ABB伺服自动分枕平台成功案例
ABB伺服锂电池极片倒带机成功应用案例

ABB伺服锂电池极片倒带机成功应用案例项目背景1.尽管新能源动力电池行业经过一轮又一轮的“洗牌”,但优质动力电池供不应求的局面仍将长期持续。
根据中国化学与物理电源行业协会(CIAPS)统计,2018年中国锂电池的产量增长到1242亿瓦时,同比增长23.1%.2.锂电制作可以分为电极制作、电芯装配和电池组装这三大块,锂电池极片倒带机属于电芯装配卷绕工艺上的应用。
3.客户原来使用的是PTO控制方案,卷绕速度低,接线繁琐,脉冲信号易受干扰。
4.ABB伺服支持内部编程,通过MINT在伺服内部编程,帮客户节省了PLC,由原来的PTO控制升级伺服内部控制,提升了产品档次,精度和稳定性大大提高。
控制简介系统配置ABB整体解决方案亮点原有控制系统弊端(1)小型PLC PTO(脉冲)控制,接线繁琐,脉冲信号易受干扰;(2)梯形图编程,程序不易做成模块化、标准化,程序开发周期长;(3)小型PLC程序扫描周期慢,机器速度无法提升,最高速度只能达到40m/min;(4)小型PLC张力控制响应慢,机器只能缓慢加减速,急加速或急减速,张力不稳定;(5)PLC梯形图控制,控制系统容易被竞争对手破解和复制。
ABB伺服系统优势(1)ABB MINT内部编程控制伺服,无需脉冲信号,简化电控柜接线;(2)MINT高级语言编程,程序易于做成模块化、标准化,可移植性强,程序开发周期短;(3)ABB伺服内部编程直接控制,机器速度可以达到50m/min,效率提高25%;(4)程序集成在伺服内,张力控制响应快,支持快速加减速操作,张力依然保持稳定;(5)ABB独特的MINT程序控制,系统无法被竞争对手复制,保护OEM客户知识产权;(6)MINT内部编程,无需PLC,节省成本。
MINT编程介绍(1)Mint编程–高端语言–功能强大,且易于使用(2)EVENTs-位置锁存,输入状态改变和错误处理等时间处理的关键功能(3)多任务流处理能力(4)简单到复杂的运动控制,HMI管理,I/O逻辑和通讯(5)用于开发,处理所有通讯和提供Mint API接口的适用于windows的PC开发库,创建基于PC的HMI和用于数据交换的简单接口。
ABB伺服单晶硅切割机成功案例

ABB伺服单晶硅切割机成功案例单晶硅切割机简介工艺流程:由于单晶硅的硬度极高,需要切割金刚线的线速度高于35m/s, 在持续进给中根据切割接触面积修改进给速度,以保证切割面的光洁度、防止切割金刚线断裂。
特点:(1)新的工艺中使用‘锯’式金刚线,减少了切割金刚线的消耗、降低成本。
(2)高速切割线速度及进给工艺的改进,提高了切割效率。
(3)相比老式的收放卷式的设备,切割面光洁度更高。
ABB解决方案及说明系统框图产品型号HMI:贝加莱 Power Panel T50PLC:贝加莱,X20,CP0484伺服驱动: E180*2,三相380V AC输入MFE180-04AN-016A-4+L518MFE180-04AN-024A-4+L518伺服电机:HDS*2HDS100C-0413AD4KBS,抱闸HDS100C-0619ASKNNABB解决方案特点(1)可连接多种编码器协议的伺服电机,此次选用Hiperface协议的机械式编码器和SmartABS编码器。
(2)伺服驱动器的E1/E2接口支持Powerlink协议,可与B&R PLC实时通讯。
(3)可编程存储卡,用于参数保存与复制,更换驱动器时,只需把原来的存储卡插上即可运行。
SDC及PDO控制SDC和PDO控制(1)位置控制通过SDC实现。
(2)速度控制通过PDO映射。
(3)可根据需求添加修改PDO对象。
(4)代码化编程,功能集成度高,易于定制化开发。
功能块进给过程中实时修改切割速度(1)根据单晶硅切割的工艺要求,需要在进给切割的过程中实时修改切割速度(2)客户在HMI根据工艺要求和硅棒的直径设定区域位置和速度对应关系。
(3)工艺参数修改,实时生效。
与竞争对手切割效果对比。
ABB伺服火焰复合机成功案例
