管道焊缝的无损检测技术及分析
管道焊缝超声波无损检测技术措施

超声波检测1超声波检测介绍焊缝埋藏的缺陷形状、大小、方向、深度等各不相同,超声波检测技术采用一种角度的探头对整个焊缝进行检测。
速度慢,检测结果受操作人员主观意识和检测水平的影响,检测人员劳动强度大,在检测工作量较大的工程中超声波检测技术已成为一种趋势。
超声波检测具有分辨率高、定位、定量准确、缺陷直观、检测速度快、效率高、安全性好、没有辐射等优点。
并能现场出结果,以便跟踪检测,提高焊接质量。
A.工艺流程:2a.● ● ● ●b.● ●c.b. 探头的选用采用频率5MHz ,前沿不大于12mm ,晶片有效面积不大于96mm 2的方晶片斜探头.探头折射角或k 值选择表C.仪器型号CUD-2080数字式超声波探伤仪、DUT-998数字式超声波探伤仪、CTS-22模拟超声波探伤仪。
3 A 型脉冲超声波探伤仪操作规程a.操作前准备● 检测人员操作前必须对所使用的探伤仪的灵敏度在“标准试块”上进行校正,保证探伤仪、探头的组合灵敏度达到要求。
● 正确的选择探头、检测方法。
● 检测人员根据仪器校正得出的数据,在超声波显示屏上绘出“DAC ”线。
●探伤仪电池电量保证充足。
●检测人员必须按规定着装。
b.检测过程●对检测对象的表面状态进行检查,符合检测条件后方可检测。
●涂刷耦合剂。
●将探头置于检测对象表面,根据《工艺卡》和《通用工艺》观察波幅的高低,调节仪器衰减器,正确的判断检测对象内部的缺陷部位及长度。
●对不合格的部位进行标识。
●检测完毕后,检测人员关闭电源并对使用的设备进行擦拭等维护工作并清理检测现场。
●检测完成后应及时给电池充电,充电的方法和时机按照使用说明书的要求进行操作。
●在使用过程中应按照标准的要求,对检测结果和仪器性能进行复验。
c.仪器的维护●本仪器为精密的电子仪器,在日常使用中应慎加维护,使仪器经常处于良好的工作状态。
●本仪器配用的GN电池充足电时,连续工作时间约5小时,若间断工作则时间可以更长,因此,停止使用时,应关掉面板上的“电源”开关,减少耗电。
管道无损检测常用方法

管道无损检测常用方法全文共四篇示例,供读者参考第一篇示例:管道无损检测是指在不影响管道结构完整性的情况下,通过各种检测方法对管道进行检测,以判断管道的运行状态、安全性和维护需求。
管道无损检测是保障管道运行安全的重要手段,可以帮助管道运营单位及时发现管道的隐患和缺陷,有效预防事故发生。
目前,管道无损检测常用的方法包括超声波检测、磁粉检测、涡流检测、射线检测等多种技术手段,下面将分别介绍这些方法的原理、优缺点及应用范围。
超声波检测是一种常用的管道无损检测方法,通过发送和接收超声波信号来检测管道内部的缺陷和损伤。
超声波检测原理是利用声波在介质中传播的特性来识别管道内部的缺陷,不仅可以检测管道的腐蚀、裂纹等缺陷,还能测量管道的壁厚、管壁之间的结合情况等参数。
超声波检测具有检测精度高、适用范围广、操作简便等优点,但是对管道表面质量要求较高,且只能检测到管道表面下方一定深度范围内的缺陷。
磁粉检测是一种利用铁磁性粉末对管道表面进行覆盖,通过施加磁场来检测管道表面裂纹和缺陷的方法。
磁粉检测原理是利用磁铁吸引磁粉末,形成磁粉层,并通过观察磁粉层的变化来判断管道表面是否存在裂纹或缺陷。
磁粉检测方法适用于检测管道表面裂纹、焊缝质量和管道连接情况等问题,但是对表面处理要求较高,且只能检测到管道表面的缺陷。
涡流检测是一种利用感应电流在导体内部引起涡流现象来检测管道内部缺陷的方法。
涡流检测原理是通过在管道表面感应电磁场,当管道表面存在缺陷时,感应电流会发生变化,通过检测感应电流的变化来判断管道内部是否存在缺陷。
涡流检测方法适用于检测管道表面的裂纹、腐蚀和管壁材料变化等问题,具有灵敏度高、速度快、无需接触等优点。
射线检测是一种利用射线穿透物体后被不同组织结构吸收、散射或透射的特性来检测管道内部缺陷的方法。
射线检测原理是通过将射线源对准管道进行照射,通过检测射线在管道内部的吸收情况来判断管道内部是否存在缺陷。
射线检测方法适用于检测管道内部的腐蚀、结构松动、异物等问题,具有检测范围广、准确性高等优点,但是需要专业设备和专业人员操作。
管道焊缝无损检测的综合方法结合及图像处理分析

管道焊缝无损检测的综合方法结合及图像处理分析
管道焊缝无损检测是一种非破坏性检测的方法,主要用于检测焊接质量和管道的完整性。
本文将介绍管道焊缝无损检测的综合方法结合及图像处理分析方法。
管道焊缝无损检测的方法综合,主要包括超声检测、射线检测和磁粉检测。
超声检测主要通过超声波的传播速度和回波信号的强度来检测焊缝的质量。
射线检测是利用射线穿透物体的原理,检测焊缝内部的缺陷。
磁粉检测是在焊缝表面涂覆磁粉,并通过磁场的变化来检测焊缝的缺陷。
在实际操作中,可以综合运用这些方法来提高检测的准确性和可靠性。
可以使用超声检测和射线检测相结合的方法。
超声检测可以检测焊缝内部的细小缺陷,射线检测可以检测焊缝的结构和内部的大缺陷。
两者结合使用可以全面评估焊缝的质量和完整性。
综合运用超声检测、射线检测和磁粉检测可以得到更准确和全面的结果。
可以先使用超声检测来初步筛选出存在问题的焊缝,然后使用射线检测和磁粉检测来进一步确认和评估缺陷的情况。
在图像处理分析方面,可以使用数字图像处理技术来对检测结果进行分析和处理。
可以将检测结果转换成数字图像,然后利用图像处理算法提取焊缝的特征和缺陷信息。
常用的图像处理算法包括图像增强、边缘检测、形态学处理和特征提取等。
