铝带热轧机组电控系统
热轧过程控制计算机系统

热轧过程控制计算机系统摘要:现阶段过程控制计算机系统已被广泛应用在各领域生产经营建设中,对提高产品生产效率,保障生产综合效益意义重大。
为充分发挥出过程控制计算机系统在热轧环节的应用优势,还需借助明确现阶段热轧设备管控要求,探索出热轧过程控制计算机新路径。
本文就针对此,首先提出过程控制计算机系统发展以及在热轧环节的应用重要性,提出热轧过程中过程控制系统种类,明确热轧过程中控制计算机系统运行要点,以供参考。
关键词:信息时代;热轧;过程控制计算机系统前言:为进一步提高热轧质量,需要分析热轧全过程的应用管控要点,确保热轧设备安装及后续运行工作能够始终处于安全高效的状态。
随社会经济及科学技术发展速度不断加快,热轧系统也逐步趋向于自动化方向发展,对从根本上提高各类资源利用率,保障热轧设备运行期间的安全性与可靠性具有重要意义。
1、概述过程控制计算机系统20世纪50年代末,第1台过程控制计算机被应用在炼油厂内,为炼油厂高效生产目标的实现奠定了坚实技术基础[1]。
随后过程控制计算机也被应用在了钢铁工业,衍生出了带钢热连轧计算机控制系统,取得了显著的技术与经济效益。
现阶段热轧过程计算机控制技术主要就是采用计算机直接数字控制方式,由于热轧环节使用到的连扎设备生产效率高,质量控制难度小,在轧制过程中更易实现自动化与机械化目标,有效推动了联闸自动化发展进程。
依照应用特征、控制目的控制方法,可以将过程计算机控制系统划分为数据收集系统、直接数字控制系统、监督计算机控制系统、多级控制系统与分散控制系统多种类型。
数字控制系统中,计算机负责对实际生产期间的各类参数进行巡回、检验、处理,合理控制数据监管期间的给定时间间隔,借助打印的方式向各部门以及工作人员准确传达数据内容[2];数字控制系统就是在信息处理平台中输入模拟处理量,依据模拟处理量通道、开关量通道,开展全面数据采集工作,计算数据控制规律,实现生产全过程控制目标;监督计算机控制系统采用两级计算机完成直接数字控制功能,下位机需要进行直接数字控制,上位机可以直接反映并计算生产过程中的数据以及数字模型;多级控制就是使用分层控制方法,由最低一层等级逐步发展到最高等级信息控制系统,能够满足规模更大的生产控制要求;分散控制系统是被称之为分布式控制系统,在实际运行过程中具有分散控制、集中管理特征。
热连轧机组电气自动化控制技术方案设计

热连轧机组电气自动化控制技术方案设计针对700mm热连轧机组生产工艺要求,对其电气自动化控制进行方案设计;选用西门子6RA70系列全数字调速装置,西门子S7-400PLC进行系统控制,组成二级网络控制;并阐述了精轧电气控制速度主令控制方式,提出了控制方案。
1、工艺设备要求1.1.生产线示意图1.2. 生产线功率要求及控制要求1.2.1、工艺要求:坯420~660×165~180;出口成品:560~700×2.0~5.0;成品速度:10m/s1.2.2、要求生产线上各工序都有控制接口1.2.3、除鳞:高压水位旋转水1.2.4 、26组辊道:3.2KW,26个异步电机1.2.5 、5道可逆轧机750(二辊):立辊,低速直流电机450KW(0~60~120)平辊,低速直流电机5000KW(0~60~120)或2个2500KW1.2.6 、56组辊道:3.2KW;56个异步电机1.2.7 、滚动飞剪:低速直流电机480KW1.2.8 、不可逆轧机:立辊,高速直流电机250KW(0~600~1200)平辊(1~2辊径:二辊650):2200KW(2个)(3~4辊径:四辊650,320):2200KW(2个)(5~8辊径:四辊650,320):2000KW(4个)活套电机:22KW直流电机,7个1.2.9 、120组辊道:1.2KW,120个异步电机1.2.10、收卷:低速直流电机:160KW,2个;最大单卷5.2吨,芯子800~12001.2.11 、液压AGC,APC1.2.12 、主控室与操作台;两级网络2.总则2.1前言根据用户对700mm带钢热轧连轧机组基本的工艺控制要求,编写本初步电气自动化控制技术方案。
2.2 技术方案原则本电气控制技术方案“采用先进、成熟、安全、可靠并经济节能的控制技术,系统自动化程度达到二十一世纪初先进水平”为目标,编写本技术方案。
在技术方案的制定及系统的配置中,既考虑到整个系统的先进性,使该项目建成后具有二十一世纪初国际先进水平,又充分考虑到系统配置的实用性及可升级性,尽量节省项目投资,使整个系统具有优良的性能价格比。
热轧机温度控制系统

热轧机温度控制系统摘要:热轧机温度控制系统采用计算机系统控制,并且,通过现场总线和工业以太网通讯模式进行数据传输和控制。
控制带材的温度直接影响产品的质量和成品率。
关键词:计算机系统;现场总线;工业以太网热轧机温度控制系统由可逆轧机温度控制系统和连轧机温度控制系统组成。
它们之间采用高速工业以太网通讯方式进行数据传输,高温测量传感器的信号通过现场总线传送到温度控制单元,计算机通过数学模型的信息处理,输出控制信号,控制轧机电机传动系统的速度和喷射系统流量,实现带材的温度控制在允许的范围内。
下图为热轧机计算机控制系统:热轧机轧制过程中,可逆轧机和连轧机的带材温度变化,直接影响带材的质量和板形,所以,为了保证连轧机能轧制出优质的产品,精确控制可逆轧机出口转移坯料的温度是非常必要的。
但是,需要考虑与温度控制相关的主要问题:带材宽度、不同的合金和用途。
它们对温度控制的要求是不同的。
特别是不同的合金,轧制过程中,带材的温度变化是不同的。
考虑到上述问题,首先在可逆轧机出口安装了带材温度控制系统,其包括:控制计算机系统、喷射系统、温度检测系统。
可逆轧机温度控制过程:可逆轧机出口安装了冷却带材的喷射装置,喷射设备分区控制,每个区域的喷嘴控制阀可以独立控制。
