AT-DKG-M使用说明书
艾特顿9PX系列无线电源系统说明说明书

Eaton 9PX5KIBPEaton 9PX UPS, 5000 VA, 4500 W, Input: Hardwired, Outputs: (3) C13, (2) C19, Hardwired, Rack/tower, 3UGeneral specificationsEaton 9PX UPS 9PX5KIBP74317204053468.5 cm 44 cm 13 cm 48 kg 2 year CE Marked TUV cULus Listed CSA 22.2UL 1778 IEC/EN 62040-1 IEC/EN 62040-2 CE EACEaton 9PX 5000i HotSwapProduct Name Catalog Number UPCProduct Length/Depth Product Height Product Width Product Weight Warranty Compliances Certifications Model CodeView runtime graph Hot-swappable internal batteries and extended battery modules (EBMs)1512 V / 5 Ah Sealed, lead-acidYes(3) C13, (2) C19, Hardwired Online/Double-conversion 4500 W 5000 VA Sine wave 230V0.9230V default (200/208/220/230/240V)200/208/220/230/240 V +/- 1%250/60 Hz 1Hardwired/fixed connection 230V default (200/208/220/230/240V)176-276 V (100-276 V with derating)50/60 HzRuntime graph Battery management Battery replacementBattery quantity Battery rating Battery type Extended battery capability ReceptacleTopologyWattage VA rating Output waveform Voltage Output power factor Output nominal voltageOutput voltage rangeVoltage distortion output (linear load) - max Output frequency Feed type Input connectionInput nominal voltageInput voltage rangeNominal frequency CommunicationABM & Temperature compensated charging method (user selectable)Automatic battery test Deep discharge protection Automatic recognition of external battery units USB port (HID compliant)Serial port (RS232)Mini terminal block for remote On/Off Mini-terminal block for remote power off Dry contacts (4 outputs, relay, DB9)DB15 for parallel operation40-70 Hz >.99One slot for optional communication card NoNoEaton Intelligent Power Manager, Eaton Intelligent Power Protector Multilingual graphical LCD display OtherYes3000 m Online: 922<45 dB at 1 meter 0-95% non-condensing 0° to 40°C (32° to 104°F)Input frequency range Input power factor Expansion slotsEthernet interface Includes network card Software compatibilityUser interfaceType of interface Potential free switch contact Altitude BTU Rating Noise level Relative humidity Temperature range Special featuresDouble conversion topology Constantly monitors power conditions and regulates voltage and frequency Provides more real power (watts) to protect more equipment with a 0.9 power factorEnergy Star qualified, provides the highest efficiency level to reduce energy and cooling costs Internal bypass allows service continuity in case of UPS faultNext-generation graphical LCD displayCompatible with Virtual environments (VMware, Hyper-V, Citrix Xen, Redhat)Meter energy consumption (at the UPS level)Parallel operation usingRack/tower3UFree standing model No9411YesYesYes Eaton 9PX UPS 5–22kVA - BrochureEaton UPS Services Quick Guide 2021Eaton UPS and battery servicesEU declaration of conformity Eaton 9PX UPSEaton 9SX-9PX UPS - 5-6 kVA-EBM 180V - Installation and user manual Eaton Bypass Power Module (BPM) user guideEaton 9PX UPS - 5/6/8/11 kVA - DatasheetForm factorRack size Construction type Rack mounting kit EfficiencyPackage contentsPhase (input)Phase (output) Internal bypassHot swap powerAuto shutdown function BrochuresCompliance information Manuals and user guides Technical data sheetsHotSync technologyHot swappable batteries Advanced Battery Management (ABM) technology to increase battery lifetimeUPS(2) IEC-IEC output cables Maintenance Bypass USB cableSerial cable(2) Supports for tower mountingCable locking system Safety instructions Quickstart guideEaton Corporation plc Eaton House30 Pembroke Road Dublin 4, Ireland © 2023 Eaton. All rights reserved. Eaton is a registered trademark.All other trademarks areproperty of their respectiveowners./socialmedia。
克立司帝自动栏杆机用户使用手册说明书

用户使用手册User Guide自动栏杆机Intelligent Barriers克立司帝控制系统(上海)股份有限公司Crest Control System(Shanghai)Co.,Ltd.安全说明1、版权通知Granity《用户使用手册》中所刊登之产品图片因摄影及印刷之故可能与实际产品存在一定差异,实际样式请以实样为准,克立司帝保留不作事先通知改变产品规格及终止产品类型的权利。
克立司帝的各项技术及产品外观已申请专利保护,应用设备亦获得检验报告,自主研发的软件均持有软件著作权登记证书,任何个人、组织或企事业单位,不得擅自拷贝、复制、模仿,克立司帝拥有最终追究法律责任的权利。
2、安全信息1、警告:为了安全,避免火灾或触电现象,在使用本产品时,一定要遵守基本的安全注意事项。
2、请阅读并了解《用户使用手册》中的所有说明。
3、为设备接线时,请勿带电操作。
如需临时用电时,请使用带接地电源插座。
设备连线采用暗埋式,不可裸露在外。
4、严格遵守产品上标出的所有警告和说明。
5、设备保养、清洁时请切断电源。
6、在安装或使用本产品之前,请参阅《用户使用手册》,如有不明之处请致电本公司售后服务部。
7、使用者请勿擅自拆装设备,如有需要,请在专业技术人员的指导下操作。
目录安全说明 (2)1、版权通知 (2)2、安全信息 (2)1、施工准备 (4)1.1.1布线原则 (4)1.1.2线型的选择 (4)1.3.3线缆的敷设工艺 (4)2、设备安装调试 (4)2.1安装调试规则 (4)2.1.1设备定位 (4)2.1.2外设安装 (5)2.1.3线路测试 (5)2.1.4接地标准 (6)2.1.5调试 (7)2.2G-F621系列自动拦杆机 (8)2.2.1技术参数 (8)2.2.2拦杆机箱体上盖帽打开流程 (8)2.2.3安装固定 (9)2.2.5电气调试 (12)2.2.6常见故障与排除 (15)2.2.7维护保养 (15)1、施工准备1.1.1布线原则导线穿于管中,较为隐蔽,一旦出现问题处理十分困难,是设备稳定可靠运行的重要组成部分。
NKG-1M带倒计时时控开关说明书
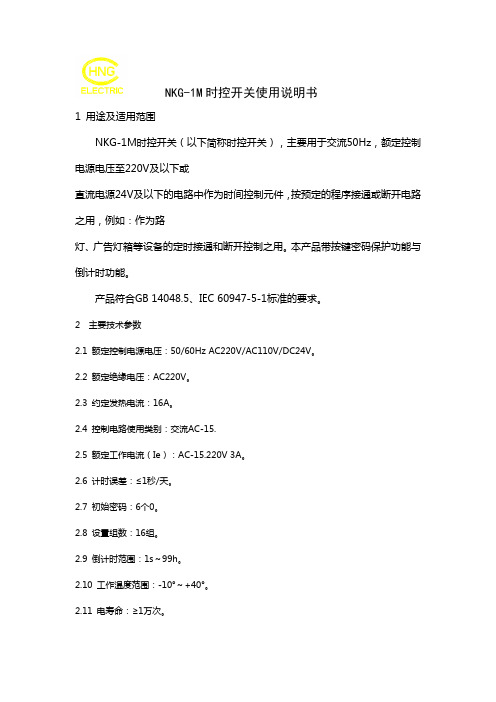
NKG-1M时控开关使用说明书1 用途及适用范围NKG-1M时控开关(以下简称时控开关),主要用于交流50Hz,额定控制电源电压至220V及以下或直流电源24V及以下的电路中作为时间控制元件,按预定的程序接通或断开电路之用,例如:作为路灯、广告灯箱等设备的定时接通和断开控制之用。
本产品带按键密码保护功能与倒计时功能。
产品符合GB 14048.5、IEC 60947-5-1标准的要求。
2 主要技术参数2.1 额定控制电源电压:50/60Hz AC220V/AC110V/DC24V。
2.2 额定绝缘电压:AC220V。
2.3 约定发热电流:16A。
2.4 控制电路使用类别:交流AC-15.2.5 额定工作电流(Ie):AC-15.220V 3A。
2.6 计时误差:≤1秒/天。
2.7 初始密码:6个0。
2.8 设置组数:16组。
2.9 倒计时范围:1s~99h。
2.10 工作温度范围:-10°~+40°。
2.11 电寿命:≥1万次。
2.12 安装方式:装置式、导轨式。
3 外形及安装尺寸和接线方式3.1 外形尺寸及安装尺寸:见图1。
a) NKG-1 外形尺寸 b) NKG-1 安装尺寸图1 NKG-1外形尺寸及安装尺寸3.2 接线方式3.2.1 直接控制方式被控制的电器是单相供电,工作电流不超过本开关的额定值,可采用直接控制方式,接线方式如图2所示;对于电流较大的负载,请采用交流接触器扩容控制方式。
3.2.2 单相扩容方式被控制的电器是单相供电,工作电流超过本开关的额定值,请采用交流接触器扩容控制方式,如图3所示。
3.2.3 三相工作方式被控制的电器三相供电,需要外接交流接触器,控制接触器的线圈电压AC220V 50Hz,接线方式如图4所示;控制接触器的线圈电压AC380V 50Hz,接线方式如图5所示。
图2 单相直接控制接线图图3 单相扩容控制接线图(接触器线圈220V)图4 三相控制接线图(接触器线圈220V)图5 三相控制接线图(接触器线圈380V)4 设置与使用本产品的面板设有“MD(模式)”、“R(取消/恢复)”、“(移位)”、“(-)”、“(+)”五个按键。
奥里安特电机产品操作手册说明书

HM-9264-2AC Standard Motors Conduit Box TypeInduction MotorThank you for purchasing an Oriental Motor product.This Operating Manual describes product handling procedures and safety precautions.• Please read it thoroughly to ensure safe operation. • Always keep the manual where it is readily available.Before useOnly qualified personnel should work with the product.Use the product correctly after thoroughly reading the section “Safety precautions”.Should you require the inspection or repair of internal parts, contact the Oriental Motor office where you purchased the product. The product described in this manual has been designed andmanufactured for use as an internal component for general industrial equipment, and must not be used for any other purpose. Oriental Motor Co., Ltd. is not responsible for any damage caused through failure to observe this warning.Standard and CE MarkingMotors are recognized by UL. Recognized name are motor model name. Voluntary display of the CE mark conforming to the Low Voltage Directives. StandardsUL 1004, UL 2111, CSA C22.2 No.100, CSA C22.2 No.77 Standards File No. UL File No.E64197 Applications for standardEN 60034-1, EN 60034-5, EN 60664-1A Running Heating Test and a Locked-Rotor Test has beenconducted with a aluminum radiation plate of size indicated below. For the motor with a gearhead, tests has been conducted with a gearhead instead of the radiation plate.First number in motor nameSize [mm (in.)] Thickness [mm (in.)]Material4 135 × 135 (5.31 × 5.31) 5 (40 W) 165 × 165 (6.50 × 6.50) 5 (60 W, 90 W)200 × 200 (7.87 × 7.87)5 (0.20)AluminiumInstallation conditionsOvervoltage category II, Pollution degree 3 (except for the motor mounting surfase and conduit opening), Class I equipment (For EN/IEC standards)When the machinery to which the motor is mounted requiresovervoltage category III specifications, connect to power supply via an isolation transformer.Hazardous substancesRoHS (Directive 2002/95/EC 27Jan.2003) compliant∗ 5IK60GU-FCH , 5IK60GU-ECH , 5IK60GU-SH , 5IK90GU-FCH , 5IK90GU-ECH and 5IK90GU-SH do not comply with the hazardous substances.The precautions described below are intended to prevent danger or injury to the user and other personnel through safe, correct use of the product. Use the product only after carefully reading and fully understanding these instructions.WarningHandling the product without observing theinstructions that accompany a “Warning” symbol may result in serious injury or death.CautionHandling the product without observing theinstructions that accompany a “Caution” symbol may result in injury or property damage.NoteThe items under this heading contain importanthandling instructions that the user should observe to ensure safe use of the product.Warning• Do not use the product in explosive or corrosive environments, in the presence of flammable gases, locations subjected to splashing water, or near combustibles. Doing so may result in fire, electric shock or injury.• Assign qualified personnel the task of installing, wiring,operating/controlling, inspecting and troubleshooting the product. Failure to do so may result in fire, electric shock or injury. • Do not transport, install the product, perform connections or inspections when the power is on. Always turn the power offbefore carrying out these operations. Failure to do so may result in electric shock.• Turn off the power in the event the overheat protection device (thermal protector) is triggered. Failure to do so may result in injury or damage to equipment, since the motor will start abruptly when the overheat protection device (thermal protector) is automatically reset.• To prevent the risk of electric shock, use the motor for class I equipment only.Motore zur Verwendung in Geräten der Schutzklasse I.• Install the motor in an enclosure in order to prevent electric shock or injury.• Install the motor so as to avoid contact with hands, or ground it to prevent the risk of electric shock.Die Gehäuse der Motore sind mit einer Schraube undZahnscheibe sicher mit dem geerdeten Gehäuse des Gerätes zu verbinden.• Keep the input power voltage within the specification to avoid fire and electric shock.• Connect the cables securely according to the wiring diagram in order to prevent fire and electric shock.• Do not forcibly bend, pull or pinch the lead wires. Doing so may result in fire and electric shock.• Turn off the power in the event of a power failure, or the motor will suddenly start when the power is restored and may cause injury or damage to equipment.• Do not touch the connection terminal of the capacitor immediately after the power is turned off (for a period of 30 seconds). Theresidual voltage may cause electric shock.• Do not disassemble or modify the motor. This may cause electric shock or injury.Caution• Do not use the motor beyond its specifications, or electric shock, injury or damage to equipment may result.• Do not touch the motor during operation or immediately after stopping. The surface is hot and may cause a burn.• Do not hold the motor output shaft or motor lead wires. This may cause injury.• Keep the area around the motor free of combustible materials in order to prevent fire or a burn.• To prevent the risk of damage to equipment, leave nothing around the motor that would obstruct ventilation.• To prevent bodily injury, do not touch the rotating parts (output shaft, cooling fan) of the motor during operation.• When an abnormality is noted, turn off the power immediately, or fire, electric shock or injury may occur.• The motor’s surface temperature may exceed70 °C, even under normal operating conditions. Ifa motor is accessible during operation, post thewarning label shown in the figure in aconspicuous position to prevent the risk of skinburn(s).Warning label• To dispose of the motor, disassemble it into parts and components as much as possible and dispose of individual parts/components as industrial waste.Checking the productVerify that the items listed below are included. Report any missing or damaged items to the branch or sales office from which you purchased the product.• Motor...............................................1 unit• OPERATING MANUAL................1 copyChecking the model nameCheck the model number against the number indicated on the product.Model Model Model4IK25GN-FCH 4IK25GN-ECH 4IK25GN-SH4IK25AA-FCH 4IK25AA-ECH 4IK25AA-SH5IK40GN-FCH 5IK40GN-ECH 5IK40GN-SH5IK40AA-FCH 5IK40AA-ECH 5IK40AA-SH5IK60GE-FCH 5IK60GE-ECH 5IK60GE-SH5IK60A-FCH 5IK60A-ECH 5IK60A-SH5IK60GU-FCH 5IK60GU-ECH 5IK60GU-SH5IK90GE-FCH 5IK90GE-ECH 5IK90GE-SH5IK90A-FCH 5IK90A-ECH 5IK90A-SH5IK90GU-FCH 5IK90GU-ECH 5IK90GU-SH Location for installationThe motor is designed and manufactured for installation in equipment.Install it in a well-ventilated location that provides easy access for inspection. The location must also satisfy the following conditions: • Inside an enclosure that is installed indoors (provide vent holes) • Operating ambient temperature−10 to +40 °C (+14 to +104 °F) (non-freezing)−10 to +50 °C (+14 to +122 °F) for three-phase 200 V• Operating ambient humidity 85%, maximum (non-condensing) • Area that is free from an explosive atmosphere or toxic gas (such as sulfuric gas) or liquid• Area not exposed to direct sun• Area free of excessive amount dust, iron particles or the like• Area not subject to splashing water (storms, water droplets), oil (oil droplets) or other liquids• Area free of excessive salt• Area not subject to continuous vibration or excessive shocks• Area free of excessive electromagnetic noise (from welders,power machinery, etc.)• Area free of radioactive materials, magnetic fields or vacuum• 1000 m (3300 ft.) or less above sea levelHow to install the motor• Round shaft typeDrill holes on the mounting plate and fix the motor on the plateusing screws, nuts, and washers (not supplied). Be careful there is nogap between the motor installation surface and the bracket.First number inmotor modelScrew size Tightening torque [N·m (lb-in)]4 M5 2.5(22)5 M6 3.0(26)Do not insert the motor into the mounting hole at anangle or force it in, as this may scratch the flange pilotsection and damage the motor.