连铸保护渣自动给料机驱动系统改进
基于自适应控制的连铸自动加保护渣机器人系统
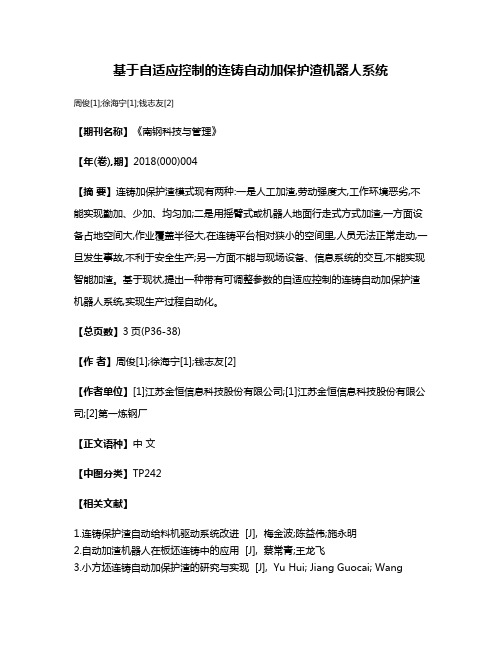
基于自适应控制的连铸自动加保护渣机器人系统
周俊[1];徐海宁[1];钱志友[2]
【期刊名称】《南钢科技与管理》
【年(卷),期】2018(000)004
【摘要】连铸加保护渣模式现有两种:一是人工加渣,劳动强度大,工作环境恶劣,不能实现勤加、少加、均匀加;二是用摇臂式或机器人地面行走式方式加渣,一方面设备占地空间大,作业覆盖半径大,在连铸平台相对狭小的空间里,人员无法正常走动,一旦发生事故,不利于安全生产;另一方面不能与现场设备、信息系统的交互,不能实现智能加渣。
基于现状,提出一种带有可调整参数的自适应控制的连铸自动加保护渣机器人系统,实现生产过程自动化。
【总页数】3页(P36-38)
【作者】周俊[1];徐海宁[1];钱志友[2]
【作者单位】[1]江苏金恒信息科技股份有限公司;[1]江苏金恒信息科技股份有限公司;[2]第一炼钢厂
【正文语种】中文
【中图分类】TP242
【相关文献】
1.连铸保护渣自动给料机驱动系统改进 [J], 梅金波;陈益伟;施永明
2.自动加渣机器人在板坯连铸中的应用 [J], 蔡常青;王龙飞
3.小方坯连铸自动加保护渣的研究与实现 [J], Yu Hui; Jiang Guocai; Wang
Zhuhong; HuangZhenghua; Hu Xinyu
4.连铸结晶器保护渣自动添加系统设计 [J], 刘春晖;牟辉龙;张政;黄存款;王立强;杨军坤
5.板坯连铸结晶器保护渣自动加渣技术的探讨 [J], 王莹叶;李保才;王伟
因版权原因,仅展示原文概要,查看原文内容请购买。
炼钢过程中的连铸技术改进与优化

炼钢过程中的连铸技术改进与优化随着现代工业的快速发展,钢铁行业在全球范围内扮演着重要的角色。
炼钢是制造钢材的关键过程之一,而连铸技术在炼钢过程中的应用越来越广泛。
本文将探讨炼钢过程中连铸技术的改进与优化措施,以提高钢材质量和生产效率。
一、连铸技术的基本原理与流程连铸技术是指将炼钢炉中液态钢水直接注入连铸机中,通过结晶器的作用,使其快速凝固为连续坯料。
基本上,连铸技术分为结晶器区、中间区和加热区三个部分。
结晶器区是最重要的部分,其作用是促使钢水迅速凝固形成坯料。
中间区则起到支撑坯料并保持其形状的作用,加热区则用来提供所需的坯料温度。
二、连铸技术改进的原因尽管连铸技术已经成为钢铁生产中主要的浇铸方法,但仍然存在一些问题和潜在的改进空间。
首先,连铸坯料的质量不稳定是一个重要问题。
由于熔铸过程中的各种因素,如温度、流速、结晶器形状等,坯料的结构和性能可能会出现变化。
这导致了产品的不均匀性和不稳定性。
其次,连铸过程中易产生气孔和夹杂物的问题也需要解决。
气孔和夹杂物对钢材的力学性能和外观质量有着显著影响。
此外,传统的连铸技术在能源消耗和生产效率方面也存在一些局限。
例如,冷却设备和传输系统的耗能较高,同时生产线上的工作效率较低。
因此,为了改进钢铁行业的连铸技术,提高生产效率和产品质量,钢铁企业已经采取了一系列的措施。
三、连铸技术改进与优化措施1. 结晶器改进结晶器是连铸技术中最关键的部分,对坯料质量起到决定性的作用。
通过改进结晶器的设计和材料,可以提高坯料的凝固性能和整体质量。
现代连铸技术使用先进的结晶器涂层和陶瓷材料,以减少坯料表面张力和增加热传导率。
此外,优化结晶器的几何形状和冷却系统,可以提高坯料的结晶行为和熔体流动性。
2. 连铸过程控制技术连铸过程中的温度、流速和加热条件等参数对坯料质量有着直接的影响。
通过引入先进的控制技术,如自动化控制系统和实时监测装置,可以实现对连铸过程的精细控制和优化。
自动化系统可以实时监测和调整炉温、浇注速度和结晶器温度等参数,以确保坯料的一致性和质量。
小方坯连铸自动加保护渣的研究与实现
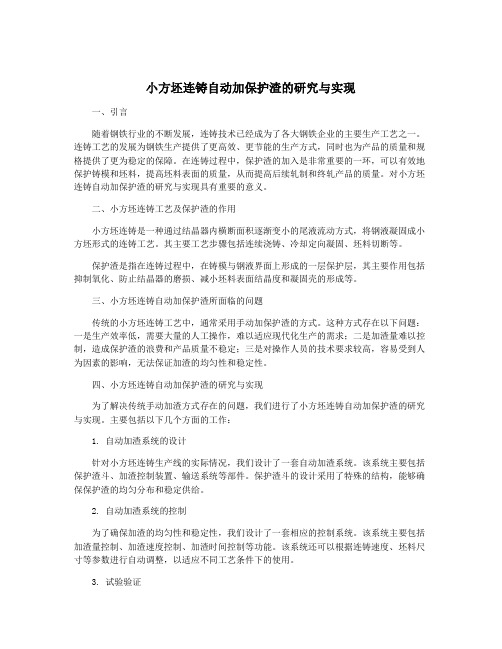
小方坯连铸自动加保护渣的研究与实现一、引言随着钢铁行业的不断发展,连铸技术已经成为了各大钢铁企业的主要生产工艺之一。
连铸工艺的发展为钢铁生产提供了更高效、更节能的生产方式,同时也为产品的质量和规格提供了更为稳定的保障。
在连铸过程中,保护渣的加入是非常重要的一环,可以有效地保护铸模和坯料,提高坯料表面的质量,从而提高后续轧制和终轧产品的质量。
对小方坯连铸自动加保护渣的研究与实现具有重要的意义。
二、小方坯连铸工艺及保护渣的作用小方坯连铸是一种通过结晶器内横断面积逐渐变小的尾液流动方式,将钢液凝固成小方坯形式的连铸工艺。
其主要工艺步骤包括连续浇铸、冷却定向凝固、坯料切断等。
保护渣是指在连铸过程中,在铸模与钢液界面上形成的一层保护层,其主要作用包括抑制氧化、防止结晶器的磨损、减小坯料表面结晶度和凝固壳的形成等。
三、小方坯连铸自动加保护渣所面临的问题传统的小方坯连铸工艺中,通常采用手动加保护渣的方式。
这种方式存在以下问题:一是生产效率低,需要大量的人工操作,难以适应现代化生产的需求;二是加渣量难以控制,造成保护渣的浪费和产品质量不稳定;三是对操作人员的技术要求较高,容易受到人为因素的影响,无法保证加渣的均匀性和稳定性。
四、小方坯连铸自动加保护渣的研究与实现为了解决传统手动加渣方式存在的问题,我们进行了小方坯连铸自动加保护渣的研究与实现。
主要包括以下几个方面的工作:1. 自动加渣系统的设计针对小方坯连铸生产线的实际情况,我们设计了一套自动加渣系统。
