高速切削技术在薄套类零件加工中的应用研究
薄壁零件的加工特点及工艺分析

薄壁零件的加工特点及工艺分析机械加工肯定少不了薄壁零件的加工,而这类零件加工更需要仔细认真,所以了解其加工特点及工艺很有必要。
以下是店铺为你整理推荐薄壁零件的加工特点及工艺分析,希望你喜欢。
薄壁零件的加工特点1)易受力变形:因工件壁薄,在夹紧力的作用下容易产生变形,从而影响工件的尺寸精度和形状精度;(2)易受热变形:因工件较薄,切削热会引起工件热变形,使工件尺寸难于控制;(3)易振动变形:在切削力(特别是径向切削力)的作用下,容易产生振动和变形,影响工件的尺寸精度、形状、位置精度和表面粗糙度。
薄壁零件的加工工艺薄壁零件加工精度的容易受到多方面因素的影响,归纳起来主要有以下三方面:(1)受力变形;(2)受热变形;(3)振动变形。
如果采用传统的数控加工工艺,很难加工出符合精度要求的薄壁零件,甚至使薄壁产生破裂。
主要原因如下:(1)在粗加工时,切削量较大,在切削力、夹紧力、残余应力和切削热的作用下,会使薄壁产生一定程度的变形。
(2)半精加工和精加工时,随着材料的去除,工件的刚度已降至非常低,薄壁部分的变形会进一步加剧。
因此,根据薄壁零件的结构特点和加工精度要求,对于薄壁零件,应尽可能选择高速切削技术来加工。
采用高速切削技术,可有效地降低切削力和切削热,消除工件的残余应力,以提高薄壁零件的尺寸稳定性,同时要兼顾加工效率。
除采用高速切削技术外,薄壁零件的加工,还要合理安排加工顺序,尽可能保证内外轮廓线依次交叉切削加工。
以进一步消除工件变形带来的尺寸误差。
薄壁零件的加工举例1、工序的划分本任务划分为两道工序,共分(1)工序一:薄壁加工;(2)工序二:铣凸台和椭圆槽。
(3)工序三:孔加工。
其中工序一是难点。
划分2个工步,具体加工顺序如下:(1)选择φ10 mm双刃键槽铣刀粗加工薄壁内外轮廓线,刀补值选8.3mm,留出半精加工余量,深度方向分层切削,留0.2mm余量;(2)换φ10 mm 四刃立铣刀,采用高速切削技术半精加工薄壁内外轮廓线,刀补值选8.1 mm,深度方向分别留0.1mm余量;(3)用φ10 mm四刃立铣刀,采用高速切削技术,精加工薄壁两条轮廓线,并根据实际测量尺寸控制零件加工精度。
高速铣削的技术特点及在模具加工的应用

削力很小,这就有利于加工复杂模具型腔中一些细筋和薄壁 , 其壁厚甚至可以小于 l m。业内已应用到薄壁的壁厚分别为 m 0r . m、0 m 2 a . m和 0 m 3 . m,薄壁高度为 2 m 4 0 m的特殊零件加工。
已成为先进制造技术 的一个重要组成部分。
随着市场竞争的需要 , 产品更新换代速度加快 , 对模具的生产效率和制造质量提出了越来越高的要求, 许多原来被认为
优秀的加工方法就逐渐暴露出问题 , 不适应时代的要求, 如电火花加工是一种靠放电烧蚀的“ 微切削” 工艺, 对工件表面进行
局部高温放电烧蚀, 加工后的型腔类零件一般还要进行费力、 费时的研磨和抛光 , 生产效率低, 在某种程度上制约了新产品 开发速度。高速铣削加工技术的出现,为模具制造技术开辟了一条崭新的道路,它能在较短的时间提供给客户满意的模具。
1高速铣削技术特点及模具加工的优越性
1 高速铣削技术缩短了模具的制造周期 . 1
高速铣削加工相对于传统的切削加工 ,由于切削机理不同,单位时间的金属材料切除率提高了 3% 6%,切削力降低 0 一0
了 3%, 0 刀具的切削寿命提高了7 %, 0 加工效率提高了, 从而缩短了产品的制造周期。 在模具的高淬硬钢件(R 4一 R 6) H C 5H C 5
结果整个凹模加工工效提高 5 ,表面粗糙度达 R O 5 0 1 倍 a. ~ .a 2 4m,质量完全符合要求。
1 高速铣削技术能加工形状复杂的薄壁模具零件 . 3 由高速L削机理可知, 刃 高速切削时, 加工余量小 , 切削力大为减少, 切削过程变得比较轻松。 高速切削可以加工淬火钢 ,
高速切削技术在薄壁零件加工中的应用研究

高速切削技术是诞生 于 2 0世纪 3 0年代 的一项 先 进 制造技术 ,其 采用超 硬材料 刀具和模具 ,利用高精
度 、高 自动化和高柔性的制造设备实现 了高效率 、高 柔性和高质量 的切 削加工 ,被称 为是 2 世 纪机械 制 1
造业 的一 场技术革命 ,在工程领 域的应用逐 渐成 熟 。由于高 速切 削技 术具 有 高 主轴 转 速 、高 进 给速 度 、低切削力和高切削速度等特点 ,能有效地缩短加 工时 间并降低加工 成本 ,加 工精 度高且 表面 质量好 , 符合薄壁箱体 生产 的发展趋势 ,因而获得广泛应用 。 作者针 对薄壁箱体零 件的工艺特点及生产实 际要 求 ,对薄壁箱体零件高速切削 的可行性进行 了分析 与
高速切削技术在薄壁零件加工中的应用研究
周 文 ( 南通纺织职业技术学院,江苏南通 260 ) 207
摘要 :从 薄壁箱体的加工效率 、加工精度等 角度出发 ,分析薄壁箱体零 件高速切 削加工 的优 势和可行 性。针对其 工艺 特点及生 产实际要求 ,分析高速加工 中存在 的工 艺问题 ,给出具体 的解决 措施 。实践 表明 :采用 高速切削加 工技术加 工薄 壁 箱体 ,加工效率高 ,工件表面质量好 。 关键词 :高速切削技术 ;加工效率 ;加 工精度 ;薄壁箱体零件
nn , te me s r s w r u o wad t e o v h r c s rb e f ma h nn . T e p a t e h w t a h p l ai n o ih i g h a u e e e p tfr r o r s le t e p o e s p o lms o c i i g h r ci s s o h tt e a p i t fh g — c c o s e d ma h n n e h o o y i c i i g t i — i k e sb x d s a e o k ic sc n g i ih e ce c n o d s ra e q a i . p e c i i g t c n lg n ma hn n n t c n s o e — h p d w r p e e a an h g f in y a d g o u f c u t h h i l y
数控高速切削加工技术的发展与应用研究
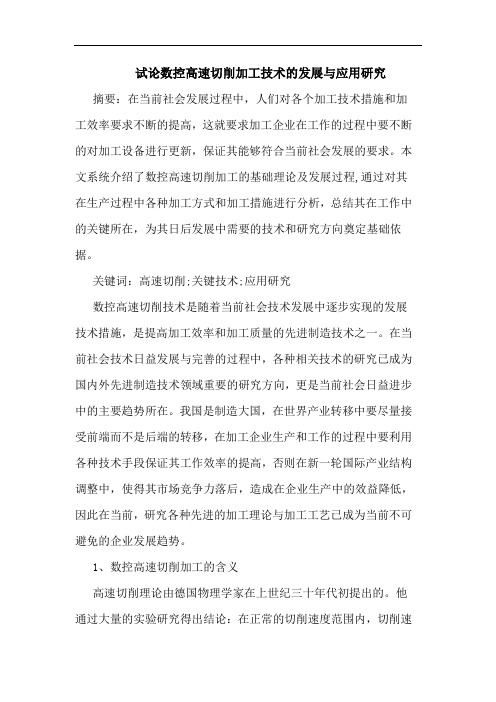
