自动化生产线自动上料站的PLC控制
生产线自动装箱的plc控制
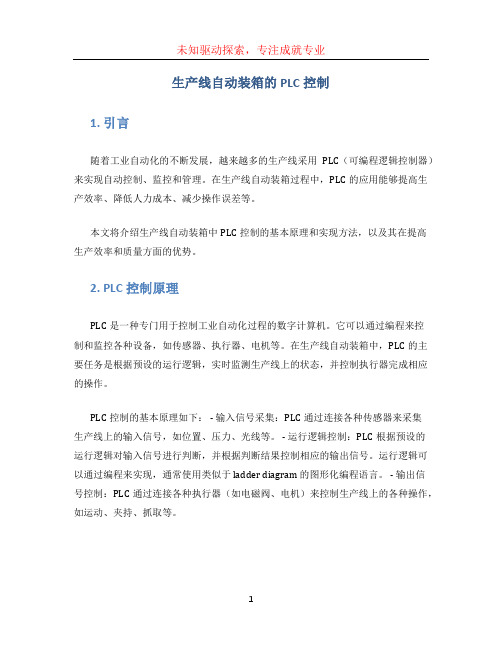
生产线自动装箱的PLC控制1. 引言随着工业自动化的不断发展,越来越多的生产线采用PLC(可编程逻辑控制器)来实现自动控制、监控和管理。
在生产线自动装箱过程中,PLC的应用能够提高生产效率、降低人力成本、减少操作误差等。
本文将介绍生产线自动装箱中PLC控制的基本原理和实现方法,以及其在提高生产效率和质量方面的优势。
2. PLC控制原理PLC是一种专门用于控制工业自动化过程的数字计算机。
它可以通过编程来控制和监控各种设备,如传感器、执行器、电机等。
在生产线自动装箱中,PLC的主要任务是根据预设的运行逻辑,实时监测生产线上的状态,并控制执行器完成相应的操作。
PLC控制的基本原理如下: - 输入信号采集:PLC通过连接各种传感器来采集生产线上的输入信号,如位置、压力、光线等。
- 运行逻辑控制:PLC根据预设的运行逻辑对输入信号进行判断,并根据判断结果控制相应的输出信号。
运行逻辑可以通过编程来实现,通常使用类似于 ladder diagram 的图形化编程语言。
- 输出信号控制:PLC通过连接各种执行器(如电磁阀、电机)来控制生产线上的各种操作,如运动、夹持、抓取等。
3. 生产线自动装箱的PLC控制流程生产线自动装箱的PLC控制流程如下:1.输入信号采集:PLC通过连接各种传感器,如光电传感器、压力传感器、位置传感器等,采集工件的信息,如位置、尺寸、重量等。
2.运行逻辑控制:PLC根据预设的运行逻辑对输入信号进行判断,并根据判断结果控制装箱操作。
例如,根据工件的位置判断是否需要进行装箱操作,根据工件的重量判断装箱的位置和强度等。
3.输出信号控制:PLC通过连接各种执行器,如电磁阀、电机,控制装箱操作。
例如,通过控制电磁阀来控制夹紧装箱箱体的气压,通过控制电机来控制装箱机械臂的运动。
4.监控和反馈:PLC实时监控装箱操作的状态,并根据需要发送报警信号或进行故障处理。
同时,PLC还可以采集装箱过程中的数据,如装箱数量、速度、故障记录等,用于生产线的管理和优化。
自动送料装车系统PLC控制设计说明

一、控制要求1.1 控制对象介绍自动送料装车系统是用于物料输送的流水线设备,主要是用于煤粉、细砂等材料的运输。
自动送料装车系统一般是由给料器、传送带、小车等单体设备组合来完成特定的过程。
这类系统的控制需要动作稳定,具备连续可靠工作的能力。
通过三台电机和三个传送带、料斗、小车等的配合,才能稳定、有效率地进行自动送料装车过程。
如下图所示:1.2 控制原理自动送料装车系统是通过电机和限位开关来控制的。
称重开关S2控制汽车开来或开走。
三台电机控制三个传送带。
进料开关K1控制控制进料与否。
检测开关S1控制料斗中物料的空满。
另外,在S2处增设两个七段数码管,用来统计每日的装车数。
装车数的统计采用脉冲计数的方法进行。
脉冲计数方法是当装料车装满时S2断开后,开始定时放送脉冲;当S2闭合时停止发送脉冲。
一个脉冲的宽度即为一辆汽车。
用两个数码管计数,所计的数即为装车数。
当S2接通时,红灯L1亮,绿灯L2灭,传送电动机M3运行,传送电动机M2延迟M3电动机2S运行,送料电动机M1延迟M2电动机2S运行,料斗K2延迟M2电动机2S打开出料。
当料满后(S2断开后),料斗K2关闭,电动机M1延时2S后关断,M2在M1停后2S后停止,M3在M2停止后2S后停止,L2灯亮,L1灯灭,此时汽车可以开走。
1.3 自动送料装车系统的启停过程示意图该图中从上到下是启动顺序,从下到上是停止顺序。
1.4 控制要求初始状态:红灯L1灭,绿灯L2亮,表示允许汽车开进装料,料斗K2,电动机M1,M2,M3皆为OFF。
当汽车到来时(S2接通表示),L1亮,L2灭,M3运行,电动机M2在M3通2S后运行,M1在M2通2S后运行,K2在M1通2S后打开出料。
当物料满后(用S2断开表示),料斗K2关闭,电动机M1延时2S后关断,M2在M1停2S后停止,M3在M2停2S后停止,L2亮,L1灭,表示汽车可以开走。
设计要求:当料不满(S1为OFF,灯灭),料斗开关K2关闭(OFF),灯灭,不出料,进料开关K1打开(K1为ON)进料,否则不进料。
自动送料装车系统PLC控制设计

自动送料装车系统PLC控制设计在设计自动送料装车系统的PLC控制时,需要考虑以下几个方面。
首先是系统的硬件设计。
自动送料装车系统的硬件设备包括传感器、执行器、电机控制器等。
传感器用于检测物料的位置和状态,如光电传感器可以检测物料的到位和离开状态,压力传感器可以检测物料的重量和压力等。
执行器用于控制物料的移动和装载,如气缸可以用于推动物料的移动,电机可以用于驱动输送带的运动。
电机控制器用于控制电机的启停和速度调节。
在PLC控制设计中,需要根据实际需求选取合适的硬件设备,并配置相应的输入输出端口。
其次是系统的逻辑控制。
