了其含有的铬量为16%,“L”则表示其具有低碳含量。
下面将从316L的化学成分、机械性能、加工性能、耐腐蚀性能等方面对其进行详细介绍。
一、化学成分316L的化学成分主要包括铬、镍、钼、铜、锰、硅、磷、硫等元素。
其中,316L的铬含量为16~18%,镍含量为10~14%,钼含量为2~3%,在这些元素中,铬是起到防腐作用的主要元素,镍可以提高316L的耐腐蚀性,钼的作用则是提高其耐蚀性和抗腐蚀性,使316L更加适合于抵御强酸、强碱等腐蚀性物质。
二、机械性能316L的机械性能相对较强,其抗张强度达到了515MPa,延伸率达到了35%~60%,抗压强度高达620MPa,同时它的密度相对较小,为7.98g/cm³,这使得它在设计轻质化设备时具有优势。
三、加工性能316L在加工时相对容易,并且具有良好的可加工性和塑性,可以被冷加工、热加工、深冲等加工。
同时,由于316L的成分较为复杂,因此在选择加工方法时需要根据具体情况进行选择,以充分发挥其优点,避免出现加工不良、变形等问题。
四、耐腐蚀性能316L的耐腐蚀性非常优异,它具有极强的抵抗海水腐蚀、氯化物腐蚀等性能,同时在酸、碱性环境中也具备出色的抗腐蚀能力。
另外,316L还具有热疲劳极限高、抗氧化以及耐磨损性强等突出优点,这使得它成为了医疗设备、海洋船舶、化工设备等领域的首选材料。
综上所述,316L作为一种具备优越抗腐蚀、高机械性能的不锈钢材料,在各个领域都有着广泛的应用价值。
而随着新材料、新工艺的不断涌现,316L的应用领域也将不断拓宽和深化,有望在未来的发展中展现更广阔的前景。
- 1、下载文档前请自行甄别文档内容的完整性,平台不提供额外的编辑、内容补充、找答案等附加服务。
- 2、"仅部分预览"的文档,不可在线预览部分如存在完整性等问题,可反馈申请退款(可完整预览的文档不适用该条件!)。
- 3、如文档侵犯您的权益,请联系客服反馈,我们会尽快为您处理(人工客服工作时间:9:00-18:30)。
四、改善切削加工性的途径
(一)改善材料切削加工性的途径
1.调整材料的化学成分
钢中加硫、铅等元素;铸铁中增加石墨成分
2.进行适当的热处理
低、中碳钢宜选正火处理,均匀组织,调整硬度塑性; 高碳钢宜用球化退火,降低硬度,均匀组织,改善加工性;
工件材料的相对加工性
1.切削速度vT的含义:当刀具使用寿命为T (min)时切削 某种材料所允许的切削速度。
vT越高,材料的切削加工性越好。 通常取T = 60 min,
vT写作v60 ;难加工材料,vT为v15或v30 。
2.相对加工性Kr:以σb=0.637GPa的45钢的v60作为基准, 写作(v60 )j ,将某种材料的v60与其相比的比值,即
工件表面若有硬皮应进行退火处理。
(三)结构钢
碳素结构钢切削加工性取决于含碳量。 低碳钢硬度低,塑韧性高,变形大,断屑难,粘屑,加 工表面粗糙,加工性较差; 高碳钢硬度高,塑性低,切削力大,温度高,刀具耐用 度低,加工性差; 中碳钢性能适中,加工性良好。 合金结构钢强度硬度提高,切削加工性变差。
(四)难加工材料
2.选用合适的设备和加工方法
难加工材料加工,机床要有足够的功率和刚性; 选择合适的切削液,供给充足;
高硬度材料加工采用磨削加工更容易;
3.选择切削加工性好的材料状态
低碳钢选冷拔状态;中碳钢选热轧状态
Kr = v60 / (v60 )j
Kr仅反映不同材料对刀具使用寿命的影响程度,并未反映表
面粗糙度和断屑问题,仅对选择切削速度有指导意义。若以
某材料的Kr 乘以45钢的切削速度即得该材料的许用切削速度。
二、工件材料的物理力学性能对加工性的影响
例 45钢 1Cr18Ni9Ti
三、常用金属材料的切削加工性
中碳以上的合金钢硬度较高,需退火以降低硬度;
不锈钢常要进行调质处理,降低塑性,以便加工; 铸铁需进行退火处理,降低表皮硬度,消除内应力
(二)改善切削加工条件
1.选择合适的刀具材料和切削用量 难加工材料,导热性差,选YG、YW合金或涂层刀片;
刀具合理几何参数,断屑槽、卷屑槽,控制排屑;
选择合理切削用量等。
(一)有色金属
普通铝及铝合金、铜及铜合金,强度硬度低,导热性高(HBS600),难切削;
灰口铸铁硬度适中,强度塑性小,切削力较小,但高硬度 碳化物对刀具有擦伤,崩碎切屑,切削力热集中刀刃上且有 波动,刀具磨损率并不低,应采用低于加工钢的切削速度。 球墨铸铁、可锻铸铁的强度塑性比灰铁高,切削性良好
3.5
工件材料的切削加工性
是一个相对的概念
工件材料切削加工性 指材料被加工成合格零件的难易程度
一、衡量材料切削加工性的指标
1.以刀具使用寿命T 或切削速度vT来衡量
相同切削条件比T ;T 一定,比速度vT 或切除材料体积 2.以切削力或切削温度来衡量 粗加工、机床刚性或功率不足用力或功率;导热差用温度 3.以已加工表面质量来衡量 一般精加工,用Ra;精密零件,用加工硬化、残余应力 4.以断屑性能来衡量 自动机床、数控机床、自动线等,断屑性能是主要指标