举例-蒸镀
电镀:水镀、溅镀、蒸镀的区别
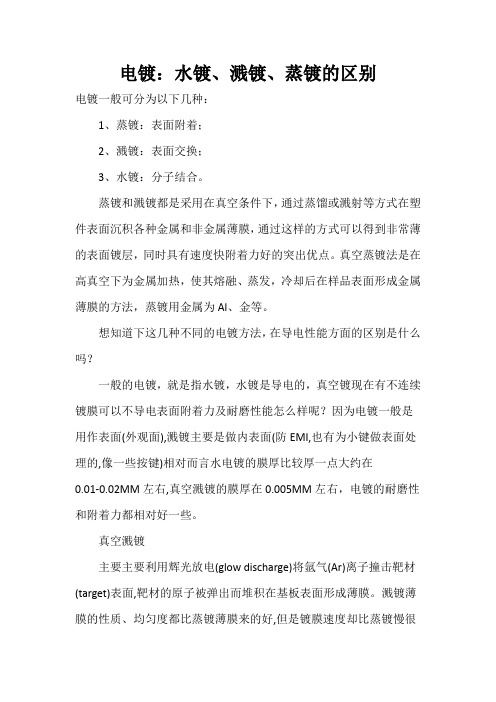
电镀:水镀、溅镀、蒸镀的区别电镀一般可分为以下几种:1、蒸镀:表面附着;2、溅镀:表面交换;3、水镀:分子结合。
蒸镀和溅镀都是采用在真空条件下,通过蒸馏或溅射等方式在塑件表面沉积各种金属和非金属薄膜,通过这样的方式可以得到非常薄的表面镀层,同时具有速度快附着力好的突出优点。
真空蒸镀法是在高真空下为金属加热,使其熔融、蒸发,冷却后在样品表面形成金属薄膜的方法,蒸镀用金属为Al、金等。
想知道下这几种不同的电镀方法,在导电性能方面的区别是什么吗?一般的电镀,就是指水镀,水镀是导电的,真空镀现在有不连续镀膜可以不导电表面附着力及耐磨性能怎么样呢?因为电镀一般是用作表面(外观面),溅镀主要是做内表面(防EMI,也有为小键做表面处理的,像一些按键)相对而言水电镀的膜厚比较厚一点大约在0.01-0.02MM左右,真空溅镀的膜厚在0.005MM左右,电镀的耐磨性和附着力都相对好一些。
真空溅镀主要主要利用辉光放电(glow discharge)将氩气(Ar)离子撞击靶材(target)表面,靶材的原子被弹出而堆积在基板表面形成薄膜。
溅镀薄膜的性质、均匀度都比蒸镀薄膜来的好,但是镀膜速度却比蒸镀慢很多。
新型的溅镀设备几乎都使用强力磁铁将电子成螺旋状运动以加速靶材周围的氩气离子化,造成靶与氩气离子间的撞击机率增加,提高溅镀速率。
一般金属镀膜大都采用直流溅镀,而不导电的陶磁材料则使用RF交流溅镀,基本的原理是在真空中利用辉光放电(glow discharge)将氩气(Ar)离子撞击靶材(target)表面,电浆中的阳离子会加速冲向作为被溅镀材的负电极表面,这个冲击将使靶材的物质飞出而沉积在基板上形成薄膜。
一般来说,利用溅镀制程进行薄膜披覆有几项特点:(1)金属、合金或绝缘物均可做成薄膜材料。
(2)再适当的设定条件下可将多元复杂的靶材制作出同一组成的薄膜。
(3)利用放电气氛中加入氧或其它的活性气体,可以制作靶材物质与气体分子的混合物或化合物。
蒸镀与溅镀介绍
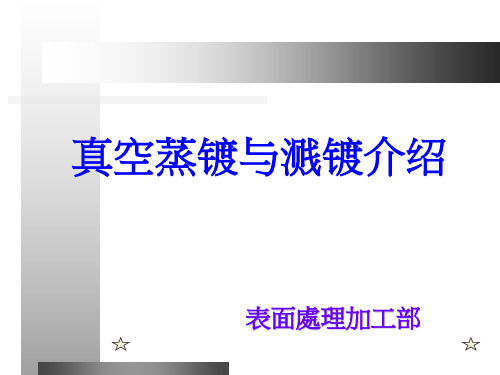
2.真空蒸发镀膜定义:在真空室中蒸发容器中待形成薄膜的原材料,
使其原子或分子从表面气化逸出,形成蒸气流,入射到固体(衬底
或基片)表面相
气相
B.气化原子或分子在蒸发源与基片之间的运输
C.蒸发原子或分子在基片表面上的沉积过程
4. 蒸发源的类型
電漿為一複雜的物質狀態其所有組成包括離子、 電子、中性原子與分子、受激態粒子、紫外線 等,有異於固態、液態、氣態亦被稱為物質的 第四態。
五.真空濺鍍之應用
1.3C產業如筆記型電腦、手機、ADSL等塑膠機殼之 金屬鍍膜以應用於防電磁波干擾;
2.3C產業如手機按鍵等塑膠元件(PC 、PMMA或 ABS),掃瞄器塑膠聚光面,與抗靜電層鍍膜;
3.IMD及其它顏色的鍍膜,不導電電鍍; 4.包裝材料; 5.生醫材料。
六.製程比較
方法
傳統水電鍍
優點
膜層厚
缺點
毒性強,工業污染大 膜厚難控制,膜質差 製程長,夾治具多 被鍍物原材質改變 材料受限 設備空間佔地大
濺鍍
環保製程無工業污染 膜質佳,膜厚易控制 被鍍物原材質不變 可連續性生產 可鍍多層金屬 材料不受限 製程短,夾治具少 佔地面積為傳統之1/3 符合TCO-99法規
真空蒸镀与溅镀介绍
表面處理加工部
真空蒸镀
真空溅镀
目录:
第一章.真空蒸镀介绍 第二章.真空溅镀介绍 第三章.离子镀介绍 第四章.应用范围 第五章.结束语
第一章.真空蒸镀介绍:
一.底涂 二.蒸镀 三.面涂
一.底漆(Basecaot)
目的: 1.填補射出模痕,增加平坦性及光澤 2.做為鍍膜的接著層,增加鍍膜附著力 3.調整鍍膜亮霧度 4.防止素材分子擴散至鍍膜層
第二章.真空溅镀介绍:
真空蒸镀的详细介绍

真空蒸镀的详细介绍真空蒸镀即真空蒸发镀膜。
这种方法是把装有基片的真空室抽成真空,气体压强达到10-2Pa以下加热镀料,使其原子或分子从表面气化逸出形成蒸气流,入射到基片表面,凝结形成固态薄膜。
1.真空蒸镀原理(1)膜料在真空状态下的蒸发特性。
单位时间内膜料单位面积上蒸发出来的材料质量称为蒸发速率。
理想的最高速率Gm(单位为kg/(m²·s))∶Gm=4.38×10-3Ps(Ar/T)1/2,式中,T为蒸发表面的热力学温度,单位为K,Ps为温度T时的材料饱和蒸发压,单位为Pa,Ar为膜料的相对原子质量或相对分子质量。
蒸镀时一般要求膜料的蒸气压在10-2~10-1Pa。
