成型加工复习题
塑料成型工艺学复习材料
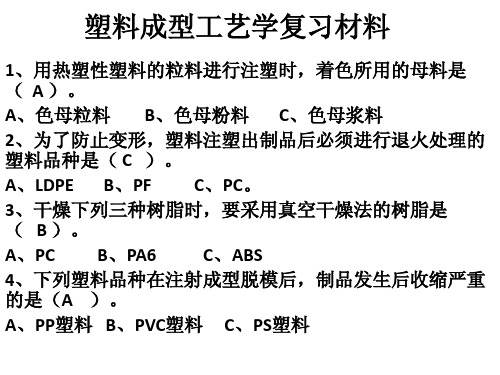
• • • • •
螺杆特性线 口模特性曲线 工作点 挤出吹膜吹胀比 冷冻线:当吹塑薄膜时(PE),管膜刚离开模 头时是透明的,至一定的高度由于冷却而结晶 (固化),变得不透明(浑浊),浑浊与透明 的交界线被称为冷冻线(霜白线)。 • 压缩率 • 硬化速率:用塑料压制标准试样(直径 100mm,厚5±0.2mm的圆片)时使制品物理, 化学性能达到最佳值时的速率s/mm厚,该值 小,硬化速率越大。
• 21、分散体又称塑料糊,是常温下可以流动的
固液混合物,主要应用于(C )。 • A 容器 B管材 C人造革 D以上都是
• 22、全电动注塑机较之于液压式或混合式注塑机,其 注射量精度及重复性( A )。 • A、更高 B、相近 C、更低 • 23、全电动注塑机的最突出的优点是(B )。 • A、对塑机零部件的质量要求低 B、重复精度 高 C、高的锁模压力
• 28.下列哪种情况塑件会产生应力开裂(B )。 A.在塑料中加入增强材料加以改性 B.金属嵌件 不进行预热,直接放入模具中 C.对塑件进行后处理D.成型前物料的预热 29.结构复杂的热固性塑料制件,固化速度应(D )。 A.快些 B.关系不大C.不能确定 D.不宜过快 30.在注射成型过程中,金属嵌件预热的目的是 ( C)。 A.可以加热物料 B.增加嵌件的强度 C.降低嵌 件周围塑料的收缩应力 D.有利于排气
A.物料温度B.室温C.模具温度D.以上都不
是
38.挤出成型模具被称为(D )。
A.牵引装置B.挤出成型零部件C.口模D.挤
出机头
• 39.挤出成型工艺过程与注射成型工艺过程最大的区 别是( D)。 A.挤出成型有牵引装置、冷却装置和切割装置,而注 射成型没有B.挤出成型模具不用预热,注射模具要预 热 C.挤出成型适用于热固性塑料,注射成型工艺适用于 热塑性塑料D.挤出成型过程是连续的,注射成型过 程是有间隔的 40.挤出速率是指(B )。 A.挤出机单位时间挤出的塑料容积B.单位时间内挤 出机口模挤出的塑料质量或长度C.牵引装置的速度 D.切割装置的速度
《工程材料及成型工艺》练习题(复习资料)
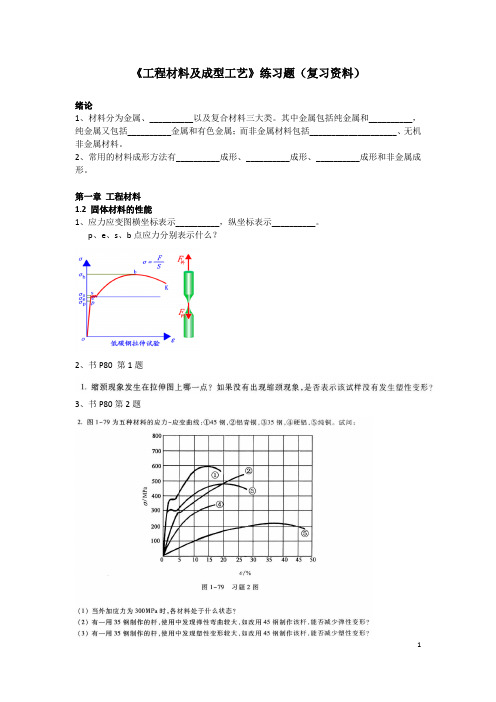
《工程材料及成型工艺》练习题(复习资料)绪论1、材料分为金属、__________以及复合材料三大类。
其中金属包括纯金属和__________,纯金属又包括__________金属和有色金属;而非金属材料包括____________________、无机非金属材料。
2、常用的材料成形方法有__________成形、__________成形、__________成形和非金属成形。
第一章工程材料1.2 固体材料的性能1、应力应变图横坐标表示__________,纵坐标表示__________。
p、e、s、b点应力分别表示什么?2、书P80 第1题3、书P80第2题4、机械零件在正常工作情况下多数处于()。
A.弹性变形状态B.塑性变形状态C.刚性状态D.弹塑性状态5、在设计拖拉机气缸盖螺栓时主要应选用的强度指标是()。
A.屈服强度B.抗拉强度C.伸长率D.断面收缩率6、用短试样做拉伸实验,根据公式,伸长率会更大,说明短试样塑性更好。
()7、工程上希望屈强比sbσσ高一些,目的在于()。
A.方便设计B.便于施工C.提高使用中的安全系数D.提高材料的有效利用率8、所有的金属材料均有明显的屈服现象。
()9、下列力学性能指标中,常被作为机械设计和选材主要依据的力学性能指标是()A.σb B.HBW C.δD.HRC10、在外力作用下,材料抵抗塑性变形和断裂的能力称为__________。
11、材料在外力去除后不能完全自动恢复而被保留下来的变形称__________。
12、金属材料抵抗硬物体压入的能力称为__________。
13、某仓库内1000根20钢和60钢热轧棒料被混在一起。
请问怎样用最简便的方法把这堆钢分开?14、常见的硬度表示方法有:__________硬度、__________硬度和维氏硬度。
15、当温度降到某一温度范围时,冲击韧性急剧下降,材料由韧性状态转变为脆性状态。
这种现象称为“__________”。
材料成型基础复习试题(含答案)

材料成型基础复习试题(含答案)试卷1⼀、思考题1.什么是机械性能?(材料受⼒作⽤时反映出来的性能)它包含哪些指标?(弹性、强度、塑性、韧性、硬度等)各指标的含意是什么?如何测得?2.硬度和强度有没有⼀定的关系?为什么? (有,强度越⾼,硬度越⾼)为什么?(都反映材料抵抗变形及断裂的能⼒)3.名词解释:过冷度,晶格,晶胞,晶粒与晶界,同素异晶转变,固溶体,⾦属化合物,机械混合物。
4.过冷度与冷却速度有什么关系?对晶粒⼤⼩有什么影响? (冷却速度越⼤过冷度越⼤,晶粒越细。
)5.晶粒⼤⼩对⾦属机械性能有何影响?常见的细化晶粒的⽅法有哪些? (晶粒越细,⾦属的强度硬度越⾼,塑韧性越好。
孕育处理、提⾼液体⾦属结晶时的冷却速度、压⼒加⼯、热处理等)6.说明铁素体、奥⽒体、渗碳体和珠光体的合⾦结构和机械性能。
7.默绘出简化的铁碳合⾦状态图,并填⼈各区域内的结晶组织。
8.含碳量对钢的机械性能有何影响?⼆、填表说明下列符号所代表的机械性能指标三、填空1. 碳溶解在体⼼⽴⽅的α-Fe中形成的固溶体称铁素体,其符号为F ,晶格类型是体⼼⽴⽅,性能特点是强度低,塑性好。
2. 碳溶解在⾯⼼⽴⽅的γ-Fe中形成的固溶体称奥⽒体,其符号为 A ,晶格类型是⾯⼼⽴⽅,性能特点是强度低,塑性⾼。
3. 渗碳体是铁与碳的⾦属化合物,含碳量为6.69%,性能特点是硬度⾼,脆性⼤。
4. ECF称共晶线线,所发⽣的反应称共晶反应,其反应式是得到的组织为 L(4.3%1148℃)=A(2.11%)+Fe3C 。
5. PSK称共析线线,所发⽣的反应称共析反应,其反应式是A(0.77%727 ℃)=F(0.0218%)+ Fe3C 得到的组织为珠光体。
6. E是碳在γ-Fe中的最⼤溶解度点,P是碳在α-Fe中的最⼤溶解度点, A l线即 PSK ,A3线即 GS , A cm线即 ES 。
7. 45钢在退⽕状态下,其组织中珠光体的含碳量是 0.77% 。
(完整版)塑料成型工艺及模具设计复习题及答案
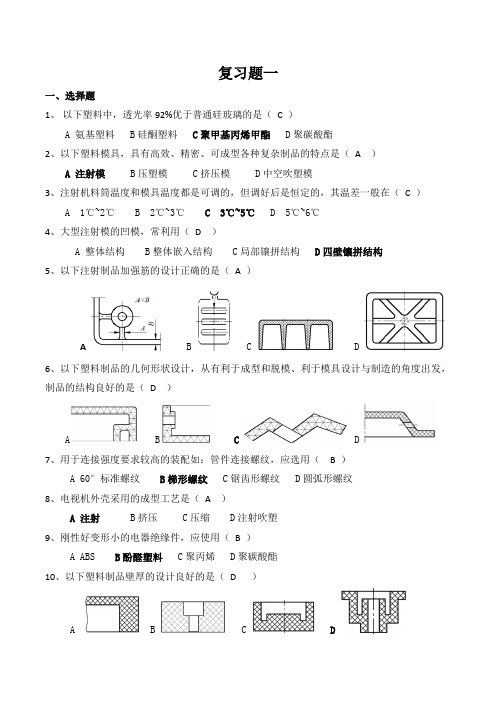
