压弯成形回弹预测方法
先进高强度钢板冲压成形回弹的预测与控制

累,具有较强的均匀变形能力。
几个钢种的成形极限图的对比图见图1.2。
成形极限图能较全面的表征各类钢在各种应力状态下的成形性,从图1.2可以看出:双相钢和DP600的成形性相当,TRIP600的成形性和IF钢相当,且在深拉延和平面应变区的成形性还优于IF钢。
②回弹回弹是指冲压构件脱模后,偏离原在模具中形状的一种变形量。
高强度钢的机械性能和普通低碳钢有很大差异,钢板高强度化易引起塑性下降,成形性变差,而屈服强度的提高则引起面畸变和回弹效应,增加形状不稳定性。
典型的成形缺陷有开裂、形状不良、尺寸精度不良和卡模具等。
材料强度升高时,残余应力增大,易产生变形后弹性回复引起的形状不良和尺寸精度不良等。
这是高强度钢板成形中最为严重的问题【n。
导致由这类材料冲压而成的汽车冲压件的回弹量远大于使用普通低碳钢板的冲压件,回弹问题更加突出。
图1.3几种钢回弹对比图Fig1.3Spdngbackofdifferentsteels从图1.3可以看出,随着板料强度的提高,回弹越严重。
由于先进强度钢独特的材料性能,成形后的回弹比普通钢及传统高强度钢大。
因此回弹是先进高强度钢冲压成形工艺的设计难点。
利用有限元仿真软件,分析先进高强度钢的回弹特性,可有效指导先进高强度钢冲压成形设计。
1.4冲压回弹的分析和控制方法冲压回弹分析是回弹控制的基础,回弹分析的准确程度,决定了回弹控制的有效性。
只有准确预测回弹,才能从根本上解决回弹问题。
1.4.1冲压回弹的分析方法常用的回弹的分析方法有两种,解析方法和有限元方法。
①解析法重庆大学硕士学位论文2先进高强度钢介绍2先进高强度钢介绍2.1先进高强度钢简介根据国际上对超轻钢汽车的研究(ULSAB.AVC),把屈服强度在210-550N/ram2范围内的钢板称为高强度钢板;屈服强度大于550N/ram2的钢板称为超高强度钢板。
根据强化机理的不同又分为普通高强度钢板和先进高强度钢板。
其中,普通高强度钢板主要包括高强度IF(无『自J隙原子)钢、烘烤硬化钢、含磷(P)钢、各向同性(IS)钢、碳一锰(C.Mn)钢和高强度低合金(HsLA)钢;先进高强度钢主要包括双相(DP)钢、相交诱发塑性(踊P)钢、复相(cP)钢、贝氏体(BP)钢和马氏体(MP)钢等。
钣金弯曲回弹计算

钣金弯曲回弹计算
钣金弯曲回弹是在进行金属钣金弯曲加工时,由于材料的弹性特性导致弯曲后形状不完全保持原始的设计形状。
这是由于金属材料在受到应力后发生弹性变形,当外力消失时,材料会有一定的回弹,使弯曲后的形状略微改变。
弯曲回弹的计算通常涉及一些复杂的工程数学和试验方法。
以下是一种简化的计算方法,但请注意,实际应用可能需要更复杂和准确的方法:
1.弯曲回弹计算公式:
在一些简单的情况下,可以使用下述的弯曲回弹计算公式:
回弹角度=实际弯曲角度−设计弯曲角度
2.材料回弹系数:
对于具体的材料,可以通过试验来确定回弹系数。
回弹系数是实际回弹角度与设计弯曲角度之比。
它通常是一个材料和弯曲工艺的固有属性。
回弹系数=回弹角度
设计弯曲角度
3.实验测定:
通过实验测定具体材料在特定条件下的回弹系数是一种更准确的方法。
这通常涉及制作一系列的试样,进行弯曲,并测量回弹的角度。
通过分析试验数据,可以得到回弹系数。
4.有限元分析:
在工程实践中,有限元分析等数值方法也可用于更复杂形状的弯曲回弹计算。
这种方法考虑了材料的非线性、应变硬化等更为精细的特性。
在实际应用中,因材料的不同、弯曲工艺的不同以及制造条件的
不同,回弹效应会有很大的差异。
因此,具体的回弹计算需要结合实际情况进行调整和验证。
板料弯曲回弹及工艺控制

板料弯曲回弹及工艺控制板料在弯曲过程中,产生塑性变形的同时会产生弹性变形。
当工件弯曲后去除外力时,会立即发生弹性变形的恢复,结果使弯曲件的角度和弯曲半径发生变化,与模具相应形状不一致,即产生回弹。
回弹是弯曲成形过程的主要缺陷,它的存在造成零件的成形精度差,显著地增加了试、修模工作量和成形后的校正工作量,故在冲压生产中,掌握回弹规律非常重要。
如果在设计模具前,能准确掌握材料的回弹规律及回弹值大小,设计模具时可预先在模具结构及工作部分尺寸上采取措施,试冲后即使尺寸精度有所差异,其修正工作量也不会太大,这不仅可以缩短模具制造周期,而且有利于模具成本的降低及弯曲件精度的提高。
1 弯曲回弹的表现形式弯曲回弹的表现形式有下列二个方面(如图1所示):(a) 弯曲半径增加:卸载前板料的内半径r (与凸模的半径吻合),在卸载后增加至r0,半径的增量为△r二r0一r(b) 弯曲件角度增大:卸荷前板料的弯曲角为α(与凸模的顶角吻合),在卸荷后增大到α0,角度增量为△α=α0一α图1 回弹导致弯曲角和弯曲半径变化2 弯曲回弹产生的原因弯曲回弹的主要原因是由于材料弹性变形所引起的。
板料弯曲时,内层受压应力,外层受拉应力。
弹塑性弯曲时,这两种应力尽管超过屈服应力,但实际上从拉应力过渡到压应力时,中间总会有一段应力小于屈服应力的弹性变形区。
由于弹性变形区的存在,弯曲卸载后工件必然产生回弹。
在相对弯曲半径较大时,弹性变形区占的比重大,回弹尤其显著。
回弹是由于在板厚方向应力或应变分布不均匀而引起的。
这种应力和应变的不均匀分布是弯曲的特点,对于只施加弯矩的弯曲方式,要有效减少回弹是困难的。
为了使回弹减小,应尽量使板厚断面内的应力和应变分布均匀,为此可采取在纵向纤维方向对板料进行拉伸或压缩的方法,也可采用在板厚方向施加强压的方法。
在沿板的长度方向单纯拉伸变形的场合,除去外力后,由于在整个板厚断面内变形的恢复是均匀的,所以不会发生形状的变化。
板材与型材弯曲回弹控制原理与方法

板材与型材弯曲回弹控制原理与方法
在机械制造和建筑行业中,板材与型材的弯曲加工是非常常见的操作。
而在弯曲完成后,材料往往会出现一定的回弹现象,导致加工精度受到影响。
因此,如何控制弯曲回弹,提高加工精度成为了重要的问题。
一、弯曲回弹原理
当一段材料被弯曲后,由于材料内部的分子结构发生了变化,使得材料内部存在的应力分布也发生了改变。
在材料恢复到原始状态之前,这些应力将继续作用于材料,导致弯曲回弹现象的发生。
二、弯曲回弹控制方法
1. 选择合适的弯曲工艺
选择合适的弯曲工艺是减少弯曲回弹的关键。
常用的弯曲工艺包括冷弯、热弯和滚弯等。
冷弯工艺的回弹最大,而热弯和滚弯工艺则可以减少回弹。
2. 适当增加弯曲角度
在弯曲时,适当增加弯曲角度可有效减少回弹。
但是过分增加弯曲角度会导致破坏材料。
3. 采用预压弯曲方法
预压弯曲方法是指在正式弯曲前先对材料进行一定的预压弯曲,以减小材料内部应力分布的差异,从而减少回弹。
但是预压弯曲方法要求对材料和弯曲机具有更高的要求。
4. 加工后热处理
通过加工后热处理,可以改变材料内部的分子结构,从而减少回弹。
但是加工后热处理时间和温度的控制需要非常精准。
三、结论
以上是板材与型材弯曲回弹控制原理与方法的介绍。
在实际生产中,需要综合考虑材料的性质、弯曲工艺的选择、弯曲角度的控制、预压弯曲和加工后热处理等因素,以减少回弹现象,提高加工精度。
板料成形回弹特征及其控制技术
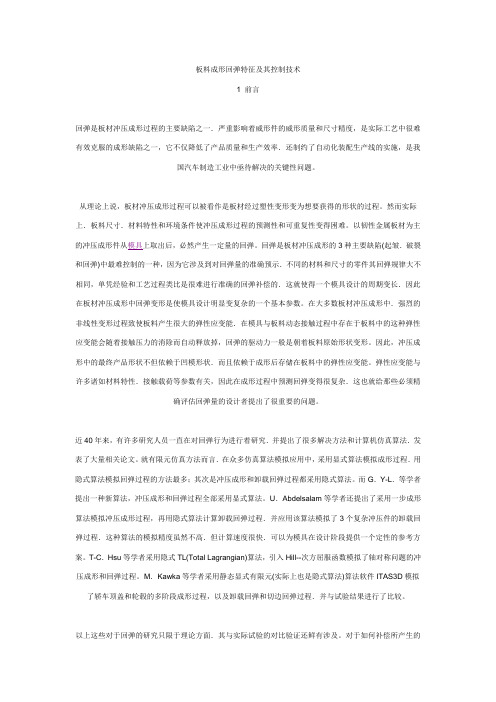
板料成形回弹特征及其控制技术1 前言回弹是板材冲压成形过程的主要缺陷之一.严重影响着威形件的威形质量和尺寸精度,是实际工艺中很难有效克服的成形缺陷之一,它不仅降低了产品质量和生产效率.还制约了自动化装配生产线的实施,是我国汽车制造工业中亟待解决的关键性问题。
从理论上说,板材冲压成形过程可以被看作是板材经过塑性变形变为想要获得的形状的过程。
然而实际上.板料尺寸.材料特性和环境条件使冲压成形过程的预测性和可重复性变得困难。
以韧性金属板材为主的冲压成形件从模具上取出后,必然产生一定量的回弹。
回弹是板材冲压成形的3种主要缺陷(起皱.破裂和回弹)中最难控制的一种,因为它涉及到对回弹量的准确预示.不同的材料和尺寸的零件其回弹规律大不相同,单凭经验和工艺过程类比是很难进行准确的回弹补偿的.这就使得一个模具设计的周期变长.因此在板材冲压成形中回弹变形是使模具设计明显变复杂的一个基本参数。
在大多数板材冲压成形中.强烈的非线性变形过程致使板料产生很大的弹性应变能.在模具与板料动态接触过程中存在于板料中的这种弹性应变能会随着接触压力的消除而自动释放掉,回弹的驱动力一般是朝着板料原始形状变形。
因此,冲压成形中的最终产品形状不但依赖于凹模形状.而且依赖于成形后存储在板料中的弹性应变能。
弹性应变能与许多诸如材料特性.接触载荷等参数有关,因此在成形过程中预测回弹变得很复杂.这也就给那些必须精确评估回弹量的设计者提出了很重要的问题。
近40年来,有许多研究人员一直在对回弹行为进行着研究.并提出了很多解决方法和计算机仿真算法.发表了大量相关论文。
就有限元仿真方法而言.在众多仿真算法模拟应用中,采用显式算法模拟成形过程.用隐式算法模拟回弹过程的方法最多;其次是冲压成形和卸载回弹过程都采用隐式算法。
而G.Y-L.等学者提出一种新算法,冲压成形和回弹过程全部采用显式算法。
U.Abdelsalam等学者还提出了采用一步成形算法模拟冲压成形过程,再用隐式算法计算卸载回弹过程.并应用该算法模拟了3个复杂冲压件的卸载回弹过程.这种算法的模拟精度虽然不高.但计算速度很快.可以为模具在设计阶段提供一个定性的参考方案。
板料多次弯曲成形回弹的数值模拟研究

板料多次弯曲成形回弹的数值模拟研究发布:2009-11-17 9:38:34 来源:模具网编辑:佚名摘要:对金属板料多次弯曲成形回弹的数值模拟方法进行研究,分析并解决了模拟过程中出现的板料与模具的干涉和各次弯曲间模拟结果的数据传递等问题。
通过金属板料的二次卷圆试验并与数值模拟结果比较.模拟结果与试验结果基本相符。
采用的有限元数值模拟方法可提高预测板料多次弯曲成形后回弹量的准确度。
关键词:金属板料;多次弯曲;回弹;数值模拟1引言金属板料弯曲成形后的回弹是加工中不可避免的现象,回弹的产生使得工件的弯曲精度降低,为后续的装配及其他工作带来困难。
目前对板料弯曲成形后的回弹模拟研究多集中在板料只进行一次弯曲成形后的回弹模拟,对多次弯曲成形回弹的数值模拟研究较少。
以下介绍对板料多次弯曲成形后的回弹进行模拟研究,分析模拟中出现的问题,并提出相应的解决措施。
2板料弯曲成形后回弹的数值模拟方法研究2.1弯曲回弹数值模拟方法通常情况下,完整的弯曲回弹数值模拟计算包括板料弯曲成形加载过程的模拟和弯曲成形后回弹过程的模拟,有限元方法也分为动力显式算法和静力隐式算法。
在弯曲回弹模拟过程中应结合冲压成形的特点来选择合适的有限元算法。