该系统主要包括保护渣斗、加渣控制装置、输送系统等部件。
保护渣斗的设计采用了特殊的结构,能够确保保护渣的均匀分布和稳定供给。
2. 自动加渣系统的控制为了确保加渣的均匀性和稳定性,我们设计了一套相应的控制系统。
该系统主要包括加渣量控制、加渣速度控制、加渣时间控制等功能。
该系统还可以根据连铸速度、坯料尺寸等参数进行自动调整,以适应不同工艺条件下的使用。
3. 试验验证在设计完成后,我们进行了一系列的试验验证。
小方坯连铸自动加保护渣的研究与实现
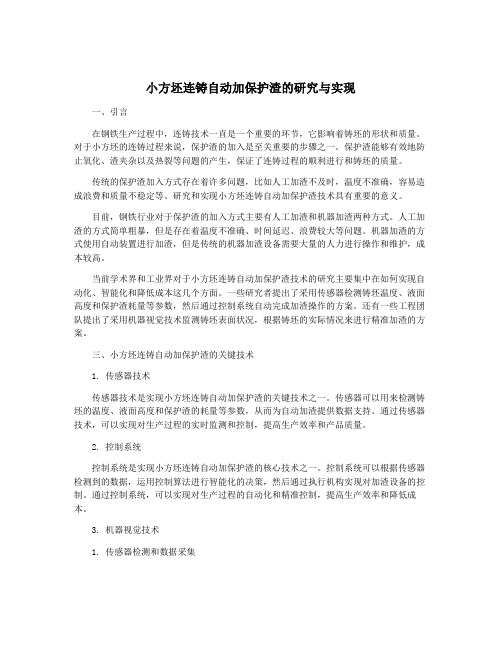
小方坯连铸自动加保护渣的研究与实现一、引言在钢铁生产过程中,连铸技术一直是一个重要的环节,它影响着铸坯的形状和质量。
对于小方坯的连铸过程来说,保护渣的加入是至关重要的步骤之一。
保护渣能够有效地防止氧化、渣夹杂以及热裂等问题的产生,保证了连铸过程的顺利进行和铸坯的质量。
传统的保护渣加入方式存在着许多问题,比如人工加渣不及时,温度不准确,容易造成浪费和质量不稳定等。
研究和实现小方坯连铸自动加保护渣技术具有重要的意义。
目前,钢铁行业对于保护渣的加入方式主要有人工加渣和机器加渣两种方式。
人工加渣的方式简单粗暴,但是存在着温度不准确、时间延迟、浪费较大等问题。
机器加渣的方式使用自动装置进行加渣,但是传统的机器加渣设备需要大量的人力进行操作和维护,成本较高。
当前学术界和工业界对于小方坯连铸自动加保护渣技术的研究主要集中在如何实现自动化、智能化和降低成本这几个方面。
一些研究者提出了采用传感器检测铸坯温度、液面高度和保护渣耗量等参数,然后通过控制系统自动完成加渣操作的方案。
还有一些工程团队提出了采用机器视觉技术监测铸坯表面状况,根据铸坯的实际情况来进行精准加渣的方案。
三、小方坯连铸自动加保护渣的关键技术1. 传感器技术传感器技术是实现小方坯连铸自动加保护渣的关键技术之一。
传感器可以用来检测铸坯的温度、液面高度和保护渣的耗量等参数,从而为自动加渣提供数据支持。
通过传感器技术,可以实现对生产过程的实时监测和控制,提高生产效率和产品质量。
2. 控制系统控制系统是实现小方坯连铸自动加保护渣的核心技术之一。
控制系统可以根据传感器检测到的数据,运用控制算法进行智能化的决策,然后通过执行机构实现对加渣设备的控制。
通过控制系统,可以实现对生产过程的自动化和精准控制,提高生产效率和降低成本。
3. 机器视觉技术1. 传感器检测和数据采集通过在小方坯连铸设备中安装温度传感器、液面高度传感器和保护渣耗量传感器等,实时检测铸坯的温度、液面高度和保护渣的耗量等参数,并将数据传输给控制系统。
连铸改造完成情况汇报

连铸改造完成情况汇报尊敬的领导:我向您汇报连铸改造完成情况如下:一、项目背景。
公司连铸设备已运行多年,存在一定的老化和磨损,为提高生产效率和产品质量,公司决定进行连铸改造项目。
二、改造内容。
1. 设备更新,更换老化设备,引进先进的连铸设备,提高生产效率和产品质量。
2. 工艺优化,优化连铸工艺,提高产品成形率,减少废品率。
3. 自动化控制,引入自动化控制系统,提高生产线的智能化水平,减少人为操作对产品质量的影响。
三、改造进展。
1. 设备更新,目前已完成设备更新的采购工作,新设备已陆续到货并开始安装调试。
2. 工艺优化,优化工艺方案已经制定完成,正在进行试验验证,初步效果良好。
3. 自动化控制,自动化控制系统已经完成采购和安装,正在进行联调测试,预计很快可以投入使用。
四、改造效果。
1. 设备更新,新设备的安装调试工作进展顺利,预计可以在规定时间内完成,提高了生产线的稳定性和可靠性。
2. 工艺优化,优化后的工艺方案有效提高了产品成形率,减少了废品率,产品质量得到了明显提升。
3. 自动化控制,自动化控制系统的引入大大减少了人为操作,提高了生产线的智能化水平,降低了人力成本,提高了生产效率。
五、下一步工作。
1. 完成设备更新的安装调试工作,确保新设备的正常运行。
2. 进一步优化工艺方案,提高产品质量和生产效率。
3. 完成自动化控制系统的联调测试,确保系统稳定可靠,投入正常生产使用。
六、结语。
连铸改造项目是公司生产线升级的重要举措,经过各部门的通力合作,项目进展顺利,效果显著。
我们将继续努力,确保项目顺利完成,为公司的发展贡献力量。
谢谢!。
小方坯连铸自动加保护渣的研究与实现

DOI:10.19392/j.cnki.1671-7341.201921150小方坯连铸自动加保护渣的研究与实现于挥姜国才汪祝红黄正华胡新宇新疆八钢公司炼钢厂新疆乌鲁木齐830022摘要:第一炼钢分厂连铸150产线现有在10机10流铸机一座,在生产时使用浸入式水口保护浇铸,采用人工向结晶器内加保护渣,效率低。
浇铸高温区,职工夏季高温容易中暑,人员劳动强度大。
人工加保护渣存在不确定性,增加了保护渣的消耗,加渣的不均匀对铸坯质量也会产生不利的影响。
造成保护渣的浪费严重、影响整个铸坯的表面质量及减短结晶器铜管的在线使用寿命等。
现在通过新上10套RAMON自动加保护渣系统,控制可实现自动加渣系统,应用自动加渣系统可以提高连铸自动水平,减轻了工人劳动强度;提高钢坯的质量。