试论数控高速切削加工技术的发展与应用研究摘要:在当前社会发展过程中,人们对各个加工技术措施和加工效率要求不断的提高,这就要求加工企业在工作的过程中要不断的对加工设备进行更新,保证其能够符合当前社会发展的要求。
本文系统介绍了数控高速切削加工的基础理论及发展过程,通过对其在生产过程中各种加工方式和加工措施进行分析,总结其在工作中的关键所在,为其日后发展中需要的技术和研究方向奠定基础依据。
关键词:高速切削;关键技术;应用研究数控高速切削技术是随着当前社会技术发展中逐步实现的发展技术措施,是提高加工效率和加工质量的先进制造技术之一。
在当前社会技术日益发展与完善的过程中,各种相关技术的研究已成为国内外先进制造技术领域重要的研究方向,更是当前社会日益进步中的主要趋势所在。
我国是制造大国,在世界产业转移中要尽量接受前端而不是后端的转移,在加工企业生产和工作的过程中要利用各种技术手段保证其工作效率的提高,否则在新一轮国际产业结构调整中,使得其市场竞争力落后,造成在企业生产中的效益降低,因此在当前,研究各种先进的加工理论与加工工艺已成为当前不可避免的企业发展趋势。
1、数控高速切削加工的含义高速切削理论由德国物理学家在上世纪三十年代初提出的。
他通过大量的实验研究得出结论:在正常的切削速度范围内,切削速度如果提高,会导致切削温度上升,从而加剧了切削刀具的磨损;然而,当切削速度提高到某一定值后,只要超过这个拐点,随着切削速度提高,切削温度就不会升高,反而会下降,因此只要切削速度足够高,就可以很好的解决切削温度过高而造成刀具磨损不利于切削的问题,获得良好的加工效益。
随着社会发展中,对制造业要求的不断提高,高速切削加工逐步的被应用在各个加工企业和加工生产当中,更是被诸多单位广泛的重视。
在此理论基础上逐渐形成了数控高速切削技术研究领域,使得其在生产的过程中能够有效的保证加工产品的质量和加工效益,是各个企业生产和加工过程中主要探索的目标和追求方向。
提高薄套类零件车削加工精度的研究

提高薄套类零件车削加工精度的研究万思敏(自贡硬质合金有限责任公司,四川自贡643000)应用科技脯要】本文针对薄套类零件车削加工的特点——零件壁滓、刚性差、易产生变形和振动。
围绕影响薄套类零件车削加工精度的因素一车床、刀具、切削用量、切削凌、工装夹具开展研究,通过分析研究,确定了选择车床、合理刀具几何参数和合适切削用量、切削液的原则及两种车削薄套类零件外圆和孔的工装夹具。
同时总结了两种简单易行的减振方法,提高薄套类零件车削加工精凰陕键间薄套类零件;加工精度;车削加工随着机械工业的逐步发展,薄套类零件需求数量日益增加。
由于薄套类零件在车削加工中易产生变形和振动,零件精度难保证,属难加工件。
下面从影响薄套类零件加工精度的因素和减振方法两方面进行研究和介绍。
1影响薄套类零件加工精度的因素1.1车床.车床是加工薄套类零件的基础,车床的精度直接影响薄套类零件的加工精度。
主轴轴颈圆度、主轴中心线与拖板导轨平行度、主轴间隙等均是影响因素。
调整车床主轴、拖板、刀架等转动和滑动部位的间隙,使车床处于最佳状态,提高薄套类零件车削加工精度。
12刀具,【..伺碜数合理的刀具几何参数是保证零件加工质量,提高效率,嘲氐成本的有效途径。
刀具门伺参数主要包括刀具的前角、后角、主偏角、副偏角、刃倾角。
这些角度是否合理,直接影响到被加工零件的质量。
下面是选择加工薄套类零件刀具几伺参数的原则:1)前角。
在主剖面内,前刀面与基面之间的夹角。
合理的前角既要切削刃锐利,又要有一定的强度和散热体积。
车削薄套类零件时,为减少振动适当加大前角。
2)后角。
在主剖面内,后刀面与切削平面之间的夹角。
车削薄套类零件时,选稍大后角,利于增加刀头强度,增大散熟,体积。
3)主偏角。
主切削刃在基面上的投影与进给运动方向之间的夹角。
加工薄套类零件为减少振动,选用较大主偏角,使主刀刃参加工作的长度越,J、越好。
4)吾蝙角。
副切削刃在基面上的投影与背进给运动方向之间的夹角。
试论数控高速切削加工技术的发展与应用研究
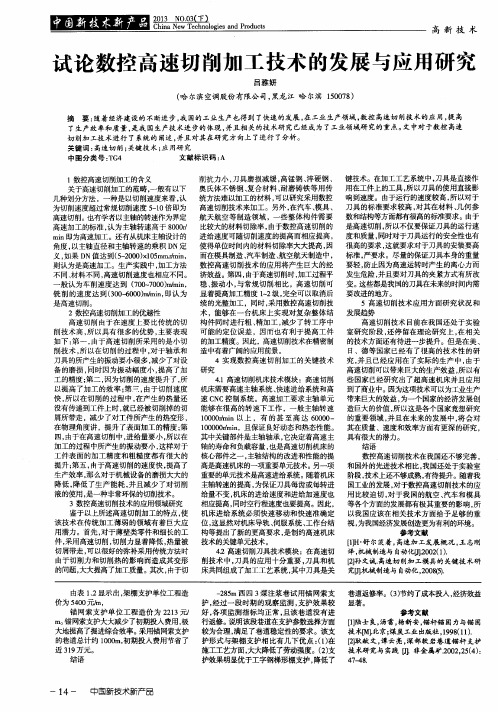
C h i n a N e w T e c h n o l o g i e s a n d P r o d u c t s
高 新 技 术
试论 数控 高速切 削加工 技术 的发展 与应用研究
吕雅 妍
( 哈 尔滨空调股份有 限公 司, 黑龙 江 哈 尔滨 1 5 0 0 7 8 )
关键 词 : 高速切 削 ; 关键 技术 ; 应 用研 究 中图分 类号 : T G 4 文献标 识码 : A
1数控高速切削加工的含义 关于高 速切 削加工 的范畴 , 一般有 以下 几 种划分方法 ,一种是 以切削速 度来 看 , 认 为切削速度超过常 规切削速度 5 — 1 O 倍即为 高速切削。 也有学者 以主轴 的转速作为界定 高速加工 的标 准 , 认为 主轴转速 高于 8 0 0 0 r / m i n 即为高速加工。还有从 机床主轴设计 的 角度 , 以主轴 直径和 主轴转速 的乘积 D N定 义, 如果 D N值达到 ( 5 - 2 0 0 0 ) x l 0 5 m m . r / m i n , 则认为是高 速加工 。生产 实践 中, 加工方 法 不 同、 材料不 同 , 高速切 削速度也相应 不同 。 般 认为 车削速度 达到 ( 7 0 0 ~ 7 0 0 0 ) m / m i n , 铣 削 的速 度 达 到( 3 0 0 - 6 0 0 0 ) m / m i n , 即认 为
一
是高 速切 削。
