叠层模具的应用技术
叠式热流道模塑原理及应用
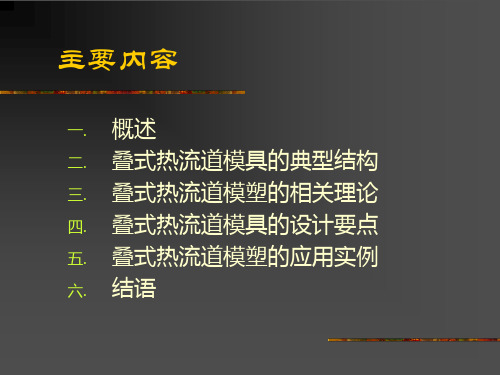
叠式热流道模顶出装置
顶出运动通常由移动中间板的同一元件启动。
3. 叠式热流道模具温控系统:
温控系统包括:加热和冷却这两个系统。
(1)加热系统:—— 作用是保持流道中塑料为熔融状态。
常用元件: 棒式加热器; 管式加热器; 板式加热器; 螺旋式加热器。
(2)中间部分:
➢ 由内部装有热流道和可向两 侧供料的进料口的两块模板 所组成。
➢ 中间部分需有支撑,在动模和定模一侧各设置有顶出机构。 在脱模过程中,用附加的移动部件使中间板移动,使其处 于模具的动模和定模的中间,便于制品从模具的2个分型面 中取出。中间板将沿注射机轴向运动,使热流道主浇道与 喷嘴脱开。
5. 热流道熔体的压力释放问题:
热流道歧管内的大流道和长注道杆均是被熔融的塑料充满着, 在注射时,通常可被压缩1~2%。当注道切断后,注射机喷嘴 拉离注道杆,热流道内的压力被释放,在流道内的塑料因此发 生膨胀,体积过量 的熔料将会溢出。
熔料溢出会有两种途径: (1)如果模具采用的是直通开式浇口,一部分塑料将会在模具
了解并认识叠式模塑技术原理、相关理论及 其设计要点,无疑会有助于推动叠式热流道技术 的应用和更快的发展。
(一)叠式热流道模塑的功效
1. 有效的生产方法:
现代电子、光学和航天等技术领域对注塑制品的要求 不仅是精度高、内在质量好,而且更加注重生产降低成本, 以获得更大的经济效益。
要到达这一目的,除了通过精心地设计模具结构外, 使其能最大限度地实现自动化的生产成型。对于成型扁平 塑件,实践证明,采用叠式热流道系统是一个非常有效手 段。
4. 实施容易:
叠式热流道注塑可以在普通的注塑机上有效 地生产制品,不需大量增加设备投资成本。
叠模资料
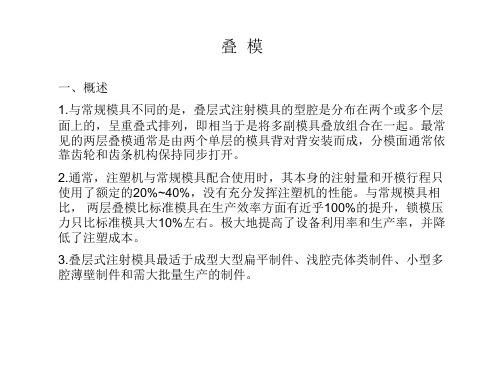
二、 两层叠层式热流道注射模具的设计要点
2.1 注塑机最大注射量 叠层式热流道注射模具在热流道板和中心主喷嘴中的物料不影响模具所需 注射量,可以忽略不计。注塑机所需的注射容积是标准模具近乎两倍。 2.2 注塑机注射压力 注射压力的校核主要是检验注射压力能否满足成型的需要。而叠层式热流 道模具由于采用了热流道技术,但由于流程增加、投影面积增大,所需注射压 力要比单层冷流道模具大。在校核注射压力时,应根据各种塑料的注塑工艺, 并结合计算机模拟流动分析来确定塑件的注射压力,再与注塑机额定注射压力 比较。 2.3 注塑机最大锁模力 叠层式注射模具的各层型腔以“背靠背”设置,理论上锁模力不增加。但 是,由于叠层式注射模具的中心主喷嘴及分流板增大了流动通道,使塑件加上 浇注系统在分型面上的投影面积有所增大;并且由于叠层而延伸了流道,压力损 失比常规单层模具大,注射压力相应增大,致使型腔压力增大,故锁模力有所 增加,校核时按相同单层模具所需锁模力增加10%~15%是比较安全的。
叠 模
一、概述 1.与常规模具不同的是,叠层式注射模具的型腔是分布在两个或多个层 面上的,呈重叠式排列,即相当于是将多副模具叠放组合在一起。最常 见的两层叠模通常是由两个单层的模具背对背安装而成,分模面通常依 靠齿轮和齿条机构保持同步打开。 2.通常,注塑机与常规模具配合使用时,其本身的注射量和开模行程只 使用了额定的20%~40%,没有充分发挥注塑机的性能。与常规模具相 比, 两层叠模比标准模具在生产效率方面有近乎100%的提升,锁模压 力只比标准模具大10%左右。极大地提高了设备利用率和生产率,并降 低了注塑成本。 3.叠层式注射模具最适于成型大型扁平制件、浅腔壳体类制件、小型多 腔薄壁制件和需大批量生产的制件。
三、 结论
采用热流道叠层式注射模具,可以充分发挥注塑机的能力,节省人力和设 备资源,极大地提高生产效率。
旋转叠层模具技术.

