常用退火方法和退火精品
常用退火方法和退火演示幻灯片
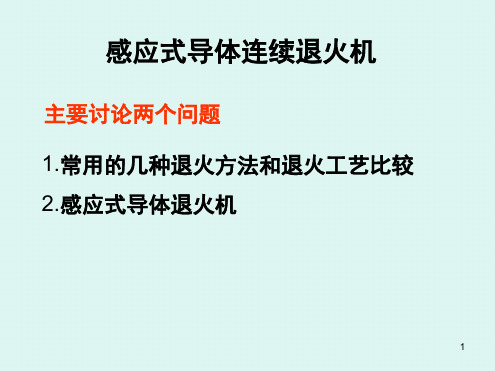
1.3 建议:由于真空退火炉工艺落后,能耗大,产品 质量不稳定,生产成本高,市场竞争能力低,建议 尽快淘汰真空退火炉。
退
轴
火
承
管
电
源
电 极 轮
图6 接触式水银传输大电流原理
11
4. 接触式水银传输大电流式退火机
? 4.1 优点:与接触式电刷传输退火电流相比, 阻力有较大的减少;与真空炉和管道炉相 比,能耗有了较大的降低;由于水银导电 不如电刷导电的接触电阻小,因而水银传 输电流比电刷传输电流的能耗稍大。但设 备制造成本相对低一些。
1
电极轮
退火管 电极轮
冷却水
变压器 可 调
压 电 源
电 极 轮
电轴 刷承
退 火 管
2 放线盘
收线盘
图3 接触式电刷传输大电流退火机
电 极 轮
图4 接触式电刷传输大电流原理
9
3 接触式电刷传输大电流退火机
? 3.1 优点:比较节能;实现了高速连续退火;导体的柔软 度比较均匀;退火电压可以跟踪退火速度。
? 3.2 缺点:电刷和电极轮间、电极轮和导线间会出现打火, 影响导线表面质量;由于靠电刷传输电流,电极轮的阻力 大,退火导线会拉细,线径得不到保障;电极轮与退火导 线间有相对运动,因此导轮磨损大。即使电极轮增加了动 力驱动,线速度的同步问题仍是难题。
? 3.3 建议:采用直流电机或变频调速系统作动力驱动,加 装储线器来补偿线速度的不同步。最好更换感应式退火机。 感应式退火机阻力很小,不需要动力驱动。
常用热处理方法
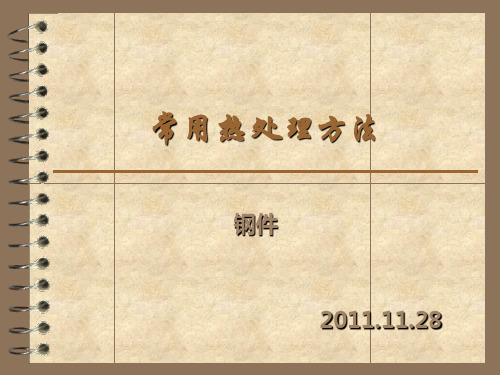
3.淬火 3.淬火
钢的淬透性概念 定义:淬透性是指钢获得淬硬层深度的能力。 按理,淬硬层的深度应该是全淬成马氏体的深度,但实际上,一般 规定从工件表层深入到半马氏体区(马氏体与非马氏体组织各占一半的地 方易测定硬度)的深度为淬硬层深度。淬硬层越深,就表明钢的淬透性越 好,如果淬硬层深度达到心部,则表明该钢全部淬透。 钢的淬透性好坏对机械性能影响很大,但并非所有的机械零件都必须完 全淬透。例如,承受弯、扭应力的轴类零件,表面热处理的零件等,只 需要一定深度的淬硬层就已满足使用要求, 钢的淬透性主要决定于临界冷却速度,临界冷却速度越小,钢的淬 透性就越好,反之,则降低钢的淬透性。除Co以外,大多数合金元素都 能显著提高钢的淬透性。 注意:淬透性和淬硬性是两个不同的概念,不可混淆。淬硬性是指淬火 后获得的最高硬度,主要取决于马氏体中的含碳量。淬透性好的钢,它 的淬硬性不一定高。如高碳工具钢与低碳合金钢相比,前者淬硬性高但 淬透性低,后0
6.钢的淬火和回火工艺 钢的淬火和回火工艺
钢的淬火和回火工艺 序号 1 2 3 4 5 6 钢号 35 45 60 85 35CrMoA 35CrMo 40Cr 50CrV 65Mn GCr15 2Cr13 淬火 温度 840-860 820-840 810-830 800-820 870-890 840-860 840-860 840-860 820-850 980-1000 回火 温度°C 200-250 350-400 180-250 340-360 400-440 180-200 400-450 180-200 430-450 360-400 160-180 560-580 530-550 510-530 530-550 520-540 380-400 520-540 硬度HRC 冷却方法 空气 空气 空气 空气 空气 空气、油 空气、油 空气 空气 油 ≥40 40-45 ≥45 37-42 40-55 35-45 40-50 42-47 46-50 58-63 31-35 小件空冷 36-40 41-45 36-40 淬火后硬度HRc52-60 41-45 46-50 43-49 淬火后硬度HRc52-60 备注 淬火介质 盐水 盐水 水 水 油 油 油 油 油 油
名词解释热处理中的退火
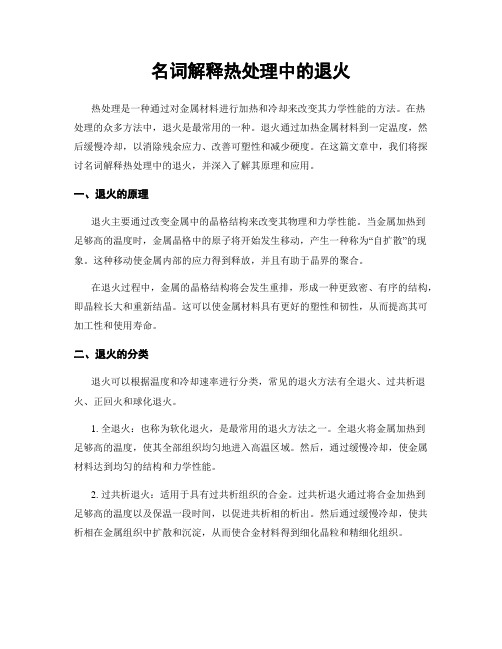
名词解释热处理中的退火热处理是一种通过对金属材料进行加热和冷却来改变其力学性能的方法。