关键词:自动加渣;质量;劳动强度Research andRealization of Automatic Adding Mold Fluxin Billet Continuous CastingYu Hui Jiang Guocai Wang Zhuhong HuangZhenghua Hu XinyuXinjiang Bagang Steel making Plant Xinjiang Urumqi830022Abstract:The150production line of No.1Steelmaking Branch now has one10-machine10-strand caster.In production,the submerged nozzle is used to protect casting,and the mould is manually added with mold powder,which is inefficient.Casting high temperature area,workers in summer high temperature easy to heatstroke,Personnel Labor intensity.Now through the new10sets ofRAMON automatic slag adding system,automatic slag adding system can be realized.The application of automatic slag adding system can improve the automatic level of continuous casting,reduce the labor intensity of workers,and improve the quality of billets.Key words:Automatic slag addition;quality;labor intensity随着我国钢铁工业的发展,企业智慧制造装备水平恶的不断提升。
连铸机闭路供水系统优化

连铸机闭路供水系统优化作者:张坤杨永霞来源:《电子技术与软件工程》2015年第23期摘要根据连铸机工艺要求,需保持连铸机闭路供水系统压力稳定,而闭路水系统存在漏损和过滤器排污等情况,压力不可避免的存在波动。
传统的解决方法是增加变频补水泵,但采用变频补水泵压力控制滞后,严重时可能影响连铸机生产。
通过增加自动稳压罐装置实现对闭路水系统压力自动控制,使压力控制准确、快速,降低了设备故障率。
【关键词】稳压罐压力 PLC 液位补水京唐公司炼钢部连铸机闭路水系统包括结晶器闭路水系统和设备水闭路水系统,为保持闭路系统压力稳定,需对闭路系统进行补水。
传统的解决办法为增加变频补水泵,但使用变频补水泵存在以下两个问题。
(1)当系统出现压力波动时,变频补水泵通过改变电机转速调节水压,这种控制方式比较准确,缺点是压力检测点一般取在用户末端,使压力传感器与控制柜的距离过长,而且管道末端压力变化滞后(管道可近似为带纯滞后的一阶惯性环节),造成压力波动,严重时会直接影响连铸机生产。
(2)每当系统压力降低时补水泵就需启动,使补水泵启停频繁,设备故障率高。
为解决这一问题,京唐公司炼钢部采用了全自动稳压罐装置,实现自动补水,保持闭路系统压力稳定。
1 闭路水系统工艺流程闭路系统工艺流程如图1所示。
闭路系统中稳压罐直径3.2米,高6米,容积48M3,每个稳压罐设有两台补水泵,利用PLC实现补水泵的自动启停,氮气进气和排气阀自动开闭、泄水阀自动动作。
闭路水系统利用稳压罐、补水装置自动调节压力,自动调节补充除盐水,以补偿泄漏等损耗。
2 稳压罐PLC系统硬件设计自动补水装置主要使用的仪表设备有起的那个调节阀、磁帆板液位计、导波雷达液位计、压力变送器、触摸屏。
CPU选择的是西门子313C型,它是紧凑型的PLC,在PLC上集成了数字量和模拟量输入、输出功能。
其他硬件包括PS307电源、12点模拟量输入模块、343-1CP模块。
3 稳压罐恒压控制的实现3.1 恒压控制PID调节过程分析在该控制系统中,设定稳压罐内压力范围为0.34-0.36Mpa,然后将稳压罐内实际压力通过压力变送器,输出 4-20mA信号至PLC作为PID 调节的实际测量值(PV值)。
小方坯连铸自动加保护渣的研究与实现

小方坯连铸自动加保护渣的研究与实现随着钢铁工业的发展,小方坯连铸技术作为主要的成形方法,在钢铁生产中得到了广泛应用。
然而,在小方坯连铸过程中,常常会存在铁水脱碳、溅渣等问题,影响铸坯的质量,降低生产效率。
因此,如何加强小方坯连铸过程中的保护措施,是当前钢铁企业需要解决的问题之一。
本文以小方坯连铸保护渣自动加保护技术为研究对象,探讨了该技术的研究现状及未来的发展方向。
首先,介绍了小方坯连铸过程中存在的问题,以及保护渣的作用;其次,阐述了小方坯连铸自动加保护渣的原理和实现方法;最后,探讨了该技术的发展趋势和应用前景。
一、小方坯连铸中的问题及保护渣的作用小方坯连铸是一种常见的钢铁成形方法,其优点在于可以生产出品质高、成本低、生产效率高的钢铁产品。
小方坯连铸的流程图如下所示:【图片】在小方坯连铸过程中,常常会存在以下问题:(1)铁水脱碳问题较为严重,严重影响铸坯的质量;(2)连铸过程中容易产生溅渣,渣皮太薄,翻转后容易坍塌,影响生产效率和产品质量;(3)保护措施不够严密,温控不稳定等问题,影响冶炼质量和生产效率。
2、保护渣的作用保护渣是指在连铸过程中,将一层渣浆覆盖在铸坯表面,起到保温、保护、减少氧化、保持温度稳定等作用的一种材料。
保护渣的主要作用如下:(1)保温保护:保护渣可以起到保温保护的作用,避免连铸时铁水受外界影响而影响铸坯质量。
(2)减少氧化:保护渣可以对铸坯表面进行覆盖,减少氧气与液态铁的接触,防止氧化作用,从而保证铸坯质量。