• Pinion shaft typeDrill holes on the mounting plate and fix the motor and gearhead on the plate using screws supplied with the gearhead. Be careful there is no gap between the motor flange and the gearhead.For details of installation, see the operating manual provided with the gearhead, which is sold separately.Use the gearhead with pinion shaft which is identicalwith one of motor.• Motor with cooling fanWhen installing a motor with cooling fan onto a device, leave10 mm (0.39 in.) or more behind the fan cover or open a ventilation hole so that the cooling inlet on the back of the motor cover is not blocked.Insulate all the wire connections, such as the connection between the motor and the capacitor connection.When the single-phase motor is run in only one direction, unused lead wires should be insulated.Ground the motor using a Protective Earth lead wire (green/yellow). The direction of motor rotation is as viewed from the side of the motor’s output shaft. The motor rotates in a clockwise (CW) and counterclockwise (CCW) direction.• Insulation class of this motor is B. Make sure that themotor case temperature does not exceed 90 °C(194 °F) during operation of the motor. Operationexceeding case temperature 90 °C (194 °F) maysignificantly deteriorate the coils and ball bearings ofthe motor and shorten the motor’s life span. Motorcase temperature can be measured by fixing athermometer on the motor surface. It can also bemeasured using thermo tape or a thermocouple.• To change rotation direction of the single-phasemotor, wait until the motor completely stops.Otherwise its direction may not change or may takemuch time to change.Rotating direction of the gearhead output shaftThe rotating direction of the gearhead output shaft may be opposite that of the motor shaft, depending on the gear ratio. For the rotating direction of the output shaft of a specific gearhead used, refer to the operating manual for the gearhead. Connection method to a terminal box• Open the terminal box and connect wires.• Use applicable cable ground and conduit for conduit opening. • After connecting, close the terminal box with the terminal cover. • Terminal cover screws tightening torqueSingle-phase 25 W, 40 W/Three-phase: 0.3 N·m (2.6 lb-in) Single-phase 60 W, 90 W: 1 N·m (8.8 lb-in)• Single-phase 25 W, 40 W/Three-phase••Connect the motor according to the figure.The connection method will vary, depending on the directionClockwiseLNCounterclockwiseLN∗ NC: Not connect. Three-phase motorsConnect the motor according to the figure.When connected according to the connection diagram, the motor will operate in the clockwise direction (CW) as viewed from the motor’s output shaft. To change the direction of rotation, change any two connections between U, V and W.ClockwiseL2 (S)L1 (R)L3 (T)Motors have a continuous rating.This motor is equipped with the feature listed below to prevent the motor from burning out as a result of abnormal heating which maybe caused by misapplication.• Thermal protection“TP” is stamped on the motor nameplate. The motor has an “auto reset” type thermal protector built into its motor coil. When themotor reaches a predetermined temperature, the internal thermal protector is activated and the motor is stopped.Always turn the power off before performing inspections.Thermal protector activation rangePower is turned off at 130±5 °C (266±9 °F)Power is turned back on at 82±15 °C (180±27 °F)When the motor cannot be operated correctly, refer to the contents provided in this section and take appropriate action. If the problem persists, contact your nearest office.Phenomena CheckitemsMotor does not rotate or rotates slowly. • Check the power supply voltage.• Connect the power supply and the motor correctly.• If terminal blocks or crimp terminals are used, check them for poor connection. • Keep the load at or below the allowable value.Motor sometimes rotates and stops. • Connect the power supply and the motor correctly.• If terminal blocks or crimp terminals are used, check them for poor connection.The motor rotates in the direction opposite to the specified direction. • Connect correctly by referring to “Wiring diagram.”• The rotating direction of the motor output shaft may be different from that of the gearhead output shaft depending on the gear ratio of the gearhead. See the operating manual for the gearhead.• The rotating direction is indicated as viewed from the motor output shaft. Check the reference direction.Motor temperature abnormally high [Motor case temperature exceeds 90 °C (194 °F)] • Check the power supply voltage. • Review the ventilation condition.Noisy operation • Assemble the motor and gearheadcorrectly by referring to the operatingmanual for the gearhead.• Assemble a gearhead of the same piniontype as the motor.• Unauthorized reproduction or copying of all or part of thismanual is prohibited.• Oriental Motor shall not be liable whatsoever for any problems relating to industrial property rights arising from use of anyinformation, circuit, equipment or device provided orreferenced in this manual.• Characteristics, specifications and dimensions are subject tochange without notice.• While we make every effort to offer accurate information in the manual, we welcome your input. Should you find uncleardescriptions, errors or omissions, please contact the nearestoffice.• is a registered trademark or trademark ofOriental Motor Co., Ltd., in Japan and other countries.© Copyright ORIENTAL MOTOR CO., LTD. 2008Printed on Recycled Paper • Please contact your nearest Oriental Motor office for further information.Headquarters Tokyo, JapanTel:(03)3835-0684 Fax:(03)3835-1890Tel:01 47 86 97 50 Fax:01 47 82 45 16Tel:(02)8228-0707 Fax:(02)8228-0708 Technical Support Tel:(800)468-39828:30 A.M. to 5:00 P.M., P.S.T. (M-F)7:30 A.M. to 5:00 P.M., C.S.T. (M-F)E-mail:*****************************Headquarters and Düsseldorf Office Tel:0211-52067-00 Fax:0211-52067-099 Munich Office Tel:089-3181225-00 Fax:089-3181225-25 Hamburg Office Tel:040-76910443 Fax:040-76910445Tel:01256-347090 Fax:01256-347099Tel:02-93906346 Fax:02-93906348Tel:(6745)7344 Fax:(6745)9405KOREATel:(032)822-2042~3 Fax:(032)819-8745Tel:(03)22875778 Fax:(03)22875528Tel:66-2-254-6113 Fax:66-2-254-6114。
MantelMount 电视杆说明书
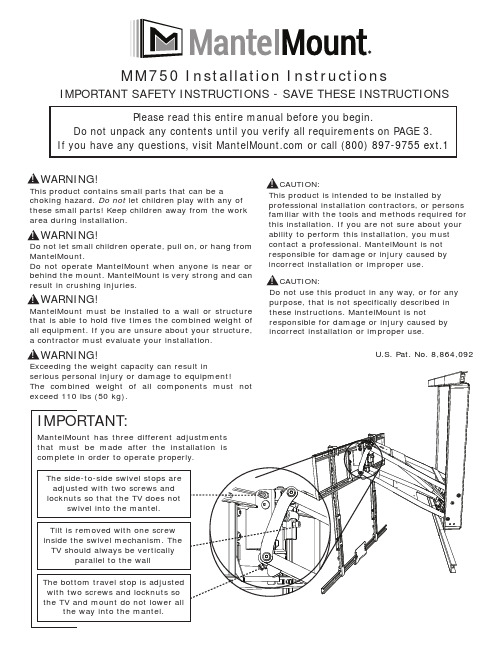
This product contains small parts that can be achoking hazard. Do not let children play with any of these small parts! Keep children away from the work area during installation.Do not use this product in any way, or for any purpose, that is not specifically described inthese instructions. MantelMount is notresponsible for damage or injury caused by incorrect installation or improper use.This product is intended to be installed byprofessional installation contractors, or persons familiar with the tools and methods required for this installation. If you are not sure about your ability to perform this installation, you must contact a professional. MantelMount is not responsible for damage or injury caused by incorrect installation or improper use.CAUTION:CAUTION:MantelMount.Do not operate MantelMount when anyone is near or behind the mount. MantelMount is very strong and can result in crushing injuries.that is able to hold five times the combined weight of all equipment. If you are unsure about your structure, a contractor must evaluate your installation.U.S. Pat. No. 8,864,092MM750 Installation InstructionsPlease read this entire manual before you begin.Do not unpack any contents until you verify all requirements on PAGE 3. If you have any questions, visit or call (800) 897-9755 ext.1IMPORTANT SAFETY INSTRUCTIONS - SAVE THESE INSTRUCTIONSBefore you begin, please verify that all components are included and undamaged. If any parts are missing or damaged, contact MantelMount. Never proceed with missing or damaged parts!Lay out all components and make sure you identify that each one has a match in the diagram. Some of the parts included will not be used during installation. Do not proceed if you do not understand and identify all of the components.{02} x4M5x30{01} x4M5x12{10} x4M5-M6{11} x12M8{12} x8Spacer{18} x8M6x12{19} x4M6x40{03} x4M5x40{05} x4M6x30{04} x4M6x16{06} x4M6x40{08} x4M8x25{07} x4M8x15{09} x4M8x45{13} x4Lag Bolt{16} x4Locknut M6{17} x4Locknut M8{14} x2Anchor{15} x8Cable Ties{20} x8M8x16{27} x2Vertical Brace{28} x2Brace Extender{26} x1TV Frame{30} x1Lift Housing{25} x6Wall Cover{21} x4Stud Bracket{29} x1Horizontal Brace, TV{31} x2Horizontal Brace{56} x1Center Handle2 MantelMount MM750MantelMount is designed for use only with decorative fireplaces that are not the primary heat source for a house. Temperature at the front edge of mantle should never exceed 110° F .ACEMantle must not extend from mounting surface more than 19 inches (22 inches for non-recessedinstallations). MantelMount can not extend past a mantel larger than 19 inches. Larger mantels will also reduce the amount of side-to-side swivel.110°F MAX.If mantle extends:Less than 10 inches 10 - 14 inches 14 - 16 inches 16 - 19 inchesThis is required space height:TV height plus 6 inches TV height plus 8 inches TV height plus 10 inches TV height plus 15 inchesThe space above the mantle must be taller than the TV . The required space depends on how far out the mantle extends. Refer to chart below and add this additional height to the TV height to determine if space is tall enough.Note: This is not an installation step, only a verification.Do not use these dimensions during installation.Customer Support 1.800.897.9755 x1 3..Irregular BackIrregular BackTV insert4 MantelMount MM750. However, the Brace Extenders {28}- The Brace Extenders areabove the bottom of the TV.- The Brace Extenders are installedonto the Horizontal Brace {29}..WithoutSound Bar:Extenders are1 or2 inchesabove the TV{12}Bottom ofCustomer Support 1.800.897.9755 x1 56 MantelMount MM750RECESSED installation using the Horizontal Braces {31} to attach to existing wall studs:The Horizontal Braces attach to the flange on the front of the Lift Housing {30}.The Braces can be located off-center to the Housing, if needed, to reach the nearest stud.Use the included Template to mark the location to cut the drywall. This installation is easiest when there is no center stud that needs to be cut to make room.Paintable Wall Covers {25} can be snapped onto the Horizontal Braces.{20}{31}{17}{13}{25}{11}Installation Options: Recessed using Horizontal Braces {31}Customer Support 1.800.897.9755 x1 7FIG. C(view facing the wall) When cutting a center stud, measure 1.5" above and below thetemplate mark before the opening is cut out. The drywall will holdthe stud in place while it is cut. Plunge cut through the stud atboth locations and attach the cut ends to the cross bracing whenthey are installed, see FIG. C.Cutting a Center Stud:{21}Stud Bracket8 MantelMount MM750washers are firmly against the Housing. Damage due to overtightening can cause property damage or injury.entire template to cut out the drywall.Customer Support 1.800.897.9755 x1 9. Always remember to tighten.{11}{20}{26}10 MantelMount MM750TV securely in the up position while also allowing the TV to gently rest in the down position. See the diagram below for the correct lifting adjustment.Neutral in the MID positionsCustomer Support 1.800.897.9755 x1 11Adjusting the Hard Stops for Range of Motion::12 MantelMount MM750Customer Support 1.800.897.9755 x1 1314 MantelMount MM750I T E M N O .P A R T N U M B E R D E S C R I P T I O N Q T Y .123456789101112131415161718192021222324253026272829121894121904121914121931219444M 5 x 12M 5 x 30M 5 x 40M 6 x 16M 6 x 30121974121984412199121954M 8 x 15M 8 x 25M 8 x 45M 6 x 401216641412636121228141374W a s h e r M 6W a s h e r M 8 x 2S p a c e r141101216284R o u n d S c r e w M 6 x 12121836121878L a g B o l t M 8 x 6041217634C a b l e T i e A n c h o r7L o c k n u t M 821050T V F r a m e , W e l d e d14038V e r t i c a l B r a c e1C a b l e T i e23121862N u t M 8140562B r a c e E x t e n d e r140601T V H o r i z o n t a l B r a c e211406W a l l C o v e r12255821088R o u n d S c r e w M 6 x 4012178S o c k e t C a p S c r e w M 8 x 2521090S o c k e t C a p S c r e w M 8 x 40L o c k n u t M 6211151R e c e s s F r a m e , 750, W e l d e d15023S t u d B r a c k e t4R o u n d S c r e w M 8 x 16Customer Support 1.800.897.9755 x1 15Full Manufacturer Warranty:MantelMount will replace or repair any product or part that proves defective due to improper workmanshipor material during the warranty period. Visit for details.S. Pat. No. 8,864,092REV 022020MM750CUSTOMER SUPPORT(800)-897-9755 。
Tekmand使用手册(简易版)

广州彩熠灯光有限公司
2
Tekmand 使用手册 (简易版)
面板介绍
Tekmand 系列灯光控制台功能十分强大,本说明书将介绍最基本的功能操作,使 初学者很快能上手进行灯光控制。
1. 屏幕 1(命令显示屏) 2. 屏幕 2 3. 屏幕 3 4. 屏幕 4 5. 云台--外接屏幕 5 6. 云台--外接屏幕 6 7. USB 接口 8. 电源按钮 9. 指纹识别 10. 总控杆 11. 调光转轮 12. 轨迹球(Pan/Tilt 功能和鼠标功能) 13. 属性转轮 14. 命令按键区 15. 多功能用户键 16. 窗口转轮 17. 推杆执行器 18. 按钮执行器 19. 通用执行器 & 翻页键
Tekmand 使用手册
(简易版)
Tekmand 使用手册 (简易版)
目录
Tekmand 控台介绍.....................................................................................2 面板介绍.....................................................................................................3 创建演出并配接灯具 ................................................................................5 控制常规灯.................................................................................................8 控制电脑灯.................................................................................................9 窗口及屏幕的使用 ..................................................................................11 灯组库 ....................................................................................................... 12 操作域 ....................................................................................................... 13 素材 ........................................................................................................... 14 场景/序列 .................................................................................................16 宏 ............................................................................................................... 18 效果 ........................................................................................................... 19 位图效果...................................................................................................22 布局 ........................................................................................................... 24 制作灯库...................................................................................................26 Tekmand 网络连接...................................................................................29
