有色金属熔炼与铸锭10
金属熔炼与铸锭—第二章

第二章
1
冶金工程学院
第2章 有色金属及合金材料
主要内容
2.1 熔铸的基本任务 2.2 熔铸的基本要求 2.3 熔铸工艺规程制定
2
冶金工程学院
2.1 熔铸的基本任务
3
冶金工程学院
2.2 熔铸的基本要求
4
冶金工程学院
2.2 熔铸的基本要求
5
冶金工程学院
2.2 熔铸的基本要求
2.3 熔铸工艺规程的制定
20
冶金工程学院
作业思考题
1.熔铸的基本任务是什么? 2.熔铸的六点要求是什么? 3.为什么在熔铸之前要制定熔铸工艺规程?
21
冶金工程学院
15
冶金工程学院
2.3 熔铸工艺规程的制定
水、电(油)、气、料
Байду номын сангаас
16
冶金工程学院
2.3 熔铸工艺规程的制定
17
冶金工程学院
18
冶金工程学院
• 铸造用(废钢熔解)里面的原材料覆盖剂在废钢熔炼过程 中覆盖在钢水表面,起到了保温、吸附夹杂物,防止钢水 氧化等作用。主要成分为C、CaO、SiO2、Al2O3等。对于 有特殊要求的,还要添加合金粉、膨胀材料等,以提高保 温、吸附夹杂的性能。 • 铸造熔炼精炼添加剂的作用及特性 熔炼精炼添加剂能加快 合金的熔化,降低熔化能耗,节省用电量,减 少电能耗损 净化 钢(铁)液,减少渣孔、气孔,提高铸件成品... • 打渣剂和清渣剂应该是一样的东西 铝合金在温度达到720度左右时加入精炼剂,用工具压到底 部缓慢移动直到不冒泡为止,主要是用来清除铝液中的氢 精炼后加入打渣剂,用工具充分搅拌后捞出渣子,主要是用 19 来清除铝液中的杂质 冶金工程学院 清渣结束后在表面撒上覆盖剂,防止空气中的氢进入铝液中
金属冶炼中的精炼和铸造
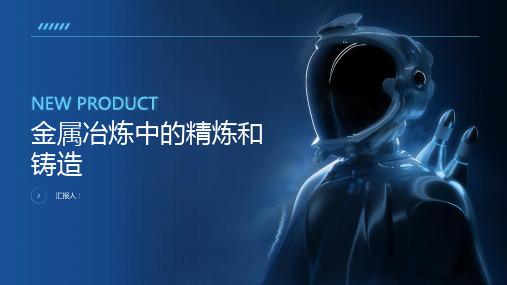
效率低:精炼过程需要较长的时间,效率较低
成本高:精炼过程需要消耗大量的能源和材料,成本较高
环境污染:精炼过程中会产生大量的废气、废水和废渣,对环境造成污染
质量不稳定:精炼过程中可能会出现杂质残留,影响产品质量
金属铸造
铸造是一种金属成型工艺,将熔融的金属倒入模具中,冷却后形成所需的形状和尺寸。
汇报人:
金属冶炼中的精炼和铸造
目录
添加目录标题
金属冶炼概述
金属精炼
金属铸造
精炼与铸造的比较
添加章节标题
金属冶炼概述
金属冶炼是指将金属矿石或金属废料通过物理或化学方法转化为金属的过程。
金属冶炼包括精炼和铸造两个主要步骤。
精炼是指将金属矿石或金属废料中的杂质去除,提高金属纯度的过程。
铸造是指将精炼后的金属熔化,形成液态金属,然后浇铸成所需形状的过程。
精炼技术:不断提高精炼效率,降低能耗和污染
铸造技术:发展新型铸造材料和工艺,提高产品质量和生产效率
绿色冶金:推广绿色冶金技术,减少环境污染和资源浪费
智能化:利用人工智能、大数据等技术,实现冶炼和铸造过程的智能化控制和优化
添加标题
添加标题
添加标题
添加标题
铸造技术:发展新型铸造材料,提高铸造精度和性能
建筑行业:门窗、栏杆、楼梯等部件
电子行业:电路板、芯片、连接器等部件
医疗行业:假肢、植入物、医疗器械等部件
精炼与铸造的比较
目的不同:精炼是为了去除金属中的杂质,提高纯度;铸造则是为了将金属制成特定的形状和尺寸。
工艺不同:精炼通常包括熔炼、电解、化学沉淀等过程;铸造则包括熔化、浇注、冷却等过程。
有色金属熔炼与铸锭
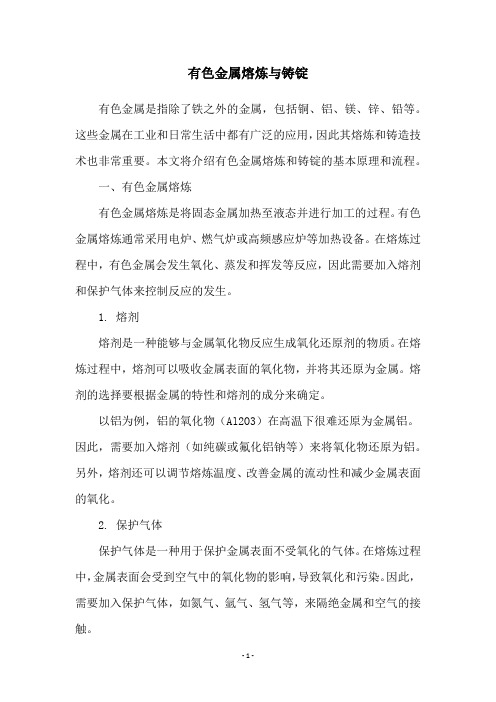
有色金属熔炼与铸锭有色金属是指除了铁之外的金属,包括铜、铝、镁、锌、铅等。
这些金属在工业和日常生活中都有广泛的应用,因此其熔炼和铸造技术也非常重要。
本文将介绍有色金属熔炼和铸锭的基本原理和流程。
一、有色金属熔炼有色金属熔炼是将固态金属加热至液态并进行加工的过程。
有色金属熔炼通常采用电炉、燃气炉或高频感应炉等加热设备。
在熔炼过程中,有色金属会发生氧化、蒸发和挥发等反应,因此需要加入熔剂和保护气体来控制反应的发生。
1. 熔剂熔剂是一种能够与金属氧化物反应生成氧化还原剂的物质。
在熔炼过程中,熔剂可以吸收金属表面的氧化物,并将其还原为金属。
熔剂的选择要根据金属的特性和熔剂的成分来确定。
以铝为例,铝的氧化物(Al2O3)在高温下很难还原为金属铝。
因此,需要加入熔剂(如纯碳或氟化铝钠等)来将氧化物还原为铝。
另外,熔剂还可以调节熔炼温度、改善金属的流动性和减少金属表面的氧化。
2. 保护气体保护气体是一种用于保护金属表面不受氧化的气体。
在熔炼过程中,金属表面会受到空气中的氧化物的影响,导致氧化和污染。