另外,一个高温检测传感器T1安装在喷射区的入口侧,另外一个高温检测传感器T2安装在喷射区的出口侧。
带材温度控制过程中,预先设定冷却液的流量、温度和喷射区域,当带材通过喷射区时,又控制计算机控制带材的移动速度、冷却液的流量和喷射时间,带材通过喷射区的速度是根据喷射区入口高温传感器T1的测量温度偏差进行修正的,带材通过喷射区时,将导致带材温度下降,并且,温度下降的多少是由带材通过喷射区域的速度和时间长短决定的.速度控制由过程控制器完成,因此,带材的温度能精确控制。
带材向前控制:喷射区入口的高温传感器T1测量带材进入喷射区时刻的温度,并且,将温度信号通过现场总线传输到过程控制计算机,计算出该时刻带材的速度和进入喷射区的温度测量点的间隔。
铝板连铸连轧机成套电控系统
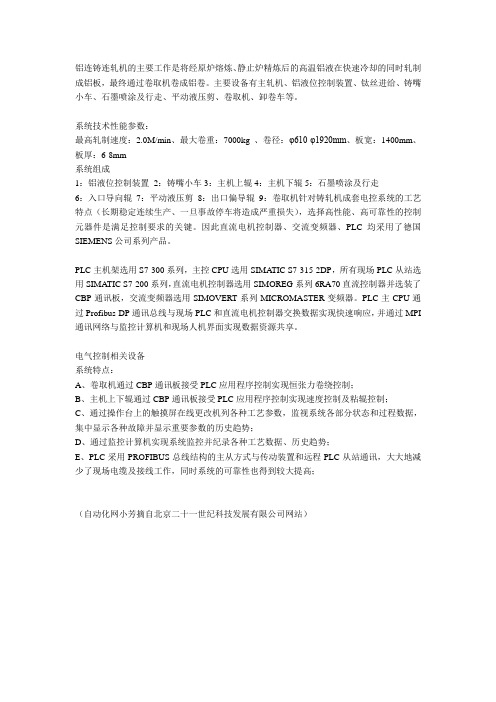
铝连铸连轧机的主要工作是将经原炉熔炼、静止炉精炼后的高温铝液在快速冷却的同时轧制成铝板,最终通过卷取机卷成铝卷。
主要设备有主轧机、铝液位控制装置、钛丝进给、铸嘴小车、石墨喷涂及行走、平动液压剪、卷取机、卸卷车等。
系统技术性能参数:最高轧制速度:2.0M/min、最大卷重:7000kg 、卷径:φ610-φ1920mm、板宽:1400mm、板厚:6-8mm系统组成1:铝液位控制装置2:铸嘴小车3:主机上辊4:主机下辊5:石墨喷涂及行走6:入口导向辊7:平动液压剪8:出口偏导辊9:卷取机针对铸轧机成套电控系统的工艺特点(长期稳定连续生产、一旦事故停车将造成严重损失),选择高性能、高可靠性的控制元器件是满足控制要求的关键。
因此直流电机控制器、交流变频器、PLC均采用了德国SIEMENS公司系列产品。
PLC主机架选用S7-300系列,主控CPU选用SIMATIC S7-315-2DP,所有现场PLC从站选用SIMATIC S7-200系列,直流电机控制器选用SIMOREG系列6RA70直流控制器并选装了CBP通讯板,交流变频器选用SIMOVERT系列MICROMASTER变频器。
PLC主CPU通过Profibus-DP通讯总线与现场PLC和直流电机控制器交换数据实现快速响应,并通过MPI 通讯网络与监控计算机和现场人机界面实现数据资源共享。
电气控制相关设备系统特点:A、卷取机通过CBP通讯板接受PLC应用程序控制实现恒张力卷绕控制;B、主机上下辊通过CBP通讯板接受PLC应用程序控制实现速度控制及粘辊控制;C、通过操作台上的触摸屏在线更改机列各种工艺参数,监视系统各部分状态和过程数据,集中显示各种故障并显示重要参数的历史趋势;D、通过监控计算机实现系统监控并纪录各种工艺数据、历史趋势;E、PLC采用PROFIBUS总线结构的主从方式与传动装置和远程PLC从站通讯,大大地减少了现场电缆及接线工作,同时系统的可靠性也得到较大提高;(自动化网小芳摘自北京二十一世纪科技发展有限公司网站)。
“1+5”铝热连轧中的一级自动化系统

差控制在一个较小的、 合适 的范 围内, 来实现负荷平
衡控 制 ;
( 2 ) N v 工具软件 , N v控制器 由 N v — T o o l 工具软
件 来配 置 , 采用 I E C 6 1 1 3 1 . 3标 准 逻辑 语 言 , 在 同一 段 程 序 中可 同时 使 用 梯 形 图 、 功能块、 顺 控 表 和 语 句 表
覆盖 的 自动 化 范 围包 括 从 粗 轧 机 前 炉 子 辊 道 直 至 卷 材运输 结束 ( 含 取样 站 ) 。
指 示
・
1 . 2 部件 介绍
一
1 系统 概 览
1 . 1 主 要功 能
软件 、 数据跟 踪 收 集 系 统 、 HM I系统 、 网络 通 讯 系 统 、 远程 I / O站及传 感器 等组 成 ( 图1 ) 。
机速 度 ;
级 自动 化 系 统 按 照 区 域 分 为 两 个 单 独 的功 能
区, 粗 轧 机 区和含 卷取 机及 取样 站 的精轧 机 区 。
2 . 1 粗 轧机 区
2 . 1 . 1 主 控 制 功 能
④ 轧机爬行 , 主传动处于低速运行 , 当主速度参 考值为零时, 保持轧辅温度;
2 . 1 . 2 辅 助 控 制 功 能
( 3 ) 系Leabharlann 通 讯 , T ME I C标 准 数 据 通 信 网络 主 要 由
T C—N e t 1 0 0 、 T C —N e t I / O 环 网、 以 太 网 连 接 和
P r o f i b u s —D P组 成 ;
流体、 润 滑和 空气 系 统 ; 受 料辊 道 控 制 ; 粗 轧 机入 口互锁控 制 ; 铸锭 清洗 控 制 ; 立 辊 控制 ; 粗 轧 机 人 口和 出 口侧 导尺 控制 ; 液 压切 断剪 T l控制 ; 液 压切 断剪 控制。
热轧卷取机自动控制系统的设计与实现
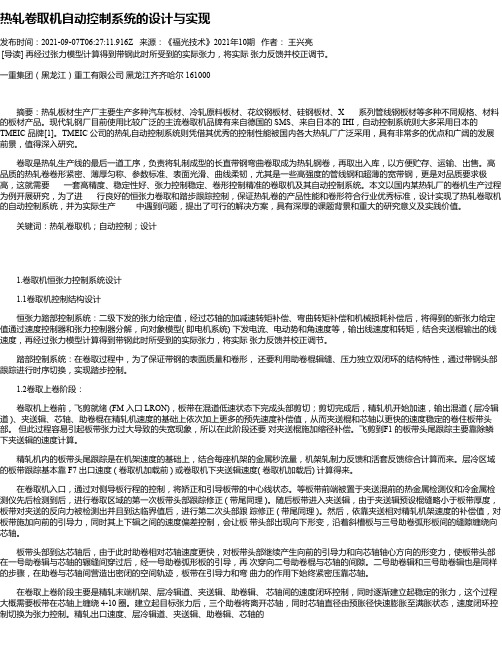
热轧卷取机自动控制系统的设计与实现发布时间:2021-09-07T06:27:11.916Z 来源:《福光技术》2021年10期作者:王兴亮[导读] 再经过张力模型计算得到带钢此时所受到的实际张力,将实际张力反馈并校正调节。
一重集团(黑龙江)重工有限公司黑龙江齐齐哈尔 161000摘要:热轧板材生产厂主要生产多种汽车板材、冷轧原料板材、花纹钢板材、硅钢板材、X 系列管线钢板材等多种不同规格、材料的板材产品。
现代轧钢厂目前使用比较广泛的主流卷取机品牌有来自德国的 SMS、来自日本的 IHI,自动控制系统则大多采用日本的TMEIC 品牌[1]。
TMEIC 公司的热轧自动控制系统则凭借其优秀的控制性能被国内各大热轧厂广泛采用,具有非常多的优点和广阔的发展前景,值得深入研究。
卷取是热轧生产线的最后一道工序,负责将轧制成型的长直带钢弯曲卷取成为热轧钢卷,再取出入库,以方便贮存、运输、出售。