材料的Cm通常处在10-4~10-1Pa,因此可以估算出已知蒸发材料的所需加热温度。
(2)蒸气粒子的空间分布。
蒸气粒子的空间分布显著地影响了蒸发粒子在基体上的沉积速率以及基体上的膜厚分布。
这与蒸发源的形状和尺寸有关。
最简单的理想蒸发源有点和小平面两种类型。
2.真空蒸镀方式(1)电阻加热蒸发。
它是用丝状或片状的高熔点金属做成适当形状的蒸发源,将膜料放在其中,接通电源,电阻加热膜料而使其蒸发。
对蒸发源材料的基本要求是高熔点,低蒸气压,在蒸发温度下不会与膜料发生化学反应或互溶,具有一定的机械强度。
另外,电阻加热方式还要求蒸发源材料与膜料容易润湿,以保证蒸发状态稳定。
常用的蒸发源材料有钨、钼、钽、石墨、氮化硼等。
(2)电子束蒸发。
电阻加热方式中的膜料与蒸发源材料直接接触,两者容易互混,这对于半导基体元件等镀膜来说是需要避免的。
电子束加热方式能解决这个问题。
它的蒸发源是e形电子枪。
膜料放入水冷铜坩埚中,电子束自源发出,用磁场线圈使电子束聚焦和偏转,电子轨迹磁偏转270°,对膜料进行轰击和加热。
(3)高频加热。
它是在高频感应线圈中放入氧化铝或石墨坩埚对膜材料进行高频感应加热。
感应线圈通常用水冷铜管制造。
此法主要用于铝的大量蒸发。
蒸镀
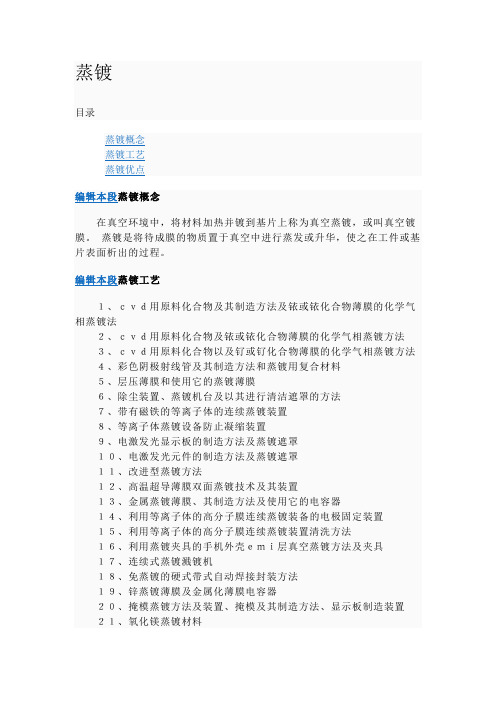
蒸镀目录编辑本段蒸镀概念在真空环境中,将材料加热并镀到基片上称为真空蒸镀,或叫真空镀膜。
蒸镀是将待成膜的物质置于真空中进行蒸发或升华,使之在工件或基片表面析出的过程。
编辑本段蒸镀工艺1、cvd用原料化合物及其制造方法及铱或铱化合物薄膜的化学气相蒸镀法2、cvd用原料化合物及铱或铱化合物薄膜的化学气相蒸镀方法3、cvd用原料化合物以及钌或钌化合物薄膜的化学气相蒸镀方法4、彩色阴极射线管及其制造方法和蒸镀用复合材料5、层压薄膜和使用它的蒸镀薄膜6、除尘装置、蒸镀机台及以其进行清洁遮罩的方法7、带有磁铁的等离子体的连续蒸镀装置8、等离子体蒸镀设备防止凝缩装置9、电激发光显示板的制造方法及蒸镀遮罩10、电激发光元件的制造方法及蒸镀遮罩11、改进型蒸镀方法12、高温超导薄膜双面蒸镀技术及其装置13、金属蒸镀薄膜、其制造方法及使用它的电容器14、利用等离子体的高分子膜连续蒸镀装备的电极固定装置15、利用等离子体的高分子膜连续蒸镀装置清洗方法16、利用蒸镀夹具的手机外壳emi层真空蒸镀方法及夹具17、连续式蒸镀溅镀机18、免蒸镀的硬式带式自动焊接封装方法19、锌蒸镀薄膜及金属化薄膜电容器20、掩模蒸镀方法及装置、掩模及其制造方法、显示板制造装置21、氧化镁蒸镀材料22、一氧化硅蒸镀材料及其制造方法、制造原料和制造装置23、一氧化硅蒸镀材料及其制造方法24、一种利用强电场的真空热蒸镀成膜方法25、一种用于半导体激光器腔面蒸镀的非接触固定方式的夹具26、阴极电弧蒸镀方式淀积类金刚石碳膜的制备方法27、用于镭射压印蒸镀的双向拉伸聚丙烯基膜28、用于镭射压印蒸镀的双向拉伸聚丙烯基膜及其制造方法29、用于生产高折射率光学涂层的蒸镀用材料30、用于制作有机电致发光显示器的蒸镀装置31、有机el元件制造用蒸镀装置的室内的清洗方法32、有机场致发光膜蒸镀用蒸镀源33、有机发光二极管蒸镀机台34、有机膜蒸镀方法35、在光学基片上蒸镀镀膜的方法36、在光学基片上蒸镀镀膜的真空镀膜设备37、真空电弧蒸镀方法及装置38、真空蒸镀设备用的蒸镀装置39、蒸镀材料及其利用该材料制造光学薄膜40、蒸镀材料其制备方法和用该材料制备光学涂层方法41、蒸镀方法及显示装置的制造方法42、蒸镀方法及蒸镀装置43、蒸镀膜44、蒸镀掩模及制法、显示装置及制法以及具有其的电子机器45、蒸镀用坩锅46、蒸镀用掩模及其制造方法47、蒸镀装置48、蒸镀装置49、蒸镀装置50、蒸镀装置51、直接蒸镀用树脂组合物、使用该组合物的模塑制品以及表面金属化处理的灯罩52、制作电致发光显示器的、使用电磁铁的蒸镀装置及采用此装置的蒸镀方法编辑本段蒸镀优点1.能在金属、半导体、绝缘体甚至塑料、纸张、织物表面上沉积金属、半导体、绝缘体、不同成分比的合金、化合物及部分有基聚合物等的薄膜,其适用范围之广是其它方法无法与之比拟的2.可以不同的沉积速率、不同的基板温度和不同的蒸气分子入射角蒸镀成膜,因而可得到不同显微结构和3.结晶形态(单晶、多晶或非晶等)的薄膜;4.薄膜的纯度很高5.易于在线检测和控制薄膜的厚度与成分。
(PVD)(蒸镀)

合金,由于原子间的结合力小于化合物中原子间的结合力, 因此,合金中各元素的蒸发过程可近似视为各元素相互独立 的蒸发过程,就像纯元素蒸发过程一样。但即使如此,合金 在蒸发和沉积过程中也会产生成分的偏差.