通过综合运用管道焊缝无损检测的方法和图像处理分析技术,可以对焊缝进行全面和准确的评估。
这些方法的结合可以提高检测的准确性和可靠性,同时图像处理分析可以提取更多的信息,为焊缝质量评估提供更多的依据。
管道焊缝的无损检测技术及分析
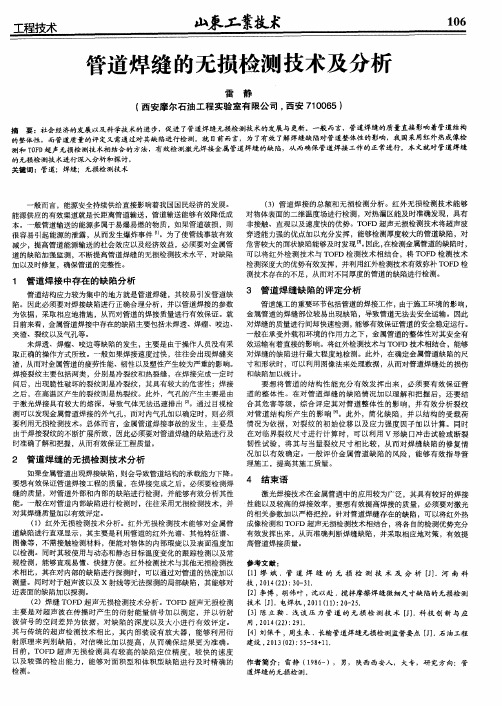
( 3 )管道焊 接的总额 和无损检 测分析 。红 外无损 检测技术 能够 对物体表面 的二维温度 场进行检测 ,对热漏 区能及 时准确发现 ,具有 非接触 、直观 以及 速度快的优势 。T O F D超声无损检 测技术将超声波 穿透能力强 的优 点加以充分发挥 ,能够检测厚度较 大的管道缺陷 ,对 危害较大的面状缺陷能够及时发现 。 因此 , 在检测金属管道的缺 陷时 , 可 以将红外检 测技 术与 T O F D 检测 技术相 结合 ,将 T O F D检测 技术 检测深度大 的优势有效发挥 ,并利用红外检测技术有效 弥补 T OF D检 测技术存在的不足 ,从而对不 同厚度的管道的缺陷进行检测 。
3 管道焊缝缺陷的评定分析
管道施工 的重要环节包括管道 的焊接工作 , 由于施工环境 的影 响 ,
金属管 道的焊缝部位较易 出现缺 陷 ,导致管 道无法去安全运输 。因此 对焊缝 的质量进行 间却快速检测 , 能够有效保证 管道的安全稳定 运行 。 般在承 受外载和环境的作用力之下 , 金属 管道的整体性对其安全 有 效运输有着直接 的影 响。将红 外检 测技 术与 T OF D技术相结合 ,能够 对焊缝 的缺陷进行最大程度地检 测。此外 ,在确定金属管道缺 陷的尺 寸和形 状时 ,可 以利用 图像法来处理 数据 ,从而对管道焊缝处 的损伤
的无损检 测技术进行深入 分析和探讨 。 关键词 :管道;焊缝;无损检 测技术
般而言 ,能源安全 持续供 给直接影响着我 国国民经济 的发 展。 能源供应 的有效 渠道就 是长距离管道输送 ,管道输送能够有效 降低成 本 。一般 管道输 送的能源多属于易爆易燃 的物质 ,如果管 道破 损 ,则 很容 易引起能源 的泄露 ,从而 发生爆炸事件 。为了使管线事故 有效 减少 ,提 高管道 能源输送的社会效应 以及经济效益 ,必须要对金 属管 道 的缺陷加强监测 , 不 断提高管道焊缝的无损检测技术水平 ,对缺陷 加 以及时修复 ,确保管道 的完整性 。
如何利用无损检测技术判断焊接质量

如何利用无损检测技术判断焊接质量无损检测技术是一种能够在不破坏材料完整性的情况下评估材料或结构的方法。
在焊接工艺中,通过利用无损检测技术可以判断焊接质量,确保焊缝的有效性和可靠性。
本文将介绍如何利用无损检测技术判断焊接质量的一些常用方法和原理。
首先,最常用的无损检测技术之一是超声波检测。
超声波检测利用超声波在材料中传播的原理来评估焊缝的质量。
通过将超声波传递到焊接部位,然后接收反射回来的超声波信号,可以获取焊缝内部的信息。
焊接缺陷,如气孔、夹渣、裂纹等会引起超声波的反射或散射,从而产生回波信号。
根据回波信号的特征,可以判断焊接缺陷的类型、大小和位置,并对焊接质量进行评估。
另一种常用的无损检测技术是磁粉检测。
磁粉检测利用磁场的特性来检测焊接缺陷。
通过在焊接部位施加磁场,使得磁粉附着在焊缝表面,然后观察磁粉是否产生裂纹和缺陷的聚集。
如果焊接缺陷存在,磁粉会在缺陷处形成磁路,从而显示出裂纹和缺陷的形态。
磁粉检测可以快速、直观地发现焊接缺陷,对于一些表面缺陷或者局部缺陷的评估非常有效。
此外,液体渗透检测也是一种常用的无损检测技术,尤其适用于表面缺陷的检测。
液体渗透检测通过将渗透液涂覆在焊接部位,然后通过渗透液的渗透作用和表面张力,使得液体进入裂纹和缺陷之中。
随后,使用显色液体或者荧光检测剂来对渗透液进行染色或者发光。
如果存在焊接缺陷,渗透液会从缺陷处渗透出来,并形成可见的染色或者发光,从而判断焊接质量。
除了上述几种常用的无损检测技术之外,还有一些其他方法也可以用于判断焊接质量。
例如,X射线检测和磁力线检测可以用来评估焊接缺陷的内部结构和分布情况。
红外热像仪可以通过检测焊接部位的热量分布来判断焊接质量。
这些方法各有特点,可以根据实际情况选择合适的方法进行使用。
综上所述,无损检测技术在焊接质量评估中起着重要的作用。
超声波检测、磁粉检测、液体渗透检测以及其他一些方法都可以用于判断焊接质量和发现焊接缺陷。
通过准确、及时地使用这些技术,可以提高焊接质量的可靠性和安全性,保障工程项目的顺利进行。
管道焊缝无损检测的综合方法结合及图像处理分析

管道焊缝无损检测的综合方法结合及图像处理分析管道焊缝无损检测是近年来在工业生产中被广泛应用的一项重要技术。
通过对焊缝进行无损检测,可以及时发现焊接质量问题,保障工程的安全和可靠性。
为了提高管道焊缝无损检测的准确性和效率,需要综合运用多种方法并结合图像处理分析技术,以实现更精准的检测和分析。
本文将综合介绍管道焊缝无损检测的综合方法以及图像处理分析的应用。
一、管道焊缝无损检测的综合方法1. 超声波检测超声波检测是一种常用的管道焊缝无损检测方法。
通过超声波的传播和反射来检测管道焊缝中的各种缺陷,如气孔、夹杂、裂纹等。
超声波检测可以实现对焊缝内部的全面检测,并且可以实现对不同材料和不同形状的焊缝进行检测。
2. X射线检测X射线检测是一种通过X射线穿透物体来检测其内部结构的方法。