艾特顿199031电源速调器说明书

Eaton 199031Eaton Moeller® series Rapid Link - Speed controllers, 8.5 A, 4 kW, Sensor input 4, Actuator output 2, 400/480 V AC, PROFINET, HAN Q4/2, with fanAllgemeine spezifikationEaton Moeller® series Rapid Link Speed controller199031195 mm270 mm 220 mm 3.64 kgIEC/EN 61800-5-1 UL approval CE RoHS UL 61800-5-14015081970896RASP5-8424PNT-4120001S1Product NameCatalog NumberProduct Length/Depth Product Height Product Width Product Weight Certifications Catalog Notes EANModel Code3 fixed speeds and 1 potentiometer speedcan be switched over from U/f to (vector) speed control Connection of supply voltage via adapter cable on round or flexible busbar junction480 VIs the panel builder's responsibility. The specifications for the switchgear must be observed.400 V AC, 3-phase480 V AC, 3-phaseMeets the product standard's requirements.4 kW500 VMeets the product standard's requirements.-40 °C380 VIGBT inverterKey switch position OFF/RESETControl unitInternal DC linkKey switch position AUTOKey switch position HANDPTC thermistor monitoringThermo-click with safe isolationPC connectionSelector switch (Positions: REV - OFF - FWD)FanTwo sensor inputs through M12 sockets (max. 150 mA) for quick stop and interlocked manual operation2 Actuator outputs0 Hz200 %, IH, max. starting current (High Overload), For 2 seconds Generation Change RA-SP to RASP5Elektromagnetische Verträglichkeit (EMV)Generationentausch RAMO4 zu RAMO5Generationswechsel RASP4 zu RASP5Generation Change RASP4 to RASP5Firmware Update RASP 4.0Anschluss von Frequenzumrichtern an Generatornetze Generationentausch RA-SP zu RASP4.0Generationenwechsel RA-SP zu RASP5Generation change from RA-MO to RAMO 4.0Configuration to Rockwell PLC Rapid Link 5 Generationentausch RA-MO zu RAMO4.0Configuration to Rockwell PLC for Rapid LinkGeneration change RAMO4 to RAMO5Generation change from RA-SP to RASP 4.0MN034004_DEMN040003_DERapid Link 5 - brochureDA-SW-USB Driver DX-COM-STICK3-KITDA-SW-Driver DX-CBL-PC-3M0DA-SW-drivesConnectDA-SW-drivesConnect - installation helpDA-SW-drivesConnect - InstallationshilfeDA-SW-USB Driver PC Cable DX-CBL-PC-1M5Material handling applications - airports, warehouses and intra-logistics ETN.RASP5-8424PNT-4120001S1.edzIL034093ZUDE | Rapid Link 5Sortimentskatalog Antriebstechnik-DEMains voltage - max10.11 Short-circuit ratingRated operational voltage10.4 Clearances and creepage distancesOutput at quadratic load at rated output voltage - max Output voltage - max10.2.3.1 Verification of thermal stability of enclosures Ambient storage temperature - minMains voltage - minFitted with:Output frequency - minStarting current - max Anmerkungen zur AnwendungBenutzerhandbücherBroschüreneCAD model Installationsanleitung InstallationsvideosKatalogeevery 20 seconds, Power section10 kA40 °CPROFINET, optional5 HP500 Hz8 kHz, 4 - 32 kHz adjustable, fPWM, Power section, Main circuitParameterization: drivesConnectParameterization: FieldbusInternal and on heat sink, temperature-controlled Fan Parameterization: drivesConnect mobile (App) Parameterization: Keypad-10 °C≤ 0.6 A (max. 6 A for 120 ms), Actuator for external motor brakeDoes not apply, since the entire switchgear needs to be evaluated.8.5 ADoes not apply, since the entire switchgear needs to be evaluated.Does not apply, since the entire switchgear needs to be evaluated.Speed controller ramo5_v36.dwgrasp5_v36.stpeaton-bus-adapter-rapidlink-speed-controller-dimensions.eps eaton-bus-adapter-rapidlink-speed-controller-dimensions-003.eps eaton-bus-adapter-rapidlink-speed-controller-dimensions-002.eps eaton-bus-adapter-rapidlink-speed-controller-dimensions-004.epsRated conditional short-circuit current (Iq)Ambient operating temperature - maxCommunication interfaceAssigned motor power at 115/120 V, 60 Hz, 1-phase Output frequency - maxSwitching frequencyFeaturesAmbient operating temperature - minBraking currentNumber of HW-interfaces (serial TTY)10.6 Incorporation of switching devices and components Nominal output current I2N10.2.6 Mechanical impact10.3 Degree of protection of assembliesProduct category mCAD model ZeichnungenRadio interference classC1: for conducted emissions onlyC2, C3: depending on the motor cable length, the connected load, and ambient conditions. External radio interference suppression filters (optional) may be necessary.Heat dissipation capacity Pdiss0 WRated control voltage (Uc)24 V DC (-15 %/+20 %, external via AS-Interface® plug) 400/480 V AC (external brake 50/60 Hz)Assigned motor power at 460/480 V, 60 Hz, 3-phase5 HPNumber of HW-interfaces (RS-422)Mains current distortion120 %ProtocolPROFINET IO10.9.2 Power-frequency electric strengthIs the panel builder's responsibility.Overvoltage categoryIIIDegree of protectionNEMA 12IP65Ambient storage temperature - max70 °CRated impulse withstand voltage (Uimp)2000 VConnectionPlug type: HAN Q4/2Overload currentAt 40 °CFor 60 s every 600 sFunctionsFor actuation of motors with mechanical brake3 fixed speeds1 potentiometer speedOutput at linear load at rated output voltage - max4 kWMains voltage tolerance380 - 480 V (-10 %/+10 %, at 50/60 Hz)Leakage current at ground IPE - max3.5 mAConverter typeU converter10.2.2 Corrosion resistanceMeets the product standard's requirements.Supply frequency50/60 Hz10.2.4 Resistance to ultra-violet (UV) radiationMeets the product standard's requirements.10.2.7 InscriptionsMeets the product standard's requirements.Shock resistance15 g, Mechanical, According to IEC/EN 60068-2-27, 11 ms, Half-sinusoidal shock 11 ms, 1000 shocks per shaftApplication in domestic and commercial area permittedYesNumber of inputs (analog)Number of phases (output)310.12 Electromagnetic compatibilityIs the panel builder's responsibility. The specifications for the switchgear must be observed.10.2.5 LiftingDoes not apply, since the entire switchgear needs to be evaluated.Number of HW-interfaces (RS-485)1Number of HW-interfaces (industrial ethernet)Efficiency98 % (η)System configuration typeCenter-point earthed star network (TN-S network)AC voltagePhase-earthed AC supply systems are not permitted.10.8 Connections for external conductorsIs the panel builder's responsibility.ProtectionFinger and back-of-hand proof, Protection against direct contact (BGV A3, VBG4)Braking voltage400/480 V AC -15 % / +10 %, Actuator for external motor brakeApplication in industrial area permittedYesClimatic proofingIn accordance with IEC/EN 50178< 95 %, no condensation10.9.3 Impulse withstand voltageIs the panel builder's responsibility.Overload current IL at 150% overload12.7 AInput current ILN at 150% overload7.8 ANumber of HW-interfaces (RS-232)Number of inputs (digital)4Current limitationAdjustable, motor, main circuit0.8 - 8.5 A, motor, main circuitCable lengthC2 ≤ 5 m, maximum motor cable lengthC3 ≤ 25 m, maximum motor cable lengthC1 ≤ 1 m, maximum motor cable length10.5 Protection against electric shockDoes not apply, since the entire switchgear needs to be evaluated.Mounting positionVerticalMains switch-on frequencyMaximum of one time every 60 seconds10.13 Mechanical functionThe device meets the requirements, provided the information in the instruction leaflet (IL) is observed.10.9.4 Testing of enclosures made of insulating materialIs the panel builder's responsibility.Heat dissipation per pole, current-dependent Pvid0 WElectromagnetic compatibility1st and 2nd environments (according to EN 61800-3)Resolution0.1 Hz (Frequency resolution, setpoint value)Assigned motor power at 460/480 V, 60 Hz5 HPRelative symmetric net voltage tolerance10 %Rated operational current (Ie)8.5 A at 150% overload (at an operating frequency of 8 kHz and an ambient air temperature of +40 °C)Number of outputs (analog)Rated operational power at 380/400 V, 50 Hz, 3-phase4 kWNumber of HW-interfaces (USB)Operating modeU/f controlSynchronous reluctance motorsPM and LSPM motorsBLDC motorsSensorless vector control (SLV)Rated frequency - min45 HzDelay time< 10 ms, On-delay< 10 ms, Off-delayNumber of outputs (digital)2Power consumption95 W10.2.3.2 Verification of resistance of insulating materials to normal heatMeets the product standard's requirements.10.2.3.3 Resist. of insul. mat. to abnormal heat/fire by internal elect. effectsMeets the product standard's requirements.Number of HW-interfaces (other)Rated frequency - max66 HzVibrationResistance: 10 - 150 Hz, Oscillation frequencyResistance: 57 Hz, Amplitude transition frequency on accelerationResistance: According to IEC/EN 60068-2-6Resistance: 6 Hz, Amplitude 0.15 mmShort-circuit protection (external output circuits)Type 1 coordination via the power bus' feeder unit, Main circuit10.7 Internal electrical circuits and connectionsIs the panel builder's responsibility.Braking torque≤ 30 % (I/Ie)Adjustable to 100 % (I/Ie), DC - Main circuitRelative symmetric net frequency tolerance10 %10.10 Temperature riseThe panel builder is responsible for the temperature rise calculation. Eaton will provide heat dissipation data for the devices.Number of HW-interfaces (parallel)Assigned motor power at 230/240 V, 60 Hz, 1-phase5 HPInterfacesSpecification: S-7.4 (AS-Interface®)Max. total power consumption from AS-Interface® power supply unit (30 V): 250 mANumber of slave addresses: 31 (AS-Interface®)Number of phases (input)3Eaton Konzern plc Eaton-Haus30 Pembroke-Straße Dublin 4, Irland © 2023 Eaton. Alle Rechte vorbehalten.Eaton ist eine eingetragene Marke.Alle anderen Warenzeichen sind Eigentum ihrer jeweiligenBesitzer./socialmedia51.6 W at 25% current and 0% speed 53.8 W at 25% current and 50% speed 60.9 W at 50% current and 0% speed 64 W at 50% current and 90% speed 65.4 W at 50% current and 50% speed 85.1 W at 100% current and 0% speed 94 W at 100% current and 50% speed 95.3 W at 100% current and 90% speed 2Max. 2000 mAbove 1000 m with 1 % performance reduction per 100 mHeat dissipation at current/speed Number of interfaces (PROFINET)Altitude。
K-TEK超声波AT100操作手册

AT100/AT100SAT100-0200-1 Rev J (05-2009) DCN02932TABLE OF CONTENTS1.0 INTRODUCTION (4)2.0 STORAGE INFORMATION (5)3.0 INSTALLATION AND BASIC WIRING (5)3.1 All Installations (5)3.1.1 Compression Fittings (5)3.1.2 Floats (5)3.1.3 Transmitter Housing Height (5)3.2 Stilling Probes (5)3.2.1 Assembly Instructions for F1 Flexible Probes (6)3.3 Loop Wiring (6)3.4 Jumper Settings (6)4.0 TRANSMITTER CALIBRATION AND SETUP (7)4.1 Level Output Calibration (7)4.1.1 Calibration Using the Pushbuttons (7)4.2 Reversing Action (7)4.2.1 Reverse Action Calibration Using the Pushbuttons (7)4.3 Damping (7)4.4 Calibration Using the LCD Setup Menu (9)4.5 Selecting a Primary Variable (PV) (9)4.6 Selecting an Engineering Unit for Measurement (EUN) (10)4.7 Level Offsets (L1O and L2O) (10)4.8 DAC Trim (10)4.9 Temperature Output (10)4.9.1 Selecting the Unit of Temperature (EUN TEMP) (10)4.9.2 Temperature Output Calibration (11)4.9.3 Temperature Reset (TMP RSET) (11)4.9.4 Temperature Master Calibration ......................................................................................... 11 4.10 Volumetric Strapping .................................................................................................................. 12 4.10.1 How the Strapping Table Works (12)4.10.2 Setting Up (or resetting) the Strapping Table (12)4.10.3 Selecting the Input Mode (Automatic or Manual) (12)4.10.4 Setting Up Strapping Table Points (13)4.10.5 Notes on Strapping Table Usage (13)4.10.6 Saving/Loading a Strapping Table (13)4.10.7 Setting Current Output Based on Volume (13)4.11 Alarm Delay (14)4.12 Custom Current Ranging (14)4.12.1 Description and Method of Operation ................................................................................ 14 4.12.2 CCR Set Up .. (14)5.0 COMMUNICATION OPTIONS ........................................................................................................................ 15 5.1 Hart Protocol Interface Option ..................................................................................................... 15 5.1.1 Using a 268/275/375 Rosemount Communicator or Equal . (15)5.2 Honeywell DE Protocol (15)5.2.1 Interoperability and Conformance Class (15)5.2.2 Operating Modes (15)5.3 Foundation Fieldbus .................................................................................................................... 16 5.3.1 Topology .. (16)5.3.2 Electrical Considerations (16)5.3.3 Field Wiring (17)5.3.4 Jumper Settings (17)5.3.5 DD Files (17)5.3.6 Transducer Block (17)5.3.7 Al Function Blocks (17)AT100-0200-1 Rev J (05-2009) DCN02933TABLE OF CONTENTS (continued)5.3.8 PID Blocks ........................................................................................................................................ 