大庆石化公司闪爆事故
07年集团公司下属企业事故案例

独山子石化分公司“1.17”亡人事故2007年1月17日,独山子石化分公司铁管处在南站跨铁路灯桥进行更换故障灯作业过程中,发生一起高空坠落亡人事故。
一、事故经过1月17日,独山子石化分公司铁管处电务段开具高空作业票,更换南站灯桥的5个故障灯。
15时30分,电工殷某(男,44岁,电工)佩戴防护用品从西侧登桥作业(该灯桥全长52米,宽82厘米,距地面高度14米,桥横梁防护栏高度为1.5米,横跨七股铁道,灯桥东西两侧距末端3米处各设计有爬梯方孔洞一个,孔洞尺寸为82x50厘米,人员作业爬梯在灯桥西侧)。
电务段电工李某和南站货检员杨某在地面进行监护,殷某从西向东依次换灯,于16时30分左右更换完处于灯桥最东端故障灯,并在灯桥东端要求通电试灯。
试灯完毕后,殷某从桥东端往西折回时,从距东端3米处的爬梯预留孔洞坠地,当场死亡。
二、原因分析1、员工安全意识淡薄,基层单位存在安全工作不落实。
2、现场存在安全隐患,预留孔洞没有任何安全防护措施。
兰州石化“2.6”火灾事故的通报2007年2月6日15时15分,兰州石化公司合成橡胶厂碳四车间4.5万吨/年碳四抽提装置脱重塔(T112)塔釜再沸器(H-125D)发生火灾事故,一、事故经过2月6日,碳四车间针对H-125D换热效果差的问题,讨论分析认为是再沸器底部积水造成,并于15时左右对再沸器检查处理。
车间主任、生产副主任、工艺技术员、高级技师和2名当班操作人员共6名员工进入现场,打开倒空线排空阀门(DN50)排液,有黄色无味溶液排出,约5分钟后有少量气相物料排出即关闭阀门;为了排净残余液体,约5分钟后,再次打开倒空线排空阀门排液(阀门开度很小),发现有气相物料排出并夹带少量液体,随即关闭阀门。
所有人员正在现场讨论下一步处理方案时,突然发生着火,造成6人受轻伤。
二、事故原因根据初步调查,再沸器排出的黄色液体中可能含有丁二烯过氧化物或自聚物,并且在排放过程中夹带出顺丁烯、丁二烯等易燃易爆气体,过氧化物或自聚物遇空气氧化着火。
大庆石化10.27硫磺装置酸性水罐爆炸事故反思

大庆石化10.27硫磺装置酸性水罐爆炸事故反思2020年10月27日,我公司炼油厂硫磺回收车间发生重大火灾爆炸事故,造成7人死亡,直接经济损失192万元。
这起事故是大庆石化历史上少有的一起重大亡人责任事故,也是集团公司、股份公司2020年发生的最严重的事故之一。
事故给遇难员工及家庭带来了灾难,也给企业造成了严重的负面影响,教训十分深刻,代价十分惨痛。
事过好多年,我们回顾和反思这起事故,依然刻骨铭心,终生难忘。
一、事故的经过2020年10月20日,我公司炼油厂硫磺回收车间新建投用仅87天的酸性水汽提装置原料水罐V403罐顶与罐壁之间焊口开裂,造成装置停产。
为尽快恢复生产,炼油厂把修复工作委托给大庆石化总厂工程公司第一安装工程公司。
修复过程要将连接原料水罐V402与V403的平台及管线拆除。
10月27日8时,施工人员在车间的指导配合下,用吊车将连接V402和V406的管线吊起,管工将盲板放入法兰内,并在盲板与上法兰之间放入一根焊条以备吹扫,随后车间用氮气对该管线进行了吹扫。
8时30分,车间开具了用火票。
8时45分,吹扫完毕后,管工将法兰螺栓紧固。
9时20分左右,施工员到车间领取火票,并送给V402罐顶的气焊工。
同时,车间设备主任、设备员、监火员和操作工也到了V402罐顶。
9时40分左右,开始切割,9时44分,V402罐发生爆炸着火。
公司立即启动了事故应急预案,展开扑救工作,10时45分火被扑灭。
爆炸导致2人当场死亡,5人失踪。
10月29日13时,5名失踪人员遗体在V402罐内找到。
二、事故原因黑龙江省、股份公司事故调查组分别对事故原因进行了调查。
V402罐爆炸的原因是:罐内的爆炸性混合气体,从正在切割的DN200管线根部焊缝或罐壁与罐顶板连接焊缝开裂引起泄漏,遇到在V402罐上气割管线作业的明火或飞溅的熔渣引起爆炸。
“10.27”事故是一起典型的在装置检修过程中发生的由于违章指挥、违章作业造成的重大安全生产责任事故。
大庆石化公司“2007.6.2”闪爆事故
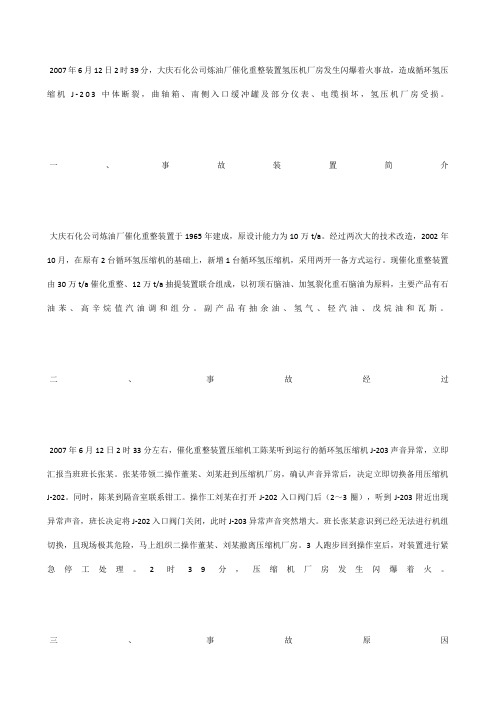
2007年6月12日2时39分,大庆石化公司炼油厂催化重整装置氢压机厂房发生闪爆着火事故,造成循环氢压缩机J-203中体断裂,曲轴箱、南侧入口缓冲罐及部分仪表、电缆损坏,氢压机厂房受损。
一、事故装置简介大庆石化公司炼油厂催化重整装置于1965年建成,原设计能力为10万t/a。
经过两次大的技术改造,2002年10月,在原有2台循环氢压缩机的基础上,新增1台循环氢压缩机,采用两开一备方式运行。
现催化重整装置由30万t/a催化重整、12万t/a抽提装置联合组成,以初顶石脑油、加氢裂化重石脑油为原料,主要产品有石油苯、高辛烷值汽油调和组分。