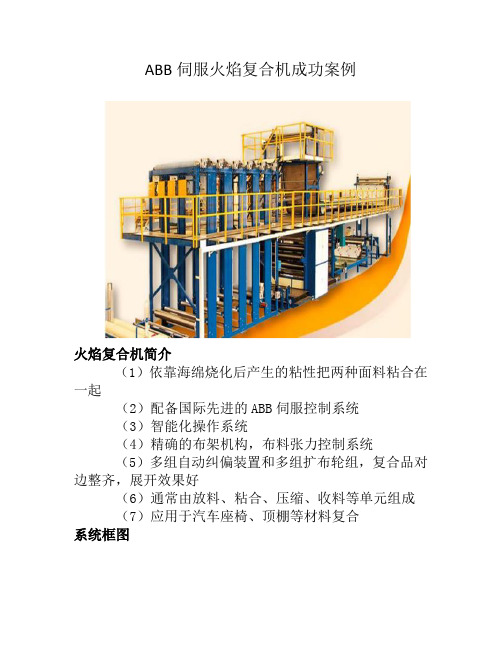
ABB伺服火焰复合机成功案例
火焰复合机简介
(1)依靠海绵烧化后产生的粘性把两种面料粘合在一起
(2)配备国际先进的ABB伺服控制系统
(3)智能化操作系统
(4)精确的布架机构,布料张力控制系统
(5)多组自动纠偏装置和多组扩布轮组,复合品对边整齐,展开效果好
(6)通常由放料、粘合、压缩、收料等单元组成
(7)应用于汽车座椅、顶棚等材料复合
系统框图
产品型号
触摸屏:CP610*1
PLC :PM585-ETH KIT&IO
伺服驱动 : E150*16
变频驱动 : ACS355*7
伺服电机:ESM13B*16
ABB解决方案特点
(1)ABB PLC为核心的集中控制
(2)速度模式下扭矩限幅
(3)实时工业以太网EtherCAT总线控制
(4)智能触屏控制
(5)开放式PLCopen运动控制库
ABB PLC为核心的集中控制
实时工业以太网EtherCAT总线控制及PLCopen运动控制库
如何实现速度模式下扭矩限幅
问题:
根据材料收卷工艺,在收卷过程中,如何实现收卷速度根据收卷厚度的增加而变慢,直至停止?
解决方案:
将当前收卷轴设置为速度模式,设置扭矩的上/下限值.在卷曲材料过程中,随着材料的厚度的增加,扭矩增加至设定最高限定值,轴速度将随着降低至零.上述步骤即为速度模式下扭矩控制。
【推荐下载】ABB-工业智能机器人在汽车组装接合技术上大有所为

张小只智能机械工业网ABB:工业机器人在汽车组装接合技术上大有所为 百余年来,整车组装的零部件接合工艺主要依赖焊接、螺栓螺母紧固等传统机械手段,而胶合、缝合等技术仅限于内饰装配等少数几个环节。
随着热塑性材料等各类新材料在现代汽车工业中的逐渐普及,零部件与金属底盘的接合工艺也在不断演进。
一开始,新型的、替代性的接合技术在应用上有比较大的局限性,短期内不见得能取代传统工艺比如点焊的地位,因为今后10 年,也就是到2020 年左右,汽车设计已经基本定型。
ABB 机器人部汽车机器人系统分部技术经理Srinivas Nidamarthi 博士预测道。
该分部专为航天和汽车企业提供包含铆接、焊接、压接、滚边、粘合等一系列作业环节在内的交钥匙组装线。
典型的ABB 白车身点焊系统 他指出,现代的白车身组装涉及15~20 种接合技术,其中最常见的3 种自动化工艺是点焊(占30%~60%)、弧焊和胶合。
其他次要技术包括铆接(以铝合金车身为主)、压接和滚边等。
Nidamarthi 认为,滚边虽是一种传统工艺,但在当今的汽车组装环节中依然不可或缺。
冷美学 车门等外露区域采用滚边加工,更具有美感,还能提高安全性。
Nidamarthi说,尾门、后备箱盖、轮罩这些地方也需要滚边。
滚边与压接类似,属于冷成型工艺。
滚边需要对金属边缘或法兰施以强力弯曲,整个流程包含三至四道工序。
压接技术则利用金属板材的塑性变形特性,通过冲压法完成部件接合。
这两种技术均属机械性紧锁,只要不涉及脆性材料,都可实现多层接合。
二者工艺相对简单,噪声小,能张小只机械知识库。
abb机器人伺服原理

abb机器人伺服原理ABB机器人伺服原理一、引言ABB机器人是瑞典ABB公司生产的一种具有自主运动能力的工业机器人。
它采用伺服控制系统,能够实现高精度、高速度的运动控制。
本文将详细介绍ABB机器人的伺服原理及其工作机制。
二、伺服系统概述伺服系统是指通过对输出位置、速度和力矩进行闭环控制,使得输出与输入信号达到所需的精确匹配。
伺服系统由伺服电机、传感器、控制器和执行器等组成。
伺服电机通过传感器获取机器人当前状态,并将其与控制器中设定的目标状态进行比较,控制器根据误差信号计算出控制命令,通过执行器控制机器人的运动。
三、伺服电机ABB机器人采用交流伺服电机作为执行器。
交流伺服电机由转子和定子组成。
定子上绕有三相绕组,通过交流电源供电,使得定子产生旋转磁场。
转子上装有永磁体,当转子受到磁场作用时,会产生转矩,从而驱动机器人的运动。