对于焊缝无损检测来说,X射线可以透过焊缝,形成X射线像,通过对X射线像的分析可以发现焊缝中的各种缺陷。
X射线检测适用于各种材料的焊缝检测,但是需要专门的X射线设备和技术人员来操作。
3. 磁粉检测磁粉检测是一种利用磁性粒子来检测表面和近表面的裂纹、夹杂和其他缺陷的方法。
对于焊缝无损检测来说,磁粉检测可以有效地发现表面和近表面的缺陷,并且可以对不同形状的焊缝进行检测。
以上三种方法分别具有其适用的范围和特点,综合运用这些方法可以实现对焊缝的全面、精准的无损检测。
二、图像处理分析在管道焊缝无损检测中的应用1. 图像获取在管道焊缝无损检测中,需要获取焊缝的图像数据,以便进行后续的分析和处理。
图像可以通过摄像头、扫描仪等设备获取,并且可以得到数字化的图像数据。
2. 图像预处理对于获取的图像数据,需要进行预处理,以去除噪声、增强对比度、调整亮度等操作,以便得到清晰、准确的焊缝图像。
3. 特征提取对于焊缝图像,需要提取其中的特征信息,如尺寸、形状、亮度等特征,以便进行后续的分析和识别。
特征提取可以通过图像处理算法实现,并且可以根据具体的检测要求进行定制化。
管道焊缝测漏方法
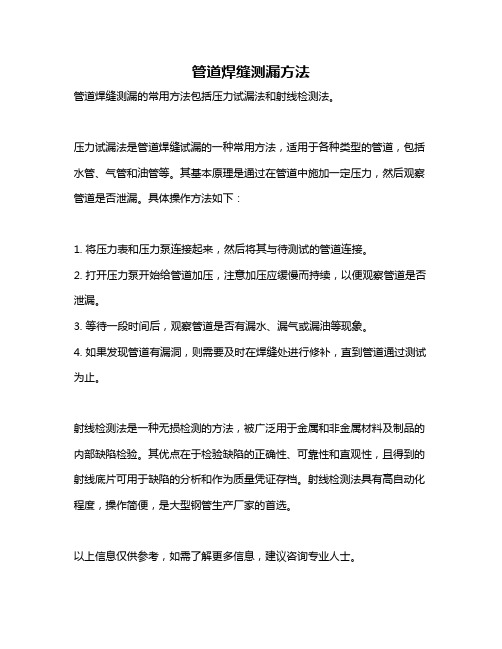
管道焊缝测漏方法
管道焊缝测漏的常用方法包括压力试漏法和射线检测法。
压力试漏法是管道焊缝试漏的一种常用方法,适用于各种类型的管道,包括水管、气管和油管等。
其基本原理是通过在管道中施加一定压力,然后观察管道是否泄漏。
具体操作方法如下:
1. 将压力表和压力泵连接起来,然后将其与待测试的管道连接。
2. 打开压力泵开始给管道加压,注意加压应缓慢而持续,以便观察管道是否泄漏。
3. 等待一段时间后,观察管道是否有漏水、漏气或漏油等现象。
4. 如果发现管道有漏洞,则需要及时在焊缝处进行修补,直到管道通过测试为止。
射线检测法是一种无损检测的方法,被广泛用于金属和非金属材料及制品的内部缺陷检验。
其优点在于检验缺陷的正确性、可靠性和直观性,且得到的射线底片可用于缺陷的分析和作为质量凭证存档。
射线检测法具有高自动化程度,操作简便,是大型钢管生产厂家的首选。
以上信息仅供参考,如需了解更多信息,建议咨询专业人士。
管道对接焊缝的无损检测
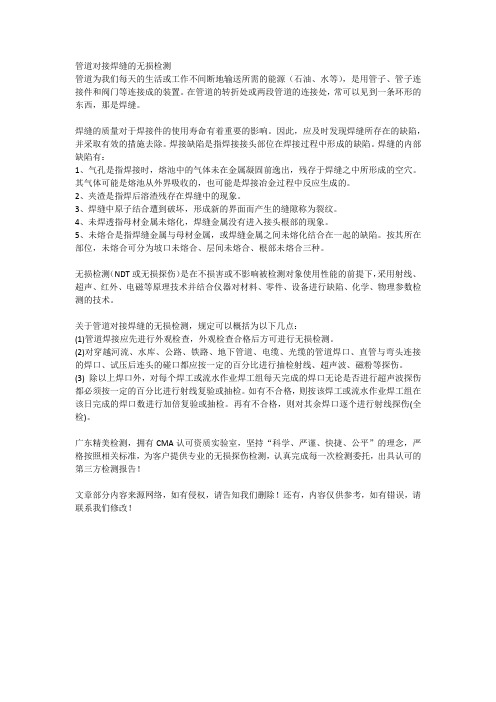
管道对接焊缝的无损检测管道为我们每天的生活或工作不间断地输送所需的能源(石油、水等),是用管子、管子连接件和阀门等连接成的装置。
在管道的转折处或两段管道的连接处,常可以见到一条环形的东西,那是焊缝。
焊缝的质量对于焊接件的使用寿命有着重要的影响。
因此,应及时发现焊缝所存在的缺陷,并采取有效的措施去除。
焊接缺陷是指焊接接头部位在焊接过程中形成的缺陷。
焊缝的内部缺陷有:1、气孔是指焊接时,熔池中的气体未在金属凝固前逸出,残存于焊缝之中所形成的空穴。
其气体可能是熔池从外界吸收的,也可能是焊接冶金过程中反应生成的。
2、夹渣是指焊后溶渣残存在焊缝中的现象。
3、焊缝中原子结合遭到破坏,形成新的界面而产生的缝隙称为裂纹。
4、未焊透指母材金属未熔化,焊缝金属没有进入接头根部的现象。
5、未熔合是指焊缝金属与母材金属,或焊缝金属之间未熔化结合在一起的缺陷。
按其所在部位,未熔合可分为坡口未熔合、层间未熔合、根部未熔合三种。
无损检测(NDT或无损探伤)是在不损害或不影响被检测对象使用性能的前提下,采用射线、超声、红外、电磁等原理技术并结合仪器对材料、零件、设备进行缺陷、化学、物理参数检测的技术。
关于管道对接焊缝的无损检测,规定可以概括为以下几点:(1)管道焊接应先进行外观检查,外观检查合格后方可进行无损检测。
(2)对穿越河流、水库、公路、铁路、地下管道、电缆、光缆的管道焊口、直管与弯头连接的焊口、试压后连头的碰口都应按一定的百分比进行抽检射线、超声波、磁粉等探伤。
(3) 除以上焊口外,对每个焊工或流水作业焊工组每天完成的焊口无论是否进行超声波探伤都必须按一定的百分比进行射线复验或抽检。
如有不合格,则按该焊工或流水作业焊工组在该日完成的焊口数进行加倍复验或抽检。
再有不合格,则对其余焊口逐个进行射线探伤(全检)。
广东精美检测,拥有CMA认可资质实验室,坚持“科学、严谨、快捷、公平”的理念,严格按照相关标准,为客户提供专业的无损探伤检测,认真完成每一次检测委托,出具认可的第三方检测报告!文章部分内容来源网络,如有侵权,请告知我们删除!还有,内容仅供参考,如有错误,请联系我们修改!。
浅析长输压力管道无损检测技术
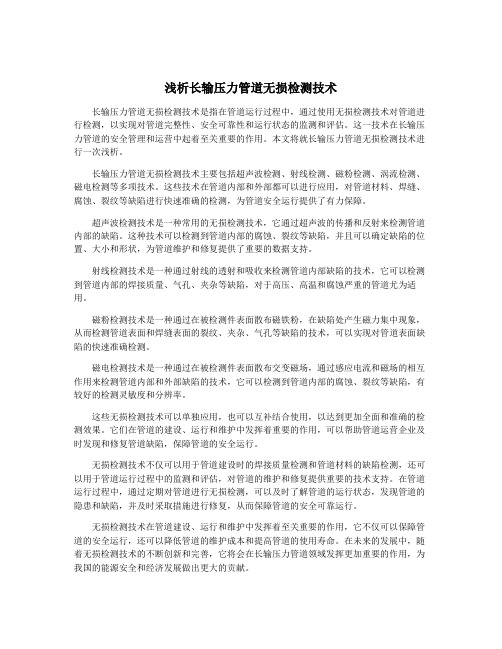
浅析长输压力管道无损检测技术长输压力管道无损检测技术是指在管道运行过程中,通过使用无损检测技术对管道进行检测,以实现对管道完整性、安全可靠性和运行状态的监测和评估。
这一技术在长输压力管道的安全管理和运营中起着至关重要的作用。
本文将就长输压力管道无损检测技术进行一次浅析。
长输压力管道无损检测技术主要包括超声波检测、射线检测、磁粉检测、涡流检测、磁电检测等多项技术。
这些技术在管道内部和外部都可以进行应用,对管道材料、焊缝、腐蚀、裂纹等缺陷进行快速准确的检测,为管道安全运行提供了有力保障。
超声波检测技术是一种常用的无损检测技术,它通过超声波的传播和反射来检测管道内部的缺陷。
这种技术可以检测到管道内部的腐蚀、裂纹等缺陷,并且可以确定缺陷的位置、大小和形状,为管道维护和修复提供了重要的数据支持。