副产品有抽余油、氢气、轻汽油、戊烷油和瓦斯。
二、事故经过2007年6月12日2时33分左右,催化重整装置压缩机工陈某听到运行的循环氢压缩机J-203声音异常,立即汇报当班班长张某。
张某带领二操作董某、刘某赶到压缩机厂房,确认声音异常后,决定立即切换备用压缩机J-202。
同时,陈某到隔音室联系钳工。
操作工刘某在打开J-202入口阀门后(2~3圈),听到J-203附近出现异常声音,班长决定将J-202入口阀门关闭,此时J-203异常声音突然增大。
班长张某意识到已经无法进行机组切换,且现场极其危险,马上组织二操作董某、刘某撤离压缩机厂房。
3人跑步回到操作室后,对装置进行紧急停工处理。
2时39分,压缩机厂房发生闪爆着火。
三、事故原因1.直接原因切换备机J-202时,采用氢气直接置换空气,机内压力升高后,空气窜入正在运行的J-203南侧入口缓冲罐内,导致该缓冲罐内发生爆燃,氢气泄漏,造成压缩机厂房闪爆着火。
2.间接原因压缩机J-203入口缓冲罐、入口法兰螺栓存在严重制造缺陷及入口法兰垫片使用错误,导致入口缓冲罐内发生爆燃后,罐体焊缝开裂、入口法兰螺栓拉断,发生氢气泄漏。
压缩机本体存在严重缺陷:(1)J-203入口管法兰断裂螺栓金相分析表明,断裂螺栓有原始疲劳裂纹,其中一条螺栓已有很深的疲劳裂痕,只有线性连接。
大庆石油化工总厂“0.27”硫磺装置酸性水罐爆炸事故分析

大庆石油化工总厂“10.27”硫磺装置酸性水罐爆炸事故分析1.事故经过2004年10月27日,大庆石化总厂工程公司第一安装公司四分公司,在大庆石化分公司炼油厂硫磺回收车间64万吨/年酸性水汽提装置V402原料水罐施工作业时,发生了重大爆炸事故,死亡7人,造成经济损失192万元。
现将大庆石化“10.27”事故汇报如下:2004年10月20日,64万吨/年酸性水汽提装置V403原料水罐发生撕裂事故,造成该装置停产。
为尽快修复破损设备,恢复生产,大庆石化分公司炼油厂机动处根据大庆石化《关联交易合同》,将抢修作业委托给大庆石化总厂工程公司第一安装公司。
该公司接到大庆石化分公司炼油厂硫磺回收车间V403原料水罐维修计划书后,安排下属的四分公司承担该次修复施工作业任务。
修复过程中,为了加入盲板,需要将V406与V407两个水封罐,以及原料水罐V402与V403的连接平台吊下。
10月27日上午8时,四分公司施工员带领16名施工人员到达现场。
8时20分,施工员带领两名管工开始在V402罐顶安装第17块盲板。
8时25分,吊车起吊V406罐和V402罐连接管线,管工将盲板放入法兰内,并准备吹扫。
8时45分,吹扫完毕后,管工将法兰螺栓紧固。
9时20分左右,施工员到硫磺回收车间安全员处取回火票,并将火票送给V402罐顶气焊工,同时硫磺回收车间设备主任、设备员、监火员和操作工也到V402罐顶。
9时40分左右,在生产单位的指导配合下,气焊工开始在V402罐顶排气线0.8米处动火切割。
9时44分,管线切割约一半时,V402罐发生爆炸着火。
10时45分,火被彻底扑灭。
爆炸导致2人当场死亡、5人失踪。
10月29日13时许,5名失踪人员遗体全部找到。
死亡的7人中,3人为大庆石化总厂临时用工,4人为大庆石化分公司员工。
2.事故原因事故的直接原因是,V402原料水罐内的爆炸性混合气体,从与V402罐相连接的DN200管线根部焊缝,或V402罐壁与罐顶板连接焊缝开裂处泄漏,遇到在V402罐上气割DN200管线作业的明火或飞溅的熔渣,引起爆炸。
大庆石化10.27闪爆事故

炼油厂“10.27”重大火灾事故2004年10月27日9时44分,大庆石化分公司炼油厂硫磺回收车间V402原料水罐发生重大爆炸事故,死亡7人,直接经济损失192.27万元。
省政府对这起事故非常重视,刘海生副省长作了重要批示,省安全生产监督管理局、省总工会、省监察厅等有关部门人员,于当日赶赴大庆市,成立了“10.27”事故省、市联合调查组。
经过现场勘察、技术鉴定和多方取证,查清了事故原因,确定这是一起重大安全生产责任事故。
一、事故单位概况“10.27”事故涉及大庆石化分公司和大庆石化总厂两个企业。
1999年,中国石油天然气集团公司进行重组改制,将原大庆石化总厂分为上市与非上市两部分,将主要生产、销售、科研系统作为上市部分,从原大庆石化总厂分离出来,成立大庆石化分公司,隶属于中国石油天然气集团公司控股的中国石油天然气股份有限公司直属地区分公司,法人为中国石油天然气股份有限公司。
其余部分组成新的大庆石化总厂,隶属于中国石油天然气集团公司,是具有独立法人资格的单位。
重组后,于2000年开始,根据中油集团公司的要求,大庆石化总厂作为地区综合性服务公司,每年与大庆石化分公司签署一次性关联交易协议,为大庆石化分公司提供全面的工程技术、生产技术、加工制造、生活和社会服务。