因此,需要加入保护气体,如氮气、氩气、氢气等,来隔绝金属和空气的接触。
以铜为例,铜熔点较低,容易氧化,因此需要使用保护气体来防止氧化。
常用的保护气体是氢气,因为氢气可以还原铜表面的氧化物,并且不会对铜产生污染。
二、有色金属铸造有色金属铸造是将熔化的金属倒入模具中,使其冷却固化成型的过程。
有色金属铸造通常采用砂型铸造、永久模铸造、压铸和注射成型等方法。
1. 砂型铸造砂型铸造是将熔化的金属倒入沙子制成的模具中,使其冷却固化成型的方法。
砂型铸造可以制造大型和复杂的零件,但是生产周期较长,成本较高。
2. 永久模铸造永久模铸造是将熔化的金属倒入金属模具中,使其冷却固化成型的方法。
永久模铸造可以制造高精度、高表面质量和高产量的零件,但是模具成本较高。
3. 压铸压铸是将熔化的金属注入压铸机中,经过高压快速冷却成型的方法。
压铸可以制造高精度、高表面质量和高产量的零件,但是一般只适用于小型和中型零件。
有色金属加工-熔炼与铸锭..

金属液中气体的溶解与检测
熔体中溶解的气体:H2(70~90%)、CO2、 CO、N2、CnHm 气体的溶解机理:与金属有一定结合能力的气 体,都能不同程度溶解于金属熔体;与金属无 结合能力的气体,不溶解于金属熔体,只被吸 附 熔体中气体的危害:引起铸锭产生气孔或组织 疏松 气体含量测定:第一气泡法
铝合金牌号
铝合金牌号
1xxx系 2xxx系 3xxx系 4xxx系 5xxx系 6xxx系 7xxx系 8xxx系 9xxx系
镁合金牌号
产品牌号以英文字母加数字再加英文字母的形式表示 。前面的2位英文字母是其最主要的合金组成元素代 号(元素代号符合表1的规定),其后的2位数字表示其 最主要的合金组成元素的大致含量。最后面的一个英 文字母为标识代号,用以标识各具体组成元素相异或 元素含量有微小差别的不同合金
火焰炉
感应炉
熔炼炉的结构
电阻反射式熔炼炉:通 过电热体放出的热量加 热炉顶和炉墙,热量再 由炉顶、炉墙以辐射方 式传递给被加热的物料, 使之不断升温熔化 固定式方形电阻反射炉 结构:炉壳、炉基、炉 底、炉墙、炉顶、炉温 控制和测量系统
静置炉
用于接受在熔炼炉中熔炼好的熔体,并在其中 进行精炼、静置和调整熔体温度,在铸造过程 中对熔体起保护作用 电阻反射炉作静置炉
确定炉料组成和配料比的基本原则
炉料组成:构成炉料的各个品种和每个品种的 品位 配料比:一炉炉料中每一种炉料所占的比例 原则:
成分原则 质量原则 工艺原则 经济原则 物料平衡原则
熔炼与铸造原理与技术 教学大纲
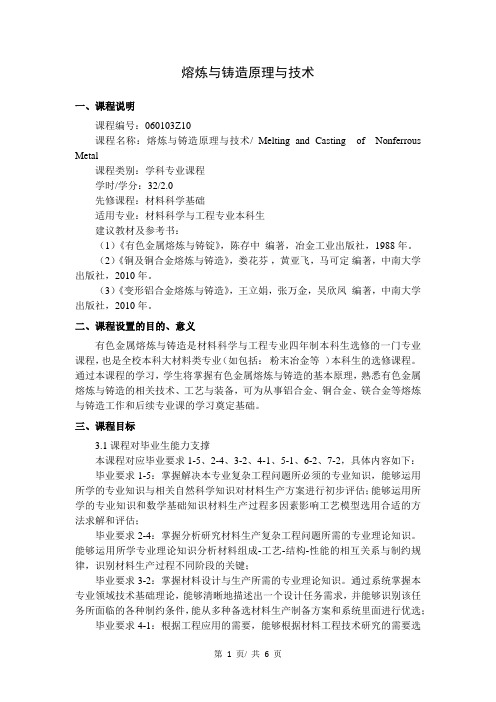
熔炼与铸造原理与技术一、课程说明课程编号:060103Z10课程名称:熔炼与铸造原理与技术/ Melting and Casting of Nonferrous Metal课程类别:学科专业课程学时/学分:32/2.0先修课程:材料科学基础适用专业:材料科学与工程专业本科生建议教材及参考书:(1)《有色金属熔炼与铸锭》,陈存中编著,冶金工业出版社,1988年。
(2)《铜及铜合金熔炼与铸造》,娄花芬,黄亚飞,马可定编著,中南大学出版社,2010年。
(3)《变形铝合金熔炼与铸造》,王立娟,张万金,吴欣凤编著,中南大学出版社,2010年。
二、课程设置的目的、意义有色金属熔炼与铸造是材料科学与工程专业四年制本科生选修的一门专业课程,也是全校本科大材料类专业(如包括:粉末冶金等)本科生的选修课程。
通过本课程的学习,学生将掌握有色金属熔炼与铸造的基本原理,熟悉有色金属熔炼与铸造的相关技术、工艺与装备,可为从事铝合金、铜合金、镁合金等熔炼与铸造工作和后续专业课的学习奠定基础。
三、课程目标3.1课程对毕业生能力支撑本课程对应毕业要求1-5、2-4、3-2、4-1、5-1、6-2、7-2,具体内容如下:毕业要求1-5:掌握解决本专业复杂工程问题所必须的专业知识,能够运用所学的专业知识与相关自然科学知识对材料生产方案进行初步评估;能够运用所学的专业知识和数学基础知识材料生产过程多因素影响工艺模型选用合适的方法求解和评估;毕业要求2-4:掌握分析研究材料生产复杂工程问题所需的专业理论知识。
能够运用所学专业理论知识分析材料组成-工艺-结构-性能的相互关系与制约规律,识别材料生产过程不同阶段的关键;毕业要求3-2:掌握材料设计与生产所需的专业理论知识。