在热处理的众多方法中,退火是最常用的一种。
退火通过加热金属材料到一定温度,然后缓慢冷却,以消除残余应力、改善可塑性和减少硬度。
在这篇文章中,我们将探讨名词解释热处理中的退火,并深入了解其原理和应用。
一、退火的原理退火主要通过改变金属中的晶格结构来改变其物理和力学性能。
当金属加热到足够高的温度时,金属晶格中的原子将开始发生移动,产生一种称为“自扩散”的现象。
这种移动使金属内部的应力得到释放,并且有助于晶界的聚合。
在退火过程中,金属的晶格结构将会发生重排,形成一种更致密、有序的结构,即晶粒长大和重新结晶。
这可以使金属材料具有更好的塑性和韧性,从而提高其可加工性和使用寿命。
二、退火的分类退火可以根据温度和冷却速率进行分类,常见的退火方法有全退火、过共析退火、正回火和球化退火。
1. 全退火:也称为软化退火,是最常用的退火方法之一。
全退火将金属加热到足够高的温度,使其全部组织均匀地进入高温区域。
然后,通过缓慢冷却,使金属材料达到均匀的结构和力学性能。
2. 过共析退火:适用于具有过共析组织的合金。
过共析退火通过将合金加热到足够高的温度以及保温一段时间,以促进共析相的析出。
然后通过缓慢冷却,使共析相在金属组织中扩散和沉淀,从而使合金材料得到细化晶粒和精细化组织。
3. 正回火:适用于高碳钢和合金钢等材料。
正回火将材料加热到临界温度以上,然后迅速冷却。
此过程会使材料的组织发生变化,降低硬度,提高塑性,并减少脆性。
4. 球化退火:球化退火主要用于冷轧钢丝等线材生产中。
球化退火通过高温加热将冷变形的钢丝塑性和韧性恢复到最佳状态。
这个过程会使钢丝的晶粒细化,松弛应力,并达到球状的形态。
三、退火的应用退火在金属材料的加工和制造过程中有着广泛的应用。
以下是退火在不同领域的一些应用示例:1. 锻造和冲压:金属在加工过程中往往会产生硬化和残余应力。
退火处理
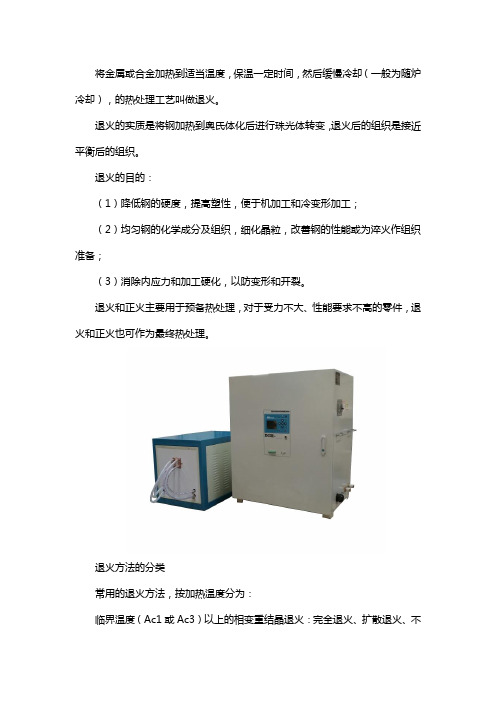
将金属或合金加热到适当温度,保温一定时间,然后缓慢冷却(一般为随炉冷却),的热处理工艺叫做退火。
退火的实质是将钢加热到奥氏体化后进行珠光体转变,退火后的组织是接近平衡后的组织。
退火的目的:(1)降低钢的硬度,提高塑性,便于机加工和冷变形加工;(2)均匀钢的化学成分及组织,细化晶粒,改善钢的性能或为淬火作组织准备;(3)消除内应力和加工硬化,以防变形和开裂。
退火和正火主要用于预备热处理,对于受力不大、性能要求不高的零件,退火和正火也可作为最终热处理。
退火方法的分类常用的退火方法,按加热温度分为:临界温度(Ac1或Ac3)以上的相变重结晶退火:完全退火、扩散退火、不完全退火、球化退火。
临界温度(Ac1或Ac3)以下的退火:再结晶退火、去应力退火。
七类退火方式1、完全退火工艺:将钢加热到Ac3以上20~30℃,保温一段时间后缓慢冷却(随炉)以获得接近平衡组织的热处理工艺(完全奥氏体化)。
完全退火主要用于亚共析钢(wc=0.3~0.6%),一般是中碳钢及低、中碳合金钢铸件、锻件及热轧型材,有时也用于它们的焊接件。
低碳钢完全退火后硬度偏低,不利于切削加工;过共析钢加热至Accm以上奥氏体状态缓慢冷却退火时,Fe3CⅡ会以网状沿晶界析出,使钢的强度、硬度、塑性和韧性显著降低,给最终热处理留下隐患。
目的:细化晶粒、均匀组织、消除内应力、降低硬度和改善钢的切削加工性。
亚共析钢完全退火后的组织为F+P。
实际生产中,为提高生产率,退火冷却至500℃左右即出炉空冷。
2、等温退火完全退火需要的时间长,尤其是过冷奥氏体化比较稳定的合金钢。
如将奥氏体化后的钢较快地冷至稍低于Ar1温度等温,是A转变为P,再空冷至室温,可大大缩短退火时间,这种退火方法叫等温退火。
工艺:将钢加热到高于Ac3(或Ac1)的温度,保温适当时间后,较快冷却到珠光体区的某一温度,并等温保持,使奥氏体转变为珠光体,然后空冷至室温的热处理工艺。
目的:与完全退火相同,转变较易控制。
连拉连退中几种常见退火工艺及比较

缺点:耗电量大,无法实现退火速度自动跟踪(退火温度不能跟随线速作及时调整)。
3、接触式电刷传输大电流退火