2004年签订的关联交易协议中双方产品和服务项目主要包括:工程技术服务类:炼化建设(包括建筑安装)、工程质量监督等;生产服务类:通讯、消防、机械维修、机械加工等;物资供应类:代理采购、质量检验等;生活服务类;社会类服务;办公楼、土地租赁。
二、事故发生经过及抢救情况2004年10月20日,大庆石化分公司所属二级单位炼油厂的硫磺回收车间,64万吨/年酸性水汽提装置V403原料水罐发生撕裂事故,造成该装置停产。
为尽快修复破损设备,恢复生产,炼油厂机动处根据大庆石化分公司与大庆石化总厂《关联交易合同》,把抢修作业委托给大庆石化总厂工程公司第一安装工程公司。
大庆石化公司炼油厂催化重整装置氢压机厂房闪爆事故

大庆石化公司炼油厂催化重整装置氢压机厂房闪爆事故文件管理序列号:[K8UY-K9IO69-O6M243-OL889-F88688]大庆石化公司炼油厂催化重整装置“6.12”氢压机厂房闪爆事故2007年6月12日2时39分,大庆石化公司炼油厂催化重整装置氢压机厂房发生闪爆着火事故,造成循环氢压缩机J-203中体断裂,南侧入口缓冲罐、曲轴箱及部分仪表、电缆损坏,氢压机厂房受损。
现将事故情况通报如下:一、装置简介大庆石化公司炼油厂催化重整装置于1965年建成,原设计能力为10万吨/年。
此后,经过两次大的技术改造。
2002年10月,在原有两台循环氢压缩机的基础上,新增一台循环氢压缩机,采用两开一备方式运行。
现该装置由30万吨/年催化重整、12万吨/年抽提装置联合组成。
二、事故经过2007年6月12日2时33分,大庆石化公司炼油厂催化重整装置当班压缩机操作工陈月潭听到运行的循环氢压缩机J-203声音异常,立即汇报当班班长张文涛。
张文涛带领操作工董岩、刘忠立赶到氢压机厂房,确认声音异常后,决定立即切换备用压缩机J-202。
同时,陈月潭到隔音室联系钳工。
操作工董岩关闭J-202放空阀后,去一楼检查冷却水系统,刘忠立在班长指挥下打开J-202入口阀门。
稍后,J-203附近出现异常声音,班长决定将J-202入口阀门关闭。
此时,异常声音突然增大,J-203南侧入口缓冲罐附近发生泄漏。
班长张文涛意识到现场已经极其危险,无法进行机组切换,马上组织现场人跑步回到操作室,对装置进行紧急停工处理。
2时39分,氢压机厂房发生闪爆着火。
三、事故原因分析1、事故的直接原因大庆石化公司炼油厂催化重整装置岗位操作人员确认J-203有异常后,在切换备机J-202时,采用氢气直接置换J-202系统内的空气,压力升高后,J-202系统内的空气窜入正在运行的J-203南侧入口缓冲罐内,在罐内发生爆燃。
爆燃造成了缓冲罐接管焊口部位及出口法兰泄漏。
大庆石化公司“”闪爆事故

2007年6月12日2时39分,大庆石化公司炼油厂催化重整装置氢压机厂房发生闪爆着火事故,造成循环氢压缩机J-203中体断裂,曲轴箱、南侧入口缓冲罐及部分仪表、电缆损坏,氢压机厂房受损。
一、事故装置简介大庆石化公司炼油厂催化重整装置于1965年建成,原设计能力为10万t/a。
经过两次大的技术改造,2002年10月,在原有2台循环氢压缩机的基础上,新增1台循环氢压缩机,采用两开一备方式运行。
现催化重整装置由30万t/a催化重整、12万t/a抽提装置联合组成,以初顶石脑油、加氢裂化重石脑油为原料,主要产品有石油苯、高辛烷值汽油调和组分。
副产品有抽余油、氢气、轻汽油、戊烷油和瓦斯。
二、事故经过2007年6月12日2时33分左右,催化重整装置压缩机工陈某听到运行的循环氢压缩机J-203声音异常,立即汇报当班班长张某。
张某带领二操作董某、刘某赶到压缩机厂房,确认声音异常后,决定立即切换备用压缩机J-202。
同时,陈某到隔音室联系钳工。
操作工刘某在打开J-202入口阀门后(2~3圈),听到J-203附近出现异常声音,班长决定将J-202入口阀门关闭,此时J-203异常声音突然增大。
班长张某意识到已经无法进行机组切换,且现场极其危险,马上组织二操作董某、刘某撤离压缩机厂房。
3人跑步回到操作室后,对装置进行紧急停工处理。
2时39分,压缩机厂房发生闪爆着火。
三、事故原因1.直接原因切换备机J-202时,采用氢气直接置换空气,机内压力升高后,空气窜入正在运行的J-203南侧入口缓冲罐内,导致该缓冲罐内发生爆燃,氢气泄漏,造成压缩机厂房闪爆着火。
2.间接原因压缩机J-203入口缓冲罐、入口法兰螺栓存在严重制造缺陷及入口法兰垫片使用错误,导致入口缓冲罐内发生爆燃后,罐体焊缝开裂、入口法兰螺栓拉断,发生氢气泄漏。
压缩机本体存在严重缺陷:(1)J-203入口管法兰断裂螺栓金相分析表明,断裂螺栓有原始疲劳裂纹,其中一条螺栓已有很深的疲劳裂痕,只有线性连接。
大庆炼化公司爆炸事故
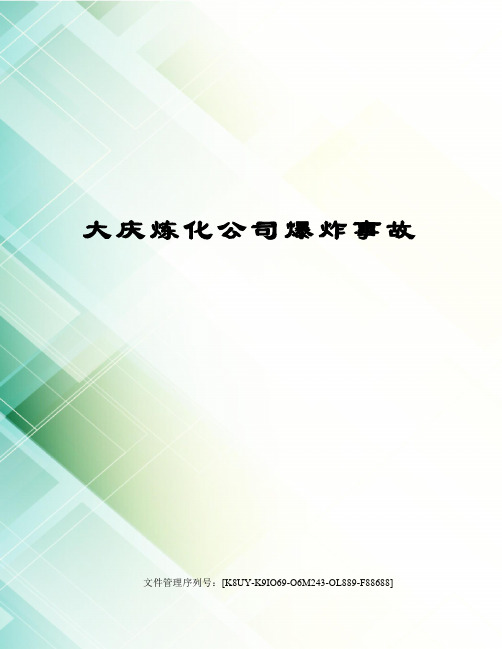