旋转叠层模具技术作者:米拉克龙Ferromatik公司塑件基材的传送典型的多组分技术通常用转台把预塑件基材沿机轴方向从一个工位送到下一个工位。
这样的工法需要较宽的拉杆间距,而且通常也需要注塑机具有较大的锁模力。
Foboha Formenbau GmbH公司和米拉克龙Ferromatik公司联合开发出了旋转叠层模具技术,这种技术通过叠层模中心模板围绕垂直旋转单元的转动实现对预塑件基材的传送。
旋转单元具有标准化的规格,从而能适用于各种各样的模具。
该旋转单元由两部分组成:下面的部分安装在注塑机基座的转轴上,由拉杆支撑;上面的部分直接安装在拉杆之间。
旋转叠层模具的中心模板安装在旋转单元的上下两部分之间,这样,较重的中心模板就固定在了机器的基座上,由机器的四根拉杆准确定位。
旋转驱动装置通常安装在旋转单元的下部并结成一体,驱动可以采用液压式,也可以采用全电动驱动。
对于每次180度的旋转动作,旋转时间在1.0到1.6秒之间,不同尺寸和重量的模具耗时各不相同。
180度旋转叠层模具技术的逻辑扩展就是四面立体模具(cube mold),这种模具在相同的四个面都装有型芯可用于注塑成型。
四面立体模具每旋转90度耗时在0.4秒到0.8秒之间。
客户获利无与伦比旋转叠层模具技术为相同的合模力提供了双倍的模腔,因而能够获得双倍的产量。
或者,模腔数量不变,但合模力仅需一半,从而削减了成本,节约了厂房空间。
这种技术让模具和注塑机受到的磨损和损耗也大幅度减少,因为不管从塑件基材到产品成型的过程中表面条件变化有多大,压力总是处于平均分布的状态。
另外,四面立体模具还能提供如下的可能性:即在注射过程进行时,其他不接受注射的以90度递进的成型面可以同时执行其他任务。
于是,以下任务可以同时进行:嵌件或装饰膜材的镶嵌、成品塑件的顶出、基材或产品成品的测试和继续冷却。
这些任务同时进行的结果就是产品成型周期比普通转台技术有了大幅度的缩短。
产品的成本缩减25%是常有之事。
叠模

.叠模技术(Stack Turning Technology )旋转型模具技术主要有两种:转盘型模具技术和内置旋转机构的模具技术。
它的特点是两种组分可以同时注射,大大缩短了制品的生产周期。
叠模又称叠式模,有模具不旋转和模具旋转两种方式。
(1)两层叠式模具方式此工艺由一台双物料注塑机,一套两层叠式模具及机械手组成。
当注塑机进行第一次注塑,经冷却后开模,机械手从第一层模芯上取出塑件,移放至第二层模芯内,合模后再进行第二次注射,在第二层模内得到最终产品,方式的第一次及第二次注射是同步进行的这种方法的优点是毋须使用转盘等装置便可进行共塑成型,采用这种方法,可用较少锁模力的机器生产较大的注塑件。
缺点是需把塑机的容模厚度增加以便能容纳较厚的叠层模,并需要配备较纵向行程较长的机械手,另外因工序需要较长的塑件取放时间,导致整个周期的延长。
此外利用双层叠模技术也可以同时生两种不同的产品,例如第一层模具生产一种产品,而第二层模具内则生产另一种产品,这些产品可以是材料相同或不同,颜色相同或不同等多种组合。
例如利用叠式模可以实现第一层注塑容器面盖;第二层模具注塑容器主体。
(2)两层叠式模+中间模板旋转式(旋转叠式模)此工艺是由一台双物料注塑机、一套两层叠式模具,以及可作180°往复旋转的中间模板组成。
注塑机完成第一注塑,经冷却后开模,中间模板会按设计要求作180°转动,把附着在模芯上的第一次注塑件转向第二层模腔,再合模进行注射。
这种方式的第一次注射和第二次注射也是同步进行的,从第二次注射开始,每次开模在第二层模内成型一次共塑制品。
旋转叠式模技术是当今共注塑技术的高难技术,技术难度大,它高度融合了机器、模具的制造技术及系统控制技术。
它既有叠式模共塑和旋转模板式共塑的优点:小的锁模力,即可用较小锁模力的的注塑机生产较大规格的塑件,另外,比机械手放件的方式更为准确,周期短、生产效率更高,十分适合大产量或生产周期长的共塑件的生产用途。
叠层模具技术总结报告

平均壁厚: 1.5mm
模具尺寸:X:720 Y:950 Z:954; A板厚:140mm, B板厚:130mm。
❖产品说明及要求
1.产品公差最高为正负0.1mm; 2.产品表面要求为EDM VDI32火花纹,后模面为SPI B1抛光; 3.所有分型夹线需控制在0.05mm内; 4.产品胶料为半透明PP; 5.各腔产品成型后重量偏差小于10%; 6.产品结构解析如页所示。
分型面圆锥管位块凸,管位块 的孔NC中光后用CNC磨床加工
上模肉
❖模具加工
三.侧向分型与抽芯机构:行位与下模肉的管位。
模肉侧边须 锣孔0.02MM,预防NC返工。
行位
模肉两端留出一段高度约为
行位一半的钢位,在行位运动 方向上做5度斜度,使得行位在 模肉中精确定位
下模肉
❖模具加工
侧向分型与抽芯机构:行位与下模肉的管位。
MM
❖模具制造、加工、装配
上模肉蓝色面是平面,请用D8R1刀具加工,效果佳
❖模具制造、加工、装配
上模肉进胶口直径为D0.6MM,高度必须做0.1MM的厚 度,采用线割加工,控制进胶点尺寸一致
❖模具制造、加工、装配
上模肉背面热嘴 孔直径为D8MM,用 EDM加工CH18#纹, 请配做,不能松!