通过系统掌握本专业领域技术基础理论,能够清晰地描述出一个设计任务需求,并能够识别该任务所面临的各种制约条件,能从多种备选材料生产制备方案和系统里面进行优选;毕业要求4-1:根据工程应用的需要,能够根据材料工程技术研究的需要选择合适的实验手段对材料组成、组织结构、性能及其相互关系,对试验数据做出正确的分析,为材料的应用提出合理建议;毕业要求5-1:系统地掌握材料科学与工程基础理论,掌握相关技术基础理论和现代分析方法在材料制备技术中的应用知识与应用技巧;系统地掌握材料工程领域主要制备技术,深入了解新材料与材料加工新技术的发展方向;毕业要求6-2:能正确认知材料科学与工程中新材料与先进加工方法对社会进步的重大促进作用,了解材料科学与工程对社会对国防的重要意义;毕业要求7-2:了解材料科学与工程中各种工程实践活动对社会对自然环境的作用,掌握一定职业保健知识与技能,了解一定环保知识与环保技术。
《金属熔炼与铸锭》课程实验指导书及实验报告撰写要求内容

图1 具有三个晶区的 铸锭晶粒组织示意图 纯铝的熔炼与铁模铸锭一、实验目的1、通过纯铝的熔炼与铁模铸锭,了解有色金属熔铸的一般工艺和操作知识。
2、观察铝锭横截面的铸造组织形貌,了解形成晶粒组织的三个晶区。
3、改变浇铸工艺条件,研究不同的浇铸工艺条件对铸锭晶粒组织的影响。
二、实验原理金属和合金的铸锭晶粒组织一般较为粗大,对铸件横断面稍加打磨、抛光和腐蚀,就可直接进行观察。
铸锭晶粒组织常见三个晶区形貌如图1所示。
(1)表面细等轴晶区当过热金属浇入锭模时,锭模对熔液产生强烈过冷,在模壁附近形成大量的晶核,生长成枝状细等轴晶。
同时,浇铸引起的动量对流,液体外温差引起的热对流,以及由对流引起的温度起伏,促使模壁上形成的晶粒脱落和游离,增加凝固区的晶核数目,因而形成了表面细等轴晶区。
(2)柱状晶区 在表面细等轴晶区,生长方向与散热方向平行的晶粒得到优先生长,而与散热方向不平行的晶粒则被抑制。
这种竞争生长的结果,使愈往铸锭部晶粒数目愈少,优先生长的晶粒最后单向生长并互相接触而形成柱状晶区。
柱状晶区是在单向导热及顺序凝固条件下形成的。
凡能阻止晶体脱离模壁和在固/液界面前沿形核的因素,均有利于扩大柱状晶区。
浇铸温度高,固/液界面前沿温度梯度大,凝固区窄,从界面上脱落的枝晶易于被完全熔化。
(3)中心等轴晶区柱状晶生长到一定程度,由于前沿液体远离模壁,散热困难,冷速变慢,而且熔液中的温差随之减小,这将阻止柱状晶的快速生长,当整个熔液温度降至熔点以下时,熔液中出现许多晶核并沿各个方向长大,就形成中心等轴晶区。
形成中心等轴晶区的晶核主要来源于三种途径:表面细等轴晶的游离;枝晶的熔断及游离;液面或凝壳上晶体的沉积。
凡能阻止游离到铸锭中心的晶粒完全熔化的因素,均有利于促进中心等轴晶区的形成。
铸锭的结晶过程及其组织与金属的冷却条件、浇铸时熔体的温度、变质处理条件等因素有关。
改变金属的浇铸温度对结晶过程有影响作用。
当液态金属过热越多时,浇筑后沿铸锭截面的温差越大,越有利于按顺序凝固的方式结晶,形成柱状晶组织。
铸锭缺陷
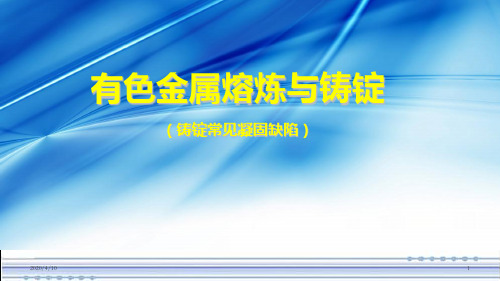
2020/4/10
A
C
B
0
固溶体不平衡结晶示意图
5
铸锭常见凝固缺陷
1.铸锭偏析
(1) 晶内偏析 由于铸锭冷凝较快,固液两相中溶质来不及扩散均匀,晶粒
内部先后结晶部分的成分不同。
晶内偏析的影响因素: a)冷却速度; b)偏析元素的扩散能力; c)液固相线间隔。
2020/4/10
6
铸锭常见凝固缺陷
1.铸锭偏析
2020/4/10
15
铸锭常见凝固缺陷
2.缩孔与缩松
(4)缩孔和缩松的形成
缩松形成示意图
缩松形成原因:是在同时凝固的条件下。最后凝固的地方因收缩造成的孔 洞得不到金属的补缩而产生的。缩松分布面广,铸锭轴线附近尤为严重。
2020/4/10
16
铸锭常见凝固缺陷
2.缩孔与缩松
(5)影响缩孔和缩松的因素
有色金属熔炼与铸锭 机械设计基础 (铸锭常见凝固缺陷)
主讲:宋绍华
2020/4/10
1
铸锭常见凝固缺陷
本章内容要点
铸锭偏析 缩孔与缩松 铸锭裂纹 铸锭冷隔 铸锭气孔 非金属夹渣
2020/4/10
2
铸锭常见凝固缺陷
铸锭质量直接影响到其后被加工成各种材料(板、带、管、 棒、型、线、锻件等)的质量。据统计轻合金材料生产中,有 60~70%的废品是因铸锭质量不良造成的。可以说,铸锭的各种 缺陷往往造成了加工车间各种不合格制品的“先天不足”,而某 些缺陷(如裂纹),显然在进入压力加工前就成了废品。因此, 如何识别、分析铸锭缺陷的产生原因,找出防止或消除这些缺 陷的措施,对提高铸锭和半制品的质量,提高整个生产过程的 成品率,意义十分重大。
2020/4/10
铝合金的熔炼与铸造

铝合金的熔炼与铸造发布时间:2012-4-3 21:37:13 | 38 人感兴趣 | 评分:3 | 收藏: 01 配料及其计算配料是熔体铸的第一道工序。
