基于塑性损伤理论的金属裂纹扩展模拟
基于损伤累积的合金钢静拉伸裂纹扩展数值模拟

航空航天科学技术科技创新导报 Science and Technology Innovation Herald17航空航天以及工程机械领域广泛使用金属合金制件,利用数值模拟研究金属构件在受载时的极限强度及其延性断裂机理与过程不仅具有学术研究价值,且对于构型优化设计、减少物理试验、降低技术成本与风险等均具有重要的工程应用价值。
断裂问题是一个几何及材料非线性问题[1],裂纹从萌生到扩展可以被认为是材料从出现屈服开始就出现损伤,损伤继而不断累积的一个过程。
本文假设合金钢材料损伤累积过程是线性的,即损伤的累积与塑性应变之间为线性相关,那么相应的损伤累积方程为:≥式中A为损伤累积量,当大于阈值c时,单元材料即失效。
本文基于以上损伤累积的理念基础,对一块中心带圆孔的合金钢材料完成了考虑损伤累积以及不考虑损伤累积的静拉伸载荷下断裂过程数值模拟。
1 前处理[2]1.1 几何模型合金钢板尺寸为200×60×5(m m ),中间圆孔直径=2.5m m,钢板不带初始缺陷。
1.2 边界约束及加载方式本例中采用位移加载方式。
对板的一端面施加固支约束,在板的另一端面施加平行于合金钢板长边方向的位移载荷。
1.3 材料参数本文所选用合金钢为典型合金钢,弹性模量为210GPa,泊松比为0.3,初始屈服应力为480M Pa。
1.4 有限元网格网格划分钢板边缘向孔中心单元从大到小,孔边单元DOI:10.16660/ k i.1674-098X.2017.20.017基于损伤累积的合金钢静拉伸裂纹扩展数值模拟江金锋(上海飞机设计研究院 上海 200436)摘 要:为了研究合金钢材料在静拉伸载荷下裂纹扩展特点,本文基于损伤累积理论,利用有限元软件中的显示动力学求解器,对不带初始缺陷的中心带圆孔的合金钢矩形板进行了静拉伸载荷下裂纹萌生及扩展数值计算,模拟出了裂纹的出现及扩展过程。
关键词:损伤累积 合金钢 显示动力学求解器 二次开发子程序中图分类号:V25文献标识码:A文章编号:1674-098X(2017)07(b)-0017-02图1 合金钢板应力云图(不带损伤)图2 合金钢板应力云图(带损伤)科技创新导报 Science and Technology Innovation Herald18航空航天科学技术尺寸为0.3m m,钢厚度方向整个模型设定统一的单元尺寸0.3m m。
金属塑性成形过程韧性断裂的准则及其数值模拟
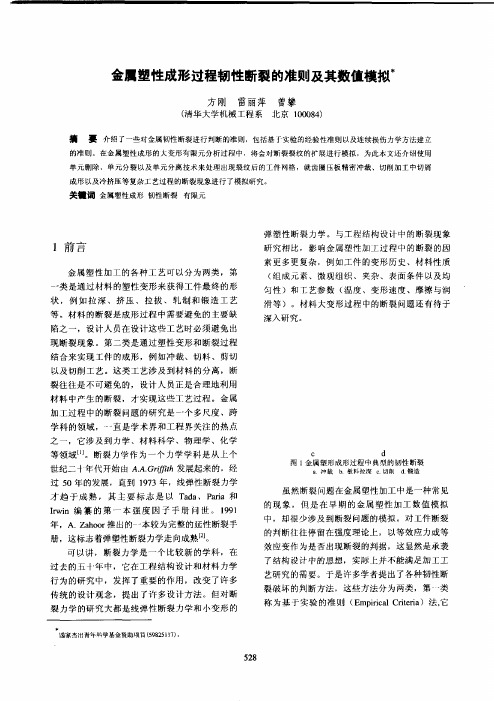
R e r y在1 9 es 9 年提出了三向应力作 i 和Tc l 6 c a ]
用下材料的韧性断裂准则为:
的应用。最后介绍作者对几个典型工艺模拟的结
果。
1 .
2韧性断裂准则
金属在加工过程中发生的断裂大多是韧性断 裂,很少发生脆性断裂。一般认为,金属中的韧
Kc nv 1 8 a a 在 9 年首先提出的另一种分析方 ho 5
法。这种研究方法主要是从细观 ( e s l m s ce oa) 的角度进行研究,对空洞的萌生和扩展角度进
行预测,建立空洞萌生准则。因为韧性断裂的
调整,局部调整还包括单元删除 ( e tn D l o)、 e i
50 3
截
国家杰出青年科学基金资助项目( 851) 5 21 . 9 7
58 2
主要是通过标准的常规实验来获取材料的实验数 据,然后用于对材料成形过程中的韧性断裂的判 断上,它还分二种,即应力、应变和应变能准 则,这类准则的代表是 C cr t a a 准则。 ok fLt m o- h 从所分析的尺度和方法上讲,它属于宏观断裂力 学的范畴。这种方法的缺陷是简单的力学实验条
申
虽然断裂问题在金属塑性加工中是一种常见 的现象,但是在早期的金属塑性加工数值模拟 中,却很少涉及到断裂问题的模拟。对工件断裂 的判断往往停留在强度理论上,以等效应力或等 效应变作为是否出现断裂的判据,这显然是承袭 了结构设计中的思想,实际上并不能满足加工工 艺研究的需要。于是许多学者提出了各种韧性断 裂破坏的判断方法,这些方法分为两类,第 类 称为基于实验的准则 (m i a Cir ) 它 E pi l ea 法, r c r i t
世纪二十年代开始由A .r h .G咖t发展起来的, A 经
金属材料疲劳裂纹扩展研究综述

内容摘要
海洋钢结构在海洋环境中承受着复杂的力学环境和疲劳载荷。疲劳裂纹扩展 是导致其结构破坏的主要原因之一,因此,对海洋钢结构的疲劳裂纹扩展进行准 确预报具有重要意义。本次演示主要探讨一种单一扩展率曲线模型在海洋钢结构 疲劳裂纹扩展预报中的应用。
一、单一扩展率曲线模型
一、单一扩展率曲线模型
单一扩展率曲线模型是一种基于应力强度因子和应力循环次数的关系来预测 裂纹扩展的方法。它假定裂纹扩展速率仅与应力强度因子幅值和应力循环次数有 关,而与应力的其它参数如平均应力、应力比等无关。这种模型的优点是能够用 一条曲线来描述裂纹扩展的全过程,简洁直观。
4、金属材料疲劳裂纹扩展的应用领域和未来研究方向
未来研究方向主要包括以下几个方面:首先是深入研究金属材料疲劳裂纹扩 展的机理和影响因素,以进一步揭示其本质和规律;其次是发展更加准确、高效 的研究方法和技术手段,以更好地模拟和分析材料的疲劳裂纹扩展行为;第三是 加强针对不同约束条件下的裂纹扩展模型和实验方法的研究,以更好地应用于实 际工程中;最后是拓展金属材料疲劳裂纹扩展的应用领域,如智能材料、生物医 用材料等领域,以发挥其更加广泛的作用。
在几何约束条件下,裂纹扩展模型主要考虑材料的几何特征、裂纹形状和扩 展方向等因素。在物理约束条件下,需要考虑材料的物理性质、力学性能和化学 成分等因素对裂纹扩展的影响。在工程约束条件下,需要考虑实际工程中材料的 服役条件、载荷形式和工作环境等因素对裂纹扩展的影响。
3、基于不同约束条件下的裂纹扩展模型和实验方法
主体部分
1、金属材料疲劳裂纹扩展的机 理和影响因素
1、金属材料疲劳裂纹扩展的机理和影响因素
金属材料疲劳裂纹扩展的机理主要包括应力腐蚀、疲劳裂纹扩展和断裂力学 等。应力腐蚀主要指在应力和腐蚀介质共同作用下,材料内部产生微裂纹并逐渐 扩展的现象。疲劳裂纹扩展则是在循环载荷作用下,材料内部初始裂纹发生疲劳 扩展的过程。断裂力学则是从材料的力学性能出发,研究裂纹扩展的规律和预测 材料的断裂行为。
裂纹扩展的扩展有限元(xfem)模拟实例详解
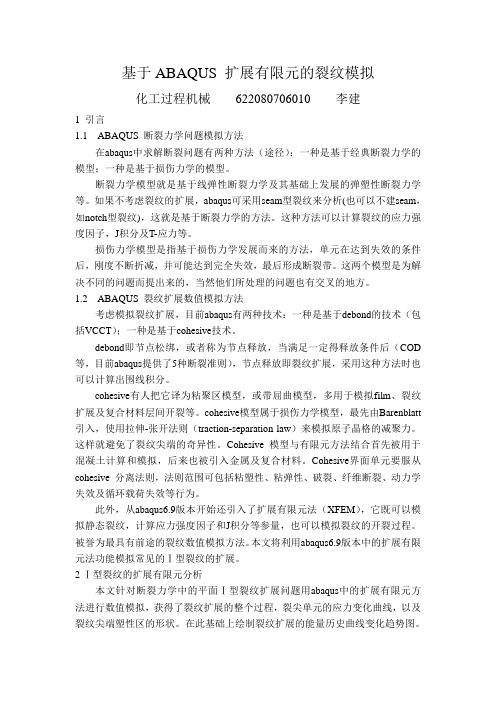
基于ABAQUS 扩展有限元的裂纹模拟化工过程机械622080706010 李建1 引言1.1 ABAQUS 断裂力学问题模拟方法在abaqus中求解断裂问题有两种方法(途径):一种是基于经典断裂力学的模型;一种是基于损伤力学的模型。
断裂力学模型就是基于线弹性断裂力学及其基础上发展的弹塑性断裂力学等。
如果不考虑裂纹的扩展,abaqus可采用seam型裂纹来分析(也可以不建seam,如notch型裂纹),这就是基于断裂力学的方法。
这种方法可以计算裂纹的应力强度因子,J积分及T-应力等。
损伤力学模型是指基于损伤力学发展而来的方法,单元在达到失效的条件后,刚度不断折减,并可能达到完全失效,最后形成断裂带。
这两个模型是为解决不同的问题而提出来的,当然他们所处理的问题也有交叉的地方。
1.2 ABAQUS 裂纹扩展数值模拟方法考虑模拟裂纹扩展,目前abaqus有两种技术:一种是基于debond的技术(包括VCCT);一种是基于cohesive技术。
debond即节点松绑,或者称为节点释放,当满足一定得释放条件后(COD 等,目前abaqus提供了5种断裂准则),节点释放即裂纹扩展,采用这种方法时也可以计算出围线积分。
cohesive有人把它译为粘聚区模型,或带屈曲模型,多用于模拟film、裂纹扩展及复合材料层间开裂等。
cohesive模型属于损伤力学模型,最先由Barenblatt 引入,使用拉伸-张开法则(traction-separation law)来模拟原子晶格的减聚力。
这样就避免了裂纹尖端的奇异性。
Cohesive 模型与有限元方法结合首先被用于混凝土计算和模拟,后来也被引入金属及复合材料。
Cohesive界面单元要服从cohesive 分离法则,法则范围可包括粘塑性、粘弹性、破裂、纤维断裂、动力学失效及循环载荷失效等行为。
此外,从abaqus6.9版本开始还引入了扩展有限元法(XFEM),它既可以模拟静态裂纹,计算应力强度因子和J积分等参量,也可以模拟裂纹的开裂过程。
基于累积塑性损伤的Q345钢疲劳裂纹扩展的过载效应研究
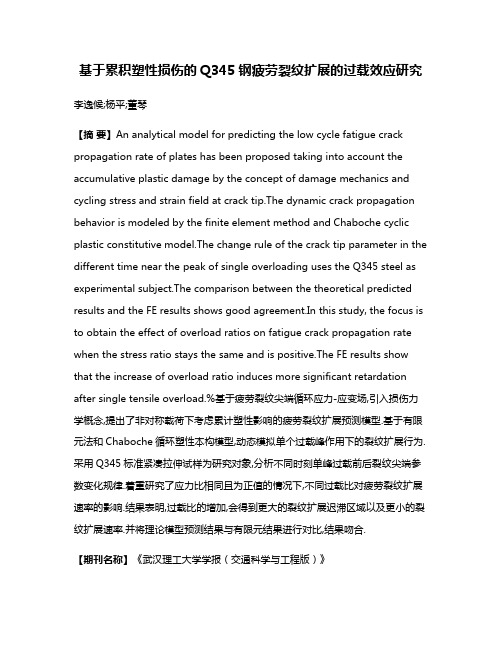