四、传感器ABB机器人的传感器主要包括编码器、力传感器和视觉传感器等。
编码器用于测量电机的转角和转速,通过与控制器中的设定值进行比较,计算出伺服电机的误差信号。
力传感器用于测量机器人的受力情况,根据测量结果,控制器可以调整机器人的力矩输出。
视觉传感器用于识别物体的位置和形状,从而实现机器人的精确定位和抓取。
五、控制器ABB机器人的控制器是伺服系统的核心部件。
控制器接收传感器的反馈信号,并根据预设的控制算法计算出控制命令。
控制器还负责监控机器人的状态,保证机器人的安全运行。
六、执行器ABB机器人的执行器主要包括减速器和传动装置。
减速器用于降低伺服电机的转速,并将转矩传递给机器人的关节。
传动装置则将电机的旋转运动转化为机器人的直线或旋转运动。
七、工作机制ABB机器人的工作机制是通过控制器对伺服电机施加电压信号,使其产生旋转磁场,驱动机器人的运动。
控制器根据传感器的反馈信号,不断调整电机的运动状态,使之与预设的目标状态保持一致。
通过不断的反馈调整,机器人可以实现高精度、高速度的运动控制。
ABB伺服在全伺服丝网印刷机成功案例

ABB伺服在全伺服丝网印刷机成功案例项目背景介绍(1)丝网印刷是制作大型广告必不可少的印刷手段。
(2)丝印的承印物材料广泛,如:有机玻璃、尼龙布、合成纸、安迪板、金属、塑料等(3)丝印不受规格的影响,印刷长度可达几米至几十米。
(4)丝网印刷成本低,经济合算,工艺灵活,适合于批量生产。
(5)丝网印刷最初采用手工操作,只有一个版架、一块丝网版和一块模版。
随着自动化技术的高速发展,丝网印刷正朝着机械化、自动化的方向发展。
(6)丝网印刷应用前景广阔,市场潜力巨大。
丝网印刷机简介(1)丝网印刷机是用丝网印版施印的机器,属于印刷机的一种。
丝网印刷机是利用丝网工艺生产印刷品的机器或设备的总称。
(2)丝网印刷机属于孔版印刷机,它的印版是一张由真丝等材料编织而成的纵横交错、经纬分明的丝网。
制作丝网的材料除真丝外,还可用尼龙丝、铜丝、钢丝或不锈钢丝等。
可分为平面丝网印刷机、曲面丝网印刷机、转式丝网印刷机等。
(3)丝网印刷机可以在各种纸张、玻璃、木板、金属、陶瓷、塑料或布匹上印刷文字和图像,可采用多种油墨,包括可导电的金属性油墨等。
丝网印刷机结构及原理(1)丝网印刷机共4个伺服轴,分别为:旋转轴、刮刀轴、上下轴和网轴(2)系统建立一个虚轴做为主轴,旋转轴跟随主轴同步运行,其他伺服轴跟随主轴实现电子凸轮运行(3)工作循环:给件→定位→落版→降刮墨板、升回墨板→刮墨行程→升刮墨板→降回墨板→抬版→回墨行程→解除定位→收件(4)刮墨板在完成单向印刷后与丝网印版一起脱离承印物,同时进行返程回墨,即完成一个印刷循环系统说明(1)欧姆龙PLC,EtherCAT实时工业以太网总线控制(2)核心控制使用4套ABB伺服控制系统,跟随主轴(虚轴)实现1轴位置同步,3轴电子凸轮运行系统配置控制器:欧姆龙 PLC通讯总线:EtherCAT伺服驱动:Microflex e190*4伺服电机:ESM motor*4方案特点(1)伺服书本式安装,节省柜内空间(2)伺服集成STO,提高系统安全性(3)E190驱动器易于安装、使用和维护(4)多轴电子凸轮联动运行实现精确位置控制,精度稳定可靠(5)EtherCAT总线控制,一网到底,布线简单简洁(6)实时工业以太网控制,系统响应更快,更稳定,同时抗干扰能力更强(7)方案开放性与灵活性强,可连接第三方控制器,方便拓展系统功能特点(1)高效、节能、安全环保、成品合格率高(2)各轴电子凸轮控制,系统运行更稳定,速度响应更快,控制精度更高(3)机、电、气一体化;具手动、半自动、全自动三种运行功能(4)高速、节省人工、产品自动计数等特点,在各种丝网印刷机中占据领先优势(5)整机集中控制,程序编排与生产速度可按生产工艺要求实时调整。
abb工件坐标系地建立及原理
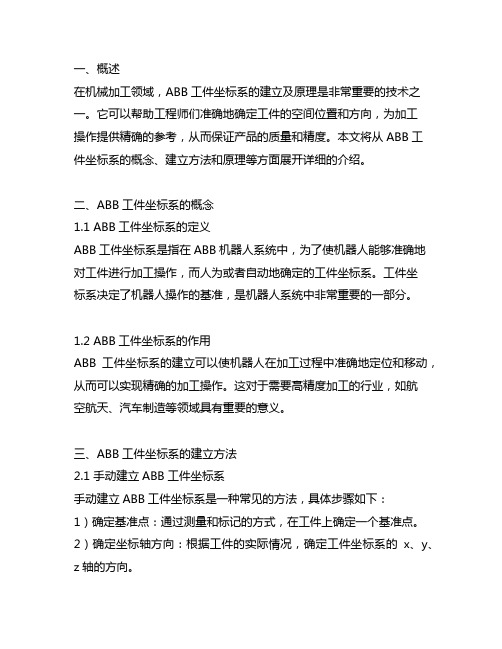
一、概述在机械加工领域,ABB工件坐标系的建立及原理是非常重要的技术之一。