大庆炼化公司爆炸事故文件管理序列号:[K8UY-K9IO69-O6M243-OL889-F88688]2006年8月14日18时16分,大庆炼化公司炼油二厂180万t/aARGG 分馏塔顶气液分离罐和气压机出口放火炬罐发生爆炸着火事故。
事故造成3人死亡、2人重伤。
一、事故装置简介大庆炼化公司炼油二厂180万t/aARGG装置,于1999年10月建成投产。
该装置是以常压重油为原料,主要是生产汽油和富含丙烯的液化气等,是目前国内规模最大的同类型生产装置。
该装置的基本流程是:原料油进入提升管反应器,在提升管内与催化剂接触并反应,生成油气进入分馏塔,在分馏塔中根据各组分沸点的不同,分离出富气、轻柴油、重柴油和油浆。
其中,轻柴油、重柴油和油浆作为产品送罐区;富气经过冷却,液相进入吸收稳定系统,气相经气压机加压液化后送至吸收稳定系统,经过吸收、解吸和蒸馏等过程,分离成干气、液化气、稳定汽油,最后产品经精制后出装置。
二、事故经过根据安排,大庆炼化公司决定180万t/aARGG装置8月份停工检修。
计划8月12日开始停工。
检修期15天。
为推进生产操作受控管理工作,公司各装置本年度检修开停工执行“四有一卡”制度。
180万t/aARGG装置编制的停工规程于7月20日通过汇签审批。
反应再生系统于8月12日4时反应开始降量,8时30分切断进料,开始卸催化剂;13日5时卸剂工作结束;13日12时15分,反应器与分馏塔之间的油气大盲板加完,实现了反再系统和分馏系统的安全隔离。
分馏系统于8月12日8时30分开始退油;反应油气盲板加完后,分馏系统全面给汽,进行系统各条管线扫线工作。
吸收稳定系统于8月12日8时30分开始退油;13日10时50分,吸收稳定系统上水向罐区顶油气;打开3个塔安全阀副线向低瓦系统泄压;13日16时,经过水顶油,系统压力与低瓦压力平衡后,关安全阀副线,微开3个塔顶放空阀门,开始排放系统内存水;14日15时吸收稳定系统各塔给蒸汽吹扫。
大庆化工厂爆炸事件

大庆化工厂爆炸事件事件概述大庆化工厂爆炸事件是指发生在中国大庆市某化工厂的一起严重事故。
该事件发生于【事件发生日期】,造成了严重的人员伤亡和财产损失。
本文将从事件背景、原因分析以及事后应对措施等方面对该事件进行详细介绍。
事件背景大庆市是中国北方地区的一个重要化工产业基地,拥有众多的化工企业。
该化工厂是当地一家规模较大的化工企业,在当地拥有较高的知名度和影响力。
然而,由于其工艺过程的复杂性,化工厂的安全风险一直备受关注。
事件原因分析通过对该化工厂爆炸事件的调查和分析,可以得出以下原因:1. 设备老化问题据初步调查,化工厂使用的一些生产设备存在严重的老化问题。
这些老化设备无法正常运行,并且存在着较大的安全隐患。
长期以来,由于维修和更换设备的成本较高,化工厂一直未能及时对这些老化设备进行更新和改造,导致了事故的发生。
2. 生产工艺管理不严格化工厂的生产工艺非常复杂,需要进行严格的管理和监控。
然而,该化工厂在生产工艺管理方面存在一定的问题。
例如,生产过程中的操作规范不完善,对于潜在的安全风险未能及时发现和处理。
此外,工艺参数的监控不到位,也导致了事故的发生。
3. 应急预案存在缺陷灾难事件发生时,及时有效的应急预案能够最大程度地减少损失。
然而,该化工厂的应急预案存在明显的缺陷。
首先,预案的制定不够详细和完善,未能覆盖各种可能发生的灾难场景。
其次,员工对应急预案缺乏必要的培训和演练,不了解应急程序,无法迅速、有效地应对事故。
事后应对措施在发生爆炸事故后,相关部门采取了一系列的措施来应对事故和减少损失:1. 伤员救治和安置当地政府组织了大规模的救援行动,迅速将伤员送往医院进行救治。
同时,政府组织了安置工作,帮助受到影响的员工和居民找到临时住所,确保了他们的基本生活需求。
2. 调查和责任追究当地政府成立了专门的调查组对爆炸事故进行调查,并追究了责任。
通过调查,查明了事故的原因,并对相关责任人进行了严肃处理。
3. 完善安全管理措施为了预防类似事故的再次发生,政府要求化工企业全面评估和改进安全管理措施。
加氢事故案例
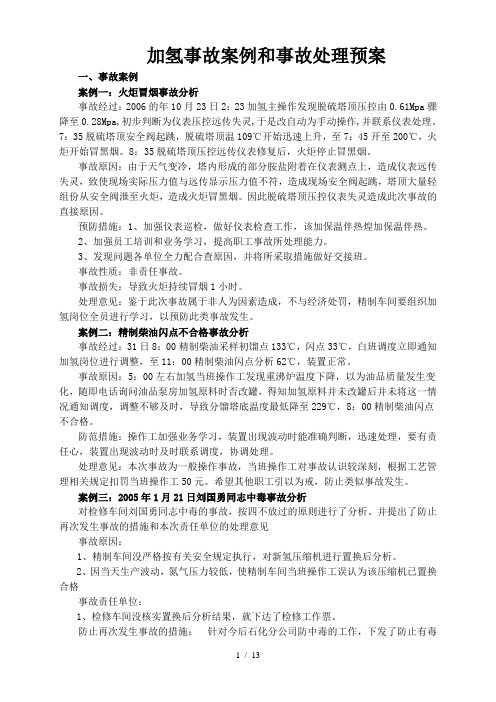
加氢事故案例和事故处理预案一、事故案例案例一:火炬冒烟事故分析事故经过:2006的年10月23日2:23加氢主操作发现脱硫塔顶压控由0.61Mpa骤降至0.28Mpa,初步判断为仪表压控远传失灵,于是改自动为手动操作,并联系仪表处理。
7:35脱硫塔顶安全阀起跳,脱硫塔顶温109℃开始迅速上升,至7:45开至200℃,火炬开始冒黑烟。
8:35脱硫塔顶压控远传仪表修复后,火炬停止冒黑烟。
事故原因:由于天气变冷,塔内形成的部分胺盐附着在仪表测点上,造成仪表远传失灵,致使现场实际压力值与远传显示压力值不符,造成现场安全阀起跳,塔顶大量轻组份从安全阀泄至火炬,造成火炬冒黑烟。
因此脱硫塔顶压控仪表失灵造成此次事故的直接原因。
预防措施:1、加强仪表巡检,做好仪表检查工作,该加保温伴热煌加保温伴热。