18 5.3.9 Link Active Scheduler / Back-up LAS .. (18)5.3.10 Threshold Adjustment (18)5.3.11 Sample Configurations (18)6.0 SAFETY, MAINTENANCE, & TROUBLESHOOTING (19)6.1 Personnel Qualifications (19)6.2 Required Tools (19)6.3 Suggested Proof Test (20)6.4 Safety Inspection (20)6.4.1 Float Inspection (20)6.4.2 Sensor Inspection (21)6.4.3 Transmitter Testing (21)6.4.4 Output Checkout (21)6.5 4-20mA, HART Transmitters (23)6.6 Foundation Fieldbus Transmitters (24)6.7 Verify Proper Power Up of the Transmitter (25)6.8 Verify Current Output Stability (25)6.9 Threshold Adjustment (26)6.10 Module Replacement (26)6.11Terminal Strip Checkout (26)6.12Threshold Adjustment Using an Oscilloscope (27)7.0 NAMETAG INFORMATION (28)8.0 WIRING DIAGRAMS (29)8.1 FM/CSA (29)8.2 ATEX/IEC (31)8.3 Typical Loop Wiring Diagram (32)8.4 Loop Powered TX Hookup /RI Dual Compartment Housing (33)8.5 Temperature Simulation Wiring Diagram (34)9.0 /F1 OPTION ASSEMBLY DRAWING (35)10.0 SIL CERTIFICATE (36)11.0 EU DECLARATION OF CONFORMITY (38)12.0 WARRANTY STATEMENT (39)AT100-0200-1 Rev J (05-2009) DCN02934K-TEK AT100 transmitters are used extensively around the world to accurately measure level in processvessels. High accuracy and no maintenance are two of the most common reasons for choosing this technology.With optional ratings to 800°F (427°C) and 3000 PSI (207 bar), K-TEK's Magnetostrictive Level Transmitters aresuitable for almost any application. HART, Honeywell DE, and Foundation Fieldbus Protocol options make ourAT100’s easy to connect digitally to most control systems. LCD displays provide indication as 4-20mA, %, and otherengineering units.When used on Storage Tanks, concerns of high accuracy, low maintenance and reasonable cost leads customers to install flexible probe versions of the AT100’s in their storage tanks. With the ability to be easily installed to a maximum of 75 feet (23 meters), almost any liquid storage application can be handled. Some common liquids include water, acids, caustics, propane, ammonia, oils, fuels, chemicals, and waste liquids. An optional internal 20-segment increment table allows the AT100 to provide volumetric output in vertical cylinder, horizontal cylinder or spherical vessels (See Section 4 for details on the Volumetric Strapping Table).K-TEK’s AT100’s can be used as "Displacer Replacers". Most Liquid Level Displacers in dynamic processes have seen many repetitive problems in operation including the following: extreme errors in output due tospecific gravity changes, leaks around the torque tube penetration, and low or stuck readings due to product buildupon the torque tube or displacer. AT100’s can be inserted into the existing Displacer Chambers or a new ExternalChambers to solve the listed problems. Tremendous improvements in accuracy will be realized. Additionally, this isan extremely easy way to update pneumatic Displacer Transmitters.The Magnetostrictive Level Transmitter (AT100) can be used to measure the level of interface between twofluids The AT100 is the finest technology available for liquid level interface measurement and control. K-TEKAT100’s can be equipped to provide two (2) level indications: one for interface and a second for total level. Designsare available for differences of specific gravity down to 0.04 differences. Most commonly applied to oil and waterseparator interface, this technique is used in many process applications. Others include HF acid / propane vessels,de-salters and sumps.The AT100 can be used as a Valve Positioner by utilizing the AT100’s non-contact style of measurement. Amagnet is attached to the valve stem and the AT100 is located along side the valve stem. The inherent 0.01% highaccuracy in our AT100 transmitter allows exceptionally fine control and measurement of valve position. K-TEK’sAT100’s never need to be re-calibrated ensuring accurate and precise control. The AT100 can also be used as an Equipment Positioner. Industrial facilities require accurate positioning of equipment. This can be accomplished withMagnetostrictive (non-contact measurement). It has been applied to many devices including gates, louvers, dampers, and hydraulic cylinders. K-TEK advantages of push button configuration, 4-20mA output, and heavy dutyconstruction ensure ease of installation and a long trouble free life.Finally, the AT100 can be used in various Sanitary Applications including the Bio-Tech, Pharmaceutical andFood Industries. A range of surface finishes are available to suit the needs of the process environment includingelectro-polishing.Based on the Functional Safety Assessment of Exida, the AT100 transmitter is suitable for use in a SafetyInstrumented Function requiring a SIL 2 risk reduction in single use and a SIL 3 risk reduction in redundant use witha Hardware Fault Tolerance of 1.Only transmitters meeting all of the following requirements may be used in a Safety Instrumented Function:• Transmitters fitted with a 4-20 mA output HART protocol /M4A or /M4B or /M4AS or /M4BS Electronic Module.• Modules marked as follow: AT_H_01_S003_090209 or AT_H_TS_01_S003_090209 (Transmitters equippedwith software revision of AT_H_090209 or AT_H_TS_090209 and a hardware revision 01).1.0 INTRODUCTIONAT100-0200-1 Rev J (05-2009) DCN02935 If required, storage prior to installation should be indoors at ambient temperature, not to exceed the following:Temperature range: -40º- 150ºF (-40º- 66ºC)Humidity: 0 to 95% R.H. non-condensing.WARNING: Transmitter probes with /SW3 option have a flexible stainless steel sensor tube which is not hermetically sealed. When removing the sensor from the sensor well, care should be taken not to expose the sensor to moisture, and to prevent water from entering the sensor well.3.1 All InstallationsPrior to installation, verify the model of the transmitter listed on the nametag is suitable for the intended application. Information regarding the model specifications may be found on the AT100 Datasheet at .3.1.1 Compression FittingsWhen fitted with a compression fitting as the process connection, the sensor tube is shipped with a set of TEFLON ferrules, and a set of metal ferrules in a separate bag. The Teflon ferrules are only intended for use in applications with operating pressures below 50 PSI (3.4 bar) and temperatures below 400ºF (204ºC.); for higher operating pressures or temperatures or for permanent installation, replace the Teflon ferrules with the metal ferrules.3.1.2 FloatsDuring installation, it may be necessary to remove the float and spacer (if included) from the sensor tube. For proper operation, the float must be reinstalled using the proper orientation. Floats may be marked with “Top for SPM” or “Top for AT”, this end of the float must face the transmitter head. Other floats may be marked with an arrow indicating the proper orientation. If a float is etched with information but does not indicate a proper orientation, it will be bidirectional and can be installed in either direction. If a float does not have any markings (sanitary applications) it will have an extra rolled seam to indicate the top half of the float.3.2 Stilling ProbesCertain transmitter options will have the sensor tube inserted into a stilling probe. These options allow the sensor tube and housing to be removed for service without breaking the seal on the vessel. These options include (consult model number) SW1, SW2, SW3 and F1. ModelSensor Type Stilling Probe SW1 1/2” rigid 5/8“ tube SW25/8” rigid 3/4” pipe (typical) SW31/2” flexible stainless 5/8” tube F1 5/8” flexible plastic 1” sectional tubeThe compression fittings which hold the sensor inside the stilling probe will contain Teflon ferrules. It is not necessary to change the Teflon ferrules to metal. This connection will not be required to hold pressure.2.0 STORAGE INFORMATION3.0 INSTALLATION AND BASIC WIRINGOption Height H0 7.75 inches (197 mm) H1, F1 14.75 inches (375 mm) H2, H3 24.75 inches (629 mm) 3.1.3 Transmitter HousingOnce installed, the top of the transmitter housing will extend above theprocess connection based on the particular model number. The extension of theprobe on some of the options is required to keep the transmitter electronicswithin its safe operating environment not to exceed:Temperature range: -40º- 150ºF (-40º- 66ºC)Humidity: 0 to 95% R.H. non-condensing.AT100-0200-1 Rev J (05-2009) DCN029363.3 Loop WiringRemove the test wires shipped with the transmitter. For field wiring, use 18 Gauge twisted shielded pair. Please refer to included wiring diagram (Section 8.0). Electrical connection to the transmitter should comply with all necessary standards as indicated by the area classification listed on the nameplate of the transmitter (Section 7.0). Apply loop power to transmitter as follows:Terminal Block + : +24 VDC (14-36 VDC)Terminal Block - (METER) : COMMONTerminal Block METER : Not used during normal operationGround screw : GROUND- Ground wires must be connected to ground screws using fork terminals to ensure proper electrical connection. - The current output of the transmitter is capable of driving a minimum of 250 ohms with a supply voltage of 19 Volts minimum.WARNING: A multi-meter may be placed between the METER positions of the terminal block to read the current outputof the transmitter without breaking the loop wiring. Do not connect multi-meter to METER test positions when instrumentis located in a hazardous environment.3.2.1 Assembly Instructions for F1 Flexible Probes Refer to Appendix B for /F1 Option Assembly Drawing1. Prepare joints #2 and #3 by lubricating the O-Ring and mating surface.2. Lower the bottom tube section with the float stop and float into the tank.3. Insert the top of the tube assembly through the mounting flange.4. Add the next section of tube and thread together using thread locking fluid to secure joints.5. Repeat step 4 for each middle tube sections.6. Add the last section (TOP) of tube, with 1” compression fitting, and thread into assembly using threadlocking fluid to secure the joint.7. Thread the tube compression fitting into the mounting flange using thread sealant.8. Lower the tube assembly until it hits the bottom of the tank. Raise the sensor well back up ½” andsecure the assembly in place by tightening the tube compression fitting.WARNING: When handling flexible tube, do not bend any section of the tube into a diameter of less than 4 ft., as thiscould permanently damage the internal assembly and prevent proper operation.9. Insert the flexible probe into the tube assembly. Secure flexible probe assembly to stainless steel tubeusing 1” tube to 1” tube compression fitting.WARNING:Insure that assembly is tight and properly sealed to prevent moisture entry.3.4 Jumper SettingsThe jumpers located on the face of the electronics module (top left hand side) can be setup as follows:See Section 6.11• ALARM (Fail Safe): (left jumper)-The Alarm jumper will determine the output of the transmitter in the event that there is a failure in detectingthe return signal from the sensor tube. This jumper should be set in the location which will send the controlstructure into a safe state.-Placing the jumper to the lower position causes the output to go to 20.99 mA when there is a loss of signalor transmitter malfunction.-Placing the jumper to the upper position causes the output to go to 3.61 mA when there is a loss of signalor transmitter malfunction.• WRITE PROTECT (right jumper)-When the jumper is in the lower position, the transmitter configuration cannot be changed via thepushbuttons or with a handheld communicator.For changes to the jumper settings to take effect, transmitter power must be turned OFF then back ON.3.0 INSTALLATION AND BASIC WIRINGAT100-0200-1 Rev J (05-2009) DCN02937 4.1 Level Output CalibrationThe AT100 is a digital transmitter with no routine calibration required. If re-calibration is required, calibration can be changed using the module pushbuttons, a HART communicator (for units with the HART option), or with the menu driven LCD readout (for units with LCD option).4.1.1 Calibration Using the Pushbuttons• Setting the 4mA point:-Establish a tank level of 0% or move the float to the desired 0% point-Enter the calibration mode by pressing the UP & DOWN buttons together for 1 second.-Press the DOWN button for 1 second to set the output at 4.00mA.• Setting the 20mA point:-Establish a tank level of 100% or move the float to the desired 100% point-Enter the calibration mode by pressing the UP & DOWN buttons together for 1 second.-Press the UP button for 1 second to set the output at 20.00mA.Note: The above steps can be repeated as many times as required4.2 Reversing ActionIf required, transmitter output can be reversed by following these steps (Note: this only reverses the 4-20 mA output, not the Engineering Unit Readout)4.2.1 Reverse Action Calibration Using The Pushbuttons1. Adjust the tank level to 50% or move the float to the 50% point ( + or - 10% ).-Enter the calibration mode by pressing the UP & DOWN buttons together for 1 second and pressthe DOWN button for 1 second to set the output at 4.00 mA.2. Adjust the level or move the float to the new SPAN (20.00mA) point.-Enter the calibration mode by pressing the UP & DOWN buttons together for 1 second and pressthe UP button for 1 second to set the output at 20.00 mA.3. Adjust the level or move the float to the new ZERO (4.00mA) point.-Enter the calibration mode by pressing the UP & DOWN buttons together for 1 second and pressthe DOWN button for 1 second to set the output at 4.00 mA.Note: Procedures 4.1.1 and 4.2.1 will only change the calibration for the selected Primary Variable.4.3 DampingDamping helps to reduce the affects of rapid or irregular movement of the fluid level in a tank or vessel. Adjustments to Damping will either increase or decrease the time required for the transmitter output to respond to changes in input from the sensor tube. A higher number allows for more output stability. A lower number will provide a quicker response. The maximum response time to a process change will be less than 110 milliseconds or the value of the Damping, whichever is greater. The factory default setting for Damping is 0.8 seconds.• The output damping amount can be changed as follows:-Press the SELECT and UP buttons together for 1 second to double the damping value.