盾构机刀盘设计要点探究
盾构机械刀盘设计中的材料与优化分析
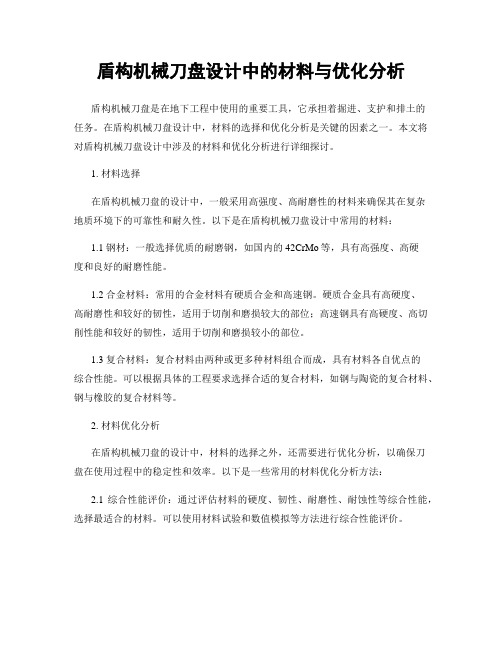
盾构机械刀盘设计中的材料与优化分析盾构机械刀盘是在地下工程中使用的重要工具,它承担着掘进、支护和排土的任务。
在盾构机械刀盘设计中,材料的选择和优化分析是关键的因素之一。
本文将对盾构机械刀盘设计中涉及的材料和优化分析进行详细探讨。
1. 材料选择在盾构机械刀盘的设计中,一般采用高强度、高耐磨性的材料来确保其在复杂地质环境下的可靠性和耐久性。
以下是在盾构机械刀盘设计中常用的材料:1.1 钢材:一般选择优质的耐磨钢,如国内的42CrMo等,具有高强度、高硬度和良好的耐磨性能。
1.2 合金材料:常用的合金材料有硬质合金和高速钢。
硬质合金具有高硬度、高耐磨性和较好的韧性,适用于切削和磨损较大的部位;高速钢具有高硬度、高切削性能和较好的韧性,适用于切削和磨损较小的部位。
1.3 复合材料:复合材料由两种或更多种材料组合而成,具有材料各自优点的综合性能。
可以根据具体的工程要求选择合适的复合材料,如钢与陶瓷的复合材料、钢与橡胶的复合材料等。
2. 材料优化分析在盾构机械刀盘的设计中,材料的选择之外,还需要进行优化分析,以确保刀盘在使用过程中的稳定性和效率。
以下是一些常用的材料优化分析方法:2.1 综合性能评价:通过评估材料的硬度、韧性、耐磨性、耐蚀性等综合性能,选择最适合的材料。
可以使用材料试验和数值模拟等方法进行综合性能评价。
2.2 材料强度分析:通过材料的强度参数(如抗拉强度、屈服强度等)和应力分析,评估材料在工作环境下的稳定性。
可以使用强度理论和有限元分析等方法进行材料强度分析。
2.3 优化设计:在材料选择和刀盘结构设计时,综合考虑材料的机械性能、梁端受力和变形等因素,以最小化刀盘的质量和尺寸,提高刀盘的效率和使用寿命。
同时,盾构机械刀盘的设计还要考虑与其他部件的匹配、制造和维修的方便性等因素。
只有在材料选择和优化分析的基础上,才能设计出安全可靠、高效耐用的盾构机械刀盘。
总结起来,盾构机械刀盘设计中的材料选择和优化分析是确保盾构机械刀盘能够在复杂地质环境下安全、高效工作的关键因素。
盾构机刀盘动力系统设计与分析
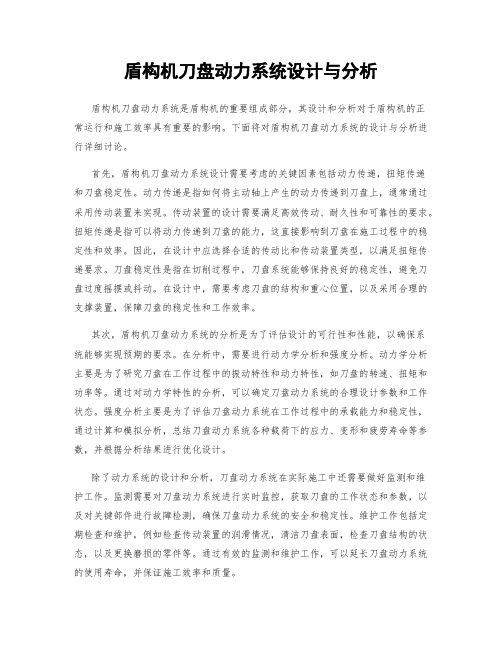
盾构机刀盘动力系统设计与分析盾构机刀盘动力系统是盾构机的重要组成部分,其设计和分析对于盾构机的正常运行和施工效率具有重要的影响。
下面将对盾构机刀盘动力系统的设计与分析进行详细讨论。
首先,盾构机刀盘动力系统设计需要考虑的关键因素包括动力传递,扭矩传递和刀盘稳定性。
动力传递是指如何将主动轴上产生的动力传递到刀盘上,通常通过采用传动装置来实现。
传动装置的设计需要满足高效传动、耐久性和可靠性的要求。
扭矩传递是指可以将动力传递到刀盘的能力,这直接影响到刀盘在施工过程中的稳定性和效率。
因此,在设计中应选择合适的传动比和传动装置类型,以满足扭矩传递要求。
刀盘稳定性是指在切削过程中,刀盘系统能够保持良好的稳定性,避免刀盘过度摇摆或抖动。
在设计中,需要考虑刀盘的结构和重心位置,以及采用合理的支撑装置,保障刀盘的稳定性和工作效率。
其次,盾构机刀盘动力系统的分析是为了评估设计的可行性和性能,以确保系统能够实现预期的要求。
在分析中,需要进行动力学分析和强度分析。
动力学分析主要是为了研究刀盘在工作过程中的振动特性和动力特性,如刀盘的转速、扭矩和功率等。
通过对动力学特性的分析,可以确定刀盘动力系统的合理设计参数和工作状态。
强度分析主要是为了评估刀盘动力系统在工作过程中的承载能力和稳定性,通过计算和模拟分析,总结刀盘动力系统各种载荷下的应力、变形和疲劳寿命等参数,并根据分析结果进行优化设计。
除了动力系统的设计和分析,刀盘动力系统在实际施工中还需要做好监测和维护工作。
监测需要对刀盘动力系统进行实时监控,获取刀盘的工作状态和参数,以及对关键部件进行故障检测,确保刀盘动力系统的安全和稳定性。
维护工作包括定期检查和维护,例如检查传动装置的润滑情况,清洁刀盘表面,检查刀盘结构的状态,以及更换磨损的零件等。
通过有效的监测和维护工作,可以延长刀盘动力系统的使用寿命,并保证施工效率和质量。
综上所述,盾构机刀盘动力系统设计与分析是盾构机设计过程中的重要环节。
复杂地层盾构机刀盘刀具优化设计研究

复杂地层盾构机刀盘刀具优化设计研究摘要:在盾构法隧道穿越江河过程中,刀盘刀具是保证盾构施工的重要部件,在盾构施工时,选用何种刀具配备通常取决于盾构机掘进的地层条件。
本论文以西气东输二线北江盾构穿越工程为例,介绍了盾构机刀具的种类和切削原理,并针对广东地区特殊地质情况,优化设计泥岩等复杂地层盾构机刀盘刀具的配置。
关键词:北江盾构;刀具种类;切削原理;优化设计Abstract: In the process of shield tunnel across the river, cutter head is the guarantee of the importantcomponents of shield construction . Choose tools type In shield tunnel usually depends on shieldconstruction machine tunneling formation conditions. This paper introduces the type of shield constructionmachine tools and cutting principle on the basis of the west-east second line of shield beijiang river projectand according to situation of guangdong area complex stratum, it optimize Cutter head configuration whenshield tunnelling in shale and sandy1 盾构机刀具种类刀具是是盾构机重要的部件,在盾构施工时选取何种刀具通常取决于盾构机掘进的地层条件。