复习题一一、选择题1、以下塑料中,透光率92%优于普通硅玻璃的是(C )A 氨基塑料 B硅酮塑料 C聚甲基丙烯甲酯 D聚碳酸酯2、以下塑料模具,具有高效、精密、可成型各种复杂制品的特点是(A )A 注射模 B压塑模 C挤压模 D中空吹塑模3、注射机料筒温度和模具温度都是可调的,但调好后是恒定的,其温差一般在(C )A 1℃~2℃B 2℃~3℃C 3℃~5℃D 5℃~6℃4、大型注射模的凹模,常利用(D )A 整体结构 B整体嵌入结构 C局部镶拼结构D四壁镶拼结构5、以下注射制品加强筋的设计正确的是(A )A B C D6、以下塑料制品的几何形状设计,从有利于成型和脱模、利于模具设计与制造的角度出发,制品的结构良好的是( D )A B C D7、用于连接强度要求较高的装配如:管件连接螺纹,应选用( B )A 60°标准螺纹B梯形螺纹 C锯齿形螺纹 D圆弧形螺纹8、电视机外壳采用的成型工艺是(A )A 注射 B挤压 C压缩 D注射吹塑9、刚性好变形小的电器绝缘件,应使用(B )A ABS B酚醛塑料 C聚丙烯 D聚碳酸酯10、以下塑料制品壁厚的设计良好的是(D )A B C D二、填空题1、根据塑料的用途,塑料分为通用塑料、工程塑料和特种塑料三大类。
2、塑料注射成型工艺中保压的作用是防止熔料逆向倒流、补充收缩。
3、使注射模具浇注系统内的塑料保持熔融粘流态的方法有两种:一是隔热保温法,二是浇注系统加热法。
4、按分流道至浇口距离相等与否,其型腔和分流道排列分为平衡排列和非平衡排列。
5、尺寸小的模具型腔,主要进行强度计算,刚度再其次。
6、注射模的浇注部分是引导从注塑机喷嘴射入的熔融塑料顺利进入并充满各型腔的通道。
7、由于普通注射机仅仅在动模部分有顶出装置,注射时,人们总希望制品滞留在动模部分,这样不仅仅模具结构简单,而且取制件也方便。
8、高分子聚合物的分子结构有线性结构、支链形结构和网状体型结构。
材料成型工艺综合复习题

问答题1、吊车大钩可用铸造、锻造、切割加工等方法制造,哪一种方法制得的吊钩承载能力大?为什么?2、什么是合金的流动性及充形能力,决定充形能力的主要因数是什么?3、铸造应力产生的主要原因是什么?有何危害?消除铸造应力的方法有哪些?4.试讨论什么是合金的流动性及充形能力?5. 分别写出砂形铸造, 熔模铸造的工艺流程图并分析各自的应用范围.6. 液态金属的凝固特点有那些,其和铸件的结构之间有何相联关系?7. 什么是合金的流动性及充形能力,提高充形能力的因素有那些?8. 熔模铸造、压力铸造与砂形铸造比较各有何特点?他们各有何应用局限性?9. 金属材料固态塑性成形和金属材料液态成形方法相比有何特点,二者各有何适用范围?10. 缩孔与缩松对铸件质量有何影响?为何缩孔比缩松较容易防止?11. 什么是定向凝固原则?什么是同时凝固原则?各需采用什么措施来实现?上述两种凝固原则各适用于哪种场合?12. 手工造型、机器造型各有哪些优缺点?适用条件是什么?13. 从铁- 渗碳体相图分析,什么合金成分具有较好的流动性?为什么?14. 铸件的缩孔和缩松是怎么形成的?可采用什么措施防止?15. 什么是顺序凝固方式和同时凝固方式?各适用于什么金属?其铸件结构有何特点?16. 何谓冒口,其主要作用是什么?何谓激冷物,其主要作用是什么?17. 何谓铸造?它有何特点?18. 既然提高浇注温度可提高液态合金的充型能力,但为什么又要防止浇注温度过高?19.金属材料的固态塑性成形为何不象液态成形那样有广泛的适应性?20.. 冷变形和热变形各有何特点?它们的应用范围如何?21. 提高金属材料可锻性最常用且行之有效的办法是什么?为何选择?22. 金属板料塑性成形过程中是否会出现加工硬化现象?为什么?23. 纤维组织是怎样形成的?它的存在有何利弊?24.许多重要的工件为什么要在锻造过程中安排有镦粗工序?25. 模锻时,如何合理确定分模面的位置?26. 模锻与自由锻有何区别?27.板料冲压有哪些特点?主要的冲压工序有哪些?28. 间隙对冲裁件断面质量有何影响?间隙过小会对冲裁产生什么影响?29. 分析冲裁模与拉深模、弯曲模的凸、凹模有何区别?30. 何谓超塑性?超塑性成形有何特点?31、落料与冲孔的主要区别是什么?体现在模具上的区别是什么?32、比较落料或冲孔与拉深过程凹、凸模结构及间隙Z 有何不同?为什么?33、手工电弧焊与点焊在焊接原理与方法上有何不同?34.手工电弧焊原理及特点是什么?35、产生焊接应力和变形的主要原因是什么,怎样防止或减少应力和变形?36. 试说明焊条牌号J422和J507中字母和数字的含义及其对应的国标型号,并比较它们的应用特点。
成型加工基础复习题

基础部分1、简述引起熔体破碎的主要的原因。
熔体破裂是液体不稳定流动的一种现象。
产生熔体破裂的原因主要是熔体中的弹性回复所引起。
熔体在管道中流动时剪切速率分布的不均匀性使熔体中弹性能不均匀分布。
当熔体中产生的弹性应力一旦增加到与滞流动阻力相当时,粘滞阻力就不能再平衡弹性应力的作用,而弹性效应所致熔体流速在某一位置上的瞬时增大形成“弹性湍流”,即“应力破碎”现象。
在园管中,如果产生弹性湍流的不稳定点沿着管的周围移动,则挤出物将呈螺旋状,如果不稳定点在整个圆周上产生,就得到竹节状的粗糙挤出物。
产生不稳定流动和熔体破裂现象的另一个原因是熔体剪切历史的波动引起的。
即剪切应力不同,熔体所产生的弹性效应不同,从而使其弹性回复产生差异,形成熔体破裂。
2、将聚丙烯丝抽伸至相同伸长比,分别用冰水或90℃热水冷却后,再分别加热到90℃的二个聚丙烯丝试样,哪种丝的收缩率高,为什么?用冰水的聚丙烯丝收缩率高,因为冰水冷却时,冰水的温度远远低于聚丙烯的最佳结晶温度,此时,聚丙烯丝的结构更多的保持了其纺丝过程中分子的取向状态,而用90℃热水冷却时,聚丙烯分子具有较为充分的解取向时间,当聚丙烯丝再次分别加热到90℃时,前者才进行较高程度的解取向,表现出较高的收缩率。
3、简述高聚物熔体流动的特点。
由于高聚物大分子的长链结构和缠绕,聚合物熔体、溶液和悬浮体的流动行为远比伤分子液体复杂。
在宽广的剪切速率范围内,这类液体流动时剪切力和剪切速率不再成比例关系,液体的粘度也不是一个常此因而聚合物液体的流变行为不服从牛顿流动定律。
即非牛顿型流动。
4、举例说明高聚物熔体粘弹性行为的表现。
聚合物流动过程最常见的弹性行为是端末效应和不稳定流动。
端末效应包括入口效应和模口膨化效应(离模膨胀)即巴拉斯效应。
不稳定流动即可由于熔体弹性回复的差异产生熔体破碎现象。
5、说明链结构对高聚物粘度的影响。
聚合物的结构因素即链构型和链的极性、分子量、分子量分布以及聚合物的组成等对聚合物液体的粘度有明显影。
(完整版)塑料成型工艺及模具设计复习题及答案
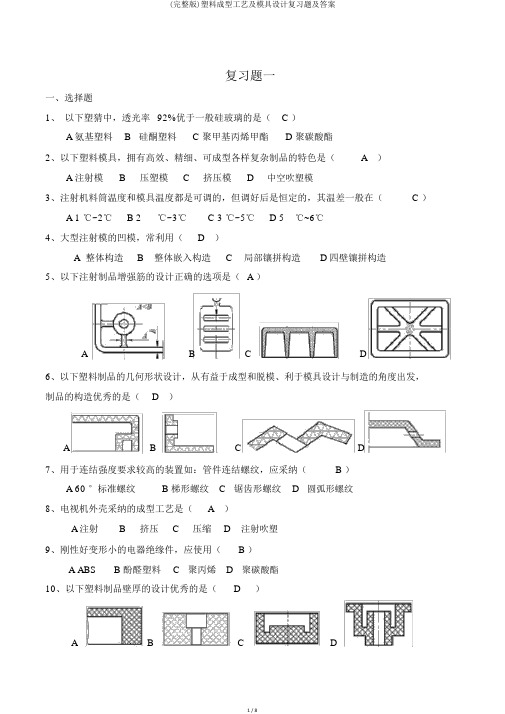