2数控高速切削加工的优越性 高速切削 由于在 速度 上要 比传统 的切 削 技术 高 , 所 以具有 很多 的优势 , 主要 表现 如下: 第一, 由于高速 切削 所采用 的是 小切 削 技术 , 所 以在切 削的过 程 中 , 对 于轴 承和 刀具的所产生 的振 动要小很 多 , 减 少了对设 备 的磨 损 , 同时 因为振动 幅度小 , 提高 了加 工的精度 ; 第二 , 因为切削 的速 度提升 了, 所 以提 高 了加 工 的效率 ; 第j, 由于切 削速度 快, 所 以在切 削 的过程 中 , 在产 生 的热 量还 没有传递到 工件 上时 , 就 已经被 切削掉 的切 屑所带走 , 减少 了对工件所产 生的热变形 , 在物理角度讲 ,提升 了表 面加工 的精度 ; 第 四, 由于在高 速切削 中 , 进 给量要小 , 所 以在 加工 的过程 中所产生 的振 动要小 , 这样对 于 工件 表面 的加工 精度 和粗糙 度都有 很大 的 提升 ; 第五, 南于高速切 削的速度快 , 提 高了 生产效率 , 那 么对于机械设 备的磨损大 大的 降低, 降低 了生 产能耗 , 并且 减少 了对切 削 液 的使用 , 是一种非常环保 的切削技术 。 3数控高速切削技术的应用领域研究 鉴 于以上所述高速切削加 工的特点 , 使 该 技术在 传统 加工薄 弱 的领域有 着 巨大应 用 潜力 。首先 , 对于薄壁 类零件 和细长的工 件, 采 用高速切削 , 切 削力显着 降低 , 热量被 切屑带走 , 可 以很好 的弥补采用传 统方法时 由于切 削力 和切削 热 的影 响而 造成其 变形 的问题 , 大大 提高了加工质量 。 其次 , 甫于切 由表 1 、 2 显示 出 , 架棚支护 单位工程造
减小薄壁铝合金零件加工变形工艺研究
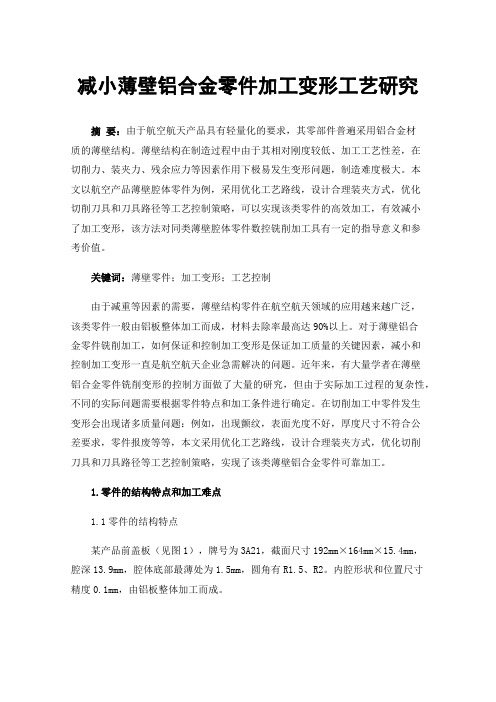
减小薄壁铝合金零件加工变形工艺研究摘要:由于航空航天产品具有轻量化的要求,其零部件普遍采用铝合金材质的薄壁结构。
薄壁结构在制造过程中由于其相对刚度较低、加工工艺性差,在切削力、装夹力、残余应力等因素作用下极易发生变形问题,制造难度极大。
本文以航空产品薄壁腔体零件为例,采用优化工艺路线,设计合理装夹方式,优化切削刀具和刀具路径等工艺控制策略,可以实现该类零件的高效加工,有效减小了加工变形,该方法对同类薄壁腔体零件数控铣削加工具有一定的指导意义和参考价值。
关键词:薄壁零件;加工变形;工艺控制由于减重等因素的需要,薄壁结构零件在航空航天领域的应用越来越广泛,该类零件一般由铝板整体加工而成,材料去除率最高达90%以上。
对于薄壁铝合金零件铣削加工,如何保证和控制加工变形是保证加工质量的关键因素,减小和控制加工变形一直是航空航天企业急需解决的问题。
近年来,有大量学者在薄壁铝合金零件铣削变形的控制方面做了大量的研究,但由于实际加工过程的复杂性,不同的实际问题需要根据零件特点和加工条件进行确定。
在切削加工中零件发生变形会出现诸多质量问题:例如,出现颤纹,表面光度不好,厚度尺寸不符合公差要求,零件报废等等,本文采用优化工艺路线,设计合理装夹方式,优化切削刀具和刀具路径等工艺控制策略,实现了该类薄壁铝合金零件可靠加工。
1.零件的结构特点和加工难点1.1零件的结构特点某产品前盖板(见图1),牌号为3A21,截面尺寸192mm×164mm×15.4mm,腔深13.9mm,腔体底部最薄处为1.5mm,圆角有R1.5、R2。
内腔形状和位置尺寸精度0.1mm,由铝板整体加工而成。
图1 薄壁腔体零件1.2零件加工难点(1)零件为典型的薄壁腔体零件,具有高精度、薄壁、低刚性等特点。
加工中急需解决的主要问题是如何控制和减小变形。
影响和造成工件加工变形的主要因素是切削热和切削力产生的应力、毛坯内的残余应力以及工件装夹产生的应力和变形等。
探析高速切削中硬态切削技术的应用
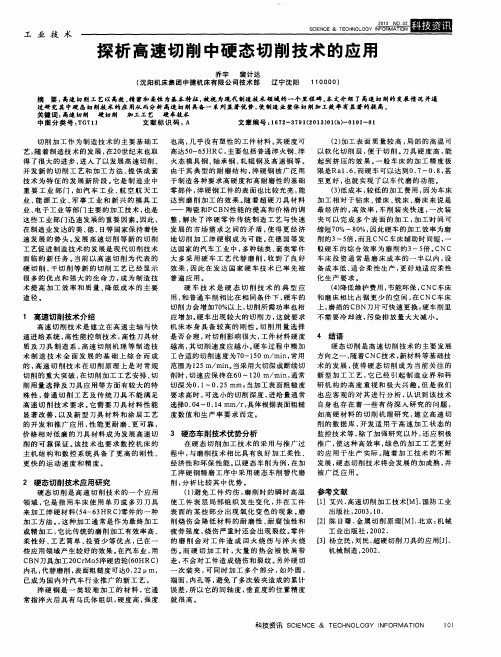
发 展 的 市场 需 求 之 间的 矛 盾 , 使 得 更 经 济 缩 短7 0 %~8 0 %, 因 此 硬 车 的加 工效 率 为磨 地切削加 工淬硬 钢成为 可能 。 在 德 国 等 发 削 的3 ~5 倍, 而且 C NC车床 辅 助 时 间短 , 一
速发展 的势头 。 发 展 高 速 切 削 等 新 的 切 削
高 速 切 削 技 术 是 建 立 在 高 速 主 轴 与 快 机 床 本 身具 备 较 高 的 刚 性 。 切 削 用 量 选 择 速进给系统 , 高性能控制技术 , 高 性 刀 具 材 是 否 合 理 , 对切 削影 响 很 大 , 工 件材 料 硬 度 4 结语 其切削速度应越小 。 硬 车 过 程 中精 加 硬 态 切 削 是 高 速 切 削 技 术 的 主 要 发 展 质 及 刀具 制 造 系 , 高 速 切 削 机 理 等 制 造 技 越 高 ,
限 是Ra 1 . 6 , 而硬车可以达到0 . 7 ~0 . 8 , 甚 也 就 实现 了 以 车 代 磨 的功 能 。 于 制造 各 种 要 求 高 硬 度 和 高 耐 磨 性 的基 础 至 更 好 , 零部件 , 淬 硬 钢 工 件 的表 面 也 比较 光 亮 , 能 ( 3 ) 低成本 , 较低的加工费用 , 因 为 车床
切 削 加 工 作 为 制 造 技 术 的 主 要 基 础 工
也高, 几乎 没 有 塑 性 的工 件 材 料 。 其 硬 度 可
( 2 ) 加 工表面 质量较高 , 局 部 的 高 温 可
艺, 随着制造技术的发展 , 在2 0 世 纪 末 也 取 得 了很 大 的 进 步 , 进 入 了以 发 展 高 速 切 削 开发新 的切 削工艺和 加工方法 、 提 供 成 套 技术 为特征 的发展新 阶段 。 它 是 制 造 业 中 重要 工业 部 门 , 如汽 车 工业 、 航 空 航 天 工
薄壁类零件加工装夹技术研究
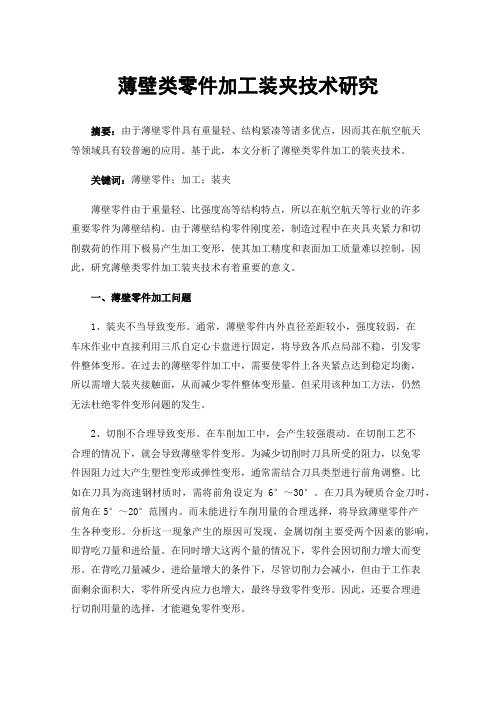
薄壁类零件加工装夹技术研究摘要:由于薄壁零件具有重量轻、结构紧凑等诸多优点,因而其在航空航天等领域具有较普遍的应用。
基于此,本文分析了薄壁类零件加工的装夹技术。
关键词:薄壁零件;加工;装夹薄壁零件由于重量轻、比强度高等结构特点,所以在航空航天等行业的许多重要零件为薄壁结构。
由于薄壁结构零件刚度差,制造过程中在夹具夹紧力和切削载荷的作用下极易产生加工变形,使其加工精度和表面加工质量难以控制,因此,研究薄壁类零件加工装夹技术有着重要的意义。
一、薄壁零件加工问题1、装夹不当导致变形。
通常,薄壁零件内外直径差距较小,强度较弱,在车床作业中直接利用三爪自定心卡盘进行固定,将导致各爪点局部不稳,引发零件整体变形。
在过去的薄壁零件加工中,需要使零件上各夹紧点达到稳定均衡,所以需增大装夹接触面,从而减少零件整体变形量。
但采用该种加工方法,仍然无法杜绝零件变形问题的发生。
2、切削不合理导致变形。
在车削加工中,会产生较强震动。
在切削工艺不合理的情况下,就会导致薄壁零件变形。
为减少切削时刀具所受的阻力,以免零件因阻力过大产生塑性变形或弹性变形,通常需结合刀具类型进行前角调整。
比如在刀具为高速钢材质时,需将前角设定为6°~30°。