静力隐式算法虽然是一种无条件稳定的算法,但其计算过程需要构造和求解刚度矩阵,求解非线性方程组,而且每一步迭代都要进行接触判断nI对于板料弯曲成形这种包含接触和摩擦高度非线性的过程分析,往往会出现迭代不收敛的情况,或即使收敛,计算时间也很长。
所以对于板料弯曲成形过程的模拟一般采用动力显式算法,以避免因迭代计算和非线性引起的收敛问题。
其有限元计算公式为:对于弯曲回弹过程的模拟由于可以采用无模法。
即在弯曲回弹模拟开始之前,首先将模具与弯曲件分离,然后加载与弯曲成形结束状态接触条件相对应的反向力学边界条件:△f=-f(f为成形结束时相对应的节点接触力),并采用增量法计算,直至所有等效节点外力趋于零。
与加载过程相比,在板料弯曲回弹过程非线性成分明显减弱,同时在进行板料的弯曲回弹模拟时,静力隐式算法更接近弯曲件回弹的本质,回弹过程的模拟更适于采用静力隐式算法,其迭代公式如下:研究表明,与其他方法相比,将显式和隐式有限元算法结合起来计算回弹的方法,具有计算效率高,计算相对准确的特点,是求解弯曲回弹问题中使用最多的一种手段伫。
冲压成形过程中板料的弯曲回弹方法研究

冲压成形过程中板料的弯曲回弹方法研究党林兵(中国煤炭科工集团太原研究院;山西天地煤机装备有限公司,山西太原030006)摘要:金属板料在冲压过程中由于弹性因素影响会产生残余应力,使板料在卸载后发生与冲压方向相反的弹回,这种现象称为回弹。
回弹问题是加工缺陷的一种,它影响了加工零件的尺寸精度,并且会影响后续的装配以及工件的使用寿命,所以应该对其进行精确的预测和控制。
关键词:回弹;冲压成形;加工缺陷中图分类号:TG38文献标识码:A文章编号:1006—7981(2018)05—0031—02由于影响回弹的因素众多、形成回弹的原因复杂、涉及的学科广泛,一直以来回弹问题都是学术界讨论的热点问题。
因此对回弹量的精确预测分析,进而实现回弹控制,对于实际加工生产过程中提高产品精度、延长使用寿命、缩短研发周期等都有着重要意义。
1回弹预测方法的研究随着弯曲成形加工零件的增加,回弹现象开始逐渐被人们所认识和重视,并开始对其进行系统的理论研究。
由于弯曲成形的几何形状和边界条件都相对比较简单,计算相对比较容易,故最初人们研究回弹问题是将弯曲成形理论作为起点的。
随着研究的不断深入和细化,回弹理论也愈加成熟。
而正因为如此,人们也同时发现了回弹问题的复杂性。
现在我们已经知道,回弹是板料冲压成形过程中不可避免的现象之一,在冲压成形过程中,板料的变形过程既存在塑性变形,也存在弹性变形。
加工结束后,来自模具上的载荷被卸载,由于弹性因素而导致的残余应力得到释放,从而使得工件的形状尺寸与预期有所偏差,这个偏差就是回弹量。
回弹产生的过程是整个冲压过程的累积效应,形成回弹的因素也是非常多的,比如材料特性、工艺参数、模具设计尺寸、零件加工形状和成形工序等等。
这些因素相互作用,使得回弹问题的预测和控制变得十分复杂。
对此,国内外的学者近些年都进行了深入的研究,并取得了多方面的成果。
其研究方向大体可分为三个方面,分别是理论研究、有限元模拟和实验研究及回弹控制。
型材拉弯成形及回弹分析

This work in the dissertation may provide a rational and useful method for
improving the quality of stretch bending forming of extrusions and a useful tool for
两华大学硕十学位论文
数。该方法可通过拉弯件轮廓曲线上布点的密度来控制模具轮廓曲线上曲率分 段的多少和误差大小。本文还通过有限元分析方法计算了拉弯型材的回弹量, 用于评估拉弯模轮廓面的回弹修正量,以及拉弯件的校形余量的减少情况。本 .文的工作为提高汽车和飞机拉弯件的质量和促进工装的数字化设计提供了一合 理有效的方法。
两华大学硕十学位论文
assumptions.In bending stages friction unit model and stress·strain analysis and bending moment was detailed.The analysis of stretch bending spring-back was introduced and the formula for calculating sheet and extrusions spring—back radius
★能成形空间结构复杂的型材零件 ★能成形屈强比大的型材弯曲零件 ★具有不同工艺方法相结合的综合成形特点 ★弯曲精度高,回弹小 因此型材拉弯在飞机、汽车型材弯曲件的生产中得到了非常广泛的应用。 在飞机生产中,飞机框肋上的缘条、机身前后段、发动机短仓的长桁等尺 寸大的型材弯曲件是组成飞机骨架的关键零件,并直接影响到飞机的气动力外 形,形状精度要求很高。’在汽车生产中,拉弯主要用于加工车身结构和保险杠 的中空铝型材弯曲件,在保持与钢铁制件同样的抗冲击强度条件下,能减轻车 体重量,降低使用成本。拉弯工艺可实现铝型材的高精度弯曲,但由于拉弯成 形中可能会出现壁厚减薄破裂、起皱、截面畸变等成形缺陷,而这些成形缺陷 与型材的材料性能、截面形状及工艺参数这些因素密切相关,非常复杂。 目前拉弯成形性的研究迫切需要解决以下两个关键技术问题【l】:1.合理确 定拉弯成形过程中的工艺参数;2.准确预测拉弯零件的回弹量。实际生产中拉 弯模修正量及工艺参数的确定主要以实际经验或通过试错法来解决,即根据经 验反复调整修模量,改变主拉力、补拉力等工艺参数。有时还需要多次预拉弯 及热处理,最终成形后还要进行人工校形。这种方法成本高,时间长,形状精 度难以保证。随着产品加工精度要求的日益提高,近/净成形的要求逐步增加, 数字化设计制造也对拉弯成形工艺提出了新的要求,传统的拉弯成形工艺已不 能满足现代生产的需要。随着科技的进步,技术的不断的革新,特别是CAD/CAE 技术的不断发展,大型的CAD通用软件为拉弯模具的设计提供了强大的技术支 持。在CAD软件环境下,可以得到零件的一些有效的几何信息,例如通过几何分 析功能,可以得到整条曲线的曲率分布及其大小,可以检查曲面的质量。为模
钢板弯曲成形回弹计算新方法

功能介绍《钣金与制作》杂志就是中国锻压协会主办得目前国内唯一一本面向钣金制作、管型线材加工行业得综合性高端杂志、杂志为月刊,每月10日出版,每期发行量2万册。
钢板折弯成形就是当前板材加工过程中非常普遍得工艺,尤其就是近些年,钢板得压圆管工艺得到了飞速发展,已成为大型钢管生产得主要手段、钢管折弯与压圆工艺中最难解决得就就是回弹问题,这一问题解决不好会造成成形不准确、二次整形、生产效率低下,甚至造成模具因设计不当而报废等诸多方面问题。
基于以上问题,在实际工作中摸索研究,结合钢板弯曲变形时内部应力与应变得变化,推导出了钢板弯曲变形时得理论回弹公式,这一公式得应用对钢板得弯曲成形工艺有着非常积极得意义,在此与大家交流分享、回弹公式得计算分析影响钢板回弹得变形因素主要由3个,即钢板得壁厚、材质与弯曲半径、钢板越厚、材料越软(屈服强度低)、半径越小(曲率大)则回弹越小;反之就越大、下面将对这三个因素对回弹所起作用及彼此之间得相互作用情况进行推导,从而得出较为准确得回弹公式。
钢板在弯曲时,被弯曲部位随着弯矩得不断加大而发生弯曲变形,当弯曲达到屈服强度得临界点时,弯曲点得变形在外力撤出时全部回弹,通常把这一临界点得回弹称为钢板弯曲变形得回弹,可用公式(1)表示,如图1所示。
ε=σs/E (1)ε——弹性变形量;σs——屈服强度;E——弹性模量。
图1钢板得最大弹性变形实际弯曲时,当弯矩超过临界点继续加大,钢板以板厚得中性层为轴内表面发生压应力屈服,外表面发生拉应力屈服,使得变形不断增加。
为了便于计算,假定钢板在发生屈服变形时,板厚不发生变化,并假定钢板变形回弹后应力全部得到释放。
图2钢板得任一无穷小段S(弧度)其变形如图2所示,这就是取内、外侧得变形量为Δs。
ρ/ s =(ρ+0、5t )/(s+2Δs) =(ρ-0。
5t )/(s-2Δs) (2)变形后可转化成ρ=t s/4Δs (3)式中t——钢板厚度;ρ--钢板得中性层半径σs-—屈服强度Δs—-内、外侧得变形量;s-—弯曲弧度、引入类似得应力应变得概念,把s设为1,那么Δs=4ρ/t,就就是这一点得最大变形比率,超过了屈服强度得“应变”, 真正得应变就是屈服强度内得、定义Δs为变形率,则(3)式可写成ρ=t/4ΔsΔs就是由模具与机械作用下钢板得变形率,其中包含了屈服强度下得变形比率ε,即ε=σs /E、这一变形率在机械压力撤销后将获得全部回复,即回弹。
弯曲回弹控制措施

回弹是影响和制约冲压件精度的重要因素之一。
随着汽车工业和航空工业的发展,对薄板类覆盖件成形精度的要求也越来越高,回弹问题显得更为突出,成为汽车工业和航空工业等关注的热点问题。
弯曲回弹控制措施有:1、传统方法传统方法有:拉弯法、加压矫正法、模具补偿法、过弯曲法等,根据零件形状和弯曲工艺的不同可选用不同的方法来控制回弹。
2、材料选用和结构在冲压覆盖件时,满足弯曲件使用要求的条件下,尽可能选用弹性模量大、屈服极限小、机械性能稳定的材料。
同时,在弯曲件设计上可以采用改进某些结构(加强筋或增加成形折边等),加强弯曲件的刚度以减小回弹。
3、工艺措施主要是是热处理工艺、加校正工序、采用拉弯工艺三种方法。
4、模具结构利用弯曲件不同部位回弹方向相反的特点,按照预先估算或试验所得的回弹量,修正凸模和凹模工作部分的尺寸和几何形状,以相反方向的回弹来补偿工件量,将回弹角做在凹模上,使凹模的工作部分具有一定斜度。
5、采用聚氨酯弯曲模利用聚氨酯弯曲模代替刚性金属凹模进行弯曲。
在弯曲时,弯曲件圆角变形区所受到的单位压力大于两侧直边部分。
由于仅受聚氨酯侧压力的作用,直边部分不发生弯曲,随着凸模进一步向下运动,激增的弯曲力将改变圆角变形区材料的应力-应变状态,达到类似校正弯曲的效果,从而减少回弹。
6、复杂拉延成形中的回弹控制主要两种方法:一是通过改变成形过程边界条件,如毛料形状、压边力、模具圆角、摩擦状态等因素来减小回弹;另一途径是在特定工艺条件下预测或实测回弹量的大小,然后通过修正模具形状使回弹后的零件形状恰好符合设计要求。
实践中应根据冲压板材的种类、板材的厚度、液压机的类型、冲压件的具体形状、凸模圆角等情况来选用上述一种方法或几种方法联合使用。
izaksjw 阳极氧化设备。
弯管工艺中回弹 伸长和成型半径的确定方法
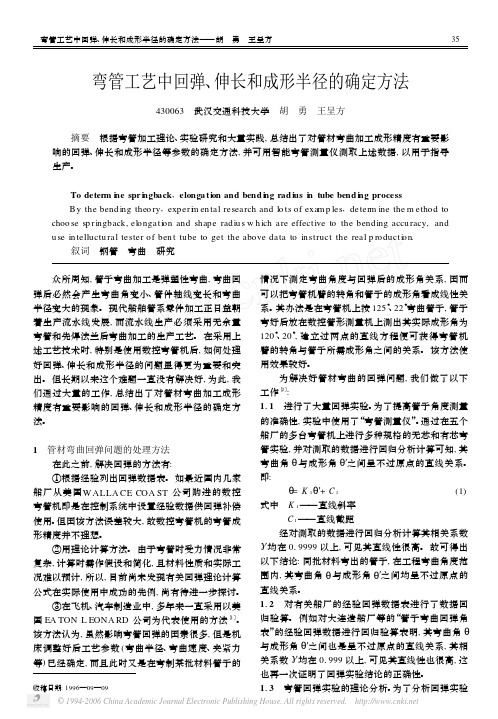