自动送料装车系统的逻辑控制包括物料的检测、移动和装载的逻辑控制。
通过光电传感器等传感器检测物料的位置和状态,PLC可以根据这些信号对电机和执行器进行控制,实现物料的移动和装载。
例如,当光电传感器检测到物料到位时,PLC可以控制执行器将物料推动到指定位置;当光电传感器检测到物料离开时,PLC可以控制电机停止运动。
在逻辑控制设计中,需要根据实际流程和要求,编写PLC的逻辑程序,明确各个信号的处理方式和相应的控制动作。
最后是系统的安全设计。
在自动送料装车系统中,安全性是一个非常重要的考虑因素。
系统设计应该考虑到可能出现的故障和意外情况,并采取相应的安全措施。
例如,可以在输送带上设置紧急停止按钮,一旦发生紧急情况,可以立即停止输送带的运动;可以在执行器上设置限位开关,一旦执行器超过了安全范围,可以自动停止运动。
同时,还应考虑到保护设备的安全性设计,如安装防护罩,避免人员接触到危险部位。
在安全设计中,需要充分考虑系统的各个环节和可能的风险,并采取相应的措施保障工作人员的安全。
综上所述,自动送料装车系统的PLC控制设计主要包括硬件设计、逻辑控制和安全设计。
通过科学合理地设计PLC控制系统,可以提高自动送料装车系统的稳定性和效率,实现工业生产的自动化控制。
PLC在生产线控制中的应用案例分享

PLC在生产线控制中的应用案例分享PLC(可编程逻辑控制器)是一种常见的工业自动化设备,广泛应用于各种生产线的控制系统中。
本文将分享几个PLC在生产线控制中的应用案例,旨在探讨PLC的功能和应用,以及它们在提高生产效率和质量方面的作用。
案例一:汽车生产线在汽车生产线上,PLC扮演着关键的角色。
它通过接收传感器和外部设备的输入信号,对各个工作站的运行进行控制和调度。
通过编程,PLC可以对不同的操作进行精确的定时和顺序控制,确保每个工作站都按照正确的步骤进行,并与其他工作站协调合作。
举个例子,在汽车装配线上,PLC可以控制机械臂的动作和位置,确保零部件的准确提取和装配。
它还可以监控传送带的速度和方向,及时调整生产节奏,以适应不同车型和订单的要求。
通过PLC的应用,汽车生产线可以实现高效、精确和稳定的生产,大大提升了生产效率和产品质量。
案例二:食品加工生产线在食品加工行业,PLC也发挥着重要的作用。
以饼干生产线为例,PLC可以控制不同工作站的温度、时间和速度等参数,实现对各个工艺环节的精确控制。
例如,在饼干生产的烘烤环节,PLC可以根据产品种类和要求,控制烤箱的温度和气流方向,确保饼干可以均匀烘烤,达到理想的口感和外观。
此外,PLC还可以监测并记录生产数据,如温度、湿度、压力等,以便质量控制人员进行分析和追溯。
案例三:包装生产线在包装行业,在PLC的应用下,生产线的包装过程可以更加高效、准确和可靠。
例如,在瓶装水生产线上,PLC可以控制灌装机的流量和速度,确保每个瓶子都按照预定的容量装满水。
它还可以监控瓶子的位置和运行速度,及时进行调整,避免瓶子的堵塞和脱落。
此外,PLC还可以与其他包装设备如贴标机、封口机等进行联动控制,实现自动化生产和包装过程。
综上所述,PLC在生产线控制中的应用案例丰富多样。
它的高可编程性和灵活性使得PLC适用于各种不同的生产线和行业。
通过合理的编程和控制,PLC能够提高生产效率、降低成本、提升产品质量,并且具备良好的稳定性和可靠性。
PLC控制自动上料系统
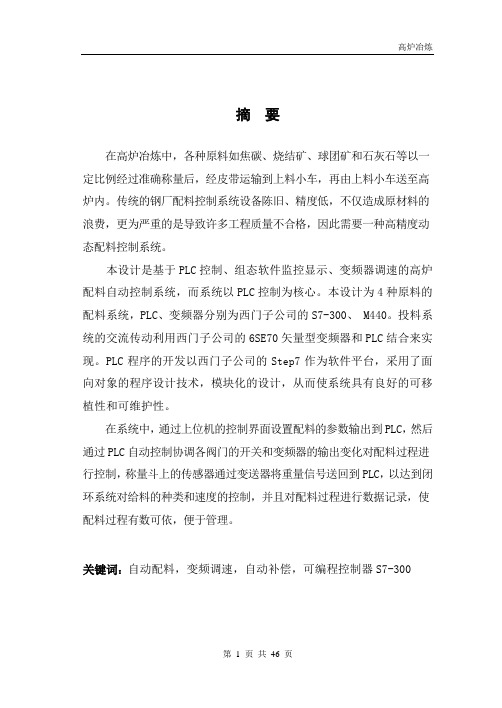
摘要在高炉冶炼中,各种原料如焦碳、烧结矿、球团矿和石灰石等以一定比例经过准确称量后,经皮带运输到上料小车,再由上料小车送至高炉内。
传统的钢厂配料控制系统设备陈旧、精度低,不仅造成原材料的浪费,更为严重的是导致许多工程质量不合格,因此需要一种高精度动态配料控制系统。
本设计是基于PLC控制、组态软件监控显示、变频器调速的高炉配料自动控制系统,而系统以PLC控制为核心。
本设计为4种原料的配料系统,PLC、变频器分别为西门子公司的S7-300、 M440。
投料系统的交流传动利用西门子公司的6SE70矢量型变频器和PLC结合来实现。
PLC程序的开发以西门子公司的Step7作为软件平台,采用了面向对象的程序设计技术,模块化的设计,从而使系统具有良好的可移植性和可维护性。
在系统中,通过上位机的控制界面设置配料的参数输出到PLC,然后通过PLC自动控制协调各阀门的开关和变频器的输出变化对配料过程进行控制,称量斗上的传感器通过变送器将重量信号送回到PLC,以达到闭环系统对给料的种类和速度的控制,并且对配料过程进行数据记录,使配料过程有数可依,便于管理。
关键词:自动配料,变频调速,自动补偿,可编程控制器S7-300引言研究背景随着课程的进度,我们开始了学业的最后部分——毕业设计。
经过了四年时间的学习,在老师的教导下,我们已经具备了一定基础,为了能够将所学联系起来,较好的应用到生产当中去,我们就需要在毕业设计中好好的锻炼自己。
在毕业设计中,我选择了这样一个题目就是为了能较好的锻炼自己的应用能力以及分析问题、解决问题的能力。