高品质的热轧卷卷形紧密、薄厚匀称、参数标准、表面光滑、曲线柔韧,尤其是一些高强度的管线钢和超薄的宽带钢,更是对品质要求极高,这就需要一套高精度、稳定性好、张力控制稳定、卷形控制精准的卷取机及其自动控制系统。
本文以国内某热轧厂的卷机生产过程为例开展研究,为了进行良好的恒张力卷取和踏步跟踪控制,保证热轧卷的产品性能和卷形符合行业优秀标准,设计实现了热轧卷取机的自动控制系统,并为实际生产中遇到问题,提出了可行的解决方案,具有深厚的课题背景和重大的研究意义及实践价值。
关键词:热轧卷取机;自动控制;设计1.卷取机恒张力控制系统设计1.1卷取机控制结构设计恒张力踏部控制系统:二级下发的张力给定值,经过芯轴的加减速转矩补偿、弯曲转矩补偿和机械损耗补偿后,将得到的新张力给定值通过速度控制器和张力控制器分解,向对象模型( 即电机系统) 下发电流、电动势和角速度等,输出线速度和转矩,结合夹送棍输出的线速度,再经过张力模型计算得到带钢此时所受到的实际张力,将实际张力反馈并校正调节。
热轧基础自动化控制系统概述 [兼容模式]
![热轧基础自动化控制系统概述 [兼容模式]](https://img.taocdn.com/s3/m/1ab1c958852458fb770b567e.png)
+
总弯辊力基准
+
+
+
板形修正量
手动修正量
正弯检测
−
PID
+
正弯负弯 基准生成
+
PID
−
负弯检测
伺服阀 非线性化
正弯辊 伺服阀给定
伺服阀 非线性化
负弯辊 伺服阀给定
RAL
液压窜辊控制系统
薄带钢轧制时,为了减小轧辊的磨 损和降低边缘降,并扩大带钢的凸 度控制范围,在轧机上装备液压窜 辊装置,在保持良好平直度的同时 得到要求的板形。
RAL
热轧自动化系统硬件及网络配置
RAL
热连轧生产线自动化系统构成
¾ 配置有基础自动化与过程自动化系统,完成轧线厚度控制系统、宽度 控制系统、主令系统及辅助逻辑控制
¾ 采用高性能PLC和PC服务器,具有很高的系统处理及执行速度,并配 置有IBA数据采集及分析系统
¾ 过程自动化和基础自动化以及基础自动化之间使用工业以太网通讯, 基础自动化与传动及远程站之间使用Profibus-DP网通讯
RAL
活套高度控制
活套高度的控制实际上是活套量的控制
采用模糊控制
A
+PID调节器
Fi
R1
Fi+1
的复合控制策
略,当活套的
B
α
L1
β
C
设定值与给定
R
值偏差较大时,
θ
L3
θ0
采用模糊控制 器;当设定和 反馈偏差小于
L
一定值时,采
用PID调节器。
ΔL = (L1+ Rcosθ)2 +(Rsinθ − L3 + R1)2 + (L − L1− Rcosθ)2 +(Rsinθ − L3 + R1)2 − L
2050铝带冷轧机的控制系统
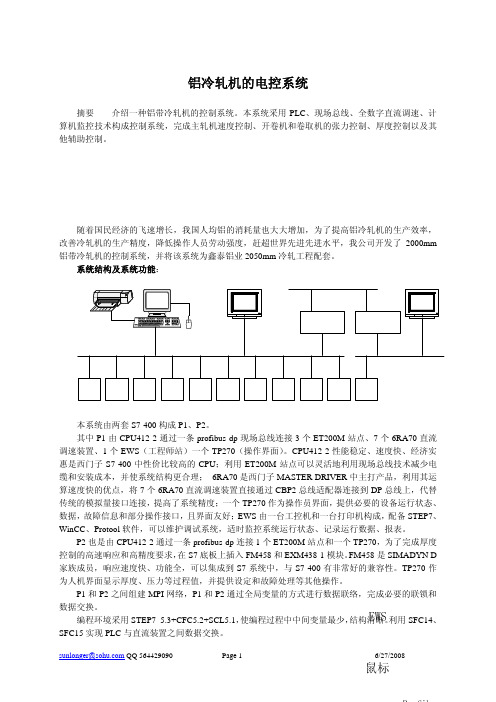
铝冷轧机的电控系统摘要介绍一种铝带冷轧机的控制系统。
本系统采用PLC、现场总线、全数字直流调速、计算机监控技术构成控制系统,完成主轧机速度控制、开卷机和卷取机的张力控制、厚度控制以及其他辅助控制。
随着国民经济的飞速增长,我国人均铝的消耗量也大大增加,为了提高铝冷轧机的生产效率,改善冷轧机的生产精度,降低操作人员劳动强度,赶超世界先进先进水平,我公司开发了2000mm 铝带冷轧机的控制系统,并将该系统为鑫泰铝业2050mm冷轧工程配套。
系统结构及系统功能:本系统由两套S7-400构成P1、P2。
其中P1由CPU412-2通过一条profibus-dp现场总线连接3个ET200M站点、7个6RA70直流调速装置、1个EWS(工程师站)一个TP270(操作界面)。
CPU412-2性能稳定、速度快、经济实惠是西门子S7-400中性价比较高的CPU;利用ET200M站点可以灵活地利用现场总线技术减少电缆和安装成本,并使系统结构更合理; 6RA70是西门子MASTER DRIVER中主打产品,利用其运算速度快的优点,将7个6RA70直流调速装置直接通过CBP2总线适配器连接到DP总线上,代替传统的模拟量接口连接,提高了系统精度;一个TP270作为操作员界面,提供必要的设备运行状态、数据,故障信息和部分操作接口,且界面友好;EWS由一台工控机和一台打印机构成,配备STEP7、WinCC、Protool软件,可以维护调试系统,适时监控系统运行状态、记录运行数据、报表。
P2也是由CPU412-2通过一条profibus-dp连接1个ET200M站点和一个TP270,为了完成厚度控制的高速响应和高精度要求,在S7底板上插入FM458和EXM438-1模块。
FM458是SIMADYN D 家族成员,响应速度快、功能全,可以集成到S7系统中,与S7-400有非常好的兼容性。
TP270作为人机界面显示厚度、压力等过程值,并提供设定和故障处理等其他操作。
热轧厂生产线电气自动化控制系统探究_1

热轧厂生产线电气自动化控制系统探究发布时间:2023-02-07T03:36:57.073Z 来源:《中国科技信息》2022年第9月第17期作者:熊腾霖[导读] 自从我国步入工业时代以来,经济就迎来了飞快的发展,熊腾霖宝钢湛江钢铁有限公司524072摘要:自从我国步入工业时代以来,经济就迎来了飞快的发展,我国也更加注重工业的现代化,这也让自动化控制系统得到了有效的发展。
在实际的发展过程中,由于我国汽车工业、建筑行业、交通运输业的发展速度都在加快,自然需要大量的生产材料供应,对于热轧带钢的需求量也是越来越高,热轧厂也迎来了全新的机遇,为了提升企业效益和生产效率,热轧厂也在不断地加强电气自动化控制系统的研究,所以相关部门需要积极的对自动化控制系统进行优化,根据实际的发展情况,让自动化控制系统更好地适应热轧厂的工作节奏,提升热轧厂的工作效率和工作质量。