在刀具为硬质合金刀时,前角在5°~20°范围内。
而未能进行车削用量的合理选择,将导致薄壁零件产生各种变形。
分析这一现象产生的原因可发现,金属切削主要受两个因素的影响,即背吃刀量和进给量。
在同时增大这两个量的情况下,零件会因切削力增大而变形。
在背吃刀量减少、进给量增大的条件下,尽管切削力会减小,但由于工作表面剩余面积大,零件所受内应力也增大,最终导致零件变形。
因此,还要合理进行切削用量的选择,才能避免零件变形。
3、刀具不合适导致变形。
薄壁零件在车削时,选取合理的刀具至关重要,尤其是对刀具几何角度的选择,不仅会影响切削力的大小,也会影响车削中产生的热变形程度,需关注的是,在薄壁零件的工作表面微观质量的把握也很重要。
浅析薄壁类零件加工
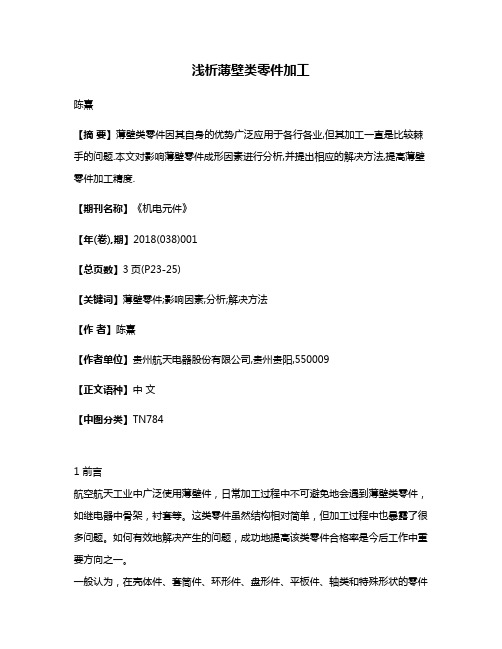
浅析薄壁类零件加工陈熹【摘要】薄壁类零件因其自身的优势广泛应用于各行各业,但其加工一直是比较棘手的问题.本文对影响薄壁零件成形因素进行分析,并提出相应的解决方法,提高薄壁零件加工精度.【期刊名称】《机电元件》【年(卷),期】2018(038)001【总页数】3页(P23-25)【关键词】薄壁零件;影响因素;分析;解决方法【作者】陈熹【作者单位】贵州航天电器股份有限公司,贵州贵阳,550009【正文语种】中文【中图分类】TN7841 前言航空航天工业中广泛使用薄壁件,日常加工过程中不可避免地会遇到薄壁类零件,如继电器中骨架,衬套等。
这类零件虽然结构相对简单,但加工过程中也暴露了很多问题。
如何有效地解决产生的问题,成功地提高该类零件合格率是今后工作中重要方向之一。
一般认为,在壳体件、套筒件、环形件、盘形件、平板件、轴类和特殊形状的零件中,当壁厚与内径曲率半径(或轮廓尺寸)之比小于1:20时,称作薄壁零件。
薄壁零件具有重量轻、节约材料、结构紧凑等优点,但其在加工中由于外形协调要求高,零件外廓尺寸相对截面尺寸较大,加工余量大,相对刚度较低等原因导致加工工艺性差,故多年来,薄壁零件一直存在加工变形、精度低等问题。
2 影响薄壁零件加工精度的因素加工精度是零件加工后的实际几何参数(尺寸、形状和位置)与理想几何参数相符合的程度。
薄壁零件加工中主要问题即加工变形问题,产生原因很多,与零件材料,零件结构以及生产条件等都有很大关系,主要表现在以下几个方面:2.1 毛坯因素影响薄壁零件材料选择范围较广,根据实际产品加工毛坯可以为塑料、不锈钢等材质。
塑料、铝等材料自身刚性较低,加工过程中极易发生变形;同样,毛坯本身的形状误差,加工后也会映射到成品上。
2.2 切削热及切削力的影响零件在加工过程中在切削力的作用下,将在各个受力方向产生相应变形,但影响最大的是误差敏感方向。
车加工中,薄壁零件误差敏感方向主要为径向。
车刀加工过程中对侧壁产生挤压,导致加工过程中受力部分变形。
高速切削及其关键技术

高速切削及其关键技术摘要自20世纪30年代德国 Carl Salomon博士首次提出高速切削概念以来,经过50年代的机理及可行性研究,70年代的工艺技术研究,80年代全面系统的高速切削技术研究,到90年代初,高速切削技术开始进入实用化,到90年代后期,商品化高速切削机床大量涌现,21世纪初,高速切削技术在工业发达国家得到普遍应用,正成为切削加工的主流技术。
根据1992年国际生产工程研究会(CIRP)年会主题报告的定义,高速切削通常指切削速度超过传统切削速度5-10倍的切削加工。
因此,根据加工材料的不同和加工方式的不同,高速切削的切削速度范围也不同。
高速切削包括高速铣削、高速车削、高速钻孔及高速车铣等,但绝大部分应用是高速铣削。
目前,加工铝合金已达到2000-7500m/min;钛合金达150-1000m/min;纤维增强塑料为2000-9000m/min。
高速切削是一项系统技术,企业必须根据产品的材料和结构特点,购置合适的高速切削机床,选择合适的切削刀具,采用最佳的切削工艺,以达到理想的高速加工效果。
高速切削是一项先进的、正在发展的综合技术,必须将高性能的高速切削机床、及工件材料相适应的刀具和对于具体加工对象最佳的加工工艺技术相结合,充分发挥高速切削技术的优势。
高速切削技术已成为切削加工的主流和先进制造技术的一个重要发展方向。
高速切削较之常规切削是一种创新的加工工艺和加工理念。
本文分析了高速切削技术的特点,研究了高速切削的关键技术:机床技术、刀具技术和工艺技术,介绍了高速切削技术在航空航天和汽车制造等领域的发展及应用。
关键词:高速切削;机床;刀具;切削工艺一.引言机械加工技术正朝着高效率、高精度、高柔性和绿色制造的方向发展。
在机械加工技术中,切削加工是应用最广泛的加工方法。
近年来,高速切削技术蓬勃发展,已成为切削加工的主流和先进制造技术的一个重要发展方向。
在数控机床出现以前,用于工件上下料、测量、换刀和调整机床等的辅助时间超过工件加工总工时的70%;以数控机床为基础的柔性制造技术的发展和应用,大大降低了工件加工的辅助时间,切削所占时间比例越来越大。
探析高速切削技术的发展及其应用
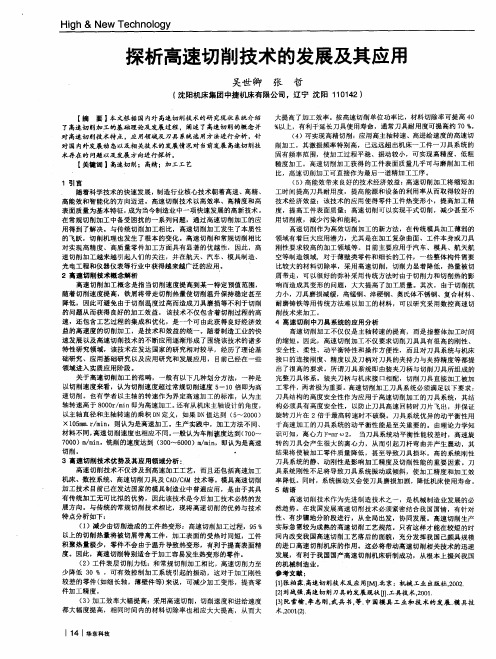
Hale Waihona Puke 探析 高速切 削技术 的发展及其应用
吴世 卿 张 哲
( 沈阳机床 集团中捷机床有 限公司 ,辽宁 沈 阳 1 1 0 1 4 2)
大提 高了加工效率。按 高速切削单位功率比,材料切除率可提高 4 O % 以上 ,有利于延长刀具使用寿命 ,通常 刀具耐用度可提高约 7 O% 。 ( 4 )可实现高精切削:应用高主轴转速 、高进给速度的 高速切 削加 工,其激振频率特别高 ,已远远超 出机床一工件一刀具系统 的 固有频率 范围,使加工过程平稳 、振动较小 ,可实现 高精度 、低粗 糙度加工。高速切 削加工 获得 的工件表面质量几乎可与磨 削加工相 【 关键词 】 高速切削 ;高 精 ;加工工艺 比,高速 切削加工可直接作为最后一道精加 工工序 。 ( 5 )高能效带来 良好的技术经济 效益 :高速切 削加工将 缩短加 1 引 言 随着科学技术的快速发展, 制造行业核心技术朝着高速、 高精 、 工时间提高刀具耐用度,提高能源和设备的利用率从 而取 得较 好的 高能效和智能化的方 向迈进 。高速切削技术 以高效率 、高精度和高 技术经济效益;该技术的应用使得零件工件 热变形 小,提 高加 工精 表面质量为基本特征, 成为当今制造业中一项快速 发展 的高新技术 。 