-Press the SELECT and DOWN buttons together for 1 second to divide the damping value by 2.• The Damping value may also be adjusted in the Calibration Menu on transmitters equipped with an LCD Display. The Damping is adjustable from 0 to 36 seconds.4.0 TRANSMITTER CALIBRATION AND SETUPAT100-0200-1 Rev J (05-2009) DCN02938AT100 Menu Flow Chart • To access a menu item press the SELECT button.• Use the UP and DOWN buttons to scroll through each menu and change the value of digits and menu entries.Notes: 1. These items will only appear based on the ordered options of the transmitter.2. Current ranging works only on Level (LU). Even though selected, volume uses 4-20mA.CAL - Calibration MenuMAIN DISPLAYCFG - Configuration MenuAT100-0200-1 Rev J (05-2009) DCN029394.4 Calibration Using the LCD Setup MenuThe LCD Display option offers a menu driven setup that uses the UP, DOWN and SELECT pushbuttons. Refer to the menu flow chart for navigation and selection instructions.• Setting the 4mA point:-Under the CAL menu, scroll DOWN to the LRV (Lower Range Value) menu option. Press SELECT tochange the value (in Engineering Units) for which the 4mA point is to be set.• Setting the 20mA point:-Under the CAL menu, scroll DOWN to the URV (Upper Range Value) menu option. Press SELECT tochange the value (in Engineering Units) for which the 20mA point is to be set.Note: The above steps can be repeated as many times as required. This procedure will only change the calibration for the selected Primary Variable.4.5 Selecting a Primary Variable (PV)This section applies to dual-float transmitters only.For a dual-float transmitter, the primary variable (LL1 or LL2) defines the float used to calculate current (mA) output. If the primary variable is set to LL1, current output will be determined by the position of the float nearest the transmitter housing. Alternately, if PV is set to LL2, current will correlate to the float farthest from the transmitter.• Selecting the Primary Variable-Under the SET menu, access the CFG menu, then go to the PV= menu option.-Press SELECT, then press UP or DOWN to cycle between LL1 and LL2 (the LCD will be blinking with your selection).-When the LCD is displaying the intended selection, press SELECT once more to set PV (the display should stop blinking).Note: If the Primary Variable is changed, it may be necessary to reset the 4 and 20 mA calibration points.Electronics WithoutLCD Display Electronics With LCD Display4.0 TRANSMITTER CALIBRATION AND SETUPAT100-0200-1 Rev J (05-2009) DCN029310 4.6 Selecting an Engineering Unit for Measurement (EUN)The unit is capable of displaying level output in inches, feet, millimeters, centimeters, meters, or in percent of range.• Selecting an Engineering Unit-Under the CFG menu, go to the EUN menu option.-Press SELECT, then press UP or DOWN to cycle between engineering units.-When the LCD is displaying the intended unit, press SELECT once more to set the engineering unit (the display should stop blinking).Note: Due to 4 digit display limitations on the display, if 9999mm will be exceeded, the metric engineeringunits must be changed to cm.4.7 Level Offsets (L1O and L2O) Level Offsets can be utilized to make the indicated level on the transmitter match the actual level in your tank or vessel. This is typically used to compensate for an un-measureable area at the bottom of the vessel. The Level Offsets can also be utilized to make the indicated level on the AT transmitter match the indicated level of another transmitter. Positive offsets will be added to the actual level of the transmitter to indicate a higher level. Conversely, negative offsets will indicate lower levels.• Changing the Level Offset- Navigate to the L1O (Level 1 Offset) menu option.- Press SELECT to change the value (in Engineering Units) of the level offset to be applied.- For dual-float units, Level 2 can be offset via the above steps with the L2O menu option.4.9.1 Selecting the Unit of Temperature (EUN TEMP)The unit will display temperature in either Celsius or Fahrenheit degrees.• Selecting the Unit of Temperature-Under the CFG menu, go to the EUN TMP menu option.-Press SELECT, then press UP or DOWN to cycle between Celsius and Fahrenheit.-When the LCD is displaying the intended unit, press SELECT once more to set the temperature unit (thedisplay should stop blinking). 4.9 Temperature OutputThis section applies only to transmitters with the temperature output option. These transmitters will have module types of M5A or M5B with or without a suffix of “D” or “F”.4.0 TRANSMITTER CALIBRATION AND SETUP4.8 DAC TrimThe output of the AT100 transmitters will be set up at the factory using calibrated multi-meters. Once installed, the current output received by the control system will be influenced by the available power and field wiring and may not indicate an exact 4.00 and 20.00 mA. To correct this error a DAC TRIM may be performed.• Performing the DAC Trim-Under the CAL menu, scroll down to the DAC TRIM option-Press UP and SELECT or DOWN and SELECT to enter the DAC TRIM menu-At D 4 or D20 enter the current reading indicated at the control system and the transmitter will correct itsoutput-Repeat each entry if needed then EXIT the menu.4.0 TRANSMITTER CALIBRATION AND SETUP4.9.2 Temperature Output CalibrationThe transmitter is factory calibrated to an accuracy of ±0.5° Celsius, over a range of -200 to 300°C. Fine calibration and trim for a custom range can be done via the following steps:• Setting the Lower Temperature Trim (LTT)-Bring the sensor (located near the bottom of the transmitter probe) to the temperature that will be the lowerend of the temperature range.-Under the CAL menu, go to the LTT (Lower Temperature Trim) menu option. Press SELECT to changeLTT to the current temperature of the sensor.• Setting the Upper Temperature Trim (UTT)-Bring the sensor (located near the bottom of the transmitter probe) to the temperature that will be the upperend of the temperature range.-Under the CAL menu, go to the UTT (Upper Temperature Trim) menu option. Press SELECT to changeUTT to the current temperature of the sensor.Note: Trim must be within 10°C of factory calibration to be accepted.4.9.3 Temperature Reset (TMP RSET)If required, the unit’s temperature settings (i.e. LTT and UTT) can be reset to the factory temperature calibration. To reset the unit to the factory temperature calibration, navigate to the TMP RSET menu option and press SELECT.4.9.4 Temperature Master CalibrationThe temperature indication of the AT100 will be factory calibrated from –200 to 300 degrees C. Under normal circumstances, it will not be necessary to recalibrate the temperature transmitter. If for some reason recalibration is required, the following steps will be used.1. Disconnect the power.2. Setup decade box per drawing in Section 8 - Wiring Diagrams3. Set resistance to 185 ohms.4. Apply power.5. Set EUN TEMP to °C (Celsius)6. Cycle through CFG menu to END.7. At END push UP and DOWN together.8. At FAC –200 press SELECT then UP and DOWN at the same time.9. Scroll Down to END and SELECT.10. Verify TMP indicates -200°C.11. Disconnect the power.12. Set decade box for 2120 ohms.13. Apply power.14. Cycle through CFG menu to END.15. At END push UP and DOWN together.16. Scroll down to FAC 300.17. Press SELECT then UP and DOWN at the same time.18. Scroll Down to END and SELECT.19. Verify TMP indicates 300°C.20. Disconnect the power.21. Reconnect RTD.22. Reapply power.4.0 TRANSMITTER CALIBRATION AND SETUP4.10 Volumetric StrappingNote: For AT100 models with Strapping Table option only. If utilizing Foundation Fieldbus refer to section 4.3.5.2 for strapping table instructions.4.10.1 How the Strapping Table WorksThe AT strapping table works by using table points set up by the user. For every point, there is a volume (provided by the user) and a measurement (provided by either the user or the transmitter). These table points are used to map sensor measurement to volume output. As the float travels the length of the probe, the volume output will change based on the two points in the table closest to the given transmitter measurement. With no points in the table, the volume output is linear between VMN (volume min) at 0 measurement and VMX (volume max) at UTP (upper trim point) which equates to the highest point of float travel. As points are added, the volume output is extrapolated with respect to VMN, the table points, and VMX.The Volumetric Table is capable of being set up in two different modes, Automatic and Manual. In Automatic mode, as a volume point is entered, the position of the transmitter float will determine the transmitter measurement associated with the volume entered. In Manual mode, as a volume point is entered, the user will be able to modify the measurement to which the volume corresponds.The points in the table are listed sequentially on the LCD as O01, O02, I02, … O19, I19, O20, I20. An ‘O’ is listed for each output point, which corresponds to volume. An ‘I’ is listed for each input point, which corre-sponds to linear measurement. If in manual mode, both output and input points will be available. In automatic mode, only output points will be shown.4.10.2 Setting Up (or resetting) the Strapping Table• Under the CAL menu:-Scroll to VOL TABL, then press SELECT.-Scroll up to VST RSET, then press SELECT. This will erase any table points currently set.• Under the CFG menu:-Scroll down to UTP, (which stands for Upper Trim Point) and note the value listed.-Scroll down to VMX (Volume Maximum).-Enter for 0 as a value ‘0000’, then press SELECT to reset the LCD decimal.-Next, enter the value of the Maximum Volume corresponding to UTP. Note: Enter only the whole number of the value, since the decimal is not present, then press SELECT.-After the decimal has been placed, set any digits to the right of the decimal, if available.-Scroll up to VMN (Volume Minimum).-Enter the volume of the tank at 0 measurement on the transmitter probe.4.10.3 Selecting the Input Mode (Automatic or Manual)• The AT transmitter provides two options for entering the values of the strapping table. The Automatic option requires the level (or float) to be at the fixed location that corresponds to the selected volumetric output point when the point is entered. If it is not possible (or feasible) for the tank level to be manipulated but a distance-to-volume conversion chart is available, the strapping table can be easily set up using Manual mode.• Under the CFG menu:-Scroll down to VOL MAN or VOL AUTO (the LCD will display the current input mode).-To switch between modes, press SELECT.-Scroll UP or DOWN to change the mode.-Press SELECT。
蜜汁公司气燃机安全控制箱DKG 972说明书
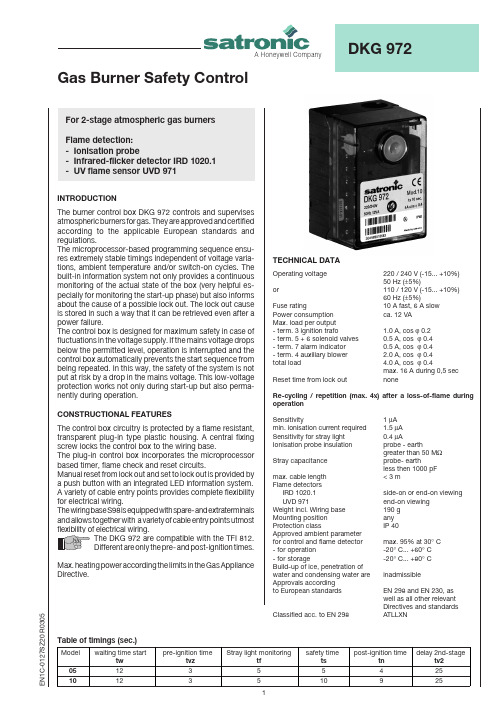
1Gas Burner Safety ControlE N 1C -0127S Z 20 R 030521.2 Lock-out diagnosesIn case of a failure the LED is permanently illuminated. Every 10 seconds the illumination is interrupted by a flash code,which indicates the cause of the error. Therefore the following sequence is performed which is repeated as long as the unit is not reset.Sequence:illuminated phase dark phase Flash-Code dark phase ❘ ❚ ❚ ❚ ❚for 10 secfor 0.6 secfor 1.2 secError diagnosis Error message Flash-Code Possible faultlockout ❘ ❚ ❚ ❚ ❚within lock out safety time no flame establishment stray light❘ ❘ ❚ ❚ ❚stray lightduring monitored phase,detector may be faultyFlash-Code for manual lock out manual/external ❘ ❘ ❚ ❚ ❚ ❚ ❚ ❚ ❚ ❚lock out(see also 3. lock out and reset)2. Flame detectionThe following types of flame detectors are suitable:–Ionisation probe, temperature resistant material, well insulated (material and insulation same as for ignition electrode).–Infrared-flicker detector type IRD 1020.1 with mounting flange M 93 or the UV solid state flame sensor UVD 971.Flame detection using an ionisation probe is only possible in conjunction with mains supplies which provides a neu-tral earth connection.Connecting the IRD 1020.1 or UVD 971 the correct wiring has to be observed.2.1 Stray light monitoringThe stray light check is performed at the end of the pre-purge time for thr duration as mentioned in the table of timings.APPLICATION FEATURES 1. Information systemThe information system is microprocessor based and re-ports on all aspects of burner control box operation and flame supervision. It informs continuously about the actual programming sequence the unit is just performing. Besides monitoring of the programming sequence it also allows to identify errors during start-up of operation without any additional testing devices. The automatically performed diagnosis is a valuable tool which facilitates service/maintenance work and therefore saves costs. The analyses of the error cause can be done directly on stage or if not possible afterwards as the lock out reason is stored in a non-volatile lock out mode memory.The information system communicates with the outside world using a LED (the used Flash-Code is similar to the Morse-Code). The messages are optically transmitted by a appropriately flashing LED. Using an additional terminal (optional), the messages can be recorded and displayed in easy readable form.1.1 Programming sequence displayThe built-in microprocessor controls not only the pro-gramming sequence but the information system too. The individual phases of the programming sequence are displayed as Flash-Code.The following messages can be distinguished:Message Flash-Code waiting time ❘ ❘ ❘ .twpre-ignition ❘ ❘ ❘ ❘ .tvzsafety time ts ❚ ❘ .post ignition tndelay time to valve V2❚ ❘ ❘ .tv2running❘ _low mains voltage ❘ ❚ ❚ _Internal fuse defect ❘ ❚ _> control box defectDescription❘=short pulse ❚=long pulse .=short pause _=long pauseD K G 9723D K G 9724D K G 9725D K G 9726Honeywell-Platz 1Postfach 324CH-8157 Dielsdorf。
DKM-2铁路道口电动栅栏控制器使用说明
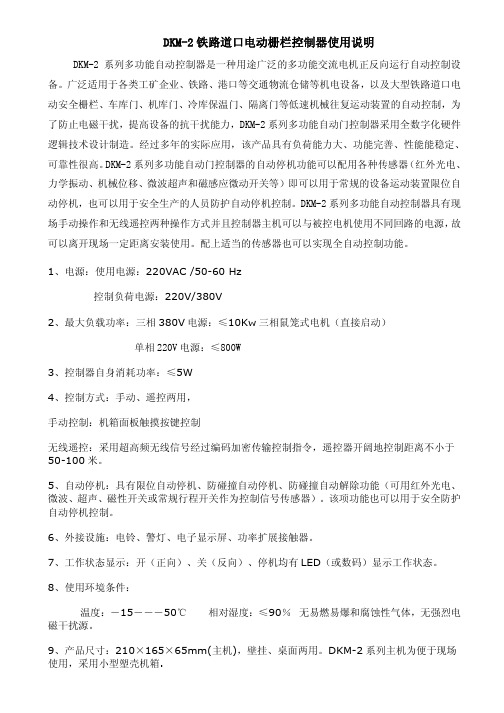