❖模具制造、加工、装配
下模肉通框用慢走丝加工控制中心不偏心,后NC挂台
❖模具制造、加工、装配
下模 肉背 面此 挂台 请锣 深 0.02M M,装 镶件 时不 顶底
❖模具制造、加工、装配
直径为12.7的推方杆孔 线割时请用标准杆配做,
预防返工
❖模具制造、加工、装配
黄色处行位镶件槽先EDM 准数,再装上镶件EDM
❖模具制造、加工、装配
「叠层式注射模具设计与应用」
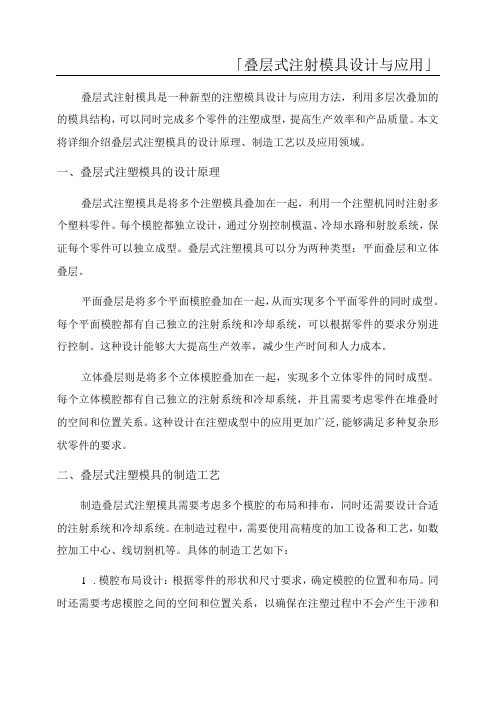
「叠层式注射模具设计与应用」叠层式注射模具是一种新型的注塑模具设计与应用方法,利用多层次叠加的的模具结构,可以同时完成多个零件的注塑成型,提高生产效率和产品质量。
本文将详细介绍叠层式注塑模具的设计原理、制造工艺以及应用领域。
一、叠层式注塑模具的设计原理叠层式注塑模具是将多个注塑模具叠加在一起,利用一个注塑机同时注射多个塑料零件。
每个模腔都独立设计,通过分别控制模温、冷却水路和射胶系统,保证每个零件可以独立成型。
叠层式注塑模具可以分为两种类型:平面叠层和立体叠层。
平面叠层是将多个平面模腔叠加在一起,从而实现多个平面零件的同时成型。
每个平面模腔都有自己独立的注射系统和冷却系统,可以根据零件的要求分别进行控制。
这种设计能够大大提高生产效率,减少生产时间和人力成本。
立体叠层则是将多个立体模腔叠加在一起,实现多个立体零件的同时成型。
每个立体模腔都有自己独立的注射系统和冷却系统,并且需要考虑零件在堆叠时的空间和位置关系。
这种设计在注塑成型中的应用更加广泛,能够满足多种复杂形状零件的要求。
二、叠层式注塑模具的制造工艺制造叠层式注塑模具需要考虑多个模腔的布局和排布,同时还需要设计合适的注射系统和冷却系统。
在制造过程中,需要使用高精度的加工设备和工艺,如数控加工中心、线切割机等。
具体的制造工艺如下:1.模腔布局设计:根据零件的形状和尺寸要求,确定模腔的位置和布局。
同时还需要考虑模腔之间的空间和位置关系,以确保在注塑过程中不会产生干涉和冲突。
2.模腔制造:根据设计要求,使用数控加工中心和线切割机等设备对模腔进行加工制造。
在加工过程中,需要保证模腔的尺寸和表面精度,以确保注塑成型的质量。
3.射胶系统设计:根据零件的形状和尺寸,设计合适的射胶系统。
射胶系统需要考虑注塑机的规格和特点,确保每个模腔都能够获得合适的注塑压力和速度。
4.冷却系统设计:根据零件的材料和尺寸,设计合适的冷却系统。
冷却系统需要保证每个模腔都能够获得均匀的冷却效果,提高注塑成型的效率和质量。
叠层制造及其它快速成型工艺与设备
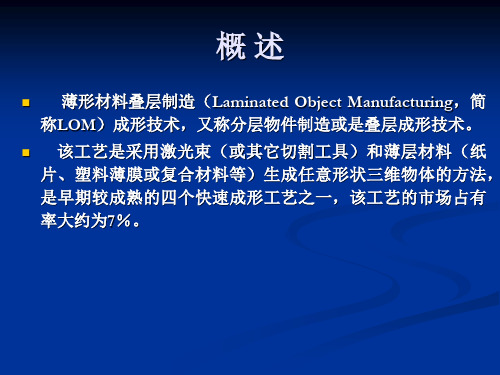
LOM快速原型工艺适合制作大中型原型件,翘曲变形较小,成型时间较短,激光器使用寿命长,制成件有良好的机械性能,适合于产品设计的概念建模和功能性测试零件,且由于制成的零件具有木质属性,特别适合于直接制作砂型铸造模。
面曝光快速成型
MPSL(Mask Projection Stereolithography)面曝光快速成型与扫描式固化快速成型最大的不同在于采用片层掩膜技术,一次曝光固化一个层面的实体。MPSL的关键技术之一是如何生成图形动态掩膜(Dynamic Mask)。 图形掩膜的生成方式有多种,早期是利用静电复印技术原理,在玻璃底版上生成图形掩膜。目前,比较典型的图形生成工艺是采用液晶显示技术(Liquid Crystal Display,LCD)和数字投影技术(Digital Light Processing,DLP)。下面对这两种技术分别进行简单地介绍,着重说明一下DLP的技术原理。
LOM快速成形技术的缺点
6. 表面比较粗糙,工件表面有明显的台阶纹,成型后要进行打磨;且纸制零件很容易吸潮,必须立即进行后处理、上漆。 7. 难以构建精细形状的零件,即仅限于结构简单的零件。 8. 由于难以(虽然并非不可能)去除里面的废料,该工艺不宜构建内部结构复杂的零件。 9. 当加工室的温度过高时常有火灾发生,因此,工作过程中需要专职人员职守。
MPSL技术基本原理
由分析可以看出,相比于LCD,DMD能更好地适应快速成型加工所需要的高精度、高可靠性以及对紫外光源能量较高的承受能力。因此将DLP技术应用到光固化快速成型技术的面曝光快速成型具有更好的发展前景。 它主要包括两大部分:固化成像器件即掩膜发生器和机械辅助装置即升降、涂覆系统等。掩膜发生器负责完成每层图像的生成,由紫外光照射投影到成像位置,即光敏树脂液面处,曝光固化一次树脂,再通过升降装置以及涂覆系统完成新一层树脂的准备工作,从而开始下一层的固化。
LCD高光面板叠层模创新技术

m od r d cin a v na e n rs a d dsu sstes c od d s n p it w i tei et n a d ls o u t d a tg sa dwo k, n i s h t km l ei on . m h j ci n p o c e a g n o
