自动化圆片落料生产线
400T自动落料线的应用
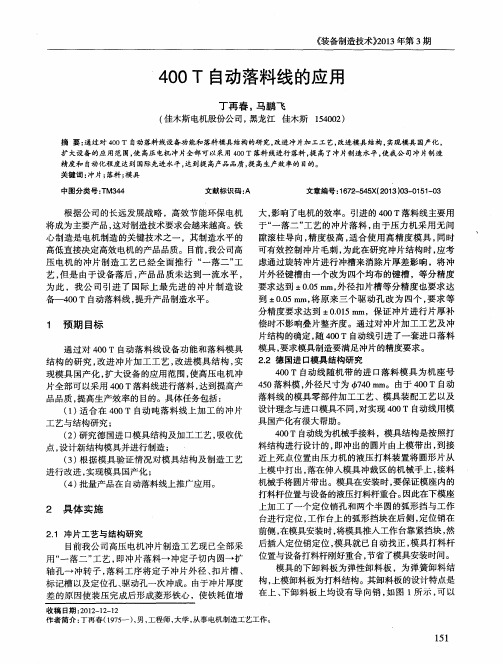
4 ( 佳木斯 电机股份公 司, 黑龙江 佳木斯 1 5 4 0 0 2 )
摘 要: 通过 对 4 0 0T 自动落料 线设 备功能和 落料模具结构 的研究 , 改进 冲片加工工 艺, 改进模具 结构 , 实现模具 国产化 ,
扩 大设备 的应 用范 围, 使 高压电机冲片全部可 以采 用 4 0 0T落料 线进行 落料 , 提 高了冲片制造 水平 , 使我公 司冲片制造
精度和 自动化程度 达到 国际先进水平 , 达到提 高产品品质 , 提 高生产效率的 目的。
关键词 : 冲片; 落料 ; 模 具
中图分类号 : T M3 4 4
大, 影响了电机的效率。引进 的 4 0 0 T 落料线主要用 于“ 一落二 ” 工艺的冲片落料 , 由于压力机采用无 间 隙滚柱导 向, 精度极高 , 适合使用 高精 度模 具 , 同时 可有效控制冲片毛刺 , 为此在研究冲片结构时 , 应考 虑通过旋转冲片进行冲槽来消除片厚差影响 ,将 冲 片外径键槽 由一个改为四个均布的键槽 ,等分精度 要求达到 ±0 . 0 5 I T t I n , 外径扣片槽等分精度也要求达 到± 0 . 0 5 m m, 将原来 三个 驱动孑 L 改为 四个 , 要求 等 分精度要 求达到 士 0 . 0 1 5 m i l l ,保证 冲片进行片厚补 偿时不影 响叠片整齐度。通过对冲片加工工艺及冲 片结构 的确定 , 随4 0 0 T自动线引进 了一套进 口落料 模具 , 要求模具制造要满足冲片的精度要求 。 2 . 2 德 国进 口模具 结构 研 究 4 0 0 T自动线随机带 的进 口落料模具为机座 号 4 5 0 落料模 , 外径尺寸为 t h 7 4 0m m 。由于 4 0 0 T自动 落料 线 的模具 零 部 件加 工 工 艺 、模 具装 配 工 艺 以及 设计理念与进口模具不同, 对实现 4 ' 0 0 T自动线用模 具 国产 化有很 大 帮助 。 4 0 0 T自动线为机械手接料 , 模具结构是按照打 料结构进行设计 的, 即冲出的圆片 由上模带出 , 到接 近上死点位置由压力机 的液压 打料装置将 圆形片从 上模中打 出, 落在伸入模具冲裁 区的机械手上 , 接料 机械手 将 圆片带 出。模具 在安 装 时 , 要 保证 模 座 内的 打料杆位置与设备的液压打料杆重合 。 因此在下模座 上加 工 了一 个 定位 销 孔 和两 个 半 圆 的弧形 挡 与工 作 台进 行定 位 , 工作 台上 的弧 形挡 块 在后 侧 , 定位 销 在 前侧 , 在模具安装时 , 将模具推人工作 台靠紧挡块 , 然 后插入定位销定位 , 模具就 已自动找正 , 模具打料杆 位置与设备打料杆刚好重合 , 节省了模具安装时间。 模具 的下卸料板为弹性卸料板 ,为弹簧卸料结 构, 上模卸料板为打料结构。其卸料板的设计特点是 在上 、 下 卸 料 板 上 均设 有 导 向销 , 如图 l 所示 , 可 以
SMT自动化生产线方案

SMT自动化生产线方案引言概述:SMT(表面贴装技术)自动化生产线方案是一种高效、精确的电子组装解决方案,它在电子创造业中得到了广泛应用。
本文将介绍SMT自动化生产线方案的五个主要方面,包括设备选型、生产流程、质量控制、人机交互以及未来发展趋势。
正文内容:1. 设备选型1.1 设备类型:选用适合生产需求的贴装机、回流炉、自动输送设备等。
1.2 设备性能:考虑设备的速度、准确性、稳定性等指标,以满足高质量的生产要求。
1.3 设备配置:根据产品特性和生产规模,选择合适的设备配置方案,如单线、双线或者多线生产。
2. 生产流程2.1 材料准备:确保原材料的质量和数量满足生产需求。
2.2 贴装过程:包括自动上料、贴装、焊接等步骤,保证高效、准确的组装。
2.3 检测与调试:通过自动检测设备对产品进行质量检测和调试,确保产品质量。
2.4 包装与出货:将组装好的产品进行包装,并进行出货准备。
3. 质量控制3.1 质量检测:使用自动光学检测设备对贴装过程中的错误进行实时检测和纠正。
3.2 过程监控:通过数据采集和分析,实时监控生产过程,及时发现和解决问题。
3.3 质量管理:建立完善的质量管理体系,包括质量标准、检验流程、异常处理等。
4. 人机交互4.1 操作界面:设计直观、易用的操作界面,提高操作人员的工作效率。
4.2 报警与提示:设置合理的报警和提示机制,及时提醒操作人员处理异常情况。
4.3 数据分析与反馈:通过数据分析和报表生成,为管理层提供决策参考。
5. 未来发展趋势5.1 智能化:引入人工智能技术,实现自动化程度更高的生产线。
5.2 灵便性:提高设备的灵便性,适应多品种、小批量生产的需求。
5.3 网络化:实现设备之间的信息共享和远程监控,提高生产效率和管理水平。
总结:综上所述,SMT自动化生产线方案是电子创造业中一种高效、精确的电子组装解决方案。
通过合理的设备选型、优化的生产流程、严格的质量控制、人机交互的改进以及未来发展趋势的把握,可以提高生产效率、降低成本、提升产品质量,为电子创造企业带来更大的竞争优势。
SMT自动化生产线方案
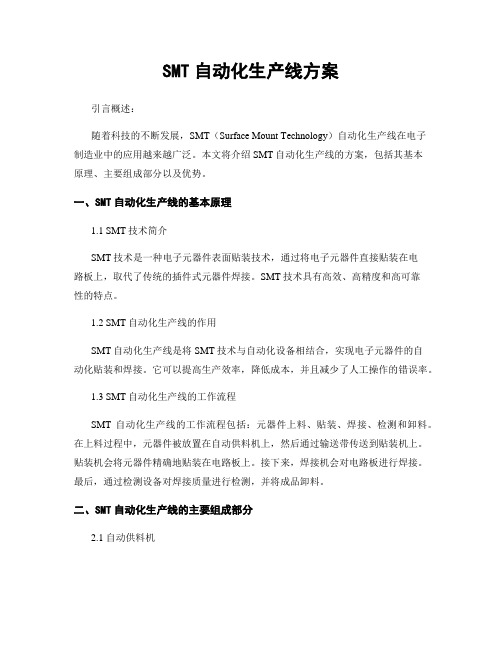
SMT自动化生产线方案引言概述:随着科技的不断发展,SMT(Surface Mount Technology)自动化生产线在电子制造业中的应用越来越广泛。
本文将介绍SMT自动化生产线的方案,包括其基本原理、主要组成部分以及优势。
一、SMT自动化生产线的基本原理1.1 SMT技术简介SMT技术是一种电子元器件表面贴装技术,通过将电子元器件直接贴装在电路板上,取代了传统的插件式元器件焊接。
SMT技术具有高效、高精度和高可靠性的特点。
1.2 SMT自动化生产线的作用SMT自动化生产线是将SMT技术与自动化设备相结合,实现电子元器件的自动化贴装和焊接。
它可以提高生产效率,降低成本,并且减少了人工操作的错误率。