(3)保持温度稳定:保护渣可以起到保持温度稳定的作用,维持适宜的冷却速度,避免产生裂纹等问题。
1、自动加保护渣的原理(1)设置加保护渣设备:通过设置加保护渣设备,实现对铸坯表面进行覆盖。
(2)控制保护渣的加入量:通过控制保护渣的加入量,保证渣层的厚度和质量。
(3)实现保温、保护、减少氧化和保持温度稳定的作用:通过加保护渣的方式,实现保温、保护、减少氧化和保持温度稳定等作用,从而保证产品质量。
连铸机铸流控制系统升级及功能优化的方法

连铸机铸流控制系统升级及功能优化的方法苏钢1#连铸机铸流PLC控制系统采用德国西门子公司生产的S5系列产品,经过十几年的运行,设备趋于老化。
随着S5系统逐渐被淘汰,大多CPU和信号模块已经不再生产,不可避免地遇到了备件价格昂贵、供货时间长、维修成本高等问题,为此公司决定于2015年5月对该连铸机铸流PLC系统进行升级改造。
标签:S7控制系统;电动调节阀;变频器1 概述1#连铸机铸流控制系统中,主站原采用双机架结构:主机架由S5 CPU 928、CP143通讯模块、WF706计数模块、4块AI 466模拟量输入模块、3块AO 470模拟量输出模块、7块DI 430数字量输入模块、以及EG300扩展模块构成;扩展机架由4块DO 451数字量输出模块、3块DO 454数字量输出模块、以及ZG-AS 312扩展模块构成。
升级改造后的新硬件系统,主机架由S7 CPU 416、CP443通讯模块、FM450计数模块、4块A0 431模拟量输出模块、7块DI 421数字量输入模块、以及IM460扩展模块构成;扩展机架由4块DO 422数字量输出模块、2块AI 432模拟量输入模块、以及IM461扩展模块构成。
现上位机采用Wincc 监控软件,上位机与PLC之间通过以太网进行通讯。
2 系统中一些主要的功能优化2.1 二次冷却水控制调节阀优化连铸热坯采用气水雾化冷却,这种冷却方式,需要对冷却水的流量进行精确调节。
原S5系统采用萨姆森电液调节阀结合ABB电磁流量计实现闭环控制。
基本工作原理是:ABB电磁流量计测量实际水流量,S5程序中将实际流量与目标流量进行比较,若在死区范围外,则根据实际流量是大于或是小于目标值,输出关闭或是打开的脉冲信号给中间继电器,从而再控制调节阀的动作,直至实际流量值进入死区范围内。
但是使用经验证明,此套调节系统存在以下这些问题:控制设备都是进口产品,且连铸二冷区共有45套,维护更换成本高;控制存在死区,精度不高;存在中间继电器,线路较多,增多了故障点;缺少现场手动功能,紧急情况只能通过程序中手动模式控制动作。
小方坯连铸自动加保护渣的研究与实现

小方坯连铸自动加保护渣的研究与实现【摘要】本文研究了小方坯连铸自动加保护渣的方法,通过分析连铸过程中存在的问题,提出了自动加保护渣方案和保护渣的优化设计。
通过实验验证,结果表明自动加保护渣能够有效提高铸坯表面质量,减少表面缺陷。
数据分析结果显示,自动加保护渣对铸坯品质有显著影响。
研究成果表明这种方法具有实际应用价值,未来可以进一步优化设计,提高连铸工艺效率和产品质量。
本研究为小方坯连铸自动加保护渣提供了新的思路和方法,对于提升铸造工艺水平具有一定的指导意义。
【关键词】小方坯连铸、自动加保护渣、研究、连铸过程、保护渣方案、优化设计、实验、数据分析、研究成果、展望未来1. 引言1.1 研究背景小方坯连铸自动加保护渣是钢铁行业中一项重要的技术,能够提高生产效率、降低生产成本,并且可以改善产品质量。
目前,传统的连铸技术存在着一些问题,例如保护渣的添加不够精准,无法及时补充和调整,容易造成坯料表面氧化和结疤,影响坯料质量。
开展小方坯连铸自动加保护渣的研究具有重要的理论意义和实际意义。
1.2 研究目的本文旨在探讨小方坯连铸过程中存在的问题,以及针对这些问题提出的自动加保护渣的方案。
通过对保护渣的优化设计以及小方坯连铸实验的开展,旨在验证新方案的有效性和可行性。
研究的目的是为了提高连铸过程的质量和效率,减少生产中的浪费和损失,进一步推动连铸工艺的发展和应用。
本研究也旨在为相关领域的学术研究和工程实践提供新的思路和方法,为行业的进步和创新提供有力支持。
通过本文的研究,希望能够取得一些新的成果和进展,为解决连铸过程中的难题和挑战提供新的解决方案,并为未来的研究工作和发展方向提供有益的参考和借鉴。
2. 正文2.1 连铸过程中的问题在小方坯连铸过程中,存在着一些问题需要解决。
由于连铸过程中金属液体受到空气氧化的影响,容易产生氧化皮和氧化夹杂物,降低了小方坯的质量。
连铸过程中温度的控制较为复杂,需要确保金属液体在适宜的温度范围内进行连铸,以保证铸坯的均匀性和稳定性。
小方坯连铸自动加保护渣的研究与实现
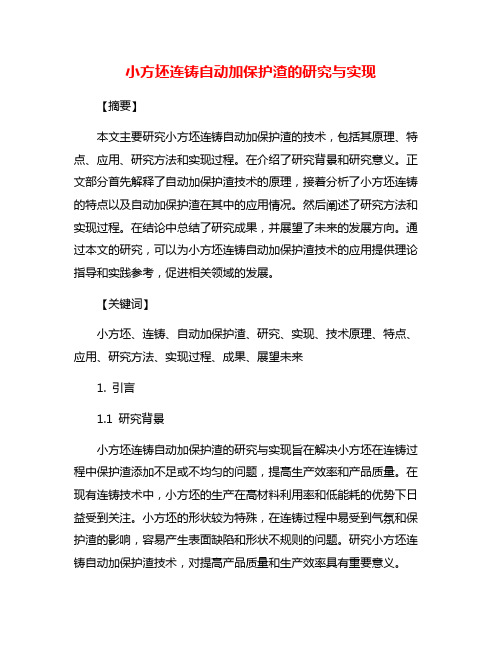
小方坯连铸自动加保护渣的研究与实现【摘要】本文主要研究小方坯连铸自动加保护渣的技术,包括其原理、特点、应用、研究方法和实现过程。
在介绍了研究背景和研究意义。
正文部分首先解释了自动加保护渣技术的原理,接着分析了小方坯连铸的特点以及自动加保护渣在其中的应用情况。
然后阐述了研究方法和实现过程。
在结论中总结了研究成果,并展望了未来的发展方向。
通过本文的研究,可以为小方坯连铸自动加保护渣技术的应用提供理论指导和实践参考,促进相关领域的发展。
【关键词】小方坯、连铸、自动加保护渣、研究、实现、技术原理、特点、应用、研究方法、实现过程、成果、展望未来1. 引言1.1 研究背景小方坯连铸自动加保护渣的研究与实现旨在解决小方坯在连铸过程中保护渣添加不足或不均匀的问题,提高生产效率和产品质量。