Gl s Fr nt Ca ne o s o bi t
W ANG u dn , AN eje L o igW W ni
( TCL u t e i c noo y Co, d En i e rn e t o o l c o y M l m da Te h l g i . , g n e i g D p . fM u d Fa t r , Lt
侧 边 修 饰 等 ( 图 I 。 总体 来 说 ,叠层 模 具 的运 用 见 )
已越来 越广 泛 。
叠
起 ,每 注塑 一次所 生产 的产 品数量是 普通 模
具 的两 倍 。除 了射 胶 、开合模 及人工 取件 时
间 比普通 模具稍 长外 ,其 余时 问均 相 同,但 是生产 出
的产 品却是普通模 具 的两 倍 ,其极 大的提 高了注塑机 的 日产 量 ,如果 减少人工取 件 的时间, 改为机 械手取
拓 宽 了叠 层模 具 的能 力 ,包 括 了 多材 料成 型 和 大 型 工 业零 部 件 ,如 电视机 外 壳 、汽 车总第 19 ) w ol c t 2 期 w wm u —r e 婪县工 d l n 程
8 9
t ie t o w c he pr duc f o di r o d.Thi ri l s rb s t tuc ur lc r c e itC fsa k m o d ,sa k t o r na y m l sa tc e de c i e he sr t a ha a t rsi S o t c ls tc
技术成型及应用7.4薄材叠层制造成型技术的应用与发展

知识拓展
美国公司LOM分层实体制造的应用
美国的Quality Metal Craft 公司利用采用LOM工艺制造的奥 迪汽车制动钳体和支架精密铸造模 型的快速原型,制件尺寸精度高, 稳定性好,表面光洁,如图5 -24 所示。
奥迪轿车刹车钳体
利用LOM技术加工原型件,通过 真空注塑机制造硅橡胶模具,可用于 试制少批量新产品。其过程如下: LOM原型经过表面处理,可作为硅橡 胶模具的母样,在真空注型机中制成 硅橡胶软模。用硅橡胶软模,在真空 注型机中可以浇注出高分子材料制件, 供新产品试制使用。图5 -25所示是 LOM成型的汽车车灯成形件。
电话机模型
马桶模型
(2)制作尺寸较 大的模具制件
利用材料的粘接性 能,可制作尺寸较 大的制件,也可制 作复杂薄壁件.
客车模型
(2)制作尺寸较 大的模具制件
利用材料的粘接性 能,可制作尺寸较 大的制件,也可制 作复杂薄壁件.
客车模型
(3)翻制 金属制件
利用材料的粘接性 能,可制作尺寸较 大的制件,也可制 作复杂薄壁件.
LOM成型叶轮原型
1.1 3D打印的产生与发展
& 课堂作业
思考 近年来,薄材叠层制造成型技术的很多应用都被其他的3D打印技术取而代
之,你认为制约薄材叠层制造成型技术的发展的主要因素是什么?未来薄材叠层制 造成型技术会彻底淘汰吗?
微信公众号:华唐集团
本节知识 点
1 薄材叠层制造成型技术的应用
2 薄材叠层制造成型技术的发展
课程导入
案例分析 某机床操作手柄的模型和LOM打印的鞋子模型,请思考
LOM技术主要应用在哪些领域?
LOM技术产品
课程学习
7. 4薄材叠层制造成型技术的应用与发展
高效注塑模具- 叠层模具的开发探讨

什么是叠层模具?
叠层模具是当今塑料模具发展的一项前沿技术; 型腔是分布在2个或多个层面上的,呈重叠式排列,相当于是将多 副模具叠放组合在一起
叠层模具产生的需求背景
通常注塑机在使用单层塑料注射模具的时候,其本身 的 注 射 量 和 开 模 行 程 只 使 用 了 额 定 的20%~40%,没有充分发挥注 射机的性能,而叠层式注塑模具能够在不增加锁模力的基础上, 在 1 台注射机 1 个操作人员的条件下能使产量根据层数成倍增加, 可以极大地提高生产效率和设备利用率,并能节约生产成本和人 力资源。叠层式注塑模具最适于成型大型扁平制件、浅腔壳体类 制件、小型多腔薄壁制件和需大批量生产的制件。
普通双层叠模的应用实例
产品模具基本信息
模号: 模腔数: B09999 8+8 客户: Zobele US 胶料: PP 产品类型: 香水盒 产品名称: Inner housing 胶料牌号: PP copolymer 缩水率: 1.017
制作部门: 精密一部 T1时间:
2009-08-18 产品尺寸: 38X64X90mm
第八步:安装同步开合模机构
第九步:接通水路、电子线路
注塑工艺
炮筒温度:230/245/240/235/220 摄氏度 射胶压力:85/95 kgf/cm2 保压:35% 注射时间:2.68s,保压时间:6S,冷却时间:9s 周期时间:29s 锁模力:350T 前模温度:35º C 后模温度: 35º C
叠层模具的优点是什么?