为了适应从软土到硬岩不同地层的切削,开发了不同种类的切削刀具。
盾构机刀盘设计及优化方法研究

盾构机刀盘设计及优化方法研究盾构机是一种用于地下隧道工程的重要设备,而刀盘是盾构机的核心组成部分之一。
刀盘的设计及优化方法研究对于提高盾构机的施工效率和工程质量具有重要意义。
本文将围绕这一主题展开研究,探讨盾构机刀盘的设计原则、刀盘形式选择、刀具材料、刀具布置以及刀盘优化方法等内容。
首先,盾构机刀盘的设计需要考虑以下几个原则:结构简单合理、适应性强、安全可靠、易于维护和更换、满足工程要求等。
刀盘应具有良好的刀具布置和刀具形式选择,以实现盾构机在施工过程中的高效率、低能耗和高质量。
刀盘形式的选择是刀盘设计的重要环节。
根据不同的工程需求和地质条件,可选择单刀盘、双刀盘、双层刀盘等不同形式。
单刀盘适用于较软的地层,双刀盘适用于较硬的地层,而双层刀盘则适用于有大块破碎岩体的地层。
刀具材料的选择对刀盘设计至关重要。
刀具材料应具备高硬度、高韧性、高耐磨性和耐腐蚀性等特性。
常见的刀具材料有高硬度合金、碳化钨和人造单晶等。
此外,刀具材料的热处理也是刀盘设计中的一个重要环节,可以通过调整热处理工艺来提高刀具的硬度和耐磨性。
刀具布置是盾构机刀盘设计中的核心问题之一。
刀具的布置应满足刀具数量适当、刀具间隔均匀以及刀具的安装和更换方便等要求。
合理的刀具布置可以有效地提高切削效率和切削质量,减少能耗和刀具磨损。
刀盘优化方法是盾构机刀盘设计的关键内容。
盾构机刀盘的优化可以通过对刀具数量、刀具材料、刀具布局以及刀盘内部流场等进行综合分析和优化设计。
例如,可以通过流场分析和模拟技术来优化刀具布局,改善切削效果和流动性。
另外,还可以利用多目标优化方法对刀具数量、刀具材料和刀具布局等进行优化,以求在满足工程要求的前提下最大程度地提高施工效率和工程质量。
总之,盾构机刀盘设计及优化方法的研究对于提高盾构机的施工效率和工程质量非常重要。
刀盘设计应考虑刀盘的结构、刀具材料、刀具布置以及刀盘优化方法等因素,以满足工程要求,并在减少能耗和刀具磨损的前提下提高切削效率和切削质量。
盾构刀盘结构设计与分析
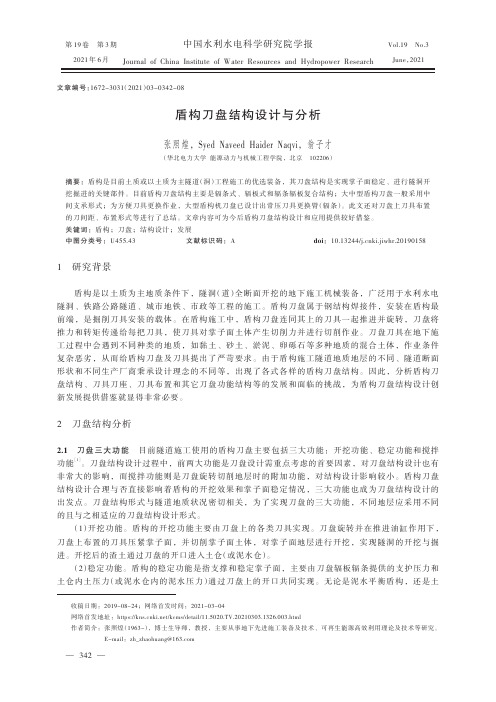
关键词:盾构;刀盘;结构设计;发展
中图分类号:U455.43
文献标识码:A
doi:10.13244/ki.jiwhr.20190158
1 研究背景
盾 构 是 以 土 质 为 主 地 质 条 件 下 , 隧 洞(道)全 断 面 开 挖 的 地 下 施 工 机 械 装 备 , 广 泛 用 于 水 利 水 电 隧洞、铁路公路隧道、城市地铁、市政等工程的施工。盾构刀盘属于钢结构焊接件,安装在盾构最 前端,是掘削刀具安装的载体。在盾构施工中,盾构刀盘连同其上的刀具一起推进并旋转,刀盘将 推力和转矩传递给每把刀具,使刀具对掌子面土体产生切削力并进行切削作业。刀盘刀具在地下施 工过程中会遇到不同种类的地质,如黏土、砂土、淤泥、卵砾石等多种地质的混合土体,作业条件 复杂恶劣,从而给盾构刀盘及刀具提出了严苛要求。由于盾构施工隧道地质地层的不同、隧道断面 形状和不同生产厂商秉承设计理念的不同等,出现了各式各样的盾构刀盘结构。因此,分析盾构刀 盘结构、刀具刀座、刀具布置和其它刀盘功能结构等的发展和面临的挑战,为盾构刀盘结构设计创 新发展提供借鉴就显得非常必要。
2 刀盘结构分析
2.1 刀盘三大功能 目前隧道施工使用的盾构刀盘主要包括三大功能:开挖功能、稳定功能和搅拌 功 能[1]。 刀 盘 结 构 设 计 过 程 中 , 前 两 大 功 能 是 刀 盘 设 计 需 重 点 考 虑 的 首 要 因 素 , 对 刀 盘 结 构 设 计 也 有 非常大的影响,而搅拌功能则是刀盘旋转切削地层时的附加功能,对结构设计影响较小。盾构刀盘 结构设计合理与否直接影响着盾构的开挖效果和掌子面稳定情况,三大功能也成为刀盘结构设计的 出发点。刀盘结构形式与隧道地质状况密切相关,为了实现刀盘的三大功能,不同地层应采用不同 的且与之相适应的刀盘结构设计形式。
盾构刀具大解析

设置部位 面板正面 面板正面 面板正面 面板正面 面板正面外沿 面板外沿 面板背面 加泥嘴部位 面板正面外围
北京铁城建设监理有限责任公司
8
滚刀的示意图和实物照片
a) 盘形 滚刀 示意 图
b) 盘形滚刀圈
c) 盘形滚刀
北京铁城建设监理有限责任公司
9
切削刀的实物照片
a) 周边刮刀
b) 周边刮刀(背面)
盘形滚刀圈
盘形滚刀
北京铁城建设监理有限责任公司
26
安装在刀盘上的盘形滚刀在千斤顶的作用下紧压在岩面上,随着刀盘的旋转,盘形滚 刀一方面绕刀盘中心轴公转,同时绕自身轴线自转。滚刀在刀盘的推力、扭矩作用下, 在掌子面上切出一系列的同心圆沟槽。当推力超过岩石的强度时,盘形滚刀刀尖下的 岩石直接破碎,刀尖贯入岩石,形成压碎区和放射状裂纹;进一步加压,当滚刀间距S 满足一定条件时,相邻滚刀间岩石内裂纹延伸并相互贯通,形成岩石碎片而崩落,盘 形滚刀完成一次破岩过程。
C