1.3 SMT自动化生产线的工作流程SMT自动化生产线的工作流程包括:元器件上料、贴装、焊接、检测和卸料。
在上料过程中,元器件被放置在自动供料机上,然后通过输送带传送到贴装机上。
贴装机会将元器件精确地贴装在电路板上。
接下来,焊接机会对电路板进行焊接。
最后,通过检测设备对焊接质量进行检测,并将成品卸料。
二、SMT自动化生产线的主要组成部分2.1 自动供料机自动供料机主要用于将元器件从料盘或者卷筒中取出,并将其放置在输送带上。
它可以实现高速、高效的元器件上料。
2.2 贴装机贴装机是SMT自动化生产线中最关键的设备之一。
它能够根据电路板上的元器件位置信息,将元器件精确地贴装在电路板上。
贴装机具有高速度、高精度和高稳定性的特点。
2.3 焊接机焊接机主要用于对贴装完成的电路板进行焊接。
它可以通过热风或者红外线加热,将焊接剂熔化,实现元器件与电路板的连接。
三、SMT自动化生产线的优势3.1 提高生产效率SMT自动化生产线可以实现高速度、高精度的贴装和焊接,大大提高了生产效率。
相比传统的手工操作,它可以节省大量的时间和人力资源。
3.2 降低生产成本SMT自动化生产线可以减少人工操作的错误率,降低了产品的不良率。
同时,它还可以减少人工操作所需的工作空间,降低了生产成本。
自动落料线
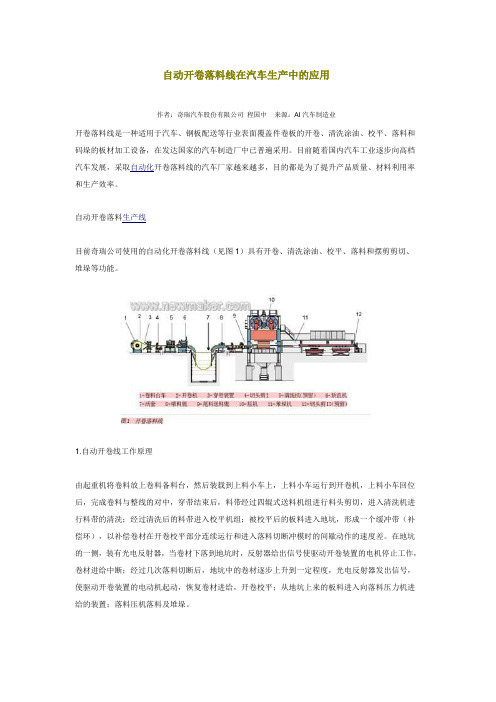
自动开卷落料线在汽车生产中的应用作者:奇瑞汽车股份有限公司程国中来源:AI汽车制造业开卷落料线是一种适用于汽车、钢板配送等行业表面覆盖件卷板的开卷、清洗涂油、校平、落料和码垛的板材加工设备,在发达国家的汽车制造厂中已普遍采用。
目前随着国内汽车工业逐步向高档汽车发展,采取自动化开卷落料线的汽车厂家越来越多,目的都是为了提升产品质量、材料利用率和生产效率。
自动开卷落料生产线目前奇瑞公司使用的自动化开卷落料线(见图1)具有开卷、清洗涂油、校平、落料和摆剪剪切、堆垛等功能。
1.自动开卷线工作原理由起重机将卷料放上卷料备料台,然后装载到上料小车上,上料小车运行到开卷机,上料小车回位后,完成卷料与整线的对中,穿带结束后,料带经过四辊式送料机组进行料头剪切,进入清洗机进行料带的清洗;经过清洗后的料带进入校平机组;被校平后的板料进入地坑,形成一个缓冲带(补偿环),以补偿卷材在开卷校平部分连续运行和进入落料切断冲模时的间歇动作的速度差。
在地坑的一侧,装有光电反射器,当卷材下落到地坑时,反射器给出信号使驱动开卷装置的电机停止工作,卷材进给中断;经过几次落料切断后,地坑中的卷材逐步上升到一定程度,光电反射器发出信号,使驱动开卷装置的电动机起动,恢复卷材进给,开卷校平;从地坑上来的板料进入向落料压力机进给的装置;落料压机落料及堆垛。
2.自动化落料模的工作原理自动化落料模与自动化开卷线相连,板料经开卷、清洗、校平和存储缓冲对中后,进入模具滚式定位中,按照模具的步距要求,实现全自动进给送料。
板料在模具中经过有效的托件方式、合理工步的冲制,废料排入废料坑中,实现集中处理,成品件经输送带运至料垛存放。
工艺要求在此,本文以压机型号S4-630-500-260和20T行车为例。
1.材料规格适合冷轧、表面处理钢板(含镀锌钢板);板厚0.5~2.5mm;板宽450~2000mm;抗拉强度270~600N/mm2;屈服点120~400N/mm2;钢卷内径508mm或610mm;钢卷外径900~2000mm;钢卷重量最大为20000kg。
SMT自动化生产线方案

SMT自动化生产线方案一、背景介绍SMT(Surface Mount Technology)自动化生产线是一种先进的电子元器件表面贴装技术,它通过将电子元器件直接焊接在印刷电路板(PCB)表面,实现电子产品的高效生产。
为了提高生产效率和质量,许多电子创造企业正在积极引入SMT 自动化生产线。
本文将详细介绍SMT自动化生产线的方案。
二、SMT自动化生产线方案概述SMT自动化生产线方案包括以下几个关键环节:物料管理、贴装机、回流焊接、质检和包装。
下面将详细介绍每一个环节的方案。
1. 物料管理物料管理是SMT自动化生产线的基础,它包括物料采购、入库、库存管理和出库等环节。
为了实现高效的物料管理,可以采用以下方案:- 建立完善的供应商管理体系,与优质供应商建立长期合作关系,确保物料的质量和供应的稳定性。
- 引入物料管理系统,实现对物料的自动化管理,包括物料的采购计划、库存监控和出库跟踪等功能。
2. 贴装机贴装机是SMT自动化生产线的核心设备,它负责将电子元器件精确地贴装在PCB上。
为了实现高效的贴装,可以采用以下方案:- 选择适合生产规模的贴装机,考虑生产线的产能和贴装精度要求,选择具有高速度和高精度的贴装机。
- 配备自动上料系统,实现对电子元器件的自动供料,提高生产效率。
- 引入视觉识别系统,实现对电子元器件的自动定位和校正,提高贴装精度。
3. 回流焊接回流焊接是将贴装好的电子元器件与PCB焊接在一起的过程。
为了实现高质量的焊接,可以采用以下方案:- 选择适合生产规模的回流焊接设备,考虑生产线的产能和焊接质量要求,选择具有稳定性和可靠性的设备。
- 控制回流焊接的温度曲线,确保焊接过程中的温度均匀分布,避免焊接缺陷的产生。
- 引入可视化检测系统,实时监控焊接质量,及时发现并修复焊接缺陷。
4. 质检质检是SMT自动化生产线中不可或者缺的环节,它负责对贴装好的PCB进行检测,以确保产品质量。
为了实现高效的质检,可以采用以下方案:- 引入自动光学检测系统,实现对PCB的自动检测,包括焊接质量、元器件位置和PCB电气性能等方面的检测。
SMT自动化生产线方案

SMT自动化生产线方案引言概述:随着科技的不断发展,SMT(表面贴装技术)自动化生产线在电子制造行业中得到了广泛应用。
该方案通过引入自动化设备和系统,提高了生产效率和质量,降低了成本和人力投入。
本文将详细介绍SMT自动化生产线的方案,并分为五个部分进行阐述。
一、自动化设备的引入1.1 选择合适的贴片机:贴片机是SMT生产线的核心设备,可以实现高速、高精度的元件贴装。