在现有连铸技术中,小方坯的生产在高材料利用率和低能耗的优势下日益受到关注。
小方坯的形状较为特殊,在连铸过程中易受到气氛和保护渣的影响,容易产生表面缺陷和形状不规则的问题。
研究小方坯连铸自动加保护渣技术,对提高产品质量和生产效率具有重要意义。
目前,国内外在小方坯连铸自动加保护渣方面的研究还比较薄弱,存在着许多未解决的技术问题。
本研究旨在探讨小方坯连铸自动加保护渣的技术原理,分析小方坯连铸的特点,并在实际生产中应用自动加保护渣技术,以提高生产效率和产品质量。
通过对研究方法和实现过程的分析,探讨研究成果及未来的发展方向,为小方坯连铸自动加保护渣技术的研究和应用提供参考和借鉴。
1.2 研究意义小方坯连铸自动加保护渣技术是针对小方坯连铸生产过程中出现的问题而研究开发的一项技术。
其研究意义主要体现在以下几个方面:1. 提高生产效率:传统小方坯连铸生产过程中,加保护渣需要手工操作,效率低下且存在一定的安全隐患。
引入自动加保护渣技术可以提高生产效率,减少人力成本。
2. 提高产品质量:保护渣在连铸过程中起到重要的保护作用,可以有效防止合金的氧化、减少杂质的夹杂,从而提高最终产品的质量和市场竞争力。
马钢方坯连铸机控制系统改进与优化研究

马钢方坯连铸机控制系统改进与优化研究本论文的工作来源于“马钢(合钢)股份公司第二炼钢2车间四机四流控制系统”整体改造项目。
全文介绍连铸生产过程控制系统的发展现状、工作原理和工艺组成。
对连铸控制系统进行了总体设计,四机四流按控制系统进行划分为公用系统,一至四流四个铸流系统,包括西门子PLC硬件配置、I/O从站分配、变频器从站分配、I/O地址分配、编程及软件设计等一系列细节,介绍了上位机监控组态软件WinCC系统,并且在上位机中实现分级管理操作,以便完成二次冷却水的自动配水和钢种研发拓展操作配置。
最后对系统进行了调试,满足生产的要求。
标签:方坯连铸机改进与优化一、连铸控制系统的工艺及组成各个系统的工艺及组成概述钢包回转台,是标志一台连铸水平的重要设备,主要是解决浇注钢包和等待钢包的定位问题,能根据需要调整其所在位置高度,以便实现无氧化浇注所需要的长水口的安装,用氧气管烧开结瘤的钢包浇注口,等铸机开浇时操作工顺利进行开浇操作的要求,以快速准确地达到多炉连浇的目的。
钢包回转台结构包括:上部的支撑台架,中部的驱动旋转装置,下部的底座,及在事故或掉电状态下需进行回转驱动的液压马达。
回转到浇注位置需要锁定的,还应有锁定装置,其支撑台上装有两个向两边伸出的臂,每个臂梁上各有一个钢包罐。
一只供浇注用,一只供调换用,支撑台上装有称重传感器,通过滑环传给PLC作为控制用。
支撑台台架由带有滚动轴承的齿圈支撑并在旋转台的底座上旋转,支撑台架由马达(事故状态下位液压马达)带动,可以旋转180度角。
中间包,是放在钢包和结晶器之间的中间容器,钢包内的钢水先流入中间包,然后通过中间包的浸渍式人水口流入结晶器内。
它是实现多炉连浇所必须的中间容器,中间包有一定深度,从而保证了钢水能在稳定的压力下,平稳地流入结晶器,减少注入结晶器的钢水因冲击而引起的紊流,使结晶器的钢水液面保持平稳,同时钢水在中间包内停留一段时使非金属夹杂物进一步上浮,净化了钢水,另外利用中间包在同时浇注几流铸坯时可以起着分流作用;在多炉连浇时,能存储一定数量的钢水,这样保证了连铸机多炉连浇的正常进行。
小方坯连铸自动加保护渣的研究与实现
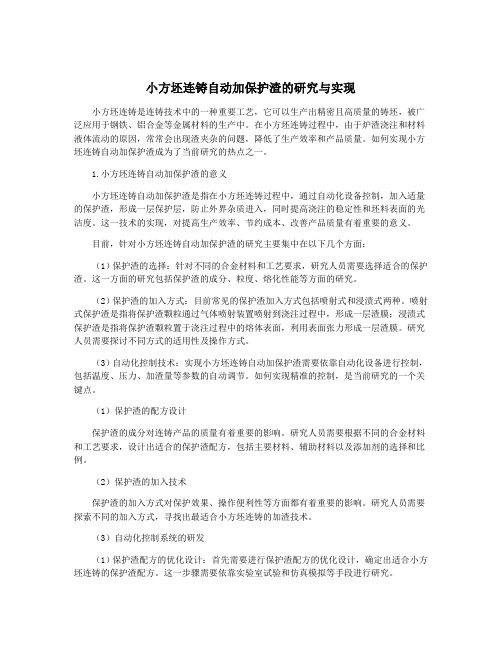
小方坯连铸自动加保护渣的研究与实现小方坯连铸是连铸技术中的一种重要工艺,它可以生产出精密且高质量的铸坯,被广泛应用于钢铁、铝合金等金属材料的生产中。
在小方坯连铸过程中,由于炉渣浇注和材料液体流动的原因,常常会出现渣夹杂的问题,降低了生产效率和产品质量。
如何实现小方坯连铸自动加保护渣成为了当前研究的热点之一。
1.小方坯连铸自动加保护渣的意义小方坯连铸自动加保护渣是指在小方坯连铸过程中,通过自动化设备控制,加入适量的保护渣,形成一层保护层,防止外界杂质进入,同时提高浇注的稳定性和坯料表面的光洁度。
这一技术的实现,对提高生产效率、节约成本、改善产品质量有着重要的意义。
目前,针对小方坯连铸自动加保护渣的研究主要集中在以下几个方面:(1)保护渣的选择:针对不同的合金材料和工艺要求,研究人员需要选择适合的保护渣。
这一方面的研究包括保护渣的成分、粒度、熔化性能等方面的研究。
(2)保护渣的加入方式:目前常见的保护渣加入方式包括喷射式和浸渍式两种。
喷射式保护渣是指将保护渣颗粒通过气体喷射装置喷射到浇注过程中,形成一层渣膜;浸渍式保护渣是指将保护渣颗粒置于浇注过程中的熔体表面,利用表面张力形成一层渣膜。
研究人员需要探讨不同方式的适用性及操作方式。
(3)自动化控制技术:实现小方坯连铸自动加保护渣需要依靠自动化设备进行控制,包括温度、压力、加渣量等参数的自动调节。
如何实现精准的控制,是当前研究的一个关键点。
(1)保护渣的配方设计保护渣的成分对连铸产品的质量有着重要的影响。
研究人员需要根据不同的合金材料和工艺要求,设计出适合的保护渣配方,包括主要材料、辅助材料以及添加剂的选择和比例。
(2)保护渣的加入技术保护渣的加入方式对保护效果、操作便利性等方面都有着重要的影响。
研究人员需要探索不同的加入方式,寻找出最适合小方坯连铸的加渣技术。
(3)自动化控制系统的研发(1)保护渣配方的优化设计:首先需要进行保护渣配方的优化设计,确定出适合小方坯连铸的保护渣配方。