5~6 5~6 5~6 5~6 5~6
用途
盾构刀具 盾构刀具 砂层刀具13
海瑞克齿刀由刀体、端部硬质合金刀片和背部球齿构成。
北京铁城建设监理有限责任公司
14
海瑞克刮刀是用硬质合金钢做为刀头,高耐磨合金钢作为刀 体。
北京铁城建设监理有限责任公司
15
• 其它进口盾构刀具在材料方面由两至三种构成,即 基体材料、硬质合金材料、刀具刃口堆焊材料等复 合制成。下表为一种用于盾构机刀具刃口的铁基堆 焊材料的化学成分和性能。
北京铁城建设监理有限责任公司
28
2) 起裂阶段:沿粉碎区周边应力大于岩体的抗拉强度或抗剪强度时,便产生张拉裂缝。 该裂缝是滚刀能否破岩的先诀条件。在应力核心区下层是应力过渡区,该区为应力衰减 区,对岩体裂缝的产生不起控制性作用。在刀刃正下方分布有主裂缝,由于其方向与破 岩方向一致,因此也不能显著地提高破岩效率,但能加大下个循环中压入阶段应力范围。
盾构机刀盘刀片材料与结构性能研究

盾构机刀盘刀片材料与结构性能研究一、引言盾构机作为一种用于地下隧道建设的重要工程设备,其刀盘刀片是其关键部件之一。
刀盘刀片的材料与结构性能对盾构机的工作效率、稳定性以及安全性都具有重要影响。
因此,对盾构机刀盘刀片的材料与结构性能进行深入研究是十分有必要的。
二、刀盘刀片的材料研究1. 材料选择刀盘刀片的材料需要具备一定的硬度、强度和耐磨性。
目前常见的材料包括合金钢、高速钢、硬质合金等。
在选择材料时,需要综合考虑刀片的工作条件、切削力以及切削速度等因素,以确保刀片在长时间工作中具有较好的性能表现。
2. 材料处理为提高刀盘刀片的材料性能,可以采用多种材料处理技术,如热处理、表面处理等。
热处理可以通过调控材料的组织结构和硬度,提高刀片的耐磨性和强度;表面处理可以形成一层保护性涂层,增加刀片的磨损抗性。
三、刀盘刀片的结构性能研究1. 刀片形状刀片的形状对其切削效果和寿命有直接影响。
目前常见的刀片形状包括圆形、方形、三角形等。
研究各种形状刀片在不同地质条件下的切削效果,可以优化刀片结构设计,提高刀片的使用寿命和切削效率。
2. 刀片连接方式刀片的连接方式直接关系到刀盘的稳定性和刀片更换的便捷性。
目前常见的连接方式有机械连接和焊接连接。
研究不同连接方式在工作中的稳定性和可靠性,可以为刀盘刀片的结构设计提供技术支持。
3. 刀片与岩石的相互作用刀片在工作中与岩石之间存在摩擦、切削力等相互作用。
研究刀片与岩石的相互作用规律,可以为刀片的材料和结构性能提供优化方案,提高工作效率和切削质量。
四、实验与模拟方法1. 实验方法通过设计合理的实验方案,使用专门的实验设备,对刀盘刀片的材料和结构性能进行测试。
例如,可以利用材料测试设备测试刀片的硬度、强度等性能指标;利用磨损试验机对刀片的耐磨性进行评估等。
2. 模拟方法通过建立刀片与岩石相互作用的力学模型,使用计算机模拟软件进行仿真计算,预测刀片的工作性能。
例如,可以采用有限元分析方法对刀片在不同切削条件下的应力、变形等进行模拟计算,以评估刀片的结构稳定性。
盾构机械刀盘及刀具设计与优化

盾构机械刀盘及刀具设计与优化随着城市地下空间的不断开发和利用,盾构机械在地铁、隧道等工程领域中得到了广泛应用。
盾构机械的刀盘及刀具是决定其施工质量和效率的重要因素之一。
本文将重点讨论盾构机械刀盘及刀具的设计与优化。
1. 刀盘设计1.1 刀盘结构设计刀盘是盾构机械的核心部件之一,其结构设计的合理性对盾构机械的工作效果有着重要的影响。
刀盘的结构设计应该考虑以下几个方面:1.1.1 刀盘刚度设计刀盘的刚度设计直接影响到刀具在施工过程中的稳定性和耐久性。
应该根据盾构机械的工作条件和土壤的物理特性,合理选择刀盘的材料和结构尺寸,确保刀盘具有足够的刚度。
1.1.2 刀盘模块化设计刀盘的模块化设计可以极大地提高刀具更换的效率,并且便于维护和保养。
刀盘的模块化设计应该考虑到刀具的安装和拆卸便捷性,同时也要保证刀具的工作性能。
1.1.3 刀盘防护设计刀盘的防护设计不仅能够保护刀具,在施工过程中还能够减少对环境的影响。
刀盘的防护设计应考虑到刀具的精度和平衡性,同时也要与盾构机械的其它部件协调配合。
1.2 刀盘传动系统设计刀盘传动系统是盾构机械的另一个重要部分,其设计的合理性对盾构机械的运行效果至关重要。
刀盘传动系统设计应该考虑以下几个方面:1.2.1 传动效率设计传动效率直接关系到盾构机械的工作效率。
刀盘传动系统的设计应该尽可能地提高传动效率,降低能量损耗。
1.2.2 齿轮设计齿轮是刀盘传动系统中常用的传动元件,其设计应考虑到负载分配、噪声控制等方面的需求。
合理选择齿轮的材料和结构尺寸,可以提高刀盘传动系统的可靠性和耐久性。
1.2.3 传动稳定性设计传动稳定性是刀盘传动系统设计时需要充分考虑的因素,合理选择传动比、减小晃动等措施,可以提高刀盘传动系统的稳定性。
2. 刀具设计与优化2.1 刀具材料选择刀具材料的选择直接影响到刀具的硬度、韧性和耐磨性等性能。
应根据盾构机械工作的土壤条件和设计要求,选择适合的刀具材料,以确保刀具有良好的工作性能和寿命。
砂卵石地层盾构机刀盘故障分析及结构优化研究

在盾构前期施工过程中,经常出现刀盘卡死以及刀盘
磨损较为严重的现象,通过现场实际情况,分析造成上述 情况的主要原因如下:
一是漂卵石粒径大、含量多,地层细颗粒少。卵石粒 径、含量较大,受刀盘开口限制,卵石不能进入土仓,导 致刀盘前方阻力增大,易引发刀盘卡滞。二是长时间停机。 盾构长时间停机,造成泡沫失效渣土和易性变差,导致阻 力增大使得刀盘卡死。三是盾构掘进超方,地层变松散。 盾构掘进过程中若发生超方、土压降低、上方土体松散, 会造成上方土体塌落,大量卵石进入土仓后使得刀盘阻力 增大,导致刀盘卡死。四是渣土改良不好,土仓结饼或卵 石沉积。渣土较干时,土仓内渣土流动性不足,导致渣土 及卵石堆积,增大了刀盘转动阻力,使得推力及扭矩增大, 易导致刀盘被困,磨损情况严重。五是刀盘正滚刀质心偏 心量和倾覆力矩较大,造成滚刀磨损速率较高。
