陶瓷窑炉余热回收利用
陶瓷窑炉余热利用节能技术改造项目节能措施

陶瓷窑炉余热利用节能技术改造项目节能措施1.1改造前后能耗需求及能耗指标1. 改造前成型车间能耗分析项目实施前成型车间消耗的能源主要是天然气,年消耗量为213.11万立方米,年消耗能源相当于2587.80吨标准煤(213.11×12.143)。
2. 改造后能耗计算过程如下:项目改造后成型车间利用回收的窖炉余热取代天然气供热来烘干坯体,因此成型车间不再直接消耗能源。
由于新增9台抽热风机,所以增加了电耗,新增能耗计算过程如下:以每年生产300天计,全年新增耗电量:300×24×9×11=71.28(万千瓦时)。
折标准煤:71.28×3.57=254.47(吨)3. 项目节能量计算本项目实施后,成型车间用回收的窖炉余热完全取代天然气供热,年节约天然气213.11万立方米,折标准煤2587.80吨。
项目新增能耗254.57吨标准煤。
项目节能量为:节约能源量-新增能源消耗量=2587.80-254.57=2333.33(吨标准煤)1.2相关节能措施1.2.1管理措施项目单位管理者认识到能源管理工作的重要性,只有有效地管理才能使节能工作再上一个台阶,才能确保公司节能达到预期的目标。
该公司成立了能源管理组织机构对所消耗能源进行统一管理。
能源管理组织机构及管理职责如下表所示:表6-3 能源管理组织机构及管理职责1.2.2技术措施拟采用余热利用系统,根据窑炉的特点,急冷抽热排放是热量最多,窑炉从冷却带抽出冷却热风与窑顶换热风混合,由抽风机集中抽出,为烤房、成型车间提供可控温度系统,改善原来供热装置,从而达到节约供热燃耗。
1.2.3节能效果评价综合以上分析,相对于改造前,本项目节能效果非常明显,有利于节约能源,减少污染,提高经济效益和社会效益。
炉窑余热的回收与利用
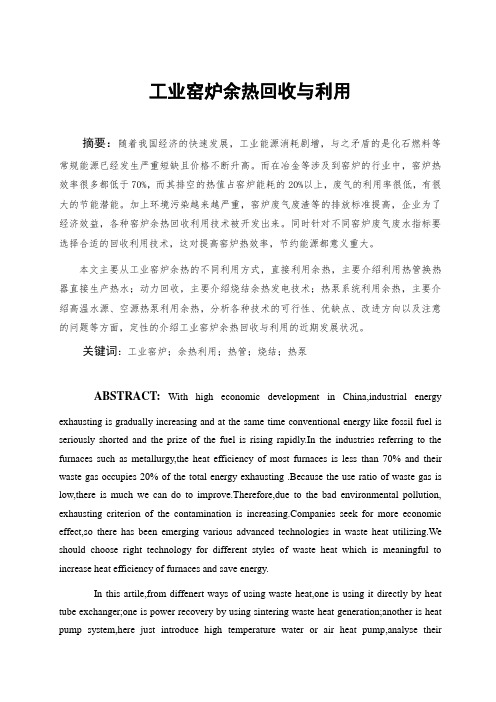
工业窑炉余热回收与利用摘要:随着我国经济的快速发展,工业能源消耗剧增,与之矛盾的是化石燃料等常规能源已经发生严重短缺且价格不断升高。
而在冶金等涉及到窑炉的行业中,窑炉热效率很多都低于70%,而其排空的热值占窑炉能耗的20%以上,废气的利用率很低,有很大的节能潜能。
加上环境污染越来越严重,窑炉废气废渣等的排放标准提高,企业为了经济效益,各种窑炉余热回收利用技术被开发出来。
同时针对不同窑炉废气废水指标要选择合适的回收利用技术,这对提高窑炉热效率,节约能源都意义重大。
本文主要从工业窑炉余热的不同利用方式,直接利用余热,主要介绍利用热管换热器直接生产热水;动力回收,主要介绍烧结余热发电技术;热泵系统利用余热,主要介绍高温水源、空源热泵利用余热,分析各种技术的可行性、优缺点、改进方向以及注意的问题等方面,定性的介绍工业窑炉余热回收与利用的近期发展状况。
关键词:工业窑炉;余热利用;热管;烧结;热泵ABSTRACT:With high economic development in China,industrial energy exhausting is gradually increasing and at the same time conventional energy like fossil fuel is seriously shorted and the prize of the fuel is rising rapidly.In the industries referring to the furnaces such as metallurgy,the heat efficiency of most furnaces is less than 70% and their waste gas occupies 20% of the total energy