与常规模具相比,叠层式模具锁模力只提高了10%~15%,但产量可 以增加90%~95%; 模具制造要求基本上与常规模具相同,且将多副型腔组合在一副模 具中,所以模具制造周期也大大缩短; 使用高效叠层注塑模可以得到双倍或者四倍于普通单层模的产出而 无须投资购买额外的机器和设备。这就节约了安装机器、设备和扩 建厂房、新增劳动力的费用; 叠层模具可以装在单层模具要求相近的注塑机上,单位时间的产出 效率却是成倍的增长 节约原料,易于自动化,提高产品性能,缩短生产周期
叠模

.叠模技术(Stack Turning Technology )旋转型模具技术主要有两种:转盘型模具技术和内置旋转机构的模具技术。
它的特点是两种组分可以同时注射,大大缩短了制品的生产周期。
叠模又称叠式模,有模具不旋转和模具旋转两种方式。
(1)两层叠式模具方式此工艺由一台双物料注塑机,一套两层叠式模具及机械手组成。
当注塑机进行第一次注塑,经冷却后开模,机械手从第一层模芯上取出塑件,移放至第二层模芯内,合模后再进行第二次注射,在第二层模内得到最终产品,方式的第一次及第二次注射是同步进行的这种方法的优点是毋须使用转盘等装置便可进行共塑成型,采用这种方法,可用较少锁模力的机器生产较大的注塑件。
缺点是需把塑机的容模厚度增加以便能容纳较厚的叠层模,并需要配备较纵向行程较长的机械手,另外因工序需要较长的塑件取放时间,导致整个周期的延长。
此外利用双层叠模技术也可以同时生两种不同的产品,例如第一层模具生产一种产品,而第二层模具内则生产另一种产品,这些产品可以是材料相同或不同,颜色相同或不同等多种组合。
例如利用叠式模可以实现第一层注塑容器面盖;第二层模具注塑容器主体。
(2)两层叠式模+中间模板旋转式(旋转叠式模)此工艺是由一台双物料注塑机、一套两层叠式模具,以及可作180°往复旋转的中间模板组成。
注塑机完成第一注塑,经冷却后开模,中间模板会按设计要求作180°转动,把附着在模芯上的第一次注塑件转向第二层模腔,再合模进行注射。
这种方式的第一次注射和第二次注射也是同步进行的,从第二次注射开始,每次开模在第二层模内成型一次共塑制品。
旋转叠式模技术是当今共注塑技术的高难技术,技术难度大,它高度融合了机器、模具的制造技术及系统控制技术。
它既有叠式模共塑和旋转模板式共塑的优点:小的锁模力,即可用较小锁模力的的注塑机生产较大规格的塑件,另外,比机械手放件的方式更为准确,周期短、生产效率更高,十分适合大产量或生产周期长的共塑件的生产用途。
液晶显示器外壳的叠层式模具设计

液晶显示器外壳的叠层式模具设计近年来,信息技术不断升级,信息技术在各行业的应用范围不断扩大,并取得了良好的应用效果。
渗透信息技术于液晶显示器外壳设计,具体指的是叠层式模具设计,在这一过程中掌握设计工艺,提高工艺设计合理性,大大提高成型效率。
本文首先简要介绍液晶显示器外壳,然后重点分析其叠层式模具设计,希望能为相关设计工作者提供思路,循序渐进提高液晶显示器外壳的叠层式模具设计水平。
标签:液晶显示器;叠层式;模具设计;外壳前言:目前,人们对液晶显示器外观提出了较高的设计要求,针对外壳应用叠层式模具设计方式,这不仅能够提高设计完成外壳合理性,而且还能满足美观性欣赏需要。
本文探究该论题具有一定现实意义,论题分析必要性十分显著,具体探究如下。
1液晶显示器外壳基本介绍1.1结构特点液晶显示器电源由外置电源适配器提供,此时供电电压相对较低,因此电源运行安全故障发生几率较低。
其外壳组成部分包括外壳前面板以及外壳后盖两部分。
外壳实际设计时,应体现安全性、人性化特点,确保设计完成的外壳结构具有适用性,下文具体介绍液晶显示器外壳工艺参数[1]。
1.2工艺要求对于外壳前面板,其外形尺寸为355mm×305mm×13mm,质量大约为54g;对于外壳后盖,其尺寸大小为355mm×305mm×43mm,质量大约315g。
制品厚度在0.25cm左右。
液晶显示屏周围内部卡扣起到了重要的连接作用,内部加强筋数量相对较多。
从叠层式注射模具角度来分析,液晶显示器外壳结构在应用设计范围内,基于此,实际设计时应用两层单腔结构。
设计过程中,制品材料主要选用ABS,外壳表面应保证完整性、美观性,一旦发现外观存在气泡,或者清洁工作不到位,那么应及时调整,直到符合材料应用要求[2]。
