典型连铸过程控制计算机系统的实现
DCS系统在钢铁生产中的应用
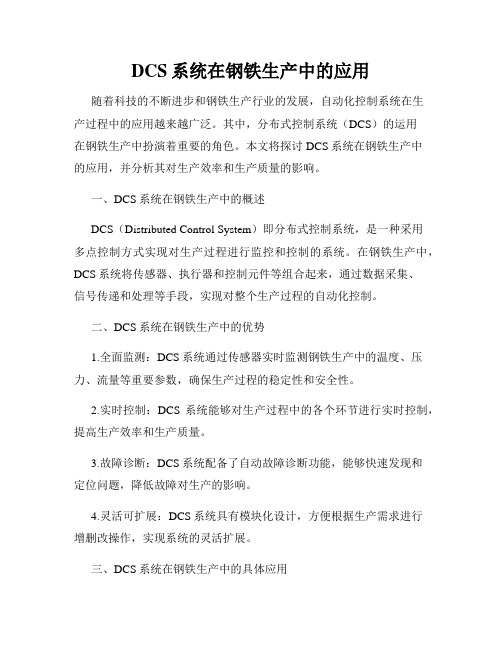
DCS系统在钢铁生产中的应用随着科技的不断进步和钢铁生产行业的发展,自动化控制系统在生产过程中的应用越来越广泛。
其中,分布式控制系统(DCS)的运用在钢铁生产中扮演着重要的角色。
本文将探讨DCS系统在钢铁生产中的应用,并分析其对生产效率和生产质量的影响。
一、DCS系统在钢铁生产中的概述DCS(Distributed Control System)即分布式控制系统,是一种采用多点控制方式实现对生产过程进行监控和控制的系统。
在钢铁生产中,DCS系统将传感器、执行器和控制元件等组合起来,通过数据采集、信号传递和处理等手段,实现对整个生产过程的自动化控制。
二、DCS系统在钢铁生产中的优势1.全面监测:DCS系统通过传感器实时监测钢铁生产中的温度、压力、流量等重要参数,确保生产过程的稳定性和安全性。
2.实时控制:DCS系统能够对生产过程中的各个环节进行实时控制,提高生产效率和生产质量。
3.故障诊断:DCS系统配备了自动故障诊断功能,能够快速发现和定位问题,降低故障对生产的影响。
4.灵活可扩展:DCS系统具有模块化设计,方便根据生产需求进行增删改操作,实现系统的灵活扩展。
三、DCS系统在钢铁生产中的具体应用1.原料处理:DCS系统能够对原料的配比、流量和质量进行控制和监测,确保原料的准确投入和混合工艺的精确控制。
2.高炉控制:DCS系统可通过温度、压力等传感器对高炉内部状态进行实时监测和控制,优化炼铁过程,提高炉温稳定性和炉渣质量。
3.连铸控制:DCS系统通过控制水流、板坯速度等参数,实现对连铸过程的精确控制,保证铸坯的质量和形状的一致性。
4.轧制控制:DCS系统对轧机的控制精度较高,可以准确控制轧辊力、板形和轧辊温度,提高轧制质量。
5.质量监控:DCS系统通过数据采集和分析,实现对产品质量的监测和报警,及时发现并解决质量问题。
四、DCS系统应用的效果评估DCS系统的应用在钢铁生产中已经取得了显著的效果。
首先,DCS系统的全面监测和实时控制能够提高生产效率,减少人工干预,降低生产成本。
钢铁连铸PLC技术体系
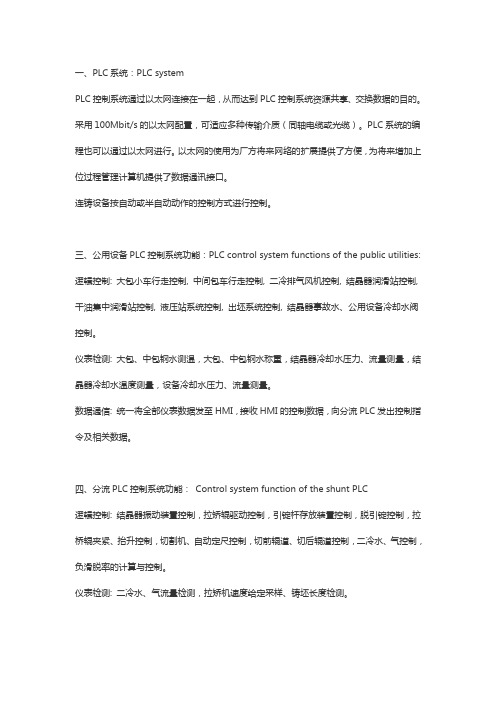
一、PLC系统:PLC systemPLC控制系统通过以太网连接在一起,从而达到PLC控制系统资源共享、交换数据的目的。
采用100Mbit/s的以太网配置,可适应多种传输介质(同轴电缆或光缆)。
PLC系统的编程也可以通过以太网进行。
以太网的使用为厂方将来网络的扩展提供了方便,为将来增加上位过程管理计算机提供了数据通讯接口。
连铸设备按自动或半自动动作的控制方式进行控制。
三、公用设备PLC控制系统功能:PLC control system functions of the public utilities: 逻辑控制: 大包小车行走控制, 中间包车行走控制, 二冷排气风机控制, 结晶器润滑站控制, 干油集中润滑站控制, 液压站系统控制, 出坯系统控制, 结晶器事故水、公用设备冷却水阀控制。
仪表检测: 大包、中包钢水测温,大包、中包钢水称重,结晶器冷却水压力、流量测量,结晶器冷却水温度测量,设备冷却水压力、流量测量。
数据通信: 统一将全部仪表数据发至HMI,接收HMI的控制数据,向分流PLC发出控制指令及相关数据。
四、分流PLC控制系统功能:Control system function of the shunt PLC逻辑控制: 结晶器振动装置控制,拉矫辊驱动控制,引锭杆存放装置控制,脱引锭控制,拉桥辊夹紧、抬升控制,切割机、自动定尺控制,切前辊道、切后辊道控制,二冷水、气控制,负滑脱率的计算与控制。
仪表检测: 二冷水、气流量检测,拉矫机速度给定采样、铸坯长度检测。
数据通信: 将仪表数据发至公用PLC,接收公用PLC的控制数据,向变频器发出控制数据,接收变频器相关数据。
轧线机由基础自动化系统控制自动或手动运行。
全面满足工艺生产要求,提高生产效率。
自动化由下列功能实现:- 级联控制- 微张力控制- 活套控制- 故障检测- 飞剪控制- HMI 系统- 物料跟踪- 其它功能。
所有任务均由分布式的PLC SIMATIC系统实现,带有开放式的通讯网络,便于扩展。
LF二级过程控制系统的研究与实现
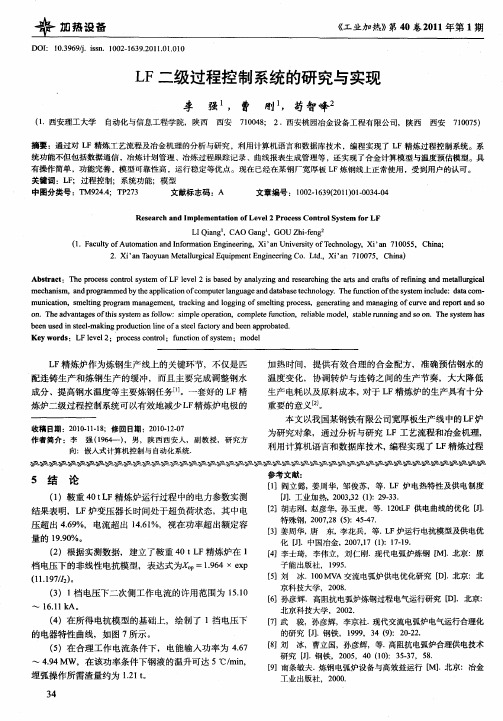
关键 词 : F L ;过程控制;系统 功能;模 型 中图分类号 :T 2 . P 7 M9 4 ;T 23 4 文献标志码 :A
文章编号 :10 —692 1) 103 .4 0 213 (0 10 .0 40
Re e r h a d I p e e t to f v l o e s n r l y t m o s a c n m lm n a i n o Le e Pr c s 2 Co t o se f r LF S
L F精炼炼钢生产 的缓冲 ,而且 主要完成调整钢水 成分 、提高钢水温度等主要炼钢任务 。一套好 的 L F精 炼炉二级过程控制系统可 以有效地减少 L 精炼炉 电极 的 F
收稿 日期 :2 1—11;修 回 日期 :2 1-20 001-8 001—7 作 者 简介 :李 强 (94 ) 男 ,陕 西 西安 人 , 副教 授 ,研 究方 16一 , 向 :嵌入 式计 算机 控 制与 自动化 系统 .