exhausting .Because the use ratio of waste gas is low,there is much we can do to improve.Therefore,due to the bad environmental pollution, exhausting criterion of the contamination is panies seek for more economic effect,so there has been emerging various advanced technologies in waste heat utilizing.We should choose right technology for different styles of waste heat which is meaningful to increase heat efficiency of furnaces and save energy.In this artile,from diffenert ways of using waste heat,one is using it directly by heat tube exchanger;one is power recovery by using sintering waste heat generation;another is heat pump system,here just introduce high temperature water or air heat pump,analyse their feasibility, advantages or disadvantages,directions of improving and matters needing attention and so on,qualitatively introduce waste heat utilizing of furnace over the dacades.KEY WORDS: industrial furnaces;waste heat utilizing;heat tube;sintering;heat pump工业窑炉余热回收与利用0引言当前,各类工业窑炉的排烟温度高,废气量大,废气带走的能量大约占到总能耗的20%~30%,虽然窑炉会利用其余热充分预热空气、物料、燃料,但是排气的温度还是很高,损失很大能量。
陶瓷窑炉余热利用技术在实践中的应用

≮ 画
1.前言
j uo s s f c Cac c啪c ei r m
道的设计尺寸做相应调整。
陶瓷 窑炉的平均热效率 只有2 % 0 左右 ,排
烟温度普遍在3 W 以上,烟 气所带走的热损失 0C
4. 热水生产工艺流程
在6 陶瓷窑炉的排烟管道 上安 装6 条 套换热 是这样的 :整个系统最初始是按J窑 、J窑、J 1 2 3
蒜 藜 _ 文 绍 江 斯 克 瓷 限 自酸本 介 了 西 束 陶 有 I
利用的烟气量l00 / 0Nm3h,换热后烟气排放 5
公司年产l0 万m 瓷砖生产线项 目 50 2 在新建的6 温度 I0 计算 , 气可以 回收的热焓达N4万 × .5 奈 O" C 烟 O 03系数 =回收热量 (clh ka ) /
1 )不能影响陶瓷窑炉的正常生产 ;
须限制在2 o a 5 P 以内; 保护措施 ,