DKM-2铁路道口电动栅栏控制器使用说明DKM-2系列多功能自动控制器是一种用途广泛的多功能交流电机正反向运行自动控制设备。
广泛适用于各类工矿企业、铁路、港口等交通物流仓储等机电设备,以及大型铁路道口电动安全栅栏、车库门、机库门、冷库保温门、隔离门等低速机械往复运动装置的自动控制,为了防止电磁干扰,提高设备的抗干扰能力,DKM-2系列多功能自动门控制器采用全数字化硬件逻辑技术设计制造。
经过多年的实际应用,该产品具有负荷能力大、功能完善、性能能稳定、可靠性很高。
DKM-2系列多功能自动门控制器的自动停机功能可以配用各种传感器(红外光电、力学振动、机械位移、微波超声和磁感应微动开关等)即可以用于常规的设备运动装置限位自动停机,也可以用于安全生产的人员防护自动停机控制。
DKM-2系列多功能自动控制器具有现场手动操作和无线遥控两种操作方式并且控制器主机可以与被控电机使用不同回路的电源,故可以离开现场一定距离安装使用。
配上适当的传感器也可以实现全自动控制功能。
1、电源:使用电源:220VAC /50-60 Hz控制负荷电源:220V/380V2、最大负载功率:三相380V电源:≤10Kw三相鼠笼式电机(直接启动)单相220V电源:≤800W3、控制器自身消耗功率:≤5W4、控制方式:手动、遥控两用,手动控制:机箱面板触摸按键控制无线遥控:采用超高频无线信号经过编码加密传输控制指令,遥控器开阔地控制距离不小于50-100米。
5、自动停机:具有限位自动停机、防碰撞自动停机、防碰撞自动解除功能(可用红外光电、微波、超声、磁性开关或常规行程开关作为控制信号传感器)。
该项功能也可以用于安全防护自动停机控制。
6、外接设施:电铃、警灯、电子显示屏、功率扩展接触器。
7、工作状态显示:开(正向)、关(反向)、停机均有LED(或数码)显示工作状态。
8、使用环境条件:温度:-15―――50℃相对湿度:≤90%无易燃易爆和腐蚀性气体,无强烈电磁干扰源。
美特尔 AM-33 3 3 4 数字智能一键自动DMM操作手册安全规则说明书

AM-333 3/4 DIGITS INTELLIGENT ONESWITCH AUTO DMMOPERATION MANUALSAFETY RULESλThis meter is designed and tested in accordance with IEC publication 1010, pollution degree II and installation category (overvoltage category) III 600V.λThis meter has been tested according to the following EC Directives♦89/336/EEC (EMC of Nov., 1992, Electromagnetic Compatibility)♦73/23/EEC (Product safety law of June 11, 1979, Low Voltage Directive of February 19, 1973)λThis meter is designed to be indoor use at temperature 41°F to 104°F (5°C to 40°C) and altitude up to 2,000m.λTo ensure that the meter is used safely, follow all safety and operating instructions in this operation manual. If the meter is not used as described in this operation manual, the safety features of this meter might be impaired.λDo not use the meter if the meter or test leads look damaged, or if you suspect that the meter is not operating properly.λWhen using the probes, keep your fingers behind the finger guards on the probes.λDisconnect the live test lead before disconnecting the common test lead.λMake sure power is off before cutting, unsoldering, or breaking the circuit. Small amount of current can be dangerous.λDo not apply more than 600Vdc or 600Vac rms between a terminal and earth ground.λTo avoid electrical shock, use CAUTION when working above 60Vdc or 25Vac rms.Such voltages pose a shock hazard.λNever make measurements with the battery cover or bottom case off.λTo avoid electrical shock or damage to the meter, do not exceed the input limits. INTERNATIONAL SYMBOLSImportant informationsee manual ContinuityAC GroundDC Double insulation FEATURESλOne switch operation.λAuto polarity with engineering units annunciator.λDC volt, AC volt, Resistance(4V threshold voltage to determine V or R function)λContinuity testλAuto power off with power resumeλData holdλFull range 600V overload protectionλConform to IEC1010-1 CAT III 600V3.1 General SpecificationsDisplay: 3 3/4 digit LCD, 3999 counts with decimal point andengineering units annunciator displayPolarity:Automatic, (-) negative polarity indication.Zero adjustment:Automatic.Measuring Method:Dual slop integration A to D converter system.Over range indication:Only the “OL” is displayed.Power:Single, standard 9 volt battery NEDA 1604, JIS 006P,IEC6F22.Dimension:70 (H) x 144 (W) x 40 (D) mm.Weight:Approx. 270gm. (including batteries and packaging)3.2 Electrical SpecificationsPANEL DESCRIPTIONS1) 3 3/4 digit LCD display2) Power resume button3) ON/OFF switch4) Data hold button5) Case6) Input and common terminals WARNINGOPERATION1) When measuring voltage ensure that the instrument is not connected. Always ensure thatthe correct terminals are used for the type of measurement to be made.2) Use extreme care when measuring voltage above 50V, especially from sources wherehigh energy exists.3) Avoid making connections to “live” circuits whenever possible.4) When making current measurements ensure that the circuit is not “live” before opening itin order to connect the test leads.5) Before making resistance measurements or continuity test, ensure that the circuit undertest is de-energised.6) Extreme care should be taken when using the instrument to conjunction with a currenttransformer connected to the terminals. High voltage may be produced at the terminals if an open circuit occurs.7) Ensure that the test leads and prods are in good condition with no damage to theinsulation.8) Take care not to exceed the over-load limits as given in the specifications.9) Fuse for replacement must be of the correct type and rating.5.1 DC and AC Voltage measurement1)Connect the black test lead to the “COM” socket and red test lead to the “ ” socket.2) Connect the test prods across the source or load under measurement.5.2 Resistance measurement1) Connect the black test lead to the “COM” socket and red test lead to the “ ” socket.2) Connect the prods across the circuit to be tested.CAUTION: Ensure that the circuit to be tested is “dead”.Max. input over-load : 600V rms < 30sec.5.3 Continuity test1) Connect the black test lead to the “COM” socket and red test lead to the “ ” socket.2) Connect the prods across the circuit to be tested, if the resistance less than approx. 47Ω,buzzer will be activated.5.4 Data holdA push switch is used to hold data during measurement. Pressing the key, reading is heldand “H” appears on display. Pressing the switch again to release the hold data.Note : In auto AC/DC voltage selection, if the source under test is AC, hold function willoperative only when source under test is in continuous contact with the test probes.5.5 Auto power offThe meter will turn off automatically to extend the battery life after approx. 30 minutes withoutoperation. Resume power by pressing “P. Resume” button.6. MAINTENANCECAUTIONBEFORE ATTEMPTING BATTERY AND FUSE REMOVAL OR REPLACEMENT,DISCONNECT TEST LEADS FROM ANY ENERGISED CIRCUITS TO AVOID SHOCKHAZARD.6.1 Fitting and replacing the battery1) Ensure that the instrument is not connected to any external circuit, switch off the meterand remove the test leads from the terminals.2) Remove the screw of the back case.3) Replace the spent battery with the same type.4) Reinstate the back case, tighten and securing screw.6.2 CleaningPeriodically wipe the case with a soft damp cloth and mild household cleanser. Do not useabrasives or solvents. Ensure that no water gets inside the equipment to prevent possibleshorts and damage.FOR TECHNICAL ASSISTANCE,PLEASE CONTACT:AMPROBETel : 305-423-7500Fax : 305-423-7554Technical Support : 800-327-5060!!!。
ATD 3- 吋重量杆包说明书

Service Jack Model Number: ATD-7504Capacity Min. Height Max HeightJack Size(L x W x H) Saddle DiameterNet Weight3 Ton 5 3/8” 19 1/2” 26 3/4” x 13 3/8” x 7 1/4”4 5/16” 78 LBJack Stands Model Number: ATD-7443Capacity Min. Height Max Height Saddle Size Base (L x W) Net Weight3 Ton 11-13/16””61/5-71”1x”2/1-3B L157-11/16” x 6-15/16”Contents:Page: 1. Speci ca ons2. Safety & Warning Informa on3. 4. & 5. Setup, Opera on & Preven ve Maintenance6. Inspec on, Storage & Troubleshoo ng7. Exploded View & Replaceable Part Numbers8. Warranty Informa on------ATD7500_rev_0417Visit us at Capacity: 3TonBefore opera ng this device, be sure to read all content within this manual, ensuring that you understand the opera ng procedures, maintenance requirements and all safety warnings. The owner and/or operator shall have an understanding of the product, its opera ng characteris cs, and safety opera ng instruc ons before opera ng this device. Safety informa on shall be emphasized and understood. If the operator is not uent in English, the product and safety instruc ons shall be read to and discussed with the operator in the operator’s na ve language by the purchaser/owner or his designee, making sure that the operator comprehends their contents.Study, understand, and follow all instruc ons before operang this device. Do not exceed the rated capacity stated. Use only on hard level surfaces.This jack is to be used as a li ing device only. Immediately a er li ing, support the vehicle with appropriate means.Do not move or dolly the vehicle while it is on the jack.Li only on areas o he vehicle as speci ed by the vehicle manufacturer.No altera ons shall be made to this product.Jack Stands are designed to support stated capacity. Stands should only be used to support par al loads that consist of one end of a vehicle. Always use as a matched pair to support one end of a vehicle only.Never use jack stands to support both ends or one side of a vehicle. Use only one (1) pair of stands per vehicle. Rated capacity is per pair only .Rated capacity of this pair is 6000 lbs.Failure to heed these markings may result in serious personal injury and/or property damage.IMPORTANT: READ ALL INSTRUCTIONS BEFORE USEACTIONS TO HELP PREVENT DANGEROUS SITUATIONSCapacity: 3TonSETUPPrior to each use, visual inspec on (See Pg. 6) shall be made to the device by checking for abnormal condi ons, such as cracked welds, leaks, and damaged, loose, or missing parts.Consult the vehicle owner’s manual to determine the loca on of li points.Be sure to set the vehicle in park with the emergency brake on and wheels securely chocked.Be sure that the vehicle and the jack are on a hard, level surface.ASSEMBLYService JackAssemble the upper sec on of the two piece handle into the lower sec on, line up the holes, insert and ghten the screw.Insert the bo om end of handle into handle fork and securely ghten the bolt and washer. Ensure the handle can turn freely.Jack StandsTools Required: Hammer & Punch (not included with set)Insert the ratchet bar into the base frame with the ratchet por on of the bar aligned with the locking pawl.Move the ratchet bar to its lowest posi on by raising the locking handle, disengaging the stopper and slowing lowering the ratchet bar downward into the base.Collar lock is achieved by simply pressing the press tab (See Pg. 5) inward using the hammer and punch. This will prevent accidental loss of the ratchet bar.LIFTINGTurn the handle/release valve clockwise to the closed posi on. Do not over ghten. Posi on the jack under the speci ed li point.Begin li ing by pumping the handle up and down.Immediately a er li ing, insert safety pins into the appropriately rated jack stands and support the vehicle. NEVER support the vehicle with only the jack.Turn the handle/release valve slowly counterclockwise to lower the vehicle onto jack stands.LOWERINGTurn the handle/release valve clockwise to the closed posi on. Do not over ghten.Pump the handle up and down to li vehicle o jack stands.Remove the jack stands and safety pins. DO NOT get under or let anyone get underthe vehicle while lowering.Turn the handle/release valve slowly counterclockwise to lower the vehicle onto theground.SERVICE JACK MAINTENANCENOTICE:Use high grade hydraulic oil only.Never use brake uid,motor oil,transmission uid, turbine oil or any other uids. ISO-VG22 or equivalent hydraulic oil is recommended.Check and ReĮll OilWith the jack in the fully lowered, level posi on, if unit cover is provided, remove unitcover, then remove oil ller plug.Proper oil level should be just covering inner cylinder as seen from the oil ller plug hole.Do not over ll. Always ll with new, clean hydraulic jack oil as recommended above.Reinstall oil ller plug, then reinstall unit cover.Lubr n and CleaningPeriodically clean and lubricate all moving parts and pivot points.Air Ven t ing ProceduresWith the jack in the fully lowered posi on, release valve open, remove oil ller plug.Pump the handle rapidly several mes. Reinstall oil ller plug.Turn the handle/release valve clockwise to the closed posi on.Pump the handle un l the li arm reaches maximum height and con nue to pumpseveral mes to remove trapped air in the system.Turn the handle/release valve counterclockwise in one full turn and lower li arm to the lowest posi on. Use force on saddle if necessary.Carefully and slowly loosen oil ller plug to release pressurized air.Repeat above steps un l trapped air is completely vented.Inspect each stand before use. Ensure all parts move freely. Only apply grease to the locking handle pivot point of this product and ensure all excess grease is wiped away before stand is used. If rust appears, sand away the rust area and cover with appropriate u lity paint. Please Any service jack that appears to be damaged in any way, is found to be worn, or operates abnormally SHALL BE REMOVED FROM SERVICE UNTIL REPAIRED . It is recommended that necessary repairs be made by a manufacturer’s or supplier’s authorized repair facility if repairs are permi ed by the manufacturer or supplier.Any jack stand that appears to be damaged, is found to be worn, oroperates abnormally in any way will be removed from service and destroyed immediately.Altera onsBecause of poten al hazards associated with this type of equipment, no altera ons shall be made to the product.A achments and AdaptersOnly a achments and/or adapters supplied by the manufacturer shall be used.JACK STANDSDAMAGED EQUIPMENTRatchet BarTabCollarLocking HandleBase Safety Pinnote that there are no replacement parts available for this product.Visual inspec on shall be made before each use of the device by checking for abnormal condi ons, such as cracked welds, leaks, and damaged, loose, or missing parts.Other inspec ons shall be made per product opera ng instruc ons.These devices shall be inspected immediately if the device is believed to have beensubjected to an abnormal load or shock.It is recommended that this inspec on be made by a manufacturer’s or supplier’s authorized repair facility.Owners and/or operators should be aware that repair of this service jack may requirespecialized knowledge and facili es. It is recommended that an annual inspec on of the product be made by a manufacturer’s or supplier’s authorized repair facility and thatany defec ve parts, decals, or safety labels or signs be replaced with manufacturer’s or supplier’s speci ed parts.The service jack and jack stands should be stored in a dry loca on on a level surface.Solu onJack will not li the load. 1. Release valve not ghtlyclosed.2. Low oil level.3. Defec ve or worn internalparts.4. Load exceeds maximumallowance. 