mu i ai n met g p o r m n g me t ra k n n o g n fs l n r c s ,g n r t g a d ma a i g o H V n p r a d S n c t ,s l n r g a ma a e n ,t c i g a d l g i g o met g p o e s e e a i n n gn f I e a d r o t o i i n C e O n o .T ea v n a e f h ss se a l w:s n h d a t g so t i y tm s o l f o i l p r t n o l t n t n eib emo e,s b er n i g a d S n mp eo e a i ,c mp e ef c i ,r l l d l t l n n n O o .T es se h s o u o a a u h y tm a
邯钢CSP过程控制系统安全架构的实现

能力 , 目前在 中高档服务器所采用 。如 H P公司的 Ap a P R S 、 l 和 A— I h C
IM 公 司的 Pw rP MIS公 司 的 MIS和 S N 公 司 的 S  ̄e B o e C、 P P U pr。
邯钢 C P过程控制 系统安全架构 的实现 S
刘建飞 王 鹏 刘延伟 河北钢铁 集团邯郸钢铁股份有限公 司连铸连 ̄ V 06 1 t t , 50 5
【 要】 摘 以河北钢铁集 团连铸连轧生产线过程控制 系统为例 , 对二级过程控制 系统的安 全冗余性能进行 分析, 详细介绍利用设备 冗余技术 、 于 基
1 言 前 邯钢薄板坯连铸连轧生产线( 简称 C P 是引进德 国西马克 9 S) O年代
世界先进技术 , 为我 国最早与珠钢 、 包钢 同期 引进了三条 C P生产线之 S
一
务器的运行 , 然后用一定的时间切换 至备用服务器 上面进行运行 , 才能
进行维修和恢复。 22 2 双机 热 备 ..
活 , 证应 用 在 短 时 间 内完 恢 复 正 常使 用 。 保 2 2 3单机 容 错 ..
情况下 , 过程控制系统的安全性就显 的非常必要及 迫切 。
2影 响 过 程控 制 系统 安全 的 因素
2 1服 务 器 的硬 件 架 构 .
单机容错技术则是在一 台服务 器实现高性 能容错的。它的容错能 力要远 比双机热备份中容错能力要 高。容 错服务器是通 过采用 同步技
的服 务器 操作 系统 主要有 : nosU i、iu Widw 、 n Lnx和 O V 。 x  ̄ MS
Wnos i w 操作系统 由于其最具人性化 的界 面, 且操作直观易 于使 d 并 用 , 目前最普及的操作系统 因此安全性也最差。随着 M c s t 是 io f r o 不断的
宝钢股份特钢事业部40T产线板带炼钢过程控制计算机系统
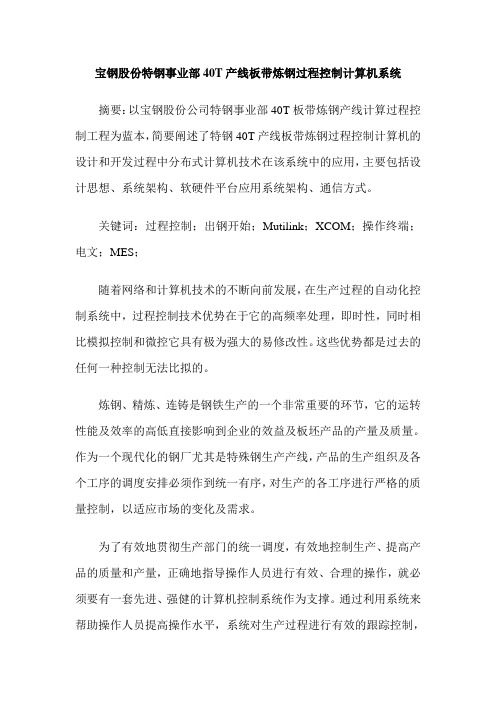
宝钢股份特钢事业部40T产线板带炼钢过程控制计算机系统摘要:以宝钢股份公司特钢事业部40T板带炼钢产线计算过程控制工程为蓝本,简要阐述了特钢40T产线板带炼钢过程控制计算机的设计和开发过程中分布式计算机技术在该系统中的应用,主要包括设计思想、系统架构、软硬件平台应用系统架构、通信方式。
关键词:过程控制;出钢开始;Mutilink;XCOM;操作终端;电文;MES;随着网络和计算机技术的不断向前发展,在生产过程的自动化控制系统中,过程控制技术优势在于它的高频率处理,即时性,同时相比模拟控制和微控它具有极为强大的易修改性。
这些优势都是过去的任何一种控制无法比拟的。
炼钢、精炼、连铸是钢铁生产的一个非常重要的环节,它的运转性能及效率的高低直接影响到企业的效益及板坯产品的产量及质量。
作为一个现代化的钢厂尤其是特殊钢生产产线,产品的生产组织及各个工序的调度安排必须作到统一有序,对生产的各工序进行严格的质量控制,以适应市场的变化及需求。
为了有效地贯彻生产部门的统一调度,有效地控制生产、提高产品的质量和产量,正确地指导操作人员进行有效、合理的操作,就必须要有一套先进、强健的计算机控制系统作为支撑。
通过利用系统来帮助操作人员提高操作水平,系统对生产过程进行有效的跟踪控制,对生产作业实绩进行有效的收集、统计以及对生产线上的主要设备进行有效管理,将大大地减少人力,提高生产效率。
本系统开发投入后,已经实现了实时地跟踪现场的生产,为生产提供必要的生产指导,实时收集生产实绩,统计必要的消耗,为MES 系统提供实绩数据。
1 系统结构本系统包含三大系统:电炉应用系统、精炼应用系统、连模铸应用系统。
其中电炉L2计算机系统:覆盖4个电炉的计算机系统;精炼L2计算机系统:覆盖5个LF炉、1个AOD炉、1个VD炉、1个VOD炉的计算机系统;连模铸L2计算机系统:覆盖1台连铸机本体、1套模铸工位的计算机系统。
1.1 系统构成特点为了系统的先进可靠,同时尽可能地降低、节约成本,本系统采用的是基于PC和PC Server的CLIENT/SERVER体系结构。
DCS系统在冶金行业中的应用及其关键技术
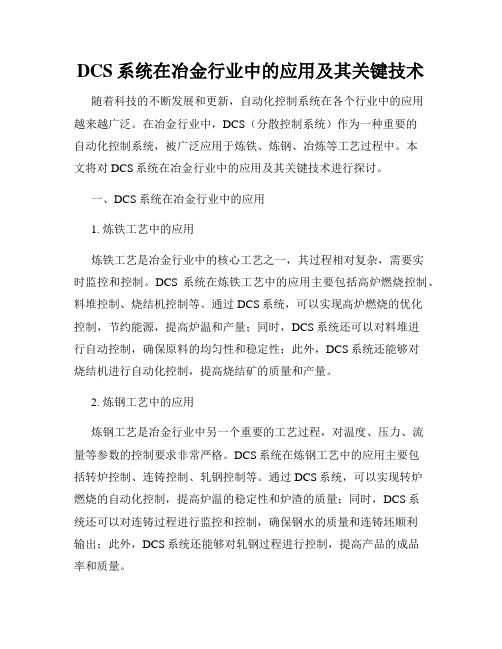