本设计的题目为高炉上料PLC控制系统,为工程类项目,是高炉冶炼中的一部分。
在高炉冶炼中,为了能高质量地进行冶炼,需要将各种原料按照一定的重量和比例准确地添加到高炉中。
传统的钢厂配料控制系统设备陈旧、精度低,不仅造成原材料的浪费,更为严重的是导致许多工程质量不合格,因此需要一种高精度动态配料控制系统。
PLC课程设计自动加料的PLC控制系统设计

软件设计注意 事项:确保程 序的稳定性、 安全性和可维 护性,以及与 硬件的兼容性。
PLC控制系统的通信设计
通信协议:选择合适的通信协议,如Modbus、Profibus等 通信接口:确定PLC与上位机、传感器等设备的通信接口,如RS232、RS485等 通信速率:根据系统需求选择合适的通信速率,如9600bps、19200bps等 通信距离:考虑通信距离,选择合适的通信介质,如双绞线、光纤等
等。
自动加料系统的基本原理
自动加料系统主要由PLC控制器、传感器、 执行器等组成
传感器检测物料的存量,并将信号传递给 PLC控制器
PLC控制器根据预设的加料程序,控制执 行器进行加料操作
执行器根据PLC控制器的指令,进行加料 操作,实现物料的自动补充
自动加料系统可以保证物料的连续供应, 提高生产效率,减少人工操作
安全性:确保 PLC控制系统 和自动加料系 统的安全性, 避免出现安全
事故。
准确性:确保 PLC控制系统 和自动加料系 统的准确性, 避免出现误差
或错误。
可维护性:确 保PLC控制系 统和自动加料 系统的可维护 性,便于进行 维护和维修。
兼容性:确保 PLC控制系统 和自动加料系 统的兼容性, 便于与其他设 备或系统进行 连接和通信。
案例二:某化工厂的自动加料系统与PLC控制系统的集成案 例
化工厂背景:某大型化工厂,生产多种化工产品
自动加料系统:采用PLC控制系统,实现自动加料
PLC控制系统:采用Siemens S7-1200 PLC,实现对自动加料系统的 控制
集成效果:提高了生产效率,降低了人工成本,提高了产品质量
案例三:某食品加工厂的自动加料系统与PLC控制系统的集 成案例
自动装料系统的plc控制课程设计
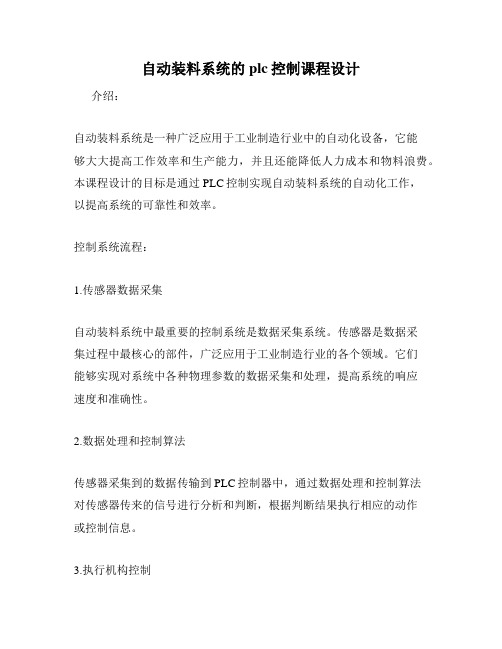
自动装料系统的plc控制课程设计介绍:自动装料系统是一种广泛应用于工业制造行业中的自动化设备,它能够大大提高工作效率和生产能力,并且还能降低人力成本和物料浪费。
本课程设计的目标是通过PLC控制实现自动装料系统的自动化工作,以提高系统的可靠性和效率。
控制系统流程:1.传感器数据采集自动装料系统中最重要的控制系统是数据采集系统。
传感器是数据采集过程中最核心的部件,广泛应用于工业制造行业的各个领域。
它们能够实现对系统中各种物理参数的数据采集和处理,提高系统的响应速度和准确性。
2.数据处理和控制算法传感器采集到的数据传输到PLC控制器中,通过数据处理和控制算法对传感器传来的信号进行分析和判断,根据判断结果执行相应的动作或控制信息。
3.执行机构控制PLC控制器会通过执行机构控制指令,将处理后的控制信息输出到执行机构,实现对自动装料系统的自动化控制。
重点内容:1.数据采集和处理系统设计数据采集和处理系统的设计是本课程设计的重点之一。
需要通过对传感器和PLC控制器的相互配合,实现对系统中各种物理参数的数据采集和处理功能。
例如应用超声波传感器,通过测量物料的高度来判断料槽中的物料是否达到了预定的装料量,从而发出控制信号控制机械臂的动作以装载物料。
2.控制算法的设计与实现控制算法的设计与实现是实现自动装料系统的关键。
系统需要根据不同的物料和机械臂结构进行优化调试,以实现在各种情况下的稳定和高效运行。
例如在机械臂空载或满载时,需要对机械臂的速度和加速度进行调整,以保证其运动速度的稳定和安全;在物料液位过高或过低时,需要根据实时反馈的数据进行动态调整,保证物料的装载量准确和稳定。
3.执行机构控制系统的设计执行机构控制系统是本课程设计的另一个重点。
主要包括机械臂、电动脉冲阀等机械结构的设计和制造,以及PLC控制器对这些机械结构的调试和控制。
例如在机械臂的结构设计中,需要考虑其防抖动和抗干扰的能力,以保证其在高速运动时的稳定性和精度;在电动脉冲阀的选择和开发中,需要考虑其反应速度、信号处理能力和耐用性等因素。
自动生产线物料供给单元的PLC控制
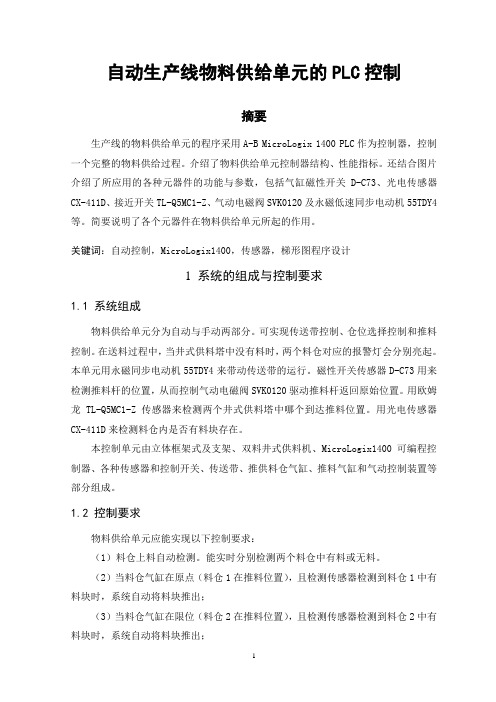
自动生产线物料供给单元的PLC控制摘要生产线的物料供给单元的程序采用A-B MicroLogix 1400 PLC作为控制器,控制一个完整的物料供给过程。
介绍了物料供给单元控制器结构、性能指标。
还结合图片介绍了所应用的各种元器件的功能与参数,包括气缸磁性开关D-C73、光电传感器CX-411D、接近开关TL-Q5MC1-Z、气动电磁阀SVK0120及永磁低速同步电动机55TDY4等。
简要说明了各个元器件在物料供给单元所起的作用。