表 2 典型工况下受力变形模拟结果
仿真结果
正常工况 静启动脱困 出洞推挤工况 堵转工况
原刀盘最大应力 /MPa 优化后刀盘最大应力 /MPa 原刀盘总变形量 /mm 优化后刀盘总变形 /mm
180.7 162.9 2.124 1.692
105.3 89.8 1.958 1.648
134.4 132.4 2.037 1.523
结果影响不大的结构。刀盘材料选用 Q345C 钢,密度设置 为 7900kg/m3,弹性模量设置为 210Gpa,泊松比设置为 0.3,
屈服强度和疲劳强度分别为 345MPa 和 298.1MPa。
根据现场施工地质条件以及遇到的不确定性,将现场
施工状况分为 4 类:一是正常工况。此时刀盘将承受正面
阻力和额定扭矩。二是静启动脱困工况。此时需要以大扭
0 引言
盾构机的刀盘

盾构机的刀盘北京固本科技有限公司胡建平盾构机的刀盘是一种用于隧道暗挖施工,具有金属外壳,壳内装有整机及辅助设备,在钢壳体掩护下进行土体开挖、土渣排运、整机推进和管片安装等作业,而使隧道一次成形的机械。
盾构机按掘进方式分为人工、半机械和机械化形式。
目前机械化盾构发展较快,它由刀盘旋转切削地层,采用螺旋输送机或泥浆管运送渣土,在壳体内拼装预制管片,依靠液压千斤顶推进。
一、盾构机的刀盘1.刀盘布置及磨损分析1.1刀盘布置刀盘的结构既要考虑刀盘的开挖性能,又要考虑渣土的流动性及掌子面的稳定性。
刀具的布置方式需要充分考虑工程地质情况。
本工程中盾构主要穿越砂性土,砂性土摩擦阻力大,渗透性强,在盾构的推进挤压下水分很快排出,土体强度提高,故不仅盾构推进摩擦阻力大,而且开挖面土压力也较大,对刀盘的磨损会比较严重。
另外,盾构土仓内刀具切削下来的砂土不易搅拌成均匀的塑流体,因此需要设置渣土改良设备。
鉴于上述工程实际情况,本工程盾构机采用了如图1所示的辐板式刀盘。
盾构刀盘由钢结构件焊接而成,目前其主流形式有面板式、辐条式及介于二者之间的幅板式。
辐板式刀盘兼有面板式和辐条式刀盘特点,由较宽的辐条和小块幅板组成,刀具分别布置在宽辐条的两侧和内部。
辐板式刀盘不仅使得土压平衡更易于控制,土砂流动顺畅,不易堵塞刀盘开口,且刀盘扭矩阻力小,保证有较好的掘进性能,又能节省设备投资,而且较大的面板有利于布置较多的刀具,同时较小的开口率也有利于保护本工程中容易坍塌的砂性土围岩的稳定。
1. 2盾构机磨损情况盾构机到达重工街站后,立即对盾构机及刀盘进行清理、检查,发现盾构机刀盘外周磨损非常严重。
盾构刀盘本体外缘侧板磨损在纵向方向上呈现中间大、两头小近似V形,在整个侧环面上形成一圈磨损凹槽,凹槽中部磨损平均为22 mm,两侧磨损平均为15 mm,如图 2 a 所示。
刀盘本体外周边缘在纵向方向上磨损约为160 mm,从外周边缘到刀盘中心径向方向上磨损约为180 mm,以致在刀盘外周边缘形成一个近似三角形的磨损区,如图 2 b 所示。
盾构机刀盘设计要点

盾构机刀盘设计要点作者:严盛越来源:《建筑工程技术与设计》2015年第04期盾构机刀盘设计五花八门,主要设计依据是盾构隧道的地质条件。
但针对相同地质条件,各制造厂家基于各自的理念设计出的刀盘又不尽相同。
作为使用单位,在进行设计联络、设计评审时,如何入手,如何判定优劣呢?刀盘设计的适应性判断是考虑问题的出发点。
刀盘结构外形的差异并不重要,只要结构强度满足力学要求,即满足极限条件下的推力、扭矩的要求即可。
我们需要关心的是另外几方面的问题:一、刀盘开口率刀盘开口率是指刀盘留空面积占整个刀盘面积的百分比。
这部分留空面积,是切削渣土的运动通道。
渣土脱离土体后,在重力及刀具刮削作用下,沿刀盘开口流动到土仓。
搅拌后,从土仓底部螺旋输送机排出。
开口率的大小对应的是渣土排放的效率。
若取值过小,破碎(切削)的渣土不能及时进入土仓,滞留在刀盘前方,跟随刀盘做摩擦运动,随着温度升高,会固结在刀具、辐条等部位形成泥饼。
因此,在结构强度允许的情况下,开口率尽可能地取较大的值较好。
开口率的取值对应刀盘的常态转速。
开口率的计算公式:K=1/(r+1)其中:K——开口率(%)r——刀盘转速(rpm)刀盘转速是一个从0到Rmax的范围值。
通常是连续可调的。
但刀盘的开口率是固定的,一经设计、制造成型就不可更改。
因此,确定刀盘开口率需要预先评估针对隧道地质条件下刀盘的经常工作状态,根据刀盘的常态转速来确定刀盘的开口率。
岩土硬度高、结理发育差的地层,刀盘转速应较大。
相应的,对刀盘开口率要求就小。
这与高硬度岩土开挖效率低,出渣量小的施工形态是对应的。
反之,岩土硬度低、结理发育丰富地层(如全、强风化地层),刀盘转速应较小。
对刀盘开口率要求就大。
例如,我单位施工的莞惠城际轨道交通GZH-6项目隧道地质主要是弱风化混合片麻岩,岩体较硬。
对于这类地层,施工时刀盘常态转速的经验值在1.5~2rpm之间。
据此,计算出开口率的值K在40%~33%范围内。
盾构机刀盘刀具的设计与优化
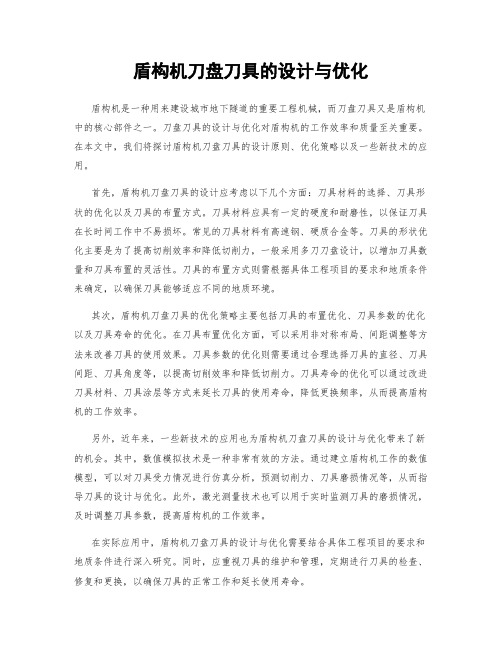
盾构机刀盘刀具的设计与优化盾构机是一种用来建设城市地下隧道的重要工程机械,而刀盘刀具又是盾构机中的核心部件之一。
刀盘刀具的设计与优化对盾构机的工作效率和质量至关重要。
在本文中,我们将探讨盾构机刀盘刀具的设计原则、优化策略以及一些新技术的应用。