基于累积塑性损伤的Q345钢疲劳裂纹扩展的过载效应研究李逸候;杨平;董琴【摘要】An analytical model for predicting the low cycle fatigue crack propagation rate of plates has been proposed taking into account the accumulative plastic damage by the concept of damage mechanics and cycling stress and strain field at crack tip.The dynamic crack propagation behavior is modeled by the finite element method and Chaboche cyclic plastic constitutive model.The change rule of the crack tip parameter in the different time near the peak of single overloading uses the Q345 steel as experimental subject.The comparison between the theoretical predicted results and the FE results shows good agreement.In this study, the focus is to obtain the effect of overload ratios on fatigue crack propagation rate when the stress ratio stays the same and is positive.The FE results show that the increase of overload ratio induces more significant retardation after single tensile overload.%基于疲劳裂纹尖端循环应力-应变场,引入损伤力学概念,提出了非对称载荷下考虑累计塑性影响的疲劳裂纹扩展预测模型.基于有限元法和Chaboche循环塑性本构模型,动态模拟单个过载峰作用下的裂纹扩展行为.采用Q345标准紧凑拉伸试样为研究对象,分析不同时刻单峰过载前后裂纹尖端参数变化规律.着重研究了应力比相同且为正值的情况下,不同过载比对疲劳裂纹扩展速率的影响.结果表明,过载比的增加,会得到更大的裂纹扩展迟滞区域以及更小的裂纹扩展速率.并将理论模型预测结果与有限元结果进行对比,结果吻合.【期刊名称】《武汉理工大学学报(交通科学与工程版)》【年(卷),期】2016(040)006【总页数】5页(P1009-1013)【关键词】损伤力学;单峰拉伸过载;裂纹扩展速率预测;有限元分析【作者】李逸候;杨平;董琴【作者单位】武汉理工大学交通学院武汉 430063;武汉理工大学交通学院武汉430063;高性能船舶技术教育部重点实验室武汉 430063;武汉理工大学交通学院武汉 430063【正文语种】中文【中图分类】U661.41疲劳是指材料在应力或应变反复作用下,局部位置产生的永久性损伤,并在一定循环次数后形成裂纹或使裂纹进一步扩展直到完全断裂的现象.在机械、土木和航天等领域,由于工程构件长期受周期性载荷的作用,疲劳所带来的影响不可忽视.自18世纪30年代起,疲劳问题的各项研究陆续展开,以提高安全性以及使用寿命为主要目的.目前,人们通过对恒幅疲劳载荷下裂纹扩展行为的研究,较好地揭示了裂纹扩展的规律.但在工程实际中,构件往往受到变幅载荷的作用,常规的Paris公式已无法正确描述其裂纹扩展行为,其裂纹扩展规律仍然是一个尚未解决的难题[1].变幅载荷下的疲劳裂纹扩展这一课题已经被研究了很长一段时间,Chen等[2]在上世纪初取得了重大突破.为解决变幅载荷下的损伤累积问题,他们提出了线性损伤假设.然而,近几十年的研究表明,载荷之间还存在很强的交互作用.载荷幅值的变化引起材料疲劳性能的变化,从而加载序列对疲劳寿命也存在一定影响.近几十年间,国内外学者在过载裂纹扩展研究方面有了不小的突破.Sander等[3]采用铝合金,进行了紧凑拉伸试样的高低载试验,总结出裂纹扩展迟滞循环数N、应力强度因子幅值和过载比之间的影响关系.Silva等[4-5]对低碳钢CK45、纯铝AL7175和铁合金Ti6A14V 3种金属材料进行了拉伸过载后疲劳裂纹扩展试验,比较了3种材料过载后的裂纹扩展迟滞,研究的大体思路包括:(1)通过过载试验和有限元模拟,研究过载引起的裂纹扩展行为的作用机理;(2)开展过载作用下的疲劳裂纹扩展试验,根据不同参数下的实验结果,总结过载对疲劳裂纹扩展行为的影响机理;(3)建立预测疲劳裂纹扩展速率和疲劳寿命的数学模型.以往对于变幅载荷作用下的疲劳裂纹扩展行为研究,以定性研究为主,并未展开较为完善的定量分析.文中针对Q345钢标准紧凑拉伸(compact tension,CT)试样,对恒幅载荷加载条件下的单峰拉伸过载的疲劳裂纹扩展机理进行研究.基于裂尖应力应变场分析,引入损伤力学概念,提出了非对称载荷下考虑累计塑性影响的疲劳裂纹扩展速率预测模型.并基于临界距离理论,考虑到塑性耗散能密度累积过程,运用ABAQUS及MATLAB软件对Q345钢的标准CT试样进行数值仿真,从而预测其疲劳裂纹扩展速率.比较发现理论预测结果与有限元结果相似,并用有限元方法探究了应力比为正且保持不变时,不同过载比对裂纹扩展速率的影响.1.1 裂纹尖端附近应力应变场描述试件在单个拉伸过载的循环载荷作用下,裂纹尖端位置处于应力集中状态,其产生的高应力促使材料发生塑性屈服.裂尖附近塑性区又可分为循环塑性区rc max和单调塑性区rm max,其大小分别为[6]式中为循环屈服强度;rc max为裂尖循环塑性区尺寸;rm max为裂尖单调塑性区尺寸;n′为循环硬化指数;κ为循环硬化系数,对于平面应力构件,κ=1,平面应变则有κ=1/(1-2μ).由于存在单个拉伸过载载荷,因此在过载所在的载荷周期,Kmax和ΔK需要取其最大值.由于裂纹尖端处于不同的应力区域,因此其应力场存在弹性、塑性等不同形式.根据Schwable所提出的弹塑性裂尖应力-应变HRR场[7].平面应力状态下裂纹尖端的线弹性应力场公式为式中:ΔK为应力强度因子幅值;E为弹性模量;μ为泊松比;r为扩展方向上材料点距裂尖的距离;r0为裂尖钝化半径.1.2 低周疲劳临界损伤构件在实际复议过程中会承受非对称载荷的作用,可能会产生塑性的循环累积现象.假设低周疲劳的总损伤为低周疲劳损伤Df和累积塑性损伤Dr之和利用线性累积损伤法则,得式中:Nf为由低周疲劳控制的失效循环周次;Nr为由累积塑性应变控制的失效循环周次.1) 采用 Manson-Coffin模型来描述构件单轴低周疲劳行为,得到其寿命关系式中为疲劳强度系数;为疲劳延性系数;b为疲劳强度指数;c为疲劳延性指数;Nf为疲劳寿命;εe为疲劳过程区域内的平均循环弹性应变;εp为疲劳过程区域内的平均循环塑性应变.因为塑性区弹性变形分量很小,故可略去弹性项,得到2) 采用Xia[8]提出的模型计算由累积塑性应变控制的失效循环周次.则式中:κr,β为相关的材料常数为累积塑性应变稳定发展时的累积应变率.因此考虑累积塑性影响的疲劳损伤参量为1.3 疲劳裂纹扩展预测将裂纹扩展的名义扩展尺寸,取裂纹扩展方向上的裂尖塑性区大小.整个疲劳扩展区内的平均单位循环损伤由此可得裂纹每次扩展的速率为式(11)即为文中裂纹扩展速率预测模型.根据此预测模型,文中将对Q345钢的标准CT试样进行低周疲劳裂纹扩展速率预测,并结合有限元仿真结果进行比较. 2.1 有限元模型通过有限元软件ABAQUS软件,建立Q345钢CT标准试样模型,采用四节点平面应力单元(CPS4)进行网格划分,见图1.a取19.5 mm,b取6.5 mm,W取15.6 mm,L取32.5 mm.材料参数见表1.本构关系采取Chaboche所提出的模型,参数见表2.2.2 有限元建模方法考虑到裂尖附近区域处于应力集中状态,应力场存在奇异性,其应力-应变梯度变化较大,因此,必须对裂尖附近区域网格进行局部加密处理,见图2.通过编写的python小程序对其进行划分.细化网格尺寸采用文献推荐的边长为55 μm的正方形单元.除此之外,在interaction-special中定义裂纹尖端处奇异性,在crack中定义完裂纹面、裂纹尖端以及裂纹扩展速度后,在singularity中选择midsidenodeparameter中输入0.25奇异单元来模拟其尖端奇异性,通过将四边形8节点单元任意2边的中点向2边交点移动1/4的距离,得到1/4奇异单元.在裂纹尖端布置此1/4奇异单元.采用定义主从接触表面的方式来分析裂纹面的接触问题.将CT试样分为上下2部分,将上下2部分的对称轴定义为X轴,将下半部分在X轴上的面定义为主面,上半部分同样在X轴上面定义为从属面.计算前,设置主从面上有接触的所有节点都处于“粘结”(bonded)状态.在有限元运算过程中,通过对裂尖处主从面粘结几点的依次“脱粘”(debond)来模拟新裂尖的产生,及裂纹动态扩展过程. Debond采用ABAQUS自带的crack length准则,对裂纹长度与加载时间的关系进行人为的规定,从而模拟裂纹扩展的过程以及得到比较准确的应力应变场.