降低GX133D眼镜组件板SMT生产不良率PPT(共 48张)
合集下载
SMT不良现象确认及如何检验不良技巧演示幻灯片

SMT不良现象&目视检验技巧
1
空焊
空焊: 零件脚或引线脚与锡垫间没有锡或 其它因素造成没有接合 假焊: 假焊之现象与空焊类似,但其锡垫 之锡量太少,低于接合面标准。 冷焊:锡或锡膏在回风炉气化后,在锡垫 上仍有模糊的粒状附着物。
2
一、空焊
3
一、空焊
4
一、空焊
1.造成的原因有:零件偏移,浮起,PIN歪,PIN翹,PIN 偏移,PCB PAD未印錫,錫少,零件PIN&PAD氧化﹐反貼﹐反向等﹔
36
Thank You
37
21
九、夾件
造成原因有:機器拋件﹐程式異常等﹔
檢驗方式﹕1.從不同角度確認零件下方是否有多余的零件存在 2.檢驗方式與多件雷同,夾件會造成零件空焊或 浮件等不良﹐BGA下原因有:零件未打到﹑打不進定位孔,PCB上有異物或零件 頂到﹐未按壓到位﹔
檢驗方式﹕ 從不同角度確認零件是否有高翹,目視無法判定 時可以用檢驗工具(塞規)﹔
29
十四、錯件
造成的原因有:手擺錯件,維修錯件,架錯料,來 料錯料,發錯料﹐置件錯﹐程式錯﹐標示錯﹐手Key in 錯等﹔
檢驗方式﹕檢驗時分時間段對照首件板﹐碑文&顏色等﹐ 疑問時及時反饋﹔
30
十五、撞件
造成的原因有:受外力碰撞,與尖銳/較硬物品放置 在一起,摔板,撞板,掉板﹐堆板﹔
檢驗方式與檢驗缺件雷同,不同之處在於非正常缺件,為 受外力碰撞造成,會有置件痕跡存在﹔
12
多件
多件是指PCB板面或PAD点上不置件位 置有置件或多余零件掉落PCB板面上
13
四、多件
14
四、多件
造成原因有:機器拋件﹐設計變更程式未更新﹐機器及程式異常等﹔
1
空焊
空焊: 零件脚或引线脚与锡垫间没有锡或 其它因素造成没有接合 假焊: 假焊之现象与空焊类似,但其锡垫 之锡量太少,低于接合面标准。 冷焊:锡或锡膏在回风炉气化后,在锡垫 上仍有模糊的粒状附着物。
2
一、空焊
3
一、空焊
4
一、空焊
1.造成的原因有:零件偏移,浮起,PIN歪,PIN翹,PIN 偏移,PCB PAD未印錫,錫少,零件PIN&PAD氧化﹐反貼﹐反向等﹔
36
Thank You
37
21
九、夾件
造成原因有:機器拋件﹐程式異常等﹔
檢驗方式﹕1.從不同角度確認零件下方是否有多余的零件存在 2.檢驗方式與多件雷同,夾件會造成零件空焊或 浮件等不良﹐BGA下原因有:零件未打到﹑打不進定位孔,PCB上有異物或零件 頂到﹐未按壓到位﹔
檢驗方式﹕ 從不同角度確認零件是否有高翹,目視無法判定 時可以用檢驗工具(塞規)﹔
29
十四、錯件
造成的原因有:手擺錯件,維修錯件,架錯料,來 料錯料,發錯料﹐置件錯﹐程式錯﹐標示錯﹐手Key in 錯等﹔
檢驗方式﹕檢驗時分時間段對照首件板﹐碑文&顏色等﹐ 疑問時及時反饋﹔
30
十五、撞件
造成的原因有:受外力碰撞,與尖銳/較硬物品放置 在一起,摔板,撞板,掉板﹐堆板﹔
檢驗方式與檢驗缺件雷同,不同之處在於非正常缺件,為 受外力碰撞造成,會有置件痕跡存在﹔
12
多件
多件是指PCB板面或PAD点上不置件位 置有置件或多余零件掉落PCB板面上
13
四、多件
14
四、多件
造成原因有:機器拋件﹐設計變更程式未更新﹐機器及程式異常等﹔
最新smt制程不良原因及改善措施分析ppt课件
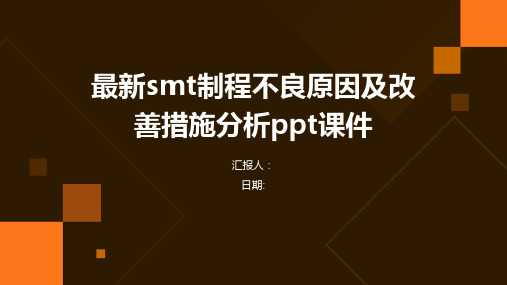
最新smt制程不良原因及改 善措施分析ppt课件
汇报人: 日期:
目录
• SMT制程概述 • SMT制程不良原因分析 • SMT制程改善措施分析 • 案例分析与实施效果评估
01
SMT制程概述
SMT制程简介
表面组装技术
SMT是表面组装技术(Surface Mounted Technology)的缩写,是一种将电 子元件直接安装在印刷电路板(PCB)表面的技术。
降低成本
SMT技术提高了生产效率 ,降低了生产成本,使得 电子产品更加普及和个性 化。
SMT制程常见问题
锡膏印刷问题:锡膏印刷是SMT制程中的关键步 骤之一,常见问题包括锡膏量不足、偏移、桥接 等,影响焊接质量。
焊接问题:焊接过程中可能出现虚焊、冷焊、焊 接不良等问题,主要原因包括温度设置不当、焊 接时间不足、PCB污染等。
元件贴装问题:元件贴装过程中可能出现元件偏 移、翻转、损坏等问题,主要原因包括设备参数 设置不当、元件供料器故障等。
针对以上问题,我们将详细介绍不良原因分析及 改善措施,以提高SMT制程的良率和生产效率。
01
SMT制程不良原因分析
设备故障导致的不良
设备老化
长时间运行的设备可能出 现磨损和老化,导致定位 不准、传输错误等不良现 象。
维护不足
设备缺乏定期维护和保养 ,可能导致精度下降、故 障率增加。
操作不当
操作人员对设备不熟悉或 操作不规范,可能引发误 操作,造成产品不良。
材料问题导致的不良
原材料缺陷
原材料本身存在缺陷,如PCB 板翘曲、元器件引脚氧化等,
影响制程质量。
储存条件不当
材料储存环境湿度过高、温度过高 或过低可能导致材料性能发生变化 。
汇报人: 日期:
目录
• SMT制程概述 • SMT制程不良原因分析 • SMT制程改善措施分析 • 案例分析与实施效果评估
01