弯管工艺中回弹、伸长和成形半径的确定方法430063 武汉交通科技大学 胡 勇 王呈方 摘要 根据弯管加工理论、实验研究和大量实践,总结出了对管材弯曲加工成形精度有重要影响的回弹、伸长和成形半径等参数的确定方法,并可用智能弯管测量仪测取上述数据,以用于指导生产。
To deter m i ne spr i ngback,elonga tion and bend i ng rad ius i n tube bend i ng processB y the bending theo ry,exp eri m en tal research and lo ts of exam p les,determ ine the m ethod to choo se sp ringback,elongati on and shap e radiu s w h ich are effective to the bending accu racy,and u se in telluctu ral tester of ben t tube to get the above data to in struct the real p roducti on.叙词 钢管 弯曲 研究 众所周知,管子弯曲加工是弹塑性弯曲,弯曲回弹后必然会产生弯曲角变小、管件轴线变长和弯曲半径变大的现象。
现代船舶管系零件加工正日益朝着生产流水线发展,而流水线生产必须采用无余量弯管和先焊法兰后弯曲加工的生产工艺。
在采用上述工艺技术时,特别是使用数控弯管机后,如何处理好回弹、伸长和成形半径的问题显得更为重要和突出。
但长期以来这个难题一直没有解决好,为此,我们通过大量的工作,总结出了对管材弯曲加工成形精度有重要影响的回弹、伸长和成形半径的确定方法。
1 管材弯曲回弹问题的处理方法在此之前,解决回弹的方法有:①根据经验列出回弹数据表。
如最近国内几家船厂从美国W ALLA CE COA ST公司购进的数控弯管机即是在控制系统中设置经验数据供回弹补偿使用。
Q235的L截面型钢压弯的有限元分析及回弹预测

Q235的L截面型钢压弯的有限元分析及回弹预测王大勇;时阳;黄永红【摘要】分析发电机风道前托架的弯曲工艺,引入相对弯曲半径系数C,对传统板材压弯回弹预测公式进行修正,得到计算L截面型钢回弹的公式.利用有限元软件DYNAFORM对Q235材料的L截面型钢压弯模拟,对回弹进行预测,结合试验反推出C值,总结出C值和相对弯曲半径r0/H关系曲线.利用该曲线可以计算出所需的凸模圆角半径值,优化了模具设计和压弯工艺,为实际生产中的压弯模的设计提供参考,减少了试模次数,降低生产成本.【期刊名称】《大连交通大学学报》【年(卷),期】2014(035)003【总页数】4页(P88-91)【关键词】回弹;压弯L截面型钢;有限元;相对弯曲半径系数C【作者】王大勇;时阳;黄永红【作者单位】大连交通大学材料科学与工程学院,辽宁大连116028;大连交通大学材料科学与工程学院,辽宁大连116028;中国北车集团大连机车车辆有限公司工艺部,辽宁大连116028【正文语种】中文回弹是板材冲压成形过程中产生的一种缺陷,回弹的存在是不可避免的,影响回弹的因素多种多样,关于回弹问题人们也做了大量工作,主要是通过对回弹的预测和控制两方面进行研究,首先是对回弹进行预测,方法主要包括理论解析法,数值模拟法,实验法,然后通过改善成形工艺和模具补偿法来实现对加工零件回弹的控制,近年来,板材回弹的研究逐渐成熟[1-7].回弹缺陷同样影响着型材的加工成形,但相对于板材型材回弹预测缺少准确的数据做指导,传统的冲压手册中关于回弹的经验公式及模具设计数据也主要针对平面板材,应用于型材有很大的误差,使得型材弯曲模具设计费时费力,严重影响生产效率.压弯成形作为一种经济,高效的加工方法在实际的生产中得到普遍应用,但是其精度较低,而且关于型材压弯回弹的资料数量更是有限.因此,参考板材回弹研究方法对型材压弯法进行回弹研究对实际生产具有一定的指导意义.图1所示为机车上使用的一个构件—发电机风道前托架,由材料为Q235的L截面型材通过压弯成形.从尺寸上看零件的弯曲半径较大,很难进行一次性压弯得到,必须通过多道压弯才能实现成形.根据板材的回弹预测公式[8]:式中,rp为凸模圆角半径(mm);r0为工件回弹后的半径(mm);A为材料的弹性模量简化系数(A=3σs/E);C为相对弯曲半径系数;H为型材翼板的高度(mm).将式(2)作为预测L截面型钢回弹的公式,确定C值的大小是要解决的主要问题,需要通过对具有不同的相对弯曲半径r0/H的L截面型材进行试验得到,试验时多次试模和修模工作量和费用巨大,因此,需要借助有限元模拟软件的辅助.随着计算机技术的快速发展数值模拟法被越来越多的应用于解决塑性成形问题,其中DYNAFORM软件在分析板材的回弹问题方面被广泛的使用,通过数值模拟的方法对公式进行检验首先,建立有限元模型并划分网格如图2所示.单元类型采用BT壳单元,抽取坯料中性层来作为模型.划分模具和坯料的最小网格尺寸均为为0.5 mm,最大为5 mm.设置凸模运行速度为300 mm/s.利用动力显式算法计算压弯过程,再通过静力隐式计算卸载后的回弹.将每一步完成回弹计算坯料的文件(后缀名为dynain)重新导入到DYNAFORM前处理中,调整坯料与模具的相对位置,再进行下一道压弯和回弹计算[9].这样做的目的是由于前一道工序的模拟结果直接影响下一道工序的模拟精度.通常在模拟板料的多步冲压过程时,都忽略了每道工序后板料的回弹,即忽略了板料在每道工序后的应力变化,而板料的回弹计算精度又与其变形历史密切相关[10].在多步冲压模拟中间加进回弹计算,相对传统的多步冲压模拟过程而然,避免了因忽略每道工序后的回弹而造成的应力变化模拟不正确,进而影响最终回弹精度[11].成形计算过程采用全积分单元,厚度方向5个积分点,LS-DYNA中提供了12种迭代方法,其中BFGS法是缺省方法,这是目前最成功的一个变尺度算法,是一种拟牛顿法,收敛速度快,且具有较好的数值稳定性.隐式参数的设置对回弹精度和收敛有重要影响[12-13].对于初步设计方案,进行每一道压弯时坯料的送进量为1倍的凸模宽度,发现在翼板上存在一定的起皱现象,如果减小送料量会改善这种现象,并调整凸模和挡板的间隙为1.1倍的板厚,经过多次模拟将每次的送料量确定为2/3倍的凸模宽度,修改后的模型如图3所示,修改模型后既改善了翼板起皱现象又保证了给料量不至于影响效率,如图4所示.对截面30 mm×30 mm,材料为Q235的L截面型钢,在不同的相对弯曲半径r0/H情况下进行模拟压弯,并结合试验测量其回弹后的半径值r0,再计算回弹半径Δr=r0-rP,最终得到相对弯曲半径r0/H与回弹半径Δr的关系如图5所示.模拟结果和试验结果得到较好的吻合,验证了模拟的可靠性.将式(2)整理成为,公式右边rp、r0和H都是已知的,A值可以通过冲压手册查到,这样就可以求出C值,最终得到Q235材料的相对弯曲半径系数C与相对弯曲半径的关系曲线如图6所示.对图1所示的发电机风道前托架进行回弹的预测,相对弯曲半径r0/H=725/30≈24,弹性模量简化系数A=0.005,由图5可以查得相对弯曲半径系数C≈0.7,根据式(2)设计凸模圆角半径rp≈619 mm,实际设计凸模圆角半径为640 mm,与实际吻合的较好.(1)借助有限元模拟软件DYNAFORM可以对回弹进行预测,并可以预先知道模具设计的不足;(2)模拟软件的参数设置的合理性直接影响模拟结果的准确性,需要结合一定的试验来对预测精度加以保证;(3)将板材回弹预测公式中的板厚t换成翼板高度H,并引入相对弯曲半径系数C 值,修改后的公式可以比较准确的预测L截面型钢压弯回弹值,为实际生产中凸模的设计提供参考,减少试模次数,降低成本.E-mail:***************.cn.径;σS/E为屈服强度和弹性模量的比值;t为板材厚度,而对于同种材料,L截面型钢相对于等厚的板材只增加了一个高度为H的翼板,翼板对回弹起到限制的作用,板厚的作用不如翼板,所以,假设将式(1)中的t 换成H,型材的相对弯曲半径为r0/H,并且引入相对弯曲半径系数C,因此将式(1)修改为【相关文献】[1]刘桂花,冯再新,贾青云,等.板料冲压成形过程中回弹预测及控制的研究进展[J].金属铸锻焊技术,2011(17):122-125.[2]余同希,章亮炽.塑性弯曲理论及其应用[M].北京:科学出版社,1992.[3]HILL R.The Mathematical Theory of Plasticity[M].London:[s.n.],1950.[4]JOHNSON W,YU T X.Springback after the biaxial elastic-plastic pure bending of a rectangular plate-I[J].International journal of mechanical sciences,1981,23:619-630. [5]JOHNSON W,YU T X.On the range of applicability of results for the springback of an elastic-perfectly plastic rectangular plate after subjecting it to biaxial pure bending II [J].International journal of mechanical sciences,1981,23:631-637.[6]林忠钦,刘罡,李淑慧,等.应用正交试验设计提高U型件的成形精度[J].机械工程学报,2002,38:83-89.[7]杨雪春,董懿琼,彭伟,等.U型件回弹控制模具补偿法的研究[J].锻压技术,2009,2(1):48-52.[8]杨玉英,崔令江.实用冲压工艺及模具设计手册[M].北京:机械工业出版社,2005.[9]陈文亮.板料成型CAE分析教程[M].北京:机械工业出版社,2005.[10]徐丙坤,施法中.板料冲压成形回弹的数值模拟[J].北京航空航天大学学报,2001(2):194-197.[11]陈炜,王晓路,高霖.板料多步冲压回弹的数值模拟研究[J].塑性工程学报,2005(5):12-15.[12]龚红英.板料冲压成形CAE实用教程[M].北京:化学工业出版社,2009.[13]BRADLEY N,MAKER,XINHAI ZHU.Input Parameters for Metal Forming Simulation using LS-DYNA[M].Livermore:Software Technology Corporation,2000:1-10.。
基于CAE仿真弯曲件冲压的回弹分析