它的首要任务是控制成分和杂质含量使之符合要求,其次是根据对合金的加工和使用性能的要求,确定各种炉料品种及配料比;再次是正确地计算每炉的全部炉料量。
合理地吊装各种原辅材料,管理好各种金属及废料(旧料)。
铝合金熔炼时,炉料大致分为三类,即:工业纯金属,或称新料或新金属;回炉的金属或合金废料,也称旧料或返回料;以及中间合金或配制合金用的纯金属。
正确地选择配制合金的炉料,对于合金成分控制,铸锭质量的保证,以及金属原料的节约,都有重要的意义。
总之,在保证性能合乎要求的前提下,允许利用各种废料,节约新金属和贵重金属。
换句话说,就是能用废料应少用纯金属,能用低品位纯金属绝不用高品位的纯金属。
做到废料用尽,次料代替好料,好料精用,搭配适当,保证质量。
1.1 工业纯金属--新料铝合金是在纯金属熔炼的基础上,加上其它合金元素配制而成.因此,在配制合金以前,首先应依所需配制的合金成分的要求,选择所需的纯金属之品位。
有色金属的工业纯金属多来源于冶炼厂,如工业纯铝(称原铝),工业纯铜(称紫铜或电解铜),工业纯镁,以及金属镍等都是从电解工厂制得的。
原铝多铸成15-20公斤的小锭(称铝锭);镁以锭状供应,镁锭的重量可分为2.5公斤和9公斤两种;纯铜和金属镍一般多以电解铜板和电解镍板的形式供应;金属锌一般铸成重40公斤左右的扁平锌锭,而金属锰和铬分别以不同的粒度供应。
这些所谓的纯金属中,杂质仍是不可避免的。
例如,原铝锭中仍含有Fe 和Si两种主要杂质。
它们大多数是从炼铝原料---铝矿石中带来的。
这两种杂质元素对铝及其合金的性能有极大的影响,因而使用原铝锭时,必须注意这些杂质的含量,根据所配制合金的要求正确地选用原铝锭。
铝冶炼厂生产的原铝新料,是按所含铁和硅二种主要杂质元素的多少而定其品位的。
《铝合金生产技术》(熔炼.铸造)教案
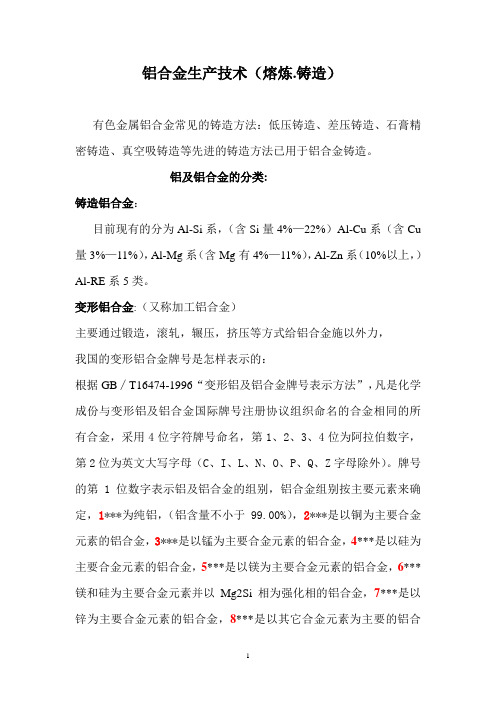
铝合金生产技术(熔炼.铸造)有色金属铝合金常见的铸造方法:低压铸造、差压铸造、石膏精密铸造、真空吸铸造等先进的铸造方法已用于铝合金铸造。
铝及铝合金的分类:铸造铝合金:目前现有的分为Al-Si系,(含Si量4%—22%)Al-Cu系(含Cu 量3%—11%),Al-Mg系(含Mg有4%—11%),Al-Zn系(10%以上,)Al-RE系5类。
变形铝合金:(又称加工铝合金)主要通过锻造,滚轧,辗压,挤压等方式给铝合金施以外力,我国的变形铝合金牌号是怎样表示的:根据GB∕T16474-1996“变形铝及铝合金牌号表示方法”,凡是化学成份与变形铝及铝合金国际牌号注册协议组织命名的合金相同的所有合金,采用4位字符牌号命名,第1、2、3、4位为阿拉伯数字,第2位为英文大写字母(C、I、L、N、O、P、Q、Z字母除外)。
牌号的第1位数字表示铝及铝合金的组别,铝合金组别按主要元素来确定,1***为纯铝,(铝含量不小于99.00%),2***是以铜为主要合金元素的铝合金,3***是以锰为主要合金元素的铝合金,4***是以硅为主要合金元素的铝合金,5***是以镁为主要合金元素的铝合金,6***镁和硅为主要合金元素并以Mg2Si相为强化相的铝合金,7***是以锌为主要合金元素的铝合金,8***是以其它合金元素为主要的铝合金,9***为备用合金组。
如:1060是最低铝含量为99.6%的工业纯铝。
1035工业纯铝是一种铝含量大于99。
50%的电工铝,其中有3种杂质应受到控制,即ω(V+Ti)≦0.02%,ω(B) ≦0.05%,ω(Ga)≦0.03%。
Al-Si铝合金其含Si量4~~22%,我国有18种。
结合我公司产品针对不同的合金使用不同的熔剂,通常根据变质方法来确定,如:使用Sr,Na,变质可使用通用型熔剂,使用P变质使用无钠型熔剂。
一般使用熔剂有:高温和低温是根据各个生产工艺来制定。
变形铝合金推荐产品有:AJ2,AZ1,AF1,(无钠型)以及元素添加剂和细化剂,微量元素与杂质对铝合金性能的影响1:Na(钠)Na可以把共晶Si的晶粒细化并变成粒状,使强度和韧性都获得很大的提高质,所以从此便出现了变处理。
金属熔炼与铸锭 第三讲 熔炼的基本任务要求及工艺规程

熔铸的基本任务
(2)配制所需的各种合金 因为大多数纯金属存在力学性能等方面 的缺陷,在实际生产生活中往往需要使用以 纯金属为基体的合金材料。因此,必须通过 熔炼过程,才能有效地将各种所需的合金配 料,如将铜、镁、锰等元素加入铝中制成铝 合金;将锌、锡、镍等元素加入铜中制成铜 合金。 合金元素通常以什么形式加入?