SMT制程概述
SMT制程简介
表面组装技术
SMT是表面组装技术(Surface Mounted Technology)的缩写,是一种将电 子元件直接安装在印刷电路板(PCB)表面的技术。
降低成本
SMT技术提高了生产效率 ,降低了生产成本,使得 电子产品更加普及和个性 化。
SMT制程常见问题
锡膏印刷问题:锡膏印刷是SMT制程中的关键步 骤之一,常见问题包括锡膏量不足、偏移、桥接 等,影响焊接质量。
焊接问题:焊接过程中可能出现虚焊、冷焊、焊 接不良等问题,主要原因包括温度设置不当、焊 接时间不足、PCB污染等。
元件贴装问题:元件贴装过程中可能出现元件偏 移、翻转、损坏等问题,主要原因包括设备参数 设置不当、元件供料器故障等。
针对以上问题,我们将详细介绍不良原因分析及 改善措施,以提高SMT制程的良率和生产效率。
01
SMT制程不良原因分析
设备故障导致的不良
设备老化
长时间运行的设备可能出 现磨损和老化,导致定位 不准、传输错误等不良现 象。
维护不足
设备缺乏定期维护和保养 ,可能导致精度下降、故 障率增加。
操作不当
操作人员对设备不熟悉或 操作不规范,可能引发误 操作,造成产品不良。
材料问题导致的不良
原材料缺陷
原材料本身存在缺陷,如PCB 板翘曲、元器件引脚氧化等,
影响制程质量。
储存条件不当
材料储存环境湿度过高、温度过高 或过低可能导致材料性能发生变化 。
降低整机生产不良率ppt课件

考核合格考核合格81781781981922工装夹具不规工装夹具不规范导致范导致包装或运输生产物料包装或运输生产物料时工装是否符合要求时工装是否符合要求现场测量调查现场测量调查是否符合工装规格是否符合工装规格及要求及要求张繁荣张繁荣81781782082033qcqc检验员工误检验员工误判所致判所致qcqc检验人员对标准检验人员对标准掌握的程度及对不良掌握的程度及对不良判定的一致性判定的一致性现场试验及调查现场试验及调查是否熟练掌握检验是否熟练掌握检验标准对不良判定标准对不良判定的一致性是否统一的一致性是否统一81781782482444软件与软件与crtcrt匹匹配配存在缺陷存在缺陷是否匹配存在缺陷是否匹配存在缺陷与设计师沟通确认与设计师沟通确认与设计师及供应商与设计师及供应商确认判断确认判断81781782482455机芯手插不良机芯手插不良利用利用paretopareto鱼鱼骨图等分析工具进行进一步的分析骨图等分析工具进行进一步的分析兵兵81781782782766机芯检焊不良机芯检焊不良81781782782777机心操作不良机心操作不良8178178278271
公司规定:凡操作员工上岗前必须经过培 训,并经考核合格获取上岗证后才能上岗。
1、通过调查发现:从事物料发放及上板工位员 工都具有上岗证;
2、于8月19日对4名机芯发料员、4名整机发料 领料员及1名上机芯板人员进行现场考核,
• 结果全部合格。符合公司要求
姓名 A1 B1
是否具有上 是
是
岗证
现场考核是 是
判断的准确率 100% 87.5% 100% 100%
SS 87.5%
GG 100%
结论:QC检验人员误判不是主要原因。
18
要因确认四:软件与CRT匹配存在缺陷;
公司规定:凡操作员工上岗前必须经过培 训,并经考核合格获取上岗证后才能上岗。
1、通过调查发现:从事物料发放及上板工位员 工都具有上岗证;
2、于8月19日对4名机芯发料员、4名整机发料 领料员及1名上机芯板人员进行现场考核,
• 结果全部合格。符合公司要求
姓名 A1 B1
是否具有上 是
是
岗证
现场考核是 是
判断的准确率 100% 87.5% 100% 100%
SS 87.5%
GG 100%
结论:QC检验人员误判不是主要原因。
18
要因确认四:软件与CRT匹配存在缺陷;
SMT制程常见缺陷分析与改善ppt课件

5
1)避免锡膏直接与空气接触,对停留在网板上长时间不使用的锡膏则回
SMT制程常见缺陷分析与改善
不良项 目 不良概 述
发生原 因
改善方 法
生半田(冷焊)
锡膏在过回流炉后未彻底的融化,存在像细沙一样的颗粒,焊点表面无光 泽
1)主要由于回流炉的回流温度偏低,回流区时间偏短,使锡膏未完全融 化而形成 2) 锡膏过期,在正常的回流温度下使锡膏未得到充分的融化。 3)较大元件回流时由于部品吸热较多,使锡膏没有吸收到较大的热量而 出现。 4)回流过程中基板被卡在回流炉中间,未通过回流区便人为取出,导致 锡膏未彻底溶化。 5)回流炉的链速设定过快或风机频率设定偏低,使锡膏未彻底的回流融 化。
改善方 法
1)调整实装程序的X,Y坐标或角度
2)更改贴装时部品相机识别方式,特别是QFP,较密集的CN类元件。
3)确认轨道宽度(轨道宽度设置一般是比基板宽度宽0.5MM),确认顶 针布置均匀合理,MAER数据正常,设置位置合理,不会错识别到旁边点。
4)调整吸料位置,使吸嘴吸在元件中间无偏移。
7
5)适当减少印刷刮刀压力及均匀分布顶针,使印刷锡量增加且均匀
1)印刷机刮刀压力过大,使刮刀将网孔中的锡膏刮掉,印刷在基板铜箔 上的 效果为四周高中间底,使回流后元件锡量少。
2)印刷网板的网孔由于未清洗干净,锡粒粘附在开口部周边凝固后造成 网孔堵塞而导致印刷锡少