关键词:自动控制,MicroLogix1400,传感器,梯形图程序设计1 系统的组成与控制要求1.1 系统组成物料供给单元分为自动与手动两部分。
可实现传送带控制、仓位选择控制和推料控制。
在送料过程中,当井式供料塔中没有料时,两个料仓对应的报警灯会分别亮起。
本单元用永磁同步电动机55TDY4来带动传送带的运行。
磁性开关传感器D-C73用来检测推料杆的位置,从而控制气动电磁阀SVK0120驱动推料杆返回原始位置。
用欧姆龙TL-Q5MC1-Z传感器来检测两个井式供料塔中哪个到达推料位置。
用光电传感器CX-411D来检测料仓内是否有料块存在。
本控制单元由立体框架式及支架、双料井式供料机、MicroLogix1400可编程控制器、各种传感器和控制开关、传送带、推供料仓气缸、推料气缸和气动控制装置等部分组成。
1.2 控制要求物料供给单元应能实现以下控制要求:(1)料仓上料自动检测。
能实时分别检测两个料仓中有料或无料。
(2)当料仓气缸在原点(料仓1在推料位置),且检测传感器检测到料仓1中有料块时,系统自动将料块推出;(3)当料仓气缸在限位(料仓2在推料位置),且检测传感器检测到料仓2中有料块时,系统自动将料块推出;(4)当推料气缸在原点时,如果料仓1内检测到没有料块,而料仓2内检测到有料块时,料仓气缸动作,将料仓2移动到推料位置,将料块推出;(5)当推料气缸在限位时,如果料仓2内检测到没有料块,而料仓1内检测到有料块时,料仓气缸动作,将料仓1移动到推料位置,将料块推出;(6)当料块从料仓被推出时,传送带动作,将料块运送到下一个单元。
PLC在工业自动化过程控制中的应用
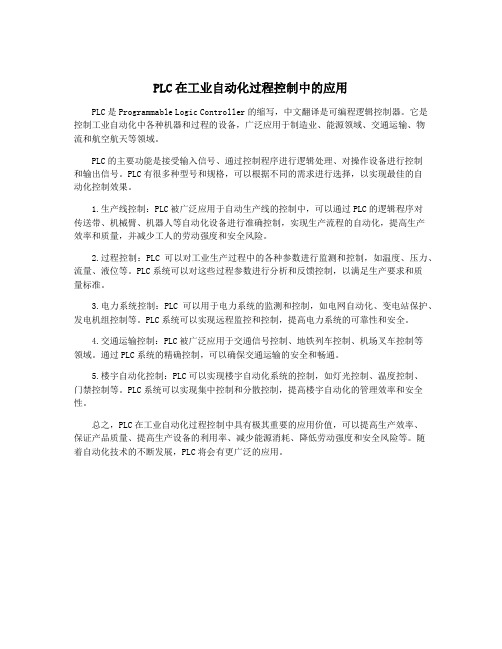
PLC在工业自动化过程控制中的应用PLC是Programmable Logic Controller的缩写,中文翻译是可编程逻辑控制器。
它是控制工业自动化中各种机器和过程的设备,广泛应用于制造业、能源领域、交通运输、物流和航空航天等领域。
PLC的主要功能是接受输入信号、通过控制程序进行逻辑处理、对操作设备进行控制和输出信号。
PLC有很多种型号和规格,可以根据不同的需求进行选择,以实现最佳的自动化控制效果。
1.生产线控制:PLC被广泛应用于自动生产线的控制中,可以通过PLC的逻辑程序对传送带、机械臂、机器人等自动化设备进行准确控制,实现生产流程的自动化,提高生产效率和质量,并减少工人的劳动强度和安全风险。
2.过程控制:PLC可以对工业生产过程中的各种参数进行监测和控制,如温度、压力、流量、液位等。
PLC系统可以对这些过程参数进行分析和反馈控制,以满足生产要求和质量标准。
3.电力系统控制:PLC可以用于电力系统的监测和控制,如电网自动化、变电站保护、发电机组控制等。
PLC系统可以实现远程监控和控制,提高电力系统的可靠性和安全。
4.交通运输控制:PLC被广泛应用于交通信号控制、地铁列车控制、机场叉车控制等领域。
通过PLC系统的精确控制,可以确保交通运输的安全和畅通。
5.楼宇自动化控制:PLC可以实现楼宇自动化系统的控制,如灯光控制、温度控制、门禁控制等。
PLC系统可以实现集中控制和分散控制,提高楼宇自动化的管理效率和安全性。
总之,PLC在工业自动化过程控制中具有极其重要的应用价值,可以提高生产效率、保证产品质量、提高生产设备的利用率、减少能源消耗、降低劳动强度和安全风险等。
随着自动化技术的不断发展,PLC将会有更广泛的应用。
自动化生产线供料单元 PLC的自动化生产线__供料单元的结构与控制
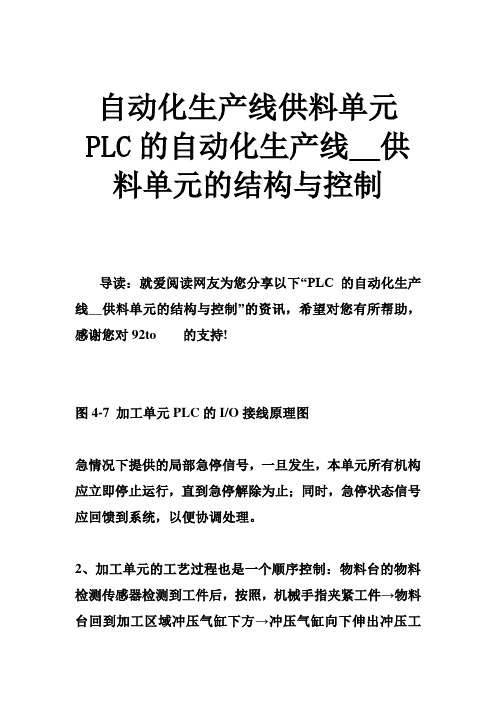
自动化生产线供料单元PLC的自动化生产线__供料单元的结构与控制导读:就爱阅读网友为您分享以下“PLC的自动化生产线__供料单元的结构与控制”的资讯,希望对您有所帮助,感谢您对92to 的支持!图4-7 加工单元PLC的I/O接线原理图急情况下提供的局部急停信号,一旦发生,本单元所有机构应立即停止运行,直到急停解除为止;同时,急停状态信号应回馈到系统,以便协调处理。
2、加工单元的工艺过程也是一个顺序控制:物料台的物料检测传感器检测到工件后,按照,机械手指夹紧工件→物料台回到加工区域冲压气缸下方→冲压气缸向下伸出冲压工件→完成冲压动作后向上缩回→物料台重新伸出→到位后机械手指松开的顺序完成工件加工工序,并向系统发出加工完成信号。
下面给出YL-335A出厂例程中加工单元程序清单供读者在实训时参考。
主程序如图4-9 所示,它只是在每一扫描周期(SM0.0 ON)调用2个子程序,一个是启动/停止子程序,其功能是在读取主站发送来的控制命令以及把本站状态信号写到通信数据存储区。
另一个子程序则是完成加工工艺控制功能。
图4-9 加工站主程序梯形图启动/停止子程序如图4-10所示图4-10 启动/停止子程序梯形图第六章分拣单元的结构与控制分拣单元的结构组成如图6-2所示。
其主要结构组成为:传送和分拣机构,传动机构,变频器模块,电磁阀组,接线端口,PLC模块,底板等。