加大蒸发源到衬底表面的距离,但此法会降低沉积速率及 增加蒸发材料损耗; 转动衬底;
如果同时需要沉积多个样品、且每个样品的尺寸相对较小 时,可以考虑采取如图所示的衬底放置方法来改善样品间薄 膜厚度的差别,此时面蒸发源和衬底表面同处一个圆周。
cos cos 1 r
2 r0
其中r0 是相应圆周的半径,则衬底 上沉积的物质的质量密度分别为:
❖蒸发源
真空蒸发所采用的设备根据使用目的的不同有很大差别。 从简单的电阻加热蒸镀装置到极其复杂的分子束外延设备, 都属于真空蒸发范畴。在蒸发沉积装置中,最重要的组成 部分是物质的蒸发源,根据其加热原理可分为以下类型。
1、电阻加热蒸发源
(1)电阻加热蒸发法:
特别适用1500度以下材料的蒸发,加热体一般采用低电压大 电流供电方式(150-500A*10V)。采用钽、钼、钨等高熔点 金属,做成适当形状的加热装置(也称“蒸发源”,注意与 “蒸发材料”区别),其上装入待蒸发材料,通以电流后, 对蒸发材料进行直接加热蒸发,或者把待蒸发材料放入Al2O3、 BeO等坩埚中进行间接加热蒸发,
残余气体对薄膜纯度的影响
在沉积过程中,残余气体的分子和蒸发物质的原子将分别
射向衬底,并可能同时沉积在衬底上,蒸发物质的沉积速
率为:
G N As
MA
其中ρ为沉积物质密度,s为厚度沉积速率。残余气体分子的
蒸镀氧化铝

蒸镀氧化铝
蒸镀氧化铝是一种常见的材料处理技术,常用于制造电子元件、光学器件和装饰品等。
蒸镀是指在真空条件下,将金属或非金属材料加热蒸发,使其沉积在基底上形成薄膜的过程。
氧化铝是一种高硬度、高熔点的材料,具有良好的耐热性、耐腐蚀性和光学性能,因此被广泛应用于蒸镀领域。
蒸镀氧化铝的过程通常包括以下步骤:
1. 准备基底:首先需要准备一个干净、平整的基底,通常使用玻璃或金属作为基底材料。
2. 真空处理:将基底放入真空室内,抽真空以去除基底表面的氧气和水分,避免氧化和污染。
3. 蒸发氧化铝:将氧化铝材料放入蒸发源中,加热蒸发,使其沉积在基底上形成薄膜。
4. 控制厚度:通过控制蒸发时间和速度,可以控制氧化铝薄膜的厚度和均匀性。
5. 后续处理:蒸镀完成后,需要对氧化铝薄膜进行后续处理,如退火、蚀刻等,以提高其性能和可靠性。
需要注意的是,蒸镀氧化铝需要在真空条件下进行,因此需要使用专门的设备和技术,以确保蒸镀过程的顺利进行和蒸镀产品的质量。
蒸镀镍基合金
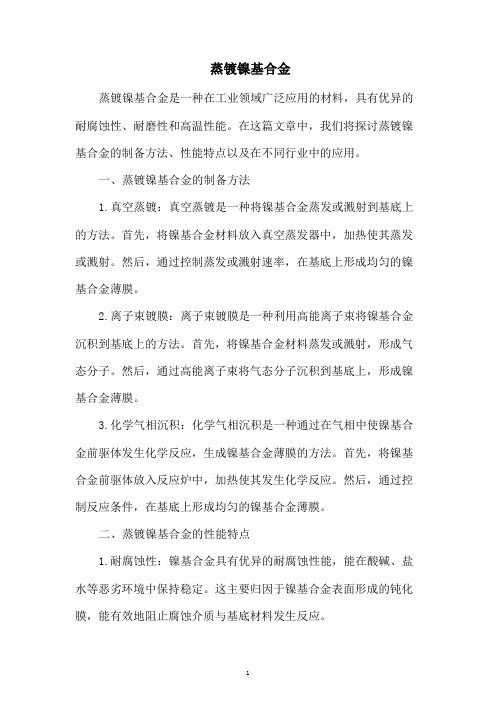
蒸镀镍基合金蒸镀镍基合金是一种在工业领域广泛应用的材料,具有优异的耐腐蚀性、耐磨性和高温性能。
在这篇文章中,我们将探讨蒸镀镍基合金的制备方法、性能特点以及在不同行业中的应用。
一、蒸镀镍基合金的制备方法1.真空蒸镀:真空蒸镀是一种将镍基合金蒸发或溅射到基底上的方法。
首先,将镍基合金材料放入真空蒸发器中,加热使其蒸发或溅射。
然后,通过控制蒸发或溅射速率,在基底上形成均匀的镍基合金薄膜。
2.离子束镀膜:离子束镀膜是一种利用高能离子束将镍基合金沉积到基底上的方法。
首先,将镍基合金材料蒸发或溅射,形成气态分子。
然后,通过高能离子束将气态分子沉积到基底上,形成镍基合金薄膜。
3.化学气相沉积:化学气相沉积是一种通过在气相中使镍基合金前驱体发生化学反应,生成镍基合金薄膜的方法。
首先,将镍基合金前驱体放入反应炉中,加热使其发生化学反应。
然后,通过控制反应条件,在基底上形成均匀的镍基合金薄膜。
二、蒸镀镍基合金的性能特点1.耐腐蚀性:镍基合金具有优异的耐腐蚀性能,能在酸碱、盐水等恶劣环境中保持稳定。
这主要归因于镍基合金表面形成的钝化膜,能有效地阻止腐蚀介质与基底材料发生反应。
2.耐磨性:镍基合金具有高硬度和优异的耐磨性,在磨损环境下能够保持表面的完整性,延长部件的使用寿命。
3.高温性能:镍基合金具有优异的高温性能,能够在1000℃以上的高温环境下保持结构和性能稳定。
这主要归因于镍基合金的优异的抗氧化性和高温下的力学性能。
4.导电性:镍基合金具有良好的导电性能,可以应用于电子元器件、导线等部件。
5.美观:镍基合金具有金属光泽,表面光滑,可以用于装饰性涂层。
三、蒸镀镍基合金的应用领域1.化工行业:镍基合金在化工行业中有广泛应用,如反应釜、换热器、阀门等。
其耐腐蚀性能能够保证设备在恶劣环境下长期稳定运行。
2.石油、天然气行业:镍基合金在石油、天然气行业中有广泛应用,如钻柱、套管、阀门等。
其耐磨性和高温性能能够保证设备在极端环境下正常工作。
钨舟蒸镀二氧化硅蒸镀

钨舟蒸镀二氧化硅蒸镀
钨舟蒸镀二氧化硅是一种常见的薄膜制备技术,通常用于光学、电子和半导体领域。
以下是一般的钨舟蒸镀二氧化硅的过程概述:
1. 准备钨舟:钨舟是一个用来盛放蒸发物质的小船,通常由钨制成。
确保钨舟干净,并将其放置在蒸发设备中。
2. 装载二氧化硅:将二氧化硅粉末或颗粒加载到钨舟中。
可以使用合适的工具将二氧化硅均匀分布在钨舟的表面上。
3. 真空系统:将蒸发设备连接到真空系统,以创造一个低气压环境。
这有助于防止气体分子与蒸发的二氧化硅相互作用,并提高薄膜的质量。
4. 加热钨舟:通过加热设备对钨舟进行加热,使二氧化硅蒸发。
加热的温度和时间取决于所使用的二氧化硅源和所需的蒸发速率。
5. 蒸镀二氧化硅:在加热钨舟的过程中,二氧化硅开始蒸发并在基底上沉积形成薄膜。
基底可以是玻璃、硅片或其他适当的材料。
6. 控制沉积速率:根据需要,可以调整加热温度和时间来控制二氧化硅的沉积速率。
较高的温度通常会导致更快的沉积速率。
7. 薄膜特性:蒸镀的二氧化硅薄膜可以具有不同的特性,如折射率、厚度和光学性能。
这些特性可以通过控制蒸发条件和沉积参数来调整。
需要注意的是,具体的蒸镀过程可能因设备和应用的不同而有所差异。
在进行钨舟蒸镀二氧化硅之前,建议参考相关的设备操作手册和实验指南,以确保正确的操作和最佳的结果。