3)印刷网板开口偏小或网板厚度偏薄不能满足元件回流后的端子锡量
4)贴装移位造成元件回流后锡少
5)印刷速度过快,锡膏在刮刀片下滚动过快,使锡膏来不及充分的印刷 在网孔中
1)在曲线图规定条件内适当增高回流区的温度与时间范围,使锡膏得到 充分融化 2)更换过期锡膏,另外可加入阻焊剂再充分搅拌(一般不采用) 3)针对有大型元件的基板,回流时可适当增加各温区的温度,使锡膏能
1)避免锡膏直接与空气接触,对停留在网板上长时间不使用的锡膏则回
SMT制程常见缺陷分析与改善
不良项 目 不良概 述
发生原 因
改善方 法
生半田(冷焊)
锡膏在过回流炉后未彻底的融化,存在像细沙一样的颗粒,焊点表面无光 泽
1)主要由于回流炉的回流温度偏低,回流区时间偏短,使锡膏未完全融 化而形成 2) 锡膏过期,在正常的回流温度下使锡膏未得到充分的融化。 3)较大元件回流时由于部品吸热较多,使锡膏没有吸收到较大的热量而 出现。 4)回流过程中基板被卡在回流炉中间,未通过回流区便人为取出,导致 锡膏未彻底溶化。 5)回流炉的链速设定过快或风机频率设定偏低,使锡膏未彻底的回流融 化。
改善方 法
1)调整实装程序的X,Y坐标或角度
2)更改贴装时部品相机识别方式,特别是QFP,较密集的CN类元件。
3)确认轨道宽度(轨道宽度设置一般是比基板宽度宽0.5MM),确认顶 针布置均匀合理,MAER数据正常,设置位置合理,不会错识别到旁边点。
4)调整吸料位置,使吸嘴吸在元件中间无偏移。
7
5)适当减少印刷刮刀压力及均匀分布顶针,使印刷锡量增加且均匀
1)印刷机刮刀压力过大,使刮刀将网孔中的锡膏刮掉,印刷在基板铜箔 上的 效果为四周高中间底,使回流后元件锡量少。
2)印刷网板的网孔由于未清洗干净,锡粒粘附在开口部周边凝固后造成 网孔堵塞而导致印刷锡少
3)印刷网板开口偏小或网板厚度偏薄不能满足元件回流后的端子锡量
4)贴装移位造成元件回流后锡少
5)印刷速度过快,锡膏在刮刀片下滚动过快,使锡膏来不及充分的印刷 在网孔中
1)在曲线图规定条件内适当增高回流区的温度与时间范围,使锡膏得到 充分融化 2)更换过期锡膏,另外可加入阻焊剂再充分搅拌(一般不采用) 3)针对有大型元件的基板,回流时可适当增加各温区的温度,使锡膏能
组件产线不良及改善措施分析报告ppt课件

影响范围
这些不良现象会导致产品质量下降、 客户投诉增加、生产成本上升等一系 列问题,严重影响企业的经济效益和 声誉。
不良原因分析
01
02
03
04
原材料问题
原材料质量不稳定、供应不及 时等都会导致产线出现不良品
。
设备故障
设备老化、维护不到位等问题 会造成产线运行不稳定,产品
不良率上升。
操作不规范
员工操作不熟练、技能水平不 够等问题也会导致产品不良率
增加。
环境因素
温度、湿度、灰尘等环境因素 也会影响产品的质量稳定性。
不良率统计与分析
01
02
03
不良率定义
不良品数量与总生产数量 的比值。
不良率统计
通过收集产线上的不良品 数量,统计出不同时间段 、不同产品的不良率。
不良率分析
采用数据分析方法,找出 不良率的波动规律、趋势 变化,为后续的改善措施 提供依据。
对组件产线的不良品进行详细的数据分析,找出主要原因,为后 续改善措施提供方向。
引进先进技术和设备
升级或引入更精确、稳定的生产设备和技术,降低不良品的产生。
强化员工培训和技能提升
通过定期的培训,提高员工的操作技能和质量意识,减少人为因素 导致的不良品。
改善措施实施与跟踪
01
制定实施计划
明确改善措施的具体步骤和时间节点,确保改善活动有条不紊地进行。
改善效果评估
对已实施的改善措施进行效果评估, 通过数据和图表展示改善前后的对比 ,证明措施的有效性。
后续建议
深化原因分析
对于尚未解决或效果不明显的不良现象,建议进一步深化 原因分析,找到根本原因,为后续改善提供方向。
强化跨部门协作
这些不良现象会导致产品质量下降、 客户投诉增加、生产成本上升等一系 列问题,严重影响企业的经济效益和 声誉。
不良原因分析
01
02
03
04
原材料问题
原材料质量不稳定、供应不及 时等都会导致产线出现不良品
。
设备故障
设备老化、维护不到位等问题 会造成产线运行不稳定,产品
不良率上升。
操作不规范
员工操作不熟练、技能水平不 够等问题也会导致产品不良率
增加。
环境因素
温度、湿度、灰尘等环境因素 也会影响产品的质量稳定性。
不良率统计与分析
01
02
03
不良率定义
不良品数量与总生产数量 的比值。
不良率统计
通过收集产线上的不良品 数量,统计出不同时间段 、不同产品的不良率。
不良率分析
采用数据分析方法,找出 不良率的波动规律、趋势 变化,为后续的改善措施 提供依据。
对组件产线的不良品进行详细的数据分析,找出主要原因,为后 续改善措施提供方向。
引进先进技术和设备
升级或引入更精确、稳定的生产设备和技术,降低不良品的产生。
强化员工培训和技能提升
通过定期的培训,提高员工的操作技能和质量意识,减少人为因素 导致的不良品。
改善措施实施与跟踪
01
制定实施计划
明确改善措施的具体步骤和时间节点,确保改善活动有条不紊地进行。
改善效果评估
对已实施的改善措施进行效果评估, 通过数据和图表展示改善前后的对比 ,证明措施的有效性。
后续建议
深化原因分析