复习题一一、选择题1、以下塑猜中,透光率92%优于一般硅玻璃的是( C )A 氨基塑料B硅酮塑料 C 聚甲基丙烯甲酯 D 聚碳酸酯2、以下塑料模具,拥有高效、精细、可成型各样复杂制品的特色是(A)A 注射模B压塑模C挤压模D中空吹塑模3、注射机料筒温度和模具温度都是可调的,但调好后是恒定的,其温差一般在( C )A 1 ℃~2℃B 2℃~3℃C 3 ℃~5℃D 5℃~6℃4、大型注射模的凹模,常利用(D)A 整体构造B整体嵌入构造C局部镶拼构造D四壁镶拼构造5、以下注射制品增强筋的设计正确的选项是( A )A B C D6、以下塑料制品的几何形状设计,从有益于成型和脱模、利于模具设计与制造的角度出发,制品的构造优秀的是(D)A B C D7、用于连结强度要求较高的装置如:管件连结螺纹,应采纳( B )A 60 °标准螺纹B 梯形螺纹C锯齿形螺纹D圆弧形螺纹8、电视机外壳采纳的成型工艺是(A)A注射B挤压C压缩D注射吹塑9、刚性好变形小的电器绝缘件,应使用( B )A ABSB 酚醛塑料C聚丙烯D聚碳酸酯10、以下塑料制品壁厚的设计优秀的是(D)A B C D二、填空题1、依据塑料的用途,塑料分为通用塑料、工程塑料和特种塑料三大类。
2、塑料注射成型工艺中保压的作用是防备熔料逆向倒流、增补缩短。
3、使注射模具浇注系统内的塑料保持熔融粘流态的方法有两种:一是隔热保温法,二是浇注系统加热法。
4、按分流道至浇口距离相等与否,其型腔和分流道摆列分为均衡摆列和非均衡摆列。
5、尺寸小的模具型腔,主要进行强度计算,刚度再其次。
6、注射模的浇注部分是指引从注塑机喷嘴射入的熔融塑料顺利进入并充满各型腔的通道。
7、因为一般注射机只是在动模部分有顶出装置,注射时,人们总希望制品滞留在动模部分,这样不只是模具构造简单,并且取制件也方便。
8、高分子聚合物的分子构造有线性构造、支链形构造和网状体型构造。
三、名词解说1、固化速度:指熔融塑料充满型腔后,分子构造从线型或支链形构造变为网状立体形三维结构即交联固化构造所需的时间。
材料成型工艺考试复习题目及答案

1 充型能力的影响因素金属的流动性浇注条件铸型填充能力2 浇口杯的作用承接金属液防止和溢出减轻液流对型腔的冲击分离溶渣和气泡防止进入型腔增加充型压力头3 横浇道的作用(1)横浇道的稳流作用:收缩式浇注系统扩张式浇注系统(2)横浇道的流量分配作用:远离直浇道的流量大流量不均匀性克服不均匀性的措施:对称设置内浇道;横浇道断面沿液流方向逐渐缩小;设置浇口窝;采用不同断面内浇道。
(3)横浇道的排渣作用浇注系统主要排渣单元4冒口补缩的条件和要求1)冒口的凝固时间应大于或等于铸件(被补缩部分)的凝固时间。
2)冒口应有足够大的体积,以保证有足够的金属液补充铸件的液态收缩和凝固收缩3)在铸件整个凝固的过程中,冒口与被补缩部位之间的补缩通道应该畅通。
即使扩张角始终向着冒口。
5 浇注位置选择的原则①铸件的重要加工面应朝下或位于侧面:②铸件宽大平面应朝下:③面积较大的薄壁部分应置于铸型下部或垂直:④易形成缩孔的铸件,较厚部分置于上部或侧面:⑤应尽量减少型蕊的数量:⑥要便于安放型蕊、固定和排气:6 湿型砂的组成及性能要求原砂(或旧砂)100 粘土(膨润土)1-5% 煤粉少于8% 水分少于6% 以及其它附加物1) 紧实率和含水量湿型砂不可太干,因为干的型砂虽然流动性极好,但是型砂中膨润土未被充分润湿,性能较为干脆,起模困难,砂型易碎,表面的耐磨强度低,铸件容易生成砂孔和冲蚀缺陷。
型砂也不可太湿,否则型砂太粘,造型时型砂容易在砂斗中搭桥和降低造型流动性,还易使铸件产生针孔、气孔、呛火、水爆炸、夹砂、粘砂等缺陷。
一是紧实率,代表型砂的手感干湿程度;另一是含水量,代表型砂的实际水分含量。
2_) 透气率砂型的排气能力除了靠冒口和排气孔来提高以外,更要靠型砂的透气率。
因此砂型的透气率不可过低,以免浇注过程中发生呛火和铸件产生气孔缺陷。
3) 常温湿态强度湿型砂必须具备一定强度以承受各种外力的作用。
4)湿压强度一般而言,欧洲铸造行业对铸铁用高密度造型型砂的的湿压强度值要求较高。
高分子材料成型加工(塑料成型工艺学)考试复习题

1.以硬质PVC为例说明管材挤出成型加工工艺及其特点以及影响因素(10分)答:挤出工艺:物料经挤出机塑化、机头口模成型后,经定型装置冷却定型、冷却水槽冷却、牵引、切割,得到管材制品。
(3分)特点:①口模横截面积不能大于挤出机料筒横截面积的40%。
②挤出机头有直通式和偏移式两类,后者只用于内径尺寸要求精确的产品,很少采用。
③定径套内径略大于管材外径;机头上调节螺钉可调节管材同心度;牵引速度可调节管材尺寸;(4分)④PVC,粘度大,流动性差,热稳定性差;生成热多,结合缝不易愈合,管材易定型。
(3分)。
影响因素:温度、螺杆转速及冷却、牵引速度、压缩空气2.简述挤出成型原理并讨论提高加料段固体输送速率的措施。
原理:粉(粒)料,加入挤出机经①加热、塑化成熔体,再经机头口模②流动成型成连续体,最后经冷却装置③冷却定型成制品。
(4分)。
措施:提高螺杆转速,提高料筒内表面摩擦系数fb,降低螺杆外表面摩擦系数fs(4分)。
3.简述管材挤出的工艺过程及管材挤出的定径方法。
答:管材挤出的基本工艺是:物料经挤出机塑化、机头口模成型后,经定型装置冷却定型、冷却水槽冷却、牵引、切割,得到管材制品。
(3分)(4分)管材的内外径应分别等于管芯的外径和口模的内径。
管材挤出的定径方法分为定内径和定外径两种。
(2分)外径定型是使挤出的管子的外壁与定径套的内壁相接触而起定型作用的,为此,可用向管内通入压缩空气的内压法或在管子外壁抽真空法来实现外径定型。
(2分)内径定型法是将定径套装于挤出的塑料管内,即使挤出管子的内壁与定径套的外壁相接触,在定径套内通以冷水对管子冷却定径。
(2分)4.挤出时,渐变螺杆和突变螺杆具有不同的加工特点。
已知:PVC软化点75~165℃;尼龙的熔融温度范围则较窄,约10℃,它们应分别选用何种螺杆进行加工?简要说明理由。
(12分)答:PVC应选用渐变螺杆而尼龙应选择突变螺杆进行加工。
(4分)因为PVC是无定形塑料,无固定的熔点,软化温度范围较宽,其熔融过程是逐渐进行的,所以选择熔融段较长的渐变螺杆;PA是结晶性塑料,有固定的熔点,熔融温度范围较窄,温度达到熔点后,熔融较快,应选择熔化区较短的突变螺杆。
材料成型期末复习题目
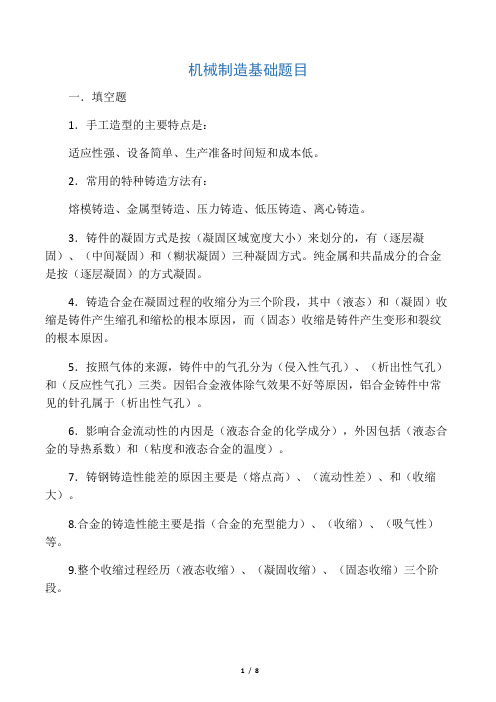
机械制造基础题目一.填空题1.手工造型的主要特点是:适应性强、设备简单、生产准备时间短和成本低。
2.常用的特种铸造方法有:熔模铸造、金属型铸造、压力铸造、低压铸造、离心铸造。
3.铸件的凝固方式是按(凝固区域宽度大小)来划分的,有(逐层凝固)、(中间凝固)和(糊状凝固)三种凝固方式。
纯金属和共晶成分的合金是按(逐层凝固)的方式凝固。
4.铸造合金在凝固过程的收缩分为三个阶段,其中(液态)和(凝固)收缩是铸件产生缩孔和缩松的根本原因,而(固态)收缩是铸件产生变形和裂纹的根本原因。
5.按照气体的来源,铸件中的气孔分为(侵入性气孔)、(析出性气孔)和(反应性气孔)三类。
因铝合金液体除气效果不好等原因,铝合金铸件中常见的针孔属于(析出性气孔)。
6.影响合金流动性的内因是(液态合金的化学成分),外因包括(液态合金的导热系数)和(粘度和液态合金的温度)。