射线检测技术是一种通过射线的透射和吸收来检测管道内部缺陷的技术,它可以检测到管道内部的焊接质量、气孔、夹杂等缺陷,对于高压、高温和腐蚀严重的管道尤为适用。
磁粉检测技术是一种通过在被检测件表面散布磁铁粉,在缺陷处产生磁力集中现象,从而检测管道表面和焊缝表面的裂纹、夹杂、气孔等缺陷的技术,可以实现对管道表面缺陷的快速准确检测。
磁电检测技术是一种通过在被检测件表面散布交变磁场,通过感应电流和磁场的相互作用来检测管道内部和外部缺陷的技术,它可以检测到管道内部的腐蚀、裂纹等缺陷,有较好的检测灵敏度和分辨率。
这些无损检测技术可以单独应用,也可以互补结合使用,以达到更加全面和准确的检测效果。
它们在管道的建设、运行和维护中发挥着重要的作用,可以帮助管道运营企业及时发现和修复管道缺陷,保障管道的安全运行。
无损检测技术不仅可以用于管道建设时的焊接质量检测和管道材料的缺陷检测,还可以用于管道运行过程中的监测和评估,对管道的维护和修复提供重要的技术支持。
在管道运行过程中,通过定期对管道进行无损检测,可以及时了解管道的运行状态,发现管道的隐患和缺陷,并及时采取措施进行修复,从而保障管道的安全可靠运行。
管道焊缝射线检测报告
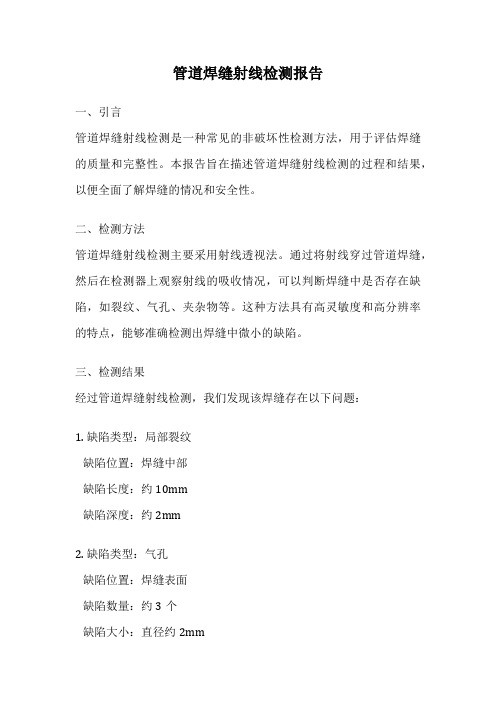
管道焊缝射线检测报告一、引言管道焊缝射线检测是一种常见的非破坏性检测方法,用于评估焊缝的质量和完整性。
本报告旨在描述管道焊缝射线检测的过程和结果,以便全面了解焊缝的情况和安全性。
二、检测方法管道焊缝射线检测主要采用射线透视法。
通过将射线穿过管道焊缝,然后在检测器上观察射线的吸收情况,可以判断焊缝中是否存在缺陷,如裂纹、气孔、夹杂物等。
这种方法具有高灵敏度和高分辨率的特点,能够准确检测出焊缝中微小的缺陷。
三、检测结果经过管道焊缝射线检测,我们发现该焊缝存在以下问题:1. 缺陷类型:局部裂纹缺陷位置:焊缝中部缺陷长度:约10mm缺陷深度:约2mm2. 缺陷类型:气孔缺陷位置:焊缝表面缺陷数量:约3个缺陷大小:直径约2mm四、分析与评估1. 关于局部裂纹由于局部裂纹的存在,焊缝的强度和密封性可能会受到影响。
需要及时修复或更换焊缝,以确保管道的安全运行。
2. 关于气孔尽管气孔的大小较小,但其存在可能导致焊缝的脆性增加,降低焊缝的强度。
建议对气孔进行修复,以保证焊缝的完整性和可靠性。
五、结论管道焊缝射线检测结果显示,该焊缝存在局部裂纹和气孔等缺陷。
这些缺陷可能会对管道的安全性和可靠性产生潜在影响。
建议采取相应的措施,及时修复焊缝,以确保管道的正常运行和安全性。
六、致谢在此,我们感谢所有参与管道焊缝射线检测工作的人员的辛勤付出和专业精神。
他们的努力为管道的安全运行提供了有力的保障。
以上是本次管道焊缝射线检测报告的全部内容。
我们将持续关注管道焊缝的情况,并采取适当的措施,确保管道的安全性和可靠性。
焊缝 无损检测标准

焊缝无损检测标准焊缝是工业生产中常见的连接方式,它被广泛应用于各种行业和领域,如航空航天、汽车制造、建筑和管道工程等。
为了确保焊接质量,防止焊缝存在隐藏的缺陷和问题,无损检测(Non-Destructive Testing,NDT)成为了焊缝质量控制的重要手段之一。
无损检测是通过非破坏性手段对焊缝进行评估,确定焊缝质量是否满足规定标准和要求的一种方法。
下面将介绍焊缝无损检测的标准和方法。
一、国际标准在焊缝无损检测领域,国际标准组织(ISO)是制定国际无损检测标准的主要机构。
ISO制定的无损检测标准根据不同的应用领域和需求,涵盖了多种焊缝的无损检测手段和要求。
其中最具代表性的焊缝无损检测标准包括:1. ISO 9712:无损检测人员资格认证要求和考试考核;2. ISO 17635:焊缝无损检测的术语和定义;3. ISO 10893:用X射线和伽马射线无损检测焊缝的材料;4. ISO 10675:压力设备的焊缝无损检测;5. ISO 17640:用超声波无损检测焊缝。
二、焊缝无损检测方法焊缝无损检测方法根据不同的需要和焊缝类型,可以选择以下几种常用的无损检测技术:1.超声波检测(Ultrasonic Testing,UT):通过超声波的传播和反射,对焊缝内部的缺陷进行检测和评估。
2.射线检测(Radiographic Testing,RT):利用X射线或伽马射线穿透焊缝,获得焊缝的内部缺陷信息。
3.磁粉检测(Magnetic Particle Testing,MT):利用磁场和磁性粒子,检测焊缝表面和近表面的缺陷。
4.渗透检测(Liquid Penetrant Testing,PT):利用带有荧光剂的渗透液,检测焊缝表面的裂纹和杂质。
5.声发射检测(Acoustic Emission Testing,AE):通过探测焊缝产生的声波,识别焊缝中的缺陷和变形。
三、焊缝无损检测标准焊缝无损检测标准主要包括三个方面的内容,分别是资格认证要求、术语和定义、检测程序和评价标准。
燃气管道施工中的管道焊缝无损检测技术

燃气管道施工中的管道焊缝无损检测技术在燃气管道施工中,管道焊缝的质量对于整个工程的安全性和可靠性至关重要。
因此,采用有效的无损检测技术对焊缝进行检测和评估显得尤为重要。
本文将探讨燃气管道施工中常用的管道焊缝无损检测技术,包括其原理、应用以及优缺点。
\textbf{磁粉探伤(MT)}磁粉探伤是一种常用的管道焊缝无损检测方法。
其原理是利用电磁感应原理,将磁粉涂布在待检测的焊缝表面,然后施加磁场,当磁粉遇到焊缝表面的裂纹或缺陷时,会产生磁场扭曲,从而形成磁粉线,用于标记缺陷位置。