它可以帮助工程师们准确地确定工件的空间位置和方向,为加工操作提供精确的参考,从而保证产品的质量和精度。
本文将从ABB工件坐标系的概念、建立方法和原理等方面展开详细的介绍。
二、ABB工件坐标系的概念1.1 ABB工件坐标系的定义ABB工件坐标系是指在ABB机器人系统中,为了使机器人能够准确地对工件进行加工操作,而人为或者自动地确定的工件坐标系。
工件坐标系决定了机器人操作的基准,是机器人系统中非常重要的一部分。
1.2 ABB工件坐标系的作用ABB工件坐标系的建立可以使机器人在加工过程中准确地定位和移动,从而可以实现精确的加工操作。
这对于需要高精度加工的行业,如航空航天、汽车制造等领域具有重要的意义。
三、ABB工件坐标系的建立方法2.1 手动建立ABB工件坐标系手动建立ABB工件坐标系是一种常见的方法,具体步骤如下:1)确定基准点:通过测量和标记的方式,在工件上确定一个基准点。
2)确定坐标轴方向:根据工件的实际情况,确定工件坐标系的x、y、z轴的方向。
3)编程输入:将基准点和坐标轴方向的信息输入到机器人控制系统中,建立工件坐标系。
2.2 自动建立ABB工件坐标系自动建立ABB工件坐标系是利用一些传感器或者测量设备,通过软件可以自动识别工件上的特征点,从而确定工件坐标系。
这种方法可以节约人力和时间,提高工作效率。
四、ABB工件坐标系的原理3.1 坐标系的确定ABB工件坐标系的确定依赖于工件的实际情况和加工要求,一般是根据工件的特征点或者几何形状来确定的。
确定坐标系的过程是基于一定的数学原理,包括向量运算、坐标变换等。
3.2 坐标系的转换在ABB机器人系统中,一般会有多个坐标系,如基坐标系、工具坐标系、工件坐标系等。
这些坐标系之间的转换是通过数学模型和运动学原理来实现的,机器人的控制系统能够根据不同的坐标系实现精确的运动和操作。
五、结论通过本文的介绍,读者对ABB工件坐标系的建立及原理应该有了更清晰的认识。
ABB伺服海绵切割机成功案例

ABB伺服海绵切割机成功案例项目背景(1)海绵切割机是一种高速高精度加工机械(2)控制要点:切刀轴双轴同步控制,保证最高的同步精度和速度稳定性(3)客户原来使用的是PTO控制方案,加工效率和可靠性都比较低。
切刀轴电机在高速运行时会出现抖动和噪音大等现象,影响加工质量。
(4)应客户要求,进行切刀轴同步控制方案设计,与上位机进行动作配合,提高了加工效率和可靠性。
切刀轴同步控制(1)两个伺服电机控制切割刀片(锯条),刀片刚性低,切割过程中容易产生扰动,控制难度较大(2)位置同步控制,位置误差和速度波动要求小(3)高速高精度运动,配合上位加工程序进行联动对于切刀轴同步控制ABB可以提供两种控制方案(1)伺服驱动器直接编程控制方案ABB MicroFlex e190可以通过编程实现伺服驱动器之间的直接编码器跟随(FOLLOW)功能,省去上位控制器(2)B&R PLC实时以太网控制方案ABB贝加莱PLC+ABB MicroFlex e190+ABB eSM伺服电机,Powerlink实时以太网控制,高性价比、高动态响应、高控制精度伺服驱动器直接编程控制方案(1)利用ABB伺服驱动器的可编程功能实现无PLC 的伺服轴同步控制(2)使用FOLLOW功能,可以分别控制主从轴且跟随比例可以微调。
(3)上位控制器直接发送PTO脉冲控制主轴的转速,同时可以通过IO点与伺服驱动器进行程序交互(4)此种控制方式满足客户现有控制要求,速度最高1500RPMB&R PLC实时以太网控制方案(1)为了进一步提高系统可靠性和加工效率,采用Powerlink实时以太网运动控制方案(2)最高至250us的实时以太网伺服控制精度,实现完美同步运动(3)ABB贝加莱PLC+ABB MicroFlex e190(e180)系列伺服驱动器+ABB ESM系列伺服电机完美搭配,实现最高性价比的运动控制组合。
(4)上位控制器可以通过多种方式与ABB贝加莱PLC 进行通讯或控制(5)可平稳运行达到最高运行速度2000RPMABB B&R PLC 编程软件平台控制画面。