7.铸钢铸造性能差的原因主要是(熔点高)、(流动性差)、和(收缩大)。
8.合金的铸造性能主要是指(合金的充型能力)、(收缩)、(吸气性)等。
9.整个收缩过程经历(液态收缩)、(凝固收缩)、(固态收缩)三个阶段。
10.铸造内应力按产生的不同原因主要分为(热应力)、(机械应力)两种。
11.灰口铸铁根据石墨的不同形态可分为(普通灰口铸铁)、(可锻铸铁)、(球墨铸铁)和(蠕墨铸铁)。
1.衡量金属锻造性能的指标是(塑性)、(变形抗力)。
2.锻造中对坯料加热时,加热温度过高,会产生(过热)、(过烧)等加热缺陷。
3.冲孔时,工件尺寸为(凸模)尺寸;落料时,工件尺寸为(凹模)尺寸。
4.画自由锻件图,应考虑(敷料)、(加工余量)及(锻造公差)三因素。
5.板料弯曲时,弯曲部分的拉伸和压缩应力应与纤维组织方向(平行)。
6.拉伸时,容易产生(拉裂)、(起皱)等缺陷。
7.弯曲变形时,弯曲模角度等于工件角度(-)回弹角、弯曲圆角半径过小时,工件易产生(弯裂)。
8.拉伸系数越大工件变形量越(小),“中间退火”适用于拉伸系数较(小)时。
材料成型复习题及答案

2—1 判断题(正确的画O,错误的画×)1.浇注温度是影响铸造合金充型能力和铸件质量的重要因素.提高浇注温度有利于获得形状完整、轮廓清晰、薄而复杂的铸件.因此,浇注温度越高越好. (×)2.合金收缩经历三个阶段。
其中,液态收缩和凝固收缩是铸件产生缩孔、缩松的基本原因,而固态收缩是铸件产生内应力、变形和裂纹的主要原因. (O)3.结晶温度范围的大小对合金结晶过程有重要影响。
铸造生产都希望采用结晶温度范围小的合金或共晶成分合金,原因是这些合金的流动性好,且易形成集中缩孔,从而可以通过设置冒口,将缩孔转移到冒口中,得到合格的铸件. (O)4.为了防止铸件产生裂纹,在零件设计时,力求壁厚均匀;在合金成分上应严格限制钢和铸铁中的硫、磷含量;在工艺上应提高型砂及型芯砂的退让性。
(O)5.铸造合金的充型能力主要取决于合金的流动性、浇注条件和铸型性质.所以当合金的成分和铸件结构一定时;控制合金充型能力的唯一因素是浇注温度。
(×)6.铸造合金在冷却过程中产生的收缩分为液态收缩、凝固收缩和固态收缩.共晶成分合金由于在恒温下凝固,即开始凝固温度等于凝固终止温度,结晶温度范围为零。
因此,共晶成分合金不产生凝固收缩,只产生液态收缩和固态收缩,具有很好的铸造性能。
(×)7.气孔是气体在铸件内形成的孔洞.气孔不仅降低了铸件的力学性能,而且还降低了铸件的气密性。
(O)8.采用顺序凝固原则,可以防止铸件产生缩孔缺陷,但它也增加了造型的复杂程度,并耗费许多合金液体,同时增大了铸件产生变形、裂纹的倾向. (O)2—2 选择题1.为了防止铸件产生浇不足、冷隔等缺陷,可以采用的措施有( D).A.减弱铸型的冷却能力;B.增加铸型的直浇口高度;C.提高合金的浇注温度;D.A、B和C;E.A和C.2.顺序凝固和同时凝固均有各自的优缺点。
为保证铸件质量,通常顺序凝固适合于( D),而同时凝固适合于(B)。
材料成型工艺学复习题汇总

1.咬入:依靠回转的轧辊和轧件之间的摩擦力,轧辊将轧件拖入轧辊之间的现象. 改善咬入条件的途径:①降低a: (1)增加轧辊直径D,(2)降低压下量实际生产:(1)小头进钢,(2)强迫咬入; ②提高:(1)改变轧件或轧辊的表面状态,以提高摩擦角;(2)清除炉生氧化铁皮;(3)合理的调节轧制速度,低速咬入,高速轧制.2.宽展:高向压缩下来的金属沿着横向移动引起的轧件宽度的变化成为宽展.3.宽展分类: ①自由宽展: 在横向变形过程中,除受接触摩擦影响外,不受任何其它任何阻碍和限制。
②限制宽展: 在横向变形过程中,除受接触摩擦影响外,还受到孔型侧壁的阻碍作用,破坏了自由流动条件,此时宽展称为限制宽展。
③强迫宽展: 在横向变形过程中,质点横向移动时,不仅不受任何阻碍,还受到强烈的推动作用,使轧件宽展产生附加增长,此时的宽展称为强迫宽展。
4.影响宽展的因素:实质因素:高向移动体积和变形区内轧件变形纵横阻力比;基本因素:变形区形状和轧辊形状。
工艺因素:①相对压下量:相对压下量越大,宽展越大。
②轧制道次:道次越多,宽展越小;单道次较大,宽展大,多道次较小,宽展小;③轧辊直径:轧辊直径增加,宽展增加;摩擦系数;④摩擦系数的增加,宽展增加(轧制温度、轧制速度、轧辊材质和表面状态,轧件的化学成分). ⑤轧件宽度的影响:假设变形区长度 l 一定:随轧件宽度增加,宽展先增加后逐渐减小,最后趋于不变。
5.前滑:轧件出口速度vh 大于轧辊在该处的线速度v,即vh>v的现象称为前滑现象。
后滑:轧件进入轧辊的速度小于轧辊该处线速度的水平分量v的现象。
前滑值:轧件出口速度vh与对应点的轧辊圆周速度的线速度之差与轧辊圆周速度的线速度之比值称为前滑值。
后滑值:后滑值是指轧件入口断面轧件的速度与轧辊在该点处圆周速度的水平分量之差同轧辊圆周速度水平分量的比值。
6.影响前滑的因素: ①压下率:前滑随压下率的增加而增加;②轧件厚度:轧后轧件厚度h减小,前滑增加;③轧件宽度:轧件宽度小于40mm时,随宽度增加前滑亦增加;但轧件宽度大于40mm时,宽度再增加时,其前滑值则为一定值;④轧辊直径:前滑值随辊径增加而增加;⑤摩擦系数:摩擦系数f越大,其前滑值越大;⑥张力:前张力增加前滑,后张力减小前滑 .7.轧制生产工艺:由锭或坯轧制成符合技术要求的轧件的一系列加工工序组合。
材料成型与加工复习-1

材料成型与加工复习试卷类型一、选择题(共20题,每题0.5分,共10分)二、填空题(共20个空,每个0.5分,共10分)三、名词解释(共4题,每题2.5分,共10分)四、是非题(共5题,每题2分,共10分)(先判断对或错,若错请写出理由。
)五、计算题(共2题,每题5分,共10分)六、简答题(共4题,每题5分,共20分)七、论述题(共2题,每题15分,共30分)成绩评定:卷面成绩:70%。
平时成绩:30%。
考勤未到一次扣5分,迟到一次扣2分;作业未交一次扣2分);PPT报告共10分(根据PPT质量及回答问题情况综合给分)。
一、填空题(1)聚合物加工通常包括两个过程,其一是:,其二是:。
(2)聚合物所具有的四种加工性质是:、、、。
(3)物料的混合有、、三种基本运动形式,聚合物成型时熔融物料的混合以运动形式为主。
(4)单螺杆挤出机的基本结构包括:、、、、五部分(5)挤出成型工艺过程大体相同,其程序为、、、,有时还包括。
(6)注塑机的基本结构由、和三部分组成。
(7)橡胶塑炼的实质是。
(8)碳黑在橡胶中分散分三个阶段,分别是第一阶段:;第二阶段:;第三阶段:。
(9)成纤聚合物的纺丝过程是在态进行的,而加工过程是在态进行的。