目录摘要 (III)ABSTRACT ................................................................................................................. I V 第一章绪论 . (1)1.1 引言 (1)1.2 课题研究的背景和意义 (2)1.3 国内外研究现状 (2)1.3.1 国内现状 (2)1.3.2 国外现状 (3)1.4 本课题主要内容 (5)第二章弯曲件的冲压理论分析 (6)2.1 弯曲件的分类及冲压变形特点 (6)2.1.1弯曲件的分类 (6)2.1.1大弯曲件及其变形特点 (7)2.1.2小弯曲件及其变形特点 (7)2.2 冲压弯曲回弹机理 (9)2.2.1 冲压弯曲的回弹机理 (9)2.2.2 弯曲件在成型过程中的应力分析 (9)第三章弯曲零件的回弹预测及控制方法 (12)3.1 回弹预测常用的计算方法 (12)3.1.1 解析法[7] (12)3.1.2 实验法 (13)3.1.3 有限元数字模拟法 (13)3.2 常用的回弹控制方法 (14)3.2.1 模具结构方面[1] (14)3.2.2 工艺方法方面 (19)3.2.3改进零件的构造工艺性方面 (19)第四章基于DYNAFORM的冲压实例的仿真分析 (21)4.1、DYNAFORM简介[1] (21)4.2、冲压回弹分析的一般过程 (21)4.3 U形弯曲零件冲压回弹过程仿真分析 (24)4.3.1U形弯曲零件冲压回弹指标[9] (24)4.3.2三维模型的创建 (24)4.3.3网格划分 (26)4.3.4零件参数设置 (28)4.3.5板料成型分析 (29)4.3.6提交运算 (32)4.3.7后处理 (32)4.3.8成型极限图(FLD图) (33)4.4回弹分析 (34)4.4.1成型分析 (34)4.4.2回弹量的计算 (34)4.5影响回弹的关键因素 (36)4.5.1摩擦系数 (37)4.5.2压边力 (37)4.5.3拉延筋阻力 (38)4.5.4模具间隙 (39)4.6本章小结 (40)结论 (41)参考文献 (42)致谢...............................................................................................错误!未定义书签。
矩形截面型材三维拉弯成形的回弹预测

华南理工大学学报(自然科学版)第43卷第2期JournalofSouthChinaUniversityofTechnologyVol畅43 No畅22015年2月(NaturalScienceEdition)February 2015文章编号:1000-565X(2015)02-0107-07 收稿日期:2014-08-06倡基金项目:国家工信部重点产业振兴和改造技术专项(吉工信投资[2011]350) Foundation item :SupportedbytheNationalMinistryKeyIndustrialRevitalizationandTransformationofSpecialTechnology(Minis-tryofJilinProvince([2011]350) 作者简介:滕菲(1985-),女,博士生,主要从事汽车材料加工研究.E-mail:tengfei325@126.com矩形截面型材三维拉弯成形的回弹预测倡滕菲1 梁继才1 张万喜1 王雪2 高嵩1(1.大连理工大学汽车工程学院∥工业装备结构分析国家重点实验室,辽宁大连116024;2.吉林大学材料科学与工程学院,吉林长春130022)摘 要:设计了用于三维拉弯成形的、可重构的柔性模具,并采用支持向量回归机和有限元模拟对柔性三维拉弯成形的回弹进行预测.使用有限元法分析了对回弹量影响较大的6个因素(包括材料参数、几何参数和工艺参数),以及它们对回弹的影响趋势.选用这6个参数设计有限元三维拉弯模拟实验,并用模拟结果训练和检验支持向量回归机回弹预测模型.通过与广泛应用的神经网络预测方法的预测值和有限元模拟试验结果的比较,检验该回弹预测模型的准确性.研究发现,该模型与神经网络相比具有更高的准确度,在试验中根据该模型预测的回弹量对模具型面进行相应的补偿,可以有效地减小回弹和形状偏差.关键词:型材;回弹预测;支持向量回归机;人工神经网络;三维拉弯成形中图分类号:TG386doi:10.3969/j.issn.1000-565X.2015.02.016 随着汽车轻量化的发展,铝型材已广泛应用于汽车行业当中[1-2].在铝型材拉弯成形过程中,回弹是影响成形质量的主要原因,其引起的与目标形状的偏差导致装配困难[3-4].因此,研究拉弯成形过程中回弹产生的原因及对回弹量进行预测具有重要的意义[5-6].Clausen等[7]探讨了拉伸力和应变硬化性能对回弹的影响规律.Miller等[8]基于截面在拉弯成形过程中长度不变的假设,提出了一种简单的回弹预测模型,并证明较大的拉力能够减小回弹.Oliveira等[9]研究发现,在回弹预测过程中应变硬化的影响没有前人研究的那么大.Yu等[10]研究了工艺参数对尺寸精度的影响,如压边力和拉力等.Panthi等[11]采用有限元法对板料成形回弹进行预测,研究了材料性质和几何参数对回弹的影响,结果表明,回弹量随弹性模量的增大而减小,随屈服应力增大而增大.以上这些研究表明,回弹随拉弯过程中拉力的增大而减小,在拉弯成形过程中影响回弹量的主要因素包括材料性质、几何参数和工艺参数.有限元是较为常用的预测回弹的方法,但它需要消耗大量的时间,通过训练和结合神经网络能够很好地解决这一问题.人工神经网络(ANN)结合有限元方法已广泛应用于回弹预测当中.Kazan等[12]提出了一种用于折弯过程中预测回弹的神经网络模型,方法中采用有限元模拟得到的数据训练该模型.Nasrollahi等[13]提出了一种采用神经网络和有限元法预测带孔薄板回弹的模型.Song等[14]基于人工神经网络方法建立了T型截面梁弯曲过程的回弹预测模型.用于回归预测的支持向量机叫做支持向量回归(SVR),目前已广泛应用于诸多领域,它能够实现少量样本的回归求解.龙玲等[15]采用SVR建立了起皱和破裂的非线性拟合,研究证实了SVR的准确性高于ANN;Liu等[16]提出了基于SVR的非线性问题代理模型,该模型的准确性和有效性已被证实;Singh等[17]采用SVR预测了冲压拉深过程中杯壁的厚度变化,研究表明采用SVR模型预测精度高于ANN.这些研究表明,SVR比传统技术ANN具有更强的泛化能力,并且能够更好地解决非线性预测问题,同时SVR能够预测板料成形等复杂问题.但是,SVR很少应用于铝型材拉弯成形回弹的预测.文中首先介绍了柔性三维拉弯模具和SVR原理;然后通过有限元模拟确认对回弹影响较大的因素;采用这些因素作为设计变量进行有限元三维拉弯模拟,建立型材柔性三维拉弯成形回弹预测的SVR模型,其中预测模型的训练样本是有限元数值模拟结果;最后,对三维拉弯成形SVR回弹预测模型的精度进行验证,将SVR模型和ANN模型的预测结果和试验结果进行比较,检验SVR模型的预测精度,并用试验对采用SVR预测模型得到的回弹量对柔性三维拉弯模具进行型面补偿后减小回弹的有效性进行验证.1 柔性模具和SVR1畅1 柔性三维拉弯模具 柔性拉弯成形模具由若干单元体组成,这些单元体代替了传统的整体模具.柔性拉弯模具的型面可通过调节单元体的位移和旋转成形滑块实现重构.每个基本体由支架、垂直导轨、导向滑块、成形面滑块,以及限位元件等构成,并安装在可以前后移动的独立支架上,如图1所示.型材三维拉弯成形过程首先实现水平面的弯曲,然后再进行垂直面弯曲.(a)前视图 (b)左视图图1 基本体示意图Fig畅1 Diagramoftheunit-body1—高度控制螺杆;2—垂直销轴;3—水平销轴;4—螺栓;5—支架;6—导向键;7—垂直导轨;8—成形面滑块底板;9—导向滑块;10—多点模具;11—垫块1畅2 回弹评价常见的回弹评价方法有3种:曲率半径的变化量、回弹角的变化量和回弹法向位移的变化量,如图2所示.很多研究者采用法向位移的变化作为衡量回弹大小的指标.但是该方法适用于二维拉弯,而不适用于三维拉弯.三维拉弯是在水平面和垂直面都进行拉弯成形,故采用法向位移不能完整地表示出回弹的大小.文中针对三维拉弯成形的特点,采用水平面拉弯成形和垂直面拉弯成形的回弹角来表征回弹量.回弹角通过以下公式计算:δ=θ-θ0(1)式中,θ为变形区域回弹后的圆心角,θ0为变形区域回弹前的圆心角,θ=arcsinx sR (2)θ0=arcsinx sR 0(3)R 0为目标曲率半径,R 为回弹后的曲率半径,x s、y s分别为回弹后变形区域末端节点的水平面内坐标.图2 回弹量评价Fig畅2 Springbackevaluation1畅3 支持向量机支持向量机是基于统计学理论和结构风险最小化原则建立起来的新机器学习方法.支持向量机主要解决非线性问题,通过核函数把初始空间非线性问题转化成高维特征空间内的线性问题,然后在高维特征空间内对线性问题求解[18].支持向量机用于解决回归问题时称为支持向量机回归(SVR),SVR能够较好地解决小样本求解问题.SVR的目的是为了寻找一决策函数y =<w ·x >+b ,求解非线性回归问题的过程如下:(1)给定一个用于训练的样本集合T =x 1,y 1,...,x i ,y i ∈R n ×Y1(4)(x i ∈R n,y i ∈R ,i =1,...,l )为了推断任意一个输入值x 所对应的输出值y ,需要根据式(4)在实数集R 上寻找一个实值函数801华南理工大学学报(自然科学版)第43卷g (x ).这类问题属于在n 维空间R n内的回归问题,回归问题分为线性回归和非线性回归问题,而三维拉弯成形过程回弹预测属于非线性回归.(2)选择恰当的核函数K (x ,x i ),以及适当的精度ε和惩罚函数C .通常情况下采用多项式核函数和高斯径向基核函数.多项式核函数:K (x ,x i )=[(x ,x i )+1]d(5)高斯径向基核函数:K (x ,x i )=exp-‖x -x i ‖22a2(6)(3)构造并求解凸二次规划问题:minα(倡)∈R 2l 12∑li ,j =1α倡i -αi α倡j -αj K x i ,x j +ε∑li =1α倡i+αi -∑li =1y i α倡i -αi(7)s畅t ∑li =l αi -α倡i=0.