ABB全伺服塑料热成型机成功案例

ABB全伺服塑料热成型机成功案例全伺服塑料热成型机成功案例近几年科学技术高速发展,各种技术产业也在我国飞速发展,越来越多的机械设备闯进我们的生活。
国内热成型机行业随着包装片材的发展不断推出先进配置和新机型。
外资和进口设备的引进,也提高了塑料热成型行业整体发展水平。
目前,塑料热成型设备主要生产热成型制品,且广泛应用于食品、蔬菜、水果、饮料、乳品、工业零件等领域的包装。
随着国内需求的日益增长,包装塑料热成型设备用途也越来越广泛,用量也逐年增加,前景看好。
热成型机简介热成型机主要用于生产、制作一次性餐饮具、冷饮杯、酸奶杯、果冻杯、冰淇淋杯、快餐盒、方便面碗等。
同时还可以加工医药、轻工、纺织、旅游、玩具等有关塑料包装制品。
原材料同样适应广泛。
如PS、PP、PVC、PET、ABS 及其他塑料片材均可加工制作。
产品之一的塑料杯是一种用来装液体或固体物品的塑料制品,具有杯厚耐热,倒入热水不软化,无需杯托,不渗透,颜色多样,重量轻便,不易摔坏等特点。
广泛适用于航空、办公、酒店、酒吧、KTV、家居等场地使用。
全伺服热成型机结构及原理(1)塑料热成型机由放料架,加热箱,成型台,收料架,空气压缩机等组成(2)设备共5个伺服轴,分别为:开合模、拉伸、送片、堆叠和输送(3)采用热成型工艺:将热塑性塑料片材加工成各种制品的较特殊的塑料加工方法(4)片材夹在框架上加热到软化状态,在外力作用下,使其紧贴模具的型面,以取得与型面相仿的形状。
冷却定型后,经修整即成制品ABB系统解决方案及说明(1)汇川PLC,EtherCAT实时工业以太网控制(2)核心控制使用4套ABB伺服控制系统,外加一套小功率雷赛伺服作为辅助输送轴系统配置控制器:汇川 Inovance AM600通讯总线:EtherCAT伺服驱动 : Motiflex e180 *4+ Leadshine servo *1伺服电机:ESM motor*4+ Leadshine motor *1系统框图ABB解决方案特点(1)伺服书本式安装,节省柜内空间(2)伺服集成STO,提高系统安全性(3)E180驱动器易于安装、使用和维护(4)多轴联动实现精确位置控制,精度稳定可靠(5)实时工业以太网EtherCAT总线控制,一网到底(6)方案开放性与灵活性强,可连接第三方控制器,方便拓展系统功能特点(1)高效、节能、安全环保、成品合格率高(2)整机集送片、加热、拉伸、成型、切边、堆叠、输送一次性完成(3)机、电、气一体化;具手动、半自动、全自动三种运行功能(4)高速、节省人工、产品自动计数堆叠等特点,在各种热成型机里占据领先优势(5)整机控制器集中控制,程序编排与生产速度可按实际生产工艺不同要求进行随机调整。
「ABB」推出有史以来最快的基于机器人的印刷机自动化解决方案

「ABB」推出有史以来最快的基于机器人的印刷机自动化解决方案导语:通过推出IRB 760PT,ABB扩大了其IRB 760工业机器人的范围。
IRB 760PT旨在用于汽车工业中的压力机自动化应用,是一种灵活的压力机维护解决方案,与其他基于机器人的压力机自动化解决方案相比,其循环时间缩短了25%。
ABB通过新的冲压加工模型扩展了IRB 760搬运机器人系列,为汽车冲压自动化提供快速灵活的性能。
通过推出IRB 760PT,ABB扩大了其IRB 760工业机器人的范围。
IRB 760PT旨在用于汽车工业中的压力机自动化应用,是一种灵活的压力机维护解决方案,与其他基于机器人的压力机自动化解决方案相比,其循环时间缩短了25%。
为了帮助消除机械手和压力机之间潜在干扰的风险,IRB 760PT具有经过改进的设计,可减少对机械手第四轴的干扰。
这使机器人可以自由移动,而不会与压夹之类的设备发生碰撞,而不会影响整个工作区域和机器人的移动自由度。
IRB 760PT能够承受最大450kg的负载,减少了重新使用专用压力机的时间,成本和中断。
具有自动更换工具的功能,IRB 760PT可以快速调整和重新编程,以处理新产品,而无需重新设计。