传送和分拣机构如图6-3所示。
传送已经加工、装配好的工件,在光纤传感器检测到并进行分拣。
它主要由传送带、物料槽、推料(分拣)气缸、漫射式光电传感器、光纤传感器、磁感应接近式传感器组成。
传送带是把机械手输送过来加工好的工件进行传输,输送至分拣区。
导向件是用纠偏机械手输送过来的工件。
两条物料槽分别用于存放加工好的黑色工件和白色工件。
传送和分拣的工作原理:本站的功能是完成从装配站送来的装配好的工件进行分拣。
当输送站送来工件放到传送带上并为入料口漫射式光电传感器检测到时,将信号传输给PLC,通过PLC的程序启动变频器,电机运转驱动传送带工作,把工件带进分拣区,如果进入分拣区工件为白色,则检测白色物料的光纤传感器动作,作为1号槽推料气缸启动信号,将白色料推到1号槽里,如果进入分拣区工件为黑色,检测黑色的光纤传感器作为2号槽推料气缸启动信号,将黑色料推到2号槽里。
基于PLC的自动配料控制系统设计
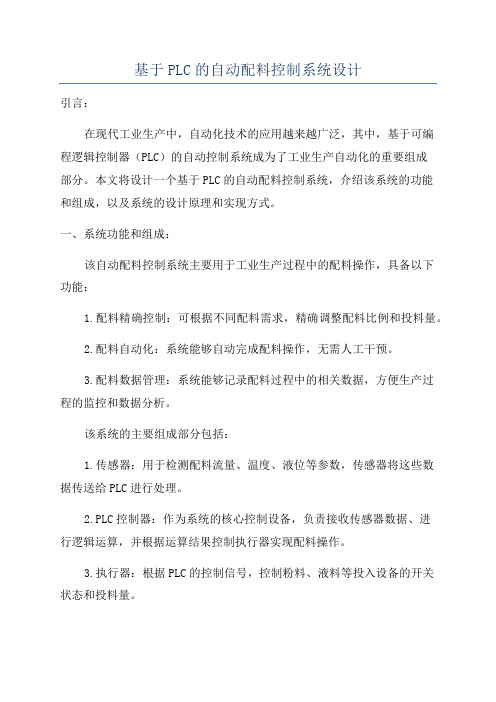
基于PLC的自动配料控制系统设计引言:在现代工业生产中,自动化技术的应用越来越广泛,其中,基于可编程逻辑控制器(PLC)的自动控制系统成为了工业生产自动化的重要组成部分。
本文将设计一个基于PLC的自动配料控制系统,介绍该系统的功能和组成,以及系统的设计原理和实现方式。
一、系统功能和组成:该自动配料控制系统主要用于工业生产过程中的配料操作,具备以下功能:1.配料精确控制:可根据不同配料需求,精确调整配料比例和投料量。
2.配料自动化:系统能够自动完成配料操作,无需人工干预。
3.配料数据管理:系统能够记录配料过程中的相关数据,方便生产过程的监控和数据分析。
该系统的主要组成部分包括:1.传感器:用于检测配料流量、温度、液位等参数,传感器将这些数据传送给PLC进行处理。
2.PLC控制器:作为系统的核心控制设备,负责接收传感器数据、进行逻辑运算,并根据运算结果控制执行器实现配料操作。
3.执行器:根据PLC的控制信号,控制粉料、液料等投入设备的开关状态和投料量。
4.人机界面:提供一个友好的操作界面,供操作员输入配料参数、查看配料数据等。
二、系统设计原理和实现方式:1.传感器的应用:通过给配料过程中的关键参数(如流量、温度、液位)配置相应的传感器,将实时的数据通过模拟量或数字量输入模块传送给PLC进行处理。
2. PLC的控制:PLC使用逻辑运算单元(Ladder Diagram)进行逻辑控制。
根据传感器数据和预设的配料参数,PLC能够判断哪些配料需要进行投料,调整投料设备的开关状态和投料量。
3.执行器的控制:PLC将控制信号发送给执行器,执行器根据信号的状态进行相应的操作,控制粉料、液料等的投入设备。
4.人机界面的设计:采用触摸屏、按钮等电子元件实现人机交互,提供一个用户友好的操作界面,操作员可以输入配料参数、查看配料数据等。
三、系统优势和应用前景:1.提高生产效率:系统能够自动完成配料操作,减少人工操作的时间和精力投入。
PLC在工业自动化中的应用:自动化生产线控制之案例分享

PLC在工业自动化中的应用:自动化生产线控制之
案例分享
PLC在工业自动化中的应用有很多具体实例。
以下是一些常见的应用案例:1.自动化生产线控制:在生产线中,PLC可以控制各种机械和电子设备,如
机器人、传送带、电动机和传感器等,处理输入信号,进行逻辑运算,并产生输出信号来控制设备的运行顺序、速度和位置等。
2.工厂设备控制:PLC可以用于控制和监控工厂中的各种设备,如压力机、
注塑机、起重机、气体处理设备等,确保它们按照预定的程序和参数进行操作,从而提高生产效率和质量。
3.自动化仓储系统:PLC可以控制自动化仓储系统中的输送设备、堆垛机、
拣选机器人等,管理货物的存储、检索和分拣过程,实现高效的仓储管理。
4.汽车制造:在汽车制造过程中,PLC被广泛应用于控制汽车组装线上的各
个工作站和机器,协调不同工序的顺序和时间,确保零部件的正确安装和车辆的顺利生产。
5.电力系统控制:在电力系统中,PLC可以用于监控和控制发电厂、输电线
路和配电系统等。
此外,PLC在矿业、食品、物流、医疗等多个行业都有广泛的应用,能够实现各种生产设备和机器的自动化控制、监测和安全保障。
PLC的自动化生产线供料单元的结构与控制要点
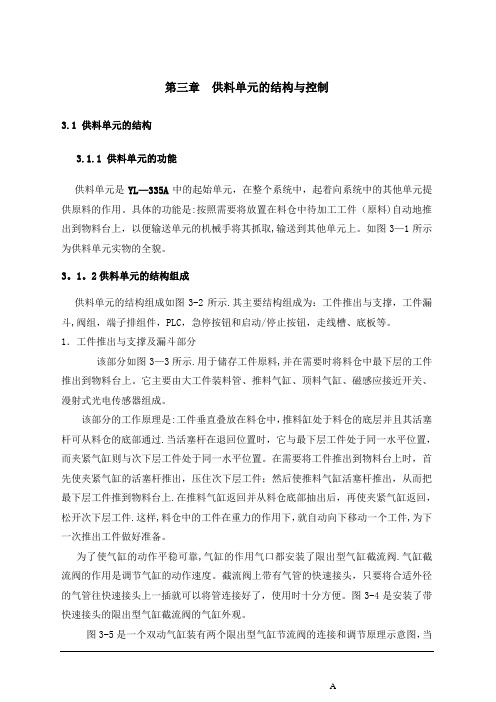
第三章供料单元的结构与控制3.1 供料单元的结构3.1.1 供料单元的功能供料单元是YL—335A中的起始单元,在整个系统中,起着向系统中的其他单元提供原料的作用。
具体的功能是:按照需要将放置在料仓中待加工工件(原料)自动地推出到物料台上,以便输送单元的机械手将其抓取,输送到其他单元上。
如图3—1所示为供料单元实物的全貌。
3。
1。
2供料单元的结构组成供料单元的结构组成如图3-2所示.其主要结构组成为:工件推出与支撑,工件漏斗,阀组,端子排组件,PLC,急停按钮和启动/停止按钮,走线槽、底板等。