斜角蒸镀 单分子-概述说明以及解释
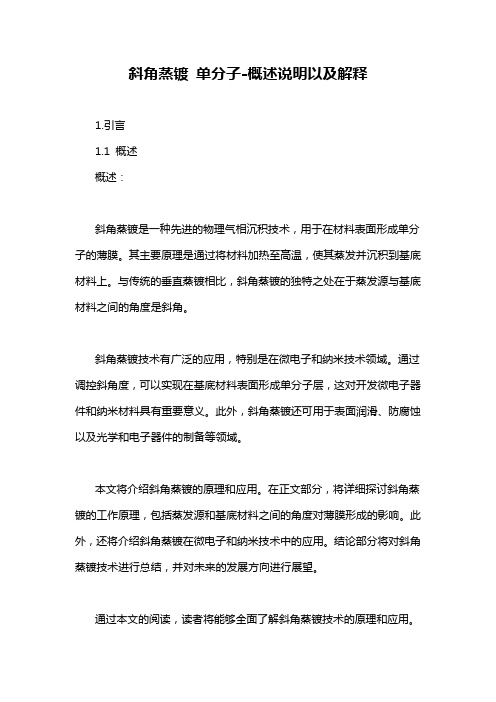
斜角蒸镀单分子-概述说明以及解释1.引言1.1 概述概述:斜角蒸镀是一种先进的物理气相沉积技术,用于在材料表面形成单分子的薄膜。
其主要原理是通过将材料加热至高温,使其蒸发并沉积到基底材料上。
与传统的垂直蒸镀相比,斜角蒸镀的独特之处在于蒸发源与基底材料之间的角度是斜角。
斜角蒸镀技术有广泛的应用,特别是在微电子和纳米技术领域。
通过调控斜角度,可以实现在基底材料表面形成单分子层,这对开发微电子器件和纳米材料具有重要意义。
此外,斜角蒸镀还可用于表面润滑、防腐蚀以及光学和电子器件的制备等领域。
本文将介绍斜角蒸镀的原理和应用。
在正文部分,将详细探讨斜角蒸镀的工作原理,包括蒸发源和基底材料之间的角度对薄膜形成的影响。
此外,还将介绍斜角蒸镀在微电子和纳米技术中的应用。
结论部分将对斜角蒸镀技术进行总结,并对未来的发展方向进行展望。
通过本文的阅读,读者将能够全面了解斜角蒸镀技术的原理和应用。
希望本文能为该领域的研究者提供参考,并为相关领域的技术发展做出贡献。
文章结构部分的内容可以描述整篇文章的组织结构和各个章节的主题。
在这篇文章中,文章结构部分可以写成以下内容:"1.2 文章结构本篇文章主要分为引言、正文和结论三个部分。
引言部分将概述斜角蒸镀单分子技术的背景和意义,并介绍本文的目的。
在概述中,将阐述斜角蒸镀技术在材料科学和表面工艺中的应用前景。
在目的部分,将明确本文的研究目标和意义,为读者提供清晰的认识和预期。
正文部分将重点介绍斜角蒸镀原理和应用。
在斜角蒸镀原理部分,将详细解释斜角蒸镀的工作原理和基本步骤,包括材料蒸发、蒸发物质运移和沉积表面的形成。
在斜角蒸镀应用部分,将探讨斜角蒸镀在材料制备、表面涂层和纳米器件等领域的具体应用,以及在这些领域中的优势和潜在挑战。
结论部分将对本文进行总结,并展望斜角蒸镀单分子技术的未来发展方向。
在总结部分,将概括文章的主要观点和重要发现,以强调斜角蒸镀单分子技术的重要性和价值。
c60蒸镀参数
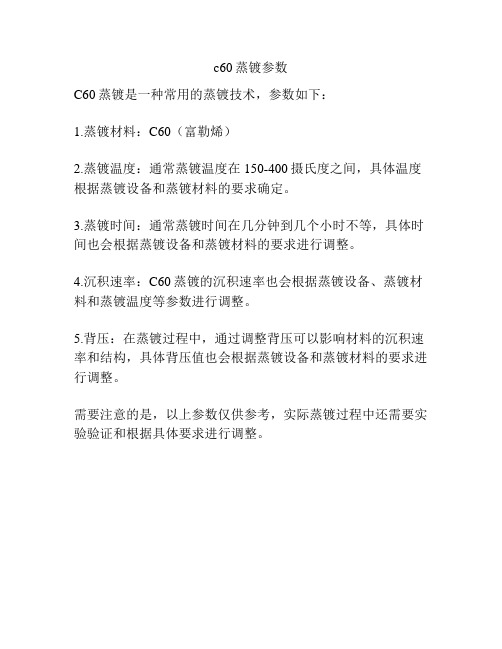
c60蒸镀参数
C60蒸镀是一种常用的蒸镀技术,参数如下:
1.蒸镀材料:C60(富勒烯)
2.蒸镀温度:通常蒸镀温度在150-400摄氏度之间,具体温度根据蒸镀设备和蒸镀材料的要求确定。
3.蒸镀时间:通常蒸镀时间在几分钟到几个小时不等,具体时间也会根据蒸镀设备和蒸镀材料的要求进行调整。
4.沉积速率:C60蒸镀的沉积速率也会根据蒸镀设备、蒸镀材料和蒸镀温度等参数进行调整。
5.背压:在蒸镀过程中,通过调整背压可以影响材料的沉积速率和结构,具体背压值也会根据蒸镀设备和蒸镀材料的要求进行调整。
需要注意的是,以上参数仅供参考,实际蒸镀过程中还需要实验验证和根据具体要求进行调整。
钨舟蒸镀二氧化硅蒸镀
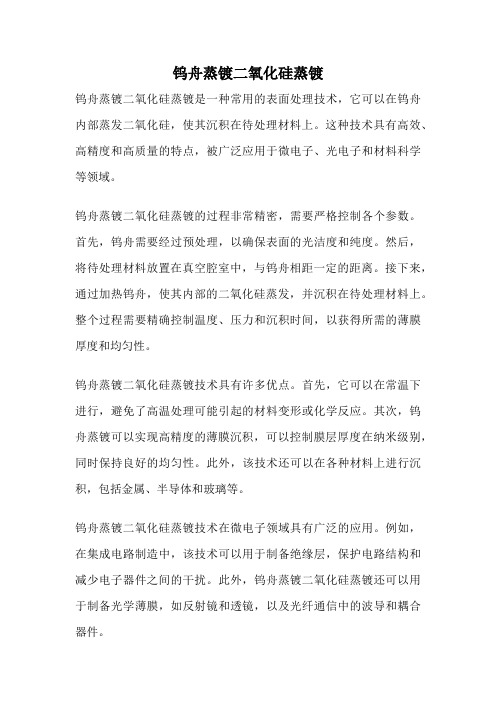
钨舟蒸镀二氧化硅蒸镀
钨舟蒸镀二氧化硅蒸镀是一种常用的表面处理技术,它可以在钨舟内部蒸发二氧化硅,使其沉积在待处理材料上。
这种技术具有高效、高精度和高质量的特点,被广泛应用于微电子、光电子和材料科学等领域。
钨舟蒸镀二氧化硅蒸镀的过程非常精密,需要严格控制各个参数。
首先,钨舟需要经过预处理,以确保表面的光洁度和纯度。
然后,将待处理材料放置在真空腔室中,与钨舟相距一定的距离。
接下来,通过加热钨舟,使其内部的二氧化硅蒸发,并沉积在待处理材料上。
整个过程需要精确控制温度、压力和沉积时间,以获得所需的薄膜厚度和均匀性。
钨舟蒸镀二氧化硅蒸镀技术具有许多优点。
首先,它可以在常温下进行,避免了高温处理可能引起的材料变形或化学反应。
其次,钨舟蒸镀可以实现高精度的薄膜沉积,可以控制膜层厚度在纳米级别,同时保持良好的均匀性。
此外,该技术还可以在各种材料上进行沉积,包括金属、半导体和玻璃等。
钨舟蒸镀二氧化硅蒸镀技术在微电子领域具有广泛的应用。
例如,在集成电路制造中,该技术可以用于制备绝缘层,保护电路结构和减少电子器件之间的干扰。
此外,钨舟蒸镀二氧化硅蒸镀还可以用于制备光学薄膜,如反射镜和透镜,以及光纤通信中的波导和耦合器件。
钨舟蒸镀二氧化硅蒸镀是一种高效、高精度和高质量的表面处理技术。
它在微电子、光电子和材料科学等领域发挥着重要作用。
通过精确控制各个参数,可以获得所需的薄膜厚度和均匀性。
我们相信,随着技术的不断发展,钨舟蒸镀二氧化硅蒸镀将在更多领域展现出其巨大潜力。
铝蒸镀参数
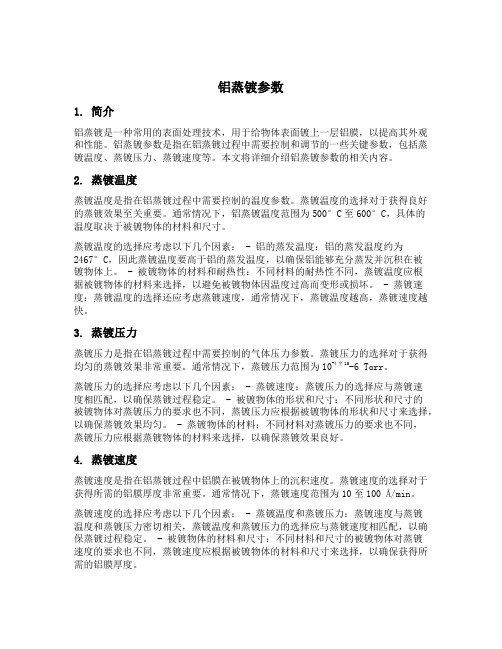
铝蒸镀参数1. 简介铝蒸镀是一种常用的表面处理技术,用于给物体表面镀上一层铝膜,以提高其外观和性能。
铝蒸镀参数是指在铝蒸镀过程中需要控制和调节的一些关键参数,包括蒸镀温度、蒸镀压力、蒸镀速度等。
本文将详细介绍铝蒸镀参数的相关内容。
2. 蒸镀温度蒸镀温度是指在铝蒸镀过程中需要控制的温度参数。
蒸镀温度的选择对于获得良好的蒸镀效果至关重要。
通常情况下,铝蒸镀温度范围为500°C至600°C,具体的温度取决于被镀物体的材料和尺寸。
蒸镀温度的选择应考虑以下几个因素: - 铝的蒸发温度:铝的蒸发温度约为2467°C,因此蒸镀温度要高于铝的蒸发温度,以确保铝能够充分蒸发并沉积在被镀物体上。
- 被镀物体的材料和耐热性:不同材料的耐热性不同,蒸镀温度应根据被镀物体的材料来选择,以避免被镀物体因温度过高而变形或损坏。
- 蒸镀速度:蒸镀温度的选择还应考虑蒸镀速度,通常情况下,蒸镀温度越高,蒸镀速度越快。
3. 蒸镀压力蒸镀压力是指在铝蒸镀过程中需要控制的气体压力参数。
蒸镀压力的选择对于获得均匀的蒸镀效果非常重要。
通常情况下,蒸镀压力范围为10-4至10-6 Torr。