其具体操作如下.在裂纹未起裂时,施加5个恒幅加载循环[9],再释放裂尖前端第1个节点的y方向位移约束,裂纹向前扩展1个单元的距离;新的裂尖产生后,系统自动更新接触对,再同样施加5个恒幅循环加载,进行下1个节点y方向位移约束的释放.照此规律完成整个裂纹扩展的过程.每个节点释放前所加的恒幅载荷作用在于得到裂纹尖端稳定的应力应变场,与裂纹扩展速率无关.2.3 裂纹尖端的应力场分布模型载荷采用循环等幅载荷条件下的单峰拉伸过载,见图3.图中d点为单峰过载峰值点,其他为循环等幅加载阶段.图4为当节点释放到过载时刻,在裂纹扩展方向上距新的裂纹尖端r距离的各点的应力分布值,图中6条曲线的时刻取值参考图3.由图4可知,a点为常幅载荷峰值时刻,裂尖出于拉伸屈服状态;d点为拉伸过载载荷峰值时刻,其应力水平较a 处有明显上升且曲线走势相似.b和f分别为一般情况下的压载峰值和经历过单次拉伸过载的压载峰值时刻,在裂尖位置,f时刻压应力略小于b时刻;逐渐远离裂尖,b点时刻压应力逐渐减小且在小范围内转变为拉应力,而f点时刻压应力较平稳的减小,其趋势与外载荷由过载峰值卸载到0时刻的趋势相近.a和d、b和f 2组曲线在裂纹尖端前局部应力分布的明显差异表明单次的拉伸过载对裂纹尖端前局部应力分布有很大的影响.2.4 裂纹扩展速率近几十年来,临界距离理论被广泛运用于预测缺口零件的疲劳强度[10].基于临界距离理论,借助软件MATLAB软件对ABAQUS数据进行后处理[11].首先运用有限元软件ABAQUS模拟裂纹扩展过程,得出每个裂尖节点前方个单元积分点1个循环下的塑性耗散能密度增量[12],再将这些数据导入MATLAB软件编制好的后处理程序.此程序主要模拟其塑性耗散能累积过程,并计算出不同时刻裂纹扩展速率.其核心思想为:裂尖前方一定距离处(结合临界距离理论),单元积分点的塑性耗散能密度累积到一临界值时,当前裂纹尖端单元发生破坏且向前扩展1个单元.瞬时裂纹扩展速率即为单个有限元单元长度除以塑性耗散能密度累积所需的循环数.根据有限元方法以及理论方法分别绘制Q345钢标准CT试样在循环拉伸载荷条件下单个拉伸过载载荷作用下的裂纹扩展速率曲线.其中常幅载荷峰为7.2 kN,应力比R取0.1,见图5~6.由图5~6可知,有限元结果与理论结果曲线基本重合,分散性较小,说明文中有限元模型以及理论模型具有一定的可行性.下面利用有限元方法,对相同应力比下,不同过载比的疲劳裂纹扩展速率进行预测,结果见图7.由图7可知,引入单个拉伸过载后,整个裂纹扩展过程受到了明显的影响.在施加过载后,裂纹扩展速率出现了快速的减小,在降至最低点后又以较快速度回升到正常水平.整个过程可以划分为几个阶段:单个拉伸过载前的稳定扩展阶段、过载造成的迟滞扩展阶段和过载后的稳定扩展阶段.通过对图7的3条曲线的比较可知,更大的过载比会形成更大的迟滞扩展区域和更小的迟滞扩展速率.1) 对比理论预测结果与有限元预测结果吻合度良好,表明考虑累积塑性影响的低周疲劳裂纹扩展速率预测方法是可行的.2) 过载对裂纹尖端位置附近局部区域应力场有很大影响,此影响会随着恒幅载荷的施加逐渐减弱,直至恢复到过载施加之前的应力水平.3) 当应力比值为正且保持不变时,对同一试件,更大的过载比会形成更明显的裂纹扩展速率迟滞现象和更小的迟滞扩展速率.【相关文献】[1]PARIS P C, ERDOGAN F. A critical analysis of crack propagation laws[J]. Journal of Basic Engineering,1963,85(4):528-533.[2]CHEN N Z, WANG G,SOARES C G. Palmgren-miner’s rule and fracture mechanics-based inspection planning[J]. Engineering Fracture Mechanics,2011,78(18):3166-3182. [3]SANDER M, RICHARD H A. Lifetime predictions for real loading situations-concepts and experimental results of fatigue crack growth[J]. International Journal ofFatigue,2003,25(9):999-1005.[4]SILVA F S. Fatigue crack propagation after overloading and underloading at negative stress ratios[J]. International Journal of Fatigue,2007,29(9):1757-1771.[5]丁振宇.过载作用下疲劳裂纹扩展行为的内在机理研究[D].杭州:浙江工业大学,2013.[6]CASTRO J T P, MEGGIOLARO M A, MIRANDA A C O. Singular and non-singular approaches for predicting fatigue crack growth behavior[J]. International Journal of Fatigue,2005,27:1366-1388.[7]SCHWABLE K H. Comparison of several fatigue crack propagation laws with experimental results[J]. Engineering Fracture Mechanics,1974,6(2):325-341.[8]XIA Z, KUJAWSKI D, ELLYIN F. Effect of mean stress and ratcheting strain on fatigue life of steel[J]. International Journal of Fatigue,1996,18(5):335-341.[9]ZHENG H, CUI X,SU C C, et al. Numerical modeling of fatigue crack propagation based on the theory of critical distances[J]. Engineering Fracture Mechanics,2013,114:151-165.[10]TAYLOR D. The theory of critical distances[J]. Engineering FractureMechanics,2008,75:1696-1705.[11]郑鑫.铸铝合金的高低周复合疲劳裂纹扩展和寿命研究[D].南京:南京航天航空大学,2012.[12]SIH G C, MOYER E T. Path dependent nature of fatigue crack growth[J]. Engineering Fracture Mechanics,1983,17(3):269-280.。
基于弹塑性力学的疲劳裂纹扩展速率的研究
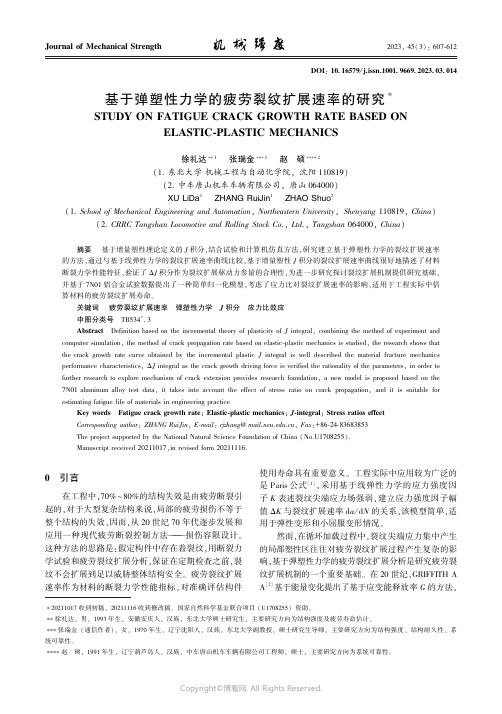
∫ fdA
(4)
D
型,如 基 于 弹 塑 性 应 力 场 的 CJP ( Christopher James
式中,D 为围道 Γ 内不包括裂纹尖端区域的围道;Φ
裂演化机制的循环内聚力模型( Cyclic Cohesive Zone
的转置;S 为第一皮奥拉⁃柯克霍夫应力;n 为围道 Γ
Patterson)模型[5] ,考虑裂纹尖端塑性区影响并基于断
(6)
为基于增
对比式( 5) 和式 ( 6) 可以看出,基于塑性变形理
足 3 个条件:①不能卸载只适用于全量理论;②仅应用
论,应用总应变能密度 Φ ( 塑性加弹性) ,而基于增量
R
实际变形过程中,塑性变形发生后不可逆,只有弹性部
于小 变 形 理 论; ③ 不 存 在 体 积 力。 因 此, RICE J
数,获得基于线弹性力学的 Paris 公式描述裂纹稳定扩
展阶段的关系曲线,表达式为
da / dN = C( ΔK) m
(7)
式中,a 为裂纹长度;N 为应力循环次数;C 和 m 为材
料常数。
对于 M ( T) 试 样, 其 应 力 强 度 因 子 ΔK 的 表 达
式为
6α1 / 2
ΔP é
ùú
ê
F( α) (8)
Journal of Mechanical Strength
2023, 45(3) : 607⁃612
DOI: 10 16579 / j.issn.1001 9669 2023 03 014
基于弹塑性力学的疲劳裂纹扩展速率的研究 ∗
STUDY ON FATIGUE CRACK GROWTH RATE BASED ON
Manuscript received 20211017,in revised form 20211116.