(10)热敏性的PVC宜用螺槽;熔体粘度低和热稳定性较高的PA宜用螺槽螺杆二、名词解释:1.均相成核:2.异相成核:3.二次结晶:4.后结晶:5.热处理(退火):6.淬火:7.压延涂层法:8.帖胶:9.擦胶:10.热成型:11.喷硫:12.弹性记忆:13.威廉氏可塑度(P):14.门尼粘度:15. 压缩比:二选择题:(1)对结晶聚合物,Tg与Tm间有一大致关系,即Tm(K):Tg(K)的比值约为:A. 3:1; B. 4:1; C. 3:2; D. 2:1。
(2)对聚合物的结晶,其最大结晶速率时的温度约为其熔点的倍。
A. 0.7;B. 0.8;C. 0.85;D.0.9.(3) 在聚合物熔点以上,下面的加工方式不适宜操作。
高分子材料成型加工原理复习题及答案
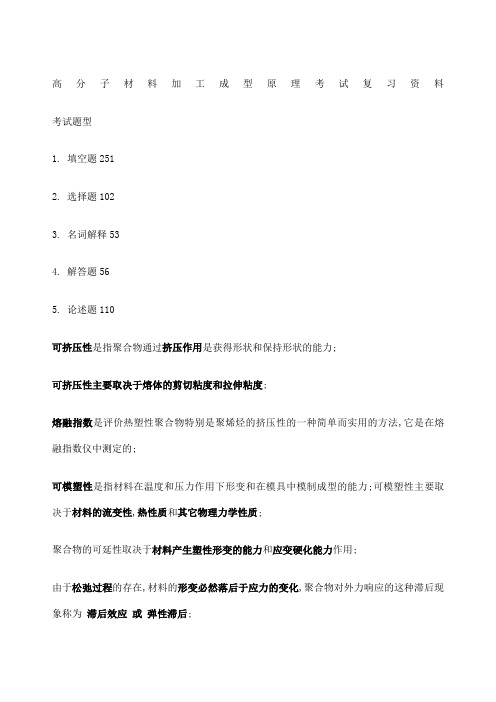
高分子材料加工成型原理考试复习资料考试题型1.填空题2512.选择题1023.名词解释534.解答题565.论述题110可挤压性是指聚合物通过挤压作用是获得形状和保持形状的能力;可挤压性主要取决于熔体的剪切粘度和拉伸粘度;熔融指数是评价热塑性聚合物特别是聚烯烃的挤压性的一种简单而实用的方法,它是在熔融指数仪中测定的;可模塑性是指材料在温度和压力作用下形变和在模具中模制成型的能力;可模塑性主要取决于材料的流变性,热性质和其它物理力学性质;聚合物的可延性取决于材料产生塑性形变的能力和应变硬化能力作用;由于松弛过程的存在,材料的形变必然落后于应力的变化,聚合物对外力响应的这种滞后现象称为滞后效应或弹性滞后;聚合物熔体的流变行为按作用力可分为剪切流动、拉伸流动;均相成核又称散现成核,是纯净的聚合物中由于热起伏而自发的生成晶核的过程,过程中晶核的密度能连续上升;异相成核又称瞬时成核是不纯净的聚合物中某些物质起晶核作用成为结晶中心,引起晶体生长过程,过程中晶核密度不发生变化;在Tg~Tm温度范围内,常对制品进行热处理以加速聚合物的二次结晶或后结晶的过程,热处理为一松弛过程,通过适当的加热能促使分子链段加速重排以提高结晶度和使晶体结构趋于完善;通常热处理的温度控制在聚合物最大结晶速度的温度Tmax;塑料成型加工一般包括原料的配制和准备、成型及制品后加工等几个过程;混合过程一般是靠扩散、对流、剪切三种作用来完成;衡量其混合效果需从物料的分散程度和组成的均匀程度两方面来考虑;最常见的螺杆直径为45~150毫米;长径比L/D一般为18~25;压缩比是螺杆加料段最初一个螺槽容积于均化段最后一个螺槽容积之比,表示塑料通过螺杆全长范围时被压缩的倍数,压缩比愈大塑料受到的挤压作用愈大;根据物料的变化特征可将螺杆分为加料段、压缩段和均化段;锁模机构在启闭模具的各阶段的速度都不一样的,闭合时应先快后慢,开启时则应先慢后快再转慢;利用本身特定形状,使塑料或聚合物成型为具有一定形状和尺寸的制品的工具称模具;浇注系统是指塑料熔体从喷嘴进入型腔前的流道部分,包括主流道、分流道、浇口等;完成一次注射成型所需的时间称注射周期或称总周期;压制成型的加料方法可以分为重量法、容量法、计数法;分离力与辊筒的半径、长度和速度成正比,而和辊间距称反比;通常可将辊筒设计和加工成略带腰鼓型,或调整两辊筒的轴,使其交叉一定角度或加预应力,就能在一定程度上克服或减轻分离力的有害作用,提高压延制品厚度的均匀性;在压延过程中,热塑性塑料由于受到很大的剪切应力的作用,因此大分子会顺着薄膜前进方向发生定向作用,使生成的薄膜在物理机械性能上出现各向异性,这种现像称为压延效应;压延效应的大小,受压延温度、转速、供料厚度和物料性能等的影响,升温或增加压延时间,均可减轻压延效应;压延机的二辊用于橡胶或PVC的塑炼,三辊用于橡胶,四辊塑料;固定倒数第二辊;人造革就是以布或纸为基体,在其上覆以聚氯乙烯糊的一种复合材料;在一定条件下将片、板、棒等塑料型材通过再次加工成型为制品的方法,称为二次成型法;二次成型包括:中空吹塑成型、热成型、取向薄膜的拉伸等;中空吹塑成型是将挤出或注射成型的塑料管坯或型坯趁热于半熔融的类橡胶状时,置于各种形状的模具中,并即时在管坯中通入压缩空气将其吹胀,使其紧贴于模腔壁上成型,经冷却脱模后即得中空制品;拉幅薄膜热定型的目的:1消除内应力2降低收缩率3改善性能;1、简述离模膨胀的含义、原因及主要影响因素;答:定义:被挤出的聚合物熔体断面积远比口模断面积大的现象;离模膨胀比定义为充分松弛的挤出物直径d与口模直径D之比;圆形口模的离模膨胀比为:B = d/D 或B’ = d2/D2=B2原因:a、取向效应b、弹性变形效应c、正应力效应影响因素:1长径比一定,B随剪切速率增加而增大;在熔体破裂临界剪切速率之前有最大值Bmax,而后下降;2低于τc之下,B随τ增加而增大;高于τc时,B值则下降;3在低于临界c的一定的剪切速率下,B随温度升高而降低;4剪切速率恒定,B随长径比L/D的增大而降低;L/D超过某一数值时,B为常数;5离模膨胀比随熔体在口模内停留时间呈指数关系地减少;6离模膨胀比随聚合物的品种和结构不同而异;线性、柔性聚合物位阻低,松弛时间短,B值小;粘度大,分子量高,分布窄,非牛顿性强,松弛缓慢,B值大;2、为什么要对一些成型物料进行干燥预处理举例说明,并列出工艺条件;答:水分以及其它低分子物的存在, 一方面因其在塑料的成型温度下会挥发成气体,从而造成制品表面缺乏光泽和出现气泡与银丝等外观缺陷;另一方面有可能促使聚合物大分子在高温下发生降解或交联反应,其结果不仅会使塑料熔体的粘度改变,给成型工艺控制带来困难,而且对制品的力学性能和电性能等也会产生不利的影响;各种热塑性塑料成型时的允许含水量很不相同;一般来说,成型温度较高而且在高温下较容易发生水解的塑料,其允许含水量就比较低;反之,允许含水量就比较高;例如,PC的成型温度高达300℃,因大分子链中有酯键,高温下的水解稳定性差,粒料的含水量大于%就很难成型,而且随含水量的增加,其制品外观和冲击强度明显下降;而PS由于成型温度不超过200℃,且大分子链中无易水解基团,故在其粒料含水量高达%时仍可顺利成型;PC干燥的工艺条件:循环鼓风干燥,温度110℃,时间:12h,料层厚度25~50mm;3、在生产硬聚氯乙烯管材时,物料经挤出塑化后,由机头挤出后,紧接着进行什么工序,说明此工序的作用,该工序是如何影响管材质量的答:紧接着进行冷却定型工序, 