2、加强员工培训和业务学习,提高职工事故所处理能力。
3、发现问题各单位全力配合查原因,并将所采取措施做好交接班。
事故性质:非责任事故。
事故损失:导致火炬持续冒烟1小时。
处理意见:鉴于此次事故属于非人为因素造成,不与经济处罚,精制车间要组织加氢岗位全员进行学习,以预防此类事故发生。
案例二:精制柴油闪点不合格事故分析事故经过:31日8:00精制柴油采样初馏点133℃,闪点33℃,白班调度立即通知加氢岗位进行调整,至11:00精制柴油闪点分析62℃,装置正常。
事故原因:5:00左右加氢当班操作工发现重沸炉温度下降,以为油品质量发生变化,随即电话询问油品泵房加氢原料时否改罐,得知加氢原料并未改罐后并未将这一情况通知调度,调整不够及时,导致分馏塔底温度最低降至229℃,8:00精制柴油闪点不合格。
防范措施:操作工加强业务学习,装置出现波动时能准确判断,迅速处理,要有责任心,装置出现波动时及时联系调度,协调处理。
处理意见:本次事故为一般操作事故,当班操作工对事故认识较深刻,根据工艺管理相关规定扣罚当班操作工50元。
希望其他职工引以为戒,防止类似事故发生。
大庆石化“”火灾事故案例分析
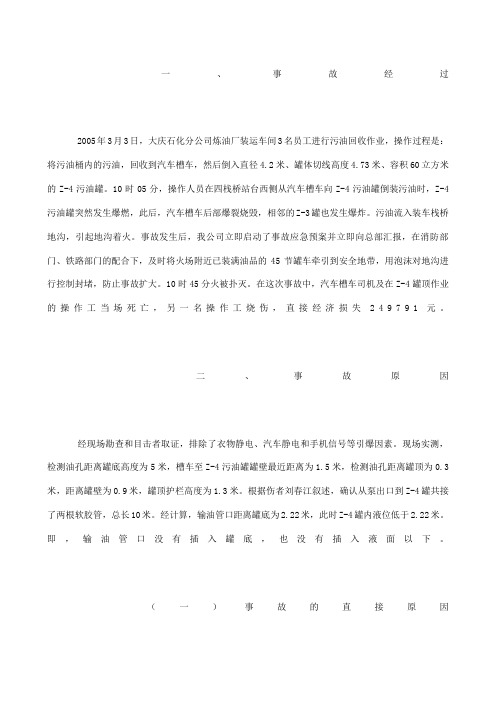
一、事故经过2005年3月3日,大庆石化分公司炼油厂装运车间3名员工进行污油回收作业,操作过程是:将污油桶内的污油,回收到汽车槽车,然后倒入直径4.2米、罐体切线高度4.73米、容积60立方米的Z-4污油罐。
10时05分,操作人员在四栈桥站台西侧从汽车槽车向Z-4污油罐倒装污油时,Z-4污油罐突然发生爆燃,此后,汽车槽车后部爆裂烧毁,相邻的Z-3罐也发生爆炸。
污油流入装车栈桥地沟,引起地沟着火。
事故发生后,我公司立即启动了事故应急预案并立即向总部汇报,在消防部门、铁路部门的配合下,及时将火场附近已装满油品的45节罐车牵引到安全地带,用泡沫对地沟进行控制封堵,防止事故扩大。
10时45分火被扑灭。
在这次事故中,汽车槽车司机及在Z-4罐顶作业的操作工当场死亡,另一名操作工烧伤,直接经济损失249791元。
二、事故原因经现场勘查和目击者取证,排除了衣物静电、汽车静电和手机信号等引爆因素。
现场实测,检测油孔距离罐底高度为5米,槽车至Z-4污油罐罐壁最近距离为1.5米,检测油孔距离罐顶为0.3米,距离罐壁为0.9米,罐顶护栏高度为1.3米。
根据伤者刘春江叙述,确认从泵出口到Z-4罐共接了两根软胶管,总长10米。
经计算,输油管口距离罐底为2.22米,此时Z-4罐内液位低于2.22米。
即,输油管口没有插入罐底,也没有插入液面以下。
(一)事故的直接原因经过认真的调查和分析,调查组确认,这起事故发生的直接原因,是作业人员违反国家《防止静电事故通用条例》、大庆石化公司《防雷、防静电安全管理规定》和车间《汽车油罐车收/倒油工作指导卡》的要求,在用车载泵向污油罐倒污油时,倒油胶管出口未插入污油罐液面,就喷溅卸油,导致污油与空气摩擦产生静电,引燃罐内气体,发生爆炸。
(二)事故的主要原因这起事故暴露出大庆石化分公司部分基层单位安全生产基础管理工作还存在薄弱环节,特别是辅助生产环节在安全生产操作规程执行上,存在着“要求不严、落实不到位”的严重问题,也暴露出以下问题:一是污油储罐设计存在缺陷。
大庆石化10.27硫磺装置酸性水罐爆炸事故反思
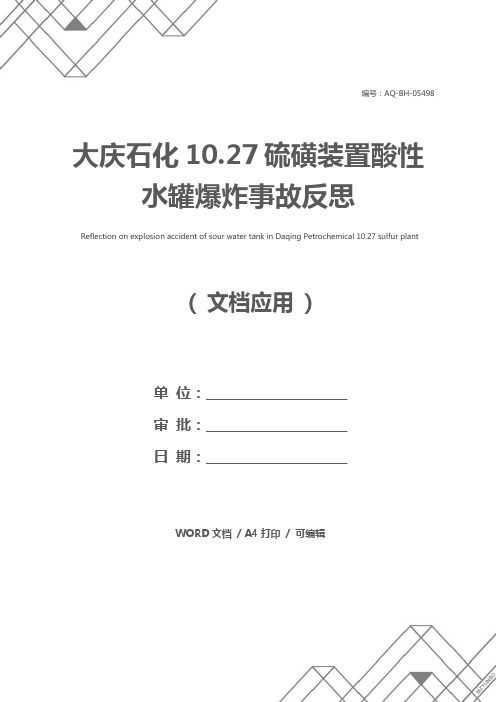
编号:AQ-BH-05498( 文档应用)单位:_____________________审批:_____________________日期:_____________________WORD文档/ A4打印/ 可编辑大庆石化10.27硫磺装置酸性水罐爆炸事故反思Reflection on explosion accident of sour water tank in Daqing Petrochemical 10.27 sulfur plant大庆石化10.27硫磺装置酸性水罐爆炸事故反思备注:每次经过学习之后总想着把自己学习到的经验记录下来,这会在潜移默化中濡染到生活中的其他事情,做事更加具有目的性,做事更加具有连贯性,不再是一股脑去做,步步摸棋。
2004年10月27日,我公司炼油厂硫磺回收车间发生重大火灾爆炸事故,造成7人死亡,直接经济损失192万元。
这起事故是大庆石化历史上少有的一起重大亡人责任事故,也是集团公司、股份公司2004年发生的最严重的事故之一。
事故给遇难员工及家庭带来了灾难,也给企业造成了严重的负面影响,教训十分深刻,代价十分惨痛。
事过好多年,我们回顾和反思这起事故,依然刻骨铭心,终生难忘。
一、事故的经过2004年10月20日,我公司炼油厂硫磺回收车间新建投用仅87天的酸性水汽提装置原料水罐V403罐顶与罐壁之间焊口开裂,造成装置停产。