关键词:热轧厂;电气自动化控制系统;工作效率引言工业时代的普及让冶金工业发生了极大的变化,因为与日俱增的需求量,20世纪六十年代就在生产过程中应用了计算机技术,并在20世纪70年代的时候实现了计算机控制,而这个阶段正好也是计算机技术飞速发展的年代,软件和硬件的更新速度也是非常的快,让热轧厂的控制功能也在发生变化,同时让带钢的质量越来越高,并且渐渐地形成了多级冶金自动化控制。
如今在网络技术的支持下,电气自动化控制系统也有了全新的特点,有了更加稳定化的发展,功能也更加的标准。
但是目前来说,在实际的操作过程中,自动化控制系统依旧存在着一定的问题,这些问题如果得不到及时的解决,那么就会影响到最终的工作质量和工作效率。
1热轧厂生产线自动化控制系统的发展特点为了更好地理解本研究课题的核心含义,必须积极了解和掌握热轧厂生产线自动控制系统的发展特点。
具体而言,主要包括以下几个方面。
首先,它的控制速度比较快。
在许多情况下,其机电液压系统可以被完全控制和管理,并且其液压控制系统的控制周期可以被更好地管理。
热轧电气知识讲座最终(1)

热轧电气知识讲座最终(1)热轧电气知识讲座最终随着社会的不断发展,热轧钢板在我们的日常生活和工业生产等领域中已经成为不可或缺的重要材料。
而要实现高质量的生产,不仅需要先进的设备技术,还需要有理性高效的电气控制技术的支持。
因此,我们在这次热轧电气知识讲座中将会详细介绍热轧电气控制的相关知识和技术。
下面,我们将针对热轧电气控制的各个方面,进行详细的讲解:1、热轧电气控制系统的框架热轧电气控制系统的框架分为以下几个层面:I/O层,数据处理层,控制逻辑层和人机交互层。
其中I/O层处理输入/输出信号,数据处理层用于处理数据进行控制,控制逻辑层主要实现多路控制,人机交互层用于交互式操控。
2、热轧电气控制系统的关键点通过现场视察、应急预案的建立和管理、定期检查等方式的复合运用,热轧电气控制系统维护管理应重点关注的有:设备运行状态检查、控制逻辑升级处理、人机界面界面升级和颁布和更新运行和操作规程等。
3、热轧电气控制的应用技术(1)PLC技术热轧电气控制中最为普遍的控制技术就是PLC。
PLC能够快速运算控制信息,并且能够在线进行通讯。
PLC可以为控制的准确可靠性提供强大支持。
(2)变频器技术变频器可以通过改变电动机的电压和频率,控制电动机的转速和负载。
因此,变频器对热轧电气控制系统的运转状态和性能的提高也是具有积极作用的。
(3)电气接口技术电气接口技术主要包括各种接口标准、接口参数、镀层和插头等,它们主要是为了使不同设备之间可以相互连接和通讯,以实现互联互通和热轧电气控制系统整合的目标。
通过以上的讲解,相信大家已经有一个比较深刻的理解了热轧电气控制的相关知识和技术。
在未来,我们需要不断地发展和应用控制技术,以使得我们在热轧钢板的生产和应用中能够发挥更大的效率和价值。
探析热轧带铝生产中电气自动化控制系统的可靠性

探析热轧带铝生产中电气自动化控制系统的可靠性摘要:由于科技的迅速发展,使得电气自动化控制系统被大量应用于相关的工业生产中,该系统的应用即提高了工作效率,又减轻了工作人员的工作强度,同时提升了相关企业的经济效益。
然而,该系统在运行过程中的可靠性还不很完善,因此应进行相关方面的完善和改进。
基于此,本文主要对热轧带铝生产中电气自动化控制系统的可靠性进行了探讨。
关键词:热轧带铝;电气自动化;控制系统;可靠性近年来电子技术得到了长足的发展,因而也使电气自动化控制系统在社会的各领域得到应用,从而给相关的企业和人员带来了巨大的转变。
针对热轧带铝的生产来说,进行该技术的应用不但显著提高了经济效益,同时展示了我国在电子行业的发展成就。
现阶段电气自动化技术已全面渗透到现实生活的各个方面。
但在对其进行使用的过程中,备受关注的还是其对相关设备进行控制的可靠程度。
1热轧带铝电气自动化控制系统简介1.1系统组成由于电气自动化技术的应用,使得热轧带铝的生产具有高速以及连续的能力,而对相关的控制实现了高精度实时控制。
在该系统中充分运用了相关的网路技术、服务器以及仪表等,从而实现了执行机构与电气传动以及自动化系统之间的通讯互动。
1.2技术运用在常规的热轧生产线中各级都有相关的自动化控制系统,其主要种类有基础自动化控制器、服务器等,在进行操作时有相关的操作系统,为了追求通讯的简便性,在相关的生产线中增加了一定的新型通讯技术,这种技术的使用能够满足计算机之间的数据交换,并且能够适应多种系统的相关通讯。
目前在相关的热轧带铝生产中已经实现了过程控制服务以及相关控制器与多种特制仪表间的实时通讯,且数据的交换速度极高。
所谓的新型通讯技术就是一种光纤环网技术,利用该技术可以在通讯过程中按照需要进行相关的设置,同时还可以满足基础自动化控制器与相关计算机间的数据实时交换,此就能够适应高速控制器与相关计算机间的通讯需求。
2保证热轧带铝电气自动化控制系统可靠性的优势2.1提升产品质量消费者在购买产品时首先考虑的会是产品的质量。
铝热连轧机温度控制

关键词: 热连轧;FDTC 模型;终轧温度;PLC:参数分析
中图分类号:TG339
文献标识码:A
文章编号:1005-4898 (2019) 02-0035-03
doi:10.3969/j.issn.1005-4898.2019.02.09
0 前言
热粗轧+多机架热精轧是目前最适合大规模生 产高精度铝板带材的生产方式,而高精铝板带材在 后续加工对材料的力学、组织性能要求很高,市场 对热轧铝板带材的质量要求也日趋严格。热连轧机 在轧制过程中对带材温度控制也至关重要。
《铝加工》
2019 年第 2 期总第 247 期
技术工程
铝热连轧机温度控制
方胜兵
(重庆西南铝机电设备工程有限公司,重庆 401326)