它的作用是将从口模挤出的物料的形状和尺寸进行精整,并将它们固定下来,从而得到具有更为精确的截面形状、表面光亮的制品;影响:定型装置的内表面的粗糙度直接影响管材的外观质量,定型装置内径尺寸决定了管材外径尺寸精度;真空度太小,吸管不紧影响尺寸和表面,真空度太大,牵引困难,不能正常生产;4、为什么说物料的初始温度过高,对加料段的固体输送能力不利答:物料的初始温度过高,易形成架桥,进料不畅,严重时不能进料;另外,高聚物与金属的摩擦因数是温度的函数,过高降低了物料与料筒的摩擦因数,降低了固体输送能力;5、为什么在一种设备上螺杆转速n不能过高并且靠增加转速来提高生产率也是有限度的答:随着转速的增加,物料所受到的剪切作用加大,即剪切速率增大,因为大多数聚合物都是假塑性流体,因此,随γ↑,η↓,则漏流↑,逆流↑,所以,当转速高到一定程度时,漏流和逆流对产量的影响就不能忽略了;在实际生产中,也不能靠提高螺杆的转速无限制的增加生产能力,随n不断提高,剪切速率达到一定范围后,就会出现熔体破裂现象;也就是说,对n的提高,限制性的因素就是是否出现了熔体破裂;经以上讨论,可知,随n的提高,可以提高生产率,但n的提高是有限制的;6、在模压成型过程中,为什么要采取预热操作预热有哪些设备答:模压前对塑料进行加热具有预热和干燥两个作用,前者为了提高料温,后者为了去除水分和其他挥发物;作用:①能加快塑料成型时的固化速度,缩短成型时间;②提高塑料流动性,增进固化的均匀性,提高制品质量,降低废品率;③可降低模压压力,可成型流动性差的塑料或较大的制品;预热:15~20 mpa,未预热:30 ±5 mpa预热设备:①电热板加热;②烘箱加热;③红外线加热;④高频加热等;7、在模压成型过程中,为什么要采取预压操作预压有那些设备预压就是在室温下将松散的粉状或纤维状的热固性模塑料压成重量一定,形状规则的型坯的工序;预压作用:①加料快、准确、无粉尘;②降低压缩率,可减少模具装料室和模具高度;③预压料紧密,空气含量少,传热快,又可提高预热温度,从而缩短了预热和固化的时间,制品也不易出现气泡;④便于成型较大或带有精细嵌件的制品;预压的设备是预压机和压模;8、压延效应产生的原因及减小的方法是什么答:产生的原因:在压延过程中,热塑性塑料由于受到很大的剪切应力和拉伸应力作用,因此高聚物大分子会沿着压延方向作定向排列,以至制品在物理机械性能上出现各向异性,即压延效应;减小的方法:物料温度适当提高,可以提高其塑性,加强大分子的运动,破坏其定向排列,可降低压延效应;降低辊筒转速,则压延时间增加,压延效应降低;辊筒存料量少,压延效应也降低;增加制品的厚度,可减小压延效应;尽量不使用各向异性的配合剂,压延后缓慢冷却,有利于取向分子松弛,也可降低压延效应;9、什么是人造革,简述其用压延法生产的工艺流程,并用示意图表示;答:人造革是以布、纸或玻璃布为基材,在其上覆以粘流态塑料如PVC、PU的一种复合材料;以压延法生产人造革时,基材应先经预热,同时粘流态塑料可先经挤压塑化或辊压塑化再喂于压延机的进料辊上,通过辊筒的挤压和加热作用,使塑料与基材紧密结合,再经压花、冷却、切边和卷取而得制品;下图为四辊压延机生产人造革示意图擦胶法;五、论述题1、论述注射成型的工艺过程;答:按其先后顺序主要包括:1)成型前的准备;①原料性能的了解,主要指热性能、流变性能、压缩率、吸湿性、细度、均匀度等;②原料的预处理,主要指原料的干燥、着色等;③料筒的清洗,在更换原料、调换颜色或发现正在加工中的塑料有一定降解现象出现时,就需要对料筒进行清洗;④嵌件预热;⑤脱模剂的选择,Ⅰ. 硬脂酸锌:不适用于PA;Ⅱ. 白油液体石蜡:对PA效果好,还可防止空隙;Ⅲ. 硅油:虽效果好,但价格高,使用麻烦需配甲苯溶液;2)注射过程;具体过程为:①加料塑化塑料粒子加入到料筒中,通过加热逐渐变成熔体柱塞式,或沿螺杆槽向前移动,通过料筒外的加热及螺杆转动时塑料产生的摩擦热逐渐转变为熔体;②充模注射柱塞或移动螺杆把塑料均匀的熔体推向料筒前端,经过喷嘴及模具浇注系统注入并充满模具的型腔;③保压充满之后,柱塞或移动螺杆仍保持施压状态,使喷嘴的熔体不断充实型腔,以确保不缺料;另可使大分子进一步松弛因有滞后;④凝封在浇注系统里的熔体体积比制品小的多先行冷却硬化,模腔内还未冷却固化的熔体就不会向喷嘴方向倒流,这一现象叫凝封;凝封则保压结束,可退螺杆和注塞;同时下一周期的加料塑化开始;⑤冷却保压结束,同时对模具内制品进行冷却、固化,一般冷却到塑料的玻璃态或结晶态;⑥脱模3)制品的后处理;主要指退火和调湿处理;退火是将制品放在一定温度的加热介质热水、热油等或热空气循环箱中静置一段时间,然后缓慢冷至室温,消除制品在加工过程中产生的复杂内应力;调湿处理是将刚出模的热制品放入热水中放置一段时间;主要是为了避免氧化变色放入热水中,隔绝氧;加快得到吸湿平衡,稳定制品尺寸;适量水分对PA等有增塑作用;可以改善柔性、韧性、拉伸强度等性能;2、论述塑料的一次成型和二次成型的联系和区别,并举例说明;答:一次成型是通过加热使塑料处于粘流态的条件下,经过流动、成型和冷却硬化或交联固化,而将塑料制成各种形状的产品的方法;一次成型包括挤出成型、注射成型、模压成型、压延成型等,成型制品从简单到极复杂形状和尺寸精密的制品,应用广泛,绝大多数塑料制品是从通过一次成型法制得的;二次成型是将一次成型所得的片、管、板等塑料型材,加热使其处于类橡胶状态,通过外力作用使其形变而成型为各种简单形状,再经冷却定型而得制品;二次成型包括中空吹塑成型、热成型、拉幅薄膜的成型等方法,仅适用于热塑性塑料的成型;二次成型是在一次成型的基础上进行成型的一种方法;区别:如PVC挤出吹塑成型过程:挤出管坯→合模→送入压缩空气,吹胀型坯→保压、冷却定型后脱模挤出管坯应属于一次成型,后面的成型过程属于二次成型,具体从成型对象、成型温度、形变来具体说明二者联系和区别;。
2014高分子材料成型加工复习题
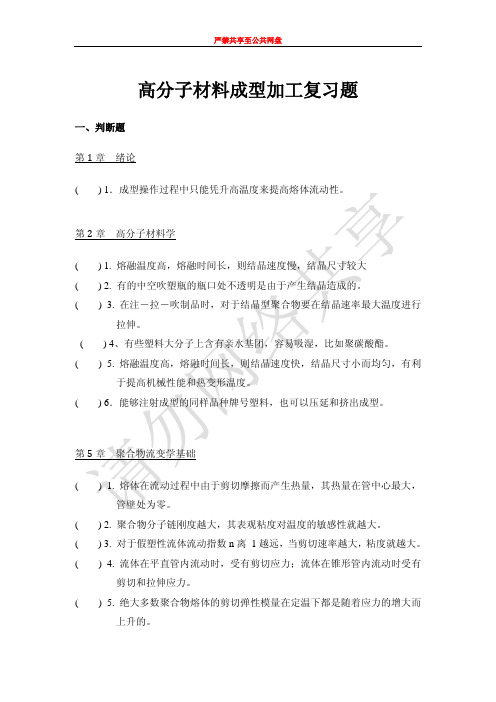
高分子材料成型加工复习题一、判断题第1章绪论( ) 1.成型操作过程中只能凭升高温度来提高熔体流动性。
第2章高分子材料学( ) 1. 熔融温度高,熔融时间长,则结晶速度慢,结晶尺寸较大( ) 2. 有的中空吹塑瓶的瓶口处不透明是由于产生结晶造成的。
( ) 3. 在注-拉-吹制品时,对于结晶型聚合物要在结晶速率最大温度进行拉伸。
( ) 4、有些塑料大分子上含有亲水基团,容易吸湿,比如聚碳酸酯。
( ) 5. 熔融温度高,熔融时间长,则结晶速度快,结晶尺寸小而均匀,有利于提高机械性能和热变形温度。
( ) 6.能够注射成型的同样品种牌号塑料,也可以压延和挤出成型。
第5章聚合物流变学基础( ) 1. 熔体在流动过程中由于剪切摩擦而产生热量,其热量在管中心最大,管壁处为零。
( ) 2. 聚合物分子链刚度越大,其表观粘度对温度的敏感性就越大。
( ) 3. 对于假塑性流体流动指数n离1越远,当剪切速率越大,粘度就越大。
( ) 4. 流体在平直管内流动时,受有剪切应力;流体在锥形管内流动时受有剪切和拉伸应力。
( ) 5. 绝大多数聚合物熔体的剪切弹性模量在定温下都是随着应力的增大而上升的。
( ) 6. 在注射过程中,为了增大熔体的流动性,对于聚丙烯来说宜提高温度,对于聚碳酸酯来说宜提高压力。
( ) 7. 聚合物挤出膨胀是由弹性恢复造成的。
( ) 8、几乎所有的聚合物的浓溶液和凝胶性糊塑料在加工中的流变行为都与假塑性流体相近。
( ) 9、聚合物熔体在挤出时通过一个狭窄的口模,即使口模很短,也会有很大的压力降,这种现象称为入口效应。
( ) 10、流体在平直管内受剪切应力而发生流动的形式有层流和湍流两种。