在选择贴片机时,需要考虑生产规模、产品种类和贴装速度等因素。
1.2 引入自动上下料机:自动上下料机可以实现对元件的自动供给和回收,提高了生产效率和减少了人力投入。
1.3 引入自动检测设备:自动检测设备可以对贴片过程中的错误进行实时监测和纠正,确保产品质量。
二、生产线布局优化2.1 合理规划工作站:根据生产流程和设备的功能,合理规划工作站的布局,使得各个工作站之间的物料流动更加顺畅,减少生产过程中的等待时间。
2.2 引入自动输送系统:自动输送系统可以将物料和产品在各个工作站之间进行快速、准确的传送,提高生产效率。
2.3 设立合理的仓储区域:在生产线上设置合理的仓储区域,方便存放和管理物料,减少物料的损耗和混乱。
三、数据管理与追溯系统3.1 引入MES系统:制造执行系统(MES)可以实现对生产过程的实时监控和数据管理,包括生产计划、物料管理、质量管理等,提高生产线的可控性和透明度。
3.2 实施追溯系统:通过在生产过程中对每个产品进行标识和追溯,可以追踪产品的生产过程和质量问题,提高产品质量和售后服务。
3.3 数据分析与优化:通过对生产数据的分析,可以发现生产线中存在的问题和瓶颈,并进行优化,提高生产效率和质量。
四、人员培训与管理4.1 培训操作人员:引入自动化生产线后,需要对操作人员进行培训,使其熟悉设备的操作和维护,提高工作效率和生产线的稳定性。
4.2 设立标准操作规程:制定标准的操作规程,明确每个工作站的操作流程和质量要求,确保生产过程的一致性和产品的稳定性。
全新一代pss4000在汽车开卷落料线的应用

全新一代PSS4000在汽车开卷落料线的应用•皮尔磁工业自动化(上海)有限公司现代化汽车制造工厂主要分为冲压环节、焊装环节、涂装环节、总装环节。
这些流程进行完毕,一辆性能优越,功能齐全的汽车就展示在我们面前。
冲压生产制造作为汽车制造工艺的第一个环节具有举足轻重的作用。
而提到冲压工艺,不可或缺的就是开卷落料工艺生产线的应用。
汽车制造的第一道工序开卷落料生产线是作为汽车制造的第一道工序,作用是将汽车需要的金属卷板材料通过开卷,清洗涂油,校平冲压,落料码垛这一系列处理,实现汽车各部位金属板材的初加工。
在如今的现代化汽车制造工厂冲压车间,越来越多的全自动化封闭式开卷落料生产线得到使用,其稳定和高效,也为后续汽车生产提供了重要保障。
开卷工艺需要将金属板通过拉伸、碾压、涂油,校准完成金属板的形变和平整,然后通过压力机的冲压将金属板压制成所需要的尺寸和形状,最后传送到落料区进行堆垛工作;而这一系列工作需要时刻保证现场操作人员的安全。
开卷落料安全控制皮尔磁公司作为安全领域的领导者,为自动化开卷落料生产线安全平稳运行起到了至关重要的作用。
众所周知,生产工厂处处存在造成人员安全隐患的危险点,而自动化开卷落料生产线如果在平常的生产中缺少对于安全考量的设计,将会时刻存在对操作人员造成伤害的隐患。
皮尔磁的安全控制系统在各个知名厂家的开卷落料生产线得到了广泛的应用,确保了自动化开卷落料生产线的安全性。
那么新一代的PSS4000安全型可编程逻辑控制器在整个自动化开卷落料生产线可以发挥哪些职能呢?1、开卷单元传统的开卷落料线设计都会进行有效的外围防护,然而生产工艺环境或多或少都需要人员的介入和定期的内部维护工作,有效的使用和监控安全门的状态是安全控制中的重要环节。
因此皮尔磁安全门锁产品的应用和PSS4000新一代安全型可编程逻辑控制器的有效配合为开卷环节做到了保驾护航。
2、冲压单元自动化开卷落料生产线中压力机的作用是将开卷好的金属板材冲压成所需要的形状和尺寸以方便后续工艺的进行,如汽车的四门两盖的金属板雏形。
SMT自动化生产线方案
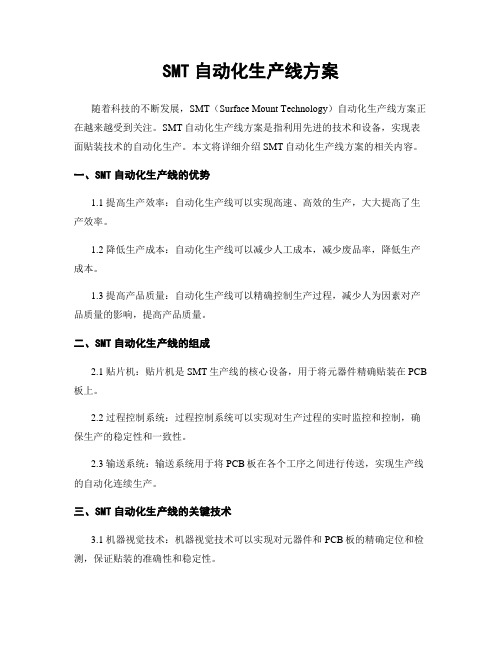
SMT自动化生产线方案随着科技的不断发展,SMT(Surface Mount Technology)自动化生产线方案正在越来越受到关注。
SMT自动化生产线方案是指利用先进的技术和设备,实现表面贴装技术的自动化生产。
本文将详细介绍SMT自动化生产线方案的相关内容。
一、SMT自动化生产线的优势1.1 提高生产效率:自动化生产线可以实现高速、高效的生产,大大提高了生产效率。
1.2 降低生产成本:自动化生产线可以减少人工成本,减少废品率,降低生产成本。
1.3 提高产品质量:自动化生产线可以精确控制生产过程,减少人为因素对产品质量的影响,提高产品质量。
二、SMT自动化生产线的组成2.1 贴片机:贴片机是SMT生产线的核心设备,用于将元器件精确贴装在PCB 板上。
2.2 过程控制系统:过程控制系统可以实现对生产过程的实时监控和控制,确保生产的稳定性和一致性。
2.3 输送系统:输送系统用于将PCB板在各个工序之间进行传送,实现生产线的自动化连续生产。
三、SMT自动化生产线的关键技术3.1 机器视觉技术:机器视觉技术可以实现对元器件和PCB板的精确定位和检测,保证贴装的准确性和稳定性。
3.2 自动化控制技术:自动化控制技术可以实现对生产线的自动化控制和调度,提高生产效率和质量。
3.3 数据分析技术:数据分析技术可以对生产过程中的数据进行分析和挖掘,发现问题并及时调整生产参数,提高生产效率和产品质量。
四、SMT自动化生产线的应用领域4.1 电子产品创造:SMT自动化生产线广泛应用于手机、电脑、电视等电子产品的创造领域。
4.2 汽车电子创造:SMT自动化生产线也被应用于汽车电子产品的创造,提高了汽车电子产品的生产效率和质量。
4.3 工业控制领域:SMT自动化生产线还被应用于工业控制领域,提高了工业控制产品的生产效率和稳定性。
五、SMT自动化生产线的发展趋势5.1 智能化:未来SMT自动化生产线将趋向智能化,实现更高效的生产和管理。
简述落料开卷自动线的工作流程
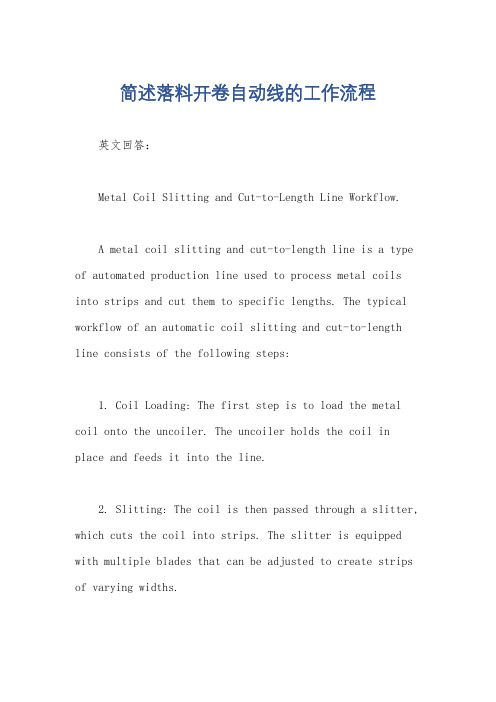