度 ,提高工件表面质量;高速切削可 以实现干式切削,减 少甚至不 在常规切削加工 中备受困扰的一系列 问题 ,通过高速切削加工的应 用 切 削 液 , 减少 污 染和 能耗 。 用得到 了解决 。与传统切 削加工相 比,高速切 削加工 发生 了本质性 高速切削作为高效切削加工的新方法 ,在传统模具加工薄弱的 的飞跃 ,切 削机理也发生 了根本 的变化 。高速切 削和常规切 削相 比 领域有着 巨大应用潜力,尤其是在加工复杂曲面、工件本 身或刀具 对实现高精度 、高质量零件加工方面具有显 著的优越 性,因此 ,高 刚性要求较高的加工领域等 。目前主要应用于汽车、模具、航天航 速切削加工越来越 引起人们的关注 ,并在航 天、汽车 、模具制造 、 空等制造领域,对于薄壁类零件和细长的工件,一些整体 构件需要 光 电工程和仪器仪表等行业中获得越来越广泛的应用。 比较大 的材料切除率 ,采用高速切削 ,切削力显着降低,热量被切 2高速切 削技术概 念解析 屑带走 ,可 以很好的弥补采用传统方法时由于切削力和切 削热的影 高速切 削加 工概念 是指当切 削速 度提高到某~特定预值 范围, 响而造成其变形 的问题 ,大大提高 了加工质量。其次,由于切削抗 随着切 削速度提 高,铁屑将带走切 削热量使切 削温升保持稳定甚至 力小,刀具磨损减缓 ,高锰钢 、淬硬钢 、奥 氏体 不锈钢 、复合材料、 降低 ,因此可避 免由于切 削温度过 高而 造成 刀具磨损 等不利 于切 削 耐磨铸铁等用传统方法难 以加工的材料 ,可 以研究采用数控高速切 的问题从而获得 良好的加工效益。 该技术不仅 包含着切削过程的 高 削技术来加工。 速 ,还包含 工艺过程 的集 成和优化 ,是 一个可 由此获 得良好经济效 4 高速切 削中刀具 系统的应用分析 益 的高速度 的切 削加工 ,是技术和效益 的统 一。随着 制造工业 的快 高速切削加工不仅仅是主轴转速 的提高 ,而是指整体加工时间 速发展 以及 高速切 削技术 的不 断应用逐渐形 成了围绕 该技术 的诸 多 的缩短 。因此 ,高速切削加工不仅要求切削刀具具有很高的刚性、 特性研宄领域 ,该技术在 发达 国家 的研 究相对较 早,经历 了理论基 安全性 、柔性、动平衡特性和操作方便性,而且对刀具系统与机床 础研 究、应用基础研 究以及应用研 究和 发展应用 , 目前已经在一些 接 口的连接刚度 、精度 以及刀柄对刀具的夹持力与夹持精度等都提 领域进入实质应用阶段 。 出了很高的要求 。所谓刀具系统即 由装夹刀柄与切削刀具所组成的 关于 高速切削 加工 的范畴,一般 有以下几种划 分方法 ,一种是 完整刀具体系 。装夹刀柄与机床接 口相配 ,切削刀具直接加工被加 以切 削速度来看 ,认为切 削速度超过常规切削速度 5 —1 O倍即为高 工零件 ,两者极为重要 。高速切削加工刀具系统必须满足 以下要求: 速切 削。也有学者 以主轴 的转速作为 界定高速加 工的标准 ,认为主 刀具结构 的高度安全性作为应用于高速切削加工的刀具系统,其结 轴转速高 于 8 0 0 0 r / m i n即为高速加工。 还有从机床主轴设计的角度 , 构必须具有高度安全性 ,以防止刀具高速回转时刀片飞出 ,并保证 以主轴直径和主轴转速的乘积 D N定义,如果 D N值达到 ( 5  ̄2 0 0 0 ) 旋转刀片在 2倍于最高转速时不破裂 。刀具系统优异的动平衡性用 X 1 0 5 m. r / m i n ,则认为是高速加工 。生产实践中,加工方法不 同、 于高速加工 的刀具系统的动平衡性能是至关重要的。 由理论力学知 材料不同 , 高速切 削速度也相应不 同。 一般认为车削速度达到 ( 7 0 0 - 识可知,离心力 F = m ru 2 , 当刀具系统动平衡性能较差时 ,高速旋 7 0 0 0)m / m i n ,铣 削的速度达到 ( 3 0 0  ̄6 0 0 0 )m / a r i n ,即认为是高速 转 的刀 具 会 产 生 很 大 的离 心 力 ,从 而 引 起 刀 杆 弯 曲并 产 生 震 动 ,其 切削 。 。 结果将使被加工零件质量降低 ,甚至导致刀具损坏。高的系统刚性 3商 速切 削技术优 势及 其应用领域分析 : 刀具系统的静、动刚性是影响加工精度及切削性能的重要因素 。刀 高速切 削技术 不仅涉及到 高速加工 工艺 ,而且还包括高速加工 具系统刚性不足将导致刀具系统振动或倾斜 ,使加工精度 和加工效 机床 、数控系统、高速切 削刀具及 C A D / C A M技术等 。模具 高速切 削 率 降低。同时,系统振动又会使 刀具磨损加剧 ,降低机床使用寿命 。 加工技术 目前已在发达 国家的模具制造业 中普遍应用 ,是 由于其具 5 结 语 有传统加工无可 比拟 的优势 ,因此该技术是今后加工技术必然 的发 高速切削技术作为先进制造技术之一 ,是机械制造业发展的必 展 方 向 。与 传 统 的常 规 切 削技 术 相 比 ,现 将 高速 切 削 的优 势 与 技 术 然趋势。在我国发展高速切削技术必须紧密结合我国国情 ,有针对 特点分析如下: 性 、有步骤地分阶段进行,从全局出发,协同发展。高速 切削生产 ( 1 )减少由切削造成 的工 件热变形 :高速切削加工过程,9 5% 实际急需较为成熟的高速切削工艺规范。只有这样才 能在 较短的时 以上的切削热量将被切屑带离工件 ,加工表面 的受热 时间短 ,工件 间 内改变我国高速切削工艺落后的面貌,充分发挥我国已颇 具规模 积聚热量极少 ,零件不会 由于温升 导致 热变形 ,有利 于提高表面精 的进 口高速切削机床的作用。这必将带动高速切削相 关技术 的迅 速 度 。因此 ,高速切削特别适合于加工容易发生热变形 的零件 。 发展,有利于我国国产高速切削机床研制成 功,从根 本上 振兴我国 ( 2 )工件表层切削力低 :和常规切削加 工相比,高速切 削力至 的 机 械 制 造 业 。 少 降低 3 0% ,可有效控制加工系统 引起 的振动 ,这对于加工刚性 参考文献 : 较差 的零件 ( 如细长轴 ,薄壁件等) 来说 ,可减少加工变形 ,提高零 【 1 ] 张柏霖 速切削技 术及应 用[ J . 北京:机械工业 出版社, 2 0 0 2 . 件加工精度 。 [ 2 】 刘战强. 高速 切削刀具的发展现状 m. 工具技术, 2 0 0 1 .