一种高效气动驱流器的改进设计

一种高效气动驱流器的改进设计本文是以原有的驱流器为研究对象,利用自动输送技术与气体驱动技术,设计改进的一个高效气动驱流器,它能防止连铸结晶器保护渣自动加渣时管路物料的脉冲和反冲现象,减少了出口处扬尘和对环境的污染,并且提高了驱流器的驱流能力。
标签:气动高效驱流器1 概述连铸结晶器保护渣是连铸生产过程中必不可少的材料之一。
在浇注過程中保护渣给料是否均匀和是否符合炼钢工艺要求,直接影响着钢坯质量和结晶器的寿命。
但是目前的保护渣给料多数是由人工完成,往往由于人为因素带来加料不均匀、渣料浪费严重、粉尘严重污染环境等弊端,同时稍有疏忽就可能造成结晶器损坏和影响钢坯质量,造成了企业的损失。
连铸结晶器保护渣自动给料[1]机实现了由自动加料代替了人工加料,能满足连铸工艺的要求,达到了稳定钢坯的质量,安全可靠和洁净环境的目的[2][3]。
在该给料装置中,是通过气动驱流器来把物料通过管路输送到结晶器表面的,工作原理如图1所示,但该驱流器在使用时,由于管路阻力随工况的不同一直变化,导致保护渣在属性过程管路中产生脉冲,甚至发生反冲现象;使得出料口有扬尘,并且驱流能力不高。
基于这些问题,本文对该驱流器的关键部位喷嘴进行改进设计。
■图1 驱流器工作原理示意图2 拉瓦尔喷嘴的设计原驱流器喷嘴为一个压缩管,为提高进气速度和压力,将喷嘴由压缩管改成拉瓦尔喷嘴的形式,使在一开始就得到一个比较理想的气体速度和压力。
拉瓦尔喷嘴是一个收缩—扩张型喷嘴。
通过此喷嘴能够使具有一定压力及较低速度的气体产生超音速流[4],如图2所示拉瓦尔喷嘴的结构示意图。
■图2 拉瓦尔喷嘴结构示意图用一维等熵流动来研究其内部流动[5][6]。
由一维恒定等熵流动的基本方程组可以得出喷管内表面直径的变化规律:d=dc×■(1)A=Ac×■■+[1+■M■(x)]■(2)式中:dc,Ac——喉口直径,截面积;d,A——任意截面的直径,截面积;M(x)——任意截面的马赫数;γ——绝热指数,空气一般取1.4。
连铸坯热装热送系统的自动化控制策略改进

连铸坯热装热送系统的自动化控制策略改进随着工业技术的发展,连铸坯热装热送系统在钢铁生产中扮演着重要的角色。
作为钢铁生产流程中的关键环节,该系统的稳定性和自动化水平直接影响到产品质量和生产效率。
本文将探讨连铸坯热装热送系统的自动化控制策略改进,以提高系统的稳定性和生产效率。
1. 概述连铸坯热装热送系统主要由热装车、热装机旋转台、热装机、运输链板等组成。
其主要功能是将铸造的热坯从连铸机上取下,运送至下一个工序。
为了提高热坯运输的效率和减少人为误差,自动化控制策略的改进显得尤为重要。
2. 自动化控制策略改进2.1 传感器优化在连铸坯热装热送系统中,传感器的作用十分关键。
通过对关键位置的传感器进行优化,可以实时监测系统各个环节的温度、压力、位置等参数,为自动化控制提供准确的数据支持。
同时,传感器的优化还可以提高其灵敏度和稳定性,从而避免因传感器故障导致的生产事故。
2.2 控制算法改进系统的控制算法直接决定了自动化控制的效果。
通过改进控制算法,可以实现更加精准和高效的控制。
例如,可以采用模糊控制算法、遗传算法等现代控制方法,提高系统对温度、速度、位置等参数的自适应性和优化控制能力。
同时,还可以引入先进的控制技术,如神经网络控制、模型预测控制等,实时调整控制策略,以确保系统运行的稳定性和可靠性。
2.3 互联网技术应用随着互联网技术的快速发展,将其应用于连铸坯热装热送系统的自动化控制中,将会带来巨大的改变。
通过互联网技术,可以实现系统的远程监控和远程控制,提高生产管理的效率和精确性。
此外,还可以通过数据采集与分析,实现对系统性能的全面监控和分析,帮助优化系统参数,提高生产效率和产品质量。
3. 改进效果与展望经过以上的自动化控制策略改进,连铸坯热装热送系统的稳定性和生产效率得到了大幅提升。
通过传感器优化、控制算法改进和互联网技术应用,系统能够更加准确和稳定地控制坯料的温度、位置和速度等参数,减少了生产事故的风险,提高了生产效率和产品质量。
连铸坯热装热送系统的自动化控制策略优化技术改进
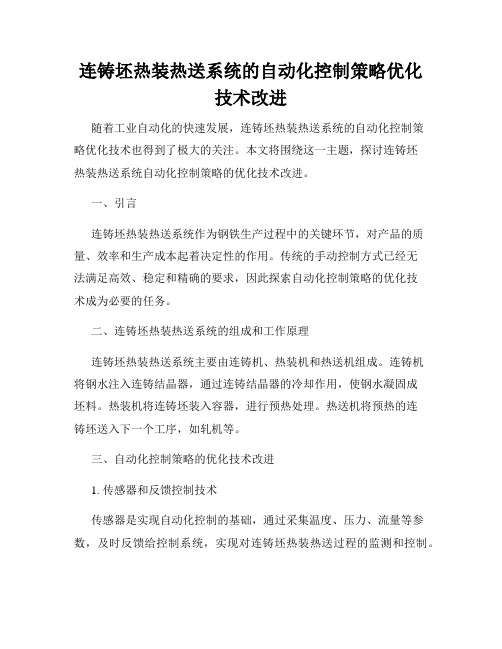
连铸坯热装热送系统的自动化控制策略优化技术改进随着工业自动化的快速发展,连铸坯热装热送系统的自动化控制策略优化技术也得到了极大的关注。
本文将围绕这一主题,探讨连铸坯热装热送系统自动化控制策略的优化技术改进。
一、引言连铸坯热装热送系统作为钢铁生产过程中的关键环节,对产品的质量、效率和生产成本起着决定性的作用。
传统的手动控制方式已经无法满足高效、稳定和精确的要求,因此探索自动化控制策略的优化技术成为必要的任务。
二、连铸坯热装热送系统的组成和工作原理连铸坯热装热送系统主要由连铸机、热装机和热送机组成。
连铸机将钢水注入连铸结晶器,通过连铸结晶器的冷却作用,使钢水凝固成坯料。
热装机将连铸坯装入容器,进行预热处理。
热送机将预热的连铸坯送入下一个工序,如轧机等。
三、自动化控制策略的优化技术改进1. 传感器和反馈控制技术传感器是实现自动化控制的基础,通过采集温度、压力、流量等参数,及时反馈给控制系统,实现对连铸坯热装热送过程的监测和控制。
优化技术改进的关键在于选择合适的传感器,并进行准确可靠的数据采集。
2. 模型预测控制技术模型预测控制技术是一种基于数学模型的优化控制方法,通过预测系统的状态和性能,优化控制策略的参数。
在连铸坯热装热送系统中,通过建立准确的数学模型,预测连铸坯的温度、形状和质量等参数,以实现系统的优化控制。