2 )安装在烟道上的换热设备 的烟气阻力必 炉 的余 热资源丰富 ,整个系统 只要有一 条窑 炉 3 )应考虑到夏季不用热水时对换热设备的 要 ,同时 ,为了避免6 条旁通烟道与垂直烟 道的 频繁切换 , 影响陶瓷窑炉的正常生产 , 保持窑炉 间相对长些 ,不要频繁切换 。所以六套控制设备 六套控制设备只要有一套在运行,其它组就都保 持初始状态 。轮流运行的概念在运行程序的表现 4 )换热设备 必须采用耐高温材料制作 ,而 的风压稳定,因此希望切换到旁通烟道的运行时 且有必要的防腐措施 ; 5 )安装在烟道内的换热器的尺寸应根据烟 是轮流运行的 , 而且在同一时间内只运行一套,
3 .窑炉余热利用的条件
在陶瓷窑炉的烟道上攫取热能 ,应注重以
下原则:
于关闭状态 ( 常闭碟 阀)。
喷雾干燥塔利用陶瓷窑炉余热技术.

喷雾干燥塔利用陶瓷窑炉余热技术一、所属行业:建材行业二、技术名称:喷雾干燥塔利用陶瓷窑炉余热技术三、适用范围:充分利用陶瓷窑炉烧结的排烟余热和冷却成品后的热风余热四、技术内容:1.技术原理按照工艺使用能源的质量(品质)要求综合地分等级使用能源,充分和合理地回收烟气和热风的余热,将制粉、干燥和烧结的工艺过程中能源转换和利用综合在一起统筹考虑,最终把没有利用价值的废气集中到喷雾干燥塔的排气口,集中进行环保处理。
2.关键技术将产品烧结过程中排放到大气中窑炉烟气和窑尾废气最大限度地进行回收,按质用能、分级合理用能,制粉、干燥和烧结的工艺过程中能源转换和利用,充分利用这部分废气进行原料干燥、烘干砖坯进入烧结辊道窑,从而对窑炉余热进行资源综合利用。
(1)首先是制粉、干燥和烧结的工艺过程中能源转换和利用的实质性问题,包括水分在制粉(空心圆形颗粒)的蒸发传质传热机理,寻求最佳的进塔干燥热风的温度;其次是坯体干燥过程中,坯体内部传热及水分渗透、蒸发过程的基本原理,寻找适当的含湿量和温度的热风和烟气作为坯体干燥的介质,并且选配适当的干燥时间,以达到最好的烘干效果;最后是通过合理预设的烧结温度和时间,充分利用工艺过程中产品烧成时的物理、化学变化过程中的放热和吸热时间和数量的配合,合理地选择加热、冷却的温度和过程配套的时间,改变或调整工艺,降低工艺能耗。
(2)按能源的等级,按质综合使用能源。
综观陶瓷产品从原料到成形的工艺过程,使用的载能热流介质的温度是从80℃到1350℃的跨幅,善用温度级差是整个成形工艺过程的节能关键问题。
(3)结合按质用能,把载能热流介质统一传输到用能的终端出口,综合脱硫和去除NOX,回收固体颗粒,实现零排放。
3.工艺流程窑炉余热回收利用的技术方案图项目方案描述:本项技术改造是把烧结工艺、干燥坯体以及喷雾干燥塔等工艺过程综合考虑、分级利用。
如上图所示:①烧结阶段是三者中耗能量最大的,而且产生大量的烟气和用于急冷、缓冷的热风,经热平衡计算烟气和热风的热量足以供给干燥和喷雾干燥塔工艺过程所需热量。
陶瓷窑炉余热利用节能技术改造项目实施的必要性及意义

陶瓷窑炉余热利用节能技术改造项目实施的必要性及意义1.1项目实施的必要性1.1.1节能减排是我国经济可持续的保证党的十六届五中全会提出把节约资源作为基本国策,“十一五”规划《纲要》进一步把“十一五”时期单位GDP 能耗降低20%左右作为约束性指标,凸显了节能工作的极端重要性和紧迫性。
节能是解决我国能源问题的根本途径,是当前经济工作的一项紧迫性任务。
1. 节能必要性分析我国经济增长模式的主要特征是投资推动和高增长。
近三十年来,国内生产总值增长率年均为9.5%,在大部分时期,投资在国内生产总值中的比重大于40%,现在接近50%。
我国经济中的主导一直是重工业。
在1985年,重工业比重占国内工业总产值的55%。
1990年降到50%,2000年回升到60%,2005年高达69%。
在经济增长和城市化进程引起的大规模基础设施投资的推动下,重工业,尤其是高耗能产业在近几年得到了快速发展。
2006年我国能源消耗达到24.6亿吨标准煤(大约占世界能源总消耗的15%)。
如果将能源需求降低到5%,年增加量也需要1.23亿吨标准煤。
事实上,如果GDP增长为9%,以目前的经济结构和增长方式,很难将能源需求降低到5%。