摘要:终轧温度是影响铝热轧性能和质量的关键工艺指标。铝热连轧机温度控制系统的出现解决了带材终轧温度控制问
题,目前国内外热连轧机普遍采用基于数学模型的温度控制系统。本文主要对卷材终轧温度控制系统和关键因素做了分析。
ASR
ASR
F1F速1 ?度?控? ?制 FF12速? ?度?控? 制F3F?1?速?度? 控制FF14F??1??速?? 度?? 控制 SSRH
终?轧? 温? ?度?控? 制
精? 轧? ?设?定? 计? 算
精? 轧? 速? ?度 主? 令? ?控? 制
MRH
T AIM FD
图 1 系统控制框图
作者简介:方胜兵 (1980-),男,江西人,工程师。 收稿日期:2018-10-20
式中: VT 为穿带速度; Li 为机架间距; TS0 为
带材初始温度; TS 为带材温度; TC 为乳液温度;
αF 为当量热传导系数。 根据式 (2) 和秒流量方程就可得到各机架的
铝带热轧机组电控系统

1300毫米单机架双卷取铝带热轧机传动电控系统摘要:本文主要介绍了应用了ABB公司的DCS500B全数字直流传动模块、ACA600交流多传动控制模块和西门子公司的S7-300程控器等完成的1300毫米铝板带热轧机电控系统;文章介绍了系统硬件、软件设计并着重介绍了辊道电机的控制思想。
关键词:热轧机交流多传动现场总线Abstract:This paper mainly introduces the 1300mm aluminium hot roll mill control system that apply the DCS500B digital DC motor controller and ACA600 AC motor multidirve controller of ABB , S7-300 programmable controller of SIEMENS;The paper also descripes the system hardware,software designation and main control idea of roll table motor control.Key words:hot roll mill AC multidrive field bus1概述本电控系统应用于我公司新开发研制的国内第一台1300毫米单机架双卷取四辊铝带可逆热轧机组中。
该热轧机将加热后的坯料先通过热初轧轧制成薄板,再通过热精轧在左、右双卷取机上高速成卷卷取。
来料板坯宽度1050毫米,厚350毫米,成品厚度4毫米,成品卷径1600毫米,卷重4950千克,机组最大轧制力12000千牛,最高轧制速度180米/分钟,最大卷取张力120千牛,卷材终轧温度超过320℃。
主要传动设备有主轧机、左、右卷取机、辊道、夹送辊、圆盘剪和压下电机等。
2电控系统组成热轧机组电气传动控制系统示意图如下图一热轧机组电气传动控制系统示意图2.1传动控制系统:直流传动控制系统采用DCS500B全数字传动控制模块;,内部集成了卷取功能块,可以方便地完成张力给定、卷径计算、动态补偿、空载补偿和转矩控制功能;2.2交流传动控制系统:采用基于直接转矩控制的ACA600交流多传动装置传动;2.3可编程程控器:采用三套SIEMENS公司的S7-300程控器;2.4人机操作界面:采用一套15英寸触模式板式计算机、两块10英寸彩色液晶触摸屏,一块5.7英寸单色液晶触摸屏;2.5上位机:采用一套P4-1.7G液晶显示屏计算机,配套HP激光打印机;2.6通讯:整个系统采用三种网络通讯:三套程控器之间采用profibus-FDL方式,编程采用MPI网,直流传动装置、交流多传动装置、现场操作台、阀台等采用profibus-DP方式通讯。
宽幅铝板带热轧计算机控制系统

宽幅铝板带热轧计算机控制系统何安瑞;荆丰伟;宗胜悦;张勇军;许磊【摘要】在充分考虑宽幅铝板带热轧工艺、装备特点及板形、表面质量控制等难点的基础上,兼顾系统的开放性、先进性及稳定性,自主研发了宽幅铝板带热轧计算机控制系统,包括传动控制(L0)级、基础自动化(L1)级和过程控制(L2)级.多条工业生产线的应用实绩表明,该计算机控制系统可靠、稳定,产品性能好,温度、厚度、凸度、楔形等各项指标命中率高,可满足超宽幅铝板带热轧自动化生产及高精度质量控制要求.【期刊名称】《世界有色金属》【年(卷),期】2015(000)010【总页数】6页(P14-19)【关键词】铝;板带;热轧;控制系统;板形【作者】何安瑞;荆丰伟;宗胜悦;张勇军;许磊【作者单位】北京科技大学冶金工程研究院,北京100083;北京科技大学冶金工程研究院,北京100083;北京科技大学冶金工程研究院,北京100083;北京科技大学冶金工程研究院,北京100083;广西柳州银海铝业股份有限公司,柳州545006【正文语种】中文【中图分类】TG339;TF35国民经济及现代工业的快速发展极大地推动了铝加工工业的发展。
我国在短短的几年内迅速发展为铝加工的大国,总产量超过世界铝加工产量的50%。
由于宽幅铝板带产品在交通运输、建筑、家电及食品包装等方面应用广泛,很多铝加工企业都将其作为产品结构调整和扩展的首要方向,并建成了不同规格尺寸的宽幅铝板带热轧生产线,包括(1+1)式热轧生产线10条、(1+3)式热连轧生产线4条、(1+4)式热连轧生产线10条、(1+5)热连轧生产线1条,年生产能力近千万吨,并有在建的(1+4)式热连轧生产线6条、(1+5)式热连轧生产线1条[1]。
由于技术复杂,建设难度大,国内投产或在建的宽幅铝板带热连轧多采用国外的技术,尤其是计算机控制系统,基本上由德国SIEMENS、日本TMEIC两家公司垄断。
这些国际知名公司提供的控制系统虽可满足投产初期的产品质量和生产控制要求,但在技术转移及交接方面存在不足,核心源代码的开放性也不尽人意,给后期的系统优化和功能扩展、新产品开发等带来很多的难题。