(0≤αi ,α倡i ≤cl ,i =1,2,...,l )这个问题的解为:α倡=(α1,α倡1,…,αl ,α倡l )(4)构造决策函数:f x =∑li =1α倡i -αi K x i ,y j +b (8)偏置b -为b -=12y j +y k -∑li =1α倡i-αi K (x i ,x j )+∑li =1α倡i-αi K (x i ,x k))(9)αi倡∈0,C l2 有限元分析2畅1 正交试验 型材拉弯成形回弹量主要受到材料参数、几何参数和工艺参数的影响.根据不同条件对回弹影响的分析,文中选取弹性模量E 、屈服应力σ0、水平弯曲角度θh、垂直弯曲角度θv、预拉量δ0和补拉量δ1作为正交试验的因子,这些因子的变化范围如表1所示,各个因子在各自范围内选取5个水平.如果采用六因素五水平全面的试验方法,则需要进行56组试验,利用正交试验设计安排试验方案,能够显著提高试验效率,减少试验数量,并能够保证结果的合理性.因此,使用L25(56)正交表设计试验方案,通过数值模拟获得训练和检验数据.为了增加样本数量,选择成形效果良好的另外15组数据增加到样本中,那么就有40组样本用于SVR模型的训练和检验.表1 正交试验设计输入参数及其变化范围Table1 Inputparametersandtheirrangesfororthogonaldesign参数变化范围弹性模量/MPa50000~250000屈服应力/MPa100~300预拉量/%0畅6~1畅4补拉量/%0畅6~1畅4水平弯曲角度/(°)10~30垂直弯曲角度/(°)10~302畅2 有限元模拟数值模拟采用商业有限元软件ABAQUS,其中ABAQUS/Explicit模块模拟型材三维拉弯成形过程,ABAQUS/Standard模块模拟卸载回弹过程.考虑到边界条件和加载的对称性,取1/2模型进行模拟.图3为柔性三维拉弯成形装配图,由铝型材、若干单元体和夹钳组成.型材的长度为1m,柔性三维拉弯成形模具由16组单元体构成,型材目标弯曲半径为1500mm,其他参数根据正交试验进行设计.考虑到夹钳和单元体的变形不需要计算,为了提高计算速度,夹钳和基本体采用离散刚体壳单元,夹钳与型材绑定,型材选用离散实体单元.图4为型材回弹前后形状对比,图中黑色图形为回弹前的型材,绿色图形为回弹后的型材,在型材的端点处回弹较明显.在三维拉弯成形过程中,首先完成水平面弯曲,然后进行垂直面弯曲.在预拉阶段,模具固定,通过对夹钳施加轴向位移实现型材的拉伸;在弯曲阶段,采用位移-时间曲线以1m/s速率控制型材逐步弯曲与模具成形面贴合;最后,施加切向位移对型材进行补拉.面与面的接触采用罚函数法.图3 有限元模型装配图Fig畅3 Assembling-upofthesimulationmodel901 第2期滕菲等:矩形截面型材三维拉弯成形的回弹预测图4 三维拉弯成形回弹Fig畅4 Springbackofthree-dimensionstretchbending为了获得样本数据需要进行40组有限元模拟,其中20组用于训练SVR和ANN模型,剩余20组用于检验SVR和ANN模型的准确性.各因素的极差如表2所示.表2 水平面和垂直面各因素极差Table2 Rangeofvariousfactorsinhorizontalandverticalplanes因素极差水平面垂直面E0畅6850畅402σ00畅2230畅103δ00畅2790畅207δ10畅2320畅232θh0畅8820畅126θv0畅2090畅736由表2可以看出,对于水平面拉弯回弹,影响较大的是水平弯曲角度、弹性模量和预拉量,而补拉量、屈服应力和垂直方向弯曲角度对回弹影响相对较小;对于垂直面回弹,影响较大的是垂直方向弯曲角度、弹性模量和补拉量;而预拉量、水平弯曲角度和屈服应力对回弹影响相对较小.3 回弹预测3畅1 SVR模型的训练 表1中的6组参数设为输入参数,水平方向回弹角θhs和垂直方向回弹角θvs作为输出参数.由表1可以看出,不同参数的输入值存在较大的量级差异,训练和检验数据需进行归一化处理.归一化能有效改善预测精度,使数据分布在较小的范围内,训练和检验数据经归一化后处于[-1,1]之间.核函数的选择对最终的预测结果有很大的影响,文中采用台湾大学开发的Libsvm-3畅17程序包进行回归预测.SVR分为epsilon-SVR和nu-SVR,核函数有3种类型:线性、多项式和径向基函数(RBF).为了找到SVR类型和核函数的最佳组合,对不同的组合进行研究,结果如表3所示.研究发现,采用epsilon-SVR和径向基核函数的回弹预测模型具有更高的准确性.表3 SVR类型和核函数的组合结果Table3 ResultsofcombinationofSVRclassandkernelfunctionSVR核函数迭代次数均方误差相关系数epsilon-SVR线性1110畅1098970畅745366epsilon-SVR多项式210畅2809370畅201485epsilon-SVR径向基20340畅0901590畅744558nu-SVR线性310畅2112220畅662721nu-SVR多项式200畅3091940畅269683nu-SVR径向基1800畅1887480畅461243在采用SVR模型预测回弹之前,需要确定惩罚系数C和参数g的大小.C和g是平衡模型的适应性和预测准确性的重要参数,对模型最终的预测结果有很大影响.在不同的C和g值组合中,通常采用交叉验证方法找出具有最高预测精度的组合.文中采用gridregression函数寻找最佳的C和g值组合,根据研究,C=512、g=1时预测结果精度最高,均方误差为0畅03426.在40组样本中随即选取20组作为SVR模型的训练样本.3畅2 SVR模型的检验采用剩余样本对SVR预测模型进行检验.为了检验SVR算法回弹预测的精度,文中选用目前已在回弹预测方面得到广泛应用的人工神经网络算法(ANN)进行对比.神经网络有3层网络结构,包括输入层、隐含层和输出层,其中隐含层包含56个节点,输出层2个节点.选用与训练SVR模型相同的数据对神经网络模型进行训练,训练误差控制在10-5内.图5为SVR和ANN模型预测结果的对比,可以看出采用SVR算法预测回弹值与实验数据更加接近;表4和5分别为两个方向上回弹量的误差比较,从均方误差的对比中可以看出SVR模型预测回弹的准确性高于ANN模型. (a)水平面回弹角预测011华南理工大学学报(自然科学版)第43卷 (b)垂直面回弹角预测图5 SVR和ANN模型的预测结果对比Fig畅5 ComparisonofspringbackpredictionresultsobtainedbySVRandANN表4 水平方向回弹角的误差对比Table4 Comparisonoferrorsofspringbackangleinthehori-zontaldirection预测模型均值最小值最大值平均误差SVR0畅702870畅102851畅133180畅11353ANN0畅612030畅398610畅783590畅30698表5 垂直方向回弹角的误差对比Table5 Comparisonoferrorsofspringbackangleintheverticaldirection预测模型均值最小值最大值平均误差SVR0畅951790畅636681畅231860畅12543ANN1畅073260畅542441畅526480畅185564 试验检验文中通过两组柔性三维拉弯成形试验,检验SVR模型对回弹的预测精度.一组试验用于检验预测模型的准确性,另一组试验根据SVR模型的回弹预测值,对模具型面进行相应的补偿,从而达到减小回弹的目的.矩形截面型材采用AA6082铝合金,其弹性模量E为71GPa,泊松比ν为0畅345,屈服应力σ0为139畅5MPa,假定材料服从Hill’48各向异性屈服准则,F=1畅625,G=1畅476,H=0畅524,N=4畅047.表6为预测模型的输入数据,表7为分别采用SVR和ANN模型的预测结果和误差.基于相同的输入数据,通过真实的柔性三维拉弯成形试验获得的水平方向回弹角和垂直方向回弹角分别为0畅685°和0畅861°;表7所示的两种模型的预测误差再次证明SVR预测结果更加准确.表6 预测模型的输入数据Table6 InputofthepredictionmodelsE/GPaσ0/MPaδ0/%δ1/%θh/°θv/°71139畅50畅80畅83030表7 模型预测结果及误差Table7 Predictionresultsanderrorsofthemodels模型预测θhs/(°)预测θvs/(°)水平回弹角误差/%垂直回弹角误差/%SVR0畅6562830畅8163624畅235畅14ANN0畅8726451畅13756427畅332畅1基于两种模型对回弹的预测结果,对模具型面进行相应的补偿,补偿后对型材进行柔性三维拉弯成形试验,从而获得根据两种模型补偿后的形状偏差.两种模型补偿后的型材形状偏差如图6所示.图6 模具补偿后形状误差的对比Fig畅6 Comparisonofshapeerrorafterthedieshapecompensation由图6可以看出,根据ANN预测对模具补偿后的形状偏差大于SVR预测补偿后的偏差.由此可知,SVR回弹补偿比ANN准确,从而证明SVR的回弹预测比ANN的回弹预测精度高.5 结语通过设计正交试验进行有限元模拟测试6组参数(包括材料参数、几何参数和工艺参数)对三维拉弯成形回弹影响大小进行分析.分析证明这些参数对水平面回弹角与垂直面的回弹角影响程度不同.设计了选用这些参数作为输入参数、对柔性三维拉弯成形进行回弹预测的SVR模型,并将该模型与ANN模型的预测精度进行对比.实验结果证明,采用SVR预测模型能够实现对三维拉弯成形回弹的预测,且预测精度高于ANN.采用SVR模型回弹预测值对三维拉弯成形试验的模具型面进行相应补偿,能够有效减小回弹和形状偏差.111 第2期滕菲等:矩形截面型材三维拉弯成形的回弹预测参考文献:[1] 李落星,周佳,张辉.车身用铝、镁合金先进挤压成形技术及应用[J].机械工程学报,2012,48(18):35-43.LiLuo-xing,ZhouJia,Zhanghui.Advancedextrusiontechnologyandapplicationofaluminummagnesiumalloyforvehiclebody[J].JournalofMechanicalEngineering,2012,48(12):35-43.[2]马铭图,李志刚,易红亮,等.汽车轻量化及铝合金的应用[J].世界有色金属,2006,10:10-14.MaMing-tu,LiZhi-gang,YiHong-liang,etal.Polarizationoflight-weightedcarsandapplicationofaluminumalloys[J].WorldNonferrousMetals,2006,10:10-14.