对于尚未解决或效果不明显的不良现象,建议进一步深化 原因分析,找到根本原因,为后续改善提供方向。
强化跨部门协作
SMT常见不良鱼骨图分析ppt课件

過久 劑含 徑過 過期 度 屬性
量大
高低
吃錫
印刷 角度 刮刀 壓力 速度
精度 不夠
行程 不足
印刷 厚度
錫膏 印刷
不良
不佳 不平 不當 過快 刮刀
錫膏機
變形 硬度 平行度 不佳
間隙 錫量 參數設 脫模 不當 不足 定不當 速度
軌道 爐膛
張力 表面 開口 鋼板
過長
錫膏廠商
上料不 冷卻 速度 內有 溫區
不足 磨損 粗糙 厚度
PCB
濕度影響 錫膏特性
包裝後氧化 灰塵多 靜電排放
熟練程度 手放散料
鋼板未擦拭干淨 鋼板
缺乏品質意識
開口
開口
PCB PAD兩邊 有異 零件規格與 PAD 變形 不一致 物 PAD不符 氧化
錫膏添加不及時 鋼板未及時清洗 零件掉落地上
缺錫
形狀 方式
零件 過大 過重
丟失零件 找回後重 新使用
腳 彎
厚度差異 零件 過保
氧化 有異 有損 位置
不良
物
不當
通設風備溫手備度印料手高厚時印薄料台手手不帶錫手印印均過膏放手台缺力緊作散上抹搖錫度態料錫錫動不度不膏夠/均情I緒PA上 用手錫 量放手量 過錫零印過 多膏手件錫多 添印P位膏C加錫B移位印不尖移刷及過零狀時長件況檢受 潮查不吃錫性關夠仔元細過周期件與重量P零PAA件DD不 吃有符錫一不邊特良殊退距零冰不件時夠間有異物新屬 低金性零助焊劑使時長件用間厚存條不度黏度高放件好不錫變錫本特均膏干膏身性暮錫膏
機器置件不穩定 MTU振動過大
加熱器風量過大 料架振動過大
SOP不完善
操作不正確
MTU吸空Tray時將 下層零件吸繙面
料架推料過快
降低组件破片率改善计划PPT课件

内衬回收无检验 和次数规定?
3. 检验手法 (光电/组件)
员工数片/检 验手法是否规
范统一?
检验人员是否 均考核合格?
2. 运输方式
打包托盘的层 数规定是否符
合要求?
托盘上下车卸 货是否符合要
求?
4.检验漏失
厂内检验漏失 率过高?
厂内缺角返工 率过高? 7
对策及实施的策划一
序Hale Waihona Puke 项目对策实施方案负责人
副组长
组内分工
负责组织/策划本次改善活动,并监督各 组员工作进度 负责整个项目的开展并协调组件相关事 宜
副组长
负责制造相关对策的开展与监督执行
副组长
组员 组员 组员 组员
负责技术支持与协助 负责品管相关对策的开展执行与其他部 门改善对策的实施追踪 负责制造相关对策的制定与实施 负责与客户端相应沟通协调事宜
品管 销售
2012.01
4
检验漏失率的 降低
成立内部专案改善
/
品管 销售
2012.01
5
缺角/隐裂返工 率的降低
成立内部专案改善
/
制造 品管
2012.01
硅片原材料的
6 改善(如氧碳含 成立内部改善专案
/
量改善)
工艺 品管
20192.01
10
0.30% 0.28% 0.25% 0.25% 0.23% 0.20% 0.20% 0.18% 0.15% 0.15% 0.15% 0.12%
P
选定主题
设定目标
现状分析
原因分析
D
提出对策
对策实施
C
效果验证
A
标准化
计划进度:
3. 检验手法 (光电/组件)
员工数片/检 验手法是否规
范统一?
检验人员是否 均考核合格?
2. 运输方式
打包托盘的层 数规定是否符
合要求?
托盘上下车卸 货是否符合要
求?
4.检验漏失
厂内检验漏失 率过高?
厂内缺角返工 率过高? 7
对策及实施的策划一
序Hale Waihona Puke 项目对策实施方案负责人
副组长
组内分工
负责组织/策划本次改善活动,并监督各 组员工作进度 负责整个项目的开展并协调组件相关事 宜
副组长
负责制造相关对策的开展与监督执行
副组长
组员 组员 组员 组员
负责技术支持与协助 负责品管相关对策的开展执行与其他部 门改善对策的实施追踪 负责制造相关对策的制定与实施 负责与客户端相应沟通协调事宜
品管 销售
2012.01
4
检验漏失率的 降低
成立内部专案改善
/
品管 销售
2012.01
5
缺角/隐裂返工 率的降低
成立内部专案改善
/
制造 品管
2012.01
硅片原材料的
6 改善(如氧碳含 成立内部改善专案
/
量改善)
工艺 品管
20192.01
10
0.30% 0.28% 0.25% 0.25% 0.23% 0.20% 0.20% 0.18% 0.15% 0.15% 0.15% 0.12%
P
选定主题
设定目标
现状分析
原因分析
D
提出对策
对策实施
C
效果验证
A
标准化
计划进度:
SMT原创改善报告ppt课件
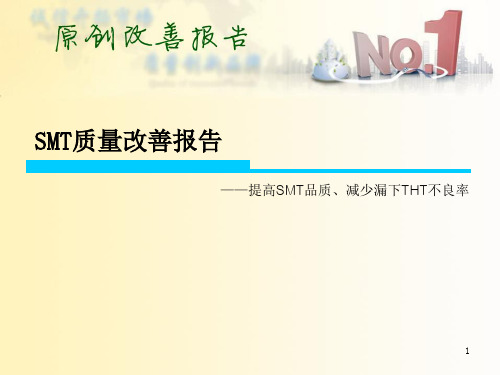
重新确认钢网验证标准
已完成
示 图
说 明
根据IPC7525(钢网开孔)标准,钢网入厂检验标准制定是合理的
14
六、对策实施
6、连焊: 对策2---根据钢网检验标准确认钢网开孔是否合理
IC引脚
示图
引脚宽度
使用品管MEGAVIEW smartmeau设备 进行测试,钢网开孔尺寸有0.25mm
534 4 21 35234466114231421
11
5
0