1. Tighten release valve.2. Check and add oil. Follow “Check and Re ll Oil” instruc ons on Pg.4.3. Discon nue use and contact a local repair center.4. Use a higher capacity jack.Jack will not hold the load. 1. Release valve not ghtlyclosed.2. Power unit malfunc on. 1.Tighten release valve.2. Discon nue use and contact a local repair center.Jack will not descend to minimum height, or will not remain in lowered posi on. 1. Air trapped in system.2. Reservoir oil over led.1. Vent air out of system. Follow“Air Ven ng Procedures” above.2. Check and ensure proper oil level.Follow “Check and Re ll Oil”instruc on on Pg.4.Jack will not li to max height. 1. Low oil level. 1. Check and ensure proper oil level.Follow “Check and Re ll Oil”instruc ons above.Jack will not func on properly a er tried solu on. 1. Internal malfunc on orstructural damage.1. Stop usage and contact anauthorized repair center.INSPECTIONSTORAGE TROUBLESHOOTINGItem Part Number* Descrip on Qty1LYD3D-100 Front wheel assembly 2 21el d d a S B 5.D 3D Y L 3LYD3D-101 Two Piece Handle 1 41t i n U r e w o P 6.C 3D Y L 5LYD3D-102 Handle Fork Assembly 1 6LYD3D-103 Rear Caster Assembly 2 71g n i r p S n r u t e R 9-2D Y L 8ATD-7443 3 Ton Jack Stands W/ Safety Pin 2 N/A 1l e b a L t c u d o r P L -0057D T A * Items not iden ed by part number are not available for replacement.9Safety Pin With Chain 2ZJ3H-PJ-5N/AOil Filler Plug (rubber)1LYD3F-100ONE YEAR LIMITED WARRANTYFor a period of one (1) year from your purchase date, ATD Tools Inc.will repair or replace (at its option) without charge, your ATD product if it was purchased new and the product has failed due to a defect in material or workmanship which you experienced during normal use of the product. This limited warranty is your exclusive remedy.To access the benefits of this warranty, contact ATD at 1-844-364-9922 for confirmation that this warranty applies. Thereafter, you may be advised to return the product under warranty, freight prepaid, to the ATD service department.If this ATD product is altered, abused, misused, modified, or undergoes service by an unauthorized technician, your warranty will be void. We are not responsible for damage to ornamental designs you place on this ATD product and such ornamentation should not cover any warnings or instructions or they may void the warranty. This warranty does not cover scratches, superficial dents, and other abrasions to the paint finish that occur under normal use.Subject to the law in your state:(1)Your sole and exclusive remedy is repair or replacement of the defective product asdescribed above.(2)ATD is not liable for any incidental damages, including but not limited to, lost profits andunforeseeable consequences.(3)The repair and replacement of this product under the express limited warranty describedabove is your exclusive remedy and is provided in lieu of all other warranties, express or implied. All other warranties, including implied warranties and warranties ofmerchantability or fitness for a particular purpose are disclaimed and, if disclaimer isprohibited, these warranties are limited to one year from your date of purchase of thisproduct.Some states’ laws do not allow limited durations on certain implied warranties and some states’ laws do not allow limitations on incidental or consequential damages. You should consult the law in your state to determine how your rights may vary.ATD Tools, Inc.160Enterprise DriveWentzville, MO 63385Toll Free Service Number 1-844-364-9922Visit us at 。
Atik Titan 用户手册说明书

Atik Titan User Manual Version 1.1 – August 2011Table of contents1 Introduction (3)1.1 Further information (3)2 Pack Contents (4)3 Getting to know your camera (5)3.1 Camera Parts (5)3.2 Sensor (5)3.3 Optical Window (5)3.4 Analog to Digital Converter (ADC) (5)3.5 Power Consumption (6)3.6 USB Port (6)3.7 Cooling (6)4 Technical Information Summary (7)5 Planetary (high-speed) Imaging (8)6 Declaration of Conformity (9)6.1 Disposal of the camera (9)7 Warranty (10)2Pack Contents1.Atik TitanB cable3.Car lighter type power cable4.CD with software and manuals5.Quick start guide1.ST-4 compatible autoguider port2. 2.1mm centre-positive 12V DC inputB port4.Cooling outlet5. 1.25” nosepiece with T2 (M42 x 0.75mm pitch) thread6.Cooling inletsSensorThe sensor inside your camera is a Sony ICX424 (the full technical data sheet is available at /external/ICX424AL.pdf).Optical WindowThe 2mm-thick optical window is BK7 glass with BBAR coatings on both sides to minimize unwanted reflections.Analog to Digital Converter (ADC)Your Atik Titan is equipped with a 16-bit ADC, allowing it to record subtle levels of grey which will provide you with enhanced dynamic range when capturing an image.3.5Power ConsumptionYour Atik Titan was designed to have very low power consumption, drawing only550mA at12V DC with the cooler running.It is possible to run the camera without cooling using the USB power alone.The 2.1mm centre-positive DC input is compatible with a wide range of 12V DC supplies. WARNING: If you have purchased the optional mains power adaptor, please note that it is for indoor or observatory use only.There is a risk of electric shock if the adaptor is used in damp environments or outside.If in doubt do not use the adaptor and consult a trained electrician.3.6USB PortThe Atik Titan uses a USB 2.0 high-speed interface, allowing for a full-frame download in approximately 100ms when using the supplied Artemis Capture application. Artemis Capture also provides a higher speed “preview” mode, which allows a full frame to be downloaded in approximately 50ms.3.7CoolingYour Atik Titan is equipped with a Peltier thermoelectric element which cools the camera to approximately 20º C below ambient temperature. After switching on the camera it is advisable to allow at least 2 minutes before taking images, in order to allow the temperature to stablilize.4Technical Information SummarySensor Type Sony ICX424Horizontal Resolution659 pixelsVertical Resolution494 pixelsPixel Size7.40μm x 7.40μmADC16 bitReadout Noise (Typ.)6e-Interface USB 2.0Power12v DC 0.55AMaximum Exposure Length UnlimitedMinimum Exposure Length1msCooling Thermoelectric, ΔT = -20°C Weight Approx. 350gDistance from top of T-thread to CCD a pprox 13 mmWindow thickness2mmAutoguider port pinout6Declaration of ConformityEU Declaration of Conformity.This product carries the CE Mark in accordance with the related European Directive. CE Marking is the responsibility of:Perseu, SAR. Dr. Agostinho Neto, 1D2690-576 Sta Iria da AzoiaPortugalCritical Applications.This product is not designed for any “critical applications”. “Critical applications” means life support systems, medical applications , connections to medical devices, commercial transportations, nuclear facilities or systems or any other applications where product failure could lead to injury to persons or loss of life or catastrophic property damage.This product is not a toy.This is a class A product. In a domestic environment this product may cause radio interference in which case the user may be required to take appropriate measures.6.1Disposal of the cameraWhen no longer required do not dispose of this electronic device with general household waste. To minimise pollution and protect the environment the camera should be recycled. Local recycling drop off points available under the Waste from Electrical and Electronic Equipment (WEEE) regulations which will accept the camera. For further information contact Perseu SA at the above address, or the shop from which the camera was bought.7WarrantyThe equipment is guaranteed against defective design,manufacture or materials for a period of one year from the date of purchase.This means that Atik Cameras will repair or replace the equipment at its sole option, at no charge to the purchaser for parts or for labour, if the fault is reported within the guarantee period, provided however that Atik Cameras is able to duplicate the defect or problem at its facilities. This warranty does not apply to damage that occurred as a result of abuse or misuse, abnormal service or handling, damage which may have been caused either directly or indirectly by another product, or if the equipment has been altered or modified in any way, or if the damage was caused by repairs or service provided or attempted by anyone other than Atik Cameras. This warranty does not include or provide for incidental or consequential damages.To exercise your rights under this warranty, you must return the equipment to the dealer from whom it was purchased together with proof of purchase and a clear description of the fault. If it’s not possible to return the equipment to your dealer,you should contact Atik Cameras.Equipment returned to Atik Cameras must be sent in appropriate packaging and at your expense (insurance is recommended),together with proof of purchase,a return address and a clear description of the fault.This does not affect your statutory rights.。
艾特汀自动转换器与艾特3S.550 UPS说明书
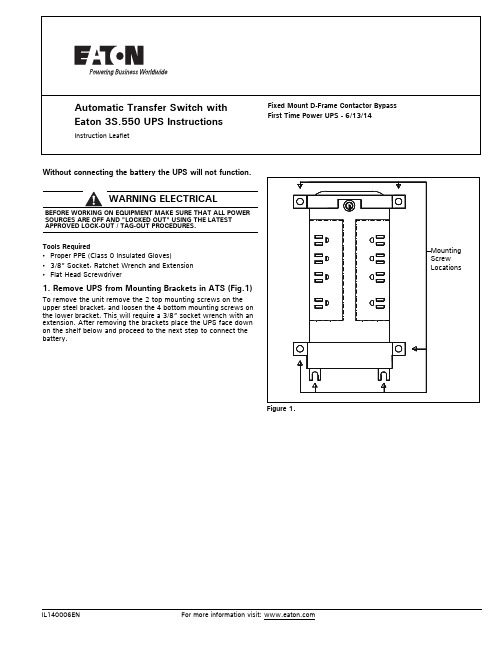
IL140006EN For more information visit: Instruction LeafletPage2Effective: June 2014Fixed Mount D-Frame Contactor BypassFirst Time Power UPS - 6/13/14 2. Connect the Battery (Figure 2)Note: Check the battery recharge date on the shipping carton label.Note: If the date has passed and the batteries were never recharged, donot use the UPS. Contact your service representative. If the UPS requiresany type of transportation, the internal UPS battery MUST be discon-nected.For safety, the UPS is shipped with the battery wires discon-nected. The UPS will not run until the wires are connected to thebattery terminals.Figure 2.1. Turn the UPS over and peel off thetape with the rubber spacer.2. Slide the battery cover off the UPS.3. Pull out the battery and connect thebattery wires firmly to the batteryterminals; red to positive (+), blackto negative (-).4. Insert the battery back into the compartment.5. Slide the battery cover on the UPSuntil the release tab locks into place.For more information visit: IL140006ENIL140006EN For more information visit: Instruction LeafletEffective: June 2014Page 3Fixed Mount D-Frame Contactor Bypass First Time Power UPS - 6/13/143. Re-Install UPS(Figure3)After connecting the battery and securing the back cover to the UPS re-mount the ups in the standard location with the two steel brackets and 6 screws that were removed earlier. After mounting the UPS plug the power cord into one of the “Battery Backup Plus Surge Protection” outlets. After everything has been reconnected press the power button to power up your UPS unit. You have now successfully set up your UPS Unit. For more information See the User’s Guide located in your documentation Packet on inside of Lower door.Figure 3.“Battery Backup Plus”Power ButtonInstruction LeafletPage 4Effective: June 2014Fixed Mount D-Frame Contactor BypassFirst Time Power UPS - 6/13/14© 2014 EatonAll Rights Reserved Printed in USAPublication No. IL140006EN/TBG1156June 2014This instruction leaflet is published solely for information purposes and should not be considered all-inclusive. If further information is required, you should consult Eaton.Sale of the product(s) shown in this literature is subject to terms and conditions outlined in appropriate Eaton selling policies or other contractual agreements between the parties. This literature is not intended to and does not enlarge or add to any such con-tract. The sole source governing the rights and remedies of any purchaser of this equipment is the contract between the pur-chaser and Eaton.NO WARRANTIES, EXPRESSED OR IMPLIED, INCLUDING WAR-RANTIES OF FITNESS FOR A PARTICULAR PURPOSE OR MER-CHANTABILITY, OR WARRANTIES ARISING FROM COURSE OF DEALING OR USAGE OF TRADE, ARE MADE REGARDING THE INFORMATION, RECOMMENDATIONS AND DESCRIPTIONS CON-TAINED HEREIN. In no event will Eaton be responsible to the pur-chaser or user in contract, in tort (including negligence), strict liability or otherwise for any special, indirect, incidental or conse-quential damage or loss whatsoever, including but not limited to damage or loss of use of equipment, plant or power system, cost of capital, loss of power, additional expenses in the use of exist-ing power facilities, or claims against the purchaser or user by its customers resulting from the use of the information, recommen-dations and description contained herein.CSA is a registered trademark of the Canadian Standards Associa-tion. National Electrical Code and NEC are registered trademarks of the National Fire Protection Association, Quincy, Mass. NEMA is the registered trademark and service mark of the National Elec-trical Manufacturers Association. Uniform Building Code (UBC) is a trademark of the International Conference of Building Officials (ICBO). UL is a federally registered trademark of the Underwriters Laboratories Inc.EatonElectrical Group1000 Eaton Boulevard Cleveland, OH 45122United States877-ETN CARE (877-386-2273)。
艾特顿过载保护设备用户说明书