1.工件推出与支撑及漏斗部分该部分如图3—3所示.用于储存工件原料,并在需要时将料仓中最下层的工件推出到物料台上。
它主要由大工件装料管、推料气缸、顶料气缸、磁感应接近开关、漫射式光电传感器组成。
该部分的工作原理是:工件垂直叠放在料仓中,推料缸处于料仓的底层并且其活塞杆可从料仓的底部通过.当活塞杆在退回位置时,它与最下层工件处于同一水平位置,而夹紧气缸则与次下层工件处于同一水平位置。
在需要将工件推出到物料台上时,首先使夹紧气缸的活塞杆推出,压住次下层工件;然后使推料气缸活塞杆推出,从而把最下层工件推到物料台上.在推料气缸返回并从料仓底部抽出后,再使夹紧气缸返回,松开次下层工件.这样,料仓中的工件在重力的作用下,就自动向下移动一个工件,为下一次推出工件做好准备。
为了使气缸的动作平稳可靠,气缸的作用气口都安装了限出型气缸截流阀.气缸截流阀的作用是调节气缸的动作速度。
截流阀上带有气管的快速接头,只要将合适外径的气管往快速接头上一插就可以将管连接好了,使用时十分方便。
图3-4是安装了带快速接头的限出型气缸截流阀的气缸外观。
图3-5是一个双动气缸装有两个限出型气缸节流阀的连接和调节原理示意图,当调节节流阀A时,是调整气缸的伸出速度,而当调节节流阀B时,是调整气缸的缩回速度。
从图3—4上可以看到,气缸两端分别有缩回限位和伸出限位两个极限位置,这两个极限位置都分别装有一个磁感应接近开关,如图3-6(a)所示。
「自动送料装车系统PLC控制设计」

「自动送料装车系统PLC控制设计」自动送料装车系统是一种可以实现自动化物料输送和装车的系统。
PLC(可编程序逻辑控制器)是一种常用于工业自动化控制的设备,用于控制和管理自动化设备的运行。
在设计自动送料装车系统的PLC控制时,需要考虑以下几个方面:1.传感器和执行器的选择:传感器用于检测物料的位置、数量和状态,执行器用于控制物料的运动。
根据具体需求,可以选择适合的传感器和执行器,并将它们连接到PLC上。
2.输入和输出界面的设计:PLC通常具有输入和输出接口,用于与外部设备进行数据交换。
输入接口可用于接收来自传感器的信号,输出接口可用于控制执行器的运动。
设计输入和输出界面时,要考虑设备连接的类型和数量,并确定合适的接口类型和数量。
3.控制逻辑的编程:PLC控制逻辑的编程是实现自动送料装车系统的关键。
根据系统的工作流程和需求,设计适当的控制算法和逻辑,编写PLC程序。
程序中应包括物料输送的控制、装车操作的控制以及故障检测和处理等功能。
4.故障检测和处理机制的设计:自动送料装车系统在运行过程中可能会出现各种故障,如传感器故障、执行器故障等。
为了确保系统的稳定和可靠性,需要设计故障检测和处理机制。
可以通过监测传感器和执行器的状态来检测故障,并采取相应的措施进行处理,例如报警、停止系统运行等。
综上所述,自动送料装车系统的PLC控制设计需要考虑传感器和执行器的选择、输入和输出界面的设计、控制逻辑的编程以及故障检测和处理机制的设计。
通过合理的设计和编程,可以实现自动化物料输送和装车,提高生产效率和质量。
PLC在生产线控制中的应用案例

PLC在生产线控制中的应用案例PLC 在生产线控制中的应用案例在现代工业领域,自动化生产线已经成为提高效率和降低成本的重要手段之一。
而可编程逻辑控制器(PLC)作为控制自动化生产线的核心设备之一,因其稳定可靠、灵活扩展等特点而被广泛应用于各个行业。
本文将介绍一个在生产线控制中应用 PLC 的实际案例,展示其在提高生产效率和质量控制方面的优势。
案例描述:某家汽车零部件制造工厂生产线上,存在着多个工序需要协同工作。
在传统的生产方式下,各个工序之间需要人工干预来完成工作任务,无法实现高效自动化的流程控制,导致生产效率低下和质量难以控制。
为解决这个问题,工厂决定引入 PLC 控制系统。
方案实施:1. 系统模块设计:针对生产线上的各个工序和对应的设备,设计了相应的控制模块,并将其连接到 PLC 控制器上。
这些模块包括传感器模块、执行模块、输入输出模块等。
传感器模块用于采集实时的工艺参数,执行模块用于控制各个执行器的动作,输入输出模块用于与外部设备进行交互。
2. 逻辑程序编写:基于生产线上的工艺流程和控制要求,编写了 PLC 的逻辑程序。
逻辑程序定义了各个工序之间的协同关系和相应的控制逻辑。
通过编写适当的程序语句和流程控制指令,实现了自动化生产线上的流程控制。
此外,逻辑程序还包括了错误处理和异常情况的处理等机制,以确保生产线的稳定运行。
3. 联机调试和优化:在完成逻辑程序编写后,对PLC 控制系统进行了联机调试和优化。
通过与实际生产线的协同工作,检验了程序的正确性和稳定性,并对其中存在的问题进行了调整和改进。
在调试过程中,利用 PLC 提供的实时监控和诊断功能,及时发现并解决了潜在的故障和异常情况。
4. 实施效果:引入PLC 控制系统后,工厂的生产线控制方面出现了显著的改善。