DCS系统在冶金行业中的应用及其关键技术随着科技的不断发展和更新,自动化控制系统在各个行业中的应用越来越广泛。
在冶金行业中,DCS(分散控制系统)作为一种重要的自动化控制系统,被广泛应用于炼铁、炼钢、冶炼等工艺过程中。
本文将对DCS系统在冶金行业中的应用及其关键技术进行探讨。
一、DCS系统在冶金行业中的应用1. 炼铁工艺中的应用炼铁工艺是冶金行业中的核心工艺之一,其过程相对复杂,需要实时监控和控制。
DCS系统在炼铁工艺中的应用主要包括高炉燃烧控制、料堆控制、烧结机控制等。
通过DCS系统,可以实现高炉燃烧的优化控制,节约能源,提高炉温和产量;同时,DCS系统还可以对料堆进行自动控制,确保原料的均匀性和稳定性;此外,DCS系统还能够对烧结机进行自动化控制,提高烧结矿的质量和产量。
2. 炼钢工艺中的应用炼钢工艺是冶金行业中另一个重要的工艺过程,对温度、压力、流量等参数的控制要求非常严格。
DCS系统在炼钢工艺中的应用主要包括转炉控制、连铸控制、轧钢控制等。
通过DCS系统,可以实现转炉燃烧的自动化控制,提高炉温的稳定性和炉渣的质量;同时,DCS系统还可以对连铸过程进行监控和控制,确保钢水的质量和连铸坯顺利输出;此外,DCS系统还能够对轧钢过程进行控制,提高产品的成品率和质量。
3. 冶炼工艺中的应用冶炼工艺是冶金行业中的另一个重要环节,其过程涉及到多个工序和设备的协同运行。
DCS系统在冶炼工艺中的应用主要包括矿石破碎、矿石浮选、冶炼反应、尾渣处理等。
通过DCS系统,可以对矿石破碎过程进行监控和控制,确保矿石的粒度和质量符合冶炼工艺要求;同时,DCS系统还可以对矿石浮选过程进行自动控制,提高选矿的效率和回收率;此外,DCS系统还能够对冶炼反应进行实时监控,确保反应的稳定性和产品质量;最后,DCS系统还能够对尾渣处理过程进行控制,减少环境污染。
二、DCS系统在冶金行业中的关键技术1. 数据采集和处理技术DCS系统需要采集大量的数据,并对数据进行实时处理和分析。
莱钢5#方坯连铸机自动控制系统的设计和实现

Abs r c : i a e r s n s t e s h me a d c n g r t n o e c n r ls s e o e n . i — ta d b le a t ri i a g t a t Th sp p rp e e t h c e n o f u a i ft — o to y t m ft o 5 s x sr n i t se n Lag n i o h h l c
其 自动化系统配置先进、合理、性能可靠 ,是先进工艺与先进 自 动化技术的完美结合 , 为莱钢年产 10万吨钢做 出了较大的贡献。 O0
22 拉矫 跨 .
2 工 艺过 程
连铸生产是钢铁冶炼企业中的—个承 匕 启下的关键环节 ,它 对钢材最终的质量好坏 , 产品开发都有着举足轻重的作用。 方坯连 铸生产线主要由钢水接受跨、 拉矫跨, 切割出坯跨三大部分组成 。1 【 1
Auo t n r I f l t se t mai Co t Bi c o o a l Ca t r e
W U a -h n , n , AN i YANG i n Zh o c e g LIHo g BI l , Ja ( GagA tmai e t no s e A e, aa 2 10 , hn ) n uo t nS ci f t l raT in, 7 14 C ia o o e
称重传感器 , 感应出的信号经过信号处理器处理后直接传到铸机 公共 P C,并通过 WI L NCC画面在主控室 HMI 上显示出来 。所
过程控制系统在石钢3号方坯连铸机的应用

A PLI P CATI ON OF ROCES P S
C T O YS E ON R L S T M
S UAR Ⅱ E AS E Q EB L T C T R
.
W AN G a — q Xi o i
( t l0k , h i h agI nadSel o ay S iah ag Hee, 50 ) se w rs S ia un o n te C mpn , h i un , b i 0 0 3 e jz r jz 1
年 第 3期
河 北 冶金
HE BEI M E TA L LU R GY
Toa 5 tl1 9 20 0 7, Nu e mb r3
过 程 控 制 系统 在 石 钢 3号 方坯 连 铸 机 的应 用
2 2 硬 件 配 置 .
过 程控 制 系 统 的 目标 是 利 用 先 进 的计 算 机 技 术 、网络通讯 技术 和数 据库 技术实 现控 制 系统 和 管 理 系统 的集成 ,达 到企 业 中信息上 传下 达 ,畅 通无 阻 ,实 现生 产过 程 中的物流 、信息 流 和经 营管 理 的 统 一和 优化 的 目标 。石 钢 3号方坯 连铸 机 在生 产 过
1 5套 P C( L 4台计 算 机 操 作 站 、 2台计 算 机服 务 器 )
以及 远程 I O组成 。整 个过 程监 控系统 底层 为远程 /
IO,负责对 分 布 的设 备 进 行 数据 采 集 及监 控 ;通 /
过 以太 网可 实 现 各 P C 系统 间 的可 靠 通 讯 ,通 过 L
ie z d.