简述落料开卷自动线的工作流程英文回答:Metal Coil Slitting and Cut-to-Length Line Workflow.A metal coil slitting and cut-to-length line is a type of automated production line used to process metal coils into strips and cut them to specific lengths. The typical workflow of an automatic coil slitting and cut-to-length line consists of the following steps:1. Coil Loading: The first step is to load the metal coil onto the uncoiler. The uncoiler holds the coil in place and feeds it into the line.2. Slitting: The coil is then passed through a slitter, which cuts the coil into strips. The slitter is equipped with multiple blades that can be adjusted to create strips of varying widths.3. Leveling: After slitting, the strips are passed through a leveler, which flattens and smooths the strips.4. Cut-to-Length: The leveled strips are then cut to the desired length using a shear. The shear is equipped with a measuring device that ensures accurate cutting.5. Stacking or Coiling: The cut strips are then stacked or coiled onto a reel. The stacking or coiling process is automated, ensuring efficient and consistent results.中文回答:落料开卷自动线工作流程。
MPS自动生产线

优化:根据生产需求和市场变化,对 生产线进行优化和调整
汽车零部件生产: MPS自动生产线 可以用于生产汽 车零部件,如发 动机、变速箱等。
汽车装配:MPS 自动生产线可以 用于汽车装配, 如车身、底盘、 内饰等。
维护成本高:MPS自动生产线的维护 成本也相对较高,需要专业的技术人 员进行维护。
灵活性较低:MPS自动生产线的设计 和生产过程较为固定,对于市场需求 的变化可能无法及时响应。
技术要求高:MPS自动生产线需要较 高的技术水平和管理水平,对于企业 的技术实力和管理能力有一定的要求。
智能化:提高生产 线的自动化程度, 实现无人化生产
汽车检测:MPS 自动生产线可以 用于汽车检测, 如质量检验、性 能测试等。
汽车维修:MPS 自动生产线可以 用于汽车维修, 如更换零部件、 维修保养等。
手机、电脑等电子产品的生产 电子元器件的制造和组装 电子产品的检测和维修 电子产品的包装和运输
食品生产自动化:提高生产效 率,减少人工成本
食品安全控制:通过自动化设 备,确保食品质量和安全
环保要求:提高生产线的环 保性能,减少废弃物和污染
排放
人才培养:培养高素质的技 术人才,提高生产线的研发
和创新能力
汇报人:XX
XX,
汇报人:XX
MPS自动生产线是一种高度自动化的生产线,可以自动完成产品的生产 过程。 MPS自动生产线主要由机械手、传送带、控制系统等部分组成。
MPS自动生产线可以实现高效率、高质量、低成本的生产。
MPS自动生产线广泛应用于汽车、电子、食品、医药等行业。
控制器:负责控制整个生 产线的运行
输送带:负责将物料从一 个工位输送到另一个工位
SMT自动化生产线方案
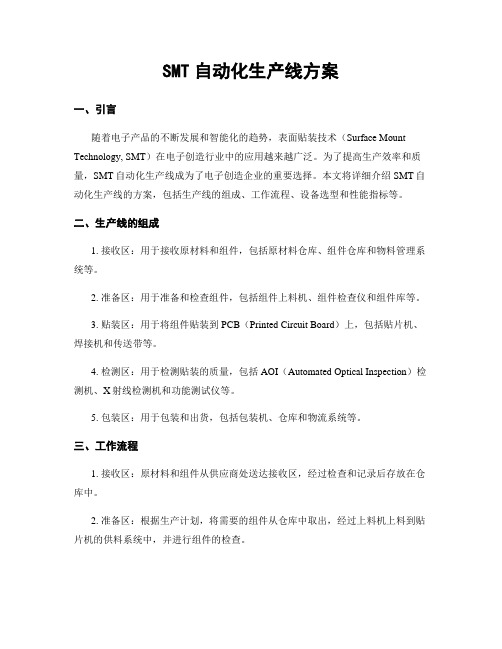
SMT自动化生产线方案一、引言随着电子产品的不断发展和智能化的趋势,表面贴装技术(Surface Mount Technology, SMT)在电子创造行业中的应用越来越广泛。
为了提高生产效率和质量,SMT自动化生产线成为了电子创造企业的重要选择。
本文将详细介绍SMT自动化生产线的方案,包括生产线的组成、工作流程、设备选型和性能指标等。
二、生产线的组成1. 接收区:用于接收原材料和组件,包括原材料仓库、组件仓库和物料管理系统等。
2. 准备区:用于准备和检查组件,包括组件上料机、组件检查仪和组件库等。
3. 贴装区:用于将组件贴装到PCB(Printed Circuit Board)上,包括贴片机、焊接机和传送带等。
4. 检测区:用于检测贴装的质量,包括AOI(Automated Optical Inspection)检测机、X射线检测机和功能测试仪等。
5. 包装区:用于包装和出货,包括包装机、仓库和物流系统等。
三、工作流程1. 接收区:原材料和组件从供应商处送达接收区,经过检查和记录后存放在仓库中。
2. 准备区:根据生产计划,将需要的组件从仓库中取出,经过上料机上料到贴片机的供料系统中,并进行组件的检查。
3. 贴装区:贴片机按照预定的程序将组件精确地贴装到PCB上,焊接机进行焊接工艺。
4. 检测区:经过贴装的PCB进入AOI检测机进行光学检测,X射线检测机进行焊点的检测,功能测试仪进行电气性能测试。
5. 包装区:通过包装机将成品进行包装,并存放在仓库中,待发货时通过物流系统进行出货。
四、设备选型1. 贴片机:根据生产需求和贴装速度选择合适的贴片机,常见的有高速贴片机、多功能贴片机和通用贴片机等。