首先,生产效率大大提高,因为各个工序之间能够无缝衔接,减少了人为操作和等待时间。
其次,生产质量得到了有效控制,因为 PLC 控制系统具备高精度和高稳定性,能够做到精确的动作控制和工艺参数监控。
自动化生产线中的PLC编程与控制策略

自动化生产线中的PLC编程与控制策略自动化生产线在现代工业领域中扮演着至关重要的角色。
为了实现高效、安全和可靠的生产,PLC(可编程逻辑控制器)编程和控制策略的设计变得尤为关键。
本文将探讨在自动化生产线中的PLC编程与控制策略,并介绍其应用和优势。
一、PLC编程的基础PLC作为自动化生产线控制的关键设备,具有高度灵活性和可编程性。
PLC编程的基础是使用类似于传统电气电路的逻辑元件定义控制程序。
这些逻辑元件包括输入、输出、中继、定时器和计数器等。
通过逻辑元件及其相互之间的逻辑关系,我们可以实现对生产线各个部分的控制。
在PLC编程中,使用一种称为“梯形图”的图形化编程语言是常见的。
梯形图是以梯子形状进行表示的,每一横栏表示一个逻辑元件的状态。
通过将逻辑元件的输入和输出进行连接,我们可以构建复杂的控制程序。
二、PLC控制策略的设计在自动化生产线中,PLC的控制策略非常重要。
有效的控制策略可以提高生产线的吞吐量、减少故障率并降低人员的操作负担。
以下是几种常见的PLC控制策略:1. 顺序控制策略顺序控制是在自动化生产线中最基本的控制策略之一。
通过设定不同的工序顺序和间隔时间,PLC可以按照设定的步骤自动控制机器和设备的操作。
顺序控制可以提高生产效率,降低故障风险,实现产品的高质量和稳定输出。
2. 工艺控制策略工艺控制涉及到对生产过程中各种参数的控制和监测。
通过PLC编程,在生产线中可以实现温度、压力、速度等参数的自动调节和监控。
这种控制策略可以提高产品的一致性和质量稳定性,减少人为因素对生产过程的影响。
3. 故障检测与报警策略PLC编程还可以设计故障检测和报警策略,提前发现和诊断生产线中的故障,并及时报警。
通过监测各个设备的状态和特定的故障标识,PLC可以在出现故障时迅速停止相关操作,并发送报警信息给操作人员,以便及时处理。
三、PLC编程与控制策略的应用PLC编程和控制策略的应用非常广泛,几乎涵盖了所有需要自动化控制的工业领域。
PLC控制的变频器在自动化生产线中的应用

PLC控制的变频器在自动化生产线中的应用1. 电机的启停控制在自动化生产线中,有许多设备需要定时启停,而变频器能够通过PLC的控制实现电机的精准启停。
PLC控制变频器的频率输出,从而实现电机的启停控制,避免了电机频繁启停带来的损坏和能耗增加。
2. 电机的速度调节在生产线中,有些需要根据生产需求调整工作速度的设备,而变频器可根据PLC的控制信号调整电机的工作频率,实现电机的速度调节。
这样不仅提高了生产线的生产效率,还能够有效地保护设备和节约能源。
3. 生产线整体调度PLC控制的变频器能够实现生产线整体的调度控制。
当需要对整条生产线进行调度和控制时,PLC通过控制各个变频器的频率输出,实现整条生产线的协调运行。
4. 传感器信号处理在自动化生产线中,有许多传感器用于检测设备运行状态,而传感器发出的信号需要通过变频器进行处理。
PLC通过控制变频器的工作频率和输出信号,实现对传感器信号的处理和解析,从而确保生产线的正常运行。
5. 故障诊断和报警PLC控制的变频器能够实时监测设备的运行状态,一旦发现设备出现异常情况,立即通过变频器发出报警信号,并将故障信息传输给PLC。
PLC能够根据接收到的故障信息及时进行诊断,并对故障设备进行处理,从而保障生产线的正常运行。
2. 灵活可靠PLC控制的变频器能够根据生产需求灵活调整设备的运行状态,实现对生产线的精准控制。
变频器具有较高的抗干扰能力和稳定性,能够适应不同的生产环境,保障生产线的可靠运行。
4. 便于维护管理PLC控制的变频器具有较高的自动化水平,能够实现对设备的自动诊断和报警,帮助企业及时发现和处理设备故障,提高了生产线的可维护性和可管理性。
四、总结PLC控制的变频器在自动化生产线中的应用,不仅提高了生产效率和产品质量,而且降低了生产成本,对企业的可持续发展具有重要意义。
未来,随着工业自动化水平的不断提高,PLC控制的变频器将在更多领域发挥重要作用,为企业创造更大的经济价值。
配料生产线控制系统的PLC自动控制

工业控制
配料生产线控制系统的 PLC 自动控制
罗及红
(湖南商务职业技术学院电控系, 湖南长沙 410205)
摘要: 为 了 实 现 典 型 配 料 生 产 线 系 统 的 实 际 控 制 要 求 , 运 用 三 菱 PLC 技 术 中 的 顺 序 控 制 步 进 STL 指 令 和 PLC 置 位 、 复 位 基 本 指
[7] 宋清, 邓捷, 邱润才. 配方奶粉生产线全自动程序化控制系
统的研发 [J] . 中国乳业, 2006 (7): 43-43. [8] 赵迎春. 基于 PLC 的自动化电镀生产线控制 系 统 [J] . 中 国
高新技术企业, 2009 (5): 9-10.