首先,盾构机刀盘刀具的设计应考虑以下几个方面:刀具材料的选择、刀具形状的优化以及刀具的布置方式。
刀具材料应具有一定的硬度和耐磨性,以保证刀具在长时间工作中不易损坏。
常见的刀具材料有高速钢、硬质合金等。
刀具的形状优化主要是为了提高切削效率和降低切削力,一般采用多刀刀盘设计,以增加刀具数量和刀具布置的灵活性。
刀具的布置方式则需根据具体工程项目的要求和地质条件来确定,以确保刀具能够适应不同的地质环境。
其次,盾构机刀盘刀具的优化策略主要包括刀具的布置优化、刀具参数的优化以及刀具寿命的优化。
在刀具布置优化方面,可以采用非对称布局、间距调整等方法来改善刀具的使用效果。
刀具参数的优化则需要通过合理选择刀具的直径、刀具间距、刀具角度等,以提高切削效率和降低切削力。
刀具寿命的优化可以通过改进刀具材料、刀具涂层等方式来延长刀具的使用寿命,降低更换频率,从而提高盾构机的工作效率。
另外,近年来,一些新技术的应用也为盾构机刀盘刀具的设计与优化带来了新的机会。
其中,数值模拟技术是一种非常有效的方法。
通过建立盾构机工作的数值模型,可以对刀具受力情况进行仿真分析,预测切削力、刀具磨损情况等,从而指导刀具的设计与优化。
此外,激光测量技术也可以用于实时监测刀具的磨损情况,及时调整刀具参数,提高盾构机的工作效率。
在实际应用中,盾构机刀盘刀具的设计与优化需要结合具体工程项目的要求和地质条件进行深入研究。
同时,应重视刀具的维护和管理,定期进行刀具的检查、修复和更换,以确保刀具的正常工作和延长使用寿命。
总结起来,盾构机刀盘刀具的设计与优化是提高盾构机工作效率和质量的重要环节。
通过合理选择刀具材料、刀具形状以及刀具布置方式,优化刀具参数和刀具寿命,并结合新技术的应用,我们可以提高盾构机的工作效率,降低切削力,提高切割质量,从而为城市地下隧道的建设贡献力量。
新型盾构机刀盘系统设计与性能评估

新型盾构机刀盘系统设计与性能评估一、引言盾构机作为一种重要的地下工程施工设备,广泛应用于隧道、地铁等各类地下工程的建设中。
而盾构机的刀盘系统是其核心部件之一,其设计与性能评估对盾构机的工作效率、安全性和稳定性具有重要影响。
本文将针对新型盾构机刀盘系统的设计与性能评估进行详细讨论。
二、新型盾构机刀盘系统设计1. 结构设计新型盾构机刀盘系统的结构设计应考虑刀盘主体、刀盘刀片、承载结构等几个主要部分。
其中,刀盘主体应具有足够的强度和刚度,以承受土层掘进时的加载,并保证系统的稳定性。
刀盘刀片应选择适当的材料和形状,以提高切削效率和刀片的寿命。
承载结构应能够有效地传递切削力和承载土层的外部载荷。
2. 动力与传动设计新型盾构机刀盘系统的动力与传动设计是确保刀盘正常工作的重要因素。
动力系统应根据工程需求选择合适的动力源,并确保提供足够的功率和转速。
传动系统应设计为可靠、高效的传动方式,以充分发挥动力的利用率。
3. 液压系统设计盾构机刀盘的液压系统起到了承载切削力、协助刀盘掘进的重要作用。
设计时应考虑系统的稳定性、响应速度和能量损失等方面的因素。
合理布置液压元件、选择合适的油缸和油泵,并设计合适的油液流程,可以提高液压系统的效率和可靠性。
4. 控制系统设计新型盾构机刀盘系统的控制系统应能够实现对刀盘的精确控制。
设计时应考虑刀盘的自动控制、状态检测和故障诊断等功能。
同时,还应考虑与盾构机其他部件的协同工作,以实现整个系统的高效运行和安全性。
三、新型盾构机刀盘系统性能评估1. 动力性能评估对新型盾构机刀盘系统的动力性能进行评估,主要包括其动力输入与输出的匹配性、转矩和功率的变化情况、转速的稳定性等。
通过实验和仿真方法,可以对系统的动力性能进行精确评估,并针对不足之处进行改进和优化。
2. 切削性能评估通过对新型盾构机刀盘系统的切削性能进行评估,可以了解其在实际工程中的切削效率、刀片寿命和切削质量等方面的表现。
切削性能评估通常包括切削力的测量、刀片磨损的观察和土层切割效果的分析等内容。
盾构机刀盘设计与刀具优化分析

盾构机刀盘设计与刀具优化分析引言:盾构机刀盘是现代隧道工程中不可或缺的工具,其设计和刀具的优化分析对于提高隧道工程的效率和质量至关重要。
本文将会就盾构机刀盘的设计要点和刀具的优化分析进行详细探讨,希望能够为相关从业人员提供有价值的参考。
一、盾构机刀盘设计要点1.适宜的刀盘直径选择:刀盘直径的选择需要根据具体的隧道工程情况进行合理的选定。
通常情况下,刀盘直径不宜过大,以免给隧道掘进带来过大的应力。
同时,刀盘直径也要足够大,以确保刀盘能够顺利穿越地下障碍物。
2.刀盘结构的设计:刀盘结构的设计需要考虑刀盘的整体强度和稳定性。
首先,需要选择适宜的刀盘材料,以确保其正常工作状态下不会发生破损。
其次,刀盘的结构应该具备合理的刚性和刚度,以能够对复杂的地质情况和地下水力进行有效的抵抗。
3.刀盘导向系统的设计:刀盘导向系统是刀盘在掘进过程中的重要支撑系统,其设计的合理与否直接影响着刀盘的准确定位和稳定性。
因此,需要在设计中充分考虑刀盘导向系统的刚度和韧性,以确保刀盘能够准确地控制掘进方向并避免出现误差。
二、刀具的优化分析1.刀具材料的选择:刀具材料的选择直接影响着刀具的使用寿命和切削效率。
通常情况下,刀具应选择硬度较高、耐磨性能好的材料,以确保刀具在长时间的切削过程中不会出现过快的磨损和损坏。
2.刀具结构的优化:刀具结构的优化主要包括刀具形状和刀具排列方式的设计。
在刀具形状方面,需要选择适合具体地质条件的刀具形状,以确保切削效果的良好。
在刀具排列方式上,需要根据地质情况和工程要求进行合理的选择,以避免切削过程中的堵塞和卡刀现象。