CCl6、CCl4、NaF
熔铸工艺规程(燃油炉)
(1)生产前的准备工作
1) 检查贮油罐油位、燃烧器、油枪、炉门、铸造平台, 供水系统等;2) 必要时应烘炉。
熔铸工艺确定及配料计算; 2) 金属锭、中间合金准备; 3)覆盖剂、精炼剂、打渣剂准备。
熔铸工艺规程
熔铸的基本任务
(5)控制铸锭的结晶组织、形态及分布 铸锭不同的结晶组织、晶粒形态与分布等对压 力加工工艺性能、使用性能有着很大的影响。 通过适当的工艺措施控制铸锭的结晶组织、晶 粒形态及分布以获得加工工艺性能、使用性能良好 的铸锭组织,一般而言,铸锭晶粒越细小越好。
熔铸的基本任务
(6)重熔回收各种废料 回收废料混杂,通过重熔可以获得明确的化学 成分,并铸成适于再次入炉的锭块。熔铸车间最后 的产品是铸锭,无论铸锭的形状、尺寸及用途如何 不同,但对质量的要求是相同的。
第二节 熔铸的基本要求
熔铸的基本要求
(1) 化学成分控制:包括主要成分范围及 杂质最大允许量、成分均匀性等,应符合规 定的标准范围,保证制品的力学性能和工艺 性能。 铝合金手册成分标准
实现的途径
原材料纯化 正确的配料计算 完善防止烧损的措施 熔炼者的经验 工具干净程度
……
熔铸的基本要求
熔铸工艺规程
(8) 均质 消除成分偏析,使铸锭成分均匀化。
大规格TA10钛合金铸锭生产工艺研究
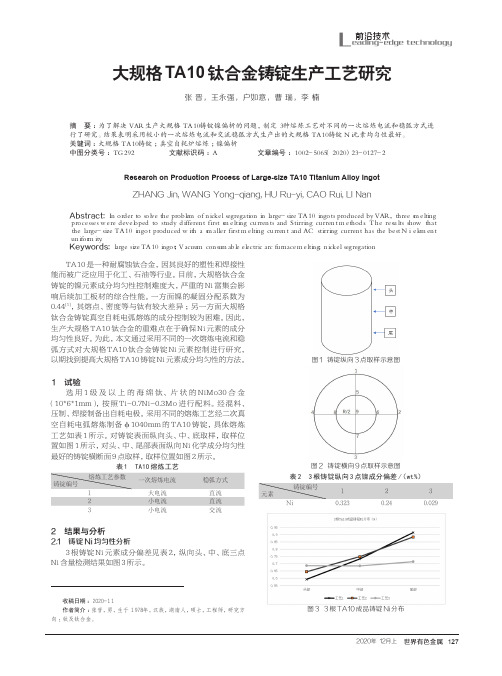
127前沿技术L eading-edge technology大规格TA10钛合金铸锭生产工艺研究张 晋,王永强,户如意,曹 瑞,李 楠(新疆湘润新材料科技有限公司,新疆 哈密 839000)摘 要:为了解决VAR生产大规格TA10铸锭镍偏析的问题,制定3种熔炼工艺对不同的一次熔炼电流和稳弧方式进行了研究。
结果表明采用较小的一次熔炼电流和交流稳弧方式生产出的大规格TA10铸锭Ni元素均匀性最好。
关键词:大规格TA10铸锭;真空自耗炉熔炼;镍偏析中图分类号:TG292 文献标识码:A 文章编号:1002-5065(2020)23-0127-2Research on Production Process of Large-size TA10 Titanium Alloy IngotZHANG Jin, WANG Yong-qiang, HU Ru-yi, CAO Rui, LI Nan(Xinjiang New Material Technology Co., Ltd.,Hami 839000,China)Abstract: In order to solve the problem of nickel segregation in large-size TA10 ingots produced by VAR, three smelting processes were developed to study different first smelting currents and Stirring current methods. The results show that the large-size TA10 ingot produced with a smaller first melting current and AC stirring current has the best Ni element uniformity.Keywords: large size TA10 ingot; Vacuum consumable electric arc furnace melting; nickel segregationTA10是一种耐腐蚀钛合金,因其良好的塑性和焊接性能而被广泛应用于化工、石油等行业。
铸造有色合金及其熔炼
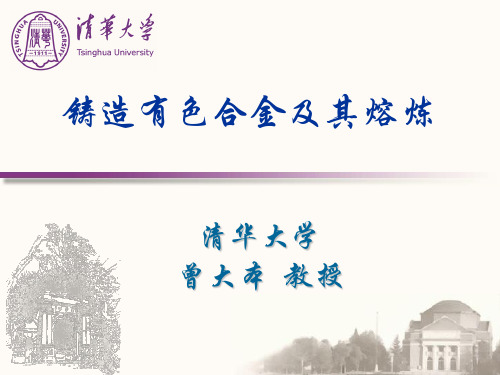
2. 铸造有色合金
——以一种有色金属为基础,加入另一种或几种其他元素, 使之熔合一起,构成新的金属组成物。 有色合金(又称非铁合金)分为:形变合金 铸造合金 1)铸造铝合金、铸造镁合金——密度小、比强度高 2)铜合金——优良导电、导热性能,良好耐蚀性、耐磨性 及力学性能 3)钛合金——很高的比强度、耐蚀性 4)铸造锌合金——良好的压铸成型性能 5)锡基合金(Sn-Sb合金)、铅基合金(Pb-Sb合金)— 油润滑条件下良好的耐磨性能
Cu:>4%
要热处理
Al-Mg
Mg:>5%
合金液易氧化 铸造工艺复杂 最便宜
5
Al-Zn
Zn:5~13%
2. 铸造Al-Si合金成分、组织、性能
图 1 Al-Si二元相图
6
2.Байду номын сангаас铸造Al-Si合金成分、组织、性能
图 2 含Si量对Al-Si二元合金铸造性能的影响
7
2. 铸造Al-Si合金成分、组织、性能
10
2.1 Al-Si合金的变质