2叠层式模具设计具体分析2.1模具结构液晶显示器外壳叠层式模具结构组成部分主要包括三部分,第一部分即定模部分,它细分为定模垫板及其中间部分;第二部分即动模部分,具体指的是分型面与动模垫板部分;第三部分即中间部分,具体指的是分型面部分。
叠层实体快速成型工艺
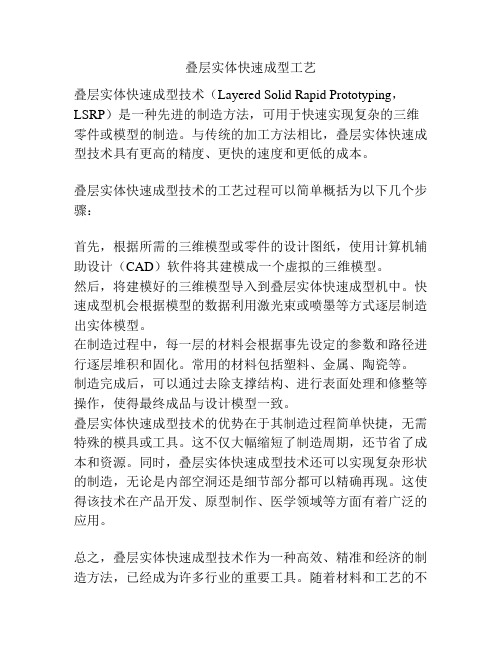
叠层实体快速成型工艺叠层实体快速成型技术(Layered Solid Rapid Prototyping,LSRP)是一种先进的制造方法,可用于快速实现复杂的三维零件或模型的制造。
与传统的加工方法相比,叠层实体快速成型技术具有更高的精度、更快的速度和更低的成本。
叠层实体快速成型技术的工艺过程可以简单概括为以下几个步骤:首先,根据所需的三维模型或零件的设计图纸,使用计算机辅助设计(CAD)软件将其建模成一个虚拟的三维模型。
然后,将建模好的三维模型导入到叠层实体快速成型机中。
快速成型机会根据模型的数据利用激光束或喷墨等方式逐层制造出实体模型。
在制造过程中,每一层的材料会根据事先设定的参数和路径进行逐层堆积和固化。
常用的材料包括塑料、金属、陶瓷等。
制造完成后,可以通过去除支撑结构、进行表面处理和修整等操作,使得最终成品与设计模型一致。
叠层实体快速成型技术的优势在于其制造过程简单快捷,无需特殊的模具或工具。
这不仅大幅缩短了制造周期,还节省了成本和资源。
同时,叠层实体快速成型技术还可以实现复杂形状的制造,无论是内部空洞还是细节部分都可以精确再现。
这使得该技术在产品开发、原型制作、医学领域等方面有着广泛的应用。
总之,叠层实体快速成型技术作为一种高效、精准和经济的制造方法,已经成为许多行业的重要工具。
随着材料和工艺的不断创新,相信叠层实体快速成型技术将会在未来有更加广泛的应用前景。
叠层实体快速成型(Layered Solid Rapid Prototyping,LSRP)技术是一种基于计算机辅助设计(CAD)的先进制造方法,通过逐层堆积和固化材料,快速制造出复杂的三维实体模型。
LSRP技术不仅可以用于原型制作,还可以直接应用于批量生产。
其工艺流程简单快捷,制造周期短,能够满足各类复杂形状和功能的需求,因此在众多领域得到了广泛的应用。
叠层实体快速成型技术最初由美国麻省理工学院在1980年代提出并发展起来。
随着计算机技术的不断进步和材料科学的发展,LSRP技术得以快速发展。
金属材料的叠加制造技术及在模具制造中的应用

金属材料的叠加制造技术及在模具制造中的应用摘要:叠加制造技术,是将金属材料以逐层叠加的形式来制造零件,从而达到零件图纸要求的先进制造技术。
近年来,金属材料的叠加制造工艺受到行业的关注和推崇。
一方面,叠加制造技术实现了传统“快速成形”只能制造非金属材料零件的局限,金属材料的零件也可借助叠加制造技术来制造;另一方面,叠加制造技术还能够实现生产效率与生产质量有效提升,进一步降低零件的制造成本。
关键词:金属材料;叠加制造技术;模具制造;应用1金属材料叠加制造技术的优势1.1复杂几何形状的加工金属材料具有良好的延展性,可以满足制造业各个领域的需要。
同时,借助叠加制造技术,可以制造出相应的图形和图案,可以满足多种工模具的制造要求,不会对金属造成其他影响。
例如,在传统工艺中很难生产出具有螺旋型腔的零件。
通过采用叠加制造技术,可以以叠加的形式生产出产品。
同时,可预留未加工区域,实现逐层生产制造。
众所周知,复杂几何形状的工件在各个领域有着广泛的应用。
叠加制造技术解决了制造中的困难,提高了产品的适用性和实用价值。
1.2各种材料的复合加工现代工业的发展对金属材料的复合加工能力提出了更高的要求。
一些工具、模具或机械零件要求表面耐磨性高,冲击载荷下韧性好。
这类工件通常采用低碳钢的化学热处理来解决。
如果采用叠加制造方法,可以制造出满足上述工况要求的功能梯度材料,并且可以比传统方法更好地控制功能梯度各层的厚度,大大提高了零件的性能。
在刀具制造领域,相应的要求更为严格,需要将具有各种特性的金属材料组合成一体,而叠加制造技术也可以实现这一目标。
1.3成本和效率的精确控制无论是在现代工业领域还是传统的机械加工领域,生产成本和效率都是最重要的因素。
成本决定了覆盖制造技术能否进行大规模的实践和应用,效率决定了覆盖制造技术能否适应当前市场化的发展模式,能够为制造企业提供巨大的经济价值和发展潜力。
准确控制成本和效率是覆盖制造技术可持续发展和应用的重要原因,也是推动技术不断升级和改进的主要因素。
多层注塑模具,模具生产效率可提升数倍!