接触式电刷传输大电流退火设备主要由可调变压器、电刷、电极轮、冷却液、收放线装置等组成。它是利用单丝通电流时会发热这一原理来实现退火的。
我们知道,铜杆和铝杆在拉丝机上拉拔的过程中,会发生硬化、变脆,为了恢复单丝的塑性,保持良好的电气性能,因此需要将线材在一定的温度下进行热处理(退火处理)。
目前常见的退火方法有:退火炉退火,热管式退火,接触式电刷传输大电流退火和感应式退火等几种方法,下面逐一ห้องสมุดไป่ตู้析、比较各种退火方法的优缺点。
1、退火炉退火
接触式电刷传输大电流退火设备,控制退火程度的方式一般有二种:控制退火电流及控制退火电压。退火电流与退火线径的平方成正比,并与退火的速度有关(速度越快,退火电流需要越大);退火电压仅取决于退火的速度和单丝的电阻率,与线径无关。基于上述原因,所以以控制退火电压来控制单丝退火程度(单丝的断裂伸长率)的方式比较常用(公司的四台铜拉机,都常用该方式给铜丝退火)。 在铜拉设备上,我们可以看到退火电气柜和退火箱之间,有二根粗大的铜(铝)排相连接,它们传输的是较低的电压(约70伏以下,可根据铜丝的生产线速自动调整),较大的电流(数千安培),打开退火箱后方的铁门,映入眼帘的就是那密密麻麻的导电炭刷(一个电极轮上有几十块烟盒般大小的炭刷),它们负责把铜(铝)排上的电流传输到电极轮上,这样电极轮转动受到的阻力较大。
该设备的主要优点:比较节能,能够实现在线连续退火,而且退火周期较短,能够实现退火速度自动跟踪(能自动根据单丝速度调整退火电压或电流,使单丝退火程度保持一致)。
常用的几种退火方法和退火
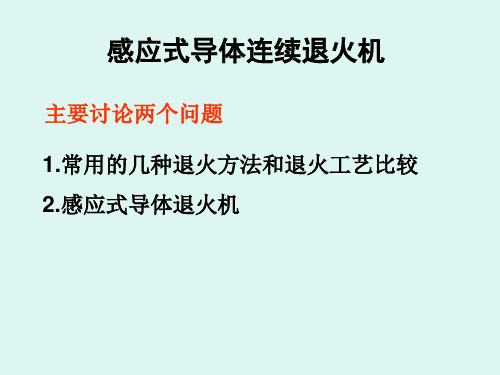
常用的退火方法和工艺有: 常用的退火方法和工艺有:(1)真空退火 ) ;(3) 炉;(2)热管式退火炉;( )接触式大电 ;( )热管式退火炉;( 流退火炉;( )感应式退火炉。其中, 流退火炉;(4)感应式退火炉。其中,接 ;( 触式大电流退火炉又分为电刷传输电流式退 火炉和水银传输电流式退火炉。 火炉和水银传输电流式退火炉。下面逐一分 析这几种退火方法和工艺的优缺点, 析这几种退火方法和工艺的优缺点,以便于 用户在选择退火设备时作参考。 用户在选择退火设备时作参考。
退火 可 调 电极轮 电 源 压
退 电 轴 火 刷 承 管
电 2 极 轮
图3 接触式电刷传输大电流退火机
图4 接触式电刷传输大电流原理
3
接触式电刷传输大电流退火机
• 3.1 优点 比较节能;实现了高速连续退火;导体的柔软 优点:比较节能 实现了高速连续退火; 比较节能; 度比较均匀;退火电压可以跟踪退火速度。 度比较均匀;退火电压可以跟踪退火速度。 • 3.2 缺点 电刷和电极轮间、电极轮和导线间会出现打火, 缺点:电刷和电极轮间 电极轮和导线间会出现打火, 电刷和电极轮间、 影响导线表面质量;由于靠电刷传输电流, 影响导线表面质量;由于靠电刷传输电流,电极轮的阻力 退火导线会拉细,线径得不到保障; 大,退火导线会拉细,线径得不到保障;电极轮与退火导 线间有相对运动,因此导轮磨损大。 线间有相对运动,因此导轮磨损大。即使电极轮增加了动 力驱动,线速度的同步问题仍是难题。 力驱动,线速度的同步问题仍是难题。 • 3.3 建议 采用直流电机或变频调速系统作动力驱动,加 建议:采用直流电机或变频调速系统作动力驱动 采用直流电机或变频调速系统作动力驱动, 装储线器来补偿线速度的不同步。最好更换感应式退火机。 装储线器来补偿线速度的不同步。最好更换感应式退火机。 感应式退火机阻力很小,不需要动力驱动。 感应式退火机阻力很小,不需要动力驱动。
退火正火淬火回火秘籍

金属热处理是将金属工件放在一定的介质中加热到适宜的温度,并在此温度中保持一定时间后,又以不同速度冷却的一种工艺方法。
金属热处理是机械制造中的重要工艺之一,与其它加工工艺相比,热处理一般不改变工件的形状和整体的化学成分,而是通过改变工件内部的显微组织,或改变工件表面的化学成分,赋予或改善工件的使用性能。
其特点是改善工件的内在质量,而这一般不是肉眼所能看到的。
为使金属工件具有所需要的力学性能、物理性能和化学性能,除合理选用材料和各种成形工艺外,热处理工艺往往是必不可少的。