一种基于累积损伤理论和裂纹尖端弹塑性应力场的裂纹扩展预测方法
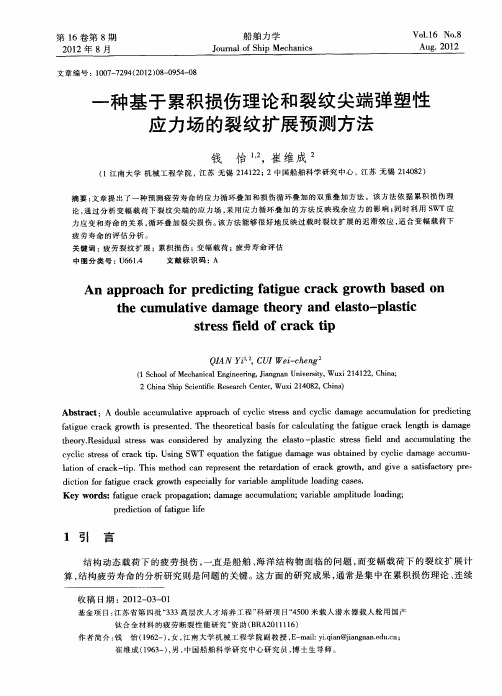
式 中 : 为 材 料 的屈 服 强 度 , 循 环 应 变 硬 化 指 数 。对 于 平 面 应 力 构 件 , = ; 面 应 变 则 有 K s n为 KI平 :
l
。
由于 裂纹 尖端 材料 处 于不 同的 应力 区域 , 以表达 应力 场 的 函数应 该相 应 分为 弹性 、 性等 不 同 所 塑 的形式 。通 常 主要 有两 种方 法描 述裂 尖 附近 应力 场 , 类是 基于 线 弹性 断裂力 学 的 Wet g ad1 一 s rar[ e 6 应力
应 力 强度 因子 的计 算 方法 ,建 立 了 d 』— K关 系 ,从 而 得 到疲劳 裂 纹 的扩展 寿命 。K jw k 在 dv A 7 ua s i
20 0 5年 的文 章 中【 出类 似 的逐单 元 计算 损伤 的方 法 , 4 ] 提 他通 过判 断应力 应 变 的弹塑 性 , 用 了描 述 o、 采 r 关 系 的 四种不 同组合 , 出裂 纹 扩展 率 的计 算 方法 。参 考 C s o和 G ik 给 at r l a扩展 单元 的思路 , n 本文 提 出 了通 过 分析裂 纹 尖端 附近 应力 应变 场 , 直接计 算 裂纹 扩展 规律 的新 方法 。
一
种 基 于 累积 损伤 理 论 和裂 纹 尖 端 弹 塑性 应 力场 的裂 纹扩 展 预 测 方 法
钱 怡 ,崔 维 成
( 1江 南 大 学 机 械 工程 学 院 ,江苏 无 锡 24 2 ; 中 国船 舶 科 学研 究 中心 ,江苏 无 锡 2 4 8 ) 1 12 2 10 2
摘 要 : 章 提 出 了一 种 预 测疲 劳 寿命 的应 力 循 环 叠加 和损 伤 循 环 叠 加 的 双重 叠 加 方 法 。该 方 法 依 据 累 积 损 伤 理 文
裂尖塑性区方向应变能裂纹扩展准则及数值模拟

应力条件下的塑性区要小 ,因而平面应变远较平面应力容易发生脆断[ 4 1 。应变能密度表 着材料构件受力 变形 过程 中贮存 的能 量 。塑性 区 内及 其方 向的应 变能在 一定 程度 上反 映 了材料 的抗断裂能力 。基于 这种情 况和想法并结合屈服条件进行研究 , 本文在应用断裂理论 和塑性力学理论对裂纹顶端分析的基础上 ,提出 了 I— I一Ⅲ复 合型 裂纹塑 性 区内方 向应 变能 的概念 ,并 建立 了基 于此 概念 琏础上 的裂纹 扩展 准则 。 I
动 态跟踪 。该方 法具有修 改 范 围小 ,编程 方便 !可操 作 性 强等特 点。文 中以单边 尖锐 缺 口 试样 为算例 进行 了数值模 拟 ,计算 结果表 明本 文的方 法是 合理 有 效的。
中 图分类 号 :0 4 . 2 21 文献标 志码 :A
0 引 言
在过去 几 十年里 ,断裂力 学处理 纯 I 、I 型或 I 型 裂纹 问题 取得 了巨大 的成功 。然 而 由于裂纹 的方 型 I I I
文 童 编 号 :1 7 -2 22 1)10 0—0 6 40 6(0 10 —101
裂 尖塑性 区方 向应 变 能 裂纹
扩展 准则 及 数 值 模 拟
陈泽 宇
( 广州 铁路 职业技 术学 院 机 电工 程系 ,广 东 广 州 50 3 140)
关 键 词 :端 塑性 区 内方 向应 变能 ;裂 纹扩展 准则 ;数 值 流 形方 法
: —
( o s c一 i s n
:
一
∞ s co s
旦
一 - i旦 -I s I n I
:
,
一
图1 裂 纹顶端处的应 力
式 中 ,KI 、Ku m 别 为 I 、 I型 、Ⅲ 型裂 纹 的应 力 强度 因子 ;v 、K 分 型 I 为材 料 的泊松 比 ,, . 为点 到裂纹 顶 端 的距 离 ; 0为其 与 x轴 的夹 角 ( 图 1 。当 r 如 ) 0时 , 当很 接近 裂纹 顶端 时 , _ ∞, I+ (产x 即 + r_∞,f 『 ,
基于损伤塑性理论的隧道衬砌结构开裂破坏的数值分析
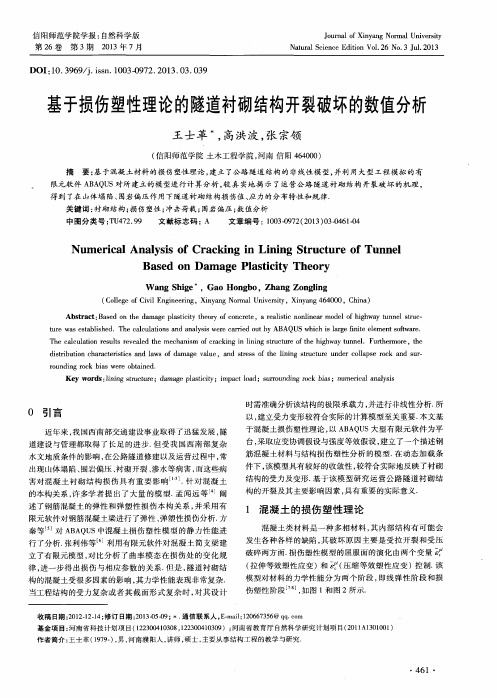
W a ng S hi g e ,Ga o Ho ng bo,Zh a ng Zo ng l i n g
( C o l l e g e o f C i v i l E n g i n e e r i n g , X i n y a n g N o r m a l U n i v e r s i t y , X i n y a n g 4 6 4 0 0 0, C h i n a )
以, 建 立受力变形较符合实际 的计算模 型至关重 要. 本文基 于混凝土损伤 塑性 理论 , 以 AB A Q U S大 型有限元软 件为平
台, 采 取应变协调假设与强度等效假设 , 建立 了一个描述钢
DO I : 1 0 . 3 9 6 9 / j . i s s n . 1 0 0 3 - 0 9 7 2 . 2 0 1 3 . 0 3 . 0 3 9
基于损伤塑性理论的隧道衬砌结构开裂破坏的数值分析
王 士 革 , 高洪波 , 张 宗领
( 信 阳师范学院 土木工程学 院 , 河南 信 阳 4 6 4 0 0 0 )
信 阳师范学院学报 : 自然科学版 第2 6卷 第 3期 2 0 1 3年 7月
J o u r n a l o f Xi n y a n g No r ma l U n i v e r s i t y N a t u r a l S c i e n c e E d i t i o n Vo 1 . 2 6 No . 3 J u 1 . 2 0 1 3
Th e c a l c u l a t i o n r e s u l t s r e v e le a d t h e me c h a n i s m o f c r a c k i n g i n l i n i n g s t r u c t ur e o f t he hi g hwa y t un n e 1 . Fur t h e r mo r e,t h e
基于塑性损伤理论的延性金属裂纹扩展模拟
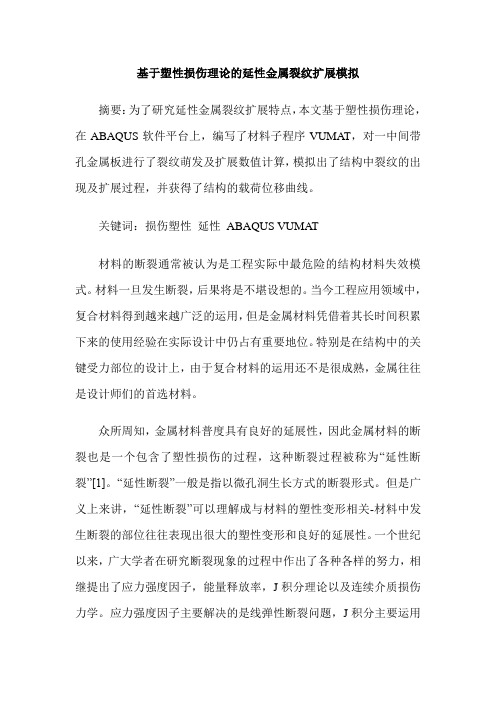
基于塑性损伤理论的延性金属裂纹扩展模拟摘要:为了研究延性金属裂纹扩展特点,本文基于塑性损伤理论,在ABAQUS软件平台上,编写了材料子程序VUMAT,对一中间带孔金属板进行了裂纹萌发及扩展数值计算,模拟出了结构中裂纹的出现及扩展过程,并获得了结构的载荷位移曲线。
关键词:损伤塑性延性ABAQUS VUMAT材料的断裂通常被认为是工程实际中最危险的结构材料失效模式。
材料一旦发生断裂,后果将是不堪设想的。
当今工程应用领域中,复合材料得到越来越广泛的运用,但是金属材料凭借着其长时间积累下来的使用经验在实际设计中仍占有重要地位。
特别是在结构中的关键受力部位的设计上,由于复合材料的运用还不是很成熟,金属往往是设计师们的首选材料。