多层注塑模具,模具生产效率可提升数倍!在塑料制品中,有相当大一部分是属于扁平状态而且是模具结构相对比较简单的制品,往往这些制品的需要量非常大,往往都是数以亿计的,譬如:塑料刀叉、梳子、衣架、挂钩、苍蝇拍、塑料夹子、元珠笔、牙刷等。
有的产品虽然在模具里占的范围很大,但是由于产品有很多空挡,实际投影面积和锁模力比较小,重量也比较小,但是模具的体积大,所用的注塑机也大,生产时电能的利用率很低。
我们平时用的塑料衣架便是最常见的例子。
下图是我们在超市里买到的最普通的衣塑料架。
我走访了一些小型的塑料衣架生产工厂,大多数是采用一模二穴的,用的注塑机是150吨左右的锁模力,24小时的产量在一万左右。
由于电耗比较大(每个衣架的电费成本为0.025元),人工的成本也比较大(每个衣架的工资成本为0.022元)。
基本上属于微利状态,假如出现一些其他的状况,工厂根本很难赚钱,这是一些中小型塑料加工厂不愿意大量生产塑料衣架的根本原因,利润太低了,假如客户延期付款,那就更困难了。
我们利用作用力和反作用力相等并且相互抵消的原理。
将原来普通的一模多穴的模具(譬如一模出8件)分多层(譬如4层)重叠布置,(每层2件)。
这样,从模具的总穴数来讲,是同样的,但是总投影面积就减少了四分之三。
因为四层的锁紧力相互抵消了三层,所以注塑机工作时所需要的锁紧力只相当于原来普通模具的四分之一。
同样每一模次生产8件制品。
所需要的注塑机的安装空间小了四分之三。
并且可使注塑机对电的利用率从原来的30%左右提高到85%左右。
这套模具打开后是这样的:还是用150吨的注塑机,24小时的产量增加到3.5万个,电费成本下降到0.01元,是原来的40%,也就是说节约了60%的电能,人工成本也下降了65%。
我们做塑料制品加工的都知道,在同样的设备和人员的条件下,加工产量每增加17%,加工费的利润就会增加100%。
现在我们的产量增加了350%,这笔帐大家算一算吧。
不难想象,原来的薄利加工,马上就变得利润可观。
第三章_叠层实体快速成型工艺

精品课件
图3-1 叠层实体制造技术的原理简图
第一节 叠层实体制造工艺的基本原理和特点
在叠层实体快速成型机上,截面轮廓被切割和叠合后所成的制品如下图所示。其中,所需的工件被废料小方格包围,剔除 这些小方格之后,便可得到三维工件。
图3-2 截面轮廓及网格废料 精品课件
第一节 叠层实体制造工艺的基本原理和特点
5 叠层实体制造工艺后置处理中的表面涂覆
6
新型叠层实体快速成型工艺方法
精品课件
第四节 提高叠层实体成型制作质量的措施
1. 叠层实体原型制作误差分析
CAD模型STL文件输出造成的误差
弦差
切片软件STL文件输入设置造成的误差
成型 过程 误差
不一致的约束
成型功率控制不当
切碎网格尺寸
工艺参数不稳定
设备 精度 误差
精品课件
第五节 叠层实体制造工ຫໍສະໝຸດ 后处理中的表面涂覆(5)对表面已经涂覆了坚硬的环氧树脂材料的原型再次用砂纸进行打磨,打磨之前和打磨过程中应注意测量原型的尺寸, 以确保原型尺寸在要求的公差范围之内; (6)对原型表面进行抛光,达到无划痕的表面质量之后进行透明涂层的喷涂,以增加表面的外观效果,如图所示。
薄层材料:纸、塑料薄膜、金属箔等 粘结剂:热熔胶 制备工艺:涂布工艺 纸的性能要求: 1)抗湿性
2)良好的浸润性 3)抗拉强度 4)收缩率小 5)剥离性能好 6)易打磨,表面光滑 7)稳定性
精品课件
第二节 叠层实体快速成型的材料和设备
热熔胶: 1)良好的热熔冷固性(约70~100℃开始熔化,室温下固化)。 2)在反复“熔融-固化”条件下,具有较好的物理化学稳定性。 3)熔融状态下与纸具有较好的涂挂性和涂匀性。 4)与纸具有足够粘结强度。 5)良好的废料分离性能。
叠层实体制造技术及其应用_李玲

激光切割速度 (89:,*.. ; < + 激光能量补偿系数 ("+*+ 工作台速度 (!*.. ; <+ 平台下移高度 ()*.. + 加热辊温度 (’9!)*=+ 切片软件的精度 (*+*>+
) 王 运 赣 !陈 国 清 !骆 际 焕 !林 国 材*快 速 成 型 技 术 及 其 系 统 的 研
究 * 锻压技术 *)++, "- #$#
" 王 广 春.赵 国 群*快 速 成 型 与 快 速 模 具 制 造 技 术 及 其 应 用 *机 械
工业出版社 *"&&! !)
- 王运赣 ! 林国才 ! 陈国清 ! 骆际焕 * 快速成型技术与分层叠纸式快
! 基底制作( 由于叠层在制作过程中
要由工作台 & 或称升降台 $ 带动频繁起降 " 为 实现原型与工作台之间的连接 " 需 要 制 作 基 底 " 通常作 )-, 层 %
图 ! 某移动通讯转换器的三维造型
" 原型制作 ( 快速原型设备根据计算机输 出的三维 #$% 模型转换的 &’( 数据以及设定的
速成型系统 * 锻压机械 *)++, %- &$-,
! 收稿日期 ""&&#/&)0&1#
!"