磁粉探伤技术具有操作简便、成本较低的优点,对于表面裂纹和缺陷的检测效果较好。
然而,其只能用于检测表面裂纹,对于深层缺陷的检测效果较差。
\textbf{超声波检测(UT)}超声波检测是一种广泛应用于管道焊缝检测的无损检测技术。
其原理是利用超声波在材料中传播的特性,通过探头将超声波传入待检测的焊缝中,当超声波遇到缺陷时,会产生反射或折射,通过分析反射信号可以确定缺陷的位置和大小。
超声波检测技术具有检测深度大、分辨率高的优点,可以检测各种类型的缺陷,包括表面缺陷和深层缺陷。
然而,其需要经过专业培训的操作人员进行操作,并且对焊缝的几何形状和材料性质有一定的要求。
\textbf{射线检测(RT)}射线检测是一种常用的管道焊缝无损检测技术,其原理是利用X射线或γ射线穿透材料,当射线遇到缺陷时,会产生吸收或散射,通过检测射线的强度变化来确定缺陷的位置和大小。
射线检测技术具有检测灵敏度高、适用于各种材料的优点,可以检测到几乎所有类型的缺陷,包括表面缺陷和体内缺陷。
然而,其需要专业设备和专业操作人员,并且对环境和人员安全有一定的要求。
综上所述,磁粉探伤、超声波检测和射线检测是燃气管道施工中常用的管道焊缝无损检测技术。
每种技术都有其独特的优点和局限性,施工单位应根据具体情况选择合适的技术,并确保操作人员经过专业培训,以保证施工质量和工程安全。
压力管道无损检测和焊接技术
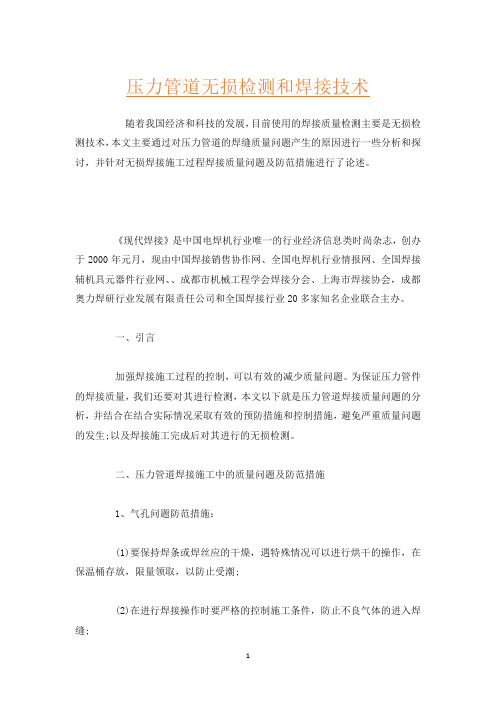
压力管道无损检测和焊接技术随着我国经济和科技的发展,目前使用的焊接质量检测主要是无损检测技术,本文主要通过对压力管道的焊缝质量问题产生的原因进行一些分析和探讨,并针对无损焊接施工过程焊接质量问题及防范措施进行了论述。
《现代焊接》是中国电焊机行业唯一的行业经济信息类时尚杂志,创办于2000年元月,现由中国焊接销售协作网、全国电焊机行业情报网、全国焊接辅机具元器件行业网、、成都市机械工程学会焊接分会、上海市焊接协会,成都奥力焊研行业发展有限责任公司和全国焊接行业20多家知名企业联合主办。
一、引言加强焊接施工过程的控制,可以有效的减少质量问题。
为保证压力管件的焊接质量,我们还要对其进行检测,本文以下就是压力管道焊接质量问题的分析,并结合在结合实际情况采取有效的预防措施和控制措施,避免严重质量问题的发生;以及焊接施工完成后对其进行的无损检测。
二、压力管道焊接施工中的质量问题及防范措施1、气孔问题防范措施:(1)要保持焊条或焊丝应的干燥,遇特殊情况可以进行烘干的操作,在保温桶存放,限量领取,以防止受潮;(2)在进行焊接操作时要严格的控制施工条件,防止不良气体的进入焊缝;(3)要对压力管道焊口有缺陷的部位可以用砂轮进行打磨处理;(4)焊接时要做好防风措施,特别是风对低氢型焊条的焊接施工有着极大影响,因此更加需要严格防风;5.压力管道的管口必须保持清洁和干燥,不能有铁锈、杂质或油污等。
2、夹渣问题防范措施:(1)组对的间隙不应该太小,尽可能在工艺参数的范围之内采取较大的电流,确保焊接的熔深,并且焊速也不能太快;(2)焊道的打磨不能过多、过薄,并且去除压力管道表面的熔渣,还要注意将压力管道的接头打平。
压力管道焊接时根焊道的打磨不合格,会造成热焊能控制烧穿现象,产生夹渣;(3)焊工应该使用正确的操作手法,合理控制运条角度和摆动幅度,以防止焊接熔深不足,容易产生夹渣;(4)断弧、更换焊条是应进行焊口打磨处理;(5)认真的清理压力管道与焊条上的杂质,以及焊道上的熔渣等,在压力管道焊接前要对焊道的毛茬、杂物以及掉落的渣垢等进行及时的清理,以防止这些杂质进入焊道,产生夹渣的现象,在压力管道的焊接过程中要保持熔池的清晰,确保熔渣的液面与熔池金属能够良好分离;6.焊接施工时的焊接速度不能过快,并且要保证熔深。
不锈钢管焊缝无损检测方法介绍

不锈钢管焊缝无损检测方法介绍作者:不锈钢管来源:未知日期:2010/10/4 13:27:50 人气:2 标签:不锈钢管不锈钢管焊缝无损检测导读:(1)渗透探伤(PT)采用带有荧光染料(荧光法)或红色染料(着色法)的渗透剂的渗透作用,来显示焊接接头表面微小缺陷的无损检验法。
检测时一要求被测表面平整光洁。
此方…(1)渗透探伤(PT)采用带有荧光染料(荧光法)或红色染料(着色法)的渗透剂的渗透作用,来显示焊接接头表面微小缺陷的无损检验法。
检测时一要求被测表面平整光洁。
此方法分为荧光探伤和着色探伤,其中荧光探伤的测量精度较高,可达10μm。
焊接构件表面检查常用着色法渗透探伤。
(2)磁粉探伤(MT)利用在强磁场中,铁磁材料表层缺陷产生的漏磁场吸附磁粉的现象而进行的无损检验方法。
在有缺陷处,由于漏磁的作用会集中吸附撒上的铁粉。
可根据吸附铁粉的形状、厚度和多少,来判断焊接缺陷的位置和大小。
该方法不适用无磁性的奥氏体型不锈钢。
(3)射线探伤(RT)采用X射线或γ射线照射焊接接头检查其内部缺陷的一种无损检验方法。
它能准确地显示出焊缝中焊接缺陷的种类、形状、尺寸、位置和分布情况。
评定标准按《钢熔化焊对接接头射线照相法和质量分级》(GB3329-87)进行。
该探伤方法长期操作,对操作者身体有一定的影响。
(4)超声波探伤(UT)借助于超声波探伤仪来检测焊缝内部缺陷的一种无损探伤方法。
此法适用于探伤厚板,可确定5mm以内缺陷。
探伤周期短、成木低、设备简单,对操作者身体无害,但不能准确判断缺陷的性质。