众所周知,金属材料普度具有良好的延展性,因此金属材料的断裂也是一个包含了塑性损伤的过程,这种断裂过程被称为“延性断裂”[1]。
“延性断裂”一般是指以微孔洞生长方式的断裂形式。
但是广义上来讲,“延性断裂”可以理解成与材料的塑性变形相关-材料中发生断裂的部位往往表现出很大的塑性变形和良好的延展性。
一个世纪以来,广大学者在研究断裂现象的过程中作出了各种各样的努力,相继提出了应力强度因子,能量释放率,J积分理论以及连续介质损伤力学。
应力强度因子主要解决的是线弹性断裂问题,J积分主要运用在小变形假设下。
而断裂问题是一个高度非线性问题,因此就必须采用损伤力学的方法来处理金属材料断裂问题。
由于塑性变形本身是不可逆的,因此可以在塑性变形和损伤累积之间建立关系,这种建模方法也被称为累积的应变损伤方法。
那么,损伤累积过程就可以采取对塑性变形进行加权积分的形式进行,如下式所示:式中D为损伤变量,εc为断裂应变阈值,为场变量函数,为等效塑性应变增量,Dc为损伤阈值。
当损伤值D达到阈值Dc,认为材料断裂。
本文算例选取最简单的线性损伤演化方程,如下式所示:在ABAQUS软件平台上,将损伤演化方程写入用户子程序VUMAT,针对一金属带孔板进行了无初始缺陷的断裂过程模拟。
210980604_金属材料损伤理论模型的研究综述★

c. andt
he
s
ede
f
e
c
t
ss
e
r
i
ous
l
e
s
t
r
i
c
tt
hep
r
oc
e
s
s
i
ngo
fme
t
a
land
yr
,
i
t
spe
r
f
o
rmanc
eimpr
ovemen
t.The
r
e
f
o
r
et
hecon
t
i
nuousdamage me
chan
i
c
st
heo
r
hef
i
ne
yandt
v
i
ew o
ft
hedamage me
其形式非常适合于有
限元程序模拟及其验证,
而且该模型一直在不断地完善与优化。
关键词:
裂纹;
损伤;
力学损伤模型;
预测;
综述
中图分类号:
TG3
1
4.
3
文献标识码:
A
/
DO
I:
1
0.
1
6
3
5
5
c
n
k
i.
i
s
s
n
1
0
0
7
9
4
3
2
t
u
t.
2
0
2
3.
0
2.
0
0
1
j.
基于塑性损伤理论的延性金属裂纹扩展模拟
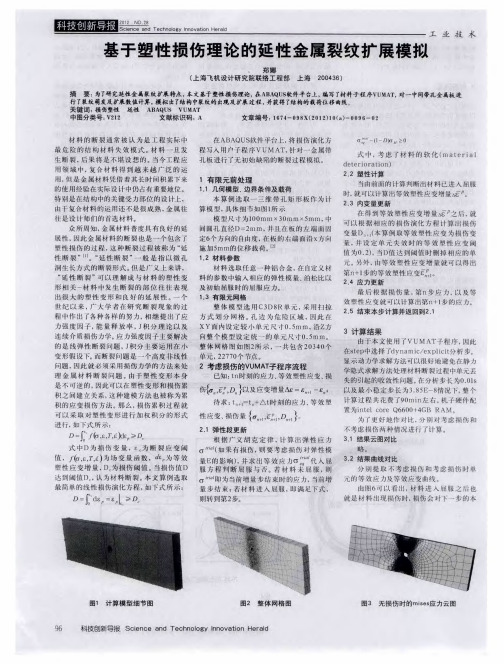
图6材 料本 构曲线 图
5 0
一
裂纹 即 0 1 .mm作 为 最 小的 单元 尺寸, 当然 具 体 到 实 际模 拟 当 中还 需 要 自行 定夺 。 于本 对
喜 。
萎3 0
2 0
1 0 0
算 例 中采 用的 最 小尺寸 为 05 m , 个单元 .r 这 a
( 上接 9 页) 5
空客 发动 机 会 产生 大 量 的 主要 温 室 气 面 八方 ( 图 4 ; 当物 体 以 声音 传播 速 度 机 氧化 剂 , 样 可以 少携 带 相 当大 量 的 氧化 再 者 , 见 )而 这 运 动 时 , 动 波 的 传 播 速 度 等 于 飞 机 前 进 剂 ( , 而 减 轻 火 箭 的 重 量 。 管 低 体 C , 给 地 球 的大 气环 境 造 成 了负面 的 扰 N0 ) 进 尽 0,这 的 速 度 , 样 , 续 时 间 的扰 动就 会 同已 有 空 含 氧 层 才几十 公里 , 样做 也 为 占火箭 总 影 响 。 用本 创 新 技 术 , 以有 效 的 降 低 油 这 后 这 使 可 尤 大 O给 延 的 扰 动 波 叠 加 在 一 起 , 成 较 强 的 波 … 重 量 的 第一 级 火箭 减 轻 很 多, 其是 第一 级 耗 , 幅 度减 少 C 环 境 造 成 的 影 响 , 形
降 在 国防领 域 , 击 机 的 发动 机 使 用本 创 由于 取 消了涡 轮 , 低 了飞 机 的制 造 成 本 , 歼 节 降低 了温 室气 为了快 速 突 破 跨 越 音 障 , 急需 大功 率 的 喷 气 新 技 术 , 可 以不 必担 忧 垂直 连 续 加 油爬 升 同时 节约 了油 料 , 省了时 间 , 发 动 机 , 掉 发 动 机 的 涡轮 部 件 这个 提 温 时 造 成 涡轮 高温 过 热 软 化 及 失 速 的危 险 , 去 体 c0 的 排 放 , 高 了 效 率 , 一 举 多 得 的 , 提 是 相 提 速 障碍 , 已是 迫 在 眉睫 。 这 样 在 空 中 的绞 杀格 斗 中就 会 占据 绝 对 的 节 能 减 排 创 新 技 术 , 信 会 为 全 球 人 类 走 个 机 体 非 常不 利 , 至 严重 危 及飞 行 安 全 。 甚 在 这 里 显 然 , 油 器 喷 油 量 可控 , 烧 优 势 。同 时在 使 用 相 同 油 量 的 前 提 下, 以 向低 碳 经济社 会 做 出一定 的贡 献。 喷 燃 可 室温 度 可 测 , 键 是 : 关 无涡轮 喷 气 发 动 机 的 大 幅 度 延长飞 机 的飞 行 时 间 , 幅度 扩大 歼 大 压 气 机 转 速 可 控 , 受 共 轴 的 涡 轮 转 速 的 击 机 的巡 航 半 径 距离 , 效 的保 卫我 国的疆 参考 文献 不 有 1 洪 航 限制 , 样 可 以 程 控 燃 烧过 程 , 到最 佳 的 土 空 域 和 海 防 空 域 。 用 此 创 新 技 术可 控 [】陈 光 , 杰 ,马 艳 红 . 空 燃 气 涡 轮 发 这 达 利 动 机 结 构 [ . 京 : 空航 天大 学 出版 M】 北 航 ( 一 ) , 现节 约 燃 料 的 目的。 趣 的 压 气 机 反 转 , 闭喷 油器 后 向前 推 气 原 理 , 油 气 比 实 有 关 社 , 0 1 2 1. 是 , 控 压 气 机 可以 反 转 , 闭喷 油 器后 向 可 以 实 现 中 国垂 直 起 降 战 斗 机 的 研 制 和 批 可 关 2 熊 郑 航 前 推 气 , 在 着陆 后 缩短 滑 跑 距离 可起 到 一 量 的生 产 ; 用本 创 新 技 术 , 以 大 幅 度 延 []宋兆 泓 , 昌炳 , 光 华 . 空 燃 气涡 轮 这 使 可 发动 机 强 度 设 计[ . 京 : 空 学 院 出 M】 北 航 定的作用。 另外 , 航 天 领域 的火 箭 发 动 机 长 无 人飞机 的飞 行时 间。 在
裂纹扩展的扩展有限元(xfem)模拟实例详解
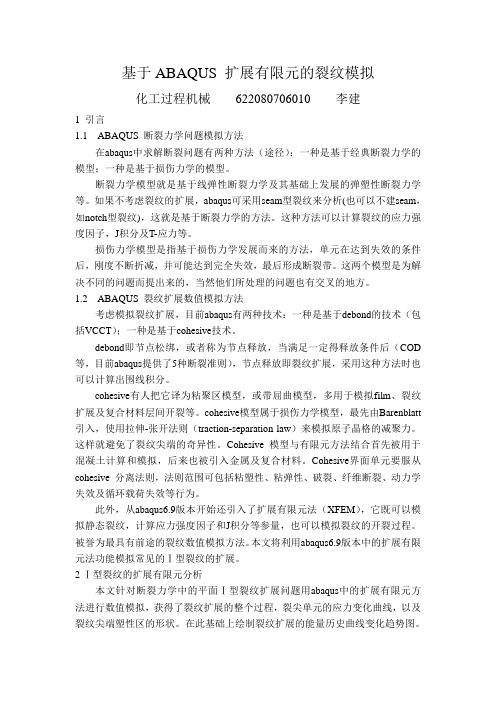
基于ABAQUS 扩展有限元的裂纹模拟化工过程机械622080706010 李建1 引言1.1 ABAQUS 断裂力学问题模拟方法在abaqus中求解断裂问题有两种方法(途径):一种是基于经典断裂力学的模型;一种是基于损伤力学的模型。
断裂力学模型就是基于线弹性断裂力学及其基础上发展的弹塑性断裂力学等。
如果不考虑裂纹的扩展,abaqus可采用seam型裂纹来分析(也可以不建seam,如notch型裂纹),这就是基于断裂力学的方法。