Eaton 278467Eaton Moeller® series ZB Overload relay, ZB150, Ir= 25 - 35 A, 1 N/O, 1 N/C, Separate mounting, IP00General specificationsEaton Moeller® series ZB Thermal overload relay278467134 mm121 mm 118 mm 1.394 kgUL 60947-4-1 CSA File No.: 012528 CSA-C22.2 No. 60947-4-1-14 IEC/EN 60947 UL File No.: E29184 CECSA Class No.: 3211-03 VDE 0660 IEC/EN 60947-4-1 ULUL Category Control No.: NKCR CSAZB150-35/KKProduct NameCatalog Number Product Length/Depth Product Height Product Width Product Weight Certifications Model CodeReset pushbutton manual/autoPhase-failure sensitivity (according to IEC/EN 60947, VDE 0660 Part 102) Test/off button Trip-free release-25 °C55 °C-25 °C40 °C CLASS 10 A Damp heat, constant, to IEC 60068-2-78 Damp heat, cyclic, to IEC 60068-2-30IP00ZB150Separate mounting Direct attachment25 A35 AIII3Finger and back-of-hand proof, Protection against direct contact when actuated from front (EN 50274)FeaturesAmbient operating temperature - min Ambient operating temperature - max Ambient operating temperature (enclosed) - min Ambient operating temperature (enclosed) - max Class Climatic proofingDegree of protection Frame size Mounting method Overload release current setting - min Overload release current setting - max Overvoltage category Pollution degree Product category ProtectionAccessoriesOverload relay ZB up to 150 A6000 V AC4000 V (auxiliary and control circuits)10 g, Mechanical, Sinusoidal, Shock duration 10 ms Branch circuits, (UL/CSA)Continuous≤ 0.25 %/K, residual error for T > 40°1 x (0.75 - 2.5) mm², Control circuit cables1 x (4 - 70) mm², Main cables2 x (4 - 70) mm², Main cables2 x (0.75 - 2.5) mm², Control circuit cables1 x (4 - 16) mm², Main cables2 x (4 - 16) mm², Main cables2 x (0.75 - 4) mm², Control circuit cables1 x (0.75 - 4) mm², Control circuit cables3/0, Main cables2 x (18 - 14), Control circuit cables1 x (16 - 70) mm², Main cables2 x (16 - 70) mm², Main cables24 mm8 mmM10, Terminal screw, Main cables5 mm AF, Hexagon socket-head spanner, Terminal screw, Main cablesM3.5, Terminal screw, Control circuit cables1 x 6 mm, Terminal screw, Control circuit cables, Standard screwdriver2, Terminal screw, Control circuit cables, Pozidriv screwdriver1.2 Nm, Screw terminals, Control circuit cables10 Nm, Screw terminals, Main cables6 A 5 kA, SCCR (UL/CSA)60 A Class J, max. Fuse, SCCR (UL/CSA)Rated impulse withstand voltage (Uimp)Shock resistanceSuitable forTemperature compensation Terminal capacity (flexible with ferrule)Terminal capacity (solid)Terminal capacity (solid/stranded AWG) Terminal capacity (stranded)Stripping length (main cable)Stripping length (control circuit cable) Screw sizeScrewdriver sizeTightening torqueConventional thermal current ith of auxiliary contacts (1-pole, open)Rated operational current (Ie) at AC-15, 120 V Short-circuit current rating (basic rating) Short-circuit protection rating1.5 A1.5 A0.9 A0.4 A0.2 A0.9 A0.75 A1000 V440 V, Between auxiliary contacts and main contacts, According to EN 61140240 V AC, Between auxiliary contacts, According to EN 61140 440 V AC, Between main circuits, According to EN 61140B600 at opposite polarity, AC operated (UL/CSA)R300, DC operated (UL/CSA)B300 at opposite polarity, AC operated (UL/CSA)600 VAC 100 A gG/gL, Fuse, Type “2” coordination125 A gG/gL, Fuse, Type “1” coordinationMax. 6 A gG/gL, fuse, Without welding, Auxiliary and control circuits111121 W0 W7 W35 A0 WMeets the product standard's requirements.Meets the product standard's requirements.Meets the product standard's requirements.Meets the product standard's requirements.Rated operational current (Ie) at AC-15, 220 V, 230 V, 240 V Rated operational current (Ie) at AC-15, 380 V, 400 V, 415 V Rated operational current (Ie) at DC-13, 110 VRated operational current (Ie) at DC-13, 220 V, 230 V Rated operational current (Ie) at DC-13, 24 VRated operational current (Ie) at DC-13, 60 VRated operational voltage (Ue) - maxSafe isolationSwitching capacity (auxiliary contacts, pilot duty) Voltage rating - max Number of auxiliary contacts (change-over contacts)Number of auxiliary contacts (normally closed contacts) Number of auxiliary contacts (normally open contacts) Number of contacts (normally closed contacts)Number of contacts (normally open contacts)Equipment heat dissipation, current-dependent PvidHeat dissipation capacity PdissHeat dissipation per pole, current-dependent PvidRated operational current for specified heat dissipation (In) Static heat dissipation, non-current-dependent Pvs10.2.2 Corrosion resistance10.2.3.1 Verification of thermal stability of enclosures10.2.3.2 Verification of resistance of insulating materials to normal heat10.2.3.3 Resist. of insul. mat. to abnormal heat/fire by internal elect. effectsMeets the product standard's requirements.Does not apply, since the entire switchgear needs to be evaluated.Does not apply, since the entire switchgear needs to be evaluated.Meets the product standard's requirements.Does not apply, since the entire switchgear needs to be evaluated.Meets the product standard's requirements.Does not apply, since the entire switchgear needs to be evaluated.Does not apply, since the entire switchgear needs to be evaluated.Is the panel builder's responsibility.Is the panel builder's responsibility.Is the panel builder's responsibility.Is the panel builder's responsibility.Is the panel builder's responsibility.The panel builder is responsible for the temperature rise calculation. Eaton will provide heat dissipation data for the devices.Is the panel builder's responsibility. The specifications for the switchgear must be observed.eaton-tripping-zb-overload-relay-characteristic-curve.epsDA-DC-00004845.pdfDA-DC-00004855.pdfDA-CE-ETN.ZB150-35_KKIL03407006ZDA-CD-zb150_kkDA-CS-zb150_kkeaton-tripping-devices-overload-relay-zb-overload-relay-dimensions-007.epseaton-tripping-devices-overload-relay-zb-overload-relay-3d-drawing-005.eps10.2.4 Resistance to ultra-violet (UV) radiation10.2.5 Lifting10.2.6 Mechanical impact10.2.7 Inscriptions10.3 Degree of protection of assemblies10.4 Clearances and creepage distances10.5 Protection against electric shock10.6 Incorporation of switching devices and components 10.7 Internal electrical circuits and connections10.8 Connections for external conductors10.9.2 Power-frequency electric strength10.9.3 Impulse withstand voltage10.9.4 Testing of enclosures made of insulating material 10.10 Temperature rise10.11 Short-circuit rating10.12 Electromagnetic compatibility Characteristic curve Declarations of conformity eCAD model Installeringsinstruksjoner mCAD modelTegningerEaton Corporation plc Eaton House30 Pembroke Road Dublin 4, Ireland © 2023 Eaton. Med enerett. Eaton is a registered trademark.All other trademarks areproperty of their respectiveowners./socialmediaIs the panel builder's responsibility. The specifications for the switchgear must be observed.The device meets the requirements, provided the information in the instruction leaflet (IL) is observed.10.13 Mechanical function。
爱斯顿 GLH3500AAM 系列 G 型电路保护器说明说明书

Eaton GLH3500AAMEaton Series G molded case circuit breaker, LG-frame, GL, Adjustable thermal, adjustable magnetic trip, Three-pole, 500A, 600 Vac, 100 kAIC at 240 Vac, 70 kAIC at 415 Vac, 65 kAIC at 480 Vac, 35 kAIC at 600 Vac, Line/load end caps, MetricGeneral specificationsEaton Series G complete molded case circuit breakerGLH3500AAM 7821169084865.48 in 5.48 in 5.48 in 14.5 lb Eaton Selling Policy 25-000, one (1) year from the date of installation of the Product or eighteen (18) months from the date of shipment of the Product, whichever occurs first.IEC Rated Product NameCatalog Number UPCProduct Length/Depth Product Height Product Width Product Weight WarrantyCertificationsMetric100 kAIC at 240 Vac70 kAIC at 415 Vac65 kAIC at 480 Vac35 kAIC at 600 VacLGGLComplete breakerLine and load end caps600 Vac500 AAdjustable thermal, adjustable magnetic Three-pole Application of Tap Rules to Molded Case Breaker Terminals Application of Multi-Wire Terminals for Molded Case Circuit BreakersMulti-wire lugs product aidMotor protection circuit breakers product aidPower metering and monitoring with Modbus RTU product aidCurrent limiting molded case circuit breaker module product aidSeries G MCCB quick selectorCircuit breaker motor operators product aidPlug-in adapters for molded case circuit breakers product aid Comprehensive circuit protection for control panel applications StrandAble terminals product aidHigh performance operating handles for Series G circuit breakers product aidCurrent limiting molded case circuit breaker module for series G, JG and CLMolded case circuit breakers providing higher levels of selective coordination product aidBreaker service centersMolded case circuit breakers catalogEaton's Volume 4—Circuit ProtectionNG and ND-Frame molded case circuit breakersMOEM MCCB product selection guideEaton Specification Sheet - GLH3500AAMMounting hardware Interrupt ratingFrameCircuit breaker type Circuit breaker frame type TerminalsVoltage rating Amperage RatingTrip TypeNumber of poles Application notesBrochuresCatalogsSpecifications and datasheetsEaton Corporation plc Eaton House30 Pembroke Road Dublin 4, Ireland © 2023 Eaton. All Rights Reserved. Eaton is a registered trademark.All other trademarks areproperty of their respectiveowners./socialmedia。
Schneider Electric ATV61 ATV71 湿度防腐封闭式装置安装配件说明书

Mounting and fixing accessory
Mounting kit
ATV61HC25N4 ATV71HC31Y without braking unit ATV71HC28N4D without braking unit ATV71HC28N4 without braking unit ATV71HC25Y without braking unit ATV71HC25N4D without braking unit ATV71HC25N4 without braking unit ATV71HC20Y without braking unit ATV71HC20N4D without braking unit ATV71HC20N4 without braking unit ATV61HC40Y without braking unit ATV61HC31Y without braking unit ATV61HC31N4D without braking unit ATV61HC31N4 without braking unit ATV61HC25Y without braking unit ATV61HC25N4D without braking unit
4.7 kg
Dust and damp proof
Not Green Premium product Compliant - since 1002 - Schneider Electric declaration of conformity
Aug 18, 2016
- 1、下载文档前请自行甄别文档内容的完整性,平台不提供额外的编辑、内容补充、找答案等附加服务。
- 2、"仅部分预览"的文档,不可在线预览部分如存在完整性等问题,可反馈申请退款(可完整预览的文档不适用该条件!)。
- 3、如文档侵犯您的权益,请联系客服反馈,我们会尽快为您处理(人工客服工作时间:9:00-18:30)。
输出方式,J-静态输出,D-动态输出 共补数量 分补组数 显示方式:M-LED显示,H-汉字液晶显示 智能无功功率补偿控制器 合肥艾通自动化工程有限公司
3.功能特点
◆ 采用三相电容△+单相电容 Y 接法,三相均需补偿时,三相电容优先投入, 某相需补偿时投入相应的单相电容;
◆ 使用一里一外双“看门狗”,应用空闲模式和数据多重备份技术,控制器具有极 高的抗干扰能力;
3-H
SET
合肥艾通自动化工程有限公司
U
U
*CI
CI
8.背板端子图
IB* IB IA* IA UN UC A+
K15 K16 K17 K18 K19 K20 UA UB B-
K1 K3 K5 K7 K9 K11 K13 K2 K4 K6 K8 K10 K12 K14
*CI CI
IB* IB IA* IA UN UC A+ K15 K16 K17 K18 K19 K20 UA UB B-
+12V K1 K3 K5 K7 K9 K11 K13 +12V K2 K4 K6 K8 K10 K12 K14
9.接线图
20路及以下混合补偿控制接线一览表
(共补路数和分补路数由控制器面板按键设定)
输出
规格(G---共补,F---分补)
路数
控制
20G
17G 1F
14G 11G 2F 3F
8G 4F
输出
规格(G---共补,F---分补)
路数
控制
20G 17G 14G 11G 8G 5G 2G 15G 12G 9G 6G 1F 2F 3F 4F 5F 6F 1F 2F 3F
3G 4FLeabharlann 5F12G9G 1F
6G 3G 2F 3F
4F
端口
K1 G1 A1 A1 A1 A1 A1 A1 G1 A1 A1 A1 A1 A1 G1 A1 A1 A1 A1 K2 G2 B1 B1 B1 B1 B1 B1 G2 B1 B1 B1 B1 B1 G2 B1 B1 B1 B1 K3 G3 C1 C1 C1 C1 C1 C1 G3 C1 C1 C1 C1 C1 G3 C1 C1 C1 C1 K4 G4 G1 A2 A2 A2 A2 A2 G4 G1 A2 A2 A2 A2 G4 G1 A2 A2 A2 K5 G5 G2 B2 B2 B2 B2 B2 G5 G2 B2 B2 B2 B2 G5 G2 B2 B2 B2 K6 G6 G3 C2 C2 C2 C2 C2 G6 G3 C2 C2 C2 C2 G6 G3 C2 C2 C2 K7 G7 G4 G1 A3 A3 A3 A3 G7 G4 G1 A3 A3 A3 G7 G4 G1 A3 A3 K8 G8 G5 G2 B3 B3 B3 B3 G8 G5 G2 B3 B3 B3 G8 G5 G2 B3 B3 K9 G9 G6 G3 C3 C3 C3 C3 G9 G6 G3 C3 C3 C3 G9 G6 G3 C3 C3 K10 G10 G7 G4 G1 A4 A4 A4 G10 G7 G4 G1 A4 A4 G10 G7 G4 G1 A4 K11 G11 G8 G5 G2 B4 B4 B4 G11 G8 G5 G2 B4 B4 G11 G8 G5 G2 B4 K12 G12 G9 G6 G3 C4 C4 C4 G12 G9 G6 G3 C4 C4 G12 G9 G6 G3 C4 K13 G13 G10 G7 G4 G1 A5 A5 G13 G10 G7 G4 G1 A5 K14 G14 G11 G8 G5 G2 B5 B5 G14 G11 G8 G5 G2 B5 K15 G15 G12 G9 G6 G3 C5 C5 G15 G12 G9 G6 G3 C5 K16 G16 G13 G10 G7 G4 G1 A6 K17 G17 G14 G11 G8 G5 G2 B6 K18 G18 G15 G12 G9 G6 G3 C6
B1 B1 B1 B1
K3 G3 C1 C1 C1 C1 C1 C1 G3 C1 C1 C1 C1 C1 G3 C1 C1 C1 C1
K4 G4 G1 A2 A2 A2 A2 A2 G4 G1 A2 A2 A2 A2 G4 G1 A2 A2 A2
K5 G5 G2 B2 B2 B2 B2 B2 G5 G2 B2 B2 B2 B2 G5 G2 B2 B2 B2
5G 5F
2G 6F
15G
12G 1F
9G 2F
6G 3F
3G 4F
5F
12G
9G 1F
6G 3G 2F 3F
4F
端口
K1 G1 A1 A1 A1 A1 A1 A1 G1 A1 A1 A1 A1 A1 G1 A1 A1 A1 A1
K2 G2 B1 B1 B1 B1 B1 B1 G2 B1 B1 B1 B1 B1
K20 G20 G17 G14 G11 G8 G5 G2
注:其它规格的共补路数和分补路数其输出端口以此类推!
动态输出接线图
注1:当接触器线包电压为AC220V时,P接N线; 当接触器线包电压为AC380V时,P接B相或C相。
20路及以下混合补偿控制接线一览表
(共补路数和分补路数由控制器面板按键设定)
4.主要技术参数
◆ 额定工作电压:AC220V±20%; ◆ 额定工作频率:45~55Hz; ◆ 输出回路: 共补最大 20 路; 共补+分补(△+ Y):2+3×6,5+3×5,8+3×4,11+3×3,14+3×2,17+3×1; ◆ 电容器组输出编码:
循环投切 1:1:1:1:1…:1 1:2:2:2:2…:2 1:2:4:4:4…:4 1:2:4:8:8…:8 1:1:2:2:2…:2 1:1:2:4:4…:4 1:1:2:4:8…:8 等共十二种; ◆ 额定工作电流:5A; ◆ 灵敏度:50 mA; ◆ 电流输入阻抗<0.1Ω; ◆ 静态补偿继电器触点容量:每路 5A,AC250V; ◆ 动态补偿直流输出容量:每路 DC12V, 50mA; ◆ 安装方式:嵌入式; ◆ 开孔尺寸:113×113; ◆ 防护等级:IP40; ◆ 整机功耗:<10VA。
输出指示
B C
输 出 指 示
A
Pr--编码预置 (ABC灯全亮共补,循环亮分补) C--第一只电容预置 (ABC灯全亮共补,循环亮分补) PF--基波/谐波设置
目标COSФ
分补回路
过压门限
自动/手动
延时时间
共补回路
CT倍率
PF
V
I
P
Q
Hz
电参数显示
相位
SET
选择
合肥艾通自动化工程有限公司
AT-DKG- F11G/J无功功率混合补偿控制器
AT-DKG-M 智能无功功率 混合补偿控制器
使用手册
合肥艾通自动化工程有限公司
GKD-TA F G
1.概述
◆ AT-DKG 系列智能无功功率混合补偿控制器和 AT-FHK 系列智能复合开关完 全满足自动过零投切、分相补偿的要求,适应于静态补偿和动态补偿。
◆ AT-DKG 系列智能无功功率混合补偿控制器同时取样三相电压、三相电流信 号,提供多种共补+分补补偿方案和多种投切编码方案。
K9 G9 G6 G3 C3 C3 C3 C3 G9 G6 G3 C3 C3 C3 G9 G6 G3 C3 C3
K10 G10 G7 G4 G1 A4 A4 A4 G10 G7 G4 G1 A4 A4 G10 G7 G4 G1 A4
K11 G11 G8 G5 G2 B4 B4 B4 G11 G8 G5 G2 B4 B4 G11 G8 G5 G2 B4
11.问题答疑:
◆分补容量如何选择? 分相补偿容量一般选择为总补偿容量的 30%。 ◆为什么手动不能投入? a.检查控制器是否处在手动运行状态; b.检查手动相位选择状态; c.检查共分补输出回路参数预置是否正确 ?如当用户将共补输出回路参数预置成 0 的 话,共补电容器组就不能手动或自动投入,如当用户将分补输出回路参数预置成 0 的 话,任意分补电容器组就不能手动或自动投入。 ◆为什么功率因数总显示 1.00 不能自动投入? 当电流信号小于 50mA 时,对应相位的功率因数就显示 1.00,表示电流信号小于控制 器的最小检测值,当信号电流超过此门限值时,控制器将会立即自动工作。 ◆为什么控制器没有投入一组电容器功率因数却为负值(超前 )? a.检查电压电流信号取样相位是否正确?
K19 G19 G16 G13 G10 G7 G4 G1 K20 G20 G17 G14 G11 G8 G5 G2
注2:其它规格的共补路数和分补路数其输出端口以此类推!
静态输出接线图
10.操作说明:
本控制器共有 4 个按键,分别为“SET”、“▲”、“▼”和“相位选择”键; 10.1 正常上电状态下,显示三相功率因数,并为自动运行状态(自动/手动灯亮),此 时按“相位选择”键可分别显示 A、B、C 相功率因数(A、B、C 指示灯分别亮,A、B、 C 指示灯全亮为三相), 按“▲”、 “▼”键可选择显示电压(V)、电流(I) 、有功功率(P) 、 无功功率(Q) 、电网频率(Hz)等电参数, 按“相位选择”键可分别显示 A、B、C 相相 应的电参数, 此时对应的电参数指示灯闪烁; 10.2 连续按“SET”键 3 秒进入设定参数状态,可分别设定“自动/手动”(自动 AOn、 手动 AOFF)、“目标 COSΦ”、“延时时间”、“分补回路数”、“共补回路数”、“编码预置” (Pr 标志,ABC 灯全亮共补,分别亮分补)、“电容容量预置”(C 标志,ABC 灯全亮共补, 分别亮分补)、“基波/谐波设置”(PF 标志;0 基波,1 谐波)、“有功/无功象限设置(pq 标志), “通讯地址”(A 闪烁),“通讯波特率”(四位同时闪烁),对应的设定指示灯 亮或有对应的显示标志;“有功/无功象限设置”为 2 选择两象限,为 4 选择四象限; 选 择两象限可自动识别电流极性,缺点是当无功功率落在第三象限时不能正确投切; 10.3 设定参数状态下, 按“▲”、“▼”键可对相应的设置参数进行加减, 连续按“▲”、 “▼”键 3 秒可对相应的设置参数进行快速加减; 10.4 循环设置结束,自动存储设置参数或连续按“SET”键 3 秒存储设置参数; 10.5 在手动状态下(自动/手动灯灭), 按“▲”、“▼”键可进行电容投切, 按“相位选 择”键可进行共补投切和分补投切。