IRB 760PT是IRB 760FX和IRB 760 Twin Robot Xbar的基本组件。
IRB 760FX是IRB 760PT和线性第7轴组合的结果。
IRB 760FX具有大中型面板和特殊工艺(例如零件重新定向,倾斜和零件分离)的压力机自动化应用所需的高度灵活性。
还可以将两个IRB 760PT机器人组合起来在10个轴上串联工作,以创建IRB 760双机器人Xbar(TRX)。
这是市场上最快的基于机器人的解决方案,适用于装卸长机距的压力机,而无需修改压力机。
TRX的生产输出速率高达每分钟16个零件,是高速压力机自动化应用的理想选择。
IRB 760PT具有3.18米的触及范围,当与线性第七轴或Twin Xbar系统结合使用时,无需在连续的冲压操作之间重新定位零件。
ABB伺服智能游乐动感车成功案例

ABB伺服智能游乐动感车成功案例智能游乐动感车(1)近年来,随着人民日益增长的美好生活需要,游乐设备行业火热发展。
(2)行业竞争日益激烈,欲在竞争中保持优势,就需要厂家有创新能力和安全稳定的产品。
(3)该客户为主题公园和游乐设备行业佼佼者,自动化控制产品用量巨大。
(4)客户希望控制系统有很高的安全性和设备稳定性,同时操作和维护简单方便。
智能游乐动感车架构及原理(1)控制模型架构:三组电机驱动小车运行,每组两台电机(2)组与组之间无严格的刚性连接,组内两台电机通过顶部安装板刚性连接,并各带一个辊轮,小车运行轨道夹在两辊轮之间(3)组内部两台驱动器为转矩同步模式,组组之间为速度同步模式(4)部分电机故障情况下,可以脱离部分同步,应急驱动小车前进系统说明(1)倍福PLC,EtherCAT实时工业以太网控制(2)共6台ABB伺服驱动器,控制第三方带增量编码器的电机(3)3台驱动器速度同步运行,3台驱动器力矩模式运行系统配置PLC :倍福, CX1024通讯总线:EtherCAT伺服驱动: Motiflex e180 *6伺服电机:第三方电机*6 ,(TTL,1024线)系统框图方案特点(1)伺服书本式安装,节省柜内空间(2)伺服集成STO,提高系统安全性(3)E180驱动器易于安装,使用和维护(4)主从实时力矩同步,多轴精确速度同步(5)实时工业以太网EtherCAT总线控制,一网到底(6)方案开放性与灵活性强,可连接第三方控制器及伺服电机,方便拓展系统功能特点(1)组内部两台伺服为转矩同步控制,组与组之间速度同步控制(2)组内分主从轴,主轴为位置模式,从轴为转矩模式,将主轴实时转矩作为从轴目标转矩,从轴跟随主轴实时转矩运行,以确保轨道外侧轮与内测轮实时扭矩同步(3)通过将其中一组内的主轴同时作为其他组的主轴,而其他组的主轴作为组组之间的从轴进行速度跟随来实现组组之间速度同步。
ABB RotAx伺服旋转第七轴在铝板自动化拆垛中的应用

企业:ABB(中国)有限公司日期:2010-06-25领域:运动控制点击数:205当今社会,由于能源和资源的限制性,减少碳排放已经成为社会共识. 建立绿色节约型社会生活方式越来越成为企业的发展趋势. 在我国,随着汽车产业的迅速发展,其对环境的影响越来越引起人们的重视.据有关测算证实,平均大约70%的油耗是由于汽车本身的重量而产生的.因此,人们在尝试用铝板来代替钢板构成车身.铝板不但重量轻可节省油耗,同时还具备散热性强有助于延长车身零部件寿命等优点.从20世纪80年代末,世界上欧、美、日等多家汽车生产厂加强了对铝制汽车车身的研究,并取得了令人鼓舞的成就。