蒸镀压力的选择应考虑以下几个因素: - 蒸镀速度:蒸镀压力的选择应与蒸镀速度相匹配,以确保蒸镀过程稳定。
- 被镀物体的形状和尺寸:不同形状和尺寸的被镀物体对蒸镀压力的要求也不同,蒸镀压力应根据被镀物体的形状和尺寸来选择,以确保蒸镀效果均匀。
- 蒸镀物体的材料:不同材料对蒸镀压力的要求也不同,蒸镀压力应根据蒸镀物体的材料来选择,以确保蒸镀效果良好。
4. 蒸镀速度蒸镀速度是指在铝蒸镀过程中铝膜在被镀物体上的沉积速度。
蒸镀速度的选择对于获得所需的铝膜厚度非常重要。
通常情况下,蒸镀速度范围为10至100 Å/mi n。
蒸镀速度的选择应考虑以下几个因素: - 蒸镀温度和蒸镀压力:蒸镀速度与蒸镀温度和蒸镀压力密切相关,蒸镀温度和蒸镀压力的选择应与蒸镀速度相匹配,以确保蒸镀过程稳定。
蒸镀 名词解释

蒸镀1. 什么是蒸镀?蒸镀是一种表面处理技术,通过在材料表面形成一层金属薄膜来改善材料的性能。
蒸镀过程涉及将金属材料加热至其蒸发温度,然后将蒸发的金属气体沉积在待处理物体的表面上。
这种技术常用于改善材料的外观、耐腐蚀性和导电性。
2. 蒸镀的原理蒸镀的原理基于蒸发和凝结的物理过程。
首先,将待处理物体放置在真空腔室中,然后加热金属源材料,使其达到蒸发温度。
蒸发的金属原子会在真空腔室中形成蒸汽,然后通过碰撞和扩散的过程,沉积在待处理物体的表面上。
在表面上沉积的金属原子会逐渐形成一层金属薄膜。
蒸镀过程中,还需要控制蒸发源和待处理物体之间的距离、加热温度和真空度等参数,以确保金属原子能够均匀沉积在待处理物体的表面上,并形成致密、均匀的薄膜。
3. 蒸镀的应用领域蒸镀技术广泛应用于多个领域,包括电子、光学、化工和材料科学等。
以下是一些常见的蒸镀应用领域:3.1 电子领域在电子领域,蒸镀常用于制造半导体器件、集成电路和显示屏等。
通过在半导体器件上蒸镀金属薄膜,可以改善其导电性能、增强信号传输和提高器件的稳定性。
同时,蒸镀还可用于制造电阻器、电容器和电感器等电子元件。
3.2 光学领域在光学领域,蒸镀常用于制造反射镜、滤光片和镀膜玻璃等光学元件。
通过在光学器件表面蒸镀金属薄膜或多层膜,可以改变其光学性能,如增强反射率、减少光损失和提高透过率。
蒸镀还可用于制造光学镜片、透镜和光学纤维等。
3.3 化工领域在化工领域,蒸镀常用于制造催化剂和防腐蚀涂层等。
通过在催化剂表面蒸镀金属薄膜,可以增加其表面积和催化活性,提高催化反应效率。
蒸镀还可用于制造防腐蚀涂层,保护金属材料免受腐蚀和氧化的侵害。
3.4 材料科学领域在材料科学领域,蒸镀常用于研究材料的表面性质和界面现象等。
通过在材料表面蒸镀金属薄膜,可以改变其表面的化学和物理性质,如增加材料的硬度、耐磨性和抗氧化性。
蒸镀还可用于制备多层膜材料和纳米结构材料等。
4. 蒸镀的优点和局限性4.1 优点•蒸镀过程简单,操作方便,适用于各种形状和材料的待处理物体。
化学蒸镀法
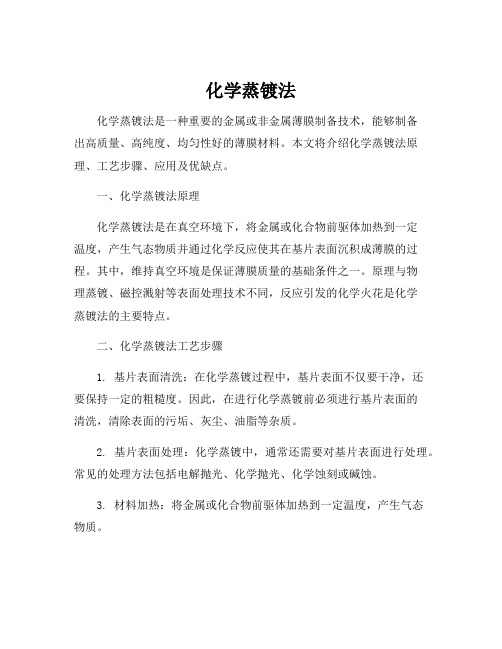
化学蒸镀法化学蒸镀法是一种重要的金属或非金属薄膜制备技术,能够制备出高质量、高纯度、均匀性好的薄膜材料。
本文将介绍化学蒸镀法原理、工艺步骤、应用及优缺点。
一、化学蒸镀法原理化学蒸镀法是在真空环境下,将金属或化合物前驱体加热到一定温度,产生气态物质并通过化学反应使其在基片表面沉积成薄膜的过程。
其中,维持真空环境是保证薄膜质量的基础条件之一。
原理与物理蒸镀、磁控溅射等表面处理技术不同,反应引发的化学火花是化学蒸镀法的主要特点。
二、化学蒸镀法工艺步骤1. 基片表面清洗:在化学蒸镀过程中,基片表面不仅要干净,还要保持一定的粗糙度。
因此,在进行化学蒸镀前必须进行基片表面的清洗,清除表面的污垢、灰尘、油脂等杂质。
2. 基片表面处理:化学蒸镀中,通常还需要对基片表面进行处理。
常见的处理方法包括电解抛光、化学抛光、化学蚀刻或碱蚀。
3. 材料加热:将金属或化合物前驱体加热到一定温度,产生气态物质。
4. 反应气氛控制:在化学蒸镀中,反应气氛非常重要。
不同的材料需要不同的反应气氛。
常见的反应气体包括氮气、氧气、氢气、氩气等。
5. 沉积控制:通过调节加热温度和反应气氛,可以对膜的厚度、成分等进行精确地控制。
6. 冷却和后处理:沉积完成后,需要进行冷却和后处理,包括基片退火、表面处理等。
三、化学蒸镀法应用化学蒸镀法广泛应用于半导体器件、光电器件、微纳电子器件等领域。
在半导体器件中,化学蒸镀法可以用于制备金属层、金属氧化物层、硅层等。
在光电器件领域,化学蒸镀法可以用于制备金属反射层、透明导电层、光吸收层等。
同时,化学蒸镀法还可以制备修饰表面的薄膜,如合成梯度薄膜和复合薄膜等。
四、化学蒸镀法优缺点优点:1)能够在低温下进行沉积,有利于保护基片性质;2)沉积后薄膜具有较高的密度和致密度,不易产生缺陷;3)化学蒸镀法制备的薄膜成分均匀,化学反应比较灵活,能够制备出多种材料。
缺点:1)制备过程中需要考虑反应气氛,反应条件比较苛刻;2)化学蒸镀过程中,不同材料之间常常造成飞溅,需要对真空炉内进行有效隔离。
真空蒸镀金属薄膜工艺
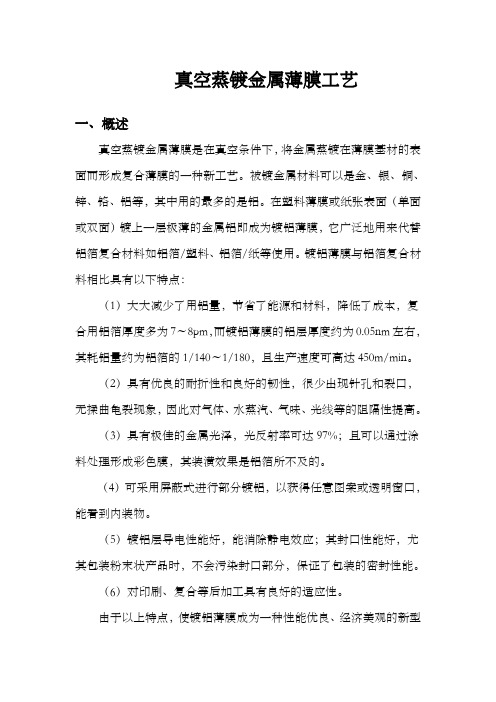
真空蒸镀金属薄膜工艺一、概述真空蒸镀金属薄膜是在真空条件下,将金属蒸镀在薄膜基材的表面而形成复合薄膜的一种新工艺。
被镀金属材料可以是金、银、铜、锌、铬、铝等,其中用的最多的是铝。
在塑料薄膜或纸张表面(单面或双面)镀上一层极薄的金属铝即成为镀铝薄膜,它广泛地用来代替铝箔复合材料如铝箔/塑料、铝箔/纸等使用。
镀铝薄膜与铝箔复合材料相比具有以下特点:(1)大大减少了用铝量,节省了能源和材料,降低了成本,复合用铝箔厚度多为7~8pm,而镀铝薄膜的铝层厚度约为0.05nm左右,其耗铝量约为铝箔的1/140~1/180,且生产速度可高达450m/min。