高速高效切削加工技术的现状及发展趋势

高速高效切削加工技术的现状及发展趋势一、前言目前,我国已成为世界飞机零部件的重要转包生产国,波音、麦道、空客等世界著名飞机制造公司都在我国转包生产从尾翼、机身、舱门到发动机等各种零部件,这些飞机零部件的加工生产必须采用先进的加工装备和加工工艺。
为此,国内各飞机制造公司均进行了大规模的技术改造,引进了大量国外先进的加工装备,使我国的飞机制造业设备的数控化率越来越高。
与此同时,大量高速、高效、柔性、复合、环保的国外切削加工新技术不断涌现,使切削加工技术发生了根本的变化。
刀具在航空航天加工领域的应用技术进入了以发展高速切削、开发新的切削工艺和加工方法、提供成套技术为特征的新阶段。
与此形成鲜明对比的是,我国的装备制造业和以制造业为主要服务对象的传统的工具工业却无法满足航空航天工业对现代制造装备和先进加工工艺的要求。
下面结合我国航空航天工业加工技术的现状及发展趋势,着重介绍我国高效、高速切削刀具的生产应用情况,对我国工具工业的发展现状和存在的问题提出自己的看法。
二、航空航天工业加工技术的现状及发展趋势1.航空结构件材料的发展趋势及其特点①以整体件为代表的铝合金结构件为了提高零件的可靠性、降低成本和减轻重量,传统的铆接结构逐步被整体薄壁的机加工结构件所代替。
这类零件由于大部分是用整体实心铝合金材料制成的薄壁、细筋结构件,70%~95%的材料要在加工中去除掉,而高速切削产生的热量少、切削力小、零件变形小,因此提高生产效率的唯一途径是采用四轴或五轴联动机床进行高速铣削加工。
②以钛基和镍基合金零件为代表的难切削材料零件由于钛(镍)合金具有比强度高、热强度好、化学活性大等特点,目前飞机发动机重要部件采用钛基和镍基合金材料的逐渐增多。
采用高速切削后,其切削速度可提高到100m/min以上,为常规切削速度的10倍。
这类材料的加工特点是:切削力大、切削温度高、加工硬化和粘刀现象严重、刀具易磨损。
③以碳纤维复合材料零件为代表的复合材料结构件复合材料现已成为新一代飞机机体结构主要材料之一,如飞机上的大型整体成形的翼面壁板、带纵墙的整体下翼面等。
高速切削(HSC)技术
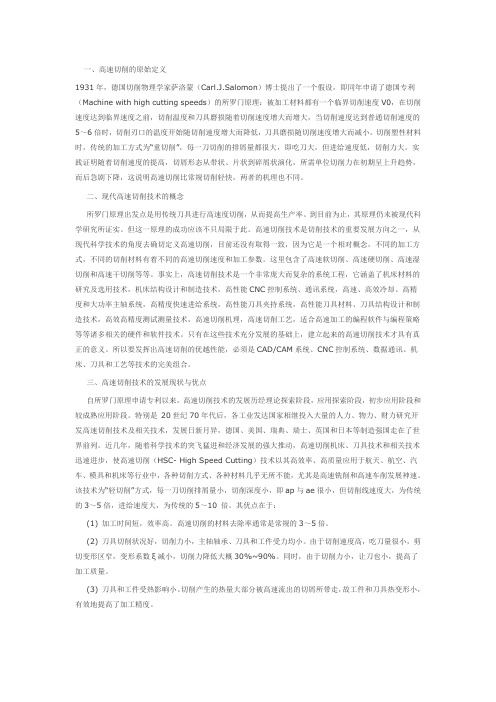
一、高速切削的原始定义1931年,德国切削物理学家萨洛蒙(Carl.J.Salomon)博士提出了一个假设,即同年申请了德国专利(Machine with high cutting speeds)的所罗门原理:被加工材料都有一个临界切削速度V0,在切削速度达到临界速度之前,切削温度和刀具磨损随着切削速度增大而增大,当切削速度达到普通切削速度的5~6倍时,切削刃口的温度开始随切削速度增大而降低,刀具磨损随切削速度增大而减小。
切削塑性材料时,传统的加工方式为“重切削”,每一刀切削的排屑量都很大,即吃刀大,但进给速度低,切削力大。
实践证明随着切削速度的提高,切屑形态从带状、片状到碎屑状演化,所需单位切削力在初期呈上升趋势,而后急剧下降,这说明高速切削比常规切削轻快,两者的机理也不同。
二、现代高速切削技术的概念所罗门原理出发点是用传统刀具进行高速度切削,从而提高生产率。
到目前为止,其原理仍未被现代科学研究所证实。
但这一原理的成功应该不只局限于此。
高速切削技术是切削技术的重要发展方向之一,从现代科学技术的角度去确切定义高速切削,目前还没有取得一致,因为它是一个相对概念,不同的加工方式,不同的切削材料有着不同的高速切削速度和加工参数。
这里包含了高速软切削、高速硬切削、高速湿切削和高速干切削等等。
事实上,高速切削技术是一个非常庞大而复杂的系统工程,它涵盖了机床材料的研究及选用技术,机床结构设计和制造技术,高性能CNC控制系统、通讯系统,高速、高效冷却、高精度和大功率主轴系统,高精度快速进给系统,高性能刀具夹持系统,高性能刀具材料、刀具结构设计和制造技术,高效高精度测试测量技术,高速切削机理,高速切削工艺,适合高速加工的编程软件与编程策略等等诸多相关的硬件和软件技术。
只有在这些技术充分发展的基础上,建立起来的高速切削技术才具有真正的意义。
所以要发挥出高速切削的优越性能,必须是CAD/CAM系统、CNC控制系统、数据通讯、机床、刀具和工艺等技术的完美组合。
技师论文薄壁零件加工

浅谈薄壁零件的加工方法单位山东技师学院姓名郭尚超考评职称车工技师浅谈薄壁零件的加工方法摘要:薄壁零件已日益广泛地应用在各工业部门,但在薄壁零件的加工中会遇到比较棘手的问题,原因是薄壁零件刚性差,强度弱,在加工中极容易变形,使零件的形位误差增大,不易保证零件的加工质量。
高精度、薄壁腔体类零件金属切除量大、工件壁薄、刚性低,加工中需要解决的主要问题是控制和减小变形,在此基础上,希望尽可能提高切削效率、缩短加工周期。
其加工工艺需要从工件装夹、工序安排、切削用量参数、刀具选用等多方面进行优化。
关键词薄壁零件精度加工方法一.影响薄壁零件加工精度的主要因素影响薄壁零件加工精度的因素有很多,但归纳起来主要有以下三个方面:1.工件的尺寸精度和形状精度。
易受力变形。
因壁薄,在夹紧力的作用下,容易产生变形,从而影响2. 易受热变形。
因工件较薄,切削热会引起工件热变形,使工件尺寸难以控制。
3. 易振动变形。
在切削力(特别是径向切削力)的作用下,容易产生振动和变形,影响工件的尺寸精度和形状,位置精度和表面粗糙度。
二.减少薄壁工件变形的方法主要是减少切削力和切削热,改善或改变夹紧力对零件的作用。
1. 在切削过程中,切削力时必然要产生的,但它的大小时可以改变的,影响切削力的大小的因素很多,主要是被加工件材料、刀具、切削用量和冷却润滑等几个方面。
2. 减少切削力的方法。
在薄壁零件的切削中,合理的刀具几何角度对车削时切削力的大小是至关重要的。
刀具前角大小,决定着切削变形与刀具前角的锋利程度。
前角大,切削变形和摩擦力减小,切削力减小,所以前角取5-20°,刀具的后角大,,摩擦力小,切削力相应减小,所以后角取4-12°。
主偏角在30-90°范围内,车薄壁零件的内外圆时,取较大的主偏角,副偏角取8-15°。
三.合理地选择切削用量降低切削力切削力的大小与切削用量密切相关,背吃刀量和进给量同时增大,切削力增大,变形也大,对车削薄壁零件极为不利。
高速切削技术在薄套类零件加工中的应用研究
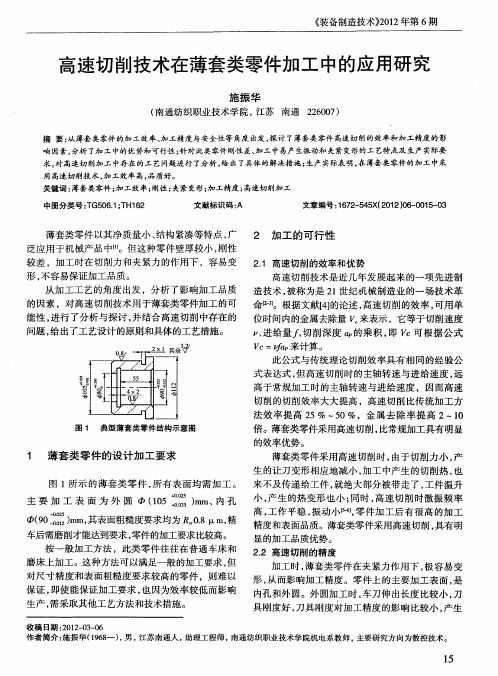
关键词 : 薄套类零件 ; 工效率; 加 刚性 ; 夹紧变形 ; 加工精度 ; 高速切 削加工 中图分 类号 :G5 61 T 6 T 0 .; H1 2 文献标识码 : A 文章编号 :6 2 5 5 2 1 0 — 0 5 0 1 7 — 4 X(0 2)6 0 1 — 3
薄套类零件以其净质量小 、 结构 紧凑等特点 , 广 2 加 工 的 可 行 性 泛应用于机械产品中【 l 1 。但这种零件壁厚较小 , 刚性 较 差 ,加工 时 在 切 削力 和 夹 紧力 的作 用下 ,容 易 变 21 高 速切 削的 效率 和优 势 . 形 , 容易 保证 加 工 品质 。 不 高速切削技术是近几年发展起来的一项先进制
的误 差 , 主要 是 夹 紧变形 引 起 的形 状 误差 ; 内孔 加 工 时 , 杆 刚性 不 足 而 引起 的孔 的尺 寸 误差 , 镗 和夹 紧 变 形 引 起 的误 差 占主导地 位 。因 此 , 薄套 类零 件 的高 在
速切削 中 , 产生 的加 工误 差 , 主要 来 源 于工 件 的夹 紧