钢铁是机械工业中应用最广的材料,钢铁显微组织复杂,可以通过热处理予以控制,所以钢铁的热处理是金属热处理的主要内容。
另外,铝、铜、镁、钛等及其合金也都可以通过热处理改变其力学、物理和化学性能,以获得不同的使用性能。
在从石器时代进展到铜器时代和铁器时代的过程中,热处理的作用逐渐为人们所认识。
早在公元前770~前222年,中国人在生产实践中就已发现,铜铁的性能会因温度和加压变形的影响而变化。
白口铸铁的柔化处理就是制造农具的重要工艺。
公元前六世纪,钢铁兵器逐渐被采用,为了提高钢的硬度,淬火工艺遂得到迅速发展。
中国河北省易县燕下都出土的两把剑和一把戟,其显微组织中都有马氏体存在,说明是经过淬火的。
随着淬火技术的发展,人们逐渐发现冷剂对淬火质量的影响。
三国蜀人蒲元曾在今陕西斜谷为诸葛亮打制3000把刀,相传是派人到成都取水淬火的。
这说明中国在古代就注意到不同水质的冷却能力了,同时也注意了油和尿的冷却能力。
中国出土的西汉(公元前206~公元24)中山靖王墓中的宝剑,心部含碳量为0.15~0.4%,而表面含碳量却达0.6%以上,说明已应用了渗碳工艺。
但当时作为个人“手艺”的秘密,不肯外传,因而发展很慢。
1863年,英国金相学家和地质学家展示了钢铁在显微镜下的六种不同的金相组织,证明了钢在加热和冷却时,内部会发生组织改变,钢中高温时的相在急冷时转变为一种较硬的相。
钢的常用退火工艺的分类及应用
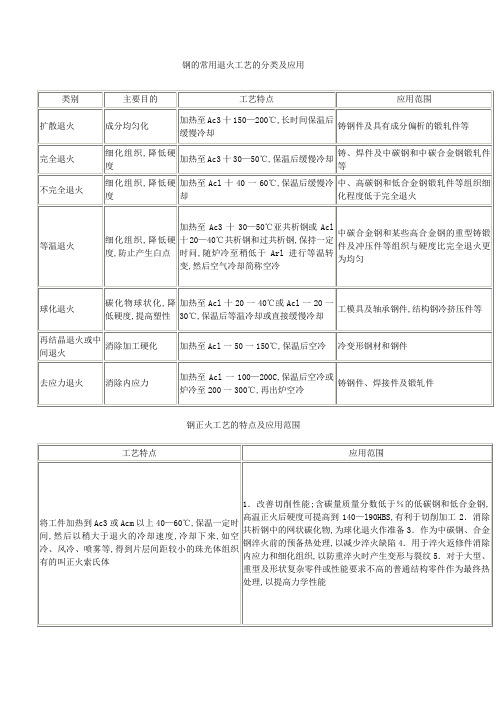
时效的目的是使淬火后的工件进一步消除内应力,稳定工件尺寸常用来处理要求形状不再发生变形的精密工件,例如精密轴承、精密丝杠、床身、箱体等低温时效实际就是低温补充回火
低温时效
将工件加热到100一150 ℃,保温较长时间约5—20h
冷处理
淬透层深度一般为2—6mm,过深往往引起零件表面严重过热,易产生淬火裂纹;表面硬度钢可达65HRC,灰铸铁为40一48HRC,合金铸铁为43—52HRC;这种方法简便,无需特殊设备,但易过热,淬火效果不稳定,因而限制了它的应用
适用于单件或小批生产的大型零件和需要局部淬火的工具或零件,加大型轴类、大模数齿轮等
1.表层硬度比普通淬火高2—3HRC,并具有较低的脆性2.疲劳强度、冲击韧度都有所提高,一般工件可提高20%一30%3.变形小4.淬火层深度易于控制5.淬火时不易氧化和脱碳6.可采用较便宜的低淬透性钢7.操作易于实现机械化和自动化,生产率高8.电流频率愈高,淬透层愈薄;例如高频淬火一般1—2mm,中频淬火一般3—5mm,工频淬火能到>l0—l 5mm缺点:处理复杂零件比渗碳困难
常用钢材为中碳钢,如35、45钢及中碳合金钢合金元素<3%,如40Cr、65Mn等,还可用于灰铸铁件、合金铸铁件;含碳量过低,淬火后硬度低,而碳和合金元素含量过高,则易碎裂,因此,以含碳量质量分数在%一%之间的碳素钢最适宜
电接触加热表面淬火
采用两电极铜滚轮或碳棒向工件表面通低电压大电流,在电极与工件表面接触处产生接触电阻,产生的热使工件表面温度达到临界点以上,电极移去后冷却淬火
1.设备简单,操作方便
2.工件变形极小,不需回火
3.淬硬层薄,仅为一4.工件淬硬层金相组织,硬度不均匀
四种常见热处理方法

四种常见热处理方法
首先是退火,退火是指将金属材料加热至一定温度,保持一定时间后,再以适
当速度冷却到室温的热处理工艺。
退火可以消除金属材料中的应力,改善塑性和韧性,降低硬度,提高加工性能。
退火分为全退火、球化退火、等温退火等不同类型,适用于不同的金属材料和工艺要求。
其次是正火,正火是指将金属材料加热至一定温度,保温一段时间后,再以适
当速度冷却到室温的热处理工艺。
正火可以使金属材料的组织变细,提高硬度和强度,改善耐磨性和耐磨损性能。
正火常用于碳钢、合金钢等材料的热处理中。
接下来是淬火,淬火是指将金属材料加热至临界温度以上,保温一定时间后,
迅速冷却到室温的热处理工艺。
淬火可以使金属材料的组织变质,提高硬度和强度,但同时会降低韧性。
淬火常用于高碳钢、合金钢等材料的热处理中。
最后是回火,回火是指将经过淬火处理的金属材料加热至一定温度,保温一定