因此,2007年4月10日国家发改委公布《能源发展“十一五”规划》,将2010年一次能源消费总量目标控制目标为27亿吨标准煤左右。
这是一个过于保守,而且从一开始就已经是落后了的总量控制目标。
因为即使所有的都做对了,仍然不可能有足够的时间去完成调整经济结构和耗能方式来达到总量控制。
能源需求总量的问题是相对于能源储量和人口而言的。
应当说我国能源资源储量并不少,但人口众多导致了我国人均能源占有率远低于世界平均水平,2005年石油、天然气和煤炭人均剩余可采储量分别只有世界平均水平的7.69%、7.05%和58.6%。
以储量最丰的煤炭为例,根据国际通行的标准,2001年我国煤炭的经济可开发剩余可采储量有1145亿吨。
2002年用煤12亿吨,煤炭可用100年;如果没有充足的储量增加,2006年再计算经济可采储量就只够用50年,按现在的年消费量(24.6亿吨)来计算,煤炭资源的开发前景不甚乐观。
(2023)陶瓷窑炉余热利用项目可行性研究报告(一)
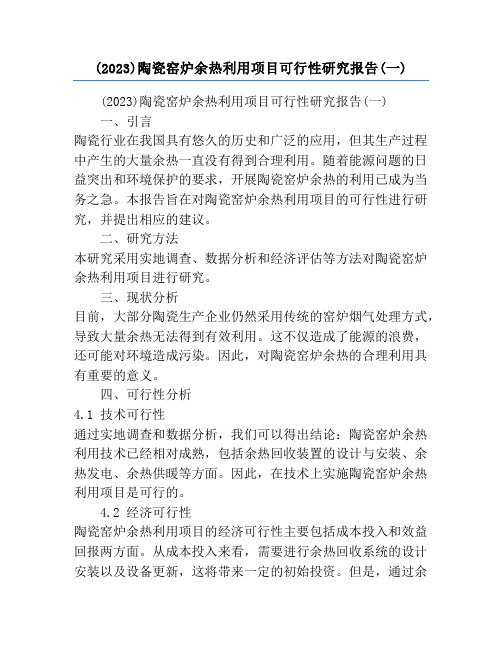
(2023)陶瓷窑炉余热利用项目可行性研究报告(一)(2023)陶瓷窑炉余热利用项目可行性研究报告(一)一、引言陶瓷行业在我国具有悠久的历史和广泛的应用,但其生产过程中产生的大量余热一直没有得到合理利用。
随着能源问题的日益突出和环境保护的要求,开展陶瓷窑炉余热的利用已成为当务之急。
本报告旨在对陶瓷窑炉余热利用项目的可行性进行研究,并提出相应的建议。
二、研究方法本研究采用实地调查、数据分析和经济评估等方法对陶瓷窑炉余热利用项目进行研究。
三、现状分析目前,大部分陶瓷生产企业仍然采用传统的窑炉烟气处理方式,导致大量余热无法得到有效利用。
这不仅造成了能源的浪费,还可能对环境造成污染。
因此,对陶瓷窑炉余热的合理利用具有重要的意义。
四、可行性分析4.1 技术可行性通过实地调查和数据分析,我们可以得出结论:陶瓷窑炉余热利用技术已经相对成熟,包括余热回收装置的设计与安装、余热发电、余热供暖等方面。
因此,在技术上实施陶瓷窑炉余热利用项目是可行的。
4.2 经济可行性陶瓷窑炉余热利用项目的经济可行性主要包括成本投入和效益回报两方面。
从成本投入来看,需要进行余热回收系统的设计安装以及设备更新,这将带来一定的初始投资。
但是,通过余热的合理利用,可以降低能源成本和减少污染治理费用,从而实现经济效益。
4.3 社会可行性陶瓷窑炉余热利用项目的实施将减少能源消耗,降低环境污染,改善生态环境。
同时,通过提升企业的技术水平和生产能力,还可以促进区域经济发展,提高就业机会,提升社会福利。
因此,从社会可行性角度来看,陶瓷窑炉余热利用项目是十分可取的。
五、结论与建议通过对陶瓷窑炉余热利用项目的研究与分析,我们得出以下结论:1. 技术上,陶瓷窑炉余热利用项目是可行的。
2. 经济上,陶瓷窑炉余热利用项目具有一定的投资回报。
3. 社会上,陶瓷窑炉余热利用项目能够带来积极的社会效益。
基于以上结论,我们提出以下建议:1. 政府应出台相应的政策支持,鼓励和推动陶瓷窑炉余热的合理利用。
窑炉余热利用节能技术改造说明

窑炉余热利用节能技术改造说明窑炉余热利用节能技术改造说明窑炉节能技术简介一、改造前窑炉热耗现状传统陶瓷窑炉制品热耗大的原因:(1)、窑体对外散热损耗大。
在升温过程中窑墙、窑顶向外散失热量并同时被加热升高温度它们所积聚的热量在燃料消耗总量中所占比例很大约10-15%这部分的热量不但不能利用而且在冷窑过程中又放出阻碍了产品的冷却__了冷窑时间。
(2)、匣钵耗热损耗大。
用匣钵隔焰烧成烧耗了的产品及加热至高温的匣钵带走大量的热约占燃料消耗的20-30%冷却时也不易利用而浪费掉。
(3)、烟气排空热损耗大。