热轧机组基础自动化系统的系统构成及控制功能

热轧机组基础自动化系统的系统构成及控制功能魏健【摘要】本文结合作者在瑞闽2400mm热轧机组调试工作中的体会,较全面的论述了热轧机组基础自动化系统的结构特点以及电气自动化控制新技术在热轧机组中的应用.【期刊名称】《有色金属加工》【年(卷),期】2012(041)004【总页数】4页(P60-62,59)【关键词】基础自动化系统;交流传动系统;西门子S7-400控制器【作者】魏健【作者单位】洛阳有色金属加工设计研究院,河南洛阳471039【正文语种】中文【中图分类】TP271基于铝加工行业的激烈竞争,目前对产品的产量和质量提出了越来越高的要求,对控制系统的期望也越来越高。
现代铝热轧机组有许多新特点:(1)轧制过程稳定,产品精度高;(2)实现带材厚度自动控制(AGC控制),使带材厚度精度提高;(3)轧制速度高;(4)轧机自动化程度高,采用计算机控制;(5)采用厚度、张力、速度AGC综合控制及最优化控制,提高了产品质量;(6)具有故障检测装置,可实时监测有关参数。
1 基础自动化系统构成热轧机组传动与自动化控制系统为多层次的电气控制系统,它主要由下列子系统构成:传动控制系统:采用全数字交流多传动模块和传动控制器(FM458)PLC控制系统:由西门子公司生产的S7-400PLC和完全分布式子站完成人机操作界面(HMI):采用工业控制计算机上位控制系统:一个上位机(工程师站)数据采集和故障监测系统:采用工业控制计算机厚度控制系统:采用S7-400PLC及FM458控制上述各个部分通过各自通讯适配器或专用通讯接口模块、交换机连接起来构成一体,系统基本网络结构分为二种,其一为现场级网络采用Profibus-DP总线结构,主要用于PLC与传动控制系统、机列、油系统控制等实时性、可靠性要求较高的现场级控制交换信息,完成现场信息的采集和实时控制;其二为上一级的工业以太网总线结构,用于L2级系统和PLC之间、多PLC之间、人机界面、AGC、数据采集系统、其它系统等的数据信息交换,完成轧机工艺数据上传、下传和轧机运行数据传递,故障信息传递及各个显示运行、报警画面、报表打印等。
X―PACT控制系统在热轧机上的应用

摘要:详细描述了南南铝1+1热轧生产线引进的西马克x-pact一级自动化控制系统,深入介绍了一级系统的硬件和软件平台及自动化网络架构,重点分析了轧制过程的工艺控制功能。
机组的投产效果表明,x-pact控制系统代表了复杂工业自动化控制的先进水平。
关键词:铝轧机;工艺控制;厚度及板型控制一、引言南南铝“1+1热轧机组”的电气自动化引进了西马克(sms)的x-pact电气自动化系统,完备高效的铝合金工艺模型、先进的系统硬件平台架构和控制技术保证了生产的高质量和高效率。
x-pact电气自动化系统集成了0级到3级系统的整体解决方案,完成现代化工厂自动化控制所需的各种任务。
二、一级自动化系统硬件和软件南南铝“1+1热轧机组”的一级系统采用了西马克x-pact电气自动化新一代硬件平台。
嵌入式工业自动化控制器和工业实时以太网ethercat技术的应用,使得生产线配备了最先进的自动化控制技术。
对比以往的vme系统,新平台具有以下优点:(1)硬件体积减小,节省柜内空间。
省掉了i/o板卡,现场对实时性要求较高的i/o直接接到就近的ethercat模块,以总线的形式连接到主机的以太网口。
(2)硬件接线和布线更方便简单。
(3)硬件成本大大降低该“1+1热轧机组”的一级系统共配备了10台嵌入式自动化控制器和2台西门子plc。
10台嵌入式控制器分别用于:粗轧区域介质控制,粗轧机主令控制(顺序控制,物料跟踪,通讯协调等),粗轧机机架及立辊机架控制(厚度控制,宽度控制等),粗轧区域传动控制(主速度控制,主传动控制,辊道电机控制等),重型剪控制,轻型剪控制,精轧区域介质控制,精轧机主令控制,精轧机机架控制,精轧区域传动控制。
2台西门子plc分别用于粗轧及精轧区域的安全控制。
(一)一级自动化系统的硬件。
一级自动化的硬件系统主要包括:嵌入式自动化控制器,人机界面计算机,软件开发服务器及工程师站计算机,iba pda系统等。
嵌入式自动化控制器基于intel core 双核技术,其强大的计算能力是获得最佳控制性能的保证。
对热轧厂生产线电气自动化控制系统研究

对热轧厂生产线电气自动化控制系统研究发布时间:2022-10-14T02:05:13.920Z 来源:《科学与技术》2022年6月第11期作者:高永红[导读] 在社会主义现代化建设的新形势之下,我国在实际发展的过程中,更加注重发展的现代化。
高永红河钢邯钢邯宝热轧厂河北邯郸 056015摘要:在社会主义现代化建设的新形势之下,我国在实际发展的过程中,更加注重发展的现代化。
落实到热轧厂生产线自动化控制系统发展中来,主要是从控制功能和带钢质量等不同的角度出发,积极对其相关的控制系统进行系统的优化,在这个过程中,要充分机加强过程控制和自动化控制时期,不断强化生产的性能和功能,从而更好的根据实际的发展情况,推动热轧厂经济效益社会效益的有效统一。
因此,从某种意义上来讲,在未来的发展过程中,还要充分加强热轧厂生产线自动化控制系统的有效应用,从而更好的推动我国社会经济逐渐朝着可持续化的方向进步与发展。
关键词:热轧厂;生产线;电气自动化;控制系统1热轧厂生产线自动化控制系统的发展特点为了更好的了解这一课题研究的核心要义,积极对热轧厂生产线自动化控制系统的发展特点有一个清晰的了解和把握是非常关键的。
具体来讲,主要包括以下几个方面。
首先,其控制速度是比较快的,很多情况之下,可以充分对其机电液压系统等进行系统的控制和管理,并且对其液压压力控制系统的控制周期可以更好的进行管理。