2. 焊接机:根据焊接工艺选择合适的焊接机,常见的有波峰焊接机、回流焊接机和热风焊接机等。
3. AOI检测机:选择具有高分辨率和高速度的AOI检测机,能够准确地检测贴装的质量和焊点的问题。
4. X射线检测机:选择能够进行焊点检测和内部缺陷检测的X射线检测机,确保焊接质量和产品可靠性。
简述落料开卷自动线的工作流程

简述落料开卷自动线的工作流程英文回答:The workflow of a blanking and opening automatic line involves several steps to efficiently process materials and prepare them for further manufacturing processes. Here is a description of the workflow:1. Material Loading: The process begins with loading the raw material onto the line. This can be done manually or using automated systems such as robotic arms. The material can be in the form of coils or sheets, depending on the specific requirements.2. Decoiling: If the material is in coil form, it needs to be decoiled to obtain individual sheets. This is done using a decoiler machine that unwinds the coil and feeds it into the next stage of the line.3. Straightening: The material may undergostraightening to remove any distortions or bends. Straightening machines are used to flatten the material and ensure its uniformity.4. Feeding: The straightened material is then fed into the blanking machine. The feeding mechanism can be mechanical or pneumatic, depending on the line's design. The machine precisely positions the material for the next step.5. Blanking: The blanking machine cuts the materialinto the desired shape or size. It uses a die and a punch to create the required cutouts or blanks. The blanks are separated from the rest of the material and collected for further processing.6. Opening: After blanking, the remaining material is opened up to create gaps or openings. This can be done using mechanical or hydraulic mechanisms. The openings are necessary for subsequent manufacturing processes, such as bending or forming.7. Sorting and Stacking: The blanks and opened material are sorted and stacked according to their specifications. This ensures easy retrieval and efficient utilization in the next stages of production.8. Quality Control: Throughout the workflow, quality control measures are implemented to ensure the accuracy and precision of the processed material. This can involvevisual inspections, measurements, and testing to meet the required standards.9. Output: The final output of the blanking and opening automatic line is a collection of accurately cut blanks and opened material, ready for further manufacturing processes such as bending, welding, or assembly.中文回答:落料开卷自动线的工作流程包括多个步骤,以高效地加工材料并为后续的制造过程做准备。
SMT自动化生产线方案

SMT自动化生产线方案一、背景介绍随着电子产品的快速发展和市场需求的增加,SMT(表面贴装技术)自动化生产线成为电子创造业中不可或者缺的一部份。
SMT自动化生产线能够实现高效、精确的电子元器件贴装,提高生产效率和质量。
本文将详细介绍SMT自动化生产线的方案,包括设备配置、工作流程、技术要求等。