烟气离开吸火孔时的温度至少要比产品的烧成温度高30-50℃若温度低了烟气就不能把热量传给制品制品就烧不熟这样高的气体一离开窑底就成为烟气由烟囱排走废气带走的热量约占燃料消耗量的30-50%。
总之传统窑炉窑体、匣钵、烟气损耗热量大损耗的热量约占燃料消耗总量的60-95%热有效利用率在40%以下甚至有些窑炉热有效利用率为5-7%这是造成单位制品热损耗大的原因。
二、窑炉改造节能技术特点(1)、对窑体进行改造采用更加优质的轻质砖窑体密封效果好强化其保温效果余热利用管道均采用优质保温棉包捆散热量达到最小值。
节能达10-15%。
(2)、对窑炉结构进行技术改造即将原隔焰式用匣钵装的窑炉改为明焰无匣钵的窑炉有利于节能节能达20-30%。
(3)、拆除烟囱采用新的余热利用装置将所有窑炉烟气余热全部回收利用用于烘干干燥用热节能达30-50%。
(4)、将间歇式窑炉改为低温快速连续式工作烧成减少窑体、窑具吸热节能达25-40%。
通过上述节能技术改造从而达到燃料总量不增加热有效利用率提高65-86%的节能效果用于烘干干燥余热利用。
余热利用节能技术改造简介一、改造前用能现状陶瓷产品烧成余热利用普遍存在一个热利用效率低的问题窑体对外散热、匣钵吸热、烟气全部排空造成热量极大消费导致陶瓷厂家每家每一条窑炉都配有一台锅炉或一台燃煤热风炉燃煤烘房等热能补充设备才能满足成型生产坯件模具等烘干、干燥的需要。
(2023)陶瓷窑炉余热利用项目可行性研究报告(一)
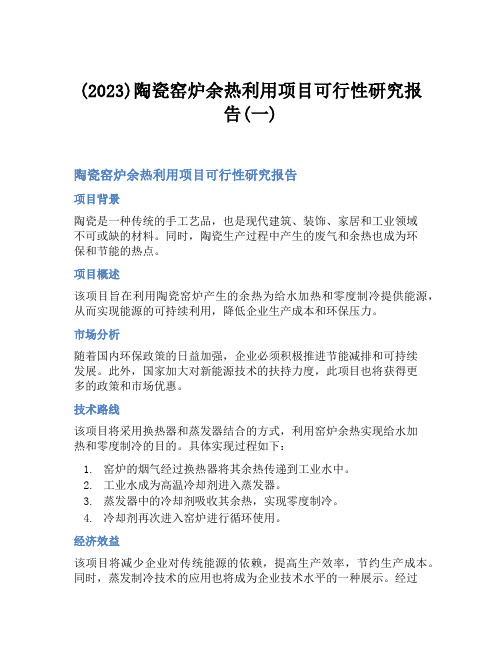
(2023)陶瓷窑炉余热利用项目可行性研究报告(一)陶瓷窑炉余热利用项目可行性研究报告项目背景陶瓷是一种传统的手工艺品,也是现代建筑、装饰、家居和工业领域不可或缺的材料。
同时,陶瓷生产过程中产生的废气和余热也成为环保和节能的热点。
项目概述该项目旨在利用陶瓷窑炉产生的余热为给水加热和零度制冷提供能源,从而实现能源的可持续利用,降低企业生产成本和环保压力。
市场分析随着国内环保政策的日益加强,企业必须积极推进节能减排和可持续发展。
此外,国家加大对新能源技术的扶持力度,此项目也将获得更多的政策和市场优惠。
技术路线该项目将采用换热器和蒸发器结合的方式,利用窑炉余热实现给水加热和零度制冷的目的。
具体实现过程如下:1.窑炉的烟气经过换热器将其余热传递到工业水中。
2.工业水成为高温冷却剂进入蒸发器。
3.蒸发器中的冷却剂吸收其余热,实现零度制冷。
4.冷却剂再次进入窑炉进行循环使用。
经济效益该项目将减少企业对传统能源的依赖,提高生产效率,节约生产成本。
同时,蒸发制冷技术的应用也将成为企业技术水平的一种展示。
经过初步测算,该项目预计年节约能源约xxx吨标准煤,年节约用水约xxx 吨。
社会效益该项目实现产业和生态的协调发展,有效减少环境污染,提升企业形象和社会责任感。
风险管理该项目仍存在一定的技术风险,需要依靠技术团队的严密把关和实时监测。
同时,市场风险和政策风险也需要进行持续的跟踪和调整。
推广前景该项目具有广阔的市场前景,不仅适用于陶瓷行业,也可用于玻璃、环保、电子等行业。
同时,随着技术的不断升级和完善,该项目未来也将呈现出更为广阔的发展前景和应用领域。
结论通过对陶瓷窑炉余热利用项目的分析和研究,可以得出该项目具有显著的经济效益、社会效益和推广前景,具有可行性和发展潜力。
同时,需要注意风险管理和技术创新,确保项目落地开展顺利。
建议措施在项目实施过程中,为确保可行性和效益最大化,可采取以下措施:1.充分调研市场和技术状况,确定最优方案和合适的产业链合作伙伴。
陶瓷窑炉余热利用节能技术改造项目设备及技术方案