第二,控制功能是比较丰富的,并且可以集中的对其相关的性能和目标进行系统的实现,通过自动加减和数据的有效控制,来加强多控制器的有效使用。
第三,功能之间可以相互影响,也就是说,很多功能之间最终在引发挥自身作用的过程中,主要是集中到精扎机之间的变形区域当中,这样可以更好的对其自动板形控制系统的相关内容进行系统的调整。
最后,在实际运行的过程中,该系统当中多个功能可以更好的对其输入和输出的模块进行系统的共享,对于CPU处理系统的有效提升也具有非常重要的影响。
- 1、下载文档前请自行甄别文档内容的完整性,平台不提供额外的编辑、内容补充、找答案等附加服务。
- 2、"仅部分预览"的文档,不可在线预览部分如存在完整性等问题,可反馈申请退款(可完整预览的文档不适用该条件!)。
- 3、如文档侵犯您的权益,请联系客服反馈,我们会尽快为您处理(人工客服工作时间:9:00-18:30)。
1300毫米单机架双卷取铝带热轧机传动电控系统摘要:本文主要介绍了应用了ABB公司的DCS500B全数字直流传动模块、ACA600交流多传动控制模块和西门子公司的S7-300程控器等完成的1300毫米铝板带热轧机电控系统;文章介绍了系统硬件、软件设计并着重介绍了辊道电机的控制思想。
关键词:热轧机交流多传动现场总线Abstract:This paper mainly introduces the 1300mm aluminium hot roll mill control system that apply the DCS500B digital DC motor controller and ACA600 AC motor multidirve controller of ABB , S7-300 programmable controller of SIEMENS;The paper also descripes the system hardware,software designation and main control idea of roll table motor control.Key words:hot roll mill AC multidrive field bus1概述本电控系统应用于我公司新开发研制的国内第一台1300毫米单机架双卷取四辊铝带可逆热轧机组中。
该热轧机将加热后的坯料先通过热初轧轧制成薄板,再通过热精轧在左、右双卷取机上高速成卷卷取。
来料板坯宽度1050毫米,厚350毫米,成品厚度4毫米,成品卷径1600毫米,卷重4950千克,机组最大轧制力12000千牛,最高轧制速度180米/分钟,最大卷取张力120千牛,卷材终轧温度超过320℃。
主要传动设备有主轧机、左、右卷取机、辊道、夹送辊、圆盘剪和压下电机等。
2电控系统组成热轧机组电气传动控制系统示意图如下图一热轧机组电气传动控制系统示意图2.1传动控制系统:直流传动控制系统采用DCS500B全数字传动控制模块;,内部集成了卷取功能块,可以方便地完成张力给定、卷径计算、动态补偿、空载补偿和转矩控制功能;2.2交流传动控制系统:采用基于直接转矩控制的ACA600交流多传动装置传动;2.3可编程程控器:采用三套SIEMENS公司的S7-300程控器;2.4人机操作界面:采用一套15英寸触模式板式计算机、两块10英寸彩色液晶触摸屏,一块5.7英寸单色液晶触摸屏;2.5上位机:采用一套P4-1.7G液晶显示屏计算机,配套HP激光打印机;2.6通讯:整个系统采用三种网络通讯:三套程控器之间采用profibus-FDL方式,编程采用MPI网,直流传动装置、交流多传动装置、现场操作台、阀台等采用profibus-DP方式通讯。
3软件系统功能3.1直流传动系统:采用GAD图形化编程语言编程,主要控制功能如下:主电机速度控制,左、右卷取机卷径、张力、动态补偿、空载补偿控制;3.2交流多传动系统:采用driveWindow调试,主要控制功能如下:控制左、右辊道电机、压下电机和圆盘剪电机的转速和转矩3.3可编程控制器:采用STEP7编程软件编制,三套程控器的控制功能如下:3.3.1 直流及交流多传动控制程控器:主要完成对所有传动模块的通讯控制,包括合、分闸控制,速度给定,张力给定;3.3.2机列操作程控器:接收现场各种传感器信号、操作台按钮、开关操作指令,完成对轧机液压元件、气动元件、信号灯的控制;3.3.4油系统程控器:完成对轧机辅助、压下等泵站的控制;4 触摸屏控制及画面编制:这套电控系统采用了较多的触摸屏,大量减少了传统的按钮、信号灯和模拟显示仪表,对操作界面带来了很大的改观,触摸屏完成功能如下:4.1 主操作台触摸屏画面:轧机主传动电机、交流多传动电机合、分闸操作及转速、电流等状态显示,左、右卷取机张力、卷径显示,轧制速度、工艺润滑喷嘴、吹扫喷嘴控制和状态显示,各泵站启、停控制及状态显示,轧机操作连锁状态显示,;4.2油系统操作触摸屏画面:辅助、压下泵站启、停控制和工作、报警状态显示;4.3工艺润滑操作触摸屏画面:工艺润滑泵站启、停控制和工作、报警状态显示;5 监控计算机:本系统采用了上位监控计算机,运行WinCC组态软件,完成对整个机组运行状况的监视;主要画面包括:轧机运行画面、各电动机速度-转矩(电流)趋势图历史记录、故障报警画面、打印。
6交流变频电机控制:我们在这台热轧机辊道、压下和圆盘剪电机传动中首次采用了ABB公司的基于直接转矩控制的交流多传动控制装置。
交流变频电动机和直流电动机相比,有维护简单、抗恶劣环境等优点;交流多传动控制装置的优点是采用一台四象限可逆整流单元,通过公共直流母线给系统内的每一台逆变器供电,这种系统结构紧凑,在公共直流母线上实现能量回馈,将制动状态的电动机的能量直接通过公共直流母线回馈给电动状态的电动机,实现了节能。