时间后,再以适当速度冷却到室温的热处理工艺。
回火可以消除淬火时产生的内应力,改善金属材料的韧性和塑性,同时保持一定的硬度和强度。
回火常用于淬火处理后的金属材料,以提高其综合性能。
总的来说,不同的热处理方法适用于不同的金属材料和工艺要求,可以通过合
理选择和控制热处理工艺参数,达到预期的组织和性能调控效果。
因此,在工程实践中,对于不同的金属材料,要根据具体情况选择合适的热处理方法,以提高材料的使用性能和延长使用寿命。
常用的钢材热处理方法[精品]
![常用的钢材热处理方法[精品]](https://img.taocdn.com/s3/m/e4f12a47ac02de80d4d8d15abe23482fb4da0282.png)
常用的钢材热处理方法一.淬火将钢件加热到临界温度以上40~60℃,保温一定时间,急剧冷却的热处理方法,称为淬火。
常用急剧冷却的介质有油、水和盐水溶液。
淬火的加温温度、冷却介质的热处理规范,见表<常用钢的热处理规范>.淬火的目的是:使钢件获得高的硬度和耐磨性,通过淬火钢件的硬度一般可达HRC60~65,但淬火后钢件内部产生了内应力,使钢件变脆,因此,要经过回火处理加以消除。
钢件的淬火处理,在[wiki]机械[/wiki]制造过程中应用比较普遍,它常用的方法有:1.单液淬火:将钢件加热到淬火温度,经保温一定时间后,在一种冷却液中冷却,这种热处理方法,称为单液淬火。
它适用于形状简单、技术要求不高的碳钢或合金钢,工件直径或厚度大于5~8mm的碳素钢,选用盐水或水中冷却;合金钢选用油冷却。
在单液淬火中,水冷容易发生变形和裂纹;油冷容易产生硬度不够或不均的现象。
2.双液淬火:将钢件加热到淬火温度,经保温后,先在水中快速冷却至300~400℃,在移入油中冷却,这种处理方法,称为双液淬火。
形状复杂的钢件,常采用此方法。
它既能保证钢件的硬度,又能防止变形和裂纹。
缺点是操作难度大,不易掌握。
3.火焰表面淬火:用乙炔和氧气混合燃烧的火焰喷射到工件表面,并使其加热到淬火温度,然后立即用水向工件表面喷射,这种处理方法,称为火焰表面淬火。
它适用于单件生产、要求表面或局部表面硬度高和耐磨的钢件,缺点是操作难度大。
4.表面感应淬火:将钢件放人感应器内,在中频或高频交流电的作用下产生交变磁场,钢件在磁场作用下产生了同频率的感应电流,使钢件表面迅速加热(2-10s)至淬火温度,立即把水喷射到钢件表面。
这种热处理方法,称为表面感应淬火。
经表面感应淬火的零件,表面硬而耐磨,而内部有较好的强度和韧性。
这种方法适用于中碳钢和中等含碳量的合金钢件。
表面感应淬火根据所采用的电流频率的不同,可分为高频、中频和工频淬火三种。
高频淬火电流频率为100~150kHz,淬硬层深1~3mm,它适用于齿轮、花键轴、活塞和其它小型零件的淬火;中频淬火电流频率为500~10000Hz,淬硬层深3—10mm,它适用于曲轴、钢轨、机床导轨、直径较大的轴类和齿轮等;工频淬火电流频率为50Hz,淬硬层一般大于10mm,适用于直径在300mm以上的大型零件的淬火,如冷轧辊等。
常用退火工艺方法中的扩散退火

退火是热处理加工工艺中的一种,主要是将金属铸锭、铸件或锻坯,在略低于固相线的温度下长期加热,消除或减少化学成分偏析及纤维组织的不均匀性,以达到均匀化目的的热处理工艺称为扩散退火,又称为均匀化退火。
下面我们就来针对扩散退火具体进行介绍。
铸件凝固时要发生偏析,造成的成分和组织的不均匀性。
如果是铸锭,这种不均匀性则在轧制成钢材时,将沿着轧制方向拉长而呈方向性,最常见的如带状组织。
低碳钢中所出现的带状组织,其特点为有的区域铁素体多,有的区域珠光体多,而区域并排地沿着轧制方向排列。
产生带状组织的原因是由于铸锭中锰等影响过冷奥氏体稳定性合金元素的偏析。
由于这种成分和结构的不均匀性,需要长程扩散才能消除,因而过程进行得很慢,消耗大量的能量,且生产效率低,只有在必要时才使用。
因此扩散退火多用于优质合金钢及偏析现象较为严重的合金。
扩散退火在铸锭开坯或锻造后进行比较有效,因为此时铸态组织已被破坏,元素扩散的障碍大为减少。
钢件扩散退火加热温度通常选择150—300摄氏度,视钢种和偏析程度而异。