二、设备配置1. 贴片机:负责将电子元器件精确贴装到PCB(Printed Circuit Board,印刷电路板)上。
常见的贴片机有X轴和Y轴挪移的单头贴片机和多头贴片机,多头贴片机能够同时贴装多个元器件,提高贴装效率。
2. 焊接设备:包括波峰焊机和回流焊机,用于焊接贴装好的电子元器件。
波峰焊机通过波峰熔化焊锡,将元器件与PCB焊接在一起;回流焊机通过加热和冷却过程,实现焊接。
3. 传送设备:包括输送带和传送机械手,用于将PCB从一工作站传送到另一工作站,实现自动化生产线的流程。
4. 检测设备:包括自动光学检测机和X光检测机,用于检测贴装和焊接的质量,确保产品符合标准。
5. 辅助设备:包括印刷机、贴装机、烘烤机等,用于辅助生产线的工作。
三、工作流程1. 准备工作:包括准备PCB、元器件和焊接材料,设置贴片机和焊接设备的参数。
2. 贴装工序:将PCB放置在传送设备上,传送到贴片机工作站。
贴片机根据预设的程序,将电子元器件精确贴装到PCB上。
3. 焊接工序:将贴装好的PCB传送到焊接设备工作站。
波峰焊机通过波峰熔化焊锡,将元器件与PCB焊接在一起;回流焊机通过加热和冷却过程,实现焊接。
4. 检测工序:将焊接好的PCB传送到检测设备工作站。
自动光学检测机和X光检测机对贴装和焊接的质量进行检测,确保产品符合标准。
5. 包装工序:将通过检测的产品进行包装,准备出货。
四、技术要求1. 精确度要求:贴片机和焊接设备需要具备高精度的运动控制和定位能力,以确保电子元器件的精确贴装和焊接。
2. 自动化程度要求:生产线需要实现自动化的工作流程,减少人工操作和人为错误,提高生产效率和产品质量。
浅谈铝圆片在炊具制造中的工艺性能及优势[权威资料]
![浅谈铝圆片在炊具制造中的工艺性能及优势[权威资料]](https://img.taocdn.com/s3/m/1d38c59d6429647d27284b73f242336c1eb9301b.png)
浅谈铝圆片在炊具制造中的工艺性能及优势[摘要]随着近年来工业的飞速发展,以铝圆片为首的众多合金板带材产品正逐步运用到各行各业中,极大地促进了工业的壮大和经济的发展。
随着人们对生活质量的要求不断增多,对合金材质的炊具的多样化、功能化的改进程度也在不断加大。
本文通过阐述炊具的生产过程,重点探讨了铝合金圆片运用在炊具生产制造中的工艺性能和优势,突出了铝合金圆片在炊具制造中的显著特点。
[关键词]铝合金圆片炊具制造工艺性能优势T96 A 1009-914X(2015)46-0372-01随着人们生活质量的提高,炊具的样式和功能呈现多样化的同时,也要求在生产加工方面优化技术和材质,提高炊具的使用性能。
人们采用不同的单金属或合金材质进行模具生产,通过运用专用的工具操作完成对金属的外形控制、属性控制,实现了对炊具的工艺优化和快速生产,因此关于金属材质的选择就变得至关重要。
本文探讨的铝合金圆片就在炊具制造方面显出足够强大的优越性,是一种用量最大的铝合金板带材深加工产品。
1 铝合金圆片概述1.1 铝的性质铝,化学元素名称为Al。
它作为在地壳中含量仅次于氧物质和硅物质的轻金属,在自然界中能够轻易找到其化合物成分。
铝在现有工业所需金属品种中作为第二大类金属,产销量和工业使用量仅次于钢铁。
铝金属本身具有银白色金属光泽,纯铝的质地极其柔软,具有特殊的物理、化学特性,重量虽轻但坚硬度不低,而且具有良好的延展性,塑性能力强。
具有特殊的导电性、导热性、耐热性和耐核辐射性,由于金属铝的外表面为一层极为致密的氧化膜(氧化铝)所保护,因此它不易被酸腐蚀,但能被碱所溶解。
这些特性足以使铝金属成为推动国民经济发展的重要战略性基础原材料。
1.2 铝板材铝板材是指运用塑性加工方法将铝坯锭制造而成的板型铝制品,制造过程需要采用轧制、挤压、拉伸和锻造等方法。
其后需要对成品进行退火处理、固溶处理、淬火处理、自然时效和人工时效处理来确保板材的性能最终达到标准要求。
SMT自动化生产线方案

SMT自动化生产线方案一、背景介绍近年来,随着电子产品的不断发展和市场需求的增加,表面贴装技术(Surface Mount Technology,简称SMT)在电子创造业中得到了广泛应用。
SMT技术具有高效、高质、高稳定性的特点,因此成为了电子产品生产的主要创造工艺之一。
为了提高生产效率和质量,许多企业开始引入SMT自动化生产线。
二、SMT自动化生产线的概述SMT自动化生产线是指通过自动化设备和系统,实现电子产品的自动化生产过程。
它主要包括以下几个环节:1. 材料供应环节:包括原材料的采购、仓储和供应,确保生产线的连续供应。
2. 贴装环节:将电子元器件精确地粘贴到PCB(Printed Circuit Board,印刷电路板)上,包括贴片机、回焊炉等设备的使用。
3. 检测环节:通过自动化检测设备对贴装后的电子产品进行检测,包括AOI (Automated Optical Inspection,自动光学检测)和SPI(Solder Paste Inspection,焊膏检测)等。
4. 焊接环节:通过自动化焊接设备对贴装后的电子产品进行焊接,包括波峰焊和热风焊等。
5. 组装环节:将焊接好的电子产品进行组装,包括组装机械手和组装工作台等设备的使用。
6. 包装环节:对组装好的电子产品进行包装,包括自动化包装机和包装材料的使用。
三、SMT自动化生产线方案的优势引入SMT自动化生产线可以带来以下几个优势:1. 提高生产效率:自动化设备能够高速、精确地完成贴装、焊接和组装等工作,大大提高了生产效率。
2. 提高产品质量:自动化设备具有高精度和稳定性,能够减少人为因素对产品质量的影响,提高产品的一致性和可靠性。
3. 降低人力成本:自动化生产线可以取代大量的人工操作,减少了人力成本和劳动强度。
4. 提升生产线灵便性:自动化设备可以通过编程实现不同产品的生产,提高了生产线的灵便性和适应性。
5. 实现生产过程的可追溯性:自动化设备可以记录和存储生产过程的数据,实现生产过程的可追溯性,方便质量管理和问题排查。