(5)涡流探伤(ET)涡流探伤是以电磁感应原理为基础,当钢管(指碳钢、合金钢和不锈钢)通过交流电的绕组时,钢管表面或近表面出现集肤效应,使其有缺陷部位的涡流发生变化,导致绕组的阻抗或感应电压产生变化,从而得到关于缺陷的信号。
从信号的幅值及相位等可以对缺陷进行判别,能有效地识别钢管内外表面的不连续性缺陷,如裂纹、未焊透、夹渣、气孔、点腐蚀等,对开放性线性缺陷最为敏感。
管道焊接接头无损检测比例及验收标准
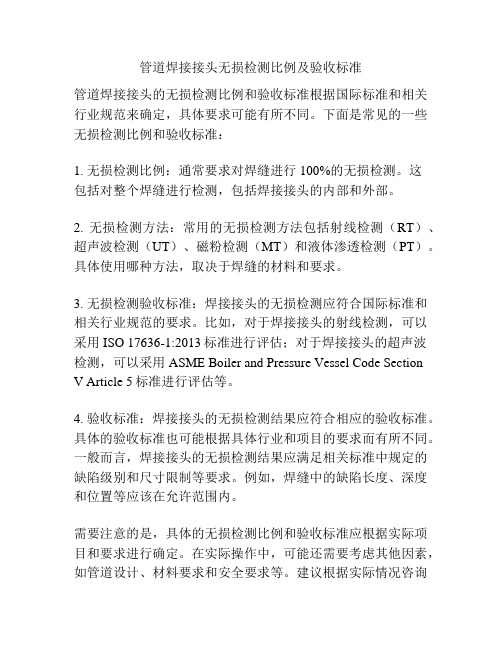
管道焊接接头无损检测比例及验收标准
管道焊接接头的无损检测比例和验收标准根据国际标准和相关行业规范来确定,具体要求可能有所不同。
下面是常见的一些无损检测比例和验收标准:
1. 无损检测比例:通常要求对焊缝进行100%的无损检测。
这
包括对整个焊缝进行检测,包括焊接接头的内部和外部。
2. 无损检测方法:常用的无损检测方法包括射线检测(RT)、超声波检测(UT)、磁粉检测(MT)和液体渗透检测(PT)。
具体使用哪种方法,取决于焊缝的材料和要求。
3. 无损检测验收标准:焊接接头的无损检测应符合国际标准和相关行业规范的要求。
比如,对于焊接接头的射线检测,可以采用ISO 17636-1:2013标准进行评估;对于焊接接头的超声波检测,可以采用ASME Boiler and Pressure Vessel Code Section
V Article 5标准进行评估等。
4. 验收标准:焊接接头的无损检测结果应符合相应的验收标准。
具体的验收标准也可能根据具体行业和项目的要求而有所不同。
一般而言,焊接接头的无损检测结果应满足相关标准中规定的缺陷级别和尺寸限制等要求。
例如,焊缝中的缺陷长度、深度和位置等应该在允许范围内。
需要注意的是,具体的无损检测比例和验收标准应根据实际项目和要求进行确定。
在实际操作中,可能还需要考虑其他因素,如管道设计、材料要求和安全要求等。
建议根据实际情况咨询
专业人士或参考相关资料来确定具体的无损检测比例和验收标准。
管道焊缝检测方法
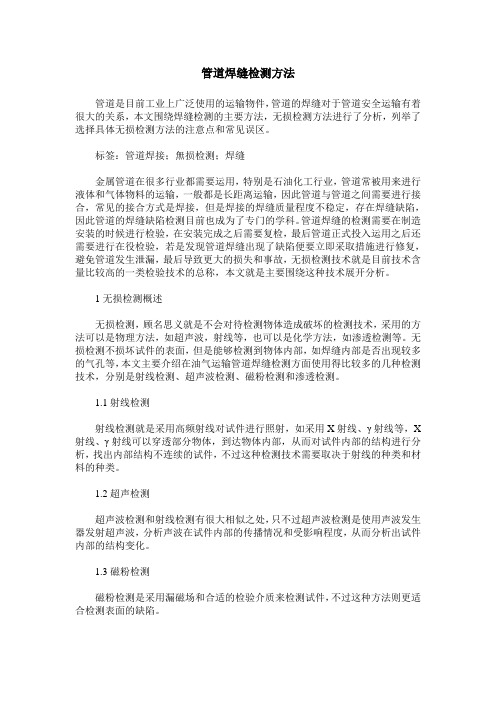
管道焊缝检测方法管道是目前工业上广泛使用的运输物件,管道的焊缝对于管道安全运输有着很大的关系,本文围绕焊缝检测的主要方法,无损检测方法进行了分析,列举了选择具体无损检测方法的注意点和常见误区。
标签:管道焊接;無损检测;焊缝金属管道在很多行业都需要运用,特别是石油化工行业,管道常被用来进行液体和气体物料的运输,一般都是长距离运输,因此管道与管道之间需要进行接合,常见的接合方式是焊接,但是焊接的焊缝质量程度不稳定,存在焊缝缺陷,因此管道的焊缝缺陷检测目前也成为了专门的学科。
管道焊缝的检测需要在制造安装的时候进行检验,在安装完成之后需要复检,最后管道正式投入运用之后还需要进行在役检验,若是发现管道焊缝出现了缺陷便要立即采取措施进行修复,避免管道发生泄漏,最后导致更大的损失和事故,无损检测技术就是目前技术含量比较高的一类检验技术的总称,本文就是主要围绕这种技术展开分析。
1无损检测概述无损检测,顾名思义就是不会对待检测物体造成破坏的检测技术,采用的方法可以是物理方法,如超声波,射线等,也可以是化学方法,如渗透检测等。
无损检测不损坏试件的表面,但是能够检测到物体内部,如焊缝内部是否出现较多的气孔等,本文主要介绍在油气运输管道焊缝检测方面使用得比较多的几种检测技术,分别是射线检测、超声波检测、磁粉检测和渗透检测。
1.1射线检测射线检测就是采用高频射线对试件进行照射,如采用X射线、γ射线等,X 射线、γ射线可以穿透部分物体,到达物体内部,从而对试件内部的结构进行分析,找出内部结构不连续的试件,不过这种检测技术需要取决于射线的种类和材料的种类。
1.2超声检测超声波检测和射线检测有很大相似之处,只不过超声波检测是使用声波发生器发射超声波,分析声波在试件内部的传播情况和受影响程度,从而分析出试件内部的结构变化。
1.3磁粉检测磁粉检测是采用漏磁场和合适的检验介质来检测试件,不过这种方法则更适合检测表面的缺陷。
1.4渗透检测渗透检测需要使用检测液和显像液,先采用检测液从已经在表面看得到缺陷的缺口处注入检测液,之后用显像液将检测液吸至表面,这种检测方法利用的是液体的毛细管渗透作用,也适合于检测表面处的缺陷,和磁粉检测一样不适用于深层缺陷检测。
管道焊缝无损检测的综合方法结合及图像处理分析
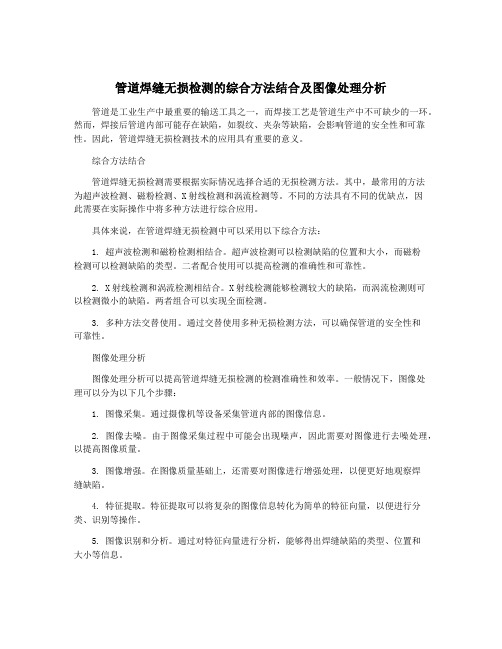
管道焊缝无损检测的综合方法结合及图像处理分析管道是工业生产中最重要的输送工具之一,而焊接工艺是管道生产中不可缺少的一环。
然而,焊接后管道内部可能存在缺陷,如裂纹、夹杂等缺陷,会影响管道的安全性和可靠性。
因此,管道焊缝无损检测技术的应用具有重要的意义。
综合方法结合管道焊缝无损检测需要根据实际情况选择合适的无损检测方法。
其中,最常用的方法为超声波检测、磁粉检测、X射线检测和涡流检测等。
不同的方法具有不同的优缺点,因此需要在实际操作中将多种方法进行综合应用。
具体来说,在管道焊缝无损检测中可以采用以下综合方法:1. 超声波检测和磁粉检测相结合。
超声波检测可以检测缺陷的位置和大小,而磁粉检测可以检测缺陷的类型。
二者配合使用可以提高检测的准确性和可靠性。
2. X射线检测和涡流检测相结合。
X射线检测能够检测较大的缺陷,而涡流检测则可以检测微小的缺陷。
两者组合可以实现全面检测。
3. 多种方法交替使用。