温度过高影响加热炉寿命,并使钢件烧损过多,碳钢一般为1100—1200摄氏度,合金钢一般为1200—1300摄氏度,加热速度长控制在每小时100—200摄氏度。
扩散退火的保温时间,理论上可以根据原始组织成分不均匀性的程度,假设其浓度分布模型用扩散方程的特解来进行计算。
但其浓度分布的测定需要很长的周期,实际上很少采用理论计算,而采用经验公式进行估算。
估算方法是:保温时间一般按界面厚度每25mm保温30—60min,或按每毫米厚度保温1.5—2.5min来计算。
由于扩散退火在高温下进行,且过程时间很长,因而退火后将使奥氏体晶粒十分粗大。
为了细化晶粒,应在扩散退火后,补充一次完全退火。
对铸锭来说,尚需压力加工,而压力加工可以细碎晶粒,故此时可不必再扩散退火后再补充一次完全退火。
应该指出,用扩散退火解决刚才成分和组织结构的不均匀性是有限度的。
常用热处理的的方法
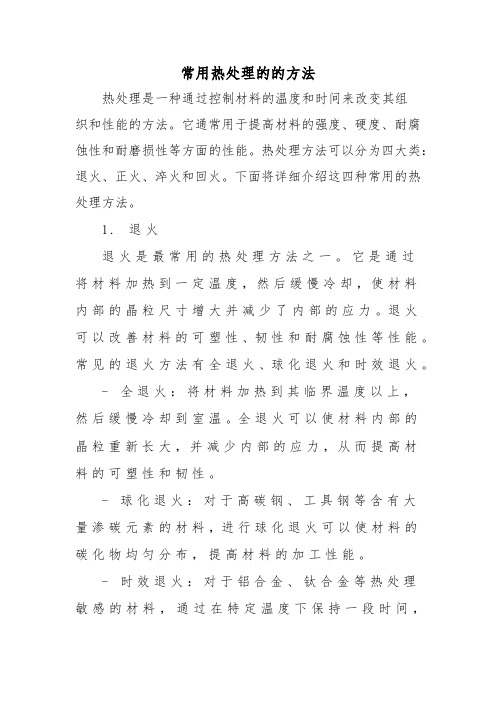
常用热处理的的方法热处理是一种通过控制材料的温度和时间来改变其组织和性能的方法。
它通常用于提高材料的强度、硬度、耐腐蚀性和耐磨损性等方面的性能。
热处理方法可以分为四大类:退火、正火、淬火和回火。
下面将详细介绍这四种常用的热处理方法。
1.退火退火是最常用的热处理方法之一。
它是通过将材料加热到一定温度,然后缓慢冷却,使材料内部的晶粒尺寸增大并减少了内部的应力。
退火可以改善材料的可塑性、韧性和耐腐蚀性等性能。
常见的退火方法有全退火、球化退火和时效退火。
-全退火:将材料加热到其临界温度以上,然后缓慢冷却到室温。
全退火可以使材料内部的晶粒重新长大,并减少内部的应力,从而提高材料的可塑性和韧性。
-球化退火:对于高碳钢、工具钢等含有大量渗碳元素的材料,进行球化退火可以使材料的碳化物均匀分布,提高材料的加工性能。
-时效退火:对于铝合金、钛合金等热处理敏感的材料,通过在特定温度下保持一段时间,然后迅速冷却,可以使材料的强度和硬度得到提高。
2.正火正火是一种热处理方法,它通过将材料加热到适当温度,然后把材料冷却到室温。
正火可以提高材料的硬度、强度和韧性等性能。
常见的正火方法有水淬正火、油淬正火和气淬正火。
-水淬正火:将材料加热到过共析温度以上,然后迅速冷却到室温。
水淬正火可以使材料的晶粒变细,并增加材料的硬度和强度,但韧性相对较低。
-油淬正火:将材料加热到过共析温度以上,然后迅速冷却到室温。
油淬正火与水淬正火相比,在冷却速度上较慢,可以提高材料的韧性和耐冲击性,适用于厚壁件等对韧性要求较高的材料。
-气淬正火:将材料加热到过共析温度以上,然后迅速冷却到室温。
气淬正火是一种较为温和的正火方法,适合对材料要求较高的精密零件。
3.淬火淬火是一种通过将材料加热到临界温度以上,然后迅速冷却的热处理方法。
淬火可以使材料的晶粒细化,增加材料的硬度和强度,但通常会降低材料的韧性。
常见的淬火方法有水淬、油淬和盐浴淬。
-水淬:将材料加热到临界温度以上,然后迅速将材料浸入冷水中冷却。
各种退火的温度范围
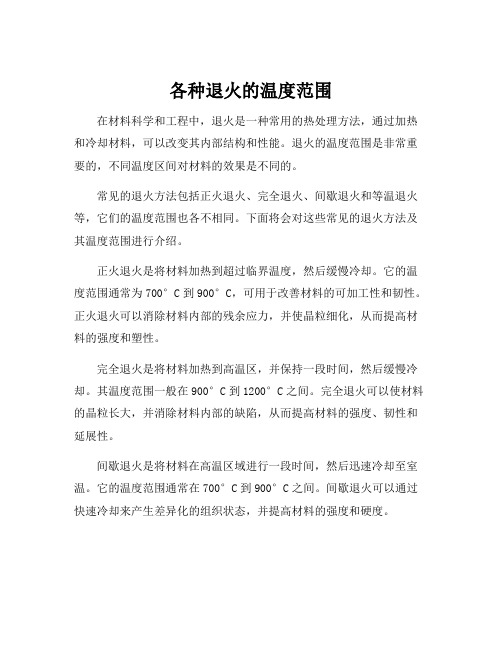
各种退火的温度范围在材料科学和工程中,退火是一种常用的热处理方法,通过加热和冷却材料,可以改变其内部结构和性能。
退火的温度范围是非常重要的,不同温度区间对材料的效果是不同的。
常见的退火方法包括正火退火、完全退火、间歇退火和等温退火等,它们的温度范围也各不相同。
下面将会对这些常见的退火方法及其温度范围进行介绍。
正火退火是将材料加热到超过临界温度,然后缓慢冷却。
它的温度范围通常为700°C到900°C,可用于改善材料的可加工性和韧性。
正火退火可以消除材料内部的残余应力,并使晶粒细化,从而提高材料的强度和塑性。
完全退火是将材料加热到高温区,并保持一段时间,然后缓慢冷却。
其温度范围一般在900°C到1200°C之间。
完全退火可以使材料的晶粒长大,并消除材料内部的缺陷,从而提高材料的强度、韧性和延展性。
间歇退火是将材料在高温区域进行一段时间,然后迅速冷却至室温。
它的温度范围通常在700°C到900°C之间。