响 因素 , 分析 了加 工 中的优势和可行性 ; 针对此类零件 刚性差、 工中易产生振动和 夹紧变形的 工艺特点及生产 实际要 加
求 , 高速切 削加工 中存在 的工艺 问题进行 了分析 , 出了具体 的解决措施 ; 对 给 生产实际表 明 , 薄套 类零 件的加工 中采 在
用高速切 削技术 , 工效率高 , 加 品质好 。
从 加 工 工艺 的角 度 出发 ,分 析 了影 响加 工 品质 造技术 , 被称为是 2 世纪机械制造业的一场技术革 l 的 因素 ,对高速切削技术用于薄套类零件加工的可 命[1 2 。根据文献[ 的论述 , - 3 4 ] 高速切削的效率 , 可用单
复杂薄壁_薄板类零件高速加工技术初探_陈战士

· 47 ·
复杂薄壁、 薄板类零件高速加工技术初探
*+ ,@AB CDB *+ ,13 *+:13 :,6, :,:6 H:>6 :,:6 HG6 M NO :,6, H:76 :,6, H:G6 IJ0;01201KL JL34 IJ0;01201KL JL34 IJL12L;L IKL34 IJL12L;L IKL34 ./012034 ./012034 ./0120;0<= 76, >?, 766E7FG >F>E7:G 7?>E7FG 77?E6 : 7?,E6>, 89 57 89 56 89 >6 89 7, 89 5, 89 5, a ! "#$ %&’() 56, 56, 56, 56, 56, 56, 56, 56,
图 2 圆弧进刀
图 3 等高层切法
图 4 插铣法
②半精加工
半精加工要避免急剧的铣切运动 。
为避免过切, 不可采用螺旋或斜坡进刀。 半精加工和精
加工的切削用量, 一般应在保证加工质量的前提下, 兼 顾切削效率、 经济性和加工成本, 高速加工中其径向进 刀量应小于 6% ~8% 的刀具直径,且满足等量切削条 件。 ③精加工 精加工要避免急剧变化的刀具运动,
Study on High-speed Machining Technology of Complicated Thin-walled and Thin-veneer Parts
CHEN Zhan-shi, SI Xiao-mei, LIU Dong-xiao, et al.
(1. Luoyang Institute of Electro-Optical Equipment, AVIC, Luoyang 471009; 2. Wuhan University of Technology Huaxia College, Wuhan, 430223 ) The processing methods, processing parameters and fixture of complicated thin-walled and thin-veneer parts were pre- [Abstract] sented. The problem of thin-walled and thin-veneer parts machining was solved. The machining technology will be used future. [Keywords] NC processing technology; high-speed machining; processing parameters; fixture
壳体类薄壁零件加工变形的控制

壳体类薄壁零件加工变形的控制发布时间:2021-01-21T06:54:31.626Z 来源:《中国科技人才》2021年第2期作者:吴挺燕纪钧王茹[导读] 需要相关人员针对性的进行处理。
所以,本文就薄壁零件加工精度影响因素以及工艺措施进行探析。
中国航发西安动力控制有限公司陕西西安 710077摘要:在众多零件中,薄壁零件作为工艺性较强的零部件之一,其本身也得到广泛应用,本文针对薄壁零件加工精度影响因素进行分析,并提出工艺措施。
关键词:薄壁零件;加工精度;工艺引言薄壁零件基本上都会应用在重要的位置,再加上其本身刚度低、结构复杂以及形状特殊等特点,所以,在实际的加工之中对于加工的精度有着极高的要求。
在实际的加工过程中,薄壁零件出现变形是非常严重的,需要相关人员针对性的进行处理。
所以,本文就薄壁零件加工精度影响因素以及工艺措施进行探析。
1 影响薄壁零件加工精度的主要因素零件的毛坯无论是锻造、铸造的,在制造过程中都有一个从高温冷却下来的过程。
在这一冷却过程中必会产生内应力,而这种内应力会引起零件变形。
在毛坯是有应力的状态下机加工时,切去部分表面或内腔后就会破坏内应力的平衡。
由于内应力需要重新分布,零件将会发生变形,另外,在切削加工的过程中,由于切削力和切削热的作用,零件表面也会发生极大的塑性变形,因而也将产生内应力。
这种残余的内应力,也与毛坯制造中形成的内应力一样,会引起薄壁零件的变形。
1.1 切削应力变形金属原子间存在着相互平衡的力,吸力和压力。
吸力使原子彼此密合到一起;而压力则使原子间不要接近得太紧密。
在通常情况下,原子占据的是这两种力保持平衡的位置。
当施加外力使原子间距靠近或拉远时,都必然产生相应的相斥抗力或相吸的抗力,并与之建立新的平衡。
金属材料塑性变形的机理是:金属的塑性变形都是金属晶体滑移或孪生造成的,而其中以晶体的滑移为主。
零件的加工过程虽然在外表看不见有什么异样,但在切削加工时当零件部分被切去后,会破坏原来内应力的平衡,零件也会发生变形。
- 1、下载文档前请自行甄别文档内容的完整性,平台不提供额外的编辑、内容补充、找答案等附加服务。
- 2、"仅部分预览"的文档,不可在线预览部分如存在完整性等问题,可反馈申请退款(可完整预览的文档不适用该条件!)。
- 3、如文档侵犯您的权益,请联系客服反馈,我们会尽快为您处理(人工客服工作时间:9:00-18:30)。
实践证明,在采取上述安全和相关工艺措施以 后,薄套类零件的高速切削的安全性,是可以保证的。
3 高速切削工艺过程
薄套类零件的结构如图 3 所示,其主要加工表 面为外圆、内孔、端面及两个退刀槽,属于典型的薄 壁零件,内孔与外圆的加工精度和表面粗糙度要求 较高,内孔与外圆的加工是关键加工工序。
(2)粗、精加工分开。在外圆与内孔的加工中产 生的加工应力,会引起工件的变形,为了消除和减小 加工应力的影响,在粗加工后松开工件一段时间,待 应力重新分布与减小后,再进行精加工。
(3)中间安排适当的热处理工序。为了尽可能减 小夹紧变形和加工应力等对加工精度的影响,在粗 加工后,精车前,安排适当的热处理;在粗磨后,最终 加工工序前,进行时效处理。经过中间热处理过程, 加工中夹紧变形对加工精度的影响,基本可以消除。 3.3 工艺路线
(2)
在轴向切削力 Ff 作用下,刀杆可以简化为受压
杆件,使刀杆受压弯曲的临界轴向切削力为 Ff max,其
值可由
16
Ff max
=
π 2EI 4L2
计算,将
I=
π·d 4 32
代入,得
Ff max
=
π 2Ed4 128L2
(3)
式(2)和式(3)表明,高速镗孔时,在主切削力 Fc
一定的情况下,刀具的原始状态(E、L、d 等)对加工
加工时,薄套类零件在夹紧力作用下,极容易变 形,从而影响加工精度。零件上的主要加工表面,是 内孔和外圆。外圆加工时,车刀伸出长度比较小,刀 具刚度好,刀具刚度对加工精度的影响比较小,产生
收稿日期:2012-03-06 作者简介:施振华(1968—),男,江苏南通人,助理工程师,南通纺织职业技术学院机电系教师,主要研究方向为数控技术。
《装备制造技术》2012 年第 6 期