SMT自动化生产线方案
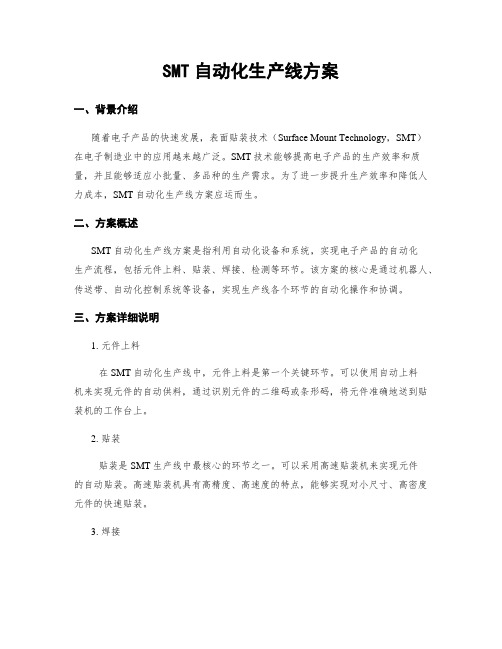
SMT自动化生产线方案一、背景介绍随着电子产品的快速发展,表面贴装技术(Surface Mount Technology,SMT)在电子制造业中的应用越来越广泛。
SMT技术能够提高电子产品的生产效率和质量,并且能够适应小批量、多品种的生产需求。
为了进一步提升生产效率和降低人力成本,SMT自动化生产线方案应运而生。
二、方案概述SMT自动化生产线方案是指利用自动化设备和系统,实现电子产品的自动化生产流程,包括元件上料、贴装、焊接、检测等环节。
该方案的核心是通过机器人、传送带、自动化控制系统等设备,实现生产线各个环节的自动化操作和协调。
三、方案详细说明1. 元件上料在SMT自动化生产线中,元件上料是第一个关键环节。
可以使用自动上料机来实现元件的自动供料,通过识别元件的二维码或条形码,将元件准确地送到贴装机的工作台上。
2. 贴装贴装是SMT生产线中最核心的环节之一。
可以采用高速贴装机来实现元件的自动贴装。
高速贴装机具有高精度、高速度的特点,能够实现对小尺寸、高密度元件的快速贴装。
3. 焊接焊接是SMT生产线中的另一个重要环节。
可以使用回流焊接炉来实现元件的自动焊接。
回流焊接炉具有温度控制精度高、焊接质量稳定的特点,能够实现对不同类型元件的精确焊接。
4. 检测检测是SMT生产线中的关键环节之一,可以采用自动化检测设备来实现对贴装后的电子产品进行自动检测。
自动化检测设备可以通过视觉检测、电气测试等方式,对电子产品的质量进行全面检测和评估。
5. 自动化控制系统SMT自动化生产线方案需要一个强大的自动化控制系统来实现各个环节的协调和管理。
自动化控制系统可以通过PLC(可编程逻辑控制器)或SCADA(监控与数据采集系统)来实现对生产线的自动控制和监控。
四、方案优势1. 提高生产效率:SMT自动化生产线方案能够实现生产过程的自动化,大大提高了生产效率。
相比手工操作,自动化生产线能够实现更快速、更准确的元件贴装和焊接。
SMT自动化生产线方案

SMT自动化生产线方案引言概述:随着科技的不断进步和市场需求的不断增长,SMT(表面贴装技术)自动化生产线方案成为了电子制造行业中的重要组成部分。
SMT自动化生产线方案通过引入自动化设备和技术,提高了生产效率、降低了成本,并且保证了产品质量的稳定性。
本文将从五个大点来阐述SMT自动化生产线方案的内容。
正文内容:1. 设备自动化1.1 自动贴片机自动贴片机是SMT自动化生产线方案中的核心设备之一。
它能够快速、准确地将电子元件精确地贴在PCB(印刷电路板)上。
自动贴片机具有高速贴装能力、多功能性和高精度等特点,可以大大提高生产效率和贴片质量。
1.2 自动焊接机自动焊接机用于将电子元件与PCB焊接在一起。
它可以通过热风或者烙铁等方式进行焊接,并且具有高效、稳定和可靠的特点。
自动焊接机的引入可以大大减少人工焊接的工作量,提高焊接质量,并且降低了生产成本。
2. 过程控制与管理2.1 自动化控制系统SMT自动化生产线方案中的自动化控制系统可以对整个生产过程进行精确控制和管理。
它可以监测设备运行状态、调整设备参数,并且实时反馈生产数据。
通过自动化控制系统,生产线可以实现高效、稳定的运行,提高生产效率和产品质量。
2.2 质量控制与检测SMT自动化生产线方案中的质量控制与检测系统可以对产品质量进行全面监测和控制。
它可以通过自动化设备进行质量检测,如检测焊接质量、贴片质量等,并且可以及时发现和修复生产过程中的问题,保证产品质量的稳定性。
2.3 数据分析与优化SMT自动化生产线方案中的数据分析与优化系统可以对生产数据进行收集、分析和优化。
通过对生产数据的分析,可以及时发现生产过程中的问题,并且通过优化参数和流程,提高生产效率和产品质量。
3. 物料管理与供应链3.1 自动化物料搬运SMT自动化生产线方案中的自动化物料搬运系统可以实现物料的自动化供应和搬运。
它可以通过自动化设备和机械臂等技术,实现物料的准确搬运和供应,提高物料的利用率和生产效率。
SMT自动化生产线方案
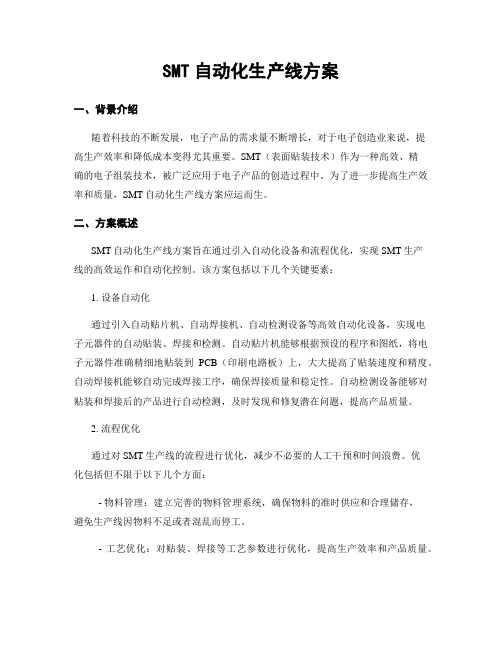
SMT自动化生产线方案一、背景介绍随着科技的不断发展,电子产品的需求量不断增长,对于电子创造业来说,提高生产效率和降低成本变得尤其重要。
SMT(表面贴装技术)作为一种高效、精确的电子组装技术,被广泛应用于电子产品的创造过程中。
为了进一步提高生产效率和质量,SMT自动化生产线方案应运而生。
二、方案概述SMT自动化生产线方案旨在通过引入自动化设备和流程优化,实现SMT生产线的高效运作和自动化控制。
该方案包括以下几个关键要素:1. 设备自动化通过引入自动贴片机、自动焊接机、自动检测设备等高效自动化设备,实现电子元器件的自动贴装、焊接和检测。
自动贴片机能够根据预设的程序和图纸,将电子元器件准确精细地贴装到PCB(印刷电路板)上,大大提高了贴装速度和精度。
自动焊接机能够自动完成焊接工序,确保焊接质量和稳定性。
自动检测设备能够对贴装和焊接后的产品进行自动检测,及时发现和修复潜在问题,提高产品质量。
2. 流程优化通过对SMT生产线的流程进行优化,减少不必要的人工干预和时间浪费。
优化包括但不限于以下几个方面:- 物料管理:建立完善的物料管理系统,确保物料的准时供应和合理储存,避免生产线因物料不足或者混乱而停工。
- 工艺优化:对贴装、焊接等工艺参数进行优化,提高生产效率和产品质量。
- 自动化传送:引入自动化传送设备,实现生产线各个环节之间的自动传送,减少人工搬运和等待时间。
- 数据管理:建立数据采集和分析系统,对生产线的各项指标进行实时监控和分析,及时发现问题并进行调整。
3. 人员培训SMT自动化生产线方案的成功实施需要有一支熟练的操作和维护团队。
因此,在引入自动化设备和优化流程之前,需要对相关人员进行培训,使其熟悉新的操作流程和设备维护知识。