图二交流多传动供电示意图6.1辊道电动机控制热轧机的辊道控制是一个重要的环节,将辊道的速度和转矩控制好,可以较好地减轻辊道和带材之间发生打滑现象,减少辊道粘铝,提高带材表面质量。
6.1.1辊道电机的速度控制:辊道电机的速度有单动和联动两种方式:单动情况下,辊道电机操作手单独控制;联动情况下辊道速度和轧机主电机联动,具体给定如下:①板坯进入轧辊(咬料)前:因这时轧辊线速V0并不高,为使板坯能有一定的冲劲,须使板坯速度V in相对于轧辊有一个附加速度ΔV,以改善咬入条件,既入口侧辊道速度V in=V0+ΔV;②板坯进入轧辊(咬料)后:因为这时出口侧板坯速度有前滑,入口侧速度有后滑,所以两侧辊道速度给定不能一致,否则容易产生打滑,既入口侧辊道速度V in =k1V0(k1≤1);出口侧辊道速度V ou=k2V0(k2≥1);③增加S曲线速度给定:为减少辊道启动/停止时板坯因惯性和辊道产生打滑,在所有辊道电机速度给定斜坡发生器中设定S曲线功能,使辊道柔性启-停,抑制打滑。
6.1.2辊道电机的转矩控制:当板坯进入轧辊后,辊道电机只需克服自身运转的摩擦力,过大的转矩也会导致和板坯之间打滑,所以在咬料后对辊道的转矩Mref 进行限幅,既Mref=k3Me其中:Me为电机额定转矩(k3≤1);6.1.3辊道电机的节能控制:这台热轧机组一共有十八台辊道电动机(包括左、右夹送辊),分列轧机左右两侧。
因为热轧坯料长度所限,同时只有一少部分辊道在工作,所以我们在辊道上重要部位设置了若干光电检测开关,通过程序对辊道分段控制,沿轧制方向使坯料将要通过的辊道自动启动、坯料刚通过的辊道自动停止,既实现了节能,又减少了人工操作。
6.2 压下电机控制:压下电机采用两台串联方式驱动,从控制上采用主-从控制,主电机采用速度系统,从电机采用外部转矩控制;主电机的转矩输出送给从电机,作为其外部转矩控制的指令。
7 应用效果本控制系统经过在现场实际使用,技术先进、工作可靠,控制性能满足轧制工艺要求;在自动化方面,配合各种传感器,更多地采用了程序智能控制,改善了操作环境,减轻了操作人员的工作强度,提高了劳动生产率。
1400mm铝带飞剪电控系统李杰(中色科技股份有限公司,河南洛阳471039)摘要:本文主要介绍1400mm铝带飞剪机组电控系统的系统组成、系统硬件、软件设计和主要控制思想。
该系统采用ABB公司的DCS500B全数字直流传动模块和西门子公司的S7-300程控器以及FM350-1高速计数模块。
关键词:飞剪;程控器;直流传动中图分类号:TG334.9 文献标识码:B 文章编号:1671-6795(2002)06-1概述1400毫米铝带飞剪机组主要机械设备包括开卷机、夹送辊、矫直机、测量辊、送料辊、飞剪、皮带运输机和垛板机等。
剪切宽度1200毫米;剪切厚度1.0~4.0毫米;剪切长度0.5~4米;最大剪切速度60米/分。
要求板材长度误差(剪切精度)在±1毫米之内。
电控系统的核心部分是飞剪剪刃的位置和速度控制。
2电控系统组成飞剪电气传动控制系统如图1所示。
图1 飞剪电控系统示意图2.1 直流传动控制系统采用ABB公司的DCS500B四象限全数字传动控制模块。
2.2 交流传动控制系统皮带运输机采用ABB公司的ACS401变频器。
2.3可编程程控器采用一套SIEMENS公司的S7-300程控器(CPU为318-2),具有高速浮点运算功能。
2.4计数模块采用SIEMENS公司的FM350-1高速计数单元。
2.5人机界面采用SIEMENS 公司的TP27-10彩色液晶触摸屏。
2.6 通讯控制系统采用PROFIBUS-DP 现场总线技术,实现对所有ABB 直流传动模块以及可编程序控制器远程子站的控制。
3 飞剪控制原理带材经过开卷机、夹送辊、矫直机,由送料辊匀速送入飞剪本体。
飞剪剪刃由上下两个摆臂同步带动两个剪刃沿带材运行方向做周期性圆周运动。
如图2所示,以上、下剪刃分别在最上、最下点作为初始点A ,在上、下剪刃分别到达最下、最上点时啮合,完成剪切工作这一点作为剪切点S ,带材在剪刃两次经过剪切点S 期间走过的距离就是剪切长度。
要完成剪切,剪刃和送料辊运行须满足下列约束条件:m b a o L .L L L 50=++o b a l .l l 50=+o m b a V /L T T 2≤+o b V V =a b aT V =a b aL V 22=b b b T V L =式中 L O ——剪刃启动前带材走过的长度;L a 、T a ——带材在剪刃从A点加速至B 点期间走过的长度及所用时间;L b 、T b ——带材在剪刃从B 点匀速运行到剪切点S期间走过的长度及所用时间; L m ——预定的剪切长度;l a 、l b ——剪刃加速段和稳速运行到剪切点S 所走过的弧长;l O ——剪刃完成一次闭环运行所走过的圆周长;V b ——剪刃到达剪切点前匀速运行的速度;V 0——带材匀速运行的速度;a ——剪刃加速度。
图2 剪切示意图(上剪刃及带材)从上述条件和示意图可以得出以下结论:①必须保证剪刃在到达剪切点S时和带材的速度保持同步,这是保证剪切精度和不损坏剪刃的首要条件;②剪刃在剪切时走过一个圆周长所用时间总和必须小于带材匀速走过一个剪切长度所用的时间。
4软件系统本系统控制软件由以下三块组成:4.1 ABB直流传动系统采用GAD图形化编程语言编程。
主要应用软件功能:开卷机卷径、张力、动态补偿、空载补偿计算;矫直机、送料辊及剪刃速度给定。
4.2可编程控制器采用STEP7编程软件平台编制;采用了LAD、FBD和STL三种方式编程;采用OB组织块和FC功能块相结合的模式。
程序主要完成以下功能:①主程序块:完成系统程序调用,现场总线控制;②定时中断块:检测剪刃和带材位置,完成剪刃闭环速度控制,完成矫直机和送料辊速度检测;③功能块:完成剪刃启动、减速位置计算;直流传动模块的通讯控制;泵站启、停控制及机组程序控制。