( ) 11、一般情况下,塑料熔体在高剪切应力下,贴近管壁处的一层流体是不发生流动的。
第6章高分子材料混合与制备( ) 1、物料混合要在玻璃化温度以下。
( ) 2、塑料的塑化温度要在树脂流动温度以上。
( ) 3.生胶的塑炼就是使生胶由柔软的塑性状态变为强韧的弹性状态的工艺过程( ) 4.生胶的塑炼的目的主要是为了提高产品的耐磨性。
金属材料成型原理复习题

金属材料成型原理复习题金属材料成型原理复习题一、选择题1. 金属材料成型的基本原理是()。
a) 热处理b) 热压缩c) 冷加工d) 热加工2. 金属材料成型的目的是()。
a) 改善材料的力学性能b) 增加材料的重量c) 降低材料的成本d) 减少材料的使用寿命3. 以下哪种成型方法属于热加工()。
a) 挤压b) 拉伸c) 深冲d) 冷锻4. 以下哪种成型方法属于冷加工()。
a) 挤压b) 热轧c) 热挤压d) 冷锻5. 金属材料成型的主要影响因素包括()。
a) 温度b) 应变速率c) 应变量d) 所用工艺设备二、判断题1. 热加工是指在高温下进行的金属材料成型过程。
()2. 冷加工是指在低温下进行的金属材料成型过程。
()3. 冷加工可以提高材料的强度和硬度。
()4. 热加工可以提高材料的塑性和韧性。
()5. 热加工和冷加工的选择主要取决于材料的性质和成型要求。
()三、简答题1. 请简要说明金属材料成型的基本原理。
金属材料成型的基本原理是通过加工和变形,改变金属材料的形状和结构,从而达到改善材料的力学性能的目的。
成型过程中,通过施加压力使金属材料发生塑性变形,使其形状和尺寸发生改变。
成型过程中,常常需要加热或降低温度,以控制材料的塑性和韧性,从而实现成型的目标。
2. 热加工和冷加工的区别是什么?热加工和冷加工的区别主要在于成型过程中的温度。
热加工是指在高温下进行的金属材料成型过程,温度一般高于材料的再结晶温度。
冷加工是指在低温下进行的金属材料成型过程,温度一般低于材料的再结晶温度。
热加工可以提高材料的塑性和韧性,适用于大变形量和复杂形状的成型。
冷加工可以提高材料的强度和硬度,适用于小变形量和精密成型。
3. 金属材料成型的影响因素有哪些?金属材料成型的影响因素包括温度、应变速率、应变量和所用工艺设备。
温度影响材料的塑性和韧性,高温下材料更容易变形。
应变速率影响材料的流动性,快速变形会导致材料的断裂。
应变量影响材料的形状和尺寸的变化程度,过大的应变量可能导致材料的破裂。
- 1、下载文档前请自行甄别文档内容的完整性,平台不提供额外的编辑、内容补充、找答案等附加服务。
- 2、"仅部分预览"的文档,不可在线预览部分如存在完整性等问题,可反馈申请退款(可完整预览的文档不适用该条件!)。
- 3、如文档侵犯您的权益,请联系客服反馈,我们会尽快为您处理(人工客服工作时间:9:00-18:30)。
成型加工复习名词解释:1.成型加工:将高分子材料成型加工为高分子材料制品的过程。
2.共混物的均匀性:指被分散物在共混体中浓度分布的均一性。
3.共混物的分散程度:分散相在共混体中的破碎程度。
4.初混合设备:是指物料在非熔融状态下进行混合所用的设备。
5.混炼胶:将各种配合剂混入并均匀分散在橡胶中的过程的产物。
6.塑化料:将各种配合剂混入并均匀分散在塑料熔体中的过程的产物。
7.塑炼:增加橡胶可塑性的工艺过程。
8.混炼:就是将各种配合剂与可塑度合乎要求的生胶或塑炼胶在机械作用下混合均匀,制成混炼胶的过程。
塑料的初混合工艺:指聚合物与各种粉状、粒状或液体配合剂的简单混合工艺。
9.塑料的塑化:是借助加热和剪切作用使物料熔化、剪切变形、进一步混合,使树脂及各种配合剂组分分散均匀。
10.挤出成型:是将物料送入加热的机筒与旋转着的螺杆之间进行物料的输送,熔融压缩、熔体均化,并定量、定压、定速地通过机头口模而获得所需的挤出制品。
11.挤出机工作点:是螺杆特性线与口模特性线的交点。
12.挤出物膨胀:聚合物熔体在模内所受形变的弹性回复。
13.注射成型:将固体聚合物加热塑化成熔融体,并高压、高速注射入模具中,赋予模腔的形状,经冷却(或交联、硫化)成型的过程。
14.注射量:是指注射机对空注射条件下,注射螺杆或柱塞在作一次最大注射行程时,注射系统所能达到的最大注射量。
15.注射压力::指在注射时,螺杆或柱塞端面施加于料筒中熔料单位面积上的压力。
16.合模力:注射机合模机构对模具所施加的最大夹紧力。
17.注射速度:指注射时,螺杆或柱塞移动速度。
18.注射速率:指单位时间内熔料从喷嘴射出的容量。
19.注射时间:指螺杆或柱塞完成一次注射量所需的时间。
20.塑化:指聚合物在料筒内经加热由固态转化为熔融的流动状态并具有良好的可塑性的过程。
21.注射过程:塑化良好的聚合物熔体,在柱塞或螺杆的压力作用下,由料筒经过喷嘴和模具的浇注系统进入并充满模腔这一重要而又复杂的阶段。
22.塑化压力(背压):螺杆顶部熔体在螺杆后退时受到的压力。
23.压延成型:将接近粘流温度的物料通过几个相向旋转着的平行辊筒的间隙,使其受到挤压和延展作用,得到表面光洁的薄片状连续制品。
24.一次成型:通过加热使塑料处于粘流态的条件下,经过流动、成型和冷却硬化,而将塑料制成各种形状产品的方法。
25.二次成型:指在一定条件下将高分子材料一次成型所得的型材通过再次成型加工,以获得制品的最终型样的技术。
26.中空吹塑成型:借助于气体的压力,把在闭合模具中呈橡胶态的塑料型坯吹胀形成中空制品的二次成型技术。
27.拉伸吹塑:将挤出或塑料注射成型的型坯,经冷却,再加热,然后用机械的方法及压缩空气,使型坯沿纵向及横向进行吹胀拉伸、冷却定型的方法.28.泡沫塑料:以树脂为基质而内部具有无数微孔性气体的塑料制品。
简答题:1.高分子材料成型加工的实际?聚合物加工通常包括两个过程:首先使原材料产生变形或流动,并取得所需要的形状,然后设法保持取得的形状,流动—硬化是聚合物过程的基本程序。
实际就是一个定构过程,也就是使聚合物结构确定,并获得一定性能的过程。
1.共混方法有哪几种?聚合物共混改性的目的是什么?(为什么要改性?)方法(1)机械共混法:将诸聚合物组分在混合设备如高速混合机,开炼机,挤出机中均匀混合。
(2)液体共混法:将聚合物溶液或乳液混合后,再干燥或沉析得到聚合物共混物的过程。
(3)共聚-共混法:接枝-共混法(HIPS、ABS)嵌段共混法(4)互穿网络聚合物(IPNs)目的:(1)提高聚合物的使用性能(2)改善聚合物的加工工艺性能(3)降低成本2.共混体系的类型有哪些?主要是哪种?聚合物共混过程中按物料的状态可分为:固体/固体混合,液体/液体混合,液体/固体混合。
在聚合物加工中,液体和液体的混合,液体和固体的混合是最主要的混合形式。
也就是常提到的聚合物的共混与聚合物的填充改性。