(2)具有优良的耐折性和良好的韧性,很少出现针孔和裂口,无揉曲龟裂现象,因此对气体、水蒸汽、气味、光线等的阻隔性提高。
(3)具有极佳的金属光泽,光反射率可达97%;且可以通过涂料处理形成彩色膜,其装潢效果是铝箔所不及的。
(4)可采用屏蔽式进行部分镀铝,以获得任意图案或透明窗口,能看到内装物。
(5)镀铝层导电性能好,能消除静电效应;其封口性能好,尤其包装粉末状产品时,不会污染封口部分,保证了包装的密封性能。
(6)对印刷、复合等后加工具有良好的适应性。
由于以上特点,使镀铝薄膜成为一种性能优良、经济美观的新型复合薄膜,在许多方面已取代了铝箔复合材料。
主要用于风味食品、农产品的真空包装,以及药品、化妆品、香烟的包装。
另外,镀铝薄膜也大量用作印刷中的烫金材料和商标标签材料等。
二、镀膜基材镀铝薄膜的基材主要是塑料薄膜和纸张。
真空蒸镀工艺对被镀基材有以下几点要求:(1)耐热性好,基材必须能耐受蒸发源的辐射热和蒸发物的冷凝潜热。
(2)从薄膜基材上产生的挥发性物质要少;对吸湿性大的基材,在镀膜前理。
(3)基材应具有一定的强度和表面平滑度。
(4)对蒸镀层的粘接性良好;对于PP、PE等非极性材料,蒸镀前应进行表面处理、以提高与镀层的粘接性。
常用的薄膜基材有:BOPET、BONY、BOPP、PE、PVC等塑料薄膜和纸张类。
蒸镀材料分类
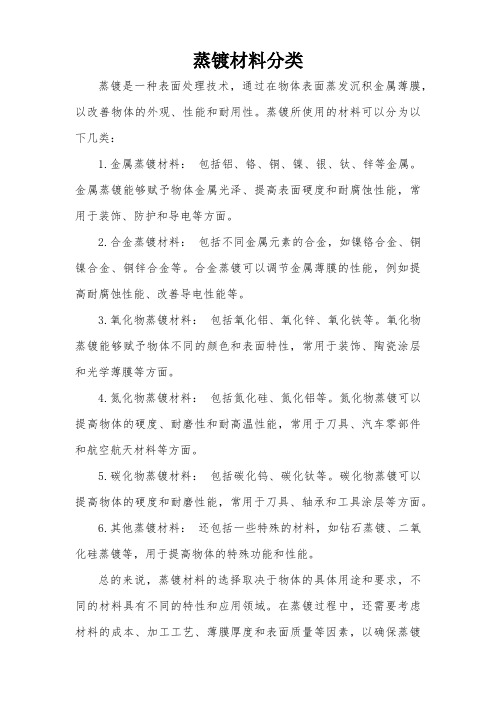
蒸镀材料分类
蒸镀是一种表面处理技术,通过在物体表面蒸发沉积金属薄膜,以改善物体的外观、性能和耐用性。
蒸镀所使用的材料可以分为以下几类:
1.金属蒸镀材料:包括铝、铬、铜、镍、银、钛、锌等金属。
金属蒸镀能够赋予物体金属光泽、提高表面硬度和耐腐蚀性能,常用于装饰、防护和导电等方面。
2.合金蒸镀材料:包括不同金属元素的合金,如镍铬合金、铜镍合金、铜锌合金等。
合金蒸镀可以调节金属薄膜的性能,例如提高耐腐蚀性能、改善导电性能等。
3.氧化物蒸镀材料:包括氧化铝、氧化锌、氧化铁等。
氧化物蒸镀能够赋予物体不同的颜色和表面特性,常用于装饰、陶瓷涂层和光学薄膜等方面。
4.氮化物蒸镀材料:包括氮化硅、氮化铝等。
氮化物蒸镀可以提高物体的硬度、耐磨性和耐高温性能,常用于刀具、汽车零部件和航空航天材料等方面。
5.碳化物蒸镀材料:包括碳化钨、碳化钛等。
碳化物蒸镀可以提高物体的硬度和耐磨性能,常用于刀具、轴承和工具涂层等方面。
6.其他蒸镀材料:还包括一些特殊的材料,如钻石蒸镀、二氧化硅蒸镀等,用于提高物体的特殊功能和性能。
总的来说,蒸镀材料的选择取决于物体的具体用途和要求,不同的材料具有不同的特性和应用领域。
在蒸镀过程中,还需要考虑材料的成本、加工工艺、薄膜厚度和表面质量等因素,以确保蒸镀
效果的稳定和可靠。
蒸镀机 蒸发源
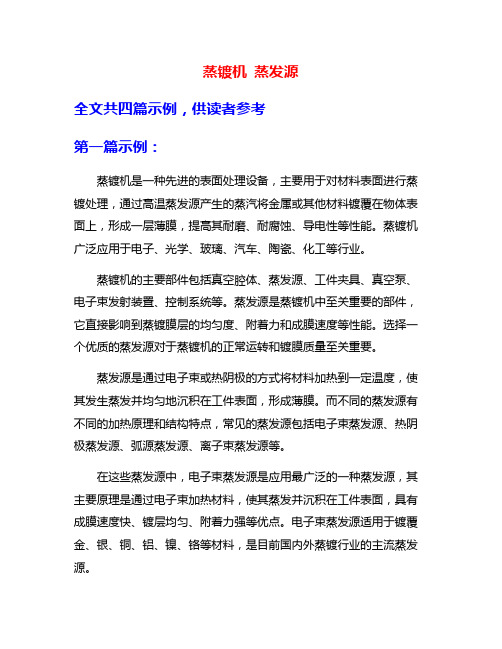
蒸镀机蒸发源全文共四篇示例,供读者参考第一篇示例:蒸镀机是一种先进的表面处理设备,主要用于对材料表面进行蒸镀处理,通过高温蒸发源产生的蒸汽将金属或其他材料镀覆在物体表面上,形成一层薄膜,提高其耐磨、耐腐蚀、导电性等性能。
蒸镀机广泛应用于电子、光学、玻璃、汽车、陶瓷、化工等行业。
蒸镀机的主要部件包括真空腔体、蒸发源、工件夹具、真空泵、电子束发射装置、控制系统等。
蒸发源是蒸镀机中至关重要的部件,它直接影响到蒸镀膜层的均匀度、附着力和成膜速度等性能。
选择一个优质的蒸发源对于蒸镀机的正常运转和镀膜质量至关重要。
蒸发源是通过电子束或热阴极的方式将材料加热到一定温度,使其发生蒸发并均匀地沉积在工件表面,形成薄膜。
而不同的蒸发源有不同的加热原理和结构特点,常见的蒸发源包括电子束蒸发源、热阴极蒸发源、弧源蒸发源、离子束蒸发源等。
在这些蒸发源中,电子束蒸发源是应用最广泛的一种蒸发源,其主要原理是通过电子束加热材料,使其蒸发并沉积在工件表面,具有成膜速度快、镀层均匀、附着力强等优点。
电子束蒸发源适用于镀覆金、银、铜、铝、镍、铬等材料,是目前国内外蒸镀行业的主流蒸发源。
弧源蒸发源和离子束蒸发源是一些特殊领域的蒸发源,其原理是通过弧放电或离子束轰击的方式将材料蒸发并沉积在工件表面,具有镀层致密、抗氧化等优点,适用于一些特殊环境下的蒸镀需求。
在选择蒸发源时,需要根据不同的工件材料、要求的镀层性能和生产效率等因素进行综合考虑。
蒸发源的性能、稳定性、寿命也是选择的重要因素。
优质的蒸发源供应商具有丰富的生产经验、技术实力和良好的售后服务体系,可以为用户提供可靠的蒸镀解决方案。
蒸发源作为蒸镀机中的核心部件,直接影响蒸镀膜层的质量和性能。
在蒸镀机的选型、使用和维护中,选择一个适合的蒸发源十分重要。
只有不断提升蒸发源的稳定性、性能和服务水平,才能更好地满足市场需求,推动蒸镀行业的发展。
【2000字】第二篇示例:蒸镀技术是一种常用的表面处理方法,广泛应用于电子、光学、医疗、汽车等领域。
- 1、下载文档前请自行甄别文档内容的完整性,平台不提供额外的编辑、内容补充、找答案等附加服务。
- 2、"仅部分预览"的文档,不可在线预览部分如存在完整性等问题,可反馈申请退款(可完整预览的文档不适用该条件!)。
- 3、如文档侵犯您的权益,请联系客服反馈,我们会尽快为您处理(人工客服工作时间:9:00-18:30)。
摘 要