综合上述方法,可以按以下工艺路线,对图 1 所 示零件进行加工:
毛坯锻造→退火→高速粗车→正火→半精车、精 车→粗磨内孔、外圆→时效处理→精磨内孔、外圆。
5 3
4 1.外圆 2.内孔 3.右端面 4.退刀槽 5.左端面
图 3 薄套类零件结构示意图
3.1 工艺设计原则 为保证精度,提高生产效率,薄套类零件高速切
薄套类零件采用高速切削时,由于切削力小,产 生的让刀变形相应地减小,加工中产生的切削热,也 来不及传递给工件,就绝大部分被带走了,工件温升 小,产生的热变形也小;同时,高速切削时激振频率 高,工作平稳,振动小[5 ̄6],零件加工后有很高的加工 精度和表面品质。薄套类零件采用高速切削,具有明 显的加工品质优势。 2.2 高速切削的精度
薄套类零件的主要加工表面是端面、外圆和内 孔,加工过程中容易产生夹紧变形。一般来说,对于薄 壁零件,保证端面的加工精度,比保证外圆与孔的加
4 结束语
薄套类零件是广泛应用于机械产品中的零件之 一,加工中容易产生夹紧变形,如何消除和减小夹紧 变形,提高加工效率,是这类零件加工中最常见的问 题。采用高速切削技术,既保证了加工精度,又提高 了加工效率,是行之有效的工艺方法,与采用普通机 床加工相比,具有加工效率高、加工表面品质好的明 显优势。
作规程操作等措施,以保证设备、人员的安全。
除了采取上述措施以外,还必须从工艺上采取
不同于常规加工的安全措施。由于在高速机床上加
工,高速旋转产生的离心力,使传统的用三爪卡盘装
夹工件的方法不能再使用。其加工过程中出现的一
个关键问题,是工件在高速旋转时夹紧出现问题时 的安全保护问题[7]。
为了防止加工过程中工件由于夹紧不可靠而松 动,甚至飞出的安全事故的出现,采用带有离心结构 的专用卡盘装夹工件,并把卡盘与工件加工区域用 安全保护装置罩住。
精度影响极大,为保证加工精度,应选择刚度大的刀
具系统,合理选择刀具直径与悬伸长度的组合,在保
证加工效率的情况下,尽可能减小主切削力 Fc,以尽
可能减小刀具系统的变形,从而保证孔的加工精度。
高速镗孔时,使用山特维克可乐满镗孔刀具:
粗加工刀杆直径 d = 40 mm;
悬伸长度 L = 100 mm;
切削深度为 aP = 0.2 mm;
(1)形状精度。为了减小夹紧变形,设计开口的 环形过渡环,在加工内孔时,让夹紧力直接作用在过 渡环上,使夹紧力分布均匀,减小夹紧变形。加工外 圆时,设计定位心轴,心轴带有一定锥度,加工时将 工件装夹在心轴上,用专用的多层卡盘夹住心轴,采 用“一夹一顶”的加工方法,减小夹紧变形。
通过以上措施,加工中的夹紧变形,就被控制在 允许的范围内,从而保证了薄壁件的形状精度。
15
Equipment Manufactring Technology No.6,2012
的误差,主要是夹紧变形引起的形状误差;内孔加工 时,镗杆刚性不足而引起的孔的尺寸误差,和夹紧变 形引起的误差占主导地位。因此,在薄套类零件的高 速切削中,产生的加工误差,主要来源于工件的夹紧 变形和镗杆刚性不足。解决好这两方面的问题,也就 解决了高速切削的精度问题。
《装备制造技术》2012 年第 6 期
高速切削技术在薄套类零件加工中的应用研究
施振华
(南通纺织职业技术学院,江苏 南通 226007)
摘 要:从薄套类零件的加工效率、加工精度与安全性等角度出发,探讨了薄套类零件高速切削的效率和加工精度的影 响因素,分析了加工中的优势和可行性;针对此类零件刚性差、加工中易产生振动和夹紧变形的工艺特点及生产实际要 求,对高速切削加工中存在的工艺问题进行了分析,给出了具体的解决措施;生产实际表明,在薄套类零件的加工中采 用高速切削技术,加工效率高,品质好。 关键词:薄套类零件;加工效率;刚性;夹紧变形;加工精度;高速切削加工
(2)尺寸精度。高速镗孔时,主切削力 Fc 远大于 其他切削力,其他切削力对加工精度的影响与主切 削力相比,可以忽略不计。根据材料力学理论,刀具 系统可以简化为受横向集中力 Fc 和轴向力 Ff 作用 下的简支梁,即图 2 所示的力学模型。
工件
Fc
Y
Fc
刀架
L Ff
图 2 高速镗孔加工力学模型
在集中力 Fc 作用下,在 Fc 方向上刀具系统会产
2 加工的可行性
2.1 高速切削的效率和优势 高速切削技术是近几年发展起来的一项先进制
造技术,被称为是 21 世纪机械制造业的一场技术革 命[2 ̄3]。根据文献[4]的论述,高速切削的效率,可用单 位时间内的金属去除量 Vc 来表示,它等于切削速度 ν、进给量 f、切削深度 aP 的乘积,即 Vc 可根据公式 Vc = νfaP 来计算。
0.8
2×1
3.2 其余
+0.025
准1050.003 +0.200
准800 -0.025
准90-0.012 准112
55
4×2 0.8
图 1 典型薄套类零件结构示意图
1 薄套类零件的设计加工要求
图 1 所示的薄套类零件,所有表面均需加工。
+0.025
主 要 加 工 表 面 为 外 圆 Φ(105 +0.033 )mm、内 孔
2005.
(下转第 27 页)
17
பைடு நூலகம்
一次的冲压循环。 5.4 导向方式的选择
为了提高模具寿命和工件品质,方便安装调整, 由于弯曲零件尺寸比较小,且零件的精度要求不高, 故使用后侧导柱式模架。
6 结束语
冲压方案是否合理,直接影响模具工艺设计、结 构设计。合理的冲压方案,可以使模具设计方案可靠 性达到 80 % 以上。从而缩短模具设计与制造周期 2/5(对于复杂模具而言),并提高模具品质和产品合
参考文献:
[1] 董德君. 薄壁零件的车削[J]. 机械工人,2001,(9):10-11.
[2] 王西彬,解丽静. 超高速切削技术及其新进展[J]. 中国机械
工程,2000,(11):190-194.
[3] 艾 兴,等. 高速切削加工技术[M]. 北京:国防工业出版社,
2003.
[4] Elbestaui M A. High Speed Milling of Dies and Moulds in Their
Hardened State[J]. Annals of the C1RP,1997,46(1):57-65.
[5] 刘战强,等. 高速切削数据库与数控编程技术[M]. 北京:国
防工业出版社,2009.
[6] 左敦稳. 现代加工技术[M]. 北京:北京航空航天大学出版
社,2005.
[7] 王贵成. 高速切削工具系统[M]. 北京:国防工业出版社,
此公式与传统理论切削效率具有相同的经验公 式表达式,但高速切削时的主轴转速与进给速度,远 高于常规加工时的主轴转速与进给速度,因而高速 切削的切削效率大大提高,高速切削比传统加工方 法效率提高 25 %~50 %,金属去除率提高 2~10 倍。薄套类零件采用高速切削,比常规加工具有明显 的效率优势。
中图分类号:TG506.1;TH162
文献标识码:A
文章编号:1672-545X(2012)06-0015-03
薄套类零件以其净质量小、结构紧凑等特点,广 泛应用于机械产品中[1]。但这种零件壁厚较小,刚性 较差,加工时在切削力和夹紧力的作用下,容易变 形,不容易保证加工品质。
从加工工艺的角度出发,分析了影响加工品质 的因素,对高速切削技术用于薄套类零件加工的可 能性,进行了分析与探讨,并结合高速切削中存在的 问题,给出了工艺设计的原则和具体的工艺措施。
压力,其对加工精度的影响可以不予考虑。高速镗
孔,能保证薄套类零件孔的尺寸精度。
2.3 高速切削的安全性
高速切削的转速很高,必须考虑安全问题。在薄