通过交替使用多种无损检测方法,可以确保管道的安全性和可靠性。
图像处理分析图像处理分析可以提高管道焊缝无损检测的检测准确性和效率。
一般情况下,图像处理可以分为以下几个步骤:1. 图像采集。
通过摄像机等设备采集管道内部的图像信息。
2. 图像去噪。
由于图像采集过程中可能会出现噪声,因此需要对图像进行去噪处理,以提高图像质量。
3. 图像增强。
在图像质量基础上,还需要对图像进行增强处理,以便更好地观察焊缝缺陷。
4. 特征提取。
特征提取可以将复杂的图像信息转化为简单的特征向量,以便进行分类、识别等操作。
5. 图像识别和分析。
通过对特征向量进行分析,能够得出焊缝缺陷的类型、位置和大小等信息。
总之,管道焊缝无损检测技术的发展离不开综合方法结合和图像处理分析等技术的应用和提高。
随着技术的不断发展,管道焊缝无损检测技术将会更加智能化和高效化。
27078884_PE燃气管道焊缝缺陷无损检测技术分析

作试验样本。
3.3 力学性能测试的选择
本文讨论的电熔焊接仅指电熔承插焊接。根据
CJJ63—2018表5.1.7-2推荐的检验与试验要求,
进行测试。
3.4 无损检测技术的选择
电熔焊缝缺陷都发生在熔融面处,且受电阻丝
的影响,因此射线检测方法不能有效检出。电熔焊
DDA 检测,A5缺陷焊缝的检测图像见图3。外观检 测发现A3缺陷与 A5缺陷焊缝外部卷边无异常,而 A7缺陷焊缝的外部卷边明显不合格;DDA 检测能 明显检测到3个缺陷焊缝的内部孔洞。这些焊缝均
不合格。
a外观检测
内部卷边不良
MII
b.DDAX 检测
在题
进.外观检测
A.DA 检测
图3 A5 缺陷焊缝的检测图像
声图中电阻丝上方能够揭示熔融区边界的超声反射
燃气行业使用最多的PE 管道规格为DN 110~ 200 mm,因此选取DN 110 mm的PE80、SDR11管道
制作试验样本。
2.3 力学性能测试的选择
根据 CJJ63—2018中表5.1.7-1规定的检验
与试验要求,进行测试。
2.4 无损检测技术的选择
对于非铁磁性材料的内部缺陷检测,射线检测
和超声检测是常用的检测方法。PE 材料透声性能 较差、声衰减严重、折射横波转换困难,且选取的缺
① 图像分析 对0.7t缺陷、0.51缺陷焊缝进行外观和 DDA
检测,0.51缺陷焊缝的检测图像见图4。0.71缺陷、
0.51缺陷焊缝的检测图像基本一致。外观检测发现
焊缝外部卷边对称性较好,但卷边宽度比正常焊接
时明显偏小,DDA 检测能清晰发现内部卷边情况较
管道焊缝无损检测的综合方法结合及图像处理分析
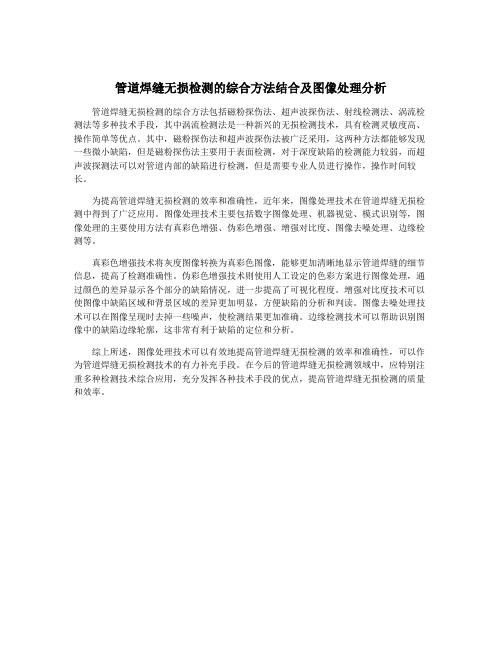
管道焊缝无损检测的综合方法结合及图像处理分析
管道焊缝无损检测的综合方法包括磁粉探伤法、超声波探伤法、射线检测法、涡流检测法等多种技术手段,其中涡流检测法是一种新兴的无损检测技术,具有检测灵敏度高、操作简单等优点。
其中,磁粉探伤法和超声波探伤法被广泛采用,这两种方法都能够发现一些微小缺陷,但是磁粉探伤法主要用于表面检测,对于深度缺陷的检测能力较弱,而超声波探测法可以对管道内部的缺陷进行检测,但是需要专业人员进行操作,操作时间较长。
为提高管道焊缝无损检测的效率和准确性,近年来,图像处理技术在管道焊缝无损检测中得到了广泛应用。
图像处理技术主要包括数字图像处理、机器视觉、模式识别等,图像处理的主要使用方法有真彩色增强、伪彩色增强、增强对比度、图像去噪处理、边缘检测等。
真彩色增强技术将灰度图像转换为真彩色图像,能够更加清晰地显示管道焊缝的细节信息,提高了检测准确性。
伪彩色增强技术则使用人工设定的色彩方案进行图像处理,通过颜色的差异显示各个部分的缺陷情况,进一步提高了可视化程度。
增强对比度技术可以使图像中缺陷区域和背景区域的差异更加明显,方便缺陷的分析和判读。
图像去噪处理技术可以在图像呈现时去掉一些噪声,使检测结果更加准确。
边缘检测技术可以帮助识别图像中的缺陷边缘轮廓,这非常有利于缺陷的定位和分析。
综上所述,图像处理技术可以有效地提高管道焊缝无损检测的效率和准确性,可以作为管道焊缝无损检测技术的有力补充手段。
在今后的管道焊缝无损检测领域中,应特别注重多种检测技术综合应用,充分发挥各种技术手段的优点,提高管道焊缝无损检测的质量和效率。
- 1、下载文档前请自行甄别文档内容的完整性,平台不提供额外的编辑、内容补充、找答案等附加服务。
- 2、"仅部分预览"的文档,不可在线预览部分如存在完整性等问题,可反馈申请退款(可完整预览的文档不适用该条件!)。
- 3、如文档侵犯您的权益,请联系客服反馈,我们会尽快为您处理(人工客服工作时间:9:00-18:30)。
管道焊缝的无损检测技术及分析
作者:雷静
来源:《山东工业技术》2015年第16期
摘要:社会经济的发展以及科学技术的进步,促进了管道焊缝无损检测技术的发展与更新。
一般而言,管道焊缝的质量直接影响着管道结构的整体性,而管道质量的评定又需通过对其缺陷进行检测。
就目前而言,为了有效了解焊缝缺陷对管道整体性的影响,我国采用红外热成像检测和TOFD超声无损检测技术相结合的方法,有效检测激光焊接金属管道焊缝的缺陷,从而确保管道焊接工作的正常进行。
本文就对管道焊缝的无损检测技术进行深入分析和探讨。
关键词:管道;焊缝;无损检测技术
一般而言,能源安全持续供给直接影响着我国国民经济的发展。
能源供应的有效渠道就是长距离管道输送,管道输送能够有效降低成本。
一般管道输送的能源多属于易爆易燃的物质,如果管道破损,则很容易引起能源的泄露,从而发生爆炸事件[1]。