Ke o d :p o e sc n o y tm ;s u e b l t a t r p l a o y W r s r c s o t ls s r e q a i e se ;a p i t n r l c ci
北京科技大学钢铁生产全流程虚拟仿真平台实习报告
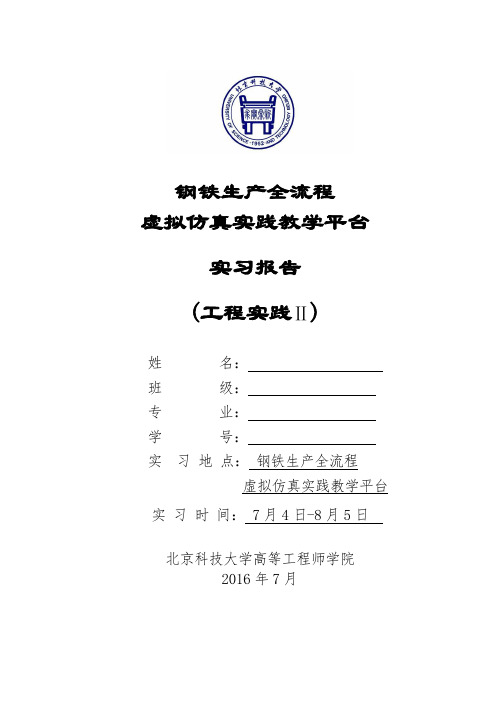
钢铁生产全流程虚拟仿真实践教学平台实习报告(工程实践Ⅱ)姓名:班级:专业:学号:实习地点:钢铁生产全流程虚拟仿真实践教学平台实习时间: 7月4日-8月5日北京科技大学高等工程师学院2016年7月目录目录 (I)1前言 (1)2实习背景描述 (1)2.1实习性质 (1)2.2实习目的 (1)2.3实习要求 (2)2.4实习单位的基本情况 (2)2.5实习安排情况 (3)3实习内容 (4)3.1 邯郸钢铁生产 (4)3.2钢铁生产全流程虚拟平台 (10)3.2.1烧结 (10)3.2.2高炉炼铁 (11)3.2.3炼钢 (13)3.2.4连铸 (26)4总结 (27)4.1收获与感受 (27)4.2建议 (28)参考文献 (28)致谢 (29)1前言我北京科技大学是“211工程”院校,“985优势学科创新平台”,求实鼎新,崇尚实践。
按照北京科技大学卓越工程师培养计划的总体要求,依托冶金工程国家一级重点学科,按照“夯实学科基础、注重专业交叉、强化工程实践、培养创新能力”的总体思路,以实际工程为背景,以工程技术研究为主线,着力提高学生的工程意识、工程素质和工程实践能力。
高等工程师学院院长刘立从项目概况、应用现状、应用愿景及发展规划等方面介绍了虚拟平台建设情况,展示了虚拟平台钢铁生产全流程实践教学资源。
技术人员现场演示了转炉炼钢虚拟仿真教学系统的认知学习、实践操作和创新实践等功能。
教务处处长宋波对虚拟平台的启用表示祝贺并指出虚拟仿真教学方式具有较强实践性与趣味性,希望各学院在实习实践及课堂教学等环节中积极引入虚拟仿真教学资源,提升实践教学效果。
虚拟平台展示了现代钢铁生产流程特点,采用了创新性教学方法与手段,不仅能为工程实践教学提供支撑,还可为学生创新创业提供平台。
钢铁生产全流程虚拟仿真实践教学平台于2013年开始筹建,2015年10月完成项目验收,2016年1月获批教育部“国家级虚拟仿真实验教学中心”。
现有实验室2个,实验教学面积400平米,虚拟仿真实践教学系统10套,形成了由软件、硬件和网络系统组成的虚拟仿真实践教学环境,具有认知学习、实践操作、考核鉴定、设计教学、创新实践、教学资源管理等功能,能够支撑专业课程、认识实习、生产实习、工程设计、毕业设计等教学环节。
热连轧过程及计算机控制(L-2)

WUST
图1-1 铁碳合金相图
WUST
热加工变形除具有上述优点,使之在生产实践中得到广泛的应用外,同其 他加工方法相比较它也有如下的不足:
(1) 对薄或细的轧件由于散热较快,在生产中保持热加工的温度条件比较 困难;
wustwust级计算机控制系统level3生产控制级level2过程控制级pclbpops模型效果分析模型数据下载pdi数据传输轧辊数据传输设定数据显示实测数据显示轧机实测数据轧机设定数据操作工干预level1设备控制级agcafcfgcapc工业以太网tcm设定模型模型数据存储ops数据输出工程文件输出实测数据获得pc轧机预设定wust2过程自动化控制功能过程自动化面向整个生产线其中心任务是对生产线上各机组和各个设备进行设定计算为此其核心功能为对粗轧精轧机组负荷进行分配包括最优化计算及数学模型的预报估为了实现此核心功能为对粗轧精轧机组负荷进行分配包括最优化计算过程控制计算机必须设有板坯数据跟踪初始数据输入在线数据采集以及模型自学习等为设定模型服务及配套的功能
(2) ISP工艺(Inline Strip Production)(图2-6) 在线热带钢生产工艺由德国德马克公司研制,于1992年1月在意大利
的Arvedi钢厂建成投产,设计能力50万吨/年,实际产量84万吨/年。这也 是欧洲第一套薄板坯连铸连轧生产线。生产线全长约180米。产品厚度为 1.0~12.7mm。
1) 生产超薄带钢和宽薄带钢,拓宽产品大纲而不降低收得率; 2) 稳定轧制条件以利于提高产品质量和收得率; 3) 消除了与穿带和甩尾有关的麻烦,大大地降低了轧辊的消耗,提高了 生产率。
WUST
WUST
过程控制系统如何实现生产过程的自动化

过程控制系统如何实现生产过程的自动化在当今的工业生产领域,实现生产过程的自动化已成为提高生产效率、保证产品质量、降低成本和增强企业竞争力的关键。
而过程控制系统则是实现这一目标的核心技术手段。
过程控制系统是指对生产过程中的各种参数进行测量、控制和调节,以确保生产过程按照预定的要求稳定运行的一套系统。
它涵盖了从传感器采集数据、控制器计算控制策略、执行器执行控制动作,到对整个生产过程的监控和优化等多个环节。
首先,传感器在过程控制系统中起着至关重要的作用。
它们就像是生产过程的“眼睛”,能够实时感知温度、压力、流量、液位、成分等各种物理量和化学量的变化,并将这些信息转化为电信号或数字信号,传递给控制系统。
例如,在石油化工生产中,温度传感器可以监测反应釜内的温度变化,压力传感器可以测量管道内的压力,流量传感器可以准确计量物料的流量。
不同类型的传感器具有不同的精度、响应时间和适用范围,因此在选择传感器时需要根据具体的生产工艺和控制要求进行精心挑选。
接收到传感器传来的信号后,控制器就开始发挥作用了。
控制器可以说是过程控制系统的“大脑”,它根据预设的控制算法和策略,对输入的信号进行分析和计算,然后输出控制信号。