翻白S1 翻白S2 翻白S3 翻白S4 翻白S5 反向S1 反向S2 反向S3 反向S4 反向S5 连焊S1 连焊S2 连焊S3 连焊S4 连焊S5 漏焊S1 漏焊S2 漏焊S3 漏焊S4 漏焊S5 漏贴S1 漏贴S2 漏贴S3 漏贴S4 漏贴S5 其它S1 其它S2 其它S3 其它S4 其它S5 翘脚S1 翘脚S2 翘脚S4 移位S1 移位S2 移位S3 移位S4 移位S5
改善前
对策
示 图
说 明
无亮度检查
增加亮度检查后,S1-S3再现无发现翻白不良 (13-01-15完成)
9
六、对策实施
1、翻白: 对策1---贴片机的PARTS库增加元件底部的亮度检查 改善效果---改善日期为2013-01-17号
改善前
改善后
示 图
说 明
改善后无再发现CHIP件翻白投诉,只有S4/S5出现3个IC反面(S4\S5的YAMAHA设备设置 亮度识别后抛料率较高,现未设置亮度识别,但YAMAHA生产空调产品的机率小,生 产普通板CHIP件少,所以松下的增加亮度识别后,翻白的不良就能减少很多)
三、现状问题
4、数据按型号的不良类型进行分析:
30 26
25
已完成
示 图
说 明
根据IPC7525(钢网开孔)标准,钢网入厂检验标准制定是合理的
14
六、对策实施
6、连焊: 对策2---根据钢网检验标准确认钢网开孔是否合理
IC引脚
示图
引脚宽度
使用品管MEGAVIEW smartmeau设备 进行测试,钢网开孔尺寸有0.25mm
534 4 21 35234466114231421
11
5
0
翻白S1 翻白S2 翻白S3 翻白S4 翻白S5 反向S1 反向S2 反向S3 反向S4 反向S5 连焊S1 连焊S2 连焊S3 连焊S4 连焊S5 漏焊S1 漏焊S2 漏焊S3 漏焊S4 漏焊S5 漏贴S1 漏贴S2 漏贴S3 漏贴S4 漏贴S5 其它S1 其它S2 其它S3 其它S4 其它S5 翘脚S1 翘脚S2 翘脚S4 移位S1 移位S2 移位S3 移位S4 移位S5
改善前
对策
示 图
说 明
无亮度检查
增加亮度检查后,S1-S3再现无发现翻白不良 (13-01-15完成)
9
六、对策实施
1、翻白: 对策1---贴片机的PARTS库增加元件底部的亮度检查 改善效果---改善日期为2013-01-17号
改善前
改善后
示 图
说 明
改善后无再发现CHIP件翻白投诉,只有S4/S5出现3个IC反面(S4\S5的YAMAHA设备设置 亮度识别后抛料率较高,现未设置亮度识别,但YAMAHA生产空调产品的机率小,生 产普通板CHIP件少,所以松下的增加亮度识别后,翻白的不良就能减少很多)
三、现状问题
4、数据按型号的不良类型进行分析:
30 26
25
SMT不良解说ppt课件

定義:元件重疊, 或不該有元件的位置而貼有元件,稱爲多件.
圖例: 圖-26
圖-27
圖-28
多件的影響:影響產品的外觀;影響產品的電性;影響板卡的裝配.
精选课件ppt
11
側立(Sideward):
定義:元件的焊接位置是在其側面焊接的,稱爲側立.
圖例: 圖-29
圖-30
圖-31
側立的影響:影響產品的外觀,降低元件的焊接可靠度,影響板卡的裝配.
精选课件ppt
15
多錫(Excess So 圖-41
圖-42
多錫的影響:影響產品的外觀,對元器件的電性連接造成潛在的危險,影響板
卡的組裝.
精选课件ppt
16
反向(Reverse):
定義: 有極性或方向要求的元件在貼片后方向錯誤或極性相 反,稱爲反向.
拒焊(Negative Solder):
定義: 零件的PAD/PIN与PCB板的PAD沒有良好的焊接或無 法吃錫,稱爲拒焊.
圖例:
圖-11
圖-12
圖-13
拒焊的影響:導致元件的焊接可靠度下降,影響元件及綫路正常的連接,影響板卡
正常功能.
精选课件ppt
5
墓碑(Tombstone):
定義: 零件的一端焊接良好,另一端未焊接且與PCB的PAD脫 離並立起,稱爲墓碑/立碑.
定義: PCB板因來料問題或經過SMT制程產生的板卡彎曲/ 變形不良,稱爲板翹.
圖例:
圖-55
圖-56
板翹的影響:嚴重影響產品的外觀,影響元件的焊錫可靠度,影響成品的組裝.
精选课件ppt
23
綫路不良(Circuit Defect):
定義: PCB板的綫路因來料問題或SMT制程問題有綫路損傷 、壓痕、斷開 等不良現象,稱爲綫路不良.
圖例: 圖-26
圖-27
圖-28
多件的影響:影響產品的外觀;影響產品的電性;影響板卡的裝配.
精选课件ppt
11
側立(Sideward):
定義:元件的焊接位置是在其側面焊接的,稱爲側立.
圖例: 圖-29
圖-30
圖-31
側立的影響:影響產品的外觀,降低元件的焊接可靠度,影響板卡的裝配.
精选课件ppt
15
多錫(Excess So 圖-41
圖-42
多錫的影響:影響產品的外觀,對元器件的電性連接造成潛在的危險,影響板
卡的組裝.
精选课件ppt
16
反向(Reverse):
定義: 有極性或方向要求的元件在貼片后方向錯誤或極性相 反,稱爲反向.
拒焊(Negative Solder):
定義: 零件的PAD/PIN与PCB板的PAD沒有良好的焊接或無 法吃錫,稱爲拒焊.
圖例:
圖-11
圖-12
圖-13
拒焊的影響:導致元件的焊接可靠度下降,影響元件及綫路正常的連接,影響板卡
正常功能.