3. 协调控制技术连铸坯热装热送系统涉及多个子系统的协调工作,如连铸机、热装机和热送机的协调控制。
优化技术改进的关键在于建立系统仿真模型,通过协调控制策略,对不同子系统之间的关系进行优化调整,以提高系统的生产效率和质量。
4. 自适应控制技术自适应控制技术可以根据系统的实际运行状况和外部环境变化,自动调整控制策略的参数。
在连铸坯热装热送系统中,考虑到钢水的温度、浓度和流速等参数会发生变化,自适应控制技术可以根据实时数据,及时调整控制策略,确保系统的稳定性和可靠性。
四、总结连铸坯热装热送系统的自动化控制策略优化技术改进是钢铁生产过程中重要的研究方向。
小方坯连铸自动加保护渣的研究与实现
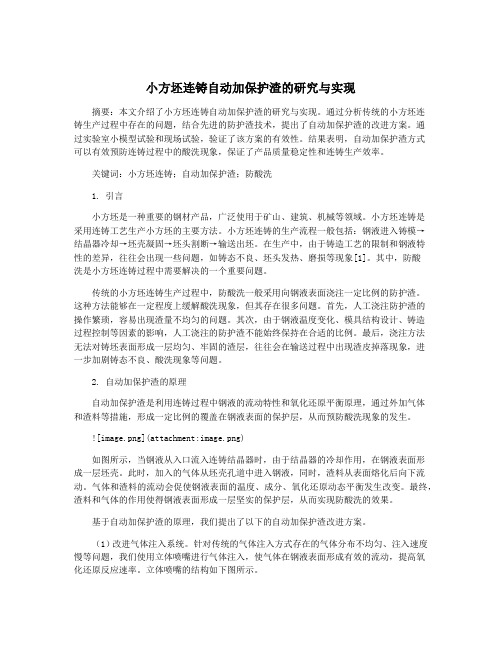
小方坯连铸自动加保护渣的研究与实现摘要:本文介绍了小方坯连铸自动加保护渣的研究与实现。
通过分析传统的小方坯连铸生产过程中存在的问题,结合先进的防护渣技术,提出了自动加保护渣的改进方案。
通过实验室小模型试验和现场试验,验证了该方案的有效性。
结果表明,自动加保护渣方式可以有效预防连铸过程中的酸洗现象,保证了产品质量稳定性和连铸生产效率。
关键词:小方坯连铸;自动加保护渣;防酸洗1. 引言小方坯是一种重要的钢材产品,广泛使用于矿山、建筑、机械等领域。
小方坯连铸是采用连铸工艺生产小方坯的主要方法。
小方坯连铸的生产流程一般包括:钢液进入铸模→结晶器冷却→坯壳凝固→坯头割断→输送出坯。
在生产中,由于铸造工艺的限制和钢液特性的差异,往往会出现一些问题,如铸态不良、坯头发热、磨损等现象[1]。
其中,防酸洗是小方坯连铸过程中需要解决的一个重要问题。
传统的小方坯连铸生产过程中,防酸洗一般采用向钢液表面浇注一定比例的防护渣。
这种方法能够在一定程度上缓解酸洗现象,但其存在很多问题。
首先,人工浇注防护渣的操作繁琐,容易出现渣量不均匀的问题。
其次,由于钢液温度变化、模具结构设计、铸造过程控制等因素的影响,人工浇注的防护渣不能始终保持在合适的比例。
最后,浇注方法无法对铸坯表面形成一层均匀、牢固的渣层,往往会在输送过程中出现渣皮掉落现象,进一步加剧铸态不良、酸洗现象等问题。
2. 自动加保护渣的原理自动加保护渣是利用连铸过程中钢液的流动特性和氧化还原平衡原理,通过外加气体和渣料等措施,形成一定比例的覆盖在钢液表面的保护层,从而预防酸洗现象的发生。
如图所示,当钢液从入口流入连铸结晶器时,由于结晶器的冷却作用,在钢液表面形成一层坯壳。
此时,加入的气体从坯壳孔道中进入钢液,同时,渣料从表面熔化后向下流动。
气体和渣料的流动会促使钢液表面的温度、成分、氧化还原动态平衡发生改变。
连铸生产装备自动智能化升级探讨
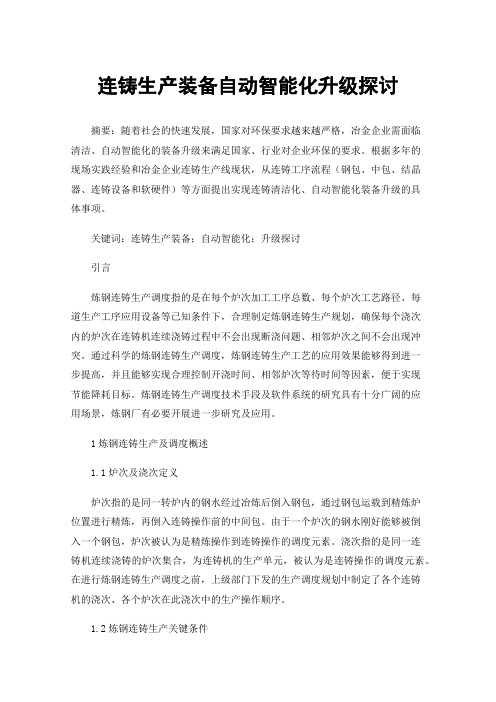
连铸生产装备自动智能化升级探讨摘要:随着社会的快速发展,国家对环保要求越来越严格,冶金企业需面临清洁、自动智能化的装备升级来满足国家、行业对企业环保的要求。
根据多年的现场实践经验和冶金企业连铸生产线现状,从连铸工序流程(钢包、中包、结晶器、连铸设备和软硬件)等方面提出实现连铸清洁化、自动智能化装备升级的具体事项。
关键词:连铸生产装备;自动智能化;升级探讨引言炼钢连铸生产调度指的是在每个炉次加工工序总数、每个炉次工艺路径、每道生产工序应用设备等已知条件下,合理制定炼钢连铸生产规划,确保每个浇次内的炉次在连铸机连续浇铸过程中不会出现断浇问题、相邻炉次之间不会出现冲突。
通过科学的炼钢连铸生产调度,炼钢连铸生产工艺的应用效果能够得到进一步提高,并且能够实现合理控制开浇时间、相邻炉次等待时间等因素,便于实现节能降耗目标。
炼钢连铸生产调度技术手段及软件系统的研究具有十分广阔的应用场景,炼钢厂有必要开展进一步研究及应用。
1炼钢连铸生产及调度概述1.1炉次及浇次定义炉次指的是同一转炉内的钢水经过冶炼后倒入钢包,通过钢包运载到精炼炉位置进行精炼,再倒入连铸操作前的中间包。
由于一个炉次的钢水刚好能够被倒入一个钢包,炉次被认为是精炼操作到连铸操作的调度元素。
浇次指的是同一连铸机连续浇铸的炉次集合,为连铸机的生产单元,被认为是连铸操作的调度元素。
在进行炼钢连铸生产调度之前,上级部门下发的生产调度规划中制定了各个连铸机的浇次、各个炉次在此浇次中的生产操作顺序。
1.2炼钢连铸生产关键条件炼钢连铸生产的关键条件为确保每个浇次内的炉次在连铸机连续浇铸,即每个浇次内的相邻炉次之间的生产时间间隔为零;需要在上一炉次生产作业结束后,才能够允许下一炉次进行生产作业。
如果炼钢连铸生产过程未能满足上述两个条件中的任意一个,便可能会导致大型炼钢厂事故。
1.3炼钢连铸生产调度需求可以得知炼钢连铸生产调度工作需要围绕上述两个约束条件展开,在此基础上确定生产调度性能指标。
- 1、下载文档前请自行甄别文档内容的完整性,平台不提供额外的编辑、内容补充、找答案等附加服务。
- 2、"仅部分预览"的文档,不可在线预览部分如存在完整性等问题,可反馈申请退款(可完整预览的文档不适用该条件!)。
- 3、如文档侵犯您的权益,请联系客服反馈,我们会尽快为您处理(人工客服工作时间:9:00-18:30)。
1 故 障分 析
杭 钢转 炉 厂 1 连 铸 机 自动 给料 机 原 先 的驱 号
动机构 是 步进 电机 , 驱 动形 式 在使 用 中经 常 出现 该
给 料 斗 卡死 、 机烧 坏 、 电 步进 电 机控 制 器 故 障等 问 题 , 重 影 响该 自动 给料 机 的正 常 使 用 , 对 其 进 严 在