常见的控制算法包括PID 控制(比例积分微分控制)、模糊控制、预测控制等。
PID 控制是应用最为广泛的一种控制算法,它通过对误差信号的比例、积分和微分运算,来调整控制输出,使系统能够快速、准确地达到设定值。
而模糊控制和预测控制则适用于一些复杂的、具有不确定性的生产过程,能够更好地应对系统的非线性和时变性。
执行器则是过程控制系统的“手脚”,负责将控制器输出的控制信号转化为实际的物理动作。
常见的执行器有调节阀、电机、变频器、泵等。
例如,当控制器计算出需要增加管道内的流量时,就会向调节阀发送控制信号,调节阀相应地开大阀门,从而增加物料的流量。
执行器的性能直接影响着控制效果的好坏,因此需要具备高精度、快速响应、可靠运行等特点。
PLC在冶金工业中的应用案例
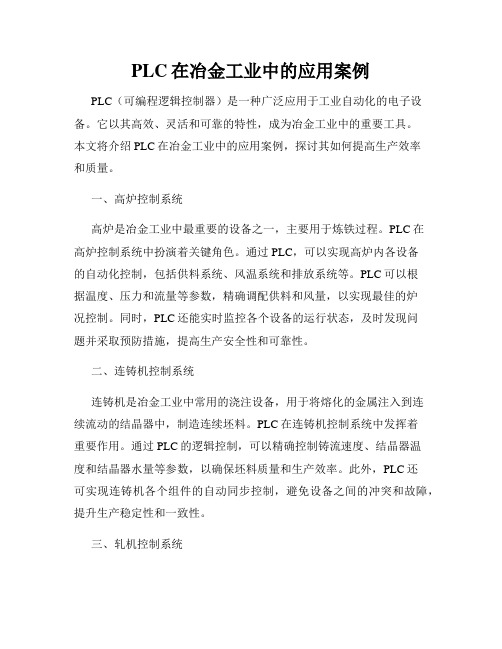
PLC在冶金工业中的应用案例PLC(可编程逻辑控制器)是一种广泛应用于工业自动化的电子设备。
它以其高效、灵活和可靠的特性,成为冶金工业中的重要工具。
本文将介绍PLC在冶金工业中的应用案例,探讨其如何提高生产效率和质量。
一、高炉控制系统高炉是冶金工业中最重要的设备之一,主要用于炼铁过程。
PLC在高炉控制系统中扮演着关键角色。
通过PLC,可以实现高炉内各设备的自动化控制,包括供料系统、风温系统和排放系统等。
PLC可以根据温度、压力和流量等参数,精确调配供料和风量,以实现最佳的炉况控制。
同时,PLC还能实时监控各个设备的运行状态,及时发现问题并采取预防措施,提高生产安全性和可靠性。
二、连铸机控制系统连铸机是冶金工业中常用的浇注设备,用于将熔化的金属注入到连续流动的结晶器中,制造连续坯料。
PLC在连铸机控制系统中发挥着重要作用。
通过PLC的逻辑控制,可以精确控制铸流速度、结晶器温度和结晶器水量等参数,以确保坯料质量和生产效率。
此外,PLC还可实现连铸机各个组件的自动同步控制,避免设备之间的冲突和故障,提升生产稳定性和一致性。
三、轧机控制系统轧机是冶金工业中用于将金属坯料轧制成板材或线材的设备。
PLC广泛应用于轧机控制系统中,实现轧机的自动化操作和控制。
通过PLC,可以实时监测和调整轧机的压力、速度和张力等参数,以确保产品尺寸和表面质量的一致性。
此外,PLC还能自动检测轧机轧辊的磨损程度,并根据需要进行自动调整,延长轧辊寿命,降低维护成本。
四、冶炼过程控制系统冶炼过程是冶金工业中的核心环节,PLC在冶炼过程控制系统中发挥着至关重要的作用。
通过PLC,可以实时监控和调控冶炼过程中的温度、压力和化学成分等参数,确保炉内条件的稳定和产品质量的一致性。
此外,PLC还可以与其他设备和系统进行联动控制,如喷吹系统、加料系统和废气处理系统等,实现全面的工艺控制和能源优化。
总结:PLC在冶金工业中的应用案例举不胜举,从高炉控制系统到冶炼过程控制系统,从连铸机到轧机控制系统,它为冶金工业的自动化生产和质量改进提供了强有力的支持。
宝钢电炉圆(方)坯连铸计算机系统运行实践

宝钢电炉圆(方)坯连铸计算机系统运行实践
宝钢电炉圆(方)坯连铸计算机系统是一套高度自动化的控制系统,
它在钢铁生产过程中扮演着至关重要的角色。
该系统通过精确控制连
铸机的各个参数,确保了生产效率和产品质量的最大化。
在宝钢的电炉圆(方)坯连铸生产线上,计算机系统负责监控和调节
整个连铸过程。
系统的主要功能包括:
1. 温度控制:系统能够实时监测钢水的温度,并根据需要调节加热设备,以确保钢水在连铸过程中保持最佳温度。
2. 速度调节:连铸速度是影响产品质量的关键因素之一。
计算机系统
通过精确控制拉速,确保铸坯的内部结构均匀,避免裂纹和缺陷的产生。
3. 结晶器液位控制:系统能够自动调节结晶器内的液位,以适应不同
的生产条件和铸坯规格。
4. 二次冷却控制:计算机系统根据铸坯的冷却需求,自动调节冷却水
的流量和分布,以实现最佳的冷却效果。
5. 质量检测:系统配备有在线检测设备,能够实时监测铸坯的尺寸和
表面质量,及时发现并处理生产过程中的问题。
6. 数据记录与分析:计算机系统能够记录生产过程中的所有关键数据,并进行分析,以便优化生产流程和提高产品质量。
7. 故障诊断与报警:系统具备故障诊断功能,能够及时发现设备异常,
并发出报警,减少生产中断的风险。
8. 人机交互界面:友好的人机交互界面使得操作人员能够直观地监控生产过程,并进行必要的手动干预。
宝钢电炉圆(方)坯连铸计算机系统的运行实践表明,通过采用先进的自动化技术,可以显著提高生产效率,降低生产成本,同时确保产品质量的稳定性和一致性。
随着技术的不断进步和优化,该系统在未来的生产中将发挥更大的作用。
八钢第一炼钢厂连铸过程控制系统的概述

换 为实际值 为 0 . 8 8 m 1 . 7 8 m, 此 次实验有效波 高为 1 . 7 2 m。相 力 曲线 的特 点是波压力过程线 出现很强的脉冲 ,最大值 出现 当于在水下 半个波 高到一个波高处, 波压力达到最大值 。 在静水面 以下 , 波压力波峰尖陡 , 为单峰。波浪破碎 , 水体打 在本 次实验中,前苏联规范所算得结果与其他家公式和 击在斜坡上 , 当波浪冲击作用较 明 时, 打击点附近产生剧烈 实验 结果相 差较大, 而冯卫兵 的公式 计算结果实验较为吻合 。 的波压 力。根据实验所得波压力 f } f I 线可得:沿整个斜坡面上 打击点处波压力最大 , 两边逐渐衰减 。 黄碧珊 的公式 偏小, 不过与冯 兵 的公式计算结果相差不大。 波压力 分布极不均匀 , 这主要是前 苏联公式足利用 射流理论进行 的理论推导,而黄 碧珊和 冯卫兵的公式足利用 实验数据进行拟合,与实验 误差 参 考文献 :
.