[3]梁继才,滕菲,高嵩,等.柔性三维拉弯成形模具型面修正关键技术的研究[J].机械工程学报,2013,49(17):187-192.LiangJi-cai,TengFei,GaoSong,etal.Keytechnologiesresearchontheiterativedie-faceadjustmentintheform-ingprocessofflexiblethree-dimensionalstretch-bending[J].JournalofMechanicalEngineering,2013,49(17):187-192.[4]梁继才,滕菲,高嵩,等.矩形铝型材柔性三维拉弯工艺的多目标优化[J].华南理工大学学报:自然科学版,2013,41(9):143-148.LiangJi-cai,TengFei,GaoSong,etal.Multi-objectiveop-timizationofflexiblethree-dimensionalstretch-bendingformingprocessrectangularhollowaluminumprofiles[J].JournalofSouthChinaUniversityofTechnology:NaturalScienceEdition,2013,41(9):143-148.[5]徐义,李落星,李光耀,等.型材弯曲工艺的现状及发展前景[J].塑性工程学报,2008,15(3):61-70.XuYi,LiLuo-xing,LiGuang-yao,etal.Extrusionben-ding:method,applicationandrecentdevelopment[J].JournalofPlasticityEngineering,2008,15(3):61-70.[6]刁可山,周贤宾,李晓星,等.矩形截面型材拉弯成形[J].北京航空航天大学学报,2005,31(2):134-137.DiaoKe-shan,ZhouXian-bin,LiXiao-xing,etal.Stretchbendingofaluminumextrusion[J].JournalofBeijingUniversityofAeronauticsandAstronautics,2005,31(2):134-137.[7]ClausenArildH,HopperstadOddS,LangsethMagnus.Sensitivityofmodelparametersinstretchbendingofalu-minumextrusions[J].InternationalJournalofMechani-calSciences,2001,43:427-453.[8]MillerJE,KyriakidesS,CoronaE.Onbend-stretchform-ingofaluminumextrudedtubes-Ⅱ:analysis[J].Interna-tionalJournalofMechanicalSciences,2001,43:1319-1338.[9]OliveiraMC,AlvesJL,ChaparroB.M,etal.Studyontheinfluenceofwork-hardeningmodelinginspringbacksimulationaccuracyofV-freebending[J].InternationalJournalofPlasticity,2007,23:516-543.[10] YuZhong-qi,LinZhong-qin.Numericalanalysisofdi-mensionprecisionofU-shapedaluminumprofilerotaystretchbending[J].TransactionsofNonferrousMetalsSocietyofChina,2007,17:581-585.[11]PanthiK,RamakrishnanN,AhmedMeraj,etal.Finiteele-mentanalysisofsheetmetalbendingprocesstopredictthespringback[J].MaterialandDesign,2010,31:657-662.[12]KazanR,FiratM,TiryakiAE.Predictionofspringbackinwipe-bendingprocessofsheetmetalusingneuralnetworks[J].MaterialsandDesign,2009,30(2):418-423.[13]NasrollahiV,ArezooB.Predictionofspringbackinsheetmetalcomponentswithholesonthebendingarea,usingexperiments,finiteelementandneuralnetworks[J].MaterialsandDesign,2012,36:331-336.[14]SongY,YuZ.SpringbackpredictioninT-sectionbeambendingprocessusingneuralnetworksandfiniteele-mentmethod[J].ArchiveofCivilandMechanicalEn-gineering,2013,3:229-241.[15]龙玲,殷国富,宋超,等.基于支持向量机的随机聚焦搜索算法优化冲压成形工艺[J].四川大学学报:工程科学版,2012,44(5):220-225.LongLing,YinGuo-fu,SongChao,etal.ApplicationofstochasticfocusingsearchalgorithmbasedonSVMinoptimizationofsheetmetalformingprocess[J].JournalofSichuanUniversity:EngineeringScienceEdition,2012,44(5):220-225.[16]LiuYu-lin,ChenWen-liang,DingLi-ping,etal.Re-sponsesurfacemethodologybasedonsupportvectorre-gressionforpolygonblankshapeoptimizationdesign[J].InternationalJournalofAdvancedManufacturingTechnology,2013,66:1397-1405.[17]SinghSwadenshKumar,GuptaAmitKumar.Applicationofsupportvectorregressioninpredictingthicknessstrainsinhydro-mechanicaldeepdrawingandcompari-sonwithANNandFEM[J].CIRPJournalofManufac-turingScienceandTechnology,2010,3:66-72.[18]丁世非,齐丙娟,谭红艳.支持向量机理论与算法研究综述[J].电子科技大学学报,2011,40(1):2-10.DingShi-fei,QiBing-juan,TanHong-yan.Anoverviewontheoryandalgorithmofsupportvectormachines[J].JournalofUniversityofElectronicandScienceandTechnologyofChina,2011,40(1):2-10.211华南理工大学学报(自然科学版)第43卷Springback Prediction of Rectangular Profiles During Three -DimensionStretch Bending FormingTeng Fei 1 Liang Ji -cai 1 Zhang Wan -xi 1 Wang Xue 2 Gao Song1(1.SchoolofAutomotiveEngineering//StateKeyLaboratoryofStructuralAnalysisforIndustrialEquipment,DalianUniversityofTechnology,Dalian116024,Liaoning,China;2.CollegeofMaterialsScienceandEngineering,JilinUniversity,Changchun130022,Jilin,China)Abstract :Inthispaper,first,areconfigurableflexibledieforthethree-dimensionstretchbendingformingisde-signed,andthespringbackofprofilesduringtheformingispredictedbymeansofthesupportvectorregressionandthefiniteelementsimulation.Then,sixfactorsthatgreatlyaffectthespringbackmagnitude(includingmaterialpa-rameters,geometricalparametersandprocessparameters)areanalyzedbyusingthefiniteelementmethod,andtheirimpacttrendsonthespringbackarealsoinvestigated.Moreover,thesesixfactorsareemployedtodesignasimulationofthree-dimensionfinite-elementstretchbending,andthesimulatedresultsareusedtotrainandtestthespringbackpredictionmodelbasedonthesupportvectorregressionmachine.Finally,forthepurposeofverifyingtheproposedapringbackpredictionmodel,thepredictedresultsarecomparedwiththoseobtainedbythewidely-usedneuralnetworkforecastingmethodandthefiniteelementsimulation.Itisfoundthattheproposedmodelismoreaccuratethantheneuralnetwork-basedmethod,andthat,inexperiments,suitablecompensationstothedieshapeaccordingtothespringbackvaluepredictedbythemodelmayeffectivelyreducethespringbackandtheshapedeviation.Key words :profile;springbackprediction;supportvectorregressionmachine;artificialneuralnetworks;three-di-mensionstretchbendingforming (上接第106页)机叶片结构优化[J].