为尽快恢复生产,炼油厂把修复工作委托给大庆石化总厂工程公司第一安装工程公司。
修复过程要将连接原料水罐V402与V403的平台及管线拆除。
10月27日8时,施工人员在车间的指导配合下,用吊车将连接V402和V406的管线吊起,管工将盲板放入法兰内,并在盲板与上法兰之间放入一根焊条以备吹扫,随后车间用氮气对该管线进行了吹扫。
8时30分,车间开具了用火票。
8时45分,吹扫完毕后,管工将法兰螺栓紧固。
9时20分左右,施工员到车间领取火票,并送给V402罐顶的气焊工。
典型事故案例分析--违章动火作业

一是严格执行动火作业票证管理制度,按照分级管理的要求,落实动火审批程序,加强作业环境危害因素辨识、分析和评估, 采取有效防范措施,确保作业风险可控。
二是进一步明确动火作业中监火人员、施工人员职责,规范作业中临时变更管理,加强作业过程监管,强化程序化、标准化作 业,杜绝违章操作、违规操作。
7人死亡。 二.原因分析
(一)直接原因:
V402原料水罐内的爆炸性混合气体,从与V402罐相连接的DN200管线根部焊缝或V402罐壁与罐顶板连接焊缝开裂处泄漏, 遇到在
V402罐上气割DN200管线作业的明火或飞溅的熔渣,引起爆炸。 (二)间接原因:
1.V403罐检修方案作业危害因素分析不到位。V403罐检修方案没有考虑到与之相连的V402酸性水罐的风险,没有制定针对性 防控措施;施工人员对V402酸性水罐存在的风险不清楚,对现场危害认识不足,没有制定针对性管控措施。 2.动火作业管理制度执行不严。作业人员在未对动火点进行气体采样分析、未对动火作业采取有效防护措施的情况下进行动火 作业,违反作业程序。
动火作业:能直接或间接产生明火的工艺设置以外的非常规作业,如使用电焊、气焊(割)、喷灯、电钻、砂轮等进行可能产 生火焰、火花和炽热表面的非常规作业。(引自《化学品生产单位动土作业安全规程》(AQ3022-2气瓶等机具设备的检查和管理,消除设备隐患。
四是做好施工作业人员安全教育和资质审查,提高安全意识和技能,杜绝违章盲干。
五是实行动火作业分区管理,划定固定动火区域和限制动火区域,减少在运行的装置区、罐区的动火作业,降低作业风险。
五.法律法规参考
1.化学品生产单位动火作业安全规范(AQ3022-2008) 2.焊接与切割安全(GB9448-1999) 注释:
大庆炼化公司“2006.8.14”爆炸事故

大庆炼化公司“2006.8.14”爆炸事故大庆炼化公司“2006.8.14”爆炸事故2006年8月14日18时16分,大庆炼化公司炼油二厂180万t/a ARGG分馏塔顶气液分离罐和气压机出口放火炬罐发生爆炸着火事故。
事故造成3人死亡、2人重伤。
一、事故装置简介大庆炼化公司炼油二厂180万t/a ARGG装置,于1999年10月建成投产。
该装置是以常压重油为原料,主要是生产汽油和富含丙烯的液化气等,是目前国内规模最大的同类型生产装置。
该装置的基本流程是:原料油进入提升管反应器,在提升管内与催化剂接触并反应,生成油气进入分馏塔,在分馏塔中根据各组分沸点的不同,分离出富气、轻柴油、重柴油和油浆。
其中,轻柴油、重柴油和油浆作为产品送罐区;富气经过冷却,液相进入吸收稳定系统,气相经气压机加压液化后送至吸收稳定系统,经过吸收、解吸和蒸馏等过程,分离成干气、液化气、稳定汽油,最后产品经精制后出装置。
二、事故经过根据安排,大庆炼化公司决定180万t/a ARGG装置8月份停工检修。
计划8月12日开始停工。
检修期15天。
为推进生产操作受控管理工作,公司各装置本年度检修开停工执行“四有一卡”制度。
180万t/a ARGG装置编制的停工规程于7月20日通过汇签审批。
反应再生系统于8月12日4时反应开始降量,8时30分切断进料,开始卸催化剂;13日5时卸剂工作结束;13日12时15分,反应器与分馏塔之间的油气大盲板加完,实现了反再系统和分馏系统的安全隔离。
分馏系统于8月12日8时30分开始退油;反应油气盲板加完后,分馏系统全面给汽,进行系统各条管线扫线工作。
吸收稳定系统于8月12日8时30分开始退油;13日10时50分,吸收稳定系统上水向罐区顶油气;打开3个塔安全阀副线向低瓦系统泄压;13日16时,经过水顶油,系统压力与低瓦压力平衡后,关安全阀副线,微开3个塔顶放空阀门,开始排放系统内存水;14日15时吸收稳定系统各塔给蒸汽吹扫。
大庆石化分公司“1027”硫黄装置酸性水罐爆炸事故

大庆石化分公司“10?27”硫黄裝置酸性水罐爆炸事故2004年10月27日,大庆石化分公司炼油厂硫黄回收车间发生重大火灾爆炸事故,造成7人死亡,直接经济损失192万元。
这起事故是大庆石化历史上少有的一起重大亡人责任事故,也是集团公司、股份公司2004年发生的最严重的事故之一。
事故给遇难员工及家庭带来了灾难,也给企业造成了严重的负面影响.教训十分深刻,代价十分惨痛。