这种方法可以计算裂纹的应力强度因子,J积分及T-应力等。
损伤力学模型是指基于损伤力学发展而来的方法,单元在达到失效的条件后,刚度不断折减,并可能达到完全失效,最后形成断裂带。
这两个模型是为解决不同的问题而提出来的,当然他们所处理的问题也有交叉的地方。
1.2 ABAQUS 裂纹扩展数值模拟方法考虑模拟裂纹扩展,目前abaqus有两种技术:一种是基于debond的技术(包括VCCT);一种是基于cohesive技术。
debond即节点松绑,或者称为节点释放,当满足一定得释放条件后(COD 等,目前abaqus提供了5种断裂准则),节点释放即裂纹扩展,采用这种方法时也可以计算出围线积分。
cohesive有人把它译为粘聚区模型,或带屈曲模型,多用于模拟film、裂纹扩展及复合材料层间开裂等。
cohesive模型属于损伤力学模型,最先由Barenblatt 引入,使用拉伸-张开法则(traction-separation law)来模拟原子晶格的减聚力。
这样就避免了裂纹尖端的奇异性。
Cohesive 模型与有限元方法结合首先被用于混凝土计算和模拟,后来也被引入金属及复合材料。
Cohesive界面单元要服从cohesive 分离法则,法则范围可包括粘塑性、粘弹性、破裂、纤维断裂、动力学失效及循环载荷失效等行为。
此外,从abaqus6.9版本开始还引入了扩展有限元法(XFEM),它既可以模拟静态裂纹,计算应力强度因子和J积分等参量,也可以模拟裂纹的开裂过程。
基于塑性损伤理论的延性金属裂纹扩展模拟
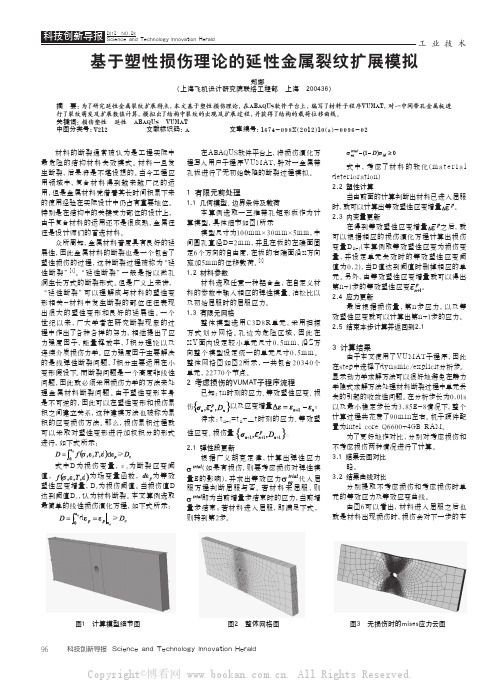
图1 计算模型细节图图2 整体网格图图3 无损伤时的mises应力云图96
科技创新导报Science and Technology Innovation Herald
构产生影响,形成相互耦合的关系,最终导致材料本构相比于无损时要明显较软。
提取结构的载荷位移曲线如图7所示,从图中可以看出,当位移载荷达到1mm的时
甚至严重危及飞行安全。
机氧化剂,这样可以少携带相当大量的氧化剂(N
2
O
4
),进而减轻火箭的重量。
尽管低空含氧层才几十公里,这样做也为占火箭总重量的第一级火箭减轻很多,尤其是第一级火箭的外围捆绑火箭可使用本发明,发电磁场可使用整体的环状磁场。
在国防领域,歼击机的发动机使用本创新技术, 可以不必担忧垂直连续加油爬升图7 结构位移载荷曲线
图5 损伤量分布云图
图4 有损伤时的mises应力云图图6 材料本构曲线图
候结构开始出现裂纹,此时力载荷也达到了
最大值。
在此之前,由于损伤的累积而导致
的材料软化使得对应位移载荷所受到的支
反力与不考虑损伤时要小一些,在出现裂纹。
基于内聚力模型的金属粉末压坯拉伸裂纹扩展模拟
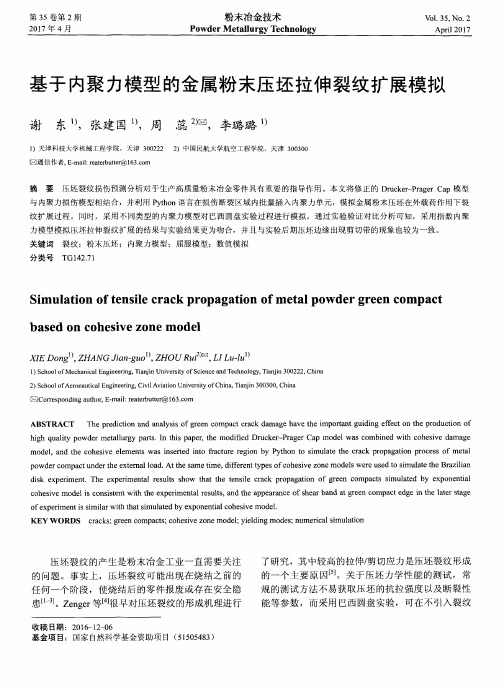
h i g h q u a l i t y p o wd e r me t a l l u r g y p a r t s .I n t h i s p a p e r , t h e mo d i i f e d Dr u c k e r - P r a g e r Ca p mo d e l wa s c o mb i n e d wi t h c o h e s i v e d a ma g e
基于韧性损伤力学的金属塑性成形研究及其数值模拟

基于韧性毁伤力学的金属塑性成形探究及其数值模拟关键词:韧性毁伤力学;金属塑性成形;本构干系;应力应变行为;材料毁伤机理;数值模拟1. 引言金属塑性成形是指通过加工变形将原材料从初始状态转化为期望的外形和尺寸的制造工艺。
其具有良好的可塑性和可加工性,已广泛应用于汽车制造、飞机制造、建筑等诸多行业。
金属塑性成形涉及材料力学、金属形变学、以及传热与流体学等多个领域,其内部机理复杂,需要深度探究。
本文旨在通过使用韧性毁伤力学分析金属塑性成形过程中材料的本构干系和应力应变行为,综合思量金属材料的实际性质,基于数值模拟方法建立新的模型,较好地模拟出金属塑性成形中的各种现象。
以此为基础,本文旨在探讨优化金属塑性成形技术的途径和方法。
2. 金属塑性成形金属塑性成形过程中,金属材料可以通过压力、拉伸、折弯、切削等方法,通过加工变形使其达到期望的外形和尺寸。
其基本原理是在大应力作用下,金属材料的晶格结构发生变化,从而导致塑性变形。
塑性形变是一种可逆变形,通过对材料施加压力,可以使其恢复到初始状态。
金属塑性成形涉及多个因素,如应力、应变、温度等。
在不同的状况下,材料的本构干系和应力应变行为均有所不同。
同时,金属材料在塑性变形中,还可能经历本质未知的材料毁伤,如微裂纹、裂缝、塑性韧性毁伤等。
这些因素的综合作用,决定了金属塑性成形的最终效果。
3. 韧性毁伤力学韧性毁伤力学是一种描述金属塑性成形材料毁伤过程的方法。
其主要思想是将材料的本质韧性与强度之间的干系思量在内。
在金属塑性成形中,韧性对材料变形能力的影响是分外重要的。
因此,韧性毁伤力学可以更好地反映材料的实际性质,有助于探究金属塑性成形中的材料毁伤机理。
基于韧性毁伤力学,可以将材料的力学行为分为两个部分:弹性和塑性。
其中,弹性变形不会导致材料的可逆变形,而塑性变形将导致材料的不行逆性变形。
在塑性变形中,材料的本质韧性和材料的强度之间的干系在整个过程中都是起重要作用的。
基于混凝土损伤力学的裂缝扩展模拟研究
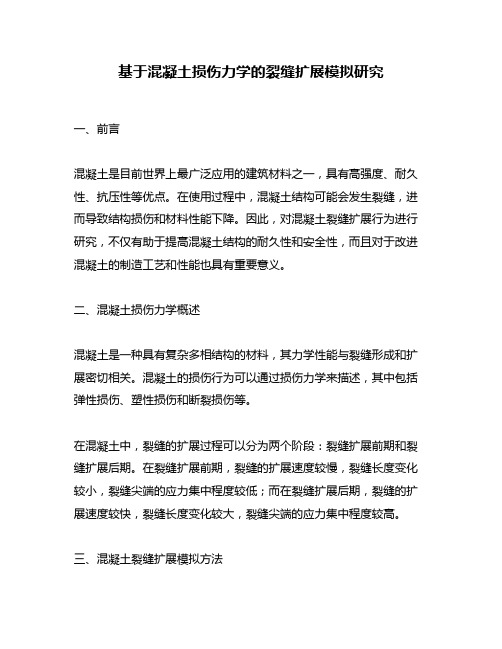
基于混凝土损伤力学的裂缝扩展模拟研究一、前言混凝土是目前世界上最广泛应用的建筑材料之一,具有高强度、耐久性、抗压性等优点。
在使用过程中,混凝土结构可能会发生裂缝,进而导致结构损伤和材料性能下降。
因此,对混凝土裂缝扩展行为进行研究,不仅有助于提高混凝土结构的耐久性和安全性,而且对于改进混凝土的制造工艺和性能也具有重要意义。
二、混凝土损伤力学概述混凝土是一种具有复杂多相结构的材料,其力学性能与裂缝形成和扩展密切相关。
混凝土的损伤行为可以通过损伤力学来描述,其中包括弹性损伤、塑性损伤和断裂损伤等。
在混凝土中,裂缝的扩展过程可以分为两个阶段:裂缝扩展前期和裂缝扩展后期。
在裂缝扩展前期,裂缝的扩展速度较慢,裂缝长度变化较小,裂缝尖端的应力集中程度较低;而在裂缝扩展后期,裂缝的扩展速度较快,裂缝长度变化较大,裂缝尖端的应力集中程度较高。
三、混凝土裂缝扩展模拟方法1.有限元方法有限元方法是目前混凝土裂缝扩展模拟中应用最广泛的方法之一。
该方法通过将混凝土结构离散化为一系列有限元,再根据弹性力学和损伤力学原理模拟裂缝扩展过程。
2.离散元方法离散元方法是另一种常用的混凝土裂缝扩展模拟方法。
该方法将混凝土结构离散化为一系列颗粒,再根据颗粒之间的相互作用力模拟裂缝扩展过程。
3.格子点方法格子点方法是最近几年新兴的混凝土裂缝扩展模拟方法。
该方法通过将混凝土结构分解为一系列网格点,并根据网格点之间的应变和应力计算裂缝扩展过程。