3.混炼三要素是什么?压缩、剪切和分配置换4.间歇式与连续式的主要区别是什么?主要区别是:间歇式混合设备的混合与混炼过程是不连续的,它的生产效率低,混合质量不稳定。
连续式混合设备的混合操作是连续的,生产能力高,易于实现自动化控制,能量消耗低,混合质量稳定,降低操作人员的劳动强度。
5.典型初混合设备常用的有哪些?转鼓式混合机、螺带混合机、Z型捏合机、高速混合机6.开炼机与密炼机的工作原理以及优缺点开炼机的工作原理:两辊筒相对回转,物料与辊筒表面之间的摩擦和粘附作用,以及物料之间的粘接作用,被拉入两辊之间间隙,受强烈剪切和挤压,变成料片。
物料被拉入辊距(开炼机正常工作)的条件是:摩擦角β大于或等于接触角ɑ。
优点:结构简单,加工适应性强,使用方便缺点:劳动条件差,劳动强度大,能量利用不尽合理,物料易发生氧化等密炼机的工作原理:转子外表面与混炼室内壁间的剪切作用;两转子之间的搅拌作用;转子轴向的往复折卷作用。
优点:工作密封性好,降低劳动强度,缩短生产周期7.连续混炼机常用混炼的设备有哪些?单螺杆挤出机、双螺杆挤出机、双阶挤出机、行星式螺杆挤出机、传递式混炼挤出机、FCM混炼机、FMVX 混炼机组8.塑炼目的是什么?就是降低生胶的弹性,使生胶获得一定的可塑性和流动性,使之适合于各种工艺操作。
同时还要使生胶的塑性均匀一致,以便制得质量均一的胶料。
(是使生胶提高可塑性、流动性,改善加工性能。
)9.塑炼机理是什么?橡胶在塑炼时,遭受到氧、电、热、机械力等因素的作用,其中氧和机械力起主要作用,塑炼机理与此密切相关。
低温塑炼:以机械降解作用为主,氧起稳定游离基作用高温塑炼:以自动氧化降解作用为主,机械作用强化橡胶与氧的接触。
10.影响塑炼的因素是什么?(1)机械力的作用(2)氧的作用(3)温度的作用(4)静电作用(5)化学塑解剂作用12.初混物和塑化料的区别?初混物主要是通过简单混合而达成各组分的均一,混合一般在树脂的熔点一下进行,主要借助搅拌作用完成;塑化料一般是在初混物的基础上,为了改变初混物料的性状,在加热和剪切力的作用下,经熔融、剪切混合而得到均匀的塑化料。
13.开炼机塑炼工艺方法薄通塑炼、一次塑炼、分段塑炼15.用开炼机和密炼机塑炼时应控制的工艺条件有哪些?它们对塑炼有何影响?开炼机应控制的工艺条件有:辊温、辊距、时间、速比、装胶量和塑解剂等。
对开炼机塑炼的影响:开炼机塑炼属于低温机械塑炼,温度越低,塑炼效果越好。
塑炼中因挤压和剪切作用,产生大量热量,需对双辊通冷水冷却(胶料温度一般控制在55℃以下);可采用分段塑炼,一般塑炼10~15分钟后冷却一段时间再塑炼。
两辊间距小,剪切作用强,塑炼效果好。
一般塑炼的开炼机速比在1:1.25 ~ 1:1.27之间。
密炼机应控制的工艺条件有:温度、时间、转子转速、装胶容量和上顶恮压力等对密炼机塑炼的影响:塑炼效果随温度升高而增大,但温度过高会使橡胶分子产生过度氧化裂解或凝胶,从而导致胶料的物理力学性能下降。
上顶詮必须加压,以增加转子对胶料的剪切作用。
14.开炼机混炼过程一般包括哪几个阶段?包辊、吃粉和翻炼14.影响开炼机混炼的工艺因素?装胶容量、辊距、辊速及速比、温度、时间、加料方式及顺序等。
15.采用加料顺序原则?用量少、难分散的配合剂先加;用量大、易分散的后加;为了防止焦烧,硫磺和超速促进剂一般最后加入。
16.塑料的初混合一般使用的设备有?转鼓式混合机、螺带式混合机、捏合机和高速混合机17.塑料的塑化的设备有?开放式炼塑机、密炼机18.挤出机挤压系统的主要作用?(1)连续、稳定地输送物料(2)将固体物料塑化成熔融物料(3)使物料在温度和组分上均匀一致21.挤出分成哪三个区域?固体输送区—物料温度较低,故呈固体状态,物料逐渐被压实,并向前输送;熔融区—料温达到熔融温度,逐渐熔融变成粘流液体;熔体输送区—已熔融的流体沿螺杆进行搅拌和混合,同时定量定压输送。
22.对应螺杆分成哪三段,作用是什么?加料段、压缩段、均化段加料段作用:将料斗供给的料送往压缩段,塑料在移动过程中一般保持固体状态由于受热而部分熔化。
压缩段作用:压实物料,使物料由固体转化为熔体,并排除物料中的空气。
均化段作用:是将熔融物料,定容定压地送入机头使其在口模中成型。
均化段的螺槽容积与加料一样恒定不变。
23.挤出机螺杆为何分段?分段的根据是什么?根据物料在螺杆中的温度、压力、黏度等的变化特征,分为三段(加料段、压缩段和计量段)24.提高挤出机加料段固体输送能力,应对设备采取什么措施?指出其理论依据?结构角度:(1)增加螺槽深度;(2)降低物料与螺杆的摩擦系数;(3)增加物料与料筒的摩擦系数;(4)选择适当的螺旋角。
工艺角度:(1)增加料筒温度(2)降低螺杆温度。
理论依据:固体对固体的摩擦静力平衡。
24.挤出机工作点的意义以及如何得到?挤出机是螺杆与机头口模安装在一起而进行工作的,由于物料不可压缩,并且连续稳定自螺杆流向机头口模而成为一定形状的制品,因此螺杆的流率、压力与口模的流率,压力相等。
意义:在给定的螺杆和口模下,当转速一定时,机头压力和流率均应符合这一点所表示的关系,即对应于工作点的流率为Qc,机头压力为Pc,工作点因螺杆转速改变而改变。
25.普通螺杆的主要形式以及分别适合那些物料?(1)等距变深螺杆:等距渐变螺杆(多用于pvc、无定形塑料)、等距突变螺杆(高结晶塑料)(2)等深变距螺杆:适合橡胶加工(3)变深变距螺杆:很少采用26.普通螺杆的主要参数如何选择?螺杆直径:螺杆直径的大小一般根据经验公式和制品截面积大小确定。
长径比:L/D↑,改善物料温度分布,有利于混合及塑化,生产能力↑;但L/D过大,物料可能发生热降解,螺杆也可能因自重而弯曲,功耗增大;L过小则塑化不良L/D通常为28~30;螺槽深度:螺槽深度↓,剪切速率↑,传热效率↑,混合及塑化效率↑,生产率↓。
故热敏性塑料宜用深螺槽,而熔体粘度低且热稳定性好的塑料宜用浅螺槽。
螺旋角:螺旋角↑,生产能力↑,对塑料的剪切作用和挤压力↓27.双螺杆挤出机的主要应用于哪些方面?热敏性材料的挤出成型、特种聚合物的加工28.挤出物膨胀的原因?聚合物熔体固有的弹性29.模内流动的不稳定性的典型现象?(1)鲨鱼皮:挤出物表面层的流动速度增加,形成对聚合物表层的拉伸,拉伸速率过高,表皮无法承受。
(2)熔体破裂:挤出物的严重畸变。
30.挤出成型过程中的聚合物为什么发生取向,对性能有何影响?原因:在成型加工时,受到剪切和拉伸力的影响,高分子化合物的分子链将发生取向。
影响:高分子材料经取向后,拉伸强度、弹性模量、冲击强度、透气性等增加31.注射机的组成有?注射系统、合模系统、液压传动系统、电器控制系统32.注射机的注射系统的主要作用是什么?1)加热塑化—能在规定的时间内将规定数量的物料均匀地熔融塑化,并达到流动状态;2)加压注射—以一定的压力和速度将熔料注射到模具型腔中去;3)保压补缩—注射完毕后,有一段时间螺杆保持不动,以向模腔内补充一部分因冷却而收缩的熔料,使制品密实和防止模腔内的物料反流。