!"# 叠层实体制造技术的前处理过程 #" $ #$% 模型及 &’( 文件 #$% 模型在原型的整 个 制 作 过 程 中 相 当 于
- 1、下载文档前请自行甄别文档内容的完整性,平台不提供额外的编辑、内容补充、找答案等附加服务。
- 2、"仅部分预览"的文档,不可在线预览部分如存在完整性等问题,可反馈申请退款(可完整预览的文档不适用该条件!)。
- 3、如文档侵犯您的权益,请联系客服反馈,我们会尽快为您处理(人工客服工作时间:9:00-18:30)。
2:叠层模具技术特点
通常,注塑机与常规模具配合使用时,其本身的注射量和开模行程只使用了额定的20%~40%, 没有充分发挥注塑机的性能。与常规模具相比,叠层式注射模具的锁模力只提高了5%~10%,但产量 可以增加90%~95%,极大地提高了设备利用率和生产率,并降低了成本[2]。
叠层注射模具作为一种新型的模具技术得到了不断的发展,特别是与热流道技术的结合,使它成 为当今塑料模具发展的一项前沿技术。传统的常规模具设计理论已经不适用于论以指导叠层式注射模具设计。下面将对叠层式注射模具的设计 要点进行说明。
叠层模具结构上由叠层模具热流道系统、专用模架系统、承载导向系统、双向顶出系统、开合 模联动系统等多个系统组成。
叠层模具技术具备以下特点: 1.1.叠层模具生产效率超过普通的单层模具一倍或多倍,大幅度降低注塑生产成本。从结构特点 来看,叠层模具将多副型腔组合在一副模具中,充分利用普通注塑设备便可满足生产。模具的充模、 保压和冷却时间与单层模具相同,这就决定了叠层模具的生产效率将超过普通单层模具一倍甚至多倍, 大大提高制品单位时间的产量。(叠层模具设计就是因为它们的生产效率远远超过普通的单面模具而 闻名) 1.2.叠层模具可安装在与单层模具相同的注塑机上,无须投资购买额外的机器和设备,从而节约 了机器、设备、厂房和新增劳动力的成本。 1.3.叠层模具制造要求基本上与普通模具相同。据统计,1副双层叠层模具的制造周期比两副单 层模具的制造周期短5%~10%。 1.4.经生产验证,叠层式注射模具结构设计合理、可靠,制品尺寸一致性好,模具费用降低30%, 成型效率提高一倍或多倍。 1.5.叠层模具适合于大批量生产形状扁平的大型制品,小型多腔壁薄制品,批量越大,制品生产 成本越低。
2.1 注塑机最大注射量 叠层式注射模具可以采用冷流道,也可以采用热流道。当使用冷流道时,需要考虑浇注系统凝料所用的塑料量; 当采用热流道时,即实现无回头凝料生产,在热流道板和中心主喷嘴中的物料不影响模具所需注射量,可以忽略不 计[3]。所以,在校核注塑机最大注射量时要视具体情况而定。 2.2 注塑机注射压力 注射压力的校核主要是检验注射压力能否满足成型的需要。对于叠层式注射模具,大多成型薄壁、投影面积大 、流程长的塑件,在充填过程中需要更高的注射压力和注射速度。而叠层式热流道模具由于采用了热流道技术,相 对叠层式冷流道模具来说,能较好地传递注射压力,故所需的注射压力要比叠层式冷流道模具小;但由于流程增加、 投影面积增大,所需注射压力要比单层冷流道模具大。在校核注射压力时,应根据各种塑料的注塑工艺,并结合计 算机模拟流动分析来确定塑件的注射压力,再与注塑机额定注射压力比较。 2.3 注塑机最大锁模力 叠层式注射模具的各层型腔以“背靠背”设置,理论上能在锁模力不增加的基础上在同一台注塑机上实现任意 数量的叠层。但是,由于叠层式注射模具的中心主喷嘴及分流板增大了流动通道,使塑件加上浇注系统在分型面上 的投影面积有所增大;并且由于叠层而延伸了流道,压力损失比常规单层模具大,注射压力相应增大,致使型腔压力 增大,故锁模力有所增加,校核时按相同单层模具所需锁模力增加10%~15%是比较安全的。
Page: 3
2.4 注塑机开模行程 叠层式注射模具在两个层面或多层分型面开模并顶出塑件,当核对开模行程时,对于采用液压—机械式锁模机 构的注塑机,则不需考虑模具厚度;当叠层式注射模具上具有侧向分型的抽芯机构时,则需考虑抽芯距离的影响。如 果采用相同传动比的齿轮齿条或曲肘连杆开模装置等同步开模机构,则叠层式注射模具各层的行程不受制品高度的 限制,其开模行程是多层模具中最大开模行程那一层的n倍(n为叠层式注射模具的层数) 。 2.5 主喷嘴长度 中心主喷嘴不能太长或太短,这样模具闭合时,中心主喷嘴不会超出注塑机喷嘴在机座后退或前进的最大距离 。由于中心主喷嘴要与模具的中间部分在分型时一起移动,所以应确保开模后中心主喷嘴仍留在定模部分内,以防 止中心主喷嘴头部的溢料滴入定模型腔壁上。(我们现采用的是用针阀热系统来控制进胶口溢料现象) 2.6 浇注系统 叠层式注射模具既可以采用普通流道浇注系统(即冷流道浇注系统),也可以采用热流道浇注系统。热流道浇注 系统能够较好地传递注射压力,有利于提高塑件的成型质量,并易于实现自动化生产,但对塑料品种有一定要求, 而且热流道系统价格昂贵。当采用冷流道时,塑件的成型质量稍差,但模具加工容易,故成本较低。所以,用何种 浇注系统应视具体情况而定。 2.7 模温控制系统 模温是影响塑件成型质量的重要因素之一,叠层式注射模具设计时应保证各层型腔的温度条件控制一致。对于 叠层式热流道注射模具,为减少热流道系统由于热传导的热量损失,应减少模具与热流道板之间的接触面积,并设 置相应的隔热垫块及增加运水。 2.8 开模机构 为使塑件收缩一致,塑件在各型腔中的停留时间(冷却时间)应当相等,故叠层式注射模具应当确保各层型腔的 分型面同时开启。齿轮齿条传动机构和机械式(肘节式)连杆机构常作为叠层式注射模具的开模机构,前者的技术 性能较好,也较经济,但后者的灵活性更大。采用液压辅助开模更容易控制开模时间,但结构较大。 2.9 脱模机构 根据冷却时间等同要求,叠层式注射模具应对各层型腔中的塑件同时顶出,采用机械顶出,油缸顶出,弹簧或 者高压空气的脱模机构能够达到这一要求。
Page: 4
4:我司相关叠层模具及叠层热流道案例
4.1.手机及机壳类的叠层模具的分析及示意图片。 4.2.薄壁包装类的叠层模具的分析及示意图片。 4.3.医疗产品及多腔产品类的叠层模具的分析及示意图片。 4.4.三层叠层模具的分析及示意图片。 4.5.叠层模具的热流道形式。 4.6.叠层模具的开模机构。 4.7.叠层模具的支撑机构。 4.8.四层叠层模具,四面叠层或多层模具,双色叠层旋转模具的发展。
叠层模具的应用技术
Page: 1
1:叠层模具应用特点
叠层模具技术是区别于普通注塑模具技术的一种模具前沿技术,即在一副模具中将多个型腔在 合模方向重叠布置。这种模具通常有多个分型面,每个分型面上可以布置一个或多个型腔。简单地说, 叠层模具就相当于将多副单层模具叠放在一起,安装在一台注塑机上进行注塑生产。