四、混凝土裂缝扩展模拟实例以有限元方法为例,对混凝土裂缝扩展进行模拟。
假设一个混凝土结构存在一个长度为20mm的裂缝,裂缝尖端的应力集中系数为2.5。
根据有限元模拟结果,裂缝扩展过程可以分为两个阶段。
在裂缝扩展前期,裂缝长度变化较小,裂缝尖端的应力集中系数在1.5左右。
在裂缝扩展后期,裂缝长度变化较大,裂缝尖端的应力集中系数在3.5左右。
五、总结混凝土裂缝扩展模拟是一个复杂的过程,需要综合考虑材料力学、损伤力学等多个方面的因素。
基于内聚力模型的双相TiAl合金裂纹扩展的多尺度模拟
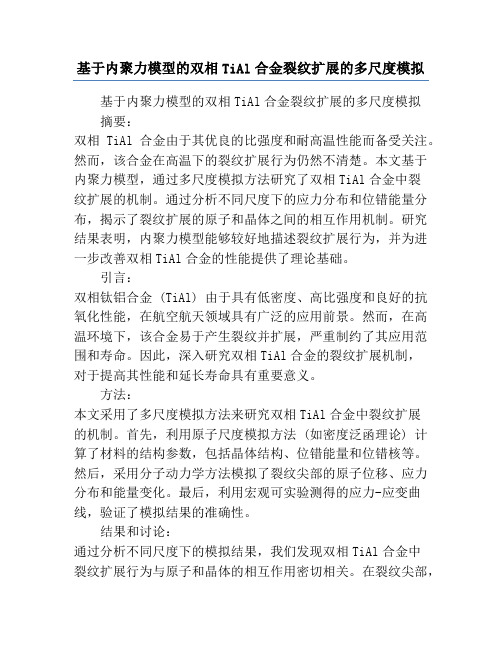
基于内聚力模型的双相TiAl合金裂纹扩展的多尺度模拟基于内聚力模型的双相TiAl合金裂纹扩展的多尺度模拟摘要:双相TiAl合金由于其优良的比强度和耐高温性能而备受关注。
然而,该合金在高温下的裂纹扩展行为仍然不清楚。
本文基于内聚力模型,通过多尺度模拟方法研究了双相TiAl合金中裂纹扩展的机制。
通过分析不同尺度下的应力分布和位错能量分布,揭示了裂纹扩展的原子和晶体之间的相互作用机制。
研究结果表明,内聚力模型能够较好地描述裂纹扩展行为,并为进一步改善双相TiAl合金的性能提供了理论基础。
引言:双相钛铝合金 (TiAl) 由于具有低密度、高比强度和良好的抗氧化性能,在航空航天领域具有广泛的应用前景。
然而,在高温环境下,该合金易于产生裂纹并扩展,严重制约了其应用范围和寿命。
因此,深入研究双相TiAl合金的裂纹扩展机制,对于提高其性能和延长寿命具有重要意义。
方法:本文采用了多尺度模拟方法来研究双相TiAl合金中裂纹扩展的机制。
首先,利用原子尺度模拟方法 (如密度泛函理论) 计算了材料的结构参数,包括晶体结构、位错能量和位错核等。
然后,采用分子动力学方法模拟了裂纹尖部的原子位移、应力分布和能量变化。
最后,利用宏观可实验测得的应力-应变曲线,验证了模拟结果的准确性。
结果和讨论:通过分析不同尺度下的模拟结果,我们发现双相TiAl合金中裂纹扩展行为与原子和晶体的相互作用密切相关。
在裂纹尖部,位错能量峰值明显高于裂纹周围的晶体,形成能量梯度。
在加载过程中,位错沿裂纹面滑移,裂纹尖部的应力集中增强,促使裂纹继续扩展。
在裂纹扩展的过程中,位错密度不断增加,晶体出现塑性变形和蠕变现象。
此外,研究还发现双相界面对裂纹扩展起到了缓冲和阻碍的作用,能够有效抑制裂纹的扩展速率。
结论:本研究基于内聚力模型,通过多尺度模拟方法揭示了双相TiAl合金中裂纹扩展的机制。
研究结果表明,裂纹扩展与原子和晶体的相互作用密切相关,位错滑移和内聚力是裂纹扩展的关键因素。
采用Cohesive方法实现材料损伤与裂纹扩展
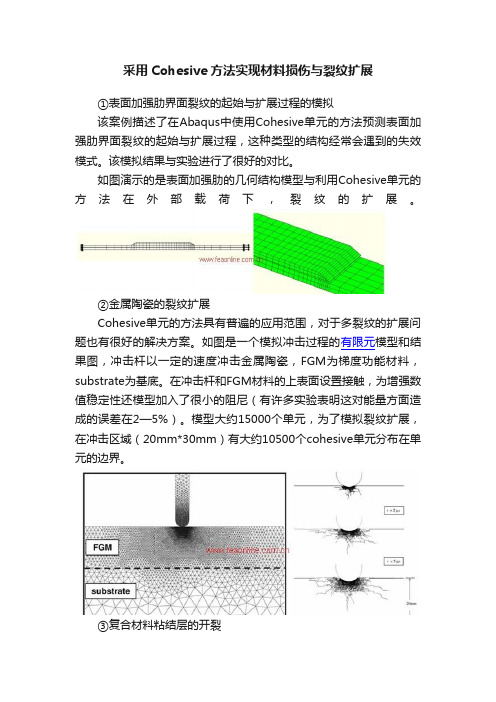
采用Cohesive方法实现材料损伤与裂纹扩展
①表面加强肋界面裂纹的起始与扩展过程的模拟
该案例描述了在Abaqus中使用Cohesive单元的方法预测表面加强肋界面裂纹的起始与扩展过程,这种类型的结构经常会遇到的失效模式。
该模拟结果与实验进行了很好的对比。
如图演示的是表面加强肋的几何结构模型与利用Cohesive单元的方法在外部载荷下,裂纹的扩展。
②金属陶瓷的裂纹扩展
Cohesive单元的方法具有普遍的应用范围,对于多裂纹的扩展问题也有很好的解决方案。
如图是一个模拟冲击过程的有限元模型和结果图,冲击杆以一定的速度冲击金属陶瓷,FGM为梯度功能材料,substrate为基底。
在冲击杆和FGM材料的上表面设置接触,为增强数值稳定性还模型加入了很小的阻尼(有许多实验表明这对能量方面造成的误差在2—5%)。
模型大约15000个单元,为了模拟裂纹扩展,在冲击区域(20mm*30mm)有大约10500个cohesive单元分布在单元的边界。
③复合材料粘结层的开裂
该模拟反映了典型的复合材料层间开裂过程的模拟。
模型中复合材料由三层粘结单元粘结而成。
在动态冲击载荷作用下,复合材料的分层表现为显著的层间失效。
④移动质量球对静止墙壁的冲击
该模型在每一个六面体单元之间创建一层粘结层,从而形成六面体粘结墙体。
采用一个质量较大的球体实现高速对静态墙体冲击损伤模拟。
模型分析采用Abaqus/Explicit实现,采用Cohesive单元还可以模拟诸如水面滑行、机加工、石油钻井、开挖以及爆炸对建筑物的影响等工程分析。
- 1、下载文档前请自行甄别文档内容的完整性,平台不提供额外的编辑、内容补充、找答案等附加服务。
- 2、"仅部分预览"的文档,不可在线预览部分如存在完整性等问题,可反馈申请退款(可完整预览的文档不适用该条件!)。
- 3、如文档侵犯您的权益,请联系客服反馈,我们会尽快为您处理(人工客服工作时间:9:00-18:30)。
d p Dc D f , ,T ,
0
c
1.2 材料参数
式中 D 为损伤变量, c 为断裂应变阈
为场变量函数, d p 为等 值, f , ,T ,
效塑性应变增量, Dc 为损伤阈值。当损伤 值 D 达到阈值 Dc ,认为材料断裂。本文算 例选取最简单的线性损伤演化方程, 如下式 材料选取任意一种铝合金, 在自定义材 所示: 料的参数中输入相应的弹性模量、 泊松比以
参考文献
[1] Xue L. Ductile fracture modeling – theory, experiment verification. investigation Ph.D. Thesis, and numerical
Massachusetts
Institute of Technology, June 2007 [2] 庄茁, 张帆, 岑松等. ABAQUS 非线性 有限元分析与实例[M]. 北京:科学出版社, 2005: 187-206
70 60 50
载荷(kN)
不考虑损伤 考虑损伤
40 30ቤተ መጻሕፍቲ ባይዱ20 10 0
图 5 损伤量分布云图
0
1
2
3 位移(mm)
4
5
6
3.2 结果曲线对比
分别提取不考虑损伤和考虑损伤时单 元的等效应力及等效应变曲线。
700 600
等效应力(MPa)
图 7 结构位移载荷曲线
4 结论与展望
本文借助于 ABAQUS 以及其用户子程 序计算模拟了基于损伤累积的金属构件断
出很大的塑性变形和良好的延展性。 一个世 纪以来, 广大学者在研究断裂现象的过程中 作出了各种各样的努力, 相继提出了应力强 度因子,能量释放率,J 积分理论以及连续 介质损伤力学。 应力强度因子主要解决的是
1 有限元前处理 [2]
1.1 几何模型、边界条件及载荷
本算例选取一三维带孔矩形板作为计 算模型,具体细节如图 1 所示
σ ,
n
p n
, Dn 以及应变增量 ε ε n1 ε n ;
待求:tn+1 =tn + t 时刻的应力、等效塑性应 变、损伤量 σ n 1 , np1 , Dn 1 。
2.1 弹性段更新
根据广义胡克定律,计算出弹性应力
2.4 应力更新
最后根据损伤量,第 n 步应力,以及等 效塑性应变就可以计算出第 n+1 步的应力;