3.刀具切削参数的优化:刀具切削参数的优化是提高切削效率和减少刀具磨损的关键。
在设计中,应合理选择切削速度、进给量和切削深度等参数,以确保刀具在长时间的切削过程中保持稳定的磨损状态和高效的切削效果。
结论:盾构机刀盘设计和刀具的优化分析对于隧道工程的顺利进行和质量的保障具有重要意义。
通过合理的刀盘设计和刀具优化分析,可以提高隧道工程的效率和质量,降低工程风险,为隧道工程从业人员提供更好的工作条件。
盾构机刀盘与刀具的设计与分析

盾构机刀盘与刀具的设计与分析盾构机是一种用于地下隧道开挖的机械设备,它的核心部件是刀盘和刀具。
刀盘是盾构机的主要工作部位,而刀具则是刀盘上的切削工具。
盾构机刀盘与刀具的设计与分析是为了提高盾构机的工作效率和安全性,下面将对这方面的内容进行讨论。
首先,盾构机刀盘与刀具的设计应考虑以下几个方面。
首先是刀盘的结构设计,包括刀盘直径、刀盘壳体的材料和强度设计。
刀盘直径的选择需要考虑隧道的尺寸和地质条件,以确保刀盘能够适应不同的工作环境。
刀盘壳体的材料选择应具有足够的强度和耐磨性,以保证刀盘的工作寿命和使用安全。
其次是刀盘上的刀具布置设计,包括刀具的数量、布局和角度。
刀具的数量应满足施工需要,布局应合理,角度的选择要考虑到土层特性和切削力的分布。
最后是刀盘与盾构机的连接设计,要确保刀盘能够与盾构机紧密连接,传递切削力和承受土压力。
其次,对于盾构机刀盘与刀具的分析,首先需要进行刀盘的载荷分析。
通过对刀盘受力情况的分析,可以确定刀盘的结构和材料,以确保其具有足够的强度来承受土压力和切削力。
其次是刀具的选择和分析。
不同的地质条件和隧道要求需要使用不同类型和材料的刀具。
刀具的选择应考虑到切削效率、耐磨性和经济性等因素。
此外,还需要对刀具的切削性能进行评估和分析,以提高切削效率和减少能耗。
最后是切削力的分析。
切削力对于刀具和刀盘的设计非常重要,因为过大或过小的切削力都会影响刀具的使用寿命和切削效率。
因此,对切削力的分析和评估可以指导刀具和刀盘的设计和优化。
此外,还可以运用有限元分析等工具对刀盘和刀具进行力学仿真分析,以评估其强度和刚度等性能指标。
通过仿真分析,可以发现潜在的结构问题和设计缺陷,并对刀盘和刀具的设计进行改进和优化。
总结起来,盾构机刀盘与刀具的设计与分析是为了提高盾构机的工作效率和安全性。
通过合理的设计和有效的分析,可以优化刀盘和刀具的结构,提高其强度和耐久性,以适应不同的地质条件和工作要求。
同时,对刀盘和刀具进行力学仿真分析,可以发现潜在的问题并进行改进和优化。
盾构机械刀盘设计与参数优化
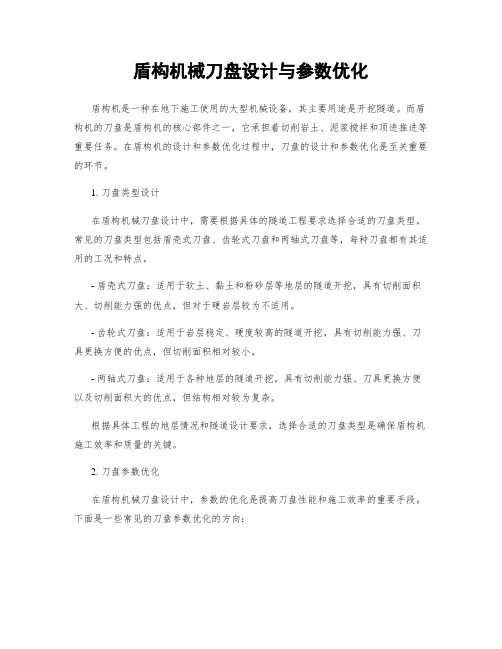
盾构机械刀盘设计与参数优化盾构机是一种在地下施工使用的大型机械设备,其主要用途是开挖隧道。
而盾构机的刀盘是盾构机的核心部件之一,它承担着切削岩土、泥浆搅拌和顶进推进等重要任务。
在盾构机的设计和参数优化过程中,刀盘的设计和参数优化是至关重要的环节。
1. 刀盘类型设计在盾构机械刀盘设计中,需要根据具体的隧道工程要求选择合适的刀盘类型。
常见的刀盘类型包括盾壳式刀盘、齿轮式刀盘和两轴式刀盘等,每种刀盘都有其适用的工况和特点。
- 盾壳式刀盘:适用于软土、黏土和粉砂层等地层的隧道开挖,具有切削面积大、切削能力强的优点,但对于硬岩层较为不适用。
- 齿轮式刀盘:适用于岩层稳定、硬度较高的隧道开挖,具有切削能力强、刀具更换方便的优点,但切削面积相对较小。
- 两轴式刀盘:适用于各种地层的隧道开挖,具有切削能力强、刀具更换方便以及切削面积大的优点,但结构相对较为复杂。
根据具体工程的地层情况和隧道设计要求,选择合适的刀盘类型是确保盾构机施工效率和质量的关键。
2. 刀盘参数优化在盾构机械刀盘设计中,参数的优化是提高刀盘性能和施工效率的重要手段。
下面是一些常见的刀盘参数优化的方向:- 刀具材料选择:选择合适的刀具材料可以提高刀具的硬度和耐磨性,延长刀具的使用寿命。
常用的刀具材料有高速钢、硬质合金和陶瓷等,根据具体工程的地层情况选择合适的刀具材料。
- 刀盘直径和刀具布局:刀盘直径的选择应根据隧道工程的要求和地质条件进行优化,一般情况下,刀盘直径越大,切削面积越大,切削能力越强。
同时,合理布局刀具的位置和角度,可以减少切削阻力和提高切削效果。
- 刀具类型和数量:根据地层条件和隧道设计要求,选择合适的刀具类型和数量。
刀具的类型包括刀片、齿轮和斗齿等,不同类型的刀具适用于不同的地层和切削任务。
- 刀盘结构设计:刀盘的结构设计包括刀盘的刚度、刀具固定方式和刀具更换等方面。
合理设计刀盘的结构可以提高刀盘的稳定性和切削效果,同时方便刀具的更换和维修。
1-3关于盾构机刀盘结构设计的几个问题
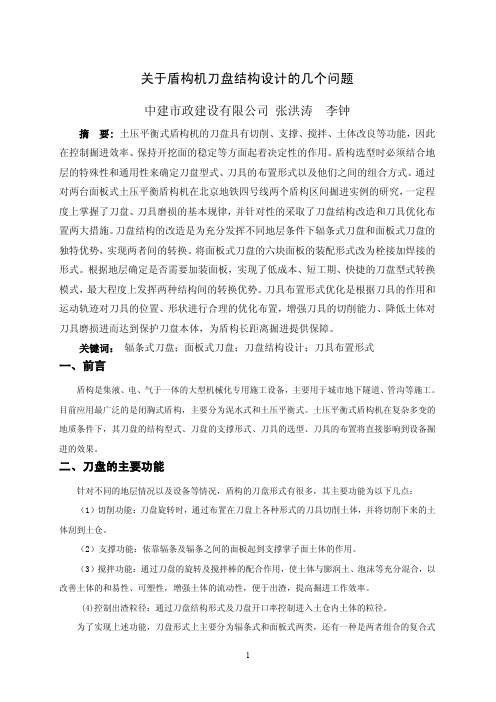
关于盾构机刀盘结构设计的几个问题中建市政建设有限公司张洪涛李钟摘要: 土压平衡式盾构机的刀盘具有切削、支撑、搅拌、土体改良等功能,因此在控制掘进效率、保持开挖面的稳定等方面起着决定性的作用。
盾构选型时必须结合地层的特殊性和通用性来确定刀盘型式、刀具的布置形式以及他们之间的组合方式。
通过对两台面板式土压平衡盾构机在北京地铁四号线两个盾构区间掘进实例的研究,一定程度上掌握了刀盘、刀具磨损的基本规律,并针对性的采取了刀盘结构改造和刀具优化布置两大措施。
刀盘结构的改造是为充分发挥不同地层条件下辐条式刀盘和面板式刀盘的独特优势,实现两者间的转换。
将面板式刀盘的六块面板的装配形式改为栓接加焊接的形式。
根据地层确定是否需要加装面板,实现了低成本、短工期、快捷的刀盘型式转换模式,最大程度上发挥两种结构间的转换优势。