一、事故经过2004年10月20日,大庆石化分公司炼油厂硫黄回收车间新建投用仅87天的酸性水汽提装置原料水罐V403罐顶与罐壁之间焊口开裂,造成装置停产。
为尽快恢复生产,炼油厂把修复工作委托给大庆石化总厂工程公司第一安装工程公司。
修复过程要将连接原料水罐V402与V403的平台及管线拆除。
10月27日8时,施工人员在车间的指导配合下,用吊车将连接V402和V406的管线吊起,管工将盲板放入法兰内,并在盲板与上法兰之间放入一根焊条以备吹扫.随后车间用氮气对该管线进行了吹扫。
8时30分,车间开具了用火票。
8时45分,吹扫完毕后,管工将法兰螺栓紧固。
9时20分左右.施工员到车间领取火票,并送给V402罐顶的气焊工。
同时,车间设备主任、设备员、监火员和操作工也到了V402罐顶。
9时40分左右,开始切割,9 时44分,V402罐发生爆炸着火。
公司立即启动了事故应急预案.展开扑救工作.10时45分火被扑灭。
爆炸导致2人当场死亡,5人失踪。
10月29日13时,5 名失踪人员遗体在V402罐内找到。
二、事故原因分析黑龙江省、股份公司事故调查组分别对事故原因进行了调査。
V4O2罐爆炸的原因是:罐内的爆炸性混合气体,从正在切割的DN200管线根部焊缝或罐壁与罐顶板连接焊缝开裂处引起泄漏. 遇到在V402罐上气割管线作业的明火或飞溅的熔渣引起爆炸。
“10 ? 27”事故是一起典型的在装置检修过程中发生的由于违章指挥、违章作业造成的重大安全生产责任事故。
主要原因有:①??? V403罐顶开裂,没有査清原因就急于组织修复。
大庆石化“”裂解炉管烧断事故
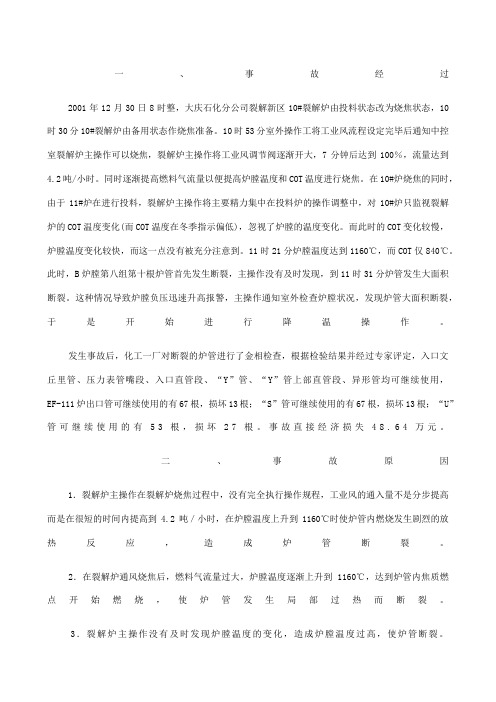
一、事故经过2001年12月30日8时整,大庆石化分公司裂解新区10#裂解炉由投料状态改为烧焦状态,10时30分10#裂解炉由备用状态作烧焦准备。
10时53分室外操作工将工业风流程设定完毕后通知中控室裂解炉主操作可以烧焦,裂解炉主操作将工业风调节阀逐渐开大,7分钟后达到100%,流量达到4.2吨/小时。
同时逐渐提高燃料气流量以便提高炉膛温度和COT温度进行烧焦。
在10#炉烧焦的同时,由于11#炉在进行投料,裂解炉主操作将主要精力集中在投料炉的操作调整中,对10#炉只监视裂解炉的COT温度变化(而COT温度在冬季指示偏低),忽视了炉膛的温度变化。
而此时的COT变化较慢,炉膛温度变化较快,而这一点没有被充分注意到。
11时21分炉膛温度达到1160℃,而COT仅840℃。
此时,B炉膛第八组第十根炉管首先发生断裂,主操作没有及时发现,到11时31分炉管发生大面积断裂。
这种情况导致炉膛负压迅速升高报警,主操作通知室外检查炉膛状况,发现炉管大面积断裂,于是开始进行降温操作。
发生事故后,化工一厂对断裂的炉管进行了金相检查,根据检验结果并经过专家评定,入口文丘里管、压力表管嘴段、入口直管段、“Y”管、“Y”管上部直管段、异形管均可继续使用,EF-111炉出口管可继续使用的有67根,损坏13根;“S”管可继续使用的有67根,损坏13根;“U”管可继续使用的有53根,损坏27根。
事故直接经济损失48.64万元。
二、事故原因1.裂解炉主操作在裂解炉烧焦过程中,没有完全执行操作规程,工业风的通入量不是分步提高而是在很短的时间内提高到4.2吨/小时,在炉膛温度上升到1160℃时使炉管内燃烧发生剧烈的放热反应,造成炉管断裂。
2.在裂解炉通风烧焦后,燃料气流量过大,炉膛温度逐渐上升到1160℃,达到炉管内焦质燃点开始燃烧,使炉管发生局部过热而断裂。
3.裂解炉主操作没有及时发现炉膛温度的变化,造成炉膛温度过高,使炉管断裂。
4.10#炉投入烧焦状态以后,主操作过多地进行11#炉的投料操作,而对烧焦炉的全部操作参数监视不够,在炉膛温度上升过程中没有及时发现可能的超温情况,没能进行及时调整。
- 1、下载文档前请自行甄别文档内容的完整性,平台不提供额外的编辑、内容补充、找答案等附加服务。
- 2、"仅部分预览"的文档,不可在线预览部分如存在完整性等问题,可反馈申请退款(可完整预览的文档不适用该条件!)。
- 3、如文档侵犯您的权益,请联系客服反馈,我们会尽快为您处理(人工客服工作时间:9:00-18:30)。
大庆石化公司闪爆事故文件管理序列号:[K8UY-K9IO69-O6M243-OL889-F88688]
2007年6月12日2时39分,大庆石化公司炼油厂催化重整装置氢压机厂房发生闪爆着火事故,造成循环氢压缩机J-203中体断裂,曲轴箱、南侧入口缓冲罐及部分仪表、电缆损坏,氢压机厂房受损。
一、事故装置简介
大庆石化公司炼油厂催化重整装置于1965年建成,原设计能力为10万t/a。
经过两次大的技术改造,2002年10月,在原有2台循环氢压缩机的基础上,新增1台循环氢压缩机,采用两开一备方式运行。