陶瓷窑炉余热利用节能技术改造项目设备及技术方案1.1 技术方案1.1.1改造前生产工艺分析1.改造前生产工艺流程原料精选处理分别粉碎过筛、除铁,控制最大颗研磨配料压滤陈腐真空炼泥修坯干燥成型素烧彩饰喷釉成品釉烧5-1改造前生产工艺流程图2.节能技术改造潜力项目实施前公司产品成型车间干燥所用燃料为天然气,能耗高,热利用率低,项目单位认为:该公司单位产品能耗较大,热利用率低,仍有很大节能潜力。
1.1.2改造后生产工艺分析改造后的主要生产工艺没有变化,主要是窑炉余热利用,工艺流程图与改造前一致。
1.2 主要设备方案本项目根据企业实际情况,决定选用适合自身规模的设备。
主要新增 9台 11千瓦的抽热风机。
1.3 关键技术和具体措施本项目主要是在原有生产设备(窑炉)上进行技术改造,以达到提高余热回收利用率的目的。
重点要解决的关键技术如下:拟采用余热利用系统窑炉排热是正常存在现象,重点是如何充分利用热排放的余热,针对性地进行技术改造。
余热利用系统根据窑炉的特点,急冷抽热排放是热量最多,窑炉从冷却带抽出冷却热风与窑顶换热风混合,由抽风机集中抽出,为烤房、成型车间提供可控温度系统,改善原来供热装置,从而达到节约供热燃耗。
1.4工程方案1.4.1供电1.负荷等级:三级负荷2.供电来源本项目由广东电网 a 市分公司提供。
3.配电系统电压确定照明系统—— 380/220V4.主要电气设备本项目的主要电气设备为高压配电柜、变压器、低压配电柜、动力 / 照明配电箱等。
1.4.2劳动安全卫生与环保本项目劳动安全卫生工程具体见劳动安全卫生与消防和环境保护章节。
窑炉余热利用方案
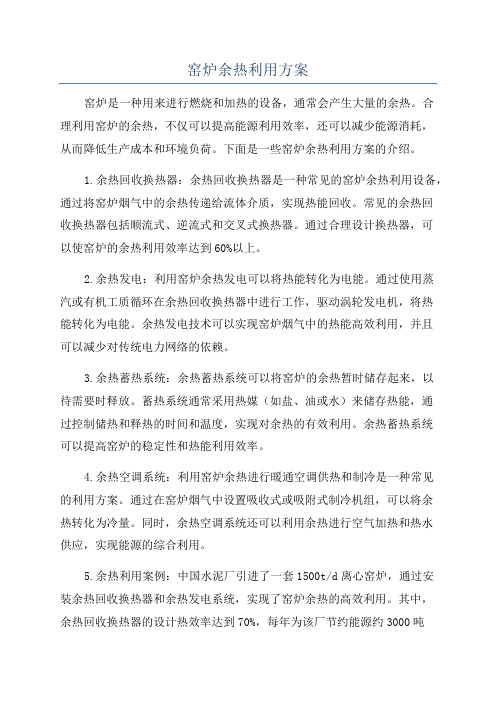
窑炉余热利用方案窑炉是一种用来进行燃烧和加热的设备,通常会产生大量的余热。
合理利用窑炉的余热,不仅可以提高能源利用效率,还可以减少能源消耗,从而降低生产成本和环境负荷。
下面是一些窑炉余热利用方案的介绍。
1.余热回收换热器:余热回收换热器是一种常见的窑炉余热利用设备,通过将窑炉烟气中的余热传递给流体介质,实现热能回收。
常见的余热回收换热器包括顺流式、逆流式和交叉式换热器。
通过合理设计换热器,可以使窑炉的余热利用效率达到60%以上。
2.余热发电:利用窑炉余热发电可以将热能转化为电能。
通过使用蒸汽或有机工质循环在余热回收换热器中进行工作,驱动涡轮发电机,将热能转化为电能。
余热发电技术可以实现窑炉烟气中的热能高效利用,并且可以减少对传统电力网络的依赖。
3.余热蓄热系统:余热蓄热系统可以将窑炉的余热暂时储存起来,以待需要时释放。
蓄热系统通常采用热媒(如盐、油或水)来储存热能,通过控制储热和释热的时间和温度,实现对余热的有效利用。
余热蓄热系统可以提高窑炉的稳定性和热能利用效率。
4.余热空调系统:利用窑炉余热进行暖通空调供热和制冷是一种常见的利用方案。
通过在窑炉烟气中设置吸收式或吸附式制冷机组,可以将余热转化为冷量。
同时,余热空调系统还可以利用余热进行空气加热和热水供应,实现能源的综合利用。
5.余热利用案例:中国水泥厂引进了一套1500t/d离心窑炉,通过安装余热回收换热器和余热发电系统,实现了窑炉余热的高效利用。
其中,余热回收换热器的设计热效率达到70%,每年为该厂节约能源约3000吨标准煤。
同时,余热发电系统每年可发电约500万千瓦时,为企业创造了可观的经济效益。
总之,合理利用窑炉的余热可以提高能源利用效率,减少能源消耗,降低生产成本,减少环境污染。
各种余热利用方案可以根据企业的需求和条件进行选择和组合。
在未来的工业发展过程中,窑炉余热利用将成为能源节约和环境保护的重要举措。
陶瓷企业窑炉烟气的余热利用

陶瓷企业窑炉烟气的余热利用摘要本文介绍了窑炉烟气余热利用的现状,提出了新型高效的窑炉烟气余热利用方式――余热制冷,并对其进行了可行性分析。
关键词陶瓷企业,窑炉烟气,余热制冷1引言陶瓷企业的窑炉所产生的烟气带走的热量是巨大的,占窑炉总热量的25%~35%,一般可从中回收15%,若将这部分余热利用起来,其经济效益相当可观。