其它变质剂: 锶(Sr)变质:加入0.02~0.06%Sr,(720℃,Al-Sr合金)
长效6~8小时,缺点形成SrH,除氢不易,且易产生铸型反应,易 产生针孔。
锑(Sb)变质
稀土元素变质
精炼—变质剂(复合作用)
过共晶Al-Si合金变质:P-Cu合金(含P10%),加1%
14
2.4 Al-Si铸造合金中有害杂质
Fe 来自坩埚、熔炼工具和炉料,形成Al3Fe、 α(Al12Fe3Si)和粗大针状的脆性β (Al9Fe2Si2)等相, 它们大大削弱基体,降低塑性和耐蚀性。(加入 Mn<0.5%可使相减少,形成新的复杂多元化合物) Sn、Pb 它们在中固溶度很小,形成共晶体的熔点 低,热处理时引起过烧,Sn还降低耐蚀性(应 ≤0.01%)。 热处理
熔炼、铸造和均质的基础理论

有色金属熔炼和铸造一. 基本原理1.熔炼和铸造的定义:熔炼的含义:就是将各种胚锭通过加温重熔的方法,实现由固态向液态转变的同时,进行合金化的过程.在熔炼的过程中,将实现净化除杂的目的.铸造的含义:将符合铸锭要求的金属熔体通过转注工具浇入到具有一定形状的铸模 中,使熔体在重力场或外力场的作用下充满模腔,冷却并凝固成型的工艺过程.它不仅要实现外部定型,而且还要实现对内部的微观组织结构的调控.二. 铝及其合金的熔炼1.熔炼的传热过程铝的熔点虽然很低(660℃),但由于熔化潜热(395.56kJ/kg)、固态热容(1.1386kJ/kg. ℃)和液态热容(1.046kJ/kg. ℃)都较高,而铝的黑度是铜铁的1/4,所以铝熔炼耗能大,很难实现理想的热效率。
热的传递方式有三种,传导、对流和辐射。
要提高金属的受热量,一方面提高炉温,这对炉体和熔体都不利,另一方面铝的黑度小,故提高辐射传热也是有限的,因此只能着眼于增大对流的传热系数(αc),它与气流速度的关系:αc=5.3+3.6v[kJ/(m2 h.℃)] V<5m/s时αc=647+v0.78 [kJ/(m2 h.℃)] V>5m/s时可见提高燃烧的气流速度是有效的。
2.合金元素的溶解和蒸发熔炼温度下(700℃)几种元素在铝中的扩散系数为(cm2/s):Ti:0.66,Mo:1.38(760℃),Co:0.79,Ni:1.44,Si:14.4,通常情况下,与铝形成易熔共晶的元素,一般较易熔解,与铝形成包晶转变的,特别是熔点相差大的元素较难于溶解。
在相同溶解条件下,一般蒸气压高的元素容易挥发,可把常用的铝合金分为两组:Cu、Cr、Fe、Ni、Ti、Si、V、Zr等元素的蒸气压比铝的小,蒸发慢,Mn、Li、Mg、Zn、Na、Cd等元素蒸气压比铝的大,容易蒸发,在熔炼过程中损失较大。
3.熔炼的吸气过程铝—氧反应金属以熔融态或半熔融态暴露于炉气中并与之相互作用时间越长,往往造成金属大量吸气,氧化和形成其它非金属夹杂,其反应分为:吸附、界面反应和熔解(扩散)。
有色金属熔铸(整理版)
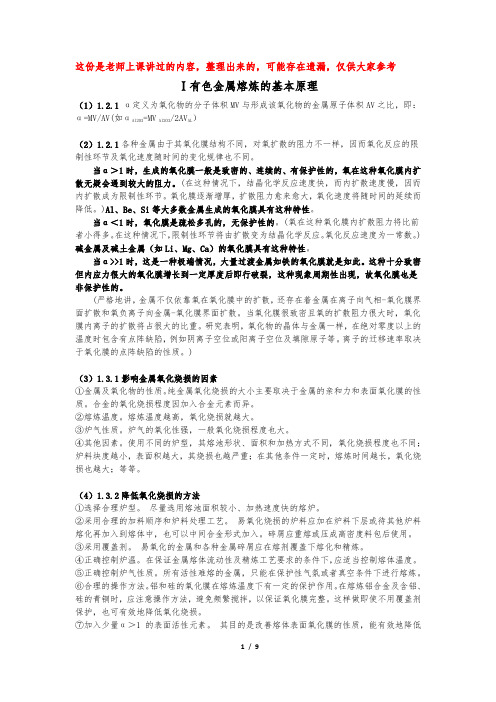
这份是老师上课讲过的内容,整理出来的,可能存在遗漏,仅供大家参考Ⅰ有色金属熔炼的基本原理(1)1.2.1 α定义为氧化物的分子体积MV与形成该氧化物的金属原子体积AV之比,即:α=MV/AV(如αAl2O3=MV Al2O3/2AV AL)(2)1.2.1各种金属由于其氧化膜结构不同,对氧扩散的阻力不一样,因而氧化反应的限制性环节及氧化速度随时间的变化规律也不同。
当α>1时,生成的氧化膜一般是致密的、连续的、有保护性的,氧在这种氧化膜内扩散无疑会遇到较大的阻力。
(在这种情况下,结晶化学反应速度快,而内扩散速度慢,因而内扩散成为限制性环节。
氧化膜逐渐增厚,扩散阻力愈来愈大,氧化速度将随时间的延续而降低。
)Al、Be、Si等大多数金属生成的氧化膜具有这种特性。
当α<1时,氧化膜是疏松多孔的,无保护性的。
(氧在这种氧化膜内扩散阻力将比前者小得多。
在这种情况下,限制性环节将由扩散变为结晶化学反应。
氧化反应速度为一常数。
)碱金属及碱土金属(如Li、Mg、Ca)的氧化膜具有这种特性。
当α>>1时,这是一种极端情况,大量过渡金属如铁的氧化膜就是如此。
这种十分致密但内应力很大的氧化膜增长到一定厚度后即行破裂,这种现象周期性出现,故氧化膜也是非保护性的。
(严格地讲,金属不仅依靠氧在氧化膜中的扩散,还存在着金属在离子向气相-氧化膜界面扩散和氧负离子向金属-氧化膜界面扩散。
当氧化膜很致密且氧的扩散阻力很大时,氧化膜内离子的扩散将占很大的比重。
研究表明,氧化物的晶体与金属一样,在绝对零度以上的温度时包含有点阵缺陷,例如阴离子空位或阳离子空位及填隙原子等。
离子的迁移速率取决于氧化膜的点阵缺陷的性质。
)(3)1.3.1影响金属氧化烧损的因素①金属及氧化物的性质。
纯金属氧化烧损的大小主要取决于金属的亲和力和表面氧化膜的性质。
合金的氧化烧损程度因加入合金元素而异。
②熔炼温度。
熔炼温度越高,氧化烧损就越大。
③炉气性质。
有色金属熔铸的基本常识