1前 言
换机, 1 台C I S C O 2 0 8 / 8口交换机和若干个 网络连接 设备组成 。
八俐作为一家快速成 长的大型企业 ,近年米更是发展迅 连 铸 过 程 控 制服 务器 在 L 2机 房 服 务 器 室 , 客 户 机 一 台位 于 连 速, 从最初的 2 0 T转炉炼钢生产线到现代化 的 1 5 0 T火型转炉 铸主控室, 供连铸操作人员崎控生产过程状态, 另一 台客户机 炼钢 ,使 八钢跻身成为一流钢铁生产企业 。1 5 0 T转炉从建设 位于连铸切割 室,主要根据采集的生产数据通过切割优化模 初期 , 就非常重视信息化建 设, 炼钢过程控制系统全线覆盖, 而 型 计 算 出最 佳切 割 定 尺 提 供 给 生 产 操 作 人 员 做 参 考 。还 有 一 连铸过程控制系统 作为炼钢系统中后 的一道控制工序 , 在生产 台客户机在 L 2机房, 供维护人 员使用 。 过程监控 , 提 高钢坯质量和控制成本等方面起着非常大的作用。 3 . 2软 件 系统 结 构 2连铸的工艺生产流程介绍 主要由服务器操作系统 Wi n d o w s S e r v e r 2 0 0 8 标 准版 , 数 连铸 即为连续铸钢的简称 。在钢铁厂生产各类钢铁产品 据库软件 Or a c l e S t a n d a r d 1 1 G, 开发工具 Vi s u a l S t u d i o 2 0 1 0专 过程 中, 使用钢 水凝同成 型有两种方法 : 传统 的模铸法和连续 业版 , 与基础 自动化通讯 软件 Ke p wa r e , 客户机操作系统 Wi n . 铸钢法 。 与传统方法相 比, 连铸技术具有大幅提高金属收得率 d o ws 7 , 办公软件 Of ic f e 2 0 1 0等软件组成。连铸二级过程控
国内首套基于机器视觉的连铸智能出坯控制系统开发与应用

国内首套基于机器视觉的连铸智能出坯控制系统开发与应用发布时间:2021-11-03T03:11:53.986Z 来源:《中国科技人才》2021年第20期作者:高仲毅孙浪波冯建斌贺增平高浪路选峰李小军[导读] 进而控制辊道、升降挡板、推钢机等装置,完成方坯自动推钢功能,该系统亦可实现钢坯自动跟踪、自动分炉和自动报表统计功能.陕钢集团陕西龙门钢铁有限责任公司陕西韩城 715403摘要:目前龙钢公司炼钢厂6台连铸机采用人工手动控制辊道、升降挡板、以及推钢机的方式,将切割后的方坯运送至推钢区域,再由推钢机将方坯推送至两个冷床区域,天车吊运至精整区域存放,整个过程需要操作人员长期操作辊道、升降挡板和推钢机等装置,劳动强度巨大,甚至会出现操作错误导致堆钢影响生产;为了减轻操作工劳动强度,提高连铸机自动化水平,增设自动出坯和自动推钢系统,该系统采用先进的机器视觉识别技术,对挡板区域、推钢区域、冷床区域进行实时监控,将图像信息通过识别算法以太网的方式发送给PLC 及CPS虚边缘计算机,边缘计算机中通过AI智能算法模型进行逻辑处理和分析,实时判定各个区域当时的状态。
自动推钢系统软件根据算法,得出最优推钢方案,通过以太网与辊道PLC通讯,进而控制辊道、升降挡板、推钢机等装置,完成方坯自动推钢功能,该系统亦可实现钢坯自动跟踪、自动分炉和自动报表统计功能.关键词:机器视觉;深度学习;连铸出坯;神经网络;数字孪生;深度自学习;自动推钢一、引言现有的炼钢生产过程中,连铸生产属于人力密集型生产过程。
而连铸生产的出坯工序包括:将连铸坯切割成定长坯体的切割过程、坯体输送过程、以及将坯体推送至待吊装位置(通常是冷床)的过程。
出坯工序中大部分工位由于监测和控制技术等的限制,仍然需要采用人工方式进行生产控制,无法实现全自动化控制。
上述的出坯工序的坯体推送过程中,由于连铸机流数多、浇铸拉速高、生产节奏快,在依靠人工进行推坯操作的过程中,操作工必须保持长时间的精神高度集中,工人劳动强度大容易疲劳,难以避免出现人为原因的操作失误,导致堆坯、钢坯推弯、推钢机掉道等生产安全事故。
大方坯连铸机自动化控制系统的设计与实现

基础 自动化级的组成分为1 组公用P L C 、 6 组铸流P L C ( 含二冷动 态配水和轻压 下) 、 6 组液压振动P L C, l 组线外液压振动P L C 、 1 台L 2 服务器 、 4 台监控计算机以及 负责各设备 之间交换信号的以太 网。 通
设计 开 发
大方坯连铸机 自动化控制系统的设计与实现
王健
( 中冶南方工程技 术有限公 司 湖北武汉 4 3 0 2 2 3 )
摘要 : 为 了改善 控制 系统性 能提 高 大方坯连铸 机的 产品质 量和生 产效率, 设计 了一种 大方坯 连铸机 自动化控 制 系统 。 论述 了大方坯 连铸机 的几 项 关键 技 术 , 电磁 搅拌 、 结 晶器液 压振 动 、 动 态二 次 冷却 配 水和 动 态轻压 下。 结 果表 明 该控 制 系统 运转 良好 。 关键 词: 大方坯连铸机 二 次冷却 动 态控制 最佳 拉速 中图分 类号 : T F 3 4 1 . 6 文献 标识码 : A 文章编 号: l 0 0 7 — 9 4 l 6 ( 2 0 1 3 ) 0 9 — 0 1 5 2 - 0 2
Ab s t r ac t : Ai mi n g t o i mp r o ve t h e c o n t r o l s  ̄t e m p e f r or ma nc e ,t he p r o d uc t q ua l i t y a n d p r o d uc iv t i y t f o r a b l o o m c a s t e r , he t mo d i ie f d c on t r o l s y s t e m Wa S
智慧化控制连铸机工作原理
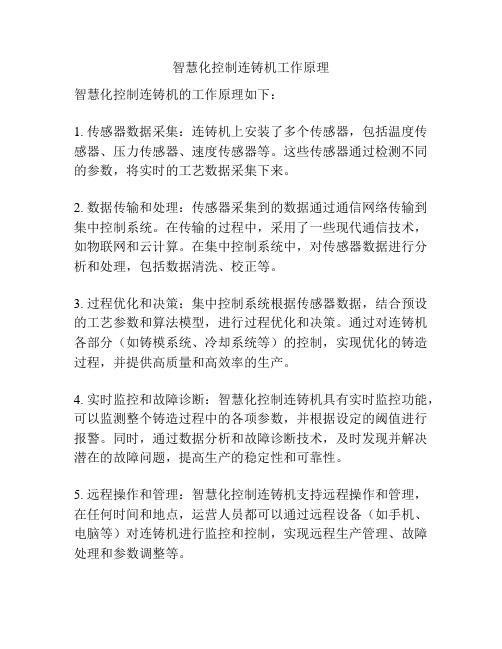
智慧化控制连铸机工作原理
智慧化控制连铸机的工作原理如下:
1. 传感器数据采集:连铸机上安装了多个传感器,包括温度传感器、压力传感器、速度传感器等。
这些传感器通过检测不同的参数,将实时的工艺数据采集下来。
2. 数据传输和处理:传感器采集到的数据通过通信网络传输到集中控制系统。
在传输的过程中,采用了一些现代通信技术,如物联网和云计算。
在集中控制系统中,对传感器数据进行分析和处理,包括数据清洗、校正等。
3. 过程优化和决策:集中控制系统根据传感器数据,结合预设的工艺参数和算法模型,进行过程优化和决策。
通过对连铸机各部分(如铸模系统、冷却系统等)的控制,实现优化的铸造过程,并提供高质量和高效率的生产。
4. 实时监控和故障诊断:智慧化控制连铸机具有实时监控功能,可以监测整个铸造过程中的各项参数,并根据设定的阈值进行报警。