1995年德国奥迪公司首先开始批量生产铝制车身,把车身用铝的研究推向了高潮,铝合金在整车使用材料中的比例逐年提高.现在, 利用铝板来逐步代替构成汽车车身的钢板被越来越多的汽车厂商作为提高汽车绿色含量的现阶段重要途径.当然,这种铝板的机械特性需要满足与钢板相当的刚性和尺寸稳定性. 不可否认,构成汽车车身的覆盖件由于轮廓尺寸较大且具有空间的不同形状. 所以,在短时间内,只能是局部车身零件能完全被铝板代替.另一方面,由于目前的汽车冲压生产线大多采用自动化上下料,不可能专为铝板的生产投资一条生产线, 所以如何利用已有的冲压自动化生产线来进行铝板的自动化生产,而且能够保证与钢板生产相媲美的生产效率.是一个值得探讨和创新的课题. 同时,面临的难题还包括铝板的自动快速拆垛.众所周知,钢板的拆垛分张利用的是磁性相斥的工作原理.这一原理不能用于铝板的拆垛.目前,ABB利用其专利产品RotAx伺服旋转第七轴和专用于冲压车间的IRB6650型机器人成功集成了一种崭新的钢板与铝板共存的冲压生产线,经过一年多时间的实际生产验证,各项工艺满足了冲压件质量的要求,生产线效率也达到了生产要求.改进前的钢板拆垛系统原有的拆垛系统(图1)为1998年12月ABB安装调试完成的磁性皮带配备垂直提升气缸方式,集成利用了左右移动拆垛工作台以实现不间断生产换板料. 生产线平均节拍在10件/分钟以上.图1 钢板拆垛系统改进后的钢,铝板拆垛系统图2为经过改造后,增加了铝板拆垛系统.通过对比可以看出,整线在增加了铝板拆垛系统并没有增加占地面积.由于替代皮带机通过折叠式设计(当板料无需清洗时,只作为传送单元)安装在了原钢板拆垛系统下方, 整个拆垛系统看起来更紧凑合理.事实证明, 在生产线的钢板和铝板生产之间生产转换,只需要在总控台同过生产模式转换即可快速实现.图 2 钢,铝板拆垛系统关键技术1. RotAx 伺服旋转第七轴 .由于受空间所限,在拆垛速度必须满足整线节拍的要求下, 如果利用传统的六轴机器人和端拾器,由于板料的运行轨迹在进行180度旋转时需要避让钢板拆垛系统部分结构, 故不能充分使用机器人的柔性速度.同时,可以看出,如果使板料在拆垛完成后以直线运动姿态进入替代皮带机将会大大缩短运行时间. 而ABB机器人和其专利产品RotAx 伺服旋转第七轴完全适应于这一要求.图 3 ABB Rotax 旋转7轴图 4 实际应用区别于在机器人第六轴通过增加连杆机构实现附加第7轴, ABB RotAx 伺服旋转第七轴是采用伺服控制,真正意义上的第7轴.借助于其360度的旋转运动。
abb 伺服发展历程

abb 伺服发展历程ABB是全球领先的工业自动化和电力技术公司,具有百年的历史。
以下是ABB伺服发展的主要历程。
20世纪70年代,ABB开发出了第一台数字伺服控制器,实现了对电机的精确控制。
该控制器具有很高的可靠性和性能,广泛应用于各种工业领域。
这一里程碑标志着ABB在伺服控制技术领域取得了重要突破。
20世纪80年代,随着工业领域对自动化和智能化的需求增加,ABB在伺服技术方面继续创新。
他们推出了更加先进的伺服电机,具有更高的精度和可靠性。
同时,他们还开发了用于伺服控制的编程软件,使用户能够更便捷地配置和定制自己的控制系统。
20世纪90年代,随着电子技术的飞速发展,ABB开始研发基于数字信号处理器的高性能伺服系统。
这种系统具有更高的响应速度和更大的运动控制能力,使得工业生产能够更加高效和准确。
此外,ABB还开发了对多轴伺服控制的支持,实现了更复杂的运动控制。
进入21世纪,ABB继续加强对伺服技术的研发和创新。
他们推出了一系列新产品,如高性能伺服驱动器和机械手系统。
这些产品的问世,使得ABB在工业自动化领域占据了重要的地位,并赢得了全球客户的广泛信赖。
近年来,ABB致力于将伺服技术与其他先进的技术相结合,如人工智能和物联网。
他们开发了智能化的伺服系统,可以根据实际需求进行自适应控制,并实现远程监控和操作。
这种智能化的伺服系统不仅提高了生产效率,而且能够更好地满足客户个性化的需求。
总的来说,ABB伺服在过去的几十年里不断迭代升级,从最初的数字控制器到如今的智能化系统,它一直处于技术创新的前沿。
通过不断地研发和创新,ABB伺服为工业自动化带来了更高的效率和准确性,推动了工业生产的进步。
未来,ABB伺服将继续致力于技术的创新和应用,为客户带来更好的解决方案。
ABB现场经验汇总