培训内容包括但不限于以下几个方面:- 设备操作:培训人员熟悉自动贴片机、自动焊接机、自动检测设备等自动化设备的操作方法和注意事项。
- 工艺知识:培训人员了解贴装、焊接等工艺的基本原理和参数设置方法,使其能够根据实际情况进行调整和优化。
SMT自动化生产线方案
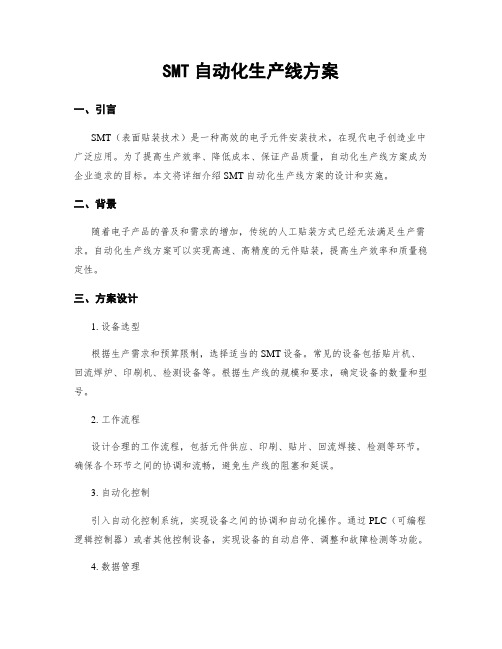
SMT自动化生产线方案一、引言SMT(表面贴装技术)是一种高效的电子元件安装技术,在现代电子创造业中广泛应用。
为了提高生产效率、降低成本、保证产品质量,自动化生产线方案成为企业追求的目标。
本文将详细介绍SMT自动化生产线方案的设计和实施。
二、背景随着电子产品的普及和需求的增加,传统的人工贴装方式已经无法满足生产需求。
自动化生产线方案可以实现高速、高精度的元件贴装,提高生产效率和质量稳定性。
三、方案设计1. 设备选型根据生产需求和预算限制,选择适当的SMT设备。
常见的设备包括贴片机、回流焊炉、印刷机、检测设备等。
根据生产线的规模和要求,确定设备的数量和型号。
2. 工作流程设计合理的工作流程,包括元件供应、印刷、贴片、回流焊接、检测等环节。
确保各个环节之间的协调和流畅,避免生产线的阻塞和延误。
3. 自动化控制引入自动化控制系统,实现设备之间的协调和自动化操作。
通过PLC(可编程逻辑控制器)或者其他控制设备,实现设备的自动启停、调整和故障检测等功能。
4. 数据管理建立完善的数据管理系统,实时监测生产线的运行状态和产品质量。
通过数据分析,及时发现问题并采取措施,提高生产效率和质量稳定性。
5. 人机界面设计友好的人机界面,方便操作员进行设备的监控和调整。
界面应具备直观、简单、易用的特点,提高操作效率和减少人为错误。
四、方案实施1. 设备安装根据方案设计,安装各个设备,并确保设备之间的连接和通信正常。
对设备进行调试和测试,确保其正常运行。
2. 系统集成将各个设备与自动化控制系统进行集成,确保设备的协调运行和自动化控制的实现。
对控制系统进行调试和测试,确保其稳定可靠。
3. 数据管理系统建设建设数据管理系统,包括数据采集、存储、分析和展示等功能。
确保数据的准确性和及时性,为生产决策提供支持。
4. 人员培训对操作员进行培训,使其熟悉设备的操作和维护。
培训内容包括设备的启停、调整、故障排除等,提高操作员的技能水平和工作效率。
SMT自动化生产线方案
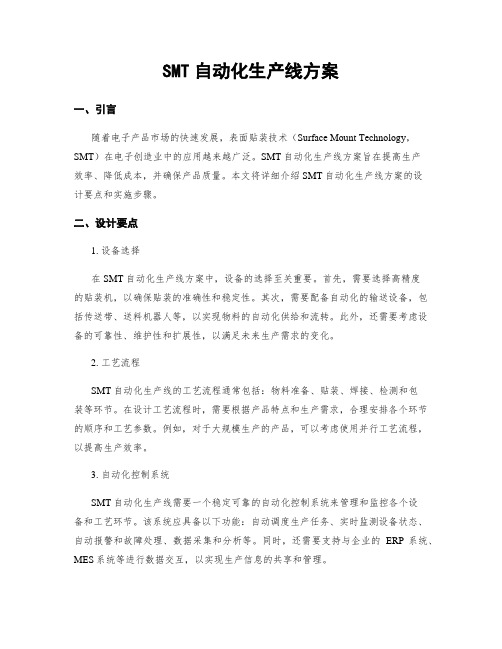
SMT自动化生产线方案一、引言随着电子产品市场的快速发展,表面贴装技术(Surface Mount Technology,SMT)在电子创造业中的应用越来越广泛。
SMT自动化生产线方案旨在提高生产效率、降低成本,并确保产品质量。
本文将详细介绍SMT自动化生产线方案的设计要点和实施步骤。
二、设计要点1. 设备选择在SMT自动化生产线方案中,设备的选择至关重要。
首先,需要选择高精度的贴装机,以确保贴装的准确性和稳定性。
其次,需要配备自动化的输送设备,包括传送带、送料机器人等,以实现物料的自动化供给和流转。
此外,还需要考虑设备的可靠性、维护性和扩展性,以满足未来生产需求的变化。
2. 工艺流程SMT自动化生产线的工艺流程通常包括:物料准备、贴装、焊接、检测和包装等环节。
在设计工艺流程时,需要根据产品特点和生产需求,合理安排各个环节的顺序和工艺参数。
例如,对于大规模生产的产品,可以考虑使用并行工艺流程,以提高生产效率。
3. 自动化控制系统SMT自动化生产线需要一个稳定可靠的自动化控制系统来管理和监控各个设备和工艺环节。
该系统应具备以下功能:自动调度生产任务、实时监测设备状态、自动报警和故障处理、数据采集和分析等。
同时,还需要支持与企业的ERP系统、MES系统等进行数据交互,以实现生产信息的共享和管理。
三、实施步骤1. 需求分析在实施SMT自动化生产线方案之前,需要进行需求分析,明确生产线的目标和要求。
这包括生产能力、质量要求、设备投资等方面的考虑。
通过与相关部门和人员的沟通,采集和整理相关数据和信息,为后续的方案设计和实施做好准备。
2. 方案设计根据需求分析的结果,进行SMT自动化生产线方案的设计。
这包括设备选型、工艺流程设计、自动化控制系统的设计等。
在设计过程中,需要考虑设备之间的协同工作、工艺参数的优化、自动化控制系统的可靠性和灵便性等因素。
3. 设备采购与安装根据方案设计的结果,进行设备的采购和安装。
- 1、下载文档前请自行甄别文档内容的完整性,平台不提供额外的编辑、内容补充、找答案等附加服务。
- 2、"仅部分预览"的文档,不可在线预览部分如存在完整性等问题,可反馈申请退款(可完整预览的文档不适用该条件!)。
- 3、如文档侵犯您的权益,请联系客服反馈,我们会尽快为您处理(人工客服工作时间:9:00-18:30)。
随着社会飞速发展,国内外对于有色金属的使用量不断加大,在民用炊具金属锅、盆、碗等圆坯、电机定转子的硅钢圆片、汽车部分钣金五金件、灯具、太阳能等生产过程中金属圆片落料生产工序是此类行业不可或缺的生产工艺,如何采取必要措施提高产品品质和材料的利用率是生产过程中的重点;另外,随着消费水平不断提高,劳动力的价格也在不断上涨,如何科学、合理的使用劳动力减少生产成本也是企业所面临的重要问题。
自动化圆片落料生产线的出现,解决了过去以往生产中所遇到的以下问题:节省原材料,有效地提高毛坯材料利用率。
圆片下料生产线的特点:
1. 高产出:可进行多次移位,按60°角计算,每一次移位可节约材料7%,在圆片大小不等时,可依材料宽度对排布角度进行改变,提供材料利用率。
2. 高效率:每分钟最高速度为60次。
3. 高精度:在连续冲压过程中,边与边的最小距离可设定在0.5mm以内,每次的移动误差可保证在±0.08mm以内。
4. 占地空间小,能源消耗低
5. 成品工作搬运方便:材料冲压后,自动掉落在成品输送带上,由输送带送到垛料台上。
6. 全自动化控制,节省人力资源:该生产线在工作中,只需一位员工操作电控箱控制机柜。
在人机面板上输入操作程序,设备将全自动化生产。