同时,通过数据分析和故障诊断技术,及时发现并解决潜在的故障问题,提高生产的稳定性和可靠性。
5. 远程操作和管理:智慧化控制连铸机支持远程操作和管理,在任何时间和地点,运营人员都可以通过远程设备(如手机、电脑等)对连铸机进行监控和控制,实现远程生产管理、故障处理和参数调整等。
通过智慧化控制连铸机的工作原理,可以实现连铸过程的智能化、自动化和优化化,提高生产效率、节约能源、减少废品率,并且降低了人工操作的风险和工作强度。
天铁热轧板公司板坯连铸的二级控制系统

天铁热轧板公司板坯连铸的二级控制系统王春义【摘要】The second level computer system completes the production process control and management, production model calculation and data collection and analysis and other functions.This paper introduces the structure design and basic functions of the second level computer system for slab continuous casting machine of Tiantie Hot Rolling Plate Co., Ltd.%二级计算机系统完成生产过程控制管理, 生产模型计算与数据采集分析等功能.本文介绍了天铁热轧板有限公司2#板坯连铸机二级计算机系统结构设计和基本功能, 并且对部分模型计算的计算方法进行了分析.【期刊名称】《天津冶金》【年(卷),期】2018(000)006【总页数】3页(P43-45)【关键词】板坯连铸机;二级控制系统;模型【作者】王春义【作者单位】天铁热轧板有限公司, 河北涉县 056404【正文语种】中文0 引言天铁热轧板有限公司2#连铸板坯机于2008年投入使用,自动化控制系统由西门子奥钢联提供,分为一级(L1)控制系统和二级(L2)控制系统。
二级系统为过程控制级,是连铸机自动控制的重要组成部分,主要提供的功能有生产计划处理、物料跟踪、设备跟踪、混钢模型、动态二冷配水模型、动态辊缝控制模型、优化切割模型、板坯质量判断模型等。
1 二级系统硬件和软件服务器硬件采用HP DL380G5专业服务器,采用外置式RAID 0+1磁盘阵列技术,数据除分布在多个盘上外,每个盘都有其物理镜像盘,提供全冗余能力,允许一个以下磁盘故障,而不影响数据可用性,并具有快速读/写能力。
- 1、下载文档前请自行甄别文档内容的完整性,平台不提供额外的编辑、内容补充、找答案等附加服务。
- 2、"仅部分预览"的文档,不可在线预览部分如存在完整性等问题,可反馈申请退款(可完整预览的文档不适用该条件!)。
- 3、如文档侵犯您的权益,请联系客服反馈,我们会尽快为您处理(人工客服工作时间:9:00-18:30)。
典型连铸过程控制计算机系统的实现摘要:随着连铸工艺水平不断发展,对生产控制(结晶器液位,拉速,冷却水流量,切割长度等)的控制精度也越来越高,同时自动化技术和企业整体信息化也越来越趋向于一个整体,连铸过程控制计算机系统正是服务于这样一个大的发展趋势的计算机系统。
一方面它接受管理系统的生产指令,并利用数学模型对实时数据分析计算的结果指导和控制生产;另一方面采集基础电气仪表自动化的数据和信号对物流进行跟踪,并对采集到的生产实绩数据进行归纳。
它同时也是 mes/erp系统与电气仪表基础自动化系统之间的桥梁和纽带,三者紧密结合,实现了生产控制的自动化,也实现了信息技术与现代管理技术相结合。
本文以宝钢集团八一钢铁股份有限公司二炼钢连铸过程控制计算机系统为例,介绍了典型连铸过程控制计算机系统的具体实现。
关键词:l1 l2 l3 连铸过程控制中图分类号:tp273.5 文献标识码:a 文章编号:1672-3791(2012)08(c)-0032-021 系统概述宝钢集团八一钢铁二炼钢连铸过程控制计算机系统覆盖八一钢厂板带工程二炼钢区域的4台垂直弯曲板坯连铸机。
连铸机主要参数为:流数:各1流;切割机:各1台;喷印机:各1台;二冷区:各9个区,16个控制回路。
铸机拉速范围:0.25~2.5m/min;铸机工作拉速:1.0~1.6m/min;板坯厚度:220mm,板坯宽度:750~1600mm;板坯长度:7500~10500mm;板坯最大单重:28.8t/块。
该连铸过程控制计算机服务器硬件配置为2台高性能双路双模块冗余机架式容错服务器,其中一台为在线服务器,一台为备份服务器,磁盘采用阵列形式,采用共享磁盘管理技术,提高磁盘的可靠性,防止数据的丢失,减少系统切换的时间。
数据库数据存放在共享磁盘阵列上,在线服务器和备份服务器共享数据库数据,保证了服务器切换的速度和数据的一致。
服务器部署在l2中心机房,各个连铸电气室和操作室的边缘交换机通过多模光缆连接到l2中心机房的核心交换机,实现连铸过程控制计算机服务器与l1系统以及现场操作终端的网络互联。
现场终端采用工控机、一般场所终端采用商务pc机。
系统软件软件上的配置和使用上,服务器的操作系统采用linux redhat as4服务器数据库使用oracle 10g for linux版本,在终端上,安装oracle的客户端开发及运行环境包,包括forms和reports(开发/运行显示画面和报表),同时安装sql net(实现客户端和数据库服务器的数据交互)。
2 主要应用技术与电气仪表基础自动化的通讯,使用了opc方式,opc是ole process control的缩写,是一种主流的工业控制数据通讯的标准。
目前全世界大多数的知名plc厂家都提供了基于该标准的opc server,任何应用系统只要通过一个opc client软件就可以对plc数据进行读写访问。
通过这种机制,应用系统可以在不更改应用程序的前提下实现与不同的plc厂家的产品通讯。
我们使用的opc client软件是multilink(由宝信软件开发的基础通信中间件),它提供了一系列的api,应用开发人员可以方便的在应用程序中对plc的数据进行读写,实现对基础自动化数据的采集、设定及plc 数据变化后通知启动过程计算机的应用程序的功能,并提供了将plc数据点配置成电文以及查看这些数据点内容的的工具。