ABB现场经验汇总预览说明:预览图片所展示的格式为文档的源格式展示,下载源文件没有水印,内容可编辑和复制CBF(或者Freenlance 2000)确实没有太多有关问题集的资料来分享,包括网上搜索都找不到全面而又实用的问题集,所以干脆自己做一个不断更新的问题集供大家交流,里面包括了一些我们自己做工程时遇到过的问题,或者需要大家注意的细节等等。
在看到一些比较低级的问题时,希望大家不要见笑。
冗余的处理器,其内部程序必须写在冗余任务下,如果不再冗余任务下,主从切换可能会造成短暂的无输出。
可能是冗余切换的问题。
ABB AC800F DCS切换的原因太多了:①当操作员站和工程师站的一个主机网口故障时,控制器切换。
(适用于一台工程师站或操作员站)②当主机网口与交换机连接的一根网线故障时,控制器切换。
(适用于一台工程师站或操作员站)③当一个交换机故障时,控制器切换。
④当交换机与以太网模块(EI803)连接的一根网线故障时,控制器切换。
⑤当一个电源模块故障时,控制器切换。
⑥当一个以太网模块(EI803)故障时,控制器切换。
⑦当一个同步模块(EI803)故障时,控制器切换。
⑧当一个Profibus DPV1 通信模块(FI830F)故障时,控制器切换。
⑨当一个Serial通信模块(FI820F)故障时,控制器切换。
⑩当一个控制器故障时,控制器切换。
当一个I/O站通讯接口模块(CI8400)故障时,控制器切换。
②ISP和OSP没设置,设置就好了!AC800F控制器在线下载注意事项在CBF软件中组态控制程序时,根据“检查编译”后的结果—控制器资源上的颜色“绿色”、“黄色”或“红色”,来判断下载后对AC800F控制器带来的影响和风险。
“绿色”表示修改后的程序结果,对控制器的任务、资源等项目对象没有影响。
“加载修改对象”或“加载选择对象”后,控制器的任务和资源正常运行。
“黄色”表示修改后的程序结果,对控制器的任务对象带来影响。
- 1、下载文档前请自行甄别文档内容的完整性,平台不提供额外的编辑、内容补充、找答案等附加服务。
- 2、"仅部分预览"的文档,不可在线预览部分如存在完整性等问题,可反馈申请退款(可完整预览的文档不适用该条件!)。
- 3、如文档侵犯您的权益,请联系客服反馈,我们会尽快为您处理(人工客服工作时间:9:00-18:30)。
ABB伺服自动分枕平台成功案例
自动分枕平台简介
(1)在铁路轨道施工中,目前普遍采用人工散铺法,施工效率较低,机械化程度低,精度不高,工人劳动强度大
(2)自动分枕平台实现轨枕的均匀排布,提升精度,配合轨排实现快速铺装,提高效率
(3)自动分枕平台包括两根主梁,两根主梁上分别设有匀枕小车,匀枕小车通过伺服电机控制实现等间距控制
方案介绍
控制器:第三方PLC
伺服驱动器: Microflex e190 * 5
伺服电机: ESM Motor * 5
通讯总线: Modbus TCP
第三方PLC通过Modbus TCP总线与伺服通讯PLC控制伺服的方式为 GDI,通过寄存器映射的方式实现对伺服的控制
系统框图
方案介绍
(1)伺服书本式安装,节省柜内空间
(2)伺服集成STO,提高系统安全性
(3)方案开放性与灵活性强,可连接第三方控制器及伺服电机,方便拓展
(4)伺服内置GDI接口程序,实现多种运动控制功能,节省PLC程序资源和开放时间
(5)基于Modbus TCP总线,可方便得与第三方PLC 通讯
ABB解决方案特点
GDI控制方式介绍
GDI控制方式,是ABB伺服的一个亮点,对脉冲+方向型的伺服控制方案有很强的替代性!
运动控制算法在伺服内,减小PLC的运算负荷,在多个伺服轴控制的场合,大大降低对PLC的性能要求,方案性价比很高。
可支持Modbus TCP, Profinet, Ethernet/IP, EtherCAT, PowerLink等主流工业以太网协议,配线简单,控制稳定。
GDI(General Drive Interface,通用驱动接口程序)通过寄存器映射的方式,无需PLC额外编程。
只需要传输控制字和状态字,即可实现监控。
对于客户来讲,只要了解了这些控制字和状态字的含义,即可快速上手并进行开发。
支持多轴的点到点运动。
GDI控制方式介绍。