间歇退火可以通过快速冷却来产生差异化的组织状态,并提高材料的强度和硬度。
等温退火是将材料在一定温度下保持一段时间,然后缓慢冷却。
它的温度范围通常在500°C到700°C之间。
等温退火可以通过固态相变来改善材料的晶粒组织和力学性能。
除了上述常见的退火方法,还有一些特殊的退火方法,如高温退火、低温退火、回火退火等。
它们的温度范围则根据具体需求和材料的种类而定。
高温退火一般在1200°C以上,用于改善材料的高温性能;低温退火一般在300°C以下,用于改善材料的低温性能;回火退火一般在200°C到600°C之间,用于调节材料的硬度和韧性。
综上所述,退火的温度范围对于改变材料的内部结构和性能起着关键作用。
正确选择适合的退火温度范围,可以得到理想的材料组织和性能,从而满足不同工程和应用的需求。
在实际应用中,需要根据具体情况和材料性质来选择合适的退火方法和温度范围,以达到最佳效果。
二维材料异质结退火的方法
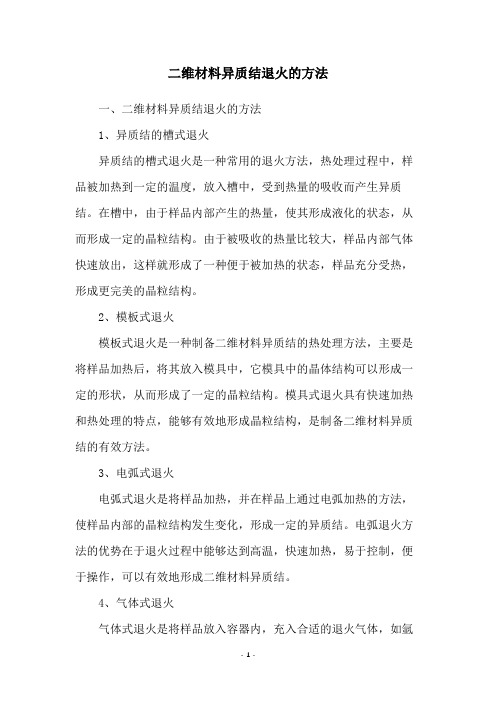
二维材料异质结退火的方法
一、二维材料异质结退火的方法
1、异质结的槽式退火
异质结的槽式退火是一种常用的退火方法,热处理过程中,样品被加热到一定的温度,放入槽中,受到热量的吸收而产生异质结。
在槽中,由于样品内部产生的热量,使其形成液化的状态,从而形成一定的晶粒结构。
由于被吸收的热量比较大,样品内部气体快速放出,这样就形成了一种便于被加热的状态,样品充分受热,形成更完美的晶粒结构。
2、模板式退火
模板式退火是一种制备二维材料异质结的热处理方法,主要是将样品加热后,将其放入模具中,它模具中的晶体结构可以形成一定的形状,从而形成了一定的晶粒结构。
模具式退火具有快速加热和热处理的特点,能够有效地形成晶粒结构,是制备二维材料异质结的有效方法。
3、电弧式退火
电弧式退火是将样品加热,并在样品上通过电弧加热的方法,使样品内部的晶粒结构发生变化,形成一定的异质结。
电弧退火方法的优势在于退火过程中能够达到高温,快速加热,易于控制,便于操作,可以有效地形成二维材料异质结。
4、气体式退火
气体式退火是将样品放入容器内,充入合适的退火气体,如氩
气等,进行加热,使样品内部的晶粒结构发生变化,形成一定的异质结。
气体式退火的优点在于温度可以控制,速度可以快速加热,而且可以控制气体的温度,方便操作,有利于形成二维材料异质结。
总之,以上是二维材料异质结退火的几种常用方法,选择不同的方法,可以根据需要获得所需的晶粒结构,但是需要注意温度控制,以免造成样品受损。
金属热处理-退火的方法及意义

金属热处理-退火的方法及意义
金属热处理是将固态金属或合金采用适当的方式进行加热、保温和冷却以获得所需要的组织结构与性能的工艺。
将钢加热到适当温度,保持一定时间,然后缓慢冷却(一般随炉冷却)的热处理工艺称为退火。
退火的目的:①降低钢的硬度,提高塑性,以利于切削加工及冷变形加工。
②细化晶粒,均匀钢的组织及成分,改善钢的性能或为以后的热处理作准备。
③消除钢中的残余内应力,以防止变形和开裂。
常用的退火方法有完全退火、球化退火、去应力退火等几种。
1、完全退火将钢完全奥氏体化,随之缓慢冷却,获得接近平衡状态①组织的工艺称为完全退火。
完全退火在加热过程中,使钢的组织全部转变为奥氏体,在冷却过程中,奥氏体转变为细小而均匀的平衡组织,从而降低钢的强度、细化晶粒、充分消除内应力。
完全退火主要用于中碳钢及低、中碳合金结构钢的锻件、铸件等。
过共析
钢不宜采用完全退火。
2、球化退火为使钢中碳化物呈球状化而进行的退火称为球化退火。
球化退火工艺为:加热温度在Acl以上20~30℃,保温一定时间,以不大于50℃/h的冷却速度随炉冷却下来,得到球状珠光体组织。
球化退火适用于共析钢及过共析钢,如碳素工具钢、合金工具钢、轴承钢等。
3、去应力退火为了去除由于塑性变形、焊接等原因造成的以及铸件内存在的残余应力而进行的退火称为去应力退火。
去应力退火工艺是:将钢加热到略低于A1的温度(一般取500~650℃),经保温缓慢冷却即可。
在去应力退火中,钢的组织不发生变化,只是消除内应力。
常用热处理方法8.1退火将钢材加热到一定温度,保温一段时间后,随...