但是,由于人们的节能观念不足以及技术水平的落后,致使我国陶瓷窑炉烟气余热的利用率非常低,一般只有2%~3%,而国外的余热利用率一般都在15%左右。
可见,我国陶瓷窑炉烟气的余热利用还有很大的开发空间。
2现有余热利用方式现有余热利用方式主要有以下几种:(1)在换热器中用烟气余热加热助燃空气和煤气;(2)设置预热段,用烟气余热加热炉料;(3)设置余热锅炉,用烟气热量生产蒸汽;(4)加热空气作为烘干坯件的热源;(5)利用烟气余热产生的蒸汽来发电和供暖等。
通过上述传统的操作方式可以将陶瓷烟气余热利用起来,提高能源的利用率。
下面我们以建陶生产基地佛山为例探讨一种新型高效的余热利用方式――余热制冷。
3余热制冷3.1 概况广东佛山是我国最大的陶瓷生产基地。
其中,禅城区辖内拥有一定规模的陶瓷企业110多家,共有工业窑炉700多条。
据资料统计,2003年全区陶瓷行业耗煤量为83688吨,占全区的16.7%。
可见,佛山陶瓷企业耗能量之大,产生热量之多。
但通过窑炉烟气排出去的余热量也是非常巨大的,这就为余热制冷提供了可靠的热源。
佛山处于亚热带,气温较高,每年需要空调工况的月份不少于6个月。
详细数据见表1。
可见,佛山的需冷时间比较长,需冷量也很大。
3.2 吸收式制冷系统简介以高沸点物质作溶剂(吸收剂)、低沸点物质作溶质(制冷剂)组成的二元溶液,其溶质的溶解度与温度有关。
温度较低时,溶解度取代对蒸汽的压缩过程,这样的制冷系统叫做吸收式制冷系统。
吸收式制冷系统主要由吸收器、溶液泵、发生器、冷凝器、节流机构和蒸发器等部件组成,而其中的吸收器、发生器体积较大。
陶瓷窑炉余热利用的探究

陶瓷窑炉余热利用的探究摘要:利用陶瓷窑炉余热进行物料烘干、取暖和洗澡。
关键词:窑炉余热利用烘干取暖中图分类号:tq174.655 文献标识码:a 文章编号:1672-3791(2012)09(b)-0240-01随着我国国民经济持续快速发展,带动了能源消费长期高速增长。
目前我国能源供给已呈现紧张局面,大力推进节能降耗,缓解资源瓶颈制约,实现能源环境和经济社会的可持续发展是我国用能工作的核心。
党的十六届五中全会提出把节约能源作为基本国策,“十一五”规划《纲要》进一步把“十一五”时期单位gdp能耗降低20%左右作为约束性指标,凸显了节能工作的极端重要性和紧迫性。
节能是解决我国能源问题的根本途径,是当前经济工作的一项紧迫性任务。
企业实施节能技术改造,不但能够显著使企业能耗降低,取得良好的节能效益,消化部分外部因素造成的成本压力,也符合企业的长远发展战略需要。
陶瓷企业作为高耗能企业,在节能方面要有重大突破,采用先进的工艺、设备和技术,是节能的关键。
但陶瓷窑炉的余热利用也是节能降耗所必须的。
1 陶瓷窑炉余热利用现状关于窑炉余热利用的文章,现在网上及一些相关书刊都有记载,但很少的利用到生产及生活中去。
很多企业对于余热利用这一块很少去投资,其实在我们生活和生产当中,余热利用不是短期的效益,而应是个长期的规划。
很多企业在余热利用上碰见了问题,往往半途而废,殊不知对于一个企业来说,余热可以为企业节省不少资金。
对于北方的企业来说,还能创造很多效益。
企业采取陶瓷窑炉余热技术改造可提高能源利用效率,也是响应国家节能减排政策的具体措施。
2 陶瓷窑炉余热利用探究陶瓷窑炉的余热来自三个方面:一是烟道排烟的热量;二是烧成后的缓冷区的热量;三是窑炉辊棒下面的热量。
关于余热,我们可以从以下几个方面来探讨研究一番。
2.1 烘干室的利用烘干室对于陶瓷企业来说,是很熟悉的了,这是个企业整体规划问题,实际上,每个决策者都规划的很好,但问题往往出在运行的过程中。
一种瓷砖窑炉余热利用装置

专利名称:一种瓷砖窑炉余热利用装置专利类型:实用新型专利