作 者 简 介 : 罗 及 红 , 男 , 1970 年 生 , 湖 南 长 沙 人 , 硕 士 , 讲 师 。 研究领域: 电气自动化。
[J] . 华中科技大学学报 (自然科学版), 2002 (4): 20-22. [2] 董秀洁, 苗凤君. 提高 PLC 控制系统可靠性 的 措 施 [J] . 郑
州纺织工学院学报, 1998, 9 (3): 80-82, 94. [3] 高 钦 和. PLC 控 制 系 统 故 障 检 测 与 处 理 功 能 的 实 现 [J] . 计
(3) Modbus 和 Modbus Plus 口地址 的 自 动 切 换 可 实 现 主机的透明通讯, 不需要专门的驱动设备。
(4) 所有的 I / O 模块均可在不影响控制系统正常操作 的情况下带电插拔。
(5) 在通讯失败的情况下, 所有离散量和模拟量 I / O 的输出均可设置为下述 3 种状态之一: 所有输出关断、 保 持最后的输出值或预定义的输出状态。 这种的选择能够保 证在通讯中断的情况下, 整个系统有计划地运行。
基于PLC的自动配料控制系统的研究

基于PLC的自动配料控制系统的研究随着工业自动化的快速发展,PLC(可编程逻辑控制器)在自动化控制领域的应用越来越广泛。
其中,基于PLC的自动配料控制系统成为了不可忽视的研究方向。
本文将从系统的基本原理、系统的优势以及未来发展方向等方面对基于PLC的自动配料控制系统进行研究。
基于PLC的自动配料控制系统的基本原理是通过PLC对物料的输送、称量、混合等过程进行控制。
系统一般包括物料输送装置、称量装置、混合装置以及PLC控制系统等组成部分。
物料输送装置负责将需要配料的物料输送到称量装置,称量装置通过传感器对物料进行精确称量,然后将称量的物料送到混合装置进行混合。
PLC控制系统根据预设的配方,通过对各个装置的控制,实现对配料过程的自动控制。
基于PLC的自动配料控制系统相较于传统的手动控制方式具有多方面的优势。
首先,系统大大提高了生产效率。
自动化控制系统可以实现物料的连续输送、精确称量和高效混合,大大减少了人力投入和生产时间。
其次,系统提高了产品质量的稳定性。
自动化控制可以减少人为因素对配料过程的影响,保证了每次配料的准确性和一致性。
此外,系统具有可编程的特点,可以实现不同配料要求下的灵活调整,提高了生产的适应性。
最后,系统的可靠性和安全性也得到了增强。
PLC控制系统具有自我诊断和故障保护功能,当发生异常情况时能及时进行报警和停机保护,保证了设备和人员的安全。
基于PLC的自动配料控制系统还有许多待发展的方向。
首先,可以进一步提高系统的可扩展性和智能化水平。
通过加入更多的传感器和设备,实现对配料过程更全面的监测和控制,使系统变得更智能化。
其次,可以进一步优化系统的人机界面。
提供更直观、友好的操作界面,使系统的使用更加方便和易于操作。
同时,可以将系统与远程监控和管理系统进行整合,实现对生产过程的远程监控和智能管理。
另外,基于PLC的自动配料控制系统还可以与其他工业自动化技术相结合,如无人机技术、物联网等,实现生产线的智能化和自动化。
- 1、下载文档前请自行甄别文档内容的完整性,平台不提供额外的编辑、内容补充、找答案等附加服务。
- 2、"仅部分预览"的文档,不可在线预览部分如存在完整性等问题,可反馈申请退款(可完整预览的文档不适用该条件!)。
- 3、如文档侵犯您的权益,请联系客服反馈,我们会尽快为您处理(人工客服工作时间:9:00-18:30)。
自动化生产线自动上料站的PLC控制
摘要:目前,一种基于PLC技术的自动化生产线教学实训系统,通过自动上料、检测传输、自动分拣和装配等工序设计,将机电气驱动技术、传感器技术、PLC技术及网络控制技术的综合实训集于一身,是培养和提高学生专业综合能力的重要实训设备。
本文阐述了该系统中自动上料站的设计过程,包括气动控制回路设计、PLC的硬件和程序设计。
关键词:气动PLC 模块自动上料
我校自主研发的自动化生产线是一套基于PLC控制的教学系统,也是一套模块化的生产实训系统。
它集电气控制、PLC应用、传感器和气动等多种技术于一体,由自动上料、传输检测、真空分拣、颜色分拣、位置调整、配件供给和装配下料等七个工作站组成。
自动上料站的功能是为其它工作站提供工件。
工件由气动机械手抓取,经平移,升降,摆动等动作,放到输送带上,然后回归原位。
1 系统的硬件设计
自动上料模块是整个自动生产线系统的起始单元,主要由工件装料管和推出装置、支架、阀组、端子排组件、PLC、按钮、走线槽及底板等组成。
主要功能是将放置在料仓中的工件自动推到物料盘上,以便使输送单元的机械手将其抓取并输送。
具有手动、自动两种操作方式。
在操作前应确保上料盘有料。
1.1 动作过程
上料单元主体是一个转动的料盘,料盘上设置两个管形料仓。
在料盘口对应上料的位置安装了一个漫反射光电开关,功能是检测料盘口中有无储料。
当工件到达料盘口时,光电开关检测到有工件存在,便向系统提供本单元物料盘有工件的信号。
在输送单元的控制程序中,就可以利用该信号状态来驱动机械手装置来抓取此工件,送到传输带上。
料仓中的工件在重力的作用下,自动向下移动一个工件,为下一次抓取工件做好准备。
若当前料盘口中无工件,料盘将在程序控制下转动到料盘口中继续检测。
直到两个料盘口均无工件,料盘停止转动。
1.2 气动回路设计
气动控制回路是本工作单元的执行机构,由气动机械手和上料转盘组成,完成上料和取料。
机械手在结构上由两个直线气缸、一个摆动气缸和气爪组成。
归位状态为:气爪闭,平移缸退,升降缸落,摆缸0°。
一个工作循环:气爪闭→气爪开→升降缸升→平移缸进→气爪闭→平移缸退→摆缸180°→平移缸进→升降缸落→气爪开→平移缸退→升降缸升→摆缸0°。
机械手可实现手臂平移、升降、摆动和气爪的抓取动作,由安装在气缸p
2 系统的软件设计
PLC梯形图程序的设计方法有经验法和顺序控制法两种。
顺序控制设计法的基本思想是将系统的一个工作周期划分为若干个顺序相
连的步,用编程元件(例如存储器位M)来代表,在任何一步内各输出量的状态不变。
使系统由当前步进入下一步的信号称为转换条件,它可以是外部的输入信号,如按钮、限位开关的通断等。
也可以是PLC内部产生的信号,如定时器和计数器的触点信号。
使用顺序控制设计方法时,首先根据系统的工艺流程,画出如图2所示的顺序功能图,再根据顺序功能图画出梯形图来完成程序设计。
参考文献
[1]廖常初.PLC编程及应用[M].北京:机械工业出版社,2005.
[2]左健民.液压与气压传动[M].北京:机械工业出版社,1999.
[3]符林芳.液压与气压传动技术[M].北京:北京理工大学出版社,2010.。