与mes(l3)系统以及其他相关系统的通讯使用基于tcp/ip协议socket方式,项目中使用xcom_pcs(由宝信软件开发的基于tcp/ip协议的socket通信中间件)来实现,与multilink类似,它也是提供了一系列简单方便的api(应用编程接口),实现在以太网环境下,基于tcp/ip协议的socket数据通信,同时提供了电文数据类型转换的功能(2进制与ascii码之间的转换,网络字节顺序和本地字节顺序之间的转换),同时也提供了查询通讯线路状态的工具和查询通讯电文内容历史记录的工具。
应用程序的开发,使用c++与pro c,pro c是oracle提供的预编译技术,将内嵌标准sql语句的又混合了c/c++语法的源程序预编译,转换成完全符合c/c++语法的源程序(后缀为.c/.cpp),这样在c++的环境下,就能如同在oracle的存储过程中一样使用标准sql语句方便的与oracle数据库交互,又能享受c++这种相对于oracle的存储过程要更强大而灵活的开发工具的各种优势。
画面的开发使用oracle的froms。
应用程序的运行平台中间件,使用plature 99(由宝信软件开发的运行平台中间件),它实现的功能包括实现各个应用程序之间的相互启动和调度,同时传递参数;在指定时刻启动某个/某些应用进程;定周期的启动某个/某些应用进程;提供管理维护和查看应用程序报警/log历史记录的功能。
3 应用功能关于连铸过程控制计算机系统的应用功能,主要是从mes和分析等系统接受出钢计划,制造命令和,根据出钢计划画面上的生产计划钢种和制造命令,制造标准等数据,并启动内部动态二冷水,切长优化计算模型,同时将计算结果发送到plc控制生产,连铸过程控制计算机系统在生产过程中对基础自动化(l1)上传的各个事件、信号进行跟踪,并将实绩生产实绩数据经过计算,过滤和组织,以连铸处理号作为键字来管理存储在连铸过程控制计算机系统的数据库,同时发送给mes(l3/l4)系统,供日后查阅分析,生成报表。
具体的,应用功能分为:工程数据管理,过程跟踪,过程数据采集,实绩数据生成,数学模型,人机界面几大模块。
系统内部各模块之间数据流及与外部系统关系如图1所示。
3.1 工程数据管理模块该模块主要功能为处理接受mes系统、分析系统及其它过程控制计算机系统发送来的信息,包括mes根据合同制定的计划类信息接收(铸造计划,炉次命令,板坯命令)、根据工艺需求制定的质量标准类信息接收(作业标准、制造标准)、其他工序作业实绩类接收(前工序实绩、分析信息,钢包信息等)和运转状况信息。
3.2 过程跟踪模块该模块主要功能为对于连铸从钢包到达回转台开始到钢包吊走的各作业状况进行跟踪。
进行作业状态变更的检查和接受、各作业时间的计算、同时收集浇铸过程中的各种浇铸信息。
连铸跟踪的主要作业点包括:钢包到达、钢包浇铸开始、铸流铸造开始、钢包浇铸结束、钢包吊走,铸流铸造开始、铸流铸造结束,切割开始、切割结束、喷印信号,去毛刺信号等。
3.3 过程数据采集模块该模块主要功能为周期性的收集连铸铸造过程数据,主要包括td钢水重量,ld钢水重量、铸造长、铸造速度,结晶器上端宽度、结晶器下端宽度、结晶器液面位置、结晶器冷却水温度、入出口温差,结晶器振动频率、振幅,结晶器冷却水流量、二次冷却水流量、二次冷却水压力,辊缝信息等。
3.4 实绩数据生成模块该模块主要功能为依据生产指令、过程采集及过程跟踪信息,生成板坯生产实绩、炉次生产实绩,把过程跟踪模块采集到的各个关键时刻和过程数据采集到的重要数据如重量,温度,长度等信息对应到具体的炉次和板坯上。
3.5 数学模型主要包含了动态二冷水,切长优化,品质异常判定三个主要数学模型。
3.5.1 动态二冷水模型连铸二冷区目标温度控制是通过对整个连铸过程铸坯表面温度的测定,由计算机控制沿拉坯方向的铸坯表面温度分布,使之符合设定的目标表面温度曲线来实现。
通过铸坯凝固传热模型计算各二冷段表面温度,与目标温度相比较。
当两者有偏差时,及时调整该冷却区的冷却强度,使铸坯表面温度与目标温度尽量靠近,实现二冷区目标温度的控制。
根据二冷模型原理,以钢水进入结晶器为其生命起点,以其根据铸造长对应的板坯出最后一个冷却段为其生命终点。
在此过程中,全过程定周期跟踪其接受的冷却水量等数据,实时计算其凝固状态,并推定出其各相区域的分布情况。
根据各铸片的计算结果,综合推定整个铸机内板坯的凝固状态,动态推定出凝固终点位置、两相区和液相区的分布情况。
3.5.2 切长优化模型切长优化模型以满足合同需求为目标,并兼顾板坯收得率为原则,针对浇铸异常点进行优化。
参照板坯制造命令中的切割长度及其上、下限为基准,同时考虑品质异常部位(插铁板、异钢种交接,中间包交换、切尾)计算出钢水不足、钢水多余并根据钢水量的多少应用相关的优化策略进行优化计算,以实现预定板坯的消化,同时争取较高的收得率。
钢包钢水浇注开始,参照制造命令,生成该炉次的切割预定,在浇铸过程中,跟踪发生的异常事件,考虑影响的区域(工艺规定),进行优化计算。
在板坯切割开始时,根据切割的实际情况进行切割优化的再计算。
并把优化结果通过人机界面展现给用户。
优化过程主要包括:切割缝隙的考虑,采样的考虑,异常段的优化,板坯在钢水不足和钢水多余情况下的优化。
3.5.3 品质异常判定模型该模型包含在线判定部分和分析部分2个模块。
在线判定:主要功能是:通过采集炼钢、连铸过程中对连铸的浇铸、板坯质量有可能产生影响的事件进行跟踪记录,并根据内建的模型进行分析,对连铸的质量给出一定的判断结论,从而达到连铸从上台到浇注成材的整个过程中对连铸浇注进行质量判断、提供操作指导,并在板坯产出时,对板坯的整体质量进行判断、提供操作指导。
并将以上数据与结论很好地展示给工艺人员。
离线分析:具备很好的开发性,提供足够的离线学习功能和在线扩展功能。
工艺人员不但能够对系统定义的异常进行调整,还能够利用模型提供的离线分析工具对历史数据进行分析,从而根据分析发现并定义新的约束条件,并将其加入到在线判定系统中实现自动判定。
3.6 人机界面人机界面主要提供了计划管理、设备管理、操作监视、模型、实绩、报警和提示信息等画面。
每个画面有共通的部分,主要是画面菜单、画面名称、报警或提示信息、工具栏功能键、班别、组别、当前时间。
各个操作室和控制室的终端画面的权限通过用户名和角色统一认证管理,不同的角色拥有的权限不一样,看到的画面数量也不一样,对同一幅画面的操作权限也不一样。
不同的用户可以拥有一个或者多个的角色。
4 结语通过实施了连铸过程控制系统,八钢二炼钢连铸区域实现了连铸生产过程的全程自动控制和对生产数据的全程监视,管理层亦能了解到现场的实时生产情况,并且所有生产都遵照合同和计划统一调度进行生产,从而提高连铸生产的自动化程度,降低生产人员的作业率,提高了生产效率。
通过模型的应用,提高和稳定了铸坯的质量,并提高了铸坯的成材率。
参考文献[1] 宝信八一钢铁二炼钢连铸过程计算机系统基本设计书.[2] 宝信自动化研究所连铸模型设计书.。