刀具布置形式优化是根据刀具的作用和运动轨迹对刀具的位置、形状进行合理的优化布置,增强刀具的切削能力、降低土体对刀具磨损进而达到保护刀盘本体,为盾构长距离掘进提供保障。
关键词:辐条式刀盘;面板式刀盘;刀盘结构设计;刀具布置形式一、前言盾构是集液、电、气于一体的大型机械化专用施工设备,主要用于城市地下隧道、管沟等施工。
目前应用最广泛的是闭胸式盾构,主要分为泥水式和土压平衡式。
土压平衡式盾构机在复杂多变的地质条件下,其刀盘的结构型式、刀盘的支撑形式、刀具的选型、刀具的布置将直接影响到设备掘进的效果。
二、刀盘的主要功能针对不同的地层情况以及设备等情况,盾构的刀盘形式有很多,其主要功能为以下几点:(1)切削功能:刀盘旋转时,通过布置在刀盘上各种形式的刀具切削土体,并将切削下来的土体刮到土仓。
(2)支撑功能:依靠辐条及辐条之间的面板起到支撑掌子面土体的作用。
(3)搅拌功能:通过刀盘的旋转及搅拌棒的配合作用,使土体与膨润土、泡沫等充分混合,以改善土体的和易性、可塑性,增强土体的流动性,便于出渣,提高掘进工作效率。
(4)控制出渣粒径:通过刀盘结构形式及刀盘开口率控制进入土仓内土体的粒径。
盾构机刀盘及刀具设计优化

盾构机刀盘及刀具设计优化盾构机是一种专门用于隧道掘进的工程机械装备,它在地下工程中起到了至关重要的作用。
盾构机的刀盘和刀具作为关键部件,直接影响着盾构机的掘进效率和质量。
因此,对于盾构机刀盘及刀具的设计优化具有重要意义。
首先,盾构机刀盘及刀具的设计需考虑到地质条件、盾构机类型和掘进要求等因素。
地质条件直接影响到盾构机的切削阻力和切削速度,需要对刀盘结构和刀具的数量和类型进行合理选择。
盾构机类型也会对刀盘设计产生影响,如土压平衡盾构机和非土压平衡盾构机,需要在设计中考虑到盾构机的形式尺寸和刀盘的结构强度。
此外,根据掘进要求,刀盘和刀具的尺寸、形状和材质也需要进行相应的优化设计。
在盾构机刀盘及刀具设计中,刀盘的结构应合理布局,刀具的材质和形状应选择适当。
刀盘结构应考虑到刀具的均布性和稳定性,以确保刀具在掘进过程中的正常工作和寿命。
刀盘的布置应遵循合理的原则,以确保刀具之间的间隙和配合尺寸符合要求,减小刀具在挖掘过程中的卡住和堵塞现象。
同时,刀盘的强度和刚度应满足设计要求,以承受掘进时的切削力和地质应力。
刀具的选择和设计是盾构机刀盘和刀具设计优化的重要部分。
刀具的材质应考虑到其硬度、耐磨性和抗冲击性等特性,以延长刀具的使用寿命和维持切削效果。
在刀具形状设计中,需要考虑到刀具的切削角度、刀片形状和锋面处理等参数,以提高切削效率和切削质量。
刀具形状的设计可以根据地质条件和掘进要求进行优化,以实现最佳的切削效果和刀具寿命。
此外,在盾构机刀盘及刀具设计优化中,还可以考虑引入先进的技术手段和智能化控制系统。
例如,利用仿真软件对刀盘和刀具进行数值模拟分析,优化刀盘结构和刀具布局,以提高掘进效率和质量。
同时,可以利用智能传感器和监测系统实时监测刀盘和刀具的工作状态,及时发现问题并进行调整和维修。
总之,盾构机刀盘及刀具的设计优化对于提高盾构机的掘进效率和质量具有重要作用。
在设计过程中,需要考虑地质条件、盾构机类型和掘进要求等因素,合理布局刀盘结构和选择刀具材质。
盾构机刀盘选型及设计理论研究

Cutter is selected
designed for the
Cutter
are
Unique geological conditions.And the three basic conditions researched by the Finite
of the
element method.it verifies the
西南交通大学 硕士学位论文 盾构机刀盘选型及设计理论研究 姓名:宋云 申请学位级别:硕士 专业:机械设计及理论 指导教师:管会生 20090401
摘要
盾构机是一种专门用于开挖地下隧道的大型成套施工设备,在城市隧道 的开挖中得到越来越广泛的应用。刀盘作为盾构机上最重要的部件,国内对 它的设计研究尚处起步阶段。本论文对盾构机刀盘选型以及设计进行了研
examples,the
useful conclusions are
analyzed
by the
selection of the CuRerhead. Secondly,the thesis has researched the curerhcad’S design parameters and formula of knives,summarized the calculation methods for the disc curer’S 10ad a11
究,具体内容如下:
研究了影响盾构机刀盘选型的因素,包括:刀盘型式、刀盘开口率、驱
动形式、支承形式、最大转速和扭矩、刀盘开挖直径以及刀盘上刀具的配置。
并且通过几个实例,分析得出了对盾构机刀盘选型有参考价值的结论。
详细地阐述了刀盘的设计参数和刀具的力学计算公式,并且总结了国内
- 1、下载文档前请自行甄别文档内容的完整性,平台不提供额外的编辑、内容补充、找答案等附加服务。
- 2、"仅部分预览"的文档,不可在线预览部分如存在完整性等问题,可反馈申请退款(可完整预览的文档不适用该条件!)。
- 3、如文档侵犯您的权益,请联系客服反馈,我们会尽快为您处理(人工客服工作时间:9:00-18:30)。
盾构机刀盘设计要点探究
盾构机刀盘设计五花八门,主要设计依据是盾构隧道的地质条件。
但针对相同地质条件,各制造厂家基于各自的理念设计出的刀盘又不尽相同。
作为使用单位,在进行设计联络、设计评审时,如何入手,如何判定优劣呢?