精选课件ppt
5
墓碑(Tombstone):
定義: 零件的一端焊接良好,另一端未焊接且與PCB的PAD脫 離並立起,稱爲墓碑/立碑.
定義: PCB板因來料問題或經過SMT制程產生的板卡彎曲/ 變形不良,稱爲板翹.
圖例:
圖-55
圖-56
板翹的影響:嚴重影響產品的外觀,影響元件的焊錫可靠度,影響成品的組裝.
精选课件ppt
23
綫路不良(Circuit Defect):
定義: PCB板的綫路因來料問題或SMT制程問題有綫路損傷 、壓痕、斷開 等不良現象,稱爲綫路不良.
如何使不良率降低(ppt 101页)

顾客的不满意及更多的浪费.
27
2.2.2 一个好的暂对策将
不制造新的问题. 评估对策所造成的风险. 设立标Байду номын сангаас来观察其有效性. 采用适当的方法‧程序来观察结果. 建立完整的文件作将来的参考.
28
某些可能的暂时对策如下: 检验 检出 修理 取代 换部品来源
29
2.2.3 我们的目标
是把我们的工作(努力)从改正 缺点移向制程管制和预防品管.
A) 缺点检查是一种过去导向的 策略,它被用来找出并分离好 与坏的输出(结果)
23
B) 缺点检查(A)
容许如报废或补修的浪费。 采用检验、稽核或检查,这些通常 不能解决全部的情况。 最终检验的訴求以顾客为对象。 是昂贵的。
对所有的缺点都采用同样的作法。
24
B) 缺点检查(B)
以规格为依据。 针对结果采取行动。 提供较慢的回馈。 缺点检查是一种依赖检验的制程 管制方法。 缺点检查专注在改正制程的输出, 亦即产品和服务。 缺点检查容忍浪费,是昂贵的 。 25
◎ 产出链的效益提升方法有二; 1)强固弱环 2)强固整个产出链
19
例: A) 原始第一时间(第一时间)成功率
(以五个工序为例): 0.9×0.9×0.9×0.6×0.9=0.39 B) 第一次改善第四工序后: 0.9×0.9×0.9×0.9×0.9=0.59
20
C) 如果第一次是改善第四工序以外的 工序时: 0.95×0.95×0.95×0.6×0.95=0.49
2.1.3 标准常态分配机率
Z 超过规格之机率 (单边)
-3.00 0.135 %
-3.05 0.114 %
-3.10 0.097 %
-3.15 0.082 %
降低不良率执行重点 优质课件

降低不良率執行重點
26.千萬不可以明知有問題但是還是允許它活生生不斷 出現.
27.問題一定得越早對策處理,才會有效,同時處理成本 會越低.
28.吵架及一味地責怪他人或毫無根據狡辯只有對公司 造成更大的傷害,斷送良機.
29.解決問題的時機很重要,時機不會等你的!該加班分析, 一定要配合加班.
成品組立線用的PCBA, 其供應者為PCBA Chassis線). 您是客 戶,一定要要求供應者提供無缺陷的產品或服務,就好 像您自 己出錢買東西一樣,不是嗎?
降低不良率執行重點
5. 你想要降低不良,就一定要在發現不良後立即很清楚的回 饋給造成不良的源頭,積極對策,同時追蹤對策之有效性.
6. 一定要填寫不良回饋及防止再發請求書,但是不要等到見 到報告才動作,太晚了!見到報表時,不良可能已經滿山滿谷 了!
10.記得: 有問題一定要即時反應並要求配合與支援 . 會哭的小孩有奶喝!(反映) . 早起的鳥兒有蟲吃!(時機)
11.問題一定要在第一現場才能看清楚,不要憑空想像問題. 12.不要自己騙自己,自己安慰自己,自欺欺人. 13.對別人善意的回饋,不要當成是責難.
降低不良率執行重點
14.不管不良的比率是“多少”, 能找出不良根源的問題就一 定“能”解決,也一定“要”解決.
忙一場,虛功一件.
降低不良率執行重點
35.天下沒有解決不了的問題,只要您以正確的心態去解 決問題,落實以上的基本動作.
36.您自己沒有信心或對策不成熟所生產出來的產品 一定要做記號及記錄.萬一出狀況,您可以不必海 底 撈針.
15.客戶有權力要求供應者處理及維修他所供應之不良品. 16.在對策前所生產的東西肯定有不良,請供應者務必記得
- 1、下载文档前请自行甄别文档内容的完整性,平台不提供额外的编辑、内容补充、找答案等附加服务。
- 2、"仅部分预览"的文档,不可在线预览部分如存在完整性等问题,可反馈申请退款(可完整预览的文档不适用该条件!)。
- 3、如文档侵犯您的权益,请联系客服反馈,我们会尽快为您处理(人工客服工作时间:9:00-18:30)。
过多
锡膏过干
锡膏使用 时间过长
PCB板 V 割槽过深
印刷偏移
Байду номын сангаас
PCB板翘 曲
贴装偏移
GL板一次回 流后PCB板
翘曲
贴片机精 度不足
贴装后锡 膏坍塌连
锡
印刷连锡 插座连锡
连锡
连锡SPI 不检出
SPI制程软 件缺陷
45度元件 连锡框SPI 无法识别
偏移
K1位偏 移
K1位回流 焊接偏移
插座固定脚 尺寸与PCB 板尺寸存在
偏差
P6位物料 规格不一致
制图:蔡正伟 12
日期:2012-8-2
八、原因分析
P DCA
经过小组成员的共同分析,共找到8条末端因素
• GL板一次回流后翘曲 • PCB板V割槽深 • SPI制程制程软件缺陷 • 操作员锡膏量添加过多 • 插座引脚钢网开孔安全间距小 • 贴片机贴装精度不足 • P6位物料规格不一致 • K1位回流焊接偏移
13
八、要因确认
针对八个末端因素,小组成员制定了要因确认表:
P DCA
序号 末端因素
确认内容
确认方法
确认标准 责任人 完成时间
1
GL板一次回流 确认PCB一次回流后翘 后PCB板翘曲 曲度
仪器测量
PCB板对角线 翘曲度≤0.5%
林亚贞 2012-8-10
2
PCB板V割槽 过深
确认PCB板V割槽余厚
仪器测量