常用热处理方法8.1退火将钢材加热到一定温度,保温一段时间后,随炉缓慢冷却(或埋在砂中或石灰中冷却)至500度以下在空气中冷却的热处理工艺。
8.1.1完全退火和等温退火完全退火又称重结晶退火,一般简称为退火,这种退火主要用于亚共析成分的各种碳钢和合金钢的铸,锻件及热轧型材,有时也用于焊接结构。
一般常作为一些不重工件的最终热处理,或作为某些工件的预先热处理。
8.1.2球化退火球化退火主要用于过共析的碳钢及合金工具钢(如制造刃具,量具,模具所用的钢种)。
其主要目的在于降低硬度,改善切削加工性,并为以后淬火作好准备。
8.1.3去应力退火去应力退火又称低温退火(或高温回火),这种退火主要用来消除铸件,锻件,焊接件,热轧件,冷拉件等的残余应力。
如果这些应力不予消除,将会引起钢件在一定时间以后,或在随后的切削加工过程中产生变形或裂纹。
8.2淬火将钢材加热到一定温度,保温一段时间后,在一定介质(水、油等)中冷却的热处理工艺。
淬火时,最常用的冷却介质是盐水,水和油。
盐水淬火的工件,容易得到高的硬度和光洁的表面,不容易产生淬不硬的软点,但却易使工件变形严重,甚至发生开裂。
而用油作淬火介质只适用于过冷奥氏体的稳定性比较大的一些合金钢或小尺寸的碳钢工件的淬火。
8.3正火将钢材或钢件加热到一定温度以上,保持一定时间后在空气中冷却的热处理工艺。
8.4回火将经过淬火的工件加热到临界点AC1以下的适当温度保持一定时间,随后用符合要求的方法冷却,以获得所需要的组织和性能的热处理工艺。
8.4.1低温回火(150-250度)低温回火其目的是在保持淬火钢的高硬度和高耐磨性的前提下,降低其淬火内应力和脆性,以免使用时崩裂或过早损坏。
它主要用于各种高碳的切削刃具,量具,冷冲模具,滚动轴承以及渗碳件等,回火后硬度一般为HRC58-64。
8.4.2中温回火(350-500度)中温回火其目的是获得高的屈服强度,弹性极限和较高的韧性。
因此,它主要用于各种弹簧和热作模具的处理,回火后硬度一般为HRC35-50。
常见的退火工艺

加热温度
对于亚共析钢Ac3以上30~70℃
对于共析钢或过共析钢Ac1以上30~70℃
保温时间
获得均匀细化奥氏体温度的时间,一般可由经验公式确定
冷却速度
由冷却介质确定,碳钢通常用水冷,合金钢用油冷
常见淬火方法的特点及适用范围
淬火方法
操作特点
优缺点评价
适用范围
单介质淬火
加热好的工件直接放入一种淬火介质中冷却
扩散退火后钢的晶粒很大,因此一般要进行完全退火或正火处理
去应力退火
(低温退火)
为消除铸件、锻件、焊接件、冷加工件的内应力,以防止钢件再以后加工或使用过程变形或开裂
加热至Ac1以下某一温度(对于碳钢为500~600℃),保温后随炉冷却
无变化
铸、锻、焊、冷压件及机加工件等
可以消除内应力约50%~80%
淬火工艺参数
强度、硬度继续下降,塑性继续升高
回火工艺分类与性能
应用
低温回火
150~250℃
M回+碳化物
高硬度、高耐磨HRC58~64
刃具、量具、冲模、轴承、渗碳件、表面淬火件
中温回火
350~500℃
T回
高屈服极限、弹性极限和韧性,HRC35~50
弹簧、弹性夹具、热锻模
高温回火
500~650℃
片状珠光体和网状渗碳体转变为球状
共析、过共析钢及合金钢的锻件、扎件等
当有网状Fe3C存在时,必须先用正火消除Fe3C网,再球化退火
扩散退火
(均匀化退火)
减少钢锭、铸件或锻坯的成分偏析和组织的不均匀性
加热到钢的熔点以下100~200℃,长时间保温后炉冷
粗大组织(组织严重过烧)
合金钢铸锭及大型铸钢件或铸件