现催化重整装置由30万t/a催化重整、12万t/a抽提装置联合组成,以初顶石脑油、加氢裂化重石脑油为原料,主要产品有石油苯、高辛烷值汽油调和组分。
副产品有抽余油、氢气、轻汽油、戊烷油和瓦斯。
二、事故经过
2007年6月12日2时33分左右,催化重整装置压缩机工陈某听到运行的循环氢压缩机J-203声音异常,立即汇报当班班长张某。
张某带领二操作董某、刘某赶到压缩机厂房,确认声音异常后,决定立即切换备用
压缩机J-202。
同时,陈某到隔音室联系钳工。
操作工刘某在打开J-202入口阀门后(2~3圈),听到J-203附近出现异常声音,班长决定将J-202入口阀门关闭,此时J-203异常声音突然增大。
班长张某意识到已经无法进行机组切换,且现场极其危险,马上组织二操作董某、刘某撤离压缩机厂房。
3人跑步回到操作室后,对装置进行紧急停工处理。
2时39分,压缩机厂房发生闪爆着火。
三、事故原因
1.直接原因
切换备机J-202时,采用氢气直接置换空气,机内压力升高后,空气窜入正在运行的J-203南侧入口缓冲罐内,导致该缓冲罐内发生爆燃,氢气泄漏,造成压缩机厂房闪爆着火。
2.间接原因
压缩机J-203入口缓冲罐、入口法兰螺栓存在严重制造缺陷及入口法兰垫片使用错误,导致入口缓冲罐内发生爆燃后,罐体焊缝开裂、入口法兰螺栓拉断,发生氢气泄漏。
压缩机本体存在严重缺陷:
(1)J-203入口管法兰断裂螺栓金相分析表明,断裂螺栓有原始疲劳裂纹,其中一条螺栓已有很深的疲劳裂痕,只有线性连接。
查阅J-203原图纸,入口法兰采用金属缠绕垫片,而厂家原始供货采用的是石棉垫片。
(2)J-203压缩机断裂缸体支撑板的固定螺栓金相分析表明,三条螺栓全部存在疲劳裂纹,螺栓断口50%为疲劳断裂。
(3)对J-203南侧入口缓冲罐进行失效分析,发现罐体有5处裂纹。
检验分析结果表明,该缓冲罐内部压力有突升迹象,即受到过内力冲击。
而该缓冲罐处于压缩机入口端,正常运行时没有造成内部超压的可能,而厂房爆炸时的冲击波也只能使该罐形成外部受压。
因此,也只有缓冲罐内部气体发生爆燃时才可能引起罐内瞬间超压。
同时检验结果也表明,该罐体原始焊接工艺质量较差,焊口严重不合格,在冲击荷载作用下,容易穿透产生裂纹。
(4)该压缩机自2002年10月安装运行,到事故发生前总计维修5次。
其中,处理轴瓦故障3次(2005年1月28日曲轴裂纹补焊一次,2006年6月21日曲轴断裂,更换新轴)。
四、防范措施
1.操作人员的综合素质不高,培训工作还需加强。
事故中表现出岗位操作人员操作技能不强。
压缩机有异常现象后,岗位人员不能做到正确判断,在事故发生前,对事故可能发生的结果估计不足,没能正确进行停机处理,造成了事故的扩大。
这些充分说明员工的日常技术培训不够。
为此,要加强对操作人员的综合业务素质训练,结合生产实际,提高员工日常操作和应急突发状态能力。
2.必须高度重视压缩机置换操作缺陷。
此压缩机系统从1965年装置建成运行至今,一直采用氢气直接置换空气的操作。
装置2002年改造时虽然增设了氮气置换系统,但日常却盲断,对此问题没有引起足够的重视,给安全生产带来了较大威胁。
要对公司类似工艺问题进行彻底清查,按照“谁主管、谁负责”的原则,组织专业技术人员对同类事故隐患进行风险评价和整改方案论证,建立各类事故隐患监控管理台账,充分利用大检修的有利时机,优先解决直接危及安全生产的重点事故隐患,清查设计缺陷,立即整改,避免同类事故的发生。
3.提高设备的可靠性,保证设备的本质安全。
该机组自2002年10月投入使用以来,5年累计运行13500h,共计维修5次,且压缩机入口缓冲罐的材质及焊接、入口法兰螺栓、支撑板固定螺栓、垫片都存在缺陷。
该压缩机只有油压、油温紧急联锁停车措施,无机组振动联锁保护停车措施。
这些充分说明该设备本质安全没能得到保证,存在事故隐患。
因此,要加强对设备基础工作的管理,严把设备设计、施工、审查关。
要完善各种设备技术档案,尤其是关键设备和重点危险部位的设备技术档案,要明确记载设备改造、更新等各种变更前后的技术内容,严格依照有关设备检测规程和特殊生产工艺、物料设备的安全要求,制定完整的设备检验检测计划,并严格执行。
4.员工缺少大型设备操作的演练,必须有针对性地进行训练。
此次事故发现员工在切换大型机组的过程中,应急应变能力较为薄弱,说明日常应急演练往往只重视中毒、火灾等事故的应急培训演练,缺乏对大型运转设备开停机操作的培训演练。
而员工恰恰因缺乏这方面的实际训练,遇到紧急情况时如没有管理人员在场就表现慌乱,最终因生产问题处理不当引发了安全事故。
5.生产受控工作不到位。
事故的发生,反映出生产受控工作还只停留在口头上,停留在文件上。
而员工在进行生产操作时只是凭经验,没有严格履行操作卡程序,没有经过步步确认。
因此,当前的工作重心是把生产受控工作落到实处,真正按“四有工作法”去做,各级管理及操作人员要提高认识,认真落实,严格执行,从根本上避免操作事故的发生。