摆动气 缸 ) 成 运行 工 况 所 需用 气 量 , 完 同时 考 虑 管
空气 的温 度 为 2  ̄ t 自 由状 态 空 气 的温 度 为 0C; o为
2  ̄ 0C
道漏损 , 动 元件 磨 损 损耗 、 同元 件 的使 用频 率 气 不 等工作状 况 。杭 钢转炉 厂 1} ≠连铸机 是 四机 四流形 式 的 , 以共 有 四 只摆 动气 缸 单 独工 作 , 先计 算 所 首
每个摆 动气缸 所需要 的最 大 自由空气量 ( 力 P = 压 o
所 以每只摆动气缸所需要的最大 自由空气量为 : Q :Q ×( +1 03×l5 ×(7 o / (7 o H . 1 O ) 2 3+t [ 23 ) +t)×1 0 3× l s H 1 O ]:3 . 0 2 7 4×1 3×( O O O+ 0— 6 OO
温 度 范 围
叶 片 式摆 动 气缸 D M一4 —2 0 S 0 7 一P—C C +0 m 4m l br o a
一1 0~8 ℃ 0
2 连铸 平 台现场 平 均温 度高 达 6 ) 0~7 ℃ , 尘 0 多 埃 、 动 等恶 劣 环 境 , 振 步进 电机 及 其 控 制 器 长期 此
3气 压 传 动 以 压 缩 空 气 为 工 作 介 质 ,பைடு நூலகம்本 低 , ) 成
气动 动 作 迅 速 , 应 快 , 污 染 , 动 系 统 维 护 简 反 无 气
单。 2 1 驱 动机 构选 择 .
给料 机 的驱 动 机 构 起 到 驱 动 料 斗转 动加 料 的 功能 , 不改 变原 主体结 构 的情 况 下选 择摆 动 气 缸 在 替代 步进 电机 作为 给料 机 的驱动 机构 。 根据 以往 现场 使用 经验 , 料机 主 体设 计 所 需 给 要传递 的扭 矩要 大 于 1N 且 考 虑 到额 外 的 负 载 0 m, 影 响 , 择 德 国 F S O公 司生 产 的一 款摆 动气 缸作 选 ET
扭 矩 ( b r时 ) 6a
16 c 3 18m
2N 0 m
最大许用摆动频率
07 z .H
替代 原步 进 电机 传 动 形 式 。 这 主要 有 以 下几 个 好
处:
由表 1 知 该 摆 动 气 缸 输 出 扭 矩 为 :0 m 大 可 2N
1气压 传动 工作 环境 适 应性 好 , 别 是 在 钢 厂 ) 特 这种 高 温 、 燃 、 爆 、 易 易 多尘 埃 、 动等 恶 劣环 境 下 振
2 气 压 传 动 能 使 给 料 机 主体 结 构及 控 制 简 单 )
化。
连铸结 晶器 自动加保 护 渣 , 连铸 工 艺 中 的新 是
型工 艺设 备 , 有 减 轻工 人 劳 动 强 度 , 免 加 料 不 具 避 均匀 、 稳 定 , 少 粉 尘危 害 , 少 拉漏 , 效 保 证 不 减 减 有 铸 坯质 量 等优 点 。 目前 转 炉 厂 在 线 使 用 的 保 护 渣 自动 给 料 机 , 于 工 作 环 境 差 、 用 频 率 高 、 障 由 使 故 多 、 修成本 大 , 维 急需 对其 改进 。
料 机 已经在 转 炉 炼钢 厂 1 号连铸 机 上投 入 运行 , 运行 结果表 明该 气动 系统 工作 性 能稳 定 、 靠 , 可 且
维护 简单 。 关键 词 : 铸机 ; 连 结晶 器 ; 给料 机 ; 气动 系统 选择 气压 传 动有利 于 系统运 行可 靠 。
0 H 吾 J I
20 1 第 期 0 年1月 四 1
江 全
1 9
连 铸 保 护 渣 自动 给 料 机 驱 动 系 统 改 进
梅 金 波 陈益 伟 施 永 明
( 4钢 铁 集 团公 司 转 炉 厂 杭 ' I 1 杭 州 30 2 ) 10 2
摘
要: 杭钢 转 炉 1号连铸 机 结 晶器保护 渣 自动给 料 机 , 不适合 连铸 高温 多尘的作 业环 境 , 进行 比较 分析 在 后 改用 气动驱 动 方式 。总 结 了 自动给 料机 气动 系统 的设 计 , 元件 选型 。驱 动 系统 改进 后 的 自动给
.
110 ) 110 0 30 / 030:0 2 6 m3 2 4 /mi
.
103×15 a t =2  ̄ .1 0P , o 0C的气 体 状 态 , 为 自 由状 称 态 )其 计算公 式如下 : , Q Q o H×( g ・ 1 P +103×l5 ×(7 o / (7 o) 23+t [2 3 )
温 度下工 作很 容 易被烧 坏 , 就使 得 整个 给 料 机 系 这
统 的可靠 性 很差 。
摆 动 角度 气 口连 接 尺 寸
o ~2 o任 意调 节 。 7。 G / 18
2 改 进 措施
在分 析 了上 述 原 因后 决 定 改 用 气 压 传 动 形 式
在 最大摆 动 角度 , 力 6a 时耗 气量 压 br
行 了分 析后 发现 原装 置存 在 以下缺 陷 :
1 由于该 步 进 电机 的输 出扭 矩 为 :0 m, 实 ) 1N 在 际使用 中显 得偏 小 , 出现卡 料 情况 下 电机 就 被 卡 在
死。
表 1 摆 动 气缸 参数 表
气缸 名 称 型 号 等 效 缸 径 最大许用工作压 力
于原 来 的 1 N 故 满足 主体 机构驱 动要 求 。 0 m,
2 0
2 2 系统供 气需 要量 .
力全
20 1 第 期 0 年1月 四 1
为压缩 空气 的表压 力为 60 0 P ; 0 00 a t n为压缩
压 缩空气需 要量 主要考 虑各 执行 机构 ( 处 指 此