Zinc oxide thin films have been grown on (100)-oriented silicon substrate at a temperature of 100℃ by reactive e-beam evaporation. Structural, electrical and optical characteristics have been compared before and after annealing in air by measurements of X-ray diffraction, real and imaginary parts of the dielectric coefficient, refractive index and electrical resistivity. X-ray diffraction measurements have shown that ZnO films are highly c-axis-oriented with a full width at half maximum (FWMH) lower than 0.58. The electrical resistivity increases from 102 V cm to reach a value about 109 V cm after annealing at 750℃. The FWHM decreases after annealing treatment, which proves the crystal quality improvement. Ellipsometer measurements show the improvement of the refractive index and the real dielectric coefficient after annealing treatment at 750℃ of the ZnO films evaporated by electron beam. Atomic force microscopy shows that the surfaces of the electron beam evaporated ZnO are relatively smooth. Finally, a comparative study on structural and optical properties of the electron beamevaporated ZnO and the rf magnetron deposited one is discussed
2. Experimental
A VG V80H MBE system was used to fabricate all the ZnSSe thin films studied in this work. Commercial ITO-coated glass substrates were first cleaned using Decon 90 detergent and then rinsed in de-ionised water in an ultrasonic bath. After being baked dry at 100℃, they were loaded into the MBE system. Prior to the deposition, the substrates were preheated at 380℃ for a period of 20 min. The growth of ZnSSe thin films was carried out using a ZnS compound source and a Se elemental source. There are in total five samples used in this study. Samples 1 and 2 (group I) were grown with the same Se/ZnS flux ratio at substrate temperatures of 330℃ and 290℃, respectively. Samples 3–5 (group II) were grown under a higher (approximately twice) Se/ ZnS flux ratio at substrate temperatures of 310℃, 280℃ and 270℃, respectively. The as-grown thin films were cut into several pieces for various structural chara 电子束蒸发
Effect of annealing on the electrical and optical properties of electron beam evaporated ZnO thin films R. Al Asmar, G. Ferblantier, F. Mailly, P. Gall-Borrut, A. Foucaran* Centre d VElectronique et de Micro-optoe´lectronique de Montpellier, CEM2-UNIVERSITE MONTPELLIER II-UMR CNRS 5507, Place E. Bataillon, 34095 Montpellier, France Thin Solid Films 473 (2005) 49– 53
Materials Science in Semiconductor Processing 4 (2001) 611–616
摘要