刀盘设计的适应性判断是考虑问题的出发点。
刀盘结构外形的差异并不重要,只要结构强度满足力学要求,即满足极限条件下的推力、扭矩的要求即可。
我们需要关心的是另外几方面的问题:
一、刀盘开口率
刀盘开口率是指刀盘留空面积占整个刀盘面积的百分比。
这部分留空面积,是切削渣土的运动通道。
渣土脱离土体后,在重力及刀具刮削作用下,沿刀盘开口流动到土仓。
搅拌后,从土仓底部螺旋输送机排出。
开口率的大小对应的是渣土排放的效率。
若取值过小,破碎(切削)的渣土不能及时进入土仓,滞留在刀盘前方,跟随刀盘做摩擦运动,随着温度升高,会固结在刀具、辐条等部位形成泥饼。
因此,在结构强度允许的情况下,开口率尽可能地取较大的值较好。
开口率的取值对应刀盘的常态转速。
开口率的计算公式:K=1/(r+1)
其中:K——开口率(%)
r——刀盘转速(rpm)
刀盘转速是一个从0到Rmax的范围值。
通常是连续可调的。
但刀盘的开口率是固定的,一经设计、制造成型就不可更改。
因此,确定刀盘开口率需要预先评估针对隧道地质条件下刀盘的经常工作状态,根据刀盘的常态转速来确定刀盘的开口率。
岩土硬度高、结理发育差的地层,刀盘转速应较大。
相应的,对刀盤开口率要求就小。
这与高硬度岩土开挖效率低,出渣量小的施工形态是对应的。
反之,岩土硬度低、结理发育丰富地层(如全、强风化地层),刀盘转速应较小。
对刀盘开口率要求就大。
例如,我单位施工的莞惠城际轨道交通GZH-6项目隧道地质主要是弱风化混合片麻岩,岩体较硬。
对于这类地层,施工时刀盘常态转速的经验值在1.5~2rpm之间。
据此,计算出开口率的值K在40%~33%范围内。
根据强度优先的
原则,采用辐条+面板的结构形式。
结合刀具的布置等其它因素,刀盘开口率最后结果值是31%。
根据K值范围看,这个结果偏小。
为保证在局部软弱地层中的开挖效率,盾构设计方采用了加大中心区域刀盘开口的方法来提高刀盘的适应性。
即将中心刀(双刃)一线排列,中心部位其余地方留空,将中心1.6m范围内的开口率提高到41%。
二、刃间距
刀盘旋转时,每一个滚刀运动轨迹都是一个以刀盘回转中心为圆心的轨迹圆。
两个相邻轨迹圆之间的距离就是刃间距。
轨迹相邻的两把刀不是物理相邻,而通常是关于圆心对称。
刃间距的确定同样有赖于盾构隧道的岩土性质。
确定合理的刃间距是要实现良好的破岩效率。
既不浪费,也不欠缺。
理想的破岩状态是相邻两轨迹的破碎截面恰好相接。
如下图:
刃间距S的计算式是:
S=2L+T
=2P*tan(a/2)+T
其中:
P——贯入度;
a——岩石破碎角;
T——刃尖宽度。
混合片麻岩的破碎角是160°,17”滚刀的刃尖宽度是20mm。
贯入度P取值为5mm时,计算的刃间距是76.48mm。
公式中,刃间距与贯入度(P)之间是正比关系。
贯入度P并不是一个恒定值,较好的围岩中,贯入度值可能会更大,可以达到10mm/r以上。
而且,围岩不变的情况下,贯入度的值也无法保持恒定。
因此,成正比变动的刃间距值也就难有一个确定值。
而要在刀盘上动态调整刃间距是难以实现的。
目前的刀盘刀具布置还都是固定间距设计。
所以,确定贯入度的取值还是必要的。
三、滚刀数量
从几何意义上讲,滚刀数量与刃间距之间有一个简单的对应关系。
即:滚刀数量=刀盘半径/刃间距+1。
但实际情况并不如此。
这是因为各个轨迹上的刀具的破岩体积是不一样的。
随着切削轨迹半径的增加,对应位置的滚刀切削路径(转动周长)逐次加大。
破岩量也随之加大。
因此,外缘的刀具磨损速度肯定远大于中心区域的刀具。
导致的直接结果是外缘刀具频繁损坏,需停机更换,整体施工效率不高。
解决的思路是缩短外缘刀具的刃间距,增加外缘刀具数量。
如此,刃间距在整个刀盘面上表现出一种不均匀性。
即内圆轨迹均匀分布,而外圈的刃间距逐渐变小。
因此,滚刀的数量就再不是上述关系式的简单计算值,而是比这个计算值要大。
例如我单位承建的莞惠城际轨道交通GZH-6项目使用的两台Φ8830盾构机刀盘直径为8830,按80mm刃间距计算的滚刀数量是56把滚刀(4415/80+1),而厂家设计为54把滚刀,比计算数量少。
显然,厂家对刃间距的设计取值比80mm 要大。
考虑到76.48mm(80mm)刃间距的值是一个下限参考值。
大于这个值也是可以接受的。
但通过对破岩量的对比分析,我们认为,将刀具数量增加到60把更加合理。
因此,要求厂家将刀盘刀具配置调整到60把。
图表-1是两种设计方案的每个滚刀的破岩体积对照图。
从图表-1中可以看出,25#~45#刀具的破岩体积明显减小。
曲线变化趋于柔和,这意味着刀具的磨损不均匀性得到进一步缓解。
图表-1
四、偏心矩
偏心矩是一个力学概念,但可以理解为另一个表征刀具布置均匀性的概念。
掘进时,刀具对前方岩土施加作用。
对应的,也受到一个大小相等,方向相反的反作用力。
这些力因为作用在不同的刀具上,每一个力都有一个相对于刀盘回转中心的力臂,产生力矩。
对称分布的刀具,相互之间能抵消彼此的力矩。
该力矩作用在主轴承上,导致刀盘运转不平稳。
另一方面,会对刀具产生一个侧向力,造成刀刃非正常损坏。
因此,刀具分布应尽可能降低这个偏心矩。
偏心矩计算公式是:
T=SQRT (T x²+Ty²)
其中,a——第i把刀在刀盘上的分布角(象限角);
θ——刀圈平面与盾构机轴线的夹角;
Fi——第i把刀受岩土的反作用力;
Ri——第i把到的轨迹半径;
n——刀具总数。
仍以上例所举刀盘为例。
根据该计算公式得出优化前后的偏心矩分别为:优化前:T=1853 KNm
优化后:T=100.6 KNm
因此,可以看出,所做优化是有效的。
五、结语
综上所述,刀盘设计需要涉及的内容很繁杂。
既要充分了解针对地层的地质条件,又要有相关的施工经验作为设计依据,更需要耐心地反复调整、验算。
本文只涉及到刀盘设计的某些方面,还有更多机械制造、结构分析等方面的工作要做。
另一方面,使用单位还应在施工生产中详细认真地做好数据采集工作,并从各项数据中分析、总结出更加合理的施工、运行参数,为进一步完善盾构机设计做出有益而坚实的贡献。