PCB板V割余厚 ≥0.35mm
郭延滨
2012-8-14
3
SPI制程软件 缺陷
确认SPI制程软件绘制 的45度角元件检测框连 锡是否可以检出
现场确认
45度角元件印 刷连锡后SPI能 正常检出
洪志 邓永东
2012-8-15
4
印刷机操作员 锡膏量添加过 量
确认员工印刷时锡膏添 加量
仪器测量
添加后锡膏直径 为: 1.0≤D≤2.0cm
GL控制板
CD充电板
2、贴装生产流程:
印刷机
SPI测试
高速机
多功能机
回流焊
AOI测试
7
三、流程&名词解释
3、名词解释 1. SMT生产不良率(DPPM)=
SMT生产不良点数+反馈不良点数
SMT生产实际贴装点数
X 1000000
2. SMT:Surface Mount Technology 的缩写,中文意思为表面贴装技术。
降低GX13-3D眼镜组件板 SMT生产不良率
TCL多媒体全球运营本部 “Zero”QC小组
1
公司简介
TCL集团创立于1981年,是中国最大的、全球性规模经营的消费类电子企业集 团之一,旗下拥有三家上市公司、四大产业集团、六大业务板块,总部设在广东省惠 州市,产品涵盖家电、通讯、信息、电工等,员工总数六万多人。
3. 贴 片:将贴片元件从指定位置拾取后贴放到PCB板上指定位置的动作。 4、项目数据来源
课题活动所用数据来自公司的PTM 系统(生产技术信息管理系统)及车间 生产日报表,数据真实可靠。
8
四、行动计划
P DCA
为保证本次QC小组活动能够顺利实现,小组成员共同制定详细、周密 的活动计划表。
阶段
内容
7月份
制表:邓永东
日期:2012-8-2
10
六、目标设定
P DCA
小组成员决定将生产不良率目标设定为:由162DPPM降至 ≤100DPPM
11
七、原因分析
P DCA
由于影响不良率的问题点相互影响且较复杂,因此小组成员对连锡、偏 移两个不良现象绘制了关联图进行分析:
插座引脚钢 网开孔安全
间距小
操作员锡 膏量添加
9
五、现状调查
P DCA
小组成员对7月份GX13-3D眼镜组件板生产不良数据进行统计分析:
需重点改善
1、通过对7月份生产不良数据进行分析:偏移,连锡占总不良的77.2%,为主要症结,是 本次项目的改善重点; 2、经小组成员讨论我们有把握改善主要症结50%的不良
162DPPM*(1-77.2%*50%)=99.5DPPM; 3、查看2012年GX13-3D眼镜组件板生产不良率,1月份最低不良率118DPPM.
生产 现状
产生 危害
选定课题
1、 1-6月份因生产不良产生的返工及返修费用累计为:47733元 2、无法满足后工序正常的生产需求,急需改善
降低GX13-3D眼镜组件板SMT生产不良率
6
三、流程&名词解释
1、完整的眼镜板组件包含:40-3DGX13-GL*4XG (GL板) 40-3DGX13-CD*2XG(CD板)
TCL多媒体GOC LCD工厂是TCL集团旗下最大的生产基地,拥有全球顶尖的数字 电视研发团队及一流的工业设计能力。拥有先进的彩电生产设备,主要生产LCD、 LED彩色电视机,2012年生产整机1500多万台,位居全球第四位。
2
目录
1. 小组介绍 2. 选题理由 3. 流程&名词解释 4. 行动计划 5. 现状调查 6. 目标设定 7. 原因分析
8. 要因确认 9. 制定对策 10.对策实施 11.效果确认 12.巩固措施 13.总结及未来规划
3
一 、小组介绍
小组名称 课题名称 课题类型
Zero
降低GX13-3D眼镜组件板 SMT生产不良率
现场型
活动周期
2012.7- 2012.11
序号 1 2 3 4 5 6
成员
组长
成员
姓名
邓永东 郭延滨 蔡正伟 洪志 林亚贞 廖冬
日期:2012-7-18
一 、小组介绍
活动口号: 突破极限!
5
二、选题理由
公司 趋势
LED-3D电视已成为市场主流产品,12年公司目标销售产量1500 万台,按公司标配一台3D电视配两副眼镜 ,3D眼镜需求量大,好的 产品质量是占据市场的重要前提。
小组成员对2012年1月--6月的GX13-3D眼镜板生产不良数据进行统 计,结果显示GX13-3D眼镜组件板生产不良率最高达到226DPPM,平均 不良率为162DPPM。
小组成员 职务
工艺工程师 主任工程师 工艺工程师 工艺工程师
工艺助工 工艺助工
制表:邓永东 4
注册编号
GIC-2012H2-40
成立时间
2012-7-14
注册时间 TQC培训时间
2012-7-14 30-60时/人
组内分工
组织、策划、跟踪指导 工艺指导、资源协调 工艺指导、组织实施 实施及效果跟踪 不良确认及问题反馈 不良确认及问题反馈
8月份
9月份
10月份
1229 1230 1231 1232 1233 1235 1236 1237 1238 1239 1240 1241 1242
11月份 12月份 1月份
1243
现状调查
设定目标
P
原因分析
要因确认
制定对策
D 实施对策
C 效果确认
巩固措施
A
总结规划
制表:邓永东
计划时间
日期:2012-7-20
锡膏过干
锡膏使用 时间过长
PCB板 V 割槽过深
印刷偏移
Байду номын сангаас
PCB板翘 曲
贴装偏移
GL板一次回 流后PCB板
翘曲
贴片机精 度不足
贴装后锡 膏坍塌连
锡
印刷连锡 插座连锡
连锡
连锡SPI 不检出
SPI制程软 件缺陷
45度元件 连锡框SPI 无法识别
偏移
K1位偏 移
K1位回流 焊接偏移
插座固定脚 尺寸与PCB 板尺寸存在
偏差
P6位物料 规格不一致
制图:蔡正伟 12
日期:2012-8-2
八、原因分析
P DCA
经过小组成员的共同分析,共找到8条末端因素