图 3 无损伤时的 mises 应力云图
时候结构开始出现裂纹, 此时力载荷也达到 了最大值。在此之前,由于损伤的累积而导 致的材料软化使得对应位移载荷所受到的 支反力与不考虑损伤时要小一些, 在出现裂 纹之后,由于裂纹的扩展,支反力出现了急 剧下降,直到结构完全断开,支反力为零。
图 4 有损伤时的 mises 应力云图
500 400 300 200 100 0 0 0.1 0.2 0.3 0.4 0.5 等效塑性应变 0.6 0.7
不考虑损伤 考虑损伤
裂过程。 本文计算过程当中采用的是线性损伤 演化方程, 这种假设在复杂受载情况下计算 精度是不高的。因此在后续的研究中,损伤 演化方程的选择是个关键问题。
图 6 材料本构曲线图
trial 即为当前增量步结束时的应力,当前
增量步结束; 若材料进入屈服, 即满足下式, 则转到第 2 步;
trial eq (1 D) M 0
式 中 , 考 虑 了 材 料 的 软 化 (material deterioration)
2.2 塑性计算
当由前面的计算判断出材料已进入屈 服 时 ,就 可以 计算 出等 效 塑性 应变 增 量
Ductile fracture simulation of metal using damage plasticity theory
JIANG Jinfeng1 SUN Qin1
(1. School of Aeronautics, Northwestern Polytechnical University, Xi’an, 710072) ABSTRACT: In order to simulate progressive fracture of metal, damage plasticity theory is taken into account. Fracture algorithm VUAMT is then coded using plasticity theory and incorporated in the commercial software ABAQUS. With the VUMA T subroutine, numerical fracture simulation of a metal plate with a hole is carried out, and PV curve is extracted from the result. Key words: damage plasticity; ductility; ABAQUS; VUMA T 材料的断裂通常被认为是工程实际中 最危险的结构材料失效模式。 材料一旦发生 断裂,后果将是不堪设想的。当今工程应用 领域中,复合材料得到越来越广泛的运用, 但是金属材料凭借着其长时间积累下来的 使用经验在实际设计中仍占有重要地位。 特 别是在结构中的关键受力部位的设计上, 由 于复合材料的运用还不是很成熟, 金属往往 是设计师们的首选材料。 众所周知, 金属材料普遍具有良好的延 展性, 因此金属材料的断裂也是一个包含了 弹塑性变形的过程,这种断裂过程被称为 “延性断裂”[1 ]。 “延性断裂”一般是指以 微孔洞生长方式的断裂形式。 但是广义上来 讲, “延性断裂”可以理解成与材料的塑性 变形相关- 材料中发生断裂的部位往往表现
c
D d p p
0
c
Dc
及初始屈服时的屈服应力。
在 ABAQUS 软件平台上,将损伤演化 方程写入用户子程序 VUMA T ,针对一金属 带孔板进行了无初始缺陷的断裂过程模拟。
1.3 有限元网格
整体模型选用 C3D8R 单元,采用扫掠 方式划分网格。孔边为危险区域,因此在 XY 面内设定较小单元尺寸 0.5mm,沿 Z 方
此外, 单元尺寸对计算结果的影响也不 能忽略。一般来说,单元尺寸越小越好,但 是太小了载荷也会继续下降, 因此最后所得 的 PV 曲线跟实验曲线也对不上,当前工程 时一般采用肉眼可见的最小裂纹即 0.1mm 作为最小的单元尺寸, 当然具体到实际模拟 当中还需要自行定夺。 对于本算例中采用的 最小尺寸为 0.5mm, 这个单元得出的计算结 果还需要实验来验证。
基于损伤塑性理论的延性金属裂纹扩展模拟
江金锋 1 孙秦 1
(1. 西北工业大学航空学院,西安,710072) 摘要:为了研究延性金属裂纹扩展特点, 本文基于塑性损伤理论, 在 ABAQUS 软件平台上, 编写了材料子程序 VUMAT , 对一中间带孔金属板进行了裂纹萌发及扩展数值计算, 模拟出 了结构中裂纹的出现及扩展过程,并提取了结构的载荷位移曲线。 关键词: 损伤塑性; 延性; ABAQUS; VUMA T
线弹性断裂问题,J 积分主要运用在小变形 假设下。而断裂问题是一个高度非线性问 题, 因此就必须采用损伤力学的方法来处理 金属材料断裂问题。 由于塑性变形本身是不 可逆的, 因此可以在塑性变形和损伤累积之 间建立关系, 这种建模方法也被称为累积的 应变损伤方法。那么,损伤累积过程就可以 采取对塑性变形进行加权积分的形式进行, 如下式所示: 模型尺寸为 100 30 5( mm) ,中间圆孔 直径 D 2mm ,并且在板的左端面固定 6 个 方向的自由度, 在板的右端面沿 x 方向施加 5mm 的位移载荷。
为了更好地作对比, 分别对考虑损伤和 不考虑损伤两种情况进行了计算。
3.1 结果云图对比
由图 6 可以看出, 材料进入屈服之后也 就是材料出现损伤时, 损伤会对下一步的本 构产生影响,形成相互耦合的关系,最终导 致材料本构相比于无损时要明显较软。 提取结构的载荷位移曲线如图 7 所示, 从图中可以看出,当位移载荷达到 1mm 的
trial (如果有损伤,则要考虑损伤对弹性模
量 E 的影响),并求出等效应力 eq 代入屈
trial
2.5 结束本步计算并返回到 2.1
服方程判断屈服与否。若材料未屈服,则
3 计算结果
由于本文使用了 VUMA T 子程序, 因此 在 step 中选择了 dynamic/explicit 分析步。 显示动力学求解方法可以很好地避免在静 力学隐式求解方法处理材料断裂过程中单 元丢失的引起的收敛性问题。 在分析步长为 0.01s 以及最小稳定步长为 3.85E-8 情况下, 整个计算过程共花费了 90 分钟左右。机子 硬件配置为 intel core Q6600 + 4GB RAM。
向整个模型设定统一的单元尺寸 0.5mm。 整 体网格图如图 2 所示, 一共包含 20340 个单 元,22770 个节点。
p;
2.3 内变量更新
在得到等效塑性应变增量 之后, 就
p
2 考虑损伤的 VUMAT 子程序 流程
已知:tn 时刻的应力、等效塑性应变、损伤
可以根据相应的损伤演化方程计算出损伤 变量 Dn +1 (本算例取等效塑性应变为损伤变 量, 并设定单元失效时的等效塑性应变阈值 为 0.2), 当 D 值达到阈值时删掉相应的单元。 另外,由等效塑性应变增量就可以得出第 n+1 步的等效塑性应变 np1 ;