有色金属熔铸的基本常识金属熔铸的主要目的是为铸锭提供高质量的金属熔体;因此,必须研究和确定各种纯金属及其合金熔炼过程中所共同遵守的规律,为制定合理的熔铸工艺、开发新工艺和新产品以及新设备,改造老工艺、老设备以及预见性地控制生产提供理论依据。
1、化学成分的控制金属材料的组织和性能除了受工艺因素影响外,主要靠化学成分来保证。
因此准确控制熔炼的化学成分是保证熔炼质量的首要任务。
金属材料的化学成分包括主成分和杂质两部分。
1.1材料准备配制合金所用原料一般包括新金属料、回角料、中间合金等三种。
1.1.1新金属料新金属料是指冶炼厂提供纯金属,其中包括火法冶炼、蒸馏及电解精炼得到的金属。
常用的有:电解铜、锌、镁、铝、铅、锰等,他们的品位应达到国家标准。
在保证质量的前提下,选用低纯度新金属料,因价格便宜。
有色车间一般采用1#电解铜,2#、3#电解铜不能用;2#锡也不能用,杂质含量不能满足生产要求。
1.1.2回角料回角料或旧料是配制合金的主要原料之一。
有色车间青铜QSn6.5-0.1新料10%,回角料90%;黄铜新料20~30%,旧料70~80%,按照来源不同,大致分为本厂回料和厂外回料两类。
1.1.2.1本厂回料熔铸车间及加工车间所产生加工余料(即几何回料)及不合格的报废料(工艺回料),如果管理的好,这些回料通常不需要处理,就可以直接加入炉内使用。
此外,各种车、锯、铣、刨、等切屑,如有油、潮湿的要烘干、去油处理;放置过久腐蚀严重的回角料,不容易辨别、难以挑选的混合料,由于污染严重、杂质过多、质量低劣,须重熔、精炼,分析成分后才能配入原料中。
质量好的黄铜切屑,也可不往重熔配入一小部分。
1.1.2.2厂外回料这部分原料来源于各机制厂或商业部门所回收的料。
其成分复杂、杂质较多,须经重熔精炼提纯后,才能适量配入原料中。
1.1.3气体来源大气中,氢的分压极其微小,可以认为除了金属原料本身含气体外,金属熔体中的气体主要来源于与熔体接触的炉气及熔剂,工具中带入的水分和碳氢化合物等。
- 1、下载文档前请自行甄别文档内容的完整性,平台不提供额外的编辑、内容补充、找答案等附加服务。
- 2、"仅部分预览"的文档,不可在线预览部分如存在完整性等问题,可反馈申请退款(可完整预览的文档不适用该条件!)。
- 3、如文档侵犯您的权益,请联系客服反馈,我们会尽快为您处理(人工客服工作时间:9:00-18:30)。
σb Y/Mpa
全过程超声耦合处理对Al-12Si力学性能的影响
超声耦合处理的作用机制分析 (1) 关于超声耦合处理对α(Al)的影响的探讨: 在无超声耦合处理时,粗大初生α(Al)枝晶的形成与亚共晶合金类 似,都是由熔体内的Al-Al团簇直接形核长大而成的,因为在液态时, 熔体内还存在一定量的保持固态特性的Al-Al团簇,这些Al-Al团簇在非 平衡凝固过程中,就将成为α(Al)枝晶非均匀形核的核心,Al-Al团簇经 过形核长大,最终形成粗大的α(Al)枝晶。 在超声耦合处理时,由于超声空化及声流对Al-Al团簇有离解作 用,结晶核心数目增加,超声耦合处理使α(Al)晶的量增多,所以,表 现为在结晶前超声耦合处理时,使α(Al)枝晶向近等轴晶方向转化,同 时,超声的声流作用,有助于液态金属在凝固界面前沿产生较大的过 冷度,使α(Al)临界晶核半径和临界形核功减小,而超声的空化过程, 在气泡崩溃时产生的巨大冲击波击碎凝固过程中正在长大初生α(Al)树 枝晶,使其断裂及增值。因此,凝固全过程超声耦合处理时,使α(Al) 枝晶完全消失。
有抑制生长作用,表现为熔体凝固全过程超声处理使Si相破碎、熔断和细化。
Si晶体的破碎和断裂过程,也是由于声阻ZSi ZAl,Si的声压透射系数 D= 2Zsi/(ZSi+Zal)1,Si对透射声波具有声压放大作用,气泡崩溃时间极短 ,相当于绝热过程,气泡崩溃施压时,Si晶体温度上升,热流将从受压一侧流 向未受压一侧,吸收气泡崩溃时的能量并转化为热能。所以 Si的破碎和断裂可 能与气泡崩溃时的压力突变和热扰动效应有关 从微观上来说,在共晶转变时,具有小平面的相(如Si)往往都会领先长大, 而具有非小平面特性的金属相(如铝)则会随着领先相生长,一般的凝固条件下 领先相的长大范围取决于第二相沿领先相形核的难易程度,在无超声耦合处理 时,水冷铸模冷却的凝固组织,其组织特点是:初晶 Si相,分布在α-Al晶界区 域,而在超声耦合处理时,由于改善了Al熔体/Si的润湿性,有利于α(Al)依附 于Si相长大。 结论 (1)功率超声通过热机制和机械机制提高液相形核率,并具有抑制 α(Al)相长 大的作用; (2)高密度超声耦合场对实验合金的初晶Si和共晶Si组织具有双重细化作用, 组 织细化后合金的强度明显提高; (3)高而在超声耦合处理时,由于改善了Al熔体/Si的润湿性,有利于α(Al)依 附于Si相长大; (4)功率超声对组织细化,特别是破碎细化作用主要与声空化有关 。