为了使管线事故有效减少,提高管道能源输送的社会效应以及经济效益,必须要对金属管道的缺陷加强监测,不断提高管道焊缝的无损检测技术水平,对缺陷加以及时修复,确保管道的完整性。
1 管道焊接中存在的缺陷分析
管道结构应力较为集中的地方就是管道焊缝,其较易引发管道缺陷。
因此必须要对焊接缺陷进行正确合理分析,并以管道焊接的参数为依据,采取相应地措施,从而对管道的焊接质量进行有效保证。
就目前来看,金属管道焊接中存在的缺陷主要包括未焊透、焊瘤、咬边、夹渣、裂纹以及气孔等。
未焊透、焊瘤、咬边等缺陷的发生,主要是由于操作人员没有采取正确的操作方式所致。
一般如果焊接速度过快,往往会出现焊缝夹渣,从而对金属管道的疲劳性能、韧性以及塑性产生较为严重的影响。
焊接裂纹主要包括两类,分别是冷裂纹和热裂缝,在焊接完成一定时间后,出现脆性破坏的裂纹则是冷裂纹,其具有较大的危害性;焊接之后,在高温区产生的裂纹则是热裂纹。
此外,气孔的产生主要是由于激光焊接具有较大的熔深,导致气体无法迅速排出[2]。
通过目视检测可以发现金属管道焊接的外气孔,而对内气孔加以确定时,则必须要利用无损检测技术。
总体而言,金属管道焊接事故的发生,主要是由于焊接裂纹的不断扩展所致,因此必须要对管道焊缝的缺陷进行及时准确了解和把握,从而有效保证工程质量。
2 管道焊缝的无损检测技术分析
如果金属管道出现焊接缺陷,则会导致管道结构的承载能力下降。
要想有效保证管道焊接工程的质量,在焊接完成之后,必须要检测焊缝的质量,对管道外部和内部的缺陷进行检测,
并能够有效分析其性能。
一般在对管道内部缺陷进行检测时,往往采用无损检测技术,并对其焊缝质量加以有效评定。
(1)红外无损检测技术分析。
红外无损检测技术能够对金属管道缺陷进行直观显示,其主要是利用管道的红外光谱、其他特征谱、图像等,不需接触检测材料,便能对物体的内部瑕疵以及表面温度加以检测。
同时其较使用与动态和静态目标温度变化的跟踪检测以及常规检测,能够直观易懂、快捷方便。
红外检测技术与其他无损检测技术相比,其在对内部的缺陷进行探测时,可以通过对管道的热流加以测量。
同时对于超声波以及X射线等无法探测的局部缺陷,其能够对近表面的缺陷加以探测。
(2)焊缝TOFD超声无损检测技术分析。
TOFD超声无损检测主要是对超声波在传播时产生的衍射能量信号加以测定,并以衍射波信号的空间差异为依据,对缺陷的深度以及大小进行有效评定。
其与传统的超声检测技术相比,其内部装设有放大器,能够利用衍射原理来判别缺陷,对信噪比加以提高,从而确保结果更为准确。
目前,TOFD超声无损检测具有较高的缺陷定位精度,较快的速度以及较强的检出能力,能够对面积型和体积型缺陷进行及时精确的检测。
(3)管道焊接的总额和无损检测分析。
红外无损检测技术能够对物体表面的二维温度场进行检测,对热漏区能及时准确发现,具有非接触、直观以及速度快的优势。
TOFD超声无损检测技术将超声波穿透能力强的优点加以充分发挥,能够检测厚度较大的管道缺陷,对危害较大的面状缺陷能够及时发现[3]。
因此,在检测金属管道的缺陷时,可以将红外检测技术与TOFD检测技术相结合,将TOFD检测技术检测深度大的优势有效发挥,并利用红外检测技术有效弥补TOFD检测技术存在的不足,从而对不同厚度的管道的缺陷进行检测。
3 管道焊缝缺陷的评定分析
管道施工的重要环节包括管道的焊接工作,由于施工环境的影响,金属管道的焊缝部位较易出现缺陷,导致管道无法去安全运输。
因此对焊缝的质量进行间却快速检测,能够有效保证管道的安全稳定运行。
一般在承受外载和环境的作用力之下,金属管道的整体性对其安全有效运输有着直接的影响。
将红外检测技术与TOFD技术相结合,能够对焊缝的缺陷进行最大程度地检测。
此外,在确定金属管道缺陷的尺寸和形状时,可以利用图像法来处理数据,从而对管道焊缝处的损伤和缺陷加以统计。
要想将管道的结构性能充分有效发挥出来,必须要有效保证管道的整体性。
在对管道焊缝的缺陷情况加以理解和把握后,还要结合其危害等级,综合评定其对管道整体性的影响,并有效分析裂纹对管道结构所产生的影响[4]。
此外,简化缺陷,并以结构的受载荷情况为依据,对裂纹的初始位移以及应力强度因子加以计算。
同时在对临界裂纹尺寸进行计算时,可以利用V形缺口冲击试验或断裂韧性试验,将其与当量裂纹尺寸相比较,从而对焊缝缺陷的修复情况加以有效确定。
一般评价金属管道缺陷的风险,能够有效指导管理施工,提高其施工质量。
4 结束语
激光焊接技术在金属管道中的应用较为广泛,其具有较好的焊接性能以及较高的焊接效率,要想有效提高焊接的质量,必须要对激光的相关参数加以严格把控。
针对管道焊缝存在的缺陷,可以将红外热成像检测和TOFD超声无损检测技术相结合,将各自的检测优势充分有效发挥出来,从而准确判断焊缝缺陷,并采取相应地对策,有效提高管道焊接质量。
参考文献:
[1]缪斌.管道焊缝的无损检测技术及分析[J].河南科技,2014(22):30-31.
[2]李博,胡伟叶,沈以赴.搅拌摩擦焊缝微细尺寸缺陷的无损检测技术[J].电焊机,2011(11):20-25.
[3]陈立鞍.浅谈压力管道的无损检测技术[J].科技创新与应用,2014(22):291.
[4]刘保平,周生来.长输管道焊缝无损检测监督要点[J].石油工程建设,2013(02):55-58+11.
作者简介:雷静(1986-),男,陕西西安人,大专,研究方向:管道焊缝的无损检测。