哈尔滨工程大学学报,2014,35(7):895-900.ChenJin,MaJin-cheng,WangQuan,etal.StructuraloptimizationofthewindturbinebladecombiningtheANSYSsecondarydevelopment[J].JournalofHarbinEngineeringUniversity,2014,35(7):895-900.[15] ShenWZ,MikkelsenR,S宝rensenJN,etal.Tiplosscorrectionforwindturbinescomputations[J].WindEnergy,2005,8:457-475.[16]TimmerW,PrjomVT.SummaryoftheDelftUniversitywindturbinededicatedairfoils[J].JournalofSolarEn-ergyEngineering,2003,125:488-496.[17]陈进,张石强,王旭东,等.基于粗糙度敏感性研究的风力机专用翼型设计[J].空气动力学学报,2011,29(2):142-149.ChenJin,ZhangShi-qiang,WangXu-dong.etal.Dedi-catedwindturbineairfoildesignbasedontheroughnesssensitivityconsiderations[J].ActaAerodynamicaSini-ca,2011,29(2):142-149.Blade Analysisof Wind Turbine Considering AeroelasticityChen Jin Li Song -lin Guo Xiao -feng Sun Zhen -ye(StateKeyLaboratoryofMechanicalTransmission,ChongqingUniversity,400044,Chongqing,China)Abstract :Anovelapproach,whichutilizesamodifiedbladeelement-momentumtheoryandthefiniteelementmethod,ispresentedtoanalyzethebladeperformanceofwindturbineconsideringaeroelasticity.Then,theap-proachisusedtoanalyzetheperformanceofthebladesofan850MWwindturbineatvariouswindspeeds.There-sultsshowthataeroelasticityobviouslyinfluencestheperformanceoflarge-sizewindturbinesathighwindspeedandgreatlyreducestheaccuracyoftheoriginaldesign.Thepresentedapproachisofguidingsignificancefortheaerody-namicshapedesign,loadcalculationandstructuraldesignofblades.Key words :windturbine;bladeperformance;aeroelasticity;bladeelement-momentumtheory;finiteelementa-nalysis311 第2期滕菲等:矩形截面型材三维拉弯成形的回弹预测矩形截面型材三维拉弯成形的回弹预测作者:滕菲, 梁继才, 张万喜, 王雪, 高嵩, Teng Fei, Liang Ji-cai, Zhang Wan-xi,Wang Xue, Gao Song作者单位:滕菲,梁继才,张万喜,高嵩,Teng Fei,Liang Ji-cai,Zhang Wan-xi,Gao Song(大连理工大学汽车工程学院∥工业装备结构分析国家重点实验室,辽宁大连,116024), 王雪,Wang Xue(吉林大学材料科学与工程学院,吉林长春,130022)刊名:华南理工大学学报(自然科学版)英文刊名:Journal of South China University of Technology (Natural Science Edition)年,卷(期):2015(2)1.李落星,周佳,张辉车身用铝、镁合金先进挤压成形技术及应用[期刊论文]-机械工程学报 2012(18)2.马鸣图,李志刚,易红亮,向晓峰,方平汽车轻量化及铝合金的应用[期刊论文]-世界有色金属 2006(10)3.梁继才,滕菲,高嵩,陈广义,魏志勇柔性三维拉弯成形模具型面修正关键技术的研究[期刊论文]-机械工程学报2013(17)4.梁继才,滕菲,高嵩,陈广义,魏志勇矩形铝型材柔性三维拉弯工艺的多目标优化[期刊论文]-华南理工大学学报(自然科学版) 2013(9)5.徐义,李落星,李光耀,钟志华型材弯曲工艺的现状及发展前景[期刊论文]-塑性工程学报 2008(3)6.刁可山,周贤宾,李晓星,金朝海矩形截面型材拉弯成形[期刊论文]-北京航空航天大学学报 2005(2)7.Clausen Arild H;Hopperstad Odd S;Langseth Magnus Sensitivity of model parameters in stretch bending of alu-minum extrusions 2001ler J E;Kyriakides S;Corona E On bend-stretch form-ing of aluminum extruded tubes-Ⅱ:analysis 20019.Oliveira M C;Alves J L;Chaparro B.M Study on the influence of work-hardening modeling in springback simulation accuracy of V-free bending 200710.YU Zhong-qi,LIN Zhong-qin Numerical analysis of dimension precision of U-shaped aluminium profile rotary stretch bending[期刊论文]-中国有色金属学会会刊(英文版) 2007(3)11.Panthi K;Ramakrishnan N;Ahmed Meraj Finite ele-ment analysis of sheet metal bending process to predict the springback 201012.Kazan R;Firat M;Tiryaki A E Prediction of springback in wipe-bending process of sheet metal using neural networks 2009(2)13.Nasrollahi V;Arezoo B Prediction of springback in sheet metal components with holes on the bending area,using experiments,finite element and neural networks 201214.Song Y;Yu Z Springback prediction in T-section beam bending process using neural networks and finite ele-ment method 201315.龙玲,殷国富,宋超,彭必友基于支持向量机的随机聚焦搜索算法优化冲压成形工艺[期刊论文]-四川大学学报:工程科学版 2012(5)16.Liu Yu-lin;Chen Wen-liang;Ding Li-ping Re-sponse surface methodology based on support vector re-gression for polygon blank shape optimization design 201317.Singh Swadensh Kumar;Gupta Amit Kumar Application of support vector regression in predicting thickness strains in hydro-mechanical deep drawing and compari-son with ANN and FEM 2010。
钣金V形折弯成形的回弹控制

· 36·
材
料
科
学
与
工
艺
第 20 卷
和多目标遗传算法建立了基于回弹控制的成形工 艺参数的集成优化模型. 国外学者也在理论模型 分析不同折弯工艺 的改进方面做了大量的研究, 参数条件下的钣金折弯回弹控制问题 等
[5 ] [3 - 4 ]
. Gan
在理论分析的基础上, 提出一种考虑折弯回
弹的下模具通用设计方法; 在有限元分析方面, 运 用有限元方法分析钣金折弯回弹的预测与控制 . Papeleux 等[6]应用有限元的方法分析钣金折弯的 回弹变形, 并通过实验验证分析结果的准确性 . 同 学者们也对钣金折弯回弹的影响因素进行了 时, 大量的研究, 分析得出材料性能参数、 板料厚度、 折弯角度及模具几何参数对于回弹变形的影 响
2 n ( n + 1 ) /2
模具参数和板料材料性能参数, 研究 料厚度参数、 了折弯深度参数的计算方法, 利用该方法可以得 到上模具的最终折弯深度参数, 完成折弯过程.