熔体强偶合超声振动系统
合金熔化,并保温一定的时间后,将定量的金属熔体浇入铸模中,在气体保护和保温条 件下,按两种方式对Al-12Si合金进行超声处理,即:在液体状态及其凝固全过程进行超 声耦合处理(见表),并吹氩气将金属熔体冷却凝固,获得金属铸锭 表:超声耦合形式
超声耦合形式 结晶前超声处理 超声耦合过程说明 在700℃~600℃的冷却过程中,对熔体超声振动处理(约15分种),之后吹氩冷却铸锭
2.7晶粒细化标准与检测方法
细化效果的检验方法。主要包括: Alcan试验法、 KBI环模试验法、 雷诺标准高尔夫T模试验法(Reynolds Standard Golf Tee Test)、 VAW法、冷指试验法(Alcoa Cold Finger Test) [128~131]。 由于这些方法使用的工具和试验条件不同,所得到晶粒细化结果 (即晶粒尺寸)不同。因此,必须提供一个共同认可的细化试验 方法。1980年美国铝业协会通过的以Alcan试验法为蓝本的“铝合 金晶粒细化剂标准试验法TP-1”。
全过程超声处理
在700℃开始,边吹氩气冷却,边对熔体进行超声振动处理,直至完全凝固(约20分种)
在铸锭上的中间部位,截取金相试样和硬度测试试样,经过打磨抛光后,再用0. 5vol, %的HF 水溶液浸蚀, 在光学显微镜和扫描电镜下观察组织,并在打磨的试样 上进行显微硬度测试。
结晶前超声耦合处理的合金组织 (a)- 声强I=1W/cm3, (b)-声强I=2W/cm3, (c)- 声强I=4W/cm3, (d)- 声强I=5W/cm3
试样制备、组织观察与评定:
分别在不同时间取样,例如30s、1min、2min、5min、10min、 30min、60min、90min、120min
课程总结: 专题安排:围绕熔体净化或细化的有关方法、
机理、装置等进行系统评述: 要求:A4纸15页以上; 文中含图表等内容; 能体现自己的观点,不要照搬原 文; 6月8日交稿
240 220
200 180 160 0 1 2 3 4 5 6
-2 声强 ? ? I/W/cm
声强与合金强度间的关系曲线,可 见超声对合金组织的细化作用存在 阈值声压Pt,当作用声压,合金组 织无明显变化(Si相未细化或断裂、 破碎)。当P Pt时,Si组织显著 变化,同时,随 P值变大细化程度 提高并趋于饱和。从合金性能上看, Pt附近b和存在突变,并且合金的 性能变化与性能的变化同时发生, 对此,可以间接的证明Si的组织变 化来源于超声的空化效应
(2) 关于超声耦合处理对Si相影响的探讨:
超声对近共晶成分合金凝固组织的影响,也可以通过团簇演变来解释。近共晶成分Al-12Si 合金熔体内存在少量的Si-Si原子团簇,由于Si-Si键能很高,所以相比Al-Al团簇,它会在较大过 热温度区间范围内存在,因此,这些Si-Si原子团簇在较低的过热温度条件下凝固时,可以直接 成为形核成为初生硅粒子 结晶前超声耦合处理时,引起熔体原子以其平衡位臵为中心振动,原子的平均距离可能增大 到超过极限位臵,破坏了熔体的结构完整性,导致出现空位和空腔,熔体的近程有序度下降, 同时,由于超声空化及声流对Si-Si团簇的离解作用,从而使凝固组织中的初生Si粒子尺寸,逐 渐减小。甚至消除。 表为Al-Si合金中双原子键的结合强度,可见Si-Si键更加稳定,Si原子相互之间,更容易结
TP-1试验法的铸模结构图 其试验方法为:将10kg 99.7,wt.%的Al置于坩埚内加热至(718 ± 5)℃静置, 除去浮渣,但要保证液体湍动最小,水槽通水,流量约为3.8L/min,如果水流 量正确,勺底浸没入水中25mm,记录熔体温度,将预热316℃的铸模浸入Al熔 体内保持30s,将充满熔体至缺口处的铸模垂直提出,垂直放入冷却水槽的保持 环内,第一次取核对用的空白试样,之后将剩余熔体加入晶粒细化剂,并搅拌 熔体30s使晶粒细化剂合金溶解,取样前用石墨棒搅拌15s,每次取样换一个取 样铸模。在距试样底部38mm的横截面评定晶粒尺寸。
合形成Si-Si原子团簇,同时,由于硅在铝液中的扩散速度较大,共晶转变时领先析出共晶Si。
超声波辅照在Si晶核表面时,使晶核界面上的Si原子活化,而处于更高的能量状态,易于向液 相中扩散,超声波的微冲流作用,加速了Si的熔化传质过程,使Si相界面上的浓度梯度增大, Si向液相的扩散作用加激,可见超声波所具有的热机制和机械机制能提高Si晶核的核率,并
该组织特征表明,增加声强可以进一步细化Si相,使其从较粗大的针片状向细小的针片 状转化,甚至在近声场区出现了细小的颗粒状Si相组织,由于声压与熔体之间的粘滞力 相互作用,导致了超声波振幅随着作用距离的增加而衰减,可见,结晶前超声耦合处理, 能使Si相细化,但Si相基本上保持了针片状的特征。
凝固全过程超声耦合处理的合金组织-2 (a)- 声强I=5, (b)-声强I=2,