The MBE growth of ZnSSe alloy thin films on ITO substrates using ZnS and Se sources was studied and various structural and opto-electronic properties of the as-grown thin films were characterised. The XRD rocking curves resulting from these films indicate that the as-grown polycrystalline ZnSSe thin films have a preferred orientation along (1 1 1) direction. The evaluated crystal sizes as deduced from the FWHM of the XRD layer peaks were found to show a strong growth temperature dependence with the optimised temperature at about 2901C. TEM measurements done on these thin films also indicate a similar growth temperature dependence. The TEM cross-sectional micrograph of the sample grown at the optimised temperature shows a well-defined columnar structure whose nucleation seems to be highly correlated with the ITO grains. UV responsivity as high as 0.01A/W and more than three orders of magnitude in rejection power for wavelengths longer than 450nm have been achieved. It was also found that the sample grown at the optimised temperature has the lowest resistivity of 4.31011Ocm, which provides a good match with that of a liquidcrystal layer. These results indicate that MBE-grown ZnSSe thin film is a promising candidate as the photoconductive material of liquid-crystal light valves for UV imaging applications
Fig. 1. (a) XRD spectrum of as-deposited ZnO film; (b) XRD spectrum of as-deposited and annealed ZnO films.
c)
Fig. 4. (a) AFM image of as-grown ZnO by reactive e-beam; (b) AFM image of the 1 h annealed ZnO at 750 8C prepared by reactive e-beam; (c) AFM image of the as-deposited ZnO by rf magnetron
实验步骤
ZnO thin films have been deposited on (100)-oriented silicon substrates by the reactive electron beam evaporation technique. The residual pressure reached in the chamber was below 1.3104 Pa, the distance between the target and the substrate was 12 cm, the substrate temperature was maintained at 100℃ and the electrons’ energy was about 5.5 keV. High-purity (99.99%) polycrystalline ZnO source has been used as an evaporation source and oxygen gas has been introduced and maintained at a pressure of 102 Pa in the evaporation chamber. Thus, the collisions of O2 molecules with both high-energy electrons and particles evaporated out from ZnO source partly ionize the O2 molecules and improve the film stoichiometry. The film growth rate, which is dependent on the substrate temperature, the oxygen pressure and the filament current of the electron beam, has ranged from 0.3 to 0.4 nm s-1. After the deposition, the films have been annealed for 1 h in air at 550 ℃ and 750℃, respectively, to investigate the effect of annealing on the electrical and optical properties