发明人:任海
申请号:CN202120974089.7
申请日:20210508
公开号:CN215810256U
公开日:
20220211
专利内容由知识产权出版社提供
摘要:本实用新型公开了一种瓷砖窑炉余热利用装置,其技术方案要点是,包括用于冷却瓷砖的冷却区,所述冷却区末端设置有送风管,所述送风管在冷却区内部设置出风口,所述送风管设置有鼓风机,所述冷却区设置排风口,所述排风口相联通与通风管连接,所述通风管有坯体烘干箱,所述烘干箱为壳体设计,所述坯体烘干箱设置有回风管,所述回风管与所述鼓风机连接,所述烘干箱内腔可设置有可盛放坯体的烘干腔。
通过以上设置形成循环利用冷却区的余热进行坯体烘干。
有效地利用了窑炉中冷却区的余热进行烘干坯体,通过鼓风机、送风管、通风管、回风管相连接从而形成一个闭合循环的通风回路,使坯体烘干箱中始终保持在稳定的温度区域,从而对坯体烘干效果更佳。
申请人:萍乡市国微陶瓷有限公司
地址:337000 江西省萍乡市湘东区产业园D区3-161号
国籍:CN
代理机构:南昌科德知识产权代理事务所(普通合伙)
代理人:刘福来
更多信息请下载全文后查看。
- 1、下载文档前请自行甄别文档内容的完整性,平台不提供额外的编辑、内容补充、找答案等附加服务。
- 2、"仅部分预览"的文档,不可在线预览部分如存在完整性等问题,可反馈申请退款(可完整预览的文档不适用该条件!)。
- 3、如文档侵犯您的权益,请联系客服反馈,我们会尽快为您处理(人工客服工作时间:9:00-18:30)。
陶瓷窑炉余热回收利用
摘要
生产陶瓷的一个重要过程是烧成,烧成是在窑炉中进行的。
陶瓷生产的窑炉有连续式的(隧道窑)也有间隙式的(倒焰窑),不管是隧道窑还是倒焰窑,其热效率都比较低。
效率低的原因除了燃烧损失、散热损失等原因外,重要的一点是排烟损失。
烧成隧道窑废气带走的热量损失约占总热量的20%~40%,而倒焰窑废气带走的热量约占燃料消耗量的30%~50%。
因之回收窑尾废气的
热量加以利用是提高窑炉效率的关
键。
国内隧道窑排烟温度一般在
200~300℃,也有高达400℃,个
别倒焰窑的排烟温度可高达560℃。
一方面窑炉排烟带走大量余热,另
一方面为了干燥坯件,一些工厂又
另外建造窑炉或锅炉产生热风和蒸
汽以满足烘干坯件的要求。
采用热管换热器来回收烟气中的余热加热空气作为烘干坯件的热源,可以取得较好的节能效果。
余热回收利用方式
一、隧道窑烟道余热利用
隧道窑余热回收主要用以加热空气作为烘干坯件的热源,也可作为助燃空气以提高窑炉本身的热效率,两者的选择可依据各工厂具体情况而定。
其回收流程如图所示。
下表中列出了四个工业应用实例,其中三个例子为用窑尾烟气余热加热空气作为烘房干燥热源以代替原来的锅炉蒸汽加热。
第四个例子为用余热加热热水供生活用,其运行参数如表所示。
与原来用蒸汽加热空气相比,不仅省去了一台蒸汽锅炉,而且因为热风量有多余,干燥后含湿的热风可及时排出,因而可以提高干燥速度并改善产品质量。
从运行情况看,例Ⅰ、例Ⅱ的烟气出口温度偏低,一般希望燃烧重油的热管换热器烟气出口温度不低于150℃为宜。
二、电瓷厂隧道窑冷却带余热利用
将电瓷厂隧道窑冷却带400℃~450℃的废气抽出通过热管换热器换热,烟气温度降至300℃,再返回窑炉中烧成带作为气氛膜风使用。
被加热的新鲜空气送入烘房,干燥电瓷坯件。
热管换热器的流程如图所示。
热管空气预热品的参数见下表。
三、倒焰窑烟道气余热利用
某厂倒焰窑排烟温度为564℃,实测该窑炉热效率仅为23%,由于坯件入窑前需要预热烘干,因之需再建一个烘干窑,以煤作为燃料,燃烧的烟气作为烘干热源。
根据计算,如将560℃烟气降到160℃排空,将新鲜空气加热到60~120℃,其热量足够烘干坯件所用。
余热回收流程如图所示。
热管空气预热器参数见下表。