• GL板一次回流后翘曲 • PCB板V割槽深 • SPI制程制程软件缺陷 • 操作员锡膏量添加过多 • 插座引脚钢网开孔安全间距小 • 贴片机贴装精度不足 • P6位物料规格不一致 • K1位回流焊接偏移
13
八、要因确认
针对八个末端因素,小组成员制定了要因确认表:
P DCA
序号 末端因素
确认内容
确认方法
确认标准 责任人 完成时间
1
GL板一次回流 确认PCB一次回流后翘 后PCB板翘曲 曲度
仪器测量
PCB板对角线 翘曲度≤0.5%
林亚贞 2012-8-10
2
PCB板V割槽 过深
确认PCB板V割槽余厚
仪器测量
PCB板V割余厚 ≥0.35mm
郭延滨
2012-8-14
3
SPI制程软件 缺陷
确认SPI制程软件绘制 的45度角元件检测框连 锡是否可以检出
现场确认
45度角元件印 刷连锡后SPI能 正常检出
洪志 邓永东
2012-8-15
4
印刷机操作员 锡膏量添加过 量
确认员工印刷时锡膏添 加量
仪器测量
添加后锡膏直径 为: 1.0≤D≤2.0cm
GL控制板
CD充电板
2、贴装生产流程:
印刷机
SPI测试
高速机
多功能机
回流焊
AOI测试
7
三、流程&名词解释
3、名词解释 1. SMT生产不良率(DPPM)=
SMT生产不良点数+反馈不良点数
SMT生产实际贴装点数
X 1000000
2. SMT:Surface Mount Technology 的缩写,中文意思为表面贴装技术。
降低GX13-3D眼镜组件板 SMT生产不良率
TCL多媒体全球运营本部 “Zero”QC小组
1
公司简介
TCL集团创立于1981年,是中国最大的、全球性规模经营的消费类电子企业集 团之一,旗下拥有三家上市公司、四大产业集团、六大业务板块,总部设在广东省惠 州市,产品涵盖家电、通讯、信息、电工等,员工总数六万多人。
3. 贴 片:将贴片元件从指定位置拾取后贴放到PCB板上指定位置的动作。 4、项目数据来源
课题活动所用数据来自公司的PTM 系统(生产技术信息管理系统)及车间 生产日报表,数据真实可靠。
8
四、行动计划
P DCA
为保证本次QC小组活动能够顺利实现,小组成员共同制定详细、周密 的活动计划表。
阶段
内容
7月份
制表:邓永东
日期:2012-8-2
10
六、目标设定
P DCA
小组成员决定将生产不良率目标设定为:由162DPPM降至 ≤100DPPM
11
七、原因分析
P DCA
由于影响不良率的问题点相互影响且较复杂,因此小组成员对连锡、偏 移两个不良现象绘制了关联图进行分析:
插座引脚钢 网开孔安全
间距小
操作员锡 膏量添加
9
五、现状调查
P DCA
小组成员对7月份GX13-3D眼镜组件板生产不良数据进行统计分析:
需重点改善
1、通过对7月份生产不良数据进行分析:偏移,连锡占总不良的77.2%,为主要症结,是 本次项目的改善重点; 2、经小组成员讨论我们有把握改善主要症结50%的不良
162DPPM*(1-77.2%*50%)=99.5DPPM; 3、查看2012年GX13-3D眼镜组件板生产不良率,1月份最低不良率118DPPM.
生产 现状
产生 危害
选定课题
1、 1-6月份因生产不良产生的返工及返修费用累计为:47733元 2、无法满足后工序正常的生产需求,急需改善
降低GX13-3D眼镜组件板SMT生产不良率
6
三、流程&名词解释
1、完整的眼镜板组件包含:40-3DGX13-GL*4XG (GL板) 40-3DGX13-CD*2XG(CD板)
TCL多媒体GOC LCD工厂是TCL集团旗下最大的生产基地,拥有全球顶尖的数字 电视研发团队及一流的工业设计能力。拥有先进的彩电生产设备,主要生产LCD、 LED彩色电视机,2012年生产整机1500多万台,位居全球第四位。
2
目录
1. 小组介绍 2. 选题理由 3. 流程&名词解释 4. 行动计划 5. 现状调查 6. 目标设定 7. 原因分析
8. 要因确认 9. 制定对策 10.对策实施 11.效果确认 12.巩固措施 13.总结及未来规划
3
一 、小组介绍
小组名称 课题名称 课题类型
Zero
降低GX13-3D眼镜组件板 SMT生产不良率
现场型
活动周期
2012.7- 2012.11
序号 1 2 3 4 5 6
成员
组长
成员
姓名
邓永东 郭延滨 蔡正伟 洪志 林亚贞 廖冬
日期:2012-7-18
一 、小组介绍
活动口号: 突破极限!
5
二、选题理由
公司 趋势
LED-3D电视已成为市场主流产品,12年公司目标销售产量1500 万台,按公司标配一台3D电视配两副眼镜 ,3D眼镜需求量大,好的 产品质量是占据市场的重要前提。
小组成员对2012年1月--6月的GX13-3D眼镜板生产不良数据进行统 计,结果显示GX13-3D眼镜组件板生产不良率最高达到226DPPM,平均 不良率为162DPPM。
小组成员 职务
工艺工程师 主任工程师 工艺工程师 工艺工程师
工艺助工 工艺助工
制表:邓永东 4
注册编号
GIC-2012H2-40
成立时间
2012-7-14
注册时间 TQC培训时间
2012-7-14 30-60时/人
组内分工
组织、策划、跟踪指导 工艺指导、资源协调 工艺指导、组织实施 实施及效果跟踪 不良确认及问题反馈 不良确认及问题反馈
8月份
9月份
10月份
1229 1230 1231 1232 1233 1235 1236 1237 1238 1239 1240 1241 1242
11月份 12月份 1月份
1243
现状调查
设定目标
P
原因分析
要因确认
制定对策
D 实施对策
C 效果确认
巩固措施
A
总结规划
制表:邓永东
计划时间
日期:2012-7-20