(
式中: K 为强化系数; n 为强化指数. 该材料模型可以进一步简化为 Rσ s R =4 r ET σ ( ) - 3 ( RET ) + 1.
s =1 c
行折弯试验. 其厚度及性能参数如表 1 所示. 加载 20ʎ , 25ʎ ) , 与卸载 的 折 弯 角 度 设 定 为: 30ʎ ( 10ʎ , 35ʎ ( 15ʎ , 25ʎ , 30ʎ ) , 40ʎ ( 20ʎ , 30ʎ , 35ʎ ) , 45ʎ 35ʎ , 40ʎ ) . 其中 ( θ1 , ( 25ʎ , θ2 , θ3 ) 表示增量折弯角 首先上模具位 度. 如设定折弯最终的角度为 40ʎ , 移使板料加载成形为 20ʎ , 板料卸载并测量板料 回弹后的角度; 然后上模具继续下移使得板料分 别加载成形为 30ʎ 和 35ʎ , 卸载并获得板料回弹后 的角度参数; 最后利用已获取的回弹角度参数计 算得到板料的材料性能参数值, 进而确定最终的 折弯深度参数, 上模具继续下移, 板料加载完成整 个折弯加工过程.
3.6弯曲件的回弹
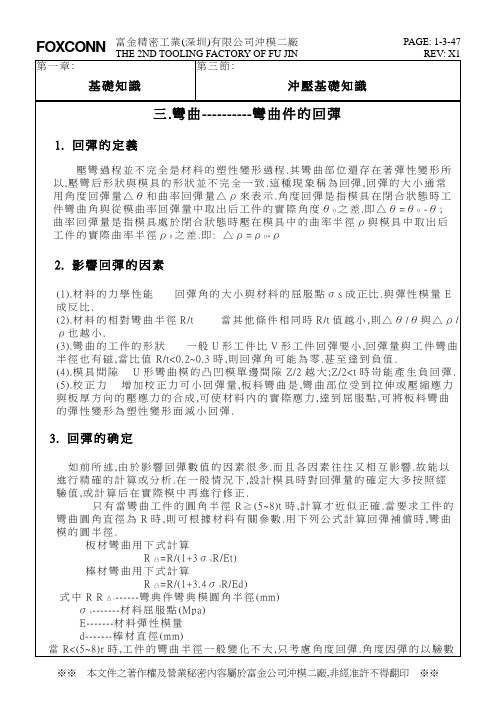
16°30'
5
1°
4°
7°
10°
12°30'
15°
18°
6
2°
5°
8°
11°
13°30'
16°30'
19°30'
2A12(軟)
LY12Y)
2
-1°30'
0°
1°30'
3°
5°
7°
8°30'
3
-1°30'
0°30'
2°30'
4°
6°
8°
9°30'
4
-1°
1°
3°
4°30'
6°30'
9°
10°30
(4).模具間隙U形彎曲模的凸凹模單邊間隙Z/2越大;Z/2<t時岢能產生負回彈.
(5).校正力增加校正力可小回彈量,板料彎曲是,彎曲部位受到拉伸或壓縮應力與板厚方向的壓應力的合成,可使材料內的實際應力,達到屈服點,可將板料彎曲的彈性變形為塑性變形面減小回彈.
3.回彈的确定
如前所述,由於影響回彈數值的因素很多.而且各因素往往又相互影響.故能以進行精確的計算或分析.在一般情況下,設計模具時對回彈量的確定大多按照經驗值,或計算后在實際模中再進行修正.
三.彎曲----------彎曲件的回彈
1.回彈的定義
壓彎過程並不完全是材料的塑性變形過程.其彎曲部位還存在著彈性變形所以,壓彎后形狀與模具的形狀並不完全一致.這種現象稱為回彈,回彈的大小通常用角度回彈量△θ和曲率回彈量△ρ來表示.角度回彈是指模具在閉合狀態時工件彎曲角與從模曲率回彈量中取出后工件的實際角度θ0之差.即△θ=θ0-θ;曲率回彈量是指模具處於閉合狀態時壓在模具中的曲率半徑ρ與模具中取出后工件的實際曲率半徑ρ0之差.即:△ρ=ρ0-ρ
板材成形回弹过程数值模拟方法研究①
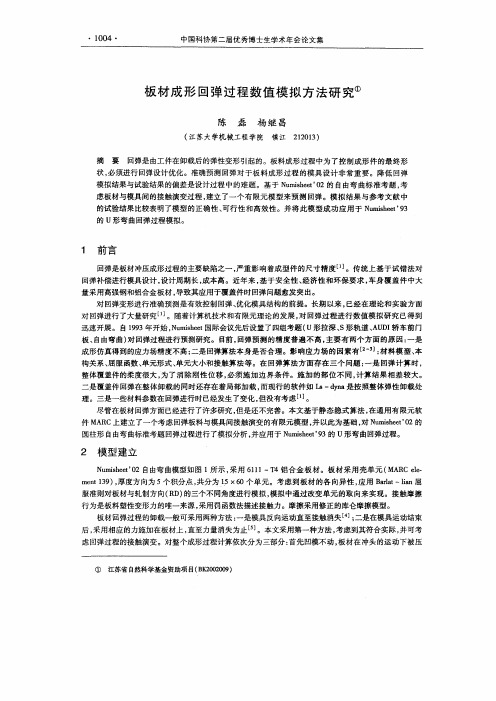
对回 弹进行了 大量研究〔 ’ 〕 。随着计算机技术和有限 元理论的发展, 对回弹过程进行数值模拟研究已得到
迅速开展。自1 9 9 3 年开始, N u m i s h e e t 国际会议先后设置了四组考题( U形拉深、 S 形轨道、 A U D I 轿车前门 板、 自由弯曲) 对回弹过程进行预测研究。目 前, 回弹预测的精度普遍不高, 主要有两个方面的原因: 一是
1 前言
回 弹 是 板材冲 压 成形过程的 主 要缺陷 之 一, 严重影响 着 成型件的尺寸精度川。 传统上基于 试错法对
回弹补偿进行模具设计, 设计周期长, 成本高。近年来, 基于安全性、 经济性和环保要求, 车身覆盖件中大 量采用高强钢和铝合金板材, 导致其应用于覆盖件时回弹问题愈发突出。 对回弹变形进行准确预测是有效控制回弹、 优化模具结构的前提。 长期以来, 已经在理论和实验方面
板材回 弹 过程的 卸载一 般可采用 两种 方法: 一 是模 具反向 运动直至 接触消失[ ]; ’ 二是 在 模具运动 结束 后, 采用相应的 力 施加 在板材上, 直至力 量消失 为 止[ [ 5 1 。 本 文采 用第一种方 法, 考虑到 其符 合实际, 并可考
虑回弹过程的接触演变。对整个成形过程计算依次分为三部分: 首先凹模不动, 板材在冲头的运动下被压
[ 2 ] N a r k e e r a n N a r a s i m h a n , M i c h a e l L o v e l l , P r e d i c t i n g s p r i n g b a c k i n s h e e t m e t a l f o r m i n g ; a n e x p l i c i t t o i m p l i c i t s e q u e n t i a l s o l u - t i o n p r o c e d u e, r F i n i t e E l e m e n t s i n A n a l y s i s a n d D e s i g n , 3 3